Episodes
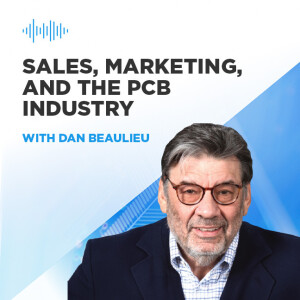
Thursday Oct 12, 2023
Sales, Marketing, and the PCB Industry
Thursday Oct 12, 2023
Thursday Oct 12, 2023
Today we are joined by Dan Beaulieu, founder and owner of Db Management Group. He and Zach chat about the PCB industry's broad marketing trends including how it's stuck in the past, the declining trade show industry, how sales reps can stay relevant, and much more.
- 0:00 Intro to Dan Beaulieu
- 5:48 Sales & Marketing Stuck in the Past
- 9:14 Impacts of the Domestic PCB Base
- 12:59 Is the Trade Show Method Going Away?
- 16:45 How do Reps Stay Relevant?
- 19:27 Focusing on Younger Designers
- 24:30 How Manufacturers Stand Out from the Competition
- 28:42 Designers and Board Shop Conflicts
- 31:42 Importance of Touring Shops
- 33:36 Capital Investment and PCB Shops
- 38:51 Focus on the Customer's Need, Then Provide It
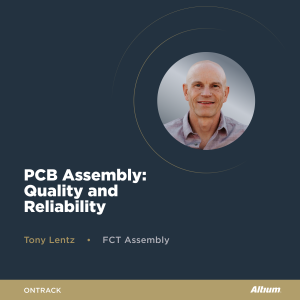
Tuesday Apr 18, 2023
Solder Formula for High Quality and Reliability PCB
Tuesday Apr 18, 2023
Tuesday Apr 18, 2023
Quality and reliability are a big deal when designing PCB for assembly. Our guest Tony Lentz, Chemist and Field Applications Engineer at FCT Solder will bring us to the PCB manufacturing space while tackling solder beyond basic thermodynamics and composition.
Listen or watch through the end. This is a great opportunity for PCB designers to learn about soldering products that are used for printed circuit board assembly.
Episode Highlights:
-
Introduction to Tony Lentz, his background, and role as a Chemist and Field Applications Engineer at FCT Solder
-
Tony talks about how they work with their clients to achieve best quality when manufacturing their PCBs
-
Diving into the chemistry side of things, Tony tackles about how the blending of different metal alloys, additives, and different inter-metallics to that solder joint composition, the pads, and the components can affect the overall reliability of the PCB
-
With the automotive industry’s growing electronic demands, thermal testing cycles are expanding aggressively. Recently between negative 40C to 175 C!
-
Tony briefly explains the different worlds involving PCB manufacturing and assembly: solder company, plating company, components manufacturing, board manufacturing, assembly and the list goes on
-
What is tombstoning?
-
Head on pillow on a BGA is another difficult defect to get rid of, Tony explains what can cause this problem
-
Expert Tip: A rule of thumb for large thermal pads is to cut it down somewhere between 60 and 80% of the total area covered with solder paste and then break that deposit up with some window pane type openings going through it
-
Are hybrid solder reliable?
-
The stability of solder alloys can differ based on the different kinds of metals, components and PCB surface finish

Wednesday Jun 15, 2022
Occam Process: Assembly without Solder
Wednesday Jun 15, 2022
Wednesday Jun 15, 2022
Have you heard of assembly without solder? In this episode, Joseph (Joe) Fjelstad, founder and president of Verdant Electronics, talks about the Occam process.
Let’s hear about Joe’s 50 years of experience in the electronics industry and how he got started with solderless assembly for electronics.
Altium 365: Where the World Designs Electronics
Show Highlights:
- Joe talks about his background and previous roles in the industry, including his position as the educational director in the IPC and Kurchatov Institute of Atomic Research in the Soviet Union
- “Assembly without solder” Joe recollects how he arrived at the idea of a better way to build electronics – build a component board and put circuits on it.
- Joe shares how he came up with the Occam process and its benefits “It absolutely doesn't need to be for everything, but it can be for a lot of things, and it can make products that will be at once cheaper, better performing, lighter, more environmentally friendly.”
- Download Joe’s book for free: Solderless Assembly for Electronics: The SAFE Approach
- More about the Occam Process
- Did Joe coin “Design with Manufacturing”? He shares his efforts in promoting solid work relationships between PCB designers and manufacturer
- Occam Process vs. 3D printing, could 3D printing bypass solderless assembly? Read Joe’s article Putting 3D interconnection technologies into perspective from chip to system
- Joe commended the microvia technology, “they know how to build these things”
Links and Resources:
Connect with Joseph Fjelstad on LinkedIn
Visit Verdant Electronics website
Read Joe Fjelstad Interview: Breaks Down His Occam Process
Download Joe’s book for free: Solderless Assembly for Electronics: The SAFE Approach
Connect with Zach on LinkedIn
Full OnTrack Podcast Library
Altium Website
Download your Altium Designer Free Trial
Learn More about Altium Nexus
Altium 365: Where the World Designs Electronics
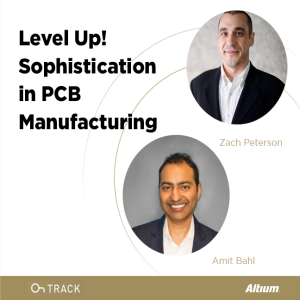
Wednesday Feb 09, 2022
Eliminating Nuances in the PCB Manufacturing Process
Wednesday Feb 09, 2022
Wednesday Feb 09, 2022
Welcome to the very first podcast of the year! Altium has been very serious about designing WITH manufacturing, and so our guest for today is Amit Bahl, the director of sales and marketing at Sierra Circuits. We will talk about his passion about promoting the level of sophistication in the PCB manufacturing floor. Watch or listen on the go, this will be fun!
Altium 365: Where the World Designs Electronics
Show Highlights:
- Amit first exposure in the PCB industry
- He grew up around printed circuit board (PCB)
- First to install a DFM tool called Valor
- First to install a LDI machine or a laser direct imaging machine
- PCB is the backbone of electronics
- The PCB designer must see a pcb factory. Sierra offers a virtual tour of the PCB factory.
- The PCB manufacturing level of sophistication, and high standards are driven by customers
- PCB designers must push the envelope and to be more courageous with their design, while understanding the maximum capability of their manufacturers to receive better products
- Equipment vendors need more motivation to make improvements
- Sierra Circuits offers PCB Fabrication, Assembly, & Components
- Connecting the dots in technological and logistical standpoint
- Semi-automated Customer portal - a real time feedback to customer on how to improve their designs
- DFA and DFM starts when complete data is on hand
- The most common feedback or mistakes in the PCB manufacturing floor
- Aspect ratio of plating a via - what is the fabricator’s capability?
- Drilling copper - where do you drill? Optimizing the drill to the material movement.
- A good fabricator will know the best material to use
- Getting the available stackup early on - knowledge base of the standard materials on stocks
- Manufacturing tools and resources for designers
- 99% success rate - eliminating nuances
- Impedance tool
- PCB Manufacturing Pro tip: Talk to your fabricator and understand the details - take the time!
- Sierra Circuit’s new website and good knowledge base
- AltiumLive Connect was successful! If you miss it, you can still sign-up to virtually attend the AltiumLive EMEA here
Links and Resources:
Connect with Amit Bahl on Linkedin
Visit Sierra Circuits Website here
Experience Sierra Circuits Virtual Factory Tour
Register to Join AltiumLive Connect EMEA
ALTIMADE Design to Manufacture, Made Easy | Request Access Now
Full OnTrack Podcast Library
Altium Website
Download your Altium Designer Free Trial
Learn More about Altium Nexus
Altium 365: Where the World Designs Electronics
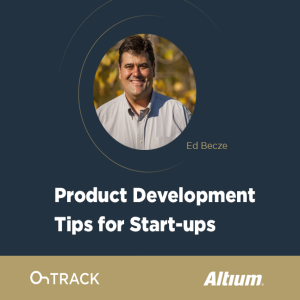
Tuesday Jul 27, 2021
Key Factors of Thoughtful Design
Tuesday Jul 27, 2021
Tuesday Jul 27, 2021
“Engage your suppliers early on the design process” - Ed Becze
Everyone wants a lower price, and often the “real cost” is not realized until it’s too late. In this episode, Ed Becze of Pegmatis, a highly experienced R&D company with end-to-end product development capabilities, joins us to help start-ups and design engineers like you avoid electronic product development failures.
Altium 365: Where the World Designs Electronics
Watch the video, click here.
Show Highlights:
- Introduction and the interesting origin of Pegmatis’s company name
- Ed explains the foundation of a good product development process
- A thoughtful development plan mitigates risk early on—engage vendors and suppliers early on the design process (understand parts, availability, vendor capabilities aligned with your product)
- Holistic understanding of electronic product development: strategy, cost, and your design team’s experience level
- Start-up challenges, how to prevent failures:
- Understanding the risk of “development by demo”
- Address the lack of system-level design experience (use external expertise if needed)
- Don’t trust the data sheets—only 5% of chipset providers give adequate design rules to follow. The rest, you are on your own.
- Manufacturing test is absolutely critical—test equipment and test development are often overlooked
- Engage early on the design process. Ed stresses the benefits of nurturing your relationships with your vendors and manufacturers.
- Successful product development relies exclusively on your network—find capable vendors
- Supply chain intelligence, plan ahead when coping with supply challenges
- Cost reduction—do it, but follow the process that is within the constraints of what you intended to create.
- What are the costs of NOT thoughtfully designing? It’s huge! Money and time. Delays inTime to market are extremely expensive.
Links and Resources:
Pegmatis Website
Ed Becze on LinkedIn
Full OnTrack Podcast Library
Altium Website
Download your Altium Designer Free Trial
Altium 365: Where the World Designs Electronics

Wednesday Jul 29, 2020
Insertion Loss is a Complex Issue: John Coonrod is Here to Explain It
Wednesday Jul 29, 2020
Wednesday Jul 29, 2020
Altium 365 Podcast Listener Discount
The OnTrack Podcast welcomes John Coonrod back to the show. John is Technical Marketing Manager at Rogers Corporation and a senior engineering professional with a rich background in PCB design, fabrication, processing, and modeling. John also has extensive experience with circuit materials, making him the ideal candidate for the topic of today’s podcast: insertion loss.
