Episodes
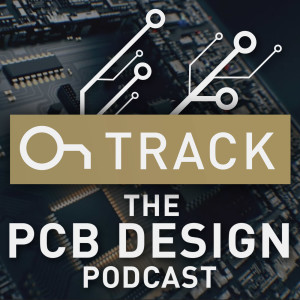
Tuesday Sep 25, 2018
Manufacturing Documentation with Duane Benson
Tuesday Sep 25, 2018
Tuesday Sep 25, 2018
Manufacturing documentation is crucial. Get pro tips from Duane Benson of Screaming Circuits on how to deliver the ideal manufacturing documentation package, so all the technical details are documented exactly as needed. Every fabrication and assembly house is different, so it pays to prepare in advance and find out what documentation to produce for your design to be manufactured. You don’t want to miss this week’s episode; it’s full of practical advice so you can navigate fabrication and assembly effectively and know what to expect in this very complicated process.
See all the show notes here.
Show Highlights:
- ActiveBom - use it! Excel is not the best tool for designing with.
- Traditionally a manufacturing house needs Gerber files. It’s a text file that creates a bit-map.
- More advanced/new way of doing this is with a single file, the most popular being is ODB++ (was proprietary, now public domain)
- What is Gerber X2? Allows you to put intelligent data on top of the Gerbers.
- Once you pick a fab or assembly provider, call and find out what files they prefer. It’s complicated to explain, so call your fabricator and assembly house.
- When you send multiple files, send the same versions. It’s really common to see different versions of files because small changes were made but not all the documentation was updated.
- IPC specifies pin location but so many of the footprints don’t follow the IPC standard.
- This is not a “no touch” process.
- If you need a fast turnaround, then be available 24/hours a day to provide answers and get back to manufacturer immediately. It’s a complex job, things happen.
Ideal Manufacturing Files:
- Everything is current and same version - everything checked
- Read me file - cover anything non-standard, covered clear and concise (include stackup)
- BoM in Excel format, possibly with substitutes
- Intelligent file formats i.e. ODB++
- If Gerbers, include Centroid file and certified that rotations are correct
Hey everyone this is Judy Warner with Altium's OnTrack Podcast thanks for joining again. You will see a familiar face on the screen next to me, but we have a great new topic to talk to you
about that I think you'll find very compelling. Before we get started you know, same old stuff.
Please subscribe to the podcast, please let us know your ideas for future topics, and also
follow us on social media. Of course, I would like to be connected to you on LinkedIn. On Twitter I'm @AltiumJudy and Altium can be found on all the usual social media channels. Something I
don't think I've mentioned before on the podcast is that I also edit the newsletter for Altium, and it also carries the OnTrack brand, so it's the OnTrack Newsletter. Duane Benson who is with me today - from Screaming Circuits, has actually been featured in that newsletter and you can find that at resources.altium.com and also in that area of our website, you can find just oodles
of information. So many, many blogs on subjects you can filter by topic and I think you'd really enjoy it. So again that's resources.altium.com, so jump in and enjoy that.
Well Duane Benson's back again from Screaming Circuits, we connected again recently and we were talking about the the kind of muddy waters of manufacturing files and formats and what it's like for someone like Duane to deal with a variety of issues that come up and so I thought, as
PCB designers, that you would like to learn some tips and tricks - kind of what some of the obstacles are - and get familiar with some language if you're not already, and then hear from an expert of what a manufacturer - what a really good design Manufacturing file package looks like. So Duane, welcome back.
Thank you, thank you for having me I had a lot of fun on the last podcast and you know I have weird, geeky interests, and manufacturing files is one of them, so anytime I get to talk about one of my weird geeky interests, I'm happy.
[laughter] Well I track with that weird geekiness of you, so I know we talked - preparing for
this podcast - it should have taken like 20 minutes; we just went off on a bunch of different topics but hopefully you'll enjoy the results of our geeky conversations. So let's start out with
just defining what you are characterizing as manufacturing files?
