Episodes
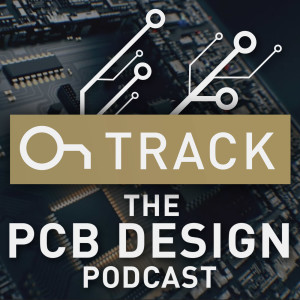
Tuesday May 14, 2019
Dk And How Datasheets Impact Your Design
Tuesday May 14, 2019
Tuesday May 14, 2019
If you design in RF, microwave or millimeter wave frequencies today’s podcast is for you. Today we talk to John Coonrad who’s the Technical Marketing Manager for Rogers Corporation, a Global Manufacturer of advanced circuit materials. John talks about what dielectric constant (Dk) is exactly, the various test methods for Dk, why datasheets can sometimes be confusing and how all of this impacts your design.
Trade In Your Outdated PCB Design Tool & Unlock 45% OFF Altium Designer today!
Show Highlights:
- John has been in the PCB industry for 32 years. His journey with Rogers began back in ‘87 when they had a division called FID (Flexible Interconnect Division) - he jokes that he was born and raised on flex circuits!
- For the past 11 years, John has been working specifically with the RF characterization of their materials as well as marketing and has been published in several trade magazines. John also chairs the IPC D24C Committee which defines high-frequency test methods for the industry.
- A working definition of Dk: The property of a material to sustain an electric charge by applying an electric GIL to it.
- In other words, dielectric constant is the ability to hold a charge and also to affect the electrical properties in regards to capacitance.
- On datasheets, the Dk can be inconsistent, which means that various manufacturers could provide different values because of how they’re testing which depends on what segment of the industry they’re serving.
- Rogers is unique because they choose to differentiate between Design Dk and Process Dk.
- Rogers performs a raw material test and does not test circuits.
- Using a clamp stripline test there is typically some trapped air, which has a lower dielectric constant and will cause a lower Dk overall.
- TIP: It’s helpful to check what test was performed when comparing datasheets.
- Currently, Rogers uses a test method specific to their in-house requirements which is process control as well as good QA test of the raw material, which is the Process Dk.
- Another test method is looking at how the Dk of the material is perceived in circuit form, i.e. testing microstrip transmission line circuits and extracting the behavior of the RF performance to get to the Dk of the material in circuit form - which is called Design Dk and provides a more realistic/real-world number.
- Bottom line: different test methods deliver different values.
- Other test methods out there: IPC has 15; the clamp stripline test is most common; full sheet resonance non-destructive test (FSR); split post dielectric resonance (SPDR), etc
- Because of the way electrical fields move through the dielectric, it’s not all about the traces, but the laminate has a massive impact, which is another reason why John’s work is so critical.
- As the chip industry evolves, there are more applications for millimeter wave frequencies - the higher the frequency the smaller the wavelength, making it more sensitive to any differences in material.
- With millimeter-wave frequencies, small differences in value can cause significant problems, especially in the automotive industry.
- Implications of incorrect Dk: Depending on the application, such as military guidance systems and base station equipment the Dk obviously has to be spot on.
- Pervasive misunderstandings that impact design engineers today: Not everything is taught in training institutions - for example, TCDk (temperature coefficient of the dielectric constant of the material) is often not accounted for. Circuit influences are also not accounted for but plated finish can affect the phase.
- How to learn about TCDK? Some sources: IEEE website; manufacturers of materials, and Rogers as well as John’s articles (see below).
- What’s driving more applications in the millimeter range? Designers and manufacturers of chips are now able to provide much higher frequency applications. The chips are being used for more varied applications.
- Is the increasing speed limiting PCB manufacturing? As you get to the higher frequencies, the features are very small and thus must be well-defined to avoid even little etching anomalies causing disruptions.
- What enabling technologies are emerging? For circuit fabrication, LDI is a definite plus. Regarding additives, some companies such as Averatek are doing excellent work and may be a potential solution.
- Thinner copper also enables fewer problems with surface waves. There’s also coupled circuit features.
- The line between chip design and board design could blur and we may adopt the precision and miniaturization.
Links and Resources:
Tech Hub
Rogers and Autonomous Driving
Rogers and 5G
Website Tools Page
Rogers ACS YouTube Page
Trade In Your Outdated PCB Design Tool & Unlock 45% OFF Altium Designer today!
Read additional articles:
The Influence of Test Method Conductor Profile and Substrate Anisotropy on the Permittivity Values Required for Accurate Modeling of High Frequency Planar Circuits, read here.
Methods for Characterizing the Dielectric Constant of Microwave PCB Laminates, read here.
Read additional articles on the Microwave Journal:
Searching for a Standard Millimeter Wave Dk Test Method, read here.
Compare Materials in a Meaningful Way, read here.
Which Dk Value is Right for my Computer Simulation, read here.
Changing Temperature Can Change Circuit Performance, read here.