Episodes
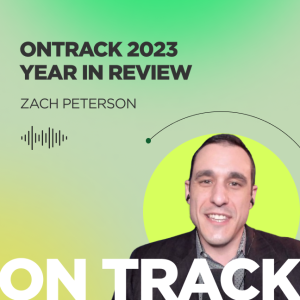
Tuesday Dec 19, 2023
OnTrack Year in Review 2023
Tuesday Dec 19, 2023
Tuesday Dec 19, 2023
Listen to the latest episode of OnTrack to hear a round up of the key PCB design trends from 2023. Explore themes such as evolving manufacturing dynamics, including shifts closer to the United States and Europe, influencing future innovations. Dive into the world of packaging design advancements and emerging trends such as robotic vision and new tools shaping the future of PCB design and the broader electronics market.

Tuesday Nov 28, 2023
Unlocking Collaboration: Altium’s New PCB CoDesign Tool in AD24
Tuesday Nov 28, 2023
Tuesday Nov 28, 2023
Dive into the future of collaborative PCB design with Altium's latest feature, the PCB CoDesign tool in AD24! In this exciting episode of the Altium OnTrack Podcast, our host, Zach Peterson, sits down with Wojciech Łaś, Product Manager at Altium, to explore the ins and outs of this innovative tool.
Discover how the PCB CoDesign tool allows multiple designers to work on the same PCB layout simultaneously, extending Altium's version control system. Learn about the compare and merge tool, a game-changer for detecting, comparing, and resolving conflicts in PCB layout files. Wojciech shares insights into the challenges of coordinating work among multiple designers and strategies to optimize the collaborative workflow.
Get a sneak peek into the future roadmap, including upcoming features like merge requests and improved conflict prevention. Find out how Altium's approach differs from real-time collaboration tools and the advantages of asynchronous collaboration.
Whether you're a seasoned Altium user or exploring the world of collaborative PCB design, this podcast provides valuable insights and a glimpse into the future of electronic design.
Show highlights:
- PCB CoDesigner Overview
- Unique Features of the PCB CoDesigner Tool
- Strategies for Collaborative Design
- Layer-Stack Locking and Rules System
- Future Developments: Merge Requests and On-Premise Availability
Links and Resources:
- Learn more about PCB CoDesign Coming Soon in Altium Designer 24

Tuesday Apr 11, 2023
Reverse Engineering: Is it Worth it?
Tuesday Apr 11, 2023
Tuesday Apr 11, 2023
Pierce Design’s Ethan Pierce will share his insight into reverse engineering with printed circuit assemblies. We will also discuss firmware reverse engineering.
Get Your First Month of Altium Designer® for FREE
Show Highlights:
- Introduction to Ethan Pierce and a quick preview of his upcoming webinar with the PCEA regarding reverse-engineering
- How to acquire reverse-engineering skill sets?
- Retrofitting a system versus creating a net new ecosystem of products
- Is reverse engineering cost-effective?
- Ethan advises designers to keep records and documentation as much as possible. “take as many pictures, take as many pictures, photos, notes.”
Links and Resources:
- Connect with Ethan Pierce on LinkedIn
- Visit Pierce Design's website
- Register for Ethan Pierce's Webinar: Reverse Engineering PCBs: How to Recreate a Lost Design
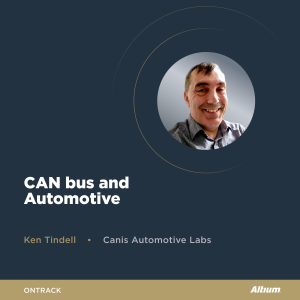
Thursday Mar 16, 2023
Security on CAN bus with Ken Tindell
Thursday Mar 16, 2023
Thursday Mar 16, 2023
In this episode, we will learn so much about embedded CAN bus, for automobile security and performance straight from the water host, Ken Tindell the CTO of Canis Labs.
A lot of interesting facts about cyber security and automobile hacking that you would not want to miss! Watch through the end and make sure to check the additional resources below.
Get Your First Month of Altium Designer® for FREE
Show Highlights:
- Ken Tindell’s background and how he got started with CAN bus and CAN security
- Ken worked with Motorola on designing the MS CAN—the first CAN controller that did all the buffer scheduling correctly
- Ethernet and CAN coexist in autonomous vehicles’ architecture, Ken explains how
- There are two types of major attacks on the CAN bus: attacking the physical wiring and attacking the computer that has access to the wiring. Zac and Ken talk about the mind-blowing advanced techniques of hacking automobiles
- Story of irony. A friend of Ken in automobile cybersecurity had his car stolen
- The biggest car-hacking horror would be through the cloud — cloud-based APIs to phone and at the same time CAN bus protocol hacking on the transceiver pins
- CAN HD, an augmentation for high speed and guarding the CAN bus
- Canis Labs is in the works to provide real solutions for security on CAN bus
Links and Resources:
- Connect with Ken Tindell on LinkedIn
- Visit Canis Automotive Labs' website
- Check out Ken’s Github Page
- Watch related podcast episodes:
Get Your First Month of Altium Designer® for FREE
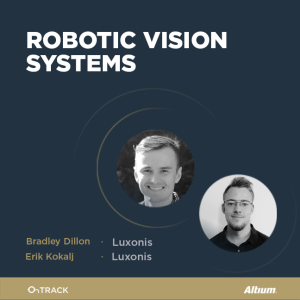
Tuesday Feb 14, 2023
The Rise of AI Interference
Tuesday Feb 14, 2023
Tuesday Feb 14, 2023
In this episode, we are fortunate to have two key personalities at Luxonis, a hardware, firmware, software, AI, and simulation company. Erik Kokalj, director of application engineering at Luxonis, and Bradley Dillon, CEO of Luxonis discuss how and who can benefit from AI technology.
Tune in and make sure to check out the show notes and additional resources below.
Show Highlights:
- Introduction to Luxonis and its founding on April 2019
- The liDAR and radar as an imaging technology, Erik briefly explains the technology behind it
- Bradley shares why they decided to open-source some aspects of their platform and design
- Luxonis’s AI training, AI conversion, and AI deployment onto hardware are all open-source, for their customers can quickly develop their own model and then deploy it on the device itself
- Future design updates, miniaturization, and thermal management
- What are some of the industrial applications that are utilizing the Luxonis imaging technology? Beekeeping was unexpected!
- Robotic applications on robotic cars, Zach and Erik talk about action recognition on top of object recognition
- Bradley talks about series 3 products and what’s coming in terms of capabilities – processing power, more AI inference
Resources and Links:
- Connect with Bradley Dillon on LinkedIn
- Connect with Erik Kokalj on LinkedIn
- Checkout Luxonis Website
- Watch Luxonis featured on Altium Story: How Luxonis uses Altium 365 to innovate AI Vision systems faster
- Connect with Zach Peterson on LinkedIn
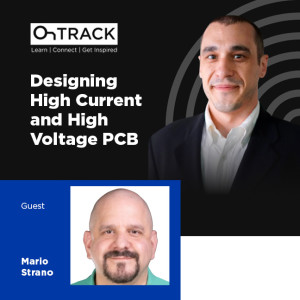
Sunday Jul 17, 2022
10-Ounce Copper PCBs and Design Library Migration
Sunday Jul 17, 2022
Sunday Jul 17, 2022
When you hear about 10-ounce copper PCBs, high current and high voltage come to mind. In this episode, we will have a deep dive discussion on designing heavy power boards with Mario Strano. Mario is the senior PCB designer at Nikola and also president of ECAD Central. He will share with us his 16 years of experience in PCB design and the migration services he provides through ECAD Central.
Watch this episode or listen on the go. We’ve touched on many other interesting topics, such as setting up clearance and creepage rules and a 57-ounce copper board.
Altium 365: Where the World Designs Electronics
Show Highlights:
- Mario’s background and professional path as PCB Designer and Component Engineer
- He is currently the only PCB designer at Nikola
- His expertise includes but is not limited to designing 10-ounce copper boards, real heavy power boards, HMI boards, human-machine interface boards
- Setting up creepage and clearance rules for heavy copper was a challenge to Mario during his transition from SQL Semiconductor to Avnet
- Mario and Zach discuss more 10-ounce copper PCBs
- Zach was amused to hear about Taiyo Kogyo’s 57-ounce copper
- The Japan-based company developed proprietary processes that allow them to do things like Bus Bar Embedded PCB
- Mario briefly shares his experience as a component engineer at Avnet for six years
- The two discuss the tantalum capacitor shortage in 2018 and compare it to the current semiconductors shortage, which started in 2020
- How is the supply chain shortage affecting PCB designers, and how are they working around it?
- ECAD Central, an Altium 365, Concord Pro, and Altium NEXUS Database service provider – setup and configuration, database migration
- Mario compared migrating data to “like moving mountains”
- Is mirroring parts between two systems possible? Mario explains what can be done. Definitely not a simple drag and drop operation, though!
Links and Resources:
Connect with Mario Strano on Linkedin
Visit the ECAD Central website
Learn More about Taiyo Kogyo and their 57-ounce copper boards
Watch related podcasts:
Easily Find Electronic Components for Your Next PCB Design
The Benefits of Diversifying PCB Industry Supply Chain
Connect with Zach on LinkedIn
Full OnTrack Podcast Library
Altium Website
Get Your First Month of Altium Designer® for FREE
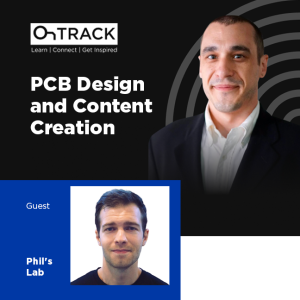
Sunday Jul 10, 2022
PCB Design Education Through Content Creation
Sunday Jul 10, 2022
Sunday Jul 10, 2022
In this OnTrack episode, Zach and Phil of Phil’s Lab Youtube channel exchange ideas on how they can stay on top of their PCB design game or learn new things. Phil Salmony, a successful youtube creator with 64.6K subscribers, shares with us how he was introduced to PCB design, his early career, and what got him to start his own Youtube channel. This is a fun episode. Watch it through the end and check out the additional resources below.
Altium 365: Where the World Designs Electronics
Show Highlights:
- Whiteboard – an essential piece for PCB design-related content
- PCB design education from the university, theories, and ideologies versus PCB design for the real world
- Phil shares that DSPs (Digital signal processors) are the coolest thing, and he has a dedicated section of them on his channel
- Zach and Phil exchange opinions about their consultation and PCB design jobs
- How do you go about learning new things? Zach and Phil have their share of different ways to acquire information to help them better their skills
- Learn through well-documented samples or PCB design projects and reverse engineer
- Seminars with experts and attending conferences
- Taking online courses like the IPC - CID (Certified Interconnect Designers) and PCEA CPCD course
- Youtube videos and keynote presentations, e,g, How to Achieve Proper Grounding By Rick Hartley
- One of the most asked questions in PCB design is about grounding. Phil and Zach suggested a couple of books supplement for PCB design
- Phil talks about how he got started with PCB design
- Designs and chip shortages and supply forecast, what to expect in the next few years?
- The value of connecting with your (youtube channel) audience for content ideas
- Altium Academy and Phil’s Lab history on Youtube and future projects
Links and Resources:
Subscribe to Phil’s Lab YT Channel
Connect with Phil on LinkedIn
Visit Phil’s Lab Website
How to Achieve Proper Grounding By Rick Hartley
Watch Podcast Episodes with Rick Hartley
Electromagnetic Compatibility Engineering by Henry Ott
Grounds for Grounding: A Circuit to System Handbook by Kai-Sang Lock
Get Your First Month of Altium Designer® for FREE
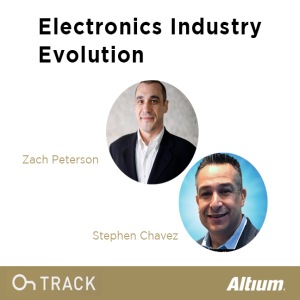
Wednesday Dec 15, 2021
Mastering Your PCB Design Tool as the Industry Evolves
Wednesday Dec 15, 2021
Wednesday Dec 15, 2021
“One of the fundamental things that I'm very passionate about is continuous development.” - Stephen Chavez
We are thrilled to have Stephen Chavez on the podcast again! He is one of the respected Electrical Engineers in the electronics industry. Stephen is the chairman of the Printed Circuit Engineering Association (PCEA) and oversees the design team of a renowned military aerospace company. In this episode, Stephen will generously share his work experience and how he sees the evolution of the electronics industry. This is a not-to-be-missed episode as it will give you enough courage and motivation to keep on learning to become a successful electronics and design engineer of today’s generation!
Altium 365: Where the World Designs Electronics
Show Highlights:
- Stephen and Zach’s best advice on how to get on top of things as the electronics industry evolves
- Stephen’s career progress in the electronics industry and his affiliation with PCEA (Printed Circuit Engineering Association)
- The need for cross-collaboration as designing changes and gets complex
- Altium 365 offers seamless collaboration in the cloud
- Digital thread or model-based design
- How’s the process today?
- The evolution of toolsets
- The difference between the tools of today and the past
- Taking advantage of the tool you’re using versus the manual approach
- The importance of tool training
- PCEA’s mission for the next generation engineers
- Secrets of PCB Optimization with Rick Hartley
- What do you need to consider when designing circuit boards
- Designer’s triangle
- Layout solvability
- Performance
- Design for Manufacturing (DFM)
- Intricate details that go into designing a PCB
- What it takes to fabricate and assemble a printed circuit board especially for young engineers
- Mike Creeden on Empowering PCB Engineers through PCEA
- Manufacturing aspect - filtering your suppliers
- Mistakes engineers make when choosing the materials for design
- Balancing success in circuit design
- Engineering learning practices in the past vs today
- MCAD, CAD for tool collaboration
- Autorouting in RF designs
Links and Resources:
Previous Podcast Episodes with Stephen Chavez
- Stephen Chavez Calls on PCB Designers to Get Involved
- Is IPC-CID Certification Really Important to Your Career?
- Stephen Chavez on Staying out of Your Comfort Zone
- Judy Warner and Stephen Chavez on the Approachability of the Pros
Printed Circuit Engineering Association (PCEA)
AltiumLive 2022 Connect: Now open for registration
Connect with Stephen Chavez on LinkedIn
Connect with Zach Peterson on LinkedIn
Watch Zach’s latest Altium Academy courses on Youtube
Read Zach’s articles on Altium’s resource hub
Full OnTrack Podcast Library
Altium Website
Download your Altium Designer Free Trial
Learn More about Altium Nexus
Altium 365: Where the World Designs Electronics
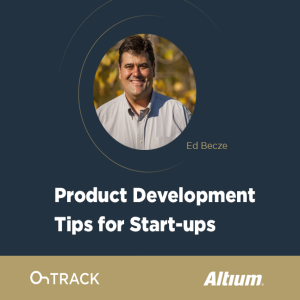
Tuesday Jul 27, 2021
Key Factors of Thoughtful Design
Tuesday Jul 27, 2021
Tuesday Jul 27, 2021
“Engage your suppliers early on the design process” - Ed Becze
Everyone wants a lower price, and often the “real cost” is not realized until it’s too late. In this episode, Ed Becze of Pegmatis, a highly experienced R&D company with end-to-end product development capabilities, joins us to help start-ups and design engineers like you avoid electronic product development failures.
Altium 365: Where the World Designs Electronics
Watch the video, click here.
Show Highlights:
- Introduction and the interesting origin of Pegmatis’s company name
- Ed explains the foundation of a good product development process
- A thoughtful development plan mitigates risk early on—engage vendors and suppliers early on the design process (understand parts, availability, vendor capabilities aligned with your product)
- Holistic understanding of electronic product development: strategy, cost, and your design team’s experience level
- Start-up challenges, how to prevent failures:
- Understanding the risk of “development by demo”
- Address the lack of system-level design experience (use external expertise if needed)
- Don’t trust the data sheets—only 5% of chipset providers give adequate design rules to follow. The rest, you are on your own.
- Manufacturing test is absolutely critical—test equipment and test development are often overlooked
- Engage early on the design process. Ed stresses the benefits of nurturing your relationships with your vendors and manufacturers.
- Successful product development relies exclusively on your network—find capable vendors
- Supply chain intelligence, plan ahead when coping with supply challenges
- Cost reduction—do it, but follow the process that is within the constraints of what you intended to create.
- What are the costs of NOT thoughtfully designing? It’s huge! Money and time. Delays inTime to market are extremely expensive.
Links and Resources:
Pegmatis Website
Ed Becze on LinkedIn
Full OnTrack Podcast Library
Altium Website
Download your Altium Designer Free Trial
Altium 365: Where the World Designs Electronics
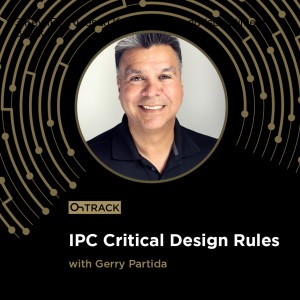
Monday Apr 12, 2021
3 Key IPC Rules to Know, Follow and (sometimes) Break
Monday Apr 12, 2021
Monday Apr 12, 2021
Listen to this episode with Gerry Partida.
Altium 365: Where the World Designs Electronics
Show Highlights:
- Introduction to Gerry Partida and Summit Interconnect
- Why knowing and following IPC standards are critical for Design Engineers
- AABUS: What is it, and when to use it (Edge clearances)
- Removing non-functional pads
- Watch for 3.5 mil minimum dielectric rule IPC 2221. Work around
- How to access standards, talk to your fabricator: IPC Expertise
- CTA: Follow Gerry on LinkedIn for tips and tricks
- Summit Interconnect Website
- IPC website
Links and Resources:
Gerry’s LinkedIn Profile
Summit Interconnect Website
IPC Website
DFM Article: PCB Front-End Engineering
Altium 365: Where the World Designs Electronics

Tuesday Jun 23, 2020
How Calumet Electronics Joined the Fight Against COVID-19 With Altium 365
Tuesday Jun 23, 2020
Tuesday Jun 23, 2020
The town of Calumet, with a population of barely seven-hundred, was once the booming epicenter of Michigan’s upper peninsula mining industry. When the industry began to fail, unemployment skyrocketed, and the townspeople sought local solutions for creating jobs that could sustain the town’s families.
Rob Cooke, Director of Engineering Services at Calumet Electronics Corp, joins the OnTrack podcast to discuss the Open Source Ventilator project, his experiences implementing Altium-365, and the radical decision business owners in that small town of Calumet, Michigan made more than 50 years ago, which led to the rise of Calumet Electronics Corp.
Altium 365 Podcast Listener Discount
Show Highlights
- Intro to Rob Cooke: how he got involved with Dugan Karnazes and the Open Source Ventilator Project.
- From copper ore to copper pours: Calumet, Michigan’s fascinating backstory.
- So what’s the hold-up? The right tool for avoiding excessive holds and other barriers to expedient design.
- Reality transcends the map: Altium-365 demos vs firsthand experience.
- The impact and implications of sudden hyper-efficiency at the designer, fabricator, and assembler level.
- The shock of realtime: “This is what can happen when things don’t go on hold!”
- Rob offers some final thoughts on the purchasing and quoting paradigm.
Resources:
- Rob Cooke on LinkedIn
- Calumet Website
- Open Source Ventilator Video
- AltiumLive 365 Demo
- Altium 365 product page
- Open Source Ventilator Project (OSV) Combats Ventilator Shortage
- Previous Episode with Rob Cooke: How to Conquer Data Package Problems
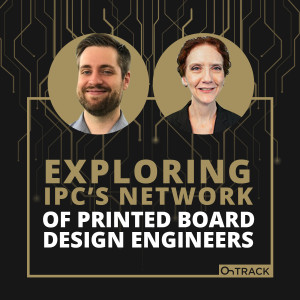
Wednesday Jun 03, 2020
Exploring IPC’s Network of Printed Board Design Engineers
Wednesday Jun 03, 2020
Wednesday Jun 03, 2020
The renowned global trade association known as IPC has put together a network of printed board design engineering affiliates under the name IPC Design. IPC Design’s affiliates are comprised of PCB design engineers across the globe who are working to advance the art and science of printed design engineering.
IPC Design’s Patrick Crawford and Teresa Rowe join the OnTrack Podcast
Work from Anywhere. Connect with Anyone.
Show Highlights
- What is IPC Design, and what is its primary mission?
- Increased global presence and participation: How IPC is molding its future.
- IPC Design’s worldwide buy-in, its fresh new participants, and how the quarantine has affected participation.
- Has productivity gone up since quarantine?
- Lessons in remote working and the importance of taking time for yourself.
- Between January 2020 and now.
- What’s in store for the future: IPC’s collaborative content model.
- America, Europe, and Asia: IPC’s leadership group and global design committee.
- IPC Design is looking to fill a leadership role in Asia.
- What’s in it for you, the designer? Teresa and Patrick count the ways designers will benefit from IPC Design.
- ”Let’s start up a chapter!”: How individuals, student groups, and companies can get affiliated with IPC Design.
- Translators of the world, connect! How IPC Design can serve and collaborate with STEM groups all over the globe.
Resources:
Teresa Rowe on LinkedIn
Patrick Crawford on LinkedIn
IPC Website
Link to IPC Design webpage
Link to IPC Design enrollment page
Patrick Crawford’s video presentation on IPC Design
Realtime with IPC
IPC CEO John Mitchell on the Impact of COVID-19 on the Electronics Supply Chain
Work from Anywhere. Connect with Anyone.

Tuesday Apr 14, 2020
The EMC Doctor is in: Ken Wyatt on EMI and PCB Health
Tuesday Apr 14, 2020
Tuesday Apr 14, 2020
The OnTrack Podcast is pleased to welcome Ken Wyatt (also known as the ‘EMC Doctor’). Ken began his career as a designer in the aerospace industry, and later worked for Hewlett Packard, where he found that his background in RF and Microwave engineering helped prepare him for his role as an Electromagnetic Compatibility (EMC) Engineer. His work has since taken him all over the world, where he develops and provides in-house training and delivers presentations and live demonstration; definitely unique among presenters!
Retiring early in 2008, Ken has since become a prolific author, co-authoring three books, including his latest, in which he identifies why products fail to meet EMI/EMC regulatory standards: ‘EMI Troubleshooting Cookbook for Product Designers’.
Ken currently provides seminars on a variety of EMC related topics—touching on subjects not often taught at the university level. He also provides EMC consultation, EMC compliance and precompliance testing, design reviews, and training services for commercial, military/aerospace, scientific, consumer, and computing industry sectors.