Well there isn't a real solid definition of what a manufacturing file set is, but if you think about an electronic design of some sort that starts with an idea in an engineer's head, and it becomes
schematics, it becomes a Bill of Material, it becomes Gerber files, layout files, things of that sort.
Essentially it's an electronic file set of everything that an engineer would feel would be needed to describe their product, and it's in a format that a company like us, an assembly house, and a
board house and part supplier, can read to turn that idea into a working board. So there's an awful lot of things that go into it. You have to describe the raw PC board, you have to describe the components, you have to describe the assembly, and anything special or unique about it. So the manufacturing file set is all of those things necessary for someone, who is not you, who is not in your head, to take your design and turn it into a working board. Well in the case of electronic manufacturing service I think kind of one of the central pieces that comes to mind for me is the Bill of Materials.
So you want to touch on that hot mess? [laughter]
The Bill of Materials really is a hot mess, it is one of the most important files. Unfortunately, this doesn't get the highest profile because it's not you know, the design. That's the bit that everything starts when we're building a board, everything really starts with the Bill of Material and that includes, a typical Bill of Material is again, that's what we need in order to communicate with the distributor to buy your parts, so it will have the manufacturers part number and every single character in that manufacturers part number is important. Some of these things are twenty characters but those little suffixes may determine the temperature grade or something like that, or how its marked, or how it's packaged all that's important as well as the manufacturers name. So you've got the manufacturers part number, the manufacturer's name, and in theory that should be enough. But we always like to be able to double-check things, we always like extras for quality control, so we would like the value of the component as well. So, if it's a 0.01 microfarad, 16 volt 0805 capacitor, we would like that, and then a package size. Again that's a double check, so if we get something that's not even close we can tell, hey that's not the right part. Then we also need the reference designator on the board, that's what tells us where the part goes on the board - the reference designator - and then a line item so that we can easily identify it. If we have to call the designer and say, you know hey this part doesn't fit, we can say it's line item six on the Bill of Materials.
So that was manufacturer, manufacturer's part number, the value, the reference designator, and a line item that we can use to identify it. Other things can go into the Bill of Material, but that's really the minimum set.
And I think, in my - at least, my experience in the past - and you can correct me here, because I'm not as adept as you are here. But I've seen Bill of Materials that are a little messy, and they only have part of the part number, so they just put in the part they know and then you're like, what do I do with this?
Yeah you know, a lot of Engineers have told us that they would love to be able to say, I just want 2.1 microfarad, 16 volt or greater cap, that's it and that's all fine and dandy if you know that, all those other parameters don't matter. A capacitor; it has the dielectric specifications, it has ESR or ISR specifications - you as the designer know if those things matter or don't. We as a manufacturer, don't know that they matter or not. If they don't matter, then sure it'd be awesome to be able to just pull some random capacitor, but we don't know that. So they need to know every single bit of that part number so we can get exactly what you want. That's a bit of a challenge, especially with capacitors and resistors these days, because of allocations - these things come and go out of stock so fast and, so anytime one of those parts is in the Bill of Material and it's out of stock, we've got to call up the engineer and ask for a substitution because again, we don't know if they need a high or a low ESR part and we've had cases where you know someone will send us a Bill of Material in the morning and if we go back to the distributor the next day, some of the parts are out of stock it's just absolutely crazy.
-Yeah.
What that says though, is the important thing is, when you create your Bill of Material, what you're doing over time as you put your design together, make sure that the very last thing you do before sending those files off to the manufacturer, is to verify that those parts are still in stock and if not, find a substitute that you know will work.
