Episodes
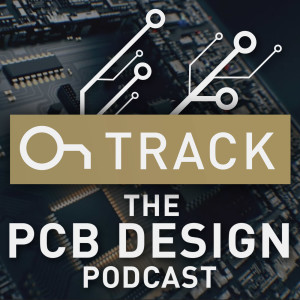
Wednesday Jul 31, 2019
Gerry Partida on Wrap Plating
Wednesday Jul 31, 2019
Wednesday Jul 31, 2019
Gerry Partida is back to talk to us about wrap plating and via filling and what the benefits, requirements and drawbacks of this technology are, and what you need to know about designing these and how this technology drives cost.
Show Highlights:
- Gerry is the Director of Engineering at Summit Interconnect with 35 years’ experience in the PCB industry, of which he spent 2 decades in boardshops.
- Were there indicators in your youth that you would end up in an engineering profession? Growing up NASA was in the middle of the Apolo program and being mesmerized by that was the beginning of it all.
- Definition of wrap plating: Wrap plating wraps copper onto the surface whenever we have a blind via or epoxy-filled hole, ensuring safe expansion and contraction during assembly.
- Benefits of wrap plating: saves real estate and protects via and with high-speed digital, it speeds up response times.
- IPC specs for wrap plating: IPC 6012 for rigid boards, 6013 for rigid-flex, and 6018 for RF. IPC4761, titled Design Guide for Protection of Printed Board Via Structures.
- The minimum wrap thickness at the knee of the hole changed recently - but the thicker the wrap, the harder it is to etch. Studies have shown that as long as you have some wrap, it’s reliable.
- By plating, epoxy-filling and plating over, we eliminate the chance of the solder going down a via next to a BGA pad.
- What are ‘butt joints’?
- Talk to your manufacturer about the optimum drill size and the requirements for epoxy-filling to prevent dimples or protrusions.
- If you have a blind via job, you must specify that they are to be filled and plated over.
- Gerry shows a hand tool that measures copper thickness around all the panels. It is used to verify, after planarizing, the lowest location and verify and cross-section to ensure that you are safe on thickness specs.
- A board shop will build in verification processes which take time - when you add epoxy-fill to a job, there are eight major manufacturing steps added to the job, which takes 24 hours in the quickest board shop. Basic board manufacture has approximately 26 to 28 steps.
- Make sure your fabricator does all the required steps for filling in-house.
- Minimizing wrap cycles creates greater consistency in your RF performance on an outer layer.
- Peel strength: when we epoxy-fill a hole it creates a smooth surface at the hole which weakens the peel strength.
- Thermal vias - conductive pastes do not conduct as much heat as copper - forget thermal paste, ask your manufacturer to plate 2mm of copper in the hole, just make the hole a bit bigger.
Links and Resources:
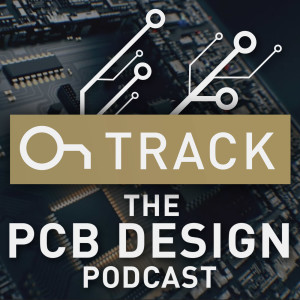
Wednesday Jul 24, 2019
Robert Feranec on How to Implement The PCB Design Process
Wednesday Jul 24, 2019
Wednesday Jul 24, 2019
In this episode we talk with Robert Feranec, a familiar name to many of our listeners. Apart from being a popular YouTuber, he’s also the founder and CEO of FEDEVEL Academy where he teaches PCB Design to people around the world. Robert shares what it takes to be a popular YouTuber, the work it takes to produce all the great content he creates and as a special bonus we’ll discuss Robert’s Keynote that he will deliver at AltiumLive PCB Summit this October in San Diego.
Show Highlights:
- Robert considers himself lucky to have started working on complex boards almost immediately after university. This early start provided much experience and he soon began freelancing.
- As a freelancer, he did whole-board design i.e. specifications, schematics, layout, as well as testing and firmware.
- He found he often couldn’t remember everything when using Altium Designer® and started doing YouTube videos, at first for himself, but soon garnered a following and today he has 24 000 followers.
- As he became more popular, he received many email questions daily, which was very time consuming and he decided to create a forum where he offered a course, and the rest is history. Robert teaches Altium Designer but also CAD-independent content.
- What goes into creating a video tutorial? Lots of preparation, a half-hour video takes almost two days to create. One hour of video training takes a week to create.
- AltiumLive Topic: How Other Companies Implement Their Hardware Design Process. Many people ask about how other companies implement hardware design, create and use libraries, collaboration (design flow) and working faster.
- Why do so many people only use a small percentage of their tool’s capacity? Most don’t need all the features. Many are nice to have but not always a necessity. Also, people learn to use the tool in a specific way and adding new features could interfere with an established workflow.
- Robert’s talk at AltiumLive will provide insight into libraries, creating new components, component lifecycle, creating new symbols as quickly as possible, ensuring correct footprints, and more.
- What are the challenges around collaboration? Communication between different types of engineers and how to manage several engineers working on the same project.
- What about versioning and backup? Most companies will do both in the same way.
- Document releases are very complex, there are too many emails back and forth. Robert will talk about ensuring correct documentation and release procedures.
- What attracts people to your training? The different levels of the courses, the variety, and junior designers love them to upskill and get better jobs.
Links and Resources:
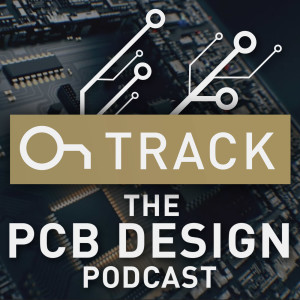
Wednesday Jul 10, 2019
PCB Design Certifications and Learning Programs
Wednesday Jul 10, 2019
Wednesday Jul 10, 2019
Today we’re going to talk about the importance of learning, as Eric Bogatin emphasized at last year’s AltiumLive. Please join my conversation with Ben Jordan where we explore a variety of ways that you can continue to learn and drive your career forward.
Show Highlights:
- A current hot topic on the forum is the value of CID or Certified Interconnect Designer Certification. This certification fills in many knowledge gaps not necessarily learned in college, such as the materials sciences and these classes are taught by gurus who started out as materials scientists.
- CID and CID+ are offered by IPC and are very useful by including how to present the results of your design to all the other stakeholders like testers, fabricators, and assembly.
- The IPC was floating the idea of recertification and it was not well received mainly due to the cost.
- Lack of practical experience is a barrier to job entry.
- Multi-disciplinary and systems-based thinking are terms we often see as criteria for finding jobs, not only the core technical skills.
- We would love to hear from our audience on whether a formal certification on a tool would help your career?
- IEEE has a recognition path called a Certified Professional Engineer which requires continual learning to maintain.
- The common thread from most industry experts is that continued and ongoing learning is crucial.
- The motivation for learning is the excitement of new technologies and most PCB Designers are very curious people by nature.
- PCB Design is never monotonous, every board is a new board.
- Robert Feranec will be a keynote speaker at the next AltiumLive; his curiosity drove him to research optimizing the hardware design flow in your company and he will be presenting his conclusions.
- AltiumLive is open to anybody, not just the Altium Designer user - pre-registration is now open.
- Keep your eye on our YouTube channels and our next Podcast.
Links and Resources:
Kelly Dack Podcast: What is PCB Design?
Circuit Assembly/UP Media article that raised the whole question on CID.
