Episodes
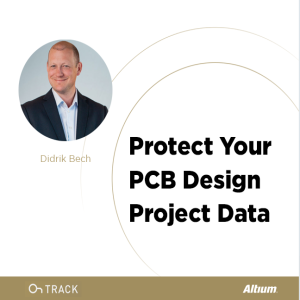
Thursday Feb 17, 2022
Cybersecurity in PCB Supply Chain
Thursday Feb 17, 2022
Thursday Feb 17, 2022
It’s a privilege to be sitting down with Didrik Beck, CEO of Elmatica, the world’s oldest PCB broker company and now part of the NCAB group and CAB group. Together we will dive into exciting topics surrounding cybersecurity, compliance, and supply chain and his upcoming presentation at IPC Apex. Didrik has some interesting insights on supply chain Cybersecurity management in the PCB design and manufacturing industry. Make sure to watch through the end and check out the additional resources below. This episode will be an insightful one!
Altium 365: Where the World Designs Electronics
Watch the video, click here.
- Dedrick Bech introducing Elmatica
- World's oldest PCB broker
- Recently acquired by the NCAB group
- Securing PCBs for different partners in the PCB supply chain
- A quick summary of what was going to be in the IPC Apex paper that Dedrick is presenting
- Different levels of compliance and to what extent does this apply in the PCB design and manufacturing
- Controlled Unclassified Information (UCI)
- Every country has a different view on it
- Two possible aspects of greater focus on compliance
- Intellectual property
- Cybersecurity concerns
- How to get IT and compliance strategy come back and get implemented together
- Data security awareness - some tips and practical steps
- Is it worth it to invest for a data security software and team
- More ways companies can do to help guarantee compliance and prevent data to be copied
- Formalized packages for a high level of compliance - how deep does this have to go for small companies
- Compliance and Cybersecurity differs from country to country and depending on:
- the company
- the country’s regulations
- where the PCB is produced
- There is a room for improvement in creating some compliance hazards for designers
- Start with a good communication with the supply chain team
- Gather data ahead of time
- Misconception about sharing data
- Securing supply chain for large subcontractors
- The importance of reading and understanding Defense Federal Acquisition Regulation Supplement (DFARS) regulation
- AltiumLive Connect was successful! Watch the exclusive recorded sessions here
Links and Resources:
Connect with Didrik Bech on LinkedIn
Visit Elmatica’s Website here
National Institute of Standards and Technology
Defense Federal Acquisition Regulation Supplement (DFARS)
Watch AltiumLive 2022 Connect Recorded Sessions Here
ALTIMADE Design to Manufacture, Made Easy | Request Access Now
Full OnTrack Podcast Library
Altium Website
Download your Altium Designer Free Trial
Learn More about Altium Nexus
Altium 365: Where the World Designs Electronics
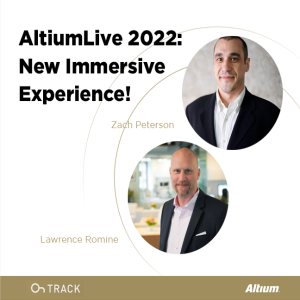
Tuesday Dec 21, 2021
AltiumLive 2022: Learn, Connect, and Get Inspired
Tuesday Dec 21, 2021
Tuesday Dec 21, 2021
In this episode, Zach chats with Lawrence Romine, Altium’s VP of Marketing. AltiumLive 2022 Virtual Summit is fast approaching, and we wanted to deliver to you some important information and reasons why you should not miss it. Lawrence gives an exciting overview and details about AltiumLive 2022’s new immersive experience!
Altium 365: Where the World Designs Electronics
Watch the video, click here.
Show Highlights:
- AltiumLive 2022 connecting the ‘User Community’ (Designers and Engineers)
- 2 Events in the Calendar
- AltiumLive 2022 Connect Americas: Wednesday, January 26th to Friday, January 28th
- AltiumLive 2022 Connect EMEA: Wednesday, February 2nd to Friday, February 4th
- FREE registration and remote accessibility worldwide
- This year’s AltiumLive is in collaboration with Institute for Printed Circuits (IPC), the Association Connecting Electronics Industries
- Adapting the hybrid model (full virtual event) to get the whole world to connect and get involved
- Bringing some of the finer points of the upcoming IPC Apex Expo
- NEXAR Partnerships
- What NEXAR Ecosystem can bring to the participants
- Altium 365, bringing the rest of the industry at large
- Altium’s real focus on the user community and its uniqueness with other CAD companies
- The real mission and purpose of AltiumLive 2022
- A non-commercial event
- All about Learning, Connecting, and Getting inspired
- Industry expert, Eric Bogatin will be one of the speakers at AltiumLive 2022
Links and Resources:
AltiumLive 2022 Connect: Now open for registration
AltiumLive 2022 Connect Americas
IPC, the Association Connecting Electronics Industries
Previous Podcast Episodes with Eric Bogatin
- Signal Integrity Evangelist Eric Bogatin, our Expert Insider to DesignCon 2020
- Why You Should Stop Hanging on to Legacy Design Rules
- Bogatin’s “Practical Guide to” Book Series
- Pathological Design Features
Connect with Lawrence Romine on LinkedIn
Connect with Zach Peterson on LinkedIn
Watch Zach’s latest Altium Academy courses on Youtube
Read Zach’s articles on Altium’s resource hub
Download your Altium Designer Free Trial
Learn More about Altium Nexar
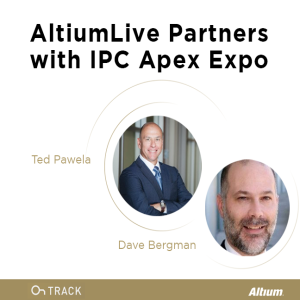
Tuesday Aug 24, 2021
AltiumLive Co-locates with IPC Apex Expo
Tuesday Aug 24, 2021
Tuesday Aug 24, 2021
AltiumLive 2022 and IPC Apex 2022 are joining forces to bring together all stakeholders in the PCB industry.
We have two executives joining us in this episode. Our very own Chief Ecosystem Officer and head of Altium Nexar, Ted Pawela; and IPC’s Vice President of Standards and Technology, Dave Bergman. They will share with us some exciting news about the most anticipated exhibits in the PCB community.
Altium 365: Where the World Designs Electronics
Show Highlights:
- Introductions:
- Ted Pawela, the Chief Ecosystem Officer and Head of Cloud (Nexar) Business Unit at Altium
- Dave Bergman, the Vice President Standards and Technology at IPC
- IPC and Altium Live conferences co-locate
- Uniting the stakeholders: PCB Design, PCB Manufacturing, PCB Supply Chain
- IPC leadership role in the industry— providing standards and educational foundation
- Bringing and exposing the PCB Designers to additional valuable education
- Dates of conferences and where overlap opportunities will be offered
- IPC Apex 2022: January 25th - 27th in San Diego with the theme “Digital Transcendence”
- AltiumLive 2022: January 26th - 28th in San Diego with the theme: “Connect”
- The intersection between the 2 conferences
- The relevance and synergies of ecosystems and community engagement
- Education strategies from Altium, IPC, and places of interest to intersect
- Understanding what’s beyond the tools
- Advancing the PCB designers’ careers through education
- IPC serves as a validation of the designers’ skills and talent through CID and CID+ training.
- IPC Foundation
- Why should you attend, what opportunities are there for you?
