Episodes
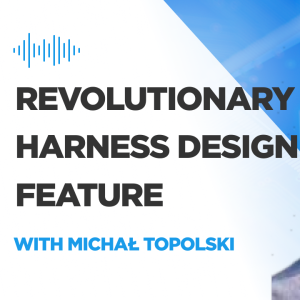
Tuesday Dec 12, 2023
Altium’s Revolutionary Harness Design Feature Unveiled
Tuesday Dec 12, 2023
Tuesday Dec 12, 2023
Explore the world of harness design with Michał Topolski, product manager at Altium, in this episode of the Altium OnTrack podcast. Learn about the two main aspects of harness design—multi-board and harness design itself—and how they are interconnected. Michał delves into the integration with MCAD tools, the importance of data integrity, and the positive user reactions during the open beta phase. Discover the features and improvements in harness design and get a sneak peek into what the future holds for this tool.
Key Highlights:
- Multi-Board & Harness Design: Explore the synergy between multi-board and harness design, unraveling the interconnected world of these crucial aspects.
- Harness Design Overview: Gain insights into the fundamentals of harness design, delving into the significance of BOM and the development rationale.
- Hands-On with Harness Design: Take a closer look at the practical aspects of harness design, understanding its physical dimensions and the seamless integration with Altium Designer.
- Altium Designer Harness Design Integration: Discover the efficiency gains by eliminating back-and-forth processes through Altium Designer's integrated harness design features.
- User Reaction and Workflow Improvements: Hear about the overwhelmingly positive user reactions during the open beta phase and explore the workflow improvements that redefine the design experience.
Transcript
Zach Peterson: So with a harness design, I think people might think of that as like probably two possible things. One might be like a custom cable assembly, one might be a custom connector housing or maybe an off-the-shelf housing that has custom wiring that is built into it. Maybe it's hand assembled, maybe it's factory assembled. But you probably have a bunch of wires spanning between two or more connectors. And then you need to integrate that into the project somehow. Is that correct?
Michał Topolski: Yes, that's precisely it. And we support both of these ways. So you can just have a off-the-Shelf cable connection and you can have it listed in BOM as a single item or you can have your own harnessing wiring drawn and have have it manufactured custom.
Zach Peterson: Hello, everyone and welcome to the Altium OnTrack podcast. I'm your host Zach Peterson. Today I'm talking with Michal Topolski, the product manager here at Altium. As I said in a previous episode, it is that time of the year where AD is coming out with a new version and we get to learn about all the cool new features that are gonna be in the latest version of Altium Designer. So I'm very happy to have Michal with us here today. Thanks for joining us.
Michał Topolski: Yeah, hello. Thank you. Thank you for a brief introduction. Hello to everybody. Yes, yes, as you mentioned, we are now launching briefly AD 24, which is obviously the next version, the next big version count and that's always a good moment to have new features introduced.
Zach Peterson: So one of the themes I've been noticing with the new group of features has been really twofold. One is collaboration and then another is in kind of multi-disciplinary design and really I guess focusing more on product design. And you're working more in the second area. So maybe tell us which feature it is you're overseeing.
Michał Topolski: Yes, thank you for this introduction. So yes, I'm working on electronic product design and part of this of it is a multi-board and the other part is harness design. And these two are very much correlated. So as I believe every electronic engineer knows, there are many elements to the electronic product and obviously, PCBs are the base of it, but then you have to have connect them somehow. So that's when the harnessing comes in. So that's wiring, cabling. We have different names and they obviously mean some other things for some people, but we generally, we call it in Altium Designer, we call it harness design.
Zach Peterson: So with a harness design, I think people might think of that as like probably two possible things. One might be like a custom cable assembly, one might be a custom connector housing or maybe an off-the-shelf housing that has custom wiring that is built into it. Maybe it's hand assembled, maybe it's factory assembled. But you probably have a bunch of wires spanning between two or more connectors. And then you need to integrate that into the project somehow. Is that correct?
Michał Topolski: Yes, that's precisely it. And we support both of these ways. So you can just have a off-the-shelf cable connection and you can have it listed in BOM as a single item or you can have your own harnessing wiring drawn and have it made, have it manufactured custom.
Zach Peterson: So when you say it can be part of the BOM, this could be like a mechanical element that appears in the BOM, is that correct?