AltiumLive Summit 2019
Altium YouTube channel
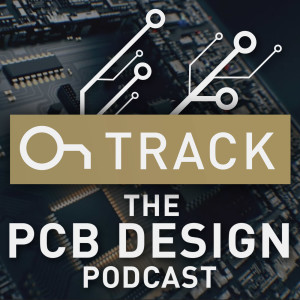
Wednesday Jun 26, 2019
Board Fabrication Tips and Myths
Wednesday Jun 26, 2019
Wednesday Jun 26, 2019
Amit Bahl, the Director of Sales and Marketing at Sierra Circuits, is here today to discuss a more holistic view of not only board fabrication, but also assembly as Sierra Circuits does both. He’s going to teach you ways to think more about your total cost of ownership. We also do some fun myth busting around PCB fabrication and assembly.
To watch the video, click here.
Show Highlights:
- Amit says his story is pretty simple: he’s here to service PCB Designers, whatever they want or need, Sierra Circuits makes it happen and have been doing so for 30 years in Sunnyvale, California. Amit spent his high school years setting up drill machines and packaging circuit boards and got his training very early on. His father started the business in 1986.
- Their business is quick-turn and they do PCB fabrication, assembly, component procurement, all really quickly from a few buildings on Evelyn Avenue.
- Tips on looking at fab and assembly more holistically: The number one mistake is a failure to send boards in, in an array; customers tend to forget to send the array panelized drawings but Sierra takes care of that for their customers.
- What data do you really need upfront? Two types of data, first for the quote and also for manufacturing.
- For quotes: Gerber or ODB data or IPC 2581 data. Then there’s everything else for fab that has to be perfect: material, surface finish, any special requirements, PCB stackup; all detailed out in a fab drawing including impedance and dielectric control.
- It’s imperative to communicate with the fabricator and visit your board shop. It helps designers understand what happens on the floor, to see where variations can come in on different machinery and to design keeping in mind that each process is in a different department.
- Some myths surrounding fab and assembly. Websites are not always updated regularly, you cannot design based merely according to what’s on the website. Pick up the phone!
- PCB materials only hold up for a maximum of three to four laminations because of thermal stress.
- Don’t trust the data sheets, even for electrical properties - every material behaves differently. Isola 370HR is very reliable and consistent.
- Price and value are not equal - look at the total cost of ownership. Do you hire supply chain first and put pricing pressure on vendors, or are you hiring a quality department first and putting quality pressures on the vendors? Focus on quality and attention to detail is essential.
- Trust begins with relationships and with trust, specific aspects can be left to the fab house.
- Sierra will be at AltiumLive 2019, October 9 - 11 in San Diego, where face to face relationships can begin.
- Sierra is launching a Google Maps Street View for their facility, where designers can ‘walk through’ the shop virtually. This should be ready within the next three weeks.
- Trends: HDI, laser drilling, flex & rigid flex.
Links and Resources:
What is Design? Podcast with Kelly Dack
AltiumLive, San Diego, October 2019
Sierra Circuit’s HDI Design Guide
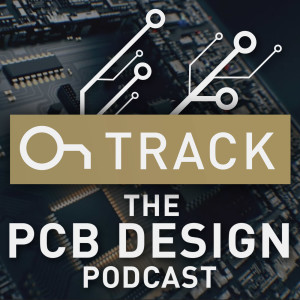
Tuesday Jun 18, 2019
Process Engineering for Advanced Assembly with Chao Vang and Sebastian Weber
Tuesday Jun 18, 2019
Tuesday Jun 18, 2019
Today we have a treat for you; we’re going to talk to two bright, young leaders at Advanced Assembly, Chao Vang, who’s the Engineering Manager there, and also Sebastian Weber who’s their Process Engineer. Both have come up through Advanced Assembly, learned in the trenches and they’re going to share great tips with you on how to make sure that your assembly is done right the first time and this will save you a lot of headaches.
Show Highlights:
- Chao’s degree and background are in Computer Engineering and Electronics Technology. She started off at Advanced Assembly ten years ago as the Coding Engineer; did sales for two years, and has been in her current role for two years now.
- Sebastian has a degree and background in Electronics Engineering and quick-turn assembly. He started as a Receiving & Shipping Supervisor and due to his technical knowledge, gradually got into more technical positions and eventually Process Engineer which he’s been doing for three-and-a-half years.
- Located in Aurora, Colorado, Advanced Assembly is the original quick-turn PCB assembly service shop; the pioneer in these services 15 years ago. Built from the ground up, they are specifically geared towards prototypes and small quantity quick-turns.
- Over the years they’ve assembled over 40 000 unique designs. With a staff complement of 105, their focus is that they are real people, with real experiences ensuring their customers get exactly what and when they need it.
- What happens after you receive the data package and files? Critical files required for DFA (design for assembly) check are: BOM, XYRS (pick and place files), and all the layers of Gerbers which must include copper, paste and silkscreen. For customers who don’t have all the files, we can create them.
- Most jobs (in fact, 95%, go on hold initially due to missing files.
- What is the first step for process engineering? Review files for special assembly notes, identify designs that aren’t necessarily the best for manufacturing and communicate on issues long before the actual build.
- What issues most routinely come up on the process engineering side? Via in pad especially on BGAs, glass top micro-BGAs, overage on very small parts.
- Common issues in front-end engineering: in the BOM, parts called out are not the same as in the description, for example, capacitors and resistors as well as polarity issues.
- How many parts on an average board? Between 250 to 500 - the DFA check takes almost two hours depending on complexity and some jobs have thousands of parts.
- What can your customers do to speed things up? Talk to the assembly house and ask what they need. A schematic and list of special requirements can help tremendously.
- Tips from engineering: Keep suggestions and feedback from the assembly house and do these implementations upon the next revision to avoid rework and related costs.
- How would customer’s implementing your suggestions impact you as an assembler? Mostly shorten lead time by preventing jobs from going on hold.
- Better planning means better results - partner up with your assembler and save money.
- All front-end engineering is done before a purchase order is even produced, meaning, the customer doesn’t pay for the DFA check.
- Parts sourced during the quoting phase through proprietary software and Octopart® shortens the sourcing time from an hour, to an average of 5 to 7 minutes!
- It’s been confirmed that Advanced Assembly will be at AltiumLive, October 9 - 11, 2019
Links and Resources:
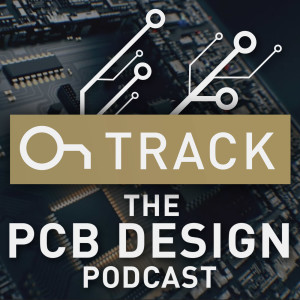
Tuesday Jun 11, 2019
How to Conquer Data Package Problems
Tuesday Jun 11, 2019
Tuesday Jun 11, 2019
Today we meet with Rob Cooke, Director of Engineering, and Jose Cordero, Lead CAM Engineer from Calumet Electronics Corporation in Michigan. We talk about something that’s often overlooked, which is making sure your data package references the most current revision of IPC Standards. Listen in as we discuss slash-sheets, ENIG, and Via Plugging.
Trade In Your Outdated PCB Design Tool & Unlock 45% OFF Altium Designer today!
Show Highlights:
- Jose jokes that nobody goes to college to end up in PCB fabrication. His background is in Art and Sound Design specifically. After completing his studies at Michigan Technical University he found Calumet Electronics, and the rest is history.
- Rob has been in the industry for almost 18 years, mostly doing design work in electronics for aircraft and military systems. He was appointed as the Director of Engineering at Calumet three months ago.
- From humble beginnings, Calumet Electronics has expanded to the point where today they produce between 600 and 800 panels a day, and over 3 million parts per year.
- The facility is unique in that it’s housed in a railway roundhouse - a very unique setting for a circuit board manufacturing factory.