Show Highlights
- 01:45—Clarifying terms: a quick overview of Microstrips vs Striplines
- 02:20—Exploring laminates, multilayered circuits, and plated through-holes
- 06:42—Applying electromagnetic fields: a prerequisite for understanding insertion loss
- 09:25—The four components of insertion loss
- 13:10—RO4350B™; a friend to all fabricators?
- 15:10—Pros and Cons of electroless nickel immersion gold (ENIG)
- 18:13—John’s advice to design engineers on modeling for ENIG’s performance range
- 21:33—Navigating the relationship between solder masks and insertion loss
- 24:20—A call to viewers and listeners: Got a copper-related topic you’d like to hear John and Judy discuss? Submit your requests!
Resources:
John Coonrod on Linkedin
Rogers Corporation Website (Advanced Connectivity Solutions)
(Includes Coonrod’s corner videos, data sheets, calculators and more)
Autonomous driving Resource Page (Guides, Videos and Material selection)
ROG Mobile App (Resources accessible from your smartphone or tablet)
White Paper High Performance PCBs: Judy Warner, Chris Savalia, Michael Ingham
Altium 365 Podcast Listener Discount
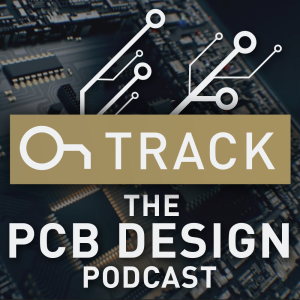
Wednesday Aug 08, 2018
Design for Manufacturability (DFM) and Assembly (DFA) tips with Jay Colognori
Wednesday Aug 08, 2018
Wednesday Aug 08, 2018
Get Design for Manufacturability (DFM) tips from Jay Colognori, Director of Business Development at Electronic Instrumentation & Technology (EIT). DFM and Design for Assembly (DFA) are important to engineers who know you can’t just design a PCB and throw it over the wall to manufacturing. Early and proactive optimization of all the manufacturing functions from fabrication to assembly of the final system is key. Listen to Jay and Judy discuss high-yield designs, EIT’s value-added engineering services and the latest state-of-the-art inspection technology and test capability.
Show Highlights:
- Jay was educated at Virginia Tech where he attained an EE Degree, followed by a Master's in Electrical Engineering at the University of Virginia.
- He spent most of his career in the mid-atlantic and his career spans from board level electronic design to applications engineering doing custom microelectronics for a couple of years, eventually ending up in PCB Design first at TTM and now at EIT.
- EIT has been in existence for 42 years, and specialize in electronic manufacturing services, turnkey builds, box builds, and demand fulfillment and consider their Engineering value add as part of their DNA.
- EIT has three facilities on the East Coast, consisting of over 200,000 sq ft. They have a facility in Danville Virginia, headquarters in Leesburg and another in Salem, New Hampshire. Altogether they have eight surface mount lines.
- The Danville facility is designated as the low-cost center of excellence and is also a 100% vertically integrated location - it is built for box builds.
- Leesburg and Salem are high-tech facilities with the latest state-of-the-art universal equipment, as well as the latest and greatest inspection technology and a full suite of test capability - with a lot going on and a story that needs to get out - it’s almost been a secret!
- New EIT website
- DFM: Bare board tips
- 2 objectives - 1) to design so that it can be fabricated reliably and with high yields, and 2) so that it can be assembled
- VM Pad requires a wrap plating process to provide a reliable button around the via.
- This process requires more copper which can wreak havoc with fine line design, so be sure to plan upfront and move those fine line geometries to the inner layers.
- Overlapping via structures can’t be made. They need to be stacked and sequential, not overlapping.
- Sit down with your PCB Fabricator at the time of stackup development, before you even start that router and make sure everyone’s happy with the stackup.
- FR4 has too high a Dk for high speed designs today and new materials such as teflon or ceramic-filled laminates are becoming more common.
- If you work with a new material, consult with your PCB fabricator to see how the rules have changed with that new material for the speed you desire.
- DFA Wisdom:
- Common Pads - so close together that they touch, rather than routing a thin signal from pad to pad is a common problem. We don’t want them to physically share the same space which will cause loss of control over the solder flow.
- Keep the pads apart and just run a small solder trace between them.
- The via in the pad has to be filled, it must be plated over and planarized.
- Sometimes the planarization isn’t done properly and even a little dimple, with a BGA on top, will cause the gas trapped beneath the solder paste, to expand ferociously and blow all the solder out of the pad at reflow.
- Always use non-conductive filler it’s much less expensive.
- The benefit of using conductive fill from a thermal point is negligible and is too expensive for the return.
- Thermal conductivity is defined in Wattmeters - if you use a conductive fill, you only get 6 more wattmeters which is rather pointless because the copper is already doing all the work.
- When a thermal via is located in a big plane, with a copper button around it - the button will be in contact with the plane and this is a big no-no. It compromises the solder flow again.
- Do a sprocket arrangement around that thermal via button. This will create a gap between the button and plane and sprockets simply act as traces surrounding it - very good design practice, frequently missed. Especially on backplanes with active components, this will require retooling to enable manufacturability.
- Why has design migrated as a service inside many EMS companies? What is the value to the customer?
- It’s a benefit to both the customer and the EMS. We want to do more for the customer than just assemble the circuit cards. We want projects going through without a hitch, no delays. What we all want is production of electronics.
- Why did EIT recently choose to onboard Altium Designer internally over other tools?
Firstly it’s an all-inclusive package. It’s schematic and design, we like the ECAD and MCAD interface which makes it easy to do 3D fit models. We love the room creation capability that allows you to reuse previous designs. It has very solid DFM rules capability which are set up in advance - that’s a nice piece of insurance. It’s reasonably priced compared to the other high-end tools as well.
- Engineers After Hours: Big hiker, especially the Rocky Mountains. We’re going to do 3 national parks this summer.
- Unique hobbies? Jay has been a dart player since the age of 19. Played in a couple of US opens. Pro advice: 2-3 beers is the sweet spot for optimal dart throwing performance.
Links and Resources:
EIT Electronic Instrumentation & Technology Website
AltiumLive 2018: Annual PCB Design Summit
Hey everyone, this is Judy Warner with Altium's OnTrack podcast. Thanks for joining us again. I appreciate everyone that's following, we are spreading like wildfire and we thank you for all your comments and opinions and we always look forward to hearing about things you want to hear - so reach out to us on Twitter; I'm @AltiumJudy, or you can connect with me on LinkedIn or Altium is on LinkedIn, Facebook, and Twitter.
So today I have a longtime friend and ex colleague, Jay Colognori and Jay is the Director of business development at EIT which is Electronic Instrumentation and Technology in Richmond Virginia, and you're gonna have fun just listening to Jay because it's like talking to Matthew McConaughey!
So you girls out there? We're gonna just have fun listening to Jay talk...
Just kidding, but he does have a nice Southern drawl.
So Jay, thanks so much for joining us today, and we look forward to talking to you about DFA and some technical stuff today. So thanks for joining.
Thank you for having me. This is an exciting time at EIT we just added on Altium capability and so I'm delighted to get to the word out, and what better way to do it than talking to you?
Well, you know when you suck up to your friends at Altium, you get on the podcast. That's how it works around here.
So Jay, Why don't you start out by telling our listeners a little bit about your educational background and your professional background sort of set the stage for us?
Okay sure. I picked up an EE Degree at Virginia Tech and then a Master's EE at the University of Virginia. So you could say I'm a son of Virginia for sure. I managed to spend most of my career here in the Mid-Atlantic and my career spans from board-level electronic design to integrated circuits, VLSI design, and then kind of jumped over to the other side of the table and became an Applications Engineer, doing custom microelectronics and had a few years running a rep firm making some commissions along the way, and then I ended up in the printed circuit board business working for DDI and VIASystems, now TTM, and one of my customers was a company called Zentech which was an Electronic Manufacturing services company, and I went to work for them. And now I work for EIT who is also situated in the Mid-Atlantic. I do want to correct one thing you mentioned. I live in Richmond, Virginia, but EIT is based in Leesburg, Virginia where we have two other facilities, I can talk some more about that.
Alright. Thanks for correcting me there.
So with all that variety of background why don't you tell us a little bit about where you are now and about EIT and what their expertise is, and what kind of technology makes they handle and so forth?
Yeah. Okay, so I joined EIT back in March, very happy to be there. This is a company that's in its 42nd year of providing...
Wow.
Yeah - Engineering services which then led to electronic manufacturing services. So we do both; engineering is very much in our DNA, we consider our engineering value-add to be an important part of most of our customer relationships.
So, you know, the thing about being in the electronic manufacturing service is that it's kind of a commodity when you look at it from the standpoint of just picking and placing parts with machines. So, we're looking to engage customers at additional levels, including engineering, turnkey builds, turnkey testing solutions, of all manner, box build if necessary, demand fulfillment, soup-to-nuts… so that we're doing more than just using those machines. And EIT has three facilities on the East Coast. Altogether we have over 200,000 square feet of brick and mortar which makes us pretty big for a small company. We have a facility in Danville, Virginia. Our headquarters is in Leesburg. And then another in Salem, New Hampshire. Altogether, I've got eight surface mount lines to keep busy.
Danville is what we designated our low-cost center of excellence. It's also a 100% vertically integrated location because they can do any kind of metalwork, cabling wire, box build. We have all that in place. It's a purpose-built facility to support the box builds, which we like to do for our customers. We don't do metal stand-alone, although occasionally I'll build a heat sink or something for somebody. We tend to allocate that factory towards our customer box builds.
Okay.
And then Leesburg, and Salem New Hampshire are high-tech facilities, they both have the latest state-of-the-art universal equipment, so we can back each other up if something goes wrong and they both have a full suite of the latest and greatest and automated inspection technologies and a full suite of test capability.
Wow that sounds impressive!
It's a heck of a lot going on, and a story that needs to get out; it's kind of been a kept a secret lately so yeah...
I haven't heard of them. I mean I'm on the left coast, of course, but I had not heard of them, but they sound like a really great facility with a really good… going all the way from true engineering to box builds. That's nice.