Michał Topolski: No, actually harness design is a separate project on its own. So it's like you have schematic and you have PCB, then you have a separate PCB project.
Michał Topolski: Right?
Zach Peterson: Gotcha.
Michał Topolski: And harness design in Altium Designer is a separate harness project, which means it has its own BOM. So yeah, well, technically these elements are mostly mechanical or electro-mechanical if you're concerned with some items. But they are in a different space right now. In the future, we'll connect these two spaces in probably one consolidated BOM in multipart. But that's speaking about the future.
Zach Peterson: So I have to ask, and I think some other people have probably asked this question themselves, why did Altium decide to develop a harness design feature? Altium, obviously known for PCB design software, and then more recently, a lot of the cloud management tools that have really helped propel enterprises to be more productive. But harness design seems a little out of left field to me.
Michał Topolski: To me, it's very complementary. So if an engineer has ever been designing a more complex design, he would notice at some point that there are electrical connections between boards and without Altium Designer, the history is quite the same. So initially, it was obviously, as you mentioned, a PCB design tool, which is very successful in this field. But then we decided that we need to grow because the modern electronic products are not just single PCBs, even very complex, like 16 layers or more, whatever. It's just so much more. So then we created multi-board and when you have this multi-board environment and you have different PCBs and models and electro-mechanical devices in that system, then obviously, you need to connect them somehow. And this is where the harness design comes in. So we've been asked by customers, okay, but I have my PCBs here and here but how do I draw my connections between them? So harness design model is a direct answer to that need and solves this problem. And yes, this is our very first approach to this area. As you mentioned, it might be a bit off in terms of PCB design that Altium's famous for but I think that when our users, and users from the outside that are willing to use Altium projects in the future, we'll see how it's implemented, how it's seamless to use. They'll notice that this is not just another harnessing tool from the electrical world because that's what our competition mostly is. Like, these tools are not tailored for the electrical engineers, electronic engineers. They're tailored for electrical work, like with the big machines and big industry and stuff like that. And in Altium, it's tailored to the needs of creating electronic products.
Zach Peterson: The most recent instance where I needed to do any type of custom interconnect design to go between multiple boards was using actually a flex connection. So doing kind of like a harness design approach, but doing it on a flex ribbon so it could bend and twist and do whatever you needed it to do. So with that type of system, you're really selecting the mating connectors and then you're designing a PCB to then connect everything and then you match up the pinouts. With a harness design, you're actually using wiring. So you're not really using a PCB layout tool to draw out those interconnects. So what does that look like for the user in order to create the physical design, not just the logical design, but the actual physical design?
Michał Topolski: I would say it's very similar to what we have in PCB. So there's this logical layer which is schematic in PCB and we have wiring diagram. You can draw the individual wires and connect splices to them and just route them in the proper way. But then you have the layout drawing and this is something like a PCB in PCB projects. So this is a place where you actually draw the topology. It seems very much like schematic, but it has different objects in Altium. So it uses bundles. So we can draw not just individual wires, but you can route them inside how they are bundled, how they go together. Obviously, we have objects like connection points, which are used to rout these bundles, to assign splice points to these connection points. And yeah, if you look at it, it's very obvious. I may share a sample project so I can show for a second. So this is wiring drawing, a wiring diagram where you can draw individual wires as I mentioned.
Zach Peterson: Well, for those listening on audio, we're looking in the Schematic Editor right now. For those watching on YouTube, you're getting the full view, but on audio, it looks like we have a bunch of boxes drawn out that would typically represent components and then you have the wires drawn between them. So it looks a lot like a schematic and I think it's really familiar for a lot of users.
Michał Topolski: Exactly, and that was our goal 'cause we're in Altium and schematic is a well-known environment, so it's very seamless to learn how to use harness design model because, essentially it looks very much the same at this point. But then we go to layout, which also kind of looks like schematic, but we can route our wires, well, actually route bundles and the wires are routed inside. So it's automatic. When the whole net is defined properly in the wiring diagram, and when the bundles are connected properly in the layout, then the wires inside are routed automatically. So then when in your BOM, you generate your wiring list from two table, which defines from which point the wire goes, and where it ends is defined automatically and generated automatically.
Zach Peterson: So what we're seeing here in this layout, like you said, it looks a lot like a schematic, but we actually see pictures and graphics that show the connectors and then we see what looks like lines drawn to represent the different wiring bundles that go between each of the connectors.