- User-centric
- Learn from the pure hard work of subject matter experts
- Improve design skills and connect with the people in the community
- Experience the biggest and the best, see you in January 2022
Links and Resources:
AltiumLive 2022 Website
IPC Apex Expo 2022
IPC CID Training (Eptac)
Altium Academy YouTube Channel
IPC Edge Educational Resources
Full OnTrack Podcast Library
Altium Website
Download your Altium Designer Free Trial
Learn More about Altium Nexus
Altium 365: Where the World Designs Electronics
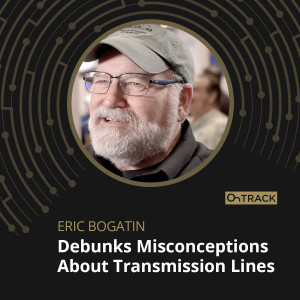
Tuesday Aug 04, 2020
Eric Bogatin Debunks Common Misconceptions About Transmission Lines
Tuesday Aug 04, 2020
Tuesday Aug 04, 2020
Signal integrity expert, Dr. Eric Bogatin, has a new book whose mission is to establish a solid educational foundation in the essential principles of signal interaction with transmission lines. The multimedia eBook, Bogatin’s Practical Guide to Transmission Line Design and Characterization for Signal Integrity Application, is currently available from Artech House and can also be found on Amazon.
Dr. Bogatin is Signal Integrity Evangelist at Teledyne LeCroy, a leading provider of oscilloscopes, protocol analyzers, and test and measurement solutions. He joins the OnTrack Podcast to discuss his book and give us a sneak peak of his upcoming AltiumLive panel with Istvan Novak, Heidi Barnes of Keysight, and Steve Sandler of Picotest.
Altium 365 Podcast Listener Discount
Show Highlights:
- In addition to so much else, Eric Bogatin is a science fiction author! Check out his books Shadow Engineer, and S is for Space
- An overview of Eric’s new multimedia eBook, ‘Bogatin’s Practical Guide to Transmission Line Design and Characterization for Signal Integrity Application’
- ”I think the most confusing topic out there...is transmission lines”; how Eric’s book builds a solid foundation for anyone seeking clarification on transmission lines.
- Clarifying engineering’s most confusing issues
- Teledyne LeCroy’s new TDR calculator
- The practical nature of transmission lines: common misconceptions among engineers
- Embedded videos, demos, and calculations: how Eric’s multimedia book provides an interactive experience
- Hard copies, soft copies, ALL the copies: how and where to find Eric’s book(s)
- AltiumLive announcement
- The plain truth about split ground planes: Eric provides a sneak peak of his upcoming AltiumLive panel with Istvan Novak, Heidi Barnes of Keysight, and Steve Sandler of Picotest.
- ”There’s one case where you wanna use a split ground plane...”: Eric previews his upcoming demo on crosstalk reduction
Links and Resources:
Eric Bogatin on LinkedIn
Bogatin’s Practical Guide to Transmission Line Design and Characterization for Signal Integrity Applications
Artech House Publishers
Eric Bogatin Author Page on Amazon
Shadow Engineer (Fiction Scifi book by Eric Bogatin)
S is for Space (2nd Scifi book by Eric Bogatin)
Teledyne LeCroy Website
Signal Integrity Journal
Podcast Episode: Signal Integrity Evangelist Eric Bogatin, our Expert Insider to DesignCon 2020
Altium 365 Podcast Listener Discount
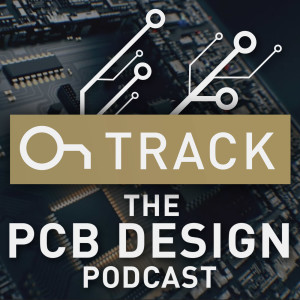
Wednesday Jul 24, 2019
Robert Feranec on How to Implement The PCB Design Process
Wednesday Jul 24, 2019
Wednesday Jul 24, 2019
In this episode we talk with Robert Feranec, a familiar name to many of our listeners. Apart from being a popular YouTuber, he’s also the founder and CEO of FEDEVEL Academy where he teaches PCB Design to people around the world. Robert shares what it takes to be a popular YouTuber, the work it takes to produce all the great content he creates and as a special bonus we’ll discuss Robert’s Keynote that he will deliver at AltiumLive PCB Summit this October in San Diego.
Show Highlights:
- Robert considers himself lucky to have started working on complex boards almost immediately after university. This early start provided much experience and he soon began freelancing.
- As a freelancer, he did whole-board design i.e. specifications, schematics, layout, as well as testing and firmware.
- He found he often couldn’t remember everything when using Altium Designer® and started doing YouTube videos, at first for himself, but soon garnered a following and today he has 24 000 followers.
- As he became more popular, he received many email questions daily, which was very time consuming and he decided to create a forum where he offered a course, and the rest is history. Robert teaches Altium Designer but also CAD-independent content.
- What goes into creating a video tutorial? Lots of preparation, a half-hour video takes almost two days to create. One hour of video training takes a week to create.
- AltiumLive Topic: How Other Companies Implement Their Hardware Design Process. Many people ask about how other companies implement hardware design, create and use libraries, collaboration (design flow) and working faster.
- Why do so many people only use a small percentage of their tool’s capacity? Most don’t need all the features. Many are nice to have but not always a necessity. Also, people learn to use the tool in a specific way and adding new features could interfere with an established workflow.
- Robert’s talk at AltiumLive will provide insight into libraries, creating new components, component lifecycle, creating new symbols as quickly as possible, ensuring correct footprints, and more.
- What are the challenges around collaboration? Communication between different types of engineers and how to manage several engineers working on the same project.
- What about versioning and backup? Most companies will do both in the same way.
- Document releases are very complex, there are too many emails back and forth. Robert will talk about ensuring correct documentation and release procedures.
- What attracts people to your training? The different levels of the courses, the variety, and junior designers love them to upskill and get better jobs.
Links and Resources:
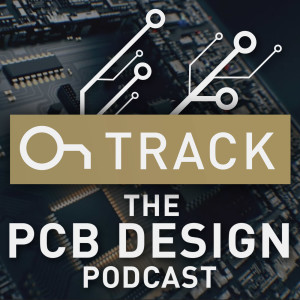
Tuesday Aug 28, 2018
Injection Molded Structural Electronics and Designing in a 3D Space
Tuesday Aug 28, 2018
Tuesday Aug 28, 2018
Sini Rytky, VP of Product Management at TactoTek, and Tuomas Heikkilä, Senior Electronics Designer, join Judy Warner on the OnTrack Podcast to talk about Injection Molded Structural Electronics, or IMSE, the integrating of electronics inside 3-dimensional electronics to create smart surfaces. TactoTek is a leading provider of solutions for 3D structural electronics, enabling the integration of printed circuitry and discrete electronic components into injection molded plastics. Listen to how TactoTek and Altium are combining forces to research and develop design rules for this entirely new technology. Learn more about this and how you can meet them at AltiumLive 2018.
To see all the show notes and VIDEO click here.
*This communication may contain forward-looking statements about strategies, products, future results, performance or achievements, financial and otherwise. These statements reflect management’s current expectations, estimates, and assumptions based on the information currently available to us. These forward-looking statements are not guarantees of future performance and involve significant risks, uncertainties and other factors that may cause our actual results, performance or achievements to be materially different from results, performance or achievements expressed or implied by the forward-looking statements contained in this communication, such as a failure to add previewed functionality to our products or the potential impact on our financial results from changes in our business models.
Transcript:
Hey everyone this is Judy with Altium's OnTrack podcast. Thanks for joining again. I have two amazing guests hailing all the way from Finland today and I look forward to sharing them with you. Before then I ask you to please connect with me on LinkedIn, on Twitter I'm @AltiumJudy and Altium is on all the traditional social media channels Facebook, LinkedIn, and Twitter.