That's a good - that's a very good point being the last check. You had asked me a little bit
about a feature inside of Altium Designer called ActiveBOM, so I did a little checking with Ben Jordan about that and so what I learned about that is that it's an interactive BOM management
tool, that's inside the design and it has multiple output files. You can scrub it at any point in the design process kind of like you're saying, do it at the end, but you can do it throughout the design process, and it will tell you the ability to parts, it can help you find alternatives. When you change a part in design it changes the BOM…
-oh nice, I love it.
Nice right, I know, and then flags will appear, like if you're designing and something is at risk of going out of stock, or end-of-life or whatever, a flag will appear on the BOM that will tell you; we better go check this one out and see what's going on. So those flags come up also kind of in real-time throughout the design process so I think that's a really helpful tool and you know I think a lot of designers that are using our tool are jumping into that because I think it would be a
really valuable kind of aspect of our tool. But I know some haven't either, so I just wanted to jump in quick - if you are using Altium Designer and you're not using ActiveBOM, use it
because I think it's an invaluable tool.
Yeah a surprising number of people just use Excel and well, that's what we end up needing, we need an Excel file as the output, but it's not the best tool for designing with.
I know and it's kind of amazing that you know, we can create these little suckers and we're still
doing our BOMs on Excel spreadsheet but, there you have it.
So why don't you go over the type of outputs that are say from a CAD tool - like Altium Designer or any other, the type of outputs that you would typically see?
Okay and this is where the industry is really on the precipice of change, but we're still stuck in the old world. Traditionally, a manufacturer like us, and a board fab house would need a set of Gerber files - and most people know what Gerber files are - if they don't it is a file - a set of files - and there's one file in each set for each layer. So copper would have - top copper would have a file, it is a text file, but I like to describe it as a one bit depth bitmap because it's a text file that creates a bitmap. So you can't, you don't at the moment, have any intelligent information in there. A pad for a component looks exactly like a trace, looks exactly like a pore, so that is the way it's done today but it's not optimal, so you've got the Gerber file set again - one file for
each layer - so you'd output that from your CAD system and you'd put that into a zip file and that's what we would call the Gerber files. Within your CAD system, quite often people will have
an assembly instructions layer, or a fab notes layer, make sure you put those in the Gerber files also, because those are the only real opportunities to integrate information into that Gerber file.
Now if you're going to have the boards assembled, you'll also need something which may be called a centroid, that's what we call it, some people call it a pick and place file, and that has the XY location on the PC board of the component. It has the reference designator, again that's why we need reference designators, and it has the rotation of the component zero to the orientation and the top and bottom side. So Gerbers - with Gerbers you have to have that centroid, or pick and place file, otherwise we don't know where a component goes. That's the basic set and then we would also like something that would have notes that tell us the layer stack up you know, which layer goes where. That's really the minimal set. You also, if you have things like some people for example, don't want to put reference designators on their board and silkscreen. That's really a bad thing, but for aesthetic reasons people don't. Well, then you need a set of fab drawings that tells us where the reference designators are, so that would be another thing that you would need to go in there.
Also in the fab notes would be, if you have overhanging parts for example, these little tiny USB micro-b connectors hang over the edge of the board, and they've got a little tab that goes down. Well if you're having your boards panelized and it's either a v-score or tab routed panel, you can't do that, and build that part, so you have to specify in the fab drawings: don't put a panel tab here, things of that sort. If you've got any special requirements, special material requirements, impedance requirements, ITAR or anything like that, again would go into the fab drawings. So, and the fab drawing can be in your Gerbers, in that fab layer, or it can be a PDF separately, but it has to be clear about what is where. Now that's the old way of doing things, which is still the current way of doing things in most cases right. There are a couple of industry movements to create intelligent CAD files that tell an awful lot more, so you can have one file that has the layers, it has the layer stackup, it has information, the XY information, it has all of that contained within the single file. The most common one of those, in use today is called ODB++, and that was a proprietary file format, but I believe that it's been released into the public domain now. If you can output ODB++ which your software can, that's an awesome way to deliver the information to your assembly house. And you notice I said 'assembly house' there; for some reason the fab folks are often behind the assembly houses in these new file formats because the Gerbers work perfectly well for building up a board.
