Episodes
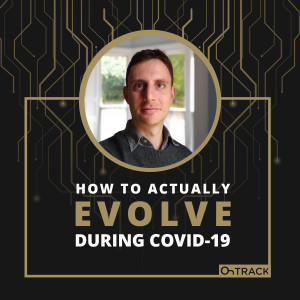
Tuesday Jul 14, 2020
How To Actually Evolve During COVID-19
Tuesday Jul 14, 2020
Tuesday Jul 14, 2020
Angus Thomson is Senior Electronic Engineer and founder of CircuitBuilder, a brand new platform for simplifying the development of custom electronics out of Suffolk, England. Angus joins the OnTrack Podcast to share his experiences as CircuitBuilder’s founder, and to discuss the fine points of CircuitBuilder’s evolving business model, which has so far proven immune to the challenges of the global pandemic.
Altium 365 Podcast Listener Discount
Show Highlights
- Introduction to Angus Thomson
- ”I thought: there’s a better way to do this”—Angus’ road to entrepreneurship
- How CircuitBuilder utilizes Altium 365 to provide customers with realtime 3D views of their designs
- The CircuitBuilder growing network of engineers
- CircuitBuilder’s successful, lightweight recruitment process
- Proving it out in your own backyard: Angus on expanding market reach
- Transparency: How Altium 365 pushes CircuitBuilder beyond the errors of the past
- Design, Manufacture, or both? CircuitBuilder’s evolving business model
- The secret of CircuitBuilder’s resilience during the coronavirus health crisis
- Angus offers his insight on the future of design in a post COVID-19 world, and on CircuitBuilder’s role in that future
Resources:

Tuesday Jul 07, 2020
Tuesday Jul 07, 2020
Istvan Novak, Principal Signal and Power Integrity Engineer for Samtec Inc. and winner of the DesignCon 2020 Engineer of the Year Award joins the OnTrack podcast to talk picosatellites, simulation tools, and the rising importance of power integrity.
Altium 365 Podcast Listener Discount
Show Highlights
- Introduction to Istvan Novak
- A brief look at Samtec Inc., the successful computer equipment manufacturing company headquartered in Indiana.
- Istvan’s path to becoming a Power Integrity expert
- CubeSats and the students who make them
- The challenges of dimensionality: has power integrity become more important than signal integrity?
- When Power Integrity is an afterthought
- The value of expert disagreement
- “Regardless of what we want to simulate, we can find good simulation tools to do it”: Good design and the challenges of modeling and simulation
- Closing thoughts; the first working Picosatellite; and the first electrosmog map of the globe
Resources:
- Istvan Novak on LinkedIn
- Samtec: gEEk spEEk SI Webinars.
- Samtec Silicon-to-Silcon Solutions Website
- The SI-List Archives
- Istvan Novak: DesignCon 2020 Engineer of the Year Award
- BUDAPEST UNIVERSITY OF TECHNOLOGY AND ECONOMICS Picosatellite
- Istvan Novak’s Electrical Integrity Website
- Picotest Website
- Signal Integrity Journal
- Design 007 Magazine, See pg. 38 Do You Really Need That Ferrite Bead in the PDN?
- First Electrosmog Map of the globe
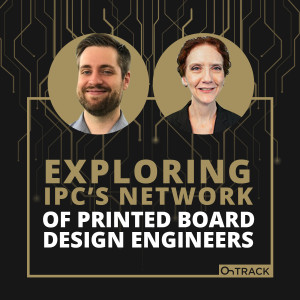
Wednesday Jun 03, 2020
Exploring IPC’s Network of Printed Board Design Engineers
Wednesday Jun 03, 2020
Wednesday Jun 03, 2020
The renowned global trade association known as IPC has put together a network of printed board design engineering affiliates under the name IPC Design. IPC Design’s affiliates are comprised of PCB design engineers across the globe who are working to advance the art and science of printed design engineering.
IPC Design’s Patrick Crawford and Teresa Rowe join the OnTrack Podcast
Work from Anywhere. Connect with Anyone.
Show Highlights
- What is IPC Design, and what is its primary mission?
- Increased global presence and participation: How IPC is molding its future.