See What's New in Altium Designer
Show Highlights
- Ken lays out his career path, from his beginnings in the aerospace industry, to his current role as a consultant.
- ‘EMI Troubleshooting Cookbook for Product Designers’—a quick look at the book Ken co-authored with Patrick G. André.
- Addressing the prevailing trends in stackups and board design in general.
- Old habits die hard: Why the PCB is the heart of most EMI and EMC issues today, and pitfalls to avoid to move past these issues.
- Signals as the flow of electrons in copper traces and wires: How our education may have left out the whole story with respect to high frequency design.
- How simultaneous trends toward diminishing device size and the Internet of Things contributes to desensing and other issues on PCBs.
- Staying “in the know”: Keeping up with our evolving understanding of the physics of PC boards and signal propagation is always challenging. Ken lays out some ways designers can stay up to speed.
- Why Electromagnetic Compability programs at the university level are few and far between, and how Missouri University of Science and Technology stands out among them.
- Case Studies: The trouble with dog trackers and blood transfusion machines. Ken discusses some challenges he’s come across in the field.
Resources:
Short video on the book with co-author Patrick André
Ken Wyatt on Twitter: @emc_guru
See What's New in Altium Designer
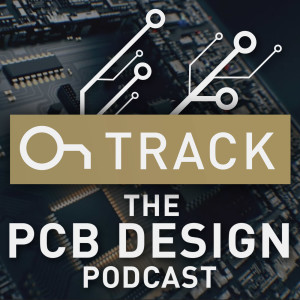
Tuesday Jun 26, 2018
Mary Elizabeth McCulloch and Project Vive’s Medical Device Innovations
Tuesday Jun 26, 2018
Tuesday Jun 26, 2018
Speech Generating Devices and speech assistive devices on the market today are expensive. Insurance policies are complicated and not everyone who needs one is always covered. Meet Mary Elizabeth McCulloch, she’s changing lives by giving a voice to the voiceless with Project Vive and Voz Box. A recent biomedical engineering graduate from a family of engineers and makers, Mary and her team are inventing Speech Generation Devices in new wearable forms by working closely with the people who most need them. Listen and find out how Mary and Project Vive are using low cost sensors and changing lives by leading the development of innovative medical devices and technology.
Show Highlights:
- It was really all about the access, not just in price, but in the sensors.
- Low cost sensors that could change someone’s life. These are sensors in our cell phones that can be used, and we’re really adapting that for the disability community.
- Wearable for independent communication - worked closely with the person using the device so that the design was modified to fit real life.
- Loop of instantaneous feedback - Gave the person using device a voice and a vote.
- People with disabilities are problem solvers.
- This is about innovation that is informed by people within the disability community.
- This is a great way to break down the stigma of disabilities.
- Cisco - 100k prize
- Projectvive.com - accepts donations via fiscal sponsor
Links and Resources:
Learn more about Mary and Voz Box
Let us know if you know anyone who needs Project Vive technology.
Or read more about Project Vive in this month’s OnTrack article.
Hey everyone this is Judy Warner with Altium's OnTrack podcast. Thank you for joining us today. If you've been listening to our podcast I would equate today's podcast with being the desert or the cherry on the sundae. It's a great story and a great woman that I look forward to sharing with you. Mary Elizabeth McCulloch who has a startup called ProjectVive. Before we get into our conversation with Mary Elizabeth please remember to connect with Altium on Facebook, Twitter and LinkedIn and I would also love to connect with you on LinkedIn or on Twitter, I'm @AltiumJudy and also, if you prefer to watch this on YouTube rather than listening just go to Altium's YouTube channel, click on videos and you'll see all of our podcasts there. So that is all the housekeeping. So let's get into the good stuff.
So, about a week or so ago I got a message through LinkedIn - an introduction to this young lady Mary Elizabeth, and she was telling me about her company and we've since connected, had a couple conversations and I'm so excited to share what this young innovator has done. So Mary Elizabeth, welcome my dear I'm so glad to have you and thank you for taking the time to to meet with me today.
Thank you it's such an honor to be on this podcast.
Ya no, it's truly our honor. You know technology does so much for us in our lives but what you're doing is such a great human story. So tell us a little bit about your educational background and tell us about your parents and background, cuz I think that does a lot to set up your story?
Yeah, yeah awesome. So I guess educational background; I studied Biomedical Engineering at Penn State, I graduated spring 2016. I was always really interested in Science and Math in high school - what else? So my dad, he was a Physics major at Penn State, he's gone into Engineering for really his whole career. He's worked a lot with CNC controls in the milling machine industry and then my mother, she has a Biology Degree, a Mechanical Engineering degree, and some Biomedical Engineering graduate work - actually on the artificial heart at Penn State - so you know my family's background and my own.
Impressive. So you shared with me a little bit about - I had asked you: did you always know you were gonna go into engineering? So tell us a little bit about the things you and your dad used to do when you were young cuz I think it speaks to your story?
Yeah so, growing up my parents really had an interesting - or an interest in - farming and fixing things around the house and not going out and buying something new and really just trying to understand how to repair motors like rototillers, tractors, things like that and I guess my dad would also buy little chemistry kits for us to work on in the basement and yeah, we kind of had a blast with that. But also, my parents always really encouraged me to try new things, and one of those new things was to go, after I graduated high school, to Ecuador and I decided to be a Rotary Exchange Student and so I spent a year in Ecuador and outside of high school I decided that it would kind of be cool to volunteer in an orphanage, and this orphanage specifically was for children and adults with disabilities. And this is kind of one of the things that it I had never really had this like experience coming from you know a student who grew up in the middle of Pennsylvania and there I was and I really was taken aback by a woman who was in a wheelchair sitting by the window who had cerebral palsy and couldn't speak. So I started asking her yes and no questions - wasn't getting a response back and then after, a couple days of working with her saw that she had voluntary movements. If it wasn't a blink of an eye and I figured out what was a yes movement and what was a no movement, what was a tremor, um and started kind of communicating with her in this way. And I - it kind of hit me that there were a lot of other individuals not just only in this orphanage but in this country who had these type of disabilities and didn't have someone there who was asking them these yes and no questions and figuring out what they like to do, what they didn't like to do. And then really the lack of opportunity because of their disability that they had. And I was, you know, 18 years old at the time, was going back to the United States to major in Biomedical Engineering, and I really thought you know, I would really like to create something to fix this and who did I tell - I told my dad - and my dad right away, was like: you can fix it, you can - we can figure it out you know, just like these little ideas that I had growing up that dad just was - got really excited about.
Yeah I mean they're - I guess I didn't go into it a little bit, but growing up there was sometimes like when I was learning how to draw flowers and stuff he's like: we could, you know make, a milling machine that would draw these into bed boards and you can program it that way, and anyway, it just kind of was a natural thing for my father to just when that inventor side of me came out, for him to encourage that and not be some crazy idea but something that yeah would take a lot of work but I knew it was something I was really passionate about and you know I'm 26 now, and I'm still just as passionate about it and I'm really glad that my dad pressed me to move on with it.
Well I was so impressed in our conversation where I almost felt like you were set up in this life to do the work you're doing because I remember you saying that when you were answering the yes and no questions, that you could see her countenance light up and she was in a better place after being able to communicate and I don't think any of us can imagine what it would be like to live with the frustration of not being able to communicate in a fluid way. And there are speech assistive devices available to people that are mostly affluent so what's the cost of speech assistive devices, on the market for people who have the money to buy them?
Yeah, so you know, a speech generating device isn't just you know, a box like a tablet, it includes things like a mount, to put it on their wheelchair. It also includes different sensors you know, if they can't do direct selection and select on a board sometimes they need a sensor and that they can control with their foot, or even with their eye movement. So if you're looking at a full speech generating device, for a low-cost one six thousand dollars, for a full one you're looking at fifteen thousand dollars and sometimes even more, so it's a thing that has you know, made some headway on getting covered by insurance. But having a communication device covered by insurance can cause issues as well. Because sometimes it's not medically necessary, and then of course, people that don't have insurance, that can be really hard to get one.
And is that kind of the disconnect you saw I mean, obviously people that are in Ecuador don't have that reach or that capacity. So is that sort of an area of compassion for you to go: they don't have access?
Yeah absolutely. It was - it really was all about the access and not just in the price but also in the type of sensors to give people access to you know, control speech generating device not just with a finger, but with eyes. And knowing that you know, there's so much technology out there and I know in the beginning we prototyped with Arduino and Raspberry Pi and these really low-cost sensors that could like change someone's life and just like you said, can you imagine not being able to communicate and connect with someone? And to think that these low-cost sensors could allow someone to make relationships, to share their dreams with and that was definitely one of those things that you know, as a freshman engineering student really gave me a passion to bring these types of sensors that we are using every day you know, in our cell phones and in all this technology all around us but really adapting that for the disability community.
So once you were in college, you have this idea, your dad's encouraging you. What was the next step for you? How did you start innovating and deciding to actually make a device?
Yeah, so I guess as soon as that, the first thing I did was decide that I was going to make a device. I think that was just like that was...
-that was a first step right?
That was the first step. The training and the business model, that kind of all came later, but I guess the first thing that I did was, I took a trash can, I carved out two sticks, put a potentiometer in the middle of them and hook that up to an Arduino Mega and basically wrote a program that allowed someone to calibrate it to say what angle, or the threshold that they needed to to make a selection. And then had these WAV files playing that basically went through menus. So for example, one was like food, the other was emotions and so if they kick the foot and they move the potentiometer for the angle that it needed, with the width of threshold that would open up the food options and then they could you know select something like: I want to eat, or I want to cook, and then yeah made that a checkmark. Then I made a glove, so that somebody who could just you know, twitch their finger also press a finger on a surface and really the whole time I was thinking about the individuals that I worked with in Ecuador you know. At one point I was like: Christina could use this..
- Ah, I love that.
-she was really - and she still is - I actually just saw her last summer, she's doing wonderful. But um really great foot control but nonverbal cerebral palsy like the things that she could do with her foot, I would give her you know my cell phone, and she could click down on a button. So I was thinking like, what is - - what are ways that I can create something that was wearable for independent communication?
Because a lot of times these people didn't have caregivers that are around them all the time to make sure that their communication device was in the right position. But then as soon as I had a working prototype you know, it was like I gotta test this you know. Let's see if this works and if what I'm doing is completely you know, not gonna work and that's where I found Arlyn. Arlyn is from Johnstown Pennsylvania, she has cerebral palsy. She's in a residency home and she also has great control of her feet - very strong legs, similar to Christina. And we used the foot sensor for her to share her poetry for the first time. And were able to really adapt our program to do that, and right away there were things you know, that didn't work. We tried an insert into a shoe, and she was like you know that doesn't feel comfortable I don't want anything in my shoes - and really just started this design process with her you know and seeing what she would be comfortable wearing and also what was working and what was efficient. And how did that integrate into her daily life and be something that she did want to use to communicate every day.
I love that you were collaborating with her, and that you gave her a voice to say, I don't like that in my shoe right. So to create this loop of instantaneous feedback, you gave her a voice, but you also gave her a vote on how she would interact with this device, how would I - that feels good, that doesn't feel good, this works for me and, by the way, for those that may be listening or watching, I will share the videos with Arlyn, they will make you tear up instantly. It's - this woman is a poet and her poetry is beautiful, and she is now sharing her poetry for the first time in her life because of Mary Elizabeth's ingenuity.
-and Arlyn you know, she - she is so smart, and really our design has so much of her in it. And I talk about this sometimes, I know I talked about it with you. With people with disabilities - just you know - being problem solvers because they have had to overcome hurdles their whole life. Like Arlyn, she sets her VCR with her foot, so many people don't even know how to set their VCRs she's doing it...
That's hilarious [laughter]
-so many people don't even - caregivers who come around, they don't know how to work this VCR and you know, to make sure that, that experience and that perspective that she has, is in this assistive technology that we're developing and I think it's a really important population that really gets overlooked in technology and innovation and especially innovation, for the disability community.
Well you have no idea how much I just love you and what you're doing. It is such an amazing thing. In just the few videos that you have Mary Elizabeth, you can see the light in her eyes and you can see the camaraderie between the two of you and the deciphering and working together on how to make this the best fit for her - it's really a beautiful thing. And so, at some point in college, you got it working right, you got a working prototype right? And did you show that to your dad at some point or how?
-Oh he was involved in this, this whole point.
Oh he was, okay.
-he you know, he had and still does - in CNC controls, so you'd have little parts that we would need to mill out so we'd be talking you know: can can you make this design for us? We didn't even have a 3d printer at the time so - we have a 3d printer now which makes rapid prototyping - but yeah, yeah he was you know really alongside of us. But also it was, taking engineers - and a lot of times you know this happened with us - was people that had all this tech skill but never interfaced with people of disability and seeing where they could apply their skills, and how much an impact that could make on a life, and on many lives. And I think really, for my father, that was you know, a really aha moment, because you know a lot of times - people with disabilities - when you meet them for the first time, and if you're not used to it - you might think that they don't have anything to contribute, and that they don't have ideas because of their communication disabilities.
Right.
And me - when my dad saw Arlyn give us design advice - he was like: oh my god you know, here is this woman in the middle of Johnstown with all these ideas. We've been working in our lab and on the bench for a year, and like we didn't come up with these things, and right away she was like: hey why don't you try it just as you know, a switch here, and place it here, move the - let's categorize the menus in a different way to make them more optimal and just all these ideas and it was really just a great way to break down the stigma of disabilities while helping people.
I love, you know obviously, I've been in this industry for a long time and I love what technology can do you know, for people's lives. And I love that you've been able to make that connection. I love that, hearing about your dad that his eyes are so wide open and I think that is something you've really made me aware of, that makes complete sense to me now, it seems like an obvious thing is people that are not speech capable would be amazing problem solvers, they would have to be and so to have those as your collaborators. What a genius idea right, plus they're gonna be the ones using it so also to have a vote in how this is. So, you continued to develop it and then did you patent it at some point?
Yeah so actually, my freshman year I filed for my first patent - provisional patent. Full application my sophomore year, which is a awesome you know. Two and a half - three years waiting to hear back from the patent examiner - but we were awarded our first patent November 2016.
Exciting.
Yeah it happened like two weeks before our IndieGoGo campaign went live, so there was just a lot of excitement going around that and yeah, so that was our first one down, hopefully many more to go, and we're always innovating new things around here. But yeah that was a huge, huge accomplishment for me.
Yeah not many have their first patent awarded while they're in college - that's pretty neat. So you got your patent, and tell us about - you had mentioned on the phone about - I think it was in your junior year about Penn State coming up with a Young Entrepreneur program and so you started filing for some competitions or some things that would actually give you some funding to help move you forward?
Yeah, so really in my junior years I kind of had this realization that if I was gonna make the impact that I wanted - a large social impact - I was gonna have to scale. If I was gonna scale, I would need a really sustainable business model to fuel that. So luckily right around ProjectVive's birth, Penn State and President Barron launched the Invent Penn State initiative which started Happy Valley Launchbox, which was a no-cost business accelerator downtown for students and community members so I, we applied for that - we were the first ones in - and so being the first cohort team, it was like an empty building, no one was there at the time, and yeah it was actually really cool for us 'cause we went from like being a dorm, to like having this awesome space. But then, they had, an NQ competition where we pitched ProjectVive in front of a shark tank kind of set up at our University, and it was actually aired on WPSU and we got $17,000 from that - which was huge for us at that time.
That's a lot of money yeah.
Yeah and that really just gave us validation, that what we were creating was something that was needed. It also pressed us to do a market analysis and realize that wow, there are so many people that need these type of devices that just can't afford it, or don't know that it exists. So yeah I took advantage of that in college.
So, before we go forward. Something we didn't mention, but I think it's good to insert here is - so jumping ahead for a moment - what is your plan to market the Voz Box at one, two, go to market?
Yeah, so you know I really have a passion for developing countries and also South America. So two things of how we're gonna go to market: One is - there's a lot of trade shows for people with disabilities - so there's ATIA the Assistive Technology International Association, ASHA, and where you can set up a booth and speech-language pathologists, parents, teachers and also a bit of alternative communication users, or people with disabilities that use speech generating devices will come to learn about new technologies. So that's definitely one way. We're also doing kind of grassroots - by reaching out to local disability organizations here in State College, that also have chapters all over the world, so and definitely all over the US - Easterseals, we've done a collaboration with them.
So what is your price point right now - we're projecting, I'm not - we won't hold you to this but what's your projected price point that you'd like to sell it for?
Yeah our projected price point is $500.
$500 ?
Yeah that's for the full communication device. And then also, we're gonna be doing a lot of open source devices that can help you and ways of creating mounting systems on your own, to even get that lower.
It's incredible. Like I see that as such a, I mean, lowering the barrier to entry to almost anyone right. Because I wanted to mention the price point before we move ahead - and so you won the $17,000 then you entered a couple other competitions tell us about those?
Yeah, so we applied for the ALS Association and Prize for Life Assistive Technology Challenge, where we were one of five out of 87 teams, it was an international competition, and we were flown out to Ireland where they brought in...
- Wow.
-Yeah, and they brought in ALS patients from all over the world to try out our technology which was a really important thing for me. I've had two uncles who have passed away with ALS and even though I had a lot of work with people with children and adults with cerebral palsy ALS is a terrible disease and 75% of people with ALS will lose their voice. You have two to five years to live after diagnosis, and to see our devices, that I had created you know, thinking of specifically people in this orphanage but then realizing that people like my uncles could also use these devices. We had someone from Iceland, another person from Japan. We've developed also these little blink detector glasses that you can basically blink to select, and he used those and he loved them, and he was able to spell out a word and just to see someone from Japan, to meet us in Ireland try out our devices, and realize that so many people around the world - not only with cerebral palsy - but with ALS and Rett Syndrome, it just really opened my eyes to the impact that this could have. And also getting this support from the ALS Association was really awesome.
That's an incredible story. You have a video on that also right Elizabeth? Okay, so we're going to share that one as well in the show notes. And the last award that I think you mentioned to me had to do with Cisco right? So tell us about that one. Well I'll let you tell the story, but because I know you had an IndieGoGo campaign too, and a patent, you had lots going on. So spell it out however - how you know - I may be getting these things out of order so.
Actually you're not.
Okay good.
So then - this is actually last summer - we applied for the Cisco Global Problem Solvers, a challenge which was inaugural, it was also the first Global Problem Solver Challenge that they've had. Some recent projects these days are the guinea pig for everything. But yeah, so we applied for that , and I really could talk about my mission, and working with you know, people in Ecuador, and just the low price point and how this - this wasn't just for people in the US, for people in Ecuador, but also we did a little work with a professor in communication disorders, who was in Sri Lanka, we sent a device out to to her where she used it with a boy who was 17 years old , with cerebral palsy. And it's just so many places in the world, don't have access to this type of technology. And in schools and education also, in just adult community life. So we applied for that, made a video for it, and they had this People's Choice Award. So the main award was for $100,000, and the People's Choice was for 10k. And I got everyone to vote for us, you know I sent out to my professors, 'vote for us'! you know ProjectVive, all my friends and family and all of Arlyn's friends and family too. Then that - the day that they were gonna announce it, I kept on refreshing the People's Choice page and all of a sudden I realized that you know this team from Costa Rica won, and I was like, oh man you know, we didn't get the people's choice! And then I checked my email, and it said: 'Congratulations Grand Prize Winner Cisco - - $100,000.'
Oh my gosh, you won a hundred grand!
I know, and I was like, what's going on? That's not 10k, and that I mean, I'm still - I still can't believe it. And you know this - it's been a couple months now - but that just really pumped into our research and development and got us to where we are right now in creating our final product. And yeah, we're just really, really thankful for that support.
That's amazing. I gotta say I'm not surprised, but it's the best story ever. And then so lastly, tell us about the IndieGoGo campaign and - and your Road to Ten Voices that ended up being more than ten voices?
Yeah so we did an IndieGoGo campaign: Journey to Ten Voices and we - I was actually in Ireland for like the end of it - but we raised enough for 14 voices actually, so that was really exciting. And really yeah - that's really allowed us to reach out to the community. For instance, a recipient of one of our Journey to Ten - well 14 Voices - was a 16 year-old, who lives an hour outside of State College and he's doing great. And we also helped him out with a wheelchair gas pedal so he not only is using his speech generating device with an e-sensor, but is also able to independently move around which has been so cool and he's just learning so much from having a device that really wasn't reliable before we helped him. And then you know, just learning from another person, so it's been really cool.
That's something else, we have pictures so when Mary Elizabeth introduced herself to me on LinkedIn she sent me a screenshot of him getting his Voz, and you've never seen a kid smile this big in your life you know. I thought he was gonna rip his ears off with a smile - he was just so happy and it just makes - you can see me also, I got this smile-grin talking to you this whole time. It's just a beautiful story. So now you have seed money right? And so tell us where you are now, and kind of what the next year or so holds as you forge forward?
Yeah - so really, it was a great thing that this whole time we've been working with users, also talking with you know doctors, and teachers that we did the I-Corps Program, where we interviewed 50 people from all over the world. Parents, speech-language pathologists, doctors, teachers, augmentative alternative communication users themselves, and really took one - you know, the user testing that we did, our feedback, what we've learned, the market analysis that we've done - and then also these interviews, to test our assumptions and make our final product. So really what we're developing now - it's the next thing of our beta product and creating something that we believe is going to be able to scale, that we can bring to places like Ecuador and Sri Lanka, and that we're gonna be able to make a sustainable business model on because I know I talked to you about this. We really want to make sure that once we give a voice that we don't take it away, and I think that it's been a great thing that during college I've been able to experiment and test and really have this quick feedback loop and creating something that will make a long lasting impact so that's what we're doing now.
I think that really shows so much a vision on your part actually Mary Elizabeth, because I can't imagine - again I can't imagine giving someone a voice and then having to take it away right, that would be so devastating, and that you've had the foresight to make sure that it's sustainable and and that you're looking at it, not only from an engineering and visionary, but a very practical standpoint to make sure that you're gonna build a solid business. So I really appreciate that about you.
Yeah there's got to be someone there to answer the phones when something goes wrong.
Right, right so I love that you're actually building a sound company and and having good mentors and, and helping you along, and that you have a really solid vision on this. Well what else do we need to talk about? So you're heading towards a scalable product. I think I'll insert here that I got to meet Mary Elizabeth's and project Phoebe's CTO, Trip what's Trip's last name?
Miller.