So today we have a look into the future of technology with TactoTek and I have two wonderful guests, Sini Rytky and Tuomas Heikkilä. So we've been working here at Altium closely with Sini, Tuomas and their whole team there and we are excited to show you, kind of this cutting-edge technology, and the amazing things that they're doing in Finland to advance a whole litany of advanced electronics manufacturing and technology and while we continue to work feverishly on AD19 and getting in the traditional functions that you would like, I wanted to give you a sneak peek on something more for the future. This is not going to be in AD19, but we continue to work together, sort of on a research kind of function, with these two and all of TactoTek. So I'm excited for you to learn more about them - so let's get started. Sini, Tuomas, welcome.
Thank you Judy for having us here.
So Sini, I think I'm going to start with you. Can you tell us a little - well before we get going, why don't you both introduce yourselves and tell us your background in the industry and what exactly your role entails at TactoTek?
Sure, so my name is Sini Rytky and I'm heading the Product Management at TactoTek. In practice it means that my team is responsible for technology productization and roadmapping and go to market strategy and planning. And also technology partnership development. My personal background: I am a Software Major, but spent about 20 years in mostly hardware driven business. In electronics manufacturing and test automation in consumer electronics and automotive industries. It is my first podcast ever - I'm very excited!
How about you Tuomas?
Okay so my name is Tuomas Heikkilä and I'm the Senior Hardware Specialist and I have worked for TactoTek, for almost six years now. All of this time I have designed and developed. I oversee technology from an electronics point of view. So my background: I have worked also in the mobile phone industry before joining TactoTek.
Along those lines Tuomas, can you tell us about - for those that aren't familiar what the acronym IMSE means?
IMSE means Injection Molded Structural Electronics.
Very good because I know we'll be using that term a lot and because you guys are sort of cutting-edge I thought there's maybe some people in the audience that might not be familiar with that term. So Sini, let's just jump right in. Can you talk about - I'm asking you three really big things: the technology, the market, and really the problems it solves for technologists in the marketplace?
Sure to start off with the technology; like Tuomas said, our technology is called Injection Molded Structural Electronics which we call IMSE. To put it simply in one sentence, we are integrating electronics inside three-dimensional plastics, and as a result we can create smart surfaces with electronic functionality such as capacitive touch functions, illuminated icons and wireless connectivity such as Bluetooth and near-field communication.
So when we look at traditional electro-mechanics assembly, they typically consist of one, or a multi PCB structure along with the surrounding mechanics and from a design point of view the challenge is that many times it is restricted with, for example, dimensional constraints or space limitations or weight limitations.
And then from a manufacturing point of view; they typically have a large number of individual toolings and assembly phases. So with IMSE we can solve many of the problems for traditional electronics and mechanics, but we can also create totally new use cases and integrate electronics in places where traditional electronics and mechanics fail to do so. So, if we just briefly visit our process. We start by printing colored and conductive inks on flexible films, and continue by mounting surface mounted electronic components and continue by forming that film along with the components into a three-dimensional shape. And then finally, we injection mold all of that into a single piece assembly. So when we look at the benefits the IMSE part structure - if we compare it with traditional electronics and mechanics - we can save up to, I'd say, 90% of the assembly depth, save up to...
Wow!
-yeah that's a big number.
That's a big number yeah, and up to 80% of the part weight and at the same time, of course, we're enabling beautiful, seamless, smart surfaces and we can create - we talk a lot about point of views at TactoTek, and by that we mean, that IMSE enables intuitive user interfaces. So no longer do we have to have a complex HMI with all of the centralized functions, but we can create point of view functionalities. So for example, integrating capacitive touch enabled volume control on top of speaker modules.
So those are some of the - let's say challenges and benefits, that we've seen. And then when we look at the market, so obviously, this is a cross-industry technology, so there's - we see a lot of benefits from various industries. A very common application for IMSE is a human machine interface and we are currently working, for example, with the automotive segment; creating for example door trims and overhead control panels, appliances control panels, and we also work quite a lot with variables. So creating electronics in textiles...
Oh wow.
-yeah and that's actually...
I actually didn't know you were doing wearables, or that had escaped me in previous conversations, that's amazing!
Yes, yeah-yeah so the fact actually, that we are injection molding everything into a single part assembly, it also means that it's fully encapsulated, which means it's protected from debris and moisture. So yeah, so definitely when you think about electronics in fabrics our structures - we call wash and go, so they are very durable, and they can withstand like dozens of cycles and washing machines.
Wow.
Yeah, yeah. And then maybe a couple of words about the business model. So we are licensing our technology for IMSE design manufacturing and validation. Which means that our customers, they can both benefit from the possibilities that IMSE creates in product design, but they can also enhance the vertical integration in a way that they can perform functions, that were previously outsourced, and further extend their offering for customers.
That's unbelievable - and I can - - my mind is just spinning with the kind of enablers that I can see, that this is going to bring over time. So thank you for sharing all that. On a more practical level, Tuomas and you know, the people who are listening to this podcast are typically engineers and printed circuit board designers. Can you talk a little bit about the kind of practical effects on PCB designers and the implications they would have, from a design standpoint, in designing what you're calling smart structures?
Yes. So if we first compare traditional PCB design and IMSE design there are few main differences which come from materials that we are using in IMSE technology and also the 3D shape. So if we first consider those materials: the substrate of printed film circuitries are the difference. So in IMSE technology we have quite a large patene plastic film, and if they convert this for rigid PCP - there is a big difference.
Yeah.
Another thing is trace resistance. So when we are printing traces using silver inks there is always some resistance, so we can never think that this resistance is zero.
Right.
So we have to always consider this in our design. Of course it depends on the ink used but the typical resistance differs between printed silver ink trace and pcb solid copper trace - roughly 100 times bigger. So there is a huge difference in resistances as well.
Okay.
The third, which is really related to materials is dielectric. In PCBs there is no need to design, especially dielectrics, between two conductive traces but in IMSE design we need always to design a dielectric layer between two conductive layers and also, as I earlier mentioned, this 3D surface - I would like to highlight this as well - because it means that when the final shape of the product is somewhat kind of the correct 3D shape.
This means that the printed circuit would need to be designed a bit different than any PCBs.
So I'm gonna ask you more about those materials in a minute. But I was really impressed when I first saw it. I really thought it was a one- or two-sided only circuit structure and I'm really impressed to find out that no, it can be multi-layer and like you said Sini, completely encapsulated, so that opens up a lot of opportunities I think. So Sini, can you talk more specifically about the materials that are used for structural electronics? I know Tuomas just mentioned the silver inks, the dielectric materials, that you can do multi layers. Just the materials overall are really different, so can you talk a little bit about those please?
Mm-hmm - yeah and I would say the key essence of our technology is really the know-how and understanding, of not just the individual materials, but the four material stack ups. So we need to, first of all, we need to obviously understand how all the elements perform together like the films, the inks, the components and so forth, and it's...
As if it wasn't complicated enough; the traditional boards.
-yes! So it all has to work in synergy and it's of course, it's like one thing to understand how they perform when they are in 2D, but in our case we are then also bending and stretching everything into that three-dimensional shape. So that process as a whole, has a huge effect on the material characteristics and performance values. Like Tuomas mentioned before, for example, the conductive ink resistance changes over the manufacturing period so it's a big pile of materials research and chemistry as a whole that we have done to understand the behavior of different material stack ups. So we - of course we try to be on top of what works together and of course - what doesn't. So...
And so do you publish those, or will you be publishing those in the form of a datasheet, so when a PCB designer might move into this space that they'd have some guidelines?
