Episodes
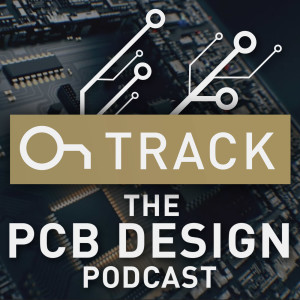
Tuesday Jan 14, 2020
Signal Integrity Evangelist Eric Bogatin, our Expert Insider to DesignCon 2020
Tuesday Jan 14, 2020
Tuesday Jan 14, 2020
Signal integrity expert, Dr. Eric Bogatin, joins us in this episode to talk about the upcoming DesignCon conference and expo that will be held in Santa Clara, CA January 28th through January 30th. Dr. Bogatin shares information about the presentations he’ll be giving; this includes a 2-part S-Parameter master class, speed training about understanding TDR measurements, and a session tackling tricks the experts use to get more out of their oscilloscopes, just to name a few. Listen in or watch the full episode!
Check out the show highlights below for some excellent free online design resources on the SI academy website and all the sessions from this year’s AltiumLive.
See What's New in Altium Designer
Show Highlights:
- Eric explains ‘Rule #9’.
- To add more value while on the expo floor at DesignCon, ‘speed training’ will be available to everyone. These are short, fun, and informal presentations covering one topic or demo. All speed training sessions at DesignCon are free.
- Four of the world’s experts in signal and power integrity—with 150 to 200 years of collective years of expertise between them—will be on stage together in the ‘Stump the Experts’ panel: Steve Sandler, Istvan Novak, Vladimir Dmitriev-Zdorov, and Larry Smith. Be sure to bring your questions and problems to this discussion.
- Every six months there is a printed version of the Signal Integrity Journal. The latest edition will be distributed at DesignCon 2020. The cover article, ‘The Myth of Three Capacitor Values’, reveals the origins of this design rule for decoupling capacitors, and why it no longer applies.
- On Thursday, Jan 30, an expert panel will untangle the countless digital communication standards. This panel discussion will be of great value to those working with high-speed serial links.
- Also on Thursday: the Career Zone Session will be an excellent opportunity for young engineers to obtain guidance on the fundamentals of starting out in this industry, followed by networking and individual coaching sessions.
- Eric will also do other speed sessions/demonstrations to increase your understanding of TDR (time-domain reflectometer), and S-Parameter measurement for differentials without a return path.
- Those unable to attend DesignCon, please take advantage of the Signal Integrity Academy hosted by Teledyne LeCroy. It features a vast collection of free best design practices for signal and power integrity, plus best measurement practices, illustrating four essential principles, including Rule #9.
- You will also find a series of webinars on the Signal Integrity Academy about the correct usage of a TDR, plus a series on their new network analyzer.
- Eric has a new book on transmission lines in the works, which will be available soon from Artech.
- Teledyne has a new high-performance, low-end scope that is also very low-cost. Look out for his presentation, ‘SI/PI on a Budget: Five Tricks to Get More out of Your Oscilloscope’ at DesignCon (also coming to various other venues in the coming months).
- Be sure to watch the video recordings of Eric’s talks at AltiumLive 2019: ‘Mastering the TDR in 45 Minutes’ and ‘Breaking Bad: A Downside of Open Source Designs.’
- Remember to like, subscribe, and tell us what you want to learn about!
Links and Resources:
Signal Integrity Academy
DesignCon 2020
Signal Integrity Journal
Sign up for Print Version of Signal Integrity Journal & Free Newsletter
Career Zone Session: What’s Next? How to Jumpstart Your Career
New this year, the DesignCon Career Zone
Mastering the TDR in 45 Minutes, Eric Bogatin at AltiumLive 2019
Breaking Bad: A Downside of Open Source Designs, Eric Bogatin AltiumLive 2019
Artech House Publishers (technical book publisher that will publish Eric’s book soon)
Teledyne LeCroy’s TDR and S-Parameter Equipment
See What's New in Altium Designer
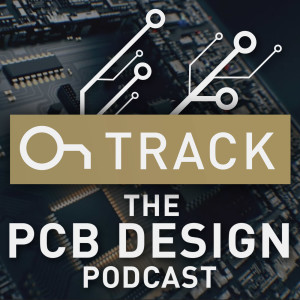
Tuesday Jan 07, 2020
Explore Arduino now Expanded and Updated by Jeremy Blum
Tuesday Jan 07, 2020
Tuesday Jan 07, 2020
See What's New in Altium Designer
Happy New Year, and welcome to the first Podcast of 2020 with OnTrack. In this edition, we shine a light on one of our design community’s brightest stars, Jeremy Blum. Jeremy is a two-time AltiumLive keynote speaker and has also been featured on this podcast twice. He’s recently released an expanded and updated edition of his book Exploring Arduino, which he originally wrote in 2013. Enjoy a few clips to get to know Jeremy better.
Show Highlights:
- Jeremy shares more about the work he does as the Head of Engineering at Shaper Tools
- Is Jeremy a prolific geek, or is he a nerd?
- More about Jeremy’s YouTube channel
- Jeremy’s first job out of university was at Google, where he helped co-develop Google Glass
- More about the updated and expanded edition of ‘Exploring Arduino’
- We are giving away two signed copies of Jeremy’s book as a thank you for the input we receive from our users. Let us know what you’d like to learn about, and who you’d like to see on the OnTrack Podcast in the year ahead.
Links and Resources:
Exploring Arduino Hard Copy
Exploring Arduino PDF
Jeremy Blum YouTube
Want to qualify to win one of two signed copies of Jeremy’s book, Exploring Arduino? Please comment on social media using the hashtag #OnTrack Podcast and let us know what people or topics you would like to hear featured on the OnTrack podcast in 2020.
See What's New in Altium Designer
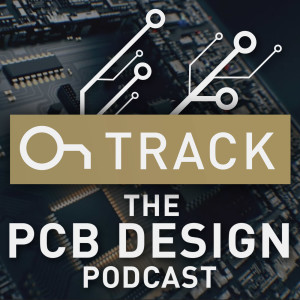
Tuesday Dec 17, 2019
Ben and Judy 2019 Wrap-Up
Tuesday Dec 17, 2019
Tuesday Dec 17, 2019
Welcome the year-end wrap with Ben Jordan, where we’ll discuss routing engines, RF and microwave and high-speed design, and how they differ. We’ll talk about signal integrity, and discuss what 2020 and beyond will hold for design. And lastly, we’ll share some resources and links as our holiday gift to you.
See What's New in Altium Designer
Show Highlights:
- The recent launch of Altium Designer 20® is getting a great response, and one of the most well-received features seems to be the routing engine—specifically the any-angle routing feature.
- Technically, with previous Altium Designer versions, you could place a trace at any angle, but it involved numerous clicks. And the response to our question ”Why don’t we design at other angles?”, was, once laid down, you couldn’t edit traces any further. That’s the real crux of it.
- The key update to Altium Designer 20 is, now we can have beautiful, flowing traces with tangential arcs—tangential to the trace they come from—and concentric with the object they’re clearing. The real key here is being able to edit after it’s laid down.
- It takes a lot of time and groundwork to build the algorithms, and it takes a lot of math, testing, and time to build libraries to do things elegantly.
- Interviews with users revealed that people weren’t using the simulator and there was a need for improvement.
- With Altium Designer 20, you don’t have to leave the comfort of the schematic environment that you know (which saves time), and the simulation is very fast. One of the themes of the next major release will be virtual prototyping and simulation.
- With the explosion of the IoT market, not everything is necessarily digital and there’s a lot we’ll have to learn. The design process is exceedingly complex and becoming more so.
- The complexity is not in the manufacturing of the board (other than tolerances). The complexity is in the design.
- Don’t let complexity fool you into paralysis—just get started. Ben Jordan’s talk, ‘The Absolute Beginner’s Guide to RF Design’, is a great resource. Ben will be presenting the talk again at Design Con, January 28th-30th, 2020, at the Santa Clara Convention Centre, and again at the IPC Apex Expo, February 4th-6th, in San Diego.
- Q: “RF and microwave are not high-speed, but typically high frequency. Then there’s high-speed digital and high-performance: what does it all mean and what’s the difference?” A: “High performance refers to anything that does its job exceptionally well, but is not necessarily high-speed. High-speed digital does boil down to frequency in current technology. The signals we’re dealing with now are very high-speed digital, meaning we’re using a higher ‘clock-rate’ (sending more bits of information in less time). The actual speed of a signal in a PCB is where frequency comes in—it’s not clock time, but rather a microwave frequency”.
- The formal partnership between Simberian and Altium brings an accurate tool for considering all the materials in the layer stackup and the way boards are made, generating a very accurate impedance profile for the traces on the board. This tool works whether you have a high-speed digital board, or an RF board with microstrip transmission lines over Rogers material on the outer layer.
- The actual delay calculation in Altium Designer 20 comes from Simberian’s static field solver.
- Rick Hartley’s comment at AltiumLive in Frankfurt was very encouraging: “...happy that Altium is doing tune for delay, because that’s the way to do it, rather than length tuning”.