- What are some of the things that slow down production due to insufficient data packages? A lot of confusion about IPC Material callouts.
- In 2017 there was a major update to IPC 4101 that changed the nominations of what materials are grouped under which category and materials are still being called out with the old specs.
- Designers need to pay more attention to their fabrication notes, and not reuse the same material callouts from previous designs. New spec updates are frequently missed, particularly in medical, aerospace and military parts where the design was produced five to ten years ago.
- Why are designers not aware of the update to IPC 4101? The pace of change can accelerate the development of the spec, and when IPC does make changes, it may not always be communicated well enough to end users.
- Via types: IPC 4761 describes seven primary types; some of the main ones are used interchangeably, even when that’s not the intent.
- Two main via types are type 5 and type 7 obviously selecting the correct type will influence both turnaround time and total board cost.
- Some folks try to specify some level of filled or capped via not using a spec but coming up with their own design notes.
- Things that throw us off: Materials instead of a class of materials are specified - there are many epoxies available. When a specific material is called for it could lead to extended wait times.
- We encourage defining plugged or capped vias by spec - the notes are ambiguous, vague, and cause the most problems.
- ENIG changes: There was a change in the spec this year. More gold is not better - the 4552 standard now has a maximum limit for gold, to prevent corrosion - whereas before there was only a minimum level.
- What is hyper corrosion and why it’s a problem: the gold is deposited on the nickel through a replacement process where each atom of gold replaces an atom of nickel - the more gold we add, the more nickel is removed, creating phosphorous molecules which is not a solderable surface.
- Designers need to verify on their drawings that specs haven’t changed.
- Ultimately the data pack is a way of communication between the designer and fabricator and it should be crystal clear. It’s also a critical point of reference for inspections.
Links and Resources:
Calumet Electronics Corporation
IPC Standards: IPC 4101 and 476, 4552
Trade In Your Outdated PCB Design Tool & Unlock 45% OFF Altium Designer today!
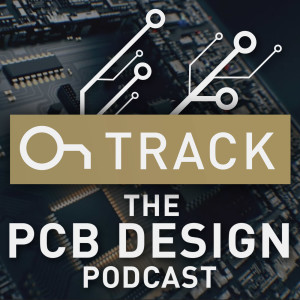
Tuesday Jun 04, 2019
How to Buy PC Boards From a Board Shop
Tuesday Jun 04, 2019
Tuesday Jun 04, 2019
Today we talk with Greg Papandrew who’s just started a new company called Better Board Buying. With more than 27 year’s experience in PCB sales, he knows all the inside tricks to help you get the most out of your vendor partnerships and to save money and time.
Trade In Your Outdated PCB Design Tool & Unlock 45% OFF Altium Designer today!
Show Highlights:
- Greg started in the industry as an inside sales and customer service guy. Believing he could provide a better service to his customers, he started The Bare Board Group in 2002, did that until 2013, and then ventured into consulting and helping customers acquire the best boards. His recent experience of the disconnect of buyers within the industry regarding their training led him to start his company to educate his customers in buying and to understand what they’re buying.
- What does Better Board Buying offer? Help buyers and engineers to buy boards better and what to look for. Improve the service that buyers are getting and help them realize that they can get better products and service - raise their expectations, most importantly bring back the personal touch. Better Board Buying offers a personal discussion about vendors, getting more buying power, taking care of all the hidden costs such as freight. Also, negotiating consignment stock and managing expectations.
- What has been lost since your start in the industry and today? I’ve been told my methods are ‘antiquated’ but they are, in fact, time tested. It does come down to relationships. The client’s confidence in the vendor to help them with any new job or problems, no matter the time of day, has been lost. Focus on the bottom line has negated the question, ‘what service are you getting for your dollar’?
- We have lost sight of the fact that the board is not just an item on a BOM that is bought on price only.
- Engineering and purchasing should collaborate more. Collaboration, inclusion, and buy-in from everyone is key.
- How should an engineer or designer think about a prototype and what does it mean to you to begin with the end in mind? First, determine the number of pieces, consider the purpose of the board, ask how it will be manufactured – a collaboration between design and manufacture is essential here – again relationships… Do you have corporate specs for PCBs to cut down on questions at the beginning?
- Why have we lost the cohesion and personal touch? The interest in manufacturing may not be what it used to. Perhaps procurement experience is not necessarily in PCB manufacturing and we lack that expertise.
- What are you personally doing to turn this thing around? LinkedIn articles, speaking at different conferences, word of mouth.
- What can people in procurement do to educate themselves? There’s plenty on the OnTrack Podcast, Circuits Assembly, PCB007, going to trade shows and talking to people there. It’s a skill you can acquire.
- What things in a board design can contribute to sticker shock once a board does go to production? There are many, but a few of importance: clarity on the finish, don’t over-design, cop away board thickness, how much routing or score is there (to save time), solder mask thickness, controlled impedance. Also, talk with your vendor, many board houses also have design engineers.
Links and Resources:
Greg LinkedIn
Greg’s article: Where have all the young PCB bloods gone?
Trade In Your Outdated PCB Design Tool & Unlock 45% OFF Altium Designer today!
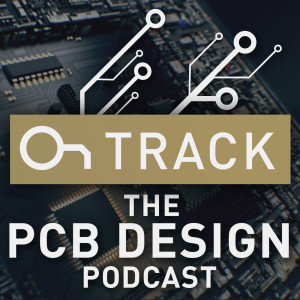
Tuesday May 28, 2019
Printed Circuit Fabrication Classes at Michigan Tech
Tuesday May 28, 2019
Tuesday May 28, 2019
In this episode we’re filming at Michigan Tech with guest Dr. Chris Middlebrook who teaches a class on Printed Circuit Fabrication. Watch or listen in on our first OnTrack Field Trip as we sit down in Dr. Middlebrook’s lab, where they make circuit boards right on campus. We talk about students, the education program at Michigan Tech and all the hands-on work they do to prepare Electrical Engineers for the real world.
Trade In Your Outdated PCB Design Tool & Unlock 45% OFF Altium Designer today!
Show Highlights:
- Dr. Middlebrook has been a professor at MTU since 2007. At this engineering-focused university, they take a hands-on approach to help create engineers that are well-versed in practical design and implementation.
- What is MTU doing regarding the shortage of talent in the industry? The resurgence in manufacturing across all sectors calls for students being fully equipped and they strive to equip their students with the necessary skill set to drive the next generation of technology.
- Several lab spaces enable students to get hands-on with chemical and wet processes as well as prototyping and research, board etching and development. They work in small groups across campus.
- Calumet is very close to campus, they have been instrumental in the success at MTU, involving their engineers and scientists to get things up and running, they supplied much of the raw materials.
- Students eagerly sign up to tour the Calumet facility once they have experienced all the processes in class. Student feedback is very positive.
- Why is there a disconnect from the hands-on side of this work pervasive in most universities? Costs of materials and chemical sets is a primary factor. Not many students are interested in tinkering with things but that mindset is changing.
- What else can the industry do to support this initiative? Lab sponsorship, one concise, larger facility as a showpiece would make it more practical and create more opportunity for visibility to parents and students.
- More interaction and mentoring is something students respond to very well.
- Guest lectures pique student interest and broaden their experience across the spectrum.
- Topics covered in lectures: From electroplating within PCBs, to solder masks to assembly and multi-layer press to the future of this industry by Happy Holden.
- Positive elements of the Millennial culture: They’re very knowledgeable, already know where they are and where they want to be, they do a lot of things before getting to University.
Links and Resources:
Trade In Your Outdated PCB Design Tool & Unlock 45% OFF Altium Designer today!