It is so true, although I have seen more of the modern, more complex, the board houses that do more complex things, they typically have ODB++ integrated throughout their factory, it really leads to more reliability, I think it's a good thing - and of course IPC 2581 right?
Mmhmm, that's the next one good.
Which has been, I was looking it up the other day preparing for this, and I was thinking its' been like 10 years, it's been a long time coming. And I don't know all the ins and outs, but I looked it up, it was started in 2004.
Wow [laughter] 14 years ago!
I mean, I thought it was a long time, but 14 years, and again I don't know what the stop gaps are, but like you said, almost every CAD, I think all the CAD manufacturers output those files
Gerbers, ODB ++, 2581. You talked to me a little bit about Gerber X2 - can you tell me a little bit about that?
Gerber X2 - I have no idea if it's going to catch on or not, or if it's going to be a viable solution, but at some point, the consortium that manages the Gerber standard, decided they'd better get with the program or Gerbers were gonna go away, so they have proposed a new standard, Gerber X2, and I don't think it goes in as in-depth as the ODB ++ or the 2581, but it does allow you to put intelligent data or metadata on top of the Gerber layers. So as I said with today's
Gerbers - I can't tell if a piece of copper is a pad or a pore, it allows you to do that sort of thing, so you can connect up what components are where and whatever information is needed to assemble them. I don't believe that that specification has been signed off on yet and I have a feeling that it's going to be a little bit of a 'too little too late' but I'm just speculating on that point so.
Yeah, and also IPC has, I think you mentioned to me, the D3-56 which is test points right?
Yes, they have I believe, they have test points, I think they even have the full IPC 2581 specification it even has room for the Bill of Material.
That's my understanding.
Yeah I think it's a whole cohesive across all the fab and all the assembly processes but again, it's not something I know a lot about and of course your NC drill files for fabrications. What
else do we need to talk about?
Well one of the, because those file formats are in such flux right now, one of the most
important things to do, is once you have picked an assembly partner and a fab provider, give them a call or send them an email and say, hey what do you prefer? It's even complicated to explain this so I have to tell people, if you have Gerbers send us the Gerbers, and if you're sending Gerber send us the centroid and any Fab or assembly instructions. If you've got ODB++ send us that, but still send us the Gerbers, just in case we need them with the fab house and we need the centroid for this, but not for this...
[laughter] Oh gosh.
Call your fab house...
Can you just send us everything in every format and...
-and that you know, the law of unintended consequences pops up there sometimes
because we will get someone who sends us Gerbers and then we'll say, hey by the way, do you have an ODB ++ and they say yeah, so they send that off. Awesome; except it's a different version. When you send multiple types of files, make sure they are all of the same version, saved at the exact same time...
-the revision it's a different revision you guys... okay. Keep your revisions, keep your old revisions out of the mainstream.
Yeah, what we found is it's real common for, even after a designer hits save for the very last
time, and sends off their files they'll tweak the silkscreen or they'll say, that component wasn't
available, let me use this one and they make these tiny little changes but sometimes it's going to a different package or you know, that part was a 'do not stuff' so let me just take it out of the design now, and so we get different versions of files literally two days apart.
Oh god bless us all, I don't know how we survive this industry. When Duane and I were
preparing for these, this podcast I was saying, you know I left the industry for 12 years and I knew there'd be like a crazy catch up, but when I came back I said I felt like Rip Van Winkle.
I can feel like Rip Van Winkle after leaving for a weekend sometimes [laughter] and I'll
think everything's cool and then Monday...
Yeah he says, I feel that way every Monday [laughter] it's so flippen true!
It is you know, I'll walk out on the manufacturing floor and one of our engineers will say,
hey Duane, because I'm out in the outside world a lot and he waves me down and shows me some component and asks me, have you ever seen this before? What do they do with this? What are we supposed to do with this? And it's like. Oh yeah, I kind of read about that, and I talked to an engineer at a trade show, about that, and it changes so fast and you know, the
changes are not slowing down, they really aren't.
And we're managing them with spreadsheets and multiple file formats just to make it fun.
Yeah and you know, some of it, is our own fault. Because we like to do things fast and you know companies, there are a bunch of companies like mine, who have decided that, gee everybody needs to do this faster than they used to be. And years ago, when I was on the OEM side, to get a board built, it was typically three or four weeks to get it quoted, then three or four weeks for he NPI process, before anybody gets that out in their line. Well those six to eight weeks, we now do in six to eight hours. And so, when you have all that much time, you can go back and forth to the
engineers, you can ask questions. Now you know, 2:00 in the morning one of those questions that were you know, years ago we would have had a week to get answered, now we need it, you know it's 2:00 a.m. we need the answer by 2:10.
We can't blame everybody else, we have to blame ourselves a little bit too.
Right.
I'm gonna blame you. All your fault Duane [laughter] anybody asks me from now on I'll go, it's
Duane's fault. I think a lot of our manufacturing folks would say the same thing, if Duane would just stop promising that.
Right yeah, exactly.
You mentioned a few problems that kind of come up during the chaos of all these different issues that we face and one thing was relative to rotation on IPC standards. Can you talk about that for a moment?
Yeah that's one of my pet projects or 'pet something.' The IPC specifies which pin should be at what part for zero rotation so you've got zero, 90°, 180°, 270°, 360° and anything in between, and what direction goes from zero to 90° on the front or the back, it's specified, it's in these standards, and these ones have been around for a long time. Well what I've found, is a large number of the footprints in CAD software, especially the CAD software that relies on user-generated content more than professionally generated content, a lot of those things, the zero - the pin1 zero rotation is wrong. So for example with an LED or a diode, the cathode is on the left, its horizontal pin one is on the left, and that's zero degrees rotation. We see them where zero degrees rotation has something vertical at 180 degrees, pin one on the right, all sorts of nutty things like that, and that's probably 80% of why we simply can't rely on data maybe even 90%. Theoretically, you should be able to output a set of files from CAD software, send it to a company like ours, and never talk to us and just magically get boards back. A huge portion
of why we can't do that is because so many of these footprints don't follow that IPC standard, and if it were a rare exception, well we'd assume they all do and catch the rare exception there. It's so common, that we have to disregard anything that any of our customers tell us about rotation. Which means we have to have someone look at every single part on that board.
Oh my gosh! It's like a bad version of pin the tail on the donkey. Can you guess which one is pin 1? Have a nice day - oh on all these parts - oh my gosh I don't know how you do anything fast.
It's crazy…
But the cost, I mean some of these parts are super expensive and if you rotate them the wrong way, and you fry them or you wreck the board like, that was a bunch of money.
Yeah we have we run across $10,000 FPGAs we come across ‘one of a kind' parts that are going into some space mission so yeah we really can't risk putting those things on wrong, I'm sorry there are only four these parts in the world don't blow it, okay.
Well and do we - like you said so new parts come out, but when new parts come out, sometimes the standard hasn't been written yet correct?
Yeah we saw that a lot in the early days of the QFNs you know, QFNs all the leads are underneath around the outside of the part and there's this big metal heat slug or ground slug in the middle of the part. The IPC standards didn't cover that yet, and a lot of the CAD software folks had never heard from manufacturers so they didn't know what to do with it. The footprints all had that big heat slug wide open, so then what happens, you put solder paste on that, there's a much higher aspect ratio of heights to volume in the center pad, so the part rises up, it kind of floats up and then all the pins on the outside don't connect and for years, for a few years, nobody knew how to do that, how to make that work properly. Again, if you've got a three week NPI cycle you can figure that out, but when you're doing it overnight... So we determined that you need a window pane solder paste stencil. Fifty to seventy-five percent cover to paste, and it works, but it was a couple of years before the rest of the industry caught up to that and with the tiny, tiny BGAs, point four millimeter pitch BGAs changed the rules on the pad and solder mask with larger BGAs you want non-solder mask defined pads, so you want the solder mask opening to be a little bit larger than the copper. Well with the point four millimeter pitch and
smaller BGAs, that causes the solder balls to squish, and you get bridging.
So you want a solder mask defined path?
Again the rest of the industry didn't keep up with that, because the component manufacturers threw these parts out, without figuring out how to build them...
That's wild.
Yeah and a lot of fun too, I think [laughter]
For those of us that are masochists and gluttons for punishment. [laughter] Okay in all that craziness that you've just spelled out for us. So for our listeners, tell us what a good or a great set, like a clean set of manufacturing files would look like if you could wave a magic wand, and you'd want to see a really clean set of manufacturing files come in?
Okay first of all, everything is the current and the same version, and everything was checked and double-checked just before sending it off to us. There would be a readme file, that includes anything that's non-standard is covered in that readme file, and it's clear, to the point, not wordy - it's not prose, including things like the the stack up. It would have a Bill of Materials in Excel format that has the information we talked about, and possibly even a few substitutes. And then
ideally it would have one of the intelligent file formats like an ODB ++ or an IPC 2581 - that would be the ideal format. If you're stuck with Gerbers, then it has to have a good set of Gerbers. Again with that stack up documented and a centroid file and of course we would love it if someone could could certify that their rotations were correct so we could believe the centroid file but that's really it. Ideally intelligent manufacturing files, a bill of materials, and Excel and a readme file and then if you are using Gerbers, then the Gerbers and the centroid.
Good - well hopefully that will help, hopefully people listen to this podcast and give you some cleaner manufacturing files Duane.
I hope so.
So, something you pointed out to me though, even if you got the perfect set of manufacturing files, we're not robots, and you said something to me: this is not a 'no touch' process.
Yeah.
-you can not throw it over the wall and go about your day so let's wrap up with your thoughts on that.
Well communicate you know, I saw a bumper sticker once that said: I didn't spend four years in engineering school to talk to people. [laughter] But the fact of the matter, you know, we will talk to you using a few sentences. We'll make it short. But talk to us, and anybody who's building your stuff, don't be afraid to pick up the phone and call them, or to have an email exchange.
I know we - a lot of us nerdy people/geeky people whatever, don't like talking to people.
But we have to, and do that, do not be afraid. And if you've sent your boards off, and you're expecting a fast turnaround time, be available 24 hours a day. Companies like us will typically work 24/6 or 24/7, and as I mentioned before, if something happens at 2 am, and things do happen you know. So yeah do we continue the build without it or stop and wait for more? We may need an answer at 2 am - be available, make sure that someone can get a message at 2 am, and then get back to your manufacturer as soon as possible if they contact you. And then do understand that yes, we are all human, we know you're all smart people and we're all smart
people, but everybody... you know it's a complex job we're trying to do
Extremely complex, god bless us all for even attempting to do it, but we do it. We do it and a lot of times we do it quite well so kudos for us in the industry. Well thanks for those tips and kind of clarifying what a clean package will look like. I know it's kind of a convoluted - there's no clear, single path forward. So I think that's really, it's kind of really basic but as you can see from our conversation it's a lot more complicated than it appears on the surface. So thank you so much Duane, for taking the time to clear that up and let us know what works and hopefully give some good advices to some designers out there.
Well thank you for giving me the opportunity I always enjoy these opportunities you know.
We enjoy having you always, and I'm sure we'll have you back again.
So well, that's it for our OnTrack Podcast today, thanks again for joining. Please drop us a message, let us know what else you'd like to hear about. Tune in next time. Until then, remember to always stay on track.