- Altium now has a dedicated development team for simulation, routing, and schematics, paving the way for future enhancements of the user interface.
- Altium has launched something new and exciting: a video series called ‘Altium Stories’ that just tells your stories! Go to YouTube and find some stories now—Ben’s favorite is the Vox Story.
- The blog by Mark Harris, ‘Geeky Holiday Gift Ideas’, is an amusing read to end the year on a fun note.
- All the AltiumLive sessions are now online.
- As we head into the new decade, PCB designers can look forward to routing boards being faster and easier, can expect more long-awaited automation, more boards in bizarre places (such as wearables, exoskeletons, precision agriculture), and much, much more.
- The role of the PCB designer will change, but it won’t disappear. The newest generation entering the industry will have to be more holistic than previous generations of engineers.
- Finally, thank you to our listeners for making this year a great one for the OnTrack Podcast.
Links and Resources:
Altium Designer 20: Any angle routing
DesignCon
IPC APEX
Altium Stories + VOX Amplifiers
Geeky Holiday Gift Ideas - Blog by Mark Harris
AltiumLive 2019 Session Links: San Diego
Sarcos Robotics
Altium365
See What's New in Altium Designer
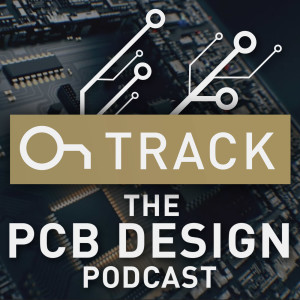
Tuesday Dec 10, 2019
Simberian’s 3D Field Solver in Altium Designer
Tuesday Dec 10, 2019
Tuesday Dec 10, 2019
Simberian makes a physics-based 3D field solver tool that helps measure not only the traces on your board but also the materials. Altium recently entered into a formal partnership with Simberian, and Roger Paje - VP of Global Marketing, discusses with us how this impacted Altium Designer® 19 and 20, and what’s we’ll see going into Altium Designer 21 and beyond.
See What's New in Altium Designer
Show Highlights:
- Roger started his career in EDA at a startup in the signal integrity and timing space, called Quad Design, which was eventually acquired into Mentor Graphics. He left EDA for the telecom market and worked on embedded designs for a while. He’s now back in EDA, and the last two companies he worked with used Altium Designer.
- According to Roger, Altium’s recent partnership with Simberian embodies the synergistic principle that in the business world, “one plus one equals five”.
- Given Simberian’s background and its contributions to the field since its founding in 2006—its contributions to electromagnetic theory, its multiple case-studies, its rich history of exercises with partners on algorithm validation, and its large library—it is apparent that Simberian is heavily focused on electromagnetic analysis and getting it correct.
- According to Roger, marrying the above “to a PCB tool with a bunch of users… just seems like an extremely logical decision”.
- Altium Designer 19 saw the first inclusion of Simberian features, starting with their field solver in the stackup manager. This ensured more accurate impedance calculations on the different layers. While Altium Designer 19 was just a starting point for these features, 80% of users were able to use the field solution and impedance calculations to their benefit.
- The field solver is extremely accurate and essential for the frequencies that users are now moving toward, and the material loss parameters are included in Altium Designer 20.
- Material measurements are becoming more important with high-speed design.
- Considering roughness factors and the characteristics of dielectrics; once you get into higher frequencies, 3 GBps is the inflection point at which loss characteristics of the materials come into play—if those aren’t modelled properly, it introduces simulation inaccuracies.
- If board manufacturers do not provide characterization and data, both in pre- and post-manufactured cases, analysis becomes almost impossible.
- The current collaboration of EDA vendors with designers and material manufacturers makes the industry more complicated than a couple of years ago.
- With the Altium Designer 20 release comes more robust geometries for those moving into more exotic materials and geometries. There are also a few algorithmic enhancements. Some characterization exercises revealed that the impedance numbers coming out were measurable.
- Most of our regular users are in the realm of transition, moving toward DDR-3, DDR-4 and onward, or any of the surreal interfaces, PCI Express, Gen 2 or -3, moving up to Gen 4.
- The practical impact and importance of Altium Designer 20 to PCB designers will be, accurate impedance and delay calculations. Even at DDR-3 skew is a big deal and as you go higher, even more so.
- As designers move toward high speeds, proper impedance modelling is important and we have a lot of confidence in Altium Designer 20 for that with the field solver.
- Designers will always benefit from knowing their Electrical Design Rules. The layout tool itself is able to find things that impact signal integrity. Some of the design rule checks in Altium Designer 20, particularly the return path checking, will ease the job of analysis.
- Designers will need less hard-core training to read modeling results and know how to interpret them with the more intuitive nature of Altium Designer 20.
- The future of the Simberian/Altium partnership already has a couple of philosophies in place, one of them is making the analysis easier. There are also plans for a trace checker, similar to a word processor’s spell checker.
Links and Resources:
Introduction of Simbeor® Electromagnetic Signal Integrity in Altium Designer 20 (in Altium Designer 20 User Manual)
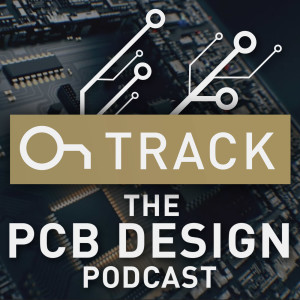
Tuesday Dec 03, 2019
Patrick Züger Talks About the Altium Designer 20 New and Exciting Features
Tuesday Dec 03, 2019
Tuesday Dec 03, 2019
Patrick Züger from GPV Switzerland, a massive fabricator and assembly facility across Europe and China, delivered a great talk at AltiumLive in Europe. He shares his feedback and design process with and as an Altium Designer® Beta User. We discuss his initial impressions of Altium Designer 20.
Trade In Your Outdated PCB Design Tool & Unlock Savings on Altium Designer today!
Show Highlights:
- As a CID+ Hardware/PCB designer in a global EMS company, Patrick sees many PCB designs and has created a workflow for Altium Designer, which he presented at AltiumLive in Europe.
- Many EMS companies have brought in designers to work alongside Project Managers. This close collaboration with the production side has vast benefits in production and assembly.
- GPV has approximately 4000 employees worldwide with locations in Mexico, Europe, Asia, China, Sri-Lanka, and Czechoslovakia. Most sites are for manufacturing, with the biggest one in Sri-Lanka, plus two engineering facilities in Switzerland.
- As one of the ten biggest manufacturers in Europe, GPV produces numerous products, from medical to consumer electronics and industrial products.
- There was excellent feedback and interest in Patrick’s workflow template which he is sharing freely.
- Patrick has been an Altium Beta user for seven years—the most significant benefit to which is being close to the developers and seeing his ideas implemented.
- Q: “How would you describe the significance of Altium Designer 20 compared to other releases?”
- A: “It is a refinement of Altium Designer 18 and the new concept of Altium. New features such as the updating of the routing engine, new schematic render, and dynamic compiler are important.”
- Q: “How long have you been using Altium Designer 20 as a Beta User now?”
- A: “About six to eight weeks.”
- Q: “What are the top three improved features?”
- A: “My favorite is the routing improvement. It’s much easier to move around different tracks and rearrange them, making the work proceed much faster. Next favorite is the dynamic compilation, and also something I’ve waited for a long time is the creepage rule—I was very happy to see it.”
- Q: “What do you think about the stability of Altium Designer 20?”
- A: “Even in Beta, I feel it’s very good, very stable, and I already use it for small designs.”
- Q: “Give us five words that describe the interactive routing.”
- A: “Impressive, intelligent, fast, forward-thinking, and smooth.”
- Q: “How would you compare the interactive routing of Altium Designer 20 with any other tool you’ve used in the past or present?”
- A: “That’s difficult to answer because I only use Altium Designer - for me, it’s the best tool.”
- Q: “What is the number one quality that helps your design flow and workflow in Altium Designer 20?”
- A: “For me, it’s the clean up of the component properties panel in the schematic, the overview is much better now.”
- Q: “What is the number one time-saving feature in Altium Designer 20?”
- A: “The efficiency of the new routing engine, before I’d have to delete all tracks and start over, but now I can rearrange them.”
- Q: “What do you feel has not been addressed, that we should address?”
- A: “The outshop files where you configure your settings to get the data out haven’t had much done to them for some time, and I think there’s room for more efficiency and automation.”
- Q: “How significant do you think the tune for delay feature is, and does that impact you?”
- A: “It does not affect me directly as we don’t have many high-speed designs, but it makes much more sense.”
- Q: “With the release of Altium Designer 20, do you think there’s any type of board that our tool cannot address?”
- A: “No, I don’t think so. Maybe one area is with huge boards, where Altium Designer does tend to be a bit slow, but Altium Designer can handle any normal design.”
- Q: “What top three features of Altium Designer in general, sets it apart from other design tools?”
- A: “The 3D capabilities, the ACTIVEBOM® with the manufacturer part search, I love that feature. It’s awesome, and of course the new routing engine.”
- Q: “You say you grew up with Altium Designer, but you have a choice what tool you use, what keeps you choosing this tool over others?”