Yes. So obviously, the material stacks are one element of our licensing content. So we are able to provide our customers with validated and functional material stacks that they can use to test our building products.
How long have you been at this? Because I know you work with materials and that, that is a long, arduous process. It takes a lot of discipline.
Mm-hmm - yeah so we've been around since 2011 and we've used a lot of time and effort for exactly materials research, and creating the validation processes. So now we're in 2018 and we are mass manufacturable so it takes time.
Yes it sure does, yeah when I've talked to friends that are chemists, it just takes a long time. So, back to you Tuomas, with all those different materials, and you mentioned also embedded components. So I would like our audience to learn more about the implications which you began to talk about - with the printed inks, the silver inks, and what not. But what are some other implications of those different materials? And what kind of components - because you're really talking about embedded components here I take it? So help us understand that a little bit more?
So like Sini said, understanding materials and materials tax, those are very important. So as I earlier said, this trace resistance for example, it is a big thing. Also another example is this flexible film which are speaking back to SMD process, for example. So typically we are using small SMD components like LEDs, resistors, diodes, transistors...
Traditional?
-traditional yes.
Oh okay.
Traditional off the shelf components.
But when we are selecting components on our IMSE products, the key element is the height of the component. So the component should fit inside the product, it's the first thing. The second thing is that when we are injection molding the product the melted plastic flows over the component - so the component should stand this injection molding and yes, the thinner the component the better.
Okay so - and I am certain that you have to take in consideration the thermal implications of what kind of thermal conditions those components can survive in?
Yes we have also considered this.
So for our listeners; I just want to let you know we're gonna connect all kinds of links and pictures because if you're like me you need some visuals to really understand - this is sort of hard to do - in the form of a podcast - it's a little difficult to talk about, but again I want to remind our listeners that we are recording simultaneously on YouTube and also we're not showing visuals here but we will put up a myriad of links and photos. Because if you're like me, you need pictures okay so.
Yeah actually we have a white paper regarding this.
Okay.
Will you share that with us Tuomas? Okay great.
Yes yes. Okay. It's just in our webpage so we can share the link of course.
Wonderful and the other thing that I wasn't clear about is: so you do the printed portion of the process and then you mold. It's not like you're creating it on a 3D surface right? Or does it go both ways?
We first print, this is 2D, then we place the component; assembly process, after that is forming process, the film takes its 3D shape, and after that comes injection molding.
This is actually the reason why we are doing this, is that we want to enable our customers to use just standard electronics manufacturing equipment. So when we are placing the components in 2D, it means that we don't have to have anything like 3D pick-and-place or anything like that - you can use standard PCB manufacturing equipment.
And then you mold. Which seems so counterintuitive? I don't know how you guys are doing it. I think you're magicians so...
You have to come and see it. I know - oh speaking of which also I'd like to let our listeners know that I'm delighted that Sini and TactoTek have agreed to come be a sponsor at AltiumLive they will have a booth there. They will have physical samples and you'll be able to see this and if you're like me , I think this all of a sudden aha moment happens when you can physically see - or like Tuomas said, read a white paper and you have some kind of visual representation of what's happening. And you will gasp. It's really incredible to watch so I invite you always to come to AltiumLive in San Diego or Munich and see them there.
So let's jump into how Altium and TactoTek had the good fortune to come together. Sini you started to talk about a challenge you guys had to face in that, there was a gap in the design tools to support your technology so, our team have been working with you for a while so can you tell us, sort of what that process has been like and, sort of how we've been working together?
Yeah, so I think for us, how we have worked so far is that, obviously we have a lot of design disciplines that contribute to the IMSE, structure not just electronics and mechanics, but also graphics design, antenna design, and illumination design. So all of those different design elements have to work in perfect synergy, because we don't have those separate structures but we only have that film and everything is on top of that one or two films. So the element that we have been missing so far in the design tools is the support of design for IMSE type of parts.
So we've been using Altium Designer for years for electronic design, but we've been sort of manipulating the tool which is meant for PCB design and we are using familiar functions for something else. So today we are not just using the tool anymore but we've been very, very happy to start really working with Altium and doing research on specific features and automation we could integrate in the tools in the future to enable more efficient design process for IMSE and printed electronics as a whole.
Which is so exciting to me. So if I understand you correctly, then we're really starting to develop design rules for a whole new technology?
Mm-hmm - exactly and in that way obviously shortening the learning curve for new technology and bringing it to the hands of the actual end users; the designers of the products.
Well I really love that you guys are using traditional mainstream tools like Altium Designer so designers, their ramp-up on the technology can be quicker and just using kind of some familiar things like a 2D manufacturing process so there's not this whole giant - there's not 20 obstacles in the way and such a learning curve, and such a huge investment, change of equipment - you've really been really thoughtful in integrating existing technology but then tweaking it.
Yeah, exactly.
Which is really exciting. Tuomas because you've been specifically on the hardware side; I look to you sort of as the voice of our audience. Can you talk about some specific examples in regards to things like stack up, DRC's. Can you give us some kind of down and dirty, you know, where the rubber meets the road sort of examples of how that's fleshing out?
Yes. So if I first start with the stack up; currently we are using PCB layer stack up in our designs, which is not it's not pure IMSE - and this stack up, this causes challenges and generates a lot of more work when we have transferred in design files between EGIT and for example in the simulator tool. So if we have a tool where we can define IMSE stack up as it is in real products, it makes the design process even faster. Second thing is the dielectrics. So at the moment we are designing and checking dielectrics manually.
It's time-consuming and there were still missing dielectrics in certain places and this caused failures during our production. This is very, very critical, so if the tool has, for example, dielectric generators, check the position for each dielectric and then place it according to user definitions, so it makes design even faster, and also makes the production more easier for us because there are no failures anymore.
Along those lines - from inside of the tool, will a designer actually have helps to help them choose a specific dielectric or is that something they'll need to know ahead of time? And then those dielectric constraints will be inside the tool - or do we know yet?
No we don't know yet.
Okay that's a good answer. That's okay. You know, I really see from my perspective in the industry, this tighter - and the lines between mechanical you know ECAD, MCAD, all the different design disciplines. the lines are just blurring - and I think that's never more true than with your technology. I think you made the lines disappear which is exciting and so enabling! Is there anything you wanted to say about that Sini, just about the different disciplines, or specific challenges that may come into play? Because you're bringing all of these things into play?
Yeah I think one very good example and Tuomas, I'm sure you are more familiar with them, is for example, a simple file transfer. So we need to be able to, first of all in IMSE, we have to be able to convert first a three-dimensional shape into a two-dimensional form. Then design electronics layout, then convert back to three-dimensional format, and during all of those processes, we need to have a file transfer mechanism that actually works in between the tools. So yah, like you said; the lines are blurring and we're excited to see how we can help in enabling this in the tools.
Well I'm very excited - before we wrap up is there anything I might have missed?
Thank you both for this interesting conversation, and I'll be sure to share your white paper and any links you like to share. Is there anything I may have missed, just because of my own ignorance - neglected to ask either of you about today?
I don't think so, not from my side. What do you think Tuomas?
No, not from my side as well.
Okay, well please be sure to share as many links as you can you guys, and again - I want to encourage our listeners to look - this is one set of show notes you're going to want to look into - and click through and see really where the future of technology is going. It's very exciting and as I say, we continue to develop our agenda. You know things like high-speed stack-up, things like that within Altium Designer 19, but in the future we hope to be able to offer the enabling technology in a future release of Altium Designer.