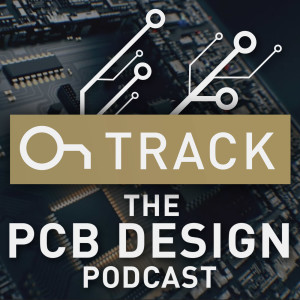
Tuesday May 21, 2019
Altium VP on New Library and Data Management Tool Concord Pro
Tuesday May 21, 2019
Tuesday May 21, 2019
Lawrence Romine, VP of Marketing for Altium, is here to discuss the release of Altium Concord Pro and it’s aim to provide a fresh approach to library and component management. Romine describes the modern, streamlined experience that reduces context switching, keeps communication in sync and enables an information flow that dramatically improves workflow, productivity and accuracy. We also talk about Altium Designer 19.1, what that includes and what you can expect from this performance-based release.
Trade In Your Outdated PCB Design Tool & Unlock 45% OFF Altium Designer today!
Show Highlights:
- Lawrence started his career in electronics like most of us. His father was an EE and since the age of ten, he knew what he wanted to do - it was always engineering. His career of 20 years has evolved through the selling or business-end of engineering.
- He started in design with a particular interest in Audio at McCormick Audio from where he became involved in the semiconductor business working for Insight Electronics, selling and supporting Xilinx. In his search for more involvement with software, he joined Altium where he’s had a varied career over the last 15 years.
- What is Concord Pro? A library and component on-premise solution that works with Altium Designer and includes the MCAD collaboration capabilities which support Solidworks, PTC, Prio, and Autodesk Inventor.
- Concord Pro is very simple; it’s focused on library and component management to include an on-premise server.
- How is Concord Pro different to Vault, NEXUS and NEXUS Server? NEXUS Server is a rebrand of Vault, and the aim was for it to become a regulated ‘or gated’ design process. It made sense at the time to consolidate Vault under the NEXUS umbrella.
- Define the NEXUS ‘Channel’: NEXUS is a process-oriented solution, not a product, comprising configurable off-the-shelf modules; that Altium Configures and deploys on the customer’s premises with a joint agreement on the outcome - it’s applicable across the board; irrespective of the size of the company.
- A good example of successful deployment is in a smaller medical device manufacturer, which has a rigorous process to which they must adhere.
- Why was there a change from Vault to NEXUS? Customer surveys about library management confirmed that elements of NEXUS Server didn’t truly fit the profile of customers in the traditional Altium Designer Channel. Everyone has a need for reliable library and component management which considers supply chain information, ideally during the design phase but it doesn’t mean they need full lifecycle approval capabilities or to enforce any rigor in the design process itself, for example, gating of approval processes. These elements have been removed from Concord Pro, to make it more streamlined for the majority of users.
- What happens to Vault and Nexus Server users now? For current subscribers, it’s a free, painless move to Concord Pro. If you’re not using TC2 or the lifecycle approval process, all you need to do is update your existing product.
- For those that are using TC2 and lifecycle approval capabilities - just keep doing what you’re doing.
- Vault and Nexus will be maintained but not added to or sold individually going forward. Features will, however, be added to Concord pro.
- How does the ECAD-MCAD integration work? With Altium Concord Pro, we have a bi-directional push-pull arrangement with Concord Pro as the intermediary. So, you can make changes in one environment or the other, be it ECAD or MCAD - and the genesis of those designs can start in one domain or the other and push those changes into the other environment.
- As soon as an engineer emails a file, it’s no longer the most recent version, because they continue designing - check out the Concord Pro Page.
- What many engineers and designers are creating and calling a Bill of Materials is indeed a parts list. What Concord Pro brings to the table is enabling users to create a Bill of Materials as they go and this applies to everyone.
- Do take advantage of the 60-day evaluation offer on Concord Pro.
- Moving beyond Concord Pro, what’s on the horizon for Altium? We want to continue our aggressive growth and enhance the capabilities of our tool as our users are requesting.
- We are releasing Altium Designer 19.1 with a significant focus on engagement with the customer across the board where our customers congregate. There are significant investments in the stability and performance of the product.
- We listen to the customers and address what they tell us they need. We will continue to give our users a stake in the product and give them a voice.
- We are also looking towards the next 3D.
- What initiatives does Altium have in regards to raising the game on BugCrunch? We definitely listen to BugCrunch. We prioritize our action according to the number of votes received.
- We are paying attention, our developers are addressing a large number of issues daily. We will do more regarding responding or communicating to the users because a user’s perception is their reality.
- BugCrunch participation is not overwhelming; we need to inform users that it is their voice, and we need to do better with acknowledging and engaging the user.
- Shout out to Kelly in Salt Lake City - the largest Altium Designer user group, who are voting collectively to get their votes to the top of the priority list.
- What keeps you here personally? I’m still here because I chose this career path, business is about sales and marketing, which is ultimately about the narrative - the story - and this is a hell of a story. People are better off at the end of the process.
- We put out a solid product and we have a great ‘why’. We focus on the user first, we engage bottom-up and it’s working really well.
- Our sales process is unique - we believe that the user is the decision maker.
Links and Resources:
Podcast with John Watson
Concord Pro Page
Concord Pro Tutorials
Do Smaller Companies Need Data Management? Podcast
Altium BugCrunch
Trade In Your Outdated PCB Design Tool & Unlock 45% OFF Altium Designer today!
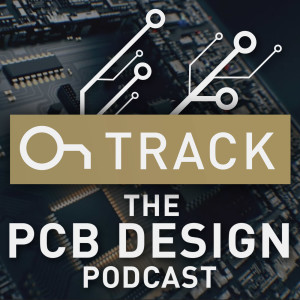
Tuesday May 14, 2019
Dk And How Datasheets Impact Your Design
Tuesday May 14, 2019
Tuesday May 14, 2019
If you design in RF, microwave or millimeter wave frequencies today’s podcast is for you. Today we talk to John Coonrad who’s the Technical Marketing Manager for Rogers Corporation, a Global Manufacturer of advanced circuit materials. John talks about what dielectric constant (Dk) is exactly, the various test methods for Dk, why datasheets can sometimes be confusing and how all of this impacts your design.
Trade In Your Outdated PCB Design Tool & Unlock 45% OFF Altium Designer today!
Show Highlights:
- John has been in the PCB industry for 32 years. His journey with Rogers began back in ‘87 when they had a division called FID (Flexible Interconnect Division) - he jokes that he was born and raised on flex circuits!
- For the past 11 years, John has been working specifically with the RF characterization of their materials as well as marketing and has been published in several trade magazines. John also chairs the IPC D24C Committee which defines high-frequency test methods for the industry.
- A working definition of Dk: The property of a material to sustain an electric charge by applying an electric GIL to it.
- In other words, dielectric constant is the ability to hold a charge and also to affect the electrical properties in regards to capacitance.
- On datasheets, the Dk can be inconsistent, which means that various manufacturers could provide different values because of how they’re testing which depends on what segment of the industry they’re serving.
- Rogers is unique because they choose to differentiate between Design Dk and Process Dk.
- Rogers performs a raw material test and does not test circuits.
- Using a clamp stripline test there is typically some trapped air, which has a lower dielectric constant and will cause a lower Dk overall.
- TIP: It’s helpful to check what test was performed when comparing datasheets.
- Currently, Rogers uses a test method specific to their in-house requirements which is process control as well as good QA test of the raw material, which is the Process Dk.