So… and we'll make sure to share the link, by the way, for any of you listeners who are looking for a good EMS or engineering service or whatever. We'll be sure to share that link on the show notes.
So yeah, and please do, because we're launching a new website next week, so I want to get that out.
Okay. Hopefully the timing for that'll work out.
Okay. Alright good. We'll send you some traffic for your new website. So Jay, because of the breadth of your knowledge and experience and background I thought it'd be great for our listeners today if you shared a few tips from, you know, being that you came from some of the largest board manufacturers and certainly in North America and almost the world - maybe three tips or so, on bare boards and then a few on DFA to help the designers in our audience, and engineers in our audience, that might want to learn a few tips and tricks from a pro?
Okay, you know I came up with a few of each, you know, really when you're looking to design a printed circuit board, you have two fundamental objectives: one, to design it so that it can be fabricated reliably and with high yields. And then two; so that it can be assembled. So there's mistakes that can be made that can affect both key processes.
So first of all, let's talk a little bit about PCB design issues that affect PCB fabrication and reliability and, you know, none of these I think are gonna be earth-shattering, but it's interesting to see the same mistakes being made a lot over and over again.So, we just kind of keep - we're banging the drum and we hope everybody gets the message sooner or later.
So, I guess beginning with VM pad. There's more and more VM pad today, by necessity, and VM pad, in order to be done reliably, requires a wrap plating process. Without getting into specifics of what that does, what the purpose of it is, it provides a reliable button around the via. Without the wrap plating process. It's an unreliable arrangement, but that requires the addition of more copper on the outer layers than you would see otherwise, and this wreaks havoc with the fine line design.
So, if you're at 3 mill tracing space or below, you really can't tolerate that extra copper; so it requires planning upfront. Understand, if you're gonna need wrap plating and if so, maybe move those fine lines geometries to the inner layers where that won't come into play.
Okay, that makes sense.
And it'll get you, I mean, you think your design's done and then the next thing you know, your fabricator says, well you know, you realize I'm going to add this much copper to the outside and now you're violating tracing space.
I've seen this happen too when there's multiple on RF and microwave boards too and you have... when you're doing sequential LAM or whatever, and you keep plating, plating, and people don't, when they do their simulations, don't add in those extra layers are getting extra copper too. So you really can throw you off.
All right. That's a good one.
Here's another one that you know, I'm told we're still seeing a lot of it in the market by the guys that I used to work with at DDI, and that is, you know, they'll see overlapping via structures where the designer has put a via from say, level one and three, and another one from level two to eight; that can't be made. They have to be stacked; they have to be sequential. They can't be overlapping but believe it or not. You see it.
I've seen it many many times, but you know, to be fair, sometimes when I look at those cords and figure out how they're gonna be stacked up, it… you know. I get confused too. So...
Well, I mean, I'll say this again and again: sit down with your PCB fabricator at the time you develop your stack up and your basic via structure and basically your structure is going to be driven by the toughest part of the design.
Maybe it's a BGA with a finer pitch than you've ever used before. You're not even sure how to route it, you're probably going to have to stack some micro vias, or at the very least, have some blind or buried vias to get the job done. Sit down with a fabricator, before you even start that router, and make sure that everybody likes the stack up and that it looks manufacturable.
Yep, very sound advice. Okay, that's another good one, got another one for us?
One more I want to talk about, because this is happening more and more, you know, all the designs are getting faster and faster. I mean, high speed digital is now in the radio frequency and, FR4 is just has too high a dielectric for most of the new designs now, so many PCB designers are going to have to work with materials they haven't worked with before, the more exotic, more expensive materials, and when you start talking about fabricating a PCB with Teflon versus FR4, you're talking about different processing altogether.
So, when you go to a new material, consult with your PCB guy as to which material would be suitable for the speed you're looking at, and ask them, okay, how have the rules changed with that material? What are your limitations?
And you can ask the EMS provider the same question, because the parent circuit board is the foundation upon which all of our business is done. So we understand PCBs, but I think especially with materials you want to talk to the fabricator.
Yeah, it's true and when I worked for an RF and microwave shop once, I told them, I said: you know, sometimes when you see a piece of Teflon material and a piece of... I don't know, Rogers 4350, until you strip the coffer off. You can't tell it's different, but inside the board shop that Teflon can turn into bubble gum, it's not reinforced. But when you take the copper off and you go like this [motions] it like flaps in the wind where 43-50 will remain rigid so, kind of gives you a visual sense of, this is radically different. And the way that it processes inside the shop, and how, the way it interacts with chemicals, moisture, heat, so it is true - the closer you can be when you go into those materials, to your fabricator. Okay, those were three good ones. All right how about DFA wisdom?
Okay, well one we see quite often, and I guess it's tempting for the designer to do this, because he thinks he's kind of found a shortcut and a way to use less PCB area, but you see a lot of guys trying to use what we call common pads, and these are pads that are so close together that they touch, rather than routing a thin signal from pad to pad.
So these pads do share the same signal, but we don't want them to physically share the same space. That causes us problems with controlling what the solder does once it flows, so keep those pads apart, and run a just a small signal trace between them. And then we'll let the solder mask do the rest, and we can control the flow of the solder. So that's a real simple one, but we run into it a lot.
Okay.
I talked before about VM pad, we see a lot of designs where people don't fill that via. If the via is in the pad, it's got to be filled, and it must be plated over and planerized. Sometimes that's done properly sometimes it's not. There's a little dimple there...
Yup.
If there's a dimple in that pad and I place a BGA ball on top of that gas, it's gonna get trapped underneath the solder paste that I apply and there'd be a little air in that dimple and heated gas expands; it expands ferociously. It doesn't want to stay where it is and it'll blow all the solder right out of the pad at reflow time and you know I have customers argue with me against it, it is expensive to fill and planerize via, but it's the right thing to do. You have to do it if you want reliable BGA connections. These are leadless parts that we can't inspect visually, we have to use x-ray.
It's not really practical to use a hundred percent x-ray inspection except on high-reliability applications like military, maybe medical. So we lot, we lot-sample these BGAs with X-ray and if we don't see any problems with a lot we carry on.
So, I can't emphasize that enough, to fill those vias and fill those vias properly. And I would add further, that there's no point, you know, we have some people that are using thermal vias, these are vias really which are designed, not necessarily to conduct an electrical signal, although they do, but to conduct electricity from a hot part from maybe a ground plane, might be an inner layer or wherever, and you run into people who call out… so there has to be a filling to fill those vias before they're plated over.
Right.
And there's two types of filling: there's conductive and there's non-conductive. I strongly recommend never to use conductive. Non conductive is much less expensive. The benefit of using conductive fill from a thermal point of view is super minimal. I mean, the copper's doing all the work...
Okay.
-and if you need to draw or pull more current or more thermal energy, just create more thermal vias because the copper's doing all of the work. I mean, I'll give you some numbers: thermal conductivity is defined in wattmeters, a typical via is going to give you over 600 wattmeters of conduction, if you fill it with conductive fill you only get six more wattmeters. What's that compared to...
Oh, yeah.
-380 I'm sorry, 380's what the copper gives you. The non-conductive only has point six wattmeters.But the point is both of those are in the noise compared to with the copper's doing.
Right.
And last but not least. Good luck trying to get a printed circuit board fabricated in China with conductive fill they don't do it over there.
Really?
Right so well, maybe somebody's doing it but we're having a hard time finding any.
Interesting hhm.Why is that?
Because it's not, it's not...
They just don't like it? It's not important so we're just not doing it?
I don't think anybody should be doing it, it doesn't make sense to me, it's too expensive for the return.
Interesting, I'd never heard that before actually, but it makes sense with those numbers. I'm kind of surprised it took root for a while.
We recommended as far back as five years ago, at DDI, not to use conductive fill, I think it's a dinosaur that it's day has come and gone, but there's probably some engineers out there right now, going no!
Huuu! [laughter]
We'll see...
Yeah well show me the data, you know, and when when there's enough good research out there and data people stop doing it. I'm sure.
Okay, so along the lines of thermal vias, here's another tip. A lot of times a thermal via will be located in a big plane so you'll have the via, and the copper button around it will actually be in contact with the plane - this is a no-no. This makes it very hard to deal with the solder flow again. So what we ask our customers to do; is do a sprocket arrangement around that thermal via button and so basically that button will exist - there'll be a gap between it and the plane around it, and then the sprockets are simply traces above, below, and the right and left and that - it's an arrangement of the sprocket - very good design practice, frequently missed and, it's not unusual that we have to go back and retool the board to add those in order to make it.
Especially back planes with active components; you see a lot of that and they have to retool to add that feature to make it manufacturable.
Well, these are good tips. You were concerned you didn't have good tips. I think these are really good tips actually.
Well glad you do.
I do, not that I spend all my days, you know, pondering DFA these days, but that's good.
You know Jay, you and I worked together for a small bit of time and something I've noticed over the years I don't know... maybe five, ten years, it seems like there's been a migration of more EMS shops that go in to have PCB designers in their shop and not so much I guess, fabricators - at least that I've noticed, they may be there, of course they do with larger shops, but why do you think that is and why do you think that's a good idea?
Well, I think it's a great idea for both the customer and the EMS. We, as I mentioned before, we want to do more for the customer than just assemble the circuit cards and if a customer, an Altium customer, finds themselves in a position where they need to outsource some of their design, maybe they you know, their designers are saturated, maybe they just need the resources.
What better place to do it than at a guy that knows how to assemble the cards and really understands the issues about fabrication and about assembly. Your chances are that the design from your EMS provider is going to go right through new product introduction without a hitch, whereas if you do it internally and you're not aware of some of the issues you know, it won't go through it without a hitch. We may not catch the problem until it's too late. And we may see several tooling iterations, and you'll see a delay and nobody wants to delay during new product introduction - everybody's in a hurry to get their prototypes.
And nobody wants to waste money because that's going to be expensive too -
Yeah, but we think there's a lot of serendipity between that particular engineering function and getting to what we all want. Which is production of electronics.
Well that does make sense in that, we both know Mike Brown, and Mike I trusted implicitly to know about fab and assembly and he would catch all that stuff so he did have a broader understanding than maybe, somebody who just does, you know has a consulting firm say, that does designs because he's around it all the time all, day long so there's certainly a lot of exposure there. So that makes sense.