- A: “Firstly its ease of use, the 3D capabilities, the beta program, the big community, for example, all our educational institutions use Altium Designer. I think it’s the best value for money, and very importantly Altium listens to their users.”
Trade In Your Outdated PCB Design Tool & Unlock Savings on Altium Designer today!
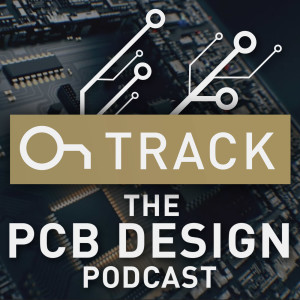
Tuesday Nov 26, 2019
TE Connectivity Paving the Way into 100 GBps Data Rates
Tuesday Nov 26, 2019
Tuesday Nov 26, 2019
Trade In Your Outdated PCB Design Tool & Unlock Savings on Altium Designer today!
Show Highlights:
- Justin has been with TE’s high-speed data development group for 11 years, and as the Principal Development SI Engineer, develops high-speed products—both connectors and cables for use in the data center market.
- Nathan is a technologist on the system architecture team responsible for managing their industry standards efforts. He’s been with TE for what he calls “an embarrassing 38 years”.
- Between 2014 and 2018, the industry standard for high-speed connectivity rose dramatically; from 25 GBps to 50 GBps, with the estimated launch of 100 GBps in 2021. A major factor driving these improvements is demand—such as the many ways people are using data (for example, ‘killer apps’).
- A vast range of technological challenges arise due not only to increasing speed but also due to heightening bandwidth but also density.
- There’s a high demand for higher-speed products which have to function at higher frequencies and send more data per unit of time, so more channels, systems, and actual bitstreams must be packed into the same space.
- With increasing data rates come new sensitivities to impairment or signal degradation. This problem manifests itself in the form of insertion loss: how far you can send the signal before it’s lost?
- Within a connector or PCB, transitions occur from the connector to the PCB or from one layer of the PCB to another, and those transition structures increase loss by introducing reflections that cause a loss of signal, affecting reach even further.
- Another problem with higher data rates is crosstalk. With multiple channels, each sending data while sitting side-by-side, one creates noise for the other.
- Density issues also come about as the data rate increases—silicon providers are increasing the number of transmitters and receivers they can put into a device, which requires higher density, and again, creates more crosstalk.
- At the PCB level, there’s usually an active device sending a signal to the PCB trace, which is a significant electrical length, and although copper is a great conductor, the actual printed material is lossy, and there’s a migration to different laminate materials as well as smoother copper.
- With the notable trend towards smaller via holes, the structures themselves are both low in impedance, which creates extra reflections as well as electrical noise or crosstalk.
- TE understands the market trends of laminates and how they can interlock different technologies and use the advantages of materials to provide higher density and higher performing interconnects.
- Different modulation techniques are also required; not only to push the bandwidth at which a device functions electrically, but also to create an even lower crosstalk profile. All of this requires considerable optimization at the PCB level.
- To address these seemingly insurmountable challenges, TE is constantly upping their game in human resources and the tools they use in concert with industry ecosystem partners who provide board layout tools and powerful signal integrity modeling tools.
- On the board side, the next-gen materials are moving toward an EPO resin with a dielectric constant of around 3 and lower loss.
- The movement in connectors is toward a different family of plastics. Instead of PCB-type laminate materials, injection-molded thermoplastics are used, such as high-end engineering polymers like LCP.
- On the metal side, high-performance copper alloys that are very springy are applied to create a denser interface.
- Different extrusion technologies are used for cabling to increase reach and density while minimizing loss.
- Products that are helping solve problems en route to 100 GBps are: internal cabling assemblies (instead of PCB routing) to overcome loss, new interconnect technology and much more.
- This podcast’s takeaway for the industry is that the robust solutions will exist and TE will help with the introduction. Things are going to change whether it be removing traces in favor of cabling or overcoming thermal problems. Get ready for 100 gigs, it’s coming and it’s going to work!
Links and Resources:
- Connectivity System Challenges of Next-Gen I/O Paper
- Delivering 100 Gbps Solutions for Chip-to-Module and DAC Paper
- STRADA Whisper Connectors Landing Page,
- STRADA Whisper Connectors Routing Guide:
- STRADA Whisper Connectors: Beyond 25 Gbps Whitepaper
- Cabled Backplane Systems: The High-Speed Alternative to PCBs Whitepaper
- Sliver Connectors & Cable Assemblies Landing Page:
- Sliver for SFF-TA-1002 Video
- Data Center Solutions Landing Page
- TE at DesignCon 2019 Highlights (includes all demo videos)
- High-Speed Pluggable I/O Connectors & Cages
- High-Speed Pluggable I/O Cable Assemblies
- 400G I/O Connector Landing Page
- LGA Sockets Landing Page
- XLA Sockets Product Flyer
Trade In Your Outdated PCB Design Tool & Unlock Savings on Altium Designer today!
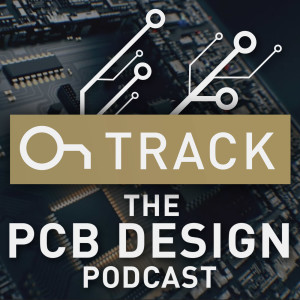
Tuesday Nov 19, 2019
Saving Time Routing in Altium Designer 20
Tuesday Nov 19, 2019
Tuesday Nov 19, 2019
Mark Ross is a long-time Altium Beta user and our guest in this podcast episode to share his insights and the value he gets from being a Beta user. He also chimes in on a long list of questions about what he thinks of Altium Designer 20. He gets into the details on this latest release of Altium Designer and what sets it apart from other eCAD packages, the most significant new feature, and - are there any designs the tool can’t handle? Listen in, read the notes, or watch the video below to find out.
Trade In Your Outdated PCB Design Tool & Unlock Savings on Altium Designer today!
Show Highlights:
- At age seven Mark took apart his first CB radio, setting the tone for what would become a lucrative career. He has now been designing circuit boards for 32 years. Beginning with Protel Easytrax, he progressed and moved on to other tools. When Altium acquired Accel in 2000, Mark moved over to Altium Designer®, which he has been using ever since.
- Mark has been designing power products for Progressive Dynamics, the market leader in RV Power conversion, for almost five years. Before joining their team, their products were exclusively through-hole technology, and he was in charge of converting everything to surface mount.
- Some of their challenges were directly related to 3D capability, and Altium was extremely helpful with component collisions and UL spacing.
With the help of Altium Designer, Mark designs a new circuit board every two weeks and does a product revision once a week. - Q: “How long have you been a Beta User for Altium?”
A: “Since 2015, and I am a firm believer in it. I believe there is a big disconnect with CAD software users in general, but Altium gives me the opportunity to provide feedback.” - Q: “How has that experience been for you and what benefits do you see in keeping at it through almost five releases?”
A: “Firstly, employability—things change so rapidly, you have to stay updated. Also, when our company starts using the latest update, I can help my colleagues, which is very beneficial.” - Q: “You’ve worked with Altium Designer well in advance of its release, what is your honest opinion of the significance of Altium Designer 20 compared to some of our previous releases?”
A: “Well I was one of the vocal guys stuck with Altium Designer 17. I did Beta on AD18 and 19 but just couldn’t afford to take the time to learn the new tools fully while also doing my work. When I started using AD20, coming from 17 to 20, 97% of the time, I don’t notice it anymore, the user interface is much smoother and the ease of use is back.” - Q: “What are your top three favorite new features of AD20?”
A: “The interactive router is absolutely amazing...it’s really helping us to make last-minute changes about 40% faster, plus the user interface, and there’s much more. Also, the 3D rendering engine is phenomenal compared to what it was.” - Q: “What’s your opinion on the stability of AD20 and what is the impact on your day-to-day?”
A: Even on the Beta I’ve noticed that it’s pretty stable, overall I have not had the system crashes that I’ve seen in the past.” - Q: “How would you compare the interactive routing and any dramatic changes in AD20 to AD17?”
A: “The router is amazing, I highly recommend that everyone go to this section of the presentation; the way the router works now is absolutely amazing especially or me typically dealing with 40 to 60 rules—I can get a lot more packed in because of the way the router can now hug around a pad, once you see it, you’ll be blown away.” - Q: “If you could pick only one thing that has improved your daily design flow, what is the #1 new thing?”
A: “Other than the router, we’re seriously starting to look at ACTIVEBOM® because that gives us a pulse on the way the industry is going.” - Q: “Not to be redundant—specific to time savings—you just went from 32-bit to 64-bit, which is a huge time saving, but besides that, what is your biggest time saver?”
A: “Again, for us, it’s the router.” - Q: “What do you feel may not have been addressed in Altium 20?”
A: “I haven’t seen anything in our industry, for the way we use the tool—speaking with other people at AltiumLive though, it seems they are very happy with the differential pair routing improvement.” - Q: “Have you played around with the creepage, it sounds like you’re dealing with a lot of high voltage?”