- Another test method is looking at how the Dk of the material is perceived in circuit form, i.e. testing microstrip transmission line circuits and extracting the behavior of the RF performance to get to the Dk of the material in circuit form - which is called Design Dk and provides a more realistic/real-world number.
- Bottom line: different test methods deliver different values.
- Other test methods out there: IPC has 15; the clamp stripline test is most common; full sheet resonance non-destructive test (FSR); split post dielectric resonance (SPDR), etc
- Because of the way electrical fields move through the dielectric, it’s not all about the traces, but the laminate has a massive impact, which is another reason why John’s work is so critical.
- As the chip industry evolves, there are more applications for millimeter wave frequencies - the higher the frequency the smaller the wavelength, making it more sensitive to any differences in material.
- With millimeter-wave frequencies, small differences in value can cause significant problems, especially in the automotive industry.
- Implications of incorrect Dk: Depending on the application, such as military guidance systems and base station equipment the Dk obviously has to be spot on.
- Pervasive misunderstandings that impact design engineers today: Not everything is taught in training institutions - for example, TCDk (temperature coefficient of the dielectric constant of the material) is often not accounted for. Circuit influences are also not accounted for but plated finish can affect the phase.
- How to learn about TCDK? Some sources: IEEE website; manufacturers of materials, and Rogers as well as John’s articles (see below).
- What’s driving more applications in the millimeter range? Designers and manufacturers of chips are now able to provide much higher frequency applications. The chips are being used for more varied applications.
- Is the increasing speed limiting PCB manufacturing? As you get to the higher frequencies, the features are very small and thus must be well-defined to avoid even little etching anomalies causing disruptions.
- What enabling technologies are emerging? For circuit fabrication, LDI is a definite plus. Regarding additives, some companies such as Averatek are doing excellent work and may be a potential solution.
- Thinner copper also enables fewer problems with surface waves. There’s also coupled circuit features.
- The line between chip design and board design could blur and we may adopt the precision and miniaturization.
Links and Resources:
Tech Hub
Rogers and Autonomous Driving
Rogers and 5G
Website Tools Page
Rogers ACS YouTube Page
Trade In Your Outdated PCB Design Tool & Unlock 45% OFF Altium Designer today!
Read additional articles:
The Influence of Test Method Conductor Profile and Substrate Anisotropy on the Permittivity Values Required for Accurate Modeling of High Frequency Planar Circuits, read here.
Methods for Characterizing the Dielectric Constant of Microwave PCB Laminates, read here.
Read additional articles on the Microwave Journal:
Searching for a Standard Millimeter Wave Dk Test Method, read here.
Compare Materials in a Meaningful Way, read here.
Which Dk Value is Right for my Computer Simulation, read here.
Changing Temperature Can Change Circuit Performance, read here.
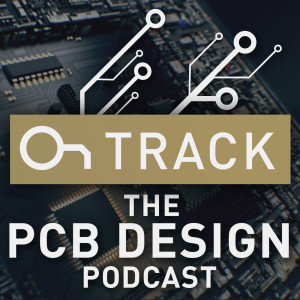
Tuesday May 07, 2019
Datasheet Reliability with Ben Jordan
Tuesday May 07, 2019
Tuesday May 07, 2019
When are datasheets accurate and can we rely on them? Ben Jordan is back on the show to discuss datasheets and how to achieve reliability for your use case. We also cover an unusual question from the forum about gilding that you won’t want to miss. Ben always enjoys catching up with the Lounge Forum, and this week, one of our users, Tim Philips, posted a datasheet that he had come across for an inductor. Listen in to explore these topics in this episode of the OnTrack Podcast.
Trade In Your Outdated PCB Design Tool & Unlock 45% OFF Altium Designer today!
Show Highlights:
- The question: “I ran into an unusual datasheet from Murata, for a common mode choke and on page 7 it says: ‘Do not use a gilded pattern. The copper wire may cause open by dissolution of metalization’ - question is, what does ‘gilded’ mean?
- The answer: Gilded means gold plating - solder plated over hard gold just doesn’t work.
- This is a good example of how crazy datasheets can be, and it’s apparent that this was translated from another language.
- Lee Ritchey always says: “app notes, should be assumed wrong unless proven right”.
- This whole question of app notes and whether you can trust them is very important. For example application notes often advise separating the analog and the digital ground, to reduce electrical noise. Which is not necessary.
- Application notes are often produced by IC Engineers, who have no exposure to field theory and their conservative nature is aimed at the worst case scenario in various industries such as medical, aerospace and automotive where people’s lives are at stake.
- What’s the solution to unreliable datasheets?
- That’s where your training comes in. Starting with reference designs is good, but it’s just a starting point, you need to apply your engineering knowledge.
- You have to speak to applications engineers, who know products and did testing to compile the data–you have to verify.
- Measuring yourself, there are no shortcuts to actual measurement, you must have a test lab due to the ‘overkill’ of most sheets.
- Dan Beeker also says: “datasheets may be functional, but could result in higher BOM costs”.
Links and Resources:
Altium Lounge Forum
Rick Hartley on The Importance of PCB Stackup
Dan Beeker presentation "It’s all about the space"
Eric Bogatin: AltiumLive talk on measurement
OnTrack Email: ontrack@altium.com
Trade In Your Outdated PCB Design Tool & Unlock 45% OFF Altium Designer today!
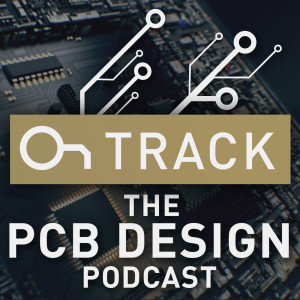
Tuesday Apr 30, 2019
Sourcing Components with Christopher Calvi
Tuesday Apr 30, 2019
Tuesday Apr 30, 2019
The Head of Octopart®, Chris Calvi is with us today to talk about sourcing components, which has never been more challenging than it is today. Chris will also share his vision of the future where sourcing components will be easy, accurate and fully transparent.
Trade In Your Outdated PCB Design Tool & Unlock 45% OFF Altium Designer today!
Show Highlights:
- Chris attended Georgia Tech and after graduation he moved to LA, where he worked at Shopzilla, a consumer product search engine. He has 13 years’ experience in vertical search engines both in Business Development and General Management roles. He’s been with Octopart in New York for eight years, of which he’s served as GM for the last three years.
- Octopart was started in 2007 by three Physicists in Grad School. Due to problems with manually finding electronic parts in thick catalogs; the idea of a search engine was born.
- All three dropped out of school and thanks to Y Combinator program, Octopart got off the ground.
- Today there are between 800 and 900,000 users on the site monthly.
Octopart works with over 200 distributors who make it possible for the user to access the database for free. - The database gives access not only to the parts but also availability, validating, finding CAD models, symbols, footprints, 3D and exploration of technical details of each component.
- Part shortages is currently a huge problem especially with ceramic capacitors and LCCs.
- Octopart has a similar parts feature on the part detail page.
- The search criteria are very smart which is very helpful for everyday decisions.
- Availability and approved vendors lists as well as backup distributors are also available.
- Feedback is very positive regarding signals of risk and particularly lifecycle status.
End of life is a huge problem in applications such as aerospace and even on the repair side. - Octopart offers authorized channels or sources where the manufacturer has formal relationships with distributors. Octopart will have the authorized components come up first in your search.
- Compliance documentation and government regulations: there are restrictions on hazardous substances or chemicals - all part of the ‘problem set’ of selecting parts which Octopart strives to address.
- Vision and strategy for Octopart: First aim is a user-friendly solution. Second aim is for Octopart to be the go-to source for any relevant data on electronic components.