Well, first of all, welcome to the Altium family! You told me recently that your designer on-boarded Altium Designer 18, that's exciting for us. So thank you for that. What made you - I'm gonna go for a little pat on the back for Altium right here. I want you to tell us why you, why EIT chose to go Altium Designer over perhaps another tool?
Okay. Well, we think some of the key features of Altium; first of all, it's an all-inclusive package so it's schematic capture and printed circuit board design. You don't have to worry about working with two different pieces of software.
We like the fact that there's an e-CAD m-CAD interface which makes it really easy for us to do three-dimensional fit models once we place the components. We love the room creation capability which as I understand it, allows you to take a previous design, a piece of it, and then just kind of cut and paste it right into your new design.
Yeah.
So you don't have to reinvent the wheel. I think that's pretty strong and then, last but not least very solid DFM rules capability that you know, is really going to help us get to where we need to be. I mean the fact is these boards need to be designed to IPC standards and the fabricators have tailored their process to meet these standards; and when you send them something that's outside those bounds, the mechanism sort of locks up. It just doesn't work. You'll get a 'no-bid' or bells will go off, so those design rules are critical and that you have the ability to set them up in advance is a nice piece of insurance so; I think it's a reasonably priced tool compared to the other high-end tools as well. So we're pleased to have it.
Good. Well, thank you again we're happy to have you on board and I'll needle you later about sending your designer to AltiumLive because we're gonna have a really good conference with some good training coming up. So your designer will probably enjoy going if you guys have the time and budget to do that.
Well, keep me posted on when and where.
I will it's coming up in October. So Jay, we're kind of wrapping up here, but if you've listened to these podcasts before, you'll know that sometimes I like to ask designers or engineers like yourself, what you like to do after hours, and we call this portion of the podcast designers after hours. So, I know you have a couple interesting hobbies...so why don't you tell those to our listeners because I think they're kind of fun?
Well, I'm looking forward to 10 days in Montana and Wyoming this September, I'm a big hiker, and nothing is more fun than hiking up in the beautiful Rocky Mountains. So we're gonna hit three national parks; we're gonna do about two to six hours of hiking a day or as much as my legs can give me and just have just an awesome lifetime outdoor experience and hopefully not run into a grizzly bear along the way… my wife's really worried about that, by the way [laughter].
Bring your grizzly repellent!
And then, I know you wanted me to talk about one other thing...
My favorite...
Yeah, as you know, we business development types are very competitive and what better setting to compete against each other than you know, in a pub throwing some darts.
So I've been a dart player since I was 19 and took it very seriously for a while, and spent way too much time on it. Actually traveled every weekend to tournaments all around the United States and played in a couple of US Opens. But that was a long time ago, now I just play for fun on Monday nights.
That cracks me up. You are the one and only competitive traveling dart player that I know... Okay, but my favorite part is - tell about the beer to success ratio of a good dart player.
Oh yeah, so so we're throwing a 27 gram projectile at a target about the size of a dime and turns out, that if you get nervous or you try too hard, you're not going to be very successful with that. So, it turns out that, that second or third beer really kind of smooths out your stroke and you generally shoot a little bit better. At least that's what we rationalize.
And what happens if you go over three?
Yeah, that's that's a slippery slope indeed. You've got to be careful...
That is so funny oh my gosh. Okay well, that is like one of my favorite, I think, designer after our hobbies yet.
So when I come out, we'll find a place and throw a few.
Okay. Alright, I'll get my three beers ready
Okay!
No, actually for me, I'd be like half a beer, like three beers you'd be putting me in an Uber and sending me home. I'm a wimp.
So Jay, thanks so much for your time. These have been great tips and it's good to see your face my friend, and I wish you all the success at EIT, and we will certainly share all the links in the show notes and we'll also put the link to AltiumLive in the show notes and we'll encourage your designer to come out and join us as one of the new new beasts of the Altium family. So we'll include that as well.
So thanks again for joining and we'll talk to you soon, my friend.
Thank you Judy, it was my pleasure. Thanks again for listening to the podcast.
This has been Judy Warner with the Altium OnTrack podcast and Jay Colognori from EIT, and we look forward to seeing you next time. Until then always stay on track.
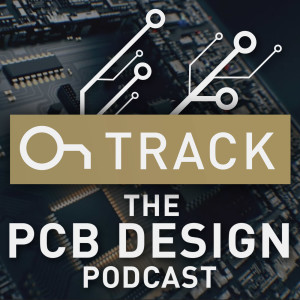
Tuesday Jul 17, 2018
Paste Interconnects and Paste Sintering with Chris Hunrath from Insulectro
Tuesday Jul 17, 2018
Tuesday Jul 17, 2018
Paste Don’t Plate! People are doing 90 layer multilayers with paste interconnects. Want to learn more? Find out about paste sintering from Chris Hunrath to learn more about its applications and benefits to PCB designers. What must designers consider and what are the advantages of Ormet’s products? Listen in for insights from the expert in this week’s episode.
Show Highlights:
- New material developments make paste interconnect technology more feasible
- Ormet’s paste sinters at one temperature forming a new alloy with higher melting point
- Paste interconnects allow for changing build sequence in which vias are formed i.e. drill, add paste, and then laminate - giving you interconnects inside a double-sided core with no visible vias
- Multilayer PCBs: Can split up a 32-layer board to two 16-layers (even as many as 4 x 18 layer multilayers - which is much easier to build
- Also reduces risk depending on design - electrically test each half and only use the good ones
- Ormet process/paste interconnect process eliminates traditional drawbacks i.e. excess copper on surface features
- Eliminate backdrilling with paste interconnect process without extra copper in the via
- Ormet paste eliminates electrolysis and plating process
- Signal integrity benefits
- Applications: RF, high-layer multi cap, avoid secondary remelt, downhole assembly etc
- Design considerations: Where to split up layers for best design benefit; Via at 1:1 or less aspect ratio - only in 1 B stage layer and correct size via for applying paste; Size of receptor pad for laser drill via must be correct to prevent paste from running - spread glass is good for B-stage; annular ring around the via to register laser drilling; with many paste interconnects - don't paste to the edge.
- Paste melts and forms alloy with inter layer copper creating a permanent metallurgical joint
- People are doing 90 layer multilayers with paste interconnects.
- HDPUG (HDP User Group) is creating HDI test vehicles with paste interconnects and HDPUG members will have access to reliability data for breaking up big PCBs
- Paste don’t plate!
- Future topics: Many ways to use conductive inks in electronics, copper foil, integrity issues and printed electronics. Material science behind electronics, new design tools, various versions of conductive inks
Links and Resources:
Chris Hunrath on Linkedin
Click to listen to Chris Hunrath’s other episodes about Spread Glass or Material Sets.
Hi everyone. This is Judy Warner with Altium's OnTrack Podcast. Welcome back, here we are again with your friend and mine, Chris Hunrath from Insulectro who's going to teach us about paste sintering today, which I don't know much about, but we're going to learn about it together. But before we get started, remember to hit all the typical Altium social media platforms Facebook, LinkedIn, and Twitter please follow me on LinkedIn and also remember we are recording on YouTube as well as Podbean and we can be found on all your favorite podcast apps.
Alright, so today we're going to talk about - I don't even know how to set this up entirely cause I'm just as much as a student. So Chris, welcome back! Thank you again, and I know this isn't a new technology - it's just not one that has crossed my path. So tell us about what paste sintering is and what the applications are, and benefits to our designers that are listening today?
Okay, interconnect technology, as you mentioned is not new, what's happened recently though is there's been some new material developments that make it more feasible for the circuit boards. Certainly in ceramic fire technology, metal - powdered metals have been used to make interconnects and traces and circuits on ceramic circuit boards, but those fire at 850-plus degrees Celsius, which would obviously destroy most PCB materials so there's some new technologies out now. There are different kinds of pastes that are used for interconnects. The one that we work with, and the one that we promote, is something from a company called Ormet, and their material is interesting because it sinters at one temperature and then it forms a new alloy with a higher melting point.
Okay I feel like we need to back up and explain what paste interconnect technology actually is. Like how it's performed and then we can go into the material science part just so I can keep up, Chris I want to be able to keep up.
So multi-layer PCBs - also not new - typically what you do is, you print and edge any number of layers, you drill and then you plate. Typically electroless copper, to make the non-conductive surfaces conductive, and then you build up the thickness with electrolytic copper.
Mmm-hm.
And some people call it a semi-edited process, because you are using the electroless first as a seed layer. There are some other technologies used to make that dielectric surface conductive, and then you build up with electrolytic copper and so that's how you link the layers of the z-axis.
So if you think of a classically - as a circuit board - as a web of foils printed and etched, all your XY connections, and then the drilled holes - whether they're laser drilled, blind vias, or drilled through holes, the plating links everything in the z-axis. Now one of the challenges when you do that, is you're consuming real estate at all the layers. So let's say you have a 12 layer multi-layer - relatively simple multi-layer by today's standards - but you need to connect layer 1 to layer 10 you've taken up the real estate in all the other layers - you can't route circuits in those places, because there's a via in the way, unless you wanted them to connect to that via and they're part of that net. So there's a term called any layer HDI - I don't know if you're familiar with that term? Basically it means you could put a via anywhere you want in any layer. Nowadays that's done typically by what we call build up technology. So you start with a core of some sort - again it could be double sided, it could be a multi-layer core, and then you sequentially build layers and you only go one layer deep with a laser drill sometimes two - depending on the design - but that's not true for any layer.
Anyway, you go one layer deep you plate, you print and etch, and you do it again and again and that allows you to put vias almost anywhere you want in any layer, the downside is, it's almost like building multiple circuit boards. So the cost really starts to increase. And of course you're putting the board through multiple lamination cycles and that has some undesirable material side effects depending on the material. Some materials can withstand three lamination cycles, some six, some ten, but it is hard on the materials to go through that lamination process, over and over again.
Right.