So thank you both for your partnership and working together. It's been a delight and I also invite you again to join us at AltiumLive either in San Diego or Europe. TactoTek will be in both locations and you'll be able to get your hands on it and see and touch this amazing technology it's really going to blow your mind.
So thank you Sini, thank you Tuomas, I really appreciate you - welcome to podcast land.
Thank you Judy, it's very exciting.
It's been a delight to have you and thank you - because I know you guys are - our hours between here and Finland are a little different. So thank you for accommodating our time frame today.
So thank you again for listening to the OnTrack Podcast, we appreciate you so very much. Join us again next time. Until then remember to always stay on track!
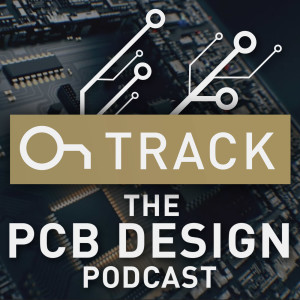
Wednesday Aug 22, 2018
Signal Integrity Expert Eric Bogatin on Best Measurement Practices
Wednesday Aug 22, 2018
Wednesday Aug 22, 2018
Signal integrity expert, Dr. Eric Bogatin, shares why best measurement practices have become his go-to topic when speaking with PCB designers around the world. As Signal Integrity Evangelist at Teledyne LeCroy, a leading provider of oscilloscopes, protocol analyzers and related test and measurement solutions, Eric lectures around the world and he will be one of the keynote presenters at AltiumLive 2018: PCB Design Summit. Listen to Eric and Judy talk about the importance of best measurement practices and where to learn more — from webinars to conferences to the Signal Integrity Journal and Rule Number 9. Eric also has some real insights, so tune in and learn more in this episode of the OnTrack Podcast.
Show Highlights:
- The OnTrack Podcast is in 84 countries! Congrats to Daud Zoss who was the closest guess at 37 countries. He gets a free pass to AltiumLive as Judy’s guest.
- Dr Eric Bogatin will be a keynote speaker at AltiumLive in October 2018
- Best measurement practices - how do you get the answer to the performance, root cause, characterization, etc. as quickly as possible?
- How do you know what the performance of your instrument is, so that you know its capabilities and what the device is doing compared to your measurement instrument? It’s important to know what the properties of your scope in the probe is, to know the properties of the device you’re testing.
- Measurement data: Such as the rise time, frequency or figure of merit must be excavated to give you useful information. How do you get the information so it’s high quality and can be trusted, how do you turn it into information that you can turn into action?
- Eric is also the Editor of Signal Integrity Journal, working with Janine Love and Patrick Hindle.
- Expert content - if anyone is interested in writing a technical article for Signal Integrity Magazine, please write: Eric or Judy.
- Janine Love manages the EDI CON coming up in Santa Clara in October (a couple weeks after AltiumLive). Part of this is EDI CON University offering tutorials by industry experts.
- Industry Experts on the Editorial Advisory Board: Bert Simonovich, Yuriy Shlepnev, Larry Smith and Steve Sandler, Rula Bakleh, Jay Diepenbrock, Vladimir Dmitriev-Zdorov, Alfred Neves, Istvan Novak, Doug Smith, and Lisa Ward.
- Rule #9 - Before you do a measurement or simulation, think about what you expect to see ahead of time, and if it’s not what you expect, there’s always a reason for it. You need to identify the reason why it’s not what you expect.
- Hands on learning is a necessity for students. Eric and Mike Horowitz put together a five-week, standalone crash course on how to design a board.
- Designing for connectivity is just about driving the board to enable finding the parts and laying them out for assembly. Really simple.
- The lack of experience with Oscilloscopes is surprising because nobody has ever taught these students the correct method.
- Hands on experience is giving students an edge in the marketplace. There isn’t enough of the ‘real world’ activity in most Universities.
Links and Resources:
AltiumLive 2018: Annual PCB Design Summit
If anyone is interested in writing a technical article, please write:
To see ALL show notes and watch the video recording please visit:
Hi everyone, this is Judy Warner with Altium's OnTrack Podcast. Thanks for joining again, if you would please connect with me on LinkedIn I like to share lots of information relative to PCB designers and engineers who are laying out boards and on Twitter I'm @AltiumJudy and Altium is on all the usual places; Facebook, LinkedIn and Twitter.
So please let us know what you'd like to hear about on the podcast and we will do our best to get it done. So today I have a rock star with us and he needs no introduction . But before we get going with Dr. Eric Bogatin; I wanted to say that a few weeks back I had put a challenge out there to see if you guys could guess how many countries the On Track podcast has reached; and we have a winner! So congratulations to Daud Zoss. He's a Senior Staff Engineer at Dexcom; he guessed 37 countries and he was the closest one, unfortunately it was only about half, because we've actually reached 84 countries, I kid you not! So anyways, thank you for listening and engaging with us and all across the world. We really appreciate it.
So today, as I mentioned, we have Dr. Eric Bogatin with us who needs no introduction; who is a signal integrity guru. You might know him from many conferences in North America and I suppose around the world Eric has has presented, and I'm lucky enough to be here in California, where I've seen him present many times on Be The Signal and now the Be The Signal and Eric Bogatin brand is flying under the Teledyne LeCroy flag. So he has lots of lectures and demos and things and I'll let him tell you more about that. So Eric, welcome, we are glad to have you.
Hey thanks Judy, I'm happy to be here with you today and tell you about all the things I've got going on.
Well, we're super excited to have you as a keynote at AltiumLive, so we really appreciate you coming out for that and we've done some neat things together with students, so we'll talk about more about that. So why don't you start off by telling us a little bit about your day job at Teledyne LeCroy?
Sure yes, so many of you may know, and I know you - - I knew you back when I had my own company it was Bogatin Enterprises, and I literally went around the world and did training classes. And about seven years ago, my training company was acquired by LeCroy and we continued the training classes and then began to make a slight transition to, most of what I've done over the years has been best design practices.
How to get the design right the first time and LeCroy is in the measurement business; we are the third largest manufacturer of oscilloscopes and some of the highest end oscilloscopes; and our CTO Dave Graef, he likes to say that that in designing, the goal is to get it right the first time, but if you don't get it right the first time then the goal is to get it right the second time; and the way you get it right the second time is, you have to find the root cause of the problem and invariably that involves some measurements. So that's kind of the connection with LeCroy, is we're number three in the scope world and have the highest end performance scopes out there.
We really specialize in the business of helping customers get it right the second time; kind of a faster time to insight. And so we started out when I joined them seven years ago, doing the same Best Design Practices presentations and classes I used to do, and then over the years since then, I've been working on this new area of Best Measurement Practices and so, with my day job at Teledyne LeCroy, I am still Signal Integrity Evangelist, but I spend more time now going around talking to folks about, and doing presentations on what are some of the best measurement practices. How do you kind of get the answer to either the performance, or the root cause, or the characterization, or get the Figure of Merit? How do you get that as quickly as possible?
And recently, in fact, I've got a couple of live events in the Bay Area coming up - actually next week - in last week in August, and then in Boston in September. And you can check the Teledyne LeCroy website for the events page to see where I'm coming next, but those presentations are really focused on, how do you - I call it kind of two aspects of in best measurement practice - one is situational awareness. How do you pay attention to - how do you know what the performance of your instrument is, so that you understand what its capabilities are, so what your device is doing, compared to your instruments. So you make sure that you are not seeing an artifact in the measurement.
Wow that's interesting.