Miller, I got to meet Trip Miller and we had a call, so one of the roadblocks that they ran into, is that they were using basically a free design tool that got them this far but they they needed something farther and God bless Altium. They were able to sponsor Mary Elizabeth and ProjectVive, and give them a license of Altium Designer, so they've been having a lot of fun trips - being like a kid in a candy store...
[laughter]
I know, we really have, I mean the trouble that we have gone through and also just working with other collaborators and not being able to get the right schematics for them and and having to basically transfer, not only our Altium files or - I don't want to say that exact names -
Yeah I know, I was trying to avoid that too. Some companies' schematic...
[gestures] yeah.
But we've just been able to very quickly start up and I know that it took us about you know four hours to start up our other PCB programs and with Altium, like within an hour, we were creating traces, which was just awesome. So we are so excited and just being able, it's - it's accelerated our development and we're very thankful for it.
We feel lucky, we feel like we get to remove - we get to have the privilege of removing a roadblock for you and just let you charge ahead my dear, so good good for you and Trip. And I'm really glad that we really have the privilege, to do that for you. So we are gonna list in the show notes everything about ProjectVive, the Voz Box, your - like anything you want us to share, let's share it because it's a beautiful story and all of us that love technology, love to see kind of the social aspect of doing good. Doing good in the world, through use of innovation and technology and you're kind of like a STEM-girl poster child which is really fun for me as a woman in tech to see how you came up, and your parents, how they inspired you, and this is really great. What else should we share with the listeners? Have I skipped anything - what else can we talk about, have we missed anything?
Um you know, if you really do feel moved by ProjectVive's story, we do have a fiscal sponsor, so we accept tax-deductible donations and if you go to Projectvive.com - you can hit the donate button or just support us, like us on social media and share our story, and if you have any family members that would be interested in our technology, let us know and we would love to help.
Great - well thank you this has been the highlight of my day and we will also be sharing Mary Elizabeth's story - I've interviewed her already and she will be also in the OnTrack newsletter, coming up in June, and so keep your eyes open for that. If you do not subscribe to the OnTrack newsletter, you can go to our resource hub and subscribe - there's a newsletter tab there, and you can subscribe. So if you're not already subscribed, you can subscribe there and again in the newsletter we'll include all these links in that because we certainly want to put her on the Altium platform, and celebrate all this young innovator's doing. So Mary Elizabeth, you are the best, thank you so much for spending your time today I know you're a busy woman and we'll stay in touch and thank you again for all you're doing, we just think you're wonderful.
Thank you so much Judy, and thank you so much to Altium, and we're just very blessed, thank you so much.
Thank you. Again, this has been Judy Warner with the OnTrack podcast with Mary Elizabeth McCulloch of ProjectVive, we look forward to hanging out with you again on this podcast. Until then, remember to always stay OnTrack.
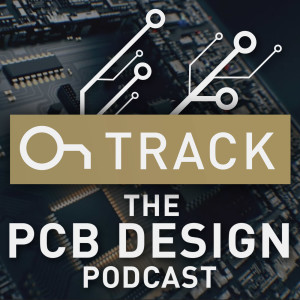
Tuesday Jun 19, 2018
Tuesday Jun 19, 2018
Bil Herd shares stories and design wisdom from years of experience as a hardware engineer, most famously at Commodore. Starting out self-taught, Bil found his way to working around brilliance and some of it rubbed off a little. Learn about his interesting journey from TV repair to Commodore, Hackaday and beyond. Today, Bil is self-employed and focused on networks, high-level architecture consulting and hardware projects.
Show Highlights:
- I never forgot how to do hardware design. It’s fun to be able to do that. I’m working on an Altium project right now.
- You get to be imaginative for a couple days, and then you spend the next couple months paying for it looking at every single line item, every footprint and trying to catch where your brain was wrong.
- Commodore Hardware lab, splitting bus for video and hired to lead the team shortly after.
- Going after a swag bag offered by Adafruit from an MIT Open hardware conference resulted in a video series with Hackaday.
- Almost all the errors I’ve made in CAD systems were related to parts I’ve made. For parts and footprints - you need to have someone check your work.
- To start a new CAD system - make a trash board, force yourself through.
- Process to start learning a new CAD system: Open CAD > Get Overwhelmed > DRINK
- Making a board on a new CAD tool. First I make a trash board knowing I won’t use it. Then make a real board, using all the rules.
Links and Resources:
See all show notes and video here.
Hey everyone, this is Judy Warner with Altium's OnTrack Podcast.
Welcome back.
Our audience continues to grow and we thank you for joining us again, and I want to give a shout out to Steven Newberry from LGS innovations who took away always marking his diodes with a K, and so many of you have chimed in and help driving actually who we have on the show and the topics we discuss. So thanks so much for joining. If you would please connect with me on LinkedIn or @AltiumJudy on Twitter and Altium is also on LinkedIn, Facebook and Twitter, and remember we're always on YouTube as well as on your favorite podcast apps.
So thanks again for joining and hold onto your hats because we're gonna have a little bit of a history lesson tied in with today's best practices. So today our guest is Bill Herd, who is actually a figure of history and he has a Wikipedia page that you will have to take a look at. So for those of you that are probably, I don't know 40s and above, might remember the Commodore personal computer. It was one of the first, I'll let Bill fill you in all the details, but I remember vividly when I was in my early 20s, my dad coming home with a Commodore 64 and it was all the rage and he thought the world is forever changed and I'll never ever use all the 64k that I possibly have.
So Bill, welcome and we're so glad to have you and can't wait. We're gonna tell some stories, you're gonna give us some design wisdom, so thanks so much for joining us.
My pleasure. Actually I do describe myself as a recovering Commodore Engineer the active recovery never stops you've just gotta keep trying to get better.
Well, I'm sorry but based on the background behind you I'm not sure about your recovery.
Okay - I've relapsed a little [laughter]
So, briefly tell us what you're - are you working now as a Consultant, you know like your own entity I forgot to clarify that with you?
Yeah actually I'm self-employed so to speak, I owned an ISP for about 15 years and had 16 people and we did all that and then it ran its course as ISPs do, and so I do a lot of networking and high-level architecture consultation, but I never forgot how to do hardware design. So actually you caught me in the middle of doing an Altium project right now, where we're going to a limited quantity but I just went through all the steps - all the dirty little details getting a PC board out, so it was kind of fun to still be able to do that.
I love the way you put it, 'the dirty little details' there's a lot of those right?
You get to be imaginative for a couple days and then you spend the next couple months paying for it by looking at each and every line item and every footprint and trying to catch where your brain was wrong you know, way back in the beginning.
Yeah well, so I also noticed you have - as I've gotten to get acquainted with you a little bit - back in the days of Commodore and the early days actually of the personal computer business the words nerds and hackers weren't really around but seeing you sit there in a Hackaday shirt with that lab behind you, I would say you are the quintessential original geek or nerd what do you have to say about that?
Well, one - we did call it home computers, back then the PC hadn't been invented yet, and I also mention I've never been to school for any of this. I was a - basically a high school dropout - and ended up in the service, and went back and almost got my degree. I own like a library book for the money $3.42; for a library book, in English class where me and the teacher just couldn't make it work.
So about three years later they sent home my diploma with my sister just going: here you'll need this someday. I used to say I was self-taught but what really happened, self-taught got me into a couple good places and then the education really started; working around really smart, really brilliant people, that's where I got the education that made it so I could do a product from beginning to end. So I was fixing TVs, got my TV Repairman License at the age of 17, in Indiana. You know and sometimes they'd answer the door and didn't want to let me in, because I got long hair and I'm carrying tube caddies and they're like: who are you? I'm like, van out front, TV repair, and people fed me cookies when they saw me fix their TV sets.
Right well we will share Bill's Wikipedia page and there are some awesome pictures of this long haired hippie, with this cut off denims...
Hey don't tease me about the shorts, it was 1980.
Hey I'm sorry, but I wore shorts just like that so yeah, so we will share that because there's a lot of history and fun and great pictures that I think you'll enjoy hearing. So tell us a little bit about how you got into the whole Commodore thing and then we're gonna dig in and give our listeners some really practical advice on those nitty gritty details you talked about, and then we'll wrap up with some more fun stories. So just briefly give us an overview of Commodore and Hackaday?
Okay if I back up just a little bit - I started at a digital scale company in Pennsylvania making instrumentation, so there I learned to do very accurate stuff with very good grounding. I understood analog and RF spectrum and all that, and it was all hand taped right. Well a guy named Terry Fisher who I just got through working with again, so after 35 years, we're still doing it and he was on Altium this time. So when I got to Commodore I had the background for how to make something expensive work. And then you just take that and you just shake it and it comes out of your head cuz now you've got to make it cheap, cheap, cheap, cheap.
Yeah.
And people are mad at me these days because they say: oh I have a 30 year old Commodore and it just failed! I'm like: it was designed to last five years. You should have put a switching supply... what? To put a dime more into it I'd have been fired if I did! So I got my job almost by accident at Commodore. I mean, there's a whole story here and I'm going to - let's just say I blew the interview like three times and still got hired. You know what, not even taking in my resume you know? But so I got there, and they didn't know what to do with me, and I read in a book that I was actually hired as a Technician. They just knew they could use people like me and then they sat me down, the guy was named Benny Prudent, and he said: well here, study all these software manuals. So now I was gonna be right for a programmer - I could do 6502 programming.
But for a disk drive - I'm like: that sounds like the most boring thing in the world, but sure. And then I walked into the hardware lab and I saw what they were doing - they were splitting the BUS for the video - which back then I was doing it at home - and that's why I said: I just built something at home where I actually don't wait till the vertical retrace time to ramp and two weeks later I was in charge of the project. The guy was leaving, they didn't have anybody else, so now I'm a Project Leader at Commodore within a couple weeks.
Oh my gosh, it was like the Wild West was it not?
Oh absolutely and I loved it and I brought a certain 'animal house' to that, because we had lost a lot of talent. I mean there was people like Chuck Peddle who designed the 6502, he's gone, but his cigar's burning in the ashtray. The chair's still warm right. So you knew that these people had been there, but they're gone - and there's these kind of older, stogier guys and me. And pretty soon it became an environment where shoes became optional, so we definitely made it into what we wanted to and you have to do that when you work 20 hour days.
That's crazy so you're sleeping in the office or not sleeping?
My record was 11 days without leaving. I had an air mattress, I would actually hot bunk with the technician so I would get something designed like 2:00 in the morning, check the air mattress out and they would build it for me and I'd go catch an hour to sleep and then they'd come back and kick the air mattress and say: it's built, and just taking showers out of the sink - things like that.
Well we'll talk more about some of your fun Commodore stories because I know we'll really want to dig into those a little bit more. But tell us also about your involvement with Hackaday?
Yeah it's actually interesting, that I used to watch Adafruit's Little Saturday Night Show right and they would do this thing where they'd give something away and usually it was a product and I didn't go for that as much because I could just - their products are so cheap I could just buy one. But one time they had been to the Open Hardware Venue - a conference - and it was actually at MIT I think - and they asked a question and I went right to a web page, found the answer because they were giving away the swag bag, so I said, that I'll go for! So in the swag bag was some cool things but one of them was a - it was like an Octopart - only it was somebody else's version of it. Well they're owned by the people that owned Pacada.
So I start talking with them, I ended up a Beta Tester, and the guy realized I just never shut up, that I'm always telling stories right? And so pretty soon he puts me in touch with Mike the head editor at Hackaday, and I'm doing the same to him only in emails, and finally he's like: all right that's it, write stuff or shut up, and so we came up with the video format because it just - it works for me - it works for my personality and I am a high school dropout which means my English ain't so good anyway, so the video works better for me.
Yeah well we will also share those for listeners here - I've seen a few of them and he is perfectly suited for that. So I'll share that as well for you wannabe hackers. So let's dig into some immediate content that I hope will help engineers and PCB designers that are listening to us. You have told me - how many EDA tools have you used over a year period?
Yeah I made it all up, hardly any at all [laughter]. No it had to be like seven, eight, or nine, depending on how you count them and to what degree. But going back to the 1980s when a workstation cost fifty thousand or a hundred thousand dollars and you couldn't get them as a home user or even as a small business and so, we started it. We started with hand tape and the cool thing with that is, if you can do good hand tape, you can use a tool like a CAD and do more. But you still have to be good to begin with right? You have to understand the principles and nowadays it's more common for engineers to do their own PCB layout but I'm still of that school that: do what you do really well, and use somebody when possible that does what he does as good as you, that's why I use a guy like I said, Terry Fisher.
He's as good and he knows when to ask me questions and I know when to shut up right so we have a good relationship for that kind of thing. And we started on Mentors, which actually we designed chips with, but he started on a system called a side card, and it was a card that plugged into the backs. Well when he'd start moving parts on the PC board everybody's computer slowed down right. These chip designers and stuff because it's on the VMBus, it's taking the cycles directly, so they give Terry his so - he actually he goes by Fish. They gave Fish his own VAX so now he's got a three hundred and fifty thousand dollar CAD system to lay out pc boards and so that's the 1980s, and in the Mentor, we - I hadn't really even seen a real mouse like we use until Sun's came out. It had a scratch pad so I actually grew my fingernail into a point so that I had a built-in stylus on my index finger - so yeah just genetically modified kind of you know... [laughter].
That's funny - so with all of those changing of tools which most people that I know, that are designers, once they get proficient on a tool they'd rather die than change tools because it can be such a painful process. So tell us about changing tools. If you have to do it, what is the least painful path?
Well management will always want you to do that right in the middle of a project right and that's - it's pretty key to not try and - we actually moved our hardware labs right in the middle of a project one time too. Just kind of in the same... But if you're going to change programs, realize that they're just tools, and after you've changed a couple times you start to go: okay I know how this play goes and and you do a couple of the same things and you sometimes learn and really appreciate your old tool and sometimes you learn that hey, the new tool's better. But they're no two the same, especially in CAD where there's so many complex things. So I think people picking up tools - I saw it a lot with EAGLE - what they did, and they did an amazing thing for the maker industry and the home users - even though I hate the program.
if you're a professional, you just go: what, I have to drag the trace off the screen to hit the menu? this is like somebody put a GUI on a command line program. Well guess what? EAGLE's were GUI on the command line program back in the old days. So you know the false attractiveness of something like EAGLE was, it did have huge libraries right, and especially for boards because I mean these, Arduino boards - I can't deal with the mechanics of them, they're not on the center's, I'm used to all that - but what you really have to come down to when you do a CAD system is, realize you've got to make your own parts at one time or another, so you might as well get proficient at it. And if you're using libraries you might just be using somebody else's problems.
So even if you do use somebody else's library - it's like you've gotta still vet the part. Right, so just realize that you're going to have to make your own parts. And then there's things like BSDL importing and stuff like, if you're doing a 250 pin FPGA, you don't want to hand-do that either, so there are tools to help you avoid the mistakes. But almost all the errors I've ever made in CAD systems are related to the parts I've made where - I actually have data books here not data sheets - a guy said: yeah you use the word book don't you? And while you're looking at the book, making the part, I've done simple things that I'll never catch myself - by having like D7 to D0, instead of D0 to D7. When I see what I think I want to see, and that's it, the mistake is in there until somebody else catches it. So we used to always have somebody else check our parts you know, in footprints or the same way I still think.
So that's the first thing, is realize you’ve got to make your parts and then I recommend you just sit down and trash a board - try not to ruin your library in the process - because you could screw up libraries right. But then throw that board away and start again. This time trying to obey every rule you know how, and actually even if you don't produce the board actually obey all the rules, look up every command you don't know that you actually need, and that's kind of how I started a new CAD system.
So for our audience, Bill sent me a few notes for the point of our conversation here, here is a note that he wrote: Starting a new CAD, do a couple of projects early on - sort of what he's talking about right now - his first line is, 'open CAD - get overwhelmed - drink' [laughter].
Yes, it can be overwhelming! It's like my drill sergeant said when I went through basics: 'we know it hurts gentlemen, you don't have to tell us' and we're like, oh I'll keep my pain to myself. It's the same thing: I'm supposed to be overwhelmed, okay let's you know. So you open it again, and you start looking for what you know. So there are some things you need to learn the quirks of upfront. Like how do you do a BUS? Everybody does it slightly different, that nomenclature, whether it's curly braces, brackets, whatever. And an 8 10 dot dot 8 zero - it might be low to high, it might be either way, but you got to learn those things. And interconnects, how to make sure that a part's really hooked up. One CAD system I was on, was called Ulti Board by National Instruments, and the DRC wasn't catching the fact that parts looked like they were hooked up, and they weren't. Well, how do you catch that?
Well yeah, how do you catch that?
Yeah so you've got to - you go around jiggling your parts and it's stupid you know, so do a good DRC and you know, Ben, when he looked over my shoulder to check my router - from Hackaday, Ben Jordan. He gave me an - actually a compliment that I took, which was: oh it's nice to see you have all your DRC errors fixed. Well I'm old enough, I don't remember fixing them, but I'm old enough that I know I would have fixed them. Cause that's it, that's your last chance to catch that you have a net floating, even though you don't know it. Whether it's a misspelling, even capitalization change, something like that. So yeah, you got to learn all those dirty deeds and details.
I was just talking to John Watson on this podcast about a week ago, we talked a lot about libraries and the same subject. It's like a theme that most headaches seem like they begin and end with the parts libraries and even having a data sheet that's correct or hasn't changed in the last five minutes. How do you address that?
I still have data books [laughter] - no, it's still like going over it, and over it, a couple of times and having somebody else look as well. I'll still take a highlighter to a schematic sometimes just if I feel I'm getting confused, out comes the highlighter to help me get more confused.
[laughter]
-at the end hopefully I get it.
That's funny! Okay (I keep bumping things sorry about that) so okay.
Let's talk about hidden nets...
Okay go!
I hate them [laughter] hidden nets are where somebody thought let's show up DIP package or something and we know we are hooking it up to +5 and grounds so there's no point in cluttering the schematic with it. Well my attitude is how do you know it hooked up to +5 and ground? Nowadays it's 9 +5 and ground is +3.3, 1.2, 1.0 - - so yeah whoever came up with that, they need to have something I don't want to say something bad happen... [laughter] They need to miss a CES deadline or something themself.
So it's the invitation for failure is what you're saying?
Yeah you can't check it, you make assumptions and that's where problems start so yeah.
Would you say that making assumptions is one of those easy pitfalls for designers to fall into?
Yeah, thinking SOIC is a size. It's not you know, there could be white body, skinny bodies, and it's like: oh but the picture looks like - no. You better learn to have - one thing is you have to learn with new CAD packages, is how to measure things. And you need to do that, and then look to see oh it's .43 inches or ... and I - one time I almost missed the fact that the the lead pitch was 0.5 instead of 0.75. That wouldn't have fit!
That would have meant instant failure. You made a comment about assembly drawings being readable what did you mean by that?
You know as parts got smaller the silkscreen no longer - it's not as important because of assembly techniques but if you still want to measure - you can't get that little silkscreen anywhere near the part sometimes, so you end up with an assembly drawing where you had to like put all these silk screens where you now want them inside the outlines and all that so it's like you can't use the silkscreen for an assembly drawing like the old days. You have to do a whole new one if you want to be able to find the part. But now these days what I do - but I'm working on a really dense... or troubleshooting, I actually keep the CAD open and I do the - jump to component - and find it that way it really is faster to use technology sometimes...
[laughter] sometimes.
Sometimes, at least I don't hand etch my boards anymore.
Yeah.
Remember that, the seventies?
I always say, because I was in the bare board industry for years, sales and marketing-wise and we would take people, walk through and do surveys, plus I actually worked on a shop floor for a short period of time like, I'm gonna die of heavy metal exposure man, the chemicals we had in there. I remember walking into a planing room at the first board shop I worked and my skin just burning, yes burning, just poor ventilation and there was sulphuric acid in there.
I'm told you can't have plating or PC board manufacture in New Jersey, that they've just kind of made it so you can't do that.
Well there's that - there's a little bit of toxicity going on in the chemicals.
Right, and at Commodore we made the ultimate printed wiring board printed circuit board right which is a chip - it's just really, really small, and we polluted the groundwater and you can look this up, but we had to buy dedicated lines for like 11 neighbors, and then we had those golf course sprinklers in the back aerating the ground water. Well my first day there I mean they're just literally spraying it in the air hoping the VOCs evaporate right.
Oh my gosh!
I parked too close my first day there and I come out and my car's covered with this sticky stuff right and not only that, I had parked under a tree so now the leaves are stuck to my windshield with this and to try and peel them off - they just break - and they're like: oh yeah dude, don't park there man, that's in the water.
Like I said, it was the Wild West days I mean.
Still a Superfund site I'm told.
I bet, like it's frightening - it's frightening and I'm glad we've gotten our act together a little bit environmentally oh my gosh because literally we could all die from those toxic...
Yeah I remember the day my dad brought home mercury to play with you know.
I remember my neighbor was an engineer - he brought home mercury to play with and we'd watch you know, roll it around on our hand or whatever, crazy! Forget about playing with it - you know putting it in your teeth we would like, oh here, pour it in my hand, let's roll it around, isn't that cool?
Yeah and you put it back in the jar and it's never quite as full as you started right because you're leaving a certain amount on the floor...
Good memories but we might die young, just saying...
[laughter] So when you start a new CAD program, do you just jump in and start designing? How do you take that on if you're gonna take on a new CAD, what's the way you approach it?
Well as I said, I kind of I go in knowing I'm going to do a trash board, it's all about just hooking some stuff up knowing that you're making mistakes and then I try and do something more real and try and really obey the rules and that's where it starts - that's how you're learning from page to page cuz every CAD system's slightly different, but it's kind of like how you think. You drop a part, you try and put a wire on it and the kind of mistakes you'll make is not having a clear way knowing how you want to do all the resistor values in the world right. Do you make a part for each resistor value, or do you use a generic part and assign the values? And those are things you just have to figure out yourself on each CAD system I think.
So I mean, I honestly don't know how it's done. I have lots of compassion for my engineering friends who are also laying out boards who really got no serious, formal training in PCB design, but alas they are laying out boards and then they get thrown a new tool like... So do you just hop on it and jump in and swim?
Remember, it's a tool too and they have some really great tools like things that'll help you plot RF noise on the ground plane or thermal or something but you know, at the end of the day that's not necessarily real life. It's a tool you know, so it's an opinion, and it might be a faster, better, more colorful opinion than we used to get with an old thermal probe. But you just got to kind of try it and if you work around people who can look over your shoulder they'll save you a lot of time - especially hot keys and stuff like that. And that's probably one of my pet peeves is I don't like having to rely on hot keys and that was even before I lost a finger, so now some of the hot key combinations are literally beyond this old man's ability to do without using my nose and stuff it's...