- IPC Design’s worldwide buy-in, its fresh new participants, and how the quarantine has affected participation.
- Has productivity gone up since quarantine?
- Lessons in remote working and the importance of taking time for yourself.
- Between January 2020 and now.
- What’s in store for the future: IPC’s collaborative content model.
- America, Europe, and Asia: IPC’s leadership group and global design committee.
- IPC Design is looking to fill a leadership role in Asia.
- What’s in it for you, the designer? Teresa and Patrick count the ways designers will benefit from IPC Design.
- ”Let’s start up a chapter!”: How individuals, student groups, and companies can get affiliated with IPC Design.
- Translators of the world, connect! How IPC Design can serve and collaborate with STEM groups all over the globe.
Resources:
Teresa Rowe on LinkedIn
Patrick Crawford on LinkedIn
IPC Website
Link to IPC Design webpage
Link to IPC Design enrollment page
Patrick Crawford’s video presentation on IPC Design
Realtime with IPC
IPC CEO John Mitchell on the Impact of COVID-19 on the Electronics Supply Chain
Work from Anywhere. Connect with Anyone.
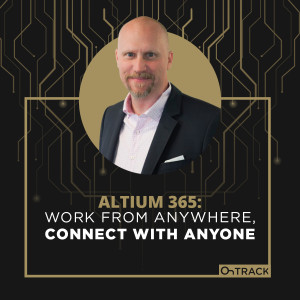
Tuesday May 05, 2020
Altium 365: Work from Anywhere, Connect with Anyone
Tuesday May 05, 2020
Tuesday May 05, 2020
Altium 365 has launched in the midst of a worldwide quarantine effort—a time when companies have drastically reduced the in-office workforce, and financial constraints and travel restrictions have never been tighter.
Altium’s VP of marketing, Lawrence Romine, joins the OnTrack Podcast to explain how Altium 365 removes the obstacles presented by the lockdown effort, why it’s the perfect tool for the post-coronavirus environment, and how the launch timing couldn’t be more serendipitous.
Work from Anywhere. Connect with Anyone.
Show Highlights:
- Altium 365 has launched on schedule; a brief look at why the timing couldn’t be more perfect.
- Working remotely. The Altium 365 cloud based platform which Altium Designer and Concord Pro run on.
- Seamless integration: the symbiotic relationship between Altium Designer and Altium 365.
- Arduino, SkyShips, and you: the various types of Altium 365 users, and how the addition of new features addresses their individual needs.
- Flattening the curve: Altium’s conscientious approach to the learning curve when adding new features.
- Design Reviews in a pandemic—a use case: How Altium 365 removes the obstacles presented by a remote work environment.
- Some users describe the experience of Altium 365’s cloud-based real-time collaboration as “similar to working in Google Docs”. Lawrence elaborates.
- It’s as easy as sending a link: How Altium 365 frees up budgets by eliminating excessive travel, phone calls, and emails.
- “Simplicity is the ultimate expression of sophistication”: Lawrence recalls an automotive experience from his life in praise of Altium 365’s design ethic.
- As simple as using a web browser: How sales personnel are utilizing Altium 365 as a demonstration tool for prospective clients.
- Lawrence’s predictions about the farside of the COVID-19 calamity.
Links and Resources:
Exclusive Sharable Listener Discount Link
Altium Designer-Altium 365
Altium 365 Customer Stories Videos: Skyship, Arduino, Project March
Altium 365 Webpage
AltiumLive: Altium 365
Altium 365 Security
Now you can get the ultimate PCB design productivity with the easiest platform for PCB design. Easily communicate design changes to your team with Altium 365.
Work from Anywhere. Connect with Anyone.

Tuesday Apr 14, 2020
The EMC Doctor is in: Ken Wyatt on EMI and PCB Health
Tuesday Apr 14, 2020
Tuesday Apr 14, 2020
The OnTrack Podcast is pleased to welcome Ken Wyatt (also known as the ‘EMC Doctor’). Ken began his career as a designer in the aerospace industry, and later worked for Hewlett Packard, where he found that his background in RF and Microwave engineering helped prepare him for his role as an Electromagnetic Compatibility (EMC) Engineer. His work has since taken him all over the world, where he develops and provides in-house training and delivers presentations and live demonstration; definitely unique among presenters!
