Episodes
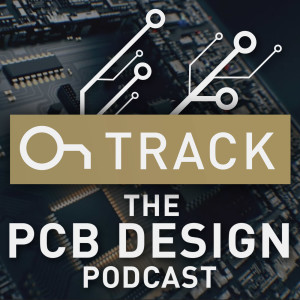
Tuesday Feb 19, 2019
Am I Big Enough for Data Management?
Tuesday Feb 19, 2019
Tuesday Feb 19, 2019
In this episode of the OnTrack Podcast we echo the style of “Ask me Anything” and feature Ben Jordan and Judy Warner who will mine the AltiumLive forum for questions. Ben will answer your questions about Engineering and PCB Design and Judy will respond to topics related to manufacturing and supply chain. Join us today as we tackle the question: If we have only one or two EEs, do we really need data management?
For future episodes, you can submit your questions on the AltiumLive forum, and sign up to be part of the community. Or email your questions directly to us.
Watch the video here.
Show Highlights:
- The Lounge is where the community talks about interesting topics related to PCB Design and Electronics Engineering, not necessarily only Altium products.
- Today’s question from the lounge is: “Is the Altium Vault really worthwhile in a company with just two EEs??” Perhaps another way to pose this question is: is it worth having a formal data management system for your electronics design, if you’re only a small business? We could even ask, is it worthwhile for an individual design contractor? The short answer is: Absolutely!
- Statistics and analytics from webinars, show that 80% of designers do not even use a formal version control system.
- A version control system allows you to have a central location for storing data, and as you work and make edits, and save files; it must be committed to the system as a revision.
- Version control allows you to go back to any point in time and restore it. Also, it allows comparison changes, in context, in a team or if you’re an individual designer.
- A normal backup system does not give you associativity between that moment in time and what you were doing, or the engineering intent.
- A version control system is not a formal data management system: it doesn’t give lifecycle management or links to supply chain data.
- A true data management system would not permit release unless everything is saved, committed to version control and contains the latest revision. Including in the component library.
- Provides accountability in the way you use and store your data.
- What are some problems with footprints in manufacturing?
- Panelization, v-cut, scoring for breakaway tabs etcetera, not following procedure.
- Slow down to hurry up - spend time upfront to set up the system, then you can move faster.
- Documentation is essential in the industry for re-use and provides a lifecycle.
- Data management keeps you accountable.
Links and Resources:
Join AltiumLive forum, and check out The Lounge
OP’s original question and related question
Email new questions to: OnTrack@altium.com
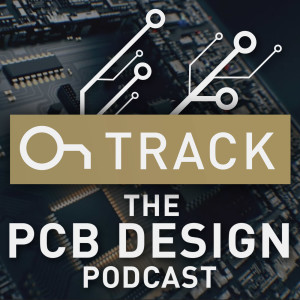
Tuesday Feb 05, 2019
Printed Electronics Applications and Innovations
Tuesday Feb 05, 2019
Tuesday Feb 05, 2019
The use of printed electronics is on the rise, and Chris Hunrath from Insulectro is here to talk about how to design for it. Learn about the different applications and design possibilities that are available to PCB designers. The proliferation of more advanced printed electronics materials from polyester film, polycarbonate, to transfer film for fabric and flexible circuitry have enabled interesting new applications for printed electronics. Listen in to learn the latest from Chris Hunrath, an expert in material supplies for circuit board design.
Watch the video, click here.
Show Highlights:
- Insulectro has seen a significant growth in sales of printed electronics products, this is an area of massive growth.
- Printed Electronics have traditionally been used in RFID along with metal f
- oils such as anti-theft devices and security access cards - items with conductive inks and membrane touch switches, for example: coffee makers, dishwashers, rear window defoggers, etc.
- Interesting new applications include: glucose test strips, wearables - sensors of all kinds, automotive, and self darkening windows.
- Self darkening windows are used in skyscrapers and aeroplanes, silver conductive ink, placing current on the window, giving the user control and saving energy.
- Printed Electronics is a high-growth area: business doubled every year in the past five years, doing very well in both substrates and inks.
- Predominant applications driving this uptick in usage: Capacitive Touch switching, in general it saves costs, lighter in weight and has no moving parts (i.e. car dashboards: a lot of work being done on it today) makes it more reliable.
- The molded structure: print the matte side and ink moves with plastic when molding, circuitry is totally encapsulated in the injection molding process.
- Ink technology: silver is used and is cheaper than gold and more conductive; silver flake or conductive particles make it possible to have the ink move with the plastic.
- Insulectro offers materials for Printed Electronics, some examples: polyester film - trade name Mylar and other brands, polycarbonate, transfer film for fabric and flexible circuitry in wearables.
- What’s the difference between conventional and printed electronics? Conductivity, and Resistance - know the sheet resistance and use a comparable copper thickness and width.
- Altium Designer 19 and Tactotek, who do in-mold structural electronics are working on relative design features in Altium.
- Printed Electronics whiteboard video
- There are inks that can sense chemistry and can be ion selective i.e. blood glucose, natural gas, carbon monoxide and so forth,
- Applications in wearables: Neural bypass, can pick up nerve impulses, movement sensors, chemistry sensors and more, and can withstand several washings.
- Higher silver loading inks can be used in many different applications.
- Chris shows an example of printed antenna that uses silver inks.
- Can be used in materials that you couldn’t use in a traditional PCB process.
- Conductive ink kits for children - you can draw conductive inks with a pen.
- Chris shows an example of substrate with high temperature ink, that has a 500-degree operating temperature.
- Events where you can see examples at the Insulectro booth: IPC Apex in San Diego, DesignCon in Santa Clara and Insulectro typically at IT TechEX.
- Conductive adhesive is more ideal for components, soldering to printed electronics is very delicate.
- Screen printing is the main way to print and is very scalable.
- Printed electronics is easier and cheaper to get started and environmentally more friendly.
- Stay posted for more developments in this exciting field!
Links and Resources:
Tactotek IMSE / Printed Electronics Podcast
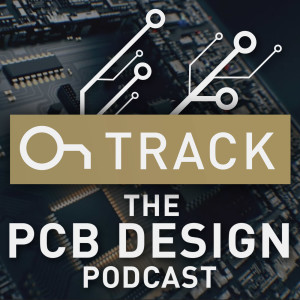
Tuesday Jan 29, 2019
Embedded Capacitance and Embedded Passives with John Andresakis
Tuesday Jan 29, 2019
Tuesday Jan 29, 2019
Listen in to Judy Warner and guest John Andresakis from DowDupont and learn about embedded resistance materials. There are several benefits that make this a beneficial technology. Did you know that you can take up to 90% of your decoupling caps off the surface of the board, while improving reliability and reducing inductance? Learn about several design considerations for using embedded capacitors and build on the knowledge of experts like Rick Hartley and Eric Bogatin who both addressed inductance in their AltiumLive San Diego keynotes.
Watch the video, click HERE.
Show Highlights:
- Senior Technical Marketing Leader - Interconnect Solutions at DowDupont; 30 years experience mostly on the materials side and now at DowDupont, soon to be the new Dupont.
- Embedded capacitance -cross connections with: Rick Hartley's keynote at Altiumlive (inductance) and Eric Bogatin's keynote as well
- This reduces inductance
- Film based materials now allow embedded capacitor layers to be 1 mil or below with excellent yields
- People were practicing some form of this 30+ years ago, but according to patents 25 years or so. There used to be material concerns, but with the advanced materials i.e. improvements in technology more is possible.
- What manufacturers are providing this service? Most of them!
- It's like a version of a rigid flex, without the flex part sticking out.
- This isn’t a very hard thing to implement, it wouldn’t be difficult for the manufacturer to get up to speed on this. The things involved are not difficult to learn.
- Learn more at IPC APEX - stop by DowDuPont and Insulectro - booth 624
Links and Resources:
IPC Standard: 2316 Design Guide for Embedded Passive Device Printed Boards
DuPont Interra HK04J Planar Capacitor Laminate
IPC Standard: 4821 for embedded passive devices
Rick Hartley on the Importance of PC Board Stack-up at AltiumLive
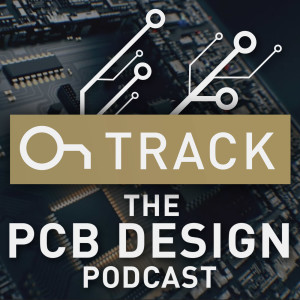
Tuesday Jan 08, 2019
Electronic Components Shortages, Insights from John Watson
Tuesday Jan 08, 2019
Tuesday Jan 08, 2019
Electronic Components Shortages, or part shortages are so big that it impacts nearly every aspect of electronics design and manufacture. Lead times continue to rise no matter how fast parts are being produced. It is just not possible for production to catch up. The reality of this current shortage means it’s time to be innovative, and guest John Watson has some ideas to help including an expert tip Altium Designer users can put to good use. (Hint: ActiveBOM can help!) Listen in to get background on the electronic component shortage, what pro PCB designers are doing to address the concern proactively and stay ahead of PCB component shortages.
Show Highlights:
Shortages first started with capacitors - specifically with multi-layer ceramic capacitors (MLCC) MLCCs - 3 trillion created a year but the supply is still not meeting demand
This is a major crisis in the industry and its spreading
The part shortages are so big, it impacts every aspect. Shortages affecting: Board sensors, MOSFETs (metal-oxide semiconductor field-effect transistors), Resistors and Transistors. Previously unaffected supply chain areas are now being affected.
No matter how fast these are being produced, not possible for production to catch up.
There are three industries driving the high demand that is leading to part shortages:
- IoT - estimated 20 billion new IoT devices in next few years
- Mobile phone - 1.5 trillion mobile phones in next year. 1,000 capacitors in each phone.
- Automotive - 2,000 - 3,000 capacitors in regular / 22,000 capacitors estimated in electric car - as newer technologies are being pulled into regular automatic cars, just think of all the electronics i.e. safety features, automatic parking, etc.
New automotive organization:
AEC - Automotive Electronic Council is putting out standards that will be required for their components. Why? Because...
More rigorous components are needed in order to perform in harsh environments.
Almost 50% of those components have fallen out, or failed, to meet their tests.
On the component / part manufacturing side:
Converting lines from large components to smaller ones because not many people buying them.
Manufacturers shutting down entire lines so they can produce more popular sizes.
On the vendor side:
Vendors have moved towards part allocation - big companies get first in line for parts.
“You can only buy parts with if you have bought with us in the past year” - this is allocation.
Once a company is in allocation, they begin to stockpile components.
What kind of lead times are most common right now:
Short lead time - 16 weeks
Medium - 32 weeks
Long - 80 weeks
What makes this part shortage so different?
Mainly a market driven shortage, that cannot be pinpointed to a specific material shortage
It’s almost an ‘emotional shortage’ where people may be hoarding more than they need.
The extended duration of it is also unlike previous shortages.
It’s a scenario where the market compounded onto itself with its reaction to it.
HOT TIP: The next big thing is Broadband Satellite. SpaceX and low flying satellites to make everybody wireless. This is huge, it’s a lot of hardware.
Component Shortage Hacks to get through the Crisis:
- Overall, be as proactive as possible.
- Evaluate common design guidelines and step out of them. For example, can we change the norm values, parameters and tolerances? It doesn’t always require the most stringent guideline, there is room for adjustment, depending on the type of device and requirements.
- Be proactive, for example run your schematic through ActiveBOM and get flags on what components are not recommended. Don’t wait until layout, do it early on.
- You can also use Octopart, there are other free services.
- Leverage your procurement organization, give them the heads up with difficult components so they can be aware of the situation in advance.
- Create multiple footprints for designs.
- No single sourcing for components, don’t get tied into a single organization.
Where do you source parts or find out about availability during the shortage?
- Read the quarterly reports to get the latest, look at the numbers, watch the trend.
- Keep aware of the issues i.e. part availability reports
- Texas Instruments also has a lot of information.
PCB Component Shortages and using ActiveBom:
“ActiveBOM came out just in time. It has been the go to tool for us.”
Now we run legacy products through ActiveBOM.
Links and Resources:
John Watson Podcast on PLM and Library management
OnTrack article about Part Shortages
Watch John Watson clips on Youtube
Download the latest Altium Designer 19 today.
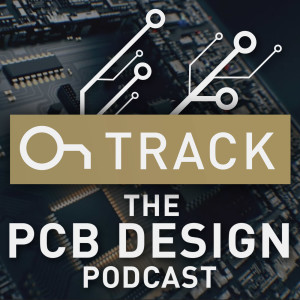
Tuesday Dec 18, 2018
Altium Designer 19: Highlights from the Latest Release with David Marrakchi
Tuesday Dec 18, 2018
Tuesday Dec 18, 2018
Altium Senior Technical Marketing Engineer, David Marrakchi is here on the show to talk about Altium Designer 19. This latest release is part two of three major releases Altium has planned to level up high-speed design capabilities. As an engineer who likes to wear multiple hats - and with experience in the field as an Electrical Engineer - David has done it all from developing requirements to schematic capture and PCB layout, across industries including home automation, military, and medical. Now he is bringing his rich skillset to the intersection of innovation and implementation by helping people understand Altium Designer and how to get the most out of the PCB design tools, easily and in the least amount of time. David is an inside expert on Altium Designer sharing his expertise on the overall processes of PCB design and product realization; playing a major role in creating product demonstrations, webinars, whiteboard videos, and interactive articles that illuminate the processes of printed circuit board manufacturing.
Watch the Podcast Video here and see more Altium Designer 19 videos.
Show Highlights:
Altium Designer 19 is released. David is hosting webinars to demonstrate new features. You can join live or on-demand--sign up for live webinars here: https://www.altium.com/webinars
What’s new in Altium Designer 19?
High Speed Design Features: What they are and how do they help designers?
- Advanced Layer Stack Management: Impedance solver, material library (vast array, pre-defined) and microvia support. Very important for tracks carrying high speed signals.
- Micro via (more info in the Interactive Routing webinar)
- Impedance modeling
- Material values - (there are always new materials coming out!)
New Part Search:
- Find a part that both meets requirements and that is also available!
- Search and filter with parametric information - global parametric supplier search. i.e. size, package, height, frequency, stock, model, and compare two parts.
Routing Improvement:
- New follow mode (allows for locking i.e. curves)
- HOTKEY / SHORTCUT: ctrl+f to lock to contour
Trace Glossing Improvements
Draftsman
Multiboard
Printed Electronics
Check out this Podcast with Tactotek to learn more.
Altium has a culture that embraces a mindset of continual “Relentless Innovation”
Some users say they’d rather us fix more bugs--why do we choose to continually innovate?
What value do you think this commitment to innovation provides to our users and the design community as a whole?
If you are an existing Altium Designer User you can download the latest version now at Altium.com.
If you are new to Altium Designer, we invite you to get behind the wheel and take it for a test drive and see why Altium has become the fastest growing PCB Design company in the world.
Links and Resources:
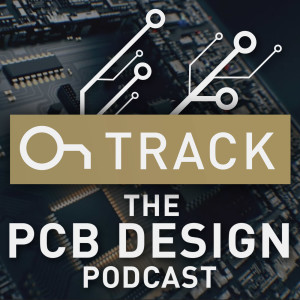
Wednesday Dec 05, 2018
Stephen Chavez Calls on PCB Designers to Get Involved
Wednesday Dec 05, 2018
Wednesday Dec 05, 2018
Stephen Chavez is a leader at a military aerospace company, former Marine, CID and CID+ instructor as well as an Executive board member of the IPC designers council. With 28 years in the industry and heavily involved with IPC, Stephen has a passion for PCB design and fabrication. If you want to keep learning or get involved in the industry, Stephen will encourage you to get connected, step out of your comfort zone and pay it forward. Listen in and get great tips about where to find training and how to push yourself to keep learning.
Listen to the Stephen Chavez Podcast or watch the video here.
Show Highlights:
The Best Professional Development:
- AltiumLive Munich - learn more or register today
- IPC APEX, San Diego - manufacturing perspective, fabricators, if you don’t have time to get into a board shop this is the place to be, machines are running live
- PCB West - pure design for PCB designers; content is second to none
- DesignCon
- Del Mar Electronics and Design Show
- PCB Carolinas (1,000 people/ 1 day conference)
- IPC Designers Council, etc.
- CID Training
- Reading--Trade magazines - UP Media (Printed Circuit Design & Fab and Circuit Assembly) and 007 iConnect - the articles and content in these magazines are the best.
Get Involved!
- Ask around (for resources, help, mentors)
- Take Risks and take initiative--spend money, assert yourself
- Serve/Volunteer
- Networking/Relationship building
Live part of everyday outside of your comfort zone
- Don’t be afraid to ask questions--others have the same questions and dont ask!
- Expand your network, meet people
- My network comes with me in every new relationship I build
- Add value to others
- Don’t sit on the sidelines
Links and Resources:
The Digital Route, November 2018 Column
Breaking the Design Data Bottleneck, interview in iConnect007
AltiumLive Munich - learn more or register today
Altium Designer 19 - learn more or call your account manager to learn more
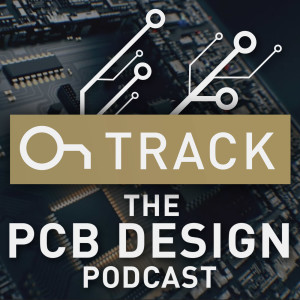
Wednesday Nov 21, 2018
Wednesday Nov 21, 2018
John Mitchell, CEO of IPC, is advocating for the electronics industry workforce in Washington D.C., and participating in the Pledge to America’s Workers. Listen in and learn how IPC has joined in pledging 1 million new job opportunities for the industry, when John shares a "state of the union" about IPC’s current direction.
If you’re a current IPC member, you’ll benefit by finding out all that IPC is up to these days and and how you can get involved. If you’re not an IPC member or not sure what IPC is - you will get a lot of value from this conversation just by learning about this incredible industry force and all that’s available, including educational programming and career development opportunities.
See the show notes and links to all the great IPC resources at: https://resources.altium.com/altium-podcast/john-mitchell-ceo-ipc-visits-the-white-house-pledge-to-americas-workers
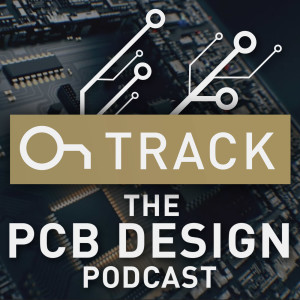
Tuesday Oct 09, 2018
AltiumLive 2018 Panel Discussion
Tuesday Oct 09, 2018
Tuesday Oct 09, 2018
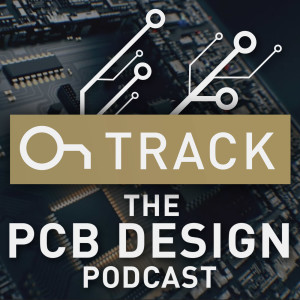
Tuesday Sep 25, 2018
Manufacturing Documentation with Duane Benson
Tuesday Sep 25, 2018
Tuesday Sep 25, 2018
Manufacturing documentation is crucial. Get pro tips from Duane Benson of Screaming Circuits on how to deliver the ideal manufacturing documentation package, so all the technical details are documented exactly as needed. Every fabrication and assembly house is different, so it pays to prepare in advance and find out what documentation to produce for your design to be manufactured. You don’t want to miss this week’s episode; it’s full of practical advice so you can navigate fabrication and assembly effectively and know what to expect in this very complicated process.
See all the show notes here.
Show Highlights:
- ActiveBom - use it! Excel is not the best tool for designing with.
- Traditionally a manufacturing house needs Gerber files. It’s a text file that creates a bit-map.
- More advanced/new way of doing this is with a single file, the most popular being is ODB++ (was proprietary, now public domain)
- What is Gerber X2? Allows you to put intelligent data on top of the Gerbers.
- Once you pick a fab or assembly provider, call and find out what files they prefer. It’s complicated to explain, so call your fabricator and assembly house.
- When you send multiple files, send the same versions. It’s really common to see different versions of files because small changes were made but not all the documentation was updated.
- IPC specifies pin location but so many of the footprints don’t follow the IPC standard.
- This is not a “no touch” process.
- If you need a fast turnaround, then be available 24/hours a day to provide answers and get back to manufacturer immediately. It’s a complex job, things happen.
Ideal Manufacturing Files:
- Everything is current and same version - everything checked
- Read me file - cover anything non-standard, covered clear and concise (include stackup)
- BoM in Excel format, possibly with substitutes
- Intelligent file formats i.e. ODB++
- If Gerbers, include Centroid file and certified that rotations are correct
Hey everyone this is Judy Warner with Altium's OnTrack Podcast thanks for joining again. You will see a familiar face on the screen next to me, but we have a great new topic to talk to you
about that I think you'll find very compelling. Before we get started you know, same old stuff.
Please subscribe to the podcast, please let us know your ideas for future topics, and also
follow us on social media. Of course, I would like to be connected to you on LinkedIn. On Twitter I'm @AltiumJudy and Altium can be found on all the usual social media channels. Something I
don't think I've mentioned before on the podcast is that I also edit the newsletter for Altium, and it also carries the OnTrack brand, so it's the OnTrack Newsletter. Duane Benson who is with me today - from Screaming Circuits, has actually been featured in that newsletter and you can find that at resources.altium.com and also in that area of our website, you can find just oodles
of information. So many, many blogs on subjects you can filter by topic and I think you'd really enjoy it. So again that's resources.altium.com, so jump in and enjoy that.
Well Duane Benson's back again from Screaming Circuits, we connected again recently and we were talking about the the kind of muddy waters of manufacturing files and formats and what it's like for someone like Duane to deal with a variety of issues that come up and so I thought, as
PCB designers, that you would like to learn some tips and tricks - kind of what some of the obstacles are - and get familiar with some language if you're not already, and then hear from an expert of what a manufacturer - what a really good design Manufacturing file package looks like. So Duane, welcome back.
Thank you, thank you for having me I had a lot of fun on the last podcast and you know I have weird, geeky interests, and manufacturing files is one of them, so anytime I get to talk about one of my weird geeky interests, I'm happy.
[laughter] Well I track with that weird geekiness of you, so I know we talked - preparing for
this podcast - it should have taken like 20 minutes; we just went off on a bunch of different topics but hopefully you'll enjoy the results of our geeky conversations. So let's start out with
just defining what you are characterizing as manufacturing files?
Well there isn't a real solid definition of what a manufacturing file set is, but if you think about an electronic design of some sort that starts with an idea in an engineer's head, and it becomes
schematics, it becomes a Bill of Material, it becomes Gerber files, layout files, things of that sort.
Essentially it's an electronic file set of everything that an engineer would feel would be needed to describe their product, and it's in a format that a company like us, an assembly house, and a
board house and part supplier, can read to turn that idea into a working board. So there's an awful lot of things that go into it. You have to describe the raw PC board, you have to describe the components, you have to describe the assembly, and anything special or unique about it. So the manufacturing file set is all of those things necessary for someone, who is not you, who is not in your head, to take your design and turn it into a working board. Well in the case of electronic manufacturing service I think kind of one of the central pieces that comes to mind for me is the Bill of Materials.
So you want to touch on that hot mess? [laughter]
The Bill of Materials really is a hot mess, it is one of the most important files. Unfortunately, this doesn't get the highest profile because it's not you know, the design. That's the bit that everything starts when we're building a board, everything really starts with the Bill of Material and that includes, a typical Bill of Material is again, that's what we need in order to communicate with the distributor to buy your parts, so it will have the manufacturers part number and every single character in that manufacturers part number is important. Some of these things are twenty characters but those little suffixes may determine the temperature grade or something like that, or how its marked, or how it's packaged all that's important as well as the manufacturers name. So you've got the manufacturers part number, the manufacturer's name, and in theory that should be enough. But we always like to be able to double-check things, we always like extras for quality control, so we would like the value of the component as well. So, if it's a 0.01 microfarad, 16 volt 0805 capacitor, we would like that, and then a package size. Again that's a double check, so if we get something that's not even close we can tell, hey that's not the right part. Then we also need the reference designator on the board, that's what tells us where the part goes on the board - the reference designator - and then a line item so that we can easily identify it. If we have to call the designer and say, you know hey this part doesn't fit, we can say it's line item six on the Bill of Materials.
So that was manufacturer, manufacturer's part number, the value, the reference designator, and a line item that we can use to identify it. Other things can go into the Bill of Material, but that's really the minimum set.
And I think, in my - at least, my experience in the past - and you can correct me here, because I'm not as adept as you are here. But I've seen Bill of Materials that are a little messy, and they only have part of the part number, so they just put in the part they know and then you're like, what do I do with this?
Yeah you know, a lot of Engineers have told us that they would love to be able to say, I just want 2.1 microfarad, 16 volt or greater cap, that's it and that's all fine and dandy if you know that, all those other parameters don't matter. A capacitor; it has the dielectric specifications, it has ESR or ISR specifications - you as the designer know if those things matter or don't. We as a manufacturer, don't know that they matter or not. If they don't matter, then sure it'd be awesome to be able to just pull some random capacitor, but we don't know that. So they need to know every single bit of that part number so we can get exactly what you want. That's a bit of a challenge, especially with capacitors and resistors these days, because of allocations - these things come and go out of stock so fast and, so anytime one of those parts is in the Bill of Material and it's out of stock, we've got to call up the engineer and ask for a substitution because again, we don't know if they need a high or a low ESR part and we've had cases where you know someone will send us a Bill of Material in the morning and if we go back to the distributor the next day, some of the parts are out of stock it's just absolutely crazy.
-Yeah.
What that says though, is the important thing is, when you create your Bill of Material, what you're doing over time as you put your design together, make sure that the very last thing you do before sending those files off to the manufacturer, is to verify that those parts are still in stock and if not, find a substitute that you know will work.
That's a good - that's a very good point being the last check. You had asked me a little bit
about a feature inside of Altium Designer called ActiveBOM, so I did a little checking with Ben Jordan about that and so what I learned about that is that it's an interactive BOM management
tool, that's inside the design and it has multiple output files. You can scrub it at any point in the design process kind of like you're saying, do it at the end, but you can do it throughout the design process, and it will tell you the ability to parts, it can help you find alternatives. When you change a part in design it changes the BOM…
-oh nice, I love it.
Nice right, I know, and then flags will appear, like if you're designing and something is at risk of going out of stock, or end-of-life or whatever, a flag will appear on the BOM that will tell you; we better go check this one out and see what's going on. So those flags come up also kind of in real-time throughout the design process so I think that's a really helpful tool and you know I think a lot of designers that are using our tool are jumping into that because I think it would be a
really valuable kind of aspect of our tool. But I know some haven't either, so I just wanted to jump in quick - if you are using Altium Designer and you're not using ActiveBOM, use it
because I think it's an invaluable tool.
Yeah a surprising number of people just use Excel and well, that's what we end up needing, we need an Excel file as the output, but it's not the best tool for designing with.
I know and it's kind of amazing that you know, we can create these little suckers and we're still
doing our BOMs on Excel spreadsheet but, there you have it.
So why don't you go over the type of outputs that are say from a CAD tool - like Altium Designer or any other, the type of outputs that you would typically see?
Okay and this is where the industry is really on the precipice of change, but we're still stuck in the old world. Traditionally, a manufacturer like us, and a board fab house would need a set of Gerber files - and most people know what Gerber files are - if they don't it is a file - a set of files - and there's one file in each set for each layer. So copper would have - top copper would have a file, it is a text file, but I like to describe it as a one bit depth bitmap because it's a text file that creates a bitmap. So you can't, you don't at the moment, have any intelligent information in there. A pad for a component looks exactly like a trace, looks exactly like a pore, so that is the way it's done today but it's not optimal, so you've got the Gerber file set again - one file for
each layer - so you'd output that from your CAD system and you'd put that into a zip file and that's what we would call the Gerber files. Within your CAD system, quite often people will have
an assembly instructions layer, or a fab notes layer, make sure you put those in the Gerber files also, because those are the only real opportunities to integrate information into that Gerber file.
Now if you're going to have the boards assembled, you'll also need something which may be called a centroid, that's what we call it, some people call it a pick and place file, and that has the XY location on the PC board of the component. It has the reference designator, again that's why we need reference designators, and it has the rotation of the component zero to the orientation and the top and bottom side. So Gerbers - with Gerbers you have to have that centroid, or pick and place file, otherwise we don't know where a component goes. That's the basic set and then we would also like something that would have notes that tell us the layer stack up you know, which layer goes where. That's really the minimal set. You also, if you have things like some people for example, don't want to put reference designators on their board and silkscreen. That's really a bad thing, but for aesthetic reasons people don't. Well, then you need a set of fab drawings that tells us where the reference designators are, so that would be another thing that you would need to go in there.
Also in the fab notes would be, if you have overhanging parts for example, these little tiny USB micro-b connectors hang over the edge of the board, and they've got a little tab that goes down. Well if you're having your boards panelized and it's either a v-score or tab routed panel, you can't do that, and build that part, so you have to specify in the fab drawings: don't put a panel tab here, things of that sort. If you've got any special requirements, special material requirements, impedance requirements, ITAR or anything like that, again would go into the fab drawings. So, and the fab drawing can be in your Gerbers, in that fab layer, or it can be a PDF separately, but it has to be clear about what is where. Now that's the old way of doing things, which is still the current way of doing things in most cases right. There are a couple of industry movements to create intelligent CAD files that tell an awful lot more, so you can have one file that has the layers, it has the layer stackup, it has information, the XY information, it has all of that contained within the single file. The most common one of those, in use today is called ODB++, and that was a proprietary file format, but I believe that it's been released into the public domain now. If you can output ODB++ which your software can, that's an awesome way to deliver the information to your assembly house. And you notice I said 'assembly house' there; for some reason the fab folks are often behind the assembly houses in these new file formats because the Gerbers work perfectly well for building up a board.
It is so true, although I have seen more of the modern, more complex, the board houses that do more complex things, they typically have ODB++ integrated throughout their factory, it really leads to more reliability, I think it's a good thing - and of course IPC 2581 right?
Mmhmm, that's the next one good.
Which has been, I was looking it up the other day preparing for this, and I was thinking its' been like 10 years, it's been a long time coming. And I don't know all the ins and outs, but I looked it up, it was started in 2004.
Wow [laughter] 14 years ago!
I mean, I thought it was a long time, but 14 years, and again I don't know what the stop gaps are, but like you said, almost every CAD, I think all the CAD manufacturers output those files
Gerbers, ODB ++, 2581. You talked to me a little bit about Gerber X2 - can you tell me a little bit about that?
Gerber X2 - I have no idea if it's going to catch on or not, or if it's going to be a viable solution, but at some point, the consortium that manages the Gerber standard, decided they'd better get with the program or Gerbers were gonna go away, so they have proposed a new standard, Gerber X2, and I don't think it goes in as in-depth as the ODB ++ or the 2581, but it does allow you to put intelligent data or metadata on top of the Gerber layers. So as I said with today's
Gerbers - I can't tell if a piece of copper is a pad or a pore, it allows you to do that sort of thing, so you can connect up what components are where and whatever information is needed to assemble them. I don't believe that that specification has been signed off on yet and I have a feeling that it's going to be a little bit of a 'too little too late' but I'm just speculating on that point so.
Yeah, and also IPC has, I think you mentioned to me, the D3-56 which is test points right?
Yes, they have I believe, they have test points, I think they even have the full IPC 2581 specification it even has room for the Bill of Material.
That's my understanding.
Yeah I think it's a whole cohesive across all the fab and all the assembly processes but again, it's not something I know a lot about and of course your NC drill files for fabrications. What
else do we need to talk about?
Well one of the, because those file formats are in such flux right now, one of the most
important things to do, is once you have picked an assembly partner and a fab provider, give them a call or send them an email and say, hey what do you prefer? It's even complicated to explain this so I have to tell people, if you have Gerbers send us the Gerbers, and if you're sending Gerber send us the centroid and any Fab or assembly instructions. If you've got ODB++ send us that, but still send us the Gerbers, just in case we need them with the fab house and we need the centroid for this, but not for this...
[laughter] Oh gosh.
Call your fab house...
Can you just send us everything in every format and...
-and that you know, the law of unintended consequences pops up there sometimes
because we will get someone who sends us Gerbers and then we'll say, hey by the way, do you have an ODB ++ and they say yeah, so they send that off. Awesome; except it's a different version. When you send multiple types of files, make sure they are all of the same version, saved at the exact same time...
-the revision it's a different revision you guys... okay. Keep your revisions, keep your old revisions out of the mainstream.
Yeah, what we found is it's real common for, even after a designer hits save for the very last
time, and sends off their files they'll tweak the silkscreen or they'll say, that component wasn't
available, let me use this one and they make these tiny little changes but sometimes it's going to a different package or you know, that part was a 'do not stuff' so let me just take it out of the design now, and so we get different versions of files literally two days apart.
Oh god bless us all, I don't know how we survive this industry. When Duane and I were
preparing for these, this podcast I was saying, you know I left the industry for 12 years and I knew there'd be like a crazy catch up, but when I came back I said I felt like Rip Van Winkle.
I can feel like Rip Van Winkle after leaving for a weekend sometimes [laughter] and I'll
think everything's cool and then Monday...
Yeah he says, I feel that way every Monday [laughter] it's so flippen true!