Especially electric phenolics, which are very common for lead-free assembly, because they're relatively economic and they're also - they also will survive lead pre-assembly, but they tend to get more brittle every time they see a thermal cycle though, so that causes some issues too. So what paste interconnects allow you to do, is change the sequence in which the vias are formed. So instead of laminating drilling and plating you can actually drill, add the paste, and then laminate, so it changes the build sequence and this is important both for the fabricator and the designer to understand what that means. So typically what you would do is, you would take a B stage layer of some sort; you can either drill it and paste, fill it with what we call a postage stamp process or you could pre-tack it, vacuum tack it at low temperature to a core of some sort, or substrate, laser drill through the B stage, apply the paste and then when you laminate the paste interconnects, the layers in the z-axis - you could literally take a piece of prepreg, laser drill it with a stencil or with a Mylar Stencil, I'll talk about how that works in a little bit - apply the paste, remove the Mylar laminate between two copper foils, and now you've got interconnects inside a double-sided cork.
That's cool.
So then if you print and etch that, now you've got a core with connections between the layers with no visible vias; they're all internal. Yeah there's some technology around the paste and again we can talk about that, in a little bit.
So how is it applied - is it squeegeed in?
Yeah.
Okay, just like with a silkscreen?
Well no screen - so what typically what you do is, you apply a 1 mm Mylar mask to the B stage and you tack it simultaneously. Then when you drill through the Mylar and the prepreg B stage to get down to your copper features, then you apply the paste, and the Mylar's your mask, and then you remove that just prior to lamination.
And that stays inside the hole? It doesn't just I don't know the consistency of it. My mind was - pictured it just wanting to drop out of that hole - but it must have some kind of stability?
Yeah it's a liquid and there is a tack right. There are a number of ways to do this, but the most common method is to laser drill, apply the paste, dry the paste... you would do it a second time to top it off and then when you remove the Mylar, the liquid paste stays on top of the paste that's already been applied. Then you dry it again, then you go to laminate.
Does it air dry or do you have to cure it what do you do?
You don't really cure it because it's metal powder - metal powder based - so there isn't really a polymer matrix. Unlike print electronic sinks - which is a again another story - you would just dry off any of the carrier solvent used for the application process. It is a liquid - well it's a paste, not a liquid - but but when you dry off the the solvent that's in it; which is less than 10 percent by weight, then it's just powdered metal and that's how it makes a connection. So think about this right, you've seen a lot of PCB designs - imagine a 32 layer board, which most shops can do, but it's not at the low end of technology. Imagine splitting it up to two 16 layer multi layers right?
A lot easier.
A lot easier to build and then you just paste them together at the end, and depending on the design, you can electrically test each half and only use the good ones. So your risk is light.
Oh, right.
There's a lot of advantages to this. Or what if you want to put together three 16 layer multi layers, or four, or 18 or four 18 layer multi layers - it's been done you know. Now a shop; instead of trying to build a 72 layer multilayer - if they're building 18 layer components - it's a lot more manageable.
Hmm, that totally makes sense. So you explained some of the benefits - it's a nightmare, and you've seen, we've all seen these cross-sections of these crazy stackups with all the sequential LAM and drilling cycles and all of that. And then - and also kind of an unintended consequence you can get, is you can - from a performance standpoint - if you do enough of that right can't you get excess copper on the surface features?
Yes - that's a very good point. So in other words, if you're going through many plating cycles depending on how you break that up and you're trying to meet a wrap requirement, that could definitely add up and make it - make fine line etching more difficult there's a lot of - there are some some drawbacks to traditional processing and then with with an Ormet style process, or a paste interconnect style process, you can eliminate some of those things even with an RF design.
Let's say you have very sensitive surface features and you don't want to play with that layer. You might want to put on the surface finish, the nickel gold, but you don't want to put any additional copper - you want just the original foil copper. You could do that with this paste because you could create that as, almost like a double sided board, and then bond it to the rest of the stack up at the very end, and you're done.
Interesting. So I think you mentioned too, there's some good signal integrity benefits, did we cover that I don't recall?
No, so one of the things that a lot of designs call for is something called back drill. So you're familiar with that, so you do the back drilling to get rid of the unwanted copper. So again, in my earlier example let's say you're connecting layer 1 and 10, and let's just say it's a 22 layer - 26 layer multi-layer. You're going to have a lot of extra copper metal in that via that you really don't need or want. So common technology is to back drill down to layer 10. Now of course drilling to that precise location or depth, to remove the copper up to layer 10, but not beyond. It can cause a reliability concern that's a bit of a challenge. So there's those issues.
What you can do with the paste technology is let's just separate that board at layer 10, and not put a via on that half that goes from layer 11 to whatever the other layer is and you're done. So you can eliminate back drilling and the parasitic effects of having that extra copper and the via so that's another application. So there's some signal integrity benefits, there are some RF applications, there are some high layer cap, multi-layer applications, but also many layer HDI applications; it really depends on how you design it and use the paste.
So if you're a designer what kind of design considerations do you need to make up front?
Okay, my recommendation would be is: think about the design, think where it would make sense to split up the layers and provide the most design benefit. Generally speaking, we like the via to have a one-to-one or less, aspect ratio. Now that might sound restrictive, but it's only in that one B stage layer.
So then that's an important consideration. So in other words, if I have 5 mm of B stage, I won't want my via to be 5 mm or larger where I'm going to apply the paste. It has to do more with the paste physics and how it fills the via and then of course the pad, the receptor pad that you're putting the laser drill via on, needs to be a sufficient size for where the paste doesn't have the opportunity to run on one side or the other of the pad.
So we do like an annular ring around the via, that's going to have a lot to do with how well you can register your laser drilling, usually that's pretty good. The other consideration is, the B stage you use, spread glasses - bringing up spread glass again. Spread glass is good, because it tends to keep the paste corralled, whereas if you have an open weave and that prepreg resin's melting and flowing and during the lamination cycle the paste could run to that area. So spread glass is better. Higher viscosity resins tend to be better. We like low flow prepregs. So those are some of the design considerations.
Another design consideration is - and I've seen this happen before - where if you have a ground area and you're making a lot of paste interconnects along a wide track. You don't want to put the paste interconnect to the edge of the track because what ends up happening is, during lamination, the resin wants to flow off the surface of the track down the sides to fill - hydraulic effect, and it's going to move the paste with it. I've seen vias actually move during lamination. So just some common-sense things. Keeping in mind that it's the B stage where your interconnect is. You want to make sure you put that in some good locations, and in that particular case all they had to do is, go back and shift the vias a little bit to one side and then everything was fine. So it's just those kinds of things. Certainly they could contact us, we can give them some design hints and I can give you some literature to go along with this video or podcast.
Yeah, yeah, very good. Ormet and the paste interconnect - paste sintering - has been around for a little while. What's been the sort of acceptance of it industry-wide? Is it being widely accepted, is it just on certain applications?
It's been around a long time. It was primarily used for quick-turn mic review work, and also large format boards where you're literally stitching very large boards together so you can - again the idea is you can make boards that are nearly finished and then electrically interconnect them. The nice thing about the Ormet paste is it doesn't melt at reflow assembly.
Hmm, so it changes chemically right, so once the sintering is done then it doesn't change, then it doesn't morph and heat?
What attracted us to this technology over some other paste interconnects - because there's other processes where you would apply a paste of some sort and then make a connection with pressure in the z-axis - but what interested us in the Ormet material is: the paste melts at one temperature and alloys - so the paste is basically copper particles with a tin alloy powder. When the tin alloy powder melts - and the melting starts at about 130° Celsius, it starts reacting with the copper and forms an alloy with the copper instead. What's interesting about the Ormet material is, it's alloying with the inner layer coppers as well, on the PCB layers. So we have a metallurgical joint, not just a pressure or contact connection.
So it's - and unlike, the tin lead or lead-free alloys and solder, the melt - the new melting point, when it forms an alloy with copper is one phase is 415°, the other is 630° Celsius. So it's not going to remelt that assembly. So it's a permanent connection, so really the paste applications from other technologies like flip chip and whatnot packages where you didn't want to have a secondary or - if you have a secondary reflow operation - you didn't want to have any more remelt. It has some applications there. Or a down hole assembly is another application where the board might be subjected to the temperatures near the solder melting point is another good application for this material.
So that's what interests us because you know when a board's in use, it heats up the z-axis expansion with other types of pastes interconnects, you have a resistance change every time the board is heated even from, let's say 40, 50, 60° Celsius in normal use, not even in any kind of environment - parts of the board would heat up from the components and you'd have a change in resistance, and that's what this is designed to circumvent because it forms that metallurgical bond with the copper inner layers.
Interesting.
So yeah it's a different technology than the paste you would use in printed electronics.
Okay well that's been fascinating. Again I feel like a newcomer to old technology but - and I've known about Ormet that I think got acquired by Merck now, but I've just never had someone sit down and explain it to me. So thank you for doing that.
90 layer multi layers people are getting - 90...
What!
Yes, 90 layer multi layers with paste interconnects yeah.
That's crazy, I didn't even know a 90 layer board existed I guess.
Yeah I've only really seen them into the 60s I guess personally, so.
Yeah you know, one common design was a 72 layer multi-layer, again made out of eighteen layer components, and one of the things with the chip tests the ATE companies, they built some high layer count multi layers and you need a lot of IOs, there's a trend to go to wafer level testing were you’re testing the entire wafer. You need lots of interconnects and that's one way to get there, is to use the Ormet paste to put in lots of layers. So we're seeing more interest in it lately, and I think that's one of the reasons why the technology hasn't taken off until now, is because there just wasn't the demand.
Right ahead of its time maybe a little bit...
Yeah.
Well, I know you've shared with me some cross-sections or I think you did, and so please be sure to share those with us and we'll put those up on our website and we can share your website and Ormet or Mark's website, so the designers can get more information. Is there any place else besides your two websites that you would recommend for more information?
You know I've mentioned HDPUG (High Density Packaging Users Group) in the past - they're actually contracting some PCB manufacturers to make some HDI test vehicles with paste interconnects. So there's going to be some data - anybody who's an HDPUG member will have some access to some really good reliability data and they're pretty complex boards so it'll really push the technology but for breaking up big thick and ugly PCBs, that's pretty well-established.
Yeah very cool. Okay well thank you. So tell us about that fish on the wall behind you?
