Episodes
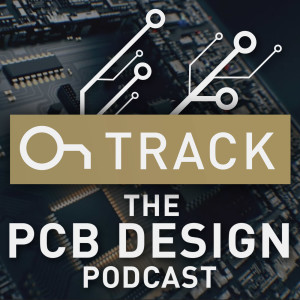
Tuesday Jul 17, 2018
Paste Interconnects and Paste Sintering with Chris Hunrath from Insulectro
Tuesday Jul 17, 2018
Tuesday Jul 17, 2018
Paste Don’t Plate! People are doing 90 layer multilayers with paste interconnects. Want to learn more? Find out about paste sintering from Chris Hunrath to learn more about its applications and benefits to PCB designers. What must designers consider and what are the advantages of Ormet’s products? Listen in for insights from the expert in this week’s episode.
Show Highlights:
- New material developments make paste interconnect technology more feasible
- Ormet’s paste sinters at one temperature forming a new alloy with higher melting point
- Paste interconnects allow for changing build sequence in which vias are formed i.e. drill, add paste, and then laminate - giving you interconnects inside a double-sided core with no visible vias
- Multilayer PCBs: Can split up a 32-layer board to two 16-layers (even as many as 4 x 18 layer multilayers - which is much easier to build
- Also reduces risk depending on design - electrically test each half and only use the good ones
- Ormet process/paste interconnect process eliminates traditional drawbacks i.e. excess copper on surface features
- Eliminate backdrilling with paste interconnect process without extra copper in the via
- Ormet paste eliminates electrolysis and plating process
- Signal integrity benefits
- Applications: RF, high-layer multi cap, avoid secondary remelt, downhole assembly etc
- Design considerations: Where to split up layers for best design benefit; Via at 1:1 or less aspect ratio - only in 1 B stage layer and correct size via for applying paste; Size of receptor pad for laser drill via must be correct to prevent paste from running - spread glass is good for B-stage; annular ring around the via to register laser drilling; with many paste interconnects - don't paste to the edge.
- Paste melts and forms alloy with inter layer copper creating a permanent metallurgical joint
- People are doing 90 layer multilayers with paste interconnects.
- HDPUG (HDP User Group) is creating HDI test vehicles with paste interconnects and HDPUG members will have access to reliability data for breaking up big PCBs
- Paste don’t plate!
- Future topics: Many ways to use conductive inks in electronics, copper foil, integrity issues and printed electronics. Material science behind electronics, new design tools, various versions of conductive inks
Links and Resources:
Chris Hunrath on Linkedin
Click to listen to Chris Hunrath’s other episodes about Spread Glass or Material Sets.
Hi everyone. This is Judy Warner with Altium's OnTrack Podcast. Welcome back, here we are again with your friend and mine, Chris Hunrath from Insulectro who's going to teach us about paste sintering today, which I don't know much about, but we're going to learn about it together. But before we get started, remember to hit all the typical Altium social media platforms Facebook, LinkedIn, and Twitter please follow me on LinkedIn and also remember we are recording on YouTube as well as Podbean and we can be found on all your favorite podcast apps.
Alright, so today we're going to talk about - I don't even know how to set this up entirely cause I'm just as much as a student. So Chris, welcome back! Thank you again, and I know this isn't a new technology - it's just not one that has crossed my path. So tell us about what paste sintering is and what the applications are, and benefits to our designers that are listening today?
Okay, interconnect technology, as you mentioned is not new, what's happened recently though is there's been some new material developments that make it more feasible for the circuit boards. Certainly in ceramic fire technology, metal - powdered metals have been used to make interconnects and traces and circuits on ceramic circuit boards, but those fire at 850-plus degrees Celsius, which would obviously destroy most PCB materials so there's some new technologies out now. There are different kinds of pastes that are used for interconnects. The one that we work with, and the one that we promote, is something from a company called Ormet, and their material is interesting because it sinters at one temperature and then it forms a new alloy with a higher melting point.
Okay I feel like we need to back up and explain what paste interconnect technology actually is. Like how it's performed and then we can go into the material science part just so I can keep up, Chris I want to be able to keep up.
So multi-layer PCBs - also not new - typically what you do is, you print and edge any number of layers, you drill and then you plate. Typically electroless copper, to make the non-conductive surfaces conductive, and then you build up the thickness with electrolytic copper.
Mmm-hm.
And some people call it a semi-edited process, because you are using the electroless first as a seed layer. There are some other technologies used to make that dielectric surface conductive, and then you build up with electrolytic copper and so that's how you link the layers of the z-axis.
So if you think of a classically - as a circuit board - as a web of foils printed and etched, all your XY connections, and then the drilled holes - whether they're laser drilled, blind vias, or drilled through holes, the plating links everything in the z-axis. Now one of the challenges when you do that, is you're consuming real estate at all the layers. So let's say you have a 12 layer multi-layer - relatively simple multi-layer by today's standards - but you need to connect layer 1 to layer 10 you've taken up the real estate in all the other layers - you can't route circuits in those places, because there's a via in the way, unless you wanted them to connect to that via and they're part of that net. So there's a term called any layer HDI - I don't know if you're familiar with that term? Basically it means you could put a via anywhere you want in any layer. Nowadays that's done typically by what we call build up technology. So you start with a core of some sort - again it could be double sided, it could be a multi-layer core, and then you sequentially build layers and you only go one layer deep with a laser drill sometimes two - depending on the design - but that's not true for any layer.
Anyway, you go one layer deep you plate, you print and etch, and you do it again and again and that allows you to put vias almost anywhere you want in any layer, the downside is, it's almost like building multiple circuit boards. So the cost really starts to increase. And of course you're putting the board through multiple lamination cycles and that has some undesirable material side effects depending on the material. Some materials can withstand three lamination cycles, some six, some ten, but it is hard on the materials to go through that lamination process, over and over again.
Right.
Especially electric phenolics, which are very common for lead-free assembly, because they're relatively economic and they're also - they also will survive lead pre-assembly, but they tend to get more brittle every time they see a thermal cycle though, so that causes some issues too. So what paste interconnects allow you to do, is change the sequence in which the vias are formed. So instead of laminating drilling and plating you can actually drill, add the paste, and then laminate, so it changes the build sequence and this is important both for the fabricator and the designer to understand what that means. So typically what you would do is, you would take a B stage layer of some sort; you can either drill it and paste, fill it with what we call a postage stamp process or you could pre-tack it, vacuum tack it at low temperature to a core of some sort, or substrate, laser drill through the B stage, apply the paste and then when you laminate the paste interconnects, the layers in the z-axis - you could literally take a piece of prepreg, laser drill it with a stencil or with a Mylar Stencil, I'll talk about how that works in a little bit - apply the paste, remove the Mylar laminate between two copper foils, and now you've got interconnects inside a double-sided cork.
That's cool.
So then if you print and etch that, now you've got a core with connections between the layers with no visible vias; they're all internal. Yeah there's some technology around the paste and again we can talk about that, in a little bit.
So how is it applied - is it squeegeed in?
Yeah.
Okay, just like with a silkscreen?
Well no screen - so what typically what you do is, you apply a 1 mm Mylar mask to the B stage and you tack it simultaneously. Then when you drill through the Mylar and the prepreg B stage to get down to your copper features, then you apply the paste, and the Mylar's your mask, and then you remove that just prior to lamination.
And that stays inside the hole? It doesn't just I don't know the consistency of it. My mind was - pictured it just wanting to drop out of that hole - but it must have some kind of stability?
Yeah it's a liquid and there is a tack right. There are a number of ways to do this, but the most common method is to laser drill, apply the paste, dry the paste... you would do it a second time to top it off and then when you remove the Mylar, the liquid paste stays on top of the paste that's already been applied. Then you dry it again, then you go to laminate.
Does it air dry or do you have to cure it what do you do?
You don't really cure it because it's metal powder - metal powder based - so there isn't really a polymer matrix. Unlike print electronic sinks - which is a again another story - you would just dry off any of the carrier solvent used for the application process. It is a liquid - well it's a paste, not a liquid - but but when you dry off the the solvent that's in it; which is less than 10 percent by weight, then it's just powdered metal and that's how it makes a connection. So think about this right, you've seen a lot of PCB designs - imagine a 32 layer board, which most shops can do, but it's not at the low end of technology. Imagine splitting it up to two 16 layer multi layers right?
A lot easier.
A lot easier to build and then you just paste them together at the end, and depending on the design, you can electrically test each half and only use the good ones. So your risk is light.
Oh, right.
There's a lot of advantages to this. Or what if you want to put together three 16 layer multi layers, or four, or 18 or four 18 layer multi layers - it's been done you know. Now a shop; instead of trying to build a 72 layer multilayer - if they're building 18 layer components - it's a lot more manageable.
Hmm, that totally makes sense. So you explained some of the benefits - it's a nightmare, and you've seen, we've all seen these cross-sections of these crazy stackups with all the sequential LAM and drilling cycles and all of that. And then - and also kind of an unintended consequence you can get, is you can - from a performance standpoint - if you do enough of that right can't you get excess copper on the surface features?
Yes - that's a very good point. So in other words, if you're going through many plating cycles depending on how you break that up and you're trying to meet a wrap requirement, that could definitely add up and make it - make fine line etching more difficult there's a lot of - there are some some drawbacks to traditional processing and then with with an Ormet style process, or a paste interconnect style process, you can eliminate some of those things even with an RF design.
Let's say you have very sensitive surface features and you don't want to play with that layer. You might want to put on the surface finish, the nickel gold, but you don't want to put any additional copper - you want just the original foil copper. You could do that with this paste because you could create that as, almost like a double sided board, and then bond it to the rest of the stack up at the very end, and you're done.
Interesting. So I think you mentioned too, there's some good signal integrity benefits, did we cover that I don't recall?
No, so one of the things that a lot of designs call for is something called back drill. So you're familiar with that, so you do the back drilling to get rid of the unwanted copper. So again, in my earlier example let's say you're connecting layer 1 and 10, and let's just say it's a 22 layer - 26 layer multi-layer. You're going to have a lot of extra copper metal in that via that you really don't need or want. So common technology is to back drill down to layer 10. Now of course drilling to that precise location or depth, to remove the copper up to layer 10, but not beyond. It can cause a reliability concern that's a bit of a challenge. So there's those issues.
What you can do with the paste technology is let's just separate that board at layer 10, and not put a via on that half that goes from layer 11 to whatever the other layer is and you're done. So you can eliminate back drilling and the parasitic effects of having that extra copper and the via so that's another application. So there's some signal integrity benefits, there are some RF applications, there are some high layer cap, multi-layer applications, but also many layer HDI applications; it really depends on how you design it and use the paste.
So if you're a designer what kind of design considerations do you need to make up front?
Okay, my recommendation would be is: think about the design, think where it would make sense to split up the layers and provide the most design benefit. Generally speaking, we like the via to have a one-to-one or less, aspect ratio. Now that might sound restrictive, but it's only in that one B stage layer.
So then that's an important consideration. So in other words, if I have 5 mm of B stage, I won't want my via to be 5 mm or larger where I'm going to apply the paste. It has to do more with the paste physics and how it fills the via and then of course the pad, the receptor pad that you're putting the laser drill via on, needs to be a sufficient size for where the paste doesn't have the opportunity to run on one side or the other of the pad.
So we do like an annular ring around the via, that's going to have a lot to do with how well you can register your laser drilling, usually that's pretty good. The other consideration is, the B stage you use, spread glasses - bringing up spread glass again. Spread glass is good, because it tends to keep the paste corralled, whereas if you have an open weave and that prepreg resin's melting and flowing and during the lamination cycle the paste could run to that area. So spread glass is better. Higher viscosity resins tend to be better. We like low flow prepregs. So those are some of the design considerations.
Another design consideration is - and I've seen this happen before - where if you have a ground area and you're making a lot of paste interconnects along a wide track. You don't want to put the paste interconnect to the edge of the track because what ends up happening is, during lamination, the resin wants to flow off the surface of the track down the sides to fill - hydraulic effect, and it's going to move the paste with it. I've seen vias actually move during lamination. So just some common-sense things. Keeping in mind that it's the B stage where your interconnect is. You want to make sure you put that in some good locations, and in that particular case all they had to do is, go back and shift the vias a little bit to one side and then everything was fine. So it's just those kinds of things. Certainly they could contact us, we can give them some design hints and I can give you some literature to go along with this video or podcast.
Yeah, yeah, very good. Ormet and the paste interconnect - paste sintering - has been around for a little while. What's been the sort of acceptance of it industry-wide? Is it being widely accepted, is it just on certain applications?
It's been around a long time. It was primarily used for quick-turn mic review work, and also large format boards where you're literally stitching very large boards together so you can - again the idea is you can make boards that are nearly finished and then electrically interconnect them. The nice thing about the Ormet paste is it doesn't melt at reflow assembly.
Hmm, so it changes chemically right, so once the sintering is done then it doesn't change, then it doesn't morph and heat?
What attracted us to this technology over some other paste interconnects - because there's other processes where you would apply a paste of some sort and then make a connection with pressure in the z-axis - but what interested us in the Ormet material is: the paste melts at one temperature and alloys - so the paste is basically copper particles with a tin alloy powder. When the tin alloy powder melts - and the melting starts at about 130° Celsius, it starts reacting with the copper and forms an alloy with the copper instead. What's interesting about the Ormet material is, it's alloying with the inner layer coppers as well, on the PCB layers. So we have a metallurgical joint, not just a pressure or contact connection.
So it's - and unlike, the tin lead or lead-free alloys and solder, the melt - the new melting point, when it forms an alloy with copper is one phase is 415°, the other is 630° Celsius. So it's not going to remelt that assembly. So it's a permanent connection, so really the paste applications from other technologies like flip chip and whatnot packages where you didn't want to have a secondary or - if you have a secondary reflow operation - you didn't want to have any more remelt. It has some applications there. Or a down hole assembly is another application where the board might be subjected to the temperatures near the solder melting point is another good application for this material.
So that's what interests us because you know when a board's in use, it heats up the z-axis expansion with other types of pastes interconnects, you have a resistance change every time the board is heated even from, let's say 40, 50, 60° Celsius in normal use, not even in any kind of environment - parts of the board would heat up from the components and you'd have a change in resistance, and that's what this is designed to circumvent because it forms that metallurgical bond with the copper inner layers.
Interesting.
So yeah it's a different technology than the paste you would use in printed electronics.
Okay well that's been fascinating. Again I feel like a newcomer to old technology but - and I've known about Ormet that I think got acquired by Merck now, but I've just never had someone sit down and explain it to me. So thank you for doing that.
90 layer multi layers people are getting - 90...
What!
Yes, 90 layer multi layers with paste interconnects yeah.
That's crazy, I didn't even know a 90 layer board existed I guess.
Yeah I've only really seen them into the 60s I guess personally, so.
Yeah you know, one common design was a 72 layer multi-layer, again made out of eighteen layer components, and one of the things with the chip tests the ATE companies, they built some high layer count multi layers and you need a lot of IOs, there's a trend to go to wafer level testing were you’re testing the entire wafer. You need lots of interconnects and that's one way to get there, is to use the Ormet paste to put in lots of layers. So we're seeing more interest in it lately, and I think that's one of the reasons why the technology hasn't taken off until now, is because there just wasn't the demand.
Right ahead of its time maybe a little bit...
Yeah.
Well, I know you've shared with me some cross-sections or I think you did, and so please be sure to share those with us and we'll put those up on our website and we can share your website and Ormet or Mark's website, so the designers can get more information. Is there any place else besides your two websites that you would recommend for more information?
You know I've mentioned HDPUG (High Density Packaging Users Group) in the past - they're actually contracting some PCB manufacturers to make some HDI test vehicles with paste interconnects. So there's going to be some data - anybody who's an HDPUG member will have some access to some really good reliability data and they're pretty complex boards so it'll really push the technology but for breaking up big thick and ugly PCBs, that's pretty well-established.
Yeah very cool. Okay well thank you. So tell us about that fish on the wall behind you?
[laughter]
So it was a gift from my sister, actually it's made from recycled materials so there's an old PCB cut up on there, and the old spark plug wire, and a few other odds and ends. Some artists put together actually I didn't buy it; my sister bought it on Catalina Island and somehow we went out there as a family trip and somehow she smuggled it off the island and gave it to me just before she headed back to Virginia. So it was kind of cool.
Oh that's fun a good throwback to your diver self.
Yeah so - just the last thing on Ormet, is 'paste don't plate'.
[laughter].
Is that their tagline or is that yours?
Actually that's their tagline. We were sharing it with the IPC shows, but another nice benefit to the Ormet - which I didn't mention earlier is - there's no electrolysis, no plating processes in these interconnect layers so it circumvents all that.
Which is like bizarre for me to think about but...
Yeah but if you're capacity constrained, no plating, that's another benefit.
Well thanks again this has been really good. If you have anything else juicy to share with the listeners just email it over before we get this one up.
Okay.
And thanks again for this one. Now I know we've talked about exploring down the road a little bit on copper foil, integrity issues, and also printed electronics. So I'm sure I'll hit you up again soon Chris.
Yeah definitely. I would like to talk about some of the material science behind printed electronics and I know you guys are working on some new design tools and print electronics; there are a lot of different ways to use that in electronics... I should back up, but there's a lot of different ways to use conductive inks in electronics there are so many different versions of the inks.
Which is another subject I know nothing about so it'll be good. I'll be a student with our listeners and, I know they're out there, I know what conductive inks are, but as far as all the applications, all the different materials available, that just seems like something that's in writing a lot, that people are really turning towards a solution.
Lots of new technologies are coming out in that space and it's going to be fun to watch it all.
Yeah yeah it will be.
Okay Chris, thanks for another good podcast and we'll see you soon.
Thanks for having me.
My pleasure. Again this has been Judy Warner with the OnTrack Podcast and Chris Hunrath from Insulectro, we'll see you next time - until then - always stay OnTrack.
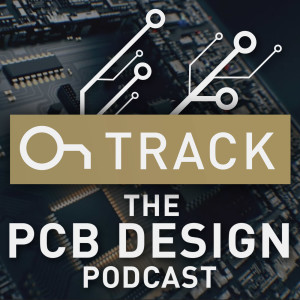
Tuesday Jul 10, 2018
Tuesday Jul 10, 2018
Learn about Embedded Passives Technology with Bruce Mahler from Ohmega Technologies. OhmegaPly® embedded resistor-conductor material is popular, but it’s not new. Ohmega has been making this product since 1972. So why is it getting so much attention lately? It’s reliable and has stood the test of time for five decades--but emerging technologies are making it more relevant than ever. Tune in to learn more about embedded passive and embedded components and find out if it may be the key to solving your current PCB Design challenges.
Show Highlights:
- OhmegaPly® is a true thin-film, Nickel-Phosphorous (NiP) alloy. In the manufacturing process, about 0.05 to 1.00 microns of the alloy is electro-deposited onto the rough, or “tooth side”, of electrodeposited copper foil.
- Embedded passive and embedded components: ER - Embedded resistors, EC - embedded capacitors
- People tend to think of this technology as something new. Ohmega has been making this product since 1972. It’s the oldest, new technology out there.
- Functionality - it can be used in so many different ways.
- Mica - old copper clad laminator, conceived the technology as a way to add functionality to a copper material. Developed in early 70s as a new product.
- First users of the technology - Cannon electronics in Japan saw the potential in the product for cameras.
- Other early user was - Control Data Corporation. From there alot of mainframes utilizing the technology.
- Ohmega ply - thin film resistive foil, plated process, nickel phosphorus, varied thickness and sheet resistivity, fractions of a micron-thick film. Very linear, as film deposit is thinner, resistivity goes up. Thin film technology.
- We make it in Culver City, CA for 40+ years.
- Work with Rogers/Arlon, Taconic, Isola, Nelco and other laminators
- If you use a tiny discreet resistive element, they can be hard to handle. Etching a 5 or 10 mil trace is no problem.
- Space restrictions, solution - print and etch a resistor
- Why would I want to use Ohmega ply? What are the cost, reliability, performance indicators? “There’s no other way I can design this unless I get rid of my resistors!”
- Most designers use Ohmega ply for densification. Helps when: hard time routing, too many passives, board is a little too thick
- Example: MEMs or Micro-Electro Mechanical System microphones for cell phones.
- Applications: military, space based applications - satellites,
- Uses include: Sensors, IOT, Wearables, Automotive, Memory, Heater, Biomedical
- Ohmega wants to talk technology with PCB designers. Leverage their expertise, they operate as a part of your design team and happy to be a resource for you. Technical people are available to help.
- Ohmega and Oak Mitsui - technology partners - Ohmega/FaradFlex is a combined resistor/capacitor core consisting of OhmegaPly RCM laminated to Oak-Mitsui’s FaradFlex capacitive laminate materials.
- Printed circuit board copper lead times are getting longer
- Self-reliant company
- Very close relationships with raw material suppliers
Links and Resources:
Ohmega Technical Library and Tools
Hey everybody it's Judy Warner again with Altium's OnTrack Podcast. Thanks for joining us again. We have yet another amazing guest on a fascinating topic that I hope you will enjoy and learn about today. But before we get started I wanted to invite you to please connect with me on LinkedIn. I like to share a lot of content relative to designers and engineers and I'd be happy to connect with you personally, and on Twitter I'm @AltiumJudy and Altium is on Facebook, Twitter and LinkedIn. We also record this podcast simultaneously on video, so on the Altium YouTube channel you can find us under videos, and then you will see the whole series of podcasts that we record. So that is all the housekeeping we have for the moment.
So let's jump right into our topic today which is, embedded passives and I have a wonderful expert for you today, and an old friend, Bruce Mahler of Ohmega Technologies. Bruce, welcome, thanks so much for joining us and giving us a lesson today on embedded technology.
Thank You Judy, it's great being on board here and I look forward to talking to you and the audience about embedded resistors in particular, as well as other embedded passives.
Okay, so before we get going I want to make sure that I'm calling this technology the right thing because I always think of them being embedded passives but I don't think I'm right. How would you characterize the technology exactly?
Well the OhmegaPly® product, our embedded resistive product, is ER embedded resistors, PCT planar component technologies it goes by many names: embedded resistors, embedded capacitors; I think the most common now is ER embedded resistors EC embedded capacitors in particular. When we're talking about passive elements - and those are the two main ones that are really driving the embedded passive world - and a better component world right now so yeah, OhmegaPly® is just fine with me.
Okay so let's jump in now, you told me something recently that I was kind of shocked to learn about and I'd like you to give us a brief history of Ohmega Technologies and sort of the evolution of this technology. What I was really shocked to learn is the age of the company. So can you tell us more about that?
Sure many people who are looking at using embedded passives, think of it as a new technology, something just on the market. It's been out a year or two - no new applications yet but people are looking at it. So when we're asked, this OhmegaPIy® product , how long have you been making it for? And I said oh since about 1972, and they said wait a second, 1972? I said yeah that's actually , we're going on 46 years now and it's amazing that it's probably the oldest new technology out there.
[laughter]
That's a good way to put it.
I think that has a lot to do with the functionality of the material, how it could be used in so many different ways. And so just briefly a history of the technology: originally the OhmegaPly® embedded resistive thin film material was developed, conceived, and developed by Mica Corporation. Many of your old listeners on board know Mica used to be a copper clad laminator, supplied epoxy glass laminates and polyamide glass, did a number of other things, and it was conceived in the early 70s as a way of adding functionality to a laminate material. So rather than just getting copper foil bonded to a dielectric it was a copper coil that had a functional purpose beyond copper traces bonded to a dielectric and so, after many years of development at Mica, a product OhmegaPly® was developed; the Mica laminate product was MicaPly that's how the name originally came about and it was originally developed in the early 70s as a new product.
Now with any new product, somebody had to be the first to go ahead and try it you know, who was going to be on the bleeding edge of any new technology, who was going to be the route maker? And the interesting thing is that back in the early seventies - about again, '72, '73 - the first users of the technology were two absolutely opposite companies in absolutely opposite areas of the electronic industry. One of those happened to be Canon electronics in Japan. Canon, making AE-1 SLR cameras at the time, looked at the technology as being a great way of making a step potentiometer who could eliminate the ceramic potentiometers circuits that they were currently using, at the time and it fit very neatly into their camera system. So they were very simple, these were surface resistors, put in FR4, make resistive elements in the potentiometers, and they started using it in their AE-1 camera. Very quickly Nikon and Pentax started doing the same thing. The other first user happened to be somebody completely opposite - now we're talking about the early 70s - and that user was Controlled Data Corporation; used to be in business a long time ago. CDC's aerospace group who had some very dense multi-layer boards of mixed dielectric layers of PTFE Teflon, layers of FR4, ECL ecologic, lots and lots of termination needs and absolutely no real estate on some of their high-speed digital boards for termination.
So the idea of being able to print and etch a resistive element, and embed it within a circuit layer, particularly underneath an IC package, speeded up board area for them, allowed them to terminate. They got some other benefits of better electricals. They started using us and then very quickly thereafter, other divisions of CDC started using us in things like their cyber mainframe computer systems, and it kind of dovetailed into people like Cray Research and their supercomputers, and we went from there to super mini computers , places like Digital Equipment and Prime and Wayne, and Data General and Harris. All the guys in the 80s who had ecologic termination needs. So it was the heyday back in the 80s, and a lot of mainframes, supercomputers, super mini computers, kind of like with those very, very powerful systems that people now carry in their cellular phones-
In their pocket right?
-at the time it was very, very powerful though. And so, although two different areas of growth we - in the 70s and 80s - found new applications and digital application, particularly termination, but we also started working very closely with the military aerospace industry where they saw the elimination of solder joints being a very positive thing. You know, high g-force doesn't affect it -vibration - there's no joint there in the resistor circuits. So we started working with a lot of them in the military aerospace, space-based applications, radars, antenna power dividers, high-speed digital systems - just a variety of different things. And it's evolved from there, it seems that every five years new technology comes on that says I need to use that. We can talk more about that - we'll get back to maybe the basics of what do we actually do, how do we make it.
Yeah so let's talk about OhmegaPly®, what is it? What is it like to process, and let's just go in and tell us the whole story.
Oh man, you want to go right back to the beginning again. Okay the OhmegaPly® technology is a thin film resistive foil. Now we became Ohmega Technologies - a spinoff of Mica - started as a separate independent company in 1983, and we basically took over that whole technology from Mica, and what that technology involves, is taking copper foil as a standard EDE electrodeposited copper foil that the printed circuit industry uses, and we threw in a reel-to-reel deposition process as a plated process. We plate a very thin coating of a nickel phosphorous NiP resistive alloy onto the mat or two side of that copper and by varying the thickness of that resistive coating we can vary the sheet resistivity. And so this product - a true thin film nickel phosphorus alloy - we're talking about fractions of a micron thick film, so it's truly thin film. So we have a variety of different sheet resistivities, a 10 ohm per square is about a 1 micron thick film, a 25 ohm per square's a 0.4 micron, 50 ohm is 0.2 micron. So it's very linear, as the film that we deposit gets thinner the sheet resistivity goes up. Now we start getting into the dangerous territory of talking about things like ohms per square and I don't want to start having your listener's eyes cross over some strange area, but suffice it to say, it follows thin film technology.
So what we do is, we make a resistive foil that's a copper foil resistive coating. Now what that foil does, that's what we make at our facilities, in our factory in Culver City California very close to LAX or a few miles away. We've been doing it now , for literally 40 years plus at that facility. That resistive foil then gets laminated or bonded to a variety of dielectrics. We work with people like Rogers Arlon, Taconic, we work with Isola we work with Noko, we do some work with DuPont we're working with others out there, but essentially the resistive foil can be bonded to almost any kind of dielectric just like any other copper foil. Standard pressing, heat pressure, it bonds to a variety of dielectrics. Now that laminate product - a copper clad laminate with the resistive film between the copper and the substrate - goes to the printed circuit board community, the PCB community, then prints and etch copper circuitry. They normally will do a print develop, extra process to create copper circuits.
Now they go through a separate (an additional) print develop bed strip so it's a two-print operation and the first print is defining where they have copper traces, then they etch away all excess copper and they etch away all excess resistive film underneath their copper. Now they have copper circuitry. Underneath all that copper circuitry is a resistive material, but electrically it's shorted out by the copper above it. Well you have a spot for tracers.
Makes sense.
That's a point think of it as a treatment of copper only like a zinc or a brass.
Okay.
Now the board shops come back and they apply more photoresist over that copper circuitry and they print a second piece of artwork and that artwork protects all the areas that they wish to keep as copper, and exposes for etching the copper that will be the resistive element. Now in almost all cases, the first etch will define the width of that copper that will be the width of that resistive element. So the second image artwork defines a length of copper that will be the length of the resistor. So it's a very simple piece of artwork to use; very easy to register, but after protecting the copper with photoresist, now they etch away the exposed copper using the 'aplan' based etchings, and they leave behind the resistive film that was underneath it, and they have a resistive element.
Interesting.
-stripping photoresist off the board; leaves them with copper circuitry with resistive elements that are integral to that copper plane. Those resistors can be tested for value, they can go through standard multi-layer processing, laid up with other cores, pressed and then forget you have the resistive elements embedded, if it goes through traditional drilling, print, develop, etch, strip process, or plate process I should say.
So you do a drilling and you desmear, you plate, you etch and your embedded resistor inside; and as a bare board now, prior to shipping for assembly, the board shop can do traditional testing, and they can measure resistor values to ensure they're within spec. They could also be used on the surface of a board, in which case you solder mask over the resistive elements along with your copper traces, and that protects them from abrasion and scratching. The key here is this though: if you use a discrete resistive element, an 0402, an O201. An O201 is a 10 mil by 20 mil resistor. They're pretty small;
Yeah.
-hard to handle, hard to assemble. So if I go to a board shop now and say: hey guys I want you to etch a copper trace that's 10 mil wide, they're gonna look and they'll laugh and say: come on you're insulting us!-
Yeah.
-we do 5 & 5, 4 & 4, 3 & 3, 2 & 2 technology. So etching a 10 mil trace isn't a big deal, five mil trace is not a biggo. When they etch that copper trace, they're essentially defining the width of the resistor, so it's like a controlled impedance trace. They're creating a resistive element of a certain width. Now you say: can you cover it with photoresist and have a little box window that's 20 ml long? Sure that's not a big deal if you etch the copper away. Now they've left themselves with a 10 mil by 20 mil resistive element, which does not push the art at all, it's already built in, no assembly, and all that. So if you say: hey can they do a 5 mil by 10 mil resistor? Sure, we have applications that are using 50 micron by 100 micron resistor. If a board shop connected that copper trace, that's the limit of the resistor width you can print. So you can get a significantly small, very, very, precise resistors that could be located right where you want them, under a package, and that's where we're doing a lot of newer applications like microfluidic heaters, you're talking about a couple mils, by four or five mils you can get very small heat rises in a very localized area, very low power, but I'm ahead of myself.
Okay yeah well so I'm thinking about our audience right now, who are EEs doing design, or just purist board designers for the most part. Why would I want to use OhmegaPly® over traditional? I mean you just mentioned one, if I had space restrictions and I didn't want to use these tiny, tiny parts that seems like a no-brainer but is it real estate, is it cost? Like what drives people - I think I'm opening a can of worms, sorry but what is the cost, performance, reliability implications? And if I was a designer, why would I want to use OhmegaPly®?
Okay, it's a good question and people use it for a variety of reasons. The best reason we like to hear is: I have a design and there's no other way I can design this thing unless I get rid of my resistor and so, kind of I get a tear, I well up a bit, I get very emotional-
[laughter]
-with those. Because then it's all driven by performance and densification.
Right.
But look at everybody - realistically - cost is a big driver, as is performance, and obviously densification all goes hand in hand with reliability. I would say most designers design with us for a number of reasons. The key reason that we focus on densification and that is this: if I have a certain number of resistors on a board and I said: I'm having a hard time routing. I have a lot of passes on my board, either I have to route in more layers, so I'm adding to a multi layer design for its traditional through hole, and I'm gonna have to go to HDI which adds a lot of cost to my board. Or my form factor, my X&Y; dimension is a little too big I need to shrink it down, or my board’s a little too thick, I'm gonna make it a little thinner. So here's a tool, a technology that allows you to do that.
So let's say I have one resistor in a unit area of a board, and somebody says, well gee I want to etch in a pretty natural resistor. Okay who’s cost’s it going to be? It's gonna cost whatever our materials, divided by one. There's gonna be one resistor. Now instead I have ten resistors - what's the cost? It's our unit cost divided by ten because it's the same material that goes through the same print and etch process. So the greater the number of the resistors lower the cost per unit resistor. One application that uses our technology - and this is where it reinvents itself. A number of years ago - five/six years ago - it started being used in MEMS microphone.
If any of your listeners out there, any of your designers have a cell phone, you very likely have us in your cell phone in the MEMS microphone that you're talking out of, or you're listening out of right now. Now why use us in a MEMS microphone? We're part of an RC filter network which improves the sound fidelity significantly. So it's been found to be a very significant offering by the MEMS microphone makers and their end customers who are the cell phone manufacturers - but in very massive, mass quantity production - for many, many years over in the Far East, particularly in China, where our product is used extensively. So in those applications it was a combination of densification, they can make these MEMS microphone boards. The PCB's thinner because they eliminate the chip resistor, you don't have to assemble it, they can make them a little bit smaller and because you're talking about such small little element - even a few resistors only a couple resistors - in that design, you're talking about a fraction of a cent to put these resistive elements in a board. Fraction of a cent, no assembly-
Yeah when they're in the millions that matters.
-all that's very important. There's another example. If I'm a designer and say: hey I have a high-density IO/IC. My fast rise times I have some termination issues but I'm on a 300 micron pad batch and there's no way I can put a discrete component on my surface. To go ahead and terminate, I have too far to go. I have too many of these line. So I have IO of hundreds of traces, maybe a thousand traces, and I do it but guess what? If you're able to take every trace, every logic trace coming off that that IO and I build a resistor as part of that trace - to have a trace it has just a little of the copper removed - leaving a resistive element behind.
So it's a resistor built-in trace which is one of our products: ORBIT Ohmega resistors built-in trace - you can terminate every one of those drivelines - they're underneath the IC package, so they take up no board area. They terminate off that driveline, you improve impedance now, naturally reduce line delay, you also save money because now you literally have hundreds of resistors in a square inch of area or a couple square inches of area, and it saves a lot of cost by not having to assemble and put those discretes on your board now. So cost is a big driver. I just mentioned a couple of them. Densification is as well, but our material also is essentially inductive free. So you know, it means that you have less inductive reactance with fast rise times. So what happens; you get less EMI coming off your board, it's a cleaner signal. Our materials, also because of that, used in certain applications for absorbers or, R cards where they used us, that resistive film, to suppress some of the EMI coming off for-
-interesting
-as a shielding agent. So there's another application. So we're used extensively, not just in power dividers and R cards and absorbers, but obviously as terminators, as in filters, pull-up/pulldown resistors and now we're seeing a lot of activity in heater elements. We're in the military aerospace uses a 'cell' so my active laser activation where they have tiny resistive elements on PCBs that can go ahead and activate a laser for laser guidance for smart munitia, missile systems, or heater elements that can go ahead and maintain heat on critical components in avionics or even in space based applications. Or our product is used in satellites and even in deep space probes. We were on the Mars Express Beagle 2 Lander, on the surface of Mars where we have an Ohmega heater, key critical components up to above minus 15° C. It would work great if the parachute did not land on top of the lander
[laughter]
and prevent the deployment of the solar array but hey it was a great application for our product.
Well it's again - I think just such a surprise - or at least it was to me, when I learned about one: how old the technology is and two: that it's really because of complexity and just all the different things that are going on in the industry right now that it's growing - it's growing at a quick pace.
Significantly so, we've had a wonderful record year; every year is a record year. But that's the nice thing, that the resistive film is like a blank slate. What you do with it is a new assignor and so yeah in the 80s it was all ecologic termination and then it goes into power dividers, and they're still doing all that stuff. But you know what's happening now is, we're saying, it’s utilized in so many different ways so we talked about the MEMS microphone. Well there's new sensor technology, there's accelerometers or other there's other MEMS-type sensors who use us. Now we see automotive sensor technology that says: hey, we could use this, not only is it obviously super-high reliability, been out for decades you know, can be done in high volumes, very cost-effective, density impact identification. But there's some critical components you could use in automotive, 5G technology-
What about IoT Bruce, it seems like ideal for IoT, provided the cost-
-in IoT you're saying?
Yes.
The Internet of Things well that's why I'm talking about sensor technologies. IoT is a combination of a lot of things.
Yes.
Technologies are getting into it, we see our stuff on flexible materials, and wearables.
Your wearables, yeah that was the other thing I was wondering about.
Wearable devices, we can get smaller home devices, home audio devices, and as things get thinner, smaller, everybody wants things densified. So getting rid of the passives especially, really allows you to do that. So yeah IoT is a big thing, automotive, even memory devices going to DDR4, going out to DDR5 , those fast data rates are causing needs for termination again, and 'Genic' has approved the embedded resistor within some of the DDR4 structures. So memory is another area. So between sensor technologies and automotive, and home devices in things like memory devices, and things like heater microfluidic heater bio biomedical type things you know. We have micro heaters on an embedded board, you can have fluid come in and have basically a breakdown to the protein to do analysis, they use us for things like that. It's pretty exciting - so yeah it's been around for 45 years but guess what, we think that the new technologies, the new applications, it's almost like just starting over again.
Yeah I can see that.
Especially, we have the reliability long-term use, high volume low volume, high density/low density, so many different ways of doing it so, that's nice to have that background, make people feel good about using the technology, but knowing that all these new things are developing. I mean I can't wait for the next 45 years.
That's fun.
Well a couple of things I wanted to ask you about what made me think of calling you and wanting to do this - sort of a side note - is, you hear about passives being on allocation and all of that and I'm like: I wonder if Bruce is seeing an uptick just because people are freaking out over automotive buying up whole lines - I don't know if you're seeing that, it was just a curiosity I had?
Well yeah I know what you're saying, we definitely see an uptick, and now part of that uptick within the context of the of the industry. First off, I do want to tell your audience, especially your designers, we've been doing this for 40 - 45 years plus, as I mentioned - 46 years. I'd like to say that I was only 2 years old when I first got introduced to technology-
-We're going with that; I was three, you were two - let's go with that!
But we also have designers at our company whose job it is to work with the design community, particularly a PCB designer who could help them optimize their design, who can develop real footprints of resistors. What we don't want your your listeners to do, is reinvent the wheel; we want you to use our knowledge, talk to our people - say: hey here's what I think I'd like to do, I have an application I want to use, does it make sense for your technology? If it doesn't, we don't want you wasting your time. So ultimately you're gonna say, we're not gonna use it anyway we want you to have an optimized design because we want you to be successful. So think of us as an extension of yourself, of your team.
We're part of your design team we're there to help and assist. If you go to our website ohmega.com, there's a lot of white papers, there's a lot of good information there that people could read and reference. But more importantly is the communication with our staff, technical people who can really help you. Now talking about in general, the industry, there is an uptick in that. We talked about passive, so I mentioned it; we're in filters and MEMS microphones, resistors and capacitors and in one case, one of the capacitive materials, the embedded capacitor material FaradFlex, which is a embedded capacitor material, it's produced by Oak Mitsui. So Ohmega Technologies, my company and Oak Mitsui, got together and combined the material and had our resistive material on their capacitor material so we'd have one layer resistive capacitor.
What? My head just exploded!
What we did was we found that it's pretty simple, from a technology standpoint, to stick two technologies, each separately have its own complexity but working together really worked very well. Importantly enough it had such synergistic effects in terms of improved power, lower RTC characteristics, or change of resistance to function the temperature down to almost nothing, the stability is astounding over a wide temperature range that we applied and we got a jointly held patent for the combined technology which we have in the US, and also all over the world now. So it's a joint technology pact between Ohmega Technologies and between Oak Mitsui and Mitsui Mine in Japan for this technology, and we see applications where if somebody wants to get a resistor and embed it, they also want to embed the capacitor. They get rid of capacitors that are passive. A lot of times they want to get rid of resistors too. So it goes hat in hand with a lot of those.
In general, there is a lot of movement in the industry to embed it, but it's a growing thing because of densification, growing needs for real estate, smaller, thinner, lighter. You touched upon something and that is material sources, right now the industry is going through some uptick. I think part of that's military aerospace that has increased the amount of funding and a lot of military programs, but also other areas. So we've seen that as well and our products are used in a lot of stuff. Radar systems F-35, F-22, a lot of missile systems, Eurofighter, just all over the place. A lot of satellites, a lot of SATCOM, a lot of other things like that.
A lot of radars on the ground as well, but we're seeing that uptick because the IoT, as you mentioned, in the Internet of Things, there's more and more sensitive technologies being demanded into a lot of different product. People are amazed at how many sensors go into so many things these days and the key with a lot of that, is densification, smaller, faster, cheaper - so that gets hand-in-hand with the 5G, the automotive, self-driving cars that are coming up; a lot of the sensors the Lidar, other sensor technologies are going to self-driving automobiles and what everybody says is: hey, this all sounds great, but you know what? If I have a printed circuit board not using a computer and I have a failure in that it's okay. So it's annoying my computer goes, I swap a board, I put up a board, but I cannot afford to have any failure. I cannot afford to have anything go wrong, if I'm in an automobile that's driving itself, do you have room for any kind of failure? And so it's taken very seriously in the industry and going to a lot of these conferences and hearing the talks, the people involved with testing a lot of these are very concerned. They have to have absolute... as tough as it was, they have to make it even tougher for testing. Nothing can fail, so a lot of that comes into what can we do to improve reliability? Hey let's get rid of solder joints.
We want a kind of thing doesn't cause something go 'ding' and fly off a board anymore - or you know X&Y; expansion or z-axis expansion, all those things. Get rid of those solder joints, mechanical joints, improve the reliability while you enhance, densify, improved electrical performance. So we're saying that that's going on right now. And the other thing is that companies are concerned about, the industry is facing some interesting things right now in the printed circuit industry copper lead times are really out.
Yeah, that's crazy too.
-yeah the industry is getting smaller and smaller, yet at the same time the end-users and designers have to rely more and more on fewer and fewer resources. So we've been around since like I said 1972, so for 46 years we've been supplying this technology and we have never ever not been able to supply this in those 46 years. It's important for us that, A) we manufacture everything ourselves we make that resistive film we test it, we have test facilities which make sure that the product is what it should be before it ships out the door. We have hands-on manufacturing that's critical we don't want to subcontract making our product because we feel it's too important to our customers. They're relying on us. If we subcontracted, what would happen if whoever we had make it, went out of business? Or they sold the business; I don't want to do it anymore, and then we can't get product, our customers can't. We don't want to rely on someone else; that's number one.
Number two, we have very good close working relationships with our raw material suppliers. Most of our raw materials are USA-based, we get them in from the US you know. We want to have a critical supply chain. When you're talking about scarce resources like copper and other things, it's important that we have that kind of relationship with our suppliers so that we always have product. We're always there to support our customer needs when they need it, how they need it, and that to me is very, very important because a lot of companies are coming to us saying: oh yeah we're giving two months lead time on getting product, and how are we supposed to deal with that? And say what about you guys? I said: you want some of our stuff we'll ship it tomorrow. To us that's very important. Customer; you've got to go ahead and satisfy customer needs and especially their concerns that's absolutely critical in the industry today.
Yeah and it's refreshing because we get in this weird cultural thing as a business and it's like: Oh faster, cheaper or we're gonna be the lean supply chain and buy out. We get into this whole frenetic thing, but we forget if we're not meeting any of the customers we'll be out of business. So I really love that philosophy. Now as far as our listeners go Bruce, we're gonna share all of this in the show notes right. Everything that's on your website I encourage it, so we're going to supply all those links and the website you guys, if you're interested you can call Ohmega Technologies directly, get the help that Bruce alluded to. But they have a really great website with some really neat things that will go into even more depth than Bruce has gone into so far.
So thank you so much. So Bruce, as we wrap up here. First of all, thank you Bruce is joining us from IMS in Philadelphia today even though he's - at Ohmega in Culver, so thank you for hopping out of the show for a few minutes to give our listeners a treat, so thank you for that. When I wrap up the podcast I always like to have a little feature in here called 'designers after hours' because most of us techie weirdos have a little bit of a right brain and have interesting hobbies I've found. Is there anything that you do after hours that is creative, compelling, interesting or otherwise, or do you have any after hours? do you just work all the time Bruce?
Do I have any after hours? That's a good question.
Yeah we encourage people to call us and that keeps me rather active and the staff at Ohmega and we welcome that; please, please, please call us, email us, we'd love to talk to you and listen to you. As to me yeah I enjoy travel, I enjoy writing you know, I always have . Now it's mostly technical things or papers that I publish. But you know, I love doing fiction as well, I do do that and I get very involved. Between that and having a lot of crazy grandchildren running underfoot, that keeps me going.
That fills up your plate. So also, would you say you are a geek or a nerd?
I'm sorry?
Would you say you are a geek or a nerd?
That's a good question, I'm probably more geek than nerd yeah they've cleaned me up over the years, so I think I'm more geeky.
Yeah I would say you're more geeky, but you are walking on the razor's edge my friend. You can you can dip into that nerd space pretty easily.
[laughter]
Oh man, and I've been so good I haven't cracked any jokes, you can be mad about.
[laughter]
Here I am, now you're telling me I'm close-
-no, no only in the best kind of way that you like go into this nerdy space of technology but that's really -
-you want to know something; it's been a long time, I've been doing this a long time and I'm so excited - it's like it's a renewal if people get that I'm excited about technology about where Ohmega fits into technology it's because I really AM. It's genuine, our president Allan Leve, over at Ohmega Technologies, here's a guy who's had the same kind of passion. So every time we see something, we're always sending articles: look at this it’s neat isn't it? So if you call that nerdy, you call that geeky, that's fine. You know what we call it being enthused with technology and how we fit into that technology.
Absolutely.
-because I've been called a nerd and a geek I'm gonna drown myself in a Phillies steak salad.
-extra cheese and onions.
[laughter]
No - when I say you teeter is only because I remember when I was working at Transline Technology, you came in and you were showing us how it's done, how it's processed as a board shop - and I remember listening to you going: this guy totally knows his stuff and it was so articulate and I'm like, boy when I grow up I want to be able to talk like this. Like Bruce Mahler does, man he's got it going on! So that's why I say-
-just wait until I grow up really.
-well it is an exciting time in technology there's no grass growing under our feet so I share your enthusiasm for everything that's in the market and you're seeing everything so that is really exciting. Well thank you again for -
-thank you I appreciate it Judy, the opportunity to spend time with you and spend time with your audience, and hi to everyone out there - look forward to talking with you, look forward to working with you and like I said; a lot of exciting things out there right now in our industry so we're working in the best industry out there.
We are, now we're gonna send poor Bruce back to booth duty where he can stand in a booth. Sorry to send you back to booth but thank you so much. Again this has been Judy Warner with Altium's OnTrack Podcast and Bruce Mahler of Ohmega Technologies. Thanks for tuning in again until we hear or talk to you next time always remember to stay on track.
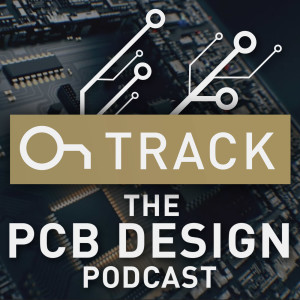
Tuesday Jul 03, 2018
Tuesday Jul 03, 2018
What finish should I use for my PCB Design? There’s no one single answer, it depends. Meet chemist and surface finish expert Mike Carano, the Vice President of Technology and Business Development at RBP Chemical, industry leaders in high performance chemical technology. Mike emphasizes a key question when it comes to surface finishes, “What are the reliability requirements of the environment?” Learn about the chemistry behind different finishes, fabrication and get tips for avoiding corrosion in unexpected environments in this episode of the OnTrack Podcast.
Show Highlights:
- Mike was Inducted into IPC hall of fame.
- RBP Chemical - veteran owned small business, based in Milwaukee, founded in 1954 as a supplier for the printing industry and over the years evolved into surface finishes and also carry product lines for Embedded Medical Devices and Semiconductor and Mining industries.
- On using solder mask over bare copper method - prior to going out to assembly the copper needs to be made pristine.
- What are the surface finishes and which to use when? 50% of industry using hot air solder leveling (HASL), a surface finish with a long successful history.
- Other surface finishes: Electroless nickel immersion gold (ENIG), Electroless Nickel Electroless Palladium Immersion Gold (ENEPIG) - which is common in IC substrate, packaging industry.
- Future of surface finishes: Tin-silver, Direct palladium copper
- What finish should I use? There’s no one answer, it depends.
- Are there common examples of things that can go wrong? ie. High frequency design applications - ENIG is a well known issue that most engineers learn about the hard way.
- Where is the final product going to be used? Is it a domestic product or for the military?
- Reliability first, cost last. Cost should not be driving force.
- The environment is what really matters i.e. Shock-drop or Brunel fracture - consider for mobile phones, ENIG - tin-nickel bond, not tin-copper, corrosion environments, temperature extremes
- What are the reliability requirements of the environment?
- The most high quality board fabricators have strong process control and automation in place to ensure chemical stability.
- Board designers are looking for electrical performance. Need to ask about the environment.
- I would put every designer in a circuit board fabricator for a week and let them build a board they design.
- To learn, you need to practice and get practical information on building the bareboards.
- Creep corrosions on the mill automation machines because the OEM is specifying the finish.
- Japanese techniques i.e. Shokuku chemical
- Most substrate work is done in Asia; IC substrate packaging at its best is in Japan.
- Advice for learning: IPC courses, CID and CID+ training is one way to learn more.
Links and Resources:
IPC Hall of Fame Interview Video
HDP Users Group (HDPUG)
Hey everyone it's Judy Warner with Altium’s OnTrack podcast. Welcome back we are glad to have you join us again today we have a very unique topic and speaker which was actually brought about by Mark Okumura who is the Senior Principal Hardware Engineer from ETS Lindgren who reached out to me and asked me about the topic of surface finishes and lucky for you I happen to know the guy who is a chemist and expert on surface finishes. A longtime friend Mike Carano from RBP Chemical. Before Mike and I get started, I wanted to please invite you to connect with me on LinkedIn or on Twitter, I'm @AltiumJudy. Altium is on LinkedIn, Twitter, and Facebook, and also please know that we're recording on YouTube in case you want to see our sunshiny faces. So Mike, welcome thanks so much we’re delighted to have you.
Thanks for inviting me.
It's good to know friends in high places right?
Well, I have friends in low places.
[Laughter]
I don't believe it, well maybe, so Mike, I’ve got a question. First of all let's talk about your background a little bit so as a way of introduction Mike Carano was inducted into the IPC Hall of Fame a few years ago and I had the privilege of doing the video interview that was highlighting his induction into the IPC Hall of Fame because he has served on so many committees and boards for IPC, but he really is the go-to guy on chemistry. So Mike, tell us a little bit about your background how you got into chemistry specifically related to the printed circuit board electronics industry?
Well sometimes Judy, things happen by accident really, chemistry and sciences were always a love of mine so I always liked to experiment - my parents got me the chemistry set, and everything from blowing up golf balls to me making things at home, everything from even experimenting with making wine that's chemistry - that seemed like a good thing to do right? I also realized that probably owning a vineyard would not be in the immediate future so onward and upward with chemistry, particularly the area of physical and advanced chemistry electrochemistry working on a Master's Degree, I happened to be walking up on campus one day back in 1980, 24 years old, and there's a gentleman standing outside this building and he noticed my chemistry books he says, hey come here I want to talk to you, and I thought, oh what's this about? And I noticed the sign on the door there, Youngstown Ohio City Electrochemicals, and he asked me if I wanted to interview for a position there. Well it was perfect because graduate school was more part-time. I was doing some teaching assistance and what do you know, I interviewed for this thing on surface finishing chemistry having no idea really what I was getting into, but I did. The idea was finishing my Master's degree, and go on and do something else - maybe do this for two years - well 39 years later here I am still in the industry. In some way, shape, or form, so that's how I got into this and as the company, Electrochemicals in those days, founded primarily on the metal finishing industry - you know, surface finishing for doorknobs and bumpers and decorative plating. Well the company was just then getting into printed circuit board chemistry and a lot of people didn't even know what that was in those days because it was a fledgling industry there was mostly - remember Judy way back then was the 80% of the industry was really run by the OEM...
Yeah
-So digital equipments the the Adelphi’s, the Delco’s the IBM's, but pretty soon there was that switch, and then I got involved in IPC and pretty soon was formulating chemistries and technical service, traveling globally around the world was fascinating for me, and here I am today, and still in the industry in some way, shape, or form. You know, you evolve, you continue to evolve matter of fact, just like surfaces they've evolved.
Yeah right.
Where we are today, I'm sure they'll continue to evolve in the very near future.
Yeah for sure, so can you give us a quick overview, I know you were Chief for many many years and now you're with RBP can you give us a quick thumb nutch of RBP?
Absolutely, great opportunity, company privately owned (veteran owned) small business, our company is based in Milwaukee Wisconsin and was founded in 1954 and has been privately held since. The current CEO and majority owner is Mr Mark Kannenberg, he's my immediate boss, Mark served in Vietnam, he's a West Point graduate and also a Harvard MBA, but he always wanted to kind of get in the business of owning his own company even though he had many, many opportunities. So he's now been running RBP for these last 30 years. Under his control the company has grown beautifully - initially, the company was founded as a supplier of materials and chemistries for the printing industry, newspapers, newsprint magazines, but over the years also evolved into surface finishing, surface treatment and printed circuit board chemistry, which is the company today, because as I said it continues to evolve. Today and we have four major product lines the printed circuit board and photochemical milling chemistries. We have a great product line in the area of embedded medical devices, and we also serve the semiconductor and the mining industries with some specialty additives. A lot of people don't understand the connection but there's a connection all the way through the platforms because the chemistries are basically adapted to work in all those industries which makes working with RBP fascinating for me - the diversification but yet the the continuity and the familiarity - so great opportunity and I've enjoyed it immensely.
Good, thank you for sharing that Mike, so let's jump right into surface finishes. I'm sure most of our listeners who are engineers and designers will be familiar with surface finishes but let's just go back to our ABCs for a second and just define surface finishes for us for PCBs.
Sure that is the part of the board that is really going to be used to prevent oxidation of the base metal, as you know, typically we have copper as the base metal if you're using the solder mask over bare copper method where you basically put solder mask down that nice green stuff and the copper is showing, you have to make that copper solderable, you have to preserve the solderability so typically, prior to that board going out to the assembly operation, the copper has to be basically made pristine with a finish that does not oxidize so that you can join the component leads, whatever they may be, whether they be surface mounts, through-hole, BGA, QFNS, QFPs, they have to be able to to wet that surface and form a reliable joint. So the surface finish is critical for that application and for that end product.
So tell us - give us just a rundown - of what the surface finishes are and then we're gonna jump in to which one to use when.
Sure well, here in North America and primarily for the military, we're still using - at least 50 or so percent of the industry - uses hot-air solder leveling. Basically you're taking that solder mask over bare copper board, flexing it, cleaning the copper and then dipping it into a molten solder pot to coat the surface. But over the years, due to a lot of other constraints, one of them was to get rid of lead. And even when we have lead-free, hot air leveling, the other surface finishes have evolved, as a matter of fact, have taken center stage primarily outside of North America. With these surface finishes are we hear the term ENIG, which is Electroless Nickel Immersion Gold we also hear about Electroless Nickel Electrons Palladium Immersion Gold also known as ENAPEG, and while that may be an expensive finish, you see that used quite a bit in the packaging industry, the semiconductor packaging IC substrate industry. Then there is OSP Organic Solderability Preservatives, which is actually the only one of these to be non-metal-containing and then we have immersion silver, and immersion in tin, and again we expect that there’ll be other additions of these finishes coming up in the near future. Potentially a tin silver or direct palladium over copper to get rid of the gold altogether. There's a lot of movement in this area to enhance the surface finish reliability at the same time managing costs because you see how precious metals like gold and palladium can contribute significantly to the cost of that board. Which then makes you wonder, okay what finish should I use and when should I use it? So that's a rundown of our finishes and each one of them - I can tell you this Judy - when people ask me, and I travel all over the world, what finish should I use...
Yeah
-no one finish fits all.
That's a loaded question isn't it Mike? It depends, that's the answer.
It depends right.
Well as I mentioned in the beginning, this gentleman Mark Okumura reached out to me and said, are you ever going to talk on your podcast, or do you have any information about surface finishes? Because in his particular case - and this is just one of many many high frequency application engineers and designers - have found out the hard way that if they use ENIG the Electroless Nickel Immersion Gold, that if it's high frequency then we have the skin effect and then the signal begins moving through the nickel and the nickel is lossy, and unfortunately that's a well-known issue it's been going on forever but it seems like people have learned that the hard way, unfortunately one at a time, that's just one example. So can we talk about when we talked a few weeks ago, about environment playing a huge role on how to make a selection on your surface finishes. So can you jump into that a little bit?
What I mean by environment is, where is that final product going to be used, and let me just preface it this way, if you're in this industry, whether you're in the printed circuit board industry directly or you're an assembler or you're an OEM. Choosing the final finish for that product may be the most important decision you make, because it is going to impact that long-term reliability of least of that solder joint now as I’m saying solder joint, I'm using it interchangeably with lead-free as well. And compounding that, is again, where are the boards going to be used? Is it to finish in harsh use environments such as automotive under the hood, military aerospace - and that's one application. But then, what about consumer items like mobile phones, smartphones, desktop computers, smart tablets, household devices. You don't need a product or a finish that adds $9 a surface square foot of the board if you're using it in a washing machine in your house, or in a microwave, or even a desktop or laptop computer. Now military aero things like class 3, or class 3A that have to work 24 hours a day, seven days a week and can't fail - you can't fail. You may look at that and you say, well do I need ENAPEG, do I need ENIG? Do I need to make the OSP also work? And some people really are surprised when they find out that OSP’s a very reliable finish. It's not wire bondable but in terms of reliability in forming the copper tin in a metallic, and having a reliable solder joint, it's fantastic.
So think about that, it also happens to be the lowest cost finish but I am of the opinion, and I asked somebody this, and I listed ten things I have cost of the finish at the bottom, because that should not be the driving force of what you put on the board. It's the environment where the board is used and then you ask yourself other questions. Is cosmetics important? Do I have to have a shiny silvery finish or don't I need one? I'm worried about shock drop, we know for example, if something I have in my hand drops a lot like a smartphone. you worry about brittle fracture of the components - actually fraction when that phone hits the ground - we've all dropped our phones and the mobile phone companies, the Apples of the world and the Samsung's, conduct shock drop tests all the time because that's important criteria. You don't want to spend money on a new phone, drop it and find out the components fell off. So that's why you don't see ENIG used a lot on the smartphone, you use things like something that makes it much stronger - copper tin and a metallic bond - whereas with ENIG, your tin is formed with the nickel so it's a tin-nickel bond not a tin copper one.
I see.
So, we all know, and there's been hundreds of papers published by many, many companies and fantastic researchers around the world, showing that the tin to copper in a metallic is much stronger than the tin to nickel in a metallic. So that's something to consider as well, not just the cost. But you might use ENIG in medical devices, we know the military is starting to look at ENIG as a final finish, but they also do some things to ensure the reliability of that component as it is attached to the surface. So there's a myriad of things to look at - oh and corrosion environment - in terms of creep corrosion, and that's an issue and silver tends to be somewhat prone to creep corrosion, but in an industrial environment kind of outside, or in a clay modeling studio or in a paper mill where sulphur is emitted.
Yeah that's interesting.