A: “Yes, thank you very much for that. That was one of the things that was tricky, with worrying about UL spacing, there’s creepage and clearance and we have to address both; having the tool do that for us—that’s going to save us a lot on board spins!” - Q: “Have you used any other CAD tools during your career, Mike?”
A: “I have used other tools, that we won’t mention, but it’s always been your tool, and honestly, everyone I’ve worked for, wanted Altium. Most of the jobs I see posted require Altium Designer experience.” - Q: “From what you’ve seen in AD20 regarding high-speed digital, do you think there are any designs that the tool can’t handle?”
A: “No, I have worked with high-speed digital before, and I don’t see anything that the tool can’t handle.” - Q: “Which three capabilities of Altium Designer as a CAD tool, sets it apart from other CAD packages?”
A: “The router, again—I think that router is absolutely fantastic. The capabilities it has, with the 3D, is far better than anything I’ve seen on any other package, and the ACTIVEBOM is another thing where Altium always seems to be one or two steps ahead of everybody else. The other thing that is going to help with collaboration is Altium 365. It removes the disconnect between the designer and everyone else in the process.” - Q: “What made you decide to make the switch from AD17, where you’d been hanging for a while, and move onto AD20?”
A: “When I got into the AD20 Beta program, I was able to start using it immediately, there’s one modal dialogue box that’s not there, but I’m not noticing any difference in the usability. I have switched over completely now.” - Q: “What has made you stay with Altium over the years?”
A: “Obviously the price point, you guys don’t nickel and dime us. The ability to go on and off maintenance while your software stays intact is very helpful, and you guys are very stable. Also, the fact that you continue to improve the tool.”
Links and Resources:
Interactive router (video of any angle routing on Linkedin)
See What’s Coming in Altium Designer 20
Trade In Your Outdated PCB Design Tool & Unlock Savings on Altium Designer today!
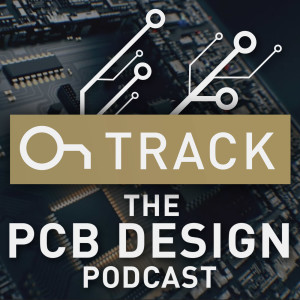
Tuesday Oct 29, 2019
Max Seeley and Carl Schattke on AltiumLive 2019
Tuesday Oct 29, 2019
Tuesday Oct 29, 2019
Trade In Your Outdated PCB Design Tool & Unlock Savings on Altium Designer today!
Recording from AltiumLive Europe—we have Max Seeley, Lead Electrical Engineer at 3M's Digital Solutions Group and Carl Schattke, Lead PCB Design Engineer from a well-known electrical vehicle manufacturer for a coffee-table chat about the value of attending and being involved with tech conferences like AltiumLive. Max and Carl also share with us how they came up with their presentation ‘Schematic to PCB Design: Passing the Baton Like a Champion’.
Show Highlights:
- Carl is a PCB designer with 46 years of experience in a range of high-speed and high-voltage
boards and complex controllers, sensors, and test equipment. He is passionate about teaching design and has been an Altium Designer® user since 1985.
- Max is in the Corporate Research Lab, and part of the Digital Solutions Group at 3M. His group supports the development of high-tech electronics.
- Q: “What is the importance of conferences, self-education and being involved with summits such as AltiumLive and PCB West? How does this serve your career?”
- A: Carl - “Exposure to different points of view and methodologies. CAD tools are complex by nature, with tons of features. When you see how other people do things, usually you’ll pick up ways of doing things to add to your repertoire. Also, making connections with different people increases your value to the community as well as the depth and breadth of your network”.
- A: Max - “Learning where to go to get the right information. I have learned which sources of information to focus on. I learned very valuable things from Carl, while Rick Hartley and Mike Creeden have been profound influencers, and the textbook, Electromagnetic Compatibility Engineering, by Henry Ott is a great textbook. It’s really important to ask if there’s a sound scientific explanation for any opinion.”
- Carl and Max delivered a talk called ‘Schematic to PCB Design: Passing the Baton Like a Champion’, here at AltiumLive. It’s a very useful look at the process of moving from schematic to PCB, covering aspects from setting up the schematic to transferring the data to communication and avoiding the pitfalls of the process like a champ. The race is lost when you drop the baton.
- Max has many tips he gathered over the years and Carl has a collection of questions he believes should always be asked.
- Max believes that doing presentations together presents a fantastic opportunity to learn from one another; also, teaching something forces you to pay more attention to your own process.
- Professionally, the most valuable skill we have is the ability to ask questions.
- It’s critical in the design process to slow down a little bit. Typically the excitement and adrenaline causes a rush once the schematic is done.
- Methodologies should be adaptable to whatever it is you’re designing and the timeline - we need to be ready to change with a positive mindset.
- Q: “What have the AltiumLive 2019 highlights been?”
- A: Max - “What sets the AltiumLive conference apart is the community.”
- A: Carl - “What I enjoyed the most is meeting new engineers and talking geek stuff about people’s different passions and projects.”
- Judy loves watching the interaction between students and experienced engineers—it’s a two-way street of inspiration.
- There will be a full recording of Max and Carl’s presentation available online within about a month.
Links and Resources:
Trade In Your Outdated PCB Design Tool & Unlock Savings on Altium Designer today!
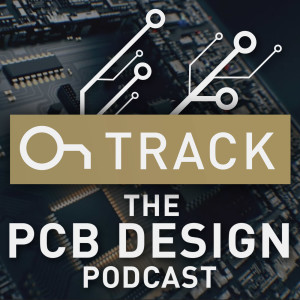
Tuesday Oct 22, 2019
Mike Konrad on Design for Reliability
Tuesday Oct 22, 2019
Tuesday Oct 22, 2019
Trade In Your Outdated PCB Design Tool & Unlock 45% OFF Altium Designer today!
Mike Konrad’s passion is educating people about cleaning their boards at assembly. If you care about Design for Reliability (DfR), you’ll learn a lot from this podcast. Mike is President & CEO of Aqueous Technologies, which manufactures, sells, and supports machines that clean circuit boards after reflow, with the goal to remove ionic residue and eliminate the chance of electrochemical migration. He is also a fellow-podcaster; hosting a show called ‘Reliability Matters’. Hear how Mike got his start in the industry and founded Aqueous Technologies and more.
Show Highlights:
- Cleaning is optional for some and mandatory for others - it adds reliability.
- What does ‘cleaning’ mean with regard to the way a board comes into an assembly house? Every board has a tolerance for residue, unique to its purpose and design. This means it’s virtually impossible to predict what level of contamination each board will have.
- We tell our customers that in controlled conditions, a board may have a substantial tolerance for contamination. However, you should never assume that your board starts at zero, no matter how much care goes into the fabrication or assembly process.
- The implication of dirty boards is mostly ECM (electrochemical migration failures) which manifests in one of three ways: dendritic growth, parasitic leakage, and CAF or CAFF.
- Dendritic growth is where metal crystals on a board grow between conductors, anodes and cathodes, creating shorts and causing the board to lose conductivity. Dendritic growth in a guided missile, for instance, could have disastrous implications.
- Parasitic leakage is a rise in conductivity and a loss in resistivity, creating a current path, but not enough to cause a dead short
- CAF (Conductive Anodic Filaments) or CAFF Conductive Anodic Filament Failure, is partially caused by micro-cracks or dry weave between the layers of a board, where the plating solution from the vias and through-holes leach into the cracks
- When considering the application, it’s essential to determine the cost of failure, e.g., a pacemaker...
- When a board catches fire, it’s pretty clear what will happen to the product housing the board.
- The Montreal Protocol was a treaty that got rid of chemicals used to clean circuit boards in 1989. Vapors from solvents and chlorine molecules were damaging the ozone layer and it was ratified by every member nation of the UN, leading to the emergence of low-residue flux (sometimes erroneously called “no-clean flux”).
- Flux is mandatory when soldering to avoid oxidization. Some assemblers turned to more environmentally-friendly cleaning products that weren’t as effective, and the rest got rid of the process.
- Circuit boards have become denser and smaller, and miniaturization is causing more problems with the no-clean protocol.
- Don’t call it no-clean flux—low-residue flux is much more accurate. 55% of our customers who are running no-clean are cleaning. No-clean doesn’t mean “don’t clean”. Instead, don’t clean what doesn’t require it, but do clean what needs cleaning; it’s as simple as that.
- Mike relates a very telling litigation case in which an OEM couldn’t deliver the goods to its contract manufacturer (due to not fully cleaning contaminants from its boards) and tells us how litigation could have been avoided.
- IPC standards regarding cleanliness have recently been updated.
- What should designers be demanding in the form of cleanliness? What is the cost of failure, the criticality of the product and its climatic environment? These aspects must be included in the specifications.
- There are third-party companies that will look at your design file and create algorithms to determine its propensity for failure due to residues. It all boils down to clean boards!
Trade In Your Outdated PCB Design Tool & Unlock Savings on Altium Designer today!
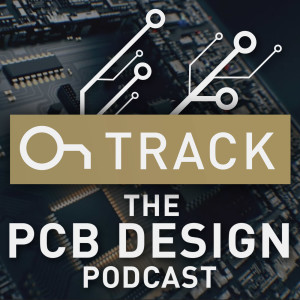
Wednesday Oct 16, 2019
Altium VP, Lawrence Romine on Altium Designer 20
Wednesday Oct 16, 2019
Wednesday Oct 16, 2019
Lawrence Romine, VP of Corporate Marketing for Altium discusses what new features you can expect from Altium Designer® 20, which will be available later this year.
Trade In Your Outdated PCB Design Tool & Unlock Savings on Altium Designer today!
Show Highlights:
- Lawrence has been with Altium for almost 15 years. At the time, the move to offshore manufacturing was prevalent and his previous experience with semi-conductors and FPGAs fit in well with Altium’s FPGA strategy. Since then, he has been involved in almost every facet of the business.
- What are the trends in the industry and why is Altium making some of the decisions we are with our product? Mainly the extreme pressure of speed and meeting intense release dates. More than half of our customers are doing 10 new designs a year and 40% of them are doing more than 25 PCB designs each year.
- This trend brings the rise of the ‘all-purpose engineer’, however, the majority of our customers are Electrical Engineers and due to the complexities and data rates of design, engineers and PCB designers must absorb more of the technical aspects and procurement responsibilities.
- What is Altium doing to absorb these trends and enhance the user experience? Altium is clearly the number one professionally-used PCB design tool. We are now in the space where the user-imperative is paramount, meaning, we must engage with users and are in the process of aligning the entire company with that strategy.
- We are diligent not to leave our existing customers behind. Some of our power users advised that they aren’t keen on some prior changes, so in Altium Designer 20 you’ll have, for example, a re-factored properties panel.
- The unified design model is coming back and being enhanced in Altium Designer 20, for example, dynamic, automatic compilation.
- The 3-release arc between Altium Designer 18 and Altium Designer 20 includes changing to 64-bit, changing the user interface, the new layer stack manager, and specifically, the materials library and the field solver technology.
- The star of Altium Designer 20 is undoubtedly interactive routing–and is already being received exceedingly well. What we have now is peerless.
- The new differential pair capability with its elegance of operation is exceptional, as well as the angle routing which can route any angle.
- Other aspects of Altium Designer 20 set us up for future development work: the first thing you’ll notice on a very large, dense schematic, is that it will be smoother and panning and zooming are enhanced.
- The new SPICE simulator was added by user request; all the models you can throw at it should work, but more development is underway.
- We added more advancements to multi-board design, such as ACTIVEBOM®, which now supports all the boards in a multi-board project.
- 3D PDF support has been enhanced, we added some library migration capability to ease the transition into Concord Pro™.
- We also added the ability to place components on the mechanical CAD side.
- If you’re doing high-voltage design, we’ve added some new creepage rules, crossover- and return path rules.
- Where are we with bug fixing? We’ve never neglected it, but perception is a reality for the person who is experiencing an issue, so an area where you will begin to see a significant enhancement is direct engagement in our forums, on the BugCrunch itself, on the ideas forum; as a mandate from the CEO directly.
- Altium Designer 20 is addressing twice as many bugs as the previous version, which amounts to +-120 bugs being crunched, based on votes collected on Altium BugCrunch.
Graph of Unique users impacted by bug fixes
See What's New. Altium Designer 20, A Computer Aided PCB design Software.
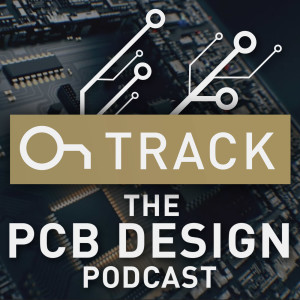
Tuesday Oct 08, 2019
Shaper Engineer Jeremy Blum on Arduino and Building Consumer Products
Tuesday Oct 08, 2019
Tuesday Oct 08, 2019
Jeremy Blum is the Director of Engineering at Shaper, a start-up company that built the world's first handheld CNC technology for woodworking. Jeremy talks about his keynote speech at the AltiumLive PCB Design Summit on October 21 - 23 in Frankfurt, Germany. His talk is about product development and lifecycle management from a holistic approach to engineering and design. Learn about his engineering journey from master’s student at Cornell, to GoogleX through his latest engineering adventure launching a consumer-based product at Shaper.
Trade In Your Outdated PCB Design Tool & Unlock 45% OFF Altium Designer today!
Show Highlights:
- Shaper is a company in San Fransisco which makes hand-held robotic power tools. Jeremy is the Director of Engineering, overseeing the embedded software team and electrical engineering.
- Before Shaper, he was at Google X for a few years where he worked on system architecture and electrical engineering as well as design projects for Google Glass.
- He first became involved with consumer electronics design at MakerBot Industries.
- His YouTube channel, where you can still see his uploads from as early as 2006, is very popular, and he has also written a textbook: Exploring Arduino, with the second, updated, full-color edition launching very soon.
- Jeremy’s keynote for AltiumLive is titled: Holistic Product Design for Electrical Engineers. He says his goal for this year’s keynote is to expand on the talk he gave at AltiumLive in 2018, which was about empathetic engineering.
- This year he will focus more on consumer products and the actual requirements of products working all around you, predominantly to make the process more fluid by meeting everyone’s needs.
- The reality of product design is not as abstract as it’s often made out to be. In fact, it’s very different, and Jeremy will discuss requirements that are sometimes out of your control—where compromises must be made.
- Jeremy’s inspiration for the keynote is his unique perspective from a smaller startup producing consumer products, and he’ll dive into the hands-on, full lifecycle of a product.
- It’s important to realize that despite the freely accessible tools today, there are still repercussions when IoT products aren’t reliable or useful; for example, security vulnerabilities in products used directly by consumers.
- Communication with suppliers, vendors, and manufacturers is consistently one of the most difficult parts of the job.
- Meticulous documentation is essential and helpful when it comes to working with vendors in other countries, and it becomes necessary to be able to express disappointment without the buying power of a massive organization behind you.
- The burden of knowledge is real: after PCB West, Jeremy finds himself overthinking work as he learns new ways of doing things.
- Jeremy’s approach to self-education is that it is imperative. He attends conferences, reads industry magazines and websites (taking it all with a grain of salt).
- There is no list of ‘rules of thumb’—they all have caveats. Take the time to ensure which rules apply to your situation, and understand the underlying physics.
- Jeremy feels strongly that the value of attending AltiumLive is meeting experienced people and building relationships with those who are as enthusiastic and excited about what they do.
Links and Resources:
Jeremy’s new book: Exploring Arduino
Jeremy on the OnTrack Podcast in Feb 2018
Learn, connect, and get inspired at AltiumLive 2019: Annual PCB Design Summit.
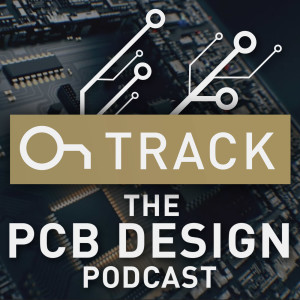
Tuesday Oct 01, 2019
Get inspired by Major League Hacking with Johathan Gottfried
Tuesday Oct 01, 2019
Tuesday Oct 01, 2019
Jonathan Gottfried is co-founder of Major League Hacking, or MLH, the official student hackathon league. Major League Hacking’s vision is to inspire students worldwide from both traditional and non-traditional backgrounds. They’ve influenced new generations of engineers; from software, hardware, and mechanical disciplines in the events they have thrown worldwide. Learn more about Jonathan and his inspiring work at MLH.
Trade In Your Outdated PCB Design Tool & Unlock 45% OFF Altium Designer today!
Show Highlights:
- Jonathan started off as a hobbyist programmer when he was a little kid, building websites and games, and playing around with different technologies.
- As a student, he would build apps for people as a source of income, and after graduation, landed the amazing role of Developer Evangelist at Twilio Inc.
- While attending CS classes he was exposed to the massive community of passionate tech students who wanted to build things for fun and saw the considerable disconnect between what they were learning in classes and the actual day-to-day work in the industry.
- Major League Hacking is the global community for student developers. They are best known for their hackathons—weekend-long invention competitions in which developers, designers, engineers, and product people come together with their own ideas and build working prototypes in a very short time.
- Major League Hacking also offers technical workshops through its Major League Hacking localhost program, where students can learn a specific, bite-sized skill in an hour or two.
- The coaches at Major League Hacking are student leaders and role models building a diverse community on a local level.
- A new acronym, ‘STEAM’ (rather than ‘STEM’) incorporates the arts. Jon feels strongly that technology is an art and incorporates building products that resonate with people.
- Because the divide between hardware and software is blurring, Major League Hacking makes hardware available at the hacking events—exposure is the first step to becoming passionate about hardware.
- What is the impact of exposure on non-traditional students? It can be a life-changing experience to be involved in a technical community of supportive, inclusive, passionate and creative people. It can provoke a passion which sitting in a normal class isn’t always able to achieve.
- The impact on traditional STEM students includes gaining skills for the customer discovery process, for example; it’s a self-driven process.