It is you know, I'll walk out on the manufacturing floor and one of our engineers will say,
hey Duane, because I'm out in the outside world a lot and he waves me down and shows me some component and asks me, have you ever seen this before? What do they do with this? What are we supposed to do with this? And it's like. Oh yeah, I kind of read about that, and I talked to an engineer at a trade show, about that, and it changes so fast and you know, the
changes are not slowing down, they really aren't.
And we're managing them with spreadsheets and multiple file formats just to make it fun.
Yeah and you know, some of it, is our own fault. Because we like to do things fast and you know companies, there are a bunch of companies like mine, who have decided that, gee everybody needs to do this faster than they used to be. And years ago, when I was on the OEM side, to get a board built, it was typically three or four weeks to get it quoted, then three or four weeks for he NPI process, before anybody gets that out in their line. Well those six to eight weeks, we now do in six to eight hours. And so, when you have all that much time, you can go back and forth to the
engineers, you can ask questions. Now you know, 2:00 in the morning one of those questions that were you know, years ago we would have had a week to get answered, now we need it, you know it's 2:00 a.m. we need the answer by 2:10.
We can't blame everybody else, we have to blame ourselves a little bit too.
Right.
I'm gonna blame you. All your fault Duane [laughter] anybody asks me from now on I'll go, it's
Duane's fault. I think a lot of our manufacturing folks would say the same thing, if Duane would just stop promising that.
Right yeah, exactly.
You mentioned a few problems that kind of come up during the chaos of all these different issues that we face and one thing was relative to rotation on IPC standards. Can you talk about that for a moment?
Yeah that's one of my pet projects or 'pet something.' The IPC specifies which pin should be at what part for zero rotation so you've got zero, 90°, 180°, 270°, 360° and anything in between, and what direction goes from zero to 90° on the front or the back, it's specified, it's in these standards, and these ones have been around for a long time. Well what I've found, is a large number of the footprints in CAD software, especially the CAD software that relies on user-generated content more than professionally generated content, a lot of those things, the zero - the pin1 zero rotation is wrong. So for example with an LED or a diode, the cathode is on the left, its horizontal pin one is on the left, and that's zero degrees rotation. We see them where zero degrees rotation has something vertical at 180 degrees, pin one on the right, all sorts of nutty things like that, and that's probably 80% of why we simply can't rely on data maybe even 90%. Theoretically, you should be able to output a set of files from CAD software, send it to a company like ours, and never talk to us and just magically get boards back. A huge portion
of why we can't do that is because so many of these footprints don't follow that IPC standard, and if it were a rare exception, well we'd assume they all do and catch the rare exception there. It's so common, that we have to disregard anything that any of our customers tell us about rotation. Which means we have to have someone look at every single part on that board.
Oh my gosh! It's like a bad version of pin the tail on the donkey. Can you guess which one is pin 1? Have a nice day - oh on all these parts - oh my gosh I don't know how you do anything fast.
It's crazy…
But the cost, I mean some of these parts are super expensive and if you rotate them the wrong way, and you fry them or you wreck the board like, that was a bunch of money.
Yeah we have we run across $10,000 FPGAs we come across ‘one of a kind' parts that are going into some space mission so yeah we really can't risk putting those things on wrong, I'm sorry there are only four these parts in the world don't blow it, okay.
Well and do we - like you said so new parts come out, but when new parts come out, sometimes the standard hasn't been written yet correct?
Yeah we saw that a lot in the early days of the QFNs you know, QFNs all the leads are underneath around the outside of the part and there's this big metal heat slug or ground slug in the middle of the part. The IPC standards didn't cover that yet, and a lot of the CAD software folks had never heard from manufacturers so they didn't know what to do with it. The footprints all had that big heat slug wide open, so then what happens, you put solder paste on that, there's a much higher aspect ratio of heights to volume in the center pad, so the part rises up, it kind of floats up and then all the pins on the outside don't connect and for years, for a few years, nobody knew how to do that, how to make that work properly. Again, if you've got a three week NPI cycle you can figure that out, but when you're doing it overnight... So we determined that you need a window pane solder paste stencil. Fifty to seventy-five percent cover to paste, and it works, but it was a couple of years before the rest of the industry caught up to that and with the tiny, tiny BGAs, point four millimeter pitch BGAs changed the rules on the pad and solder mask with larger BGAs you want non-solder mask defined pads, so you want the solder mask opening to be a little bit larger than the copper. Well with the point four millimeter pitch and
smaller BGAs, that causes the solder balls to squish, and you get bridging.
So you want a solder mask defined path?
Again the rest of the industry didn't keep up with that, because the component manufacturers threw these parts out, without figuring out how to build them...
That's wild.
Yeah and a lot of fun too, I think [laughter]
For those of us that are masochists and gluttons for punishment. [laughter] Okay in all that craziness that you've just spelled out for us. So for our listeners, tell us what a good or a great set, like a clean set of manufacturing files would look like if you could wave a magic wand, and you'd want to see a really clean set of manufacturing files come in?
Okay first of all, everything is the current and the same version, and everything was checked and double-checked just before sending it off to us. There would be a readme file, that includes anything that's non-standard is covered in that readme file, and it's clear, to the point, not wordy - it's not prose, including things like the the stack up. It would have a Bill of Materials in Excel format that has the information we talked about, and possibly even a few substitutes. And then
ideally it would have one of the intelligent file formats like an ODB ++ or an IPC 2581 - that would be the ideal format. If you're stuck with Gerbers, then it has to have a good set of Gerbers. Again with that stack up documented and a centroid file and of course we would love it if someone could could certify that their rotations were correct so we could believe the centroid file but that's really it. Ideally intelligent manufacturing files, a bill of materials, and Excel and a readme file and then if you are using Gerbers, then the Gerbers and the centroid.
Good - well hopefully that will help, hopefully people listen to this podcast and give you some cleaner manufacturing files Duane.
I hope so.
So, something you pointed out to me though, even if you got the perfect set of manufacturing files, we're not robots, and you said something to me: this is not a 'no touch' process.
Yeah.
-you can not throw it over the wall and go about your day so let's wrap up with your thoughts on that.
Well communicate you know, I saw a bumper sticker once that said: I didn't spend four years in engineering school to talk to people. [laughter] But the fact of the matter, you know, we will talk to you using a few sentences. We'll make it short. But talk to us, and anybody who's building your stuff, don't be afraid to pick up the phone and call them, or to have an email exchange.
I know we - a lot of us nerdy people/geeky people whatever, don't like talking to people.
But we have to, and do that, do not be afraid. And if you've sent your boards off, and you're expecting a fast turnaround time, be available 24 hours a day. Companies like us will typically work 24/6 or 24/7, and as I mentioned before, if something happens at 2 am, and things do happen you know. So yeah do we continue the build without it or stop and wait for more? We may need an answer at 2 am - be available, make sure that someone can get a message at 2 am, and then get back to your manufacturer as soon as possible if they contact you. And then do understand that yes, we are all human, we know you're all smart people and we're all smart
people, but everybody... you know it's a complex job we're trying to do
Extremely complex, god bless us all for even attempting to do it, but we do it. We do it and a lot of times we do it quite well so kudos for us in the industry. Well thanks for those tips and kind of clarifying what a clean package will look like. I know it's kind of a convoluted - there's no clear, single path forward. So I think that's really, it's kind of really basic but as you can see from our conversation it's a lot more complicated than it appears on the surface. So thank you so much Duane, for taking the time to clear that up and let us know what works and hopefully give some good advices to some designers out there.
Well thank you for giving me the opportunity I always enjoy these opportunities you know.
We enjoy having you always, and I'm sure we'll have you back again.
So well, that's it for our OnTrack Podcast today, thanks again for joining. Please drop us a message, let us know what else you'd like to hear about. Tune in next time. Until then, remember to always stay on track.
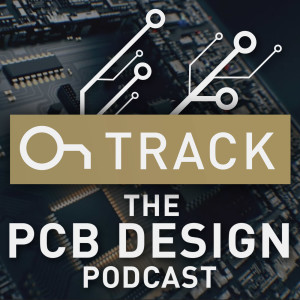
Wednesday Sep 19, 2018
Quick Turn Circuit Board Fabrication with Royal Circuits
Wednesday Sep 19, 2018
Wednesday Sep 19, 2018
From Tesla to consumer devices, Mihir Shah has been a PCB designer among the best. Now, as Director of Special Projects at Royal Circuit Solutions, he is pioneering ways to make manufacturing easy for printed circuit board designers. Meet Mihir and Jon Lass, co-founder and VP of Engineering at Royal Circuits, and listen in as they discuss manufacturing best practices and share various insights on symmetrical stackups, solder mask, and copper weights. Get a wide range of PCB design tips and learn how same-day turn times on printed circuit boards is possible at high-quality board shops like Royal Circuits.
Watch the video and read get all show notes.
Hey everyone this is Judy with Altium's OnTrack Podcast. We are glad to have you back again, the podcast continues to grow and we thank you for listening and I know that you are tuning in because I have amazing guests like I have today so I would like to introduce you to my guest but before I do I would like to invite you to connect with me on LinkedIn. I'd love to connect with you and share a lot of information relative to PCB design and engineering and also on Twitter I'm @AltiumJudy and Altium is on Facebook, Twitter, and LinkedIn so we like to have conversations with you, not just monologues; so please connect and make sure you subscribe to our podcast too so we can keep making these.
Today we are with a couple of great people that are involved in US manufacturing of printed circuit boards. I'd like to introduce you to Mihir Shah, who is Director of Special Projects at Royal Circuits. Mihir actually was an EE and has lots of experience - hands-on experience - being in the trenches and doing design work. His father right, it's your dad that owns Royal Circuits Mihir?
[Mihir nods]
And so his dad somehow sucked him into the manufacturing industry. So we're glad to have him there actually, we need more young blood and also, we have Jon Lass who is the VP of Engineering. He's also one of the original founders of Royal Circuits, so gentlemen welcome thanks for joining today.
Thanks this is great.
So Mihir, I'm going to start with you. Why don't you tell us a little bit about your background and then give us a little blurb on Royal Circuits?
Sure, so as you kind of alluded to I'm an Electrical Engineer. I started my career at Tesla Motors where I was working on a lot of the cool things with Model X, and Model X, back in the early beta days of that vehicle. I just got crazy hands-on experience learning how to design your own boards hands-on for everything, just do things quick and get a design approach to rapid prototyping, which was great. And then I went to Taser - now known as Axon - where we worked on consumer devices that are - I mean literally - the Taser device.
So I was more on the power electronics side of the Taser weapon and some things on the body camera so a really, really great experience albeit limited, but really great in the short time that I was a fulltime design engineer. And then you know, somehow, some way, my dad convinced me to join the manufacturing side of things.
Yay Dad!
I'm kind of - one of the roles is always like: look, you were buying boards and designed them for a while, now come here on the other side and try to make it as easy, clean, and simple as possible for people to order them now that you've seen often times, what a pain it is, or all the mistakes that you kind of made, or things that delayed the time, cost etc can help on the manufacturing side and now, Royal Circuits, just to give a brief overview of who we are, and kind of our main value proposition. We're a big US manufacturer of purely quick-turn, prototype, printed circuit boards. The whole idea is one, two, three-day turns in the Bay Area, same-day turns and weekend turns - totally acceptable, and all owned and operated by us, all here in the United States.
So we have two factories: one right here in Hollister where I am now, right in the Bay Area, and then we have a factory down in Los Angeles that's purely flex and rigid flex. We really focus on that technology down there, so we've been doing this for over 20 years. You know, we have our customers range anywhere from large tech companies like ones you've heard of, like Google etc. Students, Stanford, Caltech, UPN, MIT and military.We're ITAR certified, and then thousands and thousands of other customers in that group and more. So we do everything from simple two layer boards all the way to 30 layer, HDI , High Density Interconnect, PCBs, fab and assembly - no minimum order quantity.
So really, really focus on the low volume, super quick turn, with an incredible focus on customer service and making sure that people get their boards when they need them and at the price that they want them at, right here.
Wow, Jon can you tell us a little bit about your background in the industry and your history at Royal and what you do there?
Sure, so my background has been Engineering for about 30 years. I started out in the CAM/CAD industry and was involved in the very early days of photo plotting when we used to build boards with films that have, actual direct imaging as we're doing today.
My dad and I founded the company 20 years ago here in Hollister and we - like Mihir pointed out - it's always been about quick turn, 1 to 3 dating, prototypes, all the way from 2 to 30 layers and, very exotic type of materials and boards. So we've been around for 20 years servicing our customers and we still have some of the same customers 20 years later.
That's a good report card! That's an excellent report card.
That's how we look at it too.
Well my favorite stat about the company - just to interject - is that we really do have a 1 percent turnover in 20 years. I mean, I really encourage you to find another company in the United States that has such a low employee turnover. Everywhere I'm looking, Jon is a testament to that, people don't leave, we just keep growing here and in LA. And in some of the other kind of businesses that we run, same deal. Customers first.
Ok so I'm going to become a board industry geek for a moment but I want to point out something about that, that may or may not be obvious to our audience; but something that I've noted when you do work with a board house that has low turnover, your quality remains consistent because there aren't people coming in muddying the waters all the time, are on a learning curve, or trying to insert something and so your processes stay a lot tighter and cleaner. And that may be something obvious but it's just something that I observed over the years working for multiple board shops and assembly shops.
It was a statistic, before I chose to represent one of those places is, what is your turnover? Because I knew that would create a lot of chaos not only for me, but for my customers, because of the fluctuation, customers, designers, will say to me: I was doing business with XYZ company and all of a sudden - they were great for eight years - and all of a sudden they lost the recipe and I go: uh-oh, they have had employees change. I know exactly what happened. So I know, we've all seen it, maybe an obvious point but something I thought worth pointing out to our listeners.
We appreciate that point, and I will also say that our Production Manager's been here for 18 of the 20 years, so again, it does make a difference.
It does make a huge difference. And Jon, your tenure there and being - yeah that's just wonderful. That's again, a great report on you guys. So this morning what I thought we'd talk about is stack up and impedance, but from a manufacturing point - what you guys can teach designers and engineers that are laying out boards. How you can help them sort of avoid some pitfalls relative to stack up and impedance from a manufacturing standpoint?
So Jon, maybe I'll start out with you, or maybe you both want to kind of ping-pong this one for the uninitiated, let's just talk about what kind of implications there are specific to stack ups with materials?
I mean that's where you start.
Do we have enough time?
[laughter]
We could do a whole thing on materials maybe we need to do that? Because you just said you had a lot of exotic materials I'm like: oh they're one of those. Okay so all right, let's talk about materials, sorry.
You know, I'm just starting - again just the very basics. Our main is FR4 high-temperature FR4 materials but we do get into a lot of Rogers materials for the RF type designs a lot of hybrid combinations a little bit of Teflon so just there's different variances on what you can use.
But diving into stack ups, what a lot of people don't think about from the impedance standpoint is, what are we doing with the the outer layers as far as the copper weights and the plating? And I'm touching on that real quick, because when you start out with a half ounce copper foil and then you plate up another additional ounce - sometimes when they're doing the modeling in the software - they're putting in half ounce and they model it and they get a certain number. But in reality when you manufacture it, you're plating on the surface, so a lot of times I'll get, from design engineers: well my model shows that it should be, 50 ohms and you guys are coming out at 55 ohms?
It's like: well, you're not taking into consideration all the plating on the surface and that makes a big difference. And so we get a lot of that where there's a lot of model software out there on the internet people can go to. We use a software called 'Archeo' it's a very very deep system, as far as it actually takes into consideration all the dielectric constants of the materials you're using in your stack up.
For example, different cores are built with different prepregs, and so they have different dielectric constants. Some of the modeling software on the internet gives you one setting so you can put in 4.1 or 4.2 for your DK value but in reality, depending on how the materials build you have different DK values that can range all the way from maybe 3.8 to 4.2 on a certain materials like these; I sold a 370 HR for example.
So when creating the stackup, we have all of that in there, we have all the pretty products the laminates that are being used, even the LPI and all the dielectric constants and when we're modeling that, impedance becomes very very accurate compared to the models are on the internet.
So - I wanted you to pause right there, you said LPI, so that's Liquid Photo Image of a solder mask. So do you typically put the solder mask in when you're doing your models?
Absolutely you do, because that's a big, big critical part. Another example - I'm glad you brought that up because again, they go out and model on the internet; they're not putting on the solder mask, they're not putting on the copper plating. As I mentioned, they get a completely different value, and then when we come to model it we're going back and telling them we need to change their stackup they may have defined on their fab drawing, because it doesn't meet the impedance requirements. And also you do get a lot of designers that understand that and they'll put notes on the fab drawing saying the manufacturer can adjust the dielectric, spacing, or the trace width within, plus or minus 10% to obtain that value.
Yeah, and like you said, I think that's a good point, say in the case of Isola, or any laminate, they might put a datasheet that’s about 3.8, but it's not exactly 3.8, it can vary in a minor way, from lot to lot, is that correct?
Not so much lot to lot as it is from material to material so they - if you build all the way from 3 core to 47 core, they're using 106 and 108s and these are all prepreg styles that I'm mentioning, and each one has a different dielectric constant. So if you get a combination of them, you end up with a different value - and that again - depending on how your stackup is generated, one discussion Mihir and I had earlier today, is about designers that specify in their fab drawing the stackup they want you to follow, and they can send it to board house X, Y and Z but if, for example, let's say they have a four-layer and they want to specify they want 8 mil dielectric spacing between 1 & 2 and 4 & 3.
Well, we may use a different series of prepregs to obtain that than another fab house and again, DK values - different impedance readings. So all that comes into play.
Yeah and that's a trade off, that's a consideration the design engineer has to make in terms of how they're doing the prototyping, what the outlook is for them, and the turn times and the costing you know, there's other factors outside the actual design of performance on the circuit itself because if you do it, and you have it once, then you say this is my design so at least you will have more consistency amongst different manufacturers because you see, I need these materials, I need backup I did it - do it. But you'll have consistency in the final product but you more I mean most certainly, will not have consistency in the turn times. The available materials that different guys have, especially when you start getting to the more the exotics, and the high-frequency stuff.
So that could start playing into effect and people charge different amounts for it based on the lead time, what they have in stock, what they want to charge, etcetera as that gets complicated but at least, it'll be more close to a similar design on revision vs. if you say, look: I'm just gonna let the manufacturer do it and tailor it towards what I can get quickest and at best cost that'll still give me my main factors and whether they're controlled impedance or stackup height or whatever - and let them do that. So that's kind of the two different ways that people can go about designing.
My impression Jon, before you go on, is that a lot of designers do kind of hand off that stack off to their manufacturers. Do you think that's true?
Yes, we do get it kind of both ways. In some cases, we just get a stackup, for example, if they want it to be 062 plus or minus 10% that gives you the layers that have the impedance requirements, and then we go and generate the stackup and manufacture the board. To me that's probably the more straightforward way because you're guaranteed you get what you want.
Sometimes they're specific about what they want. They call out the dielectric spacings, the core material is everything and now you have to build that stack up, then plug in their numbers and model it, and then it usually doesn't come out the way they thought it was going to. And again, we touched on two reasons why.
So you kind of get a little bit of both. But what I was gonna start saying is, that we also offer a service, a stackup service that you can come to us at pre-design. You've got your board all laid out, you're ready to do your routing, and you can come to us and say: hey, I have a six layer and eight layer design, this is the material that we want to use, and you can tell us a little bit about your design. Which layers are plane layers, which ones are the signals. We don't look at the reference to this is, ninety ohm diffs, and 100 ohm diffs, and then we can go ahead and model that stack up at that time. We can come back and tell you what size traces to use for the single-ended, the tracing space for the differential pairs, the copper weights, everything. We can come back and give you that complete stackup.
So now, that's using our materials. Our DK values, our stackup software, and then when you go to Roger design - if you use those numbers - then when we get back your design and your stack up - the project’s done.
Which I think's a really great model, because then you're doing this partnership - the designers telling you where they're trying to get - you're actually informing them, from a manufacturing standpoint, best practices, and I love that whenever that happens. I wish it happened more.
That's right, that's free of charge - again right at the beginning stage - to me that's the smoothest way to do it. And then you have a stack up you can actually send in with your data package and you'll be guaranteed you'll get what you want.
That's awesome, what a great service I love that.
You've talked a little bit about it, is there anything you want to add? The distribution of copper I get. I used to specialize in RF and microwave boards and that issue you talked about where they model it without the plating ending up on the outer layers right. The inner layers it doesn't matter, but the outer layers, you have to do multiple planing cycles and then it's completely outside of the range of what they simulated and I'm like: I don't know why, and without a fundamental understanding of the manufacturing process it's easy to see how that could get missed. Is there anything else you wanted to talk about? I'm gonna ask you guys three or four or five tips and tricks to give people who are listening some takeaways. But before I do, is there anything else you wanted to add relative to stackup in regards to manufacturing or distribution of copper?
Maybe just a brief... oh sorry Jon do you want to go?
I was just gonna touch on, you were talking about outer layers and then inner layers. If they want to use heavier copper, I like to point out that that's great on plane layers because when you have a heavier copper, your z-axis is higher and now when you go to put the prepreg in, you have to have enough resin to fill in there. And if you don't have enough resin then it can cause delamination or other manufacturing issues. So again, to point out, we get a lot of that too. We get a lot where they want 2 ounce copper on the inner layers, and they'll mix their traces and planes together and they'll be putting 4 mil traces on 2 ounces of copper. That doesn't work, that doesn't work at all.
Yeah and then you have a trace that looks like this [gestures] right like or this - they're not this any more there cuz that's a hard if... yeah it's not a good idea.
So just keep in consideration, from a copper distribution standpoint in layers. You have to nest prepreg in between them, it definitely makes a difference. So, if you're dealing with half ounce copper, no problem - you can pretty much do whatever you want. When you start getting above one ounce, then it starts changing the ballgame. So, from a proper distribution standpoint, just take that into consideration when you have - I'm going back to impedance - but when you have impedance on the outer layers and you're referencing to a plane layer underneath. Try to leave it all solid plane without mixing it with signals. That makes a big difference.
Because now, you have a nice, consistent, even, solid dielectric spacing between the two - so that's a definite plus. Like a six layer, for example, where you have power ground on layer 2 & 5 and then 3 or 4 signal layers, you have to use a lot more prepreg to nest in between there. So again, try to pull up most of your dielectric spacing between those two areas because you're going to need more of it to nest the prepreg. So that's a little bit about copper distribution.
All right, all right guys, so let's talk about some real practical takeaways right now for designers and engineers who design boards that are listening today, from a manufacturing standpoint. I'm sure that you see some of the same oversights being made on a consistent basis. Can you give us three to five tips and tricks; things that designer should look out for when best design for manufacturing practices that you guys see. Mihir, why don't you kick off?
Sure, well mine has a bit of a tie-in more on the design side, because that is more of my background especially that's right now, but there's really two main design areas when it comes to stackups and manufacturability. It's the whole RF analog side and then this digital - high-speed digital - side and they're kind of characterized by two very different, but very heavy driving factors. On the RF analog side you generally find your designs more influenced by the necessity for a low dielectric constant, low signal loss, low leakage, and then generally these have a lower layer count so you really need a low and uniform dielectric constant and all these other things.
So your choice of exotic material is gonna be far more important. But you don't necessarily need to work - that's gonna be more of an important bigger part of your cost, and a factor in your design decision. It's just more important to the design. Whereas with a lot of more high-speed digital stuff, these are usually a way higher layer count, and they have all these other things like burying blind vias, really, really tight traces, and just all these crazy ICs that have like a hundred pins of BGAs that needs all sorts of fan-out etc, and so your costs on that was gonna be way more driven towards the actual manufacturing time and the complexity, and to a lot of people it sounds obvious probably, on this podcast, it is.
But I mean you'd be surprised even as you're designing stuff, people really don't fully understand that buried and blind vias, while they're so easy to throw in on in Altium and just say, this is great, everything routes up perfectly. It does add a lot of cost and time. You could manufacture it, but it's seriously gonna impact your design when you have to do board back, so that's gonna be far more important than generally your choice of material. But obviously, as layer count increases that cost is going to be driven up too. So things like that. You have to take into consideration the differences in the designs and things that engineers are looking at when they're designing them and how that plays out usually in cost and lead time.
There's a lot of trade-offs aren't there?
Yes, that's right.
What would you say Jon?
Well let's tackle unbalanced stackups for a second. Because we get a lot of that-
Pretzels?
Yeah pretty much.
So again, I mean one of the things you need to take into consideration is, you want to have a symmetrical stack up. A lot of time too - especially if they're using hybrids - so they'll put a thick ten core Rogers on the top, and then something thin on the bottom. And again you want to have a balanced stackup, otherwise you're gonna end up with a warped board that to me is a very, very key thing, is to keep it symmetrical. We'll get those stack ups, we'll have to go back and tell them: listen is it possible, the chance of warpage, and try to explain to them.
They need to be symmetrical, so that's something to take into consideration from the get-go. Another one that we get a lot of, and I think I touched base on it a little bit; is to take into consideration the copper weights you call out in the trace and space that you're routing. Because it makes a big difference. So you know, if you're going to be doing a three mil trace with a three mil space, we have to start with quarter ounce copper and then, on the outer layers we have to plate on the surface. If it's on the inner layers, you can do small trace and space on half ounce copper. But once you start getting to two ounce copper and above, you need to be around six and seven mil tracing space.
And we get a lot of that, where we have to go back and tell them: listen your design has four and four you're calling out for one ounce copper, two ounce copper, it's not possible, so we're gonna have to go ahead now and reduce the copper weight, or even worse, that they have to stick with a heavier copper. They have to go redesign their board and lose time.
Explain that, it may be obvious, but explain why that's impossible? I've run up against this a whole bunch of times, but explain because it may not be as obvious as it is to you and me Jon. Why can't you take two ounces of copper and do a four ounce or 4 mil trace or three mil trace, what happens?
There's two scenarios: one is when you give us a design that's 4 mil trace for the 4 mil space between trace and trace, and trace and pad. In order to finish - after etching that trace - we have to do what's called an x-factor. So now we have to increase that trace, X amount, might be one, two, or three mils depending on the copper weight. Because again, having copper it's a higher z-axis. So when you actually have a further distance to etch down to the base of the copper to get down to the laminate, you start losing the feature size as you edge the copper down. So we have to increase that feature size.
So if it's a 4 mil trace and it's 2 ounces of copper, we might have to increase that to a 6 or 7 mil trace. But if your air gap is 4 mils - now we're reducing that air gap down to 2 or 3 mils - which is not manufacturable. So that's where you'll be coming to the problem. And again you also have peel strength. I mean if you have a 3 or 4 mil trace on two ounce copper, I mean the chances of it actually peeling off the laminate is much higher, because you have a certain peel strength. So again, you're not gonna have a small trace on a heavy copper feature for various reasons.
And maybe even in more layman's terms, because this is what helped me understand it when I was doing - because you really don't learn this stuff when you're studying like for engineering or maybe, I don't pay attention.
No, you don't learn it, you don't learn it, you're right.
Simplistic, the thing is people, maybe we could even put this up on the video I don't know if you can add that or add a link? If you picture traces from the side view they're not straight up and down. Right?
Never.
They're at an angle, the reason they kind of look like they're little trapezoids - is because the top of the trace is under the duress of the edge - about the actual chemistry - a lot longer than the bottom. So as it edges down, the top is getting whittled away more than it is at the bottom. So you tend to add an edge like this - if your traces are really close together, you don't have that space in the middle. It looks like you have all the space in the world at the top, when you get towards the bottom of that z-axis, they're actually touching, so you can short out traces that's like the simplest example without getting too deep into everything.
Can you undercut in that scenario or am I thinking of it backwards?
Yeah, undercutting is a term you kind of get on the outer layers, but when you have the dry form you can kind of get it undercut but for the most part it comes to geometry. I mean, you have a very tight tracing space, and first of all, you have limitations on your gap. And even if you could increase the trace big enough, you're gonna end up like Mihir pointed out, with a very small trace on top and a larger trace on the bottom.
Yep it makes sense.
Oh yeah a lot of mechanical electrical kind of issues.
And as well, I have a friend in the industry who was in the board industry for 40 years, and he used to say: it looks good on paper, but he said physics trump's theory right? Like theoretically, it should work right, but he goes: but physics wins out every time. So Mihir, any more kind of practical design for manufacturing tips that you can think of, or Jon, either one of you?
I think we kind of - if people take at least a few tidbits from what they heard today - there'll be an immediate ROI on their time listening, to the success and speed of their design.
Good, well I'm excited to announce that Mihir and the Royal team, will be joining us at AltiumLive as our sponsors. They just let me know that today, so I'm very excited!
So I'm sure you guys will bring some sample boards, or some video and some great assets that they can look at. They can talk to you one-on-one, learn some more tips and tricks, face to face just gather information, which is sort of the magic of AltiumLive. Our goal is to just put the design community in a room with the supply chain, with people that are very knowledgeable, which are veterans in the industry and just let them rub shoulders and start creating new solutions or just collaborating for successful designs and take some of the pain out of it for all of us. So we're delighted to have you guys in San Diego in October.
I really needed an excuse to come to San Diego.
Right! I know, and it's on Coronado Bay, so we're staying at the Loews Coronado Bay Hotel so there's water on three sides of this hotel, and it's in October, which is like, October in San Diego is like heaven. It's like 73 degrees, on the water, so...
You already sold us!
Right it sounds like if you're not coming to learn some design stuff, at least tell your boss you are, and get a nice trip to San Diego... just kidding.
So anyways, we're glad to have you and I'm glad to to get to know you guys a little bit more. I know of Royal but I've never gotten to know you until this last week and so it's been a delight to get to know you both and learn from you. And thanks for sharing your DFM wisdom with our listeners, and we look forward to engaging with you more at AltiumLive, and we'll be sure to share many links.
I think I have eight links to share from Royal and you can dig more into what they do, who they are, and get to know them a little bit better as I have this week. So I'm sure you'll enjoy that. So Mihir, Jon, thank you again so much for joining today. Thanks for joining on our podcast.
Thank you, thank you Judy.
Well until next time please subscribe, join, engage with us at Altium we always enjoy learning from you and learning about what you would like to learn about. We're only making guesses unless you tell us specific topics you would like to learn about. So keep the comments coming. We look forward to engaging with you next time on the OnTrack Podcast. Until then, remember to always stay OnTrack.
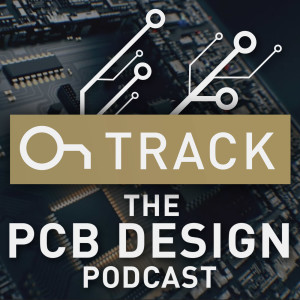
Tuesday Sep 18, 2018
Seamless Global Transfer with Julie Ellis from TTM
Tuesday Sep 18, 2018
Tuesday Sep 18, 2018
See all the show notes here.
Julie Ellis started her career as a representative for a semiconductor manufacturer after completing her Bachelor’s in Electrical Engineering. Now she is a Field Applications Engineer (FAE) at TTM Technologies, the third-largest circuit board manufacturer in the world. Listen to Julie and Judy discuss seamless global transfer and recommendations on working with offshore fabricators. Learn how to avoid excessive technical queries and how to migrate from prototype to production while optimizing global processes.
Bonus update on AltiumLive: Julie and Carl Schattke will be presenting at AltiumLive 2018, introducing new stackup and impedance tools in Altium Designer 19, so be sure not to miss them!
Show Highlights:
- Julie Ellis did a presentation about Documentation at AltiumLive 2017.
- What is Seamless Global Transfer? Transferring PCB manufacturing from onshore prototype level into production and offshore.
- Julie started her career at Hughes Aircraft, where she completed her Electrical Engineering Bachelor Degree - best decision of her life
- More women (not just circuit board barbie) need to get into STEM! #WomenInTech. Julie always encourages young women who are interested in STEM, to get a degree that will enable them to move into fascinating jobs with a variety of opportunities.
- Julie’s first job was as a semiconductor manufacturer’s representative; realized she liked the circuit board side of the business more than ICs and migrated over.
- On TTM: It’s like working at Google for circuit boards, I can always call someone for answers about manufacturing best practices.
- Seamless global transfer - the concept is that you aren’t just designing for the prototype but for global manufacturing i.e. avoid 100 technical queries
- What makes migrating over such a difficult process? Because the 6-Sigma 6Ms, are not the same when it transfers over to Asia.
- What are the 6Ms? Method, Mother Nature “Environmental”, (Man) People, Measurement, Machine, Materials.
- Equipment sets are different for mass production, production lines are longer, there is not as much human oversight, production lines must be scheduled and you cannot stop/start the process. The tolerances are different and they need to be accomodated in the designs.
- Throughput and drilling is always a bottleneck and to reduce this and reduce turn time, mass production sites have tweaked processes to get the highest yield.
- Internationally the general rule is 4 mil lines and spaces on half ounce copper; 10 mil is the most common size drill which results in an 8 mil finish hole size.
- As you go up in copper thickness you need to add a little bit to the pads.
- Blind vias are the ones that are on the outside but end up on an internal layer.
- Buried vias are buried completely inside the board.
- Working with offshore production house while still in prototype development phase.
- Recommendation - design for volume and technology. Qualify the design for the final production region and technology.