How did you lose a finger?
I tore it off!
Dare I ask?
I just caught my ring on something and I stepped eight inches off something - it stripped it off the bone, we have pictures on the web of that also. But I used to work at a trauma department and I've flown with a 103rd combat medics, I've been captain of a rescue squad. So I look down and I just go: I know where I'm going today - I didn't even tell my wife right. I figured she's away at a quilting bee, having a good day, the next day I was: Hi, uh, lost a finger and she got mad at me for not telling her.
I would get mad at you too... just saying like: oh Chee how's the quilt work? Good what did you do? I just lost my finger.
Yeah, yeah well my son actually looked at it and we took pictures - by the way I had to wait half an hour for an ambulance and being a former ambulance guy that was just like - that was an insult on top of injury literally. But I wanted him to think of it clinically and not be freaked out by it so we took pictures and stuff like that and then I told him, I said: well I'm going to - don't tell your mother - but I'm gonna leave with these ambulance people now and I'll be home probably tomorrow, because I know how things work, and he comes running to the door and he goes: dad, dad what's the key to unlock the Xbox? I'm like: okay you're gonna be fine by yourself. First time he was by himself, he's thinking about the Xbox so, all right!
Oh my gosh you crack me up. What else do you want to talk about relative to CAD tools? I'm looking at my notes here - you were talking about something - you talked about the buses, nomenclature and index based even that you'd said you hate those. So what else did we not cover?
I think the main thing is just how productive can you be? How well is it designed? And I was impressed by early CAD, which came out at like $4.99 in the 80s and we were like: whoa! I mean it's like that old monochrome purse, now there's PCs right - late 80s and the things you can do where if you copy a bunch of address lines, you can tell it when to paste it, auto-increment all those address lines as if I was continuing to do them. So if I grab a 0 to 7 and I paste it, now 8 to 15 is done for me. Well you can fly, when somebody has thought of things like that to do, you can go rogue. And it has to be controllable - sometimes you go, no I really wanted a zero to seven and - but there's tools like that, that can really make it. So, just the ability to double click and there's a new segment just like the one above it, tools like that are real important to me where I've just spent too many hours drawing in each line by hand.
Right, yeah I love when - well since I've been here at Altium, one of my fun parts of my job has been to help connect our developers with hard-working designers where they can say: do it this way, we don't work that way you know, it's really nice when CAD tools will actually get together with the guys that are watching and just watch 'em work and go: oh - because again it's easy for developers even if they've laid out boards - to make assumptions right. So I really love it when tool manufacturers actually take that into consideration and I love that we're doing that more and more these days. BOM distributor integration?
Uh it's probably the one thing we didn't have in the old days BOM integration where, and even picking the footprints, we had a three-ring binder of IPC footprints and that was always a step where errors could occur. I'm thinking this way, PCB designer's thinking that way, wrong footprint gets in there. But then even now, we can with Altium, for example, you see the part as it's a digi-key or arrow and you can make an attempt to select a part. Now; sounds great, but you end up getting into trouble when you go: oh wow, now I have to redo it for real, for the auto, for - I still call it auto insertion - for the pick and place. You know or, guess what? The stock status isn't quite what you thought it is, there's a delay in there and so now you're stalled, so you still have to, I think in my world, I still do a final BOM as a spreadsheet literally. But I get a lot closer in the tool. In the old days we were using microfiche if you didn't have the data book right? So nowadays it's integrated so it - again you have to be careful - it's a tool, it won't do your work for you and that's the thing.
I was just going to say - I've worked with also like hiCAD and now KiCAD... however they pronounce it.
I know, I never know how to say it either.
Yeah and it was good in that you could add modules to it. It was bad in that you could add modules to it. I kind of wanted already the 3d viewer working - ready to play with it and stuff like that. I'm really impressed with Proteus instead of EAGLE for that low-end market, not up here where Altium is, but that's when I was shooting little two inch by two inch boards for Hackaday and I'm doing a complete design every month and doing a video, and so I design it and it gets a minute of video time right. Then I throw it away to start on the next one. So it's called ARES and unfortunately the other one is ISIS, (nobody likes that name anymore), but that's the product name and they have an amazing auto router in there that'll get you a good completion, whereas if you've ever tried EAGLE it's like why do I even try the auto router you know? So that turns out to be in, and they singled out the maker market by including Arduino in issuing 80 mega parts in simulation and firmware simulation so now you can simulate it as if you've written the code. You don't even need to build the board to see if it works. And that's a cool feature. And we didn't talk about simulation - almost all CAD tools these days do include SPICE of some sort or a SPICE portal or something like that, and that's useful if you're down in the analog stuff especially. Again still just a tool. I've seen SPICE lie horribly to you, and you think it's going to work and it's really an artifact of zero volts or something like that.
Well there's a lot of talk these days about - because so many really capable designers like you, and like many people I know have learned this over a lifetime right - so if you're a new designer where are you gonna on board that outside of just one-on-one mentoring? Like any clues?
There's some good YouTubes out there, but I haven't found where you can - one, I don't have the attention span to watch somebody else work for five hours to pick up a couple tips right. So it's in the YouTubes showing you what they want to show you, but the best way is literally to be near somebody that's really good at it that's - unfortunately that's the best way - it's almost always like people almost pair off in engineering where one guy's learning from another even if they swap roles later that day because he's better at something else. That's just kind of the way it ends up going.
Yup, so I think what you're saying is find a mentor if you're not really good at it.
Right yeah and vice versa and mentor others. So I was talking about the wire, on each and every C128 board.
Okay, oh yeah actually Ben Jordan snuck that to me. So let's go into war stories a little bit and let's talk about 'the wire' also I'll get a screenshot of this I think Ben or do you have it? [Bill reaches over to show C128 board]
That's so cool okay for - oh my gosh okay, so for those of you that are listening to this on the straight-up podcast you need to go to this portion and look at the YouTube just to see this giant board that he's pulling out of the Commodore 128 and look at the keyboard.
This is what we call a 'barn door stop' it's too big to be a regular doorstop and that keyboard I designed by looking down at my BT 220 and I said, hey it works for me it'll work for future users too. I'll hold it up to the microphone for users at home right
Okay.
But there is a wire on each and every... we made 5.7 million of these.
Oh okay. Wait before you go into the wire story, give us the stats on Commodore 64 going towards it and compare that to the Apple because I thought it was really interesting.
Yeah the - and actually I narrated a video by a company called Junk Food about the - called the 8-Bit Generation, and I learned some things - our version of history wasn't quite as clean-cut as to who was the first and the best computer company out there so I'll give a little props there. But we often said, Apple's just using our parts, because we made the 6502. Well that's the processor they used, but we made the chip.
So in our minds Apple did come out and they were first to get a floppy drive and some color early on, but then we come whooshing by them with the Commodore 64 whereas they sold 5 million of the Apple 2 that you're always seeing on every show about the 80s right. You see a show about Silicon Valley: 'we created the home computer' I don't agree, sorry I'm from Commodore I am a competitor and we made 27 million Commodore 64's we had all 64K, we had these cool color chips and sound chips that they didn't have and we could do animation because we have these things called Sprites, except Sprite was trademarked by Texas Instruments so we had to call 'em movable object blocks, but everybody called them Sprites, so you could write a game right and the blocks are moving themselves around, you're not having to rewrite that whole screen and everything so it was an amazing computer and we called it the 'Apple killer' because we actually stopped talking about Apple.
Yeah then my boss wanted to kill Sinclair, remember the Timex Sinclairs?
I don't.
They're little tiny door stops now - I actually did use one of those for a doorstop and then the marketing department saw that and so suddenly every door in marketing has a Sinclair holding it open...
That's so funny I don't even remember that one which I'm kind of surprised. I was kind of tuned in at that time but not that tuned in I guess.
It was a $50 computer and actually, when the basic ran, the screen would go to crap because it couldn't share the BUS, remember I talked about that earlier, and then they came out with a color one and and it was cheap. I mean the Commodore 64 was $299 - by the way the Apple 2 was like $1500, $1700 and we're $299 - and then we did something like we lowered the price to $100 if you send us your old computer. So people were buying Sinclair's for $49, sending them to us to save $50 and that's of course 50 1980-dollars so this was - if you can see it through the microphone here - this was the one of the family that we called Ted and this was basically the Raspberry Pie of the day, it's all in there. The one chip does the video and the sound, and there's a processor.
Oh and the video sound chip runs all the D-RAM and does all the crazy interfaces to the keyboard. So it's literally like very close to a single chip board even though there was nine in the original - nine chips - yeah you cracked open an IBM PC and there was 280 something like that. That's crazy and even the 128, as big as that was, had a couple couple tens of chips in there. So and then Jack Turmel unfortunately left Commodore and this product I was showing, this Ted thing. Without him there to drive the vision, that product kind of failed and we even had a talking version. We had snagged the guys from TI Speak and Spell, which was a big thing in the 80s and we had them working at Commodore, so we had a talking version of a computer with a desktop that Apple tell you later they invented the desktop. Well no. The guys at PARC invented it but we had one, it was just our founder left and it floundered without the founder.
Crazy, okay show us the wire.
Okay, so then the 128. What happened was I had gone to a CES show and by the way CES shows drove everything for us, Consumer Electronics Shows, mostly cuz if you ask them if they'll move it a day so you can hit your schedule they'll say no, so the CES show is - this is a scheduled date you cannot miss - you can't miss it by five minutes, you can't miss it by a day and so we decided - and by we I mean the engineers, we didn't even really tell management about the C128 till it was too late and then we would do things to it. Like I added a z80 processor so it became - it's Commodore 64 compatible - so suddenly nobody's going to complain at me because there's no software, can run all the old software, but then turns out the z80 cartridge didn't work very well on the Commodore 64, so I just put the z80 right in the board and after the PC board Rev was done I said: oh by the way I added the z80, they knew they couldn't tell me to take it out now or we'll miss CES.
So then pretty soon the guy would be: I had a great idea to leave the z80 in there you're like, cool go tell marketing, take a doorstop with you right. So one of the things we did is, even as we're getting ready for the CES show - it was January 6th that year I think - we're already getting ready for FCC, so we're working on the final production and that's all in five months. I started this near August and we had six - five or six customized C's that needed to be done and so again that was our wheelhouse - this is custom, this is custom, this is custom, that - one of the other ones in here - and we're going like the wind right. Well right near the end, the z80 stopped working reliably. It wouldn't boot CPM 20% of the time, and me and my boss were fighting. It's bound to happen right, he'd already gotten his bonus I think to let me go around barefooted was like wearing thin right. But the - - oh, I lost my train of thought that almost never happens when you get old… [laughter]
You fought?
Oh I was fighting with the boss and he said: fine, I'll give it to somebody else to fix that problem! I said: fine, I'll take a shower and go home and get a nap! Right, so for a week, I mean I had a great week. I caught up on my hygiene, (I won't tell you some of the other things you do when you're full of testosterone when you're young). But he comes to my office Friday, and in my mind he puffed on his cigar (you could still smoke in the office back then). I don't know if he had a cigar that day, but that's my memory and he goes: fix it or you're fired. I'm, oh sure I can do that, you're ready now for me to rejoin the workforce?
Absolutely, I'm clean, I get along with people, and I just happen to luck out where I'm - the oscilloscopes of the day weren't like the Tektronix MSO scopes - like I got back there, I had to turn it up real bright, and then I would stare at it and then turn and look at a wall and I would see the reverse image and I go: there's a glitch right there - I'm pointing at it so someone can see it because he hasn't burned his retinas staring into the light - and they think I'm nuts, and I was right. There was a glitch on this A10 line, when the z80 was the processor, but when the 6502 was the processor there's no glitch. I mean it's right around when the D Rams were doing something and so it comes down to understanding how a signal propagates down and this is part of PC board layout right.
And I liken it to when the 6502 was driving the length of the line that drove it all the way to the end, like playing a flute correctly, but when the z80 drove it from an extension down the line it was like blowing into one of the holes on the flute and it's kind of not - and so I got a standing wave, where the wave’s going back and forth and bouncing into itself and it just happened to do it on A10 at the wrong time and I caught it on the scope in an hour. Of course nobody believes me right, so and the way I made it work, was I took that wire that I showed you that's redundant. There's already a trace on the PC board, I just soldered this again so now it's actually a loop right it can't bounce - -
Ah it had a return path, okay.
Yeah or propagates like this, but either way it's not a standing wave anymore at a certain spot, and it just happened to be that spot was the multiplexer for the D-RAMs and they think I'm nuts right because not only do I fix it an hour, I fixed it with a wire! So we ran 10,000 units to prove that Herd's gone off the deep end and we got a hundred percent pass rate on it. It actually fixed the problem. So now the wire drives me nuts because there's 5.7 million wires out there and people said: why didn't you just change the PC board? It's like: because actually I found it this time, if there were no tools to do anything, if I change the PC board I might have moved a glitch to somewhere I can't find right. So the devil you know - and that's how it ended up going out.
That's crazy - and from by the way - having a background in EMS. For an EMS provider, to have to put a wire on five million boards, that's crazy nobody would do that today but it's cool!
We called it post solder assembly and it's horribly expensive that's five point seven million dollars. It probably cost $1, the wire was a penny and 99 cents to put it on there, so we just did that. There was one other fun issue with the schedule of the 128.
Okay.
At one point - and see we didn't have real deep analyzers and stuff - so when the processor goes flying off the tracks because the memory is corrupted you'd go, well when in the last two minutes or two million cycles did the corruption occur? Because the analyzer's not going to catch it, unless you're so lucky right. So one of the things I noticed is, it would corrupt in the video memory and the video's memory is being scanned 15,000 times, 60 cycles a second and so I took a light pin and I put it on this spot on the screen right where the corruption would occur and I sent my analyzer, so soon as the spot on the screen occurred the light pen triggered my analyzer. And it's actually a commodore light pin - I still have it - was actually plugged into the joystick port of the system on troubleshooting and it turns out - it was called ground lift, and you're probably familiar with that. There was a stub of a little over an eighth of an inch on the ground pin of a DRAM multiplexer, and it's inductance mixed with the capacitance meant it would come off of ground when you went to switch a whole bunch of zeros to a one - except for one - that other one became a one also it just dragged everything with it.
Oh, got it.
Yeah and I also took - literally another little piece of wire - fixed it and then I yelled at Fish to fix. That one I made him fix but the only way we could catch it in that case, is I used a light pin to catch this little 1/8 inch piece of trace that was just playing with me.
Well you know what I love about these stories Bill, is that I think it's lovely to tell them and show people what a Wild West it was and how we solved, but people like you solved things really simply because now we sit on all these really complex tools and really we stand on the shoulders of people like you right, who were innovating back in the day where we did not have the complexity of tools or things and it's easy to take those things for granted now because so much can just run in the background and you so I think it's fascinating to hear these really - like these MacGyver ways that you figured out how to fix it - you're like the original PCB design MacGyver dude.
So one other quick story and it goes right to that - about the tools and the software simulations and things and it's the day I knew I was working in the right place. And this isn't my story - this actually is the chip designer stories for the Ted, for that thing I showed you. They had design roll checks when they laid out an ICs that told him if two things got too close to each other, but they didn't have an electrical rule check to tell 'em if it's supposed to be shorted together or not, so they turned a corner. They had like A7, A8 and A9 cut right across the other to address lines and it shorted 'em out, and they had no way to check that - unless they hand looked at every plot of every layer of what made up an integrated circuit. Well they - meanwhile cost a quarter million dollars to do another run. So what they did - I'm in the hardware lab, and the guy goes: okay turn on that - turn on the microscope light. Okay turn it off - good we're in NTSC mode. And I turn and I look and I'm like: did you just flip the status of a register with photons while looking at it under the microscope? And he goes: yeah uh huh, and I'm like: AH I'm in the right place, this is where I wanna be!
Yeah and they didn't have the tools that told them if what was on the schematics, what made it onto the chip. So yeah and they would spend five months, with a ruler actually called a scale, checking the plot. That's the only way they could do it.
That's amazing well thank you for sharing this - unfortunately we're running out of time. But thank you so much for sharing your history and your ingenuity and the stories of Commodore and giving our listeners really some practical ways of just jumping into a new tool, if they have to right, nobody likes change but I'm sure you would attest to that overall has probably helped you become a better designer to go ahead and jump in and you could probably jump into a new tool easily now it probably doesn't freak you out as much as it used to.
If you know you're going to be overwhelmed, then you're right on schedule when you get overwhelmed - and then you just go back into it and you know, how do you eat an elephant? A bite at a time - same thing.
Just acceptance that it's going to be frustrating and this is the cycle.
Yeah that you'll screw it up and then fix it, just don't ruin your libraries in the process.
Okay, well some good, good wisdom. So thank you again Bill for your time, it's been a delight to hear about everything and I just by the way - best background - those of you listening, you really need to go look at the YouTube version of this, because his lab looks like you'd all want to go live in it man it looks like there's everything in there it's awesome. What's up with the penguin by the way? There's a penguin, that looks like it's standing on your shoulders?
On the telly, it used to be on top of the oscilloscope but now it's just with you so that's that's a Monty Python penguin, that's from our era right?
Totally, that is so funny!
Okay, well thank you again for joining myself and Bill Herd today on Altium's OnTrack podcast. I'll make sure to share all of his colorful links and Wikipedia and videos from Hackaday and thanks for joining us again. We'll see you next time - until then remember to always stay on track.
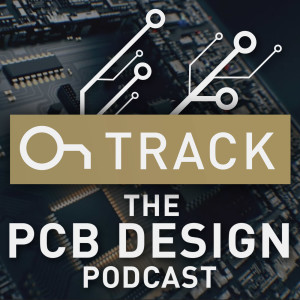
Wednesday May 30, 2018
DFA Tips from Duane Benson at Screaming Circuits
Wednesday May 30, 2018
Wednesday May 30, 2018
Duane Benson from Screaming Circuits shares DFA Tips and a piece of history as he shares the story behind the scenes in developing quick turn prototypes. Listen to learn how one entrepreneur brought fresh perspective to the business that led to great success. And see why Screaming Circuits is uniquely positioned to handle all the leading edge components that PCB designers have available.
Show Highlights:
- Screaming Circuits was founded on the premise to get prototypes built quickly. It was a struggle to get small volume prototypes built and a market need was discovered.
- For prototyping - going abroad invites its own set of risks.
- A traditionally 6-8 week process, Screaming Circuits does in hours.
- We don’t specialize in a vertical industry, so we see a lot of the leading edge components.
- Layout isn’t taught in schools or its self taught. The experts who knew how to make layouts work perfectly have retired.
- We built a business around stuff being wrong. Stuff isn’t going to be right when it arrives to us and we have to fix it.
- Why are we having a problem sourcing parts?
- Personal interests? Photography and decaying industrialism.
Links and Resources:
Downloadable Circuit Talk
Twitter: @pcbassembly, @duanebenson
Screaming Circuits on Youtube
Hey everyone this is Judy Warner with Altium’s OnTrack podcast. Welcome back to another podcast session with us. As always we have another incredible guest with us today but before we get started I wanted to invite you to please connect with me on LinkedIn. I'm very active there and share a lot of resources for engineers and PCB designers and also - I don't think I shared this in past podcasts - but we are also recording this on YouTube as well as just an audio. So you can always go to YouTube and go to the Altium channel, look under videos and you'll find these also in video format if you should prefer to listen to this and watch it in video format. And also with Altium, you can always follow us on Facebook LinkedIn or Twitter and we love engaging with you. We always love to hear from you about subject matter experts or subjects you'd like to hear or learn more about. So, without further ado, I'd like to welcome our guest today who is Duane Benson of Screaming Circuits, out of Canby, Oregon, correct Duane?
Canby that's correct.
So Duane welcome, we've crossed paths for several years now and it's a delight to have you and learn more about Screaming Circuits and EMS and how designers can do things to to be more effective in the design for assembly and just learn about Screaming Circuit’s model, which is a very unique model by the way, I'm eager to jump in.
Well thank you I'm really happy to be here thank you for asking me to participate in this.
My joy. So why don't you start out by telling our listeners a little bit about who and what Screaming Circuits is, because it really does have a highly unique model, and kind of the why behind you guys started the company and created this model?
Well it started back in 2003, actually that fifteen years ago now. Yikes..
Yeah, I know, how did that happen?
So about that time our parent company Milwaukee Electronics they had a number of customers that were struggling to get small volumes of prototypes put together back in the back in the olden days - if I can use that term. Prototypes quite often were sort of slotted in on an ‘as available’ basis. So say you might need five prototypes and the EMS company would say, well we’ve got a big run going on and I can put you u on the machine in two weeks so you can get your prototypes then. And two weeks come along and something else came up, so another week... Even going back before that, back in my day they didn't focus, for example, building a prototype.We'd have a big bag of parts and some blank circuit boards, and we'd hand them to this poor technician on a Friday afternoon and the engineers would go, could you have these built up by Monday?
So it was becoming a real struggle to to get prototypes, get small volumes of any sort built and a couple of our customers came and asked us and said, can you can you help us out with this? It's just not working and the Milwaukee Electronics’ management thought about it a little bit and thought, why can't we short-circuit the process?
No pun intended right?
Laughter.
So the management experimented a little bit and then decided, , there's an actual business here. So back about that time they brought Jared Store out here to start up what they called the Screaming Circuits division to focus specifically on getting prototypes done quickly.
Mm-hmm.
And , from that time the initial focus of the initial business was basically Jared with email and phone and one of our partners Sunstone Circuits, they built the blank circuit boards - the raw fabs. They'd give us a call and say, hey one of our customers needs some prototypes built, can you guys do it? And that's how the business started.
So you guys created the synergy. Now I've had the pleasure of meeting Jared once at least, through the phone and email and Jared was young right? He was the son of the owner so, I have to insert that. Because I kind of love that those of us who are kind of old dogs in the industry - I kind of love that he said, well why can't we do this? And he just kind of, like you said, a phone and a thing and just said why not. Because he wasn't constrained by the way things were done in the past which I kind of love that.
Exactly he was a young entrepreneur, in fact, I don't know if he'll want to admit this but this was his first job out of college this was kind of an experiment for him to get into a career, into business and he did a fantastic job. Basically by ignoring all of the old rules.
I know yeah.