- The hackathon process is: come up with an idea; get a team excited and on board, and then build the product together—encouraging more soft skills, such as team building, creative thinking, problem-solving, etc.
- In the traditional university model, there isn’t enough focus on the practical aspects of STEM because funding is mainly reserved for research.
- The barriers imposed by lack of hardware access are diminished by the prevalence of cloud hosting.
- Technology is being unleashed in this day and age, and in the coming years it’s going to be even more drastic—creators have a responsibility to ‘use their powers for good.’
- Major League Hacking provides resources to students for free, thanks to corporate sponsorship—get involved!
Links and Resources:
Find out more about how your company can get involved with MLH
If you're a student, learn more about our upcoming hackathons here
Join us in October for Local Hack Day
Host a technical workshop in your club or meetup
Come work for MLH
Altium Student Stories
Follow MLH on social media:
Jon Gottfried - @jonmarkgo
Major League Hacking - @MLHacks
Learn, connect, and get inspired at AltiumLive 2019: Annual PCB Design Summit.
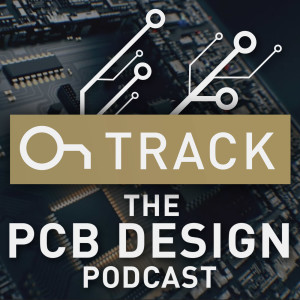
Wednesday Sep 25, 2019
Practical Applications of Designing With High-Density Interconnect-HDI
Wednesday Sep 25, 2019
Wednesday Sep 25, 2019
Happy Holden, known as the father of High-Density Interconnect and the author of The HDI Handbook, is this episode’s fascinating guest. We’ll discuss how Happy went from a small-town boy to a first-name basis with legends Bill Hewlett and David Packard, the founders of HP. Happy will be a keynote speaker at our AltiumLive Annual PCB Design Summit in Frankfurt, where he’ll discuss smart factories and how we’re going to get to the point of having digitized data. He’ll also talk about AI and his full-day talk will include HDI and the considerations you need to keep in mind.
Trade In Your Outdated PCB Design Tool & Unlock 45% OFF Altium Designer today!
Show Highlights:
- Happy feels lucky to have been at the right place at the right time throughout his career. He grew up in the mountains of Oregon in a small, highly-involved logging community.
- His math and science teacher in high school had a physics Ph.D.—not a traditional education curriculum. At university, they also had professors who were Nobel prize winners, such as Linus Pauling.
- After graduation, he was invited to interview with the integrated circuit department at Hewlett-Packard, on the recommendation of one of his professors.
- HP was more advanced than IBM when it came to integrated circuits.
At the time, HP was making high-frequency and RF integrated circuits out of germanium and silicon placed on sapphire wafers, called “Silicon on Sapphire” or SOS. - Intel was still a start-up at this time.
- As the first chemical engineer at HP in integrated circuit (IC) production; he was on a frontier at HP, the only chemical engineer at a company of fewer than 2,000 people—it was exciting for 21-year-old Happy Holden.
- During his 28 years there, HP climbed to 167,000 employees and from 200 million in sales per year to 54 billion!
- HP’s first 64-bit desktop machine was called a “Desktop Calculator”, because at the time a 64-bit computer was the size of a room.
- By 1972, Happy assisted Bill Hewlett in making an HP35 ‘calculator’ which was battery-powered and fit in his pocket.
- During his keynote, Happy will show pictures of the unique solution they used for the keyboard.
- At the time, they had no idea how to make a reliable gold-plated rigid-flex printed circuit board and the result was an eight-layer logic board, double-sided keyboard, and displays soldered in at an angle.
- Apart from the keynote, Happy will present a full-day class on October 21, which he calls ‘Product realization using HDI technology”; a course on the electrical performance and the advantages and drivers of using High-Density Interconnect and blowing up the myth that you have to pay more for it.
- He will be giving some insights into unlearning several aspects of multi-layers and how miniaturization should indeed save you money by demonstrating four different case studies where complex 18- and 24-layer boards were made into an 8- or 10-layers with High-Density Interconnect and less expensive.
- An interesting aspect of this full-day course is where do we go from here, what’s the next step after HDI?
- Also, don’t miss the keynote on October 23, titled “PCB Trends That Will Impact YOUR Future” and how he started working with AI 25 years ago!
Links and Resources:
HDI Handbook
Articles by Happy Holden
Learn, connect, and get inspired at AltiumLive 2019: Annual PCB Design Summit.
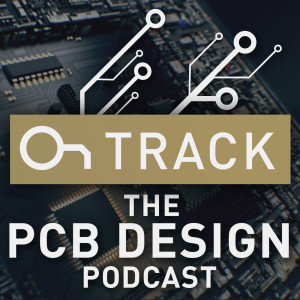
Tuesday Sep 17, 2019
Carl Schattke - Designing Complex Boards
Tuesday Sep 17, 2019
Tuesday Sep 17, 2019
Today in the studio, we welcome Carl Schattke, who works for a leading electric vehicle manufacturer. Carl has almost forty years of experience in PCB Design and will teach us about the things he thinks about when designing very complex boards. He’ll discuss what he’s going to cover as a keynote at AltiumLive in Frankfurt, October 21st through 23rd, and he’ll tell us more about a talk he’s co-presenting with Max Seeley from 3M, in which they’ll discuss going from schematic to PCB layout and passing that baton like a champ. Sign up for AltiumLive now—space is limited!
Trade In Your Outdated PCB Design Tool & Unlock 45% OFF Altium Designer today!
Show Highlights:
- Carl’s earliest memory of an engineering project and the first indication of his future career was at age three when he built a helicopter out of an Erector toy set.
His father was a mechanical/electrical engineer, and at 8 years of age, he would help with point to point continuity checks. Seeing so many designs helped him develop his own style, good symmetry, and spacing. - The advantage of having manual experience early on over someone jumping in with electronic tools is the appreciation for using the space that’s available, but today’s boards are so complicated that without that early exposure, Carl feels he would be hard-pressed to do what he does today.
- Carl will bring artwork he did to San Diego so that young designers can get a glimpse of history.
- Carl’s keynote at AltiumLive in Frankfurt will be ‘Making and Breaking the Rules’, where he’ll discuss design rules; where we’ve come from, where we are right now and where we’re going, illustrating what’s important and what we can disregard or change. Do we change the rules?
- In what ways do design rules help or hinder today’s designers? They’re a tremendous help—the clearance rule and the Altium Designer® shadow feature is quite awesome—but in order to remain profitable, we need to understand the gaps in our rules.
- One of the most important ‘tools’ designers have is the ability to communicate with their manufacturer and engineers; asking the right questions to avoid disconnects. Getting the opportunity to connect and reflect and learn, is invaluable.
- Carl will also be doing a two-hour breakout session with Max Seeley from 3M, both in Frankfurt and San Diego; ‘Schematic to PCB Design: Passing the Baton Like a Champion’. This will be very valuable for the audience because they will talk about aspects that we don’t see in videos or read about much.
- The talk will also be beneficial to the EEs laying out their own boards because several circuits will be discussed and they still have to consider all the aspects of their process.
- What is the difference between the thinking process of pure electrical engineers, vs PCB layout pros? Depending on experience, the problems are going to be the same, it all boils down to transition line theory, resistance-capacitance, inductance, and how those things work together on a circuit board.
- Where is the baton mostly dropped? Placement expectations, simple things like what side of the board is which, non-optimal layout, leaving off the timing requirements, leaving differential pairs unlabelled. Many little details can have a huge impact.
- These talks will be very practical in terms of authentic design review—things that are not generally dropped on a schematic and much more.
- Sign up now, space is limited!
Links and Resources:
AltiumLive October, San Diego
AltiumLive, October, Frankfurt
Picture of Rick Hartley on a light table
Carl and Julie’s talk at AltiumLive 2018
Trade In Your Outdated PCB Design Tool & Unlock 45% OFF Altium Designer today!
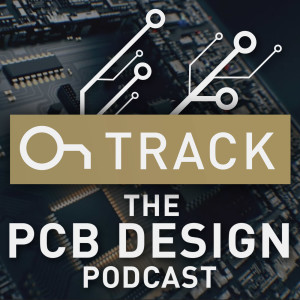
Tuesday Sep 10, 2019
Bob Martin Goes From Prototype to Production with an Arduino Board
Tuesday Sep 10, 2019
Tuesday Sep 10, 2019
Today we speak with Bob Martin, a Senior Staff Engineer with Microchip. Bob is also known as ‘the wizard of make’, and today he’ll discuss his AltiumLive Keynote on October 11th in San Diego where he’ll teach on how to go from prototype to production with Arduino Board, transitioning it into a production-ready board that you can manufacture.
Trade In Your Outdated PCB Design Tool & Unlock 45% OFF Altium Designer today!
Show Highlights:
- Bob graduated from the University of Saskatchewan, Canada in 1987 and spent his entire career in embedded systems, ending up at Microchip Technology with the unusual job title ‘Wizard of Make’ which originated at Atmel.
- The title ‘Wizard of Make’ comes from a discussion to progress his job description at Atmel. Being enamored with makers, and a maker himself - he has attended every maker fair in the Bay Area since its inception. The word ‘wizard’ came from describing some of his talents.