- HDI (High Density Interconnect) is anything 0.4 mm pitch and under that has a track running through the pads.
- Judy wants to throw everyone inside a fab house!
- There are at least 30 different processes required to manufacture one 4-layer board.
- Julie works directly with Carl Schattke and they will do a stackup presentation at AltiumLive 2018
- Materials are a significant cost in Asia, whereas here in the states the material is less of a cost (20% in USA, 50% in China).
- With production panels where you're trying to get as many cookies cut, you also need to consider and discuss with your manufacturer the tiny 2x2 inch pieces.
Links and Resources:
AltiumLive 2018: Annual PCB Design Summit
TTM’s Interface Between Designer and Fabricator
Hi everyone this is Judy with Altium's OnTrack Podcast thanks again for joining. We're happy to have you again.
I would like to continue to invite you to AltiumLive, and I also wanted to put a shout out that we have a call for presentations right now, so if you are an Altium Designer user, and you have some tips or tricks or some kind of breakthrough you've had on design please contact me at Judy.warner@altium.com and I'd love to hear from you ASAP.
We'd love to have you present in San Diego or in Munich. Munich is January 15th through 17th and San Diego we are there October 4th, and 5th so look forward to hearing from you all.
Once again I have another talented and amazing guest with me; Julie Ellis from TTM technologies which as you know is one of the largest board manufacturing companies not only in North America but in the world today so Julie is an FAE at TTM and a very well respected technologist as well as a dear friend.
So Julie, welcome it's good to have you.
Thank you.
So Julie presented at AltiumLive last year on documentation. I've sat through many of her talks and learned much from her, so today we want to talk about what it takes to move jobs from onshore prototype level into production and offshore. She calls it seamless global transfer but before we get into that we'll hear a little bit about Julie's background. We both started in the printed circuit board industry in the 80s - which dates us a little bit I know - we're not going to say the year we're just gonna go with the round numbers the 80s but I always...
-we were child savants though so we say we were 12
-we were 12
-five
-okay five, yeah we were five.
So Julie just came in and noticed my super cool Career Barbie of 2018, which is a Robotics Engineer Barbie. She's got circuit board patterns on her shirt and a laptop, she kind of looks like us, so we're just gonna call her Circuit Board Barbie and you know blondes... smart ladies you know. Finally, there's a Barbie we can really relate to, and we want women to get into science and STEM and everything - so go for it and aspire to be this Barbie here.
Right on, yeah! Girl Power. We want to get more women in here, and it's just about exposure and motivating others, so we hope that throughout this podcast we inspire maybe somebody to give a girl a little nudge out there. We've enjoyed long enjoyable careers. So, okay Julie before we get started, why don't you kick off and tell our audience a little bit about who you are and your background - how you got into this wonky industry?
I am Julie Ellis; I started as a Design Engineer at Hughes Aircraft Company. I was awarded a student engineering scholarship there, which paid for most of my schooling - the rest of my schooling after I moved out here from Iowa - so I always tell everybody that getting a Bachelor of Science in Electrical Engineering was the best decision I've ever done in my life, so I really do encourage people. If you're interested in Math, Science, Biology - anything - get a good STEM degree so that you can always move forward into interesting, fascinating jobs with a lot of variety of opportunities.
It's a really, really good way to go and I encourage youth and people to get into this kind of field. So I started as - once I graduated from Cal State Fullerton - I stayed on it until the 1990s when things got really tight in the military market, and I was on loan to one department, but I couldn't hire in, so I took the first job that was offered to me as a semiconductor manufacturer’s rep and I had circuit board industry or circuit board experience at Hughes and as a rep I also had a couple of circuit board lines and I really, really liked the printed circuit board side even compared to the ICS and memory sales and everything. So I ended up migrating toward the printed circuit boards. Fast forward eight years, landed a great job at TTM as a Field Applications Engineer just a little over four years ago and it's been a fantastic opportunity.
TTM is the world's third-largest printed circuit board fabricator, and we would probably be number two if it didn't include Flex because the top two manufacturers have a lot more flex and rigid-flex than we do, so I'm surrounded by experts in this field. It's like living in Google for printed circuit boards because whenever I really want to know something I can go call somebody within my company and find the answer, so it's it's really good working here.
Really it's impressive, and you're right - like you really can go to anyone to get the latest and greatest information on manufacturing best practices which are really, really fun.
So we wanted to talk today about Seamless Global Transfer, and I know that we've talked a lot on this podcast about there's no such thing as the quick and dirty prototype so why don't we just jump off from there? Like what does it mean? So you design a board it's gonna go into production, but you've got deadlines, you need to crank it out really quick, you crank it out really quick and then it's like: hey it works let's migrate offshore!
[laughter]
That’s right - that way exactly.
That would be like the worst case scenario, like you heading for Niagara Falls and not knowing it. So why don't you talk about the myth of the quick and dirty prototype and why you really need to think about global manufacturing up front while you're just developing the circuit board and designing it?
Yes, so Seamless Global Transfer is the concept that you're not just designing for your prototype to get it through a quick turn shop here in the United States in five days. Because I worked - one of the numerous positions - was as a Circuit Board Commodity Manager and a contract manufacturer and a lot of the projects we got had already been tested and proven and developed here in the United States. They sent it to us for mid-level production, we’d try to send the parts overseas, and everybody would come back with a hundred technical queries and say: we can't build it because we don't have this capability over in China. Oh, you need to change this on the design - it's not going to work, and by the time you've given your job to a contract manufacturer your engineers do not want to make changes to the design that they've already tested.
So global seamless transfer plans ahead and thinks about: what is our migration path from quick turn development prototype and taking it over until long-term production and so there's a lot of background that goes into that, and that's what Judy and I wanted to talk about here.
So what is it that you think that makes that migrating over makes that a difficult process?
Because the Six Ms: man, machine, materials, environment - which is another M that I can't remember. Everything is not the same when it transfers over to Asia. The equipment sets are different for mass production, the production lines are so much larger and often much more automated, so they can't get the human element, you know. Watch this, watch that, we don't get the babysitting of our project over in China like we can here. In Asia or China, we have to schedule the production lines, and you can't just interrupt a line there to quickly throw this job in front of everybody else. The schedules are a lot different, the process tolerances are different, and because the process tolerances are different, we have to accommodate those in our designs.
Okay, so there seems to be a perception anyways that once we have a pretty robust design here that we can just kind of throw it over the pond. Why is that, I mean you just talked about some reasons but what are some like tangible snags you're gonna run into if you try to do that?
A lot of it has to do with the drilling. Like over in China most mass production shops, except for the really advanced HDI shops which would all go laser micro vias all the way through, as a rule don't drill using six mil drill bits because they're expensive, they break and they can't be re-sharpened and they break more easily and they have to be changed out twice as often as bigger drill bits. And bigger drill bits can be stacked, or you know, panels can be stacked. So if you can drill two or three panels at one time you've just got your throughput and drilling which is one of the largest bottlenecks in fabrication. You reduce your turn time significantly and time is money. What we're paying for in printed circuit boards besides materials, is the time it takes to get through the processes. So Asia and mass production sites have all tweaked their processes to achieve the highest yields, in the least amount of time, at the lowest cost. But there is a sacrifice to that and sometimes at the sacrifice of we need a better, bigger pad around a drill hole. We're going to stack two or three panels high instead of drilling a six mil drill and our plating processes are a little bit different so we may have to have more edge compensation. Which means that, that will drive a little bit larger requirements for line, width, and space.
So on those, is there a recommended - that's kind of a broad question - but are there recommended kind of hole sizes and pad sizes and/or trace and space sizes to help on the throughput? If you have it.
Yeah kind of the general rule of thumb internationally, is 4 mil lines and spaces, on half ounce copper is a good start. Anything under that on half ounce copper is going to be a premium. And ten mil is the most commonly sized drill which would drop you down to an eight mill finish hole size. And we'd like to see the hole size plus ten mil for the pad. So if you've got an 18 or an 8 mil finished hole size, we would drill it probably at 10 or 12. We'd like to see at least an 8+, 10 and 18 mil pad on that hole. That's just for a single lamination through-hole in multi-layer printed circuit boards. As we go up in copper thickness, we need to start adding a little bit to the pads.
Okay, and how does that change when you start adding buried and blind vias in?
It depends on the construction. If we're talking like a real traditional blind via board; blind vias are the ones that are on the outside, and they end up on an internal layer. Buried are vias that are buried completely inside the board, and those are different technologies. But so if we're talking standard blind vias where we might have 1 to 6 and then 7 to 12, both being blind via stack-ups, we would actually stack up the material layers 1 to 6, drill and plate, and then we would stack up the materials layer 7 to 12 - drill and plate. And then we would laminate all those together, and then we would drill and plate and etch the outer layers.
So those definitely have different rules because the two outer layers already have plating - additional plating - on the outer layers which means that we have to etch through thicker copper because of the foil plus the plating, and we're going to require slightly bigger line widths and spaces on that particular design.
So one thing we were chatting about as we were preparing for the podcast, that I thought was obvious, but also fascinating, is the idea of working with your - you know, I kind of want to move into now, sort of takeaways for our audience. So you were talking about working with your offshore production house while you're in your prototype development stage which I think is kind of counterintuitive. I don't know, is it?
Actually, if we are in the prototype development stage, it's the best way to do it because if - I always recommend that my clients design for volume. Whatever their final volume is you know, we all know the term DFM, but we really have to take it to heart to figure out, qualify the design for the final production region. Final production technology, whether it's a single lamination or a multi-lamination that's not HDI board like I just brought up, or whether it's an HDI board that has blind and buried vias, but with laser micro vias and advanced HDI board which I categorize as anything 0.4 millimeter pitch and under, that has a track running through the pads. So if you start at your before-prototype stage, qualified the design for the volumes and the technology so that you can pick your final production sites, get the design guidelines for those sites, get the stack up for those sites, and have the stack up and the design guidelines identified before you even route the board.
And if you do that then you're not going to route a whole board, send it over to China, and China is going to say: oh sorry those line widths and spaces, there's not enough space for us to compensate the etch and artwork during etch, we can't build it this way. Go increase your spaces, and if you don't have room on a tightly designed board, or if your pads aren't big enough to achieve the annular ring that you're asking for, your design is no good for manufacturing. So my term is ‘design for volume,’ but it means whatever your volume is. And the reason I'm doing that, or I'm saying 'your volume' is because we have customers that do 200 printed circuit boards a month, and we have customers that do a million circuit boards a month. And the shop that does the million circuit boards a month is not going to take the 200 circuit boards per month order, but they have a much higher level technology - so I can't design for that technology knowing that I could never run it in that particular site.
Right, so it's both volume and technology.
I feel like it's such a good service, in many ways on the prototype end, that we can kind of do push-button ordering now, but I also feel like what's has been lost is how complex the fabrication process is and I just wish - I want to throw everyone inside a fab shop. Because it's like when you - think you can just push a button and then a package shows up on your door; you know what I'm saying?
That every shop is a little unique is for a variety of reasons. It's not - for reasons that enable different types of technologies - they do it with high intention and lots of precision and all of that, and so you have to design for that shop. It's not just push-a-button and out it comes. Especially the more complex the board gets, so, on the one hand, I'm a fan to get the prototypes out fast, onshore when you can, have maybe available that kind of service. But on the other side, if you're going into volume, I don't know - I think it gives people sort of a false perception of what it's like on the other end.
Talk about - I think you mentioned this stack up; getting this stack up right at the... I really like that DFM right, design for volume, that was kind of a new concept to me that you introduced me to. So you're saying that the stack up should be kind of vetted and worked out with the volume as well as, what kind of board, what kind of technology buried/blind vias, you have the space levels to also work out the stack of details.
Yeah we need all that information to be able to create the stack up because most of those multi-layer boards with VGAs also require controlled impedance like for the high-speed digital that we're doing all the autopilot, industrial controls, medical controllers, everything seems to be working off some sort of USB and PCI, and we need to manage the controlled impedance. Controlled impedances based on line width, space, and how thick the dielectric is and to a little teeny effect, how thick the copper is. So we have to play all these together while creating a stack up and also keeping track of, if we're doing stacked or offset micro vias. We build those from the inside out and just keep adding layers, drill the outer layer down to the next layer, then on both sides then we add two more layers drill the outer layer down to the next layer.
But each time we do that, we have to figure out how we're going to plate those and how thick the plating is going to be and those are process variances are you know. There are process capabilities and variations from site to site, and there can be unintended consequences along the way, like putting additional copper on that outer layers - it's the more complex it gets you have these: if you do this, then this you know, what I'm saying there's so many!
Anybody who has seen my presentations knows that I always say that I'm always splitting hairs. Because a human hair is about 2.5 to 3 mils in diameter, and I'm always worrying about unintended consequences because if a customer comes in and they say: I want thick plating inside my hole walls you know, give me 2 mils of plating inside my hole walls. Well for one I can't think of one fabricator in China that would do that. The IPC standard for class three is 1 mil average plating in the hole walls. But the other thing is, remember whenever we plate inside the hole walls we're also plating the surface, the outer surfaces, the thicker those outer surfaces get, the harder they are for us to etch fine lines and spaces.
Well, why don't you just put it through the machine that just spits out the board Julie?
We need a magic machine!
If I could do that I wouldn't have to be here... I'd be somewhere on my own Island in Bora Bora...
Barbie we need a magic machine to spit out - maybe Barbie will get you to know either a Barbie plane and maybe she'll have a Barbie magic PCB?
That'd be great.
Then you know, in Barbie's world I think we'll just spit it out, I know - it's very complex and by the way. Let me stop right here and say that Julie helps every top brand that you could probably think of in Silicon Valley and beyond; helps them to do their stack-ups and come up with these you know, calculations to help work out all this hair-splitting and she's very skilled and capable. And that's why she will be presenting at AltiumLive with a senior PCB designer who she works with directly which is Carl Schattke, I cannot tell you what brand he works for, or I would get in trouble, but suffice it to say he's in Silicon Valley and works for the top electric car manufacturer and I am delighted that Julie and Carl will present on stack up on this very subject, and you couldn't get two more qualified people - I’m so excited that you're doing that.
Thanks, we are too - I think it will be fun.
It'll be really fun, and so they're so used to being deep in the weeds they'll be such a resource.
So before you move on though, it's not just the stack up, it's also the pad stack line, widths, and spaces that need to be provided to the customer with the stack up. Because we want to make sure that they know all of those design requirements before the board guy starts routing everything.
You talked about DFM and DRC's for final site and prep for the prototype. Is that - I just wrote myself a note here - have we covered most of that here?
Yeah, we have for the stack up and the design rules. But one thing I'd like to bring up is everybody's trying to stay competitive and because of the processes and the way that production panels are laid out in Asia. Materials are a significant cost over in Asia compared to here in the prototype shops. Here we pay for the quick turns, for the setups and things like that which are insignificant compared to those. So the material here is only about 20% of the average cost compared to 50% of the cost in Asia.
So if you can also plan your size to fit well up on a production panel so that like, imagine an 18 by 24 inch production panel, and you're trying to get as many cookies cut on that production panel, but you also want to think if you've got really small pieces your assembler is not going to be able to load those tiny little 2x2 inch pieces. Their conveyor equipment can't hold them, and it would take them forever to go through those linearly, so another really cost-saving exercise is to work with both your fabricator and your assembler to come up with a multiple up-array for smaller boards and also make sure that you know whether you've got enough clearance on the two long sides of your array, or your printed circuit board for the parts to be conveyed through assembly.
There's sometimes parts hanging off the edge which really makes things fun.
Yeah and that needs to be planned for in advance, whether: do you need an extra rail on a leading edge, because there's a big connector hanging there, or is the assembler going to put that on after the fact? But if you also take into account design for assembly - put all your test points on the board because once the board is designed and you can access test points, nobody's going to be able to go back in and design an in-circuit test fixture or functional test fixture and unpick those plates.
So don't just design for volume. Like I said really, truly design for DFX, design for fabrication, assembly, test, and long-term reliability.
Good, good, good, good advice. So can you give some real-life examples from your real life career? We won't name names of brands but suffice it to say there; you work with major consumer brands that if we could say names everyone would recognize them and tell us some of the, you know challenges that they had by actually not thinking about some of these ideas ahead. And these are the brightest of the brightest - I think what we want to share here is, everybody is challenged in this area, right? It's a challenging area, so we're not saying, oh we're so smart, and you know the audience what do they know? No, the top designers, the top printed circuit board designers almost in the world, are challenged by some of these issues. So just talk about some real-life examples and how it went wrong or how it went right?
Okay one real-life example in the last quarter was a major commercial customer like you said, they had worked with a - probably a Silicon Valley shop - they built their boards, tested them out, proved them, and they wanted to go into mass production. Their start date is like August, to start delivering mass production so that they can you know, start shipping their product. Well it turns out they had a design that had a six mil drill - mechanical drill through a standard thickness board with a ten mil pad and when I said, remember I said like, do your finish hole size plus ten for the pad, this only gave the hole size plus four, and it wasn't enough to make sure that people wouldn't totally drill you know, have too much because of misregistration material movement.
Every time you add a process, you add misregistration. Nobody in Asia would take this business, and we actually had to help the customer convert the whole design to another via structure type to be able to pull it off. And the way this happens is one of two things: if you're a major customer and you go to a, you know like a smaller shop, they are going to be so hungry for your business they're not going to say, no, no, no - we can't do that. They are going to babysit every single panel and put them in the drill machine by hand and make darn sure that they're going to get that for you.
Or there are probably a few select super, super advanced shops that are just doing onesie-twosie jobs and they can meet these kind of requirements, and these tight process tolerances, using direct imaging everywhere you know, using single headed drills for the production panel rather than five or six spindles that we use. And so it's not even saying that that particular circuit board fabricator was a bad designer - it's just that they're only designing for their site capabilities and probably pushing technology to make a big customer happy.
Right, and that may be their niche, that may be their niche market - but again they're not thinking particularly ahead, they're trying to help their customer be - - so it's kind of myopia. They're just designing for that, and they're great shops, they're great shops very, very capable, but not unless you tell them up front or you start this conversation up front it can go bad like that. On a consumer product that, okay it's August let's go into production and then wait, stop. Stop everything and the cost, the headache to that customer, they have to respin the board, run the protos over again and do all the testing over again. And now, schedules are lost, time to market is lost, you know so that it can become really painful very quickly and very costly.
Yeah very costly.
And I had another similar design that my customer had a design with 5 mil mechanical drills and 9 mil pads and most shops I know don't really drill mechanical 5 mils. So that was a tough one for him to go into production. So that's a real common example. The wrong size drill with the wrong size pad, or one that I just saw recently, was a really thick dielectric that still needed a blind hole and it was planned on being a laser hole because they wanted some big RF circuits on the outer layer. Which means they needed a thick dielectric and normally if you're using laser micro vias you have very thin dielectrics. And I was able to confirm that we can do it over in China but it's - it wouldn't have been my first choice for a design you know, and it kind of set me back but - but we were capable on that one.
Yeah so, you have a saying that I like which is: pick your experts wisely. So tell us what that means? What you mean when you say that; pick your experts wisely?
Well if you're going to listen to an expert, they're going to segue you to the path that they know, and if you pick the wrong expert and they take you down a garden path that nobody else can fabricate. I know that there are shops that they'll say: let's do this and let's have the customer design it this way because then they can't go anywhere else. It's a way to guarantee their business.
I can confirm that you know, I've seen entirely that. It locks you into that job.
It locks you into that job, and you know, I can see both sides. I'm like this ambidextrous Gemini so I can see both sides of the story. I can see an internal engineer wanting to secure future business for their location. But on the other hand, it may not be good long-term for the customer. And I'm in it for the long haul you know, I've been both sales and technical support, and a lot of times I have to work with customers to make slight modifications and design engineers; these are your babies. You don't want to have somebody coming in from the outside and saying, you know what, I really can't quite achieve that. Can we tweak your design a little bit? Who wants to hear that?
But if I have credibility, as somebody who's thinking for the customer, for the fabricator, and working towards the best solution long-term. I've - you develop trust, and you can get better work done. So, I choose to do the good path even though it probably means that I tell everybody I'm a conservative designer and so that means that if you design a stack up - if I design your stack up, give you the design rules, if you can meet them chances are one of my competitors can also do the work. Yeah, but on the other hand you know, the relationship most of the time means a lot.
Right it does, and not everybody has both the technical depth that you have, the integrity you have, and you have reached to top, top fabrication experts in the world. So that gives you a really broad perspective which I appreciate.
So Julie thank you so much. This has been so great, and I feel like we've just scraped the surface but I would like to invite our listeners, if you are available, to come to AltiumLive and Julie will dig into - she and Carl Schattke have an hour-long presentation plus QA and, will be introducing some new stack up and impedance tools in Altium Designer 19, and so they will be giving a really rich treatment of the subject of stack up. So if you want to hear more from Julie, come on out to AltiumLive, and we would love to have you. Thanks again Julie, it's always - I always learn from you every-
- - thank you.
Every time we talk.
So there is one other thing that we should talk about.
What should we talk about?
Okay the other background of seamless global transfer is that if you're working with a company that has multiple sites like DTM - we can take that - we can take the lessons learned from the prototypes, and transfer the data, and transfer the lessons learned over to the final fab site, so that it's not a new learning curve once it goes overseas. And that's a real advantage about really paying attention to this.
Right, which is a good point.
Yeah.
Do you transfer the learning curve along with just the data files right?
That's right yeah.
So good point. Okay, thanks for inserting that again. This has been Judy Warner with Altium's OnTrack podcast, and Julie Ellis of TTM.
We look forward to you joining us again next time. Until then, remember to always stay OnTrack.
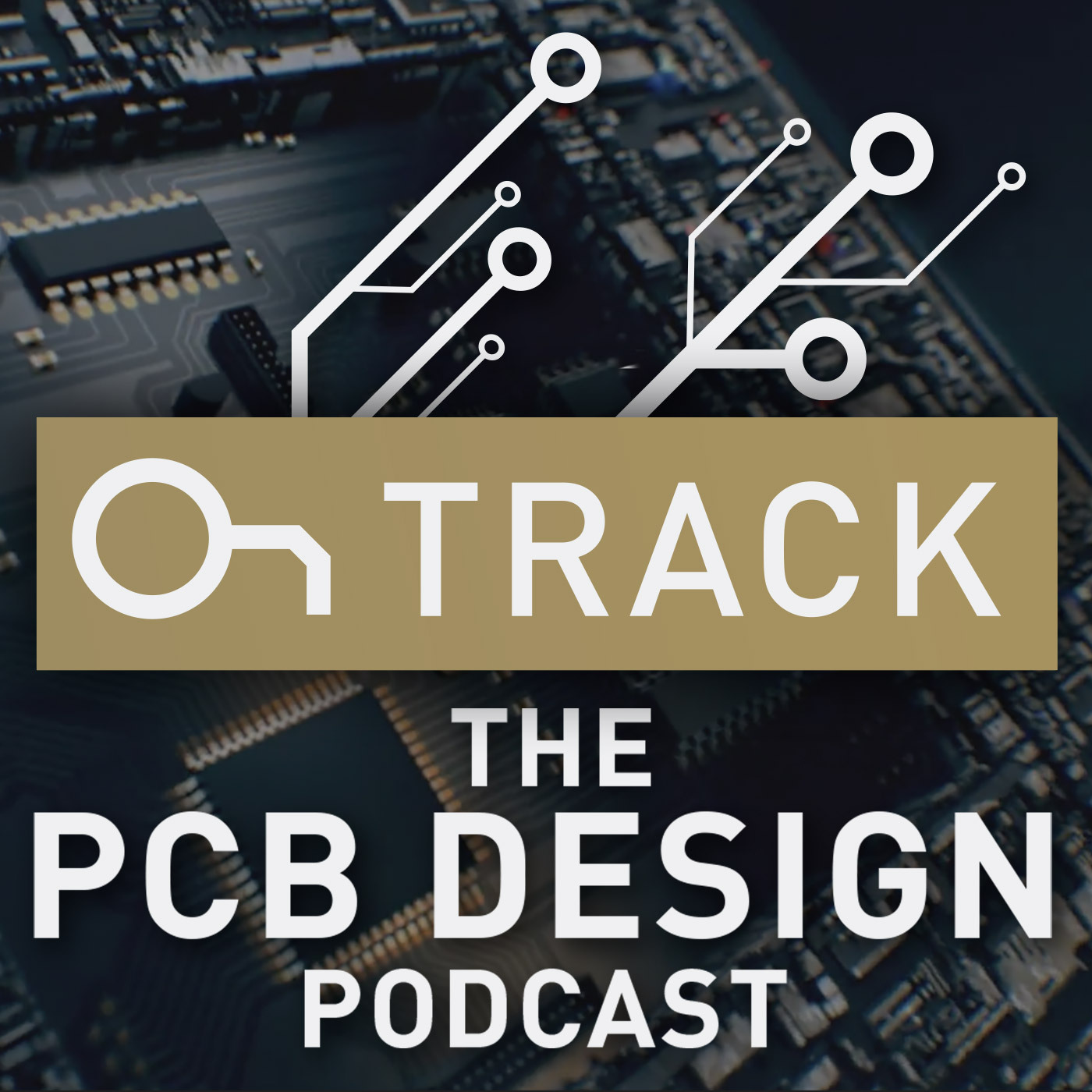
Tuesday Sep 04, 2018
Hybrid Construction Trends in the Marketplace
Tuesday Sep 04, 2018
Tuesday Sep 04, 2018
Hybrid construction is a huge growth area with a lot of opportunity for PCB designers. Learn from Chris Hunrath, VP of Technology at Insulectro, as he provides several valuable insights about the latest in hybrid construction trends. Get facts from an expert in material properties and how to use and combine them in the PCB assembly process. Learn more about polyamide film and its properties, how to use the FR4 as glue, and many more ways to make hybrid construction more familiar and approachable. Join us in this week’s OnTrack Podcast where we bring insights from the manufacturing floor to PCB design teams around the world.
Show Highlights:
- Chris will be a speaker at AltiumLive in October, so be sure not to miss him there, the title of his talk will be announced very shortly
- Chris sheds more light on the topic of inductance and plane inductance which was recently discussed by Rick Hartley in our Podcast: What to Avoid in 4 and 6-Layer Stack-ups
- Embedded capacitors: one of the things that you don't get from embedded capacitor material or planner capacitor materials, is high capacitance, so an individual component will give you a relatively high capacitance level
- There is a capacitance shortage right now too
- Also, there’s a desire to remove surface capacitors for several reasons. You get rid of the vias, you get rid of the inductance and increase the circuit density
- Even when capacitance per square inch is small you don't need as high a capacitance, because you're getting rid of a lot of the in-plane inductance and that's exactly what Rick talked about in his podcast
- Nowadays, with thinner materials, Rick’s recommendation makes sense
- Polyamide film, typically used for flex circuits can be used in a rigid board because it has a thin dielectric layer and has a very high dialect for standing voltage and you can make it really thin
- You can build it into a rigid board and get the properties you need to get rid of those capacitors which leads into hybrid construction, how do you process them?
- The building blocks used to make flex circuits. If you're using an Acrylic which we talked about in a previous podcast laminates its standard FR4 temperatures. True Polyamide films laminate at much higher temperatures like 600° F.
- You can't expose FR4 to those temperatures so in the case of very high capacitance materials you would use the FR4 as the glue and you would just use the core as its print match it, bond treat it and then build it into your FR4 part
- You can’t mix B-stages in the same spot when you laminate that all together the FR4 would be broken down
- Materials on the High Speed Digital side should also have the RF properties and you want to be able to mix those materials so it's becoming very popular
- Hybrid Constructions - a growth area - it’s become like gourmet cooking - there is new media to work with - a material science based area
- Components typically added to outside of PCB are now being embedded inside the PCB
- Solder paste reflow and interconnects can be a downside
- The new materials allow you to do things you couldn’t do before.
- Coins can be used to add inductance if you need to just for heat sinking purposes.
- Bleeding printed electronic technology into PCBs: DuPont have a very interesting liquid polyamide technology that cures at 300° Fahrenheit which is very low and we're exploring the opportunity to use that in lieu of solder mask. It would just be screened on.
- If someone needs information on Hybrid Constructions or sintering paste, please email Chris.
Links and Resources:
Listen to Chris Hunrath’s previous episodes:
Paste Interconnects and Paste Sintering
View all show notes and VIDEO here.
Hi everyone. This is Judy Warner with Altium's OnTrack Podcast. Welcome back, here we are again with your friend and mine, Chris Hunrath from Insulectro who's going to teach us about paste sintering today, which I don't know much about, but we're going to learn about it together. But before we get started, remember to hit all the typical Altium social media platforms Facebook, LinkedIn, and Twitter please follow me on LinkedIn and also remember we are recording on YouTube as well as Podbean and we can be found on all your favorite podcast apps.
Alright, so today we're going to talk about - I don't even know how to set this up entirely cause I'm just as much as a student. So Chris, welcome back! Thank you again, and I know this isn't a new technology - it's just not one that has crossed my path. So tell us about what paste sintering is and what the applications are, and benefits to our designers that are listening today?
Okay, interconnect technology, as you mentioned is not new, what's happened recently though is there's been some new material developments that make it more feasible for the circuit boards. Certainly in ceramic fire technology, metal - powdered metals have been used to make interconnects and traces and circuits on ceramic circuit boards, but those fire at 850-plus degrees Celsius, which would obviously destroy most PCB materials so there's some new technologies out now. There are different kinds of pastes that are used for interconnects. The one that we work with, and the one that we promote, is something from a company called Ormet, and their material is interesting because it sinters at one temperature and then it forms a new alloy with a higher melting point.
Okay I feel like we need to back up and explain what paste interconnect technology actually is. Like how it's performed and then we can go into the material science part just so I can keep up, Chris I want to be able to keep up.
So multi-layer PCBs - also not new - typically what you do is, you print and edge any number of layers, you drill and then you plate. Typically electroless copper, to make the non-conductive surfaces conductive, and then you build up the thickness with electrolytic copper.
Mmm-hm.
And some people call it a semi-edited process, because you are using the electroless first as a seed layer. There are some other technologies used to make that dielectric surface conductive, and then you build up with electrolytic copper and so that's how you link the layers of the z-axis.
So if you think of a classically - as a circuit board - as a web of foils printed and etched, all your XY connections, and then the drilled holes - whether they're laser drilled, blind vias, or drilled through holes, the plating links everything in the z-axis. Now one of the challenges when you do that, is you're consuming real estate at all the layers. So let's say you have a 12 layer multi-layer - relatively simple multi-layer by today's standards - but you need to connect layer 1 to layer 10 you've taken up the real estate in all the other layers - you can't route circuits in those places, because there's a via in the way, unless you wanted them to connect to that via and they're part of that net. So there's a term called any layer HDI - I don't know if you're familiar with that term? Basically it means you could put a via anywhere you want in any layer. Nowadays that's done typically by what we call build up technology. So you start with a core of some sort - again it could be double sided, it could be a multi-layer core, and then you sequentially build layers and you only go one layer deep with a laser drill sometimes two - depending on the design - but that's not true for any layer.
Anyway, you go one layer deep you plate, you print and etch, and you do it again and again and that allows you to put vias almost anywhere you want in any layer, the downside is, it's almost like building multiple circuit boards. So the cost really starts to increase. And of course you're putting the board through multiple lamination cycles and that has some undesirable material side effects depending on the material. Some materials can withstand three lamination cycles, some six, some ten, but it is hard on the materials to go through that lamination process, over and over again.
Right.
Especially electric phenolics, which are very common for lead-free assembly, because they're relatively economic and they're also - they also will survive lead pre-assembly, but they tend to get more brittle every time they see a thermal cycle though, so that causes some issues too. So what paste interconnects allow you to do, is change the sequence in which the vias are formed. So instead of laminating drilling and plating you can actually drill, add the paste, and then laminate, so it changes the build sequence and this is important both for the fabricator and the designer to understand what that means. So typically what you would do is, you would take a B stage layer of some sort; you can either drill it and paste, fill it with what we call a postage stamp process or you could pre-tack it, vacuum tack it at low temperature to a core of some sort, or substrate, laser drill through the B stage, apply the paste and then when you laminate the paste interconnects, the layers in the z-axis - you could literally take a piece of prepreg, laser drill it with a stencil or with a Mylar Stencil, I'll talk about how that works in a little bit - apply the paste, remove the Mylar laminate between two copper foils, and now you've got interconnects inside a double-sided cork.
That's cool.
So then if you print and etch that, now you've got a core with connections between the layers with no visible vias; they're all internal. Yeah there's some technology around the paste and again we can talk about that, in a little bit.
So how is it applied - is it squeegeed in?
Yeah.
Okay, just like with a silkscreen?
Well no screen - so what typically what you do is, you apply a 1 mm Mylar mask to the B stage and you tack it simultaneously. Then when you drill through the Mylar and the prepreg B stage to get down to your copper features, then you apply the paste, and the Mylar's your mask, and then you remove that just prior to lamination.
And that stays inside the hole? It doesn't just I don't know the consistency of it. My mind was - pictured it just wanting to drop out of that hole - but it must have some kind of stability?