- Another aspiration is transparent structured data (information on where parts come from, last update, etc.) is essential for the future of electronic design and manufacturing.
- Machine learning and automated part selection applications means much more opportunity in the future.
- Obstacles now: Unstructured data, no data standards.
- CAD Tools and API: Application Programming Interface means you can tap into the database irrespective of what design tool you're using. This interface is another goal of Octopart and one that is receiving attention.
- For programmatic access to our electronic part search capabilities and part database, go to: Octopart API
- How are Altium and Octopart connected? Octopart serves as the parts enterprise unit for Altium. As Altium brings digital continuity; Octopart strives to bridge the gap as a structured data piece.
- Octopart is for everyone, not only Altium Designer® users, but also the makers, students, professional engineers, sources and procurement folks etc.
Links and Resources:
Octopart
Octopart API
Search parts by technical spec
Free ECAD models
Similar Parts (alternate parts)
Advertise with Octopart
Join the Octopart newsletter
Careers at Octopart
Trade In Your Outdated PCB Design Tool & Unlock 45% OFF Altium Designer today!
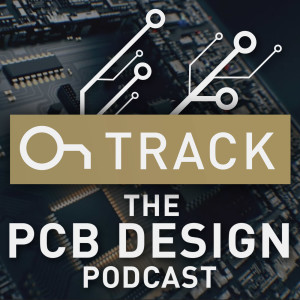
Thursday Apr 25, 2019
What to Look for in a Board Fabricator with Steve Williams
Thursday Apr 25, 2019
Thursday Apr 25, 2019
Do you know what to look for in a new Printed Circuit Board Supplier? Today’s guest, Steve Williams, is the President of TRAC, also known as The Right Approach Consulting. Today he will share his tips, based on his visits to thousands of shops around the world, on what to look for in terms of certifications and how to look beyond the marketing and window dressing to source the ideal, reliable board supplier who will get the job done.
Trade In Your Outdated PCB Design Tool & Unlock 45% OFF Altium Designer today!
Watch the video, click here.
Show Highlights:
- Steve started in the industry in 1976. He gained extensive experience as a Senior Manager in the board fabrication industry, followed by 15 years in QA, evaluating companies for best practices and technologies which proved how many companies out there needed help.
What to look for in a good board fabricator:
- Engineering Support: What kind of support do they have, how deep is their experience, and expertise? This combined with their people and the kind of software they use could save you a ton of money regarding materials selection in particular.
- Cleanliness: You can identify a good board shop by their FOD (foreign object degree) and what effort they make to keep it clean. Yes it’s a board shop but a dirty shop is an indicator of their culture and practices that affect performance and product quality.
- Dendritic growth is contamination on the surface of the board, that becomes encapsulated in the soldermask and will eventually galvanize the contamination leading to shorts from one trace or pad to another once the board goes under power, this is definitely something you do not want.
- Modern Equipment Sets: Are they keeping up with technology? If all of the equipment is old, it shows that their scope is very limited.
- Do they have Via fill, laser drills, planerizers, LDI, Inkjet printing, etc? This shows whether they’ll be able to support ongoing technology.
- Merit Badges; Such as QMS certifications, has become a first screening tool. Also, IPC training of employees signifies management’s commitment to quality; customers expect that. There should be trained IPC inspectors on staff.
- ISO Certification, must be part of the company culture, they need to be ready without prior notice for an audit. It should be a top-down culture within the company.
- Is the shop busy? Another indicator of future performance is how much activity there is. An empty is shop typically an indicator of something being out of place, even during economic down times.
- Speak to some of the employees, are they happy? You’re not going to get a good board from an unhappy employee, if the company can’t take care of their employees, how are they going to take care of their customers?
- IPC Validation Services is an excellent program. Most validated companies say that customers love it, and it’s been good for them, another priceless merit badge and a great differentiator.
Links and Resources:
Trade In Your Outdated PCB Design Tool & Unlock 45% OFF Altium Designer today!
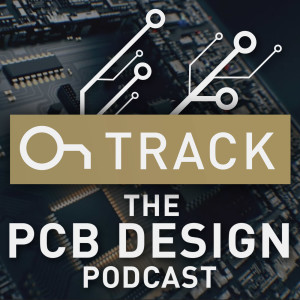
Tuesday Apr 16, 2019
EMC and Signal Integrity with Dan Beeker
Tuesday Apr 16, 2019
Tuesday Apr 16, 2019
Our guest today is Dan Beeker, Senior Principal Engineer at NXP Semiconductors, who is well known for addressing EMC and signal integrity in a really fresh way. Dan has presented twice as a Keynote Speaker at AltiumLive, both in San Diego and Munich. The information shared in this talk is extremely practical and valuable. Listen in, this information will impact the designs you do every day! Remember, it’s “all about the space”.
Trade In Your Outdated PCB Design Tool & Unlock 45% OFF Altium Designer today!
Watch the video, click here.
Show Highlights:
- Dan started out with Air Force electronics training followed by his role as Motorola’s microsystems Group Test Repair Technician, and now Dan is the Senior Principal Engineer with NXP.
- You’ve presented twice at AltiumLive events as a keynote speaker, called “It’s all about the space” What does it mean, it’s all about the space?
The real key to successful engineering is the realisation that it is energy moving through space. It’s critical to design the spaces. The concept that the energy moves through wires, is what led us to where we are today. In the past where switching was very slow, it didn’t matter, however, as technology changed and switching sped up, we saw higher failure rates in EMC. - We reduced the size of the antenna required by an order of magnitude, practicing circuit theory without realising that energy moves through the laminate (the space). Energy also moves through the board space from one dielectric layer, up to a higher one.
- Why do you think engineers and designers alike lose this perspective along the way? It’s somewhat confusing, because geometry cannot be imported. Many still believe that the energy transfer is instantaneous. If that were the case there would never be signal integrity problems because energy transfer is much slower.
- This is also happening because the physics side of electronics engineering is made out to be something that’s quite difficult. There is a lack of cohesion between the science of energy and its reality and what we’re teaching people.
- The fundamental concept is we design products that generate, manage and consume electromagnetic field energy, not electrons. This field has to be in a space.
- Physics trumps theory!
- Five minutes into that class I knew that everything I had ever designed, had worked by accident! Rick (Hartley) became a friend and a wonderful mentor.
- Ralph Morrison taught me the importance of physics and that the energy was in the spaces and not the traces. He said: ‘People travel through the halls and not the walls, signals and energy travel in the spaces not the traces,’ which inspired my song.
- The geometry of the spaces has proven to be extremely successful with the help of my mentors.
- Finding great mentors is crucial.
- If you’re still in school, pay attention, take the extra time to talk to your professors and connect the dots of the behaviors of the electromagnetic field.
- Electronics is a world of three’s: You can store energy, you can move it or you can convert it into kinetic energy - that’s it, the entire electronics world!
- This is not an extremely complicated world for managing electromagnetic fields. You have three components: a conductor, a dielectric, and a switch. This isn’t rocket science, this is plumbing!
- You have to have to start using ground as a pointer object within your board stack. The common conductor from the source of the energy to the place where that energy is consumed, next to a common dielectric, so that the ground and the dielectric next to it, is unbroken from the source of the energy to the destination.
Technical conferences where you can see Dan Beeker speak:
- Embedded Systems, Boston in May
- PCB West in September
- Embedded Systems, Santa Clara this year
- NXP Connects in October, in Detroit
Links and Resources:
- It's all about the space song
- Ralph Morrison website
Trade In Your Outdated PCB Design Tool & Unlock 45% OFF Altium Designer today!