Michał Topolski: I just want to emphasize that these graphics, as you said, they're not just graphics, they are full 3D models of components. So we can actually generate different views in design. So you don't have to pre-prepare these images as you would do in many tools. They're not just simple graphics. They are interactive, sorry. And you can, for instance, have a wireframe view, you can look from different angles. So it's very flexible in that term.
Zach Peterson: So you said there's a wireframe view. Can you describe that for us?
Michał Topolski: Sure, so what you see here right now, it's a full shaded view of a component but in some cases, it's not the best one because some details might not be visible. So we would like to go into pure black and white line mole, which only limits the contours of the component, and this is it. For those who watch us, you can see that, for instance, I have just dynamically changed this shaded model to a wireframe model just like that just because as I said, this is all generated in design. It's not pre-prepared images or graphics.
Zach Peterson: Yeah, I've had to draw out wiring diagrams in the past and I will admit I have had to go onto Google images and search for an image of that connector or find a image on DigiKey or something and copy it into a PowerPoint. So I think it's very convenient that you can automatically create a lot of these assets directly inside of Altium Designer. So this is all really interesting and one thing I, of course, have to ask is was this something that was in really high demand with users?
Michał Topolski: It was in high demand, especially among those users that were multi-board adopters, that were using multi-board previously because they have noticed the need. And this is also an endless cycle because if we get more people that are using multi-board, they get to use harness and then the other way, they also use more of the multi-board. So that's good, that's good for us and that's also good for users because then we get more attention, which means we get more development on that and we can improve it faster. So yes, we're listening very carefully to all feedback about multi-board and harness very much these days because I think the tool is very good and we have many voices of our customers that are happy with what it is. But we also know that there's a long road ahead of us, and yes, we're trying to catch all the voices. It might take some time, just be warned but in the end, I think we're gonna make it a really seamless tool for everybody that's interested.
Zach Peterson: And so this is gonna be included with all the standard multi-board design tools? This isn't like an external feature that you have to purchase or anything like that?
Michał Topolski: No, but it's where we're emphasizing that. As you mentioned, this is part of multi-board. So product design suite and this is Pro and Enterprise license level. It's not standard. Unfortunately, harness design right now, it's not standard but it's Pro and Enterprise and while harness design can be used as a standalone project, so we don't need to have a multi-board project to actually have a harness project. They can be separate project, that's no big deal. But we encourage people to use multi-board project first because if you define your connectivity inside multi-board, then it goes into the harness design. So they are interconnected this way and we plan for this connection, this strict connection between these two environments to really bloom in the future. We would like to have end-to-end connectivity checks and stuff like that. So brace yourselves. I think some interesting things are coming in this environment. But coming back to licensing, I also wanted to mention that while A365 is not necessary for using harness design but to use harness-specific library components, like wires and cables, we actually need A365 because this is a cloud-enabled feature. So you can have your wires and cables inside harness design but if you want to store them in the library, you're gonna need the A365.
Zach Peterson: Sure, that makes sense. So you brought up things like wiring and storage in the library. I guess that begs the question, what sort of information is needed to input into a design in order to use everything successfully? I ask that because obviously, we're talking about wiring harnesses. So you need wires. You need connector body. You probably also need something like, I don't know, crimp contacts. And maybe if it's gonna be hand assembled, there's gonna be a special tooling that's needed. What's the complete suite of information that someone would need in order to create a project and then pass the documentation off to their assembler who can then make this design into a physical object?
Michał Topolski: Harness designing work is not very standardized. So I would say it very much depends on individual process of the company that is using it. I've been speaking to many customers and some of them just limit to drawing connectors but very generic. They don't even have to use models. They don't care very much about the lengths and margins, production margins about how many twister are and stuff like that. They just leave it to their manufacturers because they outsource it. And then you obviously need some lower level detail. But then some of these companies also are manufacturing samples or even small batches inside their facilities and then they need complete information because they use it directly like a flow below. So yeah, I would say it very much depends. But the basic set would be obviously to have some connectors that you would like to use. But again, if you utilize multi-board, you can define mating connectors in there and then they will be brought to wiring diagrams. So you wouldn't start from scratch. You would have them in there. Then you also have to draw wires but you don't necessarily need to have them predefined. You can always change properties and like components inside the design. So you can think of wires that you have as a generic components idea that we have in schematics. So we just place generic component, generic wire and then you can assign a component or assign properties to it, whatever you would like to do. And well, I'd say that basically that that's it 'cause then other things are purely your design. So you define splices, you define the topology and from that, you can bring these drawings to Draftsman and generate your manufacturing drawings.