Yeah and then in 2004 - well somewhere between late 2003 and early 2004 - we first went online with a very, very simple quote system. We boiled it down into six different factors and based on that, came up with a quote and it was all kitted at that point. So we'd say, hey it's going to cost you this much, send us your kit, send us your files, and we'll build them up for you.
Now since that time, when we were talking earlier, it seems like it's morphed into not just specifically prototypes but just quick-turn. It could be quick-turn pre-production quick-turn production even right?
Yeah
The world of manufacturing of electronics has really changed in the last decade and a half . There was a time when electronics were not going to be designed and built in this country. Back in the 90s, when I was working for InFocus again, everybody was outsourcing everything and then over the next decade after that, it was all going going away.
Yeah.
And there was going to be nothing but high volumes manufactured offshore. Well about the time we started doing this, coincidentally the open-source hardware movement came about with the Arduino and some of the other things that came with that. Kickstarter showed up and that really changed the hardware design dynamic. It lowered the barriers to entry to building a hardware company and over the last decade and a half the hardware startup has come back with a vengeance. The problem is, as manufacturing is really, really expensive - unless you're doing super high volumes - so these companies would run a Kickstarter, they'd sell a thousand of an electronic board and nobody would build it for them. So then, , they'd then run off into into Asia and they toured all these shops and these people would either say, no that's not enough or they’d change the design, steal the intellectual property and, you can't. There's little details like that so, getting a hundred or a thousand or five thousand is extraordinarily difficult. And yet there's an awful lot of companies that sell just that many of something.
Yeah, it's really interesting that it morphed into that niche right?
Yeah.
You had, it sounds like you had everything, in place to fill it right? You'd built it to do address prototype - traditional prototypes - and as the market changed you were kind of ideally positioned to address those kind of start-up Kickstarter things. So you and Sunstone have worked together in parallel, I take it throughout this process?
Yes they've been our partners since the beginning, and at this point they build the vast majority of our circuit boards and we do, if necessary, go elsewhere. Or if a customer sends us the boards or requests something else, but the vast majority of our boards are built by Sunstone. They're about ten miles away over in Mulino Oregon.
Another big city like Canby…
Laughter - well compared to Milano Canby is the big cities...
Yes well it's a beautiful area. So, tell us about what you would see in a given day and then I would like to ask you to jump into speaking to designers that may be listening, and go into kind of some DFM tips and tricks. But before we do that, tell us about what are you going to see in a day?
To get a picture of what happens there at Screaming Circuits there's two factors that are pretty important. One is a traditional EMS company. We we see about as many different jobs through here in a week as a traditional medium-sized EMS company we'll see in a year.
Wow!
And the other factor that's important to notice, is that in - using that term the olden days - getting a quote and an order for a project might be a three to four week process going back and forth with all the files, component availability, making sure the design works and then after you place the order, you've got the NPI process which is another three to four work weeks. So, you've got a six to eight week process that we do in six to eight hours.
How is that possible? I mean we may not have enough time here Duane, but I've been in the EMS industry and it’s an extremely complex process, just getting the components you need and making sure they're right and there's not obsolete parts, and that you've got a clean BOM, and it's so complex. How have you condensed it without giving away your secrets?
Well there's a lot of things that matter if you're building a hundred thousand of something or a million of something. At that point fractions of a penny count and you're going to spend a lot more time quoting. You're gonna have to worry about getting large quantities of components if you need 20 of a board you can go to Digi-Key and get the parts for a buck, that would cost you a quarter of a penny if you bought them at high volume, and that's still fine now, that's part of it and then you don't have to worry about some of the inefficiencies that would absolutely kill a high-volume manufacturing manufacturer. You don't have to worry about those because if you have to tweak things by hand, while that is more expensive per unit, if you're building 20 or a hundred or a thousand it doesn't matter quite so much. So really what we've done is, we've stepped back and we said, what is important and what is not. The objective is to get working boards into an engineer's hands as quickly as possible and you'll notice there aren't things like how do we make it the absolute least expensive, or things of that sort, it's about getting the working board's as quick as possible so you focus on just the things that matter for that.
Right, you mentioned when we talked a few weeks ago, about it becoming what you had called a transactional model, which is really a different industry and you can go online, place your order in a very transactional fashion, but it also speeds up your time to market, and gives you something highly valuable?
Yes it does, we don't we don't spend an awful lot of time on the financial component of it. For the most part you give us a credit card and we start building so we don't have to worry about the bank component of it. For larger companies we do, because some people, the government or whatever, they have to operate that way. But for the most part you just give us a credit card and that again cuts some time out of it. We also look at each order as an individual transaction, that's why we call it transactional manufacturing, or unforecastable. We don't have to worry about the fact that you're not gonna need exactly 500 every month for the next 24 months. In traditional EMS, you have to worry about that, you plan for that. We don't worry about that, we don't care.
Yeah it's interesting as well it's neat model and I see it as a real enabler. So, congratulations to you guys. All right, let's dig in and give our listeners that are designers and engineers some tips around DFA. The way that you and I originally came to know each other is, I had been blogging and writing and then I came across a little publication you put out called Circuit Talk in which you were doing what I was doing, which was giving designers some really immediate tips to apply to make their jobs hopefully a little bit easier and so, I think you've done a really nice job of that. So can you talk about why you started Circuit Talk and then go ahead and share some of those tips or tricks that are around design for assembly that's gonna make designers’ jobs easier and smooth the time to deliver a good product in time to market.
Well thank you. You know the volume of jobs that we get - it does lead to chaos of sorts - but it also is a huge advantage in that we get to see every single mistake that anybody's gonna make. We don't specialize in a vertical industry so we don't only see mistakes related to a certain type of component tree. Name a component that's leading-edge, we've undoubtedly seen it and, so we see these things - and it's not just beginners, it's not just experienced designers, it's not just big or small or university - everybody makes the same mistakes. It's so complex and there are so many variables, so many new types of components. Geometries are shrinking and in parallel to that people have less and less time to design these things. Quite often layout isn't taught at schools, or it's self-taught. The experts who knew exactly how to make a layout work perfectly have retired now, or they've been let go, or things have changed so fast they can't keep up.
Mm-hmm.
So we see these problems every day. Case in point, one that I write about quite often relates to the QFN Quad Flat-Pack No Lead, and then the DFM. The DFM leads along one side. They have this big metal heat slug in the middle, looks like a very simple component, it's cool, it's small, has great signal characteristics. But most of the CAD software, when you try and use a QFN, the footprint is wrong. It comes from the library with the solder paste layer, not designed specifically for the component, so you've got to imagine flipping a QFN upside down. You've got a little row of contacts around the outside - very small - and then a big giant heat slug in the middle that covers almost the entire component. So most of the library components we found have a full aperture opening, so the solder paste layer is completely open for that heat slug in the middle. And what happens is you end up with too much solder in the middle, so the part floats up and the connects on the side don't connect.
Oh boy.
Yeah and this is even more prevalent with some of the open-source CAD software, or some of them with a lot of user-generated content, nobody told those folks how to make the footprint properly.
I see.
Quite often the manufacturers, in their data sheets, even specify it that way. But what you need to do is, to modify the footprint so in that center pad, you get somewhere between 50 and 75 percent paste coverage. So, you take out the default paste layer for the center pad and you put in a little windowpane-looking thing - problem solved.
Interesting. Yeah it's a little scary, unless you have a partner that's on the ball to what you can accidentally pick up off a data sheet or how to interpret that data right? So okay well, that's a good one.
Another one we run across these tiny little micro BGA's 0.4 mm pitch, some of them even 0.3 mm. I've actually seen a 0.24 mm pitch BGA. Yeah, some of the rules change with the bigger BGA's. You want non-solder mask defined pads, so you want the solder mask opening to be slightly larger than the little pad where the BGA ball’s gonna sit down.
Yeah.
With some of the 0.4 mm pitch BGAs, you want solder mask pad or defined pads, otherwise you get bridging.
Oh yeah, that makes sense.
Yeah, it kind of depends on the geometry of the solder ball, but that's a pretty common error as well. So you see these things that component manufacturers haven't fully studied, haven't fully published and they are just setting people up for problems.
Yeah, and what I have found - and not just in relation to components - I have talked to people who manufacture either components, or they manufacture laminates, and what's not widely understood is that sometimes the studies they’re doing is us.
Yeah we’re their guinea pigs.
Yeah, and then we yell and scream and we give them back data and then they produce overtime accurate data sheets. I was stunned to hear that, but it's absolutely true. They need to get stuff to market because the market is demanding it, and the testing is so complex and so widespread, and the applications are so widespread, that they can only go so far. And then the rest of the data has to come from real world.
Yeah the the hardware industry really is paralleling what the software industry did. We had open source software then open source hardware. With software, we started calling it ‘beta test the world’ because you couldn't beta test anymore, it's too complex.
Right, it’s too complex, so we become the beta testers and I don't think that's often understood. When I first understood it my jaw about dropped because I'm from the old school, like you are and it's like; wait nothing would ever go out that was not fully vetted or understood and tested, and things have just gotten so complex. And so there's just a hard limitation there, it's not a bad business practice or whatever, but it's a reality that I think is wise for designers and engineers to keep in mind - another encouragement to work closely with people like you, that can say, we've seen this already a bunch of times, we know what's going to occur here.
Yeah we've built our whole business around everything being wrong basically, start to finish. It sounds kinda funny, but It's all about this stuff probably isn't going to be right coming into us, so we've got to figure out how to make it work.
I don't know, like what happened to the world Duane? This is not how we started but here we are. Another thing you talked to me a little bit about, you had mentioned one time in a conversation, about polarity markings.
Oh yeah. That's that's maybe third or fourth in terms of the issues that we see here with diodes especially. Capacitors somewhat, but diodes even more so. Any kind of ambiguity, when you're dealing with machines, it's a problem. If you've got a barrier diode for example, it's backwards from what you would consider a conventional diode. So if someone marks it with a plus and it's a barrier diode and they're expecting us to know whether the plus goes to the anode or the cathode, we're gonna put it in the conventional manner, not knowing it's a barrier diode it's gonna be backwards so you can't use a plus to mark a diode. You might think minus, Also, does that mean negative or is that the lion on the diode symbol you can't do that because it doesn't tell us anything you've got to say K for cathode not C - because then we might think it's a capacitor, or the full diode symbol the down - lot of people will put in silkscreen, the mark that's on the bottom of a surface mount diode...
Uh-hu.
-which at first glance seems like it makes a lot of sense - but only if you give us the exact diode that you got the marker off of. I've seen two diodes 0.603s in the exact same package from the exact same manufacturer just a couple characters off, in the part number, and literally, on one the mark is the anode mark on the other it's the cathode mark. I've got to I've got to do a datasheet and I have a clipping from that data sheet on the Screaming Circuits blog that shows that it's got this part anode mark, this part cathode mark. I made the same mistake myself. On one of my boards I put the little marker on there and I gave gave the company the orientation and the CAD files, and then I made a substitution because one part was no longer available and used the other one - same thing but it was backwards because I went from cathode mark to anode mark. So, remove ambiguity. A few years ago I would say, it's okay to mimic the silkscreen - just give us the exact part. But with supply chain availability being such an issue right now, I would not rely on the mark that's underneath the diode because they can reverse if we have to substitute something.
Okay I'm gonna put a pause there and talk about what the heck is going on with supply chain. Stuff about diodes like these, very basic building blocks to design, why are we having problems sourcing parts?
Well we've been told a couple of things from suppliers. One is, they're telling us that the automotive companies are buying up literally an entire line. They'll come to a component manufacturer and say this particular part: I need all of your production, all of it and so there it goes out of stock. Internet-of-Things companies - the super, hyper-mobile devices are also causing issues because they're increasing the demand in the super small components. Well then the companies that make the parts don't have fab capacity to also make the larger ones so, some of the component manufacturers are telling us that they're going to stop making some of the bigger form factors 1206s 0805s even 0603s may become even more and more scarce because if they can make 0402 or 0201 to cover all that range they'll do it and not make the other form factors.
Holy... I don't know what to say about that - if I was a design engineer I'd be freaking out - this puts people in a really tough spot!
It really does and it's gonna change the way some things are designed. We have always had a policy that we will not substitute anything without explicit approval. Even looking at a bypass capacitor - 0.1 microfarad 16 volt bypass capacitor - in some cases you need exact parameters. There’s parameters you need to be exactly the same so you can't substitute. But there are also plenty of cases where it's just sort of by guess and by golly: yeah it's a 0.1, it could be 16 volt, 10 volt, 25 volt, 50 volt, whatever. If that's the case, people are gonna have to start being really flexible in terms of what they will accept for a component and maybe at some point the industry will have a flag on a bill of material that says: this one's engineered so it has to be exact. This one, just make it close.
Another thing, our industry is changing so fast, it's just a big reason why Altium and I've decided this podcast would be a good idea. Same reason why your Circuit Talk publication is a good idea because it's like we can't get the education out fast enough or get the news out. Like holy cow, why can't I get this capacitor? It's not a unique form factor specialized BGA they're capacitors! This is like bread and butter, so it's been puzzling to learn about that and I'm just really interested to see how these component manufacturers are going to deal with this and and again how designers are going to be forced to think hard about these parts it's really strange. Anyway sorry for taking a little side trip there.
That's important, it's a significant issue. We're being told this could last until 2020 and when we get out of this allocation, the industry is going to be different and, as I said, a lot of the bigger form factors consider moving all to 402s. It's more difficult to deal with these smaller ones but those are the ones, when the component manufacturers catch up, it's going to be in the smaller form factors because they can sell them to people building small devices as well as big. So think about that, be very, very careful when you're picking the specific component and tell us, and other manufacturers like us, what parameters are important.
Goodness that’s a great tip. You know I hadn't thought about it until just this minute when you were talking; I'm wondering if this will drive an uptick in embedded?
Embedded like embedded passives?
Uh-hu better passives.
I don't know I've been waiting to see that. I joined this company in 2005 and embedded passives were in the news at that point, and I actually made a prediction on the Screaming Circuits blog, that in ten years - I think I said - 80% of the passives would be embedded passives. I don't know that we've ever seen one. I guess technically you wouldn't see it because it's inside it.
No but you would know it was there, because I know it from my board manufacturing past, you would know cuz you would have to process it differently. It's a different process but I don't know what the cost trade-offs are there, but I've met Bruce Mahler from Omega and I've met some of those folks, and I'm just wondering if this allocation will drive, but I don't know what the cost trade-offs are or performance comparative. That makes me think, I need to call Bruce Mahler and get him on the blog because it's an interesting thing to ponder in lieu of what's going on in the marketplace.
Yeah.
Anything else you would mention off the top of your head that's something you see repeatedly that's a design for assembly thing that you would recommend designers to take a look at closely?
Well the polarity, the QFNs, BGAs as I mentioned. Something that isn't necessarily quite so obvious is the data files that is an important part of design for assembly. Ambiguity on a board is bad, ambiguity in a data file is bad. Bills of Materials, if there are parts in there that don't match the board, that's probably 80% of the jobs that come through here, have some sort of a Bill of Materials issue. So, double-check that that's accurate and that it matches your CAD files. If you can give your manufacturer the intelligent CAD files like an ODB++ or IPC 2581, that significantly reduces the chance of error, but then there's a little irony in there too that a lot of board houses still prefer Gerber's so we have seen cases where someone saves and then; oh yeah, I can give you the ODB++, but they forget they made a slight change and so now we have Gerber's that don't match the ODP++ so, make sure all of your files are consistent. Make sure the Bill of Material is clear and finalized. All in all if you add up all of the files issues that we see, that's probably one of the most common problems. I mean, I run into those problems for myself. I designed some boards and run up to the factory here, and I know how to do this, in theory I know how to do this, but I regularly make mistakes that my co-workers chide me for.
Well I think again, that leads to the complexity of the data that's available. The data sheets; whether they're right. I mean it is such a complex thing and it amazes me that we can even manufacture circuit boards and then put components on it and come out workable sometimes. Because it is such a complex process, I'm really glad that - actually I appreciate it - I don't understand all those steps but having worked for for both a really high end EMS that sold to tier one’s, very complex boards, and also having worked for a variety of board shops. I really appreciate the complexity in both those disciplines, and I think sometimes because a board shows up as a line item on a BOM that complexity sometimes can get lost on you. But yeah we're building things, even here Altium, into our own tool that helps, like an active BOM, things like that, that hopefully help. I think design tool manufacturers like us, I think we're doing a better job helping in that regard.
Right yeah, definitely!
Well the last couple items I wanted to talk to you about... well thank you for all that by the way, and again, we will share in the show notes your website. The Circuit Talking, I would recommend to anyone who is listening or watching - that you subscribe to Duane's blog or just Circuit Talk or whatever and we'll put all the links in because again, he's got his feet in the fire and runs up against these things as he said. Because they're putting through such a width of product. Like I used to work for an EMS, and like you said, it was a vertical. So we worked with military Tier one, and so the type of bores we saw was a niche, but you're seeing everything.
Yeah, literally I mean we worked on a camera board, the electronics of it, for National Geographic - it's a plexiglass globe, they drop it to the bottom of the ocean, it's got a chain on it and when the chain rusts through the camera bobs to the top and they pick it up again. We've got stuff being built for the 2020 Mars Rover so, literally down in the ocean up into space and and anything in between, we've built Ardium base stuff, real simple things, through holes; we built a board with five thousand placements. It's just all over the place and it's just absolutely the most fascinating place I've ever worked certainly, because of that.
Yeah I can see that and again, kudos for you - it's easier to do a quick podcast or write a blog post or produce a Circuit Talk that can go out to thousands of people and get that information out in that kind of global sense and be helpful right.
Yeah rather than tell one person at a time.
Exactly it's kind of a scalability of getting that knowledge out, so I really appreciate what you've done over the years. One thing I wanted to ask you about which it was a fun thing is about; I don't know six to eight months ago, I had the privilege to go with the Altium team for the first time, to a Maker Faire because we have Circuit Maker and Circuit Studio - Circuit Maker is free and and now we've bought a company called Upverter, which is also free, and in the cloud, and we also have Circuit Studio. So, we went there with those products and because of my position here as Director of Community Engagement, I hadn't had any exposure really to the Maker community, other than seeing stuff online, and I went and it was like drinking from a firehose. It was so much fun… goofiest things... it was so much fun. So, I'm walking the aisles, kind of collecting things to write about, or learn about, and I come across Duane Benson, wearing what looks like rap swag around his neck - it was like a clock you were wearing right, or something - he looks like a rapper and I'm used to thinking of him as this Duane Benson from Screaming Circuits and here you are, like fully immersed in the Maker space, and you had designed this device and had LEDs on it and I'm like: what are you doing here?
So tell me about how you've come to serve Makers. It doesn't seem like, from a profitability or a business model, that it would be a market that a company like Screaming Circuits would address. So how'd you get there Duane?
Well you could say that I'm a bit of a method actor, I mean I love... I've been designing small circuit boards for a very long time and writing the software for them for a very long time and one way of looking at it, is I'm a Hacker and a Maker who happens to be lucky enough to have a manufacturing facility. But more specifically, those Hackers and those Makers they are starting businesses.
Yes they are.
Many of those businesses become our customers whether they be crowdfunding or bootstrapping or getting investments, they are the future. The Maker community has a lot of students in it. It has a lot of weekday engineer weekend Hackers, it has a lot of people who aspire to start a new business and just such a wealth of creativity. And part of our mission I always like to look at, I'm just one person, we're just one company but if we can make our tiny little corner of the planet just a little bit better then we've been successful and all of those people who want to design electronics...
M-Hmm..
-We know what they don't know. I mean, we know what kind of problems they’re going to run across before they do, and so if we know what they don't know why don't we pass that off? And some of those people will have boards built with our competitors. Some of them will build them themselves, some of them will have us build them. Whatever, we're helping them understand this industry better. And we are helping them build better boards. That's what we really want to do. That's why we're at the Maker Faires ultimately. It does always have to lead back to more business for us, and it does. People see Screaming Circuits, they get the Circuit Talk and they read it, and it's Circuit Talk a Screaming Circuits publication so all of that winds its way back eventually, to helping the business here, and that's how we can afford to do it. But if we can help the business build and grow the business and help these budding designers - everybody wins.
This is why I love you, and love you guys. I just I love that philosophy, I love that approach. I try to live by an old Zig Ziglar thing and this reminds me of you and Screaming Circuits’ model that you just explained. Zig Ziglar used to say, you really can't have everything you want in life. If you just help enough other people get what they want.
Right.
So it's kind of knowing unconsciously that if you put good things out in the world, and you do the right thing, and you're ethical, and you have integrity, and you serve people, that good will come back to you and and you'll do okay. And I think that's a big key to your success actually, by kind of leading with service and and not ignoring the bottom line. We are in business to make money, we have to do that, or we're not in business anymore. So, I really appreciate that.
Well we're wrapping up now and I think you've listened to a couple of these podcasts now and so two questions for you. One are you a nerd or a geek?
[Laughter] I’m a Gunerd…
That's the best answer I've ever gotten yes you're a Gunerd.
Yeah, there was a time when those were really pejorative terms but I think nerds and geeks have taken it back and said, you know what, no we're not going to be ashamed of liking technology and loving it,we're proud of it. I mean, yeah so I’m a Gunerd.
Oh my gosh, I'm totally gonna steal that and use it somehow Duane, that will come back to haunt you later I promise.
[Laughter]
And the other question is, but I think I know what the answer is, if you've listened to podcasts. I always ask designers and electronics professionals in the end - this is ‘designers after hours’ - so because there is so much creativity involved a lot of people, like you said are Makers or Hackers, or they play a musical instruments or they're sculptors or whatever. So, what is your kind of guilty pleasure that you like to do after hours?
It would have to be photography. I chase animals around and take pictures of them, animals, landscapes, and then I have sort of a weird passion for old, decaying industrial sites as well. But photography would probably have to be my passion when I'm not playing with electronics.
That's so cool. Do you have a website where you share any of that or is it just mostly personal stuff and you keep your photos and share them with friends and family and whatnot?
It's mostly a personal thing I have had them on websites before but it's just my thing.
And and what do you mean about industrial sites?
Well, old decaying, industrial and rusty factories. There's a place here just north of Canby Oregon City and we've got a waterfall on the Willamette River and most people think of waterfalls as pristine, and nature and that's all wonderful, I love that. But this one: back in the 1800's they started building paper mills and they built a set of locks. It's the oldest - well till they just recently closed down - it was the oldest continuously operated locks west of the Mississippi. And so now, you overlook the river from a nice restaurant and you see this shut down, decaying, industrial plant and - well no it's not the beauty of the river - but I see a sort of beauty in the symmetry and in the the way people constructed these things. It's almost like an architectural dig, you can see things from a hundred years ago, from eighty years ago, from sixty years ago, and you can see the evolution of that, as this thing built up and then as they abandoned it, and there's just for some reason... I really enjoy that that sort of a view as well as the natural views as well.