So, if you told me, well I'm making this part because I work for General Motors and I'm modeling, I'm gonna use clay to model my next car and I'm gonna have all these computers hooked up inside that studio, I think I'll use boards with silver on them. Well you probably don't want to, your work is gonna be lost, so that's one consideration. As I said shock drop is another, but again where are you using the final product? Industrial automation, using it outside, base stations, all of those things. Industrial controllers where we're subjected to not just environmental contaminants,but maybe significant vibration, temperature extremes etc. So always look at the environment where you're using it and what the reliability requirements are. Can you afford the warranty, what is the warranty when you take something back? If it's inexpensive, you can use an inexpensive finish but if the cost of failure is great, you should rethink that finish which you're going to use and how you're going to use it.
That totally makes sense to me. You had mentioned that a lot of people think that OSP is generally a sort of low-tech product, but you were pushing back against that when we discussed that, why is that?
Well 25 years ago OSP was what you would call the single attachment finish - one reflow, maybe one through-hole, and that was it. It lasted four to five months whereas the other finishes, like hot air leveling - one year, two year shelf life - that's changed. Companies have made significant improvements in the reliability. Also the the ability of the OSP to reduce oxygen penetration on the copper, and that again is what you're trying to do, you're trying to prevent the underlying copper from oxidizing so that when the solder melts and spreads on the surface, it spreads and encapsulates the leads on the side on the components and solidifies and it's a highly reliable. If the surface is oxidized even slightly and doesn't wet properly you've lost your reliability, but OSP has come on strong now and you see it in automotive under the hoods, major telecommunication companies using it for the reasons of getting away from brittle fracture, you see them in smartphones - a significant number of smartphones - and I have experience in those areas so, I'm talking from personal experience - the reliability is there with the right finish. Now the low-tech you find, if you buy a low-tech OSP from somebody you've never heard of, you’re taking a risk, but the companies out there - two or three that are making significant contributions to the performance of OSP - they've upped the game significantly. Many of them are fifth-generation molecules, these are synthesize organic azone molecules, that just do a fantastic job, and I would not hesitate to recommend it for numerous applications.
It's interesting how that's evolved over time, I wasn't aware of that until you mentioned it to me recently, and that's some of the magic of chemistry that just runs in the background of our industry until sometimes - it seems like - until there's a problem.
That's right.
We don't talk about it, so I'm glad to sort of have this discussion.
That’s a good point, to that point Judy, when Black Pad showed up what people will call brittle fracture...
Yeah.
-it set the industry back 15 years for ENIG because they didn't understand it, they wanted to blame the phosphorus content of the nickel deposit, but that turned out to be incorrect, it turned out that the cause of that was the galvanic effect. When you put immersion gold on top of nickel you're not electrolytically plating it, you're doing an immersion deposit, also known as galvanic cells, so to deposit on nickel, some nickel actually has to corrode and leave the surface, so that the gold can take its place. And that's the main difference of an immersion deposit. Well, what was happening because of the way things were being run, pH, nickel morphology, roughness, etc that galvanic effect was significantly large, causing this corrosion - significant corrosion - to take place on the nickel surface, and that would impact negatively the formation of the solder joint. And there you would get brittle fracture, you drop something, It breaks. So, things are better now, but I still would be very careful, if you told me, I'm gonna put ENIG on my board today, I would say do a first article, make sure that the board design you have, will not end up with this issue.
That's a good advice and, for people who are listening. Again - you're going to hear me say this over and over again - and I'm not going to apologize for it, is that you need to get into a board house, find the time because most really good, world-class board houses - you're going to go in and you're going to be surprised to see... and Mike can talk about this, the complexity of the labs they have in place to make sure that their chemicals are stable and doing what they're supposed to do. Mike, I imagine you've spent just more than a little bit of time inside of board houses discussing chemical balance and, if you would, jump in on what the choice of surface finish has on the fabricator and why the designer should know about that?
Right yeah, well first let's go back to your first question about these board fabricators the ones that are high-quality board fabricators and I'm looking at not just on the surface finishing side, but also other aspects of the circuit board fabrication including electroless copper, direct metallization, the amount of control that they have in place, process control automation, to keep plating and other the key ingredients within a very tight operating window. And that's not difficult if you invest the time, and you have the commitment to ensure that. I can’t tell you how many times Judy, have been in situations where I've had to troubleshoot a problem because someone said I've got this issue, I've got that issue, you go there and you find out that they were running the chemistry basically way outside the window. Well, why'd you do this? Well, we only check it once every two shifts. Well, you can't have a high volume operation like what you're doing and then check the chemistry once every two shifts and I'm telling you, 90% of these problems that I see related to process, are related to incorrect use of the chemistry and mishandling of the controls that are available to you.
Now does that mean that the fabricator needs to work much closer with the supplier, but if the supplier is already doing this for them, the fabricator needs to take some responsibility. But again, I've been with a number of companies who have complete failure analysis labs also in their facility. So, they take it to a very high level, they're basically their own qualification facility to ensure that they understand where the issues are. They categorize every defect and those are the kinds of ones you want to work with.
Absolutely, and I've worked for shops like that where they literally had PhDs in chemistry renting the lab. They were doing their own cross section and when suddenly, there's a spike in volume - if you're not on top of it and you don't have those people and all of a sudden - whoops production went up, but we're still checking our bass at the same rate we were before. And then like, oh what happened? Well there's all these things that need to be taken into consideration and adjust it accordingly. So, what other fabrication considerations are there that that maybe designers or engineers that are designing boards would want to consider as they decide what they're going to choose?
Well good that's a good point, and you and I know design is important, because there's this conundrum in our supply chain. The fabricator is looking for design for manufacturing and the designer is designing something to work in a certain fashion. Electrical performance, dielectric spacing, and and they don't take into consideration potentially what that does, how that impacts the bare board fabrication process. That's a very significant right? What - and I'm gonna go back to this - because I find this to be an issue as well on the assembly side boards come into the assembler, they come from somewhere, and they call me and say I have the the plating is lifting from the surface when we assemble, or the solder mask is lifting well I said do you did you specify the grade of solder mask, do you even know what solder mask is being put on the board that you're bringing in to assemble? Well no. Now I find out - it's very easy for me to find out - that they’re using, the fabricator... wherever, typically not here, are using a low $10 a kilo solder mask because no one specified it. And of course, that $10 a kilo or less solder mask is probably gonna work beautifully in a handheld child's toy, it's not going to work very well for your medical device. And you're gonna have all these other problems. So I think, I hope the designers would get more involved in understanding the difficulties in making a bare board and also understand: just don't specify ENAPEG because it sounds great, or sounds sexy. Because number one, you're probably not paying for it, somebody else has to pay for that ENAPEG and at $12 and $10 a square foot. Understand - and this is where the board designers are looking for the electrical performance - do they ask where the board is going to be used? Is it going to be in a harsh-use environment, is it going to be in a benign environment clay modeling studio? These are the key questions for them. Typically what I see designers do is, say this is how the board should be built, these are the layers, these are the holes, and you should use this material with this dielectric constant. That's all great, but it's not enough.
Right
And I've been teaching this advanced troubleshooting course with printed circuit board fabrication for years, and you'd be surprised at the number of designers that actually take that course, and they ask the craziest questions. Which tells me they haven't been outside of the board fabrication, outside of their design studio. Understand that you need to live with that a little bit I would put every designer at least in a circuit board fabricator for two weeks and have them build a board that they designed.
Yep I agree it's hard - we encouraged that here a lot - and almost every guest on here says the same thing. Because you and I've been around the block a little while, and understand that there's time constraints for them to get out. However the long-term cost of not getting out there and not onboarding. And this is another plug - you and I've been around IPC awhile - this is another plug for CID and CID+ training, as well because there you onboard some of these things that may be outside of the obvious things that are around manufacturing and assembly. So Kelly Dack wants to start field trips on every CID course. I'm like, yes let's do it!
You know, to me that would be fantastic, and to be honest with you and being heavily involved myself in an IPC, one of the things that I've suggested that when CIDs and the CID+ students earned their certifications, they should also have to get some understanding in coursework and practical on the bare board fabrication. You should make it like you did in college, the practicals, you just didn't do the book work, you had to go into the lab...
Exactly!
-apply what you just learned from the book, because if you couldn't resort to practice, at the end of the day you can't practice it. You've not learned.
And as we both know, the cost of ignorance in these areas is so high, like avoidable mistakes.
Costly... I've seen an entire clay modeling studio shut down, a paper mill shut down, because, again the paper mill folks were buying the controls from the OEM who was specifying the boards to be made but the finish... So the poor industrial automation company using these expensive controls were wondering why these inexpensive instruments are no longer doing what they're supposed to do. And they find out that there's creep corrosion in there because the OEM specified immersion silver or bought the board somewhere cheap where the individual companies decided to cut corners, like they do, to meet the cost. Like not putting enough gold on, not putting enough nickel on. You know, there are specs for a reason.
There is, absolutely.
And that's obviously a discussion for another time.
Yeah that's a whole other podcast, and then there's everything you're doing - HDPUG - which is another podcast I'd like to get you on for as well. I want to put a pin in our conversation right now because I realized, in the beginning I failed to mention to our listeners that you may hear some background noise here. There's some... well, what I was telling our producers is, we're building a better podcast but it’s noisy in here, but really what's happening is we have some construction and of course it's overhead in the green room here in our La Jolla office, so it's directly overhead, on this day of course, so please, please excuse any background noise.
So Mike, you sit on boards for international companies as well as companies here and you are a respected and trusted advisor. You mentioned to me about things that the Japanese are doing that are very innovative and that is that they're mixing finishes and doing selective finishes can you tell us a little bit about that?
Yeah, and this is if you can see the IC substrate side in the Japanese, or the ones who really made miniaturization go. I mean they understood how to make things small, not just lawn mowers and engines like Toyota Camrys and things like in the Prius, but they figured out early on how to do it with circuit boards and and putting more functionality on the chip. Matter of fact, that's where OSP was actually invented was in Japan, in those days it was called pre-flux because it was in the rudimentary 1970s day, but they pioneered the OSP and matter of fact, today the leading OSP company in the world is Shikoku Chemicals out in Japan, they continue to evolve that chemistry and I trust them immensely.
So, going back to that question what you do is, in the IC substrate market, where you've got a complex chip that has to have gold leads or gold wire bonding, you have on one side of the substrate, nickel gold, and then you bond the chip with the wires to that feature. But then on the flip side, which is going to be a BGA feature, you have bare copper which is OSP. So they have the BGA balls on the bottom side and the IC substrate - the chip actually, the the die as they call it - on the top side. So you have ENIG - selectively on one side and bare copper meaning OSP - on the other and of course it's a flip chip. So with the IC substrate or the IC chip in there, you marry that BGA to the Barriss surface of the copper board meaning an OSP, and you've got this fantastic package, if you will, instead of doing it all in the nickel gold or all in ENIG and handle it selectively. And they've developed these processes, and they've also developed a selective imaging, if you will, to make that happen. but it's relatively easy to do, once you understand the ramifications and how to make it work, and make sure you don't get an OSP that doesn't say, ‘attack’ the exposed nickel gold. All these things, it's pretty pretty intricate, but it's been around for some time and with a lot of success so I've selected ENIG as they call it.
Interesting, so I was just gonna ask you, what does that do to cost and process ? You're saying it's not difficult, how about cost implications?
Well there is an additional cost of putting the second imaging step down to protect the board from plating where you don't want it to go, but instead of doing the entire IC substrate in nickel gold, you're doing just one portion of it where the wires from the chip are placed, from the die so, that does help you significantly in the long run. It also makes the BGA perform better because you're marrying basically tin to bare copper making another opportunity there.
Do you think that will find its way here into North America?
Well, the thing is there's only a few fabricators here who do work in the substrate industry, most of the substrate work is done in Asia for the Amcor’s and the Intel's and the Samsung’s so you see a lot of the supply chain there. Some big American owned companies in Asia are doing it in volume, but again, if you want to see IC substrate packaging at its best it's the Japanese.
Yeah that makes sense.
Yep they’re the leaders,and they've been doing that for 30 years, so they tend to be ahead of their time, but now the time has come.
Yeah well it's interesting to get your perspective on sort of a global scale, as well this has been great. Our time is coming to a close here, but will you please share with us links to any white papers or slide decks or anything you have? Because I think how I want to wrap up is Mike, if you are a designer what would you do with all this information? And we've kind of shared it sort of anecdotally and quickly here, but if you wanted to learn more about this where would you go, and what kind of things maybe can you share with our listeners that we can throw on the show notes so they can maybe get better at this.
Well very good. I would encourage you designers who haven't taken an IDC course outside of design - I encourage you to take them - you look on the IPC website. We just had Apex where, in addition to technical papers, there were workshops on a number of different subjects including my Advanced Troubleshooting course, but there were also courses on the Basics of Bare Board Fabrication, and some of the instructors do a great job of giving you the tour, if you will, of the very basics. So you can get a feel for how the board starts with bare laminate, actually starts from the design, and actually ends with the finished product, going out to assembly from a manufacturing standpoint, and you can follow that up by taking the Advanced Troubleshooting, so you can understand where some of the problems and technical issues come from when the board is fabricated, with the various chemical steps and the mechanical steps like drilling and plating and immersion gold and silver. Whatever you need to do, that would be something you should do, and also watch for IPC Tech Ed, where they're going to be putting more and more of these courses. Standalones in different parts of the company whether it be San Jose, San Diego. We just did a course in Boston back in April which was well attended, and we just had the High Reliability Conference in Baltimore a few weeks ago, which had a high military aero content to it. But there's a webcast as well. And also, I encourage you to look at the IPC website - http://ipc.org/. Go through the technical papers, look for the events that are going on there but obviously at every Apex there will be this myriad of courses to take, and I encourage you to go to your boss and say, look this is something I think will benefit me, and you're gonna send me there anyways for the other events, so why not get there on a Sunday and take this course?
Yeah good advice.
SMTA is another good place that has a lot of technical papers and seminars and webinars related to things like surface finishes and design for reliability etc. Matter of fact, IPC actually has a Design for Manufacturing workshop that is taught by some really highly-skilled people too, so that might be something that a designer would benefit from. Again, because the designer or an actual designer is actually teaching the course from experience because he lives it...
Yeah
-let me build bare boards... I'm talking like Gary Ferrari and Susie Webb and those folks, they've actually built boards but they also design. Happy Holden and he's built boards, he designs boards, he understands - they get it.
Right.
That would be an interesting perspective for all those out there.
Okay good, that's great stuff. Well we'll make sure to attach the links to IPC and I know they're doing a lot with education right now, and so I'll make sure - and if you have anything to share with me please do - and we'll make sure we also include links to RBP Chemical.
Yeah, https://www.rbpchemical.com/
And then we will share anything else that you want, and I'm hoping I might be able to twist Mike's arm to come teach a surface finish course at Altiumlive in October. But we'll see, he's so in demand, hie’s a popular guy - but if I had my wish, that's what we would do because I think it'd be a great place again hope to have about five six hundred designers there so I think they would benefit.
So Mike thank you again, you're a dear friend, and thank you so much for always freely sharing your information. Mike also writes a column for PCB007 Magazine, called Trouble in Your Tank, and that's where I learned a lot and actually how I became friends with Mike as I was asking him if I could please take some of his content and repurpose it for blogs I was writing. So we'll also include that link to his column. So Mikey, thank you again you're a dear contributor and friend to the industry and thanks so much for taking time out of your busy day to do this with us it's been fun.
Well, thank you Judy, thanks for inviting me. I appreciate it, you have a great day.
Thanks you too again. This has been Judy Warner with Altium’s OnTrack podcast and Mike Carano of RBP Chemical. please join us again next time - until then - always stay OnTrack.
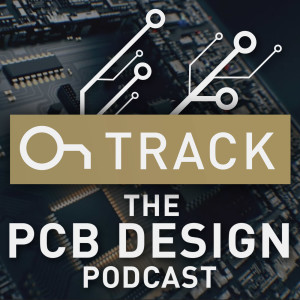
Tuesday Jun 26, 2018
Mary Elizabeth McCulloch and Project Vive’s Medical Device Innovations
Tuesday Jun 26, 2018
Tuesday Jun 26, 2018
Speech Generating Devices and speech assistive devices on the market today are expensive. Insurance policies are complicated and not everyone who needs one is always covered. Meet Mary Elizabeth McCulloch, she’s changing lives by giving a voice to the voiceless with Project Vive and Voz Box. A recent biomedical engineering graduate from a family of engineers and makers, Mary and her team are inventing Speech Generation Devices in new wearable forms by working closely with the people who most need them. Listen and find out how Mary and Project Vive are using low cost sensors and changing lives by leading the development of innovative medical devices and technology.
Show Highlights:
- It was really all about the access, not just in price, but in the sensors.
- Low cost sensors that could change someone’s life. These are sensors in our cell phones that can be used, and we’re really adapting that for the disability community.
- Wearable for independent communication - worked closely with the person using the device so that the design was modified to fit real life.
- Loop of instantaneous feedback - Gave the person using device a voice and a vote.
- People with disabilities are problem solvers.
- This is about innovation that is informed by people within the disability community.
- This is a great way to break down the stigma of disabilities.
- Cisco - 100k prize
- Projectvive.com - accepts donations via fiscal sponsor
Links and Resources:
Learn more about Mary and Voz Box
Let us know if you know anyone who needs Project Vive technology.
Or read more about Project Vive in this month’s OnTrack article.
Hey everyone this is Judy Warner with Altium's OnTrack podcast. Thank you for joining us today. If you've been listening to our podcast I would equate today's podcast with being the desert or the cherry on the sundae. It's a great story and a great woman that I look forward to sharing with you. Mary Elizabeth McCulloch who has a startup called ProjectVive. Before we get into our conversation with Mary Elizabeth please remember to connect with Altium on Facebook, Twitter and LinkedIn and I would also love to connect with you on LinkedIn or on Twitter, I'm @AltiumJudy and also, if you prefer to watch this on YouTube rather than listening just go to Altium's YouTube channel, click on videos and you'll see all of our podcasts there. So that is all the housekeeping. So let's get into the good stuff.
So, about a week or so ago I got a message through LinkedIn - an introduction to this young lady Mary Elizabeth, and she was telling me about her company and we've since connected, had a couple conversations and I'm so excited to share what this young innovator has done. So Mary Elizabeth, welcome my dear I'm so glad to have you and thank you for taking the time to to meet with me today.
Thank you it's such an honor to be on this podcast.
Ya no, it's truly our honor. You know technology does so much for us in our lives but what you're doing is such a great human story. So tell us a little bit about your educational background and tell us about your parents and background, cuz I think that does a lot to set up your story?
Yeah, yeah awesome. So I guess educational background; I studied Biomedical Engineering at Penn State, I graduated spring 2016. I was always really interested in Science and Math in high school - what else? So my dad, he was a Physics major at Penn State, he's gone into Engineering for really his whole career. He's worked a lot with CNC controls in the milling machine industry and then my mother, she has a Biology Degree, a Mechanical Engineering degree, and some Biomedical Engineering graduate work - actually on the artificial heart at Penn State - so you know my family's background and my own.
Impressive. So you shared with me a little bit about - I had asked you: did you always know you were gonna go into engineering? So tell us a little bit about the things you and your dad used to do when you were young cuz I think it speaks to your story?
Yeah so, growing up my parents really had an interesting - or an interest in - farming and fixing things around the house and not going out and buying something new and really just trying to understand how to repair motors like rototillers, tractors, things like that and I guess my dad would also buy little chemistry kits for us to work on in the basement and yeah, we kind of had a blast with that. But also, my parents always really encouraged me to try new things, and one of those new things was to go, after I graduated high school, to Ecuador and I decided to be a Rotary Exchange Student and so I spent a year in Ecuador and outside of high school I decided that it would kind of be cool to volunteer in an orphanage, and this orphanage specifically was for children and adults with disabilities. And this is kind of one of the things that it I had never really had this like experience coming from you know a student who grew up in the middle of Pennsylvania and there I was and I really was taken aback by a woman who was in a wheelchair sitting by the window who had cerebral palsy and couldn't speak. So I started asking her yes and no questions - wasn't getting a response back and then after, a couple days of working with her saw that she had voluntary movements. If it wasn't a blink of an eye and I figured out what was a yes movement and what was a no movement, what was a tremor, um and started kind of communicating with her in this way. And I - it kind of hit me that there were a lot of other individuals not just only in this orphanage but in this country who had these type of disabilities and didn't have someone there who was asking them these yes and no questions and figuring out what they like to do, what they didn't like to do. And then really the lack of opportunity because of their disability that they had. And I was, you know, 18 years old at the time, was going back to the United States to major in Biomedical Engineering, and I really thought you know, I would really like to create something to fix this and who did I tell - I told my dad - and my dad right away, was like: you can fix it, you can - we can figure it out you know, just like these little ideas that I had growing up that dad just was - got really excited about.
Yeah I mean they're - I guess I didn't go into it a little bit, but growing up there was sometimes like when I was learning how to draw flowers and stuff he's like: we could, you know make, a milling machine that would draw these into bed boards and you can program it that way, and anyway, it just kind of was a natural thing for my father to just when that inventor side of me came out, for him to encourage that and not be some crazy idea but something that yeah would take a lot of work but I knew it was something I was really passionate about and you know I'm 26 now, and I'm still just as passionate about it and I'm really glad that my dad pressed me to move on with it.
Well I was so impressed in our conversation where I almost felt like you were set up in this life to do the work you're doing because I remember you saying that when you were answering the yes and no questions, that you could see her countenance light up and she was in a better place after being able to communicate and I don't think any of us can imagine what it would be like to live with the frustration of not being able to communicate in a fluid way. And there are speech assistive devices available to people that are mostly affluent so what's the cost of speech assistive devices, on the market for people who have the money to buy them?
Yeah, so you know, a speech generating device isn't just you know, a box like a tablet, it includes things like a mount, to put it on their wheelchair. It also includes different sensors you know, if they can't do direct selection and select on a board sometimes they need a sensor and that they can control with their foot, or even with their eye movement. So if you're looking at a full speech generating device, for a low-cost one six thousand dollars, for a full one you're looking at fifteen thousand dollars and sometimes even more, so it's a thing that has you know, made some headway on getting covered by insurance. But having a communication device covered by insurance can cause issues as well. Because sometimes it's not medically necessary, and then of course, people that don't have insurance, that can be really hard to get one.
And is that kind of the disconnect you saw I mean, obviously people that are in Ecuador don't have that reach or that capacity. So is that sort of an area of compassion for you to go: they don't have access?
Yeah absolutely. It was - it really was all about the access and not just in the price but also in the type of sensors to give people access to you know, control speech generating device not just with a finger, but with eyes. And knowing that you know, there's so much technology out there and I know in the beginning we prototyped with Arduino and Raspberry Pi and these really low-cost sensors that could like change someone's life and just like you said, can you imagine not being able to communicate and connect with someone? And to think that these low-cost sensors could allow someone to make relationships, to share their dreams with and that was definitely one of those things that you know, as a freshman engineering student really gave me a passion to bring these types of sensors that we are using every day you know, in our cell phones and in all this technology all around us but really adapting that for the disability community.
So once you were in college, you have this idea, your dad's encouraging you. What was the next step for you? How did you start innovating and deciding to actually make a device?
Yeah, so I guess as soon as that, the first thing I did was decide that I was going to make a device. I think that was just like that was...
-that was a first step right?
That was the first step. The training and the business model, that kind of all came later, but I guess the first thing that I did was, I took a trash can, I carved out two sticks, put a potentiometer in the middle of them and hook that up to an Arduino Mega and basically wrote a program that allowed someone to calibrate it to say what angle, or the threshold that they needed to to make a selection. And then had these WAV files playing that basically went through menus. So for example, one was like food, the other was emotions and so if they kick the foot and they move the potentiometer for the angle that it needed, with the width of threshold that would open up the food options and then they could you know select something like: I want to eat, or I want to cook, and then yeah made that a checkmark. Then I made a glove, so that somebody who could just you know, twitch their finger also press a finger on a surface and really the whole time I was thinking about the individuals that I worked with in Ecuador you know. At one point I was like: Christina could use this..
- Ah, I love that.
-she was really - and she still is - I actually just saw her last summer, she's doing wonderful. But um really great foot control but nonverbal cerebral palsy like the things that she could do with her foot, I would give her you know my cell phone, and she could click down on a button. So I was thinking like, what is - - what are ways that I can create something that was wearable for independent communication?
Because a lot of times these people didn't have caregivers that are around them all the time to make sure that their communication device was in the right position. But then as soon as I had a working prototype you know, it was like I gotta test this you know. Let's see if this works and if what I'm doing is completely you know, not gonna work and that's where I found Arlyn. Arlyn is from Johnstown Pennsylvania, she has cerebral palsy. She's in a residency home and she also has great control of her feet - very strong legs, similar to Christina. And we used the foot sensor for her to share her poetry for the first time. And were able to really adapt our program to do that, and right away there were things you know, that didn't work. We tried an insert into a shoe, and she was like you know that doesn't feel comfortable I don't want anything in my shoes - and really just started this design process with her you know and seeing what she would be comfortable wearing and also what was working and what was efficient. And how did that integrate into her daily life and be something that she did want to use to communicate every day.
I love that you were collaborating with her, and that you gave her a voice to say, I don't like that in my shoe right. So to create this loop of instantaneous feedback, you gave her a voice, but you also gave her a vote on how she would interact with this device, how would I - that feels good, that doesn't feel good, this works for me and, by the way, for those that may be listening or watching, I will share the videos with Arlyn, they will make you tear up instantly. It's - this woman is a poet and her poetry is beautiful, and she is now sharing her poetry for the first time in her life because of Mary Elizabeth's ingenuity.
-and Arlyn you know, she - she is so smart, and really our design has so much of her in it. And I talk about this sometimes, I know I talked about it with you. With people with disabilities - just you know - being problem solvers because they have had to overcome hurdles their whole life. Like Arlyn, she sets her VCR with her foot, so many people don't even know how to set their VCRs she's doing it...
That's hilarious [laughter]
-so many people don't even - caregivers who come around, they don't know how to work this VCR and you know, to make sure that, that experience and that perspective that she has, is in this assistive technology that we're developing and I think it's a really important population that really gets overlooked in technology and innovation and especially innovation, for the disability community.
Well you have no idea how much I just love you and what you're doing. It is such an amazing thing. In just the few videos that you have Mary Elizabeth, you can see the light in her eyes and you can see the camaraderie between the two of you and the deciphering and working together on how to make this the best fit for her - it's really a beautiful thing. And so, at some point in college, you got it working right, you got a working prototype right? And did you show that to your dad at some point or how?
-Oh he was involved in this, this whole point.
Oh he was, okay.
-he you know, he had and still does - in CNC controls, so you'd have little parts that we would need to mill out so we'd be talking you know: can can you make this design for us? We didn't even have a 3d printer at the time so - we have a 3d printer now which makes rapid prototyping - but yeah, yeah he was you know really alongside of us. But also it was, taking engineers - and a lot of times you know this happened with us - was people that had all this tech skill but never interfaced with people of disability and seeing where they could apply their skills, and how much an impact that could make on a life, and on many lives. And I think really, for my father, that was you know, a really aha moment, because you know a lot of times - people with disabilities - when you meet them for the first time, and if you're not used to it - you might think that they don't have anything to contribute, and that they don't have ideas because of their communication disabilities.
Right.
And me - when my dad saw Arlyn give us design advice - he was like: oh my god you know, here is this woman in the middle of Johnstown with all these ideas. We've been working in our lab and on the bench for a year, and like we didn't come up with these things, and right away she was like: hey why don't you try it just as you know, a switch here, and place it here, move the - let's categorize the menus in a different way to make them more optimal and just all these ideas and it was really just a great way to break down the stigma of disabilities while helping people.
I love, you know obviously, I've been in this industry for a long time and I love what technology can do you know, for people's lives. And I love that you've been able to make that connection. I love that, hearing about your dad that his eyes are so wide open and I think that is something you've really made me aware of, that makes complete sense to me now, it seems like an obvious thing is people that are not speech capable would be amazing problem solvers, they would have to be and so to have those as your collaborators. What a genius idea right, plus they're gonna be the ones using it so also to have a vote in how this is. So, you continued to develop it and then did you patent it at some point?
Yeah so actually, my freshman year I filed for my first patent - provisional patent. Full application my sophomore year, which is a awesome you know. Two and a half - three years waiting to hear back from the patent examiner - but we were awarded our first patent November 2016.
Exciting.
Yeah it happened like two weeks before our IndieGoGo campaign went live, so there was just a lot of excitement going around that and yeah, so that was our first one down, hopefully many more to go, and we're always innovating new things around here. But yeah that was a huge, huge accomplishment for me.
Yeah not many have their first patent awarded while they're in college - that's pretty neat. So you got your patent, and tell us about - you had mentioned on the phone about - I think it was in your junior year about Penn State coming up with a Young Entrepreneur program and so you started filing for some competitions or some things that would actually give you some funding to help move you forward?
Yeah, so really in my junior years I kind of had this realization that if I was gonna make the impact that I wanted - a large social impact - I was gonna have to scale. If I was gonna scale, I would need a really sustainable business model to fuel that. So luckily right around ProjectVive's birth, Penn State and President Barron launched the Invent Penn State initiative which started Happy Valley Launchbox, which was a no-cost business accelerator downtown for students and community members so I, we applied for that - we were the first ones in - and so being the first cohort team, it was like an empty building, no one was there at the time, and yeah it was actually really cool for us 'cause we went from like being a dorm, to like having this awesome space. But then, they had, an NQ competition where we pitched ProjectVive in front of a shark tank kind of set up at our University, and it was actually aired on WPSU and we got $17,000 from that - which was huge for us at that time.
That's a lot of money yeah.
Yeah and that really just gave us validation, that what we were creating was something that was needed. It also pressed us to do a market analysis and realize that wow, there are so many people that need these type of devices that just can't afford it, or don't know that it exists. So yeah I took advantage of that in college.
So, before we go forward. Something we didn't mention, but I think it's good to insert here is - so jumping ahead for a moment - what is your plan to market the Voz Box at one, two, go to market?
Yeah, so you know I really have a passion for developing countries and also South America. So two things of how we're gonna go to market: One is - there's a lot of trade shows for people with disabilities - so there's ATIA the Assistive Technology International Association, ASHA, and where you can set up a booth and speech-language pathologists, parents, teachers and also a bit of alternative communication users, or people with disabilities that use speech generating devices will come to learn about new technologies. So that's definitely one way. We're also doing kind of grassroots - by reaching out to local disability organizations here in State College, that also have chapters all over the world, so and definitely all over the US - Easterseals, we've done a collaboration with them.
So what is your price point right now - we're projecting, I'm not - we won't hold you to this but what's your projected price point that you'd like to sell it for?
Yeah our projected price point is $500.
$500 ?
Yeah that's for the full communication device. And then also, we're gonna be doing a lot of open source devices that can help you and ways of creating mounting systems on your own, to even get that lower.
It's incredible. Like I see that as such a, I mean, lowering the barrier to entry to almost anyone right. Because I wanted to mention the price point before we move ahead - and so you won the $17,000 then you entered a couple other competitions tell us about those?
Yeah, so we applied for the ALS Association and Prize for Life Assistive Technology Challenge, where we were one of five out of 87 teams, it was an international competition, and we were flown out to Ireland where they brought in...
- Wow.
-Yeah, and they brought in ALS patients from all over the world to try out our technology which was a really important thing for me. I've had two uncles who have passed away with ALS and even though I had a lot of work with people with children and adults with cerebral palsy ALS is a terrible disease and 75% of people with ALS will lose their voice. You have two to five years to live after diagnosis, and to see our devices, that I had created you know, thinking of specifically people in this orphanage but then realizing that people like my uncles could also use these devices. We had someone from Iceland, another person from Japan. We've developed also these little blink detector glasses that you can basically blink to select, and he used those and he loved them, and he was able to spell out a word and just to see someone from Japan, to meet us in Ireland try out our devices, and realize that so many people around the world - not only with cerebral palsy - but with ALS and Rett Syndrome, it just really opened my eyes to the impact that this could have. And also getting this support from the ALS Association was really awesome.
That's an incredible story. You have a video on that also right Elizabeth? Okay, so we're going to share that one as well in the show notes. And the last award that I think you mentioned to me had to do with Cisco right? So tell us about that one. Well I'll let you tell the story, but because I know you had an IndieGoGo campaign too, and a patent, you had lots going on. So spell it out however - how you know - I may be getting these things out of order so.
Actually you're not.
Okay good.
So then - this is actually last summer - we applied for the Cisco Global Problem Solvers, a challenge which was inaugural, it was also the first Global Problem Solver Challenge that they've had. Some recent projects these days are the guinea pig for everything. But yeah, so we applied for that , and I really could talk about my mission, and working with you know, people in Ecuador, and just the low price point and how this - this wasn't just for people in the US, for people in Ecuador, but also we did a little work with a professor in communication disorders, who was in Sri Lanka, we sent a device out to to her where she used it with a boy who was 17 years old , with cerebral palsy. And it's just so many places in the world, don't have access to this type of technology. And in schools and education also, in just adult community life. So we applied for that, made a video for it, and they had this People's Choice Award. So the main award was for $100,000, and the People's Choice was for 10k. And I got everyone to vote for us, you know I sent out to my professors, 'vote for us'! you know ProjectVive, all my friends and family and all of Arlyn's friends and family too. Then that - the day that they were gonna announce it, I kept on refreshing the People's Choice page and all of a sudden I realized that you know this team from Costa Rica won, and I was like, oh man you know, we didn't get the people's choice! And then I checked my email, and it said: 'Congratulations Grand Prize Winner Cisco - - $100,000.'
Oh my gosh, you won a hundred grand!
I know, and I was like, what's going on? That's not 10k, and that I mean, I'm still - I still can't believe it. And you know this - it's been a couple months now - but that just really pumped into our research and development and got us to where we are right now in creating our final product. And yeah, we're just really, really thankful for that support.
That's amazing. I gotta say I'm not surprised, but it's the best story ever. And then so lastly, tell us about the IndieGoGo campaign and - and your Road to Ten Voices that ended up being more than ten voices?
Yeah so we did an IndieGoGo campaign: Journey to Ten Voices and we - I was actually in Ireland for like the end of it - but we raised enough for 14 voices actually, so that was really exciting. And really yeah - that's really allowed us to reach out to the community. For instance, a recipient of one of our Journey to Ten - well 14 Voices - was a 16 year-old, who lives an hour outside of State College and he's doing great. And we also helped him out with a wheelchair gas pedal so he not only is using his speech generating device with an e-sensor, but is also able to independently move around which has been so cool and he's just learning so much from having a device that really wasn't reliable before we helped him. And then you know, just learning from another person, so it's been really cool.
That's something else, we have pictures so when Mary Elizabeth introduced herself to me on LinkedIn she sent me a screenshot of him getting his Voz, and you've never seen a kid smile this big in your life you know. I thought he was gonna rip his ears off with a smile - he was just so happy and it just makes - you can see me also, I got this smile-grin talking to you this whole time. It's just a beautiful story. So now you have seed money right? And so tell us where you are now, and kind of what the next year or so holds as you forge forward?
Yeah - so really, it was a great thing that this whole time we've been working with users, also talking with you know doctors, and teachers that we did the I-Corps Program, where we interviewed 50 people from all over the world. Parents, speech-language pathologists, doctors, teachers, augmentative alternative communication users themselves, and really took one - you know, the user testing that we did, our feedback, what we've learned, the market analysis that we've done - and then also these interviews, to test our assumptions and make our final product. So really what we're developing now - it's the next thing of our beta product and creating something that we believe is going to be able to scale, that we can bring to places like Ecuador and Sri Lanka, and that we're gonna be able to make a sustainable business model on because I know I talked to you about this. We really want to make sure that once we give a voice that we don't take it away, and I think that it's been a great thing that during college I've been able to experiment and test and really have this quick feedback loop and creating something that will make a long lasting impact so that's what we're doing now.
I think that really shows so much a vision on your part actually Mary Elizabeth, because I can't imagine - again I can't imagine giving someone a voice and then having to take it away right, that would be so devastating, and that you've had the foresight to make sure that it's sustainable and and that you're looking at it, not only from an engineering and visionary, but a very practical standpoint to make sure that you're gonna build a solid business. So I really appreciate that about you.
Yeah there's got to be someone there to answer the phones when something goes wrong.
Right, right so I love that you're actually building a sound company and and having good mentors and, and helping you along, and that you have a really solid vision on this. Well what else do we need to talk about? So you're heading towards a scalable product. I think I'll insert here that I got to meet Mary Elizabeth's and project Phoebe's CTO, Trip what's Trip's last name?
Miller.
Miller, I got to meet Trip Miller and we had a call, so one of the roadblocks that they ran into, is that they were using basically a free design tool that got them this far but they they needed something farther and God bless Altium. They were able to sponsor Mary Elizabeth and ProjectVive, and give them a license of Altium Designer, so they've been having a lot of fun trips - being like a kid in a candy store...
[laughter]
I know, we really have, I mean the trouble that we have gone through and also just working with other collaborators and not being able to get the right schematics for them and and having to basically transfer, not only our Altium files or - I don't want to say that exact names -
Yeah I know, I was trying to avoid that too. Some companies' schematic...
[gestures] yeah.
But we've just been able to very quickly start up and I know that it took us about you know four hours to start up our other PCB programs and with Altium, like within an hour, we were creating traces, which was just awesome. So we are so excited and just being able, it's - it's accelerated our development and we're very thankful for it.
We feel lucky, we feel like we get to remove - we get to have the privilege of removing a roadblock for you and just let you charge ahead my dear, so good good for you and Trip. And I'm really glad that we really have the privilege, to do that for you. So we are gonna list in the show notes everything about ProjectVive, the Voz Box, your - like anything you want us to share, let's share it because it's a beautiful story and all of us that love technology, love to see kind of the social aspect of doing good. Doing good in the world, through use of innovation and technology and you're kind of like a STEM-girl poster child which is really fun for me as a woman in tech to see how you came up, and your parents, how they inspired you, and this is really great. What else should we share with the listeners? Have I skipped anything - what else can we talk about, have we missed anything?
Um you know, if you really do feel moved by ProjectVive's story, we do have a fiscal sponsor, so we accept tax-deductible donations and if you go to Projectvive.com - you can hit the donate button or just support us, like us on social media and share our story, and if you have any family members that would be interested in our technology, let us know and we would love to help.
Great - well thank you this has been the highlight of my day and we will also be sharing Mary Elizabeth's story - I've interviewed her already and she will be also in the OnTrack newsletter, coming up in June, and so keep your eyes open for that. If you do not subscribe to the OnTrack newsletter, you can go to our resource hub and subscribe - there's a newsletter tab there, and you can subscribe. So if you're not already subscribed, you can subscribe there and again in the newsletter we'll include all these links in that because we certainly want to put her on the Altium platform, and celebrate all this young innovator's doing. So Mary Elizabeth, you are the best, thank you so much for spending your time today I know you're a busy woman and we'll stay in touch and thank you again for all you're doing, we just think you're wonderful.
Thank you so much Judy, and thank you so much to Altium, and we're just very blessed, thank you so much.
Thank you. Again, this has been Judy Warner with the OnTrack podcast with Mary Elizabeth McCulloch of ProjectVive, we look forward to hanging out with you again on this podcast. Until then, remember to always stay OnTrack.
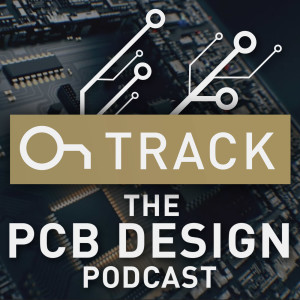
Tuesday Jun 19, 2018
Tuesday Jun 19, 2018
Bil Herd shares stories and design wisdom from years of experience as a hardware engineer, most famously at Commodore. Starting out self-taught, Bil found his way to working around brilliance and some of it rubbed off a little. Learn about his interesting journey from TV repair to Commodore, Hackaday and beyond. Today, Bil is self-employed and focused on networks, high-level architecture consulting and hardware projects.
Show Highlights:
- I never forgot how to do hardware design. It’s fun to be able to do that. I’m working on an Altium project right now.
- You get to be imaginative for a couple days, and then you spend the next couple months paying for it looking at every single line item, every footprint and trying to catch where your brain was wrong.
- Commodore Hardware lab, splitting bus for video and hired to lead the team shortly after.
- Going after a swag bag offered by Adafruit from an MIT Open hardware conference resulted in a video series with Hackaday.
- Almost all the errors I’ve made in CAD systems were related to parts I’ve made. For parts and footprints - you need to have someone check your work.
- To start a new CAD system - make a trash board, force yourself through.
- Process to start learning a new CAD system: Open CAD > Get Overwhelmed > DRINK
- Making a board on a new CAD tool. First I make a trash board knowing I won’t use it. Then make a real board, using all the rules.
Links and Resources:
See all show notes and video here.
Hey everyone, this is Judy Warner with Altium's OnTrack Podcast.
Welcome back.
Our audience continues to grow and we thank you for joining us again, and I want to give a shout out to Steven Newberry from LGS innovations who took away always marking his diodes with a K, and so many of you have chimed in and help driving actually who we have on the show and the topics we discuss. So thanks so much for joining. If you would please connect with me on LinkedIn or @AltiumJudy on Twitter and Altium is also on LinkedIn, Facebook and Twitter, and remember we're always on YouTube as well as on your favorite podcast apps.
So thanks again for joining and hold onto your hats because we're gonna have a little bit of a history lesson tied in with today's best practices. So today our guest is Bill Herd, who is actually a figure of history and he has a Wikipedia page that you will have to take a look at. So for those of you that are probably, I don't know 40s and above, might remember the Commodore personal computer. It was one of the first, I'll let Bill fill you in all the details, but I remember vividly when I was in my early 20s, my dad coming home with a Commodore 64 and it was all the rage and he thought the world is forever changed and I'll never ever use all the 64k that I possibly have.
So Bill, welcome and we're so glad to have you and can't wait. We're gonna tell some stories, you're gonna give us some design wisdom, so thanks so much for joining us.
My pleasure. Actually I do describe myself as a recovering Commodore Engineer the active recovery never stops you've just gotta keep trying to get better.
Well, I'm sorry but based on the background behind you I'm not sure about your recovery.
Okay - I've relapsed a little [laughter]
So, briefly tell us what you're - are you working now as a Consultant, you know like your own entity I forgot to clarify that with you?
Yeah actually I'm self-employed so to speak, I owned an ISP for about 15 years and had 16 people and we did all that and then it ran its course as ISPs do, and so I do a lot of networking and high-level architecture consultation, but I never forgot how to do hardware design. So actually you caught me in the middle of doing an Altium project right now, where we're going to a limited quantity but I just went through all the steps - all the dirty little details getting a PC board out, so it was kind of fun to still be able to do that.
I love the way you put it, 'the dirty little details' there's a lot of those right?
You get to be imaginative for a couple days and then you spend the next couple months paying for it by looking at each and every line item and every footprint and trying to catch where your brain was wrong you know, way back in the beginning.
Yeah well, so I also noticed you have - as I've gotten to get acquainted with you a little bit - back in the days of Commodore and the early days actually of the personal computer business the words nerds and hackers weren't really around but seeing you sit there in a Hackaday shirt with that lab behind you, I would say you are the quintessential original geek or nerd what do you have to say about that?
Well, one - we did call it home computers, back then the PC hadn't been invented yet, and I also mention I've never been to school for any of this. I was a - basically a high school dropout - and ended up in the service, and went back and almost got my degree. I own like a library book for the money $3.42; for a library book, in English class where me and the teacher just couldn't make it work.
So about three years later they sent home my diploma with my sister just going: here you'll need this someday. I used to say I was self-taught but what really happened, self-taught got me into a couple good places and then the education really started; working around really smart, really brilliant people, that's where I got the education that made it so I could do a product from beginning to end. So I was fixing TVs, got my TV Repairman License at the age of 17, in Indiana. You know and sometimes they'd answer the door and didn't want to let me in, because I got long hair and I'm carrying tube caddies and they're like: who are you? I'm like, van out front, TV repair, and people fed me cookies when they saw me fix their TV sets.
Right well we will share Bill's Wikipedia page and there are some awesome pictures of this long haired hippie, with this cut off denims...
Hey don't tease me about the shorts, it was 1980.
Hey I'm sorry, but I wore shorts just like that so yeah, so we will share that because there's a lot of history and fun and great pictures that I think you'll enjoy hearing. So tell us a little bit about how you got into the whole Commodore thing and then we're gonna dig in and give our listeners some really practical advice on those nitty gritty details you talked about, and then we'll wrap up with some more fun stories. So just briefly give us an overview of Commodore and Hackaday?
Okay if I back up just a little bit - I started at a digital scale company in Pennsylvania making instrumentation, so there I learned to do very accurate stuff with very good grounding. I understood analog and RF spectrum and all that, and it was all hand taped right. Well a guy named Terry Fisher who I just got through working with again, so after 35 years, we're still doing it and he was on Altium this time. So when I got to Commodore I had the background for how to make something expensive work. And then you just take that and you just shake it and it comes out of your head cuz now you've got to make it cheap, cheap, cheap, cheap.
Yeah.
And people are mad at me these days because they say: oh I have a 30 year old Commodore and it just failed! I'm like: it was designed to last five years. You should have put a switching supply... what? To put a dime more into it I'd have been fired if I did! So I got my job almost by accident at Commodore. I mean, there's a whole story here and I'm going to - let's just say I blew the interview like three times and still got hired. You know what, not even taking in my resume you know? But so I got there, and they didn't know what to do with me, and I read in a book that I was actually hired as a Technician. They just knew they could use people like me and then they sat me down, the guy was named Benny Prudent, and he said: well here, study all these software manuals. So now I was gonna be right for a programmer - I could do 6502 programming.
But for a disk drive - I'm like: that sounds like the most boring thing in the world, but sure. And then I walked into the hardware lab and I saw what they were doing - they were splitting the BUS for the video - which back then I was doing it at home - and that's why I said: I just built something at home where I actually don't wait till the vertical retrace time to ramp and two weeks later I was in charge of the project. The guy was leaving, they didn't have anybody else, so now I'm a Project Leader at Commodore within a couple weeks.
Oh my gosh, it was like the Wild West was it not?
Oh absolutely and I loved it and I brought a certain 'animal house' to that, because we had lost a lot of talent. I mean there was people like Chuck Peddle who designed the 6502, he's gone, but his cigar's burning in the ashtray. The chair's still warm right. So you knew that these people had been there, but they're gone - and there's these kind of older, stogier guys and me. And pretty soon it became an environment where shoes became optional, so we definitely made it into what we wanted to and you have to do that when you work 20 hour days.
That's crazy so you're sleeping in the office or not sleeping?
My record was 11 days without leaving. I had an air mattress, I would actually hot bunk with the technician so I would get something designed like 2:00 in the morning, check the air mattress out and they would build it for me and I'd go catch an hour to sleep and then they'd come back and kick the air mattress and say: it's built, and just taking showers out of the sink - things like that.
Well we'll talk more about some of your fun Commodore stories because I know we'll really want to dig into those a little bit more. But tell us also about your involvement with Hackaday?
Yeah it's actually interesting, that I used to watch Adafruit's Little Saturday Night Show right and they would do this thing where they'd give something away and usually it was a product and I didn't go for that as much because I could just - their products are so cheap I could just buy one. But one time they had been to the Open Hardware Venue - a conference - and it was actually at MIT I think - and they asked a question and I went right to a web page, found the answer because they were giving away the swag bag, so I said, that I'll go for! So in the swag bag was some cool things but one of them was a - it was like an Octopart - only it was somebody else's version of it. Well they're owned by the people that owned Pacada.
So I start talking with them, I ended up a Beta Tester, and the guy realized I just never shut up, that I'm always telling stories right? And so pretty soon he puts me in touch with Mike the head editor at Hackaday, and I'm doing the same to him only in emails, and finally he's like: all right that's it, write stuff or shut up, and so we came up with the video format because it just - it works for me - it works for my personality and I am a high school dropout which means my English ain't so good anyway, so the video works better for me.
Yeah well we will also share those for listeners here - I've seen a few of them and he is perfectly suited for that. So I'll share that as well for you wannabe hackers. So let's dig into some immediate content that I hope will help engineers and PCB designers that are listening to us. You have told me - how many EDA tools have you used over a year period?
Yeah I made it all up, hardly any at all [laughter]. No it had to be like seven, eight, or nine, depending on how you count them and to what degree. But going back to the 1980s when a workstation cost fifty thousand or a hundred thousand dollars and you couldn't get them as a home user or even as a small business and so, we started it. We started with hand tape and the cool thing with that is, if you can do good hand tape, you can use a tool like a CAD and do more. But you still have to be good to begin with right? You have to understand the principles and nowadays it's more common for engineers to do their own PCB layout but I'm still of that school that: do what you do really well, and use somebody when possible that does what he does as good as you, that's why I use a guy like I said, Terry Fisher.
He's as good and he knows when to ask me questions and I know when to shut up right so we have a good relationship for that kind of thing. And we started on Mentors, which actually we designed chips with, but he started on a system called a side card, and it was a card that plugged into the backs. Well when he'd start moving parts on the PC board everybody's computer slowed down right. These chip designers and stuff because it's on the VMBus, it's taking the cycles directly, so they give Terry his so - he actually he goes by Fish. They gave Fish his own VAX so now he's got a three hundred and fifty thousand dollar CAD system to lay out pc boards and so that's the 1980s, and in the Mentor, we - I hadn't really even seen a real mouse like we use until Sun's came out. It had a scratch pad so I actually grew my fingernail into a point so that I had a built-in stylus on my index finger - so yeah just genetically modified kind of you know... [laughter].
That's funny - so with all of those changing of tools which most people that I know, that are designers, once they get proficient on a tool they'd rather die than change tools because it can be such a painful process. So tell us about changing tools. If you have to do it, what is the least painful path?
Well management will always want you to do that right in the middle of a project right and that's - it's pretty key to not try and - we actually moved our hardware labs right in the middle of a project one time too. Just kind of in the same... But if you're going to change programs, realize that they're just tools, and after you've changed a couple times you start to go: okay I know how this play goes and and you do a couple of the same things and you sometimes learn and really appreciate your old tool and sometimes you learn that hey, the new tool's better. But they're no two the same, especially in CAD where there's so many complex things. So I think people picking up tools - I saw it a lot with EAGLE - what they did, and they did an amazing thing for the maker industry and the home users - even though I hate the program.
if you're a professional, you just go: what, I have to drag the trace off the screen to hit the menu? this is like somebody put a GUI on a command line program. Well guess what? EAGLE's were GUI on the command line program back in the old days. So you know the false attractiveness of something like EAGLE was, it did have huge libraries right, and especially for boards because I mean these, Arduino boards - I can't deal with the mechanics of them, they're not on the center's, I'm used to all that - but what you really have to come down to when you do a CAD system is, realize you've got to make your own parts at one time or another, so you might as well get proficient at it. And if you're using libraries you might just be using somebody else's problems.
So even if you do use somebody else's library - it's like you've gotta still vet the part. Right, so just realize that you're going to have to make your own parts. And then there's things like BSDL importing and stuff like, if you're doing a 250 pin FPGA, you don't want to hand-do that either, so there are tools to help you avoid the mistakes. But almost all the errors I've ever made in CAD systems are related to the parts I've made where - I actually have data books here not data sheets - a guy said: yeah you use the word book don't you? And while you're looking at the book, making the part, I've done simple things that I'll never catch myself - by having like D7 to D0, instead of D0 to D7. When I see what I think I want to see, and that's it, the mistake is in there until somebody else catches it. So we used to always have somebody else check our parts you know, in footprints or the same way I still think.
So that's the first thing, is realize you’ve got to make your parts and then I recommend you just sit down and trash a board - try not to ruin your library in the process - because you could screw up libraries right. But then throw that board away and start again. This time trying to obey every rule you know how, and actually even if you don't produce the board actually obey all the rules, look up every command you don't know that you actually need, and that's kind of how I started a new CAD system.
So for our audience, Bill sent me a few notes for the point of our conversation here, here is a note that he wrote: Starting a new CAD, do a couple of projects early on - sort of what he's talking about right now - his first line is, 'open CAD - get overwhelmed - drink' [laughter].
Yes, it can be overwhelming! It's like my drill sergeant said when I went through basics: 'we know it hurts gentlemen, you don't have to tell us' and we're like, oh I'll keep my pain to myself. It's the same thing: I'm supposed to be overwhelmed, okay let's you know. So you open it again, and you start looking for what you know. So there are some things you need to learn the quirks of upfront. Like how do you do a BUS? Everybody does it slightly different, that nomenclature, whether it's curly braces, brackets, whatever. And an 8 10 dot dot 8 zero - it might be low to high, it might be either way, but you got to learn those things. And interconnects, how to make sure that a part's really hooked up. One CAD system I was on, was called Ulti Board by National Instruments, and the DRC wasn't catching the fact that parts looked like they were hooked up, and they weren't. Well, how do you catch that?
Well yeah, how do you catch that?
Yeah so you've got to - you go around jiggling your parts and it's stupid you know, so do a good DRC and you know, Ben, when he looked over my shoulder to check my router - from Hackaday, Ben Jordan. He gave me an - actually a compliment that I took, which was: oh it's nice to see you have all your DRC errors fixed. Well I'm old enough, I don't remember fixing them, but I'm old enough that I know I would have fixed them. Cause that's it, that's your last chance to catch that you have a net floating, even though you don't know it. Whether it's a misspelling, even capitalization change, something like that. So yeah, you got to learn all those dirty deeds and details.
I was just talking to John Watson on this podcast about a week ago, we talked a lot about libraries and the same subject. It's like a theme that most headaches seem like they begin and end with the parts libraries and even having a data sheet that's correct or hasn't changed in the last five minutes. How do you address that?
I still have data books [laughter] - no, it's still like going over it, and over it, a couple of times and having somebody else look as well. I'll still take a highlighter to a schematic sometimes just if I feel I'm getting confused, out comes the highlighter to help me get more confused.
[laughter]
-at the end hopefully I get it.
That's funny! Okay (I keep bumping things sorry about that) so okay.
Let's talk about hidden nets...
Okay go!
I hate them [laughter] hidden nets are where somebody thought let's show up DIP package or something and we know we are hooking it up to +5 and grounds so there's no point in cluttering the schematic with it. Well my attitude is how do you know it hooked up to +5 and ground? Nowadays it's 9 +5 and ground is +3.3, 1.2, 1.0 - - so yeah whoever came up with that, they need to have something I don't want to say something bad happen... [laughter] They need to miss a CES deadline or something themself.
So it's the invitation for failure is what you're saying?
Yeah you can't check it, you make assumptions and that's where problems start so yeah.
Would you say that making assumptions is one of those easy pitfalls for designers to fall into?
Yeah, thinking SOIC is a size. It's not you know, there could be white body, skinny bodies, and it's like: oh but the picture looks like - no. You better learn to have - one thing is you have to learn with new CAD packages, is how to measure things. And you need to do that, and then look to see oh it's .43 inches or ... and I - one time I almost missed the fact that the the lead pitch was 0.5 instead of 0.75. That wouldn't have fit!
That would have meant instant failure. You made a comment about assembly drawings being readable what did you mean by that?
You know as parts got smaller the silkscreen no longer - it's not as important because of assembly techniques but if you still want to measure - you can't get that little silkscreen anywhere near the part sometimes, so you end up with an assembly drawing where you had to like put all these silk screens where you now want them inside the outlines and all that so it's like you can't use the silkscreen for an assembly drawing like the old days. You have to do a whole new one if you want to be able to find the part. But now these days what I do - but I'm working on a really dense... or troubleshooting, I actually keep the CAD open and I do the - jump to component - and find it that way it really is faster to use technology sometimes...
[laughter] sometimes.
Sometimes, at least I don't hand etch my boards anymore.
Yeah.
Remember that, the seventies?
I always say, because I was in the bare board industry for years, sales and marketing-wise and we would take people, walk through and do surveys, plus I actually worked on a shop floor for a short period of time like, I'm gonna die of heavy metal exposure man, the chemicals we had in there. I remember walking into a planing room at the first board shop I worked and my skin just burning, yes burning, just poor ventilation and there was sulphuric acid in there.
I'm told you can't have plating or PC board manufacture in New Jersey, that they've just kind of made it so you can't do that.
Well there's that - there's a little bit of toxicity going on in the chemicals.
Right, and at Commodore we made the ultimate printed wiring board printed circuit board right which is a chip - it's just really, really small, and we polluted the groundwater and you can look this up, but we had to buy dedicated lines for like 11 neighbors, and then we had those golf course sprinklers in the back aerating the ground water. Well my first day there I mean they're just literally spraying it in the air hoping the VOCs evaporate right.
Oh my gosh!
I parked too close my first day there and I come out and my car's covered with this sticky stuff right and not only that, I had parked under a tree so now the leaves are stuck to my windshield with this and to try and peel them off - they just break - and they're like: oh yeah dude, don't park there man, that's in the water.
Like I said, it was the Wild West days I mean.
Still a Superfund site I'm told.
I bet, like it's frightening - it's frightening and I'm glad we've gotten our act together a little bit environmentally oh my gosh because literally we could all die from those toxic...
Yeah I remember the day my dad brought home mercury to play with you know.
I remember my neighbor was an engineer - he brought home mercury to play with and we'd watch you know, roll it around on our hand or whatever, crazy! Forget about playing with it - you know putting it in your teeth we would like, oh here, pour it in my hand, let's roll it around, isn't that cool?
Yeah and you put it back in the jar and it's never quite as full as you started right because you're leaving a certain amount on the floor...
Good memories but we might die young, just saying...
[laughter] So when you start a new CAD program, do you just jump in and start designing? How do you take that on if you're gonna take on a new CAD, what's the way you approach it?
Well as I said, I kind of I go in knowing I'm going to do a trash board, it's all about just hooking some stuff up knowing that you're making mistakes and then I try and do something more real and try and really obey the rules and that's where it starts - that's how you're learning from page to page cuz every CAD system's slightly different, but it's kind of like how you think. You drop a part, you try and put a wire on it and the kind of mistakes you'll make is not having a clear way knowing how you want to do all the resistor values in the world right. Do you make a part for each resistor value, or do you use a generic part and assign the values? And those are things you just have to figure out yourself on each CAD system I think.
So I mean, I honestly don't know how it's done. I have lots of compassion for my engineering friends who are also laying out boards who really got no serious, formal training in PCB design, but alas they are laying out boards and then they get thrown a new tool like... So do you just hop on it and jump in and swim?
Remember, it's a tool too and they have some really great tools like things that'll help you plot RF noise on the ground plane or thermal or something but you know, at the end of the day that's not necessarily real life. It's a tool you know, so it's an opinion, and it might be a faster, better, more colorful opinion than we used to get with an old thermal probe. But you just got to kind of try it and if you work around people who can look over your shoulder they'll save you a lot of time - especially hot keys and stuff like that. And that's probably one of my pet peeves is I don't like having to rely on hot keys and that was even before I lost a finger, so now some of the hot key combinations are literally beyond this old man's ability to do without using my nose and stuff it's...
How did you lose a finger?
I tore it off!
Dare I ask?
I just caught my ring on something and I stepped eight inches off something - it stripped it off the bone, we have pictures on the web of that also. But I used to work at a trauma department and I've flown with a 103rd combat medics, I've been captain of a rescue squad. So I look down and I just go: I know where I'm going today - I didn't even tell my wife right. I figured she's away at a quilting bee, having a good day, the next day I was: Hi, uh, lost a finger and she got mad at me for not telling her.
I would get mad at you too... just saying like: oh Chee how's the quilt work? Good what did you do? I just lost my finger.
Yeah, yeah well my son actually looked at it and we took pictures - by the way I had to wait half an hour for an ambulance and being a former ambulance guy that was just like - that was an insult on top of injury literally. But I wanted him to think of it clinically and not be freaked out by it so we took pictures and stuff like that and then I told him, I said: well I'm going to - don't tell your mother - but I'm gonna leave with these ambulance people now and I'll be home probably tomorrow, because I know how things work, and he comes running to the door and he goes: dad, dad what's the key to unlock the Xbox? I'm like: okay you're gonna be fine by yourself. First time he was by himself, he's thinking about the Xbox so, all right!
Oh my gosh you crack me up. What else do you want to talk about relative to CAD tools? I'm looking at my notes here - you were talking about something - you talked about the buses, nomenclature and index based even that you'd said you hate those. So what else did we not cover?
I think the main thing is just how productive can you be? How well is it designed? And I was impressed by early CAD, which came out at like $4.99 in the 80s and we were like: whoa! I mean it's like that old monochrome purse, now there's PCs right - late 80s and the things you can do where if you copy a bunch of address lines, you can tell it when to paste it, auto-increment all those address lines as if I was continuing to do them. So if I grab a 0 to 7 and I paste it, now 8 to 15 is done for me. Well you can fly, when somebody has thought of things like that to do, you can go rogue. And it has to be controllable - sometimes you go, no I really wanted a zero to seven and - but there's tools like that, that can really make it. So, just the ability to double click and there's a new segment just like the one above it, tools like that are real important to me where I've just spent too many hours drawing in each line by hand.
Right, yeah I love when - well since I've been here at Altium, one of my fun parts of my job has been to help connect our developers with hard-working designers where they can say: do it this way, we don't work that way you know, it's really nice when CAD tools will actually get together with the guys that are watching and just watch 'em work and go: oh - because again it's easy for developers even if they've laid out boards - to make assumptions right. So I really love it when tool manufacturers actually take that into consideration and I love that we're doing that more and more these days. BOM distributor integration?
Uh it's probably the one thing we didn't have in the old days BOM integration where, and even picking the footprints, we had a three-ring binder of IPC footprints and that was always a step where errors could occur. I'm thinking this way, PCB designer's thinking that way, wrong footprint gets in there. But then even now, we can with Altium, for example, you see the part as it's a digi-key or arrow and you can make an attempt to select a part. Now; sounds great, but you end up getting into trouble when you go: oh wow, now I have to redo it for real, for the auto, for - I still call it auto insertion - for the pick and place. You know or, guess what? The stock status isn't quite what you thought it is, there's a delay in there and so now you're stalled, so you still have to, I think in my world, I still do a final BOM as a spreadsheet literally. But I get a lot closer in the tool. In the old days we were using microfiche if you didn't have the data book right? So nowadays it's integrated so it - again you have to be careful - it's a tool, it won't do your work for you and that's the thing.
I was just going to say - I've worked with also like hiCAD and now KiCAD... however they pronounce it.
I know, I never know how to say it either.
Yeah and it was good in that you could add modules to it. It was bad in that you could add modules to it. I kind of wanted already the 3d viewer working - ready to play with it and stuff like that. I'm really impressed with Proteus instead of EAGLE for that low-end market, not up here where Altium is, but that's when I was shooting little two inch by two inch boards for Hackaday and I'm doing a complete design every month and doing a video, and so I design it and it gets a minute of video time right. Then I throw it away to start on the next one. So it's called ARES and unfortunately the other one is ISIS, (nobody likes that name anymore), but that's the product name and they have an amazing auto router in there that'll get you a good completion, whereas if you've ever tried EAGLE it's like why do I even try the auto router you know? So that turns out to be in, and they singled out the maker market by including Arduino in issuing 80 mega parts in simulation and firmware simulation so now you can simulate it as if you've written the code. You don't even need to build the board to see if it works. And that's a cool feature. And we didn't talk about simulation - almost all CAD tools these days do include SPICE of some sort or a SPICE portal or something like that, and that's useful if you're down in the analog stuff especially. Again still just a tool. I've seen SPICE lie horribly to you, and you think it's going to work and it's really an artifact of zero volts or something like that.
Well there's a lot of talk these days about - because so many really capable designers like you, and like many people I know have learned this over a lifetime right - so if you're a new designer where are you gonna on board that outside of just one-on-one mentoring? Like any clues?
There's some good YouTubes out there, but I haven't found where you can - one, I don't have the attention span to watch somebody else work for five hours to pick up a couple tips right. So it's in the YouTubes showing you what they want to show you, but the best way is literally to be near somebody that's really good at it that's - unfortunately that's the best way - it's almost always like people almost pair off in engineering where one guy's learning from another even if they swap roles later that day because he's better at something else. That's just kind of the way it ends up going.
Yup, so I think what you're saying is find a mentor if you're not really good at it.
Right yeah and vice versa and mentor others. So I was talking about the wire, on each and every C128 board.
Okay, oh yeah actually Ben Jordan snuck that to me. So let's go into war stories a little bit and let's talk about 'the wire' also I'll get a screenshot of this I think Ben or do you have it? [Bill reaches over to show C128 board]
That's so cool okay for - oh my gosh okay, so for those of you that are listening to this on the straight-up podcast you need to go to this portion and look at the YouTube just to see this giant board that he's pulling out of the Commodore 128 and look at the keyboard.
This is what we call a 'barn door stop' it's too big to be a regular doorstop and that keyboard I designed by looking down at my BT 220 and I said, hey it works for me it'll work for future users too. I'll hold it up to the microphone for users at home right
Okay.
But there is a wire on each and every... we made 5.7 million of these.
Oh okay. Wait before you go into the wire story, give us the stats on Commodore 64 going towards it and compare that to the Apple because I thought it was really interesting.
Yeah the - and actually I narrated a video by a company called Junk Food about the - called the 8-Bit Generation, and I learned some things - our version of history wasn't quite as clean-cut as to who was the first and the best computer company out there so I'll give a little props there. But we often said, Apple's just using our parts, because we made the 6502. Well that's the processor they used, but we made the chip.
So in our minds Apple did come out and they were first to get a floppy drive and some color early on, but then we come whooshing by them with the Commodore 64 whereas they sold 5 million of the Apple 2 that you're always seeing on every show about the 80s right. You see a show about Silicon Valley: 'we created the home computer' I don't agree, sorry I'm from Commodore I am a competitor and we made 27 million Commodore 64's we had all 64K, we had these cool color chips and sound chips that they didn't have and we could do animation because we have these things called Sprites, except Sprite was trademarked by Texas Instruments so we had to call 'em movable object blocks, but everybody called them Sprites, so you could write a game right and the blocks are moving themselves around, you're not having to rewrite that whole screen and everything so it was an amazing computer and we called it the 'Apple killer' because we actually stopped talking about Apple.
Yeah then my boss wanted to kill Sinclair, remember the Timex Sinclairs?
I don't.
They're little tiny door stops now - I actually did use one of those for a doorstop and then the marketing department saw that and so suddenly every door in marketing has a Sinclair holding it open...
That's so funny I don't even remember that one which I'm kind of surprised. I was kind of tuned in at that time but not that tuned in I guess.
It was a $50 computer and actually, when the basic ran, the screen would go to crap because it couldn't share the BUS, remember I talked about that earlier, and then they came out with a color one and and it was cheap. I mean the Commodore 64 was $299 - by the way the Apple 2 was like $1500, $1700 and we're $299 - and then we did something like we lowered the price to $100 if you send us your old computer. So people were buying Sinclair's for $49, sending them to us to save $50 and that's of course 50 1980-dollars so this was - if you can see it through the microphone here - this was the one of the family that we called Ted and this was basically the Raspberry Pie of the day, it's all in there. The one chip does the video and the sound, and there's a processor.
Oh and the video sound chip runs all the D-RAM and does all the crazy interfaces to the keyboard. So it's literally like very close to a single chip board even though there was nine in the original - nine chips - yeah you cracked open an IBM PC and there was 280 something like that. That's crazy and even the 128, as big as that was, had a couple couple tens of chips in there. So and then Jack Turmel unfortunately left Commodore and this product I was showing, this Ted thing. Without him there to drive the vision, that product kind of failed and we even had a talking version. We had snagged the guys from TI Speak and Spell, which was a big thing in the 80s and we had them working at Commodore, so we had a talking version of a computer with a desktop that Apple tell you later they invented the desktop. Well no. The guys at PARC invented it but we had one, it was just our founder left and it floundered without the founder.
Crazy, okay show us the wire.
Okay, so then the 128. What happened was I had gone to a CES show and by the way CES shows drove everything for us, Consumer Electronics Shows, mostly cuz if you ask them if they'll move it a day so you can hit your schedule they'll say no, so the CES show is - this is a scheduled date you cannot miss - you can't miss it by five minutes, you can't miss it by a day and so we decided - and by we I mean the engineers, we didn't even really tell management about the C128 till it was too late and then we would do things to it. Like I added a z80 processor so it became - it's Commodore 64 compatible - so suddenly nobody's going to complain at me because there's no software, can run all the old software, but then turns out the z80 cartridge didn't work very well on the Commodore 64, so I just put the z80 right in the board and after the PC board Rev was done I said: oh by the way I added the z80, they knew they couldn't tell me to take it out now or we'll miss CES.
So then pretty soon the guy would be: I had a great idea to leave the z80 in there you're like, cool go tell marketing, take a doorstop with you right. So one of the things we did is, even as we're getting ready for the CES show - it was January 6th that year I think - we're already getting ready for FCC, so we're working on the final production and that's all in five months. I started this near August and we had six - five or six customized C's that needed to be done and so again that was our wheelhouse - this is custom, this is custom, this is custom, that - one of the other ones in here - and we're going like the wind right. Well right near the end, the z80 stopped working reliably. It wouldn't boot CPM 20% of the time, and me and my boss were fighting. It's bound to happen right, he'd already gotten his bonus I think to let me go around barefooted was like wearing thin right. But the - - oh, I lost my train of thought that almost never happens when you get old… [laughter]
You fought?
Oh I was fighting with the boss and he said: fine, I'll give it to somebody else to fix that problem! I said: fine, I'll take a shower and go home and get a nap! Right, so for a week, I mean I had a great week. I caught up on my hygiene, (I won't tell you some of the other things you do when you're full of testosterone when you're young). But he comes to my office Friday, and in my mind he puffed on his cigar (you could still smoke in the office back then). I don't know if he had a cigar that day, but that's my memory and he goes: fix it or you're fired. I'm, oh sure I can do that, you're ready now for me to rejoin the workforce?
Absolutely, I'm clean, I get along with people, and I just happen to luck out where I'm - the oscilloscopes of the day weren't like the Tektronix MSO scopes - like I got back there, I had to turn it up real bright, and then I would stare at it and then turn and look at a wall and I would see the reverse image and I go: there's a glitch right there - I'm pointing at it so someone can see it because he hasn't burned his retinas staring into the light - and they think I'm nuts, and I was right. There was a glitch on this A10 line, when the z80 was the processor, but when the 6502 was the processor there's no glitch. I mean it's right around when the D Rams were doing something and so it comes down to understanding how a signal propagates down and this is part of PC board layout right.
And I liken it to when the 6502 was driving the length of the line that drove it all the way to the end, like playing a flute correctly, but when the z80 drove it from an extension down the line it was like blowing into one of the holes on the flute and it's kind of not - and so I got a standing wave, where the wave’s going back and forth and bouncing into itself and it just happened to do it on A10 at the wrong time and I caught it on the scope in an hour. Of course nobody believes me right, so and the way I made it work, was I took that wire that I showed you that's redundant. There's already a trace on the PC board, I just soldered this again so now it's actually a loop right it can't bounce - -
Ah it had a return path, okay.
Yeah or propagates like this, but either way it's not a standing wave anymore at a certain spot, and it just happened to be that spot was the multiplexer for the D-RAMs and they think I'm nuts right because not only do I fix it an hour, I fixed it with a wire! So we ran 10,000 units to prove that Herd's gone off the deep end and we got a hundred percent pass rate on it. It actually fixed the problem. So now the wire drives me nuts because there's 5.7 million wires out there and people said: why didn't you just change the PC board? It's like: because actually I found it this time, if there were no tools to do anything, if I change the PC board I might have moved a glitch to somewhere I can't find right. So the devil you know - and that's how it ended up going out.
That's crazy - and from by the way - having a background in EMS. For an EMS provider, to have to put a wire on five million boards, that's crazy nobody would do that today but it's cool!
We called it post solder assembly and it's horribly expensive that's five point seven million dollars. It probably cost $1, the wire was a penny and 99 cents to put it on there, so we just did that. There was one other fun issue with the schedule of the 128.
Okay.
At one point - and see we didn't have real deep analyzers and stuff - so when the processor goes flying off the tracks because the memory is corrupted you'd go, well when in the last two minutes or two million cycles did the corruption occur? Because the analyzer's not going to catch it, unless you're so lucky right. So one of the things I noticed is, it would corrupt in the video memory and the video's memory is being scanned 15,000 times, 60 cycles a second and so I took a light pin and I put it on this spot on the screen right where the corruption would occur and I sent my analyzer, so soon as the spot on the screen occurred the light pen triggered my analyzer. And it's actually a commodore light pin - I still have it - was actually plugged into the joystick port of the system on troubleshooting and it turns out - it was called ground lift, and you're probably familiar with that. There was a stub of a little over an eighth of an inch on the ground pin of a DRAM multiplexer, and it's inductance mixed with the capacitance meant it would come off of ground when you went to switch a whole bunch of zeros to a one - except for one - that other one became a one also it just dragged everything with it.
Oh, got it.
Yeah and I also took - literally another little piece of wire - fixed it and then I yelled at Fish to fix. That one I made him fix but the only way we could catch it in that case, is I used a light pin to catch this little 1/8 inch piece of trace that was just playing with me.
Well you know what I love about these stories Bill, is that I think it's lovely to tell them and show people what a Wild West it was and how we solved, but people like you solved things really simply because now we sit on all these really complex tools and really we stand on the shoulders of people like you right, who were innovating back in the day where we did not have the complexity of tools or things and it's easy to take those things for granted now because so much can just run in the background and you so I think it's fascinating to hear these really - like these MacGyver ways that you figured out how to fix it - you're like the original PCB design MacGyver dude.
So one other quick story and it goes right to that - about the tools and the software simulations and things and it's the day I knew I was working in the right place. And this isn't my story - this actually is the chip designer stories for the Ted, for that thing I showed you. They had design roll checks when they laid out an ICs that told him if two things got too close to each other, but they didn't have an electrical rule check to tell 'em if it's supposed to be shorted together or not, so they turned a corner. They had like A7, A8 and A9 cut right across the other to address lines and it shorted 'em out, and they had no way to check that - unless they hand looked at every plot of every layer of what made up an integrated circuit. Well they - meanwhile cost a quarter million dollars to do another run. So what they did - I'm in the hardware lab, and the guy goes: okay turn on that - turn on the microscope light. Okay turn it off - good we're in NTSC mode. And I turn and I look and I'm like: did you just flip the status of a register with photons while looking at it under the microscope? And he goes: yeah uh huh, and I'm like: AH I'm in the right place, this is where I wanna be!
Yeah and they didn't have the tools that told them if what was on the schematics, what made it onto the chip. So yeah and they would spend five months, with a ruler actually called a scale, checking the plot. That's the only way they could do it.
That's amazing well thank you for sharing this - unfortunately we're running out of time. But thank you so much for sharing your history and your ingenuity and the stories of Commodore and giving our listeners really some practical ways of just jumping into a new tool, if they have to right, nobody likes change but I'm sure you would attest to that overall has probably helped you become a better designer to go ahead and jump in and you could probably jump into a new tool easily now it probably doesn't freak you out as much as it used to.
If you know you're going to be overwhelmed, then you're right on schedule when you get overwhelmed - and then you just go back into it and you know, how do you eat an elephant? A bite at a time - same thing.
Just acceptance that it's going to be frustrating and this is the cycle.
Yeah that you'll screw it up and then fix it, just don't ruin your libraries in the process.
Okay, well some good, good wisdom. So thank you again Bill for your time, it's been a delight to hear about everything and I just by the way - best background - those of you listening, you really need to go look at the YouTube version of this, because his lab looks like you'd all want to go live in it man it looks like there's everything in there it's awesome. What's up with the penguin by the way? There's a penguin, that looks like it's standing on your shoulders?
On the telly, it used to be on top of the oscilloscope but now it's just with you so that's that's a Monty Python penguin, that's from our era right?
Totally, that is so funny!
Okay, well thank you again for joining myself and Bill Herd today on Altium's OnTrack podcast. I'll make sure to share all of his colorful links and Wikipedia and videos from Hackaday and thanks for joining us again. We'll see you next time - until then remember to always stay on track.
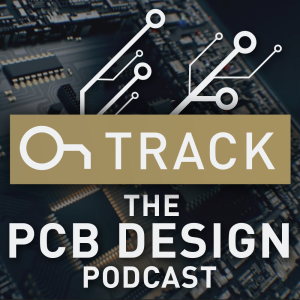
Tuesday Jun 19, 2018
John Watson, Senior PCB Designer at Legrand North America on Altium Nexus
Tuesday Jun 19, 2018
Tuesday Jun 19, 2018
John Watson and his team of 50 PCB designers at Legrand are beta partners in using Altium Nexus, the new Altium solution that takes Altium Designer and pumps it up with a healthy dose of project management capabilities. Find out why John is more excited about Altium Nexus than Altium Designer 18, and how he and his team have combat rogue libraries to tighten process and improve quality.
Show Highlights:
- Defining Your Design Process: What?, How?, Why?
- 5 mil boards was once amazing but now… old news
- Getting Parts You Can Trust
- Project Management in Altium Nexus - Streamlining and auditing processes
- Increasing the reliability of the design.
- LeGrand closes the loop - did we accomplish the why and what?
- AltiumLive is where you rub shoulders with leaders in the industry; 2 days of great learning.
- Passing the Torch - There is a concern that there are more jobs than there are designers.
Links and Resources:
Fundamentals of RF/Microwave PCBs
PCB Design: Prototyping and the PCB Design Flow (National Instruments White Paper)
Favourite White Papers
Top 10 DFM Problems That Affect Every Design
Adopting Signal Integrity In Your High Speed Design Process
Best PCB Design Books:
Printed Circuit Handbook by Coombs & Holden
High Speed Digital Designs: A Handbook of Black Magic by Howard Johnson and Martin Graham
Find all Episodes at: https://resources.altium.com/altium-podcast
Hi everyone this is Judy Warner with the OnTrack Podcast. Thanks for joining us again. Today we are here at the La Jolla headquarters of Altium and I have with me, John Watson of Legrand and we're going to have a great talk today about, just design in general, and then some of his vast experience.
Before we get going though, I'd like to invite you to connect with me on LinkedIn, @AltiumJudy on Twitter and Altium is also on Facebook, LinkedIn and Twitter. So if you are listening on the podcast be also aware that we record simultaneously on video. So, if you want to see our beautiful faces you can always tune into Altium's YouTube channel and click under videos, and you'll find that we are recording here in-office, which is a rare treat because we do this a lot on Skype.
So John, welcome to the office.
Thank you, thank you for having me. It's a pleasure being here.
Yeah thanks for joining. So, why don't you start by sharing with our listeners and watchers about what you do at Legrand, and because you really have kind of a wide... you do a lot! I don't know how you, if you have any time at home ever?
No, no I don't. No I'm the senior PCB engineer for Legrand, and we are a conglomerate of several divisions of what's called the building control systems and these divisions could basically go around the world; and in each one of these divisions we have designers, PCB designers and librarians and people who work on schematics and everything else. So I'm responsible for that, I'm the Administrator also, responsible for kind of mentoring them and training them, answering any other questions that they may have that come up. So we also then make sure that we constantly have the PCB designs that we're working on moving, flowing through there, so that's basically what I do.
Well, what I thought we'd talk about today, based on our recent conversation is, you kind of drill down to sort of the basics of designs - now tell us about how many designers you have overall at Legrand?
We have about 50 right now, 50 designers and a lot of those are, some of those are in Asia and the rest are in America here.
Okay so you started talking yesterday or... yeah it was just yesterday, we spoke right?
Yes.
You kind of talked about what I will call the why, what, how and when.
So, I thought that was an interesting way to sort of distill down the design process, but can you start talking us through that. Kind of start with the why and the what?
Yeah, I think as designers we'd love to jump into the how, we'd love to: give me the schematic and let me dive into the PCB, let me start laying copper down.
Yeah, but we we never get back to taking a step and really what has brought this on has been your new Nexus system with your design processes and your design flow charts that you guys have created. It's really caused us as a company, to take a step back and and ask, first off, ask the question: what are we doing? It may sound simplistic but the what is a direction pointer, it's an objective, it's the goal that you put up there and a lot of times it's kind of skimmed over...
In designing, because we want to get to the how, we want to get to - we want to get to the interactive routing part of this you know. And all the exciting tools that we can use and all this and that, but we never take a step back and determine are we pointed in the right direction?
Are we accomplishing what we want to start with?
So, and I would actually take what we do is, we actually take it a step further back and we ask why are we doing this?
The why is the foundation, the why is the motivation of why we're doing this.
Because what we have seen - what I've seen in PCB design - now I've been in this for about 20 years and what I've seen is that we actually, have different parameters - people look at PCB design differently. In the company, somebody for example the PCB designer, looks at a design and he's looking at: okay, here's my schematic, here's my PCB, here's my trace routing and everything else, you know. The part procurement people; they're concerned about okay, is this part even available?
How do we buy this part? How do we buy this component? How do we do this ? Then you have upper-management who looks and says how quickly can we get this thing to market.
That's their concern, they're not concerned about the routing. The, designer gets into the details and he's all, yeah look at that I'm doing the... doing differential pairs!
Yeah whatever, when do I get it back? [laughter]
Exactly, the upper management people, they're actually sitting there going, oh we really don't care. Does it work? When can we get this to market? I've had been asked that question several times by Vice Presidents of companies and things like that, and you say in interviews, they go: we have such a terrible lead time in our designs from concept to market and by the time we get this whole thing through the process we're gone... the market is gone.
So, one of their major concerns is, how do we speed this whole process up?
And one of the things that I've always pushed on, is the best way to do that, and accomplish it is, first off, know why you're doing something. What are you doing that gets you pointed in the right direction and how are you gonna do it?
And that then brings in the how. And and once you get that established, then you can start talking about how we're gonna do this.
And what tools we're going to use and those things are not major in any way just sit down, in one sentence, what do you do?
Right. Because I think, what struck me when you said that it's like well, yeah of course but sometimes we breeze over that because we're all making assumptions but I think, what you're saying is, five different people could be making five different assumptions and they're assuming they're all on the same page.
Right, exactly.
So unless you spell that out up front...
You're right.
-And the direction is clear, it can get messy real quick.
Right, and as I said, what has really brought this on has been the Nexus system.
So, I should mention to our listeners and watchers that, John and Legrand were part of our Beta group for Nexus, so they have been really instrumental in working with us giving us great feedback and also really showing us, instructing us, as much as we're instructing you I think.
Oh yeah.
It's been a real strong partnership, so he's way down the road from most people that are just starting to onboard Nexus now.
So we're very excited - I'm actually more excited about Nexus than I am Altium 18, and Altium 18 I tell you, you guys knocked it out of the park. I'm actually more excited about Nexus because this, this is beyond PCB design, you guys have taken this now beyond the PCB. You've taken it into the Project Management area. You've taken this whole design process, and I have project managers now, that have seen the Nexus system and they go: we can use that, we can use that process. The project managers now can look at the process, see whatever area that they're concerned with, they can now look at that process and understand where it's at. So you guys have now taken the whole PCB design process and kind of put it on it's head and you, you've caused me at least, to rethink this whole process.
Which is really exciting to hear from somebody who's been laying out boards and even instructing other people how to lay out boards for 20 years.
Yeah.
So that's exciting to hear.
It's very exciting, but I think this would work in any situation to understand what you're doing and how you're going to do it and having a clear plan is going to be vital. Especially with the environment we live in today, I mean especially with the whole electronic industry and where it's headed.
Yeah well, it's gotten so complex that it's hard to get your head around it sometimes.
Oh it is always...
I mean, and any one part of that, the design process is incredibly complex, the manufacturing, sourcing parts is incredibly complex and shifting all the time, and nothing's static.
Right so it's like you're shooting at a target that's moving all the time, and you're trying to get you know... what do you call that - a bull's-eye.
Right, exactly I remember, several years ago, about four or five years ago, when I was sitting at PCB West and people were amazed about how they were now going to be able to do five mill traces on boards!
You know, and it was supposed to...people were gasping, oh that's amazing you know?
And now that's old technology. Think about that.
It's just stunning.
It is, it’s absolutely stunning, but it tells you, it tells you not where we've been, but where we're heading. What's the industry going to look like in five more years? What's the industry going to look like in ten years, and it's exciting, it's an exciting time to be a part of this.
I agree it is an exciting time and I think that those of us in the electronics industry that’s part of what motivates us is, is the excitement right?
Yes exactly.
And being on that forefront like seeing what is next right, and what can we do. Yesterday you talked to us about the Item Manager, would you touch on that slightly and how that sort of impacted your own design process?
Yes, one of the important parts for us was when I first started at Legrand, we had various designers who were using various libraries but the bigger the organization the worst that can be.
The harder it is right, it becomes much, much more difficult the bigger a company becomes. But it also brings in a lot of risk with the PCB design, when what I would call 'rogue libraries' are used and you know, when someone creates their own library or things like that - and we had a lot of libraries...
Like how many, how many designers how many libraries we talking about?
We had about, at that time, we had probably thirty designers and we probably had over 900 libraries that were total and our library set and Item Manager is a great tool that you guys have placed into Altium, that allows me to look at a design, and look at the sourcing for those parts for those individual components and what it does, is it identifies whether a part is what you guys call managed or unmanaged.
So a managed part would be an example of a part that is under the vault system, or under a specific library. We specifically use the vault system.
And what it does is, it tells me where the part came from, whether it's managed or unmanaged first off, and where it came from. And then, if that part is managed, it then tells me what the life cycle is. It tells me if there's been updates done on the part, or whether there's new a new part for that in the library so it will say that the part is out of date or needs to be updated.
Okay.
Okay so, and then you simply go through a small process to update those components in that design. But we use it a lot too when we are bringing in a new design and we're comparing it and we're starting with the design review process, we want to know where those parts came from.
So that's our first question, is we say, ok where are these parts from? So it tells us managed and unmanaged parts. And then we want to know, if those parts are managed, are they up to date with our library?
So then we use that a lot - the item manager is probably one of the biggest tools we use, because that tells us exactly where the design is at.
So you're ensuring them that you have the most current revision of any given part, at any time so that's what you said kind of like the risk mitigation or increasing the reliability right of the design?
Exactly.
Before you actually make the board?
You don't want to get to that point. Yeah I was saying yesterday about, we've all been in this industry any period of time. You've put all the work into a fabrication and you play your part down and you get everything nice and shiny and everything else and and then you create your Gerber set and you send it out to a fab house and the fab house builds the boards you know. Then they go over to the assembly house, and you're sitting there and your phone starts ringing like, I'm sorry but the part that you gave us doesn't fit on your board okay, and you have to make that, what I call the long walk to the manager's office, where he then has to toe it you know, you just have to tell him: excuse me but we just spent so much money on this project we spent three months on this, and we have... it's the boards are useless we can't build the boards and we've all been there I mean...
It happens to everyone and that speaks not to the ineptitude of the designer but the complexity of the process and the craziness of managing component libraries and keeping that up to date because the data is fluid and rolling all the time, and parts are coming in and out of the supply chain and it's a very difficult thing to track.
It's a very difficult thing to track, but what we try to do is where there are steps that can be taken to definitely lower the risk of that situation.
So you told a story yesterday which made me laugh but also, made me gasp at the same time. So why don't you - you know what I'm talking about right, about the weekend - so why don't you share that story, and sort of what got you to that place of, coming from a place when you had all those designers and hundreds of libraries, and discovering that when you did a root cause analysis that most of the problems were either from footprint problems or component problems and then you did what about it?
Well what we did was you know this, I'm the sort of person as you know, it's a little thing called baptism of fire I guess we'll call it, but we had so many libraries in our system and people were using their own libraries and different tools that they had developed. I mean, they were setting up their own things so we had about over 1,200 libraries at that time, and when we ran things through the Item Manager, we would see 'Joe's library.' Well, Joe we need to have a chat. Yeah Joe, that's not going to work anymore. I mean, we need to because we had to centralize, that was the biggest problem, we had people that had rogue libraries and they were causing problems, failures, they were costing the company money.
Right, which back to your point is when the manager’s agenda is to say; if we miss our window time-to-market heads will roll okay, so you drilled down and said: okay what's causing that?
Yes.
And you're like... rogue libraries?
Rogue libraries, and what we did was after work on a Friday evening after everyone had left I basically went in and deleted all the libraries, so that was an interesting Monday morning.
I would've liked to be a fly on the wall that Monday morning did you show up for work on Monday?
Yes I did, because I was going to be there because basically it had to be done. The integrity of a PCB design which means that we try to put out the highest quality board that we can put out the very first time - we don't have time to do four, five, six spins of this the very first time, how do we have a high integrity board? Well number one is our libraries - I want all designers pulling a single part from a single library, that has a single footprint, a single sourcing and everything was in line and everything was correct, and that was how we began to basically rebuild our libraries.
Right, and that is, at that time is that when you were onboarding Vault, or you had vault but just all these rogue libraries?
All the rogue libraries yeah.
So you just we shut them off and said, there's one place you can get components.
Right exactly, and that was our whole purpose for getting the vault system was a single library source, that was it.
Tell us a little bit, we had talked several months ago, and I was really impressed with your whole vetting system really, that you've built internally of making sure. How do you make sure that the parts that you're putting in the vault are known, good parts and that they're verified and that they're up to date?
Right, well what we do is we, first off in the part itself, we follow IPC standard for our part creation we use the IPC 7351 and the IPC standards are our guideline for creating parts, and what we have now done is, because of Altium's sourcing capabilities now, we're able now to see sourcing. One of the greatest features that I have now looked at with Altium 18, has been your active BOM feature. The ability to take a BOM and throw it out there to all the vendors and suppliers and get feedback from them to determine what is the quality, what is the probability of this part, and we've actually taken several of our boards that are in production right now, through this active BOM process and what we got back was, we would get red flags on components. We would get notices like this part is end of life.
And on active parts that you're building?
That we're building.
Oh boy.
So we would get, you know, red flags stating ok, this part is the end of life, this part is not recommended for new designs, this part is obsolete and it was a situation where that was the information we needed really.
That gives us the red flags, not at the end of the project, not after the fabrication's there, not after the assemblies' done or started and after it's gone to the customer especially, it tells us at the beginning, the very first day when our schematic is complete we run it through the active BOM feature and we get the red flags, because a lot of times, what designers do is, they will either copy a design from a previous design or they will simply lay down a part. All right, that's their job, that's the double E's responsibility. What has happened now, is we have been given the ability and the tools to make sure that we are using good parts. So if I run a board now, through the active active BOM feature and it gives me a red flag, saying this is not the best part, this is not recommended for new designs, then I can go back to the EE now; and I can say, you know what we should consider not using this.
Preemptively and proactively, before you're to the expensive part...
Exactly yes, and so that now, we're able to constantly keep our sourcing information up to date so that we know exactly who we're buying the part from. And then also whether that part is deprecating in the lifecycle.
So how many parts are is Legrand managing inside of your vault in your library now?
Right now we have about 5,000 6,000 parts.
And how do you... so using the active BOM is one; but didn't you tell me that you have a system of verification before things go in or out, come out your vault?
Yeah.
Just an internal process?
It's an internal process that when anybody creates a new part it's given a life cycle of 'new' so that tells us it's a new part and what we then do, is we very go through and verify it, a verification process of that part. We'll pull up the data sheet, we'll verify the footprint, we'll verify the 3D model, the schematic symbol of course, and everything else and before then we can change the lifecycle to 'released', to where it's now available. So we make sure that, this is one of the features, also on Item Manager, it will tell you if the component lifecycle is new or if it's in a release state. So we can actually see: oh that part hasn't been verified yet, so we can then go in and make sure that everything's perfectly okay with it.
How nice, by the way, to have that clean of a library. like I think that's really rare, I don't think that's something everybody could boast about. I don't know, maybe I don't know.
Oh I wouldn't say it's too clean, it's a effort it's a constant...
Well yeah I'm sure it's something you have to continually manage?
Yeah you constantly have to manage it, you constantly have to keep a look at and watch after it, a lot of times we have components that pop up there and they just don't match - nothing matches on the datasheet or anything and they easily get deleted. So we try to keep in control of that.
So, you'd mentioned to me about, that in your multiple locations, you have three different PLM systems too?
Yeah.
How does that come into play?
Well we have different divisions, and each one of those; some of those have different PLM systems, and they also have different numbering systems for the part. So for example, you can have like a 1K resistor, 805 resistor, that you have in your library. Well for us there's - for one division - it's one part number, for another division it's another part number, and for another division it could be another part number. So what we did was, we actually set up parameters inside of that part. We set up, what's called a CPN, a Company Part Number, so we then set up a list of company part numbers that we would use for that single item, so we could put in there then, all the different part numbers. So whenever anyone lays that part down, they're also laying down all the information for that part. So all the information, for whatever division is going to use it, so it makes it very handy to then integrate the whole process.
So now that you've got this centralized and cleaned up and nobody wants to kill you anymore for deleting their parts - tell us how the overall, now kind of backing the camera up here, what's the overall effect that it's had actually on your quality your time to market, you know, the role of sanitization. What has that done for you guys really, as a company?
It's really helped to streamline the whole process because once we're starting with good information from the library, then we can talk now; what we're talking about is how are we going to streamline - how we're going to standardize our process, how we - we want to make sure that all the designers are first off, they're starting off from the same sheet, they're starting off at the same location, so they're all working from the same library. They're working from the same templates now, and they're working from the same guidelines, procedures, things like that. So what has helped is it's streamlined. Basically taking a design through different divisions and it can be handed off from division to division and it can just be carried, and continue to be worked on.
Without the disconnect.
Without a disconnect without - except for a couple of people - I'll tell you...
[laughter]
There's always those couple people.
Yeah there's always a couple people. I have to tell you that there's the one person in particular he, what he does is, the convention is, in Altium, is that the component layer is red, and the solder side is blue, well what he does is he'll go and he'll swap those.
Just to mess with your head.
[laughter]
Just to mess with my head right. So but it's - other than that, once it's done, is it's called us to streamline the process, so now with the Nexus system coming in, we are going to be bringing that online, with the Nexus system coming online, we are now looking deeper at our processes, looking further about our process, and I'm kind of looking at it in the way of where, if you have a set process and you have a set group of people, a team that is responsible for certain tasks, then we can actually have milestone setups in our process where we simply say, at this gate keeping item, or this moment of our process, we want to do for example, a design review-
Oh like an audit...
-of an audit, of where the design is at and then also, we can assign people specific tasks in that process. So basically, we can go from there into then checklist... we say, ok we give a checklist to an individual that says check one, two, three, and four is it correct?
So what we're looking now at, is streamlining our entire design review process, looking at decreasing our time to market, decreasing the time that that board is in design, and the Nexus system is going to definitely be a major part of that whole process. Because with that then, we're able to go into web reviews, which we're very excited about doing. Being able to do web reviews and have people actually go onto a website to look at this, they don't need to have Altium installed and go through the licensing and all this and that, they just get the email and the link, and they go in, review documents. So that's really exciting for us, but we're actually seeing a quicker time to market we're seeing better, improved boards, and it's really helped us also to do a self-audit which means that when we do a fabrication of a board for example, and we then go into assembly, what we then do is, we do a DFM we do a design for manufacturing review. We then look at the board and say, okay now what was the design flaws here?
What was then - we also do a build review - from an assembly house they come back with a report that says, oh we had this, and this, and this issue. Okay so now, what we're able to do is that drives the design from there, then we look back at our libraries, whether we need to improve our footprints, or do we need to improve in some way, our process. Or we look at the specific layout, or we look at component problems and such like a build review, then we can look at our design review checklist.
So it's like, it sounds like an ongoing real-time, optimization of your entire process.
Yeah. Whenever you begin a process and you go out and you do that process, we're closing the circle. We bring it back to the beginning: say, did we accomplish what we started out to do right? We talk about how we, talked about it at the beginning, 'why' and 'how' or we talked about 'why' and 'what'.
Well at the very back end it gets looped back there did we accomplish, why, what we were doing? Because I'll tell you, a lot of times, we can start a project and we can - and we just kind of go down the primrose path of design and we never get to what we were accomplishing.
Right that can't happen.
And and we never get to it, we never accomplish it, and a lot of times those sort of designs and those sort of PCB just kind of die by the wayside. That was fun, that was a nice fun project.
Now let's go do another one!
Let's do another yeah. But I always said, I've always told the designers that I work with, I said: look you do not get paid for designing, you don't get paid for designing. This company is in business for one thing, and it's not to pay you to be a designer. It's a company, we’re in the manufacturing field now, not maybe in a service area, but in manufacturing. You're here designing because you're building something that ultimately needs to be put on a shelf somewhere and someone needs to buy. We're here to sell stuff and a lot of times we lose sight of that - we lose sight of the fact that, oh well this is a nice fun project, but do we ever accomplish what we started out to do?
So what we try to do is, we're definitely trying to constantly improve our process, and constantly improving our designs and things like that, and I think that's done through our review process and looking at the very forefront of what what are we accomplishing? Did we do it? How well did we do it you know?
And where did we maybe fall down and how can we improve that. Here at Altium internally, we call that a post mortem. We've set up a process we said, well we're gonna go through it and then when it's done, we come back and we do what's known, sort of in the marketplace, as a post mortem and go, well how did that go? Did we do what we set out to do at the beginning you know, so it's very much the same of what you're talking about.
Yes.
Because if you don't come back and do that check, you could be left to center by the time you get to the end but you're like, oh that looks good, it works yeah, and you miss the target, but it's together, and it's functional. But you missed the mark right.
So it's not a board of high quality, you got 98%, you missed that 2%. I'm actually concerned about the 2%, how can we improve the process, how can we make this quicker, how can we better this?
Right well it's...I'm just in awe of the work you do actually John and I never get tired of hearing you talk about it because it's it's refreshing, and you've got a big team and it's a complex process but the discipline that you've brought to it is just, it's really impressive. So now I'd like to ask you about - is there anything else - first of all, that I missed that I asked you about..
I don't think so.
Okay, so now I want to just kind of put a microphone in front of your mouth and do a self-serving moment here, it's not really self-serving. But last October you were one of our speakers for Altium Live. And you had a lot of really positive things to say about that. I would like your honest input, because hopefully you'll be back again to speak at AltiumLive, I'd like you to encourage other designers, that maybe didn't have the chance to go. Tell them reasons why you found it valuable and so on and so forth. So if you would?
I - it was of course - it was the first one so, and it was phenomenal and I felt, when you first told me, I first heard of it I thought about AltiumLive, okay this is going to be a three-day or a two- day commercial regarding Altium 18 and you're going to sit there and just see the demos and you guys are just gonna pat each other on the back as designers, and everyone's gonna you know - but it didn't turn out to be that way, what happened was this was far more than just about Altium 18. This was about the design process, this was about designers, this was an opportunity for designers to rub shoulders with some phenomenal people and some of the leaders in the industry and this was just two days of, just great learning, to hear from experts, to hear from the people that are the leaders that's the only way I can really describe it.
They really are, I mean, the keynotes we had were thought leaders.
They were, they were phenomenal, just absolutely! Mr. Holden...
Yeah Happy Holden.
-was just phenomenal I've been reading one of his, my favorite books, it sits on my desk right now it's The Printed Circuit Handbook.
Isn't that a great book? This thick. Is that thick yeah. [gestures] But Happy doesn't ever sign up for anything that is short.
That's right.
Brevity is not his skill in life.
But it was a phenomenal time and I'm really looking forward to October I mean, to have it again, and I understand we're gonna add the one day?
We are gonna add the day on the front end because and we're doing that, again, we really are trying to make it all about people like you, and and not make it an Altium commercial because I think EDA tool companies in general have been absolutely guilty of putting on, what they call user conferences, but it's like, we're going to lock you in a room, and beat you over the head with our products - see if you'll buy some more stuff from us right. So we try to really focus on what do you guys want; what's the value to you, and again this is a complex world we swim in so let's just bring all the experts in, bring on this. And of course we did launch Altium 18 and we talked about Nexus there, but only you know, 45 minutes on day one; 45 minutes on day two - that's all, the rest of the time it was not us at all - it was about celebrating designers and the and the craft of design but when we did the exit surveys we asked.
What did you like, what you didn't like? And most of the feedback was largely good. But the one piece of feedback that people gave us is; gee I wish there was just a little bit more that was actually tool training, getting into some of the more advanced features that maybe during the workaday world, they don't have time to just sit down and learn and drill deep into some of the advanced features. So we've added a day on the front end that we're calling Altium University, and then we're gonna just do tracks all day, on the first day. And it's optional, you can go or not go, you know. If you're an expert and you don't need initial training, you don't have to go. But at least it's there and we've kept it out, so that we can kind of stay, design - somewhat design agnostic - on those other two days and really give you good depth and training and bringing in the experts, wait til you see, so far for AltiumLive - this is like breaking news right here, really you're the first to know...
Oh my goodness.
Okay, since you've been so generous with your time... so three keynote speakers that we have signed up right now is Eric Bogatin...
Oh right!
I bet you've read a few of his books, Rick Hartley, and then a young buck by the name of Jeremy Blum, who has worked at Google, went to Cornell; sharp Electrical Engineer and he's at a start-up now called Shaper and so he is like 'Forbes 30 under-30 Technologist', and he's like the startup whiz-bang kid. So that'll appeal, I think, to the younger designers and I haven't picked the fourth yet, but stay tuned - I'll keep one secret to myself. Those are three for San Diego. Dan Beeker will be joining us in Munich and I haven't decided yet, we're still working on the other ones in Munich, but it should be another great lineup of keynotes and I will put out a call for presentation soon so, and I've already inked you in, so.
Yes you have.
You don't get a vote.
I know, and you're probably gonna ink me into Munich also.
Good, good whatever we have to do to suck you in. So thank you for the AltiumLive commercial.
Right I would just add to that, I would just add to that, I would just say, that if you, if you're kind of sitting on the fence about going or not going. Go, you won't be sorry, you won't be sorry I can promise you that. It's definitely a great time; it's a learning experience, it's a time to rub shoulders, is a time to kind of get away from your job - kind of get away from all the hassles. For those of you who are going to be in the cold areas of the country, such as Montana in the middle of October, I would highly recommend you to come please, come to beautiful San Diego where it will be a chilly 72 degrees.
On Coronado Island with water on both sides of the hotel.
Exactly, so it's gonna be a great time, but above that, it's gonna be a great learning experience. It's going to be a great time to come learn and grow, I'm really a senior, not just in age, but also in this industry, and one of our concerns is, and one of the concerns that was brought up in PCB magazine, just last year; was how there's a mass exodus right now of PCB designers, and that there is a vacuum happening that there are now more jobs available than there are designers and that is not just a concern for me, it's also a challenge, a challenge to train and to teach the younger generation coming up. To teach them and train them about this whole thing. It's a phenomenal industry, it's a cutting-edge industry, but it's not something where somebody, you know, they grow up they're four or five years old; mommy when I grow up I want to be a PCB designer.
I know, I always say we all got here by accident, you know, it's like some windy road that landed us here.
I started off in my career as an Electronic Technician and I started in that route and finally got pulled into the PCB design area and I actually started off with Protel 98...
You are dating yourself.
Way back when, so and but it was phenomenal. It was it was a career that is now, is always changing and I love it, it's just... but I would highly encourage everyone to be there and to make sure that you come there to learn because that's the whole purpose of it. It's not going to be a three-day commercial for Altium, it is - this is about you - and what you need okay.
Thank you I'll give you your $20 bill later [laughter].
Check is in the mail...
Well you plugged that way more than I'd hoped for, so thank you for doing that. But I know you're a fan, and I appreciate it. The feedback you had was music to my ears because what we intended to deliver, you said we delivered so, yes that makes my heart sing and and being an - by the way - I won't give away this secret but I will put a little hook in you...
Either your age or your weight...
No neither one of those, no.
Before AltiumLive, or at AltiumLive when - I first want to say thank you - that you are one of the people in the industry that are training up the next generation through the people you're training out of the ground so I really appreciate how you personally contribute. But either before or at AltiumLive you will hear something very exciting from Altium about things we're gonna be doing. Extremely proactively, help grow up the PCB design community and in a way where they can go out and use any tool they want but we have an intention to help grow that next and we hope people will use Altium, but we're not...
Right, it's not required. That's good.
-so stay tuned.
I am really excited about that I mean, that's an exciting...
It's coming and I feel really privileged to be in the place I am because, like you, I have been around a little while and luckily Altium is a generous EDA company and they are allowing me to step in and do some of these things.
I thought your big announcement was AltiumLive, this year is going to be Altium 19.
Oh shocker, spoiler alert!
Altium 19! You heard it here first!
[laughter]
At least we're consistent.
We're consistent yeah. I'm glad you guys got, many years ago, you got away from that 2010-like the 2010 stage I don't know how many are still here, but you did the summer and the winter release. It was like a fashion show was like so...
Our summer line!
Your summer line versus your winter like
well then if we killed off teams of developers we decided to stop. Or they're like, why does it keep crashing? Maybe we should only do one release a year...
Just saying... no. Well thank you again, this has been a blast always great having you...
Thank you for having me.
-thanks for teaching us and being such a great contributor to the industry.
Well, we appreciate you, appreciate what you're doing.
Thank you.
Thank you again. This has been Judy Warner with the OnTrack podcast and my friend John Watson from Legrand. Please tune in again next time and until then remember to always stay on track.
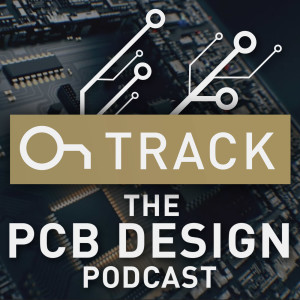
Tuesday Jun 12, 2018
Flex and Material Sets with Chris Hunrath
Tuesday Jun 12, 2018
Tuesday Jun 12, 2018
The rise in flex applications across all industries from medical to automotive, aerospace and military uses means more opportunity for material suppliers to innovate and meet demand. Here what industry expert Chris Hunrath has to share, from general guidelines for designing circuits unique for flex and materials that can be autoclaved over and over. Listen in to this week’s OnTrack expert to learn about flex and material sets.
Show Highlights:
- Medical applications (i.e. instruments for surgery), automotive, aerospace, military
- Foils - as you go thicker, its harder to make electrodeposited. More bend cycles out of rolled and yield
- General Guidelines for designing circuits unique for flex:
- In general, avoid circuits making turns or bends in bend/flex area - don’t make the circuits go in different directions there and also avoid plated holes in those areas.
- From a stackup standpoint, balance the construction. Thinner is usually better.
- Look for opportunities for cracking at the bend point.
- Cross hatch ground planes have multiple advantages.
- Pyralux HT, DuPont - new product with unbelievable thermal performance. A continuous operating temperature. Imagine a flex circuit that can be autoclaved over and over.
- We are a material sciences company. There are really unique ways to put these building blocks together.
Links and Resources:
See all the show notes
Hi everyone this is Judy Warner with the Altium OnTrack Podcast. Thanks again for joining us. Today we have another incredible subject matter expert that you'll be familiar with because we've had him here before, which is Chris Hunrath from Insulectro and we're going to talk about flex and material sets and all kinds of really great things. So hang tight for that. Before we get going please, I invite you to connect with me on LinkedIn, I share a lot of things there for designers and engineers and on Twitter I'm @AltiumJudy and Altium is on Facebook, Twitter and LinkedIn. Today Chris has some Show and Tell and so I encourage you if you - Chris will take time to describe what he's showing, but if you want to see it, feel free to go to our YouTube channel at Altium, click under videos and you'll see all our podcasts there. And you can click on this podcast and then you'll be able to visually see the materials and things that Chris is referring to today - and that's always available by the way - on YouTube so we record simultaneously in video and in audio so just know that's always an opportunity there for you.
So Chris, welcome back, thank you.
Thanks, Hi.
Thanks for joining again.
So at the end of last time's podcast, we were talking about the rise in flex applications and sort of the increasing amount of business actually Insulectro's doing around flex materials, new materials are going out so I really wanted to take this opportunity to learn about what is driving this uptick in flex, what applications are driving it , what the cost, performance implications of that is, and so let's just start with what is driving this uptick in flex?
So a lot of it's medical, you know, and the way electronics are finding their way into medical applications. Actually it's everything, it's automotive, it's aerospace military - military has always been a big user of flex, but of course you know, all the new inventions that are used in medical applications - certainly some devices are implantable and that's something that's not new, but then we're seeing a lot of applications where instruments are being created that are used, for surgeries and things and they use flex circuits and that's because you can make things very small which is always an advantage when it comes those applications and we're even seeing some applications where the products are reused. They're being sterilized, autoclaved, what have you and then they're being reused. But lots of new techniques, lots of new devices being developed using flex. Most people are familiar with traditional flex applications like your laptop screen, very often the interconnect between the main system and the screen is a flex circuit. You know the old flip phones all had flex circuits, your inkjet printers had a dynamic flex circuit between the printhead and the actual motherboard and the printer, and actually that's something I do want to point out is, you know we describe flex applications in two main buckets. One is dynamic flex and the other is the flex to install and it's just exactly what it sounds like is flex to install. Typically you're only bending the circuit once or twice to fit it in whatever it needs to go into and then that's it. Whereas dynamic flex, the part’s flexed in use many, many, many times.
I think that something that most people can relate to because you can see it, is the flex inside copy machines right, you can see that dynamic flex moving again and again and so are the materials - the entire circuitry is rated to have X amount of dynamic motions for the life of, it or how does that work?
Yeah actually that's a pretty good point and that can become very complex. A lot of it has to do with layer count, the base material. You know the most popular base material for flex circuits in reflow assembled PCB - a little different than printed electronics applications - where you're using conductive adhesive, but if you're doing reflow assembly, the most common material's polyimide film, and one of the most common materials is Kapton, but the thickness of the materials, the type of copper circuitry, the thickness of the copper foil - all those - play into a number of bend cycles even the type of copper, whether you use rolled annealed, which is very common in Flex, versus electron deposited-
Okay
-well that can get very complex. There are some good design guidelines out there by IPC and others you know. Again I always shout out to the board shops, some of them have good teams that help people choose the right construction, right stack up to get the most bend cycles out of the device.
Are those the two most common types of copper used in flex by the way Chris? Is a rolled anneal an electroless?
Oh it's electro- deposited.
I'm sorry electro-deposited okay.
Yeah - and yes but unless you're dealing with very thin foils rolled annealed is the most common. That's what we call 'RA foils' the most common. Actually I have a sample here. This is some Pyralux clad. You can't see the dielectric inside, but it's got rolled annealed copper on both sides and it can vary from - you used to be limited to half ounce or 18 micron and thicker so a little side note on foils: as you go thicker it's harder to make electro positive foils because it's more plating time on the drum. With rolled annealed it's the opposite, thinner foils are harder to manufacture because you need more rolling processes to make the foil thinner and thinner and thinner.
I see.
You used to be limited to 18 micron or half ounce, now we can get rolled annealed coppers thinner, down to 9 micron or quarter ounce. You can get a rolled annealed, but the structure is much better for flexing because the grain boundaries are in this direction platelet-type, overlapping grain boundaries which is better for bending. Any foil boundaries are like this and if you bend it you can cleave the grain boundaries in. You get more but it's not that easy - foil doesn't work and flex but you typically get more bend cycles out of rolled annealed.
Okay very good. That's something actually I didn't know and it's something I've talked to my friend Tara Dunn, who's in flex - and it's just something that's never come up so I think that's kind of an interesting point. So, you mentioned with military applications - because my background - military was always SWaP right, Size, Weight and Power - so are those the same type of things that drive the other applications - obviously in smaller spaces - we can fold things up on themselves and get them into smaller packaging. When you talk about the dynamic, what other kind of things sort of drive the desire and the fit for flex?
So something that's applicable to both military and medical, is you want to reduce the size, so I have here - this is a 50-ohm SMA coax right. It's basically one circuit, you've got the shield layer, the shielding around the center conductor - but this is one channel or one circuit and I have here flex, and you can see how many circuits you have on this piece. So, imagine if you had to have one of these - for each one of these-
For each channel right.
Now if you - depending on the design, whether it's strip line, micro strip, and whether or not you have in-plane shielding, it might be every other one's a signal. But still the weight and size is the difference between having cables right, which I'm holding up right now, versus having a flex circuit is huge right.
And in the case of medical, some of those traces can be as narrow as 20 micron. So you can fit a lot of circuitry into a very small space. And you know depending on the on the medical device. We see some of our customers will build circuits that are very, very long and very, very narrow, and you can imagine how they're used in surgery and other medical applications. And you might have twenty circuits on that part but it's in a very, very, very small space.
Oh that totally makes sense.
Now - just to be clear 20 micron circuitry - it’s not easy to do, it's doable, not easy to do, but certainly 50 microns is, most board shops can do that these days and again you can fit a lot of circuits in a small space and of course they can flex, they can bend. But in the case of rigid flex where you have a rigid part and bridged with a flex part - and here's another example where you have this - is not necessarily rigid flex but you'd have components here and then a connector here. You're replacing all these cables right, of this section, so that's how it drives weight and space and even reliability. Fewer interconnections tend to be more reliable so that really helps. So flex has been growing quite a bit for us, for our business and so, a lot of its based on DuPont Kapton and DuPont Pyralux products and then they - there's a B-stage system for laminating the different layers and of course the core, or the clad material as the foil on both sides and then our customers will print and etch to whatever pattern they need and put those layers together as building blocks.
Right so let's talk a little bit about design for flex since most folks listening here will be engineers or layout folks. What are some things that people need to keep in mind about designing these kind of circuits that's sort of unique to flex?
So there's a couple of good - again some good guides out there - both by IPC, DuPont has flex manuals, for different types of categories. Whether it's multi-layer, single sided, double-sided flex, they have some good guidelines on that, but in general what you want to avoid is you don't want circuits to make turns or bends in the bend area. So, for example, I'm going to use this one is an example again.
Okay.
If this is the flex area in this middle section here, you wouldn't have the circuits go in different directions in that area, so you might want to keep them. You want to keep them basically parallel in that area and you also don't want plated through holes in those areas. Again these are just real general rule - basic guidelines. The other thing you want to avoid is what we call an I-beam effect, where you have circuits directly above each other with a dielectric in between. You want to stagger them. That helps, again - more important for dynamic flex than bended, to install, but it's important not to have the I-beam effect because that could lead to cracks...
That makes sense.
-concentrates on bending. And in general from a stack up standpoint, you want to try and balance the construction. Thinner is typically better. There's again - there's all kinds of iterations there's - if it's a multi-layer flex - there's loose leaf constructions where you wouldn't necessarily bond the different layers together in the flex or bend region. You'd have them not connected. A bookbinder system is another way to do it where depending on the direction of the bend, the layers that are on the outside of the bend are actually longer. The layers on the inside - and again the fabricators that are skilled in that know how to space that - and to change the length of the circuit. But you know from a simpler standpoint, or from a more general standpoint thinner is typically better balanced. Balanced constructions are typically better for flex.
Well balanced construction is always a good idea, I'm just saying but I could see that right. Because I think you - what you're saying if I'm hearing you right, is you have to look for those opportunities for cracking right, or stressing at the bend radius, because that makes sense right. Just from a physics standpoint it makes sense that things would want to give or pull right?
Right, when you bend a flex circuit the other side compresses against it right, and every circuit will fail at some point. It's a matter of how many cycles you get out of it before it fails.
Right how do you measure those cycles by the way?
Well there are some standardized tests and there's an MIT bend test - there's some other testing that's done to see how a particular material, or even a design or stack up performs where it's bent repeatedly until you get failure. And then you can - you can rate the stack up or the and/or the material.
Where can you get that data? You mentioned IPC as a source. Is there any other thing - resources you could share - that I could share with the listeners where they could maybe look at some of these readings?
Yeah actually so DuPont's website, the Pyralux website, has some data on that and certainly some of the folks there could put your listeners in touch with some of the design guidelines.
Okay alright I know some folks there if you and I can't find him through the website then Jonathan just came in to talk at IPC designers Council Orange County I'll reach out to him see if...
Oh Jonathan Weldon, yeah he's a great resource for that. So speaking of Jonathan Weldon, he's been working with HDPUG; they've been looking at shield layers or for reference planes and they've been looking at the difference in solid planes and cross hatch systems, and so this is just a simple - this is actually a simple test circuit microstrip construction where you have a reference plane on one side and your tracer on the other. Imagine if there were a strip line construction and you had copper on both sides with your transmission line in the middle, one of the challenges with all PCBs, and especially with flex, is absorption of moisture and then that moisture released during assembly causing delamination and one of the things that you can do to mitigate that is to bake the parts. Well if you have soft solid copper areas - baking does not work as well - because the moisture has got to go around the copper it can't go through it.
Right.
So cross hatch ground planes are great for two purposes. One is, it's a moisture egress for baking, the other advantage is it's actually better for flexibility it makes the part more flexible.
Hmm, that makes sense.
The downside is the high frequency applications - you can run into some issues.
Yeah.
So and one of the interesting things that Jonathan and company, they were looking at, was the difference between a round opening and a - what's typically used as it's..
Kind of a diamond shape?
Exactly, exactly and really it's more of a square turned on its side, but yeah the diamond shape versus the you know... It's funny how a circuit design is always in orthogonal patterns but that's not necessarily the best way to go and anyway the round shape was better for signal performance.
Oh, for the high speed applications?
Yeah it makes sense because if you took a circle that fit inside a square you actually have less open area so...
This is true okay, alright.
Yeah, so there's some interesting data on that but I would recommend to a customer, depending on their their frequency bandwidth bit rate, depending on what kind of design it is, that they would look at using an open plane. It works basically with a screen, for lack of better words, versus a solid plane because the reliability goes way up.
Okay now you just made me think of something. Last time we talked, we were talking about prepregs and glass, being reinforced right. When you're using adhesive systems for flex, I'm assuming they're non-reinforced?
Right.
It's a more stable material though so tell us a little bit about that, about the stability, the dimensional stability?
Yeah so - so really in flex circuits the Kapton film, a polyImide film, because it's a thermoset, it is acting like the fiberglass in your flex circuit.
Okay.
You don't have skew issues because there's no glass, so you don't have micro-DK effects. Now if you do have a crosshatch plane, you will have a different - you'll have a micro impedance effect if you would. But that usually doesn't change with differential pairs unless - again depending on where you put the traces - but you don't have the fiberglass micro-DK effect at all. Now, Kapton's interesting - it's very thermally stable but it's not as mechanically strong as glass reinforced laminate. So it tends to change more from mechanical distortion than it does for thermal. It's not shrinking like epoxies do when they cure. Certainly when you - when you remove all the copper (and I actually have a piece here) this is a piece of Pyralux AP, with all the copper etched off. This is 100 percent polyimide, used to have copper cladding on it and the copper's been mostly etched off. You can see a little bit of copper left from the tape I use to run this through an etcher, but the material is pretty strong but it can distort mechanically, more so than thermally. So again this is kind of like the fiberglass in a regular PCB, and then you'd have B-stages of some sort, to put all the layers together.
So the actual substrate is creating the stability in the case of flex? Okay that makes sense.
It's a polyimide film, in the case of Pyralux, which is a DuPont branded flex material it's based on Kapton film.
Okay so we talked about ground planes, we talked about where to not put - - is there any other sort of design for flex things that you'd want to mention that are just rather commonplace?
Yeah so there's a lot of things, for example, you could use a pad that's a little bit larger than you would normally use that would go underneath the cover. Now let me backup a little bit and talk about cover lay. So what cover lay is, it's basically Kapton adhesive laminate, that is the flexible equivalent of solder mask. Now unlike solder mask which is used in PCB, which is photoimageable, cover lay has to be mechanically formed and then laminated over the circuitry. So you have openings and this - again this is a another good example - you have openings in the cover lay I don't know if you can see that on this? But there's openings on the cover lay for each individual pad and then that's laminated over. One of the ways to get more reliability out of the pads is to make the pad a little bit bigger than the opening in the cover lay. So you have cover lay over the perimeter of the pad - it's kind of like what we call solder mask defined pad and rigid - except you're doing it in flex, and that's that's one way to get reliability. But there - again there are a lot of different things in flex that you should be aware of, and that's where some of these design guides and things...
Okay well we'll try to track some of those down and put those in the show notes because I think that would be really helpful to have something kind of, tangible. Something I remember learning from someone else, is also talking about tear dropping pads?
Yes. Is that something that you would recommend as well?
Yeah that's good for a couple of different reasons. One is that the more material that goes under the cover lay, again helps mechanically support the pad. It's also important - typically you don't put holes or pads into your bend area, but it could be an area where you could concentrate bending. So in other words, you go from a trace to a pad, that's going to become a concentration of - right at the edge of the pad - concentration of stress and so if you do the teardrop, that distributes that stress over a larger area and helps prevent circuit cracking. But again, you would try and avoid that in your design. We would make that a bend area. And actually, speaking of rigid flex, one of the things that you would typically do is the cover lay would go into the rigid portion only 50 mils.
Okay.
-Okay and then you would keep the cover lay and its adhesive out of the plate through hole areas in the rigid portion and rigid flex - and that's also a 'keep out' region for plated through hole so you wouldn't want plate through holes going through that region. So again a lot of this stuff is spelled out in some of the manuals that you get from DuPont and others.
Alright, I'll reach out to Jonathan and - and you and I can scrounge up some things and we'll make sure to include those here. Last thing I wanted to talk to you about - which I was just stunned by - is that you told me that DuPont has come out with a new material that has unbelievable thermal performance. Can you tell us a little bit about that?
Yeah so - classically in flex, you have your your B-stage, or adhesives that are part of the package, and then you have your core materials, which are your building blocks and you print and etch your core, just like rigid, and you would have - you would put them together with either your rigid or your flex adhesives to make a multi-layer system. What's different about this new product, it's called Pyralux HT, and in fact, I got my Pyralux HT mug here...
Nice, nice.
-but instead of using acrylic or epoxy adhesives to bond the Kapton layers together, you would use this thermoplastic polyimide layer. It's got a very high melting point and thermoplastic's already used in PCB, people familiar with EPI-P and LC, those systems. The only way thermoplastics work in PCB, or reflow assembled PCB, is to have a high melting point otherwise it would melt at assembly. So this is a piece of the thermoplastic polyimide that DuPont manufacturers. It's the HT bonding film. This could either be a cover lay or it could be an adhesive layer to put - to make a multi-layer PCB.
Okay.
-But the nice thing about this, is it has a - 225 Celsius operating temperature, which is very, very high.
What does that convert to in Fahrenheit?
Oh gosh - 225 C it's over 400 degrees Fahrenheit.
I see, 225 - - Fahrenheit okay I wasn't hearing you correctly, so it was Fahrenheit okay.
Oh no - hang on, 225 C, I should know all this without me - - 437 Fahrenheit.
Wow.
So you know, some applications...
-and that's an operating - continuous operating temperature? Which is crazy, cuz some materials can take that heat for a little while but not continuing operating temperature right?
Right, so most PCB materials that go through a reflow assembly, which is either done at 260 Celsius, depending on the type of solder work, or 288 C, they can withstand that for a short period of time most PCB materials survive that. It's the operating temperature most epoxy systems will come in around 130 to 150 C operating temperature - maximum operating temperature.
That's wild, so I'm guessing - so what are the applications where this will be exciting news?
So applications where you had, fiberglass, coax or some other applications like that where you had wired - high temperature wired connections - or cable connections, you could replace now with a printed circuit board. So engine compartments, aircraft engine compartments, aerospace, down hole, I mean there are a lot of different applications. Even from a medical standpoint. Imagine making a flex circuit that could be auto plated over and over and over again. You don't have to worry what's gonna...
I was gonna ask you about that earlier. I don't really know what temps they autoclave at but you mentioned that before that medical applications could - to cut autoclave to kill the bacteria, but like what's the normal temp of an autoclave, how many times can you do that?
So we have one customer that builds some parts that are autoclaved at 135 C but it's with steam, and it's hard on circuits, it's hard on electronics.
Yeah seems like that would be.
But for HT it wouldn't be any issue because you're nowhere near on the melting point. Now it will absorb some moisture, which could be removed from - could be removed with a bake but a lot of applications it won't matter if the assembly is already done. It doesn't really matter.
Okay.
You know there is some change in the transmission properties of the material when it absorbs some moisture. Again that could be removed with a bake but that is one of the challenges with reusable medical devices, is sterilization and how well the materials hold up, and an HT would be good for that. The downside of HT, is it does require a 600 degree lamination - Fahrenheit.
Okay well there you go, so how many board shops have lam presses that go up to that temp?
So we took a look at our customer base, and it's not a lot of them, or some of our customers had laminate, or have lamination presses that are capable, they're rated that high, but they haven't been turned up that high for a long, long time. So it's funny, some of our customers have started making some HT, all the weaker heaters, that the press might be 10 years old, they turn it up for the first time to a higher temperature; they start popping heaters and they have to go and replace them. But actually we're seeing a trend though. A lot of our customers are buying laminating equipment and right now that's a whole 'nother story because lean times are way out on equipment in general, but what we're seeing is people are making sure they have that high temperature capability and it's not just for something like HT, it's for LCP and FEP as well.
Okay.
They have some good properties, electrical and and signal properties.
They do.
That's a big deal these days.
Performance wise they're very good.
Right they're harder to fabricate but they do have some good properties you know. Even - we talked about last time - repeat glass-reinforced PTFE materials, some of them require high lamination temperatures.
Yeah they do.
Yeah all right. One more material I do want to mention - sorry - so this material actually is a Teflon Kapton laminate it's called...
-wait hold on - Teflon Kapton? Oh okay.
It's called 'TK' - it's a Pyralux product from DuPont and so it has a core of Kapton to act as the XY stabilizer, but then it has a Teflon material on both sides and again, this is a building block but it's very low loss, and very low DK. So a DK of about two and a half with a very, very low loss. But unlike glass reinforced Teflon systems, this has no fiberglass so, no skew and no detrimental effect from the fiberglass. It's using the Kapton instead, as the stabilizer, because if you had a piece of - I should have brought out a piece of Teflon - but PTFE films you can easily - it can be mechanically stretched.
Yeah, one time when I was in the RF and microwave board space, I had the board shop I was working for take all the materials like Rogers, Taconic, whatever and I had them strip all the copper off and I went like the 4000 series 6000 series 3000 series all the way up to 58, 80 and strip off the copper. Because when you see them clad, they don't look that different from each other. But I'm like here's Teflon - this is like a piece of rubber, and imagine heating that up, exposing that to aqueous hot processes and so I think that really helped people to understand how vastly different they are and I think it was a good visual actually to help people understand how radically different these are and when you start stripping off all the copper and you have fine lines and all that then it's - it's a whole different animal.
TK material is - the core material is nice because the Kapton layer does provide mechanical strength. Again though, the TK, instead of requiring 600 degree lamination, it requires 550. So it's still a high temperature product which requires the right press book, the right materials, and lamination, and it also requires a press being capable. And the other too is the board shop needs to get accustomed to the dimensional changes during the lamination process with these materials.
Right.
Again - a lot of it's mechanically driven, but you need to know how to work with it so that's something I think the boardshop needs to have experience with.
Well and I imagine that you're not going to see these materials outside of sort of high performance or high speed capable board shops?
That's true...
-I don't know if that's true I guess I'm looking to you for an answer in there but it's an assumption I would make.
Here's the interesting thing about AP, AP by itself, is actually pretty good electrically. It's the adhesive layers you use that incur a lot of the loss. So then if you get into the thermoplastic systems that have better electrical performance, now you're getting into the temperature range. So it's one of those give-and-take situations, but you can mix and match the materials to some degree. You could use, for instance HT bonding film with AP clads, your operating temperature would default to the AP operating temperature, which is still pretty high at 180 °C, but electrically it's pretty good. You get away from the acrylic and the epoxy adhesives, which aren't great electrically, in terms of loss, dielectric constant so yeah, I think as I think as board shops become better equipped with high temperature systems, you'll see a broader use of these materials.
Right, I mean the market is going to drive us there one way or the other right, if there's a demand then the board shops will do what they need to do. One thing - a comment I want to make about that is - I was in one board shop and I was stunned and then just felt like wow I could've had a V8 moment, is they were providing really high speed, high performance circuits to some high-end military stuff, and they had moved completely away from rigid high performance laminates and used multiple layers of flex materials and the performance - and I'm like - oh well that seems like an obvious, but I had no idea that was even happening. Is that something you have seen, where they just use...
Yeah, if you wanted to get rid of skew completely you could use a film based system.
Yeah it was crazy, I mean that makes sense and I'm sure there's some challenges there cuz I could tell they had to rigidize the bottom, or put some kind of carrier or something, because they didn't want it to flex quite that much but they just stacked these film systems on top of each other and I'm like huh, didn't know you could do that but they were clearly doing it on a routine basis so that was interesting.
Yeah I've seen some board designs where you might have 12 cores of Pyralux...
Yeah,right.
-and then use regular rigid prepreg as a bonding system so and the board's not - when it's all done, it's not flexible it's rigid.
It is rigid, but it's a weird - it's weird to see anyway...
I actually have a board here.
Ok let's see it.
Unfortunately it's single sided so it's kind of like a potato chip, but because there's only one layer of copper and one layer of prepreg, but this is actually DuPont's AP product with Isola's tachyon prepreg, and it's a spread glass prepreg. So you have the spread glass prepreg on one side and you've got the Pyralux AP in the other. So you minimize how much glass is in here, which really drops the amount of impact or micro DK effect which would lead to skew and other signal performance issues. So there are lots of different ways you could use the flex materials even in a rigid design.
Yeah I did see that and I was shocked and I - it's something I hadn't heard a lot about. Anyways well, we're about out of time today, again. But thank you so much, every time I talk to you, I feel like I learned so, so much and it's fascinating to me where the industry is going and what's happening with flex and it's exciting it's really an enabler right and these high, high temp products and that so it's a really exciting time to see. We always break through one way or another it's just interesting to see who gets it done. So it's very interesting to see what we're doing with flex.
Oh thank you Judy for giving us the opportunity to talk about some of the materials we supply but yeah it's - these are all building blocks and, I kind of view it as a material science company in tech...
You are yeah.
-we provide all these different building blocks to meet the need of what the customer needs.
And there is - and there's really unique ways to put those building blocks together so it's fascinating to learn about. Ok so something I didn't ask you last time, but I'm gonna ask you now. Are you a geek or a nerd? [Laughter]
So the best way I heard the two described is the difference between a geek and a nerd is - a geek is the one who gets things done.
Oh interesting okay.
So I would like to think I'm somebody who'd get stuff done, so that would put me in the geek camp but in any case.
Alright check geek, and the second question I have for you: on a scale from one to ten how weird are you?
[Laughter] Oh gosh, I would say - five.
I'm sorry but if we're in this industry we're at least 5 or above. I think we have to be a little wacky to do what we do - okay well thanks I appreciate it so much and again, we were talking on the phone yesterday we have more to cover, so I'm gonna for sure have you back again and talk about printed electronics which is on the rise and you know a lot about. And also I'm very excited to talk about - oh there it is!
Electronics, that's a whole other - whole other world of electronics and yeah.
Wait, wait, wait bring that back and tell our listeners what exactly that is.
So this was printed with a zebra label printer where the - and no changes to the machine by the way - but the special foil is put into the system where you normally put a roller with a pigment film, so instead of printing a black label you're printing metal foil so yeah, it's kind of interesting.
Yes what is that for?
Well this is something did for me at our booth this is just an antenna but you could really you could make electronic designs on the fly now...
Dude, you're still not answering my question here. What is that intended for?
So I'm gonna use that for an antique stereo I have. I have an antique FM stereo the tube, old tube radio, I'm going to use that as an antenna.
I see - oh see definitely five-weird. I say I'm gonna make that matrix instead of the hot crazy matrix I'm gonna make like the geeky-weird matrix and so yeah - you're at least at a five -high and a geek.
But anyway printed electronics is pretty exciting, I mean and again, it's all material science based. As the materials get better you're gonna be able to do more things. Higher conductivity inks, higher temperature inks, I mean there's all kinds of things you can do in that area. Typically the substrates are different - they're typically lower cost, lower temperature capable substrates, but you could - you can make all kinds of things so we'll get it the next time.
Okay we'll definitely do that and the other thing I'm excited to talk to you about - because I know nothing about it - is paste interconnects and you shared a little bit, so anyways we have at least one or two more podcasts ahead of us, so for our listeners; stay tuned and we'll make sure and share everything Chris has talked about today and hook you up with resources through DuPont, HDPUG, IPC, wherever we can find and we'll make sure and share those resources that will help you lay out a better flex and onboard as much information as you can.
So Chris, thanks again, we'll see you next time and we'll tackle another hot topic. Again this has been Judy Warner with the OnTrack Podcast. Thanks for tuning in and thank you to Chris Hunrath from Insulectro, we will see you next time. Until then, always stay on track.
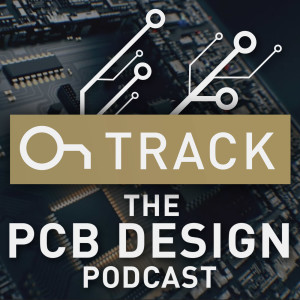
Wednesday May 30, 2018
DFA Tips from Duane Benson at Screaming Circuits
Wednesday May 30, 2018
Wednesday May 30, 2018
Duane Benson from Screaming Circuits shares DFA Tips and a piece of history as he shares the story behind the scenes in developing quick turn prototypes. Listen to learn how one entrepreneur brought fresh perspective to the business that led to great success. And see why Screaming Circuits is uniquely positioned to handle all the leading edge components that PCB designers have available.
Show Highlights:
- Screaming Circuits was founded on the premise to get prototypes built quickly. It was a struggle to get small volume prototypes built and a market need was discovered.
- For prototyping - going abroad invites its own set of risks.
- A traditionally 6-8 week process, Screaming Circuits does in hours.
- We don’t specialize in a vertical industry, so we see a lot of the leading edge components.
- Layout isn’t taught in schools or its self taught. The experts who knew how to make layouts work perfectly have retired.
- We built a business around stuff being wrong. Stuff isn’t going to be right when it arrives to us and we have to fix it.
- Why are we having a problem sourcing parts?
- Personal interests? Photography and decaying industrialism.
Links and Resources:
Downloadable Circuit Talk
Twitter: @pcbassembly, @duanebenson
Screaming Circuits on Youtube
Hey everyone this is Judy Warner with Altium’s OnTrack podcast. Welcome back to another podcast session with us. As always we have another incredible guest with us today but before we get started I wanted to invite you to please connect with me on LinkedIn. I'm very active there and share a lot of resources for engineers and PCB designers and also - I don't think I shared this in past podcasts - but we are also recording this on YouTube as well as just an audio. So you can always go to YouTube and go to the Altium channel, look under videos and you'll find these also in video format if you should prefer to listen to this and watch it in video format. And also with Altium, you can always follow us on Facebook LinkedIn or Twitter and we love engaging with you. We always love to hear from you about subject matter experts or subjects you'd like to hear or learn more about. So, without further ado, I'd like to welcome our guest today who is Duane Benson of Screaming Circuits, out of Canby, Oregon, correct Duane?
Canby that's correct.
So Duane welcome, we've crossed paths for several years now and it's a delight to have you and learn more about Screaming Circuits and EMS and how designers can do things to to be more effective in the design for assembly and just learn about Screaming Circuit’s model, which is a very unique model by the way, I'm eager to jump in.
Well thank you I'm really happy to be here thank you for asking me to participate in this.
My joy. So why don't you start out by telling our listeners a little bit about who and what Screaming Circuits is, because it really does have a highly unique model, and kind of the why behind you guys started the company and created this model?
Well it started back in 2003, actually that fifteen years ago now. Yikes..
Yeah, I know, how did that happen?
So about that time our parent company Milwaukee Electronics they had a number of customers that were struggling to get small volumes of prototypes put together back in the back in the olden days - if I can use that term. Prototypes quite often were sort of slotted in on an ‘as available’ basis. So say you might need five prototypes and the EMS company would say, well we’ve got a big run going on and I can put you u on the machine in two weeks so you can get your prototypes then. And two weeks come along and something else came up, so another week... Even going back before that, back in my day they didn't focus, for example, building a prototype.We'd have a big bag of parts and some blank circuit boards, and we'd hand them to this poor technician on a Friday afternoon and the engineers would go, could you have these built up by Monday?
So it was becoming a real struggle to to get prototypes, get small volumes of any sort built and a couple of our customers came and asked us and said, can you can you help us out with this? It's just not working and the Milwaukee Electronics’ management thought about it a little bit and thought, why can't we short-circuit the process?
No pun intended right?
Laughter.
So the management experimented a little bit and then decided, , there's an actual business here. So back about that time they brought Jared Store out here to start up what they called the Screaming Circuits division to focus specifically on getting prototypes done quickly.
Mm-hmm.
And , from that time the initial focus of the initial business was basically Jared with email and phone and one of our partners Sunstone Circuits, they built the blank circuit boards - the raw fabs. They'd give us a call and say, hey one of our customers needs some prototypes built, can you guys do it? And that's how the business started.
So you guys created the synergy. Now I've had the pleasure of meeting Jared once at least, through the phone and email and Jared was young right? He was the son of the owner so, I have to insert that. Because I kind of love that those of us who are kind of old dogs in the industry - I kind of love that he said, well why can't we do this? And he just kind of, like you said, a phone and a thing and just said why not. Because he wasn't constrained by the way things were done in the past which I kind of love that.
Exactly he was a young entrepreneur, in fact, I don't know if he'll want to admit this but this was his first job out of college this was kind of an experiment for him to get into a career, into business and he did a fantastic job. Basically by ignoring all of the old rules.
I know yeah.
Yeah and then in 2004 - well somewhere between late 2003 and early 2004 - we first went online with a very, very simple quote system. We boiled it down into six different factors and based on that, came up with a quote and it was all kitted at that point. So we'd say, hey it's going to cost you this much, send us your kit, send us your files, and we'll build them up for you.
Now since that time, when we were talking earlier, it seems like it's morphed into not just specifically prototypes but just quick-turn. It could be quick-turn pre-production quick-turn production even right?
Yeah
The world of manufacturing of electronics has really changed in the last decade and a half . There was a time when electronics were not going to be designed and built in this country. Back in the 90s, when I was working for InFocus again, everybody was outsourcing everything and then over the next decade after that, it was all going going away.
Yeah.
And there was going to be nothing but high volumes manufactured offshore. Well about the time we started doing this, coincidentally the open-source hardware movement came about with the Arduino and some of the other things that came with that. Kickstarter showed up and that really changed the hardware design dynamic. It lowered the barriers to entry to building a hardware company and over the last decade and a half the hardware startup has come back with a vengeance. The problem is, as manufacturing is really, really expensive - unless you're doing super high volumes - so these companies would run a Kickstarter, they'd sell a thousand of an electronic board and nobody would build it for them. So then, , they'd then run off into into Asia and they toured all these shops and these people would either say, no that's not enough or they’d change the design, steal the intellectual property and, you can't. There's little details like that so, getting a hundred or a thousand or five thousand is extraordinarily difficult. And yet there's an awful lot of companies that sell just that many of something.
Yeah, it's really interesting that it morphed into that niche right?
Yeah.
You had, it sounds like you had everything, in place to fill it right? You'd built it to do address prototype - traditional prototypes - and as the market changed you were kind of ideally positioned to address those kind of start-up Kickstarter things. So you and Sunstone have worked together in parallel, I take it throughout this process?
Yes they've been our partners since the beginning, and at this point they build the vast majority of our circuit boards and we do, if necessary, go elsewhere. Or if a customer sends us the boards or requests something else, but the vast majority of our boards are built by Sunstone. They're about ten miles away over in Mulino Oregon.
Another big city like Canby…
Laughter - well compared to Milano Canby is the big cities...
Yes well it's a beautiful area. So, tell us about what you would see in a given day and then I would like to ask you to jump into speaking to designers that may be listening, and go into kind of some DFM tips and tricks. But before we do that, tell us about what are you going to see in a day?
To get a picture of what happens there at Screaming Circuits there's two factors that are pretty important. One is a traditional EMS company. We we see about as many different jobs through here in a week as a traditional medium-sized EMS company we'll see in a year.
Wow!
And the other factor that's important to notice, is that in - using that term the olden days - getting a quote and an order for a project might be a three to four week process going back and forth with all the files, component availability, making sure the design works and then after you place the order, you've got the NPI process which is another three to four work weeks. So, you've got a six to eight week process that we do in six to eight hours.
How is that possible? I mean we may not have enough time here Duane, but I've been in the EMS industry and it’s an extremely complex process, just getting the components you need and making sure they're right and there's not obsolete parts, and that you've got a clean BOM, and it's so complex. How have you condensed it without giving away your secrets?
Well there's a lot of things that matter if you're building a hundred thousand of something or a million of something. At that point fractions of a penny count and you're going to spend a lot more time quoting. You're gonna have to worry about getting large quantities of components if you need 20 of a board you can go to Digi-Key and get the parts for a buck, that would cost you a quarter of a penny if you bought them at high volume, and that's still fine now, that's part of it and then you don't have to worry about some of the inefficiencies that would absolutely kill a high-volume manufacturing manufacturer. You don't have to worry about those because if you have to tweak things by hand, while that is more expensive per unit, if you're building 20 or a hundred or a thousand it doesn't matter quite so much. So really what we've done is, we've stepped back and we said, what is important and what is not. The objective is to get working boards into an engineer's hands as quickly as possible and you'll notice there aren't things like how do we make it the absolute least expensive, or things of that sort, it's about getting the working board's as quick as possible so you focus on just the things that matter for that.
Right, you mentioned when we talked a few weeks ago, about it becoming what you had called a transactional model, which is really a different industry and you can go online, place your order in a very transactional fashion, but it also speeds up your time to market, and gives you something highly valuable?
Yes it does, we don't we don't spend an awful lot of time on the financial component of it. For the most part you give us a credit card and we start building so we don't have to worry about the bank component of it. For larger companies we do, because some people, the government or whatever, they have to operate that way. But for the most part you just give us a credit card and that again cuts some time out of it. We also look at each order as an individual transaction, that's why we call it transactional manufacturing, or unforecastable. We don't have to worry about the fact that you're not gonna need exactly 500 every month for the next 24 months. In traditional EMS, you have to worry about that, you plan for that. We don't worry about that, we don't care.
Yeah it's interesting as well it's neat model and I see it as a real enabler. So, congratulations to you guys. All right, let's dig in and give our listeners that are designers and engineers some tips around DFA. The way that you and I originally came to know each other is, I had been blogging and writing and then I came across a little publication you put out called Circuit Talk in which you were doing what I was doing, which was giving designers some really immediate tips to apply to make their jobs hopefully a little bit easier and so, I think you've done a really nice job of that. So can you talk about why you started Circuit Talk and then go ahead and share some of those tips or tricks that are around design for assembly that's gonna make designers’ jobs easier and smooth the time to deliver a good product in time to market.
Well thank you. You know the volume of jobs that we get - it does lead to chaos of sorts - but it also is a huge advantage in that we get to see every single mistake that anybody's gonna make. We don't specialize in a vertical industry so we don't only see mistakes related to a certain type of component tree. Name a component that's leading-edge, we've undoubtedly seen it and, so we see these things - and it's not just beginners, it's not just experienced designers, it's not just big or small or university - everybody makes the same mistakes. It's so complex and there are so many variables, so many new types of components. Geometries are shrinking and in parallel to that people have less and less time to design these things. Quite often layout isn't taught at schools, or it's self-taught. The experts who knew exactly how to make a layout work perfectly have retired now, or they've been let go, or things have changed so fast they can't keep up.
Mm-hmm.
So we see these problems every day. Case in point, one that I write about quite often relates to the QFN Quad Flat-Pack No Lead, and then the DFM. The DFM leads along one side. They have this big metal heat slug in the middle, looks like a very simple component, it's cool, it's small, has great signal characteristics. But most of the CAD software, when you try and use a QFN, the footprint is wrong. It comes from the library with the solder paste layer, not designed specifically for the component, so you've got to imagine flipping a QFN upside down. You've got a little row of contacts around the outside - very small - and then a big giant heat slug in the middle that covers almost the entire component. So most of the library components we found have a full aperture opening, so the solder paste layer is completely open for that heat slug in the middle. And what happens is you end up with too much solder in the middle, so the part floats up and the connects on the side don't connect.
Oh boy.
Yeah and this is even more prevalent with some of the open-source CAD software, or some of them with a lot of user-generated content, nobody told those folks how to make the footprint properly.
I see.
Quite often the manufacturers, in their data sheets, even specify it that way. But what you need to do is, to modify the footprint so in that center pad, you get somewhere between 50 and 75 percent paste coverage. So, you take out the default paste layer for the center pad and you put in a little windowpane-looking thing - problem solved.
Interesting. Yeah it's a little scary, unless you have a partner that's on the ball to what you can accidentally pick up off a data sheet or how to interpret that data right? So okay well, that's a good one.
Another one we run across these tiny little micro BGA's 0.4 mm pitch, some of them even 0.3 mm. I've actually seen a 0.24 mm pitch BGA. Yeah, some of the rules change with the bigger BGA's. You want non-solder mask defined pads, so you want the solder mask opening to be slightly larger than the little pad where the BGA ball’s gonna sit down.
Yeah.
With some of the 0.4 mm pitch BGAs, you want solder mask pad or defined pads, otherwise you get bridging.
Oh yeah, that makes sense.
Yeah, it kind of depends on the geometry of the solder ball, but that's a pretty common error as well. So you see these things that component manufacturers haven't fully studied, haven't fully published and they are just setting people up for problems.
Yeah, and what I have found - and not just in relation to components - I have talked to people who manufacture either components, or they manufacture laminates, and what's not widely understood is that sometimes the studies they’re doing is us.
Yeah we’re their guinea pigs.
Yeah, and then we yell and scream and we give them back data and then they produce overtime accurate data sheets. I was stunned to hear that, but it's absolutely true. They need to get stuff to market because the market is demanding it, and the testing is so complex and so widespread, and the applications are so widespread, that they can only go so far. And then the rest of the data has to come from real world.
Yeah the the hardware industry really is paralleling what the software industry did. We had open source software then open source hardware. With software, we started calling it ‘beta test the world’ because you couldn't beta test anymore, it's too complex.
Right, it’s too complex, so we become the beta testers and I don't think that's often understood. When I first understood it my jaw about dropped because I'm from the old school, like you are and it's like; wait nothing would ever go out that was not fully vetted or understood and tested, and things have just gotten so complex. And so there's just a hard limitation there, it's not a bad business practice or whatever, but it's a reality that I think is wise for designers and engineers to keep in mind - another encouragement to work closely with people like you, that can say, we've seen this already a bunch of times, we know what's going to occur here.
Yeah we've built our whole business around everything being wrong basically, start to finish. It sounds kinda funny, but It's all about this stuff probably isn't going to be right coming into us, so we've got to figure out how to make it work.
I don't know, like what happened to the world Duane? This is not how we started but here we are. Another thing you talked to me a little bit about, you had mentioned one time in a conversation, about polarity markings.
Oh yeah. That's that's maybe third or fourth in terms of the issues that we see here with diodes especially. Capacitors somewhat, but diodes even more so. Any kind of ambiguity, when you're dealing with machines, it's a problem. If you've got a barrier diode for example, it's backwards from what you would consider a conventional diode. So if someone marks it with a plus and it's a barrier diode and they're expecting us to know whether the plus goes to the anode or the cathode, we're gonna put it in the conventional manner, not knowing it's a barrier diode it's gonna be backwards so you can't use a plus to mark a diode. You might think minus, Also, does that mean negative or is that the lion on the diode symbol you can't do that because it doesn't tell us anything you've got to say K for cathode not C - because then we might think it's a capacitor, or the full diode symbol the down - lot of people will put in silkscreen, the mark that's on the bottom of a surface mount diode...
Uh-hu.
-which at first glance seems like it makes a lot of sense - but only if you give us the exact diode that you got the marker off of. I've seen two diodes 0.603s in the exact same package from the exact same manufacturer just a couple characters off, in the part number, and literally, on one the mark is the anode mark on the other it's the cathode mark. I've got to I've got to do a datasheet and I have a clipping from that data sheet on the Screaming Circuits blog that shows that it's got this part anode mark, this part cathode mark. I made the same mistake myself. On one of my boards I put the little marker on there and I gave gave the company the orientation and the CAD files, and then I made a substitution because one part was no longer available and used the other one - same thing but it was backwards because I went from cathode mark to anode mark. So, remove ambiguity. A few years ago I would say, it's okay to mimic the silkscreen - just give us the exact part. But with supply chain availability being such an issue right now, I would not rely on the mark that's underneath the diode because they can reverse if we have to substitute something.
Okay I'm gonna put a pause there and talk about what the heck is going on with supply chain. Stuff about diodes like these, very basic building blocks to design, why are we having problems sourcing parts?
Well we've been told a couple of things from suppliers. One is, they're telling us that the automotive companies are buying up literally an entire line. They'll come to a component manufacturer and say this particular part: I need all of your production, all of it and so there it goes out of stock. Internet-of-Things companies - the super, hyper-mobile devices are also causing issues because they're increasing the demand in the super small components. Well then the companies that make the parts don't have fab capacity to also make the larger ones so, some of the component manufacturers are telling us that they're going to stop making some of the bigger form factors 1206s 0805s even 0603s may become even more and more scarce because if they can make 0402 or 0201 to cover all that range they'll do it and not make the other form factors.
Holy... I don't know what to say about that - if I was a design engineer I'd be freaking out - this puts people in a really tough spot!
It really does and it's gonna change the way some things are designed. We have always had a policy that we will not substitute anything without explicit approval. Even looking at a bypass capacitor - 0.1 microfarad 16 volt bypass capacitor - in some cases you need exact parameters. There’s parameters you need to be exactly the same so you can't substitute. But there are also plenty of cases where it's just sort of by guess and by golly: yeah it's a 0.1, it could be 16 volt, 10 volt, 25 volt, 50 volt, whatever. If that's the case, people are gonna have to start being really flexible in terms of what they will accept for a component and maybe at some point the industry will have a flag on a bill of material that says: this one's engineered so it has to be exact. This one, just make it close.
Another thing, our industry is changing so fast, it's just a big reason why Altium and I've decided this podcast would be a good idea. Same reason why your Circuit Talk publication is a good idea because it's like we can't get the education out fast enough or get the news out. Like holy cow, why can't I get this capacitor? It's not a unique form factor specialized BGA they're capacitors! This is like bread and butter, so it's been puzzling to learn about that and I'm just really interested to see how these component manufacturers are going to deal with this and and again how designers are going to be forced to think hard about these parts it's really strange. Anyway sorry for taking a little side trip there.
That's important, it's a significant issue. We're being told this could last until 2020 and when we get out of this allocation, the industry is going to be different and, as I said, a lot of the bigger form factors consider moving all to 402s. It's more difficult to deal with these smaller ones but those are the ones, when the component manufacturers catch up, it's going to be in the smaller form factors because they can sell them to people building small devices as well as big. So think about that, be very, very careful when you're picking the specific component and tell us, and other manufacturers like us, what parameters are important.
Goodness that’s a great tip. You know I hadn't thought about it until just this minute when you were talking; I'm wondering if this will drive an uptick in embedded?
Embedded like embedded passives?
Uh-hu better passives.
I don't know I've been waiting to see that. I joined this company in 2005 and embedded passives were in the news at that point, and I actually made a prediction on the Screaming Circuits blog, that in ten years - I think I said - 80% of the passives would be embedded passives. I don't know that we've ever seen one. I guess technically you wouldn't see it because it's inside it.
No but you would know it was there, because I know it from my board manufacturing past, you would know cuz you would have to process it differently. It's a different process but I don't know what the cost trade-offs are there, but I've met Bruce Mahler from Omega and I've met some of those folks, and I'm just wondering if this allocation will drive, but I don't know what the cost trade-offs are or performance comparative. That makes me think, I need to call Bruce Mahler and get him on the blog because it's an interesting thing to ponder in lieu of what's going on in the marketplace.
Yeah.
Anything else you would mention off the top of your head that's something you see repeatedly that's a design for assembly thing that you would recommend designers to take a look at closely?
Well the polarity, the QFNs, BGAs as I mentioned. Something that isn't necessarily quite so obvious is the data files that is an important part of design for assembly. Ambiguity on a board is bad, ambiguity in a data file is bad. Bills of Materials, if there are parts in there that don't match the board, that's probably 80% of the jobs that come through here, have some sort of a Bill of Materials issue. So, double-check that that's accurate and that it matches your CAD files. If you can give your manufacturer the intelligent CAD files like an ODB++ or IPC 2581, that significantly reduces the chance of error, but then there's a little irony in there too that a lot of board houses still prefer Gerber's so we have seen cases where someone saves and then; oh yeah, I can give you the ODB++, but they forget they made a slight change and so now we have Gerber's that don't match the ODP++ so, make sure all of your files are consistent. Make sure the Bill of Material is clear and finalized. All in all if you add up all of the files issues that we see, that's probably one of the most common problems. I mean, I run into those problems for myself. I designed some boards and run up to the factory here, and I know how to do this, in theory I know how to do this, but I regularly make mistakes that my co-workers chide me for.
Well I think again, that leads to the complexity of the data that's available. The data sheets; whether they're right. I mean it is such a complex thing and it amazes me that we can even manufacture circuit boards and then put components on it and come out workable sometimes. Because it is such a complex process, I'm really glad that - actually I appreciate it - I don't understand all those steps but having worked for for both a really high end EMS that sold to tier one’s, very complex boards, and also having worked for a variety of board shops. I really appreciate the complexity in both those disciplines, and I think sometimes because a board shows up as a line item on a BOM that complexity sometimes can get lost on you. But yeah we're building things, even here Altium, into our own tool that helps, like an active BOM, things like that, that hopefully help. I think design tool manufacturers like us, I think we're doing a better job helping in that regard.
Right yeah, definitely!
Well the last couple items I wanted to talk to you about... well thank you for all that by the way, and again, we will share in the show notes your website. The Circuit Talking, I would recommend to anyone who is listening or watching - that you subscribe to Duane's blog or just Circuit Talk or whatever and we'll put all the links in because again, he's got his feet in the fire and runs up against these things as he said. Because they're putting through such a width of product. Like I used to work for an EMS, and like you said, it was a vertical. So we worked with military Tier one, and so the type of bores we saw was a niche, but you're seeing everything.
Yeah, literally I mean we worked on a camera board, the electronics of it, for National Geographic - it's a plexiglass globe, they drop it to the bottom of the ocean, it's got a chain on it and when the chain rusts through the camera bobs to the top and they pick it up again. We've got stuff being built for the 2020 Mars Rover so, literally down in the ocean up into space and and anything in between, we've built Ardium base stuff, real simple things, through holes; we built a board with five thousand placements. It's just all over the place and it's just absolutely the most fascinating place I've ever worked certainly, because of that.
Yeah I can see that and again, kudos for you - it's easier to do a quick podcast or write a blog post or produce a Circuit Talk that can go out to thousands of people and get that information out in that kind of global sense and be helpful right.
Yeah rather than tell one person at a time.
Exactly it's kind of a scalability of getting that knowledge out, so I really appreciate what you've done over the years. One thing I wanted to ask you about which it was a fun thing is about; I don't know six to eight months ago, I had the privilege to go with the Altium team for the first time, to a Maker Faire because we have Circuit Maker and Circuit Studio - Circuit Maker is free and and now we've bought a company called Upverter, which is also free, and in the cloud, and we also have Circuit Studio. So, we went there with those products and because of my position here as Director of Community Engagement, I hadn't had any exposure really to the Maker community, other than seeing stuff online, and I went and it was like drinking from a firehose. It was so much fun… goofiest things... it was so much fun. So, I'm walking the aisles, kind of collecting things to write about, or learn about, and I come across Duane Benson, wearing what looks like rap swag around his neck - it was like a clock you were wearing right, or something - he looks like a rapper and I'm used to thinking of him as this Duane Benson from Screaming Circuits and here you are, like fully immersed in the Maker space, and you had designed this device and had LEDs on it and I'm like: what are you doing here?
So tell me about how you've come to serve Makers. It doesn't seem like, from a profitability or a business model, that it would be a market that a company like Screaming Circuits would address. So how'd you get there Duane?
Well you could say that I'm a bit of a method actor, I mean I love... I've been designing small circuit boards for a very long time and writing the software for them for a very long time and one way of looking at it, is I'm a Hacker and a Maker who happens to be lucky enough to have a manufacturing facility. But more specifically, those Hackers and those Makers they are starting businesses.
Yes they are.
Many of those businesses become our customers whether they be crowdfunding or bootstrapping or getting investments, they are the future. The Maker community has a lot of students in it. It has a lot of weekday engineer weekend Hackers, it has a lot of people who aspire to start a new business and just such a wealth of creativity. And part of our mission I always like to look at, I'm just one person, we're just one company but if we can make our tiny little corner of the planet just a little bit better then we've been successful and all of those people who want to design electronics...
M-Hmm..
-We know what they don't know. I mean, we know what kind of problems they’re going to run across before they do, and so if we know what they don't know why don't we pass that off? And some of those people will have boards built with our competitors. Some of them will build them themselves, some of them will have us build them. Whatever, we're helping them understand this industry better. And we are helping them build better boards. That's what we really want to do. That's why we're at the Maker Faires ultimately. It does always have to lead back to more business for us, and it does. People see Screaming Circuits, they get the Circuit Talk and they read it, and it's Circuit Talk a Screaming Circuits publication so all of that winds its way back eventually, to helping the business here, and that's how we can afford to do it. But if we can help the business build and grow the business and help these budding designers - everybody wins.
This is why I love you, and love you guys. I just I love that philosophy, I love that approach. I try to live by an old Zig Ziglar thing and this reminds me of you and Screaming Circuits’ model that you just explained. Zig Ziglar used to say, you really can't have everything you want in life. If you just help enough other people get what they want.
Right.
So it's kind of knowing unconsciously that if you put good things out in the world, and you do the right thing, and you're ethical, and you have integrity, and you serve people, that good will come back to you and and you'll do okay. And I think that's a big key to your success actually, by kind of leading with service and and not ignoring the bottom line. We are in business to make money, we have to do that, or we're not in business anymore. So, I really appreciate that.
Well we're wrapping up now and I think you've listened to a couple of these podcasts now and so two questions for you. One are you a nerd or a geek?
[Laughter] I’m a Gunerd…
That's the best answer I've ever gotten yes you're a Gunerd.
Yeah, there was a time when those were really pejorative terms but I think nerds and geeks have taken it back and said, you know what, no we're not going to be ashamed of liking technology and loving it,we're proud of it. I mean, yeah so I’m a Gunerd.
Oh my gosh, I'm totally gonna steal that and use it somehow Duane, that will come back to haunt you later I promise.
[Laughter]
And the other question is, but I think I know what the answer is, if you've listened to podcasts. I always ask designers and electronics professionals in the end - this is ‘designers after hours’ - so because there is so much creativity involved a lot of people, like you said are Makers or Hackers, or they play a musical instruments or they're sculptors or whatever. So, what is your kind of guilty pleasure that you like to do after hours?
It would have to be photography. I chase animals around and take pictures of them, animals, landscapes, and then I have sort of a weird passion for old, decaying industrial sites as well. But photography would probably have to be my passion when I'm not playing with electronics.
That's so cool. Do you have a website where you share any of that or is it just mostly personal stuff and you keep your photos and share them with friends and family and whatnot?
It's mostly a personal thing I have had them on websites before but it's just my thing.
And and what do you mean about industrial sites?
Well, old decaying, industrial and rusty factories. There's a place here just north of Canby Oregon City and we've got a waterfall on the Willamette River and most people think of waterfalls as pristine, and nature and that's all wonderful, I love that. But this one: back in the 1800's they started building paper mills and they built a set of locks. It's the oldest - well till they just recently closed down - it was the oldest continuously operated locks west of the Mississippi. And so now, you overlook the river from a nice restaurant and you see this shut down, decaying, industrial plant and - well no it's not the beauty of the river - but I see a sort of beauty in the symmetry and in the the way people constructed these things. It's almost like an architectural dig, you can see things from a hundred years ago, from eighty years ago, from sixty years ago, and you can see the evolution of that, as this thing built up and then as they abandoned it, and there's just for some reason... I really enjoy that that sort of a view as well as the natural views as well.
They do have a really unique aesthetic and things have changed. It is kind of like a little time capsule and the rest is actually beautiful and sometimes the design itself is beautiful.
Yeah well thank you again, this has been fabulous and I'm sure we can talk more and more, but thank you so much for giving me so much of your time and sharing DFA tips and the story of Screaming Circuits, and we wish you continued success and we'll certainly share the website and Circuit Talk. And if there's anything else you'd like to share with us, give me a holler and I'll make sure we include those in the show notes.
Thank you very much, it's been a privilege to be on the show here, thank you.
Again this has been Judy Warner with Altium’s OnTrack Podcast and Duane Benson from Screaming Circuits. we look forward to seeing you next time until then always stay OnTrack.
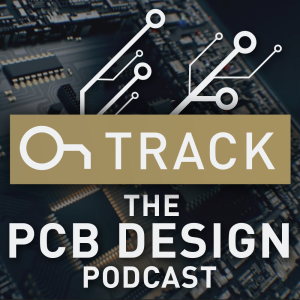
Tuesday May 22, 2018
Lee Ritchey and High Speed Digital Design
Tuesday May 22, 2018
Tuesday May 22, 2018
When Lee Ritchey “got through launching things to the moon” his career took off (in Silicon Valley...before it was Silicon Valley!) and he is now widely regarded as one of the premier authorities on high speed PCB and system design. He is the founder of Leading Edge and author of Right the First Time.
Show Highlights:
- Lee started as a microwave engineer who designed chips that went up on the Apollo
- ICs and “faking” logic
- High Speed design courses first offered at Berkeley.
- He wrote the books to make the students happy and provide the coursework that didn’t exist.
- High speed signal path losses - how do we control skew? Where does it come from?
- And what’s the answer? Spread glass.
Links and Resources:
Lee Ritchey on Linkedin
Lee Ritchey’s Presentation at AltiumLive 2017 in Munich
SI forum - an email forum that is a very good resource for SI questions.
- All one needs to do is send an email to: si-list-freelists.org
- Type subscribe in the subject line to become a member.
Disclaimer: We respect the unique perspectives of all of our OnTrack podcasts guests. Therefore, we choose to offer their uncensored opinions in favor of full transparency. However, all opinions expressed are exclusively those of our guests and do not reflect the views of Altium or our employees.
Hi everyone, this is Judy Warner. Welcome back to the OnTrack Podcast. If you would please subscribe, and let us know what you'd like to hear more about here on OnTrack.
Today, another amazing guest Lee Ritchey, who truly needs no introduction. But if you haven't met Lee before - Lee is considered to be one of the industry's premier authorities on high-speed PCB and system design. He's the founder and president of Speeding Edge - an engineering consulting and training company, some of you have read his book. He's author of 'Right the First Time' and he has a very illustrious, amazing background, and we also had the privilege of having Lee speak last year at AltiumLive in Munich, so I'm delighted to have this conversation with Lee. Not too long after Design Con, so I know he'll have some great wisdom to share.
So, before Lee and I get started, also please connect with me on LinkedIn or on Twitter @AltiumJudy and Altium is also on LinkedIn, Twitter, and Facebook. Lee I'm going to start with a very high-level question. First of all, welcome. It's good to see you again.
Thanks for the invite.
Always my pleasure.
So, you're known as the high speed authority in our industry, but how did you get there? How did you, out of all the paths you could have taken sort of in your technology field, how did you end up kind of going down this rabbit hole?
I started out as a microwave engineer on the Apollo program, which as you probably know, was a long, long time ago. And the company I went to work for was in Silicon Valley, when it was not yet Silicon Valley. Well, after we got through launching things to the moon, NASA decided, well we're done with that, and lots of us - like sixty thousand of us - had to go find something else to do.
Wow.
Well I was in Silicon Valley and integrated circuits were starting to be a big play and the big jobs were designing things with integrated circuits digitally. And so I interviewed for a job designing equipment for testing digital integrated circuits, and got the job. And said, oh now I’ve got to go learn something about logic. So I went to bookstores and got books and I faked it, and that's how I got got my start. And of course, since I was already in the microwave end of things, transmission lines were already part of that, and that was what you had to be good at if you wanted to use ECL, and the high speed computers back then were ECL.
That's how I switched from microwave to what everybody called digital, and for a long time digital was slow enough so you could pretend it was digital, but I never did and always designed on transmission lines and so, as the speed went up all around the industry, everybody needed to learn how to do something with this high speed stuff. And I had a design company from '82 to '92 where we designed pretty much all the early work for Sun, Silicon Graphics, Cray - people like that, and invariably I would get a new client and the engineers knew nothing about high-speed design. So I'd spend two days teaching them the basics so that we could design their board. Out of which grew the courses that I do now. Which I first began to offer at UC Berkeley, and the complaint after every course was: there's no book, there's no textbook, and that's where the books that you mentioned, came from as I had to write those to make the students happy at UC Berkeley. And in 1999, we decided that we didn't like working for companies so we started Speeding Edge.
Okay.
That's it, that's how I got here by - almost by accident.
Well I always say, most of us got here by accident. I mean some EEs take a nice, clean, straight path, but even they don't take that straight path., I know I didn't end up here on purpose either. But that's interesting, I didn't know that's how your book came to be. So the last time I saw you, you were actually speaking at DesignCon. And how often are you teaching these days actually ?
Most of my classes are private and I would guess about every two months or so.
Okay.
There are two-day, three, and day classes so, that's about as often as I want to do that. I don't know if you've lectured for 14 hours in a row, but it kind of wears out.
I don't think I know anything about anything enough to talk for 14 hours, maybe raising kids I don't know - like I don't think I know about anything to talk that long so now we - now we know for sure, you're way smarter than me.
Oh no, I just came from a different path that's all.
Well you and I were talking recently, preparing for this call and we sort of went down this path talking about PCI Express. So can you kind of talk a little bit about the evolution of speed and the extremely acute curve that we've taken in the last couple of years?
All right, well maybe let's start with PCI itself, which is the Bus architecture that is in - has been - in all the personal computers that you can buy, that's what PCI stands for: Personal Computer Interface, and it was a parallel Bus that you might have seven or eight plug-in cards, all on this Bus. That CPU could talk to any of those, any time, and then originally there was - it clocked at 33 megahertz, and it wasn't too long before the CPUs got faster than the Bus, and all of a sudden we were - what we call - IO-bound. We couldn't get any more performance out of a PC, because the Bus was too slow. So we upped the speed to 66 megahertz, and then a hundred, and for a lot of reasons they're too complicated for today, we couldn't go past 100 and that block limited how fast you could make a personal computer. And so we realized the architecture had to change. And the reason is that if the CPU can talk to any spot in the backplane at any time - to do that really fast, you have to have really, really short connections and that was not realistic. So we turned to an architecture that actually is old. The difference was signaling protocol, that is in PCI Express, has its origins way back with IBM. I was using it in '74, where we would connect two boxes to each other, where we couldn't do that with a parallel Bus, because the the noise in the background was too high. And so that's not a new technique adjust that early on, as you know, the guts of a computer is a parallel architecture meaning lots of bits switching in parallel, and the differential links that we're talking about here are serial.
So at each end, you had to go from a parallel Bus to a serial stream on the line, the other end - go back. And at that time, the serializers and deserializers were extremely complex and expensive. So the only reason you'd ever do that, is there were - if you were stuck, you couldn't do it any other way. Well as we'd gotten to where we have a billion transistors in an IC, these serializers and deserializers are what we call basically free. So all of a sudden it doesn't cost much to go from parallel to serial and back. And the advantage of that is, you can - you can drive... Well let me start from - in a parallel Bus were either series or parallel terminated - if you're lucky, you can drive that at 2 gigabits per second, that's very hard to do. With a serial Bus - we can drive them and we are right now driving them at 32 gigabits per second, which you could never do any other way, and this is how we're getting all the performance we need in the internet. Everyplace else is with these serial lengths and that's what PCI Express is. We switch from a parallel Bus to a serial Bus, to allow us to go faster.
Well, when you have serial links there, you can only have a driver and a CI receiver on the same net. So how is it the CPU's going to talk to six or seven devices like it was doing with the old parallel Bus? And the answer is, we have to have a switch chip somewhere so that we can switch between the CPU of whatever we want to talk to. Well early on, those were expensive chips, so we only use PCI Express in real high-end PCs like a gamer would buy. But we've now integrated those switch circuits right in the CPU so it's not an extra part to buy.
Oh okay.
So it's everywhere. So pretty much everywhere we've got PCI Express, well in itself it's not really all that big a deal because the early PCI Express was - well depends on your point of view - as fast as 500 megabits per second on the line and that's not special, to these terms. The rub is, we have started to go up the performance curve where we've got Gen 1, Gen 2, Gen 3, and so on. And Gen 3, which is it just about around the corner for everybody - it's 8 gigabit per second. That's not slow, and we start to see things that we could ignore at lower rates.
The one we're going to talk about today is not lost - it's the thing we called skew. Skew is the fact that the two sides of a differential pair don't arrive at the receiver at the same time - and some numbers on this, the most common until recently - most common data rate in switches and routers for the internet, was 10 gigabits per second. Where one bit is 100 picoseconds. And I did a test board in 2013 at DesignCon where we discovered 62 picoseconds of error in a path which is almost an entire data bit at 10 gigabits per second - which destroys the work. The link does not work and of course, we've got Gen 4 coming in at 16 gigabits and Gen 5 at 32 - where 32 of the bit period is only 30 picoseconds. So that error I just talked about, is two whole bits which means, nothing's gonna work right? So the question is, where does this skew come from?
So is that, Lee let me interrupt you for just a moment. Is that what you - the course a you taught this year at DesignCon, was that your focus?
Yes well the bootcamp, I call it 'Getting to 32 gigabits per second' which covers a number of things, skew being one of them.
Okay.
Of course the first worry almost everybody had, is loss. So we had this flurry of activity to make low loss materials and smooth Cochrane on and on like that. At the same time we were doing that, I see manufacturers figured out a way to improve their circuits so that loss is not a player anymore - not a big deal anymore. For example, the latest Vertex I guess their Vertex 8 or 9 from Xanax, at 28 gigabits per second, the Lincoln tolerates 38 GB of loss. Meaning that we start out with say a thousand millivolts and we wind up with four at the receiver, and it still works, so all the drive to have the world's best, lowest loss laminate is not a player anymore. Skew is, skew's killing everybody. All these laminates from people like Rogers and - you mentioned one earlier - I can't remember.
Taconic.
Taconic are simply not necessary - not necessary. At any rate, skew is just - and that was the theme of DesignCon this year. It is how do we control this bloody thing? So my impression - I guess that comes up next - is where's it come from?
Yeah, where does it come from Lee?
Well if the two sides were different to pair with different links, that would be, I think obviously, one way that can happen.
Right.
But pretty much everybody else had to design physical links to a few mills, so that tends not to be what the problem is. The problem is - and these are what we call micro defects or micro effects - the glass cloth in laminates you know, on average has a pitch between threads of about 16 mils - between 16 to 20 mils - Traces are 4 or 5 mils wide, so there's a huge difference between the width of a trace and the spacing of those glass fibers. Well, laminate is a mixture of glass and resin, and the dielectric constant of glass is on around 6 and the dielectric constant of resins is less than 3. That means that the lower the dielectric constant, the faster the signal is going to go.
That's right.
So if I had one side of a differential pair on the glass, and on the other one in between, there are two different speeds. That's where the problem comes from.
Now along those lines, I was just talking to Chris Hunrath from Insulectro, and he was talking about spread glass. What do you think?
That's what the answer is.
It is?
Okay cuz you know I've been here at Altium a little over a year and I guess I missed the spread glass thing, but I'm like, that actually sounds like it makes sense.
Well I and my colleagues have been the drivers of spread glass.
Really? Tell us about that.
Well so we found - I've got to confess - we found out by accident,
That's how all good inventions are found right?
Yes, and it had to do with - let me think about when that was - about 2005, we were trying to improve the uniform distribution of glass by using two plies of thin glass, hoping that they would sort of average out. And I had a fabricator in Oregon who says: you know, if you use a single ply of 33:13, you could save some money. So we built the test board and by chance that was really spread very nicely and so we had no skew problems. So all of a sudden, we thought we've solved all the world's problems by just using this glass. And then we built our test board from a different weaver.
So and this weaver spread the glass in one direction but not the other?
Yeah.
So, if you were to get that DesignCon paper you'd discover that we had really good skew one way.
One direction - - [laughter].
And so back to square one. Why aren't people spreading glass? So we got to digging around - and it was for laser drilling of blind vias.
Because, if you think about it, if you have like the classic 4 mil core was called 1080 glass. If you look at that, the glass bundles are round or not spread out, there are big voids between. Well so, if the guy drilling a laser drilled blind via wanted to get rid of the glass, he'd set the intensity to burn the glass and then go tear right through the backstop directly right, and so the laser drilling industry is the one responsible for spreading glass.
Like you said, complete accident.
It is, and they don't care about signal integrity, they care about laser drilling - so I and a guy named Scott 'Hindiga' of Cisco, started going to IPC's sessions on 'Standards for the Last Week' with the intention of getting some standards for how you spread the glass. Well it was got a whole lot like herding cats.
[laughter]
What an IPC committee being like herding cats? I don't know what you're talking about Lee [laughter]
Yeah, so around the table we had five or six weavers and they would not tell us how they wove their glass.
Because it was proprietary?
Yes, so he couldn't come up with the standard, and the only standard that the laser drilling people had was, you take the section of this cloth and they put it in the chamber and see how - put compressed air on one side and see how leaky it was. That's it - that's all there is today. If it was leaky, let's make it an X, and it was good. That would not be good enough for what we're doing here. So we are not done solving this problem, and there's about seven or eight different ways that people approach it. Now if you were at DesignCon this year, you'd discover two papers were presented by Cisco where, when they built the boards at five degrees to the weave, they got the best skew results. So that's how they're...
- Wow, yeah.
Can you imagine what that happens to you in a fab shop if you say pop this artwork on their at 5 degrees?
[Laughter]
-well I remember hearing about - from a colleague, he was an EE - they were actually at some point, because of the glass crossing and there being those bundles, they were actually starting to do it at - basically laying the prepreg at a diagonal. Do you follow what I'm saying?
Oh yes.
-do you remember that? That was kind of going on for a while to see if that would help, and I think it did help a little bit but again, the expense. There's so much loss of materials doing that, that it didn't make sense, or there was the trend of making that weave super, super tight so at least it was consistent, even if it was lossy. So, I feel like we've been going at this from a lot of angles - but hearing from Chris Hunrath, at Insulectro, it sounds like some people are really moving towards that spread glass and getting some good results.
Oh, that's my choice, but if you were to get the PCI Express Design Guide from Intel, they would tell you one of two things: you route all the signals at fifteen degrees through the X and Y-axis, or route them X and Y, and then you have the fabricator rotate the artwork 15 degrees on the panel.
Yeah.
That's in the standard for PCI Express.
I had no idea that was in the standard. I've heard about it, but that being - kind of anecdotally, but I didn't know it was actually written in the standard.
Yup it's in the standard from Intel, and you can - if you imagine a backplane where you have a regular array of pins for connectors and so forth - there is no way to route it at a 15 degree angle, because it's constrained by the pin array that's X and Y - so that's not a choice. So that leaves you with only the choice of popping the thing at an angle on the panel and then - you've been around enough to know the fab shop's gonna look at you like you have lost your mind.
Yeah.
Well we're not doing that, we're not doing that. We found some weaves that we know are well enough controlled that we're succeeding without that.
Okay good, that's good news. So this spread glass - so that's helping with the skew, you're saying, among other things?
It solves the problem.
It does?
Yeah.
That's amazing.
The rub is, you've got to be very careful who the weaver is.
Well can't you spec in a certain -
- What if I tell you that I had two weavers with the same stuff? That's the problem. When you say 33:13; there's no standard, that just means there's X in this direction Y in that direction, that's all that means.
Are there are prepreg providers that are - it sounds like there's prepreg providers that are doing it the way that you prefer. Or maybe other high speed...
There are, there are.
So do tell or can you tell?
Well the Doosan material I mentioned to you before we started this, is one of them.
Okay.
And a couple of Isola materials are okay but nothing else is.
That's a good hint, it's a good hint, look I mean I'm doing this podcast hoping to have a takeaway - so I don't just bring up all the problems and then say have a nice day thank you for sharing that. Right that's the goal like: yeah I found out what works, good luck! No.
So I have been seeing this word and this thing skews, so thanks for sharing that. One thing I could see as a potential problem - and tell me if I'm right or not - since that speed curve has risen so acutely, it seems like, the people who weren't previously doing high-speed design must be getting pulled into that space whether they want to go there or not right ? That - would that be a correct statement?
That's true yes.
When you and I were talking before this call about - let's talk about resources. About where these designers that are coming into this space I mean - speak just a moment about DesignCon, cuz I know you're pretty passionate about that show, and particularly giving out really good information?
DesignCon is the only conference I know where the level of information you need in this area exists. It's where everyone who has done research, or has studies and that sort of thing that are advancing the state of the art, that's where the papers get presented. It used to be - that was it. There were no tutorials, no education, that sort of thing. But over the last four or five years, we've added several things. This year we had three all-day boot camps on topics that matter to people who are trying to get on top of things. I did one title ‘Getting to 32 gigabits per second’ which dealt with all these topics. Intel did a three-hour on 'what is this PCI Express and what do you have to worry about' for people who have not seen it before and if it was five years ago, you might see there was nothing there for a board designer.
Now you would say it's the place you go for a board designer. There was a time when the PCB West was, but that has - I've been keeping track of that for a while - not offering the kinds of things you need for the these topics and I'm not sure why. I certainly have been talking to people who run it saying that you've got to offer tutorials, you used to do that. We used to offer stuff for engineers and they quit doing that because well, the guy who was running it was a board designer and he considered design an art, and their art dropped the stuff that appealed to engineering. Now, that stuff has to be learned by the designers.
It does, and as an old board designer person, I had to learn it from the board manufacturing side because I didn't realize - because I had left the industry for a while and come back, that things had sped up so much, that board designers all of a sudden weren't just dealing with: oh here's the specs, just adhere to the tolerances, do what the documentation says and have a nice day. There wasn't like now, high-speed board designers have to think about performance and all this wacky stuff. I mean the way we clean the board, the way we etch the board, the way we drill the board, everything can in a positive or negative way, affect the performance and it mortified me to think we got to a space where we could be completely IPC compliant and the board wouldn't perform as expected.
Yeah that's a good thing to observe and that is standards. By definition standards document the past by definition, and there are no standards group I can think of right now that has more behind the curve than IPC is, because they...
Why do you think that is? I have my suspicions, you're probably right actually, and you're more of an authority than me. But I'm just wondering why? What's caused that to happen?
Well who's driving it? Well, volunteers are driving it. Where do they come from? Well when IPC was at its prime, the standards committees were all staffed by engineers from aerospace companies.
Yeah true.
And the quality of the work was superb.
It's very true.
That's not true anymore - not true anymore, who goes to the IPC now? I don't, nothing there for me...
Why do you think the committee's aren't run by aerospace engineers anymore, or the Intels of the world, or Ciscos? Why why do you think it's not?
I wish I knew.
Yeah I really don't know either, I thought maybe you'd have some...
In the aerospace, that part of it, the aerospace contractors got out of the standards business and remember Jimmy Carter had a thing, The Commercial off-the-shelf Masters what... at any rate we're going.
Yeah - faster, cheaper...
Yes and the standards bodies that aerospace had, lost their money for example.
So they lost their funding to focus on that kind of thing.
I can see you probably heard of that. You know the last time it was updated? 1998.
[Laughter]
How outdated do you think that is?
And the update was to correct some spelling.
[laughter]
Oh my gosh, that's just plain sad, but they've come out with AS9100 and other things to replace it. I don't know the quality of those specs.
Well aerospace is on average about 15 years behind the industry now, it used to be the other way around.
Yeah, it's just really sad but I think that speaks to a lot of the way that politics have been run unfortunately, and the way things are getting funded.
Yes aerospace doesn't drive technology anymore.
Yeah, that's a crazy thing to think - to say out loud - I don't know, for you and I who have been around a little while. So, before we get too far off track, so DesignCon is definitely one place. Now because Design Con, if you pay to go to DesignCon, you can get all the proceedings. What can you do if you didn't go to DesignCon?
Well you can, for a hundred bucks, buy all the proceedings for a given year.
So someone could go on their website right now and for a hundred bucks buy...
All the papers that were presented this year correct.
That's amazing. Okay well that's a really good resource. Obviously your book which - because we were gonna talk - I went on your website and I noticed you're having some kind of fire sale on - I don't know if it's part one or something - but 'Right the First Time' - it looked like you were selling it and then it sounds like you now have a digital library of things you've published over the years?
That's true, and back on the topic of the books. We have two volumes and there was really gonna be one but - I don't know if you've written books or not - but you start out with great enthusiasm and this long list of topics. Then I had a deadline which was a Berkeley class, and I was only halfway through my list. And so I said: okay, this is volume one, next year we'll do volume two and what you probably don't know is, our books are printed in color. You have to have that in order to illustrate a lot of the things that matter. No technical publisher will publish in color, none of them.
Really, I didn't know about that I know it's expensive, but I didn't know that they wouldn't do it in color.
Yeah, so we were so focused, we formed our own publishing company and we went to a printer and said: we want to print this book. You see, there's a little secret about publishing.
Bonus material!
You have to give them a check for all the books before they turn the press on.
Oh boy that's expensive.
So for each of these two lines I wrote a check for $50,000.
Wow!
Crossed my fingers that someone would buy them, otherwise my garage would be full of books. Well, we sold out of volume 1 and volume 2 came along it sold faster than volume 1 did because it was a pull from volume 1. I am just debating, do I want to write another check for like $50,000 to get to print more volume one's, and the answer is no. So it became an eBook .
Oh ok.
So if you go on the website, when you buy you get them both, one's an e-book and the other is a hard copy.
Ok smart.
Then 200 books from now they'll both be eBook.
[laughter]
You got smarter.
My garage will be empty
[laughter].
I thought it essential that the books be in color.
That makes sense because some of those diagrams you can't distinguish between certain things without color being present.
No the color's for this industry. And so we are publishers and we sell our own books and people pay. I may be where I need to write volume through 3 and there needs to be a volume 3, to cover the things you and I just talked about. But I have told my friends - if I start talking about writing another book - their job is to slap me around until I get rid of the idea.
[laughter]
Well I'm not gonna slap you because this speed curve's going ahead now, we need to learn about skew and stuff. So - and who else Lee Ritchey, is gonna write that book?
I have actually written another book, working newsletters and articles that are on that - and someone should put them together but it's not me.
You know, we should get our friend Barry Matties to do that for you. Maybe he will.
You saw my distraction behind me which is the model railroad and that's more important.
Okay well I'm going to ask you about that, so I'm putting a hold on that subject, but let's cover a couple more quick things. One: you and I had an interesting conversation about circuit board manufacturers that are capable of doing good high-speed work and I made a comment and you corrected me right away because I said: well you know, board manufacturing hasn't changed that much in North America over ... blah, blah, blah. And you said, no that's not true. And I said except for places like TTM and you said which TTM?
Yes.
So tell me what you meant by that and fill our listeners in you know, of that conversation you and I had, cuz I thought it was very valuable actually.
Well when you say TTM, you're really talking about a dozen or so fab shops, which were acquired one by one. All have different capabilities for different markets, and if you're not careful and you get a bid from some - say TTM - they'll choose the fab shop that has the most capacity at the moment, which may not have the skills you need. And so I learned the hard way, you have to know what their capabilities are and when you give them the order, you say what plant is allowed to build the board.
And they'll accept that request and send it to the best location?
They won't get my business if they don't.
I am writing the check you will send it here.
Yes, yes and if you don't do that you won't get paid.
Yeah that totally makes sense. Well you and I talked about Stafford Springs which is a board shop, one of TTM's facilities I've always wanted to go through and it sounds like you've been through and that sounds like at least one of the locations that is capable of doing those high-speed designs?
That's right, and another one is in Hillsboro Oregon. It was originally called Merricks.
Oh yeah I remember Merricks.
Yeah and of course if I'm building small volumes it's my - my choice is a little place down in Orange called MEI.
It's not MEI anymore.
No it's got another name.
It's Summit Technologies which I agree they - I know Jerry Partita there - I hope to have him on this podcast actually because I think they've done a real good job there.
Yeah so you're sort of testing out something that we all say explicitly. If you're designing for this kind of space you need to be in direct conversation with the engineer at the fab shop, so that you don't make decisions that are not realistic. So I always have got that guy at the other end when I'm designing a new board.
I think that comes up again and again on this podcast by the way, people saying you have to talk to the key people at the board house which I totally agree with.
So let's talk about - I used to blog on Microwave Journal about what shops I thought - because I was working for Transline Technology, which is a really small board house in Orange County but they're quite good at RF and microwave. But I used to try, because I would see board houses say, sure yeah we do high-speed or the microwave because they've been built on say Rogers 4350 which processes much like FR4 -
- not really
- well not exactly but close. It's pretty stable but then they would take an order for something that was PTFE because they built some 4350, and then they'd fail and say, sorry we tried to build three times and we failed. And I kept seeing this happen over and over again. So I started writing about what I thought people should know, what they should look for in a good board manufacturer, i.e. what percentage of their work is high speed.
So let's stop for just a second and clarify what high speed means.
Okay.
Because RF & microwave is not high speed with respect to the digital world.
Yes that's true.
Actually RF and microwave were simple compared to digital boards. I consider them to be trivial.
Yeah but some of the stuff you do on those for microwave boards are funky and weird.
That's not because they need to be like that. That's because RF engineers say things that are goofy
[laughter]
It is true because again why I started blogging is because RF engineers were starting to lay out their own boards which was not a good model.
Yeah, remember I'm an RF Engineer, and so most of the stuff you see people asking for on those RF and microwave boards is goofy; it's not good engineering, pure and simple. At any rate, so when we're talking about high-speed I'm talking about, cuz this is far away the majority, of things that must be digital.
Yes high speed digital, yeah.
Yeah and the people who can do that are good at laminating high layer type boards, and very rare in our microwave or high layer board count - almost never.
- Yeah this is true.
It is two different animals.
So if a guy says I'm a high speed fabricator and I make RF microwave boards, that's a different capability than what I need.
Yes it's true. So let's just talk about high-speed digital so you're right, somebody who can do high layer counts what would you look for laundry-list wise?
Well at the top of the list, is boards like mine. If you're not making boards like mine, you're gonna lean on me, and I'm not ready for that.
Yeah good point.
Yeah it really is, that's my first thing, you're making boards with the same class that I want you to builm, if the answer is no I'm gonna go someplace else.
And I would say, and how much of their work is like your work because if it's a really small percentage that would make me nervous too.
Yeah but it's my experience that if somebody's making high count boards, that's about all they're making.
Yeah it's true, they kind of - they kind of aim at that. And they're good at it, they're busy.
Yeah and they're busy and that's what makes them profitable actually. So and that also you will see in the equipment set.
There you go, exactly - exactly.
You won't see archaic… you'll see the most modern tools that gives them the precision and...
Yeah exactly, a really good vacuum lamination guy can supply and will build a twenty four layer board with ten mill vias and 12:1 aspect ratios.
Yeah. And so you've gotta go find fabricators who are in your sweet spot.
Yeah I agree with that.
And so - and of course - if you're in it for a little while you figure out there's about six choices in the US.
Yeah there's - it's true - there's not a lot and as you're speaking those are coming to mind I won't sell for anybody today but they are relatively easy to find.
Now - and now just before we finish that - six years ago, there were none in Asia because they were busy making consumer electronics.
Yeah I'm interested in your perspective on that, because I don't really know what that is - if it wasn't kind of cookie cutter consumer. So what's the state of the ability in China these days?
We've got as good a capability in Korea and China as there is in the US.
I guess that's good news from a price point standpoint?
Yeah and it's bad news for the American laminators though.
I know I'm an American and I feel whatever but we gotta - - it is what it is.
Don't forget not so long ago we made TVs.
I know we made a lot of stuff.
It's the nature of the business that we go where the low-cost labor is.
Yes that's true.
Okay, now back to your trains. So always at the end of the podcast here, which we are beginning to wrap up here, and thank you so much for your time. I always learn a lot from you Lee. You are working on - this part of the podcast I call 'designers after hours' because my observation has been, a lot of people that I know that are pretty smart engineers and designers, have neat hobbies after hours. So tell us about your after-hours fun?
Well the one that you can see in the background - there's a lot of railroad.
Let's see it, can you flip your screen that way without disrupting us?
Oh there it is.
Can you see it?
Yip I sure can.
And the one you can't see is I repair vacuum tube radios.
You do what?
Old, radios vacuum tube radios.
No way.
Yeah.
Just for fun - who still uses vacuum tube radios?
Well we're starting to get Wi-Fi guys who think that vacuum tubes are the way to go. But I started out making my spending money as a kid, fixing the radios. I've always been in there you just may know...
I know.
-so I'm just back to fixing old radios.
That's kind of a fun hobby, but vacuum tubes - like that cracks me up.
Yeah you probably didn't know you can buy new vacuum tubes?
I didn't - I didn't but I was talking to someone recently and I - it cracked me up because I remember doing this as a kid so, is - remember going to like the drugstore - the hardware store and you could test the vacuum tubes?
Yeah, come on over I've got a tester.
No way - somebody mentioned that
- I was like whoa! Like my childhood came flooding back going with my dad to the store and sticking in the vacuum tube testers that's funny.
[laughter]
Yeah, good times - good times.
Well we're about out of time Lee, so thank you again for your time. And I know we could go further and further but I will share the link to your information about your books, and I will also share the link you shared with me for the design concept people that download white papers, and if you think of anything else just let me know and we'll put it on the show notes here. So we don't leave people feeling hopeless. We get them registered for DesignCon and get some papers in their hand, and get some books in their hands so they could do their job better.
One last thing we talked about I oughta mention, if you can - if you do those - what do you call the thing we did in Munich?
Oh AltiumLIve.
Oh yeah if you keep doing those I would argue you should start offering these training courses.
Okay, all right you heard it here from the mouth of Lee Ritchey.
I have to go show this to the CEO later - proof!
It's been my pleasure.
Thanks so much Lee. And we will talk to you soon again. This has been Judy Warner with the OnTrack podcast. Thank you for joining us and thank you Lee Ritchey, have a good day. Have a good day. Bye.
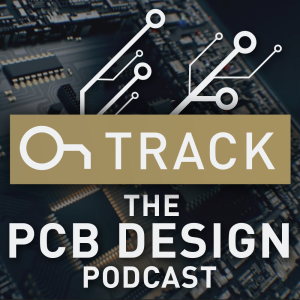
Tuesday May 15, 2018
Upverter and The Future of Browser-Based PCB Design
Tuesday May 15, 2018
Tuesday May 15, 2018
Making and checking parts is the most frustrating aspect of PCB design. Find out how Zak Homuth set out to change that and what is next for Upverter, EE Concierge and the future of PCB design in a browser-based setting.
Show Highlights:
- Why the Upverter parts library? Verified parts at scale, in a high-quality way.
- Verified parts - free to use for everybody coming soon!
- Verifying Datasheets, it’s a lot of work and at the heart of design frustrations.
- I wanted to take the magic of Github and Google Docs and create something for hardware designers.
- From concept to manufacturing in 20 hours.
- This is a conduit for bringing ideas to life.
Links and Resources:
Verified Parts on Upverter
A note about Verified Parts coming soon to Octopart
Indestructible pantyhose + Funny Video
Hey everybody, it's Judy Warner with Altium's OnTrack Podcast. Welcome back, we have
another amazing guest for you today but before we get started, please follow me on LinkedIn. I post a lot of things for engineers and PCB designers and I'd love to connect with you, and on Twitter I'm @AltiumJudy and Altium is also on Facebook, Twitter, and LinkedIn. So please
give us a follow.
Well today I have a really extra special treat for you.
Zak, I think I'm gonna destroy your last name so I can say Zak?
Yeah.
Your last name is?
Homuth.
Homuth - see I would have killed it. So, this is Zak Homuth, he is one of the - are you a co-founder of Upverter correct?
Yes.
So Altium acquired Upverter and EE Concierge in August of 2017. So a lot of people have asked me why Upverter, what was Altium's interest in Upverter, because it seems like sort
of out of our lane. So I thought I'd bring Zak in today and let you hear straight from the horse's mouth. So start out by - if you would Zak - just telling us about what is Upverter, and what is EE Concierge, and what you were trying to create when you launched that company?
Yeah sure, so Upverter is cloud-based, schematic capture and PCB layout. And what cloud-based means is, it runs in the web browser. You type Upverter.com into Google Chrome, it shows up and you can do your schematics, your layouts right there you know, order the
boards for manufacturing right from your web browser. You don't need to download anything, it's collaborative, which was kind of our big superpower for a really long time. Which is that a bunch of users can work on the same schematic, in the same layout, at the same time, in a very Google Docs kind of way. That's Upverter, and then EE Concierge came out of an experiment we ran back in 2015, trying to figure out what was the most frustrating part of doing a PCB design. And it turned out it was making and checking parts. And Upverter - until that point - had a shared global parts library and what that meant was every time I added a part, those parts were available for the community but without somebody checking those parts…
Yeah, that could be a nightmare.
-Yeah it was - it was really scary for people, they were spending a lot of time checking parts, they were spending a lot of time making their own copy of a part that was already in the library, a lot of that you know, wasted duplicates...
You can not have a messy library.
-Yeah and so EE Concierge grew out of that. It was our attempt to clean up and verify and guarantee the quality of the parts inside of Upverter, and so we built a small army of Electrical
Engineers all over the world. They work in an uber-like model where they can kind of log on, make a couple of parts, check a couple of parts, log off again. They can do it full-time, they can do it twenty hours a day, they can do it an hour a day you know, or an hour a week if that's what they want to do. And we built a machine intelligence to check all the work that they were doing to make sure that we had the best possible parts in the world inside the Upverter parts library and then, EE Concierge was born out of realizing that that's probably not specific to Upverter - probably every engineer has the problem.
Yeah there's that.
-so we built a plug-in for Altium Designer so that Altium users could leverage these verified parts which inevitably caught the eye of Altium and one thing led to another but - that you know that's EE Concierge. It was this idea of verified parts at scale, and then kind of outsourcing at scale, for electrical engineering. But in like a high quality way.
Right so, how many parts are in the library now?
Yeah so there's about a million-and-a-half parts...
Holy cow!
-in the Upverter library of those million and a half, about 275,000 are verified these days. And to
different levels of verified, some of them just have verified symbols, some have verified footprints. It depends on kind of what era of EE Concierge they were made in. But it but we've got about 25,000 like really, really rock-solid ones and they're the 25,000 that most people use.
That's awesome. So what's the plan kind of going forward, to get the rest of them? You said you have some kind of machine learning to help you verify that. Like what's the path going forward to get the rest or - you know million parts like you said - not everybody's using a million parts right? There's infrequent wonky ones in there?
Yeah there's kind of two answers to that. So how we make this maximally useful to the most engineers is similar to what Altium and Octopart did, after Octopart was acquired we worked really, really hard to make sure that Octopart was for everybody. It wasn't just you know
Octopart for Altium, it wasn't just parts for Altium, it was Octopart for everybody, or CAD, you know Mentor, everybody. So we're trying to do the same thing with the EE Concierge, we
want verified parts for everyone. So in the next couple weeks we're gonna launch verified parts on Octopart, so we're taking that 250,000 parts and we're putting them on Octopart free for everybody to use. And you can download them in EAGLE, Altium, Upverter. We're working on Mentor, I think we've got Cadence or CAD as part of that, so like in any format, free. Just find them, download them, use them. That's what we want so that's kind of one avenue for the EE Concierge. And then the other is - this is a little bit more kind of futurist and out there answer -
That's okay.
But if you were gonna build an AI that could read data sheets, first thing you would do is have a
huge number of people read data sheets and enter that information very reliably into a piece of software, so that you can check it all. And so the kind of like dot, dot, dot - is we think if we get good enough at doing EE Concierge, and we do it for long enough, potentially we can read data
sheets with a computer, kind of our self-driving car version of the Uber model.
Like and then part of me goes; and you're assuming the data sheets are correct?
Yes it's a real problem and so we had to do a lot of stuff at EE Concierge to catch like, if TI ships a datasheet, and the datasheet has a problem, they'll rev the datasheet and then they'll rev the datasheet, and then not only that, but they'll reuse packages and they'll reuse symbols and the reuse bits and pieces of that datasheet across other parts that they make. We had to build a ton of stuff to be able to catch when they made an update to one datasheet and apply those changes to all the other parts to use the same bits and pieces of the datasheet. It's an ongoing thing - it's a hard problem for us but yeah it's a real - it's a real issue.
Well it's like amazing to me that we're here like...
-at all [laughter]
I mean just from being in like - I started in the industry way back in the 80s - and like everything was done by hand and all that, so just that we could possibly even get to that point - it's just so sci-fi to me - but it's amazing, it's so great. So tell us a little bit about how did you get it, tell us about your personal history and how you went down the Upverter rabbit hole and popped up here.
Yeah sure yes, so I was kind of into software and computers before that was a cool thing I was on the internet pretty early, I was I think five or six when my dad brought home you know our first computer and you know I tore it apart and tried to figure all that kind of stuff out. I was building video games when I was seven, and...
-of course you were [laughter]
-all that but I studied Computer Engineering at the University of Waterloo in Canada and Computer Engineering is a little bit of Software Engineering, a little bit of Electrical Engineering, and then you know all the physics, and boring, normal engineering stuff that you have to do [laughter]
Waterloo is a co-op University and so every four months you'd go to school, and then every four months you'd go get a job, and so I got a bunch of these cool jobs, kind of all over the world, I used it as an excuse to travel. And so I worked in Canada's capital Ottawa, for the insurance company that insures the majority of Canadian doctors, and so they had some really interesting data. And I built a search engine and a database for them to to be able to search when wrong-side surgeries happen right, you know when they operate on the wrong lung or whatever. I built a search engine so that doctors could figure out the root cause of some of this error because that was important for the insurance company to try to prevent this from happening. So I did that, I worked in Germany for IBM, I worked in India for Infosys, and then I got a job in Waterloo working for a company called Sandvine and Sandvine build what are called deep packet inspection - telecommunications service. And so ISPs would install these in their network and it would sit between their subscribers - the people who use the Internet and the rest of the internet - and it would look at all the traffic that flowed through the box to try to figure out how much is Skype, and how much is YouTube, and how much is pornography and Facebook and everything else. Because if you think about it, ISPs are kind of like the water utility. They know that they sold so much water but they don't really know what the water was used for, how much is watering lawns right, and so we were giving ISPs that kind of intelligence. Anyways, I started off as a lab tech, I tore the boxes apart, tried to figure out why they weren't working, put them back together and made them work and I kind of worked my way up to actually designing the box. So I designed two of them for Sandvine before quitting, and I quit because I was really frustrated that on our side of the cubicle wall there were ten of us working on the hardware that was so essential for this company to exist - but on the other side of the wall there were 300 software guys who had Git, and they had version control, and they had collaborative tools, and they could test their code by pushing a button on their computer. I had to carry a 120 pound server around a building, and use screwdrivers and shit to like - and that's, that's part of hardware - I never wanted to take that away from hardware but it felt like it could be easier and you know. We were using Mentor Graphics’ tools and I was frustrated by the archaic kind of 80s feel of it all you know?
-yeah.
I used a Mac at home - I couldn't use the software on my own computer if I wanted to, and I was trying to build stuff at home and this was kind of before IoT was like a thing. This is right before Arduino, before all that stuff. But I wanted to do that stuff at home and it was just so hard to do any of that you know from my Mac, from home, without a huge budget - it's an endless amount of time and at the time we were seeing cloud tools like Gmail and Google Docs and Github, kind of emerging and so I left, because I was pretty frustrated that if this is like the state-of-the-art, if like one of the most complicated telecommunications servers that anybody had built today, was built by some punk kid in this office in Waterloo, working mostly alone, using tools that felt kind of clunky and out of date, like there has to be something better than there and and so we left to build it and it was really no more complicated than: can we take some of the magic of Github, and some of the magic of Google Docs, and build a tool like that for hardware engineers and maybe it takes forever to disrupt Mentor, or Cadence, or Altium, or any of the big guys that have been at this for decades. But we assumed there were enough people like us that just wanted to spend two hours on a Saturday afternoon designing a piece of hardware. There must be something we can build for them - a little bit like Google Docs right, it doesn't have all the features, you can't make fancy tables, you can't do it all, but it's slowly taking over the world and we wanted to do the same thing for hardware.
Well I think you point out something that I really noticed. It seems like there's a block of people that are like my age, the old 80s people and we've kinda just built upon old... and then there's the next generation that were five, okay I was 20 when I got my first computer, you guys kind of grew up with these things in your hands, and it I think it's kind of hardwired in your brain. So I think, there's more efficient, better ways to do things and we are building on old Legacy stuff, so sometimes we just can't see it. And so I think it's really very exciting because I think people are gonna be: oh thank god, somebody's built something modern you know, on the cloud that thinks, and operates you know, which I think was the big draw actually for Altium, which we can talk about that a little bit later so - so the Upverter I was going to ask you, but you've
answered it partially, is why Upverter? Out of the various other things you could do, why didn't you go into - I don't know - you have a very entrepreneurial spirit, so there's lots of things you could have done. Like why did you pick this one thing?
Yeah, so when we started Upverter, I quit my job before I knew what I was going to do. I knew I wanted to build something, I knew I wanted to start a company, I knew I was kind of done with working for the man, and I recruited two of my kind of college roommates. So these are guys that went to Waterloo with me. We lived in this terrible, decrepit, run-down house next to the campus, near the engineering buildings. You know we lived together, we worked together, we did our co-op jobs together we - you know we were thick as thieves. But I called them up and I said you know, how do you feel about quitting your job and like doing something new? And they both quit like the next day and so we got together in this old decrepit student townhouse and we wrote down hundred ideas of things that we were excited about, things that we were passionate about, things that we believed needed to be fixed. I was shouting loudly in the corner that we needed to build this - this hardware tool that was the Google Docs for hardware. That was my passion, that was what I was excited about. But Steve and Mike, they had some cool ideas of their own. There was a bunch of stuff that they wanted to build that a lot of it is actually been built, and a lot of it ended up being quite substantially large companies. So our second pick our kind of the front runners....
So what was on your cut list?
-Yeah so the second pick was, we wanted to build drones, and this was before drones were
cool. We wanted to build very large-scale drones that would be towed behind container ships and provide a bigger radar footprint than the ship can have itself because it's so close to the
water and you'd do this for a bunch of reasons. But the really burning reason at the time was Somalian pirates. If you could fly one of these drones above a container ship, you could get ten or a hundred times the radar footprints so you could really move the ship before anything bad happened. If you wanted to. Anyways, a company ended up doing this, and started right around the same time that we did and ended up being acquired for something on the order of two or three billion dollars and so we missed that one a little bit. But but we just - we just didn't even know where to start on it. But it was - it was the second pick.
That's crazy.
So we didn't really talk about this ahead of time, but you know I think I know around the time AltiumLive went down, there were people, kind of gurus in the industry, and they're like so -
ultimately it was in October, so and Altium acquired you guys in August and I remember some people, like it was like all the buzz, like what are you guys doing? Why that customer? And
so what I want to talk about is - who uses Upverter? I'm thinking makers, hackers, hobbyists and maybe EEs that want to be startups or do personal projects - like who do you think the Upverter audience is, and how's Upverter going to serve them, and how many people are on Upverter? Tell us about your ecosystem a little bit?
Yeah so it's the 'misfits' mostly, these are the guys...
The land of the misfit toys! I like these guys! It really is, these are the guys that are unserved by the eCad industry at large, they're using operating systems or tool sets, or computers that can't run traditional eCAD, they're in funny parts of the world, they're students, they don't have electrical engineering degrees. In lots of cases they're the weekend warriors that can't steal a copy of the eCad that they use at work and bring it home, they're makers and hobbyists and hackers yes, but they're also - you know we helped some Nigerian kids put their country's first satellite into orbit...
That's cool!
-and they couldn't have done it using traditional eCad tools.
That's cool I love that!
-Yeah we - some of the first augmented reality startups were built using Upverter. Like kind of odd stuff like that where you couldn't necessarily use a traditional eCAD tool, you couldn't necessarily iterate at the cycles that one of those tools would let you you iterate at. But also like children on the internet, and you know Mac users and all that kind of stuff where you just can't use a traditional eCAD tool.
Right.
But misfits mostly, we think of them as kind of an - not really the next generation of electrical engineers - but but very much a different breed, a different type of 'doer of electronics'. Well it is kind of grass roots though I think that we are gonna see more amazing things, like drones being dragged behind boats, that are gonna come up organically and kind of like you, I think you're the perfect sort of head of this brand, like 'yeah dropped out of school, this wasn't working, I don't like it whatever, so yeah I can see that happening over the next five, ten, twenty years. I think we're gonna see amazing stuff out of that space. So how many people, I don't know how you quantify that, have used Upverter, or use Upverter or actively log on a month?
Yeah-
So how do you do that?
At the time we were acquired by Altium, it was a little over 50,000 people used Upverter,
they use it in a very 'bursty' way, they'll show up - they'll work frantically for two days - ten days a month, and then they'll disappear and we won't see them for a long time ,and then they'll come back. And we correlate that with their kind of idea cycle right. They'll have an idea, looking very excited about the idea, they'll work on the idea, they'll do that thing, and then they'll go away you know, probably because they built the thing and they want to play with it. It could just be that their focus has moved and they're they're onto something new, and then we'll see them come back, six months a year you know, a couple of days later - depends on -how much time and energy they put into their ideas. But that's okay for us, like we we never aspired to be the daily tool like somebody like Altium is, like we aspired to be this conduit for people to bring their ideas to life and you can only be as useful as people have ideas right. So if you have an idea every day, we can be useful every day.
Most people don't - most people have inspiration quarterly, or a couple times a year and that's
that's what that looks like. We have many thousands of monthly active users so thousands and thousands of people log on every month, to work on their ideas, and their little projects. And the average project is worked on for quite a small amount of time, relative to you know, what you would expect from other eCAD tools. We'll see products going from conception to manufacturing in like 20 hours or less. And so that's pretty amazing, if you consider that's two or three days of work.
That's unbelievable, so if - you said something earlier that I wanted to ask you about and that was - you mentioned that people can go into manufacturing. Do you have sources like fabrication, assembly sources that are related to Upverter?
Yeah, and we've had this in a couple of different forms over the years. We've had, what we like to call the print button, kind of refactored a couple of times inside of Upverter. We're currently refactoring it again right now, and part of that is as a result of the acquisition. We have another
company we acquired, Siva, who does a lot of stuff in the manufacturing space, and we're refactoring our print button to use some of their technology and would be better linked up with Octopart, so it should be a better experience for our users as a result of doing it. But yeah,
over the years, we've had a button, you click it, you give us your credit card number, and a couple days later something shows up in the mail which, which is what you designed.
Awesome.
-And we'll do that again in the very near future.
And it - was that assembled also, or just the bare board?
-We used to just do bare boards, and then we experimented with assembly for a little while, the new - the newest, latest and greatest version - that we're working on right now will be fully assembled and it'll probably include whatever enclosure your device fits inside.
Oh my gosh, I mean I'm like ridiculously excited about this.
Yeah, it's gonna be pretty cool.
Okay so I always ask - I don't always ask this - but I wanna ask this now. Okay, are you a geek or a nerd?
I - - geek, but I don't know why. I don't know what the difference is really...
It's just your gut - open question.
Okay, geek.
-I think you're a geek cuz I don't think there's - I don't think - I think... whatever [laughter]
It's something we ponder here on the OnTrack Podcast. What is a nerd and what is a geek, we've...
-big questions [laughter]
We've decided what geeks are cooler; nerds seem more like, at least to me, physics - like...
-okay
-children 'Coopers'
-oh Science...
-yes more deep on the science side but this has not been proven, so if anyone wants to comment below and tell us what you think a geek and a nerd is, we're all ears. So but you were geeking out there, this is why I stopped you.
-Okay
-cuz I'm like, oh you are like totally geeking out and I'm tracking with you man, I'm like, oh this
is like - we're having a geeking out moment right now [laughter].
So I was talking to our Head of Operations the other day, and I was just saying that during that AltiumLive, people were asking why would Altium, a professional e-tool, pick up Upverter,
and basically I think Altium has a vision to kind of embrace every level of PCB designer and also embrace and serve those 'misfits', those marginalized, or that don't have access you know, those that can pay for Altium Designer and they do it professionally, well great...
-Yes
But that we want to serve the wider community. So I was asking Ted Pawela about it, and he was saying - and I just wanted to get you to chime in here - is that sort of what we were
talking about earlier - is that cloud - I mean a lot of software programs are going to cloud-based.
You know there used to be security issues, but they've tightened those up - so technology is
moving towards cloud based, and if we don't sort of pay attention and go that way too, I think will be sort of left behind and that, also the next generation, or the new, or the upcoming, or the
grassroots, organically-grown innovators, I think are gonna - like you - are going to be cloud natives right, and are going to be frustrated, like you were when you were at Waterloo. And to
also meet those people where they are, not expect them to cough up the money or fit into our model, but figure out where they're going, and what their model is, and what their needs are. And so that was - that's what I think Altium saw as very attractive - seeing Upverter as a huge enabler to serve that community. Would you agree with those?
Yeah - so when we were in the kind of acquisition process with Altium, I spent a lot of time on the phone with Arum, our CEO, talking about kind of his vision for the future of Altium, and his vision for the future of electronics, and one of the things we talked a lot about was making
Altium synonymous with PCB design. And part of that is, you can't just serve the tradespeople in the mainstream - there's a million people in their basements that have ideas, that want to invent stuff, and those things include electronics. You need to be there if you're gonna be synonymous with PCB design and so - so a big part of it was that. But then also a big part of it is like, the world's changing knowledge work's moving to the cloud, is becoming collaborative you know. The Windows operating system may or may not be the operating system of the future. You look
at mobile, you look at tablets, you look at what's happening with Apple, and you know all of that. They're you know, there's a version of the world where Altium is constrained to only serving a chunk of a market because of the way we built our technology, and so I don't know, Arum obviously hasn't said any of this, but there might be a little bit of this that it is an edge on
the future.
Well I can tell you that personally, it's a really exciting place to be, because I love that. I love
that you know, I interact a lot with University students and that. But we've also gone to you know, I went to the New York City Maker Faire and to see what people are developing is so
exciting. So to be able to serve that community, and see what they come up with, is just a blast. Like I love to see it, and especially like you had a start early with IoT like it's gonna explode what we can make. And like I said, they're gonna be making it in their garage, in their basement, or their shed...
-It has to - it has to explode. Like we're talking about you know billions of devices all over the world...
-billions like capital B.
-yeah like a hundred or two hundred thousand professional electrical engineers aren't gonna invent billions of devices; we need to include a bigger chunk of the world, in the design
of these things and you know, and then
- that's not to say the tradespeople won't have their place, like of course they will - but we need grassroots, we need people building stuff in their basement. And we need it at a scale that we've never needed it at, more than now.
I know, I'm really excited about what you're doing - I'm really excited what you guys developed, and I'm so excited that that you're part of our team. So sort of wrapping up here, I want to sort of segue into what I call 'designers after hours.'
Okay.
So, I don't think you have any after hours, you might get to have a beer after work once in a while. This guy's from Toronto and he's here an awful lot and I don't think you have any after hours right now, but if you did have after hours Zak, what would you do, or what do you like to do?
Yeah well my wife and I bought a house in the Canadian wilderness about 18 months ago, and so my after hours, for the last 18 months, has been turning this kind of run-down cabin into a home for my family and so I've been watching a lot of YouTube videos, and buying a lot of power tools, and trying to figure out how to do all that stuff. But when I'm - when I'm here in
San Diego, and when I'm stuck here for the weekend, [whispers] I buy a couple videogames [Judy laughs] that's - that's kind of my thing.
Okay, and here's another super fun thing about Zak. I want you to share about - his wife is also an entrepreneur. So tell us about your wife's business cuz that's really fun.
Yeah so my wife is a very successful entrepreneur, she started a company when she was quite young, that did eCommerce, and she sold that. And then she ran another company which was for angel investors, and she sold that. And then she did something with hair extensions, and
her new thing is called Sheerly Genius, and Sheerly Genius makes indestructible pantyhose.
And you can hang a human being from stuff with nothing more than a pair of pantyhose.
There is a video, we are going to share the link of Zak, hanging his wife... [Zak laughs]
from a second-floor balcony with pantyhose - it is a real thing.
It is a is real thing.
Okay, so what are the materials?
Yeah so it's heavy molecular weight polyethylene, which is what the fiber is made out of, and it's special in that it's incredibly strong, but also a low denier - or denir - I'm not sure how you're supposed to say that word - but so it's a 30 denier fiber which is what you can make hosiery products out of, but it's incredibly strong. It's like the the strongest dental floss you could
possibly imagine, and she found a way to weave this into pantyhose but also to like wrap lycra in it so that it's stretchy - but it's still sheer, but it's like incredibly and ridiculously strong, so it will never run.
-It's like 'superhero pantyhose' you guys really you're gonna have fun watching this video that we'll connect below, and we will also connect to Upverter, and EE Concierge and Zak's LinkedIn profile, if you'd like to connect with him, and any other things that we think that..
-Sounds good [laughter]
-you might want to connect to. So Zak, thanks again.
Thank you.
-I'm so looking forward to working with you and seeing what we kind of collaborate with and
sort of reach - reach to the grassroots-end of the design community.
-Me too .
I'm really excited about it so thank you so much for joining us.
Of course thanks for having me.
This has been Zak Homuth, is that close enough?
-Yeah.
Zak Homuth and Judy Warner with Upverter and Altium, and EE Concierge. And we will
look forward to seeing you next time.
Until then, always stay on track.
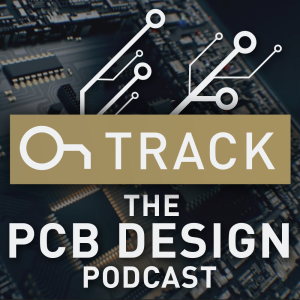
Tuesday May 08, 2018
David Carmody’s DFM Report Integrating Design and Assembly
Tuesday May 08, 2018
Tuesday May 08, 2018
Do you know your fabricator? Meet David Carmody, Division Manager and CID+ at San Diego PCB Design. As a service bureau, San Diego PCB works on a variety of PCB design projects. Learn why David says, “You gotta know who you’re fabbing with” and how he is using DFM Reports to help customers integrate design and assembly in this episode of The OnTrack Podcast.
Show Highlights:
- Memorable designs in telecom space and the development board for Dragon II, a SpaceX project, for the capsule they hope to take to Mars
- Package on packages, dropping the DDR - removing the burden on the designer
- Palomar advisory program - student programs for learning PCB design
- San Diego PCB acquired by Milwaukee Electronics, EMS and Engineering Services
- DFM report - a “stoplight report” for customers before starting build - customers love it and it fixes issues proactively especially with packaging
- A lot of engineers don’t know the manufacturing side and DFM reports can help with this
- “You gotta know who you’re fabbing with”
- Will additive manufacturing processes be the answer? The business model remains to be seen.
- 3D printing - you can’t print copper (yet)
- Altium User Groups - have Altium in the title but we don’t run them! We’d love to support.
- Altium User Group in San Diego is very active and supportive.
- Advice from a Pro: Always keep learning, it will keep you fresh and make work more fun.
- PCB design isn’t the only practice David has mastered - he’s a martial artist too
Links and Resources:
David Carmody on Linkedin
San Diego Altium Users Group Website
Tecate, NM Manufacturing Facility
Hi everyone this is Judy Warner with Altium’s OnTrack podcast - welcome back. Once again I have another incredible guest to speak with us today, but before we get started please follow me and connect with me on LinkedIn. I try to share a lot of things relative to engineering and PCB design and on Twitter I'm @AltiumJudy and Altium is on Facebook, Twitter, and LinkedIn, and if you'd please subscribe and give us some comments so we know what you'd like to hear more about that would be great.
So today again we have a great guest which is David Carmody of San Diego PCB David has a new title now: he is the division manager and he also has a CID. So David, welcome and thank you for joining me here at Altium today. So, we've known each other for a little while and I've had the benefit of being over at San Diego PCB and looking over your shoulder to some pretty wild complicated designs. So tell us a little bit about your day-to-day from the perspective of design bureaus and the kind of work that you see?
Okay, we do get a lot of different designs, a bunch of varied designs, so we see a lot of military application, we see a lot of new technology - wearable technologies and things like that as well; it is pretty much all over the map though. I mean we get a little bit of anything and everything just because of the the nature of the service entity. A lot of the more upscale - so to speak -designs are the real nanotechnology sort of stuff where we're cramming a ton of the little parts into a board that's less than a half square inch total in size, or we're packing everything into a big housing that has to get heat out somehow because, I mean, we're sending up high output micro processors into into space and there is no airflow so we need to get the heat out in other ways. So there's a lot of that sort of stuff that we do get to see and and play with and and learn from as well.
I think San Diego is kind of a neat place to work too because there is a lot of Defense here and there's also call comments and telecoms, and even in our local area, although I'm sure you see work from all over the country? We do we also have kind of some neat things right here in our own backyard.
Oh yeah.
So across that variety what would you say some of your more memorable designs would be?
I was gonna say we do have have some telecom stuff that's gone on and those are those are fun boards just because they've got big processors on them and lots of high-speed lines, things like that. Most memorable, for me personally, would probably be a SpaceX design. I was able to design the development board for the Dragon 2.
Oh my gosh!we’re not worthy! Do you mean the dragon heavy that they just launched - the second Falcon that ever went?
Yeah the the Dragon 2 which is the capsule that they hope to take to Mars one day.
Oh so that that one!
Yeah. I did the development board for that so it's just basically a big processor board with a lot of RF communications on it and things like that and they're breaking out all the other boards from that, and that was a fun project. I got to be a part of that was really cool.
Yes, I sold some R4s to them and got to go through that facility a few times so I'm like a weirdo SpaceX geek and then we also sponsor the hyperloop pod teams for universities. So Ben that's helping us here with recording this; he and I got to go up and hang out at SpaceX and see them do that.
I saw some of those pictures.
So sorry for being so weird but I’m a kinda SpaceX geek.
Yes, it’s been fun. We do have a couple of space contracts we've worked directly with NASA and MIT and also with Space Micro so, we've definitely learned our way around the Class 3A specifications and we know that inside and out.
Not easy, really dense stuff. So you talked a little bit about the nanotechnology, is that where you sort of see the bleeding edge going? What are the the most challenging designs?
I was gonna say the packaging is actually changing quite a bit, we're seeing some things that the packaging is doing that's well, quite frankly, I'm not terribly happy with because it takes away some of our place - but things like package-on packages is coming around. That's really cool technology, I mean, you put down the DSP or the PGA - whatever it happens to be - and then you can drop the DDR right on top of it. There's nothing for us to do; it's purely an assembly process, if that.
Wow.
So that stuff is definitely interesting and removing a burden, so to speak, on the designer but yeah, then the package size itself is just getting smaller and smaller. We're being pushed into HDI technology more and more often. 0.3 millimeter BGAs are pretty common, 0.4s are all over the place now. I mean even big ones. So the 0.3 three millimeter BGA's are getting common. I've been able to work on things as small as 0.15 millimeter though. So it was a flip chip sort of design where we're pushing the envelope on that thing so it was experimental, and things like that. I don't think they actually ever built it was costly, that whole get up then but that's that the trend we're seeing. Just everyone's pushing the package design more and more all the time.
Something I noticed I took a peek at, even though I've known you for a while - I took a peek at your LinkedIn profile. I don't know that I'd ever done that and I like to ask people a lot, how'd you get into this industry? Because most of us didn't start out this way, but we ended up here. So did you start out there? I notice you took courses at Palomar College which is local here, and I don't know if they still do, but they used to have PCB design courses?
That they do I'm actually on the Palomar Advisory Committee right now and we're helping to restructure some of that stuff and try to join up a little bit more, their student base through there. They've got a pretty good offering right now to make it better but yeah it's still active and it's it's one of the few places that you can really go for formal education. So it's good that they're there keeping it alive, and not just keeping it alive but updating it.
Right, and that's kind of where you started out was it not?
It was.
Or did you just join them recently as part of the Advisory Committee, or did you start learning design there?
I did technically start learning some design there but it was an accident really.
[Laughter] See, my point is, we didn't do this on purpose.
No absolutely not. Basically I had gone through their program and really gravitated - back then at least - 3d was just emerging. It was all in AutoCAD, there was no such thing as SolidWorks, it was just coming around. So I ended up jumping into AutoCAD 3d mechanical sort of stuff and and did my degree on that and then got on to nothing but waiting list after waiting list. So at that point I was talking to a guy that I was working with, he goes: call my brother in law, he does something in computers. And I talked to this guy, he was a PCB designer at Intel - I'm actually working with him now, we recently hired him, but yeah he's working out in our Arizona office but he gave me some excellent time; never actually met him face to face at the time but he gave me some phone time and told me what to look for, and what this industry had to offer and gave me a couple of places to go after. And I went after both - I ended up getting an offer from both of them, but I liked the smaller business so I took that side of things and spent 12 years back at an ‘unnamed company’ as the Design Manager.
Laughter, well not as awesome as Sandy Opie…
Well I don't know, it hasn't been a year yet, so San Diego PCB was acquired actually by Milwaukee Electronics right.
Yes it’s been about a year and four months now, time flies. So Milwaukee is a really capable EMS shop up in- remind me?
It's Milwaukee.
Oh is it Milwaukee!
Yes, their primary branch is in Milwaukee - okay this confuses everyone - because we have multiple brands out there now. So our Milwaukee electronics brand has most of our engineering services and the EMS as well there. Up in Canby, Portland Oregon, now that's where we have Screaming Circuits - that is our quick term prototype house and there is also EMS there as well. Most people don't know that but the factory shares the floor for that and then we also have - actually it's also called Milwaukee Electronics - despite that, it's in Tecate Mexico but they've got a huge building down there and they're there literally clawing the mountain out from being behind this building.
Right I've seen photos of it, it's really quite lovely, at least the photos are, it looks really modern.
It's a very impressive facility. I was able to visit there and I had seen pictures of it when the shop floor was was only 50% filled; that place is full and like I said they're calling out the mountain now behind them, so that they can add on and I think gain about 30% more square footage. Growing like crazy.
How has that been, that acquisition, for your customers and for you, there's obviously synergy there between the two firms so how has that been for you?
The two companies, the acquisition itself was great, Milwaukee Electronics is a fantastic company to work for. I really enjoy all the people that are there. The synergy has taken some time to get things rolling, but I'm starting to see a little bit of a snowball effect and so we're starting to pick up some momentum to where Screaming Circuits is sending us customers back and we're sending them customers in and we're starting to get a collaborative database of the customers going right now, so that we can take a more active role on that and and really sell to both sides. There's been a little bit of crossover, but like I said, it took probably six months before I saw even the first crossover and right then another one happened, and then another one, but now we're up to where we're getting about at least one customer a week or something like that, that's doing some sort of crossover. so it's definitely building up speed. But it's still going to take a little bit more time.
So since our listeners and watchers here will are mostly engineers and PCB designers, what do you think the benefit is to collaborating design to EMS - what are the benefits you think that occur there?
When you're collaborating, one of the biggest things that's coming out right now, is basically DFM report that we've been doing, it's something that I've been doing for years. Say a customer has their own design team, they want me to be a second set of eyes - something like that. I'll go through the design either on a cursory level if you just want me to look at DFM/DFA sort of issues. Do you want me to look at your circuits, do you want me to look at this whole thing - make sure that you placed it correctly? I coined that a ‘stoplight report’ a long time ago, and basically it's just - we give a nice little green note if it's informative only: this looks good it was done right, give a yellow note if, hey you might want to look into this, you might have some potential issues or, hey this part’s hanging off the board edge you're gonna knock it off, this needs a correction before it goes out - and those are obviously the red items - so customers seem to love that. I mean it's really easy, real clear-cut. They can kind of skim through it, hit the items that they want and that is really building up some speed right now with with a few customers because they've had an internal source for a long time. They've been using Screaming Circuits forever, but Screaming Circuits is going: okay you're going into bigger yields, you need to fix these sorts of items - let's fix them ahead of time and that's what we're being utilized to do.
That sounds absolutely incredible especially now, because in the marketplace so many engineers are laying out their own boards. They may or may not have time or access to spend a lot of time with their fabricators our assembler, so I think to have that sort of oversight would be very welcome. I don't know if that's what's driving it or just having a second set of eyes what do you think?
Probably a bit of both, I mean the engineers obviously get EMI and and EM theory, they do that really well, so they they always lay out the board well for that. But they aren't necessarily the best packagers, most PCB designers are puzzlers so, we do the packaging portion real well that's what we like to play with. But if you’re a good PCB designer you're going to know the EM side and you're also going to know the manufacturing side. A lot of the engineers don't know that, so they don't really look at that. I mean, I've been given boards that were completely routed and they said: rip out all the routing because this guy did it with 6mm vias with a 12mm pad on an 80mm thick board and so, it's just wrong all the way around. And placement wasn't bad on that…
But the aspect ratio is the killer.
-and he used decent trace widths, but I mean, the most problematic piece of the board, and he killed it.
And like it's a good thing that companies like Altium and other EDA companies make such powerful, great software - but there's no place in the software that says: no, stop dummy, you can run DRCs or whatever, but it won't necessarily flag it for for DFM if your aspect ratio is off or whatever, unless you've turned those settings on or off I can imagine right?
Yes but you can still improperly program DRCs too, you can say: hey I want 1mm holes on this board…
I've heard you and Mike Creeden say that a design tool is only as good as the designer.
-yeah you absolutely need that and I mean, someday in the future would it be great to see the tools incorporate that sort of stuff? Yes, but at the same time you’ve got to know how your fab works too…
And you don't want to limit yourself either because you could potentially create self-limiting things that are really irritating...
-oh yeah.
So I think we're gonna just keep giving you powerful tools and you guys have to work it out.
Yeah I mean, we can just zoom up and zoom up and, hey that via looks plenty big enough to me, I could put my fist through it, but not in reality. The packaging thing that I was referring to earlier that is just starting to drive this industry just because of big 0.4 millimeter pitch BGA. I'm working with a fabricator that can't quite do the the latest and greatest and all of a sudden that pattern starts to become a challenge that’s almost impossible to break out.
Right yeah I don't know where this train’s going…
Yup I don't know - it will stop somewhere at some point…
I know, I know, except it seems like we just keep creating some breakthrough so I'm keeping my eye on things like additive manufacturing, whatever we could do it 1mm, controlled trace and pull it off but there's no clear front-runner.
Yeah, the additive processes are very interesting, haven't seen anyone really start pulling off a business model out of it. The 3d printing technologies is also very interesting but you can't print copper unfortunately, so they can't - yet at least - so there's some major hurdles there too that they have to go through.
It'll be interesting. Well I wanted to shift gears a little bit because you, along with your colleague Randy Clemens here in San Diego, run a really solid Altium user group here and for those listeners that don't know this, Altium User Groups, they have our name in the title but we don't run them - they're completely run by the users, for the users they're very democratic and we just lend support and it's something that we've been talking a lot about here, is that we would like to grow the user community and help people launch groups. So can you give us a little bit of background and give us the do's and don'ts maybe, if people that are thinking about starting a local users group from what things have worked, when things maybe haven't worked, and how do we get more people to launch user groups?
Just sign up - just for a little background on that - there was a user group that was here for quite a while that was run by Bill Brooks and it had some traction, it was running for quite a while and then either the community or whatever, started to kind of drop off a little bit. Randy and I saw that as a bad thing basically, and we talked to Altium, talked to a few people here, and then put together a general terms for the the group. Randy has always done Google boards, the blog and stuff, so he's very good at that, he's got a pretty major Altium tutorial board actually that's out there. So he took some of that and ported it over and turned it into a San Diego Altium User Group Board, you can just google that: San Diego Altium User Group and you'll find his board. If you sign up you'll get meeting invites so it's really that easy. All of our IP, as it were, is all up there and and I mean fully freely distributable so anyone can go ahead and take that as a template and start porting it over. Randy would probably help if anyone asked to set up or clone a board but Altim is really great on this thing, they're really helping us out, they help promote it you guys are actually doing lunches for us and all of that, so we really, really appreciate all that support. Lunch is a good way to get people out - just feed them and they will come.
Exactly, you feed them and they show up. So we were restarting the group, it had a little bit of a slow start and it's kind of typical. I think we had all of three people show up once plus the the huge group of Altium group and San Diego PCB group because we host the location but no I mean our last last attendance was in the 30s somewhere, so it's it's doing real well now.
What do you think the benefits are to the users that participate regularly?
One of the big things is we always bring Chris Carlson out for new updates and stuff so we can see things as they're coming out. He gave us a wonderful tutorial on 18 not long ago, really to help us all dive into it as as the interphase changed.
I thought Randy was gonna eat us alive - he came out he's like yeah bring him - he had a slide deck going, and ‘what about this?’ God bless Chris Carlson, our senior FAE, he addressed most of those things and just said, no Randy we just moved it over here, it's just over there and we tackle most of it. But what I really appreciate is that Chris actually took four things back to our R&D team, and I think that kind of real-time feedback, it helps us make better tools right? And if we make better tools we sell more software, it's not rocket science right?
Right and we're happier designers…
Right your’e happier and you’re productive and so I think it's a win-win and I think Altium is doing a good job culturally. So say you were in... I don't know... New Hampshire okay, and you knew there was a pretty good-sized design community what would you say the first steps would be to get something going?
First of all, probably to clone that board that we've already got…
And we will share this, by the way, in the show notes and we'll share that if you want to go take a look at it, because Randy has done a good job of kind of making a charter, it would be a good model to share.
-so it's a fairly basic charter but yeah, clone that board, start marketing it against that, call Altium…
Me, call me I will help you.
-so get them to put it out in a newsletter and a blog or something along those lines so you can start that foot traffic and then invite your buddies, invite your friends and get them to do the same.
I interrupted you there, so you said that Chris came out and you got to see the latest and greatest, Chris did a good thing on showing you AD18 - what other kind of benefits do you think the users see over time?
I mean we've already kind of hit on the the dynamic feedback and that's obviously great information, but just the user-to-user help is always nice too. I mean I've had people come in with a laptop and and open it up and go, look I'm struggling over here, what the heck do I need to do? What rule do I need to write to make this thing work right? And we can just basically rub shoulders and get things moving and get a workaround if it needs it just to move it along.
Well I've been really impressed since I've been down here for about a year now and just seeing the group it's just very active and it seems like a really healthy thing and yeah all I get to do, is use my card and buy you guys lunch and if you want a speaker we’ll send one, if you don't want one we won't interfere so I think that user-to-user and that you guys really get to own it, is sort of a powerful model because it's not like we're going to come down and spring a free sales pitch...
Yeah well, Altium doesn't go in they're not salesy.
Yeah but we try actually, not to do it.
No, it's been fantastic for that.
Well I wanted to bring this up because you and Randy spoke at AltiumLive and Randy took a little part of his time speaking to talk about the Altium user groups and I was so surprised! I'm like, well you can spend your time talking about that if you want Randy, but I didn't think there would be that much interest - but I happened to pop in the back door just to see how it was going and people were really engaged and then people came and talked to me after. I think there's kind of a hunger to do it. I'm just wondering... I just wanted you to share with our listeners, if people did want to do it they would see, oh here's some steps to take because I don't know, though, that maybe we've done a really good job of advertising it because we do want to stay out of it, we want to contribute but not inserting ourselves into an organic user’s group. So, thanks for sharing that part.
Hm-mm yeah, for the AltiumLive, Lawrence Romine asked Randy to do a little bit of a spiel on that and yeah, there were a lot of people from LA that sounded like they were going to be starting their own, or a couple of them, depending on the demographics or Geographics up there and then there were quite a few out of state as well that that sounded like they wanted to start one.
I went to one in Utah, which I guess has been going on for a while. So, I got connected with someone actually at AltiumLive and we ended up connecting and there was like 80 people there to see Ben Jordan talk about AD18, I'm like okay, Wow! 80 - it was huge, but I think that group has been very active and been around for a long time so it wasn't like a new thing and they actually come from Salt Lake and south of there, so it was almost like two combined groups. So anyways, thank you for sharing about that. Any final thoughts?
Nothing that I can think of right off the top of my head.
Well thank you so much for coming in today…
-Thank you
You’re a good sport and we really appreciate you in San Diego PCB and thank you for sharing. Oh one thing I wanted to ask you was because the upper-end (age-wise) is starting to kind of age out in the industry and we're getting new ones coming in, what is one - since you're sort of a veteran designer - what is say, one or two pieces of advice that you would give to a young designer?
The number one thing I would say is, never stop learning. I mean I got into a rut at one point where I wasn't learning I couldn't stand up on the the current trends, things like that, and that job got to be a drag, it really did because it's - overall - we did the same thing over and over all the time. It's very repetitive, but if you're standing up on the latest trends you always have something else to reach at and something else to go after. Always have the latest way to solve something too, so it just makes the job overall a breeze; makes it a lot easier to do day-to-day and keeps it fun and interesting.
Very good. Okay, last question: I said that was the last one but I like my very last, last question - I call this part of the podcast designers after hours okay - so there's people like you and I know in common, like Bill Brooks who started the Alts Music Group. There's the sculptor, I just spoke to Chris Hunrath earlier today, who's a scuba diver. So what do you like to do after hours?
Honestly Mike my side is a little sore right now because I did some martial arts last night so that's one of my little best-kept secrets, so to speak, been doing that for a long time done Tan Sido, got a third-degree black belt there, and then migrated over to Kung Fu and have a black sash.
Well, remind me to never make you mad! You’re so soft spoken and could kick my butt.
[Laughter]
Pat's the one that always bounces that around the office but he's honestly the only one I’d ever damage too…
[Laughter]
That's cool. See, another interesting after hour designer. Well David, thanks again and I know we'll see you soon again.
This has been Judy Warner and David Carmody of San Diego PCB. Thank you for joining us today we'll make sure to share our links below and please visit us again next time.
Until then, remember to always stay on track.
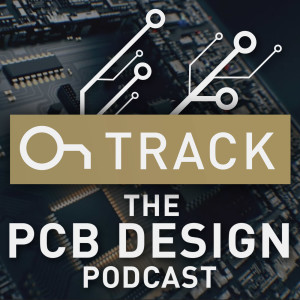
Monday Apr 30, 2018
Why is Spread Glass popular? Chris Hunrath from Insulectro
Monday Apr 30, 2018
Monday Apr 30, 2018
Why is spread glass popular? What can you use instead of FR4? Listen and learn from industry veteran Chris Hunrath, who joins us from the San Jose Insulectro facility for a deep dive into what material sets are used in printed circuit board assembly and manufacturing. Get expert insights and learn about new materials on the market to help with your PCB design before going to fabrication and assembly.
Show Highlights:
- What is Insulectro? Operating for over 50 years, Insulectro provides materials for electronics, everything from laminates, prepregs, flex materials, copper foils, conductive inks, substrates, process chemistries, imaging materials and lamination materials. With 11 stocking locations, the newest in Toronto and 9 branches, Insulectro is a leader in providing electronic materials to industry.
- Prepregs - 175 different types to cut from in San Jose facility alone!
- Spread glass is becoming more popular - electrical and fabrication benefits because it is more electrically uniform. No open areas, the filaments are spread across (aka fanned out or mechanically spread) and this has signal benefits especially for differential pairs. Better from a drilling standpoint too.
- New materials are gaining traction - with low loss that laminate at normal temperatures
- Insulectro distributes for both Isola and DuPont
- Isola’s line-up of high-speed, low-loss material sets - Isola has a suite of laminates that are low loss, some of them with DKs close to the teflon range and they laminate at the normal temperatures which makes a composite build much simpler.
- Low-loss, low-Dk materials that can help with their signal integrity requirements
- I-Speed® - Low loss system, not as cheap as FR4 but its close and could be a good next step for people looking to upgrade material
- Having the right material set for a design is critical
- Challenges are more often in the fabrication than the design
- Copper is a really good moisture barrier, you have to bake the parts prior to assembly.
- I’ve seen people underestimate the baking and end up with scrap. Moisture is avoidable.
- Bonus Material: In Designer's After Hours, Chris Hunrath shares what kind of electric creatures lurk in La Jolla!!
Links and Resources:
Chris Hunrath on Linkedin
HDPug Research on High Frequency Flex
Understanding Glass Fabric by Isola Group
Hi this is Judy Warner with the OnTrack podcast. Thanks again for joining us. Once again I have another amazing guest for us who is the go-to guy in PCB laminates.
I am with Chris Hunrath today but before Chris and I get started I would like to please invite you to subscribe, or to favorite us on your RSS feed, or you can connect with me personally on LinkedIn. I share lots of stuff relative to engineers and PCB designers and on Altium I'm at @AltiumJudy and Altium is on Facebook Twitter and LinkedIn.
So please give us a subscribe and a connection and we’d love to interact with you and hear more about what you'd like to hear on this podcast but I'm sure you're going to enjoy today's guest.
Chris is the VP of technology at Insulectro and I'm gonna let Chris go ahead and tell you a little bit about Insulectro for those three people on the planet who might not know who Insulectro is. So, welcome Chris and tell us about Insulectro.
Okay thanks.
So yeah Insulectro has been around over 50 years. We supply materials to the circuit board industry - actually multiple industries - but mostly we've been focusing on electronic materials. Everything from laminates, prepregs, flex materials. copper foils, conductive inks. Different kinds of plastic substrates used with conductive inks, process chemistries, imaging materials, drilling materials, lamination materials. Also we have 11 stocking locations. We just opened one up in Toronto and we have nine branches. So I'm based in the San Jose branch in the Silicon Valley area so that's a little bit about Insulectro.
Yeah nothing going on there in San Jose?
Lots yeah, so since the San Jose facility is one of the four branches where we do fabrication on master sheets and master roles of prepreg and laminate we do cutting, tooling, vacuum packing, and will also do that on the lamination materials, the release films, and the press pads and things like that. So we do that in four branches…
I'm going to ask you more about that later because you just told me about that yesterday and I had no idea you guys did that. Actually I saw you more as a distribution channel. But before I ask you about that, why don't you give us a little bit of background on your history in the industry and how you came to this? I always say no and no one does this on purpose, unless you're an EE right?
So yeah those printed circuit boards - those of us that got pulled into the industry ,, have been here a long time. So I started actually back in 1983, I was going to school for chemistry and one of the shops back east, actually in New Jersey, was looking for someone to work in plating on the night shift, and ,, the rest is history as they say. I got pulled into the business and the next thing I knew I was coming to California to to work with our sales team. So that's how I got started in this, and then I joined Insulectro in 2001 and it's been great being with this company. So many different materials we get to work with and so many different customers.
I think you're a familiar name and face - being the VP of Technology but you also do trade shows and stuff. You present a lot and are really articulate explaining the technology of laminates because it's gotten a lot more complicated than it used to be back in 1983. I started in ‘84 by the way, and it used to just be, we'll get some FR4 some, prepreg and you're off to the races.
Right yep, back then it was FR4 and polyimide. A little side note, actually the company I worked for made multi wire circuit boards so we also had an adhesive to embed the wires and that's a whole nother story for another time. Primarily it was FR4 and and polyimide and now there are so many different materials and then if you add the Flex materials on top. There's a lot to to work with, it's a lot of complexity but also a lot of opportunity. I mean electronics are going into everything and we're seeing that with our printed electronics products as well ,. A lot of interesting applications from wearables to medical to consumer electronics so that's been pretty cool to be a part of that as well.
Yeah so tell us about what you're seeing on the front lines of current technology and marketing trends that are having an impact on laminate suppliers - ultimately since our audience here is mostly engineers and PCB designers - how that's sort of flowing down and what the impact is?
Okay.
Yeah so big question sorry.
Yeah that's okay, that's all right. It's become a bigger opportunity - a big part of our business - but if you look at materials in general, everybody knows people are looking for higher speeds and high-speed digital and they're looking for lower loss in RF applications the Internet of Things also even data communications and those types of things; car electronics, radar, self-driving cars. All these things need low loss materials. One of our challenges - and again - it's an opportunity as a supplier to the industry; is having the right stuff available for customers and certainly the Bay Area. It's always been a quick turn market, but it's that the time window has shrunk and one of our challenges is supplying all these different materials to our customers, and of course with every laminate system, every resin system you have the different core thicknesses, the different copper weights and then you have the prepregs with different thicknesses, and resin contents. Add to that also spread glass. It’s becoming very popular I'm sure most of the people who watch this will be familiar with the spread glass systems. They have electrical and fabrication benefits but but again, it adds to the part numbers, the variety of materials we have to stock. So we we currently have here, just in San Jose, we have a hundred and seventy-five rolls of prepreg we cut from for customers. And ,, it always seems like our customers need something we don't have in stock.
Yeah.
It's the one thing they need for that application. But you know we try and up our game here and have the right things. And that comes from going to our customers and talking to the people in their design group, in their sales department and asking them; what do you see? You know, years ago we used to work on forecasts. Customers would have a very predictable usage on materials and they'd have forecasts out for some time. We would base our stock on that and we do forecasting today but it's not the same thing anymore. I mean customers may get an order and they have four days to turn it and they don't know what the build’s gonna be until the stackup’s done and and that creates those challenges. But you know, we try again, we try and improve what we stock and what we have here and get better and better at that. It's just never boring that's for sure.
Yeah right, you gotta have a big crystal ball…
Yeah just talk a little about spread glass.
Yeah spread glass now that kind of puzzles me in context of high speed so I'm curious. Teach us about spread glass?
So there's different kinds of glass, what they call standard E glass and then of course the low dielectric constant glass. I'll talk a little bit more about that in a few minutes. But the spread glass is basically that the the fibers, instead of having a crossover and a weave - like you would in a fabric for like clothing - the actual filaments and the weave are spread out, so you don't have open areas and crossover areas, or areas of higher density glass and that makes the system more electrically uniform. So when you have traces that go through the PCB they’re not either going through high resin content areas, or high glass content areas because they'll have different signal properties so you want to make it more uniform.
Are they more in glass spindles - are you saying it's not woven?
Well it is woven but instead of having a high concentration of glass with open areas of just pure resin, the filaments are spread across so you're filling in the open areas.
Okay so they're kind of fanned out you're saying?
Yes exactly there's different terminologies there’s mechanically spread, there's flat glass, but but basically what ends up happening is, the crossover areas where you would have what we call glass knuckles, they're thinner and of course, the open areas now have some glass. So again the system is more uniform it's a composite. So the composite’s more uniform and and like I said that has signal benefits, especially for differential pairs. If you had one trace and a diff pair running over mostly resin, and one running over mostly glass, they'll have different propagation velocities. So you'd have different electrical results, so the spring glass is better for that. It is better from a drilling standpoint, either laser or mechanical drilling. Because you're not going through high concentrations of glass where the crossovers are so there is a benefit there. There are some caveats though, to how it works with filling ground planes. Because the resin doesn't easily move through the glass fabric - you could have some problems filling, so we have to offer not just the spread version, we have to offer the standard versions as well because very often, designs - if they're strip line - you'll have a reference plane on either side of a signal and those reference planes could be heavy copper and they require a certain amount of fill. So you need the standard fabrics to use as well in a stack up. So you might have a mixture of those types of systems - so yeah it does add some complexity.
So now we're not only doing hybrid materials now we're doing hybrid prepreg you're saying?
Well there are different varieties I guess you have to do it that way anyways because if you're doing hybrid you're matching the materials to the bond ply that you're using anyways I suppose, but now you're adding in this kind of third layer almost.
Right.
And then we also have standard copper foil and then we have HVLP or VLP copper and low-profile coppers, so so yeah so it adds. And then of course, all the different copper weights - really everything from 5 micron through four or five/six ounces, so it's all over the place. But yeah actually going on the hybrid thing too we are seeing a lot of mixing the resin systems. In other words you would never mix B-stages in the same layer in other words you wouldn't have one kind of resin melt but you can mix cores so you could have one type of resin system as long as it's fully cured adjacent to another kind of resin system and we see that with RF, because very often what you do is, you have your low loss layer on the outside and then you would have your - whether it's high-speed digital or just DC - you would have that in the other layers and that system would be mixed and there are challenges there too even if you're not mixing the B-stages. Some materials require higher lamination temperatures and if you're not using a standard material that can withstand that, you would have issues or you would have to use a low loss material that has normal laminating temperatures. And typically when we say normal laminating temperatures, we're talking in the 375 degrees Fahrenheit range. Whereas some of the more exotic PCB materials - the filled PTFE systems LCP FEP - they require much higher laminating temperatures more like 550 to 600 Fahrenheit.
For a while I was at an RF - it really never took took flight - but I'm sure you remember not too many years ago, we got on the fusion bonding bandwagon. We thought that was going to solve all our problems but I remember being at a shop where I think we were running our lamp press at like 700 - 800 degrees Fahrenheit for 12 hours with some crazy profile. That's not very sustainable but it was homogenous DK and it had some great performance benefits but it really never took flight. So my gosh let's talk about hybrid a little bit more because I left the industry for a while to raise kids, and when I came back it was like Rumpelstiltskin waking up to all this high speed stuff and I was like wow! And what I did see was an awful lot of hybrids. So can you talk a little bit about what you think - certainly RF and microwave is an obvious one - but talk about what is driving the demand of high-speed digital RF and hybrid technology overall?
Well it's - in very broad terms - it's about electronics, doing all kinds of different things from a design standpoint though it's about mixing, mixing proper material properties in composites that's what you do. You choose one material over another because of its properties and you separate those layers out to get what you need out of a design. So it's driven by cost, some of its also driven by how you would fabricate. In other words, if you had a material that was hard to laminate you could use that as a double-sided low loss layer and then bond the other layers. Conventionally that would run the DC or other signals you would have in the design. We do have some new materials, so one thing I didn't mention earlier is that we distribute for both Isola and DuPont.
Okay.
Isola does have a suite of laminates that are low loss, some of them even with DKs close to the Teflon range, and they laminate at normal temperatures. So making a composite build is a lot simpler. You don't have to do two separate laminations, unless you had buried micro vias. But you wouldn't do it because of the materials. You would do it because it's for the design but you can do it in one lamination cycle so that's one thing we're trying to bring to market and that's something that's been a growth item for us. Some of these new materials like Tera MT40 for example, the Astra MT77. Astra has the lower dielectric constant - a dielectric constant of just under three - that's for certain, for RF designs, whereas the I-Tera is for the mid-DK, what we call the 3.4 - 3.5 DK range but they're both low loss and they’re both laminated. Again at normal temperatures, so that seems to be getting some good traction.
How do they stand up cost-wise against some of the traditional high speed laminate providers?
Well as a resin system PTFE is expensive and then if you're reinforcing it with ceramic or fiberglass, that adds cost as well, so we actually stack up - no pun intended - pretty well with the PTFE-based product. It's not as well-known, many of the designers are familiar with the PTFE based laminates for RF applications so, they go with what they know very often, until they have a need and then they start looking at alternatives. And there's so many different, projects coming on with our customers, we're quite busy trying to keep that education process going.
So I'm putting myself in a designer's shoes today and I was talking to Lee Ritchie yesterday and he was talking about how the speed curve has gone up near vertical in the last five years and I think you and I would both agree that we've seen that trend. I'm putting myself in a designer's shoes, so how do I get educated fast enough to keep up with all these moving pieces? Because like I said, when I left the industry and came back it was completely like a waterfall as far as onboarding all the different laminate manufacturers and then learning about matching bond, prepregs and bonding systems and cover weights. And then, let's just throw in, that we might have this on an aluminum carrier or whatever. How can we do a good job other than hosting a podcast so I get people educated?
I think the IPC design councils are helpful for that. Some of our folks have presented, I presented, our other people presented. Certainly, if you're an OEM or a designer and you get boards from a board shop, reach out to the board shop and say, what are my options? The board shops have to live and breathe this stuff and certainly, folks like myself and folks at DuPont and Isola will also support the board shop in that effort. In fact that's becoming a bigger part of what I do. I travel with my customer to their customers and talk about their options and the pros and cons because you would think, in theory you would want the highest performance at the lowest cost but, it's not just single performance. It could be mechanical performance, it could be thermal performance, there are a lot of different attributes that you would need in the design and you don't know unless you talk, unless the designers were talking to the folks that have the materials background. You can't put all that together and I've seen projects where people have used the same old stuff and then they get unexpected results and so that's what we're trying to do. It's better for everybody if we hit it right the first time. So, that's what we do, we go in and we say, these are the options, this is when you use fired glass, this is when you use standard, this is when you go for the lowest loss possible, this is where you go for a better economy. We have a material called high speed that's very economical and it's pretty low loss, it's a 006 loss tangent and it's compact. It's not as cheap as FR4, but it's close to a lot of the other materials out there. So it's a nice scale of economy. Now it's not for every design but those who have been using FR4 for a long time and want to upgrade to a total low loss system, it might be a good next step. And that product has actually doing pretty well for us. The 4UIS has been growing pretty well and then the high-end products are growing pretty well. The products in between not so much, but, I think it's just a matter of what people need and the design.
All right, that makes sense. Does Insulectro and/or DuPont and Isola put out resources online that designers can get a hold of?
Yeah both companies, obviously all three of us actually, have websites with links to connect slash sheets, tech data sheets, and other things but I don't know if a website will ever be a good substitute for actually having a conversation with someone who's knowledgeable. Certainly that's a good place to start. The other thing too is sometimes a design will have some IPC slash sheet numbers on them, the specification sheets for different materials, and sometimes you're locked into that. So we've seen that with our customers, sometimes they're locked into a particular material set and it may not be the best. And again that goes back to having a conversation with the people involved. And sometimes they’re willing to change and sometimes not. Sometimes they have no choice. Certainly all old legacy military designs are examples where people are really stuck on very old old systems. And there's definitely a better mousetrap in those cases. But like I said, there's no substitute for having the conversation.
So Insulectro for instance, we were just at IPC Apex and I'm sure Chris, you were doing presentations there. I assume that going to trade shows also, there would be opportunities to have face-to-face conversations?
Yeah certainly, seek out - if you're buying boards - seek out your PCB shop. The folks at those trade shows, or sit in on some of the technical sessions, and then certainly, if Insulectro, Solar DuPont are there, great place to go get some information on materials.
Great.
Well I know I sound like I repeat myself often about this, but I've often said, and I used to blog on Microwave Journal to tell people, please go talk to your workshop, please go to your workshop because I think it kind of all ends and starts there and and because, like you said they have to deal with so many laminate and resin systems and all these things every day. A lot of times they could be helpful, it's just sometimes I think designers are so strapped for time. Sometimes they're doing the jobs of two people and so I'm always trying to help the designer get resources as best they can.
Yeah and it's something we appreciate, and what we see happening too, is they'll pick up a data sheet and they look at differences there - sometimes there are very minor differences between resin contents and electrical performance. You don't know the dielectric constant of a loss and they'll pick the lowest on the datasheet, but that might not be the best for the fabrication and having the right material to make the board come out right, yield well, do well after assembly, do well in the field. You're not really giving up anything even if the loss is very minor, higher in loss, but yet the board performs well it's definitely a good trade. So that's part of the problem, sometimes some of the designers who are pressed for time will pick a particular material set. Yeah it might have the lowest numbers, but it may not be the best fabrication. If you can't build it, or if the board shop doesn't yield well, it doesn't do anybody any good.
So I was just talking also to Kelly Dack, Chris.
You would probably recognize his face. Anyways we were just talking about this and it's like what looks good on paper is... First thing, it isn’t always this linear process when it comes to design and fabricating. So, back to the hybrid designs. What would you say for someone that's designing hybrids, some of the the challenges are of those boards and some of the benefits? Obviously performance is one of the benefits.
Yes performance and cost, because very often the very low loss materials, come at a premium, because of the resin systems - the cost of the resin systems - and the cost to make the materials and so on and so forth. So that is another benefit - it can be a challenge for the board shop and it really depends on the materials. The challenges are more often in fabrication than they are in the actual design part of it. Yeah, like I said before, it just varies so much, I mean one of the requirements usually for an RF design is to have a certain level of precision when it comes to forming the circuitry. When we say forming, it could be a plating and etching, it could be just print and etch, depending on the the technology used. And then you would laminate that into a standard FR4 system, and sometimes those materials aren't really compatible. So yeah, that goes back to being able to have materials that have the right CT properties, the right adhesion the right lamination properties.
But you look at some of these high speed materials and sometimes they can be more fragile. I mean they might for instance - and correct me if I'm wrong here - this is second-hand knowledge here, but they might survive the fab process, and lamination cycles, or even multiple lamination cycles, because then you introduce buried and blind vias. And then there's multiple thermal excursions and then you take it to assembly and you've got through-hole and surface mount part and they have to go through another two thermal excursions. And so that it all adds up and it it's not obvious at the outset right?
Yeah those are all good points, all things that have to be considered in the fabrication and use of the part and there's a lot there too. One of the things I'm seeing, is copper is a really good moisture barrier. So one of the things that we try and preach to our customers and their customers or the assemblers if it's a CM, is you have to bake the parts prior to assembly and you can't underestimate that. There was a really good paper put out around 2011 - 2012 at IPC that showed just how long it takes for the moisture to get around because if you have a strip line construction, or if you have a reference plane and RF design, that moisture has got to go around that copper plane. It can't go through it and I've seen people underestimate the baking and end up with with scrap. It's kind of a shame because if moisture is the only reason why you're doing the laminating and assembly it really is avoidable yeah sometimes it's a pain did it bake a board for two, four, six, sometimes 24 hours but, that's what it takes to yield well but it's it's still worth it and that’s something that comes up a lot.
Well I know that I worked for a smaller art shop and we had the case where we were doing kind of pre-production quantities and the board was cooking along, no problem, and then one day it wasn't working. Guess what, it had rained for a week and we didn't have them in an airtight storage or whatever, so we had to completely look the way we were storing and make sure we were baking this, because in California, it doesn't rain that much and it wasn't first and foremost on our brains and when it came down to that, it was like what? Yeah didn't see that one coming at all.
I've seen that happen yeah, I've seen that it where customers or assemblers, they don't bake for years and think everything is great and they want to know what's changed and it's well material’s the same...
Had a heavy winter...
Yeah and it turns out it was something like that, it's always best practice to bake and it varies so much by design - ground planes are a problem. In fact there was a great study done recently with HD Paragon, I don't know if you if your listeners are familiar?
Maybe not, but we’ll put that link below in the show notes. Because they're an amazing asset to our industry.
So they did a great study on crosshatch ground planes on flex so there's some performance trade-offs to the crosshatch ground planes, but they do create a window. Moisture will get in more easily but it can get out more easily and when - as opposed to a solid plane - there is a frequency cut off where that is usable and one of the things the study looked at was diamond-shaped versus round openings in the ground plane. But I always like to put, or recommend putting, openings in the ground plane when you can afford it - just as a moisture egress.
Hmm, that’s new to me, so neat but it completely makes sense right? if you're locking in moisture inside of the laminate because you're capping it off, you're trapping it right?
Right, and a lot of the PCB processes are water based or aqueous based chemistries, even up to the surface finish. You know, Enog one of the most popular surface finishes, it sits in a hot bath for 30 minutes, actually two hot baths. The gold bath in the NIP and the nickel plating bath or high temperature what, 180 Fahrenheit - 190 Fahrenheit for 20 or 30 minutes in each bath. That's a big opportunity for the moisture uptake on the part, and if you can imagine, that's near when the part is finished. It usually gets routed and cleaned and electrical tests and a few other things. But then it goes out to the company that does the assembly some assemblers require the board shop to bake, which is okay if you put it in a moisture proof bag, but even that's not a guarantee because the workshop loses control over when it was opened and how long it stays in the atmosphere before it gets assembled and so on and so forth...
-or just before it gets bagged.
Yeah right.
And it may already be present and you're just vacuum sealing a moisture-laden board. It’s so many moving pieces, I always say, I wish my dear friends that were printed circuit board designers or engineers that are designing boards now understood the complexity of board manufacturing because you and I've been talking this whole time about just the laminates this is not drilling, laminating buried and blind vias, filling vias. There's so many moving pieces and I think sometimes copper bond treatments? Yeah all of that and I think in this day and age, a bare board is a line item on your bomb. It's not like pulling a component off the shelf and so I think the closer board fabricators and engineers can get together the better for both actually. Because sometimes I think the board fabricators also get exasperated with designers, but the technology is being driven in a certain way. And they're gonna be the first ones to see it and can actually help enable the board manufacturers in many cases so it kind of goes both ways
An experienced designer will know what the board shop needs and that's again - that comes from communication - things like minimum clearances, designed for manufacturability, those types of things, and in fact all the board fabricators I know are very good about working with their customers to try. And again it's in everyone's best interest to yield well and have a part that survives.
Absolutely, and back to Kelly Dack, we had a long conversation - actually two people here at Altium, all of our AEs and FEs here - are required to take the CID course and so two guys here recently took it and for the first time I got to look through the workbook. Holy cow this thing is like this thick and a huge percentage of that is the DFM things. It's understanding, so to hopefully save time and money and headache on the end of the designer.
Well Chris, I know we've only got started but we need to do this again clearly, because the other thing I want to talk with you about is flex, because flex is on the rise and I know you'll have a lot of insight there and I would love to ask you more about that. But before we go I always do this thing at the end of the podcast called ‘designers after hours’ because most people in our industry usually have some kind of interesting hobby. or a lot of us, even though we kind of act left brained, we have a pretty active right brain too actually, so sometimes we're creative or do something interesting. So do you have anything that you enjoy doing after hours, sort of unique?
Yeah so actually I've been I've been diving, gosh since the late 70s…
Diving? Oh scuba diving I thought you said dieting, okay!
Yeah so actually I started back east when I was living in New Jersey I actually did some shore diving and some wreck diving and that was a lot of fun. Now in California, when I was living in Southern California, it was Catalina Island and the Channel Islands and so on and so forth. But here in northern Cali the best place to go is Monterey. I've done some abalone diving up in Mendocino, but that's free diving that's not scuba. But, in fact, I've taken my sister my niece there. There's divers also and we've gone down to Monterey and I've done that so that's one of things I like to do. It's something I don't get to do as often as I like of course.
I know we're all so busy. Well speaking of free diving for abalone my mom and dad grew up here in San Diego - I grew up in in Orange County just about two hours north of here - but my mom, when she was a teenager used to free dive for abalone in La Jolla Cove. So about a year ago I moved down here and I'm itching to go get certified and do diving here because there's some really neat dive spots here. But we went to the area where my mom used to free dive and my daughter came up from snorkeling one day and pulled up two abalone shells, which is so rare.
Yeah
Well down here it's so picked over it's like there's divers out every weekend so it's really rare to find live abalone anymore. But anyway, she brought up a couple of shells.
Interesting fact about La Jolla, you can find electric rays down there so Rays are capable of delivering an electric shock.
Really?
Yeah well check it out they're pretty cool - but don't touch them - yeah, they're pretty cool.
Yes my interest in electronics and nature stops. Well thank you Chris, so much, this has been fascinating and I want to ask you 50 more questions but if you will say yes we'll do this again in a month or so and we'll talk about flex.
Sounds great.
Okay thanks so much Chris.
Again this has been Judy Warner and Chris Hunrath with the OnTrack podcast. Thanks for joining today, we look forward to you tuning in again and until then, remember to always stay OnTrack.
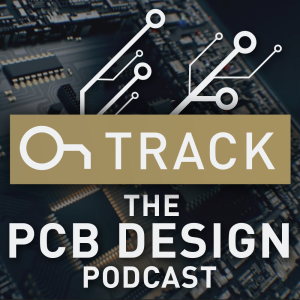
Tuesday Apr 17, 2018
SKA Africa Telescope and Multiboard PCB design
Tuesday Apr 17, 2018
Tuesday Apr 17, 2018
Omer Mahgoub, Electrical Engineer for the Square Kilometre Array (SKA) Africa talks about the project and shares how he got started in the field of PCB Design. Join Omer and Judy Warner for a conversation on Multi-board PCB design in the context of extremely sensitive devices.
Show Highlights:
- The goal of the Square Kilometre Array is to be the largest radio telescope in operation.
- Bigger and more sensitive
- Project scope - built in South Africa and Australia
- Meercat is 64 / 25% of project - Phase 1
- Next phase - Australia 158 low frequency range antennas
- Multitudes of BGA Fanouts, tight pitches, narrow tracks, etc.
- Extremely sensitive device, signal integrity is crucial
- One aspect of project is to develop local economy, so we are working with local manufacturers to improve manufacturing technology. There is a lot of giving back involved in this project.
Links and Resources:
Omer's comedic AltiumLive presentation recording
Omer’s AltiumLive presentation slides
Hi this is Judy Warner. I'm so excited to introduce you to another AltiumLive 17 Alumni speaker which is Omer Mahgoub from SKA in South Africa and he has been designing really complex boards for the SKA - which is the Square Kilometre Array - telescope and I'm gonna get out of the way and let Omer tell you a little bit about the SKA if it's something you don't know about.
So, Omer welcome and thank you so much for taking the time to tell us a little bit about your work.
Hi Judy thanks for having me, it's a pleasure to be here thank you to the SKA - which stands for the Square Kilometre Array. She SKA is a radio telescope project that's currently being built in South Africa and Australia and its goal is to be the world's largest radio telescope upon completion. I'm not sure if the listeners are familiar with what a radio telescope is but essentially, as opposed to an optical telescope, which is what most people are used to, and you look through to see the Stars and the planets. The sky a radio telescope receives radio signals. So in essence it's a large satellite receiving radio signals.
Okay. So tell us the purpose of the data you're collecting in those large receivers - what type of data they're receiving and what the purpose is?
Okay. So there are different purposes for radio telescopes. One of the main reasons is to observe the galaxy and to understand how the galaxy was formed and to understand how galaxies evolve today. Also, how they rotate and also their location, what has shaped them, and so on. Also to track new galaxies that are forming and to just map that journey. There are other purposes for example to study the earth’s magnetic fields that help guide birds and bees and compass needles and also to study interstellar gases. Another reason which most people might be interested in, is also to detect other types of life out there. Not necessarily aliens, but any any objects which might be occurring in distant planets.
Mm-hmm fascinating.
So, all the big questions of life.
That’s exactly it and which is why a lot of questions have not been answered so far by existing telescopes which is why we need to go bigger and more sensitive.
So tell us a little bit about the scope of this project. I know it's massive - and what parts of the SKA are up already and when is the due date that they feel this will be completed?
Okay so, initially when this project was started it was going to be a big process between different countries for the hosting of the telescope itself. Of the location of the telescope and so initially, the three countries that were supposed to get to be hosts were Argentina, South Africa, and Australia. South Africa and Australia, their bid went ahead and it was between the two of them and it was eventually decided that both South Africa and Australia would host this. So the actual location of the telescope will be in both South Africa and in Australia. There are a number of member countries involved in this project since it's an international consortium of countries such as Brazil, France, Japan, Malta, South Korea, Poland, Portugal, Russia, and Spain. African countries as well as Botswana, Ghana, Kenya, Madagascar, Mauritius Mozambique, Namibia and Zambia. So one source in South Africa who were bidding - they had to build, what they call pathfinders or cursor telescopes - to prove that they were capable of this. So the significant project at the time was called Meerkat which is what we are currently busy with here in South Africa and by March or April of this year that should consist of at least 64 receivers or telescopes. And then this will essentially be phase one of SKA.
Ok so Meerkat is those 64 telescopes?
Yes.
Okay with 64 telescopes making up phase 1, which towards the end should have at least 200 dishes.
So 64 is quite a quite a bit of the project really? I mean it's what - yes over 25 percent of the total project?
Yes.
Yes so, that’s for phase 1. Just to explain a bit further between the two phases. For phase 1 there will be the 200 issues including 64 Meerkat dishes but in Australia it will be 150 000 antennas for a low frequency range. So the frequency range for meerkat is between 350 to 14 gigahertz and then the low frequency antennas in Australia will be between 50 megahertz and 350 megahertz that's a lot of power.
I can imagine the boards that you make - right away my mind goes to the boards and is that just antennas? The antenna portions of the board I mean, this is kind of a novice question but how do you achieve that kind of power?
So just to explain a bit further on where I'm based with the team in South Africa. We work on what is called the digital back-end and what the back-end is responsible for is that it basically is to receive the incoming radio signals from the dish which are analog signals and essentially digitizes so you can imagine our boards are mostly to digitize these signals and just perform the processing in them.
Okay understood, very good. Going onto - so since you're doing it would it be fair to say that what you're doing there in South Africa and just sort of a little bit of the heavy lifting of this project then?
Yes you could say that.
Yeah, so tell us a little bit about specific challenges of designing these boards. I know before we got on the phone you were talking specifically about BGA fan outs. Can you talk about that and and what kind of size BGA's that you typically work with and then how you address the fan outs for those?
For those we deal with a lot of FPGA processing boards and a very high density board. Very high density BGA is starting from around 600 all the way to over thousand volts. Very, very narrow pitches of less than a millimeter point six, and six millimeters so it becomes very challenging to fan out and route all the signals in between which is why I was really glad to see all the advances on Altium 18 during the summit last year which would have made our work tremendously easier and thinner.
Yes.
But we will definitely be using those and so that's one of our biggest challenges - definitely to fan out signals and the multitudes of high-speed signals that we have running on these boards.
Have you have you had the opportunity yet to transition to Altium Designer 18?
Uhm, not yet because we're still creating our existing designs on the existing version of Altium but for which every new design that we’ll be moving onto we will definitely be on Altium 18.
Okay those are really tight pitches and I don't know how you guys do that honestly! It boggles my mind that's incredible! So talk a little bit more about the high-speed signalling and what kind of challenges that poses for you and and how you address them?
So some of the biggest challenges of this telescope is that it's an extremely sensitive device so signal integrity is crucial for our boards. And one of the main issues we have especially in South Africa, is manufacturing capability because the electronics industry is not very big here. So having to send out a board with such narrow tracks and with these kind of technicalities - a lot of our local manufacturers are unable to actually manufacture them - so it becomes really tricky because another aspect of the project is also to help develop the local economy. So we've been working very closely with some local manufacturers to help them get the equipment and expertise to be able to manufacture these kind of boards.
Yes, so tell me a little bit more about that. As one from the bare board industry and where I was focused on actually high-speed boards for a long time, that's really fascinating to me because these boards are not easily made and there's not that many in the whole wide world actually that can build consistently and reliably in that sort of phase you're talking about. So how do you go about and and where's the funding and how does that all work?
So, for example, some of our latest boards had buried vias buried and blind vias, and the manufacturers here do not have the equipment to be able to manufacture or to be able to make those. Some of them who can were able to get some government grants to buy some new equipment specifically for this project. So we were very happy to have that. Even the etching process for these narrow tracks is also quite complicated as opposed to your regular levels.
Mm-hmm.
Though as they are getting up to speed some of our initial board that we needed unfortunately had to be manufactured in China because we needed the quantities. But for the boards for which we were still prototyping we were able to successfully manufacture those here in South Africa and we were quite pleased with the results.
Oh that's wonderful! I love to hear that you're able to help through the SKA, help grow the economy and bring some technology there, that's very exciting.
Yes that that was one of the critical aspects of the SKA because the location of the SKA is also good, because you need a very radio quiet zone with no cell phone interference and that sort of thing. So it's actually based in the middle of the desert and that's also how the location has helped to uplift the community because now, you know, schools get to benefit from that a lot of extra jobs are created as well so there there is a lot of giving back involved with this project.
I love that, oh that's really great news - and you know, sometimes people say, well why go to space? Why build things like SKA?
Yes a lot of people always tell me, why is so much money being spent on this, when it can be spent on housing or help to fight poverty, without realizing that this does actually help people to uplift themselves.
I couldn't have said it better because what you realize is, when you do start doing some of these things, not only is the data that you will collect helpful and us really understanding the universe and probably have practical applications. It does really help fuel communities and put people to work and grow your seed community. So I think that's a really lovely backstory.
I think there's been thousands of scholarships already for people to get into science and engineering from this project.
Tell me a little bit more about that?
So a lot of times people, for example from the town, where the telescope is based, a lot of student’s studies are being paid for and all of them are being sponsored to attend University especially in the STEM fields. Because once this budget is complete we are going to need a lot of astronomers and engineers to work on this telescope because this is a very long-term project. I mean it's only expected to be completed around 2024 so, by that time we would need to develop the skills for people to use this and to maintain it.
That's incredible. So speaking of students how in the world does Omer Mahgoub from South Africa end up working on the SKA? You know, based in a remote area. Tell us a little bit about you and how you came to the field that you are?
All right so I studied electronic engineering, at the University of Pretoria which is about 1,500 kilometres from here, from Cape Town, and I was previously working in the electronic defense industry - about four or five years - and then I think at some point my CV was online and I wasn’t actively looking for a job, but my CV just happened to be online and I was contacted for this. And since this was in a different town, I wasn't really considering moving at the time, but I just decided to go for the interview anyway and once I got it, I started to seriously consider it and I saw what a great opportunity it would be, and I decided to accept. And it's been six years now.
That's a great story. So Omar do you remember being a kid and kind of naturally being drawn to how things worked and how did you know to choose that major?
So, I was always interested in gadgets and was something that I enjoyed. I enjoyed gadgets - but I feel like my parents actually fooled me into studying engineering because as a kid, I used to love the TV show MacGyver and I would always ask my parents, like you know, what do you see? What did he do? And they would tell me, no he's an engineer that's what his job is, and ever since then I had wanted to study engineering and it was only later on that I realized that they had actually lied to me.
God bless parents.
Yeah.
But I'm glad that they did.
Yeah well, you obviously wouldn't have lasted long if you didn't have sort of a propensity for it. So they must have heard something right? I knew a fellow, Omar, that told me once he was an electrical engineer and he was part of the early development of chips and that actually, just the 256 K chip, you know, way back in the olden days and he was from a small town in the Midwest and he saw some men climbing telephone poles and he asked his parents, what does that guy do? And they said he's an engineer so he's like, that's what I'm gonna do, I'll be an engineer. Because he wanted to climb telephone poles. Then he got to college and he's like, you people are never gonna let me climb my telephone pole are you? But then he ended up being quite a genius guy developing chips.
So hopefully he’ll get to climbing.
His son went to Princeton, I think there was some brains in that family by the way. So yeah, I don't know that he ever got to climb a telephone pole! So, well can you share some websites cause I'm sure there are some incredible photos. I know I've seen some let's share the websites where people can go both to your local website and to the the international website.
So our local website, SKA Africa is at www.SKA.co.za and the International site is https://www.skatelescope.org.
Very good. So I always ask people at the end of this podcast is that you're now shifting to what I call ‘designers after hours’ so I think there's a lot of artistry and creativity in designers like you. So what kind of interesting hobbies or things do you do in your spare time?
In my spare time I - well naturally I enjoy video games - I love playing video games and I'd like to consider myself to be a sporty person. I love playing tennis and soccer. I try to play at least three to four times a week. The thing is that I try to stay active you know, especially after sitting in an office all day, staring at your computer screen.
Yeah that totally makes sense. What would you say; would you say you were a geek or a nerd?
I would say neither, but perhaps more of a nerd.
Well you're more of a nerd, well probably with the stuff you're working on?
I'm not gonna argue with that one.
Well it's been a delight to speak with you Omer. Is there anything else you'd like to share that we haven't covered perhaps?
No not really, but I just want to say that I'm really excited about getting to use Altium 18. I'm so envious after having seen all the videos. I've actually installed it and played it on repeat but I'm looking forward to using it and seeing how easy it will make my future designs.
Well we're excited for you to use it also and we hope that you'll have the opportunity to come back to AltiumLive 18. We will make sure to post Omer’s presentation below where he spoke and had some incredible slides. And not only that, he was like a stand-up comedian and I stepped into his session and I was trying hard not to laugh really loud because they were filming. But he’s been the straight man during this call but he was really funny. Like tell the audience why the United States is not part of SKA?
That was not supposed to have been - I still don't know how I didn't remove that!
I love it, no tell us...
So the United States they're even they they're not part of the SKA is because they would have insisted that it be called the Point Three Eight Six Square Mile Ratio.
It's too wordy.
Yeah SKA, it's way easier.
Yeah well, we will definitely post your your presentation below, both the video and your slide deck because there are some beautiful photos in your slide deck that show some radio telescopes and some sites that are really inspiring. And the scope; it boggles the mind, so we will be sure to share that.
So Omer, thank you again so much for sharing your experience with us and we hope to talk to you soon. Especially after you've gotten onto Altium Designer 18 and give us some feedback so we can make it better.
Definitely will do, I'll try to find some bugs.
Okay it's on!
Thank you Judy.
Thank you so much, this has been Judy Warner with the OnTrack podcast. Thank you for joining us and we look forward to seeing you next time and until then always remember to stay OnTrack.
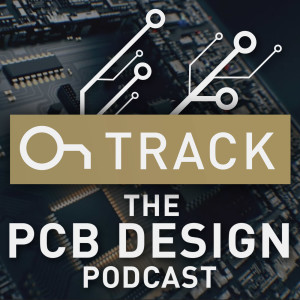
Tuesday Apr 03, 2018
Model Copper Roughness Properly, a Discussion with Bert Simonovich
Tuesday Apr 03, 2018
Tuesday Apr 03, 2018
Bert Simonovich is founder of Lamsim Enterprises and an expert in innovative signal integrity and backplane solutions. He holds two patents and author of several publications. Anyone involved with the design and fabrication of high-speed circuit cards and backplanes or people who needs to estimate PCB transmission lines losses will find value in the paper Bert shared at DesignCon 2018, “A Causal Conductor Roughness Model and Its Effect on Transmission Line Characteristics”.
Listen in to Join Judy Warner and Bert discuss copper roughness and the paper he presented at DesignCon 2018.
Copper roughness is located between the laminate and the copper
- From a manufacturing perspective, the rougher the copper the better
- But for high speed, the rougher the copper the higher the loss
- If you don’t model it correctly you cannot simulate it accurately
- The Huray model dilemma - where do you get the parameters to use for the model?
- Last year’s paper was about correcting the dielectric constant due to roughness
- New model is dubbed the Cannonball-Huray model
- The effort is collaborative, building on each others’ research i.e. Rogers, Polar
- As speed goes up, material properties are more important i.e. Fiber weave effect
- Accurate modeling is very important especially with new standards and tighter margins
Links and Resources:
Bert’s Articles on Signal Integrity Journal
Hi everyone this is Judy with the OnTrack podcast welcome back. If you are new to our podcast make sure to subscribe on your favorite RSS feed you can follow me on LinkedIn please.
Please. I love having friends on LinkedIn or at Twitter I'm @AltiumJudy and as far as Altium goes you can follow us on LinkedIn Twitter or Facebook.
So today I am at Design Con 2018 at the Santa Clara Convention Center and I'm delighted to have my dear friend Bert Simonovich who hails from Canada and so we're gonna chat with Bert today about the paper he submitted and all the things he's involved in. I also want to share with you about our fun history in Hobart and how we got to know each other. So Bert, welcome to our podcast and we only get to see each other maybe once or twice a year but I'm always so happy to see you.
Likewise, likewise Judy.
I'm glad you showed up this year and I'm glad I could get you. Last year I couldn't get you because you were so busy with your papers and everything; you were desperate, you were booked to the gunnels last year so I'm glad we got to run into each other.
So, to give you a little bit of background about Bert... well let me start from when Bert and I met. So what was it 2006 six or 2010?
Yeah 2010, something like that.
Yeah, so Bert was sort of in a transition period in his career and we met on LinkedIn and then we actually met at the show at Design Con and we connected through social media and we're old enough you know, and respectable enough in our careers that we didn't feel like that was creepy or anything. So we connected and we met upstairs; the top of the escalators here at Design Con, and we got acquainted and just networked and boy oh boy we didn't know the number of ways that our past would continue to cross over the years so, we hit it off immediately and Burt knew an awful lot about backplane and tell me again, you worked for a huge company up in Canada?
Okay so yeah we live in Ottawa area and I started my career at Bell Northern Research which was the research and development arm of Northern Telecom or eventually North Dell in Bell Canada.
There you go,
so it's essentially the same as like the AT&T; down here - researching, development and then that later got to fold it into the Nortel umbrella and I was there my entire career. It was 32 years until 2009 when they filed for bankruptcy and then my career ended…
Abruptly.
And that was kind of a shock. Then I was fortunate that I was able to you know - we weren't in bad shape financially - so it didn't hit us like it hit others. So I've considered myself fortunate, but what I missed was the day-to-day and and not knowing what the future was because at that time there was the downturn economy so it's hard for everybody and certainly harder for older ones and we were able to get out and fortunately got our pensions early and that kind of kept us going.
Yeah so that's right about the time I met you, not long after that right, and so you're like: mmm what am I gonna do now? I have all this knowledge and expertise how am I gonna apply it and so on your own dime you flew down here. We met and I was hoping that we were just networking to see how we could help one another professionally and whatnot, since that time - boy oh boy.
IMS came up from the UK to Montreal and we met again there.
That's right we met again there. We met at IMS so then, all of a sudden, our lives started weaving because I was in the RF and microwave space from the bare board side, and then I was doing the guest blogging for Microwave Journal and then you got to know all the folks - or you knew those folks in that space and then you got to know the Microwave Journal folks who have since launched the Signal Integrity Journal and now you're on that editorial review or review board for that magazine?
That's right.
And now, I think you just told me, this is your first year now that you're in the Technical Review Committee?
Technical Program Committee Yeah.
Right for Design Con so you actually reviewed the papers then that were being subpoenaed by some papers?
Yes.
Did they divvy them up?
Yes they basically divvy it up so there's quite a few reviewers for it to get the diversity and not just one person, several people review the same paper as well.
Right good. So, not only is he reviewing papers he's also submitting papers. So I want to say congratulations that you are a finalist for best paper.
Oh thanks Judy.
Well I don't know that’s third time in a row now?
Actually five.
Five! You've been nominated that many times or you've submitted, but you've been nominated that many times. I see, so you are like a rockstar! So, tell us about the paper that you submitted this year.
Okay. This paper is actually a follow-up from last year's paper that I presented and last year after I presented it, there was a great discussion afterwards. It was the end of the day and people - there were no more papers after - and people that were interested stayed and we had a good little wrap of things and were discussing some of my results. And although I was close there was some doubt as to actually what it was, why there was still differences and my co-author Vladimir he had an idea that it's possibly due to causality of the metal.
Okay.
And Vladimir works for a mentor and so he had this idea and I had data and my technique and we decided to collaborate and see how well it would work. So he incorporated his algorithms into the tool and we checked it out and that brought the data exactly right on.
Wow! So this paper is kind of a wrap or closing the loop at the end of last year's paper basically?
That's correct, it's kind of a follow-up in a way and it kind of answers the question that we were suspecting. - the people who were discussing as a group were suspecting - so that was very satisfying when I had that. So we said, well we've got to publish this now so we'll do that.
So it was a copper roughness issue?
Well it's part of modeling called copper roughness, to model copper roughness properly and get the right model afterwards so you can do the simulations.
Isn’t that hard? I mean it seems like copper roughness, which is the roughness - for anyone that's not clear on this of our listeners - copper roughness is between the laminate and the copper. Not on the topside of them it's on the bottom side where it's being bonded to the laminate but it's not always the same?
No the thing is with roughness from a PCB manufacturing perspective, the rougher the better.
Right because there's adhesion.
Right peel strength. Nowadays, for high speed past 10 gigabit, now everything starts to matter and now people are talking 25 gigabit - 56 gigabit all the stuff lost, now becomes a factor. So it turns out the rougher the copper the higher the loss, so how do you model that? If you don't model that correctly you can't simulate it in advance.
Exactly.
So the bottling techniques in accuracy - so there's been different models out there one that's been very popular is the Hury model that was presented back in 2010 because I remember going to that presentation. Basically it was dubbed the ‘snowball model’ because when you look at the roughness profile under an electron scanning microscope, it looks like a stack of snowballs type of thing.
Okay.
Uh-huh and that's where it got coined the snowball model but it's the Hury model and it's very accurately shown that you get very good results measured to simulation. The problem was where do you get the parameters to feed that model? Back then to get it, if you tuned the parameters you could get an excellent fit to the loss but that doesn't help for tools so how do I get that? Unless you're building a board or measuring the board to get the parameters so you can use those again if you're going to build that same geometry in a new design. So that's very time-consuming - pretty accurate - but not practical for smaller companies. If you need a good answer now, rather than a good answer later as Eric Bogatin always says, that never helps you. So, one of my early contract positions, because I started going in consultancy after Nortel. One of my clients they wanted to do some analysis on dielectrics but they also wanted to include their roughness and I knew nothing about roughness at that time. So I started to do my own research into this so that I could try and do the work, and found that it was all over the place in a way.
Anyway, I completed the analysis not even based on what I knew at the time and it was okay, but that seed sort of stuck. So I started in it and once you get an interest in something then try to go further and further. So it's been a pet project of mine so I decided to think about the Hury model and say: well, is there a way to get these parameters based on datasheet value only? If I know the roughness from a datasheet the, height of the roughness, can I get the radius though? So I thought about it and you know, I thought about: okay, this is the stack of spheres. If I stack them up can I determine the radius of the sphere from that stack? So you know it's basic geometry of things and eventually you can get that number if you know this height. So I thought - just out of curiosity - I'm gonna try it and when I did, I got reasonably good results, almost right off the bat. I'm not perfect, but I can tweak things a little bit more and I'm saying okay… That's how it kind of began so it's been over a few years, off and on. I did a paper earlier in 2015, when I first presented some of it, and that was quite successful and every year it's been kind of incremental and testing it against other data and then eventually other software came out like simBR and I started having success with the model there and that was great and so it kind of went. So lately, after that, then I started thinking about I never get the the actual delay property. So in order to model things, you need proper loss and then also the the delay property or the phase. So then I thought well, perhaps, how does the roughness come into it? Because I noticed the rough with the copper I get different phases for the same material. Anyway so I worked out some some things and that's what last year's paper was about, to correct the the dielectric constant due to roughness...
It was really last year's paper.
Uh-huh and so that that worked out very well and when I correct that, I get very good results with it so that's it in a nutshell how I got from there to here.
Wow. So I know you've worked also with Polar instruments. Tell us about how that came about?
Yes so last year Polar had introduced the Hurray model into their tool and I hadn't really met Martin but in his newsletters I always got it and he announced that they were going to come out with the remodel and a Polar tool so I emailed Martin and said; look let me check it out to see how well it works. So they gave me a trial thing just to check it out and I tested it out against my data and there was just a couple of hiccups, but we sorted them out and now the tool - it's a great tool - we can get the parameters now basically from data sheet to fill in. So we've dubbed the model really like a ‘cannonball’ Hury model because it's a combination of both.
Well Martin spoke, I think I shared this with you earlier that in October Martin Godean from Polar presented a talk at Altium Life in Munich and I was chairing the room he was in and he pulls up this stack of cannonballs - you and I hadn't talked about this - then he starts citing all this work by Bert Simonovich. I nearly fell out of chair, like my friend Bert? So I really love that Bert, you've like been such a collaborative force in this industry about these models and you know that you reached out to talk to Polar and really made it better. Not so much in a self-serving way but it's good for the industry really, it's good for designers right?
I think so.
And so I really appreciate that generosity of spirit that you have and it's what I liked about you when I first met you and here we are all these years later who knew.
That's right.
So, what's next Bert? Tell us first of all, where can our listeners find your papers because I'm sure they'll want to get their hands on those?
Yes so I published papers that I have on my website at my company is http://lamsimenterprises.com.
Okay.
Well I'm sensing we'll try to put that in text somewhere I relate to this podcast so folks can find that and then they can find your consulting services there as well but then find all your papers there. Did Design Con aggregate the papers that come out of the show?
Oh yeah they have the proceedings.
But only the attendees get their proceedings right? So they can come to your website is the bottom line, right?
Right, so anyways so for my papers, I have my papers that I published on my website and it's not just Design Con I’ve also done EDI Con papers and that's part of the signal integrity journal. There's an offshoot of that - is EDI Con - and I attended that the last two years, they were the first two. So there's Boston that was great time. Actually you went to the first one?
Yeah I went to the first one I can't believe how our lives have just crossed so many times. We just met each other here and went hi.
And you met and you met my wife.
Yeah I met your wife on that trip.
Bert and I got to go to Fenway Park and have a private party at night and overlooking the fields and they brought out... what are those? I'm such a sports nut.
The trophies from the World Series.
- thank you the World Series trophies. They brought those out so we could you know take photo ops with and we had great food and we got to take over Fenway for a few hours and I met Bert's wife who's just a doll and we had a great time. So who knew when we met how our paths would cross?
But I think Design Con in general is about is networking, meeting new people, learning new things spreading the seed of papers. Like I was mentioning even last year's paper - Rogers took that and then confirmed the data or the theory part of it and then they presented results this year.
It’s such a great collaborative effort and I don't know I find it very refreshing because you know, like well I have a secret and if you give me a lot of money it might tell it to you. This is much more open handed and collaborative. I liked what you said earlier today - which was somebody will present something and then an offshoot will take off and then it'll take off and then someone will build on that and bring it back as something else. It's really the industry together - collaborating.
That's also for mine like 2010 with the snowball model, who knew? That room was packed to the rafters and out - that presentation from Paul Hury and Eric Bogaton’s and he presented that year and I was just dumbfounded and I'm going, well I don't understand it but that's cool, and that who knew that that would be the seed for my work, my research work.
And and then went into Polar and Rogers and it's just like an idea that sprung legs.
And that's just my example. One example of many you just look around - like Eric likes to say - come drink from the fire hose, that's the Design Con there’s just so much stuff and it's there and it's just a great place for that kind of thing.
It is a great show. So, a couple closing items. Number one what would you say for circuit board designers, are some of the kind of greatest challenges they're facing today? Looking forward into emerging technology is there any specific - one or two things maybe - that are sort of plaguing them at this point? Or things maybe they need to onboard and that they are not taking right now?
Just in general as the speeds are going up the actual material properties are really becoming a factor. A big thing is fiber - we've talked a lot about that - fiber weave effect and the industry is looking how to mitigate that effect. A lot of nice papers over the last few years, talking about that and again there's a lot of things on the roughness, getting good modeling because it's important now. And now with everything like the new Pam-4 standards, 56 gigabit. The margins are tighter, so fabricating boards is more demanding.
Yeah it ain't what it used to be I can tell you. I started in the board fabrication industry in 1984. Oh my gosh that seems like such easy stuff compared to today. I was just speaking with John Belushi from ASC and I said it used to be you just got your board, your fab drawing you had your sort of mechanical, here's the size of the footprint, this is the size of the trace plus or minus this, and off to the races you go. Now it's like a board fabricator has to think about everything they're doing and how that is going to impact. You can go to a board shop, make a board and be well within IPC standards and its’ still not performing to the designers intent.
I think it's not just the board shop, I think sort of the industry as well, you have to specify what you want properly in your fabrication notes.
What fabrication notes. What I'm saying is documentation, I think is an issue.
Yes and and the thing I'm seeing is if you want consistent results you have to nail down your design. Basically nail it down and not let the fabricator substitute material for different weaves. For instance if you have a stack up that you first designed it's got to be included verbatim on the fabrication notes. So you must use this material, this weave.You can’t substitute, and you can't play around with all the line widths and space to do things different. By specifying things on the notes that restricts what they can do you should end up getting what you want otherwise you may not.
And you had told me earlier in your consultancy business that you will talk about modeling certainly, but then you also give them the added benefits of giving them some guidelines of how to spec in these.
Yeah so typically a lot of my business is design reviewing boards before fabrication. After they do the design like Altium Board Designer would lay it out, so now there's a design review at the end so some of the clients they'd like to get some review over that visual review and I do that sort of thing for them. But as part of that, I review the stack up even from the board shop because the stack up people are human and could make an error. Typo or a lot of times they're just templates and they don't cut and paste properly or something, and it may not be correct. I haven't found anything that wasn't correct but I do that anyways, just check it, double check that the impedance is correct in things. But on top of that I also say that I'm going to review their fabrication notes to ensure there's consistency there and usually I find that a lot of these are smaller companies or startups. They're not aware of what's needed or they have one set of fab notes and they have the same design all over. They just use it over and over but that could add confusion in the shop.
Yeah absolutely.
At the end of the day part of the design review it's also part of a bit of educating as well to some clients so they realize some of the importance and they appreciate that as well.
Yeah and it is so sorely needed and people don't, like you said especially smaller companies, they don't always have the resources to go out and spend endless hours in a board shop getting educated or whatever the issue is. Or educated about signal integrity or whatever it is, so I think what you're offering in your business and in that niche is really valuable so that's great.
Well my friend I'm gonna let you get back out on the show floor. I'm sure you have a lot to do today I'm sure you're a busy guy so yeah I so appreciate you spending a little time with me and I'm so glad we got to connect I know you're getting so busy - such a big shot these days - it's been a delight thank you.
Actually, the reason I knew you were here, I saw something on LinkedIn and saw you were responding to somebody and I go: wait a minute is Judy here? So then I LinkedIn messaged you last night and I said, are you here? and yeah so let’s connect today.
See there's a lesson to everybody, LinkedIn really is useful. Gosh you and I've met a lot of friends through LinkedIn. I'm so glad to see my friends. I don't get to see you enough so I'm glad to see you whenever I get to see you, I'm not gonna complain. So best to you, congratulations on your nomination again.
Thank you Judy and the same to you.
And have a great show and I look forward to catching up with you next time.
This has been Judy Warner with the OnTrack podcast please remember to subscribe on your favorite RSS feed and we look forward to talking with you next time and always remember to stay OnTrack.
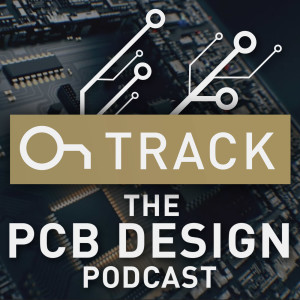
Tuesday Mar 27, 2018
What is PCB design? With Kelly Dack and Judy Warner
Tuesday Mar 27, 2018
Tuesday Mar 27, 2018
What is design? Have you been inside a board house? Join Altium’s Judy Warner and Kelly Dack, CID+, for a lively conversation about PCB design and becoming educated in the field. From CID and CID+ to visits to your fab house, learn how to learn for PCB design and where some of these resources are available today.
Show Highlights:
- Design has to do with a breadth of knowledge. The design tool is only as good as the breadth of knowledge of the designer.
- Eric Bogatin’s PCB bootcamp-style at the University of Colorado provides exposure to the manufacturing
- Dreaming a product and then embedding the process steps within the layout
- You can control so many things in Altium Designer - setup constraints, DRC rules, etc.; designers need to know how to manipulate these constraints so it will yield the best results for the stakeholders in the prTocess.
- To design is to be in touch with all the stakeholders.
- Everything in CAD are nominal values / nominal data
- Without recognizing manufacturing tolerances, we’re doomed.
- Certified Interconnect Designer or CID Certification, from IPC, teaches the start to finish manufacturing process
- Eat, sleep and breath PCB design at AltiumLive 2018 - the largest conference in the world focused exclusively on PCB design
- With Altium Designer 18, “I’m finding it easier to communicate with my mechanical cohorts”.
- Dream feature: Snap back and forth from min to max toggle
- Merging the mechanical and the electrical: Mechatronics
- Design in prototype vs .production - what is sustainable in prototype environment might not work / be scalable in the production environment
- A challenge for everyone: go visit a board shop!
- Fun facts: Kelly has a hobby farm and plays harmonica (and guitar!)
Links and Resources:
Eric Bogatin’s University of Colorado PCB design program
Certified Interconnect Designer or CID Certification
AltiumLive 2018 - save the date!
Hi everyone this is Judy Warner with the OnTrack podcast. Welcome back, we are recording today from Design Con 2018 in Santa Clara California. Today I have another amazing guest, Kelly Dack and before we get started I want to make sure that you subscribe on your favorite RSS feed and also please follow me on LinkedIn or on Twitter at @AltiumJudy and Altium is also on LinkedIn, Twitter and Facebook. So, please give us a follow and we'll continue to put out as much good content for designers and engineers as we can possibly razzle.
So today I am with Kelly Dack who is a PCB designer. Are you CID or CID + ?
CID +
CID+ so he's a hotshot. So a designer for many years, currently he is with a Northwestern EMS provider and…
How many years have you been in the industry Kelly?
Well too many dimensions, thanks for having me Judy.
I know, I know...
But I thought you're gonna introduce me; look what the cat dragged in.
Yeah no…
- well no but yeah I've been in the industry since 1978 something like that.
Okay well longer than me so yeah, I don't like to say when I started either, but I think I started in ‘84 I know Wow I know I don't want to say how old I am but it just automatically dates me so Kelly so we're here at Design Con and I know you have a completely broad perspective of this industry because you've been on the journalistic side, you've been on the design side, you know about fabrication. Now you're on the MS side, you just mentioned that the design that's being done at your current place - that you have Altium designer so we like you better already. And so tell us, you and I started to talk… I'm just gonna let you roll because I know you have a wealth of things to share. So start out with… ready? What is design?
Wow design... I've been talking about that with the cohort of mine Andy Shaughnessy all morning because we come to a show like this and we're talking design relative to high-speed and things measured in gigahertz.
Right.
Things like this typically the engineering crowd of the degreed crowd but they have to relate also. The stuff has to be translated into the classic or traditional PC board designer. There's been a lot of talk about the two merging, there's been a lot of talk about where's the next generation of the PCB designer coming from.
Oh yeah.
Now that somebody told me yesterday, you know, these guys are all dying out and I chuckled. But you know it's a fact that we're all at least hopefully retiring happily so that this generation of folks that started in the 70s doing board design and earlier, are moving on and there's been a concern about where the gap is going to be filled and a couple years ago I had a chance to have a brief stint in the Seattle area and I found the answer to that question. I worked for a Prototron for a brief period…
Yeah, oh my goodness…
- and part of my job was to reach out to designers in all of the Seattle area and so my job was to go in, drive downtown shake hands with designers and turn them on to the great things that Prototron does. Well these these people were not old designers - these people were young, hip. People that had just graduated at a university, had picked up the design tools and because they're quick studies and they're smart they learned it in a matter of weeks. At least that's what they make it seem like, yeah they're quick studies and they were laying down tracks right and left and my job was to go help them from the standpoint of how they can make their designs flow through our shop a lot easier.
Right.
So it was a little customer liaison, engineering liaison, so I was very surprised to find out that the designers are out there now.
They're out there. By the way Kelly I've talked a lot about this and if you actually read my newsletters that I sent you... just kidding, just needling you a little bit. I've actually found since I've been at Altium the same exact thing you're finding is that one, this next generation, they basically came out of the womb with a smartphone in their hand right? Playing computer games, so they learn so much faster and in the case of Altium and we’re certainly not the only ones out there who are sponsoring engineering teams and universities and so much now right? Engineers are laying out their own boards. It's not a distinct role and so these kids are bright and they're quick, and now I'm seeing globally... I would have never seen it had I not been where I am now. But I see exactly I would echo your exact thoughts is that I see them everywhere they're on Hyperloop teams, they're on SAE you know. Formula teams, they’re on there and engineering groups, there in space teams and and they're learning to lay out boards in college. And in our case we're gifting the software right, so they have a tool; a professional tool. So when they graduate it's easier for them to get a job - so I see it I and I'm so glad to hear you say it, because I feel like the only one that's kind of like, don't be afraid people, it really is gonna be okay
Well check it out now; the product is called Altium Designer and there's a lot of designer based products out there that infer and rightly so. It’s a very powerful design tool. But back to your question; what is design?
Design has to do with a depth of knowledge that's gained not necessarily by a design tool. A design tool is only as good as the knowledge of the designer, the knowledge base of the designer so what I mention (and what was fascinating) - working at a prototype bare board supplier and now - what you didn't mention - but I work at an EMS provider doing assembly work now and there's a similar stream of challenges and the same problems and issues that we would see at the bare board supplier. That needed coaching or mentorship for the designers are happening and echoing through to the assembly suppliers right. So we're seeing problems like copper pull back from the board edge. Who knows how much that needs to be. In other words if if a designer is going to design, they need to consider all the stakeholders of the process who's going to be building this board. What are the processes that are involved in building this board and there's many there are many.
Many, many along the way.
Many yes, and this is, I think many would agree, that's what's maybe - I've never taken one of those university design courses - but I know they go fast and I know sometimes they're measured in weeks not years,
Exactly. Except I will tell you I don't mean to interrupt your thought pattern here but I was overjoyed and I think you'll be glad to hear this too and maybe you already know this that Eric Bogatin is teaching at the University of Colorado, Boulder so you know he he and a colleague have written a curriculum that's PCB design with manufacturing and assembly best practices included.
Right.
Right, holy cow, like to me that's like the motherload because it's in context! Like you said of all the stakeholders so, anyways continue on.
I know Eric's really good at boot camp philosophy right? Hit that ground running but you know, know where the ground is, and be able to… I can't imagine he's not, you know, encouraging the folks that go through his programs - I can't imagine he's not encouraging them to go visit.
Yeah.
Boots on the ground. Support supplier, and they send me the supplier so they can see and meet the people who are doing the work. So back to design what is design. Design has to do with having a product - dreaming a product - and then embedding or creating all the process steps within the layout so to speak. Maybe that sounds too simple but from the standpoint of what can go wrong - things can go wrong as a new board designer starts designing. One of the things that the software tools are - the layout tools are doing so well, is they have a lot of movement is - is this a word? Manipulatable constraints set up.
Right.
Constraints, DRC rules and things and being a relatively new user to Altium I am amazed at how many things you can control and Altium - it is just amazing now, from a new user standpoint, that can be a blessing. But that can be a curse because all of these setups are are off-the-shelf setups. There are default settings right? So what a designer - to be called a designer - needs to be able to have the knowledge of doing, is manipulating those constraints so that it will yield the best outcome for all the stakeholders in the process. What do I mean by stakeholder?
Yeah I was gonna ask you that.
So we can't as a designer, a true designer, we can't design in a vacuum. We can't have our own office in our own world and live in a vacuum and think that this product we're creating, this chunk of clay - I'm bad at metaphors - this chunk of clay is going to be beautiful when we're done with it. Because there's nobody else looking at it. What I'm trying to say is design has to do with reaching out and considering who is going to be putting this thing together. It's not the designer typically right? The designer is not the one plating and etching right, we define things like stack ups. We define trace widths and via sizes and placement things right? But what do we base those things on? This is at the core of design. What are we basing these design attributes on? And without getting out and shaking hands with the stakeholders in the industry right, the bare board fabricator for instance - the engineer that may have designed the schematic, the test folks. The people that are going to be having to test this board. The assembler, the people that are going to have to be putting the stenciling the solder paste onto the board and applying the parts. Who else is down the line? The customer the overall..
What about the box builder, or you know maybe interconnecting devices maybe cable harnesses?
Sure, I'll keep it short - to design is to be in touch with all the needs of those people the stakeholders of the and their processes okay.
I 100% agree with you I've been beating this drum blogging and writing about it for a long time except I feel like people look at me and go... I remember one old-school guy that I've known for a long time - he goes it's so girly because why would you have a relationship with your fabricators?
Girlie what the heck! Like it was just sort of a silly comment but my point was; you can't design in a silo just like you're saying, you can't design in a vacuum if you don't have that design intent. One has to be communicated, and you have to need to know you can design something amazing and are not only Altium. All the EDA tools out there are extremely powerful and they can let you do really stupid stuff from a manufacturer standpoint. So do you get to be the Wizard of Oz and then it's completely unbuildable on the other end you know.
So if you're not in touch - now I'm gonna ask you a loaded question - I know you Kelly, you've been in lots of board shops and EMS shops and you're very well connected to that stream of stakeholders. How has your CID/CID+ helped equip you for that? Has it, or does it equip you more theoretically and then you gotta go get your boots on the ground?
Wow not a loaded question at all.
Okay I just don't want to get you in trouble at IPC, if you understand.
Not at all. I’ve got to say I went for my CID back in the 90s while I was during my time down in San Diego and it it had been an evolving program and I paid for it myself. I was at that point where there was no convincing a company - a telecom company - that hey there's the certification that will help give me an in-depth knowledge of all the processes and it wasn't happening. So I went and did it on my own dime and that was CID and that was a long, long time ago. A lot of has happened with the program and with technology since then, but I've got to say that the thing that I loved about it was that it described the stakeholders of the process. It defined the start to finish process of how to manufacture a board, how to document a board for manufacturing and for inspection, and even explaining that that the fabrication drawing is not as much of a how-to document as it is an inspection document. We're not telling - with a fabrication drawing - we're not telling the supplier how to do it. They know how to do it with the data right, they have all the data in the world that tells them how to do it.
But there are parameters that right?
There are parameters but the difference is they are nominal parameters. Everything in CAD data that we know of is mostly nominal data right? You lay a linewidth down at seven mil - 7 thousandths of an inch wide. If you think that that line is going to end up 7 thousandths of an inch wide on the board when you're done, you may be in for a surprise. You know it depends on manufacturing tolerance and without recognizing manufacturing tolerances we’re doomed.
Right so let's just say that. You know this gets a little crazy to me is because a lot of engineers have not had the benefit of being inside a board house and because they are used to using a lot of physics phased holes and stuff. They think it’s 7 mils - make it 7 mils - if you don't understand how the printed circuit board is made, the print edge process, what happens inside of an etching bath, it is not possible. Let me tell you engineers - I don't mean to be condescending at all - it's that I really care about this that it cannot be made perfectly seven mills ever.
Yeah.
I mean it's that's why we have tolerances plus or minus this or that but now with these high speed stuff it's like: oh yeah can you give us a 1 mil trace,plus or minus zero and I'm like NO. No no no no...
Yeah well, very very important to understand that and like I said - back to the CID program from IPC. I had gone on, years later I went back and did the advanced. The advanced portion of that course, the CID+ and I gotta say that then I didn't go job jumping very often, but when I did, in this particular case, I was able to list my CID and they seemed to scratch their head a little bit at the interview process but I was able to define or describe just what I've described to you about about some in-depth knowledge of the processes and the people involved. That's when I got their attention so this is what I'm saying: that the CID program helps that in a lot of ways and CID+ all the more, goes into more advanced processes and ideas about circuit boards.
Fast forward to a few years ago, I was invited and Gary Ferrari was invited - to help instruct on the program. So I get my certification to teach - I did that - and let me tell you that is wonderful. To take a class of 10 or 20 people through the materials that have been evolving, but are now pretty much set in stone, is a real solid curricula for what was a three day class. Three days of intensive review of materials that the students had been studying for months. Now it's a four-day - we've expanded. I was going, there's so much information in there, it's expanded to a four day class and the pressure that you see on some of these students faces as we're getting toward test time - because it's an exam. It's an audited exam, very official. There's a lot of pressure and let me tell you that the pass rate is very, very high now because of the the level of training and the level of study materials. I mean you need to study this material it's not easy. We're condensing a lot of material into a four day class. The expressions on some of these designers - they are designers - but now they have more of an in-depth knowledge of design, what design is. You know it's stakeholders and its processes, and it's materials and things that now we're giving them is a lot more in depth. When they pass that test I have had people jump and hop around and clench their fists and say, yes! They're so happy to have done this and it's really gaining traction, as far as a certification. We talked about University classes and you know maybe those are measured in weeks.
Yeah well, and CID, like you are saying really has to do with the stakeholders you mentioned.
Right.
We're in the university, as you said, I've heard some professors say, yeah I teach the printed circuit board design but don't be impressed it's three 50-minute classes. One on schematic, one on routing and one whatever...
Yes and let me tell you I was in 3rd grade classes and 4th grade classes where at least we’d jump on a bus and go visit the fire strips right. We talk about the fire station but at least we hold hands and I'll walk up to it or you jump on a bus and go see it. I'd like to challenge all of those University professors right now to to get their students on a bus and go visit a board shop or an EMS supplier I mean brother.
No I feel the same because I think there really is a disconnect there and sometimes, honestly on the board side, there's a disconnect in our understanding of what the designers are and sometimes we’re like - errr we treat them like... Instead of partnering with them and going, what are you trying to accomplish and how can we get together and move you in that direction? So it can go both ways, it's not just one way.
Absolutely I didn't get a chance to attend the Altium event.
Yeah Altium Live, well don’t miss it this year.
Well I have heard so many great things, I mean, powerful, powerful things from people that attended and the people that were there-
Thank you.
-The notables that were there speaking.
Oh yeah, we had the big guns there yeah.
Yeah but but speaking along those lines I think again you and I are just lockstep on this issue and when I began at Altium they said, ok we're gonna give you a team to pull this event off Judy, but you're gonna run the strategy and you're gonna get the speakers and I'm like, ok. And so I'm like designers need to hear from other designers right? So it's not just theoretical but they also need to hear from fabricators, assemblers. They need to hear from the whole gamut. So we did a call for papers but we also had people talking about what you need to know when you're designing Flex circuits, because you might all of a sudden have to be doing flex or rigid flex and you didn't have to do them before. Or multi board systems, so you know we worked to kind of sprinkle that in throughout. And then also have sponsors who were there that they could interact with and, boy I knew it would be a good experience but I didn't know how good. Kelly, I can't wait you have to come this year.
Yes, yes sounds very holistic PCB design - holistic - but yeah amazing.
Yeah holistic, sounds very Zen.
And what we tried really hard not to do was just to beat the Altium drum like sell/buy our stuff. Here's our new... of course we're proud of our tools and our new releases. So out of two days we took two 45 minute slots for ourselves and the rest was about them. Resources, plugging them in and I remember Laurence, my colleague, saying oh my gosh these people - it's like they're really inches away you know - as far as functionality goes - but they never talked to each other and I said, exactly right, and so to put them all together and the energy was just absolutely electric. So yeah come, come again and yeah yeah we would love to have you. So that's been truly a highlight of my career honestly, to see that all those light bulbs go out probably how you feel after you teach a CID class you know.
The afterglow.
Yeah the afterglow. Yes we were all singing kumbaya and so - oh good I heard great things - thank you, thank you. It was really it was a blast and it was a giant team effort you know I'm not tooting my own horn at all, I just got to go get the speakers and oh my gosh our team worked really hard to do all the logistics stuff and they did an amazing job.
So I'm dying to interview you and I'm trying not to. I know I'm being interviewed I'm just dying to ask again. Being a new Altium user I know version 18’s out and I don't want to ask you about it because that would be me interviewing you. But as a new user I have to say that I'll confess you know, a lot of this 3D capability that I haven't been exposed to in the past and now, becoming new to it I've got to say it's it's a lot easier than I thought it would be and like I say, Altium is my first tool to have introduced me to that. So that's where the industry is going and I found that it's pretty easy now to communicate with my mechanical cohorts you know.
Yup, because that’s our goal.
We're back to design - the design flavor of our discussion. It's not only electrical constraints that we're talking about but there are mechanical constraints and we talked about everything being in CAD being in nominal values in CAD so there's a natural dialogue that designers, in order to design, have to have with each other with regards to these nominal settings and these nominal layout features and geometries. So 3D CAD - 3D capability step files and things, have made things a lot easier to visualize and you can check alignments and things. But again I want to look at - I'm still learning how to use the tool in consideration with tolerancing. I can see a very nominal conditions like a mounting boss and nylon mounting bosses centered within a hole on the board. It looks really nice but I know that that hole is perfect in the step file I have to consider, as a designer, what kind of tolerancing - that locational tolerancing - and diameter tolerancing that that hole has. So that's something I have to encourage myself, admonish myself, without trying to admonish others. My purpose here is to inspire others to consider beyond the nominal condition. So I'd love to see the tools of the future as they evolve. Be able to address that somehow and you know, about the best we have in the design world is to design our maybe our part bodies at a maximum material condition or something like that.But wouldn't that be nice if we can if we get to toggle back and forth we could snap back and forth.
Yeah yes - min to max. I was picturing in my mind if you could open and close down that hole and see.
Yeah and i can see our R&D guys right now screaming when they're listening to this.
It’s encouragement you know that might be somewhere that we're going - there's a term that I'm loving right now, that's a buzz term that's been out for a while. I I guess where the industry is bringing together the electrical constraints, the electrical designers, and the mechanical designers which theoretically all are going to become merged into one designer pretty soon. Sooner than we know and as it it's called mechatronics right?
Yup.
And I've heard there's courses being taught in mechatronics and it's just that, to me, is an inspiring place to go. I'm too old to go to school again I know. I feel like I'm in school every day you know, we're learning new software tools and things. Every every day we go to work and we we lay down trax or have to address problems. It's like a new day in school: are we gonna ‘BS’ our way through something or are we really gonna get into what's going on here and learn about it? And you know, that may mean a call to the supplier. How do I handle this? What are your capabilities? And not forgetting that just because we talk to that one supplier that doesn't mean the rest of the suppliers have those capabilities and other things. That's where we're kind of freestyling...
Yeah we are freestyling.
That made me think about pet topic and that is prototype versus production. How do we design and prototype versus how do we design a production just because we can go to a supplier that'll quick turn a board for us in a few days.
Yeah
The biggest mistake - let me go with a case scenario - the biggest mistake I see engineers make, some designers - is they'll get a design made at a quick turn board house and guess what they'll get it back into their shop, they'll give it to a tech have it assembled. You know what, that thing works perfect okay, and it's made with all these special core materials and special weights of copper. It's been printed and etched just fine. It's got purple solder mask just like it's specified and then because it's working perfect they say okay let's go to print and they want to go order a million of them. But that prototype shop’s not going to be able to make a million of them right. So you know, what's going offshore? So, what do you think's gonna happen to that specialized recipe? The designer, the engineer has to cut and paste the actual recipe of the design onto the board?
What's going to happen? Yeah it's gonna be a bloody disaster it's gonna get kicked back.
Yeah it'll probably just get kicked back. So we're talking design, and design involves creating you know. Sometimes hybrid stack-ups, but we have to be so aware of where this project’s pointing.
Is it producible in production? If you're heading towards - this is going into consumer market - you have to be thinking about that at the proto level. You cannot, oh let's just do this you know, get a Ferrari with all these special processes and then think that that's going to go into mass production because that takes... By the way when you talked about Prototron and shops like that. I worked for a shop much like that and there’s guys hanging over that job, kind of hand-carrying it through and making sure that everything goes perfect. That's not sustainable in a production environment. And you know that's not always understood.
That's right it needs to be understood.
Yeah how do we get that done?
Well the awareness needs to be there. I think it gets done but it gets learned the hard way.
Yeah for sure, and this is one that makes me feel, actually a lot of empathy for engineers. I feel like they're having to learn things over and over and over again that it's like reinventing the wheel over and over again instead of there being like some recipe book or some definitive guidelines of course CID+ plus and those things are are hugely enormous Lea valuable yeah but I don't know that there's a there's a straight cut and dried answer for that because it's complex process.
Yeah back to the CID - you know the guidelines - the CID program - points the designer to our specifications and again I'm a big proponent of not only getting designers out to the board shops, EMS shops, but out to the trade shows. I mean if you're a designer, I ask the students in the CID courses. Y'all been to trade shows y'all been to APEX or PCB West, or you know SMT shows and Design Con like we are here right now? If you haven't been out to these shows you might be missing out. This is not only a great place to shake hands and talk to people that are in the business of you know, selling of the products, but it's a network. Just like we're doing right now, it's a networking opportunity and a lot of what you're learning as a designer is going to come from networking
And in a tradeshow, you can do it like at hyperspeed. You can take in so much in two or three days like drinking from the fire hose level - like you can so much!
Yeah yeah, well that's me others that to drink it from the fire hose and then drinking... So you know you can take in so much information in that period of time. So how often do you teach the CID courses?
Ep Tag has been a instructor - supplier of teachers - for many many of the IPC specifications there. They're based back east in New Hampshire, and they have - for the CID program - they have a dozen or so instructors. Again these these instructors were pretty much hand-picked out of the industry to be able to go out and teach these classes. However, you know a lot of them, myself included. We have day jobs right? It'd be nice to be teaching - the teaching is so positive - I would love to do it every day but I would never want to get burned out and the travel involved... because they're offered all around the United States, Canada even down in South America. We have instructors like Mike Creeden.
Mike Creeden he's like a globetrotter.
Yeah he is he's putting lots of miles on doing classes down South way-
Yeah, WAY down South,
We keep it to you know, three to four classes spread out among the instructors. Yeah so keeps it fun, keeps it manageable and and keeps us fresh I guess.
So it's about time to wrap up but I feel like we just got started we could go on and on. But thank you so much for this conversation.
Oh, my pleasure...
-and boy I really see eye to eye with you. I bet you've articulated it's so much better than I could so, thank you so much Kelly. Okay my last question for you - I think I already know the answer - when I ask it. So at the end of the OnTrack podcasts, I've observed that many people who are designers have interesting creative hobbies or things they do. So this part of the podcast, we call ‘designers after hours.’ So I know one talent you have after hours. So tell me what you do for fun with that creative brain of yours after hours?
You know I just recently moved to Spokane so there's not many after hours. After hours gets dark really fast up there, in the wintertime. However in the summertime it's just the opposite. We have lots of daylight up in the Pacific Northwest and I don't know if this is the answer you're looking for, but one of the purposes of the movement up there was to fulfill a bucket list of getting a hobby farm and raising cows,
No way! I wasn’t going for that, but that’s cool.
I know you weren’t so we did the hobby farm part. We moved to Spokane…
When? Wait time out, what’s a hobby farm?
A hobby farm is where you really don't know what you're doing some folks call it gentleman farmer but that's too nice of a term. I call it a hobby farm and so far we've got the chickens down we had 16 chickens laying eggs and we have 26 acres - and a barn - that we're gonna put cows on. But a sage old guy, one of my neighbors told me: You know Kelly - I asked him about what do you need to do to get cows going - he says, the first thing you need to do is build good fences. So, for two years now I've been trying to build good fences and the only thing I've been doing is tearing them down in the industry by shaking hands. How's that for an ending, yeah tearing down fences, shaking hands with the stakeholders!
That was corny! You’re a stand-up comedian as well. What I was really pointing at - and then I swear we will stop talking - is about your musical outlet?
Oh that, yeah did a lot of really really fun stuff over the last couple decades with the Porch Dogs, remember Pete Waddell and the Porch Dogs?
Oh my goodness, yeah they used to play at shows sometimes by the way.
Every time yeah it was - or it it's even fun to think about. So I'm a hacker, I uh play a little blues harp and a little guitar I'm a guitar hacker but it's another thing where this industry needs an outlet and interestingly enough the designer type is typically right brained.
Right that's what I'm saying.
A lot of them are musicians or like Bill Brooks’ sculpting I don't know... I really love hanging out with designers.
Yeah so to get together - you know it was a natural occurrence to just start playing music and jamming it. So Pete Waddell was a great mentor for me way back.
So, for our listeners, Peter Waddell is the publisher at UP Media, so not only an industry guru but founded the Porch Dogs.
Yeah, yeah, and so we played and played and I met so many great people through that and we still carry on. At trade shows somebody will bring their guitar, somebody will bring a harp and that's all we need.
That's all we need - fun! Okay Kelly thanks so much for joining me, I could talk to you all day, it's so great to connect and you only get to connect at trade shows.
It’s my pleasure Judy.
But now I want to come to your hobby for…
Where are your boots?
I have them I suppose. Well that's it for this edition of OnTrack Podcast. Thank you so much for joining and we'll see you next time.
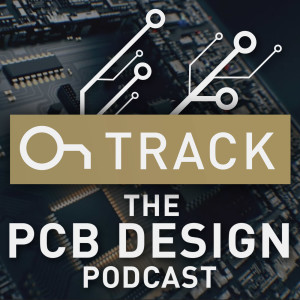
Tuesday Mar 20, 2018
RF and Microwave PCB Design with John Bushie from ASC
Tuesday Mar 20, 2018
Tuesday Mar 20, 2018
What material do I use? Many PCB designers ask this question. This is an episode about RF and Microwave PCB Design as well as Design for Manufacturing or DFM and it will help you to understand material choices and where to get answers about high speed laminates. Join John Bushie, Director of Technology at American Standard Circuits and Altium's Judy Warner in a discussion about High Speed laminates and the exciting world of RF/Microwave PCBs.
Show Highlights:
- John and Anaya's new book on iConnect007 about RF/Microwave PCBs
- You can design something that meets IPC standards and still have problems.
- What kind of material do you need? That depends.
- There's what you simulate, and then there's physics. Physics trumps theory.
- PCB101, a manufacturing educational experience pioneered at ASC
Links and Resources:
- American Standard Circuits website
- The Printed Circuit Designer's Guide to Fundamentals of RF/Microwave PCBs
- The Printed Circuit Designer's Guide to Flex and Rigid-Flex Fundamentals
- John Bushie on Linkedin
Hi everyone, this is Judy Warner with the OnTrack Podcast, welcome back. Today we have a really great guest for you. I'm really looking forward to sharing my guests with you and please, if you would follow me on LinkedIn or on my Twitter which is @AltiumJudy and if you would like to follow Altium you can go to our Facebook, Twitter or LinkedIn profiles.
So let's get started. Today I have the great pleasure of being with John Bushie who is the Director of Technology for American Standard Circuits which is outside of Chicago area and ASE specializes in both RF microwave circuits and also flexible circus but today I want to talk to John about a new micro Ebook that they have published through iConnect007 and this book is near and dear to me.
Some years ago I wrote a guest blog on a microwave journal because so many RF and microwave engineers and just engineers in general are being tasked with designing their own boards. And particularly in the RF and microwave space a lot of these designers, these guys are designing boards and haven't had the opportunity to spend a lot of time in a fab shop.
Yeah, and they really just don't get a chance to be exposed to as much as we do being a fabricator. Since a lot of the people at our organization tend to be a little bit grayer in appearance we all have a lot of experience and the reality is is we can share this with them. One of our most important jobs is being able to educate them, and that's really how I think of myself, educating other people sharing the knowledge that I've gained over the years and just trying to help them out with their designs because ultimately we just both want to be successful.
Yeah absolutely and as you know, I spent 25 years or so in the fabrication industry and when I had a stint in the RF and microwave industry and it was like culture shock, John, like it just felt like a whole different animal, it was like drinking from the fire,
Were you working with the designers at that time?
Yeah so it was like... and I felt completely inept at first when I started there to talk about laminates but all of a sudden we're talking about performance instead of just mechanical dimensioning and making…
- sure we're just used to meeting specifications right?
Right!
- And those have a physical dimension to them and the route is you start getting into this realm of higher frequencies and you start to find out what's really important to these designers.
Yeah, and I started to feel it, the more and more I learned the more kind of stupid I felt and the more I realized; holy cow there are so many ways that a board shop could screw up and there's literally…
There’s literally thousands of different ways we could manufacture the same board and the reality is is we always have to try to manage any of the risks that the design presents and certain aspects of certain designs actually will will present problems, or they'll complicate other features that are important to the RF designer’s ultimate performance goals, and so working around those issues is what is so exciting about it.
It is exciting.
It's really challenging and fun and what was really stunning to me is to really get to the point where I realized; oh my gosh we could be 100% compliant to IPC standards...
-and still have something that doesn't work...
… and make a trash board - that's exactly correct.
Because you know we’re within tolerances so we did a little of that, but you know what, if we over etched and you know that circuit had a little too much under or over etch or whatever that the performance went to heck and and they're like, no this is not what we simulated in and we're like, too bad so sad it's the IPC standards so it's a lot more complicated. So why don't you go ahead and talk about, sort of this is now? This is a book I wish I had enough brains to write so I'm glad you did.
Don't give me too much credit.
So why don't you tell us a little bit about it? Well first why this book?
I just wanted to share the knowledge that I've gained and I've had the opportunity and the great fortune to be able to work at several world-class fabricators. Poly Circuits in my early days helped get Mega Circuits into PTFE materials and now with American Standard circuits. But in the middle there - I was also able to work for an RF circuit board laminate company at Taconic. Well I got to work very intimately with the designers in North America as well as Asia and Europe so it's the ability to be able to interface with what are some of the most brilliant people I've ever met just taught me so much and when you talk about coming into something feeling completely ignorant… well that was me a long time ago and the reality is now I I hope that I can share some of the knowledge that I've gained through all this experience.
So since I know you've been it Taconic you probably told me that before, and just wasn't remembering it. But let's just pause there for a second and just talk about composition of high speed materials.
Sure.
Because that was kind of the first place I started and the realization of you know with Upper 4 you've got some fiberglass resin…
- resin, glass, maybe fillers and there you go and you're off to the races. Now talk about high speed materials, the different compositions what, they are?
What they are and… traditionally high-frequency materials were generally all PTFE based and what that meant in the early days is that there was very few flavors I think everybody knows the term Duroid. great materials fantastic from an electrical performance standpoint. But some of the mechanical properties were perhaps a little lacking and that's really the largest improvement we've seen in materials throughout the years.
It’s the increase in strength and dimensional stability of these materials which makes it easier for us to fabricate because honestly if a material moves around a lot during the physical stresses that we put it through then we have tendencies to have registration issues, or it causes other issues within our manufacturing. The biggest change in the materials nowadays is the change to higher thermal conductivity materials. That's where we see the market going and respect to those types of products as the power levels go up and designs get small. Everybody's got to deal with these heat issues that they've got.
And I'm sure automotive is driving a lot of that.
Well automotive does too... that's an interesting… another realm that we're talking about, is these very high temperature materials and a lot of the underhood automotive application. It's something we just get a little bit of exposure to but it's also a very interesting field.
Yeah just one of the things you mentioned too are... I neglected to mention to our listeners that we are here at Design Con in Santa Clara, so if you hear some voices in the background it's because we're here at a trade show and so just wanted to mention that so ASC is here with a booth and also rolling out hard copies of their book so. So the going back to the laminate side. So, I know from the RF experience I've had that each of these compositions of materials behave differently right?
Mm-hmm.
Like when I think of PTFE distinctly and there's a completely different system, you know?
Distinctly, and when you go from the the thermoplastics to the thermoset materials both have their advantages you know. PTFE is a fantastic material in that it's largely inert. It's inert to the effects of high frequency radiation and it doesn't change and that's what yields the fairly consistent results that you get with PTFE materials.
Now there's the introduction of the lower-cost thermosetting materials that also have pretty good electrical properties and that that can be a huge benefit just in the rigidity. Overall dimensional stability and the fairly low CTE values you know. At the same time, they've been filling PTFE materials for years in order to alter their properties and they've actually done a phenomenal job and bringing the CTE values very close to those of copper, which is the ideal since every board, every layer is clad with some level of coppers.
Right.
Yeah I mean we could devote…
You know I this is an interesting subject and there's a new material that comes out virtually every couple months all right and there's just a lot of good materials out there there it really is which is really what the whole key to this.
Yeah which is really actually good for industry great for designers right?
Which is why when we get asked the first question that everybody asks is what's the right material for my design. That's an impossible question to answer on the face of it but the reality is, as we dig deeper and deeper into these designs, we can kind of get a sense of where their price sensitivity lies, what level of performance they need, and just just seeking to go through the process and understand what their requirements are.
Before we got down that road... if I read - I had the pleasure of reviewing your book before it got published - and don't if I remember correctly. Don't you have a chart there or is it on your website that shows, like side by side, all the differences?
We do, it compares all of the various laminates that we use and actually, I had had a ex-colleague from that company that I used to work for mention that.. hey I left out a few of the most recent materials particularly in Europe. I apologize Manfred, I did not know that there were materials released, but thank you for catching that and I appreciate your insights. Because you know again going back to that subject. I've been phenomenally lucky to have worked with some fantastic minds as well as fantastic people in this.
Which I'm sure is an awesome asset for you at ASC. So okay so give us a quick rundown again. This is a micro book this is not a textbook?
Yeah and it was never intended to be a treatise on the subject it's really to touch on some of the major - I'm gonna call them issues for lack of a better word - because if we don't deal with them at the beginning of the design they can end up taking what is otherwise a fantastic board and make it virtually non manufacturable and this is really about DFM.
It really is.
You know we go into all the subjects - obviously not every subject as it relates to circuit boards - but from material selection, to copper roughness, to choosing the right stack ups and balancing your constructions whenever possible. How does copper thickness play a role in the ability to be able to manufacture? To find fine lines and spaces, edge plating, cavity constructions, thermal management. It touches on that wide variety of subjects and it just kind of gives you an overview of what we deal with. What to be thinking about when you're going through this process and hopefully it'll be an aid.
Yeah well, I can imagine that this will be a great sort of starting place because I'm sure you get asked these same questions over and over again?
Yes and the reality is, is we want it to start the dialogue right you know - and we want to be able to put something in your hands that can aid you right now. But also help you think about certain aspects so that we can work together right. We've dealt with some designs that deal with basically a composition of every circuit technology known to man in one board but since we've worked so in-depth with this customer for a very long period of time we've ended up balancing out the performance requirements that they need with our ability to be able to manufacture right. Because it doesn't matter whether it's the highest performing smallest assembly in the world, if we can't make it or we get 10% yields, it's it's not going to end up satisfying the customer.
Yeah and that's another thing I remember feeling kind of pounding my head against a wall like you know now that I'm on the EDA side of the market right, there's such good powerful EDA tools out there and, but they won't necessarily flag you and say, no dummy you can't...
Yes indeed you're right, and that's exactly what ends up happening. I mean we've gone through designs where people expect to get a certain level of performance and all the materials are there, the components are there and we find that one aspect was missed and you know, there could be copper roughness. Oh we didn't account for that right. So you know we get, hey I'm getting minus 3db down from what I expect to be getting that's a huge loss it’s almost double.
Yes so there's what you model and then there’s reality.
My friend used to say, there's what you simulate and then there's physics.
Exactly then there's, yeah physics gets in the way right? And then John Toussaint who actually works for you guys, his favorite line used to, be physics trumps theory.
Right very true.
Right? So you know there's just limitations to what we can manufacture so well this is a really, really great again as I said I wish I had the ability to be the one that wrote this but I'm so delighted. I think it's truly a great service not only to your customers but just to the industry to get this information out because it's sorely needed and to my ability no one has really put this out you know...
No I'll be very honest if an a hadn't worked so hard on this project it never would have been realized either so thank you for pushing on this project and driving it forward I do think it will be helpful to great many people and who knows, maybe there'll be some addition to this in the future.
Yeah that would be great and I know you guys have written one actually which maybe is another Podcast series we can talk about…
The rigid flax which is that is becoming more and more.
We're actually seeing the two integrated in some instances. Yeah when I was referring to that one design that's exactly what we're talking about. Yeah IMS flex RF FR4, multilayer blind and buried vias and flex later. Right and the middle core I'm sorry I left that out.
Oh good lord... but manufacturable - piece of cake! Can’t you give me. you know $10 off that board John?
Sure exactly we're gonna deal on price, but you know, you do what you can there and you know you've got to try to make it. You've got to try to make it successfully and usually we try to make it for a cost.
Of course like people, not everyone really understands. I wish I could take every designer and engineer and they would be like forced to go through board shops like five times.
You're right. I mean we even created a tool for that called PCB 101 just to kind of give you a good overview. Once you start breaking it down and you think of the circuit board processing as each path is in itself a process right. Then you start to add up all the processes that the board is exposed to as it goes to the manufacturing operation. When we get to some of these complex designs it might be going through 150 - 200 different operations.
Yeah, exactly right.
And all of them have potential risks so absolutely...
Yeah people don't really… you know, we've come to sort of take for granted printed circuit board manufacturing. I think we're all impressed with semiconductors and their performance and bla bla bla - boards are… they're dumb and they’re just boards and they just lay there or whatever.. except unless that that board is made right none of those parts work.
And with high-speed digital ou have controlled impedance with RF its dielectric constant line width and loss. So I mean you've got one or the other.
Yeah and now with the added dimension of thermal management, since people are becoming a much more... which is fantastic because it can offer performance levels that weren't even theoretically possible just you know five ten fifteen years ago you know.
So let's talk about where people can find the book first which I think is on the iConnect007 website correct?
That's correct.
And and then where can people find more information about ASC John?
They can go to www.asc-i.com.
Okay let me check that one more time - www dot ASC (that’s American Standard Circuits) dash-i dot com - okay very good.
So is there anything else that I may have not covered or asked you relative to this awesome book you just put out?
No it's just all I do, is just encourage people to give it a read, say that it's downloadable for free.
Yes it doesn’t get less expensive right?
It doesn't get less expensive.
So you basically just put in your name and your email and download it and it’s a PDF right? So it's a digital ebook.
I'm gonna look over just to get a little bit of agreement, that is in PDF form is that correct?
Yes it’s in PDF form.
Excellent okay PDF form and, here at Design Con you guys have brought a limited number of hard copies to give away so I'm sure those will be appreciated and and I'm sure once you start getting readers you'll probably end up printing out more of those but, well thanks so much for your time okay.
So now for the fun stuff I'm going to ask you two fun questions. First what is your favorite techie gadget that you own?
Wow that's difficult…
Like that you can't live without...
Well I mean everybody's gonna say their smartphone nowadays but besides that, yeah I'll be honest, no I always go back to home entertainment. I'm sorry okay.
Well hey that is totally okay. Do you have like a pimped-out home entertainment?
I have a pimped-out setup at home.
Okay let's hear it let's hear the specs!
It's got over a horsepower of wattage, it’s considerable it's got 13 speakers. It's a little excessive - nuts. People say I’m nuts when they go into my house but that's alright.
Is it like a home theater.. little home... wait how big is your screen?
It's only 60 inches I'm trying trying to talk five feet I'm trying to talk the wife into the 80 inch OLED but for some reason that thirteen thousand dollar price tag is a little steep. So we're gonna wait for the price point to go down.
My second question is… I know you're not a printed circuit board designer but a lot of us techie people have kind of interesting creative hobbies and things.
I'll be honest I'm the exception to that. No I shouldn't say that actually... actually I've been a bit of a computer nerd always have been, uh used to spend way too much time on computers. I think I set my first network up at home to be able to online game with, or at least network game with buddies back in 93.
So you're dating yourself?
Yes I am.
I was there.
Right but I know you can't stop getting older Judy, so...
That's right.
Okay I decided I'm gonna start counting backwards on my birthdays, that's how I'm solving that.
Okay so anything else or shall we wrap up here? Is there anything else you wanted to share that I might have left out John?
I think we pretty much covered everything Judy, appreciate the opportunity.
Oh and is there anything of note that you guys, other than booths and talking to a whole bunch of people for a couple days. Is there anything else that you guys are bringing besides your book to this show that may be of interest to or listeners?
I don't have any specifics that come to mind. I mean the reality is this is what we're working on right now. We're bringing this effort forward and hopefully, like I said, people will find value in that but the nice thing is there's our rigid flex expert Dave Lackey and myself so when we come here we try to bring some value to the people that might stop by
Okay so while I have you recorded on it, will you promise to say... send Dave Lackey back to talk to us about rigid flex?
Well we will round them up and send them in here okay?
Great tie them up okay!
Great well John thank you so much and thank you again for taking the time and effort to put this book out. I think it's going to be of great value to the industry for certain. Your customers and I really appreciate that laminate chart you put together - I wish I had that a long time ago.
Exactly.
Well thank you very much and have a great show.
Thank you again this has been Judy Warner with the OnTrack Podcast please remember to subscribe and add us to your favorite RSS feeds and we look forward to talking to you next time and always stay OnTrack.
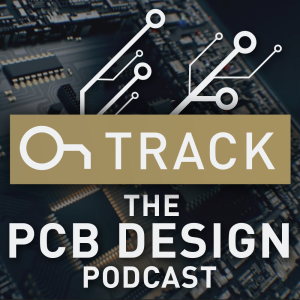
Monday Feb 19, 2018
Monday Feb 19, 2018
More than ever, people are doing Flex and Rigid Flex for the very first time as industries drive for smaller, more user-friendly devices. Join Altium's Judy Warner and OmniPCB CEO, Tara Dunn for a conversation on industry trends and cost drivers.
Show Highlights:
- What is driving growth in the market? Space, weight, packaging.
- Flex is everywhere especially handhelds and medical devices, uptick in flex and rigid flex PCB across every industry.
- Three main cost drivers for Flex and Rigid Flex: Materials selection, Panel utilization and Technology.
- And a fourth consideration - understanding your fabricator capabilities and making sure you’re matching your design to their capabilities.
- Most common materials: copper and polymide.
Links and Resources:
- OmniPCB Company website
- Tara Dunn’s AltiumLive presentation
- Geekapalooza
- PCB Advisor site
- Flex Talk
- FlexFactor by NextFlex
- Jabil’s Blue Sky facility in San Jose
Hi everyone, this is Judy Warner with Altium's OnTrack podcast. Welcome back, if this is your first time we're glad to have you. Before we get going today I've got a great guest for you, but before we get going I wanted to remind you to please subscribe to this podcast, and you can follow us on iTunes, on your favorite RSS feed, or wherever, whatever app you like to use for your podcasts.
Today I have with me Tara, oh before I get going on Tara I wanted to also say, please follow me on LinkedIn and also on Twitter, I'm at Altium Judy, and Altium you can also follow us on Facebook, Twitter, and LinkedIn. Okay, Tara, hi my friend, so good to see you, welcome to La Jolla, California.
Thank you.
So, Tara was a recent, is a dear, dear friend of mine in the industry. There's not many of us women that have actually been in the printed circuit board business and understand how circuit boards are made, but we do indeed know how that's done, and Tara owns OmniPCB. She's based in the Minneapolis area, and she is a real flex expert, and we've been friends for, how long has it been now?
I don't know, what six or seven, eight years? Probably something like that. Anyways, Tara and I met at a trade show and instantly started introducing each other to our friends and colleagues and next thing you know, we just created this energy, and we both have written columns for iConnect 007. Tara has an event in Minnesota called Geekapalooza.
Which Judy helped bring out to California. California, so I brought it out here to Irvine, and then we brought it together to Boston, so we've had lots of professional adventures together, so it's my joy to have you and for us to
learn more about your expertise in flex. So, how are you liking La Jolla?
I know you're here for a few weeks, I bet you're glad to get out of the snow.
Oh yeah, it's no hardship to leave Minnesota winter this time of year.
I'm loving the sun and the beach, so like- What was the temperature when you left?
Minus five, something like that, and slippery roads and cars were going into ditches, we're driving to the airport I'm like "just please make it there so I don't miss my flight"-
Oh my gosh. -and I landed here, it was sunny and beautiful.
Right? I know.
I know, that's why we like it here. It's expensive to live here, but we love it.
So, welcome to the La Jolla office, anyways. So we want to talk today about your deep knowledge on flex circuits, which are becoming more and more commonplace, right?
You and I started out in our careers really focusing on Rigid FR-4, very standard boards, but it's really evolved now. Oh yeah, flex is a significantly growing portion of the market.
And what do you think's driving that?
Space, weight, packaging. You know, it's small it can be smaller, lighter, folded, it's really perfect for all of those electronics, the handheld electronics, medical devices.
Right. So what would you say, give us an overview, you just said medical devices, what other things are you seeing an uptick in the flex market?
You know, really across the board. Across all industries.
Really?
Absolutely. You know, we've got companies that have been working with flex that are developing maybe more complex flex or rigid flex and, you know, easily once a week somebody's contacting me brand new, just trying to figure out how to work with flex and how to design flex and what's different, what do I need to know. So a lot of new applications cropping up are people that are just trying it for the first time.
Well, that's why we invited Tara to be our flex expert at this year's Altium Live, and we'll share the link below but there's a really great presentation that Tara gave at Altium Live, and we have the video and her slide deck, so we'll share that at the bottom here so you can check into that later.
So, let's talk a little bit about that presentation. That was speaking a lot about cost drivers. So, for the designers and engineers listening, what are some of the just overview, basic overview, of what cost drivers are for flex and rigid flex?
Okay, so we often talk about three primary cost drivers, materials selection, panel utilization, and technology. I kind of like to throw, a little bit tongue-in-cheek but not really, a fourth one in there, which is understanding your fabricators capabilities and making sure that you're matching their capabilities with your design. Yeah. That's not just true in flex, by the way.
True, it's across the industry. It's across the board.
Yes. [laughter]
So, start with materials. How does that affect cost? Okay, so there are just so many materials you can choose from with flex, so, but just for this quick discussion let's focus on the most common which is copper and polyamide.
So, even focusing just on that segment, your fabricators are going to purchase laminates. They come in generally three different types which would be, two of them are adhesive-based, one with a standard acrylic adhesive, one with a flame retardant version of that adhesive, and then adhesive-less materials.
So, all of those types come in a range. Typically your copper thickness is going to be a quarter, or a half ounce to two ounces. It doesn't mean you can't get a flex circuit greater than two ounces, it just means that your fabricator has to create the material themselves.
Right.
And polyamide thicknesses are generally between half mil and six mil.
When you said your fabricator has to create that, does that mean they actually take the material and plate it up in their tanks, or you're buying a specialized material from the materials supplier?
Right, you would buy the polyamide, the adhesive and the copper and the thicknesses that you need.
So, like I said, huge range of options that you have when selecting materials for flex. So cost drivers, keeping that in mind, you know, why would you choose one over another or how does that progression go?
Typically, the adhesive-based options are going to be a little bit less expensive.
Okay. Okay, and they are typically used in single- sided, double- sided, maybe three or four layer flex is where you'll see those applications.
As you go into higher layer count, or rigid flex, the adhesive-less material becomes necessary. Highly recommended for rigid flex.
There's a z-axis mismatch between the FR-4 material and that acrylic adhesive, so you don't want to introduce the acrylic adhesive into the FR-4 stack-up.
So that's why, you know, your fabricators are always going to recommend adhesive-less materials.
All right, that makes sense. Mhmm. So, it's kind of like cost versus function-
Right.
-at certain point-
Right.
-that you need to keep in mind.
Right. So, other than materials, I know, what are other things that help drive the cost? I mean I think that's what people are afraid of, right? They think "oh flex is too expensive, I can't go that way" but they really need to go that way, route, for functionality, and I think really what you taught us at AltiumLive was it's not that cut-and-dry, right? If you evaluate all these different things then it may not be as expensive as you think.
Exactly, and as you decide to move to flex, you know, working with your fabricator on the materials side specifically can really help drive out cost.
Is it looking at just the raw material? You know, you're generally going to be FR, flame-retardant, material, LF adhesive, and adhesive-less, but if your fabricator is building a lot of rigid flex they're gonna stock more adhesive-less materials, and your adhesive-less material is gonna be probably less expensive-
Because they're buying more of it, they have it in stock you don't have to worry about minimum.
Make that match, and so finding someone that does a lot of flex and rigid flex is going to help you right off the bat. Exactly, and understanding the material sets that they're using, and you know a great way to do that is to ask their field applications engineering group to help you with a stack-up.
'Cause if you're not directing them in a certain direction they will default to the material that they're using most commonly.
So it's a really good way to make sure you're fitting that gap. Right. So what are some of the other cost drivers?
You know, we look at different types of coverlay. Coverlay kind of follows a progression.
So like, explain what coverlay is. So, with flexible circuits there's two types of coverlay.
There's a flexible solder mask, which is very similar to our board type solder mask other than formulated to be flexible but applied the same way.
It's a good option for circuits that might be single sided, double sided or less than two ounces of copper. Okay.
Tends to be a little bit less expensive. I see.
It does have a limitation in flexibility. It is flexible, but if you're having a highly dynamically flexing application it's probably not your best choice.
Right. But another advantage is it does allow you to form those nice 90-degree angles on your surface mount pads.
Of course. But when you need to, when you're concerned about reliability for flex life, the polyamide cover length, so it would be the polyamide that's the same as your base material and a layer of adhesive.
That would be the next option that you would want to go to. The limitations on that tend to be, you know, because you're drilling or routing that coverlay, you're gonna have a round or an oval opening.
Oh, okay. So as your circuits get more and more dense, it gets more and more difficult. We jokingly call it the Swiss cheese effect-
Right, you drill it and you take off the back route entry and there's not enough material there to even hold it together. You know, it looks great on the screen when it's this big but when the part's little. So your fabricator will watch out for that if you're doing a design. We all do try to minimize that impact.
The circuit board designer may be asked to gang open or, you know, make a larger opening over several pads to kind of alleviate that problem. And then continuing on that cost spectrum if you need the polyimide coverlay and you need that individual pad coverage, laser-cut coverlay would be the next option.
Okay. So that allows you to get the nice 90 degree angles for the surface mount pad, much tighter registration.
I would think from a cost standpoint too, in this case like laser cut, again a fabricator that doesn't do a lot of production of these kind of circuits may not have that equipment, may have to send it out, which drives the price up.
Exactly, exactly.
So, you know, I could see, that would be another benefit to making sure you're finding a fabricator that's really good at this technology.
Exactly.
Okay. Are there other areas or did we did exhaust that one?
I think on the materials, yeah I think that those are the two primary things to look at, is the base material and the coverlay.
Okay.
So, it's always easy to kind of relate to that if we can hear a case study or an example that you've had, you know in your career, is there a couple stories you could tell us?
Sure, sure. So, there is a medical application, for example, and trying to reduce the material cost it was designed as a three layer rigid flex and flex being on the outer layer in that case.
Oh on the outer layer, okay.
Because of the three layers, okay?
So, but then in this case that required the flex to be button plated to maintain the flexibility and it required the circuit to have to be sent out to laser-cut for the coverlay to maintain the surface mount pads. So those two together required it to be done on a smaller manufacturing panel for the tighter registration.
So, very expensive circuit and very difficult to manufacture. After a review with a fabricator, they decided to go to a four layer rigid flex, more standard construction. So the material costs are higher but it eliminated the need for the laser cut of the coverlay, it eliminated the need for the button plating and it was processed more standard. So although the material costs were higher the overall cost of that flex circuit dropped dramatically. So it's not always about look at the material cost and run, right, it really is about collaboration, which you and I both over the course of our careers have sang that song, you know, in a variety of circuits right? It's not, but I can see how in the case of flex and rigid flex it's even more important, right, because there's all these variables.
Exactly, and that tends, flex and rigid flex tends to be a product that people are a little less sure of themselves when they're designing, have a lot more questions, so my advice is always to identify a few fabricators that you think will be good partners and then involve your fabricators early in the design. You know, because they're doing flex and rigid flex all day.
Right.
They've learned a lot of lessons so we all might as well take advantage of those lessons. Yes, absolutely, and that reminds me, another plug for Miss Tara is that she writes a column for the PCB 007 magazine monthly?
Yes. Monthly, specifically about flex- Yep, it's called Flex Talk.
Flex Talk, there you go.
So there's another resource that, and she usually covers a lot of these in that magazine and I always, I always look forward to reading your columns. So another case study?
Okay. A second case study I can think of is a military application.
The product was, I would say having probably 90% failure in the field after assembly. So, very very expensive after a fully populated board and what happened was it's a rigid flex and it was being bent and it was cracking.
So back to the drawing board, what can we learn from that?
Turns out, simply re-did the stack up and went from adhesive based materials to adhesive-less materials.
Oh wow.
So it eliminated only three mils thickness in the overall stack up but it was a thickness, and the bend radius was causing that cracking. So by making that one simple change in that stack up, you know they've had 300 assemblies completed now with no cracking at all.
And there's the expertise, right? Like who would know that three mils could fix that problem. I would have never guessed that in-
Yeah, it seems insignificant, especially when we're used to looking at thick rigid boards 3 doesn't seem like anything at all. It doesn't seem like anything at all.
That's so cool.
Well, thank you. Those are great stories.
You know, since you and I started in this industry, there were, I'm kind of shifting subjects now, a little bit and I wanted to talk to you a little bit about women in our industry. So, there are far more women in this industry now than there used to be. There still isn't that many of us who actually are on the front lines of sales and marketing that kind of thing. How did, I know I didn't end up in this industry on purpose. I love it and I love the industry, so how did you find your way, and I don't think I've ever asked you this?
I'm here completely by accident. See? We didn't do this on purpose.
No, my first job out of college was in the accounting department of a flexible circuit manufacturer. Okay, what was your major?
Economics and industrial relations. Well, there you go.
I didn't know what a flex circuit was when I started there. Right.
Because of that, they required me to work out on their manufacturing floor and learn how to build a circuit, so I was out on that manufacturing floor for a few months.
No way, I did the same thing but- Really?
Yes, yes I-
I'm so sorry to interrupt you, but the first circuit boards shop I worked at, and they had this whole language, these terms and things I'd never heard, you know what is SMOBC and I'm like, I don't know, solder mask over bare copper, and so I asked a production manager
I'm going to come in on Saturdays and he's like, I'll put you in every department.
That was like the best education ever, wouldn't you agree?
I agree and I totally didn't appreciate it at the time.
Yeah.
But looking back I would have never learned the process as well, because I was running equipment and, I'm really terrible at registering coverlay. I've learned this. It's not something I should do. I don't have that hand-eye coordination, but it was it was a good thing to learn.
Yeah, absolutely. That's so funny, I never knew that about you.
So, what do you think we can do to sort of encourage, I mean we're doing a lot to encourage women in STEM and encourage them to become exposed to these types of careers. What do you think would be a good way, or how are some ways that you've seen, oh I know one thing you're going to tell me about right!
Okay the Flex Factor program, Flex Factor, put on by NextFlex, so centered around flexible hybrid electronics, they have a program that reaches out to high school kids and it's an entrepreneurship program that ties in advanced manufacturing.
So they go to Jabil, they get to see all the cool things, it's a month-long program.
And this is in the middle of Silicon Valley?
Yes.
So fun.
And I believe it's expanding beyond that.
Wow.
I was lucky enough to be on the judging panel at the end of one of their last ones.
So much fun, but what it does is - it takes students who may or may not be interested in a technical field, they might be interested in marketing or entrepreneurship, and it is a month program.
First week they kind of get the charter and you have to develop, it's about product development, what kind of need do you see around Health and Human Services and what how could you solve it using a product that's using advanced manufacturing?
Uh-huh.
And then they get to go into the fancy Jabil building and see all the really cool things that they do there. They tie that into the next step, is entrepreneurship at a community college, and the students are actually given credit, college credit for this program, and then the fourth and final week they need to pitch kind of shark tank style to a panel and go through the whole product development process, profit and loss, and I mean it's just it's an amazing program, and it's so fun to watch kids you know who, I talked to one girl
Jordan and she had really no interest in manufacturing or advanced manufacturing until, she wasn't exposed to it until this program, and now she's got a lot of ideas.
Which is so great! I don't know how kids otherwise would get exposed to manufacturing, and when you go into a facility like Jabil or TTM or some of these big facilities, you know I think kids think manufacturing is like a dark, dank building with, you know, I don't know, something awful and you go in and there's robotics and chip shooters and all this amazing high-tech equipment and these clean rooms and you have to wear the whole bunny suit and the glasses and you go in and you're like wow this was not what I was expecting and that's so great. I forgot that you told me about that program and the whole shark tank, which makes it so- oh it was so much fun.
-so what did the students pitch? Or like what are a couple things that the students pitched?
You know there was all kinds of different things. They tended to kind of centre around babies or athletes.
What?
Well, different injuries that you might have as a student-athlete and how to rehab those injuries.
Oh, okay.
Or baby monitoring devices.
Oh that kind of, okay.
Yeah.
So, what was the winner? Was there, is there a clear winner, do you remember?
I don't remember who won for the panel I was on because they didn't announce it the day that I was there.
All right. And so you're continuing now, right? To be involved with this initiative, and is this gonna be each year, or how often do they offer it?
They do it throughout, throughout the year. I think they just had another round that went through so, and I might mix up the numbers slightly, but I think that the first program that they did which would have been the fall of 2016. I think they had eight students participate and its teams of four. So now they are up to thousands of students participating in this program. It's just growing and growing so fast.
We're going to make sure that we put that website, so you have to make sure and share that, the URL, so people that are listening can look into that. Such an exciting program and I, you know, here at Altium we're doing so much with the universities and stuff and I love to see it happening, and it's so fun when you see the light bulbs go on and, you know, we love our industry and we want to keep it vitalized.
Yes, yes. I think this is a great tool for generating some excitement. I know, I love it.
I want a program for people our age to go back and do that.
Right? Wouldn't that be fun?
Yeah. What would we call it?
I don't know, we'll have to think about that later.
So okay, here's a really wonky question I think I already know the answer but I'm asking anyway. Are you a nerd or a geek?
Geek.
I asked the woman who runs Geekapalooza, that was a really easy answer.
I know, okay but why do you think a geek? Why is it not Nerdapalooza?
Like, why do you think you're a geek and not a nerd?
That is an excellent question.
Other than geek sounds better than nerd. See, I know, well- It's the general excitement over something that other people-
Right, like geeking out over something right? Geek Squad.
It's become cooler.
I think geeks are cooler than nerds still, like just generally. I think that's the consensus. And my other wonky question is, on a scale from one to ten how weird are you? Well, pretty high up there, yeah.
So like, what are some wonky things that make you weird?
You know, I -
Well first of all you're in this industry.
First of all it's the industry right? I laugh because I'll go out to have lunch, a work lunch, and sometimes I think if anybody is listening to our conversations, we're talking about impedance control and stack-ups and EMI and I'm like, what are they talking about over lunch?
I know I posted a video of me talking about fusion bonding on my personal Facebook page, and it blew up and people are like who are you? What are those words? They had no idea that I spoke this whole other tech language. And if you're out of the industry, you know, most of my friends, you know, my parents, my family, they don't know what I really do.
I know, I know. We're gonna put your podcast, this podcast.
We're gonna put this podcast on your- Can you cut that part out?
No we'll put it on this and see what they think of you on a podcast talking about coverlay. They'll be like what? And my final question would be, well, one thing I know about Tara Dunn is that you love the beach even though you live in the snowiest place in the country.
I live in a landlocked state.
Yeah, there's that. But I noticed that a lot of technical people have really interesting hobbies, so what kind of things you like to do with your family or places you like to vacation or things you like to do in you're very few off hours that you have Tara because you don't have a lot of off hours.
I don't, but with the job that I have it allows me to travel quite a bit because I can work pretty much remotely from anywhere and make that easy. So, yeah we love to travel.
Specifically the beach. It's one of my favorites or in the winter anywhere warm. Desert area, everything's great, and I don't know what happened this year but suddenly I've become a music buff.
Oh. I haven't been to a live concert in a few years and all of a sudden I think I have six or seven things booked so..
That's so funny.
I don't know why. It's because your son went to college and you have a little more free time. That could be it.
I don't know, I'm picking up new things now that my kids are out to college so that's probably the reason why.
Well Tara, thanks.
It's always a blast to hang out with you, and it's so fun to have you in California.
Thanks for having me here. Usually we're on the phone on conference calls and we actually get to see each other in person, it's fun.
So again we'll share lots of informative links for, that Tara has shared on this podcast and some that she didn't have time to talk about, we'll share them below so you can tap into all the interesting resources that Tara has, and I want to thank you again for what, for listening and or watching the OnTrack podcasts today. Please remember to subscribe at your favorite podcast app. Until then, always remember to stay on track.
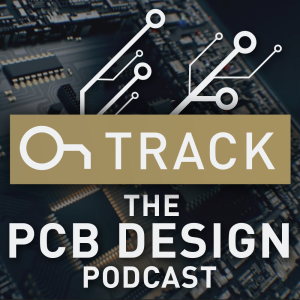
Monday Feb 19, 2018
Monday Feb 19, 2018
Jeremy Blum is working at Shaper, reinventing hand held power tools starting with the revolutionary CNC router, Shaper Origin. Join Altium’s Judy Warner and Jeremy for a conversation on making tools for making things.
Show Highlights:
- Shaper is a human in the loop company
- CNC, or computer numerical control varies in implementation. Large CNCs can be Desktop size to warehouse size.
- Shaper Origin created to be an affordable, portable handheld tool and the way The Shaper Origin works, computer vision based and real time motor control.
- Precisely calibrated and sophisticated industrial robot that we are selling as a consumer device
- “We’re both making tools to help other people make things”
Links and Resources:
- Exploring Arduino: Tools and Techniques for Engineering Wizardry
- Jeremyblum.com
- Jeremy Blum’s Youtube Channel
- Shaper and The Shaper Origin
- How to take a chessboard with Shaper Origin
- Shaper Projects - Forum
- Shaper Instagram
Hi everyone welcome back to Altium’s OnTrack Podcast. This is Judy Warner and today we have a special guest that I'm eager for you to meet but before we get going I'd like to make sure that you subscribe to our podcast and favorite us on your favorite RSS feed. You can follow me personally on LinkedIn which I would love or on Twitter @AltiumJudy and Altium is also on Facebook, Twitter and LinkedIn.
So today we have a young rockstar of engineering with us, named Jeremy Blum, and I'm gonna read a little bit so forgive me while my eyes leave the screen for a moment. On his website it says this my passion - using engineering to improve people's lives and giving people the tools they need to do the same.
Jeremy is currently the head of Electrical Engineering at Shaper where they're using computer vision to reinvent the way people use handheld power tools. Prior to joining Shaper he was a lead electrical architect for confidential products at GoogleX including Google glass. He has his master's and bachelor's degree in electrical and computer engineering from Cornell University. He did a lot of amazing things at Cornell and he has an insatiable passion for building things: prosthetic hands, fiber optic LED lighting systems, 3d printers and scanners and on and on.
Some of his work has been featured not only in international conferences in peer-reviewed journal but in also popular media outlets such as the Discovery Channel, Wall Street Journal, and Popular Science magazine. He was also named Forbes magazine 30 under 30 as recognition for his work that has helped America make things and get stuff done.
He also holds several patents and he loves to teach. He has a YouTube channel with lots of video tutorials and his latest, well I guess I don't know if it's your latest, but he's writing a book called Exploring Arduino. He spends most of his time investing his talents and time at Shaper. So, Jeremy welcome that was a mouthful so thanks, really.
Yeah.
So you're awfully young to have such a pedigree so I want to ask you first after watching a few of your YouTube things since they go way back I noticed a couple t-shirts you had worn and those that said you were a geek but my first kind of tongue-in-cheek question is are you a geek or are you a nerd?
I think geek is the cool term now I think so I go with geek I think right, if you consider a nerd to be the person who is really into reading into like super in-depth topics and getting really in the weeds and stuff. I'm kind of guilty of all the above.
I would concur with that and I think geek is... that geek is like a cool term now. It used to be the uncool term like now you know nerd seems like this but nerds are like Sheldon Cooper like physics, chemistry, right?
Look smart guy, so tell us a little bit what your earliest memories were of sort of making and building things I mean most people like you remember some pretty vivid memories of taking apart home appliances are putting stuff together.
Mm-hmm, yeah so you know it makes a very perfect circle of my life if you will and that some might release memories building things are woodworking and no I work at a company making woodworking tools but the some of the early memories I have are my dad and his dad are fairly experienced woodworkers so it was spending a lot of time in the garage at home building stuff with him. I went to summer camp where they gave you all these outdoor activities and think you can do water skiing and hiking and all this stuff but I ended up spending as much time as they would allow me to in the woodworking bunk which is this little basically an 8 foot by 8 foot room with a couple of tools that, you know, I feel like it wouldn't let kids do this nowadays. But at least when I was 12, they let us use jig saws and band saws like that and I feel the liability issue is different. It's changed in the last decade or two, but when I was ten or twelve that's what I was doing, I was building furniture that was admittedly not great, but I think pretty good for like 11 years old right? And so those are some of my earliest memories.
Before that it’s the same thing you'll hear from most engineers, which is Legos and connects and things along those lines, taking apart stuff in my parents house and family’s. After I did that a couple of times I knew better about keeping track of what screws go where. It's like we put it back together but I've been taking things apart and building stuff for as long as I can remember. It started more on the mechanical side of things in this transition towards the electrical and electromechanical and robotic side of things.
As I've gotten older I saw a comment you wrote on your personal website that said you felt that engineering was sort of along the same lines as artistry. What did you mean by that exactly?
I think people use art to express themselves and to leave some kind of impact on the world around them. Convey an idea, convey a concept and I don't really think it’s any different than that. It's a lot more based in equations and math and physics, but at the end of the day, you're still kind of taking some input, some desire that you have and trying to generate an output that'll have some kind of impact on people, right?
So yeah whether you're building a spaceship or a car or some little doodad or trinket, the goal, at the end of the day, is you want to be able to give it to someone or show up someone, and have some kind of impact on them and affect the way they think. In some way similar to art in my opinion, it's funny that they've kind of come out with this new acronym. Right, there was STEM you know, and now it's STEAM right, because they've added art. I think the thinking is starting to change. I was raised by an artist and so I've always had that bug, but I like, you know, you and I were just geeking out about the Falcon Heavy launching. Like oh, I'm just as happy you know - I'm thrilled as much sort of, being in the work I am with technology as I am with art, so I think there really is a connection there.
So you are good, that's a really good job of bridging the divide STEM was, so it felt like this other thing and you were like an artist or you're in a STEM field.
Yeah that's not the case, there's so much overlap. I work with designers and everything every day and right, I couldn't do my job without them.
Well I can tell you that for me, I'm a little bit more of a creative person. I write a lot and express myself through writing and speaking communication, but I was horrible at math but I loved making things and I took things apart.
But just because I didn't have that aptitude for math, or it wasn't encouraged and it made me feel like I was in no-man's land, so for me personally I'm with you. I like that it's sort of crossing over because I'm like, oh you know I am sort of in this you know? I'm like why have I spent the last 30 years you know, in circuit boards and you know, how did I get here? But I think it is that connection and that curiosity, right so you will get up to talking about Shaper which is really what I wanted to talk to you mostly about today but I wanted to also mention that when you were very young you started this YouTube channel and you've recorded an awful lot of educational videos and really helpful stuff for makers hackers and different people have sort of used that as a jumping-off place and inspiration. So what inspired you to do that in the first place?
In the first place, well... so, I think the very first video I published was me building the computer and it was my first experience building a computer. I didn't really know what I was doing and I just thought I was really cool and I wanted to make a video of it and my friends and I were already hobbyist videographers. We really liked making short movies you know, like kids make short movies - action movies, things like that.
But we had already developed that into a business and we got pretty good at it. When I was 12 or 13, a friend of mine and I, from high school, started our first business which was doing video production and it was pretty successful for like weddings and birthday parties. Video montages, things like that. Now you can like press one button on your Macbook and it'll do it for you, but we lived in this golden age where people hadn't figured that out yet so we could do it as 12-year-olds and charge money for it.
And by the way, the 12 year olds were the sharpest people in the room. I mean, I still ask my 20-something kids, like my phone's not working you know, you guys really had an affinity and like there's, like you said; there's more than one but we're like, yeah. But it was really the rise of Technology and you were kind of right in the middle of that I suppose?
Yeah the timing was really good, YouTube had kind of just come into existence when I was building that first computer and we had experience making videos. But they were mostly you know, pictures of other people for their weddings and things like that and so we wanted to do something we were passionate about. So, a friend and I, we were going to build this computer. Anyway, they filmed it, we set it to music, people seemed really into it and then started asking us lots of questions like, oh, how did you pick this, how did you do that, and it just kind of grew from there and people seemed to really like it and appreciative and positive. You hear about all the terrible things that people say on YouTube comments right, but it was all positive. People were appreciating it and so it snowballs from there.
That's so nice - there's your creativity again right? The crossover of your creativity and your your scientific self. So, do you still keep that website up or are you pretty much tied up with the startup work?
I've been pretty damn busy with Shaper you know if I could I'd love to. The reality is it turns my YouTube stuff from the one-man show. I do all the writing, a lot of those videos involve me developing projects and all the documentation around the open source stuff you know. If a 10 or 15-minute video takes me, you know, many dozens or or more hours to produce, because I'm such a perfectionist. Like if I was less of a perfectionist and I could make just kind of slightly crappier, but still informative videos, I would do it. But I have trouble putting a thing that doesn't have high production value so I'd love to make more videos and I hope to get back to doing more. But I will admit the frequency of my postings has dropped off considerably especially in the last two and a half years or so that it that I've been in shape works.
I've been so focused here. Yeah okay, well it looks like you still have like a hundred and sixty thousand subscribers and a whole bunch so it looks like people are still engaging with your stuff even if you're not keeping up with it so yeah, kudos to you. So you did your Bachelor's and Master's at Cornell and what was your first job when you got out of school.
I had a bunch of cows, I was in school and I was also working on my own stuff overlapping with with a lot of that. My first real job, real full-time job I guess, was at Google after I finished my Master's degree but before that I had had a startup that I was working on for a while that ended up. Peter hangout, and before that I worked at MakerBot the 3D printing company for a few years. First as an intern and then I consulted for them remotely while I was in school working on their electrical stuff. But my first full-time job was that Google X.
Yeah, so... um, what kind of things did you work on at Google that you wouldn't have to kill us to tell us?
It's pretty out there now so I can talk about most of it now not all of it, but most of it, the majority of my time there was spent working on the electrical engineering and system architecture for what became Google Glass Enterprise Edition. So there was the first version of Google Glass that came out to consumers and I won't spend the time going into all the social implications of that product and things that were done poorly or things that were done well. My focus was on what became the Enterprise Edition of the products, just totally new hardware and is used by a variety of very large companies and medical practices around the country now as an augmented reality platform for basically helping with productivity. So that's a piece of hardware that's basically an upgraded version of Google Glass one most people saw, right um... all new processor and everything inside, everything's new and different but that's used by big companies like I think Boeing uses it on their assembly line to do cable assemblies. Things that they used to look at a manual for, they now see heads-up and they get feedback as they're doing it and they like cut their time in half. There's a bunch of startups building software on top of the enterprise version of Glass now for medical applications, so doctors use it in their patient interactions to pull up medical records and things like that in real time and make them more efficient and more productive. There's a bunch of other applications as well that's those kinds of applications are the things that originally got me excited about going into work on that project.
Don't get me wrong I have several pairs of glasses. I don't really wear them anymore but there was a period right, where I wore them almost every day and use them for all the mundane things. They showed in the original marketing videos like sending text messages and getting, turn-by-turn navigation and stuff and they were cool for that but the application that they ended up developing for the Enterprise Edition that I think were an augmented reality platform really shines so I'm from the department that worked on that.
That sounds like a pretty exciting project and company, a workforce you know. pretty much fresh out of a Master's program so that's exciting. So how did you go from Google to Shaper? And then let's start talking about Shaper because I've seen some of the videos and I want to run out. I want one when I go build some stuff. So tell us about that transition and then start filling our listeners in about this incredible new handheld CNC you guys have developed.
Yeah happily. So when I was at Google, one of my tasks in addition to kind of leading the system architecture for some of the products we were working on, but in addition to those responsibilities one of the other things I did there was kind of always be scouting for external technologies that might be relevant partners for things that were doing things in the computer vision space, things like that. So I go to a lot of conferences for this and me and my colleague from Google, Joe. Joe is now the CEO at Shaper. Me and Joe went to this conference called Solid-con in San Francisco where we met Alec, who is one of the two co-founders of what is now Shaper, at the time it was still called something else and so into this conference and Joe and I walked out, and everything in there was like eh, but man... did you see that one booth that auto correcting hand tool thing? That thing was so cool and so one thing leads to another. Joe ends up leaving Google and going to what is now Shaper to become the CEO to join Alec and align co-founders and shortly after Joe left I also left to come over to Shaper to lead up the electrical engineering efforts here and to basically be responsible for taking a prototyped product that was not manufacturable at all, and making it into a manufacturable piece of hardware that we can mass produce and sell to people at a reasonable price. It would perform well and be reliable and all the things that you want a power tool to do right?
So let me now explain what Shaper is. So Schaffer is a handheld robotics company. We like to call ourselves a human in the loop robotics company and our first product shape or Origin just started shipping to customers about three or four months ago.
Uh-huh and the Shaper Origin is a handheld CNC. For listeners who aren't familiar with CNC or computer numerical control; CNC machines are what you can imagine a company like IKEA might use to mass-produce furniture. They can range anywhere from desktop size for several thousand dollars, to the size of a warehouse basically, you know, going up to millions of dollars. The way a CNC machine works is, you say, I want to cut X design, you throw in some sheet material.
Normally you pre-program all the paths that a cutting bit is going to take and it moves around and cuts out this material, so CNC machining is basically the opposite of 3D printing; 3d printing as an end of manufacturing technology. CNC machining is a subtractive technology - you start with the material, you cut stuff away until you have a solid item that you want in the right shape. So what shape or Origin is; it takes that concept and basically shrinks it down to a portable handheld power tool. So we're trying to bridge the gap between capabilities what you can do with hand tools and the capabilities of what you can do with, you know, multi-tens of thousands of dollar CNC machines, kind of in the middle, that gives a lot of versatile capability. So the way Origin works is, it's computer vision based. We use computer vision and real-time motor control to basically scan your workpiece.
We have this stuff called Shaper tape, you put down on whatever it is you're going to cut. It can be a piece of sheet material, like you can cut on a CNC machine, or it can be an already fully-built table and you want to make a particular feature, and if you want to put a mother-of-pearl inlay in it or something.
Okay you scan and you put your clamp down or whatever that cut is, you scan it in and the tool now knows, based on tracking vision off of those partners, exactly where it is in 3D space. You load in a design file - the tool is connected to Wi-Fi or this USB port, so you can make your design totally CAD agnostic. You can make it any 2D or 3D CAD program you want.
Yeah so like AutoCAD, like what kind of tools?
Anything in the 3D realm. The most common tool that our users use is fusion 360 okay, but in the 2D world the most common is Inkscape or Adobe Illustrator. Really anything that can generate an SVG or vector file format and so you can do some color coding of that design in advance to instruct it to how you wanna put it, or you can do it all on the tool but basically the gist is, you make your design advanced, get it to the tool, it flies magically over your Wi-Fi.
You put the design in your account online, it just appears on the triple click of the design. You move the tool around your workpiece like a cursor, click to lock the design as its workpiece and now that design is like virtually locked to wherever you chose on your workpiece. At this point it's like a video game, the screen is a capacitive five inch, capacitive multi-touch screen. You move the tool around the workpiece - the tool is basically auto correct for your hands. So there's a corrective region on the tool, there's motors that compensate for the movements in real time so do you do the rough cuts and the machine does the precision.
Oh, see when I was watching it you know you could see the image on the screen like you were following a pattern, say you were cutting out a rectangle and I was trying to get my head around, yeah wonder if you slipped? To me what the human was the problem in that equation so after you do the rough cut how do you literally handle it?
Okay it all happens in real-time, automatically.
Oh, okay, I see.
Let's say you want to cut a perfect square you cut mostly a perfect square but you're human so you're moving back and forth you you're making micro adjustments as you go your shaking back and forth whatever, it doesn't matter any movement that you do that's contrary to the design you've placed on the tool virtually is compensated for in real-time. So if you want to cut a perfectly straight line you're moving the zigzag you get a perfectly straight line because the tool is moving opposite to your zigzag direction in real time that's internal, so what you end up with is the cut that looks like it came off of a $10,000 or $100,000 CNC machine that might take up an entire room and so it opens up a tremendous amount of possibility. With CNC machines you work with sheet goods. With our tool you can work on any existing work surface you have, you can inlay designs into your existing wooden toys you can go to your kitchen countertop installation and cut out the opening for your sink without any jigs or fixtures. You're really thinking about it at all in advance and most of these things you can even do without ever involving a computer in the process because we have on tool design capabilities as well so you can design things directly on the tool, lock them to your workpiece and then automatically cut.
Yeah.
So what kind of materials, like what stuff - obviously wood, say plastics what kind of other types of materials can it work on?
Yes so at the heart of our engine is a 720 watt trim router motor and so you can really cut anything that you would cut with that. We do hardwood, softwood, plastics composites, soft metals like aluminum and brass. We've done our fair share jewellery - dog tags, things like that with our tool. We’ve done composite Corian countertop material, soapstone; really anything that you can imagine cutting with a traditional router you can you can cut with our tool. We're not changing the physics of cutting we're just making it a lot easier and guaranteeing you get a high quality cut with a handheld tool instantly regardless of experience level.
Which is so great like I've always thought it would be so great to work with wood but I know the learning curve I'd go through would totally discourage me, but when I saw that - there is, I think it was a recent video that came out basically creating an outdoor chess-board on what looked like a tree stump right? The kind you'd find in the park, I think that's what it was anyways. and cutting out each square and then laying it with the darker wood and it was stunning. And I was watching the screen and just this interactive thing I was like: I think I could do that with a little training.
Yeah, you totally could, so no computer was ever involved in doing it, they literally got a slab of wood, said they want to make a chessboard with the tool because it knows exactly where it is in the scale of everything. You can lock and grid to whatever you're gonna do, so lots of grid to it you know. Say I want a one by one inch square grid, andI want to cut out every other square to put an inlay in for my chessboard and and you're done.
And the the learning curve on it and you know - you don't have to take my word for it. If you go to the Shaper Tools Instagram or anything like that or, if you search Shaper-made on Instagram there’s just a lot of people getting them and unboxing them and you can watch this pretty funny progression. Someone just posted a video on Instagram yesterday and they're like, oh my god I got Shaper Origin and in 30 seconds they'd be like, oh my god I'm opening the box. 30 seconds later, like I'm doing my first cut with shape or again 30 seconds later, I already figured it out, this thing is so easy like I cant’ believe how easy it was for me to figure out how to do this! And that's that's part of what we're trying to accomplish.
Well I love that, I can't wait to see I'm sure you guys are excited to see too because I'm sure your imaginations have run wild with what you can do with it but once you start shipping it and getting it in people's hands what they're going to come up with is gonna be phenomenal.
Right, oh yeah absolutely, and we've been beta testing various versions of the prototype of this product for going on two years now - more than two years I think, so we have a lot of data about how people use and abuse this tool and we've tried to design all of those workflows and eventualities into it. But people continue to surprise us every day and it's great they love it, it's so fun.
Well you know, like I was just saying, for me personally it’s, oh that sounds fun but all that work ugh, the barrier would be the learning curve. The other barrier is good lumber tools are a bit expensive so you don't want to screw them up right? So I would think that to sort of have this sort of foolproof once you've learned it to feel really confident going to buy a piece of really beautiful wood you know. I think that would take away that sort of barrier to entry for people to try that, pretty confident.
Yeah, I mean to give you context I think one of my co-workers is is doing a test today where he's over at some guy's house doing straight-up inlays into like a wooden floor.
Right, so that's brave.
Yeah, there’s just room for mistakes there yeah, and and this is not the first time we’ve done that. In fact there's a there's a bunch of patches on the floor in our office here. We're in a pretty old building in the Mission District and in San Francisco and the the wooden floors here have seen better days. We ripped out the carpet when we moved into this office and some wooden floors were not in good shape. And you know we found all the halls we did live inlays for them and patched them up and that's great.
That's so cool, so you just said you just started shipping, how long ago?
So the first units started shipping out in October.
October okay, so what's the feedback you're getting from these early shipments?
I mean it's great people are getting them in using them and doing all kinds of amazing projects and they're posting them online and we have a forum on our website with a lot of people posting projects but also lots of people post on Instagram and Twitter and Facebook and I've been sharing what they're doing and it's been a very exciting, nerve-wracking and exciting, experience to see people getting this tool in their hands finally, that we've been working on really hard for several years the and the anticipation. We started doing pre-orders for the tool at the end of 2016 so a lot of these people have been waiting for well over a year to receive this this product that they put their faith in. We told them we're gonna make this, here's the pedigree of a team we know what we're doing, we know how to make stuff but still, as with any pre-order, we didn't use Kickstarter or anything similar to that you know. It's an amount of risk and you don’t want people not receiving it. You want them getting it and saying, WOW the build quality is excellent and this thing works exactly the way you said it would, and it's intuitive. It's very heartening to see that.
That's so great, so what is next to your shipping Origin? I'm sure you have some things in your back pocket perhaps, you know future dreams for your next iterations or other types of tools? Don't tell your secrets I'm not asking your secrets - no IP spoiling.
We've got for the future - the key focus right now, is we're still catching up to pre-orders right, so we've been ramping up our manufacturing capability and just are now kind of getting up to full speed, you know. The maximum output that we can expect from our factory it's still gonna be a little while before we finished filling those pre-orders, especially since more and more orders come in every day and so we have to keep keep adding more and more to what we're going to be manufacturing since that's the key focus right now. Yeah it’s making sure that it goes smoothly and where we're generating a high quality product that meets a lot of very exacting quality standards. I mean we really are building a precisely calibrated and sophisticated, basically industrial robot that we are selling as a consumer electronic device. And so making sure that everyone that comes off the line is identical and works the same way and we know exactly how it's going to behave and it's gonna work with the accuracy and precision that we've promised. This is a big focus right now, yeah that's what we’re focused on and there will be more things in the future for us too.
Now one reason we became acquainted with you Jeremy, as we know with every startup you have to wear multiple hats and it sounds like you're wearing multiple hats but one of the hats you've been wearing is as an electrical engineer. Electrical engineers and PCB designers who will be the bulk of our listeners here. So can you give us a little insight to your electrical design and I know that you've been using Altium and I know you've used some other tools in your lifetime but I know you're using Altium now. So tell us a little bit about what's under the hood and what it took to to get Origin running from an electrical and electronics standpoint?
Absolutely, I mean I'll leave some of the exact details but yeah we use Altium for all the design of the rigid and flex PCBs inside the product of which there are many like I mentioned, since it is effectively an industrial robot. The electromechanical requirements of the tool and where the physical electronics are for different things is complicated. So, it's a large multi board system; there's the camera that’s used for doing the workpiece, there's the capacitive multi-touch display, there's the application processor and the microcontroller that's responsible for all the motor controls, there's the boards that are out controlling the correction motors and the z-axis motor that that moves the actual cutting bit up and down.
There's a sensor in the base that's that's used to do Z touch draw so that the bit knows where it is in space so there's a lot of boards in there. Boards and flexes, all designed with Altium. One of the things - and as you mentioned - that I've used many CAD packages in the past, basically any major one that you can think of, and one of the first things that I was tasked with when I came to join Shaper is there was no real electrical or formal electrical design before I was here. There were prototypes and one-off boards that were used to simulate and test certain aspects of the design, but the whole architecture has been new over the last two or three years since I've been here to make the product manufacturable.
So the first thing I was tasked with was I had to decide, okay, in the past that mostly been dictated to for one reason or another like here's the CAD package you have to use and I'll say something that was difficult for me at Google as I was working in Altium for some of our work, and then for reasons that I won't go into, it had to use a competitor product to Altium’s and I did not enjoy the experience. So, it was a pretty easy choice when I came here but one of the driving factors of that was we're a very lean team here, as you said I'm responsible for a lot more than just the electrical engineering and the PCB design and so the 3D capabilities of Altium have been super important. We have really tight tolerances inside of this product we have to meet a lot of requirements because it's a lot. And we want things put together perfectly to make sure that it's performing the way we expect it to.
So a lot of that ends up playing back down to the PCBs and understanding exactly how much space things are going to take up and exactly where every component is, and how big it is, and which things are touching off to thermal pads or which things are gonna have a certain amount of clearance.
There's AC power; where that comes in from the raw, we have to meet certain clearance requirements and make sure those distance are, not just in 2D but in 3D, also correct and acceptable to ship this product. So the 3D capabilities of Altium have been incredible. You saw actually, with the new release of Altium 18 I just started playing with the multi board assembly feature which is already been very useful for some of our rigid and flex assemblies that go together and seeing how those fit together has been super useful and a really important part of my job and makes it faster to go from an idea to something that fits. We can build into the mechanical CAD model of the tool and know that everything is going to assemble together the way that we expect it to and designed to do.
Well, looking at Shape or Origin it does have a really, for all the capability that it has you know, it really doesn't appear to be terribly larger than a typical hand router like you’re saying it has so much more capability so there's got to be a lot crammed inside and including that display in the sensors and all of this so it kind of reminds me actually, coming from the board industry, is like drones where you have to fold everything up and fit it mechanically - weight, power, that's the mantra you know. In military - weight and power - to keep things in that really tight but super functional footprint and be able to stand the thermal stresses of being in a small package and the vibration and all these other things so I'm sure was not an easy design?
Yeah we were a startup, we're a lean small team of engineers here doing this so we've built a lot of our own testing equipment and fixtures to stress test this machine so it's working in a dusty environment and we want to know. is this machine gonna be tests proof okay. So we used Shaper Origin to build a dust chamber for itself stuck an air compressor to it… there's videos of this online. Plastic talcum powder and sawdust for you know, running it for days straight with all the motors cycling. We're going to do that to analyze different configurations of our z-axis assembly and how the PCBs are sealed and things like that to protect them. We've done all that; same thing goes for our spindle motor and building systems to test the functionality and lifetime of that. All things that we've developed in-house to make sure that the design works the way we expect it to and is gonna stand the test of time and be a reliable tool that you can use in your shop for many years.
Well it sounds like wonderfully brutal work you've done in the last couple of years. Really rigorous engineering standpoint. Now are you manufacturing it but you know, short term and long term - I don't mean to say that in a loaded way - but are you manufacturing it now locally and in-house or are you contracting out? I mean how will you handle the manufacturing challenges over time?
Well Origin today, like basically any product that you buy, to say the whole product is quote-unquote ‘made anywhere’ is sort of deceptive because parts come from all over the world.
This is true.
In one country in the motor comes from Germany, extrusions and plastic parts come from another country, the final assembly currently happens in the United States. I won't go into more detail than that but yeah you know that's the final you'll see on most products now if you really dig into it, it's made everywhere!
They really are, it's a really good answer and it really is a global economy and that's never more true than electronics because we source our parts from all over. So yeah, that and when you're in the startup scrappy mode especially right? You have to be able to get it to market affordably and reliably and do all these things. Well thank you so much Jeremy I I have really enjoyed this conversation especially the part about the electronics and we love supporting startups here and and I hope soon we’ll come up and shoot a video at your plant and be able to show our audience some of the neat things you've been able to do with our tool, to make your tool and and we love that we support companies like Shaper and engineers and designers like you. It's what wakes us up in the morning so thank you so much for telling the story.
Yeah, my pleasure. You know, Shaper and Altium have a lot in common - we're both making tools help other people make things.
Exactly that's what we that's what we do we wake up in the morning and that story of Altium started from it's very beginnings from a couple of university students that were teaching and you know, they thought the young hungry startup minded population should have tools and at that time they weren't available. There were many computers and large expensive engineering stations and they weren't available, and so our two scrappy founders said, to heck with that we need tools. And so they started making them on a PC and haven't looked back since. So that spirit still kind of lives in our building and I think, that's what people kind of still relate to that to. So that spirit we do share that in common.
So, my last last question is - and I hate to ask this of you because you work so much I'm sure you don't have any spare time - but I have noticed because of the overlap of Arts and Technology a lot of people I know that our design engineers usually have really incredible hobbies like woodworking or painting or music or you know, some kind of really interesting hobby life and so I always like to ask at the end of this program. I call it design after-hours and so I want to ask you what you do after hours but I'm worried you don't have any hours after hours.
I do still try to try to make time to work on personal projects and I have the great fortune of working in a fully-featured wood shop so that is definitely some of what I do. A lot of things in my apartment are made in the wood shop here mostly using Shape Origin, so various pieces of furniture in my apartment and game boards, Chinese checkers set and organizers for my kitchen. Simple things like that - just fun projects and when I'm not doing that stuff, for me my hobbies are the same I'm very fortunate that I really like things I work on so my hobbies aren't the same things I work on but when I'm not working on the electronics for Shape Origin. I do other software and electronics projects, I document them on my website and on github and in other places. The thing that's been really interesting for me has been home automation and this has kind of been an ongoing project for me for the last couple years, building a natural language voice controlled home automation system. Something along the lines of how Amazon echo works. The first version that I built - just to get the record straight - was working long before Amazon Alexa came out. I will cede and say that the current products manufactured by Amazon and Google are way better than anything I've made. But still a fun learning process and it is a system I use in my house everyday. It's a natural language voice control system that I have hooked into my lights and my music and I had hooked into the shades of my old apartment but not anymore, and I have it pinned to my phone. My number one most used feature is… because it's still like kind of weird to talk to an imaginary computer thing to ask it to do stuff and so I still don't feel super great about that but I do do it because it's an interesting engineering problem too. It was interesting to learn how to write those natural language processing software and I've been doing a bunch of that. My most used feature is still just like at night when I'm ready to go to bed and I have my phone, I just like give it a shake and it turns off all my lights.
Oh!
So simple.
But I want one I haven't got, I have two Echos in my house and still I'm not using them for half the stuff that they could do but they are super fun. Well again thank you Jeremy it's been great to have you and so great to learn about Shaper. Give us your website real quick and then we'll share some links below with our audience.
Yeah if you want to learn more about Shaper go to https://shapertools.com/ or just Google shape Origin on Google and there's tons of YouTube videos, lots to see what the tool is capable of and if you want to know more about what I'm doing I’m at jeremyblum.com.
Very good. Jeremy thanks so much, you're really fun to watch and we'll keep keep our eyes on you and keep our eyes on Shaper and we look forward to talking to you soon.
Thank you this has been Judy Warner with the Ontrack Podcast. Thank you for joining us for our talk with Jeremy Blum. Please remember to subscribe and we'll see you next time and remember to always stay OnTrack.
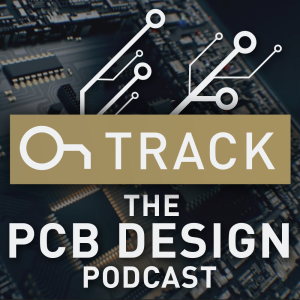
Monday Feb 19, 2018
Monday Feb 19, 2018
Charles Pfeil and Judy take a look back on the days of manual design, before exploring today’s very different eCAD competitive landscape and the tools that take designers to the next level. Join Altium’s Judy Warner and Charles Pfeil for a conversation on PCB design, autorouters and the future of software design tools.
Show Highlights:
- Introducing the iconic and award-winning Charles Pfeil
- Tape ups and touch ups with red pen precision
- Artistry not OCD, PCB design for form and function
- Charles on joining Altium and Activeroute
- “You know we’re paid by the hour, right?!”
- Where are we going to be in 10 years?
Links and Resources:
- Charles Pfeil and Happy Holden at AltiumLive
- A lifetime designing PCBs: Surprising acquisition brings stability
- A lifetime designing PCBs: Focus on functional specs
- A lifetime deisgning PCBs: early design adventures
- Job Shopper to Service Bureau
- Changing Roles
- Switching to eCAD
- From Design to Software
- Merging Design and Fabrication
- An Excellent History of CAD
- Improving Autorouting and Design Software
- See all of Charles Pfeil’s articles on EDN here
Hey everybody, Judy Warner here, Director of Community Engagement for Altium. Welcome to the OnTrack Podcast. If this is your first
time listening, we're glad to have you. If you're returning, we're happy to have you back.
The OnTrack podcast is produced every week, so please add the OnTrack podcast to your favorite RSS feeds or iTunes. You can also follow me on LinkedIn and Twitter @AltiumJudy, and be sure to follow Altium on LinkedIn, Twitter, and Facebook.
So let's get into the show. Well, I have a treat for you today. I have a guest, Charles Pfeil, who is, he won't say it but I will, he's iconic in the industry and we're gonna talk a little bit about the history of routing.
So, I want to tell you a little bit about Charles, forgive me for reading here for a moment.
Charles has been in the PCB industry for over 50 years as a designer and owner of a service bureau and has worked in marketing and engineering management at Racal Redac, ASI, Cadence, PADS, VeriBest, and Mentor Graphics, so pretty much everybody, and now Altium. He was inducted into the PCB Design Hall of Fame through UP Media in 2013 for his contribution to PCB design software.
Charles has been working at Altium since 2015 as a Senior Product Manager. So, welcome Charles, we always have a blast when we talk together, so thanks for doing this adventurous podcast with me.
You're welcome, glad to be here.
So, you are on the other side of the country from me right now.
I'm here in La Jolla as you know and I get to see you sometimes once a month, and you and I have had some interesting conversations here in the office, kind of a shared belief that we're sort of losing some of the history, right? Of our industry, particularly design, sort of where we've come from and where we're going, and I really value people like you, Happy Holden, Lee Ritchie, these people in the industry really that carry this whole history inside of them, so I'm always happy to have a chance to sort of glean some of that from you and you've told me some great stories, so thank you again for doing this.
So, how I met Charles was when I was a journalist from iConnect 007 and I interviewed him to learn about ActiveRoute, which was a new product for Altium at the time, and just sort of casually at the end of the conversation I mentioned to Charles "So, what's your history?" not knowing who Charles was and then, out he comes with the history of PCB design.
So yeah. I felt like a knucklehead, but it ended up being a good article, so you were a good sport.
So let's start talking about where at least you and I remember things which is tape-up. So, tell us about your earliest memories of doing tape-ups and what that was like and sort of what some of the problems were.
Okay, well my first job, I worked inspecting Rubyliths, and at that time the way that people routed boards was to essentially cut away the things that they didn't want, so what was left was the routing.
So there's a process in which they used an exacto knife and my job was to look for scratches on the Rubylith and patch them up, and I would have to say from that to what we do today is a tremendous change, and it went through an evolution where for manual design that the methods changed, the materials changed, and also the complexity of the design changed, and the same thing has happened once we started working with computers to design, right?
The materials change in the sense of the board materials. The methods change in that there's constantly an evolution of how much the software is able to do to help the designer, but just a note on the manual design and where this term 'artwork' came from. That, the interconnect would be done by drawing it, right?
Usually with red and blue pencils and most of the designs are two layers, and you would try and interconnect them and, you know, erase a line if it doesn't work out, but generally, you know, the type of components back then were DIP high C's if you had any at all, and it was, it was fairly simple and you could draw with red and blue pencils what you wanted and then you would either use black tape or red and blue tape in order to create an artwork that would be used in fabrication in order to get the design made.
Well, there were many different styles when you get to the artwork side. Some people like to use the black tape and create curves and arcs on everything, and some would not care about concentric arts, others, like me, would be very OCD and want to make every single corner perfect and make it look like some kind of art. It's not really art, but it's just the implication is that the person who's doing it is really caring about how it looks.
Absolutely, which by the way, one question I want ask you I know the answer to but I think the listeners will appreciate, what were you touching up that Rubylith with? Just a red pen.
Yeah, a red pen. I would just, because I had a magnifying glass to find the scratches 'cause with an exacto knife they would be really small, you know nicks.
Right.
And, so I'd go through looking at it with a magnifying glass and then use a red pen to fill it in so that there's no place with the light to shine through, because the way they were doing it back then, if enough light shined through then there'd be a hole in the mask for etching the board. Yep. Which could, what would that-
Well, you'd have a- -well, it could have an open, well you'll have an open if the scratch went all the way across, right.
Yeah. Yeah, yeah. So anyways, continue on. I just-
Yeah. It's okay.
-it's just a funny thing, like, when I think of how much precision we have now, to think of us touching up artwork with red pens just cracks me up.
Yeah, yeah, and when using black tape I think it was common to start out with arcs and you'd do that by kind of using the knife to create a little cinch in the corner, but eventually arcs became the less productive method, let's put it that way, and so you would start making 45-degree corners by just cutting maybe three quarters of the tape and folding it over to create a corner, and so then the art was to make sure that everything was right on the grid, and when you did a 45 it'd be perfectly 45, and it got kind of excessive, but when computers came.
Yeah.
That's where it changed, and I do have an experience in that area when my service bureau switched to computer design as opposed to manual design.
So you were right in that transition then, you went on your service bureau right from Rubylith black tape right into computer-aided design.
Yeah, from tape-ups in 1978, from tape-ups to computer design, and that was a Racal-Redec system, and I lost all my customers because the only customers who wanted the computer design were people who already had it themselves. Most people who didn't have computer systems, they didn't trust it. We would give them plotted artwork and they couldn't edit it, so as a service bureau, I had to go out and find customers who not only used computers but Racal-Redec computers.
So was Racal-Redec's price point, was there a barrier to entry there, kind of for that kind of system for OEMs?
Sure. So, I bought two used systems, you know with a basic vector graphics monitor, PDP1134 with the software. I bought two used systems for, I think, my memory is not great on this, but I think it was around $125,000.
Holy cow, that's a lot.
It was a lot. For used.
It was an investment and it paid off over time. I did increase my price per IC by a factor of 10.
Wow.
-which helps, you know, because you gotta pay for the apartment, but that's what happened in the industry.
So, routing in a computer system was different because with the computer of course you're effectively laying down the edge as you route as opposed to going through a stage and sketching the, you know, red and blue pencils
Right.
-but, so interactive routing was really, click-click click-click at every corner, okay? And if you wanted to make a change then you would either delete those and reroute it or some more sophisticated systems allows you to move the track around, and it was either that or autorouting and at that time autorouting, well it hasn't changed much but autorouting was primarily just an X&Y; exercise and adding a lot of vias. In a sense it was similar to the way that I see routing. I see routing doesn't care about vias and they just, whenever you got to make a change in direction you just pop a via and go, and with printed circuit board autorouters that's what they would do. They didn't care about how many vias you added and really vias, the only problem with vias back then was the cost of drilling them.
Right. At that time there was, wasn't.
Yeah, it was nominal.
It, yeah, well the cost was still there, but in terms of vias affecting the high-speed behavior-
Right, uh-huh. -there weren't high-speed designs. There were companies of course who were doing that, but vias didn't become a cost for signaling performance.
Right. So, people still didn't like vias. They could see with their mind that, "Hey I could route that without vias" so they would rather just go ahead and route it without vias, and so even though autorouters, every company tried to come out with the ultimate autorouter, and it could never match what the designer was thinking or what the designer really wanted as a final result, and I'd say generally that's been the problem with autorouting.
Too many vias, not really ending up with a route path that the designer had in his mind, and also the most common thing I hear is that it would take more time to clean it up than it would to just route it manually. Now I remember back in my early fabrication days knowing designers that would autoroute a portion, say 60% of the board they would autoroute, and then they'd do all the rest by hand.
Was that because of what you're talking about or was that just the speed to design at the time?
That would be a method. There's so many different ways of approaching it, but a method would be to route the critical signals first manually, and then just give it to the autorouter to finish everything else, because that would save time.
Now, autorouters evolved. The early autorouters really didn't care about anything but is there an open channel and is there space for a via, right? Then it evolved over time where there is a recognition that, well what can we do to try and eliminate vias, and I say eliminate because they would route with vias and then they'd have a pass to remove vias if they can, right? So, but it really wasn't fundamentally in the algorithm of the router to try and route without vias. Now, a number of autorouters gave the designer control, like CCT with a DO file where you could, you could put costs on the router to try and minimize vias, but it was difficult.
You really had to be an expert and I went to a number of companies where they had one person who was the router specialist and the designers would place the board and then send it to the router specialist who would do the automatic routing and that person would know how to set it up and it would be pretty good, but when it came back there still had to be a quite a bit of editing.
Who was, who created the best sort of autorouter of that time, and what kind of time frame are we talking about now, as we're moving forward?
Yeah, I would say, well it depends on who you talk to, okay, because-
Everybody has their favorites, right?
-everybody has their favorite.
So I would say though, obviously the Cooper Chan Technology, CCT. Their autorouter was the favorite, especially among Mentor, Cadence, PADS. Those companies all had interfaces to it and relied upon to do their autorouting, but once CCT was bought by Cadence for a measly four hundred and thirty or four hundred and fifty million dollars- Whoa. -whoa. All the other companies, Mentor, Very Best, and also PADS felt "whoops we can't go down this road" because, as usually happens in a competitive environment, those who have a relationship with one of their competitors, it's possible that that relationship could diminish over time.
Right of course, and we have to remind listeners right now that at that time PADS was not part of Mentor. Correct.
Correct. Neither was Very Best.
Very Best, right, so it was a whole different environment. So Very Best, they had autorouting capability and it was different. It was, it had some different data structures and different algorithms and actually that was one of the primary reasons why Mentor bought Very Best, was for that autorouting capability. Oh, okay interesting. See, I love, I mean, people that are around our ages know this but so many now that are, I don't know maybe 40 and under don't. You know that how, this used to be a, there used to be more than three or four players in this space, right?
Sure, sure. And we kind of all, ate each other up until we have what we have today. I would say the 90's and early 2000's there were so many mergers and acquisitions.
Yeah. Unbelievable-Unbelievable. -and you know, I went from Intergraph to PADS to Very Best to Mentor, right? And then now I'm at Altium, and looking at the evolution and the tools over that time the autorouter was a key thing, but realistically designers still preferred to route it just by themselves and manually, right?
It's true. It's, it really has a lot to do with what the designer thinks about when they're placing the board.
They know that a certain bus needs to go in a certain direction on a certain layer, and to set up those kind of controls and cost adjustments for an autorouter is a lot of work and it requires a lot of knowledge about the core capabilities. So, I think routing in general after, yeah after CCT was bought started turning in a different direction where rather than just autorouting, let's see what we can do to give the designer the kind of control with interactive routing that they want, and increase their performance.
What can we do to increase the performance?
Right, and is, tell me again now is this around the time that you joined Mentor's team?
Yeah, I joined Mentor in 1998.
Okay, so late 90's.
Yeah, it was-
And you helped, and you helped architect that vision right?
Yeah, I was part of it. I mean-
Part of it right, it's a team.
-it's always a lot of people involved, and I was involved in it, and I always tried to put my designer perspective into it, right? And I think that's my contribution, is not only being able to work with the development people but to be able to communicate the knowledge and expectation of a designer so that the software that we develop is something that a designer would appreciate.
Right, you had a designer-
Not that.you had a designer brain so you knew, which by the way, as you, as you alluded to in the beginning, is an artistic brain, really. It's, there's a lot of creativity there and an appreciation for not only function but also aesthetics and to put things in really neat, tight patterns, or.
Well, yeah-
Yeah, you call it OCD but there's that.
-there is that.
You know, this is a topic that has come up quite a bit in the last 10 years and I like to say the following, that yeah there's that artistic side but ultimately I believe it's about efficiency. And in the context of CAD design, efficiency means that the routing is as direct as required, of course if you're doing some kind of, you know, tuning on it it's not going to be direct, you're adding lights to it, but you want it to be as direct as possible. You want to manage many more things than we had to manage, you know back in the 60's and 70's, right?
Right, absolutely.
Now you have to manage high-speed requirements, so you don't necessarily want to have everything tightly packed in parallel. I remember I was demonstrating some ActiveRoute capabilities to a high-speed product manager, probably a little over a year ago.
And there was a bug in the routing where it was, it was kind of messy, you know and the high-speed engineer says, "Oh that's great!" Right? Because it would totally eliminate cross-talk, you know? Exactly.
Yeah, so there has to be the balance and that fundamentally, that is the job of the designer.
How do you figure out the compromises, right, to achieve the right balance where you fulfill manufacturing, you fulfill high-speed requirements, and ultimately the design works, right?
And if it comes out looking where everything is nice and neat, that's a bonus because the next person who has to make edits on it - it'll be much easier, right? Right.
And yeah, frankly most of time or many times if it's not a high-speed net, those geometries don't matter so much, but if it doesn't take any extra time to make it nice and neat what's the problem with it?
Yeah, I get what you're saying, yeah.
There's sort of some elegance about the design, and like you said, many boards go into respins and you're not always doing that on your own work, so that totally makes sense.
So, you joined Altium what two years ago about, approximately?
Yeah, in May of 2016, excuse me, 2015. 2015, and so you've been working on ActiveRoute here, so what, you know, you've always throughout your whole career been pushing for trying to make things better, what are you trying to accomplish sort of on the work you're working on now, on the ActiveRoute?
Yeah, so it is one of a number of things that I have worked on, but I would say most of my time has been spent on ActiveRoute, and the intent of ActiveRoute is to give the designer another tool in their interactive tool set, okay? It's not for everything, but the intent is that when you have a group of signals that you want to route together, whether it be, you know, a bus or just individual nets that start and end in approximately the same place, I want to give the designer the ability to just, through a couple simple clicks, have those routes the way that he's thinking, okay? And what is the designer thinking? That's the key. But I would say that, you know, it, with most boards is pretty clear. You see the connections, that's where they start and end, and I'm looking for a tool that can allow that designer to just select those connections and have it route on the layers that he wants them on, ability to spread them out, ability to pack them together. These little techniques are there as options so that ultimately it looks like he would do manually. It's not a replacement for interactive routing, it's instead an accelerator.
Oh, okay. By the way, along the lines of accelerator, I was talking to somebody, I have to share this story with you, I was talking to a designer and he was telling me that he was sitting in your session at AltiumLive where I think you were showing ActiveRoute, and he said someone in the room said, "You know we're paid by the hour, right?" because it was making it more efficient, so I think that's a compliment to you Charles, to the work you're doing.
There is that trade-off, but that's been there forever, that designers fear being replaced by the computer, right?
Right, so that's gonna be my next question, just, so get ready about, to talk to me about AI and designers being replaced.
Okay, well, we can go there now.
Okay, you ready?
Yeah, I'm ready.
So, I know there is this fear or I've heard there's fears of designers being replaced by AI or computers and all that. So, what say you, Charles Pfeil?
Well, I say that it's going to be a while, all right? If you can imagine all the energy and all the time and talent that has been focused on auto routing over the years since, you know you have companies like ASI in the 60's, late 60's had automatic routing for IBM, okay on mainframes-
Oh I didn't know that.
- and, you know, programming it with punch cards. So, from there until now the ability to get autorouting to succeed has failed all right?
And this is just-
Or has it gotten us there since the 1960's, right?
We're still not, you know. It's not there, and generally designers have rejected it and it's not because they're afraid they're going to lose their job.
And, besides that, like I say usually, you don't sell these tools directly to the designer, you sell it to their manager, and if they can get the job done faster they're all for it okay?
Right, right.
But the problem is that it hasn't been adequate, the autorouting capability. It's a tough, tough problem. Every design is different, right? It's different.
And- And it's very, and because of that it's such a complex brain task, really.
Right, and there are standard circuits, of course you know, standard interfaces and memory circuits that need to be routed the same way, but then the placement's different, the board size is bigger or smaller or a different aspect ratio or it's flex or, you know, could be a lot of different variables.
There's many, many more variables right now, too. So, to fully automate that is going to take a completely different perspective for design I believe, and it's going to take a huge investment, and the interesting thing is okay in ten years, let’s suppose somebody started on-
You know, are you reading my mind? My next question was gonna be where are we gonna be in ten years Charles? So-
Yeah, exactly. Let's suppose somebody started a project to use AI and that's in the, in the context of doing machine learning and analyzing databases and building decision trees, and even if you got that working over five of those ten years, a lot of the things will change. They'll evolve and this is one reason why software vendors can't keep up with the technology.
There's always something new, always something new and on our list of enhancements to work on, it's always the latest technology, right?
And there's only so much we can do so we have to pick and choose which technology we're gonna focus on with each release.
Well, and, I was just talking to Ben Jordan here about this.
Well, until I came here, since I came from the board and assembly side, I had no real appreciation for the time and discipline it takes for development and for coding that software.
It takes a lot of time and a lot of discipline to put in all these new features and we're so, sort of instant gratification, we're just like "oh, well, put it in your next release." Not so easy.
Yeah, it's just a fact of life, and our customers, they want these things and we want to give them to them, but it has to be an evolution.
So if a company decides okay we're going to use AI to automate the design process, sure they could analyze all the different types of designs and understand them and how to use them, but then when they start with a new design, how could an AI decide on its own what the board size should be? What the stack up should be? Whether or not to use micro vias? What are the critical signals? I guess it would have to be able to read a data sheet, that is hard enough for humans to read.
That aren't always accurate, may I add.
Yeah, that's true.
I mean, most of the time they are, but. I'm not saying it's not possible, it certainly is possible. But, it's going to be a long time.
Yeah.
And maybe, who knows, maybe MCM's will come back and we won't have printed circuit boards. There's always that possibility. Yeah, yeah.
We just don't know, and the, even, you know, printing circuit boards - where is that technology going to be in 10 years?
Exactly, yeah. 3D printing and there's, gosh, so much that they're grappling with, so who knows?
Yeah, and the core problem is that a company is not going to design a product, let me rephrase that, a innovative company is not going to design a product that uses all these standards and circuit technology of the past. They have to have something new and different.
Right. This is why Intel stays in business, and all the other chip manufacturers, because you know they need higher performance, they need more capabilities, and so it's a complete redesign except for like I say standard interface is a memory, that's not a redesign, until the next standard comes out, but those tend to last a couple years and then, you know, you look at memory DDR 2, 3 & 4 they just change over the years.
And the interesting thing about, I wanted to comment here, about memory in terms of the PCB designer, the DDR2 circuit was the most difficult to route because of the T branching. Then the DDR3 came with the fly-by signal technology, that was much easier for the designer to work with as long as you have some kind of electrical signals, and DDR4 is really just a minor evolution, significant in terms of performance over the DDR3, so who knows where that's going next. Will the next phase be like the change between DDR2 and 3? I don't know. They have the specs for DDR5 and I'm just unfamiliar with them. But, so technology will continue to change.
Maybe AI will be able to support a segment at a time, and I know that there's people in the industry who are talking about this and wanting to do something with it, but I'm unaware of a officially funded project to do it at this time.
I'm with you there, and I would think you would hear about it from your connections, I don't know. Maybe, we don't know. And would a company you know like Cadence or Altium or Mentor fund a project that they know is going 2 to 3 years and maybe, maybe not work?
It's a risk. A potential risk, so. Yeah, so I would say to all the designers who are concerned about losing their job, don't worry.
But what will be extremely important is that they make sure that they continue to be educated and understand the latest technology and what requirements those bring to the design process. Then you have your value. Yep.
And you won't lose your job.
And I would say to that, that almost through the OnTrack newsletter and now podcast I hear that message over and over and over again from leaders saying, "the key to my success was I continued to learn and evolve" and so it's been great to talk with you Charles I always learn so much from you.
I wanted to ask you one last question. I have this part of the podcast I like to call "Designer After Hours".
I've just noticed a lot of designers have a creative bent and usually have some interesting hobby, so what are maybe one or two of your favorite hobbies?
Well, I could list three, all right?
Okay.
One is playing golf. I love to play golf. Second would be, photography, taking pictures, mostly landscape pictures.You can see behind me a couple landscapes, but I like to say that I prefer landscapes because they don't move very much. I've tried to do a few weddings and it was a total disaster, so I'm just not that, but and then third I do write a lot and I've, you know, written poetry and I really enjoyed doing that, so those are the three things.
Speaking of writing, I wanted to let our listeners know that Charles has written, which I'm delighted about my passion for history being preserved, how many parts are we now up to, ten? How many are we gonna finish at?
Well, actually 8 of them have been published in EDN magazine.
EDN Magazine, right, so there's a whole series of Charles' experience over all these years and goes into depth, so if you want to learn more please go to EDN.com and probably just search by Charles Pfeil and you'll find that. How many are you gonna, I know eight have been published, so how many- It'll be, eight have been published, I think it'll be twelve or thirteen in the end.
Twelve total, okay. Okay, well thanks again Charles, we've gotta run, but I could, I'm never tired of talking to you. You're a dear and thank you so much for your contribution to the industry, and it's always great to talk to you.
Well, that's all we have for today. Please remember to subscribe to the OnTrack podcast and follow us on social media, and remember to always stay OnTrack.
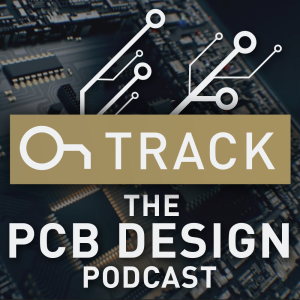
Monday Feb 19, 2018
Multi-board Design, a discussion with Ben Jordan and Judy Warner
Monday Feb 19, 2018
Monday Feb 19, 2018
Join Altium’s Judy Warner and Ben Jordan for a conversation on Multiboard PCB design.
Show Highlights:
- Many different product areas are being impacted by developments in Electronics, opening new frontiers - beauty products, wearables
- Electronics are replacing things that traditionally were not electronics
- Electronics product development are increasingly driven by engineers, but other makers are inspiring growth in the market - i.e. sofas, smart homes
- Design and product driven electronics, PCB designers are being pushed to partion boards into multiboard systems
- Everybody faces this multiboard challenge
- Immediate visual feedback in 3D design / 3D modeling definitely helps
- Major recurring challenge in industry: aligning connectors and aligning components that have some kind of outward expression on the actual product; MCAD and PCB assembly alignment. Multiboard design editor allows you to do this.
- Altium trivia and the origin of making tools for makers
- Ben's brother and his first soldering tool
Links and Resources:
Hey everybody, Judy Warner here. Welcome to the OnTrack podcast.
I'm the Director of Community Engagement here at Altium and this is our very first podcast.
You're very brave to listen and we're happy to have you. If you're new to OnTrack altogether be sure to sign up for our OnTrack newsletter which is online at resources.altium.com, or watch our OnTrack instructional video series which you can find on YouTube, and our goal with OnTrack is our tagline is to inspire, educate, and connect, and by bringing you together, the PCB design community, we hope to do that.
So, please add this podcast to your favorite RSS feed or on iTunes and you can also follow me personally, please oh please, on LinkedIn or at Twitter at Altium, at Altium Judy and follow Altium on LinkedIn, Twitter, and Facebook. Now, let's get into the fun stuff. So, today I thought we would talk about a subject that seems to be prevalent today in PCB design conversation, and that is about multi-board design. Many designs are going, as things become more complex, as we all know the automotive market, and so many others, because of size, weight, and power, they're being smaller, we're having to do rigid flex design, we're folding things upon themselves, we're fiting things into very tight spaces so you may have just been laying out single board designs not long ago and then you find yourself entering this sort of complex world that comes with it, comes with it a lot of, you know, new and challenging new aspects of things you need to think about in the overall design. So, a few of those things that I've learned about from my guest Ben Jordan is partitioning, connection management, and signal and power integrity. So I brought in Ben Jordan, who is our resident multi-board expert, and my friend and colleague, and partner in crime.
Thanks for having me.
So Ben, talk about what you see sort of currently going on in the EDA market as a whole, what's going on at Altium, and what kind of challenges specifically you see designers facing and sort of how they overcome them.
Yeah, well, if you look at the PCB design and electronics board level electronics design sort of industry over history over the last, I don't know, even four decades, the march has always been in it. I can't see it changing any time really soon, to make things smaller, cheaper, more reliable,
better for production runs, and more compact, and that's really taken an uptick. It's, to me, if I could graph complexity versus board area, I'm sure it would look something like a hockey stick.
You know, up-
Mmhm.
-up and to the right, and that really has always been that way, it's just that with exponential things like this, we see it, the further to the right you go the more acute it becomes, the issue of trying to fit more in less space, and this is partly brought on by higher levels of integration in the
semiconductor side, sometimes it's alleviated by that as our guest at AltiumLive recently in Munich, Lee Richie, aptly pointed out that-
Mmhm.
PCB designs can in some cases get simpler and simpler because more integration on the actual microprocessor is happening,but at the same time we're dealing with greater densities, greater pin out densities, but something that we have noticed in our industry is, is that there are many companies that were not electronics companies or that on the outside their products may not be considered primarily an electronic device, but- I just saw this in a magazine, like a whole article about electronics and beauty products, like, what?
Right, exactly.
Or like, a device you can put on your thumbnail so you know if you're gonna get sunburned, and it's an electronic device, t's, it's everywhere. Like you said, it's very prevalent.
Yeah, like, wearables is actually a classic sort of prescient example of that, where we, we no longer have mechanical watches. A mechanical watch is considered a luxury item these days and is very expensive if it is a genuine mechanical watch.
Mmhm.
Just like having a horse has become a luxury item after the automobile replaced the entire horse industry, and we see the same thing happen in many different sort of product realms, and so wearables is a good example of that.
I wear a Fitbit, I love this thing, it's cool.
Me too, yours is cooler than mine now. A lot of my friends have Apple Watches as well and, so electronics is replacing things that traditionally weren't and these companies are primarily driven by product design and function, not by the engineering team having a good idea. So electronics companies in the past, and there's still many of them that do do this, see themselves as an electronics company and the product development is driven by engineering and inventors who are electrical engineers or equivalent, but then there's this whole growth in the market that happens through furniture makers, ar makers, you name it.
That's another weird thing I saw.
You name it, and they're becoming- -about the sofa, there's like a whole device
set being embedded into a sofa, I'm like what?
And smart homes, just think of all the control going on.
Yeah, yeah yeah.
So, so these, but a lot of these are design slash mechanically driven product manufacturers or designers and so the electronics has to fit within that and as a result PCB designers more and more are being forced to partition the design into a multi-board system. So how do you think we're doing as an EDA industry and addressing that and giving them tools that are, you know, easy to onboard and get up to speed quickly, right?
They can't spend six months learning how to do really excellent multi-board design, so- -Exactly, so everybody, that's just it, every, everybody faces this multi-board challenge, but in the past, we're not the first company, we're not the first, Altium is not the first EDA company to provide
a multi-board design solution, but we are the first in that range of the market where anybody can actually afford our, our tools. If they're a professional designer they can afford Altium Designer and it's pretty well known, and our mission has always been to include the technology people need for everyday kind of design, and advanced technology for design and not withhold that just because somebody is not an enterprise customer. I mean the enterprise has different needs around data management and workflow management, but from an actual design and computer-aided design perspective every PCB designer should have multi-board design capabilities because they all face the same problems, and so I think this is the first time
that in the mainstream we've seen anybody address this multi-board design issue with proper connectivity management and 3D modeling of the system to make sure everything's going to fit.
So typically, if you, if you're a PCB designer, and you want multi-board capabilities,
that's going to be, it's going to be a huge cost driver for the software at large, I'm not talking about Altium per-se but if you wanted to acquire that ability inside your EDA software it's expensive than, you're saying.
Yeah, up until now it's been very high-end packages that had this capability that we're, we're talking maybe ten times the licensing cost, but.
Wow.
But, I mean there's many different ways of doing it, and most people out there, even myself in my hobby context in my shed, I've done multi-board design systems, and so I realized, and Altium, you know we realized, that it's something everybody needs and we shouldn't withhold it and charge extra for it. It's, it's just, it is a mainstream problem and so the technology should be available to the mainstream. So, that the other way of doing it of course is how people are
doing it up until now if they don't have those tools. You have to create Excel spreadsheets or Google Sheets to maintain lists of pins on different connectors, which connector is where on the design. You have to create a hop, a high level or top level, I nearly said hop level. [laughter]
You have to, I know, it's crazy but you have to, you have to do this kind of stuff because if you think about the actual problems associated with it there's, there's, there's a couple of different things. If you're doing a simple stacking design, you can reuse a board shape, for example. The boards will always, not always but maybe they will be the same shape. Think of an Arduino or a Raspberry Pi that has, has shields or capes or whatever they plug into it and they stack up vertically through the connectors and that's, that's a nice elegant way to prototype things, but
to go to production it's a bit tricky, and if you're, if you're developing a multi-board system like that it's fairly straightforward, but most systems are not that straightforward, and the different PCBs within the overall product may be in different locations, different planes of orientation, and can interconnect with board to board connectors or cables and harnesses, and then you get into issues like, how do you, how do you manage the pin outs?
That's a big one.
Connection management is a big issue, with multi-board designs even if you're stacking one board on top of another and you have a header and a socket, a mating socket, most people don't even realize until this, the blue, magic blue smoke is coming out of the first prototype [laughter] that, well actually the female connectors pin out is numbered from looking top down on it, in terms of the library and the footprint in the library you start traditionally pin one is at the top left and you go anti-clockwise, but that means when that connector is on the bottom side of a board plugging into another board beneath it, it's mirrored.
Yeah.
And this very simple thing can wreak havoc on the design process and time-to-market so, so we needed to provide tools to prevent those kinds of problems.
And I'm not a designer. I am, come from the fab and EMS side, so I'm honestly asking these questions, I'm not, but doesn't the ability of our software to do 3D help with that to visually give
you a sense that it's flipping instead of just sort of imagining how it's gonna go together-
It certainly does.
-until it's physically in front of you?
Yeah, it's really important to have that immediate visual feedback in whatever tools you're using, and if what you do is design anything, you need immediate visual feedback to get things right, and having that 3D modeling helps you align things, but the other side of this, the other area which is probably aside from incorrect pin assignments, one of the other areas that we noted in the industry that people struggle the most with is aligning connectors and aligning components that have some kind of outward expression on the actual product.
So, in my, I think of audio gear all the time because I'm into that, right, but, so one example is if I were designing a new amplifier I'm going to have some potentiometers and other controls on the front panel and so I have an enclosure, I have a front panel that has markings, and it has holes, and that's designed in MCAD, but the PCB assembly has to align perfectly to that, and I may actually want to realign components to match external holes and cutouts in the enclosure, and the multi-board design editor actually allows you to do that, allows you to go into a mode where you can actually move individual components and there could be things like potentiometers, or that their main intent is connectors that have to interface with other mating connectors on other boards, and you can actually cause them to snap together so that on the other PCB design you've got absolute confidence that you can make that first prototype and the connector will be in the right place and other components won't interfere with it in 3D space.
Yeah, I've seen some of you designers here in our office doing these, you know, rotating and showing, oh if I fold this over then this component is gonna run into that part or whatever I'm being able to just shift things slightly and it move kind of globally, is it's really fun to watch.
It looks almost like a computer game to me, right?
Yeah.
But it's really great how you can move that and and see it mechanically, you know in that 3D space instead of, remember the old days of prototyping, going whoops, forgot about that, and it was completely built out and there's all these expensive parts and you would salvage what you can but some were just like going in the trash can, and
I actually have an interesting bit of Altium history trivia about that.
Alright let's hear trivia, cool.
because we had, we had that exact issue, we, some people who've been around our orbit
for a while will have, will remember that we used to do FPGA design stuff, and we actually had a hardware design team, and their role was to design development boards for developing FPGA designs in Altium Designer, and those boards were modular so we had the Nanoboard 2 is the one on thinking of, we had this huge motherboard, and on top of that you had a daughter card that plugged right in that had, that could have different FPGAs you could try from different FPGA manufacturers, and we had another three different modules you could plug into different locations on the board and each had different input output options, and so during the design process of this we ran into issues with 3D clearance. There were some actual problems, this is a multi-board system, and back then the only way our hardware team were able to model this was to print the board designs that they did have in outlines out in 2D and cut those out and glue them one-to-one on bits of cardboard, corrugated cardboard.
I would cut it all out of cardboard and glue with hot melt glue or hot snot we'd call it. [laughter]
They'd use hot snot to glue the connectors in the positions where they would be on the final boards and plug them all together like this multi-board mock-up using cardboard, and the actual bulky components would be on it.
That's funny.
And it was so time-consuming and, too tempting sometimes to leave out some parts that should have been on that model but just, due to time constraints were left off, and I remember-
Plus I'm thinking, and then the CEO walks by and thinks you're doing arts and crafts, I mean.
Well, I mean it was necessary, but we actually had some boards that couldn't be plugged in in their first revision and had to be revised with a different bill of materials because there was, there were some power supply inductors that stuck out too far and when the whole assembly was together they, they seriously would not fit.
So, it had, it's like, if only we'd had this then maybe we could have reduced the cost of the product, products, and so on. So there's a lot of, and as I was saying earlier I think it's inevitable that any professional designer will run into these sorts of problems at some point, the tools need to be provided for them.
Well, I had the rare and cool opportunity to speak to Dave Warren one time on a Skype call from Australia, one of our original founders, and I was just trying to get a sense of who the company was and he just reminded me of like, a swashbuckling pirate, like give 'em the tools, you know like, he just he, you can tell he was so passionate about, nobody should pay these, you know, crazy prices for functionality. Whoever wants 'em should have them, by God.
You know, in his Aussie accent like you and he cracked me up but I really, it really came through to me that he was about make sure that anyone who wants these tools can have them. That they're reachable and that, it's a fun story by the way.
That's cool well that has been an undercurrent of the whole history since the founding and, to hear that straight from the horse's mouth is not at all surprising to me.
I remember him sharing a similar story about when we acquired NeuroCAD in-
Oh he told me about that, yeah.
-the late 90's.
So NeuroCAD was the first neural net based, you know routing technology.
Yeah, he told me they were charging 118 grand for that software, and he said "we, so we bought it and we cut the" I'm doing like Scottish accent now, "we cut the bloody horns off it and gave it to the people."
Yeah, they priced it-
So, how much did you sell it for after that?
It was $395 I believe.
$395, after $118 grand.
And the company that developed it sold maybe three or four licenses to a few big companies.
We acquired the technology and start, immediately put the price at like, 395 or, you know, under
$400 and it sold in the first month, it was over a million dollars of sales because it just, people wanted it they just couldn't afford it.
Well, we are out of time, but one last thing I want to thank you by the way for sharing all that.
Every time I talk I learn something amazing from you, Ben. So, on the fun side, I've always noticed, I've worked with PCB designers over 25 years plus, and something I noticed they all had in common is they have really interesting lives. I like to call it designers after hours. So Ben Jordan, what do you do after hours?
Ooh, ooh that sounds risqué.
Yeah no no, this is a G-rated podcast.
I'm a very G-rated person after hours actually.
I've always been into technology but I'm also from, I'm the youngest of six and from a very musical family so all my brothers and sisters were into music and played instruments and actually the reason I'm into electronics is because of my oldest brother, Les, he was a great guitarist but he was also an electronics technician and used to build his own tube amps and all sorts of cool stuff, so he gave me my first lessons in electronics and my first lessons in guitar right around the time, he bought me my first soldering iron actually for my eighth birthday and taught me how to solder.
I burned myself on that thing many times and I loved every minute.
I'm like, this was learning but it was, I've never looked back and then, and then right around when I turned 12 he bought me myfirst electric guitar and I haven't looked back on that either. I mean, we just, we are influenced by the world around us but sometimes in our lives we have kind of heroes, and he's definitely one of my biggest heroes and showed me this, this is, this was what my life was always going to be about.
Electronics and guitar and, you know, and now I have a family too, so between, between family and work and, I squeeze hobby electronics and guitar in-between those, but it's very full and very fun.
That's great. Well it was great having you and I'm sure we'll have you again 'cause you are a wealth of information on lots of subjects.
So, let's just wrap up our first podcast here. Well thanks everyone for listening in on this conversation with myself and Ben Jordan.
Please remember to subscribe to this podcast and remember to always stay OnTrack!