Yeah it's a liquid and there is a tack right. There are a number of ways to do this, but the most common method is to laser drill, apply the paste, dry the paste... you would do it a second time to top it off and then when you remove the Mylar, the liquid paste stays on top of the paste that's already been applied. Then you dry it again, then you go to laminate.
Does it air dry or do you have to cure it what do you do?
You don't really cure it because it's metal powder - metal powder based - so there isn't really a polymer matrix. Unlike print electronic sinks - which is a again another story - you would just dry off any of the carrier solvent used for the application process. It is a liquid - well it's a paste, not a liquid - but but when you dry off the the solvent that's in it; which is less than 10 percent by weight, then it's just powdered metal and that's how it makes a connection. So think about this right, you've seen a lot of PCB designs - imagine a 32 layer board, which most shops can do, but it's not at the low end of technology. Imagine splitting it up to two 16 layer multi layers right?
A lot easier.
A lot easier to build and then you just paste them together at the end, and depending on the design, you can electrically test each half and only use the good ones. So your risk is light.
Oh, right.
There's a lot of advantages to this. Or what if you want to put together three 16 layer multi layers, or four, or 18 or four 18 layer multi layers - it's been done you know. Now a shop; instead of trying to build a 72 layer multilayer - if they're building 18 layer components - it's a lot more manageable.
Hmm, that totally makes sense. So you explained some of the benefits - it's a nightmare, and you've seen, we've all seen these cross-sections of these crazy stackups with all the sequential LAM and drilling cycles and all of that. And then - and also kind of an unintended consequence you can get, is you can - from a performance standpoint - if you do enough of that right can't you get excess copper on the surface features?
Yes - that's a very good point. So in other words, if you're going through many plating cycles depending on how you break that up and you're trying to meet a wrap requirement, that could definitely add up and make it - make fine line etching more difficult there's a lot of - there are some some drawbacks to traditional processing and then with with an Ormet style process, or a paste interconnect style process, you can eliminate some of those things even with an RF design.
Let's say you have very sensitive surface features and you don't want to play with that layer. You might want to put on the surface finish, the nickel gold, but you don't want to put any additional copper - you want just the original foil copper. You could do that with this paste because you could create that as, almost like a double sided board, and then bond it to the rest of the stack up at the very end, and you're done.
Interesting. So I think you mentioned too, there's some good signal integrity benefits, did we cover that I don't recall?
No, so one of the things that a lot of designs call for is something called back drill. So you're familiar with that, so you do the back drilling to get rid of the unwanted copper. So again, in my earlier example let's say you're connecting layer 1 and 10, and let's just say it's a 22 layer - 26 layer multi-layer. You're going to have a lot of extra copper metal in that via that you really don't need or want. So common technology is to back drill down to layer 10. Now of course drilling to that precise location or depth, to remove the copper up to layer 10, but not beyond. It can cause a reliability concern that's a bit of a challenge. So there's those issues.
What you can do with the paste technology is let's just separate that board at layer 10, and not put a via on that half that goes from layer 11 to whatever the other layer is and you're done. So you can eliminate back drilling and the parasitic effects of having that extra copper and the via so that's another application. So there's some signal integrity benefits, there are some RF applications, there are some high layer cap, multi-layer applications, but also many layer HDI applications; it really depends on how you design it and use the paste.
So if you're a designer what kind of design considerations do you need to make up front?
Okay, my recommendation would be is: think about the design, think where it would make sense to split up the layers and provide the most design benefit. Generally speaking, we like the via to have a one-to-one or less, aspect ratio. Now that might sound restrictive, but it's only in that one B stage layer.
So then that's an important consideration. So in other words, if I have 5 mm of B stage, I won't want my via to be 5 mm or larger where I'm going to apply the paste. It has to do more with the paste physics and how it fills the via and then of course the pad, the receptor pad that you're putting the laser drill via on, needs to be a sufficient size for where the paste doesn't have the opportunity to run on one side or the other of the pad.
So we do like an annular ring around the via, that's going to have a lot to do with how well you can register your laser drilling, usually that's pretty good. The other consideration is, the B stage you use, spread glasses - bringing up spread glass again. Spread glass is good, because it tends to keep the paste corralled, whereas if you have an open weave and that prepreg resin's melting and flowing and during the lamination cycle the paste could run to that area. So spread glass is better. Higher viscosity resins tend to be better. We like low flow prepregs. So those are some of the design considerations.
Another design consideration is - and I've seen this happen before - where if you have a ground area and you're making a lot of paste interconnects along a wide track. You don't want to put the paste interconnect to the edge of the track because what ends up happening is, during lamination, the resin wants to flow off the surface of the track down the sides to fill - hydraulic effect, and it's going to move the paste with it. I've seen vias actually move during lamination. So just some common-sense things. Keeping in mind that it's the B stage where your interconnect is. You want to make sure you put that in some good locations, and in that particular case all they had to do is, go back and shift the vias a little bit to one side and then everything was fine. So it's just those kinds of things. Certainly they could contact us, we can give them some design hints and I can give you some literature to go along with this video or podcast.
Yeah, yeah, very good. Ormet and the paste interconnect - paste sintering - has been around for a little while. What's been the sort of acceptance of it industry-wide? Is it being widely accepted, is it just on certain applications?
It's been around a long time. It was primarily used for quick-turn mic review work, and also large format boards where you're literally stitching very large boards together so you can - again the idea is you can make boards that are nearly finished and then electrically interconnect them. The nice thing about the Ormet paste is it doesn't melt at reflow assembly.
Hmm, so it changes chemically right, so once the sintering is done then it doesn't change, then it doesn't morph and heat?
What attracted us to this technology over some other paste interconnects - because there's other processes where you would apply a paste of some sort and then make a connection with pressure in the z-axis - but what interested us in the Ormet material is: the paste melts at one temperature and alloys - so the paste is basically copper particles with a tin alloy powder. When the tin alloy powder melts - and the melting starts at about 130° Celsius, it starts reacting with the copper and forms an alloy with the copper instead. What's interesting about the Ormet material is, it's alloying with the inner layer coppers as well, on the PCB layers. So we have a metallurgical joint, not just a pressure or contact connection.
So it's - and unlike, the tin lead or lead-free alloys and solder, the melt - the new melting point, when it forms an alloy with copper is one phase is 415°, the other is 630° Celsius. So it's not going to remelt that assembly. So it's a permanent connection, so really the paste applications from other technologies like flip chip and whatnot packages where you didn't want to have a secondary or - if you have a secondary reflow operation - you didn't want to have any more remelt. It has some applications there. Or a down hole assembly is another application where the board might be subjected to the temperatures near the solder melting point is another good application for this material.
So that's what interests us because you know when a board's in use, it heats up the z-axis expansion with other types of pastes interconnects, you have a resistance change every time the board is heated even from, let's say 40, 50, 60° Celsius in normal use, not even in any kind of environment - parts of the board would heat up from the components and you'd have a change in resistance, and that's what this is designed to circumvent because it forms that metallurgical bond with the copper inner layers.
Interesting.
So yeah it's a different technology than the paste you would use in printed electronics.
Okay well that's been fascinating. Again I feel like a newcomer to old technology but - and I've known about Ormet that I think got acquired by Merck now, but I've just never had someone sit down and explain it to me. So thank you for doing that.
90 layer multi layers people are getting - 90...
What!
Yes, 90 layer multi layers with paste interconnects yeah.
That's crazy, I didn't even know a 90 layer board existed I guess.
Yeah I've only really seen them into the 60s I guess personally, so.
Yeah you know, one common design was a 72 layer multi-layer, again made out of eighteen layer components, and one of the things with the chip tests the ATE companies, they built some high layer count multi layers and you need a lot of IOs, there's a trend to go to wafer level testing were you’re testing the entire wafer. You need lots of interconnects and that's one way to get there, is to use the Ormet paste to put in lots of layers. So we're seeing more interest in it lately, and I think that's one of the reasons why the technology hasn't taken off until now, is because there just wasn't the demand.
Right ahead of its time maybe a little bit...
Yeah.
Well, I know you've shared with me some cross-sections or I think you did, and so please be sure to share those with us and we'll put those up on our website and we can share your website and Ormet or Mark's website, so the designers can get more information. Is there any place else besides your two websites that you would recommend for more information?
You know I've mentioned HDPUG (High Density Packaging Users Group) in the past - they're actually contracting some PCB manufacturers to make some HDI test vehicles with paste interconnects. So there's going to be some data - anybody who's an HDPUG member will have some access to some really good reliability data and they're pretty complex boards so it'll really push the technology but for breaking up big thick and ugly PCBs, that's pretty well-established.
Yeah very cool. Okay well thank you. So tell us about that fish on the wall behind you?
[laughter]
So it was a gift from my sister, actually it's made from recycled materials so there's an old PCB cut up on there, and the old spark plug wire, and a few other odds and ends. Some artists put together actually I didn't buy it; my sister bought it on Catalina Island and somehow we went out there as a family trip and somehow she smuggled it off the island and gave it to me just before she headed back to Virginia. So it was kind of cool.
Oh that's fun a good throwback to your diver self.
Yeah so - just the last thing on Ormet, is 'paste don't plate'.
[laughter].
Is that their tagline or is that yours?
Actually that's their tagline. We were sharing it with the IPC shows, but another nice benefit to the Ormet - which I didn't mention earlier is - there's no electrolysis, no plating processes in these interconnect layers so it circumvents all that.
Which is like bizarre for me to think about but...
Yeah but if you're capacity constrained, no plating, that's another benefit.
Well thanks again this has been really good. If you have anything else juicy to share with the listeners just email it over before we get this one up.
Okay.
And thanks again for this one. Now I know we've talked about exploring down the road a little bit on copper foil, integrity issues, and also printed electronics. So I'm sure I'll hit you up again soon Chris.
Yeah definitely. I would like to talk about some of the material science behind printed electronics and I know you guys are working on some new design tools and print electronics; there are a lot of different ways to use that in electronics... I should back up, but there's a lot of different ways to use conductive inks in electronics there are so many different versions of the inks.
Which is another subject I know nothing about so it'll be good. I'll be a student with our listeners and, I know they're out there, I know what conductive inks are, but as far as all the applications, all the different materials available, that just seems like something that's in writing a lot, that people are really turning towards a solution.
Lots of new technologies are coming out in that space and it's going to be fun to watch it all.
Yeah yeah it will be.
Okay Chris, thanks for another good podcast and we'll see you soon.
Thanks for having me.
My pleasure. Again this has been Judy Warner with the OnTrack Podcast and Chris Hunrath from Insulectro, we'll see you next time - until then - always stay OnTrack.
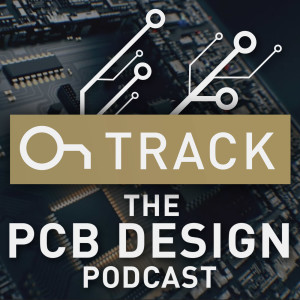
Thursday Aug 30, 2018
BONUS episode: All About Design007 Resources
Thursday Aug 30, 2018
Thursday Aug 30, 2018
Meet Andy Shaughnessy, Managing Editor of iConnect007’s Design007 Magazine. Listen in to learn about all the resources available to PCB designers from this industry publication, website and e-book publisher brought to you by iConnect007 which publishes of a variety of specialized publications relative to the electronics industry. Learn more about what resources are available, as well as where you can meet Andy and other members of the iConnect007 team.
Show Highlights:
- It was the PCB Design Magazine, now it is Design007
- Resources on the iConnect 007 Website: THE DAILY NEWS, SMT WEEK, INSIDE DESIGN, MIL/AERO007 WEEKLY, SMT007 Magazine, PCB007 Magazine, DESIGN007 Magazine and FLEX007 Magazine
- Design for Manufacturing (DFM) Ebook
- Next up: PCB West in Santa Clara, and AltiumLive 2018: Annual PCB Design Summit
Links and Resources:
Design for Manufacturing (DFM) Ebook
AltiumLive 2018: Annual PCB Design Summit
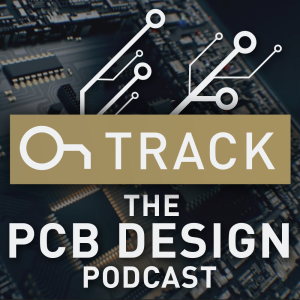
Wednesday Aug 29, 2018
Let Them Build Robots! All About AltiumLive
Wednesday Aug 29, 2018
Wednesday Aug 29, 2018
Meet Andy Shaughnessy, Managing Editor of iConnect007’s Design007 Magazine and learn all about AltiumLive 2018: Annual PCB Design Summit as he interviews Judy Warner in this special bonus episode of the OnTrack Podcast. Learn everything there is to know about AltiumLive from Judy and Andy and find out what Altium has planned for the PCB design community.
Links and Resources:
AltiumLive 2018: Annual PCB Design Summit
Meet the Keynotes at AltiumLive 2018
REGISTER for AltiumLive 2018: Annual PCB Design Summit
View all show notes and VIDEO here: https://resources.altium.com/altium-podcast/let-them-build-robots-all-about-altiumlive-pcb-design-summit
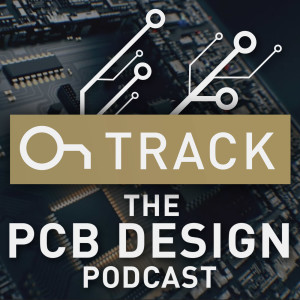
Tuesday Aug 28, 2018
Injection Molded Structural Electronics and Designing in a 3D Space
Tuesday Aug 28, 2018
Tuesday Aug 28, 2018
Sini Rytky, VP of Product Management at TactoTek, and Tuomas Heikkilä, Senior Electronics Designer, join Judy Warner on the OnTrack Podcast to talk about Injection Molded Structural Electronics, or IMSE, the integrating of electronics inside 3-dimensional electronics to create smart surfaces. TactoTek is a leading provider of solutions for 3D structural electronics, enabling the integration of printed circuitry and discrete electronic components into injection molded plastics. Listen to how TactoTek and Altium are combining forces to research and develop design rules for this entirely new technology. Learn more about this and how you can meet them at AltiumLive 2018.
To see all the show notes and VIDEO click here.
*This communication may contain forward-looking statements about strategies, products, future results, performance or achievements, financial and otherwise. These statements reflect management’s current expectations, estimates, and assumptions based on the information currently available to us. These forward-looking statements are not guarantees of future performance and involve significant risks, uncertainties and other factors that may cause our actual results, performance or achievements to be materially different from results, performance or achievements expressed or implied by the forward-looking statements contained in this communication, such as a failure to add previewed functionality to our products or the potential impact on our financial results from changes in our business models.
Transcript:
Hey everyone this is Judy with Altium's OnTrack podcast. Thanks for joining again. I have two amazing guests hailing all the way from Finland today and I look forward to sharing them with you. Before then I ask you to please connect with me on LinkedIn, on Twitter I'm @AltiumJudy and Altium is on all the traditional social media channels Facebook, LinkedIn, and Twitter.
So today we have a look into the future of technology with TactoTek and I have two wonderful guests, Sini Rytky and Tuomas Heikkilä. So we've been working here at Altium closely with Sini, Tuomas and their whole team there and we are excited to show you, kind of this cutting-edge technology, and the amazing things that they're doing in Finland to advance a whole litany of advanced electronics manufacturing and technology and while we continue to work feverishly on AD19 and getting in the traditional functions that you would like, I wanted to give you a sneak peek on something more for the future. This is not going to be in AD19, but we continue to work together, sort of on a research kind of function, with these two and all of TactoTek. So I'm excited for you to learn more about them - so let's get started. Sini, Tuomas, welcome.
Thank you Judy for having us here.
So Sini, I think I'm going to start with you. Can you tell us a little - well before we get going, why don't you both introduce yourselves and tell us your background in the industry and what exactly your role entails at TactoTek?
Sure, so my name is Sini Rytky and I'm heading the Product Management at TactoTek. In practice it means that my team is responsible for technology productization and roadmapping and go to market strategy and planning. And also technology partnership development. My personal background: I am a Software Major, but spent about 20 years in mostly hardware driven business. In electronics manufacturing and test automation in consumer electronics and automotive industries. It is my first podcast ever - I'm very excited!
How about you Tuomas?
Okay so my name is Tuomas Heikkilä and I'm the Senior Hardware Specialist and I have worked for TactoTek, for almost six years now. All of this time I have designed and developed. I oversee technology from an electronics point of view. So my background: I have worked also in the mobile phone industry before joining TactoTek.
Along those lines Tuomas, can you tell us about - for those that aren't familiar what the acronym IMSE means?
IMSE means Injection Molded Structural Electronics.
Very good because I know we'll be using that term a lot and because you guys are sort of cutting-edge I thought there's maybe some people in the audience that might not be familiar with that term. So Sini, let's just jump right in. Can you talk about - I'm asking you three really big things: the technology, the market, and really the problems it solves for technologists in the marketplace?
Sure to start off with the technology; like Tuomas said, our technology is called Injection Molded Structural Electronics which we call IMSE. To put it simply in one sentence, we are integrating electronics inside three-dimensional plastics, and as a result we can create smart surfaces with electronic functionality such as capacitive touch functions, illuminated icons and wireless connectivity such as Bluetooth and near-field communication.
So when we look at traditional electro-mechanics assembly, they typically consist of one, or a multi PCB structure along with the surrounding mechanics and from a design point of view the challenge is that many times it is restricted with, for example, dimensional constraints or space limitations or weight limitations.
And then from a manufacturing point of view; they typically have a large number of individual toolings and assembly phases. So with IMSE we can solve many of the problems for traditional electronics and mechanics, but we can also create totally new use cases and integrate electronics in places where traditional electronics and mechanics fail to do so. So, if we just briefly visit our process. We start by printing colored and conductive inks on flexible films, and continue by mounting surface mounted electronic components and continue by forming that film along with the components into a three-dimensional shape. And then finally, we injection mold all of that into a single piece assembly. So when we look at the benefits the IMSE part structure - if we compare it with traditional electronics and mechanics - we can save up to, I'd say, 90% of the assembly depth, save up to...
Wow!
-yeah that's a big number.
That's a big number yeah, and up to 80% of the part weight and at the same time, of course, we're enabling beautiful, seamless, smart surfaces and we can create - we talk a lot about point of views at TactoTek, and by that we mean, that IMSE enables intuitive user interfaces. So no longer do we have to have a complex HMI with all of the centralized functions, but we can create point of view functionalities. So for example, integrating capacitive touch enabled volume control on top of speaker modules.
So those are some of the - let's say challenges and benefits, that we've seen. And then when we look at the market, so obviously, this is a cross-industry technology, so there's - we see a lot of benefits from various industries. A very common application for IMSE is a human machine interface and we are currently working, for example, with the automotive segment; creating for example door trims and overhead control panels, appliances control panels, and we also work quite a lot with variables. So creating electronics in textiles...
Oh wow.
-yeah and that's actually...
I actually didn't know you were doing wearables, or that had escaped me in previous conversations, that's amazing!
Yes, yeah-yeah so the fact actually, that we are injection molding everything into a single part assembly, it also means that it's fully encapsulated, which means it's protected from debris and moisture. So yeah, so definitely when you think about electronics in fabrics our structures - we call wash and go, so they are very durable, and they can withstand like dozens of cycles and washing machines.
Wow.
Yeah, yeah. And then maybe a couple of words about the business model. So we are licensing our technology for IMSE design manufacturing and validation. Which means that our customers, they can both benefit from the possibilities that IMSE creates in product design, but they can also enhance the vertical integration in a way that they can perform functions, that were previously outsourced, and further extend their offering for customers.
That's unbelievable - and I can - - my mind is just spinning with the kind of enablers that I can see, that this is going to bring over time. So thank you for sharing all that. On a more practical level, Tuomas and you know, the people who are listening to this podcast are typically engineers and printed circuit board designers. Can you talk a little bit about the kind of practical effects on PCB designers and the implications they would have, from a design standpoint, in designing what you're calling smart structures?
Yes. So if we first compare traditional PCB design and IMSE design there are few main differences which come from materials that we are using in IMSE technology and also the 3D shape. So if we first consider those materials: the substrate of printed film circuitries are the difference. So in IMSE technology we have quite a large patene plastic film, and if they convert this for rigid PCP - there is a big difference.
Yeah.
Another thing is trace resistance. So when we are printing traces using silver inks there is always some resistance, so we can never think that this resistance is zero.
Right.
So we have to always consider this in our design. Of course it depends on the ink used but the typical resistance differs between printed silver ink trace and pcb solid copper trace - roughly 100 times bigger. So there is a huge difference in resistances as well.
Okay.
The third, which is really related to materials is dielectric. In PCBs there is no need to design, especially dielectrics, between two conductive traces but in IMSE design we need always to design a dielectric layer between two conductive layers and also, as I earlier mentioned, this 3D surface - I would like to highlight this as well - because it means that when the final shape of the product is somewhat kind of the correct 3D shape.
This means that the printed circuit would need to be designed a bit different than any PCBs.
So I'm gonna ask you more about those materials in a minute. But I was really impressed when I first saw it. I really thought it was a one- or two-sided only circuit structure and I'm really impressed to find out that no, it can be multi-layer and like you said Sini, completely encapsulated, so that opens up a lot of opportunities I think. So Sini, can you talk more specifically about the materials that are used for structural electronics? I know Tuomas just mentioned the silver inks, the dielectric materials, that you can do multi layers. Just the materials overall are really different, so can you talk a little bit about those please?
Mm-hmm - yeah and I would say the key essence of our technology is really the know-how and understanding, of not just the individual materials, but the four material stack ups. So we need to, first of all, we need to obviously understand how all the elements perform together like the films, the inks, the components and so forth, and it's...
As if it wasn't complicated enough; the traditional boards.
-yes! So it all has to work in synergy and it's of course, it's like one thing to understand how they perform when they are in 2D, but in our case we are then also bending and stretching everything into that three-dimensional shape. So that process as a whole, has a huge effect on the material characteristics and performance values. Like Tuomas mentioned before, for example, the conductive ink resistance changes over the manufacturing period so it's a big pile of materials research and chemistry as a whole that we have done to understand the behavior of different material stack ups. So we - of course we try to be on top of what works together and of course - what doesn't. So...
And so do you publish those, or will you be publishing those in the form of a datasheet, so when a PCB designer might move into this space that they'd have some guidelines?
Yes. So obviously, the material stacks are one element of our licensing content. So we are able to provide our customers with validated and functional material stacks that they can use to test our building products.
How long have you been at this? Because I know you work with materials and that, that is a long, arduous process. It takes a lot of discipline.
Mm-hmm - yeah so we've been around since 2011 and we've used a lot of time and effort for exactly materials research, and creating the validation processes. So now we're in 2018 and we are mass manufacturable so it takes time.
Yes it sure does, yeah when I've talked to friends that are chemists, it just takes a long time. So, back to you Tuomas, with all those different materials, and you mentioned also embedded components. So I would like our audience to learn more about the implications which you began to talk about - with the printed inks, the silver inks, and what not. But what are some other implications of those different materials? And what kind of components - because you're really talking about embedded components here I take it? So help us understand that a little bit more?
So like Sini said, understanding materials and materials tax, those are very important. So as I earlier said, this trace resistance for example, it is a big thing. Also another example is this flexible film which are speaking back to SMD process, for example. So typically we are using small SMD components like LEDs, resistors, diodes, transistors...
Traditional?
-traditional yes.
Oh okay.
Traditional off the shelf components.
But when we are selecting components on our IMSE products, the key element is the height of the component. So the component should fit inside the product, it's the first thing. The second thing is that when we are injection molding the product the melted plastic flows over the component - so the component should stand this injection molding and yes, the thinner the component the better.
Okay so - and I am certain that you have to take in consideration the thermal implications of what kind of thermal conditions those components can survive in?
Yes we have also considered this.
So for our listeners; I just want to let you know we're gonna connect all kinds of links and pictures because if you're like me you need some visuals to really understand - this is sort of hard to do - in the form of a podcast - it's a little difficult to talk about, but again I want to remind our listeners that we are recording simultaneously on YouTube and also we're not showing visuals here but we will put up a myriad of links and photos. Because if you're like me, you need pictures okay so.
Yeah actually we have a white paper regarding this.
Okay.
Will you share that with us Tuomas? Okay great.
Yes yes. Okay. It's just in our webpage so we can share the link of course.
Wonderful and the other thing that I wasn't clear about is: so you do the printed portion of the process and then you mold. It's not like you're creating it on a 3D surface right? Or does it go both ways?
We first print, this is 2D, then we place the component; assembly process, after that is forming process, the film takes its 3D shape, and after that comes injection molding.
This is actually the reason why we are doing this, is that we want to enable our customers to use just standard electronics manufacturing equipment. So when we are placing the components in 2D, it means that we don't have to have anything like 3D pick-and-place or anything like that - you can use standard PCB manufacturing equipment.
And then you mold. Which seems so counterintuitive? I don't know how you guys are doing it. I think you're magicians so...
You have to come and see it. I know - oh speaking of which also I'd like to let our listeners know that I'm delighted that Sini and TactoTek have agreed to come be a sponsor at AltiumLive they will have a booth there. They will have physical samples and you'll be able to see this and if you're like me , I think this all of a sudden aha moment happens when you can physically see - or like Tuomas said, read a white paper and you have some kind of visual representation of what's happening. And you will gasp. It's really incredible to watch so I invite you always to come to AltiumLive in San Diego or Munich and see them there.
So let's jump into how Altium and TactoTek had the good fortune to come together. Sini you started to talk about a challenge you guys had to face in that, there was a gap in the design tools to support your technology so, our team have been working with you for a while so can you tell us, sort of what that process has been like and, sort of how we've been working together?
Yeah, so I think for us, how we have worked so far is that, obviously we have a lot of design disciplines that contribute to the IMSE, structure not just electronics and mechanics, but also graphics design, antenna design, and illumination design. So all of those different design elements have to work in perfect synergy, because we don't have those separate structures but we only have that film and everything is on top of that one or two films. So the element that we have been missing so far in the design tools is the support of design for IMSE type of parts.
So we've been using Altium Designer for years for electronic design, but we've been sort of manipulating the tool which is meant for PCB design and we are using familiar functions for something else. So today we are not just using the tool anymore but we've been very, very happy to start really working with Altium and doing research on specific features and automation we could integrate in the tools in the future to enable more efficient design process for IMSE and printed electronics as a whole.
Which is so exciting to me. So if I understand you correctly, then we're really starting to develop design rules for a whole new technology?
Mm-hmm - exactly and in that way obviously shortening the learning curve for new technology and bringing it to the hands of the actual end users; the designers of the products.
Well I really love that you guys are using traditional mainstream tools like Altium Designer so designers, their ramp-up on the technology can be quicker and just using kind of some familiar things like a 2D manufacturing process so there's not this whole giant - there's not 20 obstacles in the way and such a learning curve, and such a huge investment, change of equipment - you've really been really thoughtful in integrating existing technology but then tweaking it.
Yeah, exactly.
Which is really exciting. Tuomas because you've been specifically on the hardware side; I look to you sort of as the voice of our audience. Can you talk about some specific examples in regards to things like stack up, DRC's. Can you give us some kind of down and dirty, you know, where the rubber meets the road sort of examples of how that's fleshing out?
Yes. So if I first start with the stack up; currently we are using PCB layer stack up in our designs, which is not it's not pure IMSE - and this stack up, this causes challenges and generates a lot of more work when we have transferred in design files between EGIT and for example in the simulator tool. So if we have a tool where we can define IMSE stack up as it is in real products, it makes the design process even faster. Second thing is the dielectrics. So at the moment we are designing and checking dielectrics manually.
It's time-consuming and there were still missing dielectrics in certain places and this caused failures during our production. This is very, very critical, so if the tool has, for example, dielectric generators, check the position for each dielectric and then place it according to user definitions, so it makes design even faster, and also makes the production more easier for us because there are no failures anymore.
Along those lines - from inside of the tool, will a designer actually have helps to help them choose a specific dielectric or is that something they'll need to know ahead of time? And then those dielectric constraints will be inside the tool - or do we know yet?
No we don't know yet.
Okay that's a good answer. That's okay. You know, I really see from my perspective in the industry, this tighter - and the lines between mechanical you know ECAD, MCAD, all the different design disciplines. the lines are just blurring - and I think that's never more true than with your technology. I think you made the lines disappear which is exciting and so enabling! Is there anything you wanted to say about that Sini, just about the different disciplines, or specific challenges that may come into play? Because you're bringing all of these things into play?
Yeah I think one very good example and Tuomas, I'm sure you are more familiar with them, is for example, a simple file transfer. So we need to be able to, first of all in IMSE, we have to be able to convert first a three-dimensional shape into a two-dimensional form. Then design electronics layout, then convert back to three-dimensional format, and during all of those processes, we need to have a file transfer mechanism that actually works in between the tools. So yah, like you said; the lines are blurring and we're excited to see how we can help in enabling this in the tools.
Well I'm very excited - before we wrap up is there anything I might have missed?
Thank you both for this interesting conversation, and I'll be sure to share your white paper and any links you like to share. Is there anything I may have missed, just because of my own ignorance - neglected to ask either of you about today?
I don't think so, not from my side. What do you think Tuomas?
No, not from my side as well.
Okay, well please be sure to share as many links as you can you guys, and again - I want to encourage our listeners to look - this is one set of show notes you're going to want to look into - and click through and see really where the future of technology is going. It's very exciting and as I say, we continue to develop our agenda. You know things like high-speed stack-up, things like that within Altium Designer 19, but in the future we hope to be able to offer the enabling technology in a future release of Altium Designer.
So thank you both for your partnership and working together. It's been a delight and I also invite you again to join us at AltiumLive either in San Diego or Europe. TactoTek will be in both locations and you'll be able to get your hands on it and see and touch this amazing technology it's really going to blow your mind.
So thank you Sini, thank you Tuomas, I really appreciate you - welcome to podcast land.
Thank you Judy, it's very exciting.
It's been a delight to have you and thank you - because I know you guys are - our hours between here and Finland are a little different. So thank you for accommodating our time frame today.
So thank you again for listening to the OnTrack Podcast, we appreciate you so very much. Join us again next time. Until then remember to always stay on track!
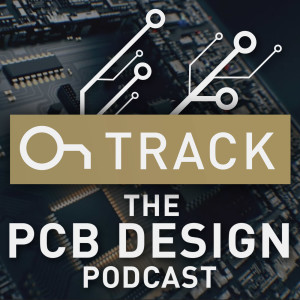
Wednesday Aug 22, 2018
Signal Integrity Expert Eric Bogatin on Best Measurement Practices
Wednesday Aug 22, 2018
Wednesday Aug 22, 2018
Signal integrity expert, Dr. Eric Bogatin, shares why best measurement practices have become his go-to topic when speaking with PCB designers around the world. As Signal Integrity Evangelist at Teledyne LeCroy, a leading provider of oscilloscopes, protocol analyzers and related test and measurement solutions, Eric lectures around the world and he will be one of the keynote presenters at AltiumLive 2018: PCB Design Summit. Listen to Eric and Judy talk about the importance of best measurement practices and where to learn more — from webinars to conferences to the Signal Integrity Journal and Rule Number 9. Eric also has some real insights, so tune in and learn more in this episode of the OnTrack Podcast.
Show Highlights:
- The OnTrack Podcast is in 84 countries! Congrats to Daud Zoss who was the closest guess at 37 countries. He gets a free pass to AltiumLive as Judy’s guest.
- Dr Eric Bogatin will be a keynote speaker at AltiumLive in October 2018
- Best measurement practices - how do you get the answer to the performance, root cause, characterization, etc. as quickly as possible?
- How do you know what the performance of your instrument is, so that you know its capabilities and what the device is doing compared to your measurement instrument? It’s important to know what the properties of your scope in the probe is, to know the properties of the device you’re testing.
- Measurement data: Such as the rise time, frequency or figure of merit must be excavated to give you useful information. How do you get the information so it’s high quality and can be trusted, how do you turn it into information that you can turn into action?
- Eric is also the Editor of Signal Integrity Journal, working with Janine Love and Patrick Hindle.
- Expert content - if anyone is interested in writing a technical article for Signal Integrity Magazine, please write: Eric or Judy.
- Janine Love manages the EDI CON coming up in Santa Clara in October (a couple weeks after AltiumLive). Part of this is EDI CON University offering tutorials by industry experts.
- Industry Experts on the Editorial Advisory Board: Bert Simonovich, Yuriy Shlepnev, Larry Smith and Steve Sandler, Rula Bakleh, Jay Diepenbrock, Vladimir Dmitriev-Zdorov, Alfred Neves, Istvan Novak, Doug Smith, and Lisa Ward.
- Rule #9 - Before you do a measurement or simulation, think about what you expect to see ahead of time, and if it’s not what you expect, there’s always a reason for it. You need to identify the reason why it’s not what you expect.
- Hands on learning is a necessity for students. Eric and Mike Horowitz put together a five-week, standalone crash course on how to design a board.
- Designing for connectivity is just about driving the board to enable finding the parts and laying them out for assembly. Really simple.
- The lack of experience with Oscilloscopes is surprising because nobody has ever taught these students the correct method.
- Hands on experience is giving students an edge in the marketplace. There isn’t enough of the ‘real world’ activity in most Universities.
Links and Resources:
AltiumLive 2018: Annual PCB Design Summit
If anyone is interested in writing a technical article, please write:
To see ALL show notes and watch the video recording please visit:
Hi everyone, this is Judy Warner with Altium's OnTrack Podcast. Thanks for joining again, if you would please connect with me on LinkedIn I like to share lots of information relative to PCB designers and engineers who are laying out boards and on Twitter I'm @AltiumJudy and Altium is on all the usual places; Facebook, LinkedIn and Twitter.
So please let us know what you'd like to hear about on the podcast and we will do our best to get it done. So today I have a rock star with us and he needs no introduction . But before we get going with Dr. Eric Bogatin; I wanted to say that a few weeks back I had put a challenge out there to see if you guys could guess how many countries the On Track podcast has reached; and we have a winner! So congratulations to Daud Zoss. He's a Senior Staff Engineer at Dexcom; he guessed 37 countries and he was the closest one, unfortunately it was only about half, because we've actually reached 84 countries, I kid you not! So anyways, thank you for listening and engaging with us and all across the world. We really appreciate it.
So today, as I mentioned, we have Dr. Eric Bogatin with us who needs no introduction; who is a signal integrity guru. You might know him from many conferences in North America and I suppose around the world Eric has has presented, and I'm lucky enough to be here in California, where I've seen him present many times on Be The Signal and now the Be The Signal and Eric Bogatin brand is flying under the Teledyne LeCroy flag. So he has lots of lectures and demos and things and I'll let him tell you more about that. So Eric, welcome, we are glad to have you.
Hey thanks Judy, I'm happy to be here with you today and tell you about all the things I've got going on.
Well, we're super excited to have you as a keynote at AltiumLive, so we really appreciate you coming out for that and we've done some neat things together with students, so we'll talk about more about that. So why don't you start off by telling us a little bit about your day job at Teledyne LeCroy?
Sure yes, so many of you may know, and I know you - - I knew you back when I had my own company it was Bogatin Enterprises, and I literally went around the world and did training classes. And about seven years ago, my training company was acquired by LeCroy and we continued the training classes and then began to make a slight transition to, most of what I've done over the years has been best design practices.
How to get the design right the first time and LeCroy is in the measurement business; we are the third largest manufacturer of oscilloscopes and some of the highest end oscilloscopes; and our CTO Dave Graef, he likes to say that that in designing, the goal is to get it right the first time, but if you don't get it right the first time then the goal is to get it right the second time; and the way you get it right the second time is, you have to find the root cause of the problem and invariably that involves some measurements. So that's kind of the connection with LeCroy, is we're number three in the scope world and have the highest end performance scopes out there.
We really specialize in the business of helping customers get it right the second time; kind of a faster time to insight. And so we started out when I joined them seven years ago, doing the same Best Design Practices presentations and classes I used to do, and then over the years since then, I've been working on this new area of Best Measurement Practices and so, with my day job at Teledyne LeCroy, I am still Signal Integrity Evangelist, but I spend more time now going around talking to folks about, and doing presentations on what are some of the best measurement practices. How do you kind of get the answer to either the performance, or the root cause, or the characterization, or get the Figure of Merit? How do you get that as quickly as possible?
And recently, in fact, I've got a couple of live events in the Bay Area coming up - actually next week - in last week in August, and then in Boston in September. And you can check the Teledyne LeCroy website for the events page to see where I'm coming next, but those presentations are really focused on, how do you - I call it kind of two aspects of in best measurement practice - one is situational awareness. How do you pay attention to - how do you know what the performance of your instrument is, so that you understand what its capabilities are, so what your device is doing, compared to your instruments. So you make sure that you are not seeing an artifact in the measurement.
Wow that's interesting.
Situational, because I find in talking a lot of folks about measurements; gosh there's a lot of confusion about what's the scope doing. And unfortunately there's no such thing as the ideal instrument; they're always - - or ideal probe, for that matter. There are always interactions of the probe and the scope with the device we're looking at, and it's important to understand what the properties of your scope in the probe are, to know how far away you are from the properties of the device you're testing so that you're getting good quality information about the device you care about and not an artifact of how you're doing the measurement. So that's the first piece of what we try to present and teach - those principles.
And the second piece is - and I see this with my students all the time - that they sometimes feel that just getting the data, just getting the measurement is enough. So they, push the right buttons and they get a screenshot and say: okay , here's my data. And I see a lot of engineers doing that as well, and the data is just the starting place. That's not - you're not done with the data - you need to take that data, the measurement and turn it into information. So you need to extract out, what's the few pieces of valuable information.
Like what's the rise time, or what's the frequency, or what's the jitter? It's a figure of merit that takes a lot of data and gives you one or two numbers that you can do something with. I was giving a talk at one of my events a couple weeks ago, and as I mentioned, that we have this huge amount of data in a scope. I mean, one acquisition can be we can take up to five Giga samples worth of data - but you know stupidly maybe - 10 - 20 mega samples but that's 10 or 20 million data points in one acquisition. It's a huge amount of data but you only want one or two numbers out of it. And so I used to call it data mining, and someone said: hey with all that data there it's not mining, it's excavating.
So it's kind of excavating the data for useful information, and then the third piece - once we have the information - is this: so what? It's how do you turn that information into action? How do you use the information you've got, to tell you is this good or bad? Should I, raise the line width or decrease the line width? What do I want to do with that information now? How am I going to use that to influence a decision? So it's those three steps that we talk about in our workshops; of how do you get the information, do you have high quality of confidence for the data, do you have high confidence in it? How do you turn that data into information, extract a couple of figures of merit, the nuggets of valuable information and how do you take that information and turn it into action?
So that's what I'm focusing on these days, the idea of best measurement practices. In addition to the stuff I've done forever, of best design practices. So that's kind of what I'm involved in now, spending a lot of time going around, doing live demonstrations, incorporating them in my workshops. Now we've got some really cool scopes and bring a lot of test vehicles and structures, so we can do live measurements of various signals. And so it's always a lot of fun when you can have...
A physical scope there, right.
-yeah a working device and the scope, and then people that come to these; you know I love working the crowd, and we talk about: well, if that's really what's going on, if you made the the rise time shorter, what what will you see? Or if I expanded the time base, what's the signal going to look like? And so we can do that as a live experiment in the group. So they're a lot of fun, very interactive activities. So that's that's what I do is my day job now.
Well, that's a lot, and it sounds - you make it sound really fun and engaging. So also, Teledyne LeCroy will have a table at AltiumLive, I hope we can talk you guys into bringing an oscilloscope so we'll let you work our crowd and I'm sure.
You know, another thing - oh by the way - I would encourage people that are listening to connect with Eric on LinkedIn, or connect with me I've been sharing those classes that Eric is teaching, so you'll be able to pick those up and see the different locations that he's teaching those courses. And we will also add those links below here in the show notes.
So if you're in those areas you can hop into one of Eric's classes, and he's super fun too it's a very plain spoken - and like I, can learn things from Eric Bogatin, and I am not, my technical prowess is limited, so I really appreciate that about Eric. The other thing you do, we have some friends in common which are Horizon House, the publishers of Microwave Journal, have published a new magazine called the SI Journal, which I am very excited about and you are also the editor of SI Journal, and we have friend in common Janine Love and Pat Hindle and the whole group. I used to write a blog for Microwave Journal that is put out by the same publishers on their website, talking about making RF boards and all the fun that goes along with that. And so now, Eric is editor of SI Journal, so you can also subscribe to that online. We will also share that link. So how's that been so far? Tell us about your job - how long has it been now? It hasn't been too terribly long?
You know what, I think it was about - - it's almost 2 years now, so I'm just going to...
Wow! I was gonna say a year and it's like two years. Wow.
So I think it was it'd be - - between Pat and Janine they kind of came up - they've been focusing on the Microwave Journal which has been around for 30-some years and this is one of the - I think it's the top...
I think it's like 60 years or something.
Is it 60 years?
I don't know I might be...
It's a long time - it's been around forever.
And it's been a real icon in the industry for good quality articles about microwave technology and with Janine's experience with the Design Con and in the signal integrity world; I think between she and Pat they realized: hey, the industry could really use another kind of curated source of high value information and so many of the magazines that we're used to getting have - - the print magazines have disappeared and they're all online, and so Pat and Janine decided to create this as an online journal initially. And they asked me to come on board as the editor; really the technical editor right at the beginning - about two years ago -
and so since then we've been kind of planning it out, putting together the editorial review board - of really some industry heavyweights and kind of creating a lot of new content, soliciting content from other experts in the industry, in fact, while I have a captive audience here, if anybody out there listening, is interested in writing technical articles for us, that'd be great.
Drop me an email or send it through Judy, and I'd be happy to take a look at what you like to do. We created this and our focus is to provide high value content that's curated. That there's so much information out there online right now. If you do a google search on Signal Integrity or Power Integrity it's not that you don't find anything, you find like 10 gazillion different sources.
You get flooded.
Yeah it's hard to know what's the good stuff and what the stuff is that I should waste my time with and so I think that's really the value of having an online publication or portal that is curated, and that's what we try to do is between myself and Janine and Pat and the editorial advisory board; we try to curate the content so that it's in our opinion what we would consider to be high-value content. And so we don't want to waste people's time or our own time and so there's, we think, a lot of really good valuable content. We've done the traditional stuff of short columns, of feature-length articles. Janine manages the annual conference EDI CON, which is now coming to the Santa Clara area in October. I think it's a couple weeks after AltiumLive.
Yah, it is, it's really close.
And part of that is now I think Janine's calling it the EDI CON University which is going to be tutorials by industry experts that are available for all the attendees. And then she also manages webinars, and if I can just plug a previous webinar. So we had Rick Hartley do a webinar...
Which we love and you know as I mentioned you and Rick are just so well respected and the SI field so I'm glad you snatched him up.
Yes we got him to do one a couple months ago and then that's recorded and posted on the...
Oh great!
-and then I did one a couple weeks ago that's also up there. So we have maybe it's 20 or 30 different webinars and they're all free and all available for anybody if you go to the SI Journal.com website, and you can look under videos and webinars, anybody can access all the content on the SI Journal is free as well.
So, there's some other people that are dear friends Bert Simonovich I know is on your team on the magazine who - - I think is Yuriy on that team as well?
Yeah Yuriy's been involved Istvan Novak has been on the Editorial Advisory Board. We just brought on Steve Sandler - - let's see; Larry Smith who is, he's my buddy, we worked on a book together that came out last year on Power Integrity and he now is at Micron; used to be at Qualcomm, he's maybe the one or two world expert on power integrity. So I learned a lot working with Larry. Let's see - - so yeah those are them.
They're all heavy hitters I mean, all really, they are the industry experts you really have, kudos to Horizon House for putting together such a crack team with you at the helm, which is just incredible, and like you said curating that content. Because there's so much noise out there. How do we bring the noise down and just cherry-pick, the best pieces? And I was kind of around before and as they were launching EDI CON and I was really glad to see them, as the high-speed digital and the RF world kind of moved together and some of the challenges were kind of overlapping to launch a show like EDI CON I think is really exciting and this magazine so, yay! Very excited about that so I can't... and again we'll put all these links below.
I'll even I'll see if I'll go pluck out some of those webinars and put those links in too if you didn't send those to me already.
So while I'm plugging webinars can I plug one other webinar too-
Yeah,
-that I should have mentioned. So I've been spending a lot of time, too much time, traveling doing these live events but also doing webinars; I mentioned the one with SI Journal. I've also been doing some through LeCroy, and we have a whole landing page on what LeCroy has done.
Yeah there's a lot there.
There's a lot of high value content that's all free. Anybody can view them and I'm hoping you'll put up a link to the webinar page from from LeCroy as well.
Okay.
I've put a series together on, a little bit about fundamentals of measurements, part of this best measurement practices series that I mentioned earlier they're one-hour webinars on various scope measurement principles and I'm doing them on a regular basis. I think we have two or three more scheduled for the rest of this year and then we'll have another series starting up in January.
Exciting, I like the idea of this best measurement practices, it's like really practical.
Yeah and it's the same thing with design practice. There are accepted practices that you want to follow unless you have a strong, compelling reason. Otherwise these are the right ways of doing things.
Right.
And same thing with measurement; there are just as many ways of screwing up a measurement as there is a design and so you've got to pay attention to both of them.
And there's a human in the loop too besides your probe and all that, so.
Oh absolutely.
So if the human isn't 'tuned up' -
Yeah
- now so one of the principles that I teach my graduate students and at University and also engineers I talk to, is I call it rule number nine and... have I talked to you about rule nine? Okay I'm definitely gonna be mentioning it at the at my keynote because I think it's one of the most important rules for any engineer and basically it says: before you do a measurement or simulation, you want to first anticipate. Think about what you expect to see and I have found that to be the most valuable kind of habit to get into, because just like you said, when there's a human involved it's easy to make a mistake. And how do you know that you don't have the connector connected where it should be, or how do you know: I think I'm looking on channel two, but I'm really going on channel three? Or I typed in 17 but I meant 71? How do you know?
You can check yourself but there's a limit to, how well you can check yourself and so, if you think about what you expect to see ahead of time, whether measurement or simulation and you look at the result and it's not what you expect, there's always a reason for it and you shouldn't proceed with that information until you've identified how come it's not what I expect. And when I do these live demos in front of groups, I'm constantly making mistakes because you know, it's under pressure. I get a screw in that connector and I'm not sure which demo am I on right now, and so I'm always looking at the screen to see, is it what I expect to see, and I can tell instantly when I've done something wrong because I use rule number nine. And I sometimes play a game with the audience, the engineers there, and say: okay, we expect to see this waveform go up and then down and it's flat - how come?
And it's good experience, good practice, that thinking of what could go wrong in the debugging process because that's what we all end up doing and the more experienced we can become at finding the root cause and why it's not what we expect I think, the quicker we can get to a good answer and move on to the next problem. So it's an incredibly powerful habit that I use all the time and I try to teach all my students.
This is what I love about your classes and things you teach Eric. I've sat in a few of them over the years is, that they're insanely practical and intuitive and memorable. Like rule number nine, I can remember that right, so I really have to say that about you.
Of course, don't forget I also reinforce good behavior with chocolate so that...
Oh yeah he does! He throws chocolate out at his classes so yeah it's like Pavlov's dog, yeah it's so true. Well I wanted to jump into the way that you and I started working together, is I think a month or two ago Iconnect007 came out with a magazine with an empty pair of shoes walking down the street, and it said, who's gonna fill your shoes? And everybody seems to get on this bandwagon about all the people that really, fundamentally understand PCB design in regards to, not just designing but manufacturing, assembly, the whole, all the stakeholders that are kind of implied in that process are greying and gonna retire, and so you know, there's been studies out by UP Media saying - by a pretty large sample - saying that in under 10 years half of PCB designers are going to be gone and so everyone has sort of gotten to this hysteria about it seems like the unanswerable question.
What I appreciate that you've done is I'm going to call you professor now - he wears lots of hats - professor Bogatin called me up and said, Judy, you know, I'm gonna do this program, he's used different tools right now that this - I think the students were sort of driving, or somebody was driving one at Altium Designer, so you kicked off this amazing semester-long course at the University of Colorado Boulder and you - I think co-teach that right Eric?
Yeah so I can give you the quick history.
Okay let's hear it.
So I've been teaching a graduate signal integrity class at CU Boulder for a number of years, based on my textbook and in talking to folks there, we realized that our students - so CU Boulder tends to be very project oriented very hands-on we believe in that, you know you learn from textbooks, you learn from studying, but you understand by doing. And it's the hands-on part that you really - everything comes together. And there were a number of classes that required building circuit boards and I would get called in as a consultant to help them in designing the circuit boards and there's relatively simple boards, two layer boards. But these kids had absolutely no idea. They could push the buttons on the tool, but they had absolutely no idea how the performance was influenced by it by what they do in the layout. And so it became really clear that, boy it sure would help if they had a little bit of guidance in how to design boards correctly. And so a number of us got together and realized: hey, we need this more formal training and a buddy of mine Mike Horowitz, who is an expert at design of circuit boards, we got together and put this course together which was - and it's kind of a funny organization too - we're also trying another experiment.
At CU you are semester based, and some courses are typically like 15 weeks or so. But we are experimenting with creating short five-week modules so it'll be the full regular course, that is a normal schedule of of 3 hours per week but it only lasts for five weeks. And so, Mike and I were tasked with putting a course on Printed Circuit Board Design and Manufacture together, that would have a five week beginning piece that could be a standalone so that most students, undergraduates, would take that and that'd be enough to get them going on their projects and then everybody else would continue for the rest of the ten weeks. And that would go into more detail so it gets them more experienced at circuit board design. And so that's how it got started, and Mike and I worked on it - it's every semester; so we did it twice last year and now. So that was kind of our joint development. And now Mike has gotten more involved in his CEO activities and so I'm gonna solo it this semester.
Oh okay.
So the format is basically a five-week crash course on how to design a board so you have a good chance of success when you build a two layer board. And then the other five weeks are more the same, more the technical detail about measurement technique - this idea the best measurement practices. How do you bring up a board? How do you design a board for simple tests and bring up? And then we'll do four layer boards, and then a little bit on the more high-performance systems. So it's a little bit more advanced and really you know, the way we've positioned it as: there are two levels of design. The first is if you can build a prototype and build it with a solderless breadboard and have wires going all over the place; if that works then designing the circuit board and having it work is really straightforward.
We call it designing just for connectivity you don't have to worry about performance, it's about, you want to be able to manufacture it, but performance isn't on; the interconnects don't matter, and and some of the student designs are just designed for connectivity. It's just about driving the board so you can find the parts of the library and build it in the schematic and then place them on the board and lay them out, so you can assemble it by hand - pretty straightforward.
But many of our student designs these days, are getting more sophisticated. They use a Wi-Fi connection, so you have RF on the board, they have sensitive analog to digital converters on the boards, they have components that sometimes -even BGA components - where the microcontrollers are using a really fine pitch; hard to design by hand, and some of these have a couple nanosecond edges where ground bounce is a tremendous problem. And so we're focusing our class on how to design a board. Not just for connectivity - that's the easy part - but for performance, so that you can designed so it's manufacturable, it's lower-cost reduce the - so much of it is risk management - and then kind of the basic performance issues to worry about.
And in my keynote, I'm thinking that I will probably present on what we have found to be the two most impactful design issues in designing a board, not for connectivity but for performance. If all you think about is connectivity you're gonna run into two significant problems. And so one of the topics is this idea of rethinking how signals propagate on interconnects and I've done this at PCB West and I did it at some of my other courses - and I had a couple people come up to me afterwards and tell me that it was a life-changing moment for them. Because I completely changed the way they've been working on boards for 20 years, and I completely changed how they thought about signals on boards. So I hope it will have a similar impact at AltiumLive, but it's going to be about how to rethink and how to train your intuition to think about how signals really propagate on interconnects.
I loved your Be the Signal....
so... and I'm sure this is a little bit more complex than what you're gonna present, but I remember the first time I ever sat in a course by Eric Bogatin, and he was talking about 'be the signal' and he's like: if this signal's moving from A to B what do you think is gonna happen to la-la-la... and I'm sitting there as a non-designer and he's like: no, be the signal. What would you do? And kind of helped us to frame, kind of this visual - and I'm a visual person - so I like to kind of visualize, what the things that were going on, in that signal path to create whatever it was. So I really loved that.
And that's basically what I'm going to be talking about, that Zen approach to thinking about signals propagating and and how to apply you know - I'll probably mention it once, in my talk, about how to apply master's equations but in an intuitive way, to understand what's really going on in the interconnect.
So Eric's talk is called 'Living in the White Space' and that will be relative to signal propagation and I'm sure all of us, our brain will explode a little. I have these moments with Rick Hartley from time to time too where he says something and I'm like: nah! You know it could be that simple or whatever and I'm sure, you know Rick Hartley is a student of Eric Bogatin so, I'm sure it's more of the same.
So, well I really appreciate you Eric, taking on these students at university level. Here at Altium absolutely, I think I would do this part of my job for free; is to help students get equipped with not only tools - like I can give them free tools - but that's a really incomplete model, for them to learn. They're learning about electrical theory in school but really how to design a board, and how does - - I just finished a podcast today with Julie Ellis who's a Field Applications Engineer from TTM - what about stack-up? What about all these variables and how they come into play, that are not taught at university? But I love that you've brought them in at a university level because I think these are the kids - I think these are exactly who's going to fill some of those shoes, and they may be EEs laying out boards, they may end up like Rick Hartley did saying, I like just designing boards better than circuit design. Who knows? We don't know.
What has been some of your surprises by the way? What feedback from students?
So I think two things absolutely surprise me; one is, their lack of experience with oscilloscopes. That their way of using oscilloscope is first to push the autoscale button. And I slap their wrist if I catch them doing that, or pushing every button without knowing what it is until they see something, on the screen...
Until the light goes on, they're looking for the LED.
-and and so they, just the basic understanding of what an oscilloscope does and how to control the vertical/ horizontal and the trigger. You know the very basic things. A lot of these kids; nobody's ever sat them down and talked to them about it, so we focus on good - again - best measurement practices in the class as well as the design. The second thing is, there is a disconnect between what you learn in the textbook and what you see in the real world and it's the same thing, but you have to know how to apply what you learn in the textbook. And I don't think any university does enough of that hands-on, real-world activity. We try to do it a lot at CU, we have a lot of projects that students get involved in. Most of them are really about designing a little robot or designing some gadget that does something with the code that you write in there. So a lot of it is - some software, as well as the hardware.
But in our class we try to close the loop of the; here I do an estimate or calculation, and here I do a measurement. Like one of the first labs we do is blowing up traces.
That's fun! It is. Everybody likes blowing up something.
Everybody likes to blow shit up
[laughter].
And so the question, the first question I ask them is: okay, you're gonna lay out a board and you're gonna put some tracer - what line width should you use? You can select it to be anything you want.What line width should you use?
And so one of the things that surprised me is, when I asked the students is, they thought that a six mm wide line, just the narrowest that most fab shops will do. A six mm wide line, was too narrow because it's way too much resistance, or I can't put more than a couple milliamps of current through it. So I gotta use a twenty mm wide line, or fifty mm wide line. And it's the kind of thing that, the very first day in class, we calculate or we look at how do you calculate the resistance of a trace? How do you calculate what the maximum current handling it, using the IPC guidelines that Doug Brooks has been so heavily involved in.
And when you put in the numbers you realize: oh my gosh, it looks really narrow on this board it's only six mm wide but but gosh; it's resistance is going to be still in the tens hundreds of milli ohms for typical lengths. So it really isn't that high a resistance even though it looks really narrow because copper is an incredibly good conductor.
Exactly.
People don't have good calibration of that. And then, so I'll give you the number, and I hope none of my students are listening to this because they're gonna figure it out in class. But if you look in the IPC specs for maximum current handling for a six mm wide surface trace; it's like two amps or three amps and when we put two amps through, we have a test board with the different line widths on them. When you put six amp - - two amps through it, you find we can monitor the voltage across it with constant current and see the voltage increasing because it gets hotter, as you see the beginning of the runway, and RNDF around three amps, IPC's around two amps, around three amps, darned if it doesn't go to thermal runaway and we zap the trace and so, you can really get a good estimate by putting in the numbers ahead of time, of how some of these interconnects are going to behave.
But it's that habit of putting in the numbers doing simple estimates, applying what we learn in class to the real world, that the students don't have that good experience with and that's what we try to do in our class at CU.
Well to your point of hands-on, I feel like that's something that for whatever reason has left our education system too much right there's no shop at school anymore, there's no metal, there's no like just - and it's not just, what they would consider low labor skills or whatever. It's just hands-on learning the kinesthetics of it because I bet you dollars to doughnuts that kid, is gonna remember blowing up a three amp trace, more than if he read something about it in a book right?
Right, and sees the smoke and it pops and, there's this feedback well, what I was telling you about is, again one of my favorite parts of my job is, we just came back about three weeks ago from filming these kids that are doing the Hyperloop Competition -
Oh I'm gonna send you this video Eric - you're gonna die because what they do is so awesome and it's just because they get to do hands-on and they make a good - - there's no way they're not making, more mistakes per minute than everybody else in their field, but because of that and because the lack of constraints they have on them as far as businesses and law and whatever, you know this one team we sponsor is from Munich Germany, they just broke the world speed record inside the tube that Elon built at 290 miles per hour.
Crushing!
There's commercial companies with venture capitalists that haven't hit that number. Because they're young and they're hungry and they're hands-on, and they're excited. But these are the kids who I think, there needs to be much more of what you're doing. I wish every University would, hopefully you'll set an example that others will follow. And by the way, I've cited your course to a group of six universities I was invited to speak at UCSD, UC Davis was there, five other universities and I put a screenshot of your course -
Oh that's great
-and so I, so if you start getting weird phone calls...
(laughter]
-because I'm like see what he's doing - you all need to do this you know, so hopefully the word will spread but until that happens things like the Hyperloop competition, the FSEA competition, where kids get to get their hands on it and blow stuff up and do it wrong, until they do it right, and learn how to use an oscilloscope in this really hands-on manner well these kids are coming out of college and the internships of these kids, one of these kids from University Wisconsin in the Hyperloop team he's a Qualcomm right now, the team lead is going to SpaceX on internship - companies are plucking them out because of the hands-on. So I think the more we sort of beat this drum and spread this message, I again, something I'm very passionate about - I know you are too - and thank you so much for doing that course and we cannot wait to hear from you and about Living in the White Space at AltiumLive.
Thank you so much for taking time out of your busy schedule.
Well I look forward to seeing you at AltiumLive and all the other viewers that you have and I hope folks come up in and say hi while I'm over there.
Okay will do, and make sure - well not make sure - see if we can get LeCroy and company to bring out an oscilloscope so you can - -
We will definitely have one at our table.
Okay good, good I think that would be something notable and something that people, the attendees would enjoy so thank you again Eric this has been...
Thank you Judy.
Thank you again, this has been Judy Warner with Altium's OnTrack podcast and Dr. Eric Bogatin of Teledyne LeCroy. We look forward to being with you next time. Until then, remember to always stay on track.
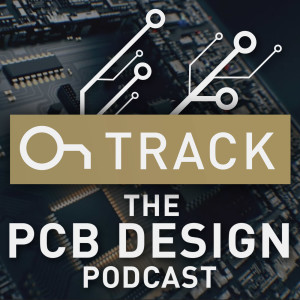
Tuesday Aug 14, 2018
Concurrent Engineering with Bill Brooks from Nordson Asymtek
Tuesday Aug 14, 2018
Tuesday Aug 14, 2018
Learn about what is involved in true concurrent engineering and get practical tips for including stakeholders early on in the design process with Bill Brooks from Nordson Asymtek. When project collaborators come together up front, then they move forward together. Hear how Bill spends the time up front to get everyone aligned during the PCB design process to ensure fabrication and assembly processes progress with minimal issues.
Show Highlights:
- Bill had an interesting childhood. His Dad was an inventor and worked on the Pioneer 10 spacecraft. He introduced Bill to the electronics industry.
- He also started a board shop in the garage and created his own hydro-squeegee, using peanut oil.
- Bill’s career started when he worked as an Electronics Technician for almost two years. When his employer started hiring designers to do PCB layout work, he grasped the opportunity.
- Back in the day, people used to sign their PCB artwork.
- There are a host of stakeholders involved, the designer is like the glue that holds everything together. Some of the stakeholders are: Fabrication, Assembly, Testing, Marketing, Managers and Engineers.
- When do you get the stakeholders involved in the PCB Design process? The IPC standard is to have a design review upfront, before design.
- The designer is the only one who can control moving the design through the process and make the board survive.
- We involve many stakeholders from the outset. Divisions like purchasing takes care of primary suppliers to ensure they can provide what’s required.
- We do system integration in-house. Partnering with other companies has become a big deal and it’s working very well.
- What does Concurrent Engineering mean? Considering all aspects, together, upfront, then moving forward together. Spend the time upfront to avoid wasted time and effort later in the process.
- Educate people who have control, they take care of everyone and everything goes smoothly, works correctly, and is right first time.
- Bill’s Dad used to say ‘the hurrier I go, the behinder I get.’ You need a disciplined management team to do the work upfront, be quick but don’t hurry.
- A ‘quick and dirty prototype’ is a myth.
- Use software to load projects into a common depository - keep it current and work in cohesion with regular refreshing.
- Bill and their team use Playbook, which enables managers to have a full overview of every division’s progress and enable proper scheduling.
- Designers after hours: in 2008 Bill was introduced to sculpting. Started attending classes, commencing a 6-year love affair with sculpting. He now teaches on Saturdays.
- Rick Hartley encouraged Bill to do mentoring. Bill is now part of the International IPC Executive Board and has received an award for his contributions.
Links and Resources:
AltiumLive 2018: Annual PCB Design Summit
Hey everyone this is Judy Warner with Altium's OnTrack Podcast. Thanks again for joining. Today we have another great guest - do you ever get tired of me saying that? Another great guest because we just have them every time, and we'll be talking with Bill Brooks today from Nordson ASYMTEK, and before we get started, I just wanted to remind you to please follow me on LinkedIn. On Twitter I'm @AltiumJudy and Altium is on LinkedIn, Facebook, and Twitter - and also if you'd rather watch this on video we also have this on Altium's YouTube channel under videos, and you'll see all of our podcasts recorded there as well.
So today we have Bill Brooks, has been a great contributor to the industry, as well as being a very talented designer in his own right. So I thought you would enjoy learning about his long history in the craft of PCB design, so Bill welcome; thank you so much for joining us here. Bill comes from just up the freeway here from our office in La Jolla, so it's handy to get him over. So Bill won't you talk about your professional history? I think you, like many printed circuit board designers; you were kind of set up to be in this industry, but you found your own path. So, tell us a little bit about that?
Yeah I guess when I was a kid I didn't know where I was gonna go...
Yeah me neither.
-my dad kind of introduced me to the electronics world, and right out of high school actually, I was still in high school - my dad was working in the aerospace industry and he decided to start his own printed circuit board shop. He looked around San Diego at the time, and there weren't a lot of shops to go get boards made and he said: well, I can do this. And so he looked up the information and we started making printed circuit boards in the garage.
Good times, that was a long time ago where you could set up a board shop in your garage.
Yeah it was - today it'd be completely illegal.
Yeah right.
[laughter]
I think the neighbors complained, he created his own hydro-squeegee and he was using a fusing oil, which was I guess peanut oil, and he bought this big 50 gallon drum of peanut oil and he used a check valve, and he put this - - he used air pressure to push it through a check valve and to spray it so he could put the boards down to get them hot after they had been coated with solder and then squeegee ''em out as he pushed on the pedal on the floor. And it would just make this nice beautiful-
It's a handheld hot air leveling machine!
-Yeah it was very dangerous, in fact, I think he got burned a couple times.
Oh I'm sure!
-but the neighbors just loved it because they’d look down at the corner of the cul-de-sac and they’d see this giant plume of black smoke coming out the back of the house, going: what's he doing over there? But dad was kind of an inventor and he liked to invent things. So he didn't go out and he was kind of a 'shade tree mechanic' - he'd figure out how to get something done on a dime and do it himself. And I guess that same ingenuity was something I picked up, I figure out how to get things done.
So how did you end up going down the design path, from building boards in the garage?
Hmmm it was kind of convoluted. I thought I wanted to be an Electronics Tech and eventually Electronics Engineer, and I started down that path. I got a job with a company that was making television headend equipment; the transmitter part of it, there was channel 52 UHF subscription television, Oak Systems and I started working as Electronics Tech for them and I did a lot of work for them for, oh at least two years as a Tech, and they were hiring in printed circuit board designers to do the layout work. And I had already learned how to do layout work with my dad's shop when I was younger and I looked at that, and I said: welI can do that. How much do you make? And I think I was making like seven bucks an hour at the time, and they were making like 10 or 11. And I said: I could do that, and I told my bosses I want to do that - I can do that! And they were: okay we'll get you in the other department and I started working in the drafting department. So I got a $3 an hour raise and I started doing layout work instead. And it kind of set me down that path. So that's how I got started anyway.
So Bill, a lot of people that have been around a while, both you and I have been around a while. There's no college to learn what you've learned. So how did you pick up, we were discussing this earlier; you've done so many aspects - RF, some electronics and mechanical, how did you pick up all those skill sets, sort of along the way?
Yeah that's kind of a long story really. My dad started me when he had his shop, and gave me a printed circuit board to do as a way to teach me how to do layout-
Okay.
-and we went to the TI Handbook and found a circuit for an audio amplifier - 10 watt audio amplifier and he said, why don't you try to build that? And so I made a schematic, I took the schematic from it, and I laid out the board and we manufactured the board and I bought the parts and I put them on the board, and I soldered them and turned it on and talked through a microphone - it worked and I went: yes that's hot!
It's so funny.
I remember in seventh or eighth grade, we had a science fair in junior high and everybody made their science project; we had a bunch of tables all set up and my dad said, well why don't you make something - - an electronic metronome? It has to do with music, and so I drew a schematic and I put the whole thing up there, and I built the metronome and I turned it on so it'd go 'tick-tock' 'tick-tock' you know, and I thought that was amazing. It was a really great and one of my friends said: Bill that was so cool, how you did that because I didn't have to do any of the work and I still got credit for it and I said well it was it was a challenge. So I took it on I put it up there but I didn't win a darn thing!
The guys who made the volcano that spews out all the stuff - they got that prize. So people didn't appreciate what I was doing. I felt a little bit geeky and kind of out of the norm as I was growing up. But I was fascinated with electronics. I was almost intimidated by it. My dad was a very good R&D guy, and he worked in the aerospace industry and he actually worked on the Pioneer 10 spacecraft, it traveled all the way past Jupiter and it's outside our solar system headed on for Aldebaran now I think.
That's crazy.
So that's kind of a neat thing and I think on one of his print circuit boards, if you find down in the little corner you'll find his initials there-
Out in the outer regions of space.
-yeah and I talked with Dr. Walker Fillius, he was the principal on the project at UCSD and after my dad passed away and he sent me back an email and he said: you know someday these little green men out there they're gonna find that and wonder: what does that mean? Why did they put that there? And a lot of people did that back in those days, you used to be so proud of your artwork you'd want to sign it and they did.
Right, that's funny.
Yeah.
So from I have to say, I think that was probably really invaluable experience for you, very young, to put together that design affected manufacturing, affected assembly, affected performance. Like at a very young age, you saw that whole overarching process - sort of on a small scale - but still; and not everybody gets that experience even today, few designers.
Few designers have ever been in a shop and actually made a print circuit board. A lot of them are dealing with the drafting side of it; they don't see the whole process.
Right and it makes such a difference to decisions you make as a designer.
Absolutely.
Right and so I can see how that sort of set you on a path to be a little bit more globally minded about the whole soup-to-nuts kind of - - from design to reliability or how something is actually functioning.
It has a lot to do with curiosity, it's funny; I've been listening to a book about Leonardo da Vinci and one thing that was amazing about him is, he had this insatiable curiosity, to almost distraction, I mean he would look at things and go: why does it work that way? And he'd start, he'd set himself a task to figure it out - and he didn't have a college or someplace to go learn those things - he had to do it himself. I've done a lot of the same kind of things in my life. I get fascinated with something and I go: well, I can figure that out, I'll go figure it out - all it takes is being brave enough to try and not being afraid to fail. Failure is just an opportunity to learn more.
So I think it was Edison once said , he did like hundreds of different ways to try to do a light bulb and he said, well now I know a hundred different ways not to make a light bulb, it's okay-
I still finally need way to know how to do it right?
-but those those skills and the curiosity drove me into expanding my knowledge base. Getting into printed circuit boards, I wanted to learn how to take the thing I knew how to make, and turn it into something that was a product. I wanted to find out how to make that product appealing to somebody so that it made them happy with the product and not unhappy with it. And that kind of dovetails with what we were talking about before.
We have, as designers we're kind of the glue to the whole design process. We may not come up with the initial idea that needs to be created, but we take that idea and we turn it into reality and we not only have to turn it into reality, so that it's electrically functional, but it can be manufactured in a reasonable way that's not super expensive, that's reliable, that survives harsh environments or abuse. It has to be testable so you can provide for test points and things of that nature. There are a whole bunch of stakeholders involved.
People who are - their job is keyed on being able to take what I create and turn it into a product that they can actually sell. The marketing people have to make sure that the product meets the customer’s needs. I have to be aware of that when I'm designing it so, I don't design in some function that makes it fail there. I have to be aware of those things. So the designer - they're kind of the key glue to the whole group.
But I find that very refreshing and I think most professional designers, from our early days of making a simple 2 layer board say, it's so much more complex now. So we tend to like head down, into our specialty right and I think, as you have said some engineers/designers have never been inside of a board shop.
Right it gives you myopia, you can only see just your part of the whole process.
And I can understand that because, I don't say that from a critical perspective, it's a very complex process. We're time constrained, resource-constrained, so it's hard to put your head up for a moment so-
You just named some of the stakeholders.
-I would say fabrication for sure, assembly, testing...
You mentioned a marketing department, probably managers too.
Managers all have cost and time constraints, they have time to market that they have to be worried about. The engineers of course, typically are going to be concerned about, can they get the parts or are the parts available; are they gonna be end of life parts?
Yeah that's a whole fun bag of fun there.
The hardest part for some designers is, they'll get the board 90% done and then the engineer comes back and goes: I can't get that part anymore, I need to put a different part in and that's bigger than the one I gave you before. And so you got to go back and fix the circuit, so you can fit that bigger part in there and make it work. And it gets quite challenging.
So when do you recommend to get those stakeholders on board and collaborating?
That's a great question and funny - if you go through the IPC; I think it's 2221-standard - it's like the very first - almost first paragraph and the thing it says: make sure you have a design review up front first, before the designing begins. Why do they say that? Those people all are going to bring their expertise, and their wants and desires, and their concerns to that meeting. Well they're gonna be a part of that and give that information to the designer who really is the only person who has control over what it ends up being. The creator - they are the creator; they take all the information and they create something that can be built, tested, cost-effective, survive, functional, not have EMI problems, EMC problems... it has to pass safety agency requirements like TV and UL you know?
Yeah.
Or stand somebody handling it and giving it an ESD shock - thousands of volts - how's it going to survive that? You know, we do Hipot testing, there's a lot of work that goes into making a board that just is not - just connect the dots.
So you're now working with Nordson ASYMTEK, which makes assembly equipment correct, or is there more than that?
Their key thing, the company I work for they're making robotic equipment. The equipment allows manufacturers to do high-speed manufacturing very reliably and typically they're dispensing fluids. They have a few divisions that do board inspection. They have one that does plasma cleaning-
Mm-hmm.
-it's very common, I think it's MARCH - - I think is the name of it, something like that, but primarily we focus on fluid dispensing; got lots of patents on fluid dynamics, how to dispense a dot of material that's the exact amount of the material, in the right viscosity, of the right mix of materials, and at the right place , at the right time.
Right.
Very, very challenging stuff - we've come up with some really high tech equipment that are making our customers real happy.
That's great, so when you do, on a practical, where the rubber meets the road stuff - when you embark on a new design - do you get the stakeholders together? I mean how do you do that?
We get a large number of them involved. We have a purchasing department that cares about who our primary suppliers are. They review them; we go qualify them, make sure that they're going to be able to supply what we want, when we want it, at the price we want it. We use third-party vendors to make the boards, assemble the boards, test them. We put everything together in-house. They call us a system integrator kind of thing - and I guess that's one way to refer it. So the final assembly stuff all happens in the factory; and then we ship overseas and here in the United States and Europe.
So you used a term which I've heard before and just tell me what it means to you, is the term 'concurrent engineering'?
I was introduced to that a while back, and to me it was confusing at first. Of course I've been in the industry a long time and there used to be a model where engineering would be a little black box and inside, all the engineers do all their stuff in there, and it was black magic, and they got it all done and then they went; pop - and they threw it over the fence and said: okay, you guys figure out how to make it. And that's as far as they went. Engineers were done; okay, I'm working on my next thing have fun. And the manufacturing engineers get it and go: oh my god, how are we gonna build this thing? And they almost had to re-engineer it to make it producible. So that model was going along for quite a long time here in the United States, before they started analyzing what the Japanese were doing and looking at their manufacturing process. It was very organized, and they introduced just-in-time, which has affected the whole supplier chain.
But partnering with other companies to be able to be successful has become a big deal and they can reduce the number of staff that they need to do what they need to do. They can have highly qualified people doing what they need to do - they don't need masses of people - and then they can subcontract things out get them delivered on time, put them together and get them out the door and they're very very good at it.
Concurrent engineering means thinking about everything up front. Not just your part of putting it in a black box and playing around with it until you're happy and then flipping it out and saying: you guys figure out how to build it. You want to bring the people that are stakeholders in up front. And then together, you move as a group. And the people involved in the engineering part of it have to understand those people's jobs, because they're their customers.
Right.
They're the ones - they're gonna use what they create. So we spend more time up front to make sure that they don't have to work harder, that they don't have to redo it, that we don't waste money and time out there with failures and have to come back and make changes and send it back out, saying: how about this one? No that's not good enough you've got to do it again. Oh how about that one? No that's not good either. So you educate the people that have control of it - they put the intelligence into it to take care of them and everything goes smoothly, and we make a lot more product, a lot less expensive, and that's right the first time.
You and I were swapping some little statements right? So one I remember you saying - - I don't remember who you cited: the hurrier I go...
That was my dad...
-that was your dad.
Yeah 'the hurrier I go, the behinder I get'.
[laughter]
Yeah and that's so true I mean it's funny if you have this: I'm the only important person in the world, and what I'm doing is the most important thing and I don't care what anybody else thinks or wants to do. You can create something, in fact, I've seen some amazing sculpture, of components that were soldered together and in the most amazing ways and it was an electrical circuit, it worked, functioned.
Yeah - but if you touched it, it would fail, if you moved it, it would fail. It wasn't built - it was just to see what would happen to the electrons when they get moved around that way. So people - and there's a desire - typically management, has traditionally figured, well - if you whip the horses harder and make them go faster you'll get there sooner.
I have seen that by the way being a board manufacturer and selling to and working with designers. The constraints are brutal sometimes...
They can be.
-and it's like, well if you want me to put out good work, you need to give me a little bit more margin right and so I think, to your point is, you had also said that it's really a myth, the idea of a quick and dirty prototype.
Yeah it really is
- it's kind of a myth - I've worked in environments where there was a philosophy that said: we can be faster if we just slap something together and we go build it and we bring it back and see what it does. I think the people that had that idea probably didn't have any simulation tools. They didn't have any way to predict how it was going to behave - so they would make one and go try it, and then they'd find out how it didn't work and make another adjustment. So I remember working on a board that had 17 or 18 different iterations of them trying different things...
That's so expensive and such a time suck!
-Very expensive and it takes a lot of patience - you just kind of have to work with them and keep going and keep going. But we win when you get a management group who - I happen to work for one - it's very, very smart people, they'd like to do it right the first time. So they spend the extra time upfront. They do the research, they analyze what's going on, and then they go build it. When they build it and bring it in we're like 98 percent there, most of the time. Very few times maybe we get one or two little blue wires and we're good to go and take a few changes boom - you're out the door. And that's a good thing and CAD tools help us do that too, by the way.
Yeah well, and that's a really insightful management team I think, to know that if you take the disciplined time to do it up front, it really saves you so much on the back end in regards to time, money, and resources. I always like John Wooden's quote; he used to say: be quick but don't hurry, it's the same thing - like be nimble and quick - we don't want you dragging your feet but don't be hasty.
I think part of it is just having a good work ethic, the self-discipline to say: you know what, I'm here, I'm gonna focus on this, I'm gonna get it done, and I'm not gonna let Joe come over and talk to me over a half hour about the thing he was doing up on the mountains last weekend, or stop and shoot with people at the water cooler or whatever. I'm gonna stay focused on it and when I'm not here then I'm doing other things, but when I'm here I'm focused. And I think that the managers; they should analyze the people and look and see what kind of people they have, and try to work with them to get them to have that work ethic. We've got lots of distractions in our world, plenty of them, things that can take us all over the place, so it's just a personal discipline I think.
So we talked about, in those cases - I'm thinking about the people that are designers that are listening to us that may not have such an insightful management team as the one you work with and I'm sure you've worked for other less insightful management teams. How do you recommend that you tactfully, and professionally, push back to say, I need five more minutes to get this right - how do you do that?
Well to frame it as pushback, is probably not politically nice but it's a communication. I think one of the things that you don't do, is you don't go off into a dark room somewhere and then pop out with a design later on and they're going: what's happening what's, happening, what's happening. So you have to have a lot of open lines of communication with your team.
We use SVN as a way to load our projects into a common repository and then the other engineers that are working, can download that and refresh it, make it current so the master is in the SVN file. So I'm working on basically a copy that I refresh every time I do some work. And I do that regularly, I don't wait very long and I'm refreshing it - I'd do it many times an hour sometimes. And sometimes maybe I go for a couple hours and then we'll refresh it, but it's mostly based on how much change I have made to it.
The idea is to keep it current and keep the lines of communication with the other people concurrent so that they're aware of what's going on if they're busy working on the schematic while I'm working on the board we can do that in parallel, and I can do my parts get them done and then they can say, oh I found out I have to change this part, or I need this other circuit in there and I've just uploaded it - you can pull it in and and make the changes. And we do that very often.
Which is really great and I know here at Altium, R&D is working very hard to make sure that people can work concurrently and building those subversion networks and, even going beyond that, as we delve into Nexus and other products is to enable that, so you guys are seeing each other work in real time.
Often times this is kind of a neat thing about that tool. We typically, the group I'm in is the new product development group, so we take the 'pie in the sky guys' stuff and we turn it into a product. Then we have Reliability Engineers who have to design a testbed to test the product. So oftentimes when the schematic gets to 90% they've got a copy of it and they're looking at it while we're designing it...
And there's the concurrent engineering isn't there!
-Exactly.
It really is a tool that enables that concurrent chain.
It enables it - so we're able to do that and then the guys in production want to know what's going on with it, so they can pull down a copy and look at it, and then the next time we have a review meeting they'll bring their thoughts to the meeting and they can say: we like what you did over here, but we'd like to change this because it helps us be more efficient, and we can run that back there because we need to do that; we listen to them...
Which is so great.
-having that dynamic - real-time communication - it's really huge in being successful the first time.
Yeah that's great, it's great to hear. So but...
tact is used to push back.
-tact yes.
I used to joke with my boss; did you ever see the movie The Money Pit?
Yes.
And the: we're gonna fix the house and the farmer shows up and says, how long is it gonna take? Two weeks, two weeks. We used to do that. Looks like, wow this will take two weeks. Most people can accept two weeks, but we've got a new tool now at work; Playbook - and it allows them to get all the stakeholders involved in helping us schedule the project. So people who say I'm gonna have my test part of it ready at this time, and I'm gonna have the board ready at this time, and I'm gonna have my schematic ready at this time.
The managers can see the whole thing without having a good run around and bug everybody - it's all right there.
If there's a problem with a schedule - update it so we know what's going on. Tell us, and they get it; they see the impacts, they see when things are going to happen and they can strategize and make plans on how they're gonna pull something in or adjust something to be successful.
That's great to create the level of transparency right?
Yeah so pushback is really more...
Well you know, that makes it sound like the manager's a bad guy. They've got a job to do and they've got to get a product to market in a timely way, at the right cost, so I'm just saying is sometimes to your earlier comment like the whips to the backs - at times it feels like that and sometimes you have to stop and go: okay...
How can I communicate better?
Yes, how can I communicate this in a way that makes me me your ally here?
Exactly.
I want to help you win, we're on the same team by the way, and me getting this done right the first time...
You can help me be successful in doing it the first time, and you, and you, because I want to get all the things that you need into the design. That way you're happy with it and you can make it and you're not gonna go; damn that Bill Brooks - why did he do this?
Oh gosh we love the finger pointing don't we?
Yeah I've lived through a lot of that.
Well Bill, this has been really good and really practical, I think where the rubber meets the road. And this part of the podcast, I sometimes like to call Designers After Hours. I want to particularly focus on what you do after hours because you are a very creative kind of - use both sides of your brain - but you have a very strong right brain. So can you tell us a little bit about what you do after hours when you're not designing boards?
Gosh - let's see; was it 2008? I went through a divorce and I was trying to find something to do with my spare time and I got introduced by another engineer at Datron World Communications where I used to work; and he was taking classes in sculpting and he showed me a picture of a sculpture that he was creating; this head of his wife, and I had met his wife - she was wheelchair bound and it was so neat to see the love, you know. He is caring for her and she needs him to push her around and whatever. But he was making a sculpture of her and I thought that was really cool and the likeness was amazing! I thought, you really did a good job, I was really impressed with it. How in the world did you learn how to do that? Because I'm taking classes in Carlsbad.
Bullshit - what? Nobody teaches that right, I don't see classes for sculpture anywhere. Where do you find that? And he says, no it's real, you should come check it out. So I made a point to go down and meet the teacher and the teacher introduced me to it and I thought, this looks like too much fun I’ve got try it. And that started about a six-year love affair with sculpting. And now I'm currently teaching it so - there's a place called The Green Art House in Fallbrook and every Saturday I've got a class there and I teach sculpting and it's fun.
And we will share this link by the way, because your mind will be blown. He doesn't just do a little hobby sculpting - these are amazing sculptures he makes! And oh my goodness, and then I start prodding him about painting... Oh yeah I would love to take a painting class. Bill says, oh yeah I do that too.
About two years ago - maybe almost three - I was at a gallery where I had my bronze sculptures that I had made from the sculpting studio and I was trying to see how they would be accepted in the public and so forth. So I had them in a gallery and I met a guy there, Richard Struggles who's a teacher, and he teaches how to paint and so I got brave one day and I thought: I could do this. So I went down to Michael's and I went through the paint department found the primary colors and some paintbrushes and a canvas and I said I could do this and I just bought it and took it home and I thought I'll find a picture I like and I'm gonna try it.
Well about three hours later I said, you know it's not bad - it doesn't look too bad, I bet if somebody taught me I could do better. So I asked him, I says I see you teaching people, can I come? He said sure come on down. So that started me learning how to paint and I've done about eight or nine paintings. One of them's a triptych; it's some cheetahs it's hanging in my mother's home, behind her couch and it's real pretty and a lot of horses.
I know I love horses I owned a horse and so I love your sculptures and your paintings of horses.
I used to have horses too - so I know that bond and the connection with the animal - it's amazing.
So anyways, just for giggles we will share Bill's amazing artwork there because he does have a good after-hours gift there. Will you please share with me any - I know you've shared with me some links and things we'll make sure we put those up for our listeners that could glean more information from Bill. Bill's also taught PCB at our local college here, and he has mentored many people as well as being mentored throughout his career.
I can blame that on Rick Hartley.
Rick Hartley who we just had on the podcast today.
Yes he was, in fact, he cornered me. We were doing an interview right after the Top Gun at PCB West, and he said: Bill, you've got a lot of experience. Have you ever thought of mentoring? And I said, no I never thought about it, to me making boards was just a way to get a paycheck. Get paid, go home, buy food take care of family do all that stuff. And that seed it planted, made me seek out the IPC Designers Council and I joined the local group in San Diego, eventually became part of the board, and then I joined the International Group and actually became part of the Executive Committee and also the Education Committee. And I think I've got an Emeritus Status now with them. I mean I've been with them a long time and I've contributed as much as I could. In fact they gave me an award once for contributing to the industry so it's good fun.
Yeah we'll provide all the links we can. We thank you again for joining us Bill.
Thanks for joining us today in office and again this has been Judy Warner with Altium's OnTrack Podcast and Bill Brooks with Nordson ASYMTEK. Thanks for listening, we'll see you next time. Until then, always stay on track.
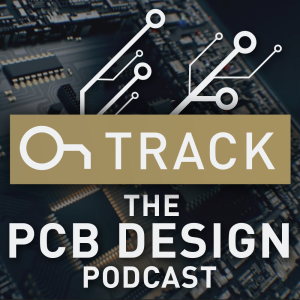
Wednesday Aug 08, 2018
Design for Manufacturability (DFM) and Assembly (DFA) tips with Jay Colognori
Wednesday Aug 08, 2018
Wednesday Aug 08, 2018
Get Design for Manufacturability (DFM) tips from Jay Colognori, Director of Business Development at Electronic Instrumentation & Technology (EIT). DFM and Design for Assembly (DFA) are important to engineers who know you can’t just design a PCB and throw it over the wall to manufacturing. Early and proactive optimization of all the manufacturing functions from fabrication to assembly of the final system is key. Listen to Jay and Judy discuss high-yield designs, EIT’s value-added engineering services and the latest state-of-the-art inspection technology and test capability.
Show Highlights:
- Jay was educated at Virginia Tech where he attained an EE Degree, followed by a Master's in Electrical Engineering at the University of Virginia.
- He spent most of his career in the mid-atlantic and his career spans from board level electronic design to applications engineering doing custom microelectronics for a couple of years, eventually ending up in PCB Design first at TTM and now at EIT.
- EIT has been in existence for 42 years, and specialize in electronic manufacturing services, turnkey builds, box builds, and demand fulfillment and consider their Engineering value add as part of their DNA.
- EIT has three facilities on the East Coast, consisting of over 200,000 sq ft. They have a facility in Danville Virginia, headquarters in Leesburg and another in Salem, New Hampshire. Altogether they have eight surface mount lines.
- The Danville facility is designated as the low-cost center of excellence and is also a 100% vertically integrated location - it is built for box builds.
- Leesburg and Salem are high-tech facilities with the latest state-of-the-art universal equipment, as well as the latest and greatest inspection technology and a full suite of test capability - with a lot going on and a story that needs to get out - it’s almost been a secret!
- New EIT website
- DFM: Bare board tips
- 2 objectives - 1) to design so that it can be fabricated reliably and with high yields, and 2) so that it can be assembled
- VM Pad requires a wrap plating process to provide a reliable button around the via.
- This process requires more copper which can wreak havoc with fine line design, so be sure to plan upfront and move those fine line geometries to the inner layers.
- Overlapping via structures can’t be made. They need to be stacked and sequential, not overlapping.
- Sit down with your PCB Fabricator at the time of stackup development, before you even start that router and make sure everyone’s happy with the stackup.
- FR4 has too high a Dk for high speed designs today and new materials such as teflon or ceramic-filled laminates are becoming more common.
- If you work with a new material, consult with your PCB fabricator to see how the rules have changed with that new material for the speed you desire.
- DFA Wisdom:
- Common Pads - so close together that they touch, rather than routing a thin signal from pad to pad is a common problem. We don’t want them to physically share the same space which will cause loss of control over the solder flow.
- Keep the pads apart and just run a small solder trace between them.
- The via in the pad has to be filled, it must be plated over and planarized.
- Sometimes the planarization isn’t done properly and even a little dimple, with a BGA on top, will cause the gas trapped beneath the solder paste, to expand ferociously and blow all the solder out of the pad at reflow.
- Always use non-conductive filler it’s much less expensive.
- The benefit of using conductive fill from a thermal point is negligible and is too expensive for the return.
- Thermal conductivity is defined in Wattmeters - if you use a conductive fill, you only get 6 more wattmeters which is rather pointless because the copper is already doing all the work.
- When a thermal via is located in a big plane, with a copper button around it - the button will be in contact with the plane and this is a big no-no. It compromises the solder flow again.
- Do a sprocket arrangement around that thermal via button. This will create a gap between the button and plane and sprockets simply act as traces surrounding it - very good design practice, frequently missed. Especially on backplanes with active components, this will require retooling to enable manufacturability.
- Why has design migrated as a service inside many EMS companies? What is the value to the customer?
- It’s a benefit to both the customer and the EMS. We want to do more for the customer than just assemble the circuit cards. We want projects going through without a hitch, no delays. What we all want is production of electronics.
- Why did EIT recently choose to onboard Altium Designer internally over other tools?
Firstly it’s an all-inclusive package. It’s schematic and design, we like the ECAD and MCAD interface which makes it easy to do 3D fit models. We love the room creation capability that allows you to reuse previous designs. It has very solid DFM rules capability which are set up in advance - that’s a nice piece of insurance. It’s reasonably priced compared to the other high-end tools as well.
- Engineers After Hours: Big hiker, especially the Rocky Mountains. We’re going to do 3 national parks this summer.
- Unique hobbies? Jay has been a dart player since the age of 19. Played in a couple of US opens. Pro advice: 2-3 beers is the sweet spot for optimal dart throwing performance.
Links and Resources:
EIT Electronic Instrumentation & Technology Website
AltiumLive 2018: Annual PCB Design Summit
Hey everyone, this is Judy Warner with Altium's OnTrack podcast. Thanks for joining us again. I appreciate everyone that's following, we are spreading like wildfire and we thank you for all your comments and opinions and we always look forward to hearing about things you want to hear - so reach out to us on Twitter; I'm @AltiumJudy, or you can connect with me on LinkedIn or Altium is on LinkedIn, Facebook, and Twitter.
So today I have a longtime friend and ex colleague, Jay Colognori and Jay is the Director of business development at EIT which is Electronic Instrumentation and Technology in Richmond Virginia, and you're gonna have fun just listening to Jay because it's like talking to Matthew McConaughey!
So you girls out there? We're gonna just have fun listening to Jay talk...
Just kidding, but he does have a nice Southern drawl.
So Jay, thanks so much for joining us today, and we look forward to talking to you about DFA and some technical stuff today. So thanks for joining.
Thank you for having me. This is an exciting time at EIT we just added on Altium capability and so I'm delighted to get to the word out, and what better way to do it than talking to you?
Well, you know when you suck up to your friends at Altium, you get on the podcast. That's how it works around here.
So Jay, Why don't you start out by telling our listeners a little bit about your educational background and your professional background sort of set the stage for us?
Okay sure. I picked up an EE Degree at Virginia Tech and then a Master's EE at the University of Virginia. So you could say I'm a son of Virginia for sure. I managed to spend most of my career here in the Mid-Atlantic and my career spans from board-level electronic design to integrated circuits, VLSI design, and then kind of jumped over to the other side of the table and became an Applications Engineer, doing custom microelectronics and had a few years running a rep firm making some commissions along the way, and then I ended up in the printed circuit board business working for DDI and VIASystems, now TTM, and one of my customers was a company called Zentech which was an Electronic Manufacturing services company, and I went to work for them. And now I work for EIT who is also situated in the Mid-Atlantic. I do want to correct one thing you mentioned. I live in Richmond, Virginia, but EIT is based in Leesburg, Virginia where we have two other facilities, I can talk some more about that.
Alright. Thanks for correcting me there.
So with all that variety of background why don't you tell us a little bit about where you are now and about EIT and what their expertise is, and what kind of technology makes they handle and so forth?
Yeah. Okay, so I joined EIT back in March, very happy to be there. This is a company that's in its 42nd year of providing...
Wow.
Yeah - Engineering services which then led to electronic manufacturing services. So we do both; engineering is very much in our DNA, we consider our engineering value-add to be an important part of most of our customer relationships.
So, you know, the thing about being in the electronic manufacturing service is that it's kind of a commodity when you look at it from the standpoint of just picking and placing parts with machines. So, we're looking to engage customers at additional levels, including engineering, turnkey builds, turnkey testing solutions, of all manner, box build if necessary, demand fulfillment, soup-to-nuts… so that we're doing more than just using those machines. And EIT has three facilities on the East Coast. Altogether we have over 200,000 square feet of brick and mortar which makes us pretty big for a small company. We have a facility in Danville, Virginia. Our headquarters is in Leesburg. And then another in Salem, New Hampshire. Altogether, I've got eight surface mount lines to keep busy.
Danville is what we designated our low-cost center of excellence. It's also a 100% vertically integrated location because they can do any kind of metalwork, cabling wire, box build. We have all that in place. It's a purpose-built facility to support the box builds, which we like to do for our customers. We don't do metal stand-alone, although occasionally I'll build a heat sink or something for somebody. We tend to allocate that factory towards our customer box builds.
Okay.
And then Leesburg, and Salem New Hampshire are high-tech facilities, they both have the latest state-of-the-art universal equipment, so we can back each other up if something goes wrong and they both have a full suite of the latest and greatest and automated inspection technologies and a full suite of test capability.
Wow that sounds impressive!
It's a heck of a lot going on, and a story that needs to get out; it's kind of been a kept a secret lately so yeah...
I haven't heard of them. I mean I'm on the left coast, of course, but I had not heard of them, but they sound like a really great facility with a really good… going all the way from true engineering to box builds. That's nice.
So… and we'll make sure to share the link, by the way, for any of you listeners who are looking for a good EMS or engineering service or whatever. We'll be sure to share that link on the show notes.
So yeah, and please do, because we're launching a new website next week, so I want to get that out.
Okay. Hopefully the timing for that'll work out.
Okay. Alright good. We'll send you some traffic for your new website. So Jay, because of the breadth of your knowledge and experience and background I thought it'd be great for our listeners today if you shared a few tips from, you know, being that you came from some of the largest board manufacturers and certainly in North America and almost the world - maybe three tips or so, on bare boards and then a few on DFA to help the designers in our audience, and engineers in our audience, that might want to learn a few tips and tricks from a pro?
Okay, you know I came up with a few of each, you know, really when you're looking to design a printed circuit board, you have two fundamental objectives: one, to design it so that it can be fabricated reliably and with high yields. And then two; so that it can be assembled. So there's mistakes that can be made that can affect both key processes.
So first of all, let's talk a little bit about PCB design issues that affect PCB fabrication and reliability and, you know, none of these I think are gonna be earth-shattering, but it's interesting to see the same mistakes being made a lot over and over again.So, we just kind of keep - we're banging the drum and we hope everybody gets the message sooner or later.
So, I guess beginning with VM pad. There's more and more VM pad today, by necessity, and VM pad, in order to be done reliably, requires a wrap plating process. Without getting into specifics of what that does, what the purpose of it is, it provides a reliable button around the via. Without the wrap plating process. It's an unreliable arrangement, but that requires the addition of more copper on the outer layers than you would see otherwise, and this wreaks havoc with the fine line design.
So, if you're at 3 mill tracing space or below, you really can't tolerate that extra copper; so it requires planning upfront. Understand, if you're gonna need wrap plating and if so, maybe move those fine lines geometries to the inner layers where that won't come into play.
Okay, that makes sense.
And it'll get you, I mean, you think your design's done and then the next thing you know, your fabricator says, well you know, you realize I'm going to add this much copper to the outside and now you're violating tracing space.
I've seen this happen too when there's multiple on RF and microwave boards too and you have... when you're doing sequential LAM or whatever, and you keep plating, plating, and people don't, when they do their simulations, don't add in those extra layers are getting extra copper too. So you really can throw you off.
All right. That's a good one.
Here's another one that you know, I'm told we're still seeing a lot of it in the market by the guys that I used to work with at DDI, and that is, you know, they'll see overlapping via structures where the designer has put a via from say, level one and three, and another one from level two to eight; that can't be made. They have to be stacked; they have to be sequential. They can't be overlapping but believe it or not. You see it.
I've seen it many many times, but you know, to be fair, sometimes when I look at those cords and figure out how they're gonna be stacked up, it… you know. I get confused too. So...
Well, I mean, I'll say this again and again: sit down with your PCB fabricator at the time you develop your stack up and your basic via structure and basically your structure is going to be driven by the toughest part of the design.
Maybe it's a BGA with a finer pitch than you've ever used before. You're not even sure how to route it, you're probably going to have to stack some micro vias, or at the very least, have some blind or buried vias to get the job done. Sit down with a fabricator, before you even start that router, and make sure that everybody likes the stack up and that it looks manufacturable.
Yep, very sound advice. Okay, that's another good one, got another one for us?
One more I want to talk about, because this is happening more and more, you know, all the designs are getting faster and faster. I mean, high speed digital is now in the radio frequency and, FR4 is just has too high a dielectric for most of the new designs now, so many PCB designers are going to have to work with materials they haven't worked with before, the more exotic, more expensive materials, and when you start talking about fabricating a PCB with Teflon versus FR4, you're talking about different processing altogether.
So, when you go to a new material, consult with your PCB guy as to which material would be suitable for the speed you're looking at, and ask them, okay, how have the rules changed with that material? What are your limitations?
And you can ask the EMS provider the same question, because the parent circuit board is the foundation upon which all of our business is done. So we understand PCBs, but I think especially with materials you want to talk to the fabricator.
Yeah, it's true and when I worked for an RF and microwave shop once, I told them, I said: you know, sometimes when you see a piece of Teflon material and a piece of... I don't know, Rogers 4350, until you strip the coffer off. You can't tell it's different, but inside the board shop that Teflon can turn into bubble gum, it's not reinforced. But when you take the copper off and you go like this [motions] it like flaps in the wind where 43-50 will remain rigid so, kind of gives you a visual sense of, this is radically different. And the way that it processes inside the shop, and how, the way it interacts with chemicals, moisture, heat, so it is true - the closer you can be when you go into those materials, to your fabricator. Okay, those were three good ones. All right how about DFA wisdom?
Okay, well one we see quite often, and I guess it's tempting for the designer to do this, because he thinks he's kind of found a shortcut and a way to use less PCB area, but you see a lot of guys trying to use what we call common pads, and these are pads that are so close together that they touch, rather than routing a thin signal from pad to pad.
So these pads do share the same signal, but we don't want them to physically share the same space. That causes us problems with controlling what the solder does once it flows, so keep those pads apart, and run a just a small signal trace between them. And then we'll let the solder mask do the rest, and we can control the flow of the solder. So that's a real simple one, but we run into it a lot.
Okay.
I talked before about VM pad, we see a lot of designs where people don't fill that via. If the via is in the pad, it's got to be filled, and it must be plated over and planerized. Sometimes that's done properly sometimes it's not. There's a little dimple there...
Yup.
If there's a dimple in that pad and I place a BGA ball on top of that gas, it's gonna get trapped underneath the solder paste that I apply and there'd be a little air in that dimple and heated gas expands; it expands ferociously. It doesn't want to stay where it is and it'll blow all the solder right out of the pad at reflow time and you know I have customers argue with me against it, it is expensive to fill and planerize via, but it's the right thing to do. You have to do it if you want reliable BGA connections. These are leadless parts that we can't inspect visually, we have to use x-ray.
It's not really practical to use a hundred percent x-ray inspection except on high-reliability applications like military, maybe medical. So we lot, we lot-sample these BGAs with X-ray and if we don't see any problems with a lot we carry on.