They do have a really unique aesthetic and things have changed. It is kind of like a little time capsule and the rest is actually beautiful and sometimes the design itself is beautiful.
Yeah well thank you again, this has been fabulous and I'm sure we can talk more and more, but thank you so much for giving me so much of your time and sharing DFA tips and the story of Screaming Circuits, and we wish you continued success and we'll certainly share the website and Circuit Talk. And if there's anything else you'd like to share with us, give me a holler and I'll make sure we include those in the show notes.
Thank you very much, it's been a privilege to be on the show here, thank you.
Again this has been Judy Warner with Altium’s OnTrack Podcast and Duane Benson from Screaming Circuits. we look forward to seeing you next time until then always stay OnTrack.
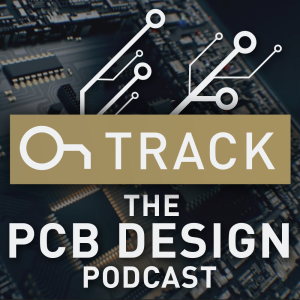
Tuesday May 15, 2018
Upverter and The Future of Browser-Based PCB Design
Tuesday May 15, 2018
Tuesday May 15, 2018
Making and checking parts is the most frustrating aspect of PCB design. Find out how Zak Homuth set out to change that and what is next for Upverter, EE Concierge and the future of PCB design in a browser-based setting.
Show Highlights:
- Why the Upverter parts library? Verified parts at scale, in a high-quality way.
- Verified parts - free to use for everybody coming soon!
- Verifying Datasheets, it’s a lot of work and at the heart of design frustrations.
- I wanted to take the magic of Github and Google Docs and create something for hardware designers.
- From concept to manufacturing in 20 hours.
- This is a conduit for bringing ideas to life.
Links and Resources:
Verified Parts on Upverter
A note about Verified Parts coming soon to Octopart
Indestructible pantyhose + Funny Video
Hey everybody, it's Judy Warner with Altium's OnTrack Podcast. Welcome back, we have
another amazing guest for you today but before we get started, please follow me on LinkedIn. I post a lot of things for engineers and PCB designers and I'd love to connect with you, and on Twitter I'm @AltiumJudy and Altium is also on Facebook, Twitter, and LinkedIn. So please
give us a follow.
Well today I have a really extra special treat for you.
Zak, I think I'm gonna destroy your last name so I can say Zak?
Yeah.
Your last name is?
Homuth.
Homuth - see I would have killed it. So, this is Zak Homuth, he is one of the - are you a co-founder of Upverter correct?
Yes.
So Altium acquired Upverter and EE Concierge in August of 2017. So a lot of people have asked me why Upverter, what was Altium's interest in Upverter, because it seems like sort
of out of our lane. So I thought I'd bring Zak in today and let you hear straight from the horse's mouth. So start out by - if you would Zak - just telling us about what is Upverter, and what is EE Concierge, and what you were trying to create when you launched that company?
Yeah sure, so Upverter is cloud-based, schematic capture and PCB layout. And what cloud-based means is, it runs in the web browser. You type Upverter.com into Google Chrome, it shows up and you can do your schematics, your layouts right there you know, order the
boards for manufacturing right from your web browser. You don't need to download anything, it's collaborative, which was kind of our big superpower for a really long time. Which is that a bunch of users can work on the same schematic, in the same layout, at the same time, in a very Google Docs kind of way. That's Upverter, and then EE Concierge came out of an experiment we ran back in 2015, trying to figure out what was the most frustrating part of doing a PCB design. And it turned out it was making and checking parts. And Upverter - until that point - had a shared global parts library and what that meant was every time I added a part, those parts were available for the community but without somebody checking those parts…
Yeah, that could be a nightmare.
-Yeah it was - it was really scary for people, they were spending a lot of time checking parts, they were spending a lot of time making their own copy of a part that was already in the library, a lot of that you know, wasted duplicates...
You can not have a messy library.
-Yeah and so EE Concierge grew out of that. It was our attempt to clean up and verify and guarantee the quality of the parts inside of Upverter, and so we built a small army of Electrical
Engineers all over the world. They work in an uber-like model where they can kind of log on, make a couple of parts, check a couple of parts, log off again. They can do it full-time, they can do it twenty hours a day, they can do it an hour a day you know, or an hour a week if that's what they want to do. And we built a machine intelligence to check all the work that they were doing to make sure that we had the best possible parts in the world inside the Upverter parts library and then, EE Concierge was born out of realizing that that's probably not specific to Upverter - probably every engineer has the problem.
Yeah there's that.
-so we built a plug-in for Altium Designer so that Altium users could leverage these verified parts which inevitably caught the eye of Altium and one thing led to another but - that you know that's EE Concierge. It was this idea of verified parts at scale, and then kind of outsourcing at scale, for electrical engineering. But in like a high quality way.
Right so, how many parts are in the library now?
Yeah so there's about a million-and-a-half parts...
Holy cow!
-in the Upverter library of those million and a half, about 275,000 are verified these days. And to
different levels of verified, some of them just have verified symbols, some have verified footprints. It depends on kind of what era of EE Concierge they were made in. But it but we've got about 25,000 like really, really rock-solid ones and they're the 25,000 that most people use.
That's awesome. So what's the plan kind of going forward, to get the rest of them? You said you have some kind of machine learning to help you verify that. Like what's the path going forward to get the rest or - you know million parts like you said - not everybody's using a million parts right? There's infrequent wonky ones in there?
Yeah there's kind of two answers to that. So how we make this maximally useful to the most engineers is similar to what Altium and Octopart did, after Octopart was acquired we worked really, really hard to make sure that Octopart was for everybody. It wasn't just you know
Octopart for Altium, it wasn't just parts for Altium, it was Octopart for everybody, or CAD, you know Mentor, everybody. So we're trying to do the same thing with the EE Concierge, we
want verified parts for everyone. So in the next couple weeks we're gonna launch verified parts on Octopart, so we're taking that 250,000 parts and we're putting them on Octopart free for everybody to use. And you can download them in EAGLE, Altium, Upverter. We're working on Mentor, I think we've got Cadence or CAD as part of that, so like in any format, free. Just find them, download them, use them. That's what we want so that's kind of one avenue for the EE Concierge. And then the other is - this is a little bit more kind of futurist and out there answer -
That's okay.
But if you were gonna build an AI that could read data sheets, first thing you would do is have a
huge number of people read data sheets and enter that information very reliably into a piece of software, so that you can check it all. And so the kind of like dot, dot, dot - is we think if we get good enough at doing EE Concierge, and we do it for long enough, potentially we can read data
sheets with a computer, kind of our self-driving car version of the Uber model.
Like and then part of me goes; and you're assuming the data sheets are correct?
Yes it's a real problem and so we had to do a lot of stuff at EE Concierge to catch like, if TI ships a datasheet, and the datasheet has a problem, they'll rev the datasheet and then they'll rev the datasheet, and then not only that, but they'll reuse packages and they'll reuse symbols and the reuse bits and pieces of that datasheet across other parts that they make. We had to build a ton of stuff to be able to catch when they made an update to one datasheet and apply those changes to all the other parts to use the same bits and pieces of the datasheet. It's an ongoing thing - it's a hard problem for us but yeah it's a real - it's a real issue.
Well it's like amazing to me that we're here like...
-at all [laughter]
I mean just from being in like - I started in the industry way back in the 80s - and like everything was done by hand and all that, so just that we could possibly even get to that point - it's just so sci-fi to me - but it's amazing, it's so great. So tell us a little bit about how did you get it, tell us about your personal history and how you went down the Upverter rabbit hole and popped up here.
Yeah sure yes, so I was kind of into software and computers before that was a cool thing I was on the internet pretty early, I was I think five or six when my dad brought home you know our first computer and you know I tore it apart and tried to figure all that kind of stuff out. I was building video games when I was seven, and...
-of course you were [laughter]
-all that but I studied Computer Engineering at the University of Waterloo in Canada and Computer Engineering is a little bit of Software Engineering, a little bit of Electrical Engineering, and then you know all the physics, and boring, normal engineering stuff that you have to do [laughter]
Waterloo is a co-op University and so every four months you'd go to school, and then every four months you'd go get a job, and so I got a bunch of these cool jobs, kind of all over the world, I used it as an excuse to travel. And so I worked in Canada's capital Ottawa, for the insurance company that insures the majority of Canadian doctors, and so they had some really interesting data. And I built a search engine and a database for them to to be able to search when wrong-side surgeries happen right, you know when they operate on the wrong lung or whatever. I built a search engine so that doctors could figure out the root cause of some of this error because that was important for the insurance company to try to prevent this from happening. So I did that, I worked in Germany for IBM, I worked in India for Infosys, and then I got a job in Waterloo working for a company called Sandvine and Sandvine build what are called deep packet inspection - telecommunications service. And so ISPs would install these in their network and it would sit between their subscribers - the people who use the Internet and the rest of the internet - and it would look at all the traffic that flowed through the box to try to figure out how much is Skype, and how much is YouTube, and how much is pornography and Facebook and everything else. Because if you think about it, ISPs are kind of like the water utility. They know that they sold so much water but they don't really know what the water was used for, how much is watering lawns right, and so we were giving ISPs that kind of intelligence. Anyways, I started off as a lab tech, I tore the boxes apart, tried to figure out why they weren't working, put them back together and made them work and I kind of worked my way up to actually designing the box. So I designed two of them for Sandvine before quitting, and I quit because I was really frustrated that on our side of the cubicle wall there were ten of us working on the hardware that was so essential for this company to exist - but on the other side of the wall there were 300 software guys who had Git, and they had version control, and they had collaborative tools, and they could test their code by pushing a button on their computer. I had to carry a 120 pound server around a building, and use screwdrivers and shit to like - and that's, that's part of hardware - I never wanted to take that away from hardware but it felt like it could be easier and you know. We were using Mentor Graphics’ tools and I was frustrated by the archaic kind of 80s feel of it all you know?
-yeah.
I used a Mac at home - I couldn't use the software on my own computer if I wanted to, and I was trying to build stuff at home and this was kind of before IoT was like a thing. This is right before Arduino, before all that stuff. But I wanted to do that stuff at home and it was just so hard to do any of that you know from my Mac, from home, without a huge budget - it's an endless amount of time and at the time we were seeing cloud tools like Gmail and Google Docs and Github, kind of emerging and so I left, because I was pretty frustrated that if this is like the state-of-the-art, if like one of the most complicated telecommunications servers that anybody had built today, was built by some punk kid in this office in Waterloo, working mostly alone, using tools that felt kind of clunky and out of date, like there has to be something better than there and and so we left to build it and it was really no more complicated than: can we take some of the magic of Github, and some of the magic of Google Docs, and build a tool like that for hardware engineers and maybe it takes forever to disrupt Mentor, or Cadence, or Altium, or any of the big guys that have been at this for decades. But we assumed there were enough people like us that just wanted to spend two hours on a Saturday afternoon designing a piece of hardware. There must be something we can build for them - a little bit like Google Docs right, it doesn't have all the features, you can't make fancy tables, you can't do it all, but it's slowly taking over the world and we wanted to do the same thing for hardware.
Well I think you point out something that I really noticed. It seems like there's a block of people that are like my age, the old 80s people and we've kinda just built upon old... and then there's the next generation that were five, okay I was 20 when I got my first computer, you guys kind of grew up with these things in your hands, and it I think it's kind of hardwired in your brain. So I think, there's more efficient, better ways to do things and we are building on old Legacy stuff, so sometimes we just can't see it. And so I think it's really very exciting because I think people are gonna be: oh thank god, somebody's built something modern you know, on the cloud that thinks, and operates you know, which I think was the big draw actually for Altium, which we can talk about that a little bit later so - so the Upverter I was going to ask you, but you've
answered it partially, is why Upverter? Out of the various other things you could do, why didn't you go into - I don't know - you have a very entrepreneurial spirit, so there's lots of things you could have done. Like why did you pick this one thing?
Yeah, so when we started Upverter, I quit my job before I knew what I was going to do. I knew I wanted to build something, I knew I wanted to start a company, I knew I was kind of done with working for the man, and I recruited two of my kind of college roommates. So these are guys that went to Waterloo with me. We lived in this terrible, decrepit, run-down house next to the campus, near the engineering buildings. You know we lived together, we worked together, we did our co-op jobs together we - you know we were thick as thieves. But I called them up and I said you know, how do you feel about quitting your job and like doing something new? And they both quit like the next day and so we got together in this old decrepit student townhouse and we wrote down hundred ideas of things that we were excited about, things that we were passionate about, things that we believed needed to be fixed. I was shouting loudly in the corner that we needed to build this - this hardware tool that was the Google Docs for hardware. That was my passion, that was what I was excited about. But Steve and Mike, they had some cool ideas of their own. There was a bunch of stuff that they wanted to build that a lot of it is actually been built, and a lot of it ended up being quite substantially large companies. So our second pick our kind of the front runners....
So what was on your cut list?
-Yeah so the second pick was, we wanted to build drones, and this was before drones were
cool. We wanted to build very large-scale drones that would be towed behind container ships and provide a bigger radar footprint than the ship can have itself because it's so close to the
water and you'd do this for a bunch of reasons. But the really burning reason at the time was Somalian pirates. If you could fly one of these drones above a container ship, you could get ten or a hundred times the radar footprints so you could really move the ship before anything bad happened. If you wanted to. Anyways, a company ended up doing this, and started right around the same time that we did and ended up being acquired for something on the order of two or three billion dollars and so we missed that one a little bit. But but we just - we just didn't even know where to start on it. But it was - it was the second pick.
That's crazy.
So we didn't really talk about this ahead of time, but you know I think I know around the time AltiumLive went down, there were people, kind of gurus in the industry, and they're like so -
ultimately it was in October, so and Altium acquired you guys in August and I remember some people, like it was like all the buzz, like what are you guys doing? Why that customer? And
so what I want to talk about is - who uses Upverter? I'm thinking makers, hackers, hobbyists and maybe EEs that want to be startups or do personal projects - like who do you think the Upverter audience is, and how's Upverter going to serve them, and how many people are on Upverter? Tell us about your ecosystem a little bit?
Yeah so it's the 'misfits' mostly, these are the guys...
The land of the misfit toys! I like these guys! It really is, these are the guys that are unserved by the eCad industry at large, they're using operating systems or tool sets, or computers that can't run traditional eCAD, they're in funny parts of the world, they're students, they don't have electrical engineering degrees. In lots of cases they're the weekend warriors that can't steal a copy of the eCad that they use at work and bring it home, they're makers and hobbyists and hackers yes, but they're also - you know we helped some Nigerian kids put their country's first satellite into orbit...
That's cool!
-and they couldn't have done it using traditional eCad tools.
That's cool I love that!
-Yeah we - some of the first augmented reality startups were built using Upverter. Like kind of odd stuff like that where you couldn't necessarily use a traditional eCAD tool, you couldn't necessarily iterate at the cycles that one of those tools would let you you iterate at. But also like children on the internet, and you know Mac users and all that kind of stuff where you just can't use a traditional eCAD tool.
Right.
But misfits mostly, we think of them as kind of an - not really the next generation of electrical engineers - but but very much a different breed, a different type of 'doer of electronics'. Well it is kind of grass roots though I think that we are gonna see more amazing things, like drones being dragged behind boats, that are gonna come up organically and kind of like you, I think you're the perfect sort of head of this brand, like 'yeah dropped out of school, this wasn't working, I don't like it whatever, so yeah I can see that happening over the next five, ten, twenty years. I think we're gonna see amazing stuff out of that space. So how many people, I don't know how you quantify that, have used Upverter, or use Upverter or actively log on a month?
Yeah-
So how do you do that?
At the time we were acquired by Altium, it was a little over 50,000 people used Upverter,
they use it in a very 'bursty' way, they'll show up - they'll work frantically for two days - ten days a month, and then they'll disappear and we won't see them for a long time ,and then they'll come back. And we correlate that with their kind of idea cycle right. They'll have an idea, looking very excited about the idea, they'll work on the idea, they'll do that thing, and then they'll go away you know, probably because they built the thing and they want to play with it. It could just be that their focus has moved and they're they're onto something new, and then we'll see them come back, six months a year you know, a couple of days later - depends on -how much time and energy they put into their ideas. But that's okay for us, like we we never aspired to be the daily tool like somebody like Altium is, like we aspired to be this conduit for people to bring their ideas to life and you can only be as useful as people have ideas right. So if you have an idea every day, we can be useful every day.
Most people don't - most people have inspiration quarterly, or a couple times a year and that's
that's what that looks like. We have many thousands of monthly active users so thousands and thousands of people log on every month, to work on their ideas, and their little projects. And the average project is worked on for quite a small amount of time, relative to you know, what you would expect from other eCAD tools. We'll see products going from conception to manufacturing in like 20 hours or less. And so that's pretty amazing, if you consider that's two or three days of work.
That's unbelievable, so if - you said something earlier that I wanted to ask you about and that was - you mentioned that people can go into manufacturing. Do you have sources like fabrication, assembly sources that are related to Upverter?
Yeah, and we've had this in a couple of different forms over the years. We've had, what we like to call the print button, kind of refactored a couple of times inside of Upverter. We're currently refactoring it again right now, and part of that is as a result of the acquisition. We have another
company we acquired, Siva, who does a lot of stuff in the manufacturing space, and we're refactoring our print button to use some of their technology and would be better linked up with Octopart, so it should be a better experience for our users as a result of doing it. But yeah,
over the years, we've had a button, you click it, you give us your credit card number, and a couple days later something shows up in the mail which, which is what you designed.
Awesome.
-And we'll do that again in the very near future.
And it - was that assembled also, or just the bare board?
-We used to just do bare boards, and then we experimented with assembly for a little while, the new - the newest, latest and greatest version - that we're working on right now will be fully assembled and it'll probably include whatever enclosure your device fits inside.
Oh my gosh, I mean I'm like ridiculously excited about this.
Yeah, it's gonna be pretty cool.
Okay so I always ask - I don't always ask this - but I wanna ask this now. Okay, are you a geek or a nerd?
I - - geek, but I don't know why. I don't know what the difference is really...
It's just your gut - open question.
Okay, geek.
-I think you're a geek cuz I don't think there's - I don't think - I think... whatever [laughter]
It's something we ponder here on the OnTrack Podcast. What is a nerd and what is a geek, we've...
-big questions [laughter]
We've decided what geeks are cooler; nerds seem more like, at least to me, physics - like...
-okay
-children 'Coopers'
-oh Science...
-yes more deep on the science side but this has not been proven, so if anyone wants to comment below and tell us what you think a geek and a nerd is, we're all ears. So but you were geeking out there, this is why I stopped you.
-Okay
-cuz I'm like, oh you are like totally geeking out and I'm tracking with you man, I'm like, oh this
is like - we're having a geeking out moment right now [laughter].
So I was talking to our Head of Operations the other day, and I was just saying that during that AltiumLive, people were asking why would Altium, a professional e-tool, pick up Upverter,
and basically I think Altium has a vision to kind of embrace every level of PCB designer and also embrace and serve those 'misfits', those marginalized, or that don't have access you know, those that can pay for Altium Designer and they do it professionally, well great...
-Yes
But that we want to serve the wider community. So I was asking Ted Pawela about it, and he was saying - and I just wanted to get you to chime in here - is that sort of what we were
talking about earlier - is that cloud - I mean a lot of software programs are going to cloud-based.
You know there used to be security issues, but they've tightened those up - so technology is
moving towards cloud based, and if we don't sort of pay attention and go that way too, I think will be sort of left behind and that, also the next generation, or the new, or the upcoming, or the
grassroots, organically-grown innovators, I think are gonna - like you - are going to be cloud natives right, and are going to be frustrated, like you were when you were at Waterloo. And to
also meet those people where they are, not expect them to cough up the money or fit into our model, but figure out where they're going, and what their model is, and what their needs are. And so that was - that's what I think Altium saw as very attractive - seeing Upverter as a huge enabler to serve that community. Would you agree with those?
Yeah - so when we were in the kind of acquisition process with Altium, I spent a lot of time on the phone with Arum, our CEO, talking about kind of his vision for the future of Altium, and his vision for the future of electronics, and one of the things we talked a lot about was making
Altium synonymous with PCB design. And part of that is, you can't just serve the tradespeople in the mainstream - there's a million people in their basements that have ideas, that want to invent stuff, and those things include electronics. You need to be there if you're gonna be synonymous with PCB design and so - so a big part of it was that. But then also a big part of it is like, the world's changing knowledge work's moving to the cloud, is becoming collaborative you know. The Windows operating system may or may not be the operating system of the future. You look
at mobile, you look at tablets, you look at what's happening with Apple, and you know all of that. They're you know, there's a version of the world where Altium is constrained to only serving a chunk of a market because of the way we built our technology, and so I don't know, Arum obviously hasn't said any of this, but there might be a little bit of this that it is an edge on
the future.
Well I can tell you that personally, it's a really exciting place to be, because I love that. I love
that you know, I interact a lot with University students and that. But we've also gone to you know, I went to the New York City Maker Faire and to see what people are developing is so
exciting. So to be able to serve that community, and see what they come up with, is just a blast. Like I love to see it, and especially like you had a start early with IoT like it's gonna explode what we can make. And like I said, they're gonna be making it in their garage, in their basement, or their shed...
-It has to - it has to explode. Like we're talking about you know billions of devices all over the world...
-billions like capital B.
-yeah like a hundred or two hundred thousand professional electrical engineers aren't gonna invent billions of devices; we need to include a bigger chunk of the world, in the design
of these things and you know, and then
- that's not to say the tradespeople won't have their place, like of course they will - but we need grassroots, we need people building stuff in their basement. And we need it at a scale that we've never needed it at, more than now.
I know, I'm really excited about what you're doing - I'm really excited what you guys developed, and I'm so excited that that you're part of our team. So sort of wrapping up here, I want to sort of segue into what I call 'designers after hours.'
Okay.
So, I don't think you have any after hours, you might get to have a beer after work once in a while. This guy's from Toronto and he's here an awful lot and I don't think you have any after hours right now, but if you did have after hours Zak, what would you do, or what do you like to do?