- Bob’s talk at AltiumLive will encompass the many facets of Arduino which enable rapid prototyping and doesn’t require starting designs over during transition to production. He will detail mostly the hardware aspects and how to make the transition to production easier.
- Because of the complexity of systems and the need for rapid prototyping today, the ease of using products like Arduino are becoming more prevalent. You need to be able to talk to your electro-mechanical designer and be more involved in systems-down thinking.
- Quick paths to production through Arduino: there are things that you need and others that you don’t and the keynote will explain what to keep and what to discard to ensure lower production costs.
- Ben will also discuss concepts of testing: where to put test points and why they’re more cost-effective, as well as lowering BOM costs.
Pete Wilson, from Microchip, will do another talk about dropping pre-certified RF models on designs. - The ecosystem of products like Adafruit, CircuitMaker, SparkFun, Pololu, MikroElektronika are all very easy to use, relatively inexpensive and almost plug and play, once again enabling rapid prototyping.
- The name ‘Arduino’ is the name of a bar in a town in Italy where Massimo Banzi taught and they used to gather there to discuss the product. Arduino’s software system made things easy, leveling the embedded field.
- Who would this talk be of interest to? Anyone who is interested will be enlightened about what, hardware-wise, makes an Arduino platform, and receive an extension of their knowledge about ACE (Arduino Component Elements).
- What is a professional maker? The pro-maker could be an electrical or mechanical engineer or some other technologist who has recognized a problem or has an idea, using Arduino or a similar system to implement a solution, but in the back of their mind, there’s always the matter of the implications of going into production.
- Eric Bogatin’s talk ‘A Downside of Open Source Designs’ fits in very well with Bob’s regarding the software component and what to look out for when using open-source designs.
Links and Resources:
History of Arduino
Jeremy Blum - Handheld shaper tool video
Learn, connect, and get inspired at AltiumLive 2019: Annual PCB Design Summit.
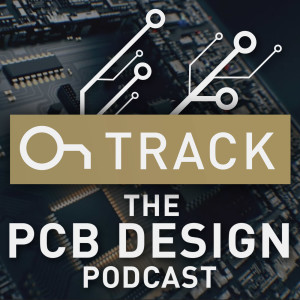
Friday Sep 06, 2019
Seven Design Guidelines to Break Bad Habits from Using Open-Source Designs
Friday Sep 06, 2019
Friday Sep 06, 2019
Welcome back, today we speak with Dr. Eric Bogatin who is the Dean of Signal Integrity at Teledyne Lecroy. Eric has agreed, once again, to be a keynote speaker at AltiumLive, San Diego - October 9th to 11th and today he shares more with us about his keynote and the courses he teaches at Colorado University, Boulder, some books he’s writing, and the makers he serves. There’s no grass growing under this man’s feet.
Trade In Your Outdated PCB Design Tool & Unlock 45% OFF Altium Designer today!
Show Highlights:
- LinksEric has spent most of his career in the signal integrity field on multiple sides of the fence, including R&D, product and tool development, which was his springboard into education, keeping him busy for 30 years.
- After selling his company to Teledyne le Croy, as they’re now known, he is still focusing on best design practices, and how to eliminate problems before they happen.
- Currently, Eric is more focused on best measurement practices, or how to use scopes and other instruments to analyze a product and find the weak links and root cause of issues.
- At AltiumLive this year, Eric’s talk, ‘Breaking Bad,’ encapsulates best design principles and the downside of open-source designs as well as in-depth, specific design features on boards.
- Approximately a million Arduino Uno R3 boards have been manufactured in the last ten years, but they have many ground bounce issues and terrible return path control - Eric uses them as an example of how NOT to design a two-layer board.
Using open-source designs may lead to bad habits. At AltiumLive he will discuss how to use the Arduino design and show how to measure ground bounce and implement the right design guidelines - refer to Seven Design Guidelines link below. - The message of the keynote is: don’t apply what you see in a popular open-source design, believing that it’s the right way of designing.
- Right after the keynote, Eric will be doing another talk on ‘Mastering the TDR in 45 Minutes’.
- The TDR is the most valuable instrument to characterize, as a first pass, electrical properties of circuit boards, but it has several little-known applications in the lab environment, which will all be discussed.
- Besides his work at Lecroy Eric is also involved in writing textbooks and another book on the design and characterization of transmission lines through Horizon House/Artech.
Links and Resources:
Article: Seven design guidelines, Signal Integrity Journal
Learn, connect, and get inspired at AltiumLive 2019: Annual PCB Design Summit.
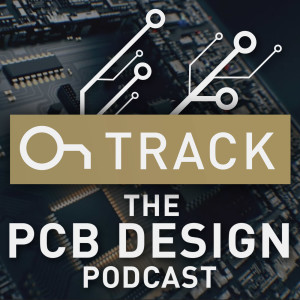
Thursday Aug 29, 2019
Mike Buetow on PCB West
Thursday Aug 29, 2019
Thursday Aug 29, 2019
Mike Buetow, the Editor in Chief and Vice President of Printed Circuit Design & Fab magazine as well as Circuit Assembly’s magazine, joins us to talk about PCB West. The publishers UP Media put on PCB West every year in Santa Clara, this year’s will be September 9 to 12. We talk about what you can expect from the show, how it got started and some colorful history from their background. Altium is also a sponsor of the show this year, and we’ll be there with a booth and Ben Jordan will be giving a class; ‘The Absolute Beginner’s Guide to RF Design.’
Trade In Your Outdated PCB Design Tool & Unlock 45% OFF Altium Designer today!
Show Highlights:
- After two semesters of applied math, Mike switched courses to journalism and ended up working for a trade magazine in the SMT industry. He also worked for IPC for six years where he became embedded in this industry.
- PCB West predates UP Media by almost a decade, the original conference and exhibition launched in 1991 and is now in its 28th year.
- What sets PCB West apart as a conference after 28 years, is the in-depth format itself; a deep dive into tutorials on printed circuit design and manufacturing.
- 70% of the sessions this year, will be at least two and a half hours long, there are also 20 half-day workshops and 5 full-day workshops.
- There will be 14 talks on EMI/EMC and noise control, 20 involve some element of DFM or board fabrication, and more than 20 will cover high-speed design. The sessions are longer, attacking subjects from all angles.
- PCB West has seen considerable growth over recent years due in part, to holding it in September rather than the first quarter of the year, and has been sold out for the past eight years.
- Highlights at PCB West this year include: Eric Bogatin with two presentations, Lee Ritchey with a not-to-be-missed, full-day high-speed tutorial, Daniel Smith from Raytheon will discuss an AI development to address CAD/CAM design bottlenecks. Altium’s Ben Jordan, who is a real designer’s designer, will also be there talking on RF and microwave design.
- Susy Webb and Paul Cooke will be covering a variety of basics to include schematics, layout, and fabrication.
- Rick Hartley, the most popular speaker in the history of PCB West is back with seven presentations, including new talks on design for IoT devices.
- Joe Fama will explain his model on how Tier 3 EMS companies can compete with Tier 1 companies on BOM costs.
- Greg Papandrew is representing his new company ‘Better Board Buying’ and will highlight how to improve procurement processes.
- ‘Free Tuesday’ offers 13 free sessions including Eric Bogatin on SI and PI, and a very participative session on ‘21 (and Counting) Most Common Design Errors, Caught by Fabrication, and How to Prevent Them’ by Dave Hoover, TTM Technologies, Ray Fugitt, Downstream Technologies and Mike Tucker, Kinwong Corporation.
- Writing Your Résumé and Marketing Yourself Within Your Company by Gary Ferrari will be very interesting as it’s an often-neglected area.
- PCB West has changed over the years; today we see many more degreed engineers - a fun component (think ‘The Porch Dogs’) has been added, timing has changed, but one constant remains - the educational component.
- This year there will be a one-day exhibition on September 10, with 110 exhibits offering a lot of hands-on, equipment suppliers, demos and around 20 board shops with product samples, also some assembly people, and much more. For pre-registered attendees the exhibition is free, admittance on the day is $25, so do be sure to register on time.
Links and Resources:
PCB West Guide
Tuesday, September 10 Free Sessions
Exhibitors List
UP Media Magazines
PCB Chat Podcast
Learn, connect, and get inspired at AltiumLive 2019: Annual PCB Design Summit.
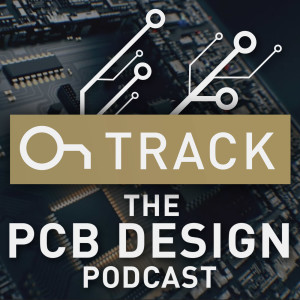
Tuesday Aug 20, 2019
Mark Forbes on the Evolution of Chip Technology and Origin Stories
Tuesday Aug 20, 2019
Tuesday Aug 20, 2019
Welcome back to the OnTrack Podcast. Today we speak with Mark Forbes, Director of Product Marketing at Altium, about the history of IC development and how that directly impacted you and will continue to impact you and your design practices. Capturing some of the history is important so that we know why we do things that we may not have known happened 30 years ago - you’re really going to enjoy this deep dive into what’s happened over the last 30 years and how it impacts your career every day.