Situational, because I find in talking a lot of folks about measurements; gosh there's a lot of confusion about what's the scope doing. And unfortunately there's no such thing as the ideal instrument; they're always - - or ideal probe, for that matter. There are always interactions of the probe and the scope with the device we're looking at, and it's important to understand what the properties of your scope in the probe are, to know how far away you are from the properties of the device you're testing so that you're getting good quality information about the device you care about and not an artifact of how you're doing the measurement. So that's the first piece of what we try to present and teach - those principles.
And the second piece is - and I see this with my students all the time - that they sometimes feel that just getting the data, just getting the measurement is enough. So they, push the right buttons and they get a screenshot and say: okay , here's my data. And I see a lot of engineers doing that as well, and the data is just the starting place. That's not - you're not done with the data - you need to take that data, the measurement and turn it into information. So you need to extract out, what's the few pieces of valuable information.
Like what's the rise time, or what's the frequency, or what's the jitter? It's a figure of merit that takes a lot of data and gives you one or two numbers that you can do something with. I was giving a talk at one of my events a couple weeks ago, and as I mentioned, that we have this huge amount of data in a scope. I mean, one acquisition can be we can take up to five Giga samples worth of data - but you know stupidly maybe - 10 - 20 mega samples but that's 10 or 20 million data points in one acquisition. It's a huge amount of data but you only want one or two numbers out of it. And so I used to call it data mining, and someone said: hey with all that data there it's not mining, it's excavating.
So it's kind of excavating the data for useful information, and then the third piece - once we have the information - is this: so what? It's how do you turn that information into action? How do you use the information you've got, to tell you is this good or bad? Should I, raise the line width or decrease the line width? What do I want to do with that information now? How am I going to use that to influence a decision? So it's those three steps that we talk about in our workshops; of how do you get the information, do you have high quality of confidence for the data, do you have high confidence in it? How do you turn that data into information, extract a couple of figures of merit, the nuggets of valuable information and how do you take that information and turn it into action?
So that's what I'm focusing on these days, the idea of best measurement practices. In addition to the stuff I've done forever, of best design practices. So that's kind of what I'm involved in now, spending a lot of time going around, doing live demonstrations, incorporating them in my workshops. Now we've got some really cool scopes and bring a lot of test vehicles and structures, so we can do live measurements of various signals. And so it's always a lot of fun when you can have...
A physical scope there, right.
-yeah a working device and the scope, and then people that come to these; you know I love working the crowd, and we talk about: well, if that's really what's going on, if you made the the rise time shorter, what what will you see? Or if I expanded the time base, what's the signal going to look like? And so we can do that as a live experiment in the group. So they're a lot of fun, very interactive activities. So that's that's what I do is my day job now.
Well, that's a lot, and it sounds - you make it sound really fun and engaging. So also, Teledyne LeCroy will have a table at AltiumLive, I hope we can talk you guys into bringing an oscilloscope so we'll let you work our crowd and I'm sure.
You know, another thing - oh by the way - I would encourage people that are listening to connect with Eric on LinkedIn, or connect with me I've been sharing those classes that Eric is teaching, so you'll be able to pick those up and see the different locations that he's teaching those courses. And we will also add those links below here in the show notes.
So if you're in those areas you can hop into one of Eric's classes, and he's super fun too it's a very plain spoken - and like I, can learn things from Eric Bogatin, and I am not, my technical prowess is limited, so I really appreciate that about Eric. The other thing you do, we have some friends in common which are Horizon House, the publishers of Microwave Journal, have published a new magazine called the SI Journal, which I am very excited about and you are also the editor of SI Journal, and we have friend in common Janine Love and Pat Hindle and the whole group. I used to write a blog for Microwave Journal that is put out by the same publishers on their website, talking about making RF boards and all the fun that goes along with that. And so now, Eric is editor of SI Journal, so you can also subscribe to that online. We will also share that link. So how's that been so far? Tell us about your job - how long has it been now? It hasn't been too terribly long?
You know what, I think it was about - - it's almost 2 years now, so I'm just going to...
Wow! I was gonna say a year and it's like two years. Wow.
So I think it was it'd be - - between Pat and Janine they kind of came up - they've been focusing on the Microwave Journal which has been around for 30-some years and this is one of the - I think it's the top...
I think it's like 60 years or something.
Is it 60 years?
I don't know I might be...
It's a long time - it's been around forever.
And it's been a real icon in the industry for good quality articles about microwave technology and with Janine's experience with the Design Con and in the signal integrity world; I think between she and Pat they realized: hey, the industry could really use another kind of curated source of high value information and so many of the magazines that we're used to getting have - - the print magazines have disappeared and they're all online, and so Pat and Janine decided to create this as an online journal initially. And they asked me to come on board as the editor; really the technical editor right at the beginning - about two years ago -
and so since then we've been kind of planning it out, putting together the editorial review board - of really some industry heavyweights and kind of creating a lot of new content, soliciting content from other experts in the industry, in fact, while I have a captive audience here, if anybody out there listening, is interested in writing technical articles for us, that'd be great.
Drop me an email or send it through Judy, and I'd be happy to take a look at what you like to do. We created this and our focus is to provide high value content that's curated. That there's so much information out there online right now. If you do a google search on Signal Integrity or Power Integrity it's not that you don't find anything, you find like 10 gazillion different sources.
You get flooded.
Yeah it's hard to know what's the good stuff and what the stuff is that I should waste my time with and so I think that's really the value of having an online publication or portal that is curated, and that's what we try to do is between myself and Janine and Pat and the editorial advisory board; we try to curate the content so that it's in our opinion what we would consider to be high-value content. And so we don't want to waste people's time or our own time and so there's, we think, a lot of really good valuable content. We've done the traditional stuff of short columns, of feature-length articles. Janine manages the annual conference EDI CON, which is now coming to the Santa Clara area in October. I think it's a couple weeks after AltiumLive.
Yah, it is, it's really close.
And part of that is now I think Janine's calling it the EDI CON University which is going to be tutorials by industry experts that are available for all the attendees. And then she also manages webinars, and if I can just plug a previous webinar. So we had Rick Hartley do a webinar...
Which we love and you know as I mentioned you and Rick are just so well respected and the SI field so I'm glad you snatched him up.
Yes we got him to do one a couple months ago and then that's recorded and posted on the...
Oh great!
-and then I did one a couple weeks ago that's also up there. So we have maybe it's 20 or 30 different webinars and they're all free and all available for anybody if you go to the SI Journal.com website, and you can look under videos and webinars, anybody can access all the content on the SI Journal is free as well.
So, there's some other people that are dear friends Bert Simonovich I know is on your team on the magazine who - - I think is Yuriy on that team as well?
Yeah Yuriy's been involved Istvan Novak has been on the Editorial Advisory Board. We just brought on Steve Sandler - - let's see; Larry Smith who is, he's my buddy, we worked on a book together that came out last year on Power Integrity and he now is at Micron; used to be at Qualcomm, he's maybe the one or two world expert on power integrity. So I learned a lot working with Larry. Let's see - - so yeah those are them.
They're all heavy hitters I mean, all really, they are the industry experts you really have, kudos to Horizon House for putting together such a crack team with you at the helm, which is just incredible, and like you said curating that content. Because there's so much noise out there. How do we bring the noise down and just cherry-pick, the best pieces? And I was kind of around before and as they were launching EDI CON and I was really glad to see them, as the high-speed digital and the RF world kind of moved together and some of the challenges were kind of overlapping to launch a show like EDI CON I think is really exciting and this magazine so, yay! Very excited about that so I can't... and again we'll put all these links below.
I'll even I'll see if I'll go pluck out some of those webinars and put those links in too if you didn't send those to me already.