Yeah well my wife and I bought a house in the Canadian wilderness about 18 months ago, and so my after hours, for the last 18 months, has been turning this kind of run-down cabin into a home for my family and so I've been watching a lot of YouTube videos, and buying a lot of power tools, and trying to figure out how to do all that stuff. But when I'm - when I'm here in
San Diego, and when I'm stuck here for the weekend, [whispers] I buy a couple videogames [Judy laughs] that's - that's kind of my thing.
Okay, and here's another super fun thing about Zak. I want you to share about - his wife is also an entrepreneur. So tell us about your wife's business cuz that's really fun.
Yeah so my wife is a very successful entrepreneur, she started a company when she was quite young, that did eCommerce, and she sold that. And then she ran another company which was for angel investors, and she sold that. And then she did something with hair extensions, and
her new thing is called Sheerly Genius, and Sheerly Genius makes indestructible pantyhose.
And you can hang a human being from stuff with nothing more than a pair of pantyhose.
There is a video, we are going to share the link of Zak, hanging his wife... [Zak laughs]
from a second-floor balcony with pantyhose - it is a real thing.
It is a is real thing.
Okay, so what are the materials?
Yeah so it's heavy molecular weight polyethylene, which is what the fiber is made out of, and it's special in that it's incredibly strong, but also a low denier - or denir - I'm not sure how you're supposed to say that word - but so it's a 30 denier fiber which is what you can make hosiery products out of, but it's incredibly strong. It's like the the strongest dental floss you could
possibly imagine, and she found a way to weave this into pantyhose but also to like wrap lycra in it so that it's stretchy - but it's still sheer, but it's like incredibly and ridiculously strong, so it will never run.
-It's like 'superhero pantyhose' you guys really you're gonna have fun watching this video that we'll connect below, and we will also connect to Upverter, and EE Concierge and Zak's LinkedIn profile, if you'd like to connect with him, and any other things that we think that..
-Sounds good [laughter]
-you might want to connect to. So Zak, thanks again.
Thank you.
-I'm so looking forward to working with you and seeing what we kind of collaborate with and
sort of reach - reach to the grassroots-end of the design community.
-Me too .
I'm really excited about it so thank you so much for joining us.
Of course thanks for having me.
This has been Zak Homuth, is that close enough?
-Yeah.
Zak Homuth and Judy Warner with Upverter and Altium, and EE Concierge. And we will
look forward to seeing you next time.
Until then, always stay on track.
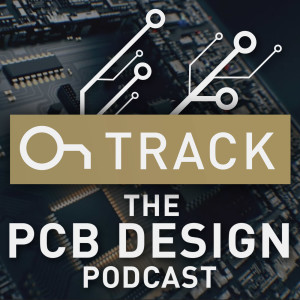
Monday Apr 30, 2018
Why is Spread Glass popular? Chris Hunrath from Insulectro
Monday Apr 30, 2018
Monday Apr 30, 2018
Why is spread glass popular? What can you use instead of FR4? Listen and learn from industry veteran Chris Hunrath, who joins us from the San Jose Insulectro facility for a deep dive into what material sets are used in printed circuit board assembly and manufacturing. Get expert insights and learn about new materials on the market to help with your PCB design before going to fabrication and assembly.
Show Highlights:
- What is Insulectro? Operating for over 50 years, Insulectro provides materials for electronics, everything from laminates, prepregs, flex materials, copper foils, conductive inks, substrates, process chemistries, imaging materials and lamination materials. With 11 stocking locations, the newest in Toronto and 9 branches, Insulectro is a leader in providing electronic materials to industry.
- Prepregs - 175 different types to cut from in San Jose facility alone!
- Spread glass is becoming more popular - electrical and fabrication benefits because it is more electrically uniform. No open areas, the filaments are spread across (aka fanned out or mechanically spread) and this has signal benefits especially for differential pairs. Better from a drilling standpoint too.
- New materials are gaining traction - with low loss that laminate at normal temperatures
- Insulectro distributes for both Isola and DuPont
- Isola’s line-up of high-speed, low-loss material sets - Isola has a suite of laminates that are low loss, some of them with DKs close to the teflon range and they laminate at the normal temperatures which makes a composite build much simpler.
- Low-loss, low-Dk materials that can help with their signal integrity requirements
- I-Speed® - Low loss system, not as cheap as FR4 but its close and could be a good next step for people looking to upgrade material
- Having the right material set for a design is critical
- Challenges are more often in the fabrication than the design
- Copper is a really good moisture barrier, you have to bake the parts prior to assembly.
- I’ve seen people underestimate the baking and end up with scrap. Moisture is avoidable.
- Bonus Material: In Designer's After Hours, Chris Hunrath shares what kind of electric creatures lurk in La Jolla!!
Links and Resources:
Chris Hunrath on Linkedin
HDPug Research on High Frequency Flex
Understanding Glass Fabric by Isola Group
Hi this is Judy Warner with the OnTrack podcast. Thanks again for joining us. Once again I have another amazing guest for us who is the go-to guy in PCB laminates.
I am with Chris Hunrath today but before Chris and I get started I would like to please invite you to subscribe, or to favorite us on your RSS feed, or you can connect with me personally on LinkedIn. I share lots of stuff relative to engineers and PCB designers and on Altium I'm at @AltiumJudy and Altium is on Facebook Twitter and LinkedIn.
So please give us a subscribe and a connection and we’d love to interact with you and hear more about what you'd like to hear on this podcast but I'm sure you're going to enjoy today's guest.
Chris is the VP of technology at Insulectro and I'm gonna let Chris go ahead and tell you a little bit about Insulectro for those three people on the planet who might not know who Insulectro is. So, welcome Chris and tell us about Insulectro.
Okay thanks.
So yeah Insulectro has been around over 50 years. We supply materials to the circuit board industry - actually multiple industries - but mostly we've been focusing on electronic materials. Everything from laminates, prepregs, flex materials. copper foils, conductive inks. Different kinds of plastic substrates used with conductive inks, process chemistries, imaging materials, drilling materials, lamination materials. Also we have 11 stocking locations. We just opened one up in Toronto and we have nine branches. So I'm based in the San Jose branch in the Silicon Valley area so that's a little bit about Insulectro.
Yeah nothing going on there in San Jose?
Lots yeah, so since the San Jose facility is one of the four branches where we do fabrication on master sheets and master roles of prepreg and laminate we do cutting, tooling, vacuum packing, and will also do that on the lamination materials, the release films, and the press pads and things like that. So we do that in four branches…
I'm going to ask you more about that later because you just told me about that yesterday and I had no idea you guys did that. Actually I saw you more as a distribution channel. But before I ask you about that, why don't you give us a little bit of background on your history in the industry and how you came to this? I always say no and no one does this on purpose, unless you're an EE right?
So yeah those printed circuit boards - those of us that got pulled into the industry ,, have been here a long time. So I started actually back in 1983, I was going to school for chemistry and one of the shops back east, actually in New Jersey, was looking for someone to work in plating on the night shift, and ,, the rest is history as they say. I got pulled into the business and the next thing I knew I was coming to California to to work with our sales team. So that's how I got started in this, and then I joined Insulectro in 2001 and it's been great being with this company. So many different materials we get to work with and so many different customers.
I think you're a familiar name and face - being the VP of Technology but you also do trade shows and stuff. You present a lot and are really articulate explaining the technology of laminates because it's gotten a lot more complicated than it used to be back in 1983. I started in ‘84 by the way, and it used to just be, we'll get some FR4 some, prepreg and you're off to the races.
Right yep, back then it was FR4 and polyimide. A little side note, actually the company I worked for made multi wire circuit boards so we also had an adhesive to embed the wires and that's a whole nother story for another time. Primarily it was FR4 and and polyimide and now there are so many different materials and then if you add the Flex materials on top. There's a lot to to work with, it's a lot of complexity but also a lot of opportunity. I mean electronics are going into everything and we're seeing that with our printed electronics products as well ,. A lot of interesting applications from wearables to medical to consumer electronics so that's been pretty cool to be a part of that as well.
Yeah so tell us about what you're seeing on the front lines of current technology and marketing trends that are having an impact on laminate suppliers - ultimately since our audience here is mostly engineers and PCB designers - how that's sort of flowing down and what the impact is?
Okay.
Yeah so big question sorry.
Yeah that's okay, that's all right. It's become a bigger opportunity - a big part of our business - but if you look at materials in general, everybody knows people are looking for higher speeds and high-speed digital and they're looking for lower loss in RF applications the Internet of Things also even data communications and those types of things; car electronics, radar, self-driving cars. All these things need low loss materials. One of our challenges - and again - it's an opportunity as a supplier to the industry; is having the right stuff available for customers and certainly the Bay Area. It's always been a quick turn market, but it's that the time window has shrunk and one of our challenges is supplying all these different materials to our customers, and of course with every laminate system, every resin system you have the different core thicknesses, the different copper weights and then you have the prepregs with different thicknesses, and resin contents. Add to that also spread glass. It’s becoming very popular I'm sure most of the people who watch this will be familiar with the spread glass systems. They have electrical and fabrication benefits but but again, it adds to the part numbers, the variety of materials we have to stock. So we we currently have here, just in San Jose, we have a hundred and seventy-five rolls of prepreg we cut from for customers. And ,, it always seems like our customers need something we don't have in stock.
Yeah.
It's the one thing they need for that application. But you know we try and up our game here and have the right things. And that comes from going to our customers and talking to the people in their design group, in their sales department and asking them; what do you see? You know, years ago we used to work on forecasts. Customers would have a very predictable usage on materials and they'd have forecasts out for some time. We would base our stock on that and we do forecasting today but it's not the same thing anymore. I mean customers may get an order and they have four days to turn it and they don't know what the build’s gonna be until the stackup’s done and and that creates those challenges. But you know, we try again, we try and improve what we stock and what we have here and get better and better at that. It's just never boring that's for sure.
Yeah right, you gotta have a big crystal ball…
Yeah just talk a little about spread glass.
Yeah spread glass now that kind of puzzles me in context of high speed so I'm curious. Teach us about spread glass?
So there's different kinds of glass, what they call standard E glass and then of course the low dielectric constant glass. I'll talk a little bit more about that in a few minutes. But the spread glass is basically that the the fibers, instead of having a crossover and a weave - like you would in a fabric for like clothing - the actual filaments and the weave are spread out, so you don't have open areas and crossover areas, or areas of higher density glass and that makes the system more electrically uniform. So when you have traces that go through the PCB they’re not either going through high resin content areas, or high glass content areas because they'll have different signal properties so you want to make it more uniform.
Are they more in glass spindles - are you saying it's not woven?
Well it is woven but instead of having a high concentration of glass with open areas of just pure resin, the filaments are spread across so you're filling in the open areas.
Okay so they're kind of fanned out you're saying?
Yes exactly there's different terminologies there’s mechanically spread, there's flat glass, but but basically what ends up happening is, the crossover areas where you would have what we call glass knuckles, they're thinner and of course, the open areas now have some glass. So again the system is more uniform it's a composite. So the composite’s more uniform and and like I said that has signal benefits, especially for differential pairs. If you had one trace and a diff pair running over mostly resin, and one running over mostly glass, they'll have different propagation velocities. So you'd have different electrical results, so the spring glass is better for that. It is better from a drilling standpoint, either laser or mechanical drilling. Because you're not going through high concentrations of glass where the crossovers are so there is a benefit there. There are some caveats though, to how it works with filling ground planes. Because the resin doesn't easily move through the glass fabric - you could have some problems filling, so we have to offer not just the spread version, we have to offer the standard versions as well because very often, designs - if they're strip line - you'll have a reference plane on either side of a signal and those reference planes could be heavy copper and they require a certain amount of fill. So you need the standard fabrics to use as well in a stack up. So you might have a mixture of those types of systems - so yeah it does add some complexity.
So now we're not only doing hybrid materials now we're doing hybrid prepreg you're saying?
Well there are different varieties I guess you have to do it that way anyways because if you're doing hybrid you're matching the materials to the bond ply that you're using anyways I suppose, but now you're adding in this kind of third layer almost.
Right.
And then we also have standard copper foil and then we have HVLP or VLP copper and low-profile coppers, so so yeah so it adds. And then of course, all the different copper weights - really everything from 5 micron through four or five/six ounces, so it's all over the place. But yeah actually going on the hybrid thing too we are seeing a lot of mixing the resin systems. In other words you would never mix B-stages in the same layer in other words you wouldn't have one kind of resin melt but you can mix cores so you could have one type of resin system as long as it's fully cured adjacent to another kind of resin system and we see that with RF, because very often what you do is, you have your low loss layer on the outside and then you would have your - whether it's high-speed digital or just DC - you would have that in the other layers and that system would be mixed and there are challenges there too even if you're not mixing the B-stages. Some materials require higher lamination temperatures and if you're not using a standard material that can withstand that, you would have issues or you would have to use a low loss material that has normal laminating temperatures. And typically when we say normal laminating temperatures, we're talking in the 375 degrees Fahrenheit range. Whereas some of the more exotic PCB materials - the filled PTFE systems LCP FEP - they require much higher laminating temperatures more like 550 to 600 Fahrenheit.
For a while I was at an RF - it really never took took flight - but I'm sure you remember not too many years ago, we got on the fusion bonding bandwagon. We thought that was going to solve all our problems but I remember being at a shop where I think we were running our lamp press at like 700 - 800 degrees Fahrenheit for 12 hours with some crazy profile. That's not very sustainable but it was homogenous DK and it had some great performance benefits but it really never took flight. So my gosh let's talk about hybrid a little bit more because I left the industry for a while to raise kids, and when I came back it was like Rumpelstiltskin waking up to all this high speed stuff and I was like wow! And what I did see was an awful lot of hybrids. So can you talk a little bit about what you think - certainly RF and microwave is an obvious one - but talk about what is driving the demand of high-speed digital RF and hybrid technology overall?
Well it's - in very broad terms - it's about electronics, doing all kinds of different things from a design standpoint though it's about mixing, mixing proper material properties in composites that's what you do. You choose one material over another because of its properties and you separate those layers out to get what you need out of a design. So it's driven by cost, some of its also driven by how you would fabricate. In other words, if you had a material that was hard to laminate you could use that as a double-sided low loss layer and then bond the other layers. Conventionally that would run the DC or other signals you would have in the design. We do have some new materials, so one thing I didn't mention earlier is that we distribute for both Isola and DuPont.
Okay.
Isola does have a suite of laminates that are low loss, some of them even with DKs close to the Teflon range, and they laminate at normal temperatures. So making a composite build is a lot simpler. You don't have to do two separate laminations, unless you had buried micro vias. But you wouldn't do it because of the materials. You would do it because it's for the design but you can do it in one lamination cycle so that's one thing we're trying to bring to market and that's something that's been a growth item for us. Some of these new materials like Tera MT40 for example, the Astra MT77. Astra has the lower dielectric constant - a dielectric constant of just under three - that's for certain, for RF designs, whereas the I-Tera is for the mid-DK, what we call the 3.4 - 3.5 DK range but they're both low loss and they’re both laminated. Again at normal temperatures, so that seems to be getting some good traction.
How do they stand up cost-wise against some of the traditional high speed laminate providers?
Well as a resin system PTFE is expensive and then if you're reinforcing it with ceramic or fiberglass, that adds cost as well, so we actually stack up - no pun intended - pretty well with the PTFE-based product. It's not as well-known, many of the designers are familiar with the PTFE based laminates for RF applications so, they go with what they know very often, until they have a need and then they start looking at alternatives. And there's so many different, projects coming on with our customers, we're quite busy trying to keep that education process going.
So I'm putting myself in a designer's shoes today and I was talking to Lee Ritchie yesterday and he was talking about how the speed curve has gone up near vertical in the last five years and I think you and I would both agree that we've seen that trend. I'm putting myself in a designer's shoes, so how do I get educated fast enough to keep up with all these moving pieces? Because like I said, when I left the industry and came back it was completely like a waterfall as far as onboarding all the different laminate manufacturers and then learning about matching bond, prepregs and bonding systems and cover weights. And then, let's just throw in, that we might have this on an aluminum carrier or whatever. How can we do a good job other than hosting a podcast so I get people educated?
I think the IPC design councils are helpful for that. Some of our folks have presented, I presented, our other people presented. Certainly, if you're an OEM or a designer and you get boards from a board shop, reach out to the board shop and say, what are my options? The board shops have to live and breathe this stuff and certainly, folks like myself and folks at DuPont and Isola will also support the board shop in that effort. In fact that's becoming a bigger part of what I do. I travel with my customer to their customers and talk about their options and the pros and cons because you would think, in theory you would want the highest performance at the lowest cost but, it's not just single performance. It could be mechanical performance, it could be thermal performance, there are a lot of different attributes that you would need in the design and you don't know unless you talk, unless the designers were talking to the folks that have the materials background. You can't put all that together and I've seen projects where people have used the same old stuff and then they get unexpected results and so that's what we're trying to do. It's better for everybody if we hit it right the first time. So, that's what we do, we go in and we say, these are the options, this is when you use fired glass, this is when you use standard, this is when you go for the lowest loss possible, this is where you go for a better economy. We have a material called high speed that's very economical and it's pretty low loss, it's a 006 loss tangent and it's compact. It's not as cheap as FR4, but it's close to a lot of the other materials out there. So it's a nice scale of economy. Now it's not for every design but those who have been using FR4 for a long time and want to upgrade to a total low loss system, it might be a good next step. And that product has actually doing pretty well for us. The 4UIS has been growing pretty well and then the high-end products are growing pretty well. The products in between not so much, but, I think it's just a matter of what people need and the design.
All right, that makes sense. Does Insulectro and/or DuPont and Isola put out resources online that designers can get a hold of?
Yeah both companies, obviously all three of us actually, have websites with links to connect slash sheets, tech data sheets, and other things but I don't know if a website will ever be a good substitute for actually having a conversation with someone who's knowledgeable. Certainly that's a good place to start. The other thing too is sometimes a design will have some IPC slash sheet numbers on them, the specification sheets for different materials, and sometimes you're locked into that. So we've seen that with our customers, sometimes they're locked into a particular material set and it may not be the best. And again that goes back to having a conversation with the people involved. And sometimes they’re willing to change and sometimes not. Sometimes they have no choice. Certainly all old legacy military designs are examples where people are really stuck on very old old systems. And there's definitely a better mousetrap in those cases. But like I said, there's no substitute for having the conversation.
So Insulectro for instance, we were just at IPC Apex and I'm sure Chris, you were doing presentations there. I assume that going to trade shows also, there would be opportunities to have face-to-face conversations?
Yeah certainly, seek out - if you're buying boards - seek out your PCB shop. The folks at those trade shows, or sit in on some of the technical sessions, and then certainly, if Insulectro, Solar DuPont are there, great place to go get some information on materials.
Great.
Well I know I sound like I repeat myself often about this, but I've often said, and I used to blog on Microwave Journal to tell people, please go talk to your workshop, please go to your workshop because I think it kind of all ends and starts there and and because, like you said they have to deal with so many laminate and resin systems and all these things every day. A lot of times they could be helpful, it's just sometimes I think designers are so strapped for time. Sometimes they're doing the jobs of two people and so I'm always trying to help the designer get resources as best they can.
Yeah and it's something we appreciate, and what we see happening too, is they'll pick up a data sheet and they look at differences there - sometimes there are very minor differences between resin contents and electrical performance. You don't know the dielectric constant of a loss and they'll pick the lowest on the datasheet, but that might not be the best for the fabrication and having the right material to make the board come out right, yield well, do well after assembly, do well in the field. You're not really giving up anything even if the loss is very minor, higher in loss, but yet the board performs well it's definitely a good trade. So that's part of the problem, sometimes some of the designers who are pressed for time will pick a particular material set. Yeah it might have the lowest numbers, but it may not be the best fabrication. If you can't build it, or if the board shop doesn't yield well, it doesn't do anybody any good.
So I was just talking also to Kelly Dack, Chris.
You would probably recognize his face. Anyways we were just talking about this and it's like what looks good on paper is... First thing, it isn’t always this linear process when it comes to design and fabricating. So, back to the hybrid designs. What would you say for someone that's designing hybrids, some of the the challenges are of those boards and some of the benefits? Obviously performance is one of the benefits.
Yes performance and cost, because very often the very low loss materials, come at a premium, because of the resin systems - the cost of the resin systems - and the cost to make the materials and so on and so forth. So that is another benefit - it can be a challenge for the board shop and it really depends on the materials. The challenges are more often in fabrication than they are in the actual design part of it. Yeah, like I said before, it just varies so much, I mean one of the requirements usually for an RF design is to have a certain level of precision when it comes to forming the circuitry. When we say forming, it could be a plating and etching, it could be just print and etch, depending on the the technology used. And then you would laminate that into a standard FR4 system, and sometimes those materials aren't really compatible. So yeah, that goes back to being able to have materials that have the right CT properties, the right adhesion the right lamination properties.
But you look at some of these high speed materials and sometimes they can be more fragile. I mean they might for instance - and correct me if I'm wrong here - this is second-hand knowledge here, but they might survive the fab process, and lamination cycles, or even multiple lamination cycles, because then you introduce buried and blind vias. And then there's multiple thermal excursions and then you take it to assembly and you've got through-hole and surface mount part and they have to go through another two thermal excursions. And so that it all adds up and it it's not obvious at the outset right?
Yeah those are all good points, all things that have to be considered in the fabrication and use of the part and there's a lot there too. One of the things I'm seeing, is copper is a really good moisture barrier. So one of the things that we try and preach to our customers and their customers or the assemblers if it's a CM, is you have to bake the parts prior to assembly and you can't underestimate that. There was a really good paper put out around 2011 - 2012 at IPC that showed just how long it takes for the moisture to get around because if you have a strip line construction, or if you have a reference plane and RF design, that moisture has got to go around that copper plane. It can't go through it and I've seen people underestimate the baking and end up with with scrap. It's kind of a shame because if moisture is the only reason why you're doing the laminating and assembly it really is avoidable yeah sometimes it's a pain did it bake a board for two, four, six, sometimes 24 hours but, that's what it takes to yield well but it's it's still worth it and that’s something that comes up a lot.
Well I know that I worked for a smaller art shop and we had the case where we were doing kind of pre-production quantities and the board was cooking along, no problem, and then one day it wasn't working. Guess what, it had rained for a week and we didn't have them in an airtight storage or whatever, so we had to completely look the way we were storing and make sure we were baking this, because in California, it doesn't rain that much and it wasn't first and foremost on our brains and when it came down to that, it was like what? Yeah didn't see that one coming at all.
I've seen that happen yeah, I've seen that it where customers or assemblers, they don't bake for years and think everything is great and they want to know what's changed and it's well material’s the same...
Had a heavy winter...
Yeah and it turns out it was something like that, it's always best practice to bake and it varies so much by design - ground planes are a problem. In fact there was a great study done recently with HD Paragon, I don't know if you if your listeners are familiar?
Maybe not, but we’ll put that link below in the show notes. Because they're an amazing asset to our industry.
So they did a great study on crosshatch ground planes on flex so there's some performance trade-offs to the crosshatch ground planes, but they do create a window. Moisture will get in more easily but it can get out more easily and when - as opposed to a solid plane - there is a frequency cut off where that is usable and one of the things the study looked at was diamond-shaped versus round openings in the ground plane. But I always like to put, or recommend putting, openings in the ground plane when you can afford it - just as a moisture egress.
Hmm, that’s new to me, so neat but it completely makes sense right? if you're locking in moisture inside of the laminate because you're capping it off, you're trapping it right?
Right, and a lot of the PCB processes are water based or aqueous based chemistries, even up to the surface finish. You know, Enog one of the most popular surface finishes, it sits in a hot bath for 30 minutes, actually two hot baths. The gold bath in the NIP and the nickel plating bath or high temperature what, 180 Fahrenheit - 190 Fahrenheit for 20 or 30 minutes in each bath. That's a big opportunity for the moisture uptake on the part, and if you can imagine, that's near when the part is finished. It usually gets routed and cleaned and electrical tests and a few other things. But then it goes out to the company that does the assembly some assemblers require the board shop to bake, which is okay if you put it in a moisture proof bag, but even that's not a guarantee because the workshop loses control over when it was opened and how long it stays in the atmosphere before it gets assembled and so on and so forth...
-or just before it gets bagged.
Yeah right.
And it may already be present and you're just vacuum sealing a moisture-laden board. It’s so many moving pieces, I always say, I wish my dear friends that were printed circuit board designers or engineers that are designing boards now understood the complexity of board manufacturing because you and I've been talking this whole time about just the laminates this is not drilling, laminating buried and blind vias, filling vias. There's so many moving pieces and I think sometimes copper bond treatments? Yeah all of that and I think in this day and age, a bare board is a line item on your bomb. It's not like pulling a component off the shelf and so I think the closer board fabricators and engineers can get together the better for both actually. Because sometimes I think the board fabricators also get exasperated with designers, but the technology is being driven in a certain way. And they're gonna be the first ones to see it and can actually help enable the board manufacturers in many cases so it kind of goes both ways
An experienced designer will know what the board shop needs and that's again - that comes from communication - things like minimum clearances, designed for manufacturability, those types of things, and in fact all the board fabricators I know are very good about working with their customers to try. And again it's in everyone's best interest to yield well and have a part that survives.
Absolutely, and back to Kelly Dack, we had a long conversation - actually two people here at Altium, all of our AEs and FEs here - are required to take the CID course and so two guys here recently took it and for the first time I got to look through the workbook. Holy cow this thing is like this thick and a huge percentage of that is the DFM things. It's understanding, so to hopefully save time and money and headache on the end of the designer.
Well Chris, I know we've only got started but we need to do this again clearly, because the other thing I want to talk with you about is flex, because flex is on the rise and I know you'll have a lot of insight there and I would love to ask you more about that. But before we go I always do this thing at the end of the podcast called ‘designers after hours’ because most people in our industry usually have some kind of interesting hobby. or a lot of us, even though we kind of act left brained, we have a pretty active right brain too actually, so sometimes we're creative or do something interesting. So do you have anything that you enjoy doing after hours, sort of unique?
Yeah so actually I've been I've been diving, gosh since the late 70s…
Diving? Oh scuba diving I thought you said dieting, okay!
Yeah so actually I started back east when I was living in New Jersey I actually did some shore diving and some wreck diving and that was a lot of fun. Now in California, when I was living in Southern California, it was Catalina Island and the Channel Islands and so on and so forth. But here in northern Cali the best place to go is Monterey. I've done some abalone diving up in Mendocino, but that's free diving that's not scuba. But, in fact, I've taken my sister my niece there. There's divers also and we've gone down to Monterey and I've done that so that's one of things I like to do. It's something I don't get to do as often as I like of course.
I know we're all so busy. Well speaking of free diving for abalone my mom and dad grew up here in San Diego - I grew up in in Orange County just about two hours north of here - but my mom, when she was a teenager used to free dive for abalone in La Jolla Cove. So about a year ago I moved down here and I'm itching to go get certified and do diving here because there's some really neat dive spots here. But we went to the area where my mom used to free dive and my daughter came up from snorkeling one day and pulled up two abalone shells, which is so rare.
Yeah
Well down here it's so picked over it's like there's divers out every weekend so it's really rare to find live abalone anymore. But anyway, she brought up a couple of shells.
Interesting fact about La Jolla, you can find electric rays down there so Rays are capable of delivering an electric shock.
Really?
Yeah well check it out they're pretty cool - but don't touch them - yeah, they're pretty cool.
Yes my interest in electronics and nature stops. Well thank you Chris, so much, this has been fascinating and I want to ask you 50 more questions but if you will say yes we'll do this again in a month or so and we'll talk about flex.
Sounds great.
Okay thanks so much Chris.
Again this has been Judy Warner and Chris Hunrath with the OnTrack podcast. Thanks for joining today, we look forward to you tuning in again and until then, remember to always stay OnTrack.
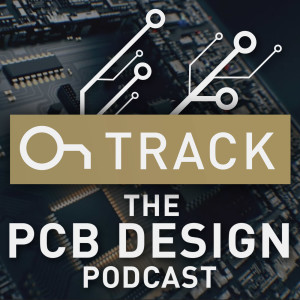
Tuesday Apr 03, 2018
Model Copper Roughness Properly, a Discussion with Bert Simonovich
Tuesday Apr 03, 2018
Tuesday Apr 03, 2018
Bert Simonovich is founder of Lamsim Enterprises and an expert in innovative signal integrity and backplane solutions. He holds two patents and author of several publications. Anyone involved with the design and fabrication of high-speed circuit cards and backplanes or people who needs to estimate PCB transmission lines losses will find value in the paper Bert shared at DesignCon 2018, “A Causal Conductor Roughness Model and Its Effect on Transmission Line Characteristics”.
Listen in to Join Judy Warner and Bert discuss copper roughness and the paper he presented at DesignCon 2018.
Copper roughness is located between the laminate and the copper
- From a manufacturing perspective, the rougher the copper the better
- But for high speed, the rougher the copper the higher the loss
- If you don’t model it correctly you cannot simulate it accurately
- The Huray model dilemma - where do you get the parameters to use for the model?
- Last year’s paper was about correcting the dielectric constant due to roughness
- New model is dubbed the Cannonball-Huray model
- The effort is collaborative, building on each others’ research i.e. Rogers, Polar
- As speed goes up, material properties are more important i.e. Fiber weave effect
- Accurate modeling is very important especially with new standards and tighter margins
Links and Resources:
Bert’s Articles on Signal Integrity Journal
Hi everyone this is Judy with the OnTrack podcast welcome back. If you are new to our podcast make sure to subscribe on your favorite RSS feed you can follow me on LinkedIn please.
Please. I love having friends on LinkedIn or at Twitter I'm @AltiumJudy and as far as Altium goes you can follow us on LinkedIn Twitter or Facebook.
So today I am at Design Con 2018 at the Santa Clara Convention Center and I'm delighted to have my dear friend Bert Simonovich who hails from Canada and so we're gonna chat with Bert today about the paper he submitted and all the things he's involved in. I also want to share with you about our fun history in Hobart and how we got to know each other. So Bert, welcome to our podcast and we only get to see each other maybe once or twice a year but I'm always so happy to see you.
Likewise, likewise Judy.
I'm glad you showed up this year and I'm glad I could get you. Last year I couldn't get you because you were so busy with your papers and everything; you were desperate, you were booked to the gunnels last year so I'm glad we got to run into each other.
So, to give you a little bit of background about Bert... well let me start from when Bert and I met. So what was it 2006 six or 2010?
Yeah 2010, something like that.
Yeah, so Bert was sort of in a transition period in his career and we met on LinkedIn and then we actually met at the show at Design Con and we connected through social media and we're old enough you know, and respectable enough in our careers that we didn't feel like that was creepy or anything. So we connected and we met upstairs; the top of the escalators here at Design Con, and we got acquainted and just networked and boy oh boy we didn't know the number of ways that our past would continue to cross over the years so, we hit it off immediately and Burt knew an awful lot about backplane and tell me again, you worked for a huge company up in Canada?
Okay so yeah we live in Ottawa area and I started my career at Bell Northern Research which was the research and development arm of Northern Telecom or eventually North Dell in Bell Canada.
There you go,
so it's essentially the same as like the AT&T; down here - researching, development and then that later got to fold it into the Nortel umbrella and I was there my entire career. It was 32 years until 2009 when they filed for bankruptcy and then my career ended…
Abruptly.
And that was kind of a shock. Then I was fortunate that I was able to you know - we weren't in bad shape financially - so it didn't hit us like it hit others. So I've considered myself fortunate, but what I missed was the day-to-day and and not knowing what the future was because at that time there was the downturn economy so it's hard for everybody and certainly harder for older ones and we were able to get out and fortunately got our pensions early and that kind of kept us going.
Yeah so that's right about the time I met you, not long after that right, and so you're like: mmm what am I gonna do now? I have all this knowledge and expertise how am I gonna apply it and so on your own dime you flew down here. We met and I was hoping that we were just networking to see how we could help one another professionally and whatnot, since that time - boy oh boy.
IMS came up from the UK to Montreal and we met again there.
That's right we met again there. We met at IMS so then, all of a sudden, our lives started weaving because I was in the RF and microwave space from the bare board side, and then I was doing the guest blogging for Microwave Journal and then you got to know all the folks - or you knew those folks in that space and then you got to know the Microwave Journal folks who have since launched the Signal Integrity Journal and now you're on that editorial review or review board for that magazine?
That's right.
And now, I think you just told me, this is your first year now that you're in the Technical Review Committee?
Technical Program Committee Yeah.
Right for Design Con so you actually reviewed the papers then that were being subpoenaed by some papers?
Yes.
Did they divvy them up?
Yes they basically divvy it up so there's quite a few reviewers for it to get the diversity and not just one person, several people review the same paper as well.
Right good. So, not only is he reviewing papers he's also submitting papers. So I want to say congratulations that you are a finalist for best paper.
Oh thanks Judy.
Well I don't know that’s third time in a row now?
Actually five.
Five! You've been nominated that many times or you've submitted, but you've been nominated that many times. I see, so you are like a rockstar! So, tell us about the paper that you submitted this year.
Okay. This paper is actually a follow-up from last year's paper that I presented and last year after I presented it, there was a great discussion afterwards. It was the end of the day and people - there were no more papers after - and people that were interested stayed and we had a good little wrap of things and were discussing some of my results. And although I was close there was some doubt as to actually what it was, why there was still differences and my co-author Vladimir he had an idea that it's possibly due to causality of the metal.
Okay.
And Vladimir works for a mentor and so he had this idea and I had data and my technique and we decided to collaborate and see how well it would work. So he incorporated his algorithms into the tool and we checked it out and that brought the data exactly right on.
Wow! So this paper is kind of a wrap or closing the loop at the end of last year's paper basically?
That's correct, it's kind of a follow-up in a way and it kind of answers the question that we were suspecting. - the people who were discussing as a group were suspecting - so that was very satisfying when I had that. So we said, well we've got to publish this now so we'll do that.
So it was a copper roughness issue?
Well it's part of modeling called copper roughness, to model copper roughness properly and get the right model afterwards so you can do the simulations.
Isn’t that hard? I mean it seems like copper roughness, which is the roughness - for anyone that's not clear on this of our listeners - copper roughness is between the laminate and the copper. Not on the topside of them it's on the bottom side where it's being bonded to the laminate but it's not always the same?
No the thing is with roughness from a PCB manufacturing perspective, the rougher the better.
Right because there's adhesion.
Right peel strength. Nowadays, for high speed past 10 gigabit, now everything starts to matter and now people are talking 25 gigabit - 56 gigabit all the stuff lost, now becomes a factor. So it turns out the rougher the copper the higher the loss, so how do you model that? If you don't model that correctly you can't simulate it in advance.
Exactly.
So the bottling techniques in accuracy - so there's been different models out there one that's been very popular is the Hury model that was presented back in 2010 because I remember going to that presentation. Basically it was dubbed the ‘snowball model’ because when you look at the roughness profile under an electron scanning microscope, it looks like a stack of snowballs type of thing.
Okay.
Uh-huh and that's where it got coined the snowball model but it's the Hury model and it's very accurately shown that you get very good results measured to simulation. The problem was where do you get the parameters to feed that model? Back then to get it, if you tuned the parameters you could get an excellent fit to the loss but that doesn't help for tools so how do I get that? Unless you're building a board or measuring the board to get the parameters so you can use those again if you're going to build that same geometry in a new design. So that's very time-consuming - pretty accurate - but not practical for smaller companies. If you need a good answer now, rather than a good answer later as Eric Bogatin always says, that never helps you. So, one of my early contract positions, because I started going in consultancy after Nortel. One of my clients they wanted to do some analysis on dielectrics but they also wanted to include their roughness and I knew nothing about roughness at that time. So I started to do my own research into this so that I could try and do the work, and found that it was all over the place in a way.
Anyway, I completed the analysis not even based on what I knew at the time and it was okay, but that seed sort of stuck. So I started in it and once you get an interest in something then try to go further and further. So it's been a pet project of mine so I decided to think about the Hury model and say: well, is there a way to get these parameters based on datasheet value only? If I know the roughness from a datasheet the, height of the roughness, can I get the radius though? So I thought about it and you know, I thought about: okay, this is the stack of spheres. If I stack them up can I determine the radius of the sphere from that stack? So you know it's basic geometry of things and eventually you can get that number if you know this height. So I thought - just out of curiosity - I'm gonna try it and when I did, I got reasonably good results, almost right off the bat. I'm not perfect, but I can tweak things a little bit more and I'm saying okay… That's how it kind of began so it's been over a few years, off and on. I did a paper earlier in 2015, when I first presented some of it, and that was quite successful and every year it's been kind of incremental and testing it against other data and then eventually other software came out like simBR and I started having success with the model there and that was great and so it kind of went. So lately, after that, then I started thinking about I never get the the actual delay property. So in order to model things, you need proper loss and then also the the delay property or the phase. So then I thought well, perhaps, how does the roughness come into it? Because I noticed the rough with the copper I get different phases for the same material. Anyway so I worked out some some things and that's what last year's paper was about, to correct the the dielectric constant due to roughness...
It was really last year's paper.
Uh-huh and so that that worked out very well and when I correct that, I get very good results with it so that's it in a nutshell how I got from there to here.
Wow. So I know you've worked also with Polar instruments. Tell us about how that came about?
Yes so last year Polar had introduced the Hurray model into their tool and I hadn't really met Martin but in his newsletters I always got it and he announced that they were going to come out with the remodel and a Polar tool so I emailed Martin and said; look let me check it out to see how well it works. So they gave me a trial thing just to check it out and I tested it out against my data and there was just a couple of hiccups, but we sorted them out and now the tool - it's a great tool - we can get the parameters now basically from data sheet to fill in. So we've dubbed the model really like a ‘cannonball’ Hury model because it's a combination of both.
Well Martin spoke, I think I shared this with you earlier that in October Martin Godean from Polar presented a talk at Altium Life in Munich and I was chairing the room he was in and he pulls up this stack of cannonballs - you and I hadn't talked about this - then he starts citing all this work by Bert Simonovich. I nearly fell out of chair, like my friend Bert? So I really love that Bert, you've like been such a collaborative force in this industry about these models and you know that you reached out to talk to Polar and really made it better. Not so much in a self-serving way but it's good for the industry really, it's good for designers right?
I think so.
And so I really appreciate that generosity of spirit that you have and it's what I liked about you when I first met you and here we are all these years later who knew.
That's right.
So, what's next Bert? Tell us first of all, where can our listeners find your papers because I'm sure they'll want to get their hands on those?
Yes so I published papers that I have on my website at my company is http://lamsimenterprises.com.
Okay.
Well I'm sensing we'll try to put that in text somewhere I relate to this podcast so folks can find that and then they can find your consulting services there as well but then find all your papers there. Did Design Con aggregate the papers that come out of the show?
Oh yeah they have the proceedings.
But only the attendees get their proceedings right? So they can come to your website is the bottom line, right?
Right, so anyways so for my papers, I have my papers that I published on my website and it's not just Design Con I’ve also done EDI Con papers and that's part of the signal integrity journal. There's an offshoot of that - is EDI Con - and I attended that the last two years, they were the first two. So there's Boston that was great time. Actually you went to the first one?
Yeah I went to the first one I can't believe how our lives have just crossed so many times. We just met each other here and went hi.
And you met and you met my wife.
Yeah I met your wife on that trip.
Bert and I got to go to Fenway Park and have a private party at night and overlooking the fields and they brought out... what are those? I'm such a sports nut.
The trophies from the World Series.
- thank you the World Series trophies. They brought those out so we could you know take photo ops with and we had great food and we got to take over Fenway for a few hours and I met Bert's wife who's just a doll and we had a great time. So who knew when we met how our paths would cross?
But I think Design Con in general is about is networking, meeting new people, learning new things spreading the seed of papers. Like I was mentioning even last year's paper - Rogers took that and then confirmed the data or the theory part of it and then they presented results this year.
It’s such a great collaborative effort and I don't know I find it very refreshing because you know, like well I have a secret and if you give me a lot of money it might tell it to you. This is much more open handed and collaborative. I liked what you said earlier today - which was somebody will present something and then an offshoot will take off and then it'll take off and then someone will build on that and bring it back as something else. It's really the industry together - collaborating.
That's also for mine like 2010 with the snowball model, who knew? That room was packed to the rafters and out - that presentation from Paul Hury and Eric Bogaton’s and he presented that year and I was just dumbfounded and I'm going, well I don't understand it but that's cool, and that who knew that that would be the seed for my work, my research work.
And and then went into Polar and Rogers and it's just like an idea that sprung legs.
And that's just my example. One example of many you just look around - like Eric likes to say - come drink from the fire hose, that's the Design Con there’s just so much stuff and it's there and it's just a great place for that kind of thing.
It is a great show. So, a couple closing items. Number one what would you say for circuit board designers, are some of the kind of greatest challenges they're facing today? Looking forward into emerging technology is there any specific - one or two things maybe - that are sort of plaguing them at this point? Or things maybe they need to onboard and that they are not taking right now?
Just in general as the speeds are going up the actual material properties are really becoming a factor. A big thing is fiber - we've talked a lot about that - fiber weave effect and the industry is looking how to mitigate that effect. A lot of nice papers over the last few years, talking about that and again there's a lot of things on the roughness, getting good modeling because it's important now. And now with everything like the new Pam-4 standards, 56 gigabit. The margins are tighter, so fabricating boards is more demanding.
Yeah it ain't what it used to be I can tell you. I started in the board fabrication industry in 1984. Oh my gosh that seems like such easy stuff compared to today. I was just speaking with John Belushi from ASC and I said it used to be you just got your board, your fab drawing you had your sort of mechanical, here's the size of the footprint, this is the size of the trace plus or minus this, and off to the races you go. Now it's like a board fabricator has to think about everything they're doing and how that is going to impact. You can go to a board shop, make a board and be well within IPC standards and its’ still not performing to the designers intent.
I think it's not just the board shop, I think sort of the industry as well, you have to specify what you want properly in your fabrication notes.
What fabrication notes. What I'm saying is documentation, I think is an issue.
Yes and and the thing I'm seeing is if you want consistent results you have to nail down your design. Basically nail it down and not let the fabricator substitute material for different weaves. For instance if you have a stack up that you first designed it's got to be included verbatim on the fabrication notes. So you must use this material, this weave.You can’t substitute, and you can't play around with all the line widths and space to do things different. By specifying things on the notes that restricts what they can do you should end up getting what you want otherwise you may not.
And you had told me earlier in your consultancy business that you will talk about modeling certainly, but then you also give them the added benefits of giving them some guidelines of how to spec in these.
Yeah so typically a lot of my business is design reviewing boards before fabrication. After they do the design like Altium Board Designer would lay it out, so now there's a design review at the end so some of the clients they'd like to get some review over that visual review and I do that sort of thing for them. But as part of that, I review the stack up even from the board shop because the stack up people are human and could make an error. Typo or a lot of times they're just templates and they don't cut and paste properly or something, and it may not be correct. I haven't found anything that wasn't correct but I do that anyways, just check it, double check that the impedance is correct in things. But on top of that I also say that I'm going to review their fabrication notes to ensure there's consistency there and usually I find that a lot of these are smaller companies or startups. They're not aware of what's needed or they have one set of fab notes and they have the same design all over. They just use it over and over but that could add confusion in the shop.
Yeah absolutely.
At the end of the day part of the design review it's also part of a bit of educating as well to some clients so they realize some of the importance and they appreciate that as well.
Yeah and it is so sorely needed and people don't, like you said especially smaller companies, they don't always have the resources to go out and spend endless hours in a board shop getting educated or whatever the issue is. Or educated about signal integrity or whatever it is, so I think what you're offering in your business and in that niche is really valuable so that's great.
Well my friend I'm gonna let you get back out on the show floor. I'm sure you have a lot to do today I'm sure you're a busy guy so yeah I so appreciate you spending a little time with me and I'm so glad we got to connect I know you're getting so busy - such a big shot these days - it's been a delight thank you.
Actually, the reason I knew you were here, I saw something on LinkedIn and saw you were responding to somebody and I go: wait a minute is Judy here? So then I LinkedIn messaged you last night and I said, are you here? and yeah so let’s connect today.
See there's a lesson to everybody, LinkedIn really is useful. Gosh you and I've met a lot of friends through LinkedIn. I'm so glad to see my friends. I don't get to see you enough so I'm glad to see you whenever I get to see you, I'm not gonna complain. So best to you, congratulations on your nomination again.
Thank you Judy and the same to you.
And have a great show and I look forward to catching up with you next time.
This has been Judy Warner with the OnTrack podcast please remember to subscribe on your favorite RSS feed and we look forward to talking with you next time and always remember to stay OnTrack.