Zach Peterson: So as far as like what the wiring is concerned, there are some properties that you could assign as I think what you said. So that could be like wire gauge, strip length, number, you said number of twists, which which would make sense. Number of strands if it's stranded wire, those kinds of things.
Michał Topolski: Yes, exactly, exactly. Color, gauge. These are very basic stuff. And one thing that maybe it's worth mentioning at this point is as I've been showing this layout, drawing, some may have noticed, this is a 2D, so two-dimensional drawing, it's flat only. And many complex harnesses are needed to be routed in 3D environment. And this is right now not possible inside Altium but we have CoDesigner feature, which has been with us for many years now and I think many Altium users are familiar of that. We right now have tests with Creo regarding current design integration, which means that you can take your wiring diagram and direct the information stream directly to MCAD, so you then get connectors, you get the connectivity, you get it from to table inside Creo and then you can route the design in 3D in there and then get back with the information, which is most crucial, which means lengths. And with these lengths, you can create your BOM and your lengths, wires and stuff like that. So this is a flow that many customers has been asking about and right now, as I said, this is Creo but we intend to also support our other environments, which CoDesigner already supports for PCBs.
Zach Peterson: So that's really interesting. It sounds like someone can take the import from the harness design in terms of let's say the connections, connector bodies and what's involved in terms of wiring. The mechanical engineer can then place those, move them around to where they need to be inside an enclosure and then that information can get pushed back into the harness design. Is that the correct way to think about it?
Michał Topolski: Right now, it's less about positions, especially in three-dimensional space. We don't support that yet inside harness design. It's more about the pure length because there's a difference if you route a cable or wire in between two points and you do not take into consideration how they're routed in 3D space because they might go around some elements that you have and if you don't account for that, then the wire would be just too short. You just draw it on plane surface. So this is actually the goal here right now, but there are some plans to bring the 3D model of harness design that you design in MCAD to a multi-board assembly environment. So then you have this represented inside our Altium environment and as I mentioned before, 'cause we own the connectivity that you defined in multi-board, we can also show point-to-point connections in the future obviously. So yeah, this is our goal here.
Zach Peterson: So this is interesting because I think normally, someone might use an MCAD application to try and model a wiring harness. I know that there are specialty applications that are out there that are specifically for wiring and cabling and stuff. But I think as you said, they're for larger machines, industrial settings, that kind of thing. It sounds like the real difference with an MCAD application is that the MCAD application has the ability to give the information back to the PCB designer so that they can quickly generate an entire bill of materials for every part in their system. So each of the PCBs, the cable, cable assembly, all of that.
Michał Topolski: Exactly, exactly. That's the way we see it. And this is a place where actually starting harness design, not in MCAD but in Altium Designer and harness design model can be superior to just purely MCAD. Obviously, there are some components that we don't have in Altium, which would be like fasteners and some mechanical parts. And obviously, the enclosure, so it has to be designed in MCAD environment and about that, this is the way to do it. But then, I think in the end, at least this is what I've learned, there are many, many engineers that would like to own this information inside Altium and generate, as you mentioned, this unified documentation from Altium Designer.
Zach Peterson: So if you were starting in the MCAD side and then going into defining the constraints for the PCB, essentially the MCAD user would have an opportunity to possibly select some of those connectors on the front end and then just pass that information onto the designer, rather than having the designer receive the board and the enclosure information and then try to fit connectors within that. Then it has to get passed back again to get verified. And so you eliminate some of that back and forth if the MCAD user could start first. Would you agree?
Michał Topolski: Yes, yes, that's perfectly the goal. I think it's not yet supported exactly the way you described it. This is the ultimate goal. Right now, we usually start with the information from harness design, but I think it's like a new feature if we do that 'cause right now, we're very much focusing on the integrity of the data, so there is no corruption happening. That's the most crucial for us. And all these improvements, like starting in MCAD, defining connectors there, other parts, obviously, it's coming as well.
Zach Peterson: Okay, but at at least someone could start an MCAD and at least have kind of a paper doll model and then say these are your three connectors, copy and paste into a Slack chat or something and then the designer can just take that, put it in their BOM and then they're off and running. So I think you mentioned two other tools within Altium Designer where there's an integration with harness design that was Draftsman and then exporting to the BOM, is that correct?
Michał Topolski: Harness design is a standard BOM, as you know from PCB projects, and standard Draftsman, as you know, from PCB projects. And I think this is the only way to do it actually in Altium. So they have this unified environment. This is our goal. This is still one Altium design. There is no separate harness design software. It's part of our suite. So it's only only natural for us to utilize the same environments. And I think it's very, very useful. I've heard these kind of voices that having wiring diagram and layout drawing in the same drawing, in the end, is something that not many tools in the market can do and can be beneficial. And also our active BOM and our connection to the Octopart and having lifecycle statuses and all that, that's also very, very useful to engineers to not design something that will be obsolete in a month or so. That would be very bad.
Zach Peterson: So inside of Draftsman, for example, since this is all its own project, essentially, you're just placing the region where you want the wiring harness drawing to appear in Draftsman, right click, import and then bam, your drawing appears there.
Michał Topolski: And when you make changes to one of these drawings, wiring or layout, you just have to again click the magic import button and it updates. That's it. That's all we need.
Zach Peterson: Very cool. Very cool. So I think we have time for one more question, which is really about the user reaction. I know that earlier I asked you if it was in high demand and now that it's been in beta for a little bit, I have to ask, what's been the user reaction? What are people saying, positive or negative?
Michał Topolski: Yes, thank you very much for this question. User reaction was largely positive, very positive. And I want to emphasize that when we launched into open beta in January, that was after a few months of development with some very, very engaged customers that were helping us to get through the MVP process. So when we launched, well, it was a newborn obviously. But I think the dynamics of the team that is developing the tool and all the people that are involved in the process, especially customers and everyone that's helping is really helping us to learn this baby to walk very fast and then ride a bike very soon also. So the reactions are very positive and this dynamic is also very visible to people. I've heard reactions like, "Oh, we have not seen this tool for three months 'cause we're exploring and now we're exploring again 'cause we have a project that we need harness for and it's a different tool now. It's so much better." So yeah, that's like genuinely the reaction I've had and I hope that this will persist in future. So that's the message to everyone that has been exploring Altium harness design in January this year and has dropped it since. And please, try again. If not now, then in January in '24 when the tool will to go out of open beta. You'll notice that the tool has changed a lot. It has become much more stable and there are many features that were missing, the big ones, but also the small ones, you know, the quality of life improvements, all that. I think it's very important. Especially in last months, we were very focused on improving all these tiny little things that are very useful in everyday life of every engineer. So just to reduce the count of clicks and all these things that make us bored and nervous at some point. So yes, and I also would like to encourage everyone that has touched the tool, but not only harness design, I mean about Altium Designer to go to forum if you have not done it and express your voice because this feedback really matters. We would like to hear that. I am one of the people that would like to hear it, we listen to it. And then we react to these voices when creating the tools for you.
Zach Peterson: Yeah, we'll include a link to the forum in the show notes. So final question before we let you go. You alluded to some potential improvements on the workflow, like starting from MCAD, going back to PCB. Are there any other interesting nuances or feature upgrades or improvements to this tool that are on the horizon that you can reveal? Or are people just gonna have to subscribe to the channel if they wanna learn more?
Michał Topolski: I'll just generally say that we seek for improvements, some big improvements in the management of components, how they are linked in between and there are also some improvements coming in terms of how you can define models inside multi-board. But I don't want to go into details right now 'cause as you know, deadlines are dangerous. I should not be showing any details about these. So just please stay tuned and if you are interested in some very particular features that you would like to see or have heard about from somebody, then just please contact us directly and we'll have a chat.
Zach Peterson: Sounds great, and I guess as all of this rolls out and slowly improves over time, we'd love to have you back to talk about this more.
Michał Topolski: Thank you very much.
Zach Peterson: Thank you very much. To everyone that's been listening on audio or watching on YouTube, We've been talking with Michal Topolski, product manager at Altium who is overseeing the harness design rollout. If you are watching on YouTube, make sure to hit the Subscribe button, hit the Like button. You'll be able to keep up with all of our tutorials and feature announcements as they become available. And last but not least, don't stop learning, stay OnTrack and we will see you next time. Thanks, everybody.