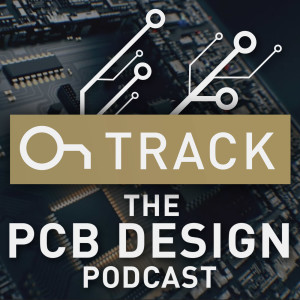
Tuesday Apr 09, 2019
Design for Reliability with Yizhak Bot
Tuesday Apr 09, 2019
Tuesday Apr 09, 2019
Today we talk to Yizhak Bot who started his career in the Israeli DOD, and today he will share with us what derating is and how you can work on the schematic level with their simulation software to eliminate field failures. With a background including about ten years working with the reliability of very big systems gaining much insight into how systems work and fail, Yizhak is an expert you’ll want to listen in and learn from. Today he is the founder and CTO of BQR Reliable Engineering.
Show Highlights:
- Yizhak was a sponsor at both previous AltiumLive conferences and at the most recent, he spoke about the technology that BQR offers to engineers who lay out boards.
- A few common design errors that lead to field failures are: 1. Sudden CPU reboots, for example in aircraft - imagine an in-flight computer failure. 2. With safety- and non-safety functions together on one board, the non-safety functions will affect the safety functions - they need to be separated. 3. If you have a DC to DC converter - you’ll want to test if the voltage is correct and remember to connect them to the same ground, in the field it can be difficult to establish where the problem originates.
- What is derating as discussed at AltiumLive? You cannot use any component, current, or junction temperature running at its maximum rating; you must derate it.
- Integration, quality and field tests cannot find all failures that may occur because you cannot test all the combinations; using the simulation tool ensures your design is robust.
- Tell us about Fixstress and what inspired you to develop it? We wanted to find something to check for issues before products are in the field. We developed a tool that calculates stress levels of components, and a schematic review which detects design errors.
- Additionally, the simulation can do a thermal analysis and MTBF prediction to complete the analysis for the designer.
- What is the impact on your customers when using Fixstress? Almost zero failures in the field leading to the longevity of products.
- What kind of applications do you address and in which geographic regions? Mostly in big systems such as aerospace, also trains, automotive, shipping, telecoms, gas and oil, server farms, wind farms, power distribution. Our geographic market reach currently is the USA, Canada, Brazil, Europe, UK, Sweden and the Netherlands as well as China, Singapore, Japan and starting to work in Korea.
- Most of our growth is due to mouth-to-mouth referrals and clients asking sub-contractors to use the technology.
Links and Resources:
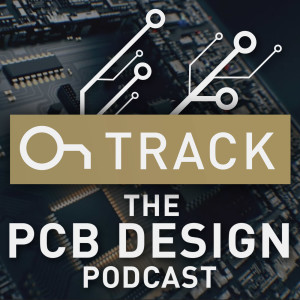
Tuesday Apr 02, 2019
Materials 101 with EIPC Chairman Alun Morgan
Tuesday Apr 02, 2019
Tuesday Apr 02, 2019
Meet Alun Morgan, Technology Ambassador for Ventec, a world leader in the production of high quality, high performance copper clad laminates and prepregs with a world-wide distribution network. Alun interacts with customers around the world promoting Ventec materials, and brings the latest market requirements to Ventec in order to develop new products.
Watch the Video here.
Show Highlights:
- Alun is a Material Scientist, with a B.Sc. Hons in Metallurgy from the University of Surrey. Once he became involved in PCB manufacturing he found it such a fascinating field that he has spent his entire career refining his knowledge.
- Everything Ventec does can also apply to smaller scale operations who are making PCBs.
- Alun was a Keynote Speaker at AltiumLive
- The FR-4 we use today has it roots around 60 years ago; there was an FR1, 2 and 3, as well as FR-5. According to the NEMA specification from the 1960s, FR is defined as Flame Retardant.
- FR-4 also means the fourth generation of materials in the NEMA classifications system. It defines the resin kind and the reinforcement type.
- FR-4 is an epoxy resin and the reinforcement is typically woven glass fibres for strength.
- The substrate itself is a composite of these two materials; the resin, the reinforcement and the conductor which is copper.
- Why the different composites? The main reason is its strength, it’s a very good insulator, and it’s available. It also bonds chemically to glass fibres very well.
- Lead-Free soldering created a major change about 20 years ago when lead was banned from electronic assemblies causing a range of performance issues.
- Higher temps expand materials dramatically, and because there is no reinforcement in the Z-axis, the expansion is considerable.
- When materials are heated beyond the TG, or Glass Transition temperature, thermal expansion is rapid and massive.
- The solution to this is adding inorganic fillers to modified, lead-free compatible materials to reduce the Z-axis expansion of which there are several types such as silica-based materials.
- Losses impact - some inorganic fillers have lower loss than the epoxy resin they’re replacing.
- How to choose materials? Talk to your manufacturers about the correct materials, ask which material they use the most and which of them work most successfully. Do beware of SI though, as this is a very fast-moving aspect currently.
- It is strongly advised to attend materials courses, and ask questions. Ventec is always ready to assist and answer questions. Go to a boardshop and see how these things are produced.
- Alun is also the EIPC Chairman and anyone involved with PCBs is welcome to attend their events. There are two conferences every year and the next will be in Austria, on June 14th and 15th. This will include a facility tour of ATNS, the biggest grossing PCB shop in Europe.
Links and Resources:
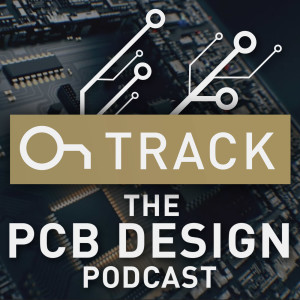
Tuesday Mar 26, 2019
From CAD to PCB: The Data You Give Me and What I Actually Do With It
Tuesday Mar 26, 2019
Tuesday Mar 26, 2019
Gerry Partida, Director of Engineering at Summit Interconnect Technologies, a world class PCB Fabricator, is back to discuss your data package and what he actually does with it. Gerry began his career in the Printed Board industry in 1984 at Everett Charles Test Equipment and joined Optrotech/Orbotech in 1986. He was a member of the team that introduced CAM automation, net list compare, AOI Cad Reference to industry. His current position is focused on cutting edge high density interconnect, high speed digital, Flex/Rigid Flex and RF/microwave printed circuit board fabrication for the military and commercial industries. He is a certified IPC trainer, and a member of the IPC-6012 and IPC-6018 review committees. He is an excellent resource for a wide-range of PCB related topics. Listen to the discussion and learn how to produce an excellent data package which will save you time, money and increase your reliability.
Watch the Video here.
Show Highlights:
- Data has to be modified for manufacturing
- 60% of jobs go on hold due to questions on the documentation
- What data is necessary for a boardshop? One set of Gerber Data for all the layers, legend, solder mask, all the circuit layers, all the drill files, and an IPCD 356 Netlist
- Ensure formats and resolution of Gerber and drill file settings have the same resolution
- What is unnecessary? Title blocks, crop marks; dots showing location on non-plated drill holes, zero sized apertures
- Often the hole count doesn’t match the data received
- The dimensions on drawings often do not match data
- Verify the count and quantity
- When last-minute updates must be sent to fabricator, send ONLY the file pertaining to that layer which the board shop can incorporate. Avoid sending an entirely new data set. This will force the fabricator to verify all the data all over again.
- Always consider the reliability of design: drill diameter, aspect ratio, annular ring, drill to copper, and environment product will go into
- A fab drawing should not be an estimation but a quality tool used to verify that the board was built to all the requirements.
Links and Resources:
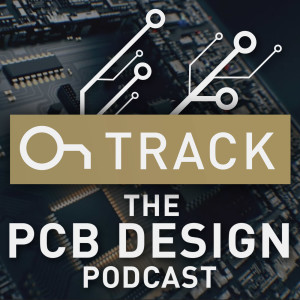
Tuesday Mar 19, 2019
Why Protect Vias and What is IPC 4761?
Tuesday Mar 19, 2019
Tuesday Mar 19, 2019
Why do we need to protect vias? Here to answer is Gerry Partida, Director of Engineering at Summit Interconnect Technologies. Summit is an advanced technology manufacturer creating custom printed circuit boards. Summit focuses on complex rigid and rigid-flex products and offers extensive expertise in RF/Microwave applications. In today’s episode, Gerry will help us untangle IPC 4761 and get actionable info that you can apply to your designs.
Watch the Video here.
Show Highlights:
- IPC 4761 comprises design guidelines on seven existing methods of via protection
- Combinations: Capping one side vs the other side, dry film soldermask with soldermask over, or via plugged with solder mask capped over with soldermask or not, plated shut via epoxy filled and plated over, or via and pad also known as Type 7 which is popular for HDI (High Density Interconnect)
- Why protect Vias? To prevent solder paste from running down an open via to the other side of the board, preventing solder balls on the secondary side, moisture protection, sealing to prevent chemistry entering and becoming trapped, to ease the subsequent processes, and finally assembly
- For via protection with a surface finish like ENIG or ENEPIG, both sides of the via need to be open during the ENIG or ENEPIG process.
- IPC 6012 Class 3 now prescribes the same thickness for copper wrap plating
- Why do people fill? Primary reason is to get the via at the pad connection in the component
- When you’re talking about High Speed Digital, you don’t want to go from trace to via
- Place via in land to avoid delay and reduced real estate for routing
- Slight reduction in reliability when via is plated, epoxy-filled and plated over versus a via only plated in the final
- Peel strength is much lower when you epoxy-fill is in the center and plated over
- You have to buy IPC standards
- Encroach soldermask clearances - encroaching soldermask on top of the LAN but not in the hole is an excellent solution.
Links and Resources:
Click here to view all Episodes
Or click here to access the Altium Designer Free Trial Today.
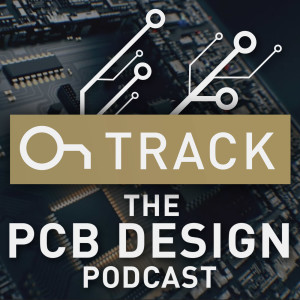
Tuesday Mar 05, 2019
Bolt: Part Venture Capitalist, Part Engineering Team and Pure Awesome
Tuesday Mar 05, 2019
Tuesday Mar 05, 2019
In this episode of the OnTrack podcast we have as our guest; Tyler Mincey, who is the VP of Engineering for Bolt. Bolt is located in San Francisco and Boston and is a hybrid venture that is part venture capitalist and part engineering team. Bolt offers a unique model to help startups get off the ground, and get product to market.
Watch the video here.
Show Highlights:
- Tyler’s background is in product design, especially the intersection of hardware and software product development
- Worked at Apple at new product development team for 5 years
- Digital agency in New York, doing web app and mobile app development in UI/UX
- VP of Product at Pearl Automation - automotive aftermarket startup
- Bolt - Mechanical, hardware and software as well as product development
- At Bolt we are a venture capital firm and we invest in concept-stage businesses developing technology products.
- Usually there is a physical aspect. We help companies develop feature sets and get traction in the market. We help build companies while they’re growing and have full time engineering resources to support the portfolio companies.
- Startups are different: More resource constrained, and less marketing muscle after launch
- Why did Bolt adopt a model that includes engineering support?
- When you need to create a physical product, these technology products require a lot of cross functional work completed, for a startup there are a lot of needs that can’t be fulfilled.
- The things available today make it possible for companies to create things faster and on smaller budgets than ever before.
- Project Vive is a good example of a new technology company that would not have been possible before.
- Bolt has about 70 portfolio companies at the moment: B2B companies, sensor systems, wellness devices, medical devices, and direct to consumer electronics.
- Digital native protocol brands, such as flower delivery services, or baby formula and other physical goods with the same challenges in design, quality control and logistics and acquiring and retaining customers.
- Bolt Portfolio Page
- Interested in companies building out infrastructure for space.
- What are common mistakes you see? We see people falling in love with the concept of their own product. We encourage companies to test with real customers as soon as possible. The product needs to be tested and iterated upon. Try to frontload the market validation as much as possible!
- Can people succinctly communicate the value of your product? Will word-of-mouth work?
- Does it have a snappy, succinct selling point?
- Is the experience of using it so sticky they don’t want to stop using it and they want to tell all their friends about it.
- Validation and verification of just their product specs is one side. Engineering the actual technology is a separate track. Often people couple these together as one, but you can really do both in parallel.
- Why Bolt? Why Startups? There is a culture of sharing in software that hasn’t happened yet for hardware. We try to distill information here so people can tap into shared knowledge and if possible, avoid pitfalls that other people have already experienced.
- A few favorites: Core Wellness - guided meditation trainer, a consumer product with beautiful industrial design; OrbitFAB - orbital gas stations for refueling in space.
- Pitches can be submitted on Bolt’s website.
Links and Resources:
Tempo Automation - turnkey PCB fabrication
Core Wellness - guided meditation trainer
OrbitFAB - orbital gas stations
Submit Your Pitch to Bolt
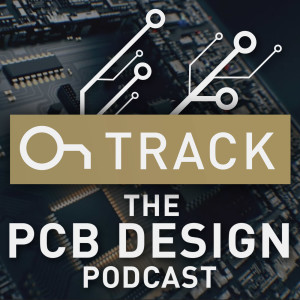
Tuesday Feb 26, 2019
Semi-Additive Process Technology at Averatek
Tuesday Feb 26, 2019
Tuesday Feb 26, 2019
In today’s OnTrack Podcast Judy talks to Mike Vinson, the COO of Averatek about their breakthrough innovation in which they use a semi-additive process incorporating a liquid metal ink as the catalyst seed layer. This special catalytic precursor “ink” can be imaged to create the patterns or areas where conducting metal is to be deposited. This ink controls the horizontal dimensions of line width and spacing and creates the ability to get down to 1 mm and sub-1 mm line and traces. Keep an eye on this technology! Welcome to the future.
Watch the VIDEO HERE.
Show Highlights:
- Mike’s background is in semiconductors primarily in the area of interconnects.
- At Averatek they create HDI solutions.
- What does Averatek’s technology enable engineers and product developers to realize? Lower layer count, Improve Yield, Cost reduction and High Value
- What is Semi-Additive Process Technology? Fundamentally the ink carries plating onto the surface of the substrate, depositing them in very thin layers.
- Also called atomic layer deposition - Averatek calls it lipid metal ink.
- Process allows for very precise and very small circuits.
- Learn the jargon: SAP (Semi-Additive Process).
- Copper can be left undisturbed by the etching process.
- Can be run in a traditional board shop - new technologies are emerging.
- Lithography capital equipment is indeed a worthwhile investment.
- Liquid Metal Ink where are you in getting this to market? Strategy is to license and sell liquid metal ink.
- What type of design considerations will EDA tools need to build-in to enable design with this technology? Smaller lands and increased density.
- Evolution: Lines & Spaces first then other areas.
- Thieving areas parameters will change.
- This tech will work for both flex, rigid-flex, and rigid circuits.
Links and Resources:
Email: mike@averatek.com