Retiring early in 2008, Ken has since become a prolific author, co-authoring three books, including his latest, in which he identifies why products fail to meet EMI/EMC regulatory standards: ‘EMI Troubleshooting Cookbook for Product Designers’.
Ken currently provides seminars on a variety of EMC related topics—touching on subjects not often taught at the university level. He also provides EMC consultation, EMC compliance and precompliance testing, design reviews, and training services for commercial, military/aerospace, scientific, consumer, and computing industry sectors.
See What's New in Altium Designer
Show Highlights
- Ken lays out his career path, from his beginnings in the aerospace industry, to his current role as a consultant.
- ‘EMI Troubleshooting Cookbook for Product Designers’—a quick look at the book Ken co-authored with Patrick G. André.
- Addressing the prevailing trends in stackups and board design in general.
- Old habits die hard: Why the PCB is the heart of most EMI and EMC issues today, and pitfalls to avoid to move past these issues.
- Signals as the flow of electrons in copper traces and wires: How our education may have left out the whole story with respect to high frequency design.
- How simultaneous trends toward diminishing device size and the Internet of Things contributes to desensing and other issues on PCBs.
- Staying “in the know”: Keeping up with our evolving understanding of the physics of PC boards and signal propagation is always challenging. Ken lays out some ways designers can stay up to speed.
- Why Electromagnetic Compability programs at the university level are few and far between, and how Missouri University of Science and Technology stands out among them.
- Case Studies: The trouble with dog trackers and blood transfusion machines. Ken discusses some challenges he’s come across in the field.
Resources:
Short video on the book with co-author Patrick André
Ken Wyatt on Twitter: @emc_guru
See What's New in Altium Designer
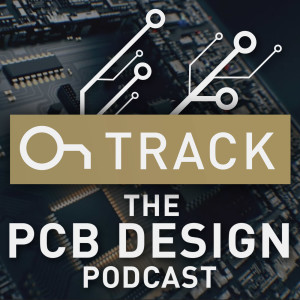
Tuesday Mar 26, 2019
From CAD to PCB: The Data You Give Me and What I Actually Do With It
Tuesday Mar 26, 2019
Tuesday Mar 26, 2019
Gerry Partida, Director of Engineering at Summit Interconnect Technologies, a world class PCB Fabricator, is back to discuss your data package and what he actually does with it. Gerry began his career in the Printed Board industry in 1984 at Everett Charles Test Equipment and joined Optrotech/Orbotech in 1986. He was a member of the team that introduced CAM automation, net list compare, AOI Cad Reference to industry. His current position is focused on cutting edge high density interconnect, high speed digital, Flex/Rigid Flex and RF/microwave printed circuit board fabrication for the military and commercial industries. He is a certified IPC trainer, and a member of the IPC-6012 and IPC-6018 review committees. He is an excellent resource for a wide-range of PCB related topics. Listen to the discussion and learn how to produce an excellent data package which will save you time, money and increase your reliability.
Watch the Video here.
Show Highlights:
- Data has to be modified for manufacturing
- 60% of jobs go on hold due to questions on the documentation
- What data is necessary for a boardshop? One set of Gerber Data for all the layers, legend, solder mask, all the circuit layers, all the drill files, and an IPCD 356 Netlist
- Ensure formats and resolution of Gerber and drill file settings have the same resolution
- What is unnecessary? Title blocks, crop marks; dots showing location on non-plated drill holes, zero sized apertures
- Often the hole count doesn’t match the data received
- The dimensions on drawings often do not match data
- Verify the count and quantity
- When last-minute updates must be sent to fabricator, send ONLY the file pertaining to that layer which the board shop can incorporate. Avoid sending an entirely new data set. This will force the fabricator to verify all the data all over again.
- Always consider the reliability of design: drill diameter, aspect ratio, annular ring, drill to copper, and environment product will go into
- A fab drawing should not be an estimation but a quality tool used to verify that the board was built to all the requirements.
Links and Resources:
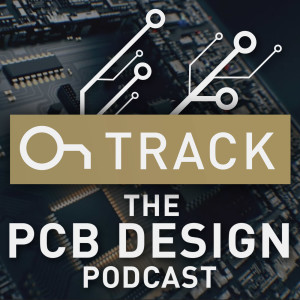
Tuesday Feb 26, 2019
Semi-Additive Process Technology at Averatek
Tuesday Feb 26, 2019
Tuesday Feb 26, 2019
In today’s OnTrack Podcast Judy talks to Mike Vinson, the COO of Averatek about their breakthrough innovation in which they use a semi-additive process incorporating a liquid metal ink as the catalyst seed layer. This special catalytic precursor “ink” can be imaged to create the patterns or areas where conducting metal is to be deposited. This ink controls the horizontal dimensions of line width and spacing and creates the ability to get down to 1 mm and sub-1 mm line and traces. Keep an eye on this technology! Welcome to the future.
Watch the VIDEO HERE.
Show Highlights:
- Mike’s background is in semiconductors primarily in the area of interconnects.
- At Averatek they create HDI solutions.
- What does Averatek’s technology enable engineers and product developers to realize? Lower layer count, Improve Yield, Cost reduction and High Value
- What is Semi-Additive Process Technology? Fundamentally the ink carries plating onto the surface of the substrate, depositing them in very thin layers.
- Also called atomic layer deposition - Averatek calls it lipid metal ink.
- Process allows for very precise and very small circuits.
- Learn the jargon: SAP (Semi-Additive Process).
- Copper can be left undisturbed by the etching process.
- Can be run in a traditional board shop - new technologies are emerging.
- Lithography capital equipment is indeed a worthwhile investment.
- Liquid Metal Ink where are you in getting this to market? Strategy is to license and sell liquid metal ink.
- What type of design considerations will EDA tools need to build-in to enable design with this technology? Smaller lands and increased density.
- Evolution: Lines & Spaces first then other areas.
- Thieving areas parameters will change.
- This tech will work for both flex, rigid-flex, and rigid circuits.
Links and Resources:
Email: mike@averatek.com
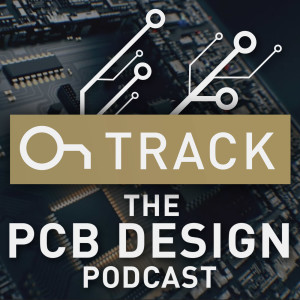
Tuesday Jan 08, 2019
Electronic Components Shortages, Insights from John Watson
Tuesday Jan 08, 2019
Tuesday Jan 08, 2019
Electronic Components Shortages, or part shortages are so big that it impacts nearly every aspect of electronics design and manufacture. Lead times continue to rise no matter how fast parts are being produced. It is just not possible for production to catch up. The reality of this current shortage means it’s time to be innovative, and guest John Watson has some ideas to help including an expert tip Altium Designer users can put to good use. (Hint: ActiveBOM can help!) Listen in to get background on the electronic component shortage, what pro PCB designers are doing to address the concern proactively and stay ahead of PCB component shortages.
Show Highlights:
Shortages first started with capacitors - specifically with multi-layer ceramic capacitors (MLCC) MLCCs - 3 trillion created a year but the supply is still not meeting demand
This is a major crisis in the industry and its spreading
The part shortages are so big, it impacts every aspect. Shortages affecting: Board sensors, MOSFETs (metal-oxide semiconductor field-effect transistors), Resistors and Transistors. Previously unaffected supply chain areas are now being affected.
No matter how fast these are being produced, not possible for production to catch up.
There are three industries driving the high demand that is leading to part shortages:
- IoT - estimated 20 billion new IoT devices in next few years
- Mobile phone - 1.5 trillion mobile phones in next year. 1,000 capacitors in each phone.
- Automotive - 2,000 - 3,000 capacitors in regular / 22,000 capacitors estimated in electric car - as newer technologies are being pulled into regular automatic cars, just think of all the electronics i.e. safety features, automatic parking, etc.
New automotive organization:
AEC - Automotive Electronic Council is putting out standards that will be required for their components. Why? Because...
More rigorous components are needed in order to perform in harsh environments.
Almost 50% of those components have fallen out, or failