Episodes
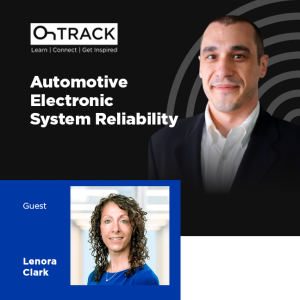
Wednesday Sep 14, 2022
Better Performance and Enhanced Reliability in the Automotive Electronics industry
Wednesday Sep 14, 2022
Wednesday Sep 14, 2022
Performance and reliability are big in the automotive industry, especially now that electronically powered and automated vehicles are starting to become more popular.
In this episode, we will learn so much about automotive electronics and the reliability of electronics systems that goes in the vehicle. Our guest Lenora Clark, the director of autonomous driving and safety technology at ESI automotive will share with us the importance of material choices for your PCB can affect the reliability and performance of your vehicle’s system design.
Show Highlights:
- Lenora is Chemist by education. She joined MacDermid, now MacDermid Alpha Electronic Solutions, as a bench top chemist, developing chemicals for PCB manufacturers
- Her focus was on surface finishing helping PCB fabricator improve their process from a chemical standpoint to enhance the performance and reliability of PCBs
- From working with surface finishing, she worked her way up and became the project manager, product line director for surface finishing, and later the Director of OEMs
- She is now a director at ESI automotive
- Chips don’t float, they are anchored to a PCB to work
- Lenora briefly described her role and emphasis on enhanced reliability to meet the end users' needs
- There is so much happening in the automotive space towards reinventing themselves and keeping up with the amount of innovation that's happening right now
- One of the challenges in the industry is extreme miniaturization
- Miniaturization is not just the board itself and the packaging but also feature density
- Other than the heat, electromagnetic shielding is also a concern with enclosure designs
- Lenora emphasizes that her current role is to make recommendations based on a material perspective, both for liability and for enhanced function
- ECUs (Electronic control unit) manages data transmission between different parts of the vehicle
- Lenora is Chemist by education. She joined MacDermid, now MacDermid Alpha Electronic Solutions, as a bench top chemist, developing chemicals for PCB manufacturers
- I think the future of the vehicle architecture is not completely defined yet. I do think it will be less complex than what we see today - Lenora Clark
- Collaborators like Mobileeye by Intel are working with makers to bring an entire system where there are different, sensors and a central computing unit to help make the decision – autonomous driving
Links and Resources:
Connect with Lenora Clark on LinkedIn
Visit ESI Auto website
Related Podcast Episode:
How to Select the Best Surface Finish for your PCB
Electronics Manufacturability and Reliability
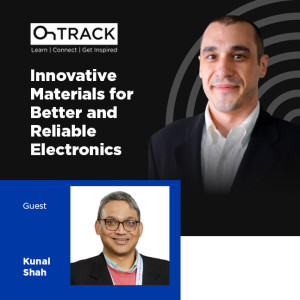
Wednesday Aug 31, 2022
How to Select the Best Surface Finish for Your PCB
Wednesday Aug 31, 2022
Wednesday Aug 31, 2022
You would not want to miss this informative, knowledge-packed conversation with Dr. Kunal Shah. Dr, Kunal generously gives us all a crash course on surface finishes and understanding different types of materials that could affect signal integrity, reliability and electronic shelf life. He will also tackle in detail the pros and cons of various types of nickel-free finishes.
Watch this podcast episode now or listen on the go. Make sure to check the notes and additional resources below.
Show Highlights:
- PCB Designers must be knowledgeable of various manufacturing processes and materials
- One of the things that makes liloTree unique is its innovation in materials development and ensuring better and robust reliability of the electronic assembly
- liloTree offers eco-friendly solutions (organic surface finishes) that enhance reliability and offer better performance in terms of signal integrity
- Dr. Kunal shares his background and how he founded liloTree
- Manufacturers are trying to find alternatives for ENIG (Electroless nickel immersion gold) due to nickel causing signal integrity loss in the high-frequency application
- There are several nickel-free surface finish, but designers must understand selection criteria – pros and cons of each types of materials
- immersion tin does have higher insertion loss
- OSP (organic solderability preservatives) is an organic-based surface finish. It provides good signal integrity, but has low shelf life issues
- Hard Gold has good signal integrity but very costly
- Electro-less palladium, immersion gold or autocatalytic gold it includes cumbersome process and need to babysit it
- A PCB must have both good signal integrity, great performance, and extended shelf life
- Designers must realize the impact of the supply chain issues on the PCB manufacturing life cycle
- Shelf life is critical. Boards are getting manufactured in one part of the world and it may take a few months before they get assembled in another side of the world
- LiloTree has developed the best nickel-free option, specifically designed from a signal integrity perspective, reliability perspective, and cost effectiveness perspective
- Another challenge of nickel based finishes is overplating and the skip plating in the PCB pads that could lead to micron scale level failures
- The liloTree nickel free solution includes a “barrier layer” which has multiple benefits including slower growth of intermetallics, delaying of natural embrittlement and eventually an extended shelf life
- How to overcome multiple reflow issues?
- Dr. Kunal explains the different ways they offer their solution to the market
- They offer their prototype lab where manufacturers and OEM can apply liloTree technology to evaluate and test it
- PCB manufacturer from OEM or assemblies feedback, the solution will be shipped directly to the manufacturer and set it up in their existing plating line
- Sending the boards to liloTree’s in-house plating line
Links and Resources:
Connect with Dr. Kunal Shah on LinkedIn
Visit liloTree website
Connect with Zach on LinkedIn
Full OnTrack Podcast Library
Altium Website
Get Your First Month of Altium Designer® for FREE
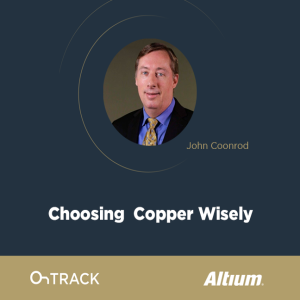
Tuesday Jul 20, 2021
8 Things you Need to Know about Copper
Tuesday Jul 20, 2021
Tuesday Jul 20, 2021
Copper roughness has an impact on high-speed digital designs. Choose your copper wisely!
In this episode, circuit materials expert John Coonrod of Rogers Corporation shares his extensive knowledge on copper roughness. Watch this episode or listen on the go; it will help a PCB designer make a sound decision about picking the most suitable copper to use on your next design.
Altium 365: Where the World Designs Electronics
Watch the video, click here.
Show Highlights:
- Introduction, John Coonrod’s role, expertise, and experience in the Rogers lab
- How the two basic types of copper are made (Rolled and ED) electric deposit (check out the slide)
- Copper overview
- Surface Roughness, the rougher the copper, the more the bond area
- Copper Treatments
- What is a reverse treat? The benefits, thermal properties, and adhesion
- IPC classifications of Low Profile (LP), Very Low Profile (VLP)
- Surface roughness for different types of copper and different types of surface roughness measurement units (check out the slides)
- Best practices when selecting a material
- Normal variations of copper for thickness, roughness, and etching differences
- Copper roughness impact on high-speed digital designs
- Copper roughness impact on RF concerns
- Future MMW 9 micron copper
Links and Resources:
Rogers Advanced Connectivity Solutions Website
Rogers (Free) Technology Support Hub
DesignCon 2021 August 17-19, San Jose, CA
PCB West 2021 October 5-8, Santa Clara, CA
Copper Foils for High-Frequency Circuit Materials
Different Copper Foils for Different Reasons
Choosing Copper Foils for High-Frequency PCBs
Materials for High Speed Interconnects: Physics & Chemistry of Copper Clad Laminates
How Copper Properties Impact PCB RF and High-Speed Digital Performance
Download your Altium Designer Free Trial
Altium 365: Where the World Designs Electronics
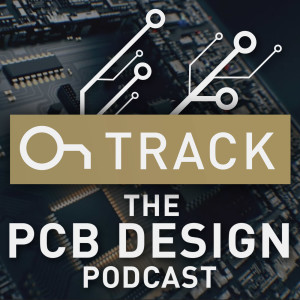
Tuesday Apr 02, 2019
Materials 101 with EIPC Chairman Alun Morgan
Tuesday Apr 02, 2019
Tuesday Apr 02, 2019
Meet Alun Morgan, Technology Ambassador for Ventec, a world leader in the production of high quality, high performance copper clad laminates and prepregs with a world-wide distribution network. Alun interacts with customers around the world promoting Ventec materials, and brings the latest market requirements to Ventec in order to develop new products.
Watch the Video here.
Show Highlights:
- Alun is a Material Scientist, with a B.Sc. Hons in Metallurgy from the University of Surrey. Once he became involved in PCB manufacturing he found it such a fascinating field that he has spent his entire career refining his knowledge.
- Everything Ventec does can also apply to smaller scale operations who are making PCBs.
- Alun was a Keynote Speaker at AltiumLive
- The FR-4 we use today has it roots around 60 years ago; there was an FR1, 2 and 3, as well as FR-5. According to the NEMA specification from the 1960s, FR is defined as Flame Retardant.
- FR-4 also means the fourth generation of materials in the NEMA classifications system. It defines the resin kind and the reinforcement type.
- FR-4 is an epoxy resin and the reinforcement is typically woven glass fibres for strength.
- The substrate itself is a composite of these two materials; the resin, the reinforcement and the conductor which is copper.
- Why the different composites? The main reason is its strength, it’s a very good insulator, and it’s available. It also bonds chemically to glass fibres very well.
- Lead-Free soldering created a major change about 20 years ago when lead was banned from electronic assemblies causing a range of performance issues.
- Higher temps expand materials dramatically, and because there is no reinforcement in the Z-axis, the expansion is considerable.
- When materials are heated beyond the TG, or Glass Transition temperature, thermal expansion is rapid and massive.
- The solution to this is adding inorganic fillers to modified, lead-free compatible materials to reduce the Z-axis expansion of which there are several types such as silica-based materials.
- Losses impact - some inorganic fillers have lower loss than the epoxy resin they’re replacing.
- How to choose materials? Talk to your manufacturers about the correct materials, ask which material they use the most and which of them work most successfully. Do beware of SI though, as this is a very fast-moving aspect currently.
- It is strongly advised to attend materials courses, and ask questions. Ventec is always ready to assist and answer questions. Go to a boardshop and see how these things are produced.
- Alun is also the EIPC Chairman and anyone involved with PCBs is welcome to attend their events. There are two conferences every year and the next will be in Austria, on June 14th and 15th. This will include a facility tour of ATNS, the biggest grossing PCB shop in Europe.
Links and Resources:
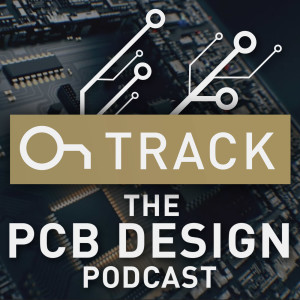
Tuesday Feb 05, 2019
Printed Electronics Applications and Innovations
Tuesday Feb 05, 2019
Tuesday Feb 05, 2019
The use of printed electronics is on the rise, and Chris Hunrath from Insulectro is here to talk about how to design for it. Learn about the different applications and design possibilities that are available to PCB designers. The proliferation of more advanced printed electronics materials from polyester film, polycarbonate, to transfer film for fabric and flexible circuitry have enabled interesting new applications for printed electronics. Listen in to learn the latest from Chris Hunrath, an expert in material supplies for circuit board design.
Watch the video, click here.
Show Highlights:
- Insulectro has seen a significant growth in sales of printed electronics products, this is an area of massive growth.
- Printed Electronics have traditionally been used in RFID along with metal f
- oils such as anti-theft devices and security access cards - items with conductive inks and membrane touch switches, for example: coffee makers, dishwashers, rear window defoggers, etc.
- Interesting new applications include: glucose test strips, wearables - sensors of all kinds, automotive, and self darkening windows.
- Self darkening windows are used in skyscrapers and aeroplanes, silver conductive ink, placing current on the window, giving the user control and saving energy.
- Printed Electronics is a high-growth area: business doubled every year in the past five years, doing very well in both substrates and inks.
- Predominant applications driving this uptick in usage: Capacitive Touch switching, in general it saves costs, lighter in weight and has no moving parts (i.e. car dashboards: a lot of work being done on it today) makes it more reliable.
- The molded structure: print the matte side and ink moves with plastic when molding, circuitry is totally encapsulated in the injection molding process.
- Ink technology: silver is used and is cheaper than gold and more conductive; silver flake or conductive particles make it possible to have the ink move with the plastic.
- Insulectro offers materials for Printed Electronics, some examples: polyester film - trade name Mylar and other brands, polycarbonate, transfer film for fabric and flexible circuitry in wearables.
- What’s the difference between conventional and printed electronics? Conductivity, and Resistance - know the sheet resistance and use a comparable copper thickness and width.
- Altium Designer 19 and Tactotek, who do in-mold structural electronics are working on relative design features in Altium.
- Printed Electronics whiteboard video
- There are inks that can sense chemistry and can be ion selective i.e. blood glucose, natural gas, carbon monoxide and so forth,
- Applications in wearables: Neural bypass, can pick up nerve impulses, movement sensors, chemistry sensors and more, and can withstand several washings.
- Higher silver loading inks can be used in many different applications.
- Chris shows an example of printed antenna that uses silver inks.
- Can be used in materials that you couldn’t use in a traditional PCB process.
- Conductive ink kits for children - you can draw conductive inks with a pen.
- Chris shows an example of substrate with high temperature ink, that has a 500-degree operating temperature.
- Events where you can see examples at the Insulectro booth: IPC Apex in San Diego, DesignCon in Santa Clara and Insulectro typically at IT TechEX.
- Conductive adhesive is more ideal for components, soldering to printed electronics is very delicate.
- Screen printing is the main way to print and is very scalable.
- Printed electronics is easier and cheaper to get started and environmentally more friendly.
- Stay posted for more developments in this exciting field!
Links and Resources:
Tactotek IMSE / Printed Electronics Podcast
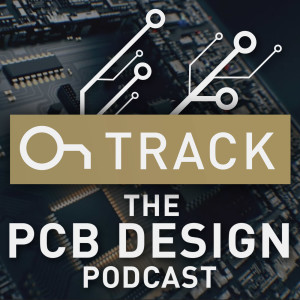
Tuesday Jan 29, 2019
Embedded Capacitance and Embedded Passives with John Andresakis
Tuesday Jan 29, 2019
Tuesday Jan 29, 2019
Listen in to Judy Warner and guest John Andresakis from DowDupont and learn about embedded resistance materials. There are several benefits that make this a beneficial technology. Did you know that you can take up to 90% of your decoupling caps off the surface of the board, while improving reliability and reducing inductance? Learn about several design considerations for using embedded capacitors and build on the knowledge of experts like Rick Hartley and Eric Bogatin who both addressed inductance in their AltiumLive San Diego keynotes.
Watch the video, click HERE.
Show Highlights:
- Senior Technical Marketing Leader - Interconnect Solutions at DowDupont; 30 years experience mostly on the materials side and now at DowDupont, soon to be the new Dupont.
- Embedded capacitance -cross connections with: Rick Hartley's keynote at Altiumlive (inductance) and Eric Bogatin's keynote as well
- This reduces inductance
- Film based materials now allow embedded capacitor layers to be 1 mil or below with excellent yields
- People were practicing some form of this 30+ years ago, but according to patents 25 years or so. There used to be material concerns, but with the advanced materials i.e. improvements in technology more is possible.
- What manufacturers are providing this service? Most of them!
- It's like a version of a rigid flex, without the flex part sticking out.
- This isn’t a very hard thing to implement, it wouldn’t be difficult for the manufacturer to get up to speed on this. The things involved are not difficult to learn.
- Learn more at IPC APEX - stop by DowDuPont and Insulectro - booth 624
Links and Resources:
IPC Standard: 2316 Design Guide for Embedded Passive Device Printed Boards
DuPont Interra HK04J Planar Capacitor Laminate
IPC Standard: 4821 for embedded passive devices
Rick Hartley on the Importance of PC Board Stack-up at AltiumLive
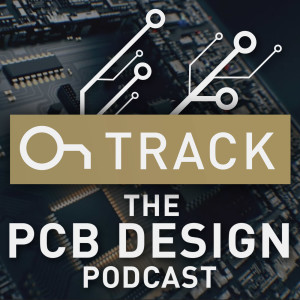
Tuesday Jul 17, 2018
Paste Interconnects and Paste Sintering with Chris Hunrath from Insulectro
Tuesday Jul 17, 2018
Tuesday Jul 17, 2018
Paste Don’t Plate! People are doing 90 layer multilayers with paste interconnects. Want to learn more? Find out about paste sintering from Chris Hunrath to learn more about its applications and benefits to PCB designers. What must designers consider and what are the advantages of Ormet’s products? Listen in for insights from the expert in this week’s episode.
Show Highlights:
- New material developments make paste interconnect technology more feasible
- Ormet’s paste sinters at one temperature forming a new alloy with higher melting point
- Paste interconnects allow for changing build sequence in which vias are formed i.e. drill, add paste, and then laminate - giving you interconnects inside a double-sided core with no visible vias
- Multilayer PCBs: Can split up a 32-layer board to two 16-layers (even as many as 4 x 18 layer multilayers - which is much easier to build
- Also reduces risk depending on design - electrically test each half and only use the good ones
- Ormet process/paste interconnect process eliminates traditional drawbacks i.e. excess copper on surface features
- Eliminate backdrilling with paste interconnect process without extra copper in the via
- Ormet paste eliminates electrolysis and plating process
- Signal integrity benefits
- Applications: RF, high-layer multi cap, avoid secondary remelt, downhole assembly etc
- Design considerations: Where to split up layers for best design benefit; Via at 1:1 or less aspect ratio - only in 1 B stage layer and correct size via for applying paste; Size of receptor pad for laser drill via must be correct to prevent paste from running - spread glass is good for B-stage; annular ring around the via to register laser drilling; with many paste interconnects - don't paste to the edge.
- Paste melts and forms alloy with inter layer copper creating a permanent metallurgical joint
- People are doing 90 layer multilayers with paste interconnects.
- HDPUG (HDP User Group) is creating HDI test vehicles with paste interconnects and HDPUG members will have access to reliability data for breaking up big PCBs
- Paste don’t plate!
- Future topics: Many ways to use conductive inks in electronics, copper foil, integrity issues and printed electronics. Material science behind electronics, new design tools, various versions of conductive inks
Links and Resources:
Chris Hunrath on Linkedin
Click to listen to Chris Hunrath’s other episodes about Spread Glass or Material Sets.
Hi everyone. This is Judy Warner with Altium's OnTrack Podcast. Welcome back, here we are again with your friend and mine, Chris Hunrath from Insulectro who's going to teach us about paste sintering today, which I don't know much about, but we're going to learn about it together. But before we get started, remember to hit all the typical Altium social media platforms Facebook, LinkedIn, and Twitter please follow me on LinkedIn and also remember we are recording on YouTube as well as Podbean and we can be found on all your favorite podcast apps.
Alright, so today we're going to talk about - I don't even know how to set this up entirely cause I'm just as much as a student. So Chris, welcome back! Thank you again, and I know this isn't a new technology - it's just not one that has crossed my path. So tell us about what paste sintering is and what the applications are, and benefits to our designers that are listening today?
Okay, interconnect technology, as you mentioned is not new, what's happened recently though is there's been some new material developments that make it more feasible for the circuit boards. Certainly in ceramic fire technology, metal - powdered metals have been used to make interconnects and traces and circuits on ceramic circuit boards, but those fire at 850-plus degrees Celsius, which would obviously destroy most PCB materials so there's some new technologies out now. There are different kinds of pastes that are used for interconnects. The one that we work with, and the one that we promote, is something from a company called Ormet, and their material is interesting because it sinters at one temperature and then it forms a new alloy with a higher melting point.
Okay I feel like we need to back up and explain what paste interconnect technology actually is. Like how it's performed and then we can go into the material science part just so I can keep up, Chris I want to be able to keep up.
So multi-layer PCBs - also not new - typically what you do is, you print and edge any number of layers, you drill and then you plate. Typically electroless copper, to make the non-conductive surfaces conductive, and then you build up the thickness with electrolytic copper.
Mmm-hm.
And some people call it a semi-edited process, because you are using the electroless first as a seed layer. There are some other technologies used to make that dielectric surface conductive, and then you build up with electrolytic copper and so that's how you link the layers of the z-axis.
So if you think of a classically - as a circuit board - as a web of foils printed and etched, all your XY connections, and then the drilled holes - whether they're laser drilled, blind vias, or drilled through holes, the plating links everything in the z-axis. Now one of the challenges when you do that, is you're consuming real estate at all the layers. So let's say you have a 12 layer multi-layer - relatively simple multi-layer by today's standards - but you need to connect layer 1 to layer 10 you've taken up the real estate in all the other layers - you can't route circuits in those places, because there's a via in the way, unless you wanted them to connect to that via and they're part of that net. So there's a term called any layer HDI - I don't know if you're familiar with that term? Basically it means you could put a via anywhere you want in any layer. Nowadays that's done typically by what we call build up technology. So you start with a core of some sort - again it could be double sided, it could be a multi-layer core, and then you sequentially build layers and you only go one layer deep with a laser drill sometimes two - depending on the design - but that's not true for any layer.
Anyway, you go one layer deep you plate, you print and etch, and you do it again and again and that allows you to put vias almost anywhere you want in any layer, the downside is, it's almost like building multiple circuit boards. So the cost really starts to increase. And of course you're putting the board through multiple lamination cycles and that has some undesirable material side effects depending on the material. Some materials can withstand three lamination cycles, some six, some ten, but it is hard on the materials to go through that lamination process, over and over again.
Right.
Especially electric phenolics, which are very common for lead-free assembly, because they're relatively economic and they're also - they also will survive lead pre-assembly, but they tend to get more brittle every time they see a thermal cycle though, so that causes some issues too. So what paste interconnects allow you to do, is change the sequence in which the vias are formed. So instead of laminating drilling and plating you can actually drill, add the paste, and then laminate, so it changes the build sequence and this is important both for the fabricator and the designer to understand what that means. So typically what you would do is, you would take a B stage layer of some sort; you can either drill it and paste, fill it with what we call a postage stamp process or you could pre-tack it, vacuum tack it at low temperature to a core of some sort, or substrate, laser drill through the B stage, apply the paste and then when you laminate the paste interconnects, the layers in the z-axis - you could literally take a piece of prepreg, laser drill it with a stencil or with a Mylar Stencil, I'll talk about how that works in a little bit - apply the paste, remove the Mylar laminate between two copper foils, and now you've got interconnects inside a double-sided cork.
That's cool.
So then if you print and etch that, now you've got a core with connections between the layers with no visible vias; they're all internal. Yeah there's some technology around the paste and again we can talk about that, in a little bit.
So how is it applied - is it squeegeed in?
Yeah.
Okay, just like with a silkscreen?
Well no screen - so what typically what you do is, you apply a 1 mm Mylar mask to the B stage and you tack it simultaneously. Then when you drill through the Mylar and the prepreg B stage to get down to your copper features, then you apply the paste, and the Mylar's your mask, and then you remove that just prior to lamination.
And that stays inside the hole? It doesn't just I don't know the consistency of it. My mind was - pictured it just wanting to drop out of that hole - but it must have some kind of stability?
Yeah it's a liquid and there is a tack right. There are a number of ways to do this, but the most common method is to laser drill, apply the paste, dry the paste... you would do it a second time to top it off and then when you remove the Mylar, the liquid paste stays on top of the paste that's already been applied. Then you dry it again, then you go to laminate.
Does it air dry or do you have to cure it what do you do?
You don't really cure it because it's metal powder - metal powder based - so there isn't really a polymer matrix. Unlike print electronic sinks - which is a again another story - you would just dry off any of the carrier solvent used for the application process. It is a liquid - well it's a paste, not a liquid - but but when you dry off the the solvent that's in it; which is less than 10 percent by weight, then it's just powdered metal and that's how it makes a connection. So think about this right, you've seen a lot of PCB designs - imagine a 32 layer board, which most shops can do, but it's not at the low end of technology. Imagine splitting it up to two 16 layer multi layers right?
A lot easier.
A lot easier to build and then you just paste them together at the end, and depending on the design, you can electrically test each half and only use the good ones. So your risk is light.
Oh, right.
There's a lot of advantages to this. Or what if you want to put together three 16 layer multi layers, or four, or 18 or four 18 layer multi layers - it's been done you know. Now a shop; instead of trying to build a 72 layer multilayer - if they're building 18 layer components - it's a lot more manageable.
Hmm, that totally makes sense. So you explained some of the benefits - it's a nightmare, and you've seen, we've all seen these cross-sections of these crazy stackups with all the sequential LAM and drilling cycles and all of that. And then - and also kind of an unintended consequence you can get, is you can - from a performance standpoint - if you do enough of that right can't you get excess copper on the surface features?
Yes - that's a very good point. So in other words, if you're going through many plating cycles depending on how you break that up and you're trying to meet a wrap requirement, that could definitely add up and make it - make fine line etching more difficult there's a lot of - there are some some drawbacks to traditional processing and then with with an Ormet style process, or a paste interconnect style process, you can eliminate some of those things even with an RF design.
Let's say you have very sensitive surface features and you don't want to play with that layer. You might want to put on the surface finish, the nickel gold, but you don't want to put any additional copper - you want just the original foil copper. You could do that with this paste because you could create that as, almost like a double sided board, and then bond it to the rest of the stack up at the very end, and you're done.
Interesting. So I think you mentioned too, there's some good signal integrity benefits, did we cover that I don't recall?
No, so one of the things that a lot of designs call for is something called back drill. So you're familiar with that, so you do the back drilling to get rid of the unwanted copper. So again, in my earlier example let's say you're connecting layer 1 and 10, and let's just say it's a 22 layer - 26 layer multi-layer. You're going to have a lot of extra copper metal in that via that you really don't need or want. So common technology is to back drill down to layer 10. Now of course drilling to that precise location or depth, to remove the copper up to layer 10, but not beyond. It can cause a reliability concern that's a bit of a challenge. So there's those issues.
What you can do with the paste technology is let's just separate that board at layer 10, and not put a via on that half that goes from layer 11 to whatever the other layer is and you're done. So you can eliminate back drilling and the parasitic effects of having that extra copper and the via so that's another application. So there's some signal integrity benefits, there are some RF applications, there are some high layer cap, multi-layer applications, but also many layer HDI applications; it really depends on how you design it and use the paste.
So if you're a designer what kind of design considerations do you need to make up front?
Okay, my recommendation would be is: think about the design, think where it would make sense to split up the layers and provide the most design benefit. Generally speaking, we like the via to have a one-to-one or less, aspect ratio. Now that might sound restrictive, but it's only in that one B stage layer.
So then that's an important consideration. So in other words, if I have 5 mm of B stage, I won't want my via to be 5 mm or larger where I'm going to apply the paste. It has to do more with the paste physics and how it fills the via and then of course the pad, the receptor pad that you're putting the laser drill via on, needs to be a sufficient size for where the paste doesn't have the opportunity to run on one side or the other of the pad.
So we do like an annular ring around the via, that's going to have a lot to do with how well you can register your laser drilling, usually that's pretty good. The other consideration is, the B stage you use, spread glasses - bringing up spread glass again. Spread glass is good, because it tends to keep the paste corralled, whereas if you have an open weave and that prepreg resin's melting and flowing and during the lamination cycle the paste could run to that area. So spread glass is better. Higher viscosity resins tend to be better. We like low flow prepregs. So those are some of the design considerations.
Another design consideration is - and I've seen this happen before - where if you have a ground area and you're making a lot of paste interconnects along a wide track. You don't want to put the paste interconnect to the edge of the track because what ends up happening is, during lamination, the resin wants to flow off the surface of the track down the sides to fill - hydraulic effect, and it's going to move the paste with it. I've seen vias actually move during lamination. So just some common-sense things. Keeping in mind that it's the B stage where your interconnect is. You want to make sure you put that in some good locations, and in that particular case all they had to do is, go back and shift the vias a little bit to one side and then everything was fine. So it's just those kinds of things. Certainly they could contact us, we can give them some design hints and I can give you some literature to go along with this video or podcast.
Yeah, yeah, very good. Ormet and the paste interconnect - paste sintering - has been around for a little while. What's been the sort of acceptance of it industry-wide? Is it being widely accepted, is it just on certain applications?
It's been around a long time. It was primarily used for quick-turn mic review work, and also large format boards where you're literally stitching very large boards together so you can - again the idea is you can make boards that are nearly finished and then electrically interconnect them. The nice thing about the Ormet paste is it doesn't melt at reflow assembly.
Hmm, so it changes chemically right, so once the sintering is done then it doesn't change, then it doesn't morph and heat?
What attracted us to this technology over some other paste interconnects - because there's other processes where you would apply a paste of some sort and then make a connection with pressure in the z-axis - but what interested us in the Ormet material is: the paste melts at one temperature and alloys - so the paste is basically copper particles with a tin alloy powder. When the tin alloy powder melts - and the melting starts at about 130° Celsius, it starts reacting with the copper and forms an alloy with the copper instead. What's interesting about the Ormet material is, it's alloying with the inner layer coppers as well, on the PCB layers. So we have a metallurgical joint, not just a pressure or contact connection.
So it's - and unlike, the tin lead or lead-free alloys and solder, the melt - the new melting point, when it forms an alloy with copper is one phase is 415°, the other is 630° Celsius. So it's not going to remelt that assembly. So it's a permanent connection, so really the paste applications from other technologies like flip chip and whatnot packages where you didn't want to have a secondary or - if you have a secondary reflow operation - you didn't want to have any more remelt. It has some applications there. Or a down hole assembly is another application where the board might be subjected to the temperatures near the solder melting point is another good application for this material.
So that's what interests us because you know when a board's in use, it heats up the z-axis expansion with other types of pastes interconnects, you have a resistance change every time the board is heated even from, let's say 40, 50, 60° Celsius in normal use, not even in any kind of environment - parts of the board would heat up from the components and you'd have a change in resistance, and that's what this is designed to circumvent because it forms that metallurgical bond with the copper inner layers.
Interesting.
So yeah it's a different technology than the paste you would use in printed electronics.
Okay well that's been fascinating. Again I feel like a newcomer to old technology but - and I've known about Ormet that I think got acquired by Merck now, but I've just never had someone sit down and explain it to me. So thank you for doing that.
90 layer multi layers people are getting - 90...
What!
Yes, 90 layer multi layers with paste interconnects yeah.
That's crazy, I didn't even know a 90 layer board existed I guess.
Yeah I've only really seen them into the 60s I guess personally, so.
Yeah you know, one common design was a 72 layer multi-layer, again made out of eighteen layer components, and one of the things with the chip tests the ATE companies, they built some high layer count multi layers and you need a lot of IOs, there's a trend to go to wafer level testing were you’re testing the entire wafer. You need lots of interconnects and that's one way to get there, is to use the Ormet paste to put in lots of layers. So we're seeing more interest in it lately, and I think that's one of the reasons why the technology hasn't taken off until now, is because there just wasn't the demand.
Right ahead of its time maybe a little bit...
Yeah.
Well, I know you've shared with me some cross-sections or I think you did, and so please be sure to share those with us and we'll put those up on our website and we can share your website and Ormet or Mark's website, so the designers can get more information. Is there any place else besides your two websites that you would recommend for more information?
You know I've mentioned HDPUG (High Density Packaging Users Group) in the past - they're actually contracting some PCB manufacturers to make some HDI test vehicles with paste interconnects. So there's going to be some data - anybody who's an HDPUG member will have some access to some really good reliability data and they're pretty complex boards so it'll really push the technology but for breaking up big thick and ugly PCBs, that's pretty well-established.
Yeah very cool. Okay well thank you. So tell us about that fish on the wall behind you?
[laughter]
So it was a gift from my sister, actually it's made from recycled materials so there's an old PCB cut up on there, and the old spark plug wire, and a few other odds and ends. Some artists put together actually I didn't buy it; my sister bought it on Catalina Island and somehow we went out there as a family trip and somehow she smuggled it off the island and gave it to me just before she headed back to Virginia. So it was kind of cool.
Oh that's fun a good throwback to your diver self.
Yeah so - just the last thing on Ormet, is 'paste don't plate'.
[laughter].
Is that their tagline or is that yours?
Actually that's their tagline. We were sharing it with the IPC shows, but another nice benefit to the Ormet - which I didn't mention earlier is - there's no electrolysis, no plating processes in these interconnect layers so it circumvents all that.
Which is like bizarre for me to think about but...
Yeah but if you're capacity constrained, no plating, that's another benefit.
Well thanks again this has been really good. If you have anything else juicy to share with the listeners just email it over before we get this one up.
Okay.
And thanks again for this one. Now I know we've talked about exploring down the road a little bit on copper foil, integrity issues, and also printed electronics. So I'm sure I'll hit you up again soon Chris.
Yeah definitely. I would like to talk about some of the material science behind printed electronics and I know you guys are working on some new design tools and print electronics; there are a lot of different ways to use that in electronics... I should back up, but there's a lot of different ways to use conductive inks in electronics there are so many different versions of the inks.
Which is another subject I know nothing about so it'll be good. I'll be a student with our listeners and, I know they're out there, I know what conductive inks are, but as far as all the applications, all the different materials available, that just seems like something that's in writing a lot, that people are really turning towards a solution.
Lots of new technologies are coming out in that space and it's going to be fun to watch it all.
Yeah yeah it will be.
Okay Chris, thanks for another good podcast and we'll see you soon.
Thanks for having me.
My pleasure. Again this has been Judy Warner with the OnTrack Podcast and Chris Hunrath from Insulectro, we'll see you next time - until then - always stay OnTrack.
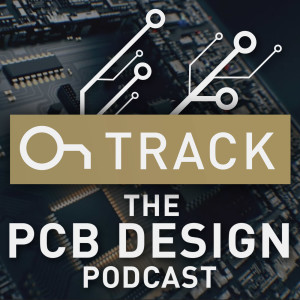
Tuesday Jul 10, 2018
Tuesday Jul 10, 2018
Learn about Embedded Passives Technology with Bruce Mahler from Ohmega Technologies. OhmegaPly® embedded resistor-conductor material is popular, but it’s not new. Ohmega has been making this product since 1972. So why is it getting so much attention lately? It’s reliable and has stood the test of time for five decades--but emerging technologies are making it more relevant than ever. Tune in to learn more about embedded passive and embedded components and find out if it may be the key to solving your current PCB Design challenges.
Show Highlights:
- OhmegaPly® is a true thin-film, Nickel-Phosphorous (NiP) alloy. In the manufacturing process, about 0.05 to 1.00 microns of the alloy is electro-deposited onto the rough, or “tooth side”, of electrodeposited copper foil.
- Embedded passive and embedded components: ER - Embedded resistors, EC - embedded capacitors
- People tend to think of this technology as something new. Ohmega has been making this product since 1972. It’s the oldest, new technology out there.
- Functionality - it can be used in so many different ways.
- Mica - old copper clad laminator, conceived the technology as a way to add functionality to a copper material. Developed in early 70s as a new product.
- First users of the technology - Cannon electronics in Japan saw the potential in the product for cameras.
- Other early user was - Control Data Corporation. From there alot of mainframes utilizing the technology.
- Ohmega ply - thin film resistive foil, plated process, nickel phosphorus, varied thickness and sheet resistivity, fractions of a micron-thick film. Very linear, as film deposit is thinner, resistivity goes up. Thin film technology.
- We make it in Culver City, CA for 40+ years.
- Work with Rogers/Arlon, Taconic, Isola, Nelco and other laminators
- If you use a tiny discreet resistive element, they can be hard to handle. Etching a 5 or 10 mil trace is no problem.
- Space restrictions, solution - print and etch a resistor
- Why would I want to use Ohmega ply? What are the cost, reliability, performance indicators? “There’s no other way I can design this unless I get rid of my resistors!”
- Most designers use Ohmega ply for densification. Helps when: hard time routing, too many passives, board is a little too thick
- Example: MEMs or Micro-Electro Mechanical System microphones for cell phones.
- Applications: military, space based applications - satellites,
- Uses include: Sensors, IOT, Wearables, Automotive, Memory, Heater, Biomedical
- Ohmega wants to talk technology with PCB designers. Leverage their expertise, they operate as a part of your design team and happy to be a resource for you. Technical people are available to help.
- Ohmega and Oak Mitsui - technology partners - Ohmega/FaradFlex is a combined resistor/capacitor core consisting of OhmegaPly RCM laminated to Oak-Mitsui’s FaradFlex capacitive laminate materials.
- Printed circuit board copper lead times are getting longer
- Self-reliant company
- Very close relationships with raw material suppliers
Links and Resources:
Ohmega Technical Library and Tools
Hey everybody it's Judy Warner again with Altium's OnTrack Podcast. Thanks for joining us again. We have yet another amazing guest on a fascinating topic that I hope you will enjoy and learn about today. But before we get started I wanted to invite you to please connect with me on LinkedIn. I like to share a lot of content relative to designers and engineers and I'd be happy to connect with you personally, and on Twitter I'm @AltiumJudy and Altium is on Facebook, Twitter and LinkedIn. We also record this podcast simultaneously on video, so on the Altium YouTube channel you can find us under videos, and then you will see the whole series of podcasts that we record. So that is all the housekeeping we have for the moment.
So let's jump right into our topic today which is, embedded passives and I have a wonderful expert for you today, and an old friend, Bruce Mahler of Ohmega Technologies. Bruce, welcome, thanks so much for joining us and giving us a lesson today on embedded technology.
Thank You Judy, it's great being on board here and I look forward to talking to you and the audience about embedded resistors in particular, as well as other embedded passives.
Okay, so before we get going I want to make sure that I'm calling this technology the right thing because I always think of them being embedded passives but I don't think I'm right. How would you characterize the technology exactly?
Well the OhmegaPly® product, our embedded resistive product, is ER embedded resistors, PCT planar component technologies it goes by many names: embedded resistors, embedded capacitors; I think the most common now is ER embedded resistors EC embedded capacitors in particular. When we're talking about passive elements - and those are the two main ones that are really driving the embedded passive world - and a better component world right now so yeah, OhmegaPly® is just fine with me.
Okay so let's jump in now, you told me something recently that I was kind of shocked to learn about and I'd like you to give us a brief history of Ohmega Technologies and sort of the evolution of this technology. What I was really shocked to learn is the age of the company. So can you tell us more about that?
Sure many people who are looking at using embedded passives, think of it as a new technology, something just on the market. It's been out a year or two - no new applications yet but people are looking at it. So when we're asked, this OhmegaPIy® product , how long have you been making it for? And I said oh since about 1972, and they said wait a second, 1972? I said yeah that's actually , we're going on 46 years now and it's amazing that it's probably the oldest new technology out there.
[laughter]
That's a good way to put it.
I think that has a lot to do with the functionality of the material, how it could be used in so many different ways. And so just briefly a history of the technology: originally the OhmegaPly® embedded resistive thin film material was developed, conceived, and developed by Mica Corporation. Many of your old listeners on board know Mica used to be a copper clad laminator, supplied epoxy glass laminates and polyamide glass, did a number of other things, and it was conceived in the early 70s as a way of adding functionality to a laminate material. So rather than just getting copper foil bonded to a dielectric it was a copper coil that had a functional purpose beyond copper traces bonded to a dielectric and so, after many years of development at Mica, a product OhmegaPly® was developed; the Mica laminate product was MicaPly that's how the name originally came about and it was originally developed in the early 70s as a new product.
Now with any new product, somebody had to be the first to go ahead and try it you know, who was going to be on the bleeding edge of any new technology, who was going to be the route maker? And the interesting thing is that back in the early seventies - about again, '72, '73 - the first users of the technology were two absolutely opposite companies in absolutely opposite areas of the electronic industry. One of those happened to be Canon electronics in Japan. Canon, making AE-1 SLR cameras at the time, looked at the technology as being a great way of making a step potentiometer who could eliminate the ceramic potentiometers circuits that they were currently using, at the time and it fit very neatly into their camera system. So they were very simple, these were surface resistors, put in FR4, make resistive elements in the potentiometers, and they started using it in their AE-1 camera. Very quickly Nikon and Pentax started doing the same thing. The other first user happened to be somebody completely opposite - now we're talking about the early 70s - and that user was Controlled Data Corporation; used to be in business a long time ago. CDC's aerospace group who had some very dense multi-layer boards of mixed dielectric layers of PTFE Teflon, layers of FR4, ECL ecologic, lots and lots of termination needs and absolutely no real estate on some of their high-speed digital boards for termination.
So the idea of being able to print and etch a resistive element, and embed it within a circuit layer, particularly underneath an IC package, speeded up board area for them, allowed them to terminate. They got some other benefits of better electricals. They started using us and then very quickly thereafter, other divisions of CDC started using us in things like their cyber mainframe computer systems, and it kind of dovetailed into people like Cray Research and their supercomputers, and we went from there to super mini computers , places like Digital Equipment and Prime and Wayne, and Data General and Harris. All the guys in the 80s who had ecologic termination needs. So it was the heyday back in the 80s, and a lot of mainframes, supercomputers, super mini computers, kind of like with those very, very powerful systems that people now carry in their cellular phones-
In their pocket right?
-at the time it was very, very powerful though. And so, although two different areas of growth we - in the 70s and 80s - found new applications and digital application, particularly termination, but we also started working very closely with the military aerospace industry where they saw the elimination of solder joints being a very positive thing. You know, high g-force doesn't affect it -vibration - there's no joint there in the resistor circuits. So we started working with a lot of them in the military aerospace, space-based applications, radars, antenna power dividers, high-speed digital systems - just a variety of different things. And it's evolved from there, it seems that every five years new technology comes on that says I need to use that. We can talk more about that - we'll get back to maybe the basics of what do we actually do, how do we make it.
Yeah so let's talk about OhmegaPly®, what is it? What is it like to process, and let's just go in and tell us the whole story.
Oh man, you want to go right back to the beginning again. Okay the OhmegaPly® technology is a thin film resistive foil. Now we became Ohmega Technologies - a spinoff of Mica - started as a separate independent company in 1983, and we basically took over that whole technology from Mica, and what that technology involves, is taking copper foil as a standard EDE electrodeposited copper foil that the printed circuit industry uses, and we threw in a reel-to-reel deposition process as a plated process. We plate a very thin coating of a nickel phosphorous NiP resistive alloy onto the mat or two side of that copper and by varying the thickness of that resistive coating we can vary the sheet resistivity. And so this product - a true thin film nickel phosphorus alloy - we're talking about fractions of a micron thick film, so it's truly thin film. So we have a variety of different sheet resistivities, a 10 ohm per square is about a 1 micron thick film, a 25 ohm per square's a 0.4 micron, 50 ohm is 0.2 micron. So it's very linear, as the film that we deposit gets thinner the sheet resistivity goes up. Now we start getting into the dangerous territory of talking about things like ohms per square and I don't want to start having your listener's eyes cross over some strange area, but suffice it to say, it follows thin film technology.
So what we do is, we make a resistive foil that's a copper foil resistive coating. Now what that foil does, that's what we make at our facilities, in our factory in Culver City California very close to LAX or a few miles away. We've been doing it now , for literally 40 years plus at that facility. That resistive foil then gets laminated or bonded to a variety of dielectrics. We work with people like Rogers Arlon, Taconic, we work with Isola we work with Noko, we do some work with DuPont we're working with others out there, but essentially the resistive foil can be bonded to almost any kind of dielectric just like any other copper foil. Standard pressing, heat pressure, it bonds to a variety of dielectrics. Now that laminate product - a copper clad laminate with the resistive film between the copper and the substrate - goes to the printed circuit board community, the PCB community, then prints and etch copper circuitry. They normally will do a print develop, extra process to create copper circuits.
Now they go through a separate (an additional) print develop bed strip so it's a two-print operation and the first print is defining where they have copper traces, then they etch away all excess copper and they etch away all excess resistive film underneath their copper. Now they have copper circuitry. Underneath all that copper circuitry is a resistive material, but electrically it's shorted out by the copper above it. Well you have a spot for tracers.
Makes sense.
That's a point think of it as a treatment of copper only like a zinc or a brass.
Okay.
Now the board shops come back and they apply more photoresist over that copper circuitry and they print a second piece of artwork and that artwork protects all the areas that they wish to keep as copper, and exposes for etching the copper that will be the resistive element. Now in almost all cases, the first etch will define the width of that copper that will be the width of that resistive element. So the second image artwork defines a length of copper that will be the length of the resistor. So it's a very simple piece of artwork to use; very easy to register, but after protecting the copper with photoresist, now they etch away the exposed copper using the 'aplan' based etchings, and they leave behind the resistive film that was underneath it, and they have a resistive element.
Interesting.
-stripping photoresist off the board; leaves them with copper circuitry with resistive elements that are integral to that copper plane. Those resistors can be tested for value, they can go through standard multi-layer processing, laid up with other cores, pressed and then forget you have the resistive elements embedded, if it goes through traditional drilling, print, develop, etch, strip process, or plate process I should say.
So you do a drilling and you desmear, you plate, you etch and your embedded resistor inside; and as a bare board now, prior to shipping for assembly, the board shop can do traditional testing, and they can measure resistor values to ensure they're within spec. They could also be used on the surface of a board, in which case you solder mask over the resistive elements along with your copper traces, and that protects them from abrasion and scratching. The key here is this though: if you use a discrete resistive element, an 0402, an O201. An O201 is a 10 mil by 20 mil resistor. They're pretty small;
Yeah.
-hard to handle, hard to assemble. So if I go to a board shop now and say: hey guys I want you to etch a copper trace that's 10 mil wide, they're gonna look and they'll laugh and say: come on you're insulting us!-
Yeah.
-we do 5 & 5, 4 & 4, 3 & 3, 2 & 2 technology. So etching a 10 mil trace isn't a big deal, five mil trace is not a biggo. When they etch that copper trace, they're essentially defining the width of the resistor, so it's like a controlled impedance trace. They're creating a resistive element of a certain width. Now you say: can you cover it with photoresist and have a little box window that's 20 ml long? Sure that's not a big deal if you etch the copper away. Now they've left themselves with a 10 mil by 20 mil resistive element, which does not push the art at all, it's already built in, no assembly, and all that. So if you say: hey can they do a 5 mil by 10 mil resistor? Sure, we have applications that are using 50 micron by 100 micron resistor. If a board shop connected that copper trace, that's the limit of the resistor width you can print. So you can get a significantly small, very, very, precise resistors that could be located right where you want them, under a package, and that's where we're doing a lot of newer applications like microfluidic heaters, you're talking about a couple mils, by four or five mils you can get very small heat rises in a very localized area, very low power, but I'm ahead of myself.
Okay yeah well so I'm thinking about our audience right now, who are EEs doing design, or just purist board designers for the most part. Why would I want to use OhmegaPly® over traditional? I mean you just mentioned one, if I had space restrictions and I didn't want to use these tiny, tiny parts that seems like a no-brainer but is it real estate, is it cost? Like what drives people - I think I'm opening a can of worms, sorry but what is the cost, performance, reliability implications? And if I was a designer, why would I want to use OhmegaPly®?
Okay, it's a good question and people use it for a variety of reasons. The best reason we like to hear is: I have a design and there's no other way I can design this thing unless I get rid of my resistor and so, kind of I get a tear, I well up a bit, I get very emotional-
[laughter]
-with those. Because then it's all driven by performance and densification.
Right.
But look at everybody - realistically - cost is a big driver, as is performance, and obviously densification all goes hand in hand with reliability. I would say most designers design with us for a number of reasons. The key reason that we focus on densification and that is this: if I have a certain number of resistors on a board and I said: I'm having a hard time routing. I have a lot of passes on my board, either I have to route in more layers, so I'm adding to a multi layer design for its traditional through hole, and I'm gonna have to go to HDI which adds a lot of cost to my board. Or my form factor, my X&Y; dimension is a little too big I need to shrink it down, or my board’s a little too thick, I'm gonna make it a little thinner. So here's a tool, a technology that allows you to do that.
So let's say I have one resistor in a unit area of a board, and somebody says, well gee I want to etch in a pretty natural resistor. Okay who’s cost’s it going to be? It's gonna cost whatever our materials, divided by one. There's gonna be one resistor. Now instead I have ten resistors - what's the cost? It's our unit cost divided by ten because it's the same material that goes through the same print and etch process. So the greater the number of the resistors lower the cost per unit resistor. One application that uses our technology - and this is where it reinvents itself. A number of years ago - five/six years ago - it started being used in MEMS microphone.
If any of your listeners out there, any of your designers have a cell phone, you very likely have us in your cell phone in the MEMS microphone that you're talking out of, or you're listening out of right now. Now why use us in a MEMS microphone? We're part of an RC filter network which improves the sound fidelity significantly. So it's been found to be a very significant offering by the MEMS microphone makers and their end customers who are the cell phone manufacturers - but in very massive, mass quantity production - for many, many years over in the Far East, particularly in China, where our product is used extensively. So in those applications it was a combination of densification, they can make these MEMS microphone boards. The PCB's thinner because they eliminate the chip resistor, you don't have to assemble it, they can make them a little bit smaller and because you're talking about such small little element - even a few resistors only a couple resistors - in that design, you're talking about a fraction of a cent to put these resistive elements in a board. Fraction of a cent, no assembly-
Yeah when they're in the millions that matters.
-all that's very important. There's another example. If I'm a designer and say: hey I have a high-density IO/IC. My fast rise times I have some termination issues but I'm on a 300 micron pad batch and there's no way I can put a discrete component on my surface. To go ahead and terminate, I have too far to go. I have too many of these line. So I have IO of hundreds of traces, maybe a thousand traces, and I do it but guess what? If you're able to take every trace, every logic trace coming off that that IO and I build a resistor as part of that trace - to have a trace it has just a little of the copper removed - leaving a resistive element behind.
So it's a resistor built-in trace which is one of our products: ORBIT Ohmega resistors built-in trace - you can terminate every one of those drivelines - they're underneath the IC package, so they take up no board area. They terminate off that driveline, you improve impedance now, naturally reduce line delay, you also save money because now you literally have hundreds of resistors in a square inch of area or a couple square inches of area, and it saves a lot of cost by not having to assemble and put those discretes on your board now. So cost is a big driver. I just mentioned a couple of them. Densification is as well, but our material also is essentially inductive free. So you know, it means that you have less inductive reactance with fast rise times. So what happens; you get less EMI coming off your board, it's a cleaner signal. Our materials, also because of that, used in certain applications for absorbers or, R cards where they used us, that resistive film, to suppress some of the EMI coming off for-
-interesting
-as a shielding agent. So there's another application. So we're used extensively, not just in power dividers and R cards and absorbers, but obviously as terminators, as in filters, pull-up/pulldown resistors and now we're seeing a lot of activity in heater elements. We're in the military aerospace uses a 'cell' so my active laser activation where they have tiny resistive elements on PCBs that can go ahead and activate a laser for laser guidance for smart munitia, missile systems, or heater elements that can go ahead and maintain heat on critical components in avionics or even in space based applications. Or our product is used in satellites and even in deep space probes. We were on the Mars Express Beagle 2 Lander, on the surface of Mars where we have an Ohmega heater, key critical components up to above minus 15° C. It would work great if the parachute did not land on top of the lander
[laughter]
and prevent the deployment of the solar array but hey it was a great application for our product.
Well it's again - I think just such a surprise - or at least it was to me, when I learned about one: how old the technology is and two: that it's really because of complexity and just all the different things that are going on in the industry right now that it's growing - it's growing at a quick pace.
Significantly so, we've had a wonderful record year; every year is a record year. But that's the nice thing, that the resistive film is like a blank slate. What you do with it is a new assignor and so yeah in the 80s it was all ecologic termination and then it goes into power dividers, and they're still doing all that stuff. But you know what's happening now is, we're saying, it’s utilized in so many different ways so we talked about the MEMS microphone. Well there's new sensor technology, there's accelerometers or other there's other MEMS-type sensors who use us. Now we see automotive sensor technology that says: hey, we could use this, not only is it obviously super-high reliability, been out for decades you know, can be done in high volumes, very cost-effective, density impact identification. But there's some critical components you could use in automotive, 5G technology-
What about IoT Bruce, it seems like ideal for IoT, provided the cost-
-in IoT you're saying?
Yes.
The Internet of Things well that's why I'm talking about sensor technologies. IoT is a combination of a lot of things.
Yes.
Technologies are getting into it, we see our stuff on flexible materials, and wearables.
Your wearables, yeah that was the other thing I was wondering about.
Wearable devices, we can get smaller home devices, home audio devices, and as things get thinner, smaller, everybody wants things densified. So getting rid of the passives especially, really allows you to do that. So yeah IoT is a big thing, automotive, even memory devices going to DDR4, going out to DDR5 , those fast data rates are causing needs for termination again, and 'Genic' has approved the embedded resistor within some of the DDR4 structures. So memory is another area. So between sensor technologies and automotive, and home devices in things like memory devices, and things like heater microfluidic heater bio biomedical type things you know. We have micro heaters on an embedded board, you can have fluid come in and have basically a breakdown to the protein to do analysis, they use us for things like that. It's pretty exciting - so yeah it's been around for 45 years but guess what, we think that the new technologies, the new applications, it's almost like just starting over again.
Yeah I can see that.
Especially, we have the reliability long-term use, high volume low volume, high density/low density, so many different ways of doing it so, that's nice to have that background, make people feel good about using the technology, but knowing that all these new things are developing. I mean I can't wait for the next 45 years.
That's fun.
Well a couple of things I wanted to ask you about what made me think of calling you and wanting to do this - sort of a side note - is, you hear about passives being on allocation and all of that and I'm like: I wonder if Bruce is seeing an uptick just because people are freaking out over automotive buying up whole lines - I don't know if you're seeing that, it was just a curiosity I had?
Well yeah I know what you're saying, we definitely see an uptick, and now part of that uptick within the context of the of the industry. First off, I do want to tell your audience, especially your designers, we've been doing this for 40 - 45 years plus, as I mentioned - 46 years. I'd like to say that I was only 2 years old when I first got introduced to technology-
-We're going with that; I was three, you were two - let's go with that!
But we also have designers at our company whose job it is to work with the design community, particularly a PCB designer who could help them optimize their design, who can develop real footprints of resistors. What we don't want your your listeners to do, is reinvent the wheel; we want you to use our knowledge, talk to our people - say: hey here's what I think I'd like to do, I have an application I want to use, does it make sense for your technology? If it doesn't, we don't want you wasting your time. So ultimately you're gonna say, we're not gonna use it anyway we want you to have an optimized design because we want you to be successful. So think of us as an extension of yourself, of your team.
We're part of your design team we're there to help and assist. If you go to our website ohmega.com, there's a lot of white papers, there's a lot of good information there that people could read and reference. But more importantly is the communication with our staff, technical people who can really help you. Now talking about in general, the industry, there is an uptick in that. We talked about passive, so I mentioned it; we're in filters and MEMS microphones, resistors and capacitors and in one case, one of the capacitive materials, the embedded capacitor material FaradFlex, which is a embedded capacitor material, it's produced by Oak Mitsui. So Ohmega Technologies, my company and Oak Mitsui, got together and combined the material and had our resistive material on their capacitor material so we'd have one layer resistive capacitor.
What? My head just exploded!
What we did was we found that it's pretty simple, from a technology standpoint, to stick two technologies, each separately have its own complexity but working together really worked very well. Importantly enough it had such synergistic effects in terms of improved power, lower RTC characteristics, or change of resistance to function the temperature down to almost nothing, the stability is astounding over a wide temperature range that we applied and we got a jointly held patent for the combined technology which we have in the US, and also all over the world now. So it's a joint technology pact between Ohmega Technologies and between Oak Mitsui and Mitsui Mine in Japan for this technology, and we see applications where if somebody wants to get a resistor and embed it, they also want to embed the capacitor. They get rid of capacitors that are passive. A lot of times they want to get rid of resistors too. So it goes hat in hand with a lot of those.
In general, there is a lot of movement in the industry to embed it, but it's a growing thing because of densification, growing needs for real estate, smaller, thinner, lighter. You touched upon something and that is material sources, right now the industry is going through some uptick. I think part of that's military aerospace that has increased the amount of funding and a lot of military programs, but also other areas. So we've seen that as well and our products are used in a lot of stuff. Radar systems F-35, F-22, a lot of missile systems, Eurofighter, just all over the place. A lot of satellites, a lot of SATCOM, a lot of other things like that.
A lot of radars on the ground as well, but we're seeing that uptick because the IoT, as you mentioned, in the Internet of Things, there's more and more sensitive technologies being demanded into a lot of different product. People are amazed at how many sensors go into so many things these days and the key with a lot of that, is densification, smaller, faster, cheaper - so that gets hand-in-hand with the 5G, the automotive, self-driving cars that are coming up; a lot of the sensors the Lidar, other sensor technologies are going to self-driving automobiles and what everybody says is: hey, this all sounds great, but you know what? If I have a printed circuit board not using a computer and I have a failure in that it's okay. So it's annoying my computer goes, I swap a board, I put up a board, but I cannot afford to have any failure. I cannot afford to have anything go wrong, if I'm in an automobile that's driving itself, do you have room for any kind of failure? And so it's taken very seriously in the industry and going to a lot of these conferences and hearing the talks, the people involved with testing a lot of these are very concerned. They have to have absolute... as tough as it was, they have to make it even tougher for testing. Nothing can fail, so a lot of that comes into what can we do to improve reliability? Hey let's get rid of solder joints.
We want a kind of thing doesn't cause something go 'ding' and fly off a board anymore - or you know X&Y; expansion or z-axis expansion, all those things. Get rid of those solder joints, mechanical joints, improve the reliability while you enhance, densify, improved electrical performance. So we're saying that that's going on right now. And the other thing is that companies are concerned about, the industry is facing some interesting things right now in the printed circuit industry copper lead times are really out.
Yeah, that's crazy too.
-yeah the industry is getting smaller and smaller, yet at the same time the end-users and designers have to rely more and more on fewer and fewer resources. So we've been around since like I said 1972, so for 46 years we've been supplying this technology and we have never ever not been able to supply this in those 46 years. It's important for us that, A) we manufacture everything ourselves we make that resistive film we test it, we have test facilities which make sure that the product is what it should be before it ships out the door. We have hands-on manufacturing that's critical we don't want to subcontract making our product because we feel it's too important to our customers. They're relying on us. If we subcontracted, what would happen if whoever we had make it, went out of business? Or they sold the business; I don't want to do it anymore, and then we can't get product, our customers can't. We don't want to rely on someone else; that's number one.
Number two, we have very good close working relationships with our raw material suppliers. Most of our raw materials are USA-based, we get them in from the US you know. We want to have a critical supply chain. When you're talking about scarce resources like copper and other things, it's important that we have that kind of relationship with our suppliers so that we always have product. We're always there to support our customer needs when they need it, how they need it, and that to me is very, very important because a lot of companies are coming to us saying: oh yeah we're giving two months lead time on getting product, and how are we supposed to deal with that? And say what about you guys? I said: you want some of our stuff we'll ship it tomorrow. To us that's very important. Customer; you've got to go ahead and satisfy customer needs and especially their concerns that's absolutely critical in the industry today.
Yeah and it's refreshing because we get in this weird cultural thing as a business and it's like: Oh faster, cheaper or we're gonna be the lean supply chain and buy out. We get into this whole frenetic thing, but we forget if we're not meeting any of the customers we'll be out of business. So I really love that philosophy. Now as far as our listeners go Bruce, we're gonna share all of this in the show notes right. Everything that's on your website I encourage it, so we're going to supply all those links and the website you guys, if you're interested you can call Ohmega Technologies directly, get the help that Bruce alluded to. But they have a really great website with some really neat things that will go into even more depth than Bruce has gone into so far.
So thank you so much. So Bruce, as we wrap up here. First of all, thank you Bruce is joining us from IMS in Philadelphia today even though he's - at Ohmega in Culver, so thank you for hopping out of the show for a few minutes to give our listeners a treat, so thank you for that. When I wrap up the podcast I always like to have a little feature in here called 'designers after hours' because most of us techie weirdos have a little bit of a right brain and have interesting hobbies I've found. Is there anything that you do after hours that is creative, compelling, interesting or otherwise, or do you have any after hours? do you just work all the time Bruce?
Do I have any after hours? That's a good question.
Yeah we encourage people to call us and that keeps me rather active and the staff at Ohmega and we welcome that; please, please, please call us, email us, we'd love to talk to you and listen to you. As to me yeah I enjoy travel, I enjoy writing you know, I always have . Now it's mostly technical things or papers that I publish. But you know, I love doing fiction as well, I do do that and I get very involved. Between that and having a lot of crazy grandchildren running underfoot, that keeps me going.
That fills up your plate. So also, would you say you are a geek or a nerd?
I'm sorry?
Would you say you are a geek or a nerd?
That's a good question, I'm probably more geek than nerd yeah they've cleaned me up over the years, so I think I'm more geeky.
Yeah I would say you're more geeky, but you are walking on the razor's edge my friend. You can you can dip into that nerd space pretty easily.
[laughter]
Oh man, and I've been so good I haven't cracked any jokes, you can be mad about.
[laughter]
Here I am, now you're telling me I'm close-
-no, no only in the best kind of way that you like go into this nerdy space of technology but that's really -
-you want to know something; it's been a long time, I've been doing this a long time and I'm so excited - it's like it's a renewal if people get that I'm excited about technology about where Ohmega fits into technology it's because I really AM. It's genuine, our president Allan Leve, over at Ohmega Technologies, here's a guy who's had the same kind of passion. So every time we see something, we're always sending articles: look at this it’s neat isn't it? So if you call that nerdy, you call that geeky, that's fine. You know what we call it being enthused with technology and how we fit into that technology.
Absolutely.
-because I've been called a nerd and a geek I'm gonna drown myself in a Phillies steak salad.
-extra cheese and onions.
[laughter]
No - when I say you teeter is only because I remember when I was working at Transline Technology, you came in and you were showing us how it's done, how it's processed as a board shop - and I remember listening to you going: this guy totally knows his stuff and it was so articulate and I'm like, boy when I grow up I want to be able to talk like this. Like Bruce Mahler does, man he's got it going on! So that's why I say-
-just wait until I grow up really.
-well it is an exciting time in technology there's no grass growing under our feet so I share your enthusiasm for everything that's in the market and you're seeing everything so that is really exciting. Well thank you again for -
-thank you I appreciate it Judy, the opportunity to spend time with you and spend time with your audience, and hi to everyone out there - look forward to talking with you, look forward to working with you and like I said; a lot of exciting things out there right now in our industry so we're working in the best industry out there.
We are, now we're gonna send poor Bruce back to booth duty where he can stand in a booth. Sorry to send you back to booth but thank you so much. Again this has been Judy Warner with Altium's OnTrack Podcast and Bruce Mahler of Ohmega Technologies. Thanks for tuning in again until we hear or talk to you next time always remember to stay on track.
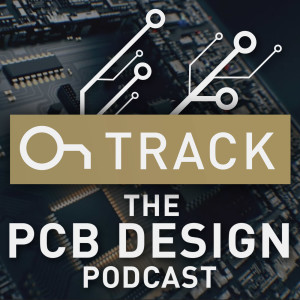
Tuesday Jul 03, 2018
Tuesday Jul 03, 2018
What finish should I use for my PCB Design? There’s no one single answer, it depends. Meet chemist and surface finish expert Mike Carano, the Vice President of Technology and Business Development at RBP Chemical, industry leaders in high performance chemical technology. Mike emphasizes a key question when it comes to surface finishes, “What are the reliability requirements of the environment?” Learn about the chemistry behind different finishes, fabrication and get tips for avoiding corrosion in unexpected environments in this episode of the OnTrack Podcast.
Show Highlights:
- Mike was Inducted into IPC hall of fame.
- RBP Chemical - veteran owned small business, based in Milwaukee, founded in 1954 as a supplier for the printing industry and over the years evolved into surface finishes and also carry product lines for Embedded Medical Devices and Semiconductor and Mining industries.
- On using solder mask over bare copper method - prior to going out to assembly the copper needs to be made pristine.
- What are the surface finishes and which to use when? 50% of industry using hot air solder leveling (HASL), a surface finish with a long successful history.
- Other surface finishes: Electroless nickel immersion gold (ENIG), Electroless Nickel Electroless Palladium Immersion Gold (ENEPIG) - which is common in IC substrate, packaging industry.
- Future of surface finishes: Tin-silver, Direct palladium copper
- What finish should I use? There’s no one answer, it depends.
- Are there common examples of things that can go wrong? ie. High frequency design applications - ENIG is a well known issue that most engineers learn about the hard way.
- Where is the final product going to be used? Is it a domestic product or for the military?
- Reliability first, cost last. Cost should not be driving force.
- The environment is what really matters i.e. Shock-drop or Brunel fracture - consider for mobile phones, ENIG - tin-nickel bond, not tin-copper, corrosion environments, temperature extremes
- What are the reliability requirements of the environment?
- The most high quality board fabricators have strong process control and automation in place to ensure chemical stability.
- Board designers are looking for electrical performance. Need to ask about the environment.
- I would put every designer in a circuit board fabricator for a week and let them build a board they design.
- To learn, you need to practice and get practical information on building the bareboards.
- Creep corrosions on the mill automation machines because the OEM is specifying the finish.
- Japanese techniques i.e. Shokuku chemical
- Most substrate work is done in Asia; IC substrate packaging at its best is in Japan.
- Advice for learning: IPC courses, CID and CID+ training is one way to learn more.
Links and Resources:
IPC Hall of Fame Interview Video
HDP Users Group (HDPUG)
Hey everyone it's Judy Warner with Altium’s OnTrack podcast. Welcome back we are glad to have you join us again today we have a very unique topic and speaker which was actually brought about by Mark Okumura who is the Senior Principal Hardware Engineer from ETS Lindgren who reached out to me and asked me about the topic of surface finishes and lucky for you I happen to know the guy who is a chemist and expert on surface finishes. A longtime friend Mike Carano from RBP Chemical. Before Mike and I get started, I wanted to please invite you to connect with me on LinkedIn or on Twitter, I'm @AltiumJudy. Altium is on LinkedIn, Twitter, and Facebook, and also please know that we're recording on YouTube in case you want to see our sunshiny faces. So Mike, welcome thanks so much we’re delighted to have you.
Thanks for inviting me.
It's good to know friends in high places right?
Well, I have friends in low places.
[Laughter]
I don't believe it, well maybe, so Mike, I’ve got a question. First of all let's talk about your background a little bit so as a way of introduction Mike Carano was inducted into the IPC Hall of Fame a few years ago and I had the privilege of doing the video interview that was highlighting his induction into the IPC Hall of Fame because he has served on so many committees and boards for IPC, but he really is the go-to guy on chemistry. So Mike, tell us a little bit about your background how you got into chemistry specifically related to the printed circuit board electronics industry?
Well sometimes Judy, things happen by accident really, chemistry and sciences were always a love of mine so I always liked to experiment - my parents got me the chemistry set, and everything from blowing up golf balls to me making things at home, everything from even experimenting with making wine that's chemistry - that seemed like a good thing to do right? I also realized that probably owning a vineyard would not be in the immediate future so onward and upward with chemistry, particularly the area of physical and advanced chemistry electrochemistry working on a Master's Degree, I happened to be walking up on campus one day back in 1980, 24 years old, and there's a gentleman standing outside this building and he noticed my chemistry books he says, hey come here I want to talk to you, and I thought, oh what's this about? And I noticed the sign on the door there, Youngstown Ohio City Electrochemicals, and he asked me if I wanted to interview for a position there. Well it was perfect because graduate school was more part-time. I was doing some teaching assistance and what do you know, I interviewed for this thing on surface finishing chemistry having no idea really what I was getting into, but I did. The idea was finishing my Master's degree, and go on and do something else - maybe do this for two years - well 39 years later here I am still in the industry. In some way, shape, or form, so that's how I got into this and as the company, Electrochemicals in those days, founded primarily on the metal finishing industry - you know, surface finishing for doorknobs and bumpers and decorative plating. Well the company was just then getting into printed circuit board chemistry and a lot of people didn't even know what that was in those days because it was a fledgling industry there was mostly - remember Judy way back then was the 80% of the industry was really run by the OEM...
Yeah
-So digital equipments the the Adelphi’s, the Delco’s the IBM's, but pretty soon there was that switch, and then I got involved in IPC and pretty soon was formulating chemistries and technical service, traveling globally around the world was fascinating for me, and here I am today, and still in the industry in some way, shape, or form. You know, you evolve, you continue to evolve matter of fact, just like surfaces they've evolved.
Yeah right.
Where we are today, I'm sure they'll continue to evolve in the very near future.
Yeah for sure, so can you give us a quick overview, I know you were Chief for many many years and now you're with RBP can you give us a quick thumb nutch of RBP?
Absolutely, great opportunity, company privately owned (veteran owned) small business, our company is based in Milwaukee Wisconsin and was founded in 1954 and has been privately held since. The current CEO and majority owner is Mr Mark Kannenberg, he's my immediate boss, Mark served in Vietnam, he's a West Point graduate and also a Harvard MBA, but he always wanted to kind of get in the business of owning his own company even though he had many, many opportunities. So he's now been running RBP for these last 30 years. Under his control the company has grown beautifully - initially, the company was founded as a supplier of materials and chemistries for the printing industry, newspapers, newsprint magazines, but over the years also evolved into surface finishing, surface treatment and printed circuit board chemistry, which is the company today, because as I said it continues to evolve. Today and we have four major product lines the printed circuit board and photochemical milling chemistries. We have a great product line in the area of embedded medical devices, and we also serve the semiconductor and the mining industries with some specialty additives. A lot of people don't understand the connection but there's a connection all the way through the platforms because the chemistries are basically adapted to work in all those industries which makes working with RBP fascinating for me - the diversification but yet the the continuity and the familiarity - so great opportunity and I've enjoyed it immensely.
Good, thank you for sharing that Mike, so let's jump right into surface finishes. I'm sure most of our listeners who are engineers and designers will be familiar with surface finishes but let's just go back to our ABCs for a second and just define surface finishes for us for PCBs.
Sure that is the part of the board that is really going to be used to prevent oxidation of the base metal, as you know, typically we have copper as the base metal if you're using the solder mask over bare copper method where you basically put solder mask down that nice green stuff and the copper is showing, you have to make that copper solderable, you have to preserve the solderability so typically, prior to that board going out to the assembly operation, the copper has to be basically made pristine with a finish that does not oxidize so that you can join the component leads, whatever they may be, whether they be surface mounts, through-hole, BGA, QFNS, QFPs, they have to be able to to wet that surface and form a reliable joint. So the surface finish is critical for that application and for that end product.
So tell us - give us just a rundown - of what the surface finishes are and then we're gonna jump in to which one to use when.
Sure well, here in North America and primarily for the military, we're still using - at least 50 or so percent of the industry - uses hot-air solder leveling. Basically you're taking that solder mask over bare copper board, flexing it, cleaning the copper and then dipping it into a molten solder pot to coat the surface. But over the years, due to a lot of other constraints, one of them was to get rid of lead. And even when we have lead-free, hot air leveling, the other surface finishes have evolved, as a matter of fact, have taken center stage primarily outside of North America. With these surface finishes are we hear the term ENIG, which is Electroless Nickel Immersion Gold we also hear about Electroless Nickel Electrons Palladium Immersion Gold also known as ENAPEG, and while that may be an expensive finish, you see that used quite a bit in the packaging industry, the semiconductor packaging IC substrate industry. Then there is OSP Organic Solderability Preservatives, which is actually the only one of these to be non-metal-containing and then we have immersion silver, and immersion in tin, and again we expect that there’ll be other additions of these finishes coming up in the near future. Potentially a tin silver or direct palladium over copper to get rid of the gold altogether. There's a lot of movement in this area to enhance the surface finish reliability at the same time managing costs because you see how precious metals like gold and palladium can contribute significantly to the cost of that board. Which then makes you wonder, okay what finish should I use and when should I use it? So that's a rundown of our finishes and each one of them - I can tell you this Judy - when people ask me, and I travel all over the world, what finish should I use...
Yeah
-no one finish fits all.
That's a loaded question isn't it Mike? It depends, that's the answer.
It depends right.
Well as I mentioned in the beginning, this gentleman Mark Okumura reached out to me and said, are you ever going to talk on your podcast, or do you have any information about surface finishes? Because in his particular case - and this is just one of many many high frequency application engineers and designers - have found out the hard way that if they use ENIG the Electroless Nickel Immersion Gold, that if it's high frequency then we have the skin effect and then the signal begins moving through the nickel and the nickel is lossy, and unfortunately that's a well-known issue it's been going on forever but it seems like people have learned that the hard way, unfortunately one at a time, that's just one example. So can we talk about when we talked a few weeks ago, about environment playing a huge role on how to make a selection on your surface finishes. So can you jump into that a little bit?
What I mean by environment is, where is that final product going to be used, and let me just preface it this way, if you're in this industry, whether you're in the printed circuit board industry directly or you're an assembler or you're an OEM. Choosing the final finish for that product may be the most important decision you make, because it is going to impact that long-term reliability of least of that solder joint now as I’m saying solder joint, I'm using it interchangeably with lead-free as well. And compounding that, is again, where are the boards going to be used? Is it to finish in harsh use environments such as automotive under the hood, military aerospace - and that's one application. But then, what about consumer items like mobile phones, smartphones, desktop computers, smart tablets, household devices. You don't need a product or a finish that adds $9 a surface square foot of the board if you're using it in a washing machine in your house, or in a microwave, or even a desktop or laptop computer. Now military aero things like class 3, or class 3A that have to work 24 hours a day, seven days a week and can't fail - you can't fail. You may look at that and you say, well do I need ENAPEG, do I need ENIG? Do I need to make the OSP also work? And some people really are surprised when they find out that OSP’s a very reliable finish. It's not wire bondable but in terms of reliability in forming the copper tin in a metallic, and having a reliable solder joint, it's fantastic.
So think about that, it also happens to be the lowest cost finish but I am of the opinion, and I asked somebody this, and I listed ten things I have cost of the finish at the bottom, because that should not be the driving force of what you put on the board. It's the environment where the board is used and then you ask yourself other questions. Is cosmetics important? Do I have to have a shiny silvery finish or don't I need one? I'm worried about shock drop, we know for example, if something I have in my hand drops a lot like a smartphone. you worry about brittle fracture of the components - actually fraction when that phone hits the ground - we've all dropped our phones and the mobile phone companies, the Apples of the world and the Samsung's, conduct shock drop tests all the time because that's important criteria. You don't want to spend money on a new phone, drop it and find out the components fell off. So that's why you don't see ENIG used a lot on the smartphone, you use things like something that makes it much stronger - copper tin and a metallic bond - whereas with ENIG, your tin is formed with the nickel so it's a tin-nickel bond not a tin copper one.
I see.
So, we all know, and there's been hundreds of papers published by many, many companies and fantastic researchers around the world, showing that the tin to copper in a metallic is much stronger than the tin to nickel in a metallic. So that's something to consider as well, not just the cost. But you might use ENIG in medical devices, we know the military is starting to look at ENIG as a final finish, but they also do some things to ensure the reliability of that component as it is attached to the surface. So there's a myriad of things to look at - oh and corrosion environment - in terms of creep corrosion, and that's an issue and silver tends to be somewhat prone to creep corrosion, but in an industrial environment kind of outside, or in a clay modeling studio or in a paper mill where sulphur is emitted.
Yeah that's interesting.
So, if you told me, well I'm making this part because I work for General Motors and I'm modeling, I'm gonna use clay to model my next car and I'm gonna have all these computers hooked up inside that studio, I think I'll use boards with silver on them. Well you probably don't want to, your work is gonna be lost, so that's one consideration. As I said shock drop is another, but again where are you using the final product? Industrial automation, using it outside, base stations, all of those things. Industrial controllers where we're subjected to not just environmental contaminants,but maybe significant vibration, temperature extremes etc. So always look at the environment where you're using it and what the reliability requirements are. Can you afford the warranty, what is the warranty when you take something back? If it's inexpensive, you can use an inexpensive finish but if the cost of failure is great, you should rethink that finish which you're going to use and how you're going to use it.
That totally makes sense to me. You had mentioned that a lot of people think that OSP is generally a sort of low-tech product, but you were pushing back against that when we discussed that, why is that?
Well 25 years ago OSP was what you would call the single attachment finish - one reflow, maybe one through-hole, and that was it. It lasted four to five months whereas the other finishes, like hot air leveling - one year, two year shelf life - that's changed. Companies have made significant improvements in the reliability. Also the the ability of the OSP to reduce oxygen penetration on the copper, and that again is what you're trying to do, you're trying to prevent the underlying copper from oxidizing so that when the solder melts and spreads on the surface, it spreads and encapsulates the leads on the side on the components and solidifies and it's a highly reliable. If the surface is oxidized even slightly and doesn't wet properly you've lost your reliability, but OSP has come on strong now and you see it in automotive under the hoods, major telecommunication companies using it for the reasons of getting away from brittle fracture, you see them in smartphones - a significant number of smartphones - and I have experience in those areas so, I'm talking from personal experience - the reliability is there with the right finish. Now the low-tech you find, if you buy a low-tech OSP from somebody you've never heard of, you’re taking a risk, but the companies out there - two or three that are making significant contributions to the performance of OSP - they've upped the game significantly. Many of them are fifth-generation molecules, these are synthesize organic azone molecules, that just do a fantastic job, and I would not hesitate to recommend it for numerous applications.
It's interesting how that's evolved over time, I wasn't aware of that until you mentioned it to me recently, and that's some of the magic of chemistry that just runs in the background of our industry until sometimes - it seems like - until there's a problem.
That's right.
We don't talk about it, so I'm glad to sort of have this discussion.
That’s a good point, to that point Judy, when Black Pad showed up what people will call brittle fracture...
Yeah.
-it set the industry back 15 years for ENIG because they didn't understand it, they wanted to blame the phosphorus content of the nickel deposit, but that turned out to be incorrect, it turned out that the cause of that was the galvanic effect. When you put immersion gold on top of nickel you're not electrolytically plating it, you're doing an immersion deposit, also known as galvanic cells, so to deposit on nickel, some nickel actually has to corrode and leave the surface, so that the gold can take its place. And that's the main difference of an immersion deposit. Well, what was happening because of the way things were being run, pH, nickel morphology, roughness, etc that galvanic effect was significantly large, causing this corrosion - significant corrosion - to take place on the nickel surface, and that would impact negatively the formation of the solder joint. And there you would get brittle fracture, you drop something, It breaks. So, things are better now, but I still would be very careful, if you told me, I'm gonna put ENIG on my board today, I would say do a first article, make sure that the board design you have, will not end up with this issue.
That's a good advice and, for people who are listening. Again - you're going to hear me say this over and over again - and I'm not going to apologize for it, is that you need to get into a board house, find the time because most really good, world-class board houses - you're going to go in and you're going to be surprised to see... and Mike can talk about this, the complexity of the labs they have in place to make sure that their chemicals are stable and doing what they're supposed to do. Mike, I imagine you've spent just more than a little bit of time inside of board houses discussing chemical balance and, if you would, jump in on what the choice of surface finish has on the fabricator and why the designer should know about that?
Right yeah, well first let's go back to your first question about these board fabricators the ones that are high-quality board fabricators and I'm looking at not just on the surface finishing side, but also other aspects of the circuit board fabrication including electroless copper, direct metallization, the amount of control that they have in place, process control automation, to keep plating and other the key ingredients within a very tight operating window. And that's not difficult if you invest the time, and you have the commitment to ensure that. I can’t tell you how many times Judy, have been in situations where I've had to troubleshoot a problem because someone said I've got this issue, I've got that issue, you go there and you find out that they were running the chemistry basically way outside the window. Well, why'd you do this? Well, we only check it once every two shifts. Well, you can't have a high volume operation like what you're doing and then check the chemistry once every two shifts and I'm telling you, 90% of these problems that I see related to process, are related to incorrect use of the chemistry and mishandling of the controls that are available to you.
Now does that mean that the fabricator needs to work much closer with the supplier, but if the supplier is already doing this for them, the fabricator needs to take some responsibility. But again, I've been with a number of companies who have complete failure analysis labs also in their facility. So, they take it to a very high level, they're basically their own qualification facility to ensure that they understand where the issues are. They categorize every defect and those are the kinds of ones you want to work with.
Absolutely, and I've worked for shops like that where they literally had PhDs in chemistry renting the lab. They were doing their own cross section and when suddenly, there's a spike in volume - if you're not on top of it and you don't have those people and all of a sudden - whoops production went up, but we're still checking our bass at the same rate we were before. And then like, oh what happened? Well there's all these things that need to be taken into consideration and adjust it accordingly. So, what other fabrication considerations are there that that maybe designers or engineers that are designing boards would want to consider as they decide what they're going to choose?
Well good that's a good point, and you and I know design is important, because there's this conundrum in our supply chain. The fabricator is looking for design for manufacturing and the designer is designing something to work in a certain fashion. Electrical performance, dielectric spacing, and and they don't take into consideration potentially what that does, how that impacts the bare board fabrication process. That's a very significant right? What - and I'm gonna go back to this - because I find this to be an issue as well on the assembly side boards come into the assembler, they come from somewhere, and they call me and say I have the the plating is lifting from the surface when we assemble, or the solder mask is lifting well I said do you did you specify the grade of solder mask, do you even know what solder mask is being put on the board that you're bringing in to assemble? Well no. Now I find out - it's very easy for me to find out - that they’re using, the fabricator... wherever, typically not here, are using a low $10 a kilo solder mask because no one specified it. And of course, that $10 a kilo or less solder mask is probably gonna work beautifully in a handheld child's toy, it's not going to work very well for your medical device. And you're gonna have all these other problems. So I think, I hope the designers would get more involved in understanding the difficulties in making a bare board and also understand: just don't specify ENAPEG because it sounds great, or sounds sexy. Because number one, you're probably not paying for it, somebody else has to pay for that ENAPEG and at $12 and $10 a square foot. Understand - and this is where the board designers are looking for the electrical performance - do they ask where the board is going to be used? Is it going to be in a harsh-use environment, is it going to be in a benign environment clay modeling studio? These are the key questions for them. Typically what I see designers do is, say this is how the board should be built, these are the layers, these are the holes, and you should use this material with this dielectric constant. That's all great, but it's not enough.
Right
And I've been teaching this advanced troubleshooting course with printed circuit board fabrication for years, and you'd be surprised at the number of designers that actually take that course, and they ask the craziest questions. Which tells me they haven't been outside of the board fabrication, outside of their design studio. Understand that you need to live with that a little bit I would put every designer at least in a circuit board fabricator for two weeks and have them build a board that they designed.
Yep I agree it's hard - we encouraged that here a lot - and almost every guest on here says the same thing. Because you and I've been around the block a little while, and understand that there's time constraints for them to get out. However the long-term cost of not getting out there and not onboarding. And this is another plug - you and I've been around IPC awhile - this is another plug for CID and CID+ training, as well because there you onboard some of these things that may be outside of the obvious things that are around manufacturing and assembly. So Kelly Dack wants to start field trips on every CID course. I'm like, yes let's do it!
You know, to me that would be fantastic, and to be honest with you and being heavily involved myself in an IPC, one of the things that I've suggested that when CIDs and the CID+ students earned their certifications, they should also have to get some understanding in coursework and practical on the bare board fabrication. You should make it like you did in college, the practicals, you just didn't do the book work, you had to go into the lab...
Exactly!
-apply what you just learned from the book, because if you couldn't resort to practice, at the end of the day you can't practice it. You've not learned.
And as we both know, the cost of ignorance in these areas is so high, like avoidable mistakes.
Costly... I've seen an entire clay modeling studio shut down, a paper mill shut down, because, again the paper mill folks were buying the controls from the OEM who was specifying the boards to be made but the finish... So the poor industrial automation company using these expensive controls were wondering why these inexpensive instruments are no longer doing what they're supposed to do. And they find out that there's creep corrosion in there because the OEM specified immersion silver or bought the board somewhere cheap where the individual companies decided to cut corners, like they do, to meet the cost. Like not putting enough gold on, not putting enough nickel on. You know, there are specs for a reason.
There is, absolutely.
And that's obviously a discussion for another time.
Yeah that's a whole other podcast, and then there's everything you're doing - HDPUG - which is another podcast I'd like to get you on for as well. I want to put a pin in our conversation right now because I realized, in the beginning I failed to mention to our listeners that you may hear some background noise here. There's some... well, what I was telling our producers is, we're building a better podcast but it’s noisy in here, but really what's happening is we have some construction and of course it's overhead in the green room here in our La Jolla office, so it's directly overhead, on this day of course, so please, please excuse any background noise.
So Mike, you sit on boards for international companies as well as companies here and you are a respected and trusted advisor. You mentioned to me about things that the Japanese are doing that are very innovative and that is that they're mixing finishes and doing selective finishes can you tell us a little bit about that?
Yeah, and this is if you can see the IC substrate side in the Japanese, or the ones who really made miniaturization go. I mean they understood how to make things small, not just lawn mowers and engines like Toyota Camrys and things like in the Prius, but they figured out early on how to do it with circuit boards and and putting more functionality on the chip. Matter of fact, that's where OSP was actually invented was in Japan, in those days it was called pre-flux because it was in the rudimentary 1970s day, but they pioneered the OSP and matter of fact, today the leading OSP company in the world is Shikoku Chemicals out in Japan, they continue to evolve that chemistry and I trust them immensely.
So, going back to that question what you do is, in the IC substrate market, where you've got a complex chip that has to have gold leads or gold wire bonding, you have on one side of the substrate, nickel gold, and then you bond the chip with the wires to that feature. But then on the flip side, which is going to be a BGA feature, you have bare copper which is OSP. So they have the BGA balls on the bottom side and the IC substrate - the chip actually, the the die as they call it - on the top side. So you have ENIG - selectively on one side and bare copper meaning OSP - on the other and of course it's a flip chip. So with the IC substrate or the IC chip in there, you marry that BGA to the Barriss surface of the copper board meaning an OSP, and you've got this fantastic package, if you will, instead of doing it all in the nickel gold or all in ENIG and handle it selectively. And they've developed these processes, and they've also developed a selective imaging, if you will, to make that happen. but it's relatively easy to do, once you understand the ramifications and how to make it work, and make sure you don't get an OSP that doesn't say, ‘attack’ the exposed nickel gold. All these things, it's pretty pretty intricate, but it's been around for some time and with a lot of success so I've selected ENIG as they call it.
Interesting, so I was just gonna ask you, what does that do to cost and process ? You're saying it's not difficult, how about cost implications?
Well there is an additional cost of putting the second imaging step down to protect the board from plating where you don't want it to go, but instead of doing the entire IC substrate in nickel gold, you're doing just one portion of it where the wires from the chip are placed, from the die so, that does help you significantly in the long run. It also makes the BGA perform better because you're marrying basically tin to bare copper making another opportunity there.
Do you think that will find its way here into North America?
Well, the thing is there's only a few fabricators here who do work in the substrate industry, most of the substrate work is done in Asia for the Amcor’s and the Intel's and the Samsung’s so you see a lot of the supply chain there. Some big American owned companies in Asia are doing it in volume, but again, if you want to see IC substrate packaging at its best it's the Japanese.
Yeah that makes sense.
Yep they’re the leaders,and they've been doing that for 30 years, so they tend to be ahead of their time, but now the time has come.
Yeah well it's interesting to get your perspective on sort of a global scale, as well this has been great. Our time is coming to a close here, but will you please share with us links to any white papers or slide decks or anything you have? Because I think how I want to wrap up is Mike, if you are a designer what would you do with all this information? And we've kind of shared it sort of anecdotally and quickly here, but if you wanted to learn more about this where would you go, and what kind of things maybe can you share with our listeners that we can throw on the show notes so they can maybe get better at this.
Well very good. I would encourage you designers who haven't taken an IDC course outside of design - I encourage you to take them - you look on the IPC website. We just had Apex where, in addition to technical papers, there were workshops on a number of different subjects including my Advanced Troubleshooting course, but there were also courses on the Basics of Bare Board Fabrication, and some of the instructors do a great job of giving you the tour, if you will, of the very basics. So you can get a feel for how the board starts with bare laminate, actually starts from the design, and actually ends with the finished product, going out to assembly from a manufacturing standpoint, and you can follow that up by taking the Advanced Troubleshooting, so you can understand where some of the problems and technical issues come from when the board is fabricated, with the various chemical steps and the mechanical steps like drilling and plating and immersion gold and silver. Whatever you need to do, that would be something you should do, and also watch for IPC Tech Ed, where they're going to be putting more and more of these courses. Standalones in different parts of the company whether it be San Jose, San Diego. We just did a course in Boston back in April which was well attended, and we just had the High Reliability Conference in Baltimore a few weeks ago, which had a high military aero content to it. But there's a webcast as well. And also, I encourage you to look at the IPC website - http://ipc.org/. Go through the technical papers, look for the events that are going on there but obviously at every Apex there will be this myriad of courses to take, and I encourage you to go to your boss and say, look this is something I think will benefit me, and you're gonna send me there anyways for the other events, so why not get there on a Sunday and take this course?
Yeah good advice.
SMTA is another good place that has a lot of technical papers and seminars and webinars related to things like surface finishes and design for reliability etc. Matter of fact, IPC actually has a Design for Manufacturing workshop that is taught by some really highly-skilled people too, so that might be something that a designer would benefit from. Again, because the designer or an actual designer is actually teaching the course from experience because he lives it...
Yeah
-let me build bare boards... I'm talking like Gary Ferrari and Susie Webb and those folks, they've actually built boards but they also design. Happy Holden and he's built boards, he designs boards, he understands - they get it.
Right.
That would be an interesting perspective for all those out there.
Okay good, that's great stuff. Well we'll make sure to attach the links to IPC and I know they're doing a lot with education right now, and so I'll make sure - and if you have anything to share with me please do - and we'll make sure we also include links to RBP Chemical.
Yeah, https://www.rbpchemical.com/
And then we will share anything else that you want, and I'm hoping I might be able to twist Mike's arm to come teach a surface finish course at Altiumlive in October. But we'll see, he's so in demand, hie’s a popular guy - but if I had my wish, that's what we would do because I think it'd be a great place again hope to have about five six hundred designers there so I think they would benefit.
So Mike thank you again, you're a dear friend, and thank you so much for always freely sharing your information. Mike also writes a column for PCB007 Magazine, called Trouble in Your Tank, and that's where I learned a lot and actually how I became friends with Mike as I was asking him if I could please take some of his content and repurpose it for blogs I was writing. So we'll also include that link to his column. So Mikey, thank you again you're a dear contributor and friend to the industry and thanks so much for taking time out of your busy day to do this with us it's been fun.
Well, thank you Judy, thanks for inviting me. I appreciate it, you have a great day.
Thanks you too again. This has been Judy Warner with Altium’s OnTrack podcast and Mike Carano of RBP Chemical. please join us again next time - until then - always stay OnTrack.
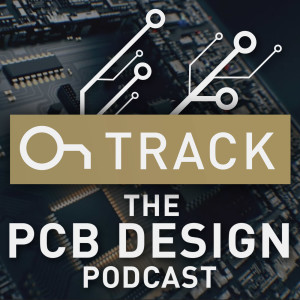
Tuesday Jun 12, 2018
Flex and Material Sets with Chris Hunrath
Tuesday Jun 12, 2018
Tuesday Jun 12, 2018
The rise in flex applications across all industries from medical to automotive, aerospace and military uses means more opportunity for material suppliers to innovate and meet demand. Here what industry expert Chris Hunrath has to share, from general guidelines for designing circuits unique for flex and materials that can be autoclaved over and over. Listen in to this week’s OnTrack expert to learn about flex and material sets.
Show Highlights:
- Medical applications (i.e. instruments for surgery), automotive, aerospace, military
- Foils - as you go thicker, its harder to make electrodeposited. More bend cycles out of rolled and yield
- General Guidelines for designing circuits unique for flex:
- In general, avoid circuits making turns or bends in bend/flex area - don’t make the circuits go in different directions there and also avoid plated holes in those areas.
- From a stackup standpoint, balance the construction. Thinner is usually better.
- Look for opportunities for cracking at the bend point.
- Cross hatch ground planes have multiple advantages.
- Pyralux HT, DuPont - new product with unbelievable thermal performance. A continuous operating temperature. Imagine a flex circuit that can be autoclaved over and over.
- We are a material sciences company. There are really unique ways to put these building blocks together.
Links and Resources:
See all the show notes
Hi everyone this is Judy Warner with the Altium OnTrack Podcast. Thanks again for joining us. Today we have another incredible subject matter expert that you'll be familiar with because we've had him here before, which is Chris Hunrath from Insulectro and we're going to talk about flex and material sets and all kinds of really great things. So hang tight for that. Before we get going please, I invite you to connect with me on LinkedIn, I share a lot of things there for designers and engineers and on Twitter I'm @AltiumJudy and Altium is on Facebook, Twitter and LinkedIn. Today Chris has some Show and Tell and so I encourage you if you - Chris will take time to describe what he's showing, but if you want to see it, feel free to go to our YouTube channel at Altium, click under videos and you'll see all our podcasts there. And you can click on this podcast and then you'll be able to visually see the materials and things that Chris is referring to today - and that's always available by the way - on YouTube so we record simultaneously in video and in audio so just know that's always an opportunity there for you.
So Chris, welcome back, thank you.
Thanks, Hi.
Thanks for joining again.
So at the end of last time's podcast, we were talking about the rise in flex applications and sort of the increasing amount of business actually Insulectro's doing around flex materials, new materials are going out so I really wanted to take this opportunity to learn about what is driving this uptick in flex, what applications are driving it , what the cost, performance implications of that is, and so let's just start with what is driving this uptick in flex?
So a lot of it's medical, you know, and the way electronics are finding their way into medical applications. Actually it's everything, it's automotive, it's aerospace military - military has always been a big user of flex, but of course you know, all the new inventions that are used in medical applications - certainly some devices are implantable and that's something that's not new, but then we're seeing a lot of applications where instruments are being created that are used, for surgeries and things and they use flex circuits and that's because you can make things very small which is always an advantage when it comes those applications and we're even seeing some applications where the products are reused. They're being sterilized, autoclaved, what have you and then they're being reused. But lots of new techniques, lots of new devices being developed using flex. Most people are familiar with traditional flex applications like your laptop screen, very often the interconnect between the main system and the screen is a flex circuit. You know the old flip phones all had flex circuits, your inkjet printers had a dynamic flex circuit between the printhead and the actual motherboard and the printer, and actually that's something I do want to point out is, you know we describe flex applications in two main buckets. One is dynamic flex and the other is the flex to install and it's just exactly what it sounds like is flex to install. Typically you're only bending the circuit once or twice to fit it in whatever it needs to go into and then that's it. Whereas dynamic flex, the part’s flexed in use many, many, many times.
I think that something that most people can relate to because you can see it, is the flex inside copy machines right, you can see that dynamic flex moving again and again and so are the materials - the entire circuitry is rated to have X amount of dynamic motions for the life of, it or how does that work?
Yeah actually that's a pretty good point and that can become very complex. A lot of it has to do with layer count, the base material. You know the most popular base material for flex circuits in reflow assembled PCB - a little different than printed electronics applications - where you're using conductive adhesive, but if you're doing reflow assembly, the most common material's polyimide film, and one of the most common materials is Kapton, but the thickness of the materials, the type of copper circuitry, the thickness of the copper foil - all those - play into a number of bend cycles even the type of copper, whether you use rolled annealed, which is very common in Flex, versus electron deposited-
Okay
-well that can get very complex. There are some good design guidelines out there by IPC and others you know. Again I always shout out to the board shops, some of them have good teams that help people choose the right construction, right stack up to get the most bend cycles out of the device.
Are those the two most common types of copper used in flex by the way Chris? Is a rolled anneal an electroless?
Oh it's electro- deposited.
I'm sorry electro-deposited okay.
Yeah - and yes but unless you're dealing with very thin foils rolled annealed is the most common. That's what we call 'RA foils' the most common. Actually I have a sample here. This is some Pyralux clad. You can't see the dielectric inside, but it's got rolled annealed copper on both sides and it can vary from - you used to be limited to half ounce or 18 micron and thicker so a little side note on foils: as you go thicker it's harder to make electro positive foils because it's more plating time on the drum. With rolled annealed it's the opposite, thinner foils are harder to manufacture because you need more rolling processes to make the foil thinner and thinner and thinner.
I see.
You used to be limited to 18 micron or half ounce, now we can get rolled annealed coppers thinner, down to 9 micron or quarter ounce. You can get a rolled annealed, but the structure is much better for flexing because the grain boundaries are in this direction platelet-type, overlapping grain boundaries which is better for bending. Any foil boundaries are like this and if you bend it you can cleave the grain boundaries in. You get more but it's not that easy - foil doesn't work and flex but you typically get more bend cycles out of rolled annealed.
Okay very good. That's something actually I didn't know and it's something I've talked to my friend Tara Dunn, who's in flex - and it's just something that's never come up so I think that's kind of an interesting point. So, you mentioned with military applications - because my background - military was always SWaP right, Size, Weight and Power - so are those the same type of things that drive the other applications - obviously in smaller spaces - we can fold things up on themselves and get them into smaller packaging. When you talk about the dynamic, what other kind of things sort of drive the desire and the fit for flex?
So something that's applicable to both military and medical, is you want to reduce the size, so I have here - this is a 50-ohm SMA coax right. It's basically one circuit, you've got the shield layer, the shielding around the center conductor - but this is one channel or one circuit and I have here flex, and you can see how many circuits you have on this piece. So, imagine if you had to have one of these - for each one of these-
For each channel right.
Now if you - depending on the design, whether it's strip line, micro strip, and whether or not you have in-plane shielding, it might be every other one's a signal. But still the weight and size is the difference between having cables right, which I'm holding up right now, versus having a flex circuit is huge right.
And in the case of medical, some of those traces can be as narrow as 20 micron. So you can fit a lot of circuitry into a very small space. And you know depending on the on the medical device. We see some of our customers will build circuits that are very, very long and very, very narrow, and you can imagine how they're used in surgery and other medical applications. And you might have twenty circuits on that part but it's in a very, very, very small space.
Oh that totally makes sense.
Now - just to be clear 20 micron circuitry - it’s not easy to do, it's doable, not easy to do, but certainly 50 microns is, most board shops can do that these days and again you can fit a lot of circuits in a small space and of course they can flex, they can bend. But in the case of rigid flex where you have a rigid part and bridged with a flex part - and here's another example where you have this - is not necessarily rigid flex but you'd have components here and then a connector here. You're replacing all these cables right, of this section, so that's how it drives weight and space and even reliability. Fewer interconnections tend to be more reliable so that really helps. So flex has been growing quite a bit for us, for our business and so, a lot of its based on DuPont Kapton and DuPont Pyralux products and then they - there's a B-stage system for laminating the different layers and of course the core, or the clad material as the foil on both sides and then our customers will print and etch to whatever pattern they need and put those layers together as building blocks.
Right so let's talk a little bit about design for flex since most folks listening here will be engineers or layout folks. What are some things that people need to keep in mind about designing these kind of circuits that's sort of unique to flex?
So there's a couple of good - again some good guides out there - both by IPC, DuPont has flex manuals, for different types of categories. Whether it's multi-layer, single sided, double-sided flex, they have some good guidelines on that, but in general what you want to avoid is you don't want circuits to make turns or bends in the bend area. So, for example, I'm going to use this one is an example again.
Okay.
If this is the flex area in this middle section here, you wouldn't have the circuits go in different directions in that area, so you might want to keep them. You want to keep them basically parallel in that area and you also don't want plated through holes in those areas. Again these are just real general rule - basic guidelines. The other thing you want to avoid is what we call an I-beam effect, where you have circuits directly above each other with a dielectric in between. You want to stagger them. That helps, again - more important for dynamic flex than bended, to install, but it's important not to have the I-beam effect because that could lead to cracks...
That makes sense.
-concentrates on bending. And in general from a stack up standpoint, you want to try and balance the construction. Thinner is typically better. There's again - there's all kinds of iterations there's - if it's a multi-layer flex - there's loose leaf constructions where you wouldn't necessarily bond the different layers together in the flex or bend region. You'd have them not connected. A bookbinder system is another way to do it where depending on the direction of the bend, the layers that are on the outside of the bend are actually longer. The layers on the inside - and again the fabricators that are skilled in that know how to space that - and to change the length of the circuit. But you know from a simpler standpoint, or from a more general standpoint thinner is typically better balanced. Balanced constructions are typically better for flex.
Well balanced construction is always a good idea, I'm just saying but I could see that right. Because I think you - what you're saying if I'm hearing you right, is you have to look for those opportunities for cracking right, or stressing at the bend radius, because that makes sense right. Just from a physics standpoint it makes sense that things would want to give or pull right?
Right, when you bend a flex circuit the other side compresses against it right, and every circuit will fail at some point. It's a matter of how many cycles you get out of it before it fails.
Right how do you measure those cycles by the way?
Well there are some standardized tests and there's an MIT bend test - there's some other testing that's done to see how a particular material, or even a design or stack up performs where it's bent repeatedly until you get failure. And then you can - you can rate the stack up or the and/or the material.
Where can you get that data? You mentioned IPC as a source. Is there any other thing - resources you could share - that I could share with the listeners where they could maybe look at some of these readings?
Yeah actually so DuPont's website, the Pyralux website, has some data on that and certainly some of the folks there could put your listeners in touch with some of the design guidelines.
Okay alright I know some folks there if you and I can't find him through the website then Jonathan just came in to talk at IPC designers Council Orange County I'll reach out to him see if...
Oh Jonathan Weldon, yeah he's a great resource for that. So speaking of Jonathan Weldon, he's been working with HDPUG; they've been looking at shield layers or for reference planes and they've been looking at the difference in solid planes and cross hatch systems, and so this is just a simple - this is actually a simple test circuit microstrip construction where you have a reference plane on one side and your tracer on the other. Imagine if there were a strip line construction and you had copper on both sides with your transmission line in the middle, one of the challenges with all PCBs, and especially with flex, is absorption of moisture and then that moisture released during assembly causing delamination and one of the things that you can do to mitigate that is to bake the parts. Well if you have soft solid copper areas - baking does not work as well - because the moisture has got to go around the copper it can't go through it.
Right.
So cross hatch ground planes are great for two purposes. One is, it's a moisture egress for baking, the other advantage is it's actually better for flexibility it makes the part more flexible.
Hmm, that makes sense.
The downside is the high frequency applications - you can run into some issues.
Yeah.
So and one of the interesting things that Jonathan and company, they were looking at, was the difference between a round opening and a - what's typically used as it's..
Kind of a diamond shape?
Exactly, exactly and really it's more of a square turned on its side, but yeah the diamond shape versus the you know... It's funny how a circuit design is always in orthogonal patterns but that's not necessarily the best way to go and anyway the round shape was better for signal performance.
Oh, for the high speed applications?
Yeah it makes sense because if you took a circle that fit inside a square you actually have less open area so...
This is true okay, alright.
Yeah, so there's some interesting data on that but I would recommend to a customer, depending on their their frequency bandwidth bit rate, depending on what kind of design it is, that they would look at using an open plane. It works basically with a screen, for lack of better words, versus a solid plane because the reliability goes way up.
Okay now you just made me think of something. Last time we talked, we were talking about prepregs and glass, being reinforced right. When you're using adhesive systems for flex, I'm assuming they're non-reinforced?
Right.
It's a more stable material though so tell us a little bit about that, about the stability, the dimensional stability?
Yeah so - so really in flex circuits the Kapton film, a polyImide film, because it's a thermoset, it is acting like the fiberglass in your flex circuit.
Okay.
You don't have skew issues because there's no glass, so you don't have micro-DK effects. Now if you do have a crosshatch plane, you will have a different - you'll have a micro impedance effect if you would. But that usually doesn't change with differential pairs unless - again depending on where you put the traces - but you don't have the fiberglass micro-DK effect at all. Now, Kapton's interesting - it's very thermally stable but it's not as mechanically strong as glass reinforced laminate. So it tends to change more from mechanical distortion than it does for thermal. It's not shrinking like epoxies do when they cure. Certainly when you - when you remove all the copper (and I actually have a piece here) this is a piece of Pyralux AP, with all the copper etched off. This is 100 percent polyimide, used to have copper cladding on it and the copper's been mostly etched off. You can see a little bit of copper left from the tape I use to run this through an etcher, but the material is pretty strong but it can distort mechanically, more so than thermally. So again this is kind of like the fiberglass in a regular PCB, and then you'd have B-stages of some sort, to put all the layers together.
So the actual substrate is creating the stability in the case of flex? Okay that makes sense.
It's a polyimide film, in the case of Pyralux, which is a DuPont branded flex material it's based on Kapton film.
Okay so we talked about ground planes, we talked about where to not put - - is there any other sort of design for flex things that you'd want to mention that are just rather commonplace?
Yeah so there's a lot of things, for example, you could use a pad that's a little bit larger than you would normally use that would go underneath the cover. Now let me backup a little bit and talk about cover lay. So what cover lay is, it's basically Kapton adhesive laminate, that is the flexible equivalent of solder mask. Now unlike solder mask which is used in PCB, which is photoimageable, cover lay has to be mechanically formed and then laminated over the circuitry. So you have openings and this - again this is a another good example - you have openings in the cover lay I don't know if you can see that on this? But there's openings on the cover lay for each individual pad and then that's laminated over. One of the ways to get more reliability out of the pads is to make the pad a little bit bigger than the opening in the cover lay. So you have cover lay over the perimeter of the pad - it's kind of like what we call solder mask defined pad and rigid - except you're doing it in flex, and that's that's one way to get reliability. But there - again there are a lot of different things in flex that you should be aware of, and that's where some of these design guides and things...
Okay well we'll try to track some of those down and put those in the show notes because I think that would be really helpful to have something kind of, tangible. Something I remember learning from someone else, is also talking about tear dropping pads?
Yes. Is that something that you would recommend as well?
Yeah that's good for a couple of different reasons. One is that the more material that goes under the cover lay, again helps mechanically support the pad. It's also important - typically you don't put holes or pads into your bend area, but it could be an area where you could concentrate bending. So in other words, you go from a trace to a pad, that's going to become a concentration of - right at the edge of the pad - concentration of stress and so if you do the teardrop, that distributes that stress over a larger area and helps prevent circuit cracking. But again, you would try and avoid that in your design. We would make that a bend area. And actually, speaking of rigid flex, one of the things that you would typically do is the cover lay would go into the rigid portion only 50 mils.
Okay.
-Okay and then you would keep the cover lay and its adhesive out of the plate through hole areas in the rigid portion and rigid flex - and that's also a 'keep out' region for plated through hole so you wouldn't want plate through holes going through that region. So again a lot of this stuff is spelled out in some of the manuals that you get from DuPont and others.
Alright, I'll reach out to Jonathan and - and you and I can scrounge up some things and we'll make sure to include those here. Last thing I wanted to talk to you about - which I was just stunned by - is that you told me that DuPont has come out with a new material that has unbelievable thermal performance. Can you tell us a little bit about that?
Yeah so - classically in flex, you have your your B-stage, or adhesives that are part of the package, and then you have your core materials, which are your building blocks and you print and etch your core, just like rigid, and you would have - you would put them together with either your rigid or your flex adhesives to make a multi-layer system. What's different about this new product, it's called Pyralux HT, and in fact, I got my Pyralux HT mug here...
Nice, nice.
-but instead of using acrylic or epoxy adhesives to bond the Kapton layers together, you would use this thermoplastic polyimide layer. It's got a very high melting point and thermoplastic's already used in PCB, people familiar with EPI-P and LC, those systems. The only way thermoplastics work in PCB, or reflow assembled PCB, is to have a high melting point otherwise it would melt at assembly. So this is a piece of the thermoplastic polyimide that DuPont manufacturers. It's the HT bonding film. This could either be a cover lay or it could be an adhesive layer to put - to make a multi-layer PCB.
Okay.
-But the nice thing about this, is it has a - 225 Celsius operating temperature, which is very, very high.
What does that convert to in Fahrenheit?
Oh gosh - 225 C it's over 400 degrees Fahrenheit.
I see, 225 - - Fahrenheit okay I wasn't hearing you correctly, so it was Fahrenheit okay.
Oh no - hang on, 225 C, I should know all this without me - - 437 Fahrenheit.
Wow.
So you know, some applications...
-and that's an operating - continuous operating temperature? Which is crazy, cuz some materials can take that heat for a little while but not continuing operating temperature right?
Right, so most PCB materials that go through a reflow assembly, which is either done at 260 Celsius, depending on the type of solder work, or 288 C, they can withstand that for a short period of time most PCB materials survive that. It's the operating temperature most epoxy systems will come in around 130 to 150 C operating temperature - maximum operating temperature.
That's wild, so I'm guessing - so what are the applications where this will be exciting news?
So applications where you had, fiberglass, coax or some other applications like that where you had wired - high temperature wired connections - or cable connections, you could replace now with a printed circuit board. So engine compartments, aircraft engine compartments, aerospace, down hole, I mean there are a lot of different applications. Even from a medical standpoint. Imagine making a flex circuit that could be auto plated over and over and over again. You don't have to worry what's gonna...
I was gonna ask you about that earlier. I don't really know what temps they autoclave at but you mentioned that before that medical applications could - to cut autoclave to kill the bacteria, but like what's the normal temp of an autoclave, how many times can you do that?
So we have one customer that builds some parts that are autoclaved at 135 C but it's with steam, and it's hard on circuits, it's hard on electronics.
Yeah seems like that would be.
But for HT it wouldn't be any issue because you're nowhere near on the melting point. Now it will absorb some moisture, which could be removed from - could be removed with a bake but a lot of applications it won't matter if the assembly is already done. It doesn't really matter.
Okay.
You know there is some change in the transmission properties of the material when it absorbs some moisture. Again that could be removed with a bake but that is one of the challenges with reusable medical devices, is sterilization and how well the materials hold up, and an HT would be good for that. The downside of HT, is it does require a 600 degree lamination - Fahrenheit.
Okay well there you go, so how many board shops have lam presses that go up to that temp?
So we took a look at our customer base, and it's not a lot of them, or some of our customers had laminate, or have lamination presses that are capable, they're rated that high, but they haven't been turned up that high for a long, long time. So it's funny, some of our customers have started making some HT, all the weaker heaters, that the press might be 10 years old, they turn it up for the first time to a higher temperature; they start popping heaters and they have to go and replace them. But actually we're seeing a trend though. A lot of our customers are buying laminating equipment and right now that's a whole 'nother story because lean times are way out on equipment in general, but what we're seeing is people are making sure they have that high temperature capability and it's not just for something like HT, it's for LCP and FEP as well.
Okay.
They have some good properties, electrical and and signal properties.
They do.
That's a big deal these days.
Performance wise they're very good.
Right they're harder to fabricate but they do have some good properties you know. Even - we talked about last time - repeat glass-reinforced PTFE materials, some of them require high lamination temperatures.
Yeah they do.
Yeah all right. One more material I do want to mention - sorry - so this material actually is a Teflon Kapton laminate it's called...
-wait hold on - Teflon Kapton? Oh okay.
It's called 'TK' - it's a Pyralux product from DuPont and so it has a core of Kapton to act as the XY stabilizer, but then it has a Teflon material on both sides and again, this is a building block but it's very low loss, and very low DK. So a DK of about two and a half with a very, very low loss. But unlike glass reinforced Teflon systems, this has no fiberglass so, no skew and no detrimental effect from the fiberglass. It's using the Kapton instead, as the stabilizer, because if you had a piece of - I should have brought out a piece of Teflon - but PTFE films you can easily - it can be mechanically stretched.
Yeah, one time when I was in the RF and microwave board space, I had the board shop I was working for take all the materials like Rogers, Taconic, whatever and I had them strip all the copper off and I went like the 4000 series 6000 series 3000 series all the way up to 58, 80 and strip off the copper. Because when you see them clad, they don't look that different from each other. But I'm like here's Teflon - this is like a piece of rubber, and imagine heating that up, exposing that to aqueous hot processes and so I think that really helped people to understand how vastly different they are and I think it was a good visual actually to help people understand how radically different these are and when you start stripping off all the copper and you have fine lines and all that then it's - it's a whole different animal.
TK material is - the core material is nice because the Kapton layer does provide mechanical strength. Again though, the TK, instead of requiring 600 degree lamination, it requires 550. So it's still a high temperature product which requires the right press book, the right materials, and lamination, and it also requires a press being capable. And the other too is the board shop needs to get accustomed to the dimensional changes during the lamination process with these materials.
Right.
Again - a lot of it's mechanically driven, but you need to know how to work with it so that's something I think the boardshop needs to have experience with.
Well and I imagine that you're not going to see these materials outside of sort of high performance or high speed capable board shops?
That's true...
-I don't know if that's true I guess I'm looking to you for an answer in there but it's an assumption I would make.
Here's the interesting thing about AP, AP by itself, is actually pretty good electrically. It's the adhesive layers you use that incur a lot of the loss. So then if you get into the thermoplastic systems that have better electrical performance, now you're getting into the temperature range. So it's one of those give-and-take situations, but you can mix and match the materials to some degree. You could use, for instance HT bonding film with AP clads, your operating temperature would default to the AP operating temperature, which is still pretty high at 180 °C, but electrically it's pretty good. You get away from the acrylic and the epoxy adhesives, which aren't great electrically, in terms of loss, dielectric constant so yeah, I think as I think as board shops become better equipped with high temperature systems, you'll see a broader use of these materials.
Right, I mean the market is going to drive us there one way or the other right, if there's a demand then the board shops will do what they need to do. One thing - a comment I want to make about that is - I was in one board shop and I was stunned and then just felt like wow I could've had a V8 moment, is they were providing really high speed, high performance circuits to some high-end military stuff, and they had moved completely away from rigid high performance laminates and used multiple layers of flex materials and the performance - and I'm like - oh well that seems like an obvious, but I had no idea that was even happening. Is that something you have seen, where they just use...
Yeah, if you wanted to get rid of skew completely you could use a film based system.
Yeah it was crazy, I mean that makes sense and I'm sure there's some challenges there cuz I could tell they had to rigidize the bottom, or put some kind of carrier or something, because they didn't want it to flex quite that much but they just stacked these film systems on top of each other and I'm like huh, didn't know you could do that but they were clearly doing it on a routine basis so that was interesting.
Yeah I've seen some board designs where you might have 12 cores of Pyralux...
Yeah,right.
-and then use regular rigid prepreg as a bonding system so and the board's not - when it's all done, it's not flexible it's rigid.
It is rigid, but it's a weird - it's weird to see anyway...
I actually have a board here.
Ok let's see it.
Unfortunately it's single sided so it's kind of like a potato chip, but because there's only one layer of copper and one layer of prepreg, but this is actually DuPont's AP product with Isola's tachyon prepreg, and it's a spread glass prepreg. So you have the spread glass prepreg on one side and you've got the Pyralux AP in the other. So you minimize how much glass is in here, which really drops the amount of impact or micro DK effect which would lead to skew and other signal performance issues. So there are lots of different ways you could use the flex materials even in a rigid design.
Yeah I did see that and I was shocked and I - it's something I hadn't heard a lot about. Anyways well, we're about out of time today, again. But thank you so much, every time I talk to you, I feel like I learned so, so much and it's fascinating to me where the industry is going and what's happening with flex and it's exciting it's really an enabler right and these high, high temp products and that so it's a really exciting time to see. We always break through one way or another it's just interesting to see who gets it done. So it's very interesting to see what we're doing with flex.
Oh thank you Judy for giving us the opportunity to talk about some of the materials we supply but yeah it's - these are all building blocks and, I kind of view it as a material science company in tech...
You are yeah.
-we provide all these different building blocks to meet the need of what the customer needs.
And there is - and there's really unique ways to put those building blocks together so it's fascinating to learn about. Ok so something I didn't ask you last time, but I'm gonna ask you now. Are you a geek or a nerd? [Laughter]
So the best way I heard the two described is the difference between a geek and a nerd is - a geek is the one who gets things done.
Oh interesting okay.
So I would like to think I'm somebody who'd get stuff done, so that would put me in the geek camp but in any case.
Alright check geek, and the second question I have for you: on a scale from one to ten how weird are you?
[Laughter] Oh gosh, I would say - five.
I'm sorry but if we're in this industry we're at least 5 or above. I think we have to be a little wacky to do what we do - okay well thanks I appreciate it so much and again, we were talking on the phone yesterday we have more to cover, so I'm gonna for sure have you back again and talk about printed electronics which is on the rise and you know a lot about. And also I'm very excited to talk about - oh there it is!
Electronics, that's a whole other - whole other world of electronics and yeah.
Wait, wait, wait bring that back and tell our listeners what exactly that is.
So this was printed with a zebra label printer where the - and no changes to the machine by the way - but the special foil is put into the system where you normally put a roller with a pigment film, so instead of printing a black label you're printing metal foil so yeah, it's kind of interesting.
Yes what is that for?
Well this is something did for me at our booth this is just an antenna but you could really you could make electronic designs on the fly now...
Dude, you're still not answering my question here. What is that intended for?
So I'm gonna use that for an antique stereo I have. I have an antique FM stereo the tube, old tube radio, I'm going to use that as an antenna.
I see - oh see definitely five-weird. I say I'm gonna make that matrix instead of the hot crazy matrix I'm gonna make like the geeky-weird matrix and so yeah - you're at least at a five -high and a geek.
But anyway printed electronics is pretty exciting, I mean and again, it's all material science based. As the materials get better you're gonna be able to do more things. Higher conductivity inks, higher temperature inks, I mean there's all kinds of things you can do in that area. Typically the substrates are different - they're typically lower cost, lower temperature capable substrates, but you could - you can make all kinds of things so we'll get it the next time.
Okay we'll definitely do that and the other thing I'm excited to talk to you about - because I know nothing about it - is paste interconnects and you shared a little bit, so anyways we have at least one or two more podcasts ahead of us, so for our listeners; stay tuned and we'll make sure and share everything Chris has talked about today and hook you up with resources through DuPont, HDPUG, IPC, wherever we can find and we'll make sure and share those resources that will help you lay out a better flex and onboard as much information as you can.
So Chris, thanks again, we'll see you next time and we'll tackle another hot topic. Again this has been Judy Warner with the OnTrack Podcast. Thanks for tuning in and thank you to Chris Hunrath from Insulectro, we will see you next time. Until then, always stay on track.