So while I'm plugging webinars can I plug one other webinar too-
Yeah,
-that I should have mentioned. So I've been spending a lot of time, too much time, traveling doing these live events but also doing webinars; I mentioned the one with SI Journal. I've also been doing some through LeCroy, and we have a whole landing page on what LeCroy has done.
Yeah there's a lot there.
There's a lot of high value content that's all free. Anybody can view them and I'm hoping you'll put up a link to the webinar page from from LeCroy as well.
Okay.
I've put a series together on, a little bit about fundamentals of measurements, part of this best measurement practices series that I mentioned earlier they're one-hour webinars on various scope measurement principles and I'm doing them on a regular basis. I think we have two or three more scheduled for the rest of this year and then we'll have another series starting up in January.
Exciting, I like the idea of this best measurement practices, it's like really practical.
Yeah and it's the same thing with design practice. There are accepted practices that you want to follow unless you have a strong, compelling reason. Otherwise these are the right ways of doing things.
Right.
And same thing with measurement; there are just as many ways of screwing up a measurement as there is a design and so you've got to pay attention to both of them.
And there's a human in the loop too besides your probe and all that, so.
Oh absolutely.
So if the human isn't 'tuned up' -
Yeah
- now so one of the principles that I teach my graduate students and at University and also engineers I talk to, is I call it rule number nine and... have I talked to you about rule nine? Okay I'm definitely gonna be mentioning it at the at my keynote because I think it's one of the most important rules for any engineer and basically it says: before you do a measurement or simulation, you want to first anticipate. Think about what you expect to see and I have found that to be the most valuable kind of habit to get into, because just like you said, when there's a human involved it's easy to make a mistake. And how do you know that you don't have the connector connected where it should be, or how do you know: I think I'm looking on channel two, but I'm really going on channel three? Or I typed in 17 but I meant 71? How do you know?
You can check yourself but there's a limit to, how well you can check yourself and so, if you think about what you expect to see ahead of time, whether measurement or simulation and you look at the result and it's not what you expect, there's always a reason for it and you shouldn't proceed with that information until you've identified how come it's not what I expect. And when I do these live demos in front of groups, I'm constantly making mistakes because you know, it's under pressure. I get a screw in that connector and I'm not sure which demo am I on right now, and so I'm always looking at the screen to see, is it what I expect to see, and I can tell instantly when I've done something wrong because I use rule number nine. And I sometimes play a game with the audience, the engineers there, and say: okay, we expect to see this waveform go up and then down and it's flat - how come?
And it's good experience, good practice, that thinking of what could go wrong in the debugging process because that's what we all end up doing and the more experienced we can become at finding the root cause and why it's not what we expect I think, the quicker we can get to a good answer and move on to the next problem. So it's an incredibly powerful habit that I use all the time and I try to teach all my students.
This is what I love about your classes and things you teach Eric. I've sat in a few of them over the years is, that they're insanely practical and intuitive and memorable. Like rule number nine, I can remember that right, so I really have to say that about you.
Of course, don't forget I also reinforce good behavior with chocolate so that...
Oh yeah he does! He throws chocolate out at his classes so yeah it's like Pavlov's dog, yeah it's so true. Well I wanted to jump into the way that you and I started working together, is I think a month or two ago Iconnect007 came out with a magazine with an empty pair of shoes walking down the street, and it said, who's gonna fill your shoes? And everybody seems to get on this bandwagon about all the people that really, fundamentally understand PCB design in regards to, not just designing but manufacturing, assembly, the whole, all the stakeholders that are kind of implied in that process are greying and gonna retire, and so you know, there's been studies out by UP Media saying - by a pretty large sample - saying that in under 10 years half of PCB designers are going to be gone and so everyone has sort of gotten to this hysteria about it seems like the unanswerable question.
What I appreciate that you've done is I'm going to call you professor now - he wears lots of hats - professor Bogatin called me up and said, Judy, you know, I'm gonna do this program, he's used different tools right now that this - I think the students were sort of driving, or somebody was driving one at Altium Designer, so you kicked off this amazing semester-long course at the University of Colorado Boulder and you - I think co-teach that right Eric?
Yeah so I can give you the quick history.
Okay let's hear it.
So I've been teaching a graduate signal integrity class at CU Boulder for a number of years, based on my textbook and in talking to folks there, we realized that our students - so CU Boulder tends to be very project oriented very hands-on we believe in that, you know you learn from textbooks, you learn from studying, but you understand by doing. And it's the hands-on part that you really - everything comes together. And there were a number of classes that required building circuit boards and I would get called in as a consultant to help them in designing the circuit boards and there's relatively simple boards, two layer boards. But these kids had absolutely no idea. They could push the buttons on the tool, but they had absolutely no idea how the performance was influenced by it by what they do in the layout. And so it became really clear that, boy it sure would help if they had a little bit of guidance in how to design boards correctly. And so a number of us got together and realized: hey, we need this more formal training and a buddy of mine Mike Horowitz, who is an expert at design of circuit boards, we got together and put this course together which was - and it's kind of a funny organization too - we're also trying another experiment.
At CU you are semester based, and some courses are typically like 15 weeks or so. But we are experimenting with creating short five-week modules so it'll be the full regular course, that is a normal schedule of of 3 hours per week but it only lasts for five weeks. And so, Mike and I were tasked with putting a course on Printed Circuit Board Design and Manufacture together, that would have a five week beginning piece that could be a standalone so that most students, undergraduates, would take that and that'd be enough to get them going on their projects and then everybody else would continue for the rest of the ten weeks. And that would go into more detail so it gets them more experienced at circuit board design. And so that's how it got started, and Mike and I worked on it - it's every semester; so we did it twice last year and now. So that was kind of our joint development. And now Mike has gotten more involved in his CEO activities and so I'm gonna solo it this semester.
Oh okay.
So the format is basically a five-week crash course on how to design a board so you have a good chance of success when you build a two layer board. And then the other five weeks are more the same, more the technical detail about measurement technique - this idea the best measurement practices. How do you bring up a board? How do you design a board for simple tests and bring up? And then we'll do four layer boards, and then a little bit on the more high-performance systems. So it's a little bit more advanced and really you know, the way we've positioned it as: there are two levels of design. The first is if you can build a prototype and build it with a solderless breadboard and have wires going all over the place; if that works then designing the circuit board and having it work is really straightforward.
We call it designing just for connectivity you don't have to worry about performance, it's about, you want to be able to manufacture it, but performance isn't on; the interconnects don't matter, and and some of the student designs are just designed for connectivity. It's just about driving the board so you can find the parts of the library and build it in the schematic and then place them on the board and lay them out, so you can assemble it by hand - pretty straightforward.
But many of our student designs these days, are getting more sophisticated. They use a Wi-Fi connection, so you have RF on the board, they have sensitive analog to digital converters on the boards, they have components that sometimes -even BGA components - where the microcontrollers are using a really fine pitch; hard to design by hand, and some of these have a couple nanosecond edges where ground bounce is a tremendous problem. And so we're focusing our class on how to design a board. Not just for connectivity - that's the easy part - but for performance, so that you can designed so it's manufacturable, it's lower-cost reduce the - so much of it is risk management - and then kind of the basic performance issues to worry about.
And in my keynote, I'm thinking that I will probably present on what we have found to be the two most impactful design issues in designing a board, not for connectivity but for performance. If all you think about is connectivity you're gonna run into two significant problems. And so one of the topics is this idea of rethinking how signals propagate on interconnects and I've done this at PCB West and I did it at some of my other courses - and I had a couple people come up to me afterwards and tell me that it was a life-changing moment for them. Because I completely changed the way they've been working on boards for 20 years, and I completely changed how they thought about signals on boards. So I hope it will have a similar impact at AltiumLive, but it's going to be about how to rethink and how to train your intuition to think about how signals really propagate on interconnects.
I loved your Be the Signal....
so... and I'm sure this is a little bit more complex than what you're gonna present, but I remember the first time I ever sat in a course by Eric Bogatin, and he was talking about 'be the signal' and he's like: if this signal's moving from A to B what do you think is gonna happen to la-la-la... and I'm sitting there as a non-designer and he's like: no, be the signal. What would you do? And kind of helped us to frame, kind of this visual - and I'm a visual person - so I like to kind of visualize, what the things that were going on, in that signal path to create whatever it was. So I really loved that.
And that's basically what I'm going to be talking about, that Zen approach to thinking about signals propagating and and how to apply you know - I'll probably mention it once, in my talk, about how to apply master's equations but in an intuitive way, to understand what's really going on in the interconnect.
So Eric's talk is called 'Living in the White Space' and that will be relative to signal propagation and I'm sure all of us, our brain will explode a little. I have these moments with Rick Hartley from time to time too where he says something and I'm like: nah! You know it could be that simple or whatever and I'm sure, you know Rick Hartley is a student of Eric Bogatin so, I'm sure it's more of the same.
So, well I really appreciate you Eric, taking on these students at university level. Here at Altium absolutely, I think I would do this part of my job for free; is to help students get equipped with not only tools - like I can give them free tools - but that's a really incomplete model, for them to learn. They're learning about electrical theory in school but really how to design a board, and how does - - I just finished a podcast today with Julie Ellis who's a Field Applications Engineer from TTM - what about stack-up? What about all these variables and how they come into play, that are not taught at university? But I love that you've brought them in at a university level because I think these are the kids - I think these are exactly who's going to fill some of those shoes, and they may be EEs laying out boards, they may end up like Rick Hartley did saying, I like just designing boards better than circuit design. Who knows? We don't know.
What has been some of your surprises by the way? What feedback from students?
So I think two things absolutely surprise me; one is, their lack of experience with oscilloscopes. That their way of using oscilloscope is first to push the autoscale button. And I slap their wrist if I catch them doing that, or pushing every button without knowing what it is until they see something, on the screen...
Until the light goes on, they're looking for the LED.
-and and so they, just the basic understanding of what an oscilloscope does and how to control the vertical/ horizontal and the trigger. You know the very basic things. A lot of these kids; nobody's ever sat them down and talked to them about it, so we focus on good - again - best measurement practices in the class as well as the design. The second thing is, there is a disconnect between what you learn in the textbook and what you see in the real world and it's the same thing, but you have to know how to apply what you learn in the textbook. And I don't think any university does enough of that hands-on, real-world activity. We try to do it a lot at CU, we have a lot of projects that students get involved in. Most of them are really about designing a little robot or designing some gadget that does something with the code that you write in there. So a lot of it is - some software, as well as the hardware.
But in our class we try to close the loop of the; here I do an estimate or calculation, and here I do a measurement. Like one of the first labs we do is blowing up traces.
That's fun! It is. Everybody likes blowing up something.
Everybody likes to blow shit up
[laughter].
And so the question, the first question I ask them is: okay, you're gonna lay out a board and you're gonna put some tracer - what line width should you use? You can select it to be anything you want.What line width should you use?
And so one of the things that surprised me is, when I asked the students is, they thought that a six mm wide line, just the narrowest that most fab shops will do. A six mm wide line, was too narrow because it's way too much resistance, or I can't put more than a couple milliamps of current through it. So I gotta use a twenty mm wide line, or fifty mm wide line. And it's the kind of thing that, the very first day in class, we calculate or we look at how do you calculate the resistance of a trace? How do you calculate what the maximum current handling it, using the IPC guidelines that Doug Brooks has been so heavily involved in.
And when you put in the numbers you realize: oh my gosh, it looks really narrow on this board it's only six mm wide but but gosh; it's resistance is going to be still in the tens hundreds of milli ohms for typical lengths. So it really isn't that high a resistance even though it looks really narrow because copper is an incredibly good conductor.
Exactly.
People don't have good calibration of that. And then, so I'll give you the number, and I hope none of my students are listening to this because they're gonna figure it out in class. But if you look in the IPC specs for maximum current handling for a six mm wide surface trace; it's like two amps or three amps and when we put two amps through, we have a test board with the different line widths on them. When you put six amp - - two amps through it, you find we can monitor the voltage across it with constant current and see the voltage increasing because it gets hotter, as you see the beginning of the runway, and RNDF around three amps, IPC's around two amps, around three amps, darned if it doesn't go to thermal runaway and we zap the trace and so, you can really get a good estimate by putting in the numbers ahead of time, of how some of these interconnects are going to behave.
But it's that habit of putting in the numbers doing simple estimates, applying what we learn in class to the real world, that the students don't have that good experience with and that's what we try to do in our class at CU.
Well to your point of hands-on, I feel like that's something that for whatever reason has left our education system too much right there's no shop at school anymore, there's no metal, there's no like just - and it's not just, what they would consider low labor skills or whatever. It's just hands-on learning the kinesthetics of it because I bet you dollars to doughnuts that kid, is gonna remember blowing up a three amp trace, more than if he read something about it in a book right?
Right, and sees the smoke and it pops and, there's this feedback well, what I was telling you about is, again one of my favorite parts of my job is, we just came back about three weeks ago from filming these kids that are doing the Hyperloop Competition -
Oh I'm gonna send you this video Eric - you're gonna die because what they do is so awesome and it's just because they get to do hands-on and they make a good - - there's no way they're not making, more mistakes per minute than everybody else in their field, but because of that and because the lack of constraints they have on them as far as businesses and law and whatever, you know this one team we sponsor is from Munich Germany, they just broke the world speed record inside the tube that Elon built at 290 miles per hour.
Crushing!
There's commercial companies with venture capitalists that haven't hit that number. Because they're young and they're hungry and they're hands-on, and they're excited. But these are the kids who I think, there needs to be much more of what you're doing. I wish every University would, hopefully you'll set an example that others will follow. And by the way, I've cited your course to a group of six universities I was invited to speak at UCSD, UC Davis was there, five other universities and I put a screenshot of your course -
Oh that's great
-and so I, so if you start getting weird phone calls...
(laughter]
-because I'm like see what he's doing - you all need to do this you know, so hopefully the word will spread but until that happens things like the Hyperloop competition, the FSEA competition, where kids get to get their hands on it and blow stuff up and do it wrong, until they do it right, and learn how to use an oscilloscope in this really hands-on manner well these kids are coming out of college and the internships of these kids, one of these kids from University Wisconsin in the Hyperloop team he's a Qualcomm right now, the team lead is going to SpaceX on internship - companies are plucking them out because of the hands-on. So I think the more we sort of beat this drum and spread this message, I again, something I'm very passionate about - I know you are too - and thank you so much for doing that course and we cannot wait to hear from you and about Living in the White Space at AltiumLive.
Thank you so much for taking time out of your busy schedule.
Well I look forward to seeing you at AltiumLive and all the other viewers that you have and I hope folks come up in and say hi while I'm over there.
Okay will do, and make sure - well not make sure - see if we can get LeCroy and company to bring out an oscilloscope so you can - -
We will definitely have one at our table.
Okay good, good I think that would be something notable and something that people, the attendees would enjoy so thank you again Eric this has been...
Thank you Judy.
Thank you again, this has been Judy Warner with Altium's OnTrack podcast and Dr. Eric Bogatin of Teledyne LeCroy. We look forward to being with you next time. Until then, remember to always stay on track.