Trade In Your Outdated PCB Design Tool & Unlock 45% OFF Altium Designer today!
Show Highlights:
- Mark has spent his entire career in electronics, equally divided between hardware and software.
- PCB design has been dramatically affected over time by the trajectory of ICs.
The 8080 microprocessor exploded the idea that we don’t have to design discretely, but could program a computer to do all our functions. - The main effect of increased integration on PCB design is that so many functions have been shrunk into a single chip and how to get those out to other parts of the board, is a major problem.
- The higher speeds create more heat in these smaller spaces and heat dissipation/cooling is also a major problem.
- Geometry is a huge factor in why we are able to integrate more stuff on the same chip, for example in 1971, the geometry was 10 microns (µ); on the current Snapdragon, it’s 7 nanometres (nm). If you had a thousand-page book that represents 10 microns; one twentieth of one page is 7 nm.
- Now we’re running into some physical issues such as speed - the original 4004 ran at 740 kHz, and the Snapdragon runs at 2.9GHz. If you put that into perspective, if the 4004 was a car, and you’re going 60 miles ph, the Snapdragon is going 65 miles per second.
- Speed has become important because of EMI/RMI. Back in the day the 8080 ran at 1mHz, and an antenna was a few feet long, none of the traces on the board acted as resonant antennas so, there was no radiated signal - only radio designers were concerned with frequencies and gHz whereas now, these concepts apply to the vast majority of PCBs.
- We are getting near the physical limits that can’t be broken. For example, sometimes as you try to locate a memory on a pc board that’s too far from the processor, the electrons can’t get there in one clock cycle, which is revealed by data errors. We are now fighting the flight time of an electron.
- To increase speed there are only two things you can do: 1] more cores 2] change the geometry to accommodate physical limits which are the speed of light and the size of an atom.
- Every time we leap forward with the ICs, it directly impacts board design, how do we keep up with that? Ongoing engineering education; online trade magazines; manufacturer seminars.
- Curiosity is exceedingly important.
- Where are we headed? In 20 years we probably won’t be using electronics… there will be some fundamental breakthrough.
- Telling the stories of history will inspire more development, again, stay curious!
Links and Resources:
Charles Pfeil Presentation: Effective Methods for Advanced Routing
Customer success story of increased yield rate of corn
Learn, connect, and get inspired at AltiumLive 2019: Annual PCB Design Summit.
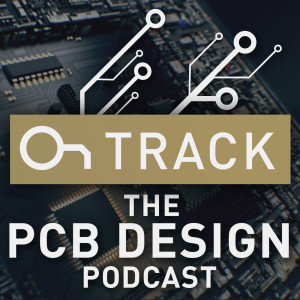
Wednesday Aug 14, 2019
Joe Grand on Hacking, Badgelife and AltiumLive
Wednesday Aug 14, 2019
Wednesday Aug 14, 2019
Today we have an extra-special guest named Joe Grand of Grand Idea Studio. Joe started hacking software and hardware at the ripe old age of seven! He ended up becoming a part of hacker history and you’re going to love hearing about it. He’s also co-founder of The Badgelife movement, and co-host of a Discovery TV channel called ‘Prototype This.’ We’re delighted to announce that he’s agreed to be a keynote speaker at AltiumLive, October 9 to 11 in San Diego. Registrations are now open and we encourage you to sign up now because space is limited.
Trade In Your Outdated PCB Design Tool & Unlock Savings on Altium Designer today!
Show Highlights:
- Joe got involved with computers in 1982 and has always been fascinated by computers and electronics. When he discovered the hacker community, he fell in love and was able to make a career of it.
- They started filming ‘Prototype This’ in 2006/2007 with the producers of ‘Myth Busters’ with the aim of following the real-life engineering of building projects, showing engineering to the masses in fun ways to share the process and even explain technical concepts to grandparents.
- Joe started using Altium Designer® in the very early days and still does so to design his badges.
- The Badgelife phenomenon started at Def Con through Jeff Moss, known as Dark Tangent. It also led to the idea to present training at conferences, ushering in Joe’s training program ‘Hardware Hacking’ which he still teaches to this day.
Many people are starting to make and sell badges, it’s almost a gateway to a professional engineering career. - Joe demonstrates his flex substrate badge for Def Con China. This is where he learned to use the Altium teardrop function.
- The Def Con USA badge included blind vias and via in pads which Joe had never worked with and once again Altium Designer came to the rescue. They went from six prototypes to 28 650 pieces in one week.
- Joe’s pseudonym is Kingpin - why do hackers have pseudonyms? Most of them grew up in the hacker world, where connecting to bulletin boards required a nickname, it was about having an anonymous identity in the hacker world back then.
- The hacker world now has many different branches and is more focused on not taking everything at face value, asking questions and being curious.
- Joe relates his experience with the group called ‘L0pht’ where they were called before the US Senate to testify on the state of computer security in government.
Joe will bring a world view of a hacker in engineering to AltiumLive in his keynote address: ‘When Hacking and Engineering Collide’ to include design tips, projects, and crazy contraptions built for television to mention a few.
Links and Resources:
Grand Idea Studio
Twitter (@joegrand)
A History of Badgelife, Def Con’s Unlikely Obsession with Artistic Circuit Boards
For Hackers, Anonymity Was Once Critical. That’s Changing
Def Con China Tree
L0pht Heavy Industries
L0pht Senate Testimony Video
https://en.wikipedia.org/wiki/L0pht
https://www.washingtonpost.com/sf/business/2015/06/22/net-of-insecurity-part-3/
https://duo.com/decipher/an-oral-history-of-the-l0pht
AltiumLive San Diego Keynote Speakers
Learn, connect, and get inspired at AltiumLive 2019: Annual PCB Design Summit.
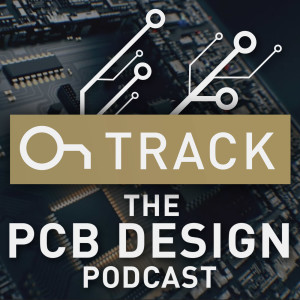
Wednesday Aug 07, 2019
Rick Hartley on EMI, Noise Reduction
Wednesday Aug 07, 2019
Wednesday Aug 07, 2019
Today we talk to Rick Hartley about EMI, noise control and why it can be so difficult to get under control in your PCB designs. Listen in, because this is really a sneak peek into the full-day class Rick will be presenting at AltiumLive.
Trade In Your Outdated PCB Design Tool & Unlock 45% OFF Altium Designer today!
Show Highlights:
- What in your childhood gave you some clues that you’d end up being an Engineer? It started with trying to repair an old alarm clock at age 5, by the time I was 12 I was dabbling in radios and repairing home appliances by age 14, which made it obvious that I would end up going in this direction.
- Rick has agreed to teach a full-day class at both of this year’s AltiumLive Summits in San Diego and Frankfurt; the title of his class on October 9 in San Diego is Keys to Control Noise, Interference and EMI in Printed Circuit Boards.
- What inspires this topic? During the mid-eighties, many issues became apparent, listening to Lee Ritchey motivated action and they formed a design council with Rick sharing the information, which continued growing to where we are today.
- In September 2019, Rick will also teach at PCB West as well as Eric Bogatin, Lee Ritchey, Susy Webb, Gary Ferrari, Mark Finstad on Flex Design, Dan Beeker - and the list goes on.
- Altium will also have a booth at PCB West where Ben Jordan will speak on RF Design and do demonstrations.
- AltiumLive is not just for Altium users, Rick believes the thoughts generated at these summits are extremely valuable.
- Why is the AltiumLive class so important for designers today? Everything is fast because the rise times of IC outputs have become so fast.
- Faster rise times equates to higher frequencies, it doesn’t matter what your clock frequency is, what matters is what devices you use.
- According to Dan Beeker, most of his customers design expecting to fail EMI the first time. People need these classes to ensure solid design from the outset and passing EMI the first time.
- Dr. Bruce Archambeault recently quoted that there really is no such thing as voltage.
- Topics that will be covered at AltiumLive: The relationship between energy and noise; what to look for when you’re selecting ICs; the impact of frequency; length versus distributed circuits; the basics of grounding and grounding methods; the keys to controlling common mode current - the leading cause of EMI; routing and termination styles of transmission lines to prevent reflections and signal integrity problems; basic component placement and the impact it can have on EMI; IO connector placement and IO connector pin-out; routing to control EMI; power delivery; capacitor placement relative to via inductance; decoupling boards with routed power; how to create proper power distribution on boards based on their stackup.
- Rick will be presenting the same talk in Frankfurt at AltiumLive October 21.
- Registrations for AltiumLive will be opening soon, don’t miss it.
Links and Resources:
Previous Podcasts with Rick
Last year’s AltiumLive Keynote
Cartoon ‘the knack’
PCB West 2019
AltiumLive 2019, San Diego
Learn, connect, and get inspired at AltiumLive 2019: Annual PCB Design Summit.