So, I can't emphasize that enough, to fill those vias and fill those vias properly. And I would add further, that there's no point, you know, we have some people that are using thermal vias, these are vias really which are designed, not necessarily to conduct an electrical signal, although they do, but to conduct electricity from a hot part from maybe a ground plane, might be an inner layer or wherever, and you run into people who call out… so there has to be a filling to fill those vias before they're plated over.
Right.
And there's two types of filling: there's conductive and there's non-conductive. I strongly recommend never to use conductive. Non conductive is much less expensive. The benefit of using conductive fill from a thermal point of view is super minimal. I mean, the copper's doing all the work...
Okay.
-and if you need to draw or pull more current or more thermal energy, just create more thermal vias because the copper's doing all of the work. I mean, I'll give you some numbers: thermal conductivity is defined in wattmeters, a typical via is going to give you over 600 wattmeters of conduction, if you fill it with conductive fill you only get six more wattmeters. What's that compared to...
Oh, yeah.
-380 I'm sorry, 380's what the copper gives you. The non-conductive only has point six wattmeters.But the point is both of those are in the noise compared to with the copper's doing.
Right.
And last but not least. Good luck trying to get a printed circuit board fabricated in China with conductive fill they don't do it over there.
Really?
Right so well, maybe somebody's doing it but we're having a hard time finding any.
Interesting hhm.Why is that?
Because it's not, it's not...
They just don't like it? It's not important so we're just not doing it?
I don't think anybody should be doing it, it doesn't make sense to me, it's too expensive for the return.
Interesting, I'd never heard that before actually, but it makes sense with those numbers. I'm kind of surprised it took root for a while.
We recommended as far back as five years ago, at DDI, not to use conductive fill, I think it's a dinosaur that it's day has come and gone, but there's probably some engineers out there right now, going no!
Huuu! [laughter]
We'll see...
Yeah well show me the data, you know, and when when there's enough good research out there and data people stop doing it. I'm sure.
Okay, so along the lines of thermal vias, here's another tip. A lot of times a thermal via will be located in a big plane so you'll have the via, and the copper button around it will actually be in contact with the plane - this is a no-no. This makes it very hard to deal with the solder flow again. So what we ask our customers to do; is do a sprocket arrangement around that thermal via button and so basically that button will exist - there'll be a gap between it and the plane around it, and then the sprockets are simply traces above, below, and the right and left and that - it's an arrangement of the sprocket - very good design practice, frequently missed and, it's not unusual that we have to go back and retool the board to add those in order to make it.
Especially back planes with active components; you see a lot of that and they have to retool to add that feature to make it manufacturable.
Well, these are good tips. You were concerned you didn't have good tips. I think these are really good tips actually.
Well glad you do.
I do, not that I spend all my days, you know, pondering DFA these days, but that's good.
You know Jay, you and I worked together for a small bit of time and something I've noticed over the years I don't know... maybe five, ten years, it seems like there's been a migration of more EMS shops that go in to have PCB designers in their shop and not so much I guess, fabricators - at least that I've noticed, they may be there, of course they do with larger shops, but why do you think that is and why do you think that's a good idea?
Well, I think it's a great idea for both the customer and the EMS. We, as I mentioned before, we want to do more for the customer than just assemble the circuit cards and if a customer, an Altium customer, finds themselves in a position where they need to outsource some of their design, maybe they you know, their designers are saturated, maybe they just need the resources.
What better place to do it than at a guy that knows how to assemble the cards and really understands the issues about fabrication and about assembly. Your chances are that the design from your EMS provider is going to go right through new product introduction without a hitch, whereas if you do it internally and you're not aware of some of the issues you know, it won't go through it without a hitch. We may not catch the problem until it's too late. And we may see several tooling iterations, and you'll see a delay and nobody wants to delay during new product introduction - everybody's in a hurry to get their prototypes.
And nobody wants to waste money because that's going to be expensive too -
Yeah, but we think there's a lot of serendipity between that particular engineering function and getting to what we all want. Which is production of electronics.
Well that does make sense in that, we both know Mike Brown, and Mike I trusted implicitly to know about fab and assembly and he would catch all that stuff so he did have a broader understanding than maybe, somebody who just does, you know has a consulting firm say, that does designs because he's around it all the time all, day long so there's certainly a lot of exposure there. So that makes sense.
Well, first of all, welcome to the Altium family! You told me recently that your designer on-boarded Altium Designer 18, that's exciting for us. So thank you for that. What made you - I'm gonna go for a little pat on the back for Altium right here. I want you to tell us why you, why EIT chose to go Altium Designer over perhaps another tool?
Okay. Well, we think some of the key features of Altium; first of all, it's an all-inclusive package so it's schematic capture and printed circuit board design. You don't have to worry about working with two different pieces of software.
We like the fact that there's an e-CAD m-CAD interface which makes it really easy for us to do three-dimensional fit models once we place the components. We love the room creation capability which as I understand it, allows you to take a previous design, a piece of it, and then just kind of cut and paste it right into your new design.
Yeah.
So you don't have to reinvent the wheel. I think that's pretty strong and then, last but not least very solid DFM rules capability that you know, is really going to help us get to where we need to be. I mean the fact is these boards need to be designed to IPC standards and the fabricators have tailored their process to meet these standards; and when you send them something that's outside those bounds, the mechanism sort of locks up. It just doesn't work. You'll get a 'no-bid' or bells will go off, so those design rules are critical and that you have the ability to set them up in advance is a nice piece of insurance so; I think it's a reasonably priced tool compared to the other high-end tools as well. So we're pleased to have it.
Good. Well, thank you again we're happy to have you on board and I'll needle you later about sending your designer to AltiumLive because we're gonna have a really good conference with some good training coming up. So your designer will probably enjoy going if you guys have the time and budget to do that.
Well, keep me posted on when and where.
I will it's coming up in October. So Jay, we're kind of wrapping up here, but if you've listened to these podcasts before, you'll know that sometimes I like to ask designers or engineers like yourself, what you like to do after hours, and we call this portion of the podcast designers after hours. So, I know you have a couple interesting hobbies...so why don't you tell those to our listeners because I think they're kind of fun?
Well, I'm looking forward to 10 days in Montana and Wyoming this September, I'm a big hiker, and nothing is more fun than hiking up in the beautiful Rocky Mountains. So we're gonna hit three national parks; we're gonna do about two to six hours of hiking a day or as much as my legs can give me and just have just an awesome lifetime outdoor experience and hopefully not run into a grizzly bear along the way… my wife's really worried about that, by the way [laughter].
Bring your grizzly repellent!
And then, I know you wanted me to talk about one other thing...
My favorite...
Yeah, as you know, we business development types are very competitive and what better setting to compete against each other than you know, in a pub throwing some darts.
So I've been a dart player since I was 19 and took it very seriously for a while, and spent way too much time on it. Actually traveled every weekend to tournaments all around the United States and played in a couple of US Opens. But that was a long time ago, now I just play for fun on Monday nights.
That cracks me up. You are the one and only competitive traveling dart player that I know... Okay, but my favorite part is - tell about the beer to success ratio of a good dart player.
Oh yeah, so so we're throwing a 27 gram projectile at a target about the size of a dime and turns out, that if you get nervous or you try too hard, you're not going to be very successful with that. So, it turns out that, that second or third beer really kind of smooths out your stroke and you generally shoot a little bit better. At least that's what we rationalize.
And what happens if you go over three?
Yeah, that's that's a slippery slope indeed. You've got to be careful...
That is so funny oh my gosh. Okay well, that is like one of my favorite, I think, designer after our hobbies yet.
So when I come out, we'll find a place and throw a few.
Okay. Alright, I'll get my three beers ready
Okay!
No, actually for me, I'd be like half a beer, like three beers you'd be putting me in an Uber and sending me home. I'm a wimp.
So Jay, thanks so much for your time. These have been great tips and it's good to see your face my friend, and I wish you all the success at EIT, and we will certainly share all the links in the show notes and we'll also put the link to AltiumLive in the show notes and we'll encourage your designer to come out and join us as one of the new new beasts of the Altium family. So we'll include that as well.
So thanks again for joining and we'll talk to you soon, my friend.
Thank you Judy, it was my pleasure. Thanks again for listening to the podcast.
This has been Judy Warner with the Altium OnTrack podcast and Jay Colognori from EIT, and we look forward to seeing you next time. Until then always stay on track.
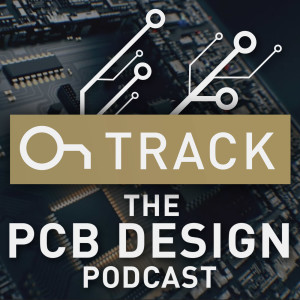
Tuesday Jul 31, 2018
Ted Pawela, Altium COO, Shares Vision for the Future
Tuesday Jul 31, 2018
Tuesday Jul 31, 2018
Ted Pawela, Altium COO, joins Judy Warner to discuss how Altium intends to fundamentally transform the electronics design industry, what Altium’s vision for the future looks like, and what to expect in Altium Designer 19. They also touch on Altium’s upcoming international design conference, AltiumLive: Annual PCB Design Summit, and why everyone in the community is encouraged to attend. Learn about Altium’s vision to bring PCB design and manufacturing closer together — a world where design turnbacks and respins can be avoided by bringing DFM constraints into the design tool itself. Listen to this special episode of the OnTrack podcast to learn more and remember to share your comments and ideas below.
Show Highlights:
- Ted started out in ocean engineering - multidisciplinary in nature, not just physics or mechanical.
- Altium’s commitment and advocacy of engineers/industry - Altium stands for the Engineer
- The Altium origin story - anyone who needs a tool should have it, so let’s give them tools no matter what age or budget i.e. free product including Octopart and Upverter
- Upverter is for the makers and inventors of tomorrow.
- It’s our mission to transform the electronics industry.
- The whole product realization process is discontinuous. We want to change that.
- AltiumLive announcement and AD19 announcement
- Goal is to deliver incremental pcb design capabilities that would take us to places we haven’t been before - like High Speed Design - it’s not something we can deliver in one release. AD18 was the foundation.
- Design and manufacturing worlds can come closer together.
- The power of CAD can be problematic - it can be overwhelming, needs to be feedback from the tool to help find problems.
- New company acquired - PCB:ng (NG=next generation) is board assembly manufacturing, low volume, high mix. Good for prototypes. Their mission is to create a manufacturing line where designers can know everything about it so design constraints can be removed from the start.
- Ciiva - another company trying to solve the same problem. They created a bill of material that allows you to know the lifecycle state of what you are selecting.
- We all want manufacturing insights at design time, Altium is bringing the pieces together to transform the industry.
- AltiumLive - Designers, manufacturers, fab, assembly, all came together to discuss industry problems. It’s about inspiring the community to think about current industry challenges and discuss possible solutions.
- How many Industry Conferences are out there? PCB West, DesignCon (chip and board level), PCB Carolinas, Electronica, Embedded World - but are there any that put the PCB designer front and center?
- Altium wants to provide this for the PCB designer; see AltiumLive 2017 Retrospective to see the presentations from last year. You don’t have to be an Altium Designer user to come to AltiumLive.
- Altiumlive 2018 this year will have one day, before AltiumLive officially begins, of extra learning sessions you can add on, the two options (which will run concurrently) include: University Day, focused on learning Altium Designer or High Speed Design with Lee Ritchey.
Links and Resources:
Hi everyone, this is Judy Warner with Altium's OnTrack Podcast, thanks for joining us again.
Today I have a rare treat for you, but before we get started I'd like to invite you to please subscribe to our podcast on your favorite podcast app or favorite us on an RSS feed, and remember we also record this on video simultaneously, so if you want to see our sunshiny faces you can go over to YouTube on Altium's channel and go under videos, and you'll see all the podcasts recorded in video.
I'd also like to invite you to connect with me on LinkedIn, I share lots of information to engineers and PCB designers and I'd love to connect with you there as well and on Twitter, I'm @AltiumJudy. So today, I have the rare treat of inviting in one of our esteemed executives; I esteem you Ted. So Ted Pawela is with us today, he is the COO here at Altium and we're going to talk a lot about the direction of Altium and really kind of get a peek behind the curtain. So I'm excited to share him with you, so Ted, welcome.
Thanks Judy, I appreciate you having me on here and I'm actually really excited about the the podcast series that you're doing, and see a lot of the feedback from people and it's a little bit humbling to be here given the actual magnitude of the guests that you've had here from industry and so forth, so I'm not sure I can live up to that but I'll do my very best.
Well, I think you rank but we're glad to have you. So before we get started, I thought it'd be fun for the audience to know a little bit about your engineering background. So you haven't always dwelled in the halls of the executive world; you kind of came up through engineering, so tell us a little bit about your background there?
That's true it's probably not a very prototypical upbringing into the industry and so forth, but I actually started my... I guess you could say my engineering career, back in the education space. My undergraduate degree was actually in Ocean Engineering, and the interesting thing, I think about Ocean Engineering and Altium, is that Ocean Engineering is one of those disciplines, or one of those engineering fields that is multidisciplinary in nature, so it doesn't focus only on mechanical or only on physics, or any given thing, but it's actually very multidisciplinary. In fact, like when I think back on it, I did a thesis project that was to create an underwater acoustic transponder system - which sounds pretty fancy, but it was basically a device where you could send acoustic signals underwater to tell this device to do something. In this case, it was to release a buoy from the bottom, that had a rope tied to it. It might be attached to an anchor or something else you might want to recover, and that system, we had to actually design the electronics as well as the mechanical system. It all had to work underwater so I think back on that a lot because, following that, I spent a lot of time more in kind of mechanical domains, and so this in some ways as a homecoming for me.
Right.
To come back to being at Altium and be involved in electronics, so that was kind of the beginning. I worked in the underwater defense industry for 10 or 11 years as a real engineer doing actual design work and at that time I wasn't really focused on electronics, but more in the worlds of underwater acoustics and mechanical systems and how those converged. So they're kind of different kinds of physics, different equations that you have to solve, and so I spent a lot of time trying to make those two things mathematically work together. And then from there I actually ended up, because I was working with software, and in this case it was Ansys software and, actually Abacus software at the time you know, that has now become Somalia over at TISOL, but I was working with those two softwares which are simulation softwares in the mechanical world and I was presenting at conferences and things like that. And I had the opportunity actually, to join Ansys and I did, and that kinda took me from that world of, real hardcore engineering into the software side of the business and and I loved that and I've now been at a number of software companies, all engineering software companies, and it's become something that I have a passion for, and that I really enjoy and love and feel really fortunate to have found my way to Altium.
Well we're glad to have you, you've definitely been a change agent here for good and what I really love about Altium and I think that you appreciate it like I do, is if you walk through these halls very long here at the La Jolla office there really are a lot of people that have kind of that cross-disciplinary feel or... but we really do advocate and care about the engineer and that sounds kind of corny.
Yeah...
But I think because there are lots of people, even like myself that were in fabrication or where I was selling and sort of in the weeds, It makes me feel excited to come to work in the morning and to be able to advocate and to help enable, sort of the next generation of technology, and be part of that so...
Yeah, I'm excited about that as well and I think, fundamentally it comes down to this sort of basic notion that's independent of any industry, is that if you do the right thing for your customers and you really think about them, that they do good things by you as well and so I think we get that here.
Yeah.
From the top of the organization through to, and across all places in the organization and definitely that is kind of a cultural element here that I both appreciate and I'm kind of committed to perpetuating and extending as much as we can.
Well a fun note here, is that Ted actually hired me into the organization.
That's true...
-and I actually reported direct to him when I first joined and I - I think we really resonated on that note, and that really, Ted's really been the empowering force behind everything that I do here personally at Altium. So I really appreciate this Podcast, the Newsletter, AltiumLive, so we've had a blast doing some of that stuff and doing things really with with the designer and engineer mind. So that's been fun - well to your point, I think that's a good jumping-off point what we wanted to talk about today is Altium's identity, you know.
What from your perspective, what is it that Altium stands for?
So, I think, you said it, maybe in different words at the beginning of this and I think Altium stands for the engineer, for the designer, for the people who actually have to do the work. And I think that it's one of the things that makes us different from other software companies so we're not really thinking about things like, typical things that I've seen in other companies, like how do we sell higher into organizations? How do we get executives to buy in so that we can do kind of top-down? How we can get top-down decisions to standardize on our software and things like that. The thing about - that I really noted about Altium - and the culture of doing business and working with people here, is that it's really focused on that. The guy who's got to do the work.
And and I think largely, I believe that's the thing that we, that we really stand for and you'll probably remember that... you know, I tell the story to a lot of people and pretty frequently, about when I came here you know, trying to uncover what I felt was, or what was the fundamental kind of characteristics of Altium's brand and it's identity and, and it kind of rooted in a discussion I had with one of our board members David Warren, who has since retired, but but David was one of the first couple of guys into the company and when they started the company it wasn't, it wasn't a company yet, it was actually a couple of guys who are trying to build electronics at the time, and this goes back 30 years or so.
You know CAD software, E-CAD software in particular, it existed but it was really expensive. It only ran on expensive high-end computers and I think, nobody in the room, yourself included may remember those days but I remember those days when we had to buy Apollo workstations and big expensive machines.
Yes.
You know that $50,000 in back - this was back in the 80s...
Yeah.
-that was your barrier to entry so it was a lot of money and a lot of people who were involved in design didn't have access to that, they didn't have those budgets.
Right.
And so, and these two guys were among those. And they actually set out to say, how could we - how could we have software like that for ourselves? Well they decided to create it, and they wanted to create it in a way that it would be accessible not just for themselves but for anybody who needed it so they built it to run on on PCs and that was the genesis of Altium.
Right
There were people out there who were doing and trying to do amazing things in the world of technology and engineering who didn't have access to all the tools and they wanted to provide that access for themselves, and for others, and you know for me, and for the company, I mean that's really a core part of what we stand for. Be for the engineer but make that technology accessible and make it accessible to people who need it, even when they don't have big budgets to work with, sometimes they don't have any budgets to work with. So that, to me, that's really what Altium stands for.
Yeah I think we have the best sort of origin story ever, especially because Dave Warren, at the time was - I believe he was teaching at University - he said to me once that there was all these young passionate people that have these great ideas and no access and so there was he was kind of incensed by that and that sort of, filtered and still sort of lives in this company, this feeling of anyone - anyone who needs a tool should have it. Because you can have a great idea at any age, at any phase so let's give them tools. And I really love that, that it's lasted long past the time that Dave Warren and these two guys sort of kicked this company off, it's really persisted and I really I really like that.
Yeah, I think it's not just persisted because it's in the spirit of the employees who work here and everything, but I can tell you that we make our decisions on that basis. I mean the basis of, kind of being true to what we represent, and so we think about that. We think about who are the underdogs, and how do we empower them? And not, kind of like leave them behind, in pursuit of purely making money in business - and we are a business - we're a commercial business, and of course we want to make money; our shareholders expect us to make money and, on the other hand we think that there's many ways to do that. And you know, everyone may know, we have multiple products and kind of like multiple price points - that's one way. But we also try to think out of the box a little bit and so as an example; we have, I guess one of our brands called Octopart, where people can go and search for parts and so forth, and you can do that as an engineer and you don't pay to use that - it's actually kind of a seller pays model right?
Right.
So when somebody buys parts after they've searched throughout the parts and we may get a small fraction of that revenue, or people advertise on that site and we get a little bit of revenue from that, but we don't have to charge it to the user and we think about - that's an example - but we are always thinking about how do we take a product like Upverter for example, that actually was, before we acquired it, they charged a subscription fee. We made it free, with the intent that we would find ways to kind of indirectly monetize that in a in a seller pays kind of model.
Right.
Because we want to make that technology accessible to the maker community, to the kind of inventors and creators of tomorrow who who don't have money today. So you know, it's like I said, it's a core part of the decision-making process here; is how do we stay true to that vision of making technology accessible to everyone?
Yeah, it's just so refreshing to hear from an executive a software company I think - you know - it's not something I think you hear a lot, like money does lead in many cases, but it's clear to me that there's a guiding principle behind that. That,of course you have to be disciplined and answer to stockholders and do all those things, but you can do that in fresh and new ways and...
That's the key, because I think again, we want it, we need to be a sustainable business or else the technology that we provide won't be here.
Right.
In ten years or something and of course we don't want that to happen…
Right but there are, interesting and different ways you can do it requires that you maybe, are willing to think outside of the conventional wisdom or the best practices and so forth and… that's one of the things that I like about Altium, is that we really do try to break those... mmm... norms and...
Yeah.
-and you know, think about how we can do it differently and just don't accept status quo. Don't accept best practice just because that's the way it's always been done.
Well to me, it's innovation and...
Yeah.
-and we try to build innovation into our software all the time, so we're building innovation into our model too which I really love. So what would you say, do we... would you say we have a defined mission? I mean, beyond what you kind of spelled out, so like an actual defined mission?
Oh absolutely, so I think everyone at Altium, we've refined this thinking in the way that we articulate it internally, but if you were to look at the things that we present externally, like when we do go to shareholder meetings, and in particular, we do a technology day to our Investor Community and we've done it the last several years in Australia. And that you can see the presentations on the web and so forth, but that's a real clue for anybody who really wants to know where Altium is going. If you'd look at those things directionally that gives you a lot of guidance and the thing that we say over and over and over again is that it's our mission to transform the electronics industry.
And specifically, what I mean by that, is that creating electronics is more than just about the design process and the design tools and and so there's what I would - kind of call it a value chain - that's involved right, you have people who think about the product and what's the intent of the product and that kind of breaks down into requirements for mechanical systems, for electronic systems, and all of that.
But even then, the job's not over, because there have to be components that are supplied to that or that are selected from that and then found and acquired. There has to be a board that gets manufactured; the bare board. There has to be the assembly and fabrication of the full, system level board and everything and sometimes it's multiple boards, and then it's all got to be put together and so the job’s not really done until everybody does that and the thing that is sort of striking about the electronics industry, is that that's a really discontinuous process, we kind of like, all think within our sort of domains with our blinders on and we believe that it's our... it's gonna sound a little silly - but it's our self-directed destiny to kind of change that. That's what we want to do, so the mission of the company is to really change, to transform the way that electronics are conceived, designed, manufactured and delivered to the world, and we think there's lots of opportunities to do that a lot better.
Well I know personally, a lot of people have asked me about, why are you buying these... you know, how does... why? I remember Happy Holden last year saying; Upverter? And so it's because they think of us primarily as just a CAD provider right?
Right.
And so I think not a lot of people understand that we have our sights set much higher than that - along those lines - I'd like to dig into that a little bit more. But before we do that, we are sort of - AltiumLive will be here in San Diego in October, and we will be, at least doing a marketing release then, of showing what will be in Altium Designer 19.
We will.
And you mentioned to me that I had kind of thought - even just working here - you're down the hall from me but my impression was that Altium Designer 19 was going to be sort of an iterative release and that Altium Designer 18 was massive. We changed the platform, we really revolutionized the tool in so many ways so I thought: well we're going to catch our breath, add a few little bells and whistles and be on our way down the road, but you're telling me no, it's going to be big. So, can you without giving away the secret sauce, tell us a little bit about sort of the intent?
Yeah well, so I mean there's things that are still forming, it's kind of like the cake is still in the oven baking right now, so not necessarily ready to share a lot of detail but here's what I will tell you about that.
First of all you're right, Altium Designer 19, it's not just another release, just like 18 wasn't just another release and, in fact, if I shorten it just for the sake of simplicity, AD, AD18, AD19 and, AD20 are really a set of releases that are linked together in a fundamental way, and so what we wanted to do with that series of releases was in part - it kind of gets to this thing that I was talking about, this idea of transforming the electronics industry and specifically what we wanted to do with AD18, 19 and 20 - was to deliver incremental PCB design capabilities that would take us to places we hadn't been before so, and specifically into high speed design. Historically... you know...
Yay! my favorite subject
I know you have lots of time invested into that segments of the industry and know lots of people there and and we think that's important that we can do better to support that and AD18, 19, and 20, that was one of the core kind of objectives there, was to help Altium to kind of grow up in terms of high speed design capabilities. But it wasn't something that... I mean it's kind of massive, and it's, in terms of being able to do it, so it wasn't something we were able to deliver in a single release...
Right.
-in fact when I think about high speed design, specifically AD18, was kind of like delivering foundational capabilities that are required to do the kind of complex and large designs that typically we see in high speed.
Right.
So you didn't see particular high speed capabilities there, not big ones yet, anyways in AD18, but what you did see was that we moved from our old 32-bit platform to 64-bit.
Right.
We went from single threaded activity to multi-threaded within the application, and things like that; that are kind of the plumbing...
Yeah, it's like the foundation...
That's right, they need to be there for us to be able to exercise those high-speed capabilities that we wanted to build in. With AD19 you'll start to see more of the capabilities now coming out. It won't be complete but there will certainly be designs in the realm of high speed that people will start to be able to do and it'll become visible that we're really going somewhere with that and then AD20, will be the one where we move a lot towards a more completed set of capabilities for high speed.
So that's one sort of key thing that I would say is that - certainly at AltiumLive, and as we come out with AD19 - you will see real capabilities that start to bring us into that world. The other thing though, is making real this idea of beginning to bring about industry transformation, and specifically, even at AltiumLive last year, one of the things we heard over and over again in the talks was people who were in board fabrication and assembly and manufacturing and who think about DFM and things like that, who were saying over and over and over again: you guys out there in the design community don't think about us. I know the manufacturing world, not nearly enough and often enough, and conversely we heard from people on the design side saying kind of similar things back to manufacturing so those two worlds have been historically siloed, as you said.
It comes up, I cannot tell you how often this comes up in this podcast series it's just a persistent problem, everybody knows it's there.
Yeah it is a huge problem and I think in one of the things that I'm really excited about with AD19 is that you're going to see some you're gonna see some things that are fairly dramatic in terms of helping to bring those two worlds together to where people who are doing design will be in contact with people who are involved in manufacturing while they're designing. And you know, the ultimate endgame for that, is that you would imagine a world where when you are doing design, you don't only have design constraints to think about but the manufacturing constraints are things that guide what you can and can't do and how you create that so that you avoid those kind of like downstream... not exactly mistakes,but those downstream things that you didn't think about that cause design turn backs and spends that are really not needed.
Right, they're not needed and cost so much money and time.
Yes so, AD19 is going to be, I think it's gonna be really impactful and kind of transformative in the way that design and designers, and people in the manufacturing side of the business will be able to work together. So I don't want to spill too much of that, but it's gonna be, I honestly think this is in many ways, a bigger, more transformative thing than AD18 was which was pretty huge, for us at least, in seeing our tool transform.
When you said that to me I'm like: wait what? I was shocked when you said that to me about a week ago I was like, wait I work here and I don't know, and I talked to developers regularly and I think because I get just little glimpses of pieces I'm not seeing the overarching where I think you, from where you sit, you're getting the overarching perspective.
Maybe so, but like I said, I think the key thing here is it will really be something that changes the way we think about CAD and what we should expect from our CAD tools.
Which is great; I've said for many years, that the power of CAD has actually been problematic, because, if you are not 30-40 years into this industry you can get so much power in that tool. It's like, I was saying to someone, I go: there needs to be a feedback from the tool that says, no stop dummy, you know. Like there is no place that says, no stop, this is a bad idea...
Right.
-those cores don't match. Those holes are too small those vias are... you know. There's, of course we can put in parameters and things that help them design well, but there's... so to hear that coming together would just be life-changing, so that's very exciting.
Yeah, and like I said, it's not something that I think we won't realize - that full vision of AD19.
Right.
It'll be that again, this combination of 18, 19, and 20 - you'll be able to see now with AD19, how those things kind of link together and we'll be telling people, we'll disclose our road map for AD20, so people can see how that whole thing plays out but there's gonna be a lot there and it will be enough to change the way that designers and manufacturers are working together. It will change more; well it'll be changing them in even more dramatic ways as we are able to deliver everything through those three releases.
Right.
But there's gonna be enough there that I think, it's really exciting to think about, and talk about and you know...I guess, the other thing for me, or maybe not the other thing - but on a related note - I remember last year at AltiumLive how all those conversations seemed to be centered around standards. And so, couldn't we come out with a single standard for how data is represented and so forth and...
(that's a hot topic)
Standardization, I just have to say, I mean standardization is such a hard thing to do to get everybody within an industry to do that and I think the reality is that standardization isn't the answer. The standardization is a solution that people kind of assume is the right way to solve the problem, so they... and so we tend to kind of like think about how. First you know, how could we solve this problem? If the problem is that people just don't work together and when I design I don't end up with something that's manufacturable until I go through many spins, as an example that's the problem right and then, the solution is just to make it work right. I mean as a designer, or as for somebody in manufacturing, do I really care about standardization? No, I don't, but what I wanted to have happen is that it just works.
Right.
-and I don't have to think about it, I don't have to do anything extra, nor does the person on the other side of the wall that we're throwing things back and forth over. We just want it to work.
Right.
-and that's the approach that we're taking and and again you'll see the it gets to what you were saying why do we acquire these companies for example?
Right.
So we did, just recently, a small acquisition of a company called PCB:NG; NG is for Next Generation and that's a company that does board assembly manufacturing and they do it on small scale, so it's the idea that they do low-volume, high-variety kind of, high-mix kind of designs. So when people want to build prototypes and so forth and their whole mission has been to really change, to be able to create a manufacturing line where the designers can know everything about it so they kind of design in those constraints from the start. Which is very aligned with the idea that I was talking about, and where Altium has been thinking, and now if you rewind back a couple of years ago we acquired a company called Ciiva and Ciiva was really focused on a couple of things. One was to have a Bill of Material that was smarter, and smarter in the sense that you understood straight away what was the life cycle state of the components that you select.
Right.
And the parts that you select - are those things even available anymore? So you don't select and design in things that you couldn't even buy if you wanted to.
Right.
And then there's the notion… that it happens frequently by the way - it does happen frequently.
And it's such a headache.
And in Ciiva you know, the other thing that they were really focused on was to understand those manufacturing constraints as well and so there's kind of this nice convergence of thinking where the Ciiva guys were trying to solve that problem, PCB:NG guys were trying to solve that problem, and Altium is trying to solve that problem, and so bringing them all together now gives us a way that we can say, how do we make it just work and so having that small manufacturing company gives us a way that we can prove this out. We can make it happen having sort of, like full access to everything in that facility and on their line and as well having the people on the side of thinking about the supply chain in the Bill of Material and the design side. We can do all of those things and so we don't intend to kind of like make PCB:NG into some big volume manufacturer. It's never gonna be Foxcon, what we want it to be but we want to make it just work and once we prove it there, then we can take it to all manufacturers.
Right.
And that's the idea and and so we'll again, start to give you a glimpse of that, and more than a glimpse, we'll give actual real capabilities in AD19 that will allow people to begin to solve that problem or, not even salvage, just make it work.
Right just make it work.
So AD19 in my mind is, is a huge step forward.
Well I'm very excited so I'm gonna put a pin in our conversation real quick and just let our listeners know that, all of... you know, sometimes people just think of us being the creators of Altium Designer and don't realise we sort of have been acquiring these companies so we will have an area at AltiumLive in San Diego and in Munich if you're able to join us, where all of those brands will be joining us. I'm hoping to put them in an area that I'm calling Altium Alley, so we'll have Upverter, Ciiva, the PCB:NG, and so, we can start to see how this all fits together.
Yeah.
So I'm excited about that. So let's talk a little bit about AltiumLive, since we are rolling out AD19 at that time, at least to give a sneak peak of it. You and I worked very closely together and sort of had a shared passion for the idea - it was AltiumLive, our first ever users' conference was really Ted's brainchild and then, I was brought on board and then we worked closely together and then it took a village - it took an Altium village - to put on that users conference so can we talk a little bit about why AltiumLive, why do we decide, as a company to begin doing a users' conference, and sort of what, is our intention behind that? Because we want to sell more software?
[Laughter]
Well of course we want we always want to sell more software.
Of course we do, there's no doubt about that... I'm obviously being very facetious.
-yeah but if I come back to the beginning of our conversation, you know I mentioned this notion that if you do the right thing for your customers that they support you and and good things happen as a result of that and and I think, AltiumLive is really built on that idea. So we wanted to create a forum in which our users, but more than that, people in the industry could come together to kind of talk about and collaborate on how do we solve the challenges that we face as an industry. So the fact that we had manufacturers there and manufacturer's reps and everything else as well as... you know, so these are people that don't know Altium Designer. If they saw it they wouldn't know whether it was Altium Designer or another tool per se...
Right.
-possibly but they're involved in the industry and they're relevant right, to the way that we do design and so forth. As well as all the design people. So we wanted a place where our users could come and they could learn and they could get better at their craft and they could connect with one another so - I think Judy you came up with the idea - that it was about, connect, learn and inspire...
Right.
-and that's really the idea right, I mean in terms of connect; it's always good to be able to meet your peers, to talk with your peers, who you face common challenges with, and talk about how do you overcome those, how do you approach them, how does your company support you in those things. Those are always really valuable conversations and so that's - I think - what the connect part is all about. Learning is pretty obvious, people always want to learn how do I get better and that's both in terms of using tools but more than that, it's about becoming better as an engineer. So a lot of the curriculum, if you will, that was associated with that, and in the sessions that we had they weren't about how do I use Altium Designer, they were how do I solve these challenges from an engineering perspective...