[laughter]
So it was a gift from my sister, actually it's made from recycled materials so there's an old PCB cut up on there, and the old spark plug wire, and a few other odds and ends. Some artists put together actually I didn't buy it; my sister bought it on Catalina Island and somehow we went out there as a family trip and somehow she smuggled it off the island and gave it to me just before she headed back to Virginia. So it was kind of cool.
Oh that's fun a good throwback to your diver self.
Yeah so - just the last thing on Ormet, is 'paste don't plate'.
[laughter].
Is that their tagline or is that yours?
Actually that's their tagline. We were sharing it with the IPC shows, but another nice benefit to the Ormet - which I didn't mention earlier is - there's no electrolysis, no plating processes in these interconnect layers so it circumvents all that.
Which is like bizarre for me to think about but...
Yeah but if you're capacity constrained, no plating, that's another benefit.
Well thanks again this has been really good. If you have anything else juicy to share with the listeners just email it over before we get this one up.
Okay.
And thanks again for this one. Now I know we've talked about exploring down the road a little bit on copper foil, integrity issues, and also printed electronics. So I'm sure I'll hit you up again soon Chris.
Yeah definitely. I would like to talk about some of the material science behind printed electronics and I know you guys are working on some new design tools and print electronics; there are a lot of different ways to use that in electronics... I should back up, but there's a lot of different ways to use conductive inks in electronics there are so many different versions of the inks.
Which is another subject I know nothing about so it'll be good. I'll be a student with our listeners and, I know they're out there, I know what conductive inks are, but as far as all the applications, all the different materials available, that just seems like something that's in writing a lot, that people are really turning towards a solution.
Lots of new technologies are coming out in that space and it's going to be fun to watch it all.
Yeah yeah it will be.
Okay Chris, thanks for another good podcast and we'll see you soon.
Thanks for having me.
My pleasure. Again this has been Judy Warner with the OnTrack Podcast and Chris Hunrath from Insulectro, we'll see you next time - until then - always stay OnTrack.
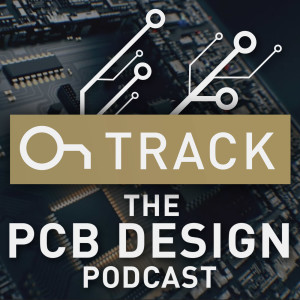
Wednesday May 30, 2018
DFA Tips from Duane Benson at Screaming Circuits
Wednesday May 30, 2018
Wednesday May 30, 2018
Duane Benson from Screaming Circuits shares DFA Tips and a piece of history as he shares the story behind the scenes in developing quick turn prototypes. Listen to learn how one entrepreneur brought fresh perspective to the business that led to great success. And see why Screaming Circuits is uniquely positioned to handle all the leading edge components that PCB designers have available.
Show Highlights:
- Screaming Circuits was founded on the premise to get prototypes built quickly. It was a struggle to get small volume prototypes built and a market need was discovered.
- For prototyping - going abroad invites its own set of risks.
- A traditionally 6-8 week process, Screaming Circuits does in hours.
- We don’t specialize in a vertical industry, so we see a lot of the leading edge components.
- Layout isn’t taught in schools or its self taught. The experts who knew how to make layouts work perfectly have retired.
- We built a business around stuff being wrong. Stuff isn’t going to be right when it arrives to us and we have to fix it.
- Why are we having a problem sourcing parts?
- Personal interests? Photography and decaying industrialism.
Links and Resources:
Downloadable Circuit Talk
Twitter: @pcbassembly, @duanebenson
Screaming Circuits on Youtube
Hey everyone this is Judy Warner with Altium’s OnTrack podcast. Welcome back to another podcast session with us. As always we have another incredible guest with us today but before we get started I wanted to invite you to please connect with me on LinkedIn. I'm very active there and share a lot of resources for engineers and PCB designers and also - I don't think I shared this in past podcasts - but we are also recording this on YouTube as well as just an audio. So you can always go to YouTube and go to the Altium channel, look under videos and you'll find these also in video format if you should prefer to listen to this and watch it in video format. And also with Altium, you can always follow us on Facebook LinkedIn or Twitter and we love engaging with you. We always love to hear from you about subject matter experts or subjects you'd like to hear or learn more about. So, without further ado, I'd like to welcome our guest today who is Duane Benson of Screaming Circuits, out of Canby, Oregon, correct Duane?
Canby that's correct.
So Duane welcome, we've crossed paths for several years now and it's a delight to have you and learn more about Screaming Circuits and EMS and how designers can do things to to be more effective in the design for assembly and just learn about Screaming Circuit’s model, which is a very unique model by the way, I'm eager to jump in.
Well thank you I'm really happy to be here thank you for asking me to participate in this.
My joy. So why don't you start out by telling our listeners a little bit about who and what Screaming Circuits is, because it really does have a highly unique model, and kind of the why behind you guys started the company and created this model?
Well it started back in 2003, actually that fifteen years ago now. Yikes..
Yeah, I know, how did that happen?
So about that time our parent company Milwaukee Electronics they had a number of customers that were struggling to get small volumes of prototypes put together back in the back in the olden days - if I can use that term. Prototypes quite often were sort of slotted in on an ‘as available’ basis. So say you might need five prototypes and the EMS company would say, well we’ve got a big run going on and I can put you u on the machine in two weeks so you can get your prototypes then. And two weeks come along and something else came up, so another week... Even going back before that, back in my day they didn't focus, for example, building a prototype.We'd have a big bag of parts and some blank circuit boards, and we'd hand them to this poor technician on a Friday afternoon and the engineers would go, could you have these built up by Monday?
So it was becoming a real struggle to to get prototypes, get small volumes of any sort built and a couple of our customers came and asked us and said, can you can you help us out with this? It's just not working and the Milwaukee Electronics’ management thought about it a little bit and thought, why can't we short-circuit the process?
No pun intended right?
Laughter.
So the management experimented a little bit and then decided, , there's an actual business here. So back about that time they brought Jared Store out here to start up what they called the Screaming Circuits division to focus specifically on getting prototypes done quickly.
Mm-hmm.
And , from that time the initial focus of the initial business was basically Jared with email and phone and one of our partners Sunstone Circuits, they built the blank circuit boards - the raw fabs. They'd give us a call and say, hey one of our customers needs some prototypes built, can you guys do it? And that's how the business started.
So you guys created the synergy. Now I've had the pleasure of meeting Jared once at least, through the phone and email and Jared was young right? He was the son of the owner so, I have to insert that. Because I kind of love that those of us who are kind of old dogs in the industry - I kind of love that he said, well why can't we do this? And he just kind of, like you said, a phone and a thing and just said why not. Because he wasn't constrained by the way things were done in the past which I kind of love that.
Exactly he was a young entrepreneur, in fact, I don't know if he'll want to admit this but this was his first job out of college this was kind of an experiment for him to get into a career, into business and he did a fantastic job. Basically by ignoring all of the old rules.
I know yeah.
Yeah and then in 2004 - well somewhere between late 2003 and early 2004 - we first went online with a very, very simple quote system. We boiled it down into six different factors and based on that, came up with a quote and it was all kitted at that point. So we'd say, hey it's going to cost you this much, send us your kit, send us your files, and we'll build them up for you.
Now since that time, when we were talking earlier, it seems like it's morphed into not just specifically prototypes but just quick-turn. It could be quick-turn pre-production quick-turn production even right?
Yeah
The world of manufacturing of electronics has really changed in the last decade and a half . There was a time when electronics were not going to be designed and built in this country. Back in the 90s, when I was working for InFocus again, everybody was outsourcing everything and then over the next decade after that, it was all going going away.
Yeah.
And there was going to be nothing but high volumes manufactured offshore. Well about the time we started doing this, coincidentally the open-source hardware movement came about with the Arduino and some of the other things that came with that. Kickstarter showed up and that really changed the hardware design dynamic. It lowered the barriers to entry to building a hardware company and over the last decade and a half the hardware startup has come back with a vengeance. The problem is, as manufacturing is really, really expensive - unless you're doing super high volumes - so these companies would run a Kickstarter, they'd sell a thousand of an electronic board and nobody would build it for them. So then, , they'd then run off into into Asia and they toured all these shops and these people would either say, no that's not enough or they’d change the design, steal the intellectual property and, you can't. There's little details like that so, getting a hundred or a thousand or five thousand is extraordinarily difficult. And yet there's an awful lot of companies that sell just that many of something.
Yeah, it's really interesting that it morphed into that niche right?
Yeah.
You had, it sounds like you had everything, in place to fill it right? You'd built it to do address prototype - traditional prototypes - and as the market changed you were kind of ideally positioned to address those kind of start-up Kickstarter things. So you and Sunstone have worked together in parallel, I take it throughout this process?
Yes they've been our partners since the beginning, and at this point they build the vast majority of our circuit boards and we do, if necessary, go elsewhere. Or if a customer sends us the boards or requests something else, but the vast majority of our boards are built by Sunstone. They're about ten miles away over in Mulino Oregon.
Another big city like Canby…
Laughter - well compared to Milano Canby is the big cities...
Yes well it's a beautiful area. So, tell us about what you would see in a given day and then I would like to ask you to jump into speaking to designers that may be listening, and go into kind of some DFM tips and tricks. But before we do that, tell us about what are you going to see in a day?
To get a picture of what happens there at Screaming Circuits there's two factors that are pretty important. One is a traditional EMS company. We we see about as many different jobs through here in a week as a traditional medium-sized EMS company we'll see in a year.
Wow!
And the other factor that's important to notice, is that in - using that term the olden days - getting a quote and an order for a project might be a three to four week process going back and forth with all the files, component availability, making sure the design works and then after you place the order, you've got the NPI process which is another three to four work weeks. So, you've got a six to eight week process that we do in six to eight hours.
How is that possible? I mean we may not have enough time here Duane, but I've been in the EMS industry and it’s an extremely complex process, just getting the components you need and making sure they're right and there's not obsolete parts, and that you've got a clean BOM, and it's so complex. How have you condensed it without giving away your secrets?