Right what are better routing practices...
-Right, speakers about specific tools, because it's like, how do I do these things? So the learning part of it was really important. And inspire, obviously if we're going to transform the industry, we want to bring together the people, the stakeholders in the industry, who are likewise, facing these bigger challenges, not just how do I design better, but how do I design in a way that I know it can be manufactured and that manufacturers don't have to go back and completely recast the Bill of Materials and force me to change the design. And how do I ensure that these parts are actually available and all of that - but it's really again about inspiring the community to think about how we solve these problems of the industry. The fact that it's sort of discontinuous in terms of that flow and so forth and we've got a lot of ideas at Altium about how we solve that, but we definitely don't have all the answers and and nor would we want to try to solve those in absence of all the thought leaders and practitioners in the industry right.
So I think that's the third part of it, is really to bring together those leading practitioners and thought leaders from the industry to say, how do we take this, how do we take our whole industry forward in a way that I... don't want this to sound a little too trivial but, we talk about IoT how do we deliver 50 billion devices by 2025 or whatever.
Right,
-whatever those numbers are, but I think that there's lots of places where electronics are important even in absence of IoT, but the smarter we make our world, the better that's going to be, the more ability we have to solve some of the big picture problems in the world using electronics and engineering and so forth and that's only going to happen when we all come together to figure out how do we do all this better and more effectively.
I loved the convergence at our event it was like magical to see - and such spirited conversations - between fabricators and even our keynotes right. I remember one of the keynotes in Munich saying something about fabrication and then our friend Julie Ellis is like, wait a minute, and then having this really honest challenging almost debate right, but it was so beneficial. I think everybody was really, I think empowered, by having really those frank conversations and really learning from each other. You know a thing that I really like Ted, is that if you look across North America at least, well I would even say Europe, how many events are there for designers? I mean for printed circuit board designers or engineers already, what events are out there? We have PCB West which has some good tracks, Design Con is chip and board level, PCB Carolinas I can think, Electronica, Embedded World... so there's just a handful, but is there any that just focuses and kind of exclusively puts the designer front and center?
No, they're kind of lost - they don't really have a place and what I love about AltiumLive, is that gets to be sort of the center of the conversation but shoulder to shoulder with all the other stakeholders right, so it's like they get their own party where they can just dig in and get such deep learning not only from really incredible thought leaders like our keynotes but also from each other.
Right, we saw that happening a lot right then, and now you can see it just if you go even on the website for AltiumLive and you look at last year's recorded sessions and so forth you see that pretty clearly. It was pretty striking, and my hope is that over time people will actually start to see this event as something that's not an Altium event it's their event.
Right.
And that's the spirit behind it frankly, is that the same as with products, and solving these problems that everything we can't there's no way that Altium can do it on its own or any one company could on its own. We have to do it as a community so I really see AltiumLive as a community and I hope it grows and I hope that the control of the agenda and the content and all of that kind of stuff stays with the users, the designers and the people in the industry who are actually doing the work. That's my vision for it, that it's not us and it's not about our software...
Right
-it's really just about us using the fact that we have lots of customers and users and so forth as a way of using our position to help bring them together.
Right, absolutely, and I've shared with people that you don't need to be an Altium user to come to this event.
No that's true...
-and it's like no one really believes that but it really is true. You could come using another mainstream tool and you would have to endure us rolling out the new release of Altium Designer for 45 minutes...
Right.
-other than that, you will just be getting good learning, meeting with other designers so...
Yeah if I go by memory right, we had something in the order of, I don't know, a dozen main stage presentations or so, and of those, two of them were by Altium people.
Right.
And the rest were not. We had probably, I think two dozen, actual learning sessions that were, kind of focused on training and developing skills and so forth and of those, I think maybe four or so were really focused on Altium Designer. And sure, we could show what we typically did was show, how after you spent the bulk of the time learning, how you attack a problem, you'd show how that could be done in Altium Designer, but it wasn't about solving it with Altium Designer, it was about solving it so, and I'm frankly, I'm kind of like proud of that and proud we didn't make it a place where you just come and hear about Altium and we market to you, and sell to you and so forth it's not about that.
Well you really are the champion of that and I am your proud sidekick in that regards because honestly I didn't know any company would let somebody like me, do this, but it's being driven from the top so I love that, that you're kind of holding on to that. This is about community...
Right.
-dang it - so for those of you who are listening, please know that you are welcome to join us at AltiumLive 2018 in San Diego, October 3rd through 5th, and the website is up, registration's open, and because the attendees asked us to last year, we've added a full university's day, where there's more tool training because people actually complained a little bit that we didn't train them enough on our tool. So kudos to us, but we again, didn't want to mingle that into our main program, so we set aside 100 - 160 spots on the front end where we will teach you in the tool, and keep the rest of it rather tool agnostic and then also in parallel our friendly Ritchie has agreed to teach a full day on high speed design which will be a real treat. And all of this, the price is silly-low, and it's in beautiful San Diego so there's just no downside to it as far as I can see so we're all looking forward to seeing you there.
Absolutely.
I wrote a note here Ted, and I'm just gonna ask you about it and we may have already covered it but you had mentioned something to me about AltiumX was that about the transformation part, our x-factor?
Well that's a little bit of a, little bit of an internal code name, right now for the the projects surrounding this connection between Altium Designer 19 and manufacturing...
Okay.
So we've kind of covered it and you won't see a product called AltiumX, but yeah, you know as often happens when products and projects kind of come to life, they don't have a brand associated with them and we look for clever little ways to talk about them internally before we know that people can kind of rally around and know what we're talking about and AltiumX was that, well for this project at least for a while. And we've talked about different ways to brand it and talk about it and so forth but it's really the key thing; is it's a part of Altium Designer, this isn't gonna be a separate product and actually I will say that that's one of the things that's interesting and and I think valuable about Altium Designer, is that it's always been this idea of that it's not kind of like module, by module, by module, but it's one thing that gives you the capabilities that you need and where there are exceptions, it's because we have partners involved and they need to know how much of their product is going on, and so forth but largely if it's Altium, if it's things that we develop internally, we make it a part of that product.
So it's really simple to know what it is you want, you want that one thing Altium Designer, it's really simple to buy it there's one price and it's hopefully really simple to to work with us, and do business with us and in that notion, we call it easy-to but that's when you get to the spirit of Altium, and and our identity and everything, I think that's another piece of it that I didn't talk about before, but it's another part of what we think is really important, is that we just make it easy for people to know what they're dealing with, who they're dealing with and how they work with us and so forth. Even how they use the product, try to work hard to make everything easy to do.
Right, and I think we're living up to that - we're not perfect, we've got lots of growing to do...
That's true.
Always but when I, because I have the privilege of sponsoring teams and different things as part of my job. Often people will come to me and go, oh my gosh! This was so easy to install it only took me... I was up and running in an hour instead of half a day or whatever, so I I sort of hear that feedback so it makes me proud to be part of this team.
So Ted, thanks so much, I know you're such a busy guy and you're spinning a few dozen plates at all times so, thanks for taking the time to sit down with us and share with the people who are listening to podcast.
Well, thanks for giving me the chance to do that and I hope that I was able to give enough insight and something interesting and exciting for people to think about. Love to have people come to AltiumLive and hear more about what we're doing and also hear from their peers in the community but, like I said we're really excited about kind of the journey that we're on. This whole transformation of electronics and we are now starting to feel like we can, we're starting to see light at the end of that tunnel and we've got a long ways to go but there's enough light there that I think with AD19 and AltiumLive that's gonna really start to be exposed in ways that will stop people in their tracks, and so I'm excited about that.
I'm so excited about that and I don’t even know about some of the stuff you guys do, so we'll all learn at AltiumLive so, I hope you will join us. Thank you so much for listening to our podcast. I do encourage you to register for AltiumLive, coming up in October in San Diego we should be in Munich, I believe the mid-January. We're just locking that down now, so bear with us while we get that locked down. And remember, whether you use our tools or not, you're more than welcome and we would love to have you just join us and rub shoulders and be part of the community. So thank you, again Ted, for joining us today. And thank you for listening, or watching, and we look forward to being with you next time, until then always stay on track.
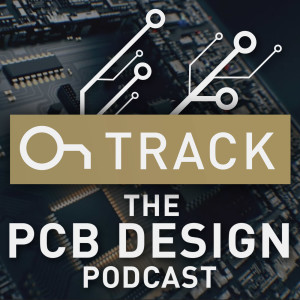
Tuesday Jul 24, 2018
PC Board Stack-up Best Practices with Rick Hartley
Tuesday Jul 24, 2018
Tuesday Jul 24, 2018
What do you do if you have an interference problem? Rick Hartley is an industry leader in the correct design of circuits and PC boards to prevent and solve noise, signal integrity and EMI problems. He consults and teaches internationally and he has taught seminars at numerous conferences, including the IEEE EMC Symposium, PCB West, IPC Apex/Expo and others. He is a past member of the Editorial Review Board of Printed Circuit Design Magazine and has written numerous technical papers and articles on methods to control noise, EMI and signal integrity.
Listen to this episode where Rick shares the worst ideas for a 4-layer and 6-layer stackups. He also offers a sneak peek of what to expect at his AltiumLive 2018 Keynote Presentation: The Extreme Importance of PC Board Stack-up.
Show Highlights:
- Contest - can you guess how many countries the OnTrack podcast has reached? You can win a Summit pass to be Judy’s personal guest at AltiumLive 2018! Just tag #OnTrackPodcast on Twitter with your best guess!
- Mid-80s - in digital domain things started to not work right and no one had answers. There was research to do (120 books later), learned what causes function vs. not function
- In the 90s, began to realize the problem wasn’t clock frequency, the problem is the frequency associated with the rising and falling edges of signals.
- Person who helped me the most - Ralph Morrison
- I didn’t learn what I needed in college, it had to come from experience.
- Energy and Fields and how they move - the energy is in the fields, not in the Voltage and current.
- Field dielectric / routing
- AltiumLive Keynote talk: The Extreme Importance of PC Board Stack-up
- If I’m contacted with an Interference problem, the question I ask is: “What is your printed circuit board stackup?”
- The most critical item is the board stackup, and it’s what people most often get wrong.
- Two or three voltage planes in a stackup with no grounds anywhere - a very serious problem e.g. high layer count board, 20 ground planes in board + signal routed on layer 1 and ground plane on layer 2 - return - 100% of signal on layer 1 would be in ground plane on layer 2. No current from that trace would be in any other ground layers, because energy is in the dielectric between layers 1 and 2
- With 2 or 3 signal layers, and then a plane - all signals try to reference one plane, all fields intermingling in the dielectric space, all coupling energy into one another and that’s one of the places where EMI comes from.
- It’s a matter of keeping fields isolated from one another for proper functioning.
- 4-Layer worst stack-up
- 6-Layer worst stack-up
- What to expect at AltiumLive (Early bird pricing - 10% off through end of July.)
- Setting the record straight: 15 years ago, Rick wrote a paper called ‘Board Stackup to Control EMI’ and “some ideas that I suggested in that paper, I have since learned are not good ideas.” Ignore this paper because the physics have changed. The speeds have become too fast.
Links and Resources:
High Speed PCB Designer’s Guide, Martyn Gaudion
You can also read more articles featuring Rick Hartley in the OnTrack Newsletter here and here.
Hey everyone this is Judy Warner with Altium's OnTrack podcast. Thank you again for joining. We want to thank you so much for continuing to listen and we wanted to share with you that from May to June the listenership has doubled and absolutely exploded because I have amazing guests like I have today. Which is Rick Hartley.
But before we get going with Rick, I wanted to give a few of you a shout out. I wanted to say thank you for the notes and ideas for the show that you sent: To Daud Zoss, I'm sorry if I'm killing your name; Dave Rehack, Spencer Kelly gave us some really good ideas for our future shows. Enoch Sotello and also a nice sharp shout out from a LinkedIn group, the Arkansas Signal Integrity community and I'm sure you guys will enjoy hearing from Rick today.
So I thought I'd throw a fun thing out there since AltiumLive is going to be hosted in San Diego, October 3rd, 4th, and 5th. I thought I'd give you a little trivia question today. So can you guess how many countries the OnTrack Podcast has reached? If you guess close to the number, then I you will be my personal guest at AltiumLive and I'll give you a free ticket there. So how about that? So you can tweet your answers using the hashtag #ontrackpodcast.
So whoever is closest, and we will announce the winner on our next podcast. Thanks again for listening. So today we are talking to, in fact, one of our keynote speakers for AltiumLive, a dear friend and longtime associate, Rick Hartley and I'm sure for many of you, he is no stranger and he is a celebrated speaker. He's been a leader in IPC for many years and a very gifted designer. So Rick, welcome thank you so much for joining me today, it's a joy to have you.
Thank you Judy, it's a pleasure to be here.
So what I thought we'd talk about today Rick, well first let's queue up and tell people who may not know you - the six people on the planet that may not know Rick Hartley - a little bit about your education and your background and sort of how you became a signal integrity guru?
Oh, you want me to tell this?
Yes I do.
I'll try to make it brief.
Okay.
I basically started life in 1965 as a technician with a two-year tech degree and working for a large company in the east, and I spent a couple of years there and decided that wearing one hat a day for six to eight months wasn't what I wanted to do at the age of 20. That I really wanted to be able to wear five hats a day. And so I moved to a small company in Columbus Ohio - I'm still in Columbus - and basically joined an R&D group where I got to do just that. I would be testing boards one day and troubleshooting the next, and so on. Within a couple of years I moved to field service, and from field service I learned a lot about troubleshooting problems and field service as you can well imagine. From field service I moved into the engineering department in that company where I became a designer and as a designer - the designers back then designed everything but the circuit - they designed the circuit boards, the cabinets, the chassis, the wiring harnesses, the interconnects, everything except the actual circuit schematic and I spent a fair amount of time doing that.
And then, over time, with school in the evening I earned a degree in engineering became an EE and worked several years as a circuit designer around 1976, seven-ish time frame, the company - I had moved companies by then. The company I was working for asked me to; they said you have some background with printed circuit design? I said yes, we would like for you to help out doing part-time circuit design, part-time board layout. I said, sure no problem. After six months of that, I decided board design was really the thing I liked most.
And so I moved full-time into circuit board design, away from full-time circuit design. For a long time I was doing basically RF design, RF layout, which is a little more challenging, especially back then. Digital layout then wasn't too challenging. Anyway moved into board layout, spent a number of years there and along the way somewhere, about the mid eighties, things started to not work right in the digital domain, and frankly, most people didn't know why this was happening. They - most of the engineers I worked with, - were scratching their heads; I was certainly scratching mine. And over time, by doing a lot of reading; I purchased over 120 books since then, between the mid 80s and now, and read them all. Some of them, three or four times, and basically learned what causes things to function versus not function, what causes interference and so on, and probably the person that helped me the most to get to the understanding I have today, is Ralph Morrison, and I'm going to talk a little bit about Ralph as I go through this.
But anyway, by just getting my arms around why people have signal integrity problems, why there are interference issues, it's helped me over time to become I guess what people call a guru, I'm not sure I am, but you know whatever, whatever the title is.
A good guru will never say they're a guru Rick so it's okay, I'll call you a guru.
All right.
That's pretty much how I got there it was just a matter of, it was a matter of stumbling along frankly, for years and years - not fully knowing why, and little by little, gathering the knowledge, because sadly, I didn't learn in college, the stuff I really needed to know to take me to where I needed to be. I mean, it had to come through experience, it had to come through just hard-won, hands-on on the job experience. Because it didn't come from college, sadly. And that's kind of where, how I got to where I am today. And of course this all started in the mid-80s. By the mid-90s, I was really beginning to have a pretty good understanding of the issues and it's really all just built since then.
And I think, you and I had a talk and you were actually in our OnTrack newsletter a year or so ago, and I remember you saying around that time is, when you... didn't you talk about... oh I'm gonna forget the term now, because I'm not an engineer - rise times.
Yes oh absolutely.
Was that something, was it around that time that you started realizing that rise times were problematic?
That's exactly, it was actually in the 90s, when I started realizing that the problem wasn't clock frequency, the problem is the frequency associated with the rising and falling edges of signals. If you have a device on a circuit board, that is being clocked at a low frequency - two, three megahertz, but you have a rise time with two, three, four, five hundred picoseconds, you'll have energy in every transmission event that extends upwards to a gigahertz or beyond, even though you're only clocking at a low frequency. So it isn't the clock, the clock really sets the timing for the circuit. That's really why it's called a clock, it sets timing. The rise times are really the key element that drive signal integrity, and even worse; drive EMI issues and interference issues. It's really all about rise time, yes.
That's - I thought that was fascinating when you talked about that earlier. Now I've sat in a few of your classes and I've learned a couple, in my novice kind of way, a couple really key things that really impressed me when I sat in one of your classes at IPC, and in that room of say 50 people, you asked the people in that room: who in this room are EEs and also printed circuit board designers? And a handful of people raised their hand and you asked the question; which one's harder, the circuit design or the board design? And they all like guffawed at that and just said, duh, printed circuit board design.
To which someone like me went, wait - I thought the EE was the heavy lifter, the one that kind of got the creds for doing the hard work but you really taught me then, that - and I think this is a lot - because circuit boards have become so complex over time too but that probably wasn't always true - and I had just missed that, that it had become. So why is it that you asked that question, and what made you choose to go from EE to actual board design?
The, just frankly, the challenges. I found even in the late 70s, I found the challenges of board design to be more stimulating and more invigorating and it made me feel just more alive everyday to go to work than to be designing circuits and setting up test procedures and that sort of thing. And not that there's anything wrong with that, my god, I asked the question of those guys which is more challenging and most of them said board design. If you ask them which took them longer to learn, they would probably say circuit design took them longer, there's more to understand to become a good quality circuit designer, to really get what it takes to design circuits, to function properly. But once you have that knowledge, the actual effort and energy and time expended once you're there - once you're at that knowledge level - is actually greater to lay out a circuit board than it is to do a circuit design and that's why they all answered that way.
There is you're right.
There was a time when circuit board design was ridiculously easy. I have a circuit hanging on my wall, you can't see it from this camera but it's a two layer board that I designed in 1985. It has no planes and it's just routed power and ground and routed signals it's hideously complex because it's over 200 ICs, on a circuit board it's really packed, and that's why it's hanging there because it is such a complex, by the way hand taped, artwork. It's a very complex artwork and that makes people go 'oooh' when they walk in that's why it's there.
But the reality is, how that was laid out was immaterial, because its layout just almost didn't matter, you could do almost anything back then and the circuit would still work. I remember seeing a tape layout in the 1990s, of a guy from the aerospace world where I spent in the early 90s; a board this guy laid out in the 80s, that there was a corner powering ground pin IC for, like a 20 pin part, and there was a decoupling cap sitting above the IC, and he had a trace routed from the decoupling cap, all the way around the body of the IC and back up to the power pin of the device. It was probably an inch and a half long trace from it, and it was a skinny little, 10 mil trace, and the circuit worked. And it's because things were so slow back then compared to today. And it's about rise time not clock frequency. Rise times back then were measured in the tens, in some cases even hundreds, of nanoseconds.
Today they're measured in the hundreds of Picoseconds so they are at least a thousand times faster than then - a hundred to a thousand times faster than they were in the 80s and that's why, things today are harder to make work than they were in those days.
Well that just blows my mind to think of things - I mean, I know that it's happened it's just hard to get your head around those kind of numbers sometimes.The other thing you said, and then we're going to jump into what you're going to talk about at AltiumLive. The other thing I learned from you, which I've told you about this. A few times it just made my head explode was when you started talking about the energy in a circuit board is in the dielectric and it was like; wait what? No it's running like water through pipes on the traces, like that's how I pictured it and you explained it, and you showed a field you had and I all of a sudden, like well, I knew some energy moves through the dielectric, but not the way you explained and literally; it was like I felt embarrassed, and I remember walking up to you and going: okay don't tell anyone but I didn't know that. And you said...
People don't know that.
-then you said, it's okay judy EEs don't know that, and I'm like, okay all right I don't feel so bad. So why don't we know that Rick?
Because it's not talked about generally in college. Voltage and current are important parameters, they are - I just had a discussion very recently with Eric Bogatin on this exact subject. Voltage and current are extremely important parameters for identifying how transmission lines work, why signal integrity issues arise. These are all things that you need to know, but the reality is if - and if you're trying to track down signal integrity issues - probably best to talk about voltage and current more than the fields. But when you're trying to identify why an interference problem has occurred, why did energy move from circuit A to circuit B, how in the world did it get over to circuit B?
Where did that - because the voltage and current followed the traces that we routed in circuit A. So how did the energy...
The reason is that, as you just said, the energy is in the fields, not in the voltage and current and the fields travel through the dielectric space between the copper features. And that's the key element. When you route a trace you're routing half of a transmission line, the other half of the transmission line is the plane, usually in most boards today, a plane where the energy returns. So you have the forward current traveling down the trace that you've routed, and you have the return current traveling in the plane directly under the trace that's routing across the board. And that current is being established because there are fields with energy creating the voltage and current in the transmission line. And that's the key element to understand. If the energy weren't in the voltage IRAM, sorry, weren't in the fields; radio wouldn't work. Think about it, radio broadcasting of fields into free space, that get picked up by antenna that focused the energy into a radio. Anything that uses broadcast medium works in exactly that fashion. And the reason it works, is because the energy is in the fields. Now you can capture those fields with copper structures.
And when you do, then they will channel through the dielectric between the copper features; that's what an antenna does and an antenna focuses the fields into a center point, that focuses them to a transmission line, to the receiver and that's exactly what an antenna is. So bottom line, because the energy is in the fields, and the fields travel through the dielectric space, that's how things can sometimes spread. If we don't route traces properly, if we route, for example, two or three layers of traces above a plane; all of those trace layers are capable of coupling energy into one another, which causes the fields to then spread to places where they shouldn't be. Or, if you change layers improperly - that's something I'm going to talk about, at AltiumLive, is well - the main thing I want to talk about is board stackup.
Yeah so let's just jump in right there I think that's a good place to segue. So Rick is doing, han hour keynote at AltiumLive and the title of his talk is: 'The extreme importance of PC board stack up.' So let's just jump right off there. So you've already started to talk about energy and fields and how they move. Talk about that relative to stack up and why that can be problematic in not so obvious places?
Yeah I will, yes the main question that I ask people; if someone contacts me and says: Rick we've got an interference problem of some kind, be it EMI, be it interference between circuits, whatever. I've had, within the last year of it, people contact me to talk about op-amp circuits that were being interfered with by other things in a circuit board or inside a system. Why does this happen is the question that's often asked. The first question I ask them is, what is your printed circuit board stack up? Because the most critical item to get correct, to have correctly done, is the board stack up.
The most critical item is the board stack up and that's why I ask that question because what people often get wrong is the board stack. I will often see examples of people who have put two or three voltage planes next to each other in a board stack, with no grounds anywhere nearby. And that's one of the things I'm going to talk about at AltiumLive; why that's a problem. It's a very serious problem. For example, if you had a circuit board that was many layers thick, and you had, let's say twenty ground planes in the board. If you had a signal routed on layer 1, and there was a ground plane on layer 2, all 100% of the return current from that signal on layer 1 would be in the ground plane on layer 2, and there will be no current from that trace in any of the other ground layers because the energy is in the dielectric...
Yeah.
Between layers one and two, it establishes a forward current in the trace and a return current - a reverse current, in that. All the other planes, it's like they're not even there. They don't even get used because the energy focuses itself in that tight area, and as I said a minute ago, if you have two or three signal layers and then a plane, now all these signals are all trying to reference that one plane. So all of those fields are intermingling with one another, in that dielectric space and they're all coupling energy into one another, and that's where the interference factor comes from. That's where - it's one of the places where EMI comes from - there are many things that cause EMI, that's just one of the many problems. So it's a matter of keeping fields isolated from one another. That's what we have to do if we expect things to function properly.
Well I think, besides your prolific reading habits being an EE, I think, has obviously served you well and so, to understand how fields move and because, like I said, I have a very fundamental understanding of designs and certainly not of field theory and all of that, and how physics work but I think that's one reason why you've been such a popular speaker and consultant. You talked about - or you're going to talk about - and let's kind of tease it up a little bit; is the worst four layer stack up. What does that mean?
Well there are actually two four layer stack ups that I'm particularly not fond of. One of them is - and I see this a lot in the automotive and appliance industries - where they will put a single ground plane on, let's say layer three, and they'll put routing with routed power, on one, two, and four. And what we talked about a minute ago, having more than one routing layer referencing a single plane,in this case layers one and two; are both trying to reference the plane on layer three. And the result is the field, even if you route them in orthogonal directions, the traces, the fields will still inter-lead one another and we'll couple energy. And the energy that couples, won't be enough to cause a signal integrity problem if you do the stack - if you just do the routing correctly - but it will still be enough that it can cause EMI problems.
What a lot of people don't realize is that it takes as little as eight to ten microamps - microamps, millionths of an amp of common load current coupled into a balanced antenna to cause an FCC Class B, radiated admissions failure.
Wow.
So as it takes that little bit of current to cause an EMI problem, and it doesn't take much coupling of fields to create eight to ten, or even milliamps of noise current. So it's a problem that people need to pay attention to. So that's one of the four layers. The other four layer that's a problem, is the one everybody uses - and that's powering ground on two and three, and the reason that's a problem - if a circuit board is extremely thin - if a circuit board is say 10, 15, 20 mils thick; then those two power and ground planes on 2 & 3 are going to be very close together. And when you do that, when the power and ground planes are extremely tight - a few mils to maybe at most 10 mils away from one another, then you can get away with having power and ground on 2 & 3 or 4 layer. But if it's a 62 Milotic, a 1.6 millimeter thick board, and you have the planes on 2 & 3, they're going to be about a millimeter apart - and when planes are a millimeter apart, there's several things that go wrong.
One, we rely on the planes to help deliver power. The planes basically become the low impedance path for power delivery 2 and IC, if you asked a lot of people, a lot of Engineers, where does power come from in a circuit board? Their answer will be the power plane.
All right.
Of course we know that's not true. The energy comes from the dielectric space between the power plane and the ground plane.
See there it is again...
Exactly. If the dielectric space is tight, the capacitance will be fairly high but most of all the inductance of the planes will be very low, and when the inductance is low, now you have a low impedance delivery path for power. If the planes are far apart, as they are in a conventional 62 ml thick, four layer board, the impedance is so high it doesn't do a good job of delivering power, and you end up with large LD/IDT voltage drops across the power system that we can refer to as power bus switching noise, and that issue alone can cause signal integrity problems but mostly will cause EMI problems.
That's, again, it's like can't, my head's exploding again. Four layer board, 062 - standard thickness of your run-of-the-mill board, I mean this is not fancy, and you're saying this is a bad idea! And I'm like wait, what the earth does not flash? I mean it just that's what it sounds like to me like - it's crazy but it's fascinating and I can't wait to hear - I'm sure you'll dig into this more?
Well I'm gonna get into it more because there are routing implications with that four layer board as well.
Okay.
I mean it's worse than just - than just power delivery. If you have a trace routed on layer one referencing the power plane and you want to change layers to layer four, you're going to have to move the reference to the ground plane, which means the energy in the dielectric space between one and two has to somehow move through that board to the dielectric space between three and four. How is it going to get there? And there are people who will say, oh, it uses the decoupling capacitors. Well that's true, if the frequency is low enough. If rise times look low enough, then that's what will happen. That's why for years, we could get away with four layer boards with power and ground on two and three because rise times were so slow.
Gotcha.
But now all of a sudden, rise times are measured in the hundreds of Picoseconds and that four layer board just doesn't work well. But we're gonna get into that in more detail at AltiumLive.
Okay. You also talked about a six layer?
mm-hmm...
-please don't make my brain explode again Rick, but go ahead, tell me the six layer that's a bad idea?
The six layer board that everyone uses is signal, plane - like power ground, two signals, the other plane. If you put power into that, they'll put ground on five and then a signal and six. And this is a common six layer board that just about everybody on the planet uses and it's even worse than the four layer board with power and ground on two and three. And we're gonna get into intimate detail at AltiumLive about why. It's about, I mean, think about what we said about power delivery with the four layer board. If you have planes a millimeter apart and that's not good enough, what do you think putting them on two and five, of a six layer board where they're even further apart, is gonna do two power delivery?
And now, worse than that, you have the fields between two and five sharing the dielectric space with signals that are on three and four, and all of those fields are saying hello to each other; hey let's get together and party, and they do get together to party and they wreak havoc! And this is a bad board stack, and we're going to talk more about why it's a bad board stack, and then we're gonna get into exactly what to do to fix it. There is a solution. To be able to use that board stack and make it work, and we're gonna talk about how to do that.
Well I can't wait and I intentionally wanted to have you on today to tease that out because, for those of you that don't know already, Rick teaches all over North America, and sometimes out of the country as well. If you haven't seen it, we will share all these links in the show notes. But he's been teaching, he's been on, at least a North American tour, with a series put on by UP Media called 'PCB Today' and those are two days right, Rick?
It's a two day event, and then we go through everything we've discussed here and much, much, much, much more.
Right so two days; so I highly recommend UP Media's PCB2DAY with Rick Hartley. We will share that link for any of you that might want to get a full two days. At AltiumLive we're gonna have you drink from the fire hose and give you an hour of Rick Hartley talking as fast as he can. Rick also speaks at PCB West, which is in Santa Clara in September, I think it's September 12 this year, or that week of September.
It's September 11, 12, and 13 I believe -
It's a three-day event, again loaded with great content there's an exposition day but Rick teaches more than one class there and they're always packed, so.
I'm actually teaching six classes this year.
That's crazy and besides Rick, there's a lot of really other illustrious teachers. It's like good luck with that one; picking your courses because it's a really good show also put on by UP Media so...
I mean that show has Dan Beeker and Susy Webb, there's a host of people; Mike Creeden, I think is going to be there this year, there's just a boatload of people with talent talking about...
Such talent! And by the way, I want to boast just for five seconds, because I have the neatest friends in the whole wide world. And that is that Susy Webb will also be teaching at all AltiumLive, Mike Creeden will be there; I don't know if he's teaching yet, Eric Bogatin, who Rick mentioned, will also be a keynote speaker , and I think that conversation you were talking about having with Eric, was probably on an email feed that I was eavesdropping on.
It was actually just a direct email with Eric because yah, I think you were involved?
I got looped in there and, a significant portion went over my head, but it was just interesting to see you guys kind of bantering about your subject. So again, Eric will be one of the other keynote speakers so I'm very privileged to know some very bright, gifted people, and Altium is bringing all these wonderful folks together. So I hope you will join us and I hope this conversation has encouraged you to join us. And we do have early bird pricing, which is like ten percent off through the end of July. So please be my guest we will - - Rick has shared links with us to other resources. Oh! You wanted to mention something about a paper that's floating out there, that you no longer endorse. So why don't you mention something about that?
Yeah about 15 years ago, I wrote a paper called 'Board Stack Up to Control EMI,' and while the basic content of the paper is more or less correct, some of the board stacks that I I suggested in that paper; I have since learned were not good ideas, and in fact, the four layer and six layer that we just talked about, are two of them, that I recommended in that paper, because I believed at that time, that they were the right thing to do. I've since learned why they aren't, so if you happen to stumble across that paper again; it's called ' 'Board Stack Up to Control EMI,' ... or to help control EMI, something to that effect, and if you stumble across that, just ignore it.
Ignore it cause we're gonna get Rick Hartley 2.0 where things have gotten faster and he's, I don't know that you've gotten smarter; I think just the physics of the boards people are designing have changed.
The physics have changed and that's a key point. That's a very good point Judy, and that's partly why, I mean, it's possible that when I wrote that paper, that four and six layer boards were fine...
Yeah exactly but the speed...
-but they're not today.
And again that's why we always advocate here that you need to always be learning because technology does not stand still and what worked yesterday, is not going to work tomorrow. And so we we try our best to stay on top of it. Rick thank you so much for joining us. I also am going to put in a photo, hopefully it won't embarrass you Rick; of - -
You know, what I want to say about Rick Hartley and people like Susy Webb, Mike Creeden, Eric Bogatin; we are all - you all as designers and engineers are really standing on their shoulders and they used to do this stuff by hand. So I have the neatest photo ever of Rick Hartley with a big fat 70s tie I think, handling out the biggest board ever that I've seen - the biggest tape up I've ever seen.
That's actually the one hanging on my wall...
It is, that's the one? So I'm going to share that and the links too because you guys that just have snazzy racy tools and you started designing ten years ago won't believe the stuff these guys and gals did by hand. So, well Rick we totally and completely look forward to AltiumLive, thanks so much for agreeing to come and invest in the design community, and thanks again for doing this podcast you are a dear friend.
Judy, thank you so much for having me. Yeah and thank you so much for all that you do for the industry Rick, we really appreciate you.
It's a pleasure.
Again this has been Judy Warner with Altium's OnTrack Podcast and Rick Hartley of - how do you say that?
R Hartley Enterprises.
We look forward to seeing, or we look forward to you tuning in next time. Until then, remember to always stay on track.