Well there's a lot of things that matter if you're building a hundred thousand of something or a million of something. At that point fractions of a penny count and you're going to spend a lot more time quoting. You're gonna have to worry about getting large quantities of components if you need 20 of a board you can go to Digi-Key and get the parts for a buck, that would cost you a quarter of a penny if you bought them at high volume, and that's still fine now, that's part of it and then you don't have to worry about some of the inefficiencies that would absolutely kill a high-volume manufacturing manufacturer. You don't have to worry about those because if you have to tweak things by hand, while that is more expensive per unit, if you're building 20 or a hundred or a thousand it doesn't matter quite so much. So really what we've done is, we've stepped back and we said, what is important and what is not. The objective is to get working boards into an engineer's hands as quickly as possible and you'll notice there aren't things like how do we make it the absolute least expensive, or things of that sort, it's about getting the working board's as quick as possible so you focus on just the things that matter for that.
Right, you mentioned when we talked a few weeks ago, about it becoming what you had called a transactional model, which is really a different industry and you can go online, place your order in a very transactional fashion, but it also speeds up your time to market, and gives you something highly valuable?
Yes it does, we don't we don't spend an awful lot of time on the financial component of it. For the most part you give us a credit card and we start building so we don't have to worry about the bank component of it. For larger companies we do, because some people, the government or whatever, they have to operate that way. But for the most part you just give us a credit card and that again cuts some time out of it. We also look at each order as an individual transaction, that's why we call it transactional manufacturing, or unforecastable. We don't have to worry about the fact that you're not gonna need exactly 500 every month for the next 24 months. In traditional EMS, you have to worry about that, you plan for that. We don't worry about that, we don't care.
Yeah it's interesting as well it's neat model and I see it as a real enabler. So, congratulations to you guys. All right, let's dig in and give our listeners that are designers and engineers some tips around DFA. The way that you and I originally came to know each other is, I had been blogging and writing and then I came across a little publication you put out called Circuit Talk in which you were doing what I was doing, which was giving designers some really immediate tips to apply to make their jobs hopefully a little bit easier and so, I think you've done a really nice job of that. So can you talk about why you started Circuit Talk and then go ahead and share some of those tips or tricks that are around design for assembly that's gonna make designers’ jobs easier and smooth the time to deliver a good product in time to market.
Well thank you. You know the volume of jobs that we get - it does lead to chaos of sorts - but it also is a huge advantage in that we get to see every single mistake that anybody's gonna make. We don't specialize in a vertical industry so we don't only see mistakes related to a certain type of component tree. Name a component that's leading-edge, we've undoubtedly seen it and, so we see these things - and it's not just beginners, it's not just experienced designers, it's not just big or small or university - everybody makes the same mistakes. It's so complex and there are so many variables, so many new types of components. Geometries are shrinking and in parallel to that people have less and less time to design these things. Quite often layout isn't taught at schools, or it's self-taught. The experts who knew exactly how to make a layout work perfectly have retired now, or they've been let go, or things have changed so fast they can't keep up.
Mm-hmm.
So we see these problems every day. Case in point, one that I write about quite often relates to the QFN Quad Flat-Pack No Lead, and then the DFM. The DFM leads along one side. They have this big metal heat slug in the middle, looks like a very simple component, it's cool, it's small, has great signal characteristics. But most of the CAD software, when you try and use a QFN, the footprint is wrong. It comes from the library with the solder paste layer, not designed specifically for the component, so you've got to imagine flipping a QFN upside down. You've got a little row of contacts around the outside - very small - and then a big giant heat slug in the middle that covers almost the entire component. So most of the library components we found have a full aperture opening, so the solder paste layer is completely open for that heat slug in the middle. And what happens is you end up with too much solder in the middle, so the part floats up and the connects on the side don't connect.
Oh boy.
Yeah and this is even more prevalent with some of the open-source CAD software, or some of them with a lot of user-generated content, nobody told those folks how to make the footprint properly.
I see.
Quite often the manufacturers, in their data sheets, even specify it that way. But what you need to do is, to modify the footprint so in that center pad, you get somewhere between 50 and 75 percent paste coverage. So, you take out the default paste layer for the center pad and you put in a little windowpane-looking thing - problem solved.
Interesting. Yeah it's a little scary, unless you have a partner that's on the ball to what you can accidentally pick up off a data sheet or how to interpret that data right? So okay well, that's a good one.
Another one we run across these tiny little micro BGA's 0.4 mm pitch, some of them even 0.3 mm. I've actually seen a 0.24 mm pitch BGA. Yeah, some of the rules change with the bigger BGA's. You want non-solder mask defined pads, so you want the solder mask opening to be slightly larger than the little pad where the BGA ball’s gonna sit down.
Yeah.
With some of the 0.4 mm pitch BGAs, you want solder mask pad or defined pads, otherwise you get bridging.
Oh yeah, that makes sense.
Yeah, it kind of depends on the geometry of the solder ball, but that's a pretty common error as well. So you see these things that component manufacturers haven't fully studied, haven't fully published and they are just setting people up for problems.
Yeah, and what I have found - and not just in relation to components - I have talked to people who manufacture either components, or they manufacture laminates, and what's not widely understood is that sometimes the studies they’re doing is us.
Yeah we’re their guinea pigs.
Yeah, and then we yell and scream and we give them back data and then they produce overtime accurate data sheets. I was stunned to hear that, but it's absolutely true. They need to get stuff to market because the market is demanding it, and the testing is so complex and so widespread, and the applications are so widespread, that they can only go so far. And then the rest of the data has to come from real world.
Yeah the the hardware industry really is paralleling what the software industry did. We had open source software then open source hardware. With software, we started calling it ‘beta test the world’ because you couldn't beta test anymore, it's too complex.
Right, it’s too complex, so we become the beta testers and I don't think that's often understood. When I first understood it my jaw about dropped because I'm from the old school, like you are and it's like; wait nothing would ever go out that was not fully vetted or understood and tested, and things have just gotten so complex. And so there's just a hard limitation there, it's not a bad business practice or whatever, but it's a reality that I think is wise for designers and engineers to keep in mind - another encouragement to work closely with people like you, that can say, we've seen this already a bunch of times, we know what's going to occur here.
Yeah we've built our whole business around everything being wrong basically, start to finish. It sounds kinda funny, but It's all about this stuff probably isn't going to be right coming into us, so we've got to figure out how to make it work.
I don't know, like what happened to the world Duane? This is not how we started but here we are. Another thing you talked to me a little bit about, you had mentioned one time in a conversation, about polarity markings.
Oh yeah. That's that's maybe third or fourth in terms of the issues that we see here with diodes especially. Capacitors somewhat, but diodes even more so. Any kind of ambiguity, when you're dealing with machines, it's a problem. If you've got a barrier diode for example, it's backwards from what you would consider a conventional diode. So if someone marks it with a plus and it's a barrier diode and they're expecting us to know whether the plus goes to the anode or the cathode, we're gonna put it in the conventional manner, not knowing it's a barrier diode it's gonna be backwards so you can't use a plus to mark a diode. You might think minus, Also, does that mean negative or is that the lion on the diode symbol you can't do that because it doesn't tell us anything you've got to say K for cathode not C - because then we might think it's a capacitor, or the full diode symbol the down - lot of people will put in silkscreen, the mark that's on the bottom of a surface mount diode...
Uh-hu.
-which at first glance seems like it makes a lot of sense - but only if you give us the exact diode that you got the marker off of. I've seen two diodes 0.603s in the exact same package from the exact same manufacturer just a couple characters off, in the part number, and literally, on one the mark is the anode mark on the other it's the cathode mark. I've got to I've got to do a datasheet and I have a clipping from that data sheet on the Screaming Circuits blog that shows that it's got this part anode mark, this part cathode mark. I made the same mistake myself. On one of my boards I put the little marker on there and I gave gave the company the orientation and the CAD files, and then I made a substitution because one part was no longer available and used the other one - same thing but it was backwards because I went from cathode mark to anode mark. So, remove ambiguity. A few years ago I would say, it's okay to mimic the silkscreen - just give us the exact part. But with supply chain availability being such an issue right now, I would not rely on the mark that's underneath the diode because they can reverse if we have to substitute something.
Okay I'm gonna put a pause there and talk about what the heck is going on with supply chain. Stuff about diodes like these, very basic building blocks to design, why are we having problems sourcing parts?
Well we've been told a couple of things from suppliers. One is, they're telling us that the automotive companies are buying up literally an entire line. They'll come to a component manufacturer and say this particular part: I need all of your production, all of it and so there it goes out of stock. Internet-of-Things companies - the super, hyper-mobile devices are also causing issues because they're increasing the demand in the super small components. Well then the companies that make the parts don't have fab capacity to also make the larger ones so, some of the component manufacturers are telling us that they're going to stop making some of the bigger form factors 1206s 0805s even 0603s may become even more and more scarce because if they can make 0402 or 0201 to cover all that range they'll do it and not make the other form factors.
Holy... I don't know what to say about that - if I was a design engineer I'd be freaking out - this puts people in a really tough spot!
It really does and it's gonna change the way some things are designed. We have always had a policy that we will not substitute anything without explicit approval. Even looking at a bypass capacitor - 0.1 microfarad 16 volt bypass capacitor - in some cases you need exact parameters. There’s parameters you need to be exactly the same so you can't substitute. But there are also plenty of cases where it's just sort of by guess and by golly: yeah it's a 0.1, it could be 16 volt, 10 volt, 25 volt, 50 volt, whatever. If that's the case, people are gonna have to start being really flexible in terms of what they will accept for a component and maybe at some point the industry will have a flag on a bill of material that says: this one's engineered so it has to be exact. This one, just make it close.
Another thing, our industry is changing so fast, it's just a big reason why Altium and I've decided this podcast would be a good idea. Same reason why your Circuit Talk publication is a good idea because it's like we can't get the education out fast enough or get the news out. Like holy cow, why can't I get this capacitor? It's not a unique form factor specialized BGA they're capacitors! This is like bread and butter, so it's been puzzling to learn about that and I'm just really interested to see how these component manufacturers are going to deal with this and and again how designers are going to be forced to think hard about these parts it's really strange. Anyway sorry for taking a little side trip there.
That's important, it's a significant issue. We're being told this could last until 2020 and when we get out of this allocation, the industry is going to be different and, as I said, a lot of the bigger form factors consider moving all to 402s. It's more difficult to deal with these smaller ones but those are the ones, when the component manufacturers catch up, it's going to be in the smaller form factors because they can sell them to people building small devices as well as big. So think about that, be very, very careful when you're picking the specific component and tell us, and other manufacturers like us, what parameters are important.
Goodness that’s a great tip. You know I hadn't thought about it until just this minute when you were talking; I'm wondering if this will drive an uptick in embedded?
Embedded like embedded passives?
Uh-hu better passives.
I don't know I've been waiting to see that. I joined this company in 2005 and embedded passives were in the news at that point, and I actually made a prediction on the Screaming Circuits blog, that in ten years - I think I said - 80% of the passives would be embedded passives. I don't know that we've ever seen one. I guess technically you wouldn't see it because it's inside it.
No but you would know it was there, because I know it from my board manufacturing past, you would know cuz you would have to process it differently. It's a different process but I don't know what the cost trade-offs are there, but I've met Bruce Mahler from Omega and I've met some of those folks, and I'm just wondering if this allocation will drive, but I don't know what the cost trade-offs are or performance comparative. That makes me think, I need to call Bruce Mahler and get him on the blog because it's an interesting thing to ponder in lieu of what's going on in the marketplace.
Yeah.
Anything else you would mention off the top of your head that's something you see repeatedly that's a design for assembly thing that you would recommend designers to take a look at closely?
Well the polarity, the QFNs, BGAs as I mentioned. Something that isn't necessarily quite so obvious is the data files that is an important part of design for assembly. Ambiguity on a board is bad, ambiguity in a data file is bad. Bills of Materials, if there are parts in there that don't match the board, that's probably 80% of the jobs that come through here, have some sort of a Bill of Materials issue. So, double-check that that's accurate and that it matches your CAD files. If you can give your manufacturer the intelligent CAD files like an ODB++ or IPC 2581, that significantly reduces the chance of error, but then there's a little irony in there too that a lot of board houses still prefer Gerber's so we have seen cases where someone saves and then; oh yeah, I can give you the ODB++, but they forget they made a slight change and so now we have Gerber's that don't match the ODP++ so, make sure all of your files are consistent. Make sure the Bill of Material is clear and finalized. All in all if you add up all of the files issues that we see, that's probably one of the most common problems. I mean, I run into those problems for myself. I designed some boards and run up to the factory here, and I know how to do this, in theory I know how to do this, but I regularly make mistakes that my co-workers chide me for.
Well I think again, that leads to the complexity of the data that's available. The data sheets; whether they're right. I mean it is such a complex thing and it amazes me that we can even manufacture circuit boards and then put components on it and come out workable sometimes. Because it is such a complex process, I'm really glad that - actually I appreciate it - I don't understand all those steps but having worked for for both a really high end EMS that sold to tier one’s, very complex boards, and also having worked for a variety of board shops. I really appreciate the complexity in both those disciplines, and I think sometimes because a board shows up as a line item on a BOM that complexity sometimes can get lost on you. But yeah we're building things, even here Altium, into our own tool that helps, like an active BOM, things like that, that hopefully help. I think design tool manufacturers like us, I think we're doing a better job helping in that regard.
Right yeah, definitely!
Well the last couple items I wanted to talk to you about... well thank you for all that by the way, and again, we will share in the show notes your website. The Circuit Talking, I would recommend to anyone who is listening or watching - that you subscribe to Duane's blog or just Circuit Talk or whatever and we'll put all the links in because again, he's got his feet in the fire and runs up against these things as he said. Because they're putting through such a width of product. Like I used to work for an EMS, and like you said, it was a vertical. So we worked with military Tier one, and so the type of bores we saw was a niche, but you're seeing everything.
Yeah, literally I mean we worked on a camera board, the electronics of it, for National Geographic - it's a plexiglass globe, they drop it to the bottom of the ocean, it's got a chain on it and when the chain rusts through the camera bobs to the top and they pick it up again. We've got stuff being built for the 2020 Mars Rover so, literally down in the ocean up into space and and anything in between, we've built Ardium base stuff, real simple things, through holes; we built a board with five thousand placements. It's just all over the place and it's just absolutely the most fascinating place I've ever worked certainly, because of that.
Yeah I can see that and again, kudos for you - it's easier to do a quick podcast or write a blog post or produce a Circuit Talk that can go out to thousands of people and get that information out in that kind of global sense and be helpful right.
Yeah rather than tell one person at a time.
Exactly it's kind of a scalability of getting that knowledge out, so I really appreciate what you've done over the years. One thing I wanted to ask you about which it was a fun thing is about; I don't know six to eight months ago, I had the privilege to go with the Altium team for the first time, to a Maker Faire because we have Circuit Maker and Circuit Studio - Circuit Maker is free and and now we've bought a company called Upverter, which is also free, and in the cloud, and we also have Circuit Studio. So, we went there with those products and because of my position here as Director of Community Engagement, I hadn't had any exposure really to the Maker community, other than seeing stuff online, and I went and it was like drinking from a firehose. It was so much fun… goofiest things... it was so much fun. So, I'm walking the aisles, kind of collecting things to write about, or learn about, and I come across Duane Benson, wearing what looks like rap swag around his neck - it was like a clock you were wearing right, or something - he looks like a rapper and I'm used to thinking of him as this Duane Benson from Screaming Circuits and here you are, like fully immersed in the Maker space, and you had designed this device and had LEDs on it and I'm like: what are you doing here?
So tell me about how you've come to serve Makers. It doesn't seem like, from a profitability or a business model, that it would be a market that a company like Screaming Circuits would address. So how'd you get there Duane?
Well you could say that I'm a bit of a method actor, I mean I love... I've been designing small circuit boards for a very long time and writing the software for them for a very long time and one way of looking at it, is I'm a Hacker and a Maker who happens to be lucky enough to have a manufacturing facility. But more specifically, those Hackers and those Makers they are starting businesses.
Yes they are.
Many of those businesses become our customers whether they be crowdfunding or bootstrapping or getting investments, they are the future. The Maker community has a lot of students in it. It has a lot of weekday engineer weekend Hackers, it has a lot of people who aspire to start a new business and just such a wealth of creativity. And part of our mission I always like to look at, I'm just one person, we're just one company but if we can make our tiny little corner of the planet just a little bit better then we've been successful and all of those people who want to design electronics...
M-Hmm..
-We know what they don't know. I mean, we know what kind of problems they’re going to run across before they do, and so if we know what they don't know why don't we pass that off? And some of those people will have boards built with our competitors. Some of them will build them themselves, some of them will have us build them. Whatever, we're helping them understand this industry better. And we are helping them build better boards. That's what we really want to do. That's why we're at the Maker Faires ultimately. It does always have to lead back to more business for us, and it does. People see Screaming Circuits, they get the Circuit Talk and they read it, and it's Circuit Talk a Screaming Circuits publication so all of that winds its way back eventually, to helping the business here, and that's how we can afford to do it. But if we can help the business build and grow the business and help these budding designers - everybody wins.
This is why I love you, and love you guys. I just I love that philosophy, I love that approach. I try to live by an old Zig Ziglar thing and this reminds me of you and Screaming Circuits’ model that you just explained. Zig Ziglar used to say, you really can't have everything you want in life. If you just help enough other people get what they want.
Right.
So it's kind of knowing unconsciously that if you put good things out in the world, and you do the right thing, and you're ethical, and you have integrity, and you serve people, that good will come back to you and and you'll do okay. And I think that's a big key to your success actually, by kind of leading with service and and not ignoring the bottom line. We are in business to make money, we have to do that, or we're not in business anymore. So, I really appreciate that.
Well we're wrapping up now and I think you've listened to a couple of these podcasts now and so two questions for you. One are you a nerd or a geek?
[Laughter] I’m a Gunerd…
That's the best answer I've ever gotten yes you're a Gunerd.
Yeah, there was a time when those were really pejorative terms but I think nerds and geeks have taken it back and said, you know what, no we're not going to be ashamed of liking technology and loving it,we're proud of it. I mean, yeah so I’m a Gunerd.
Oh my gosh, I'm totally gonna steal that and use it somehow Duane, that will come back to haunt you later I promise.
[Laughter]
And the other question is, but I think I know what the answer is, if you've listened to podcasts. I always ask designers and electronics professionals in the end - this is ‘designers after hours’ - so because there is so much creativity involved a lot of people, like you said are Makers or Hackers, or they play a musical instruments or they're sculptors or whatever. So, what is your kind of guilty pleasure that you like to do after hours?
It would have to be photography. I chase animals around and take pictures of them, animals, landscapes, and then I have sort of a weird passion for old, decaying industrial sites as well. But photography would probably have to be my passion when I'm not playing with electronics.
That's so cool. Do you have a website where you share any of that or is it just mostly personal stuff and you keep your photos and share them with friends and family and whatnot?
It's mostly a personal thing I have had them on websites before but it's just my thing.
And and what do you mean about industrial sites?
Well, old decaying, industrial and rusty factories. There's a place here just north of Canby Oregon City and we've got a waterfall on the Willamette River and most people think of waterfalls as pristine, and nature and that's all wonderful, I love that. But this one: back in the 1800's they started building paper mills and they built a set of locks. It's the oldest - well till they just recently closed down - it was the oldest continuously operated locks west of the Mississippi. And so now, you overlook the river from a nice restaurant and you see this shut down, decaying, industrial plant and - well no it's not the beauty of the river - but I see a sort of beauty in the symmetry and in the the way people constructed these things. It's almost like an architectural dig, you can see things from a hundred years ago, from eighty years ago, from sixty years ago, and you can see the evolution of that, as this thing built up and then as they abandoned it, and there's just for some reason... I really enjoy that that sort of a view as well as the natural views as well.
They do have a really unique aesthetic and things have changed. It is kind of like a little time capsule and the rest is actually beautiful and sometimes the design itself is beautiful.
Yeah well thank you again, this has been fabulous and I'm sure we can talk more and more, but thank you so much for giving me so much of your time and sharing DFA tips and the story of Screaming Circuits, and we wish you continued success and we'll certainly share the website and Circuit Talk. And if there's anything else you'd like to share with us, give me a holler and I'll make sure we include those in the show notes.
Thank you very much, it's been a privilege to be on the show here, thank you.
Again this has been Judy Warner with Altium’s OnTrack Podcast and Duane Benson from Screaming Circuits. we look forward to seeing you next time until then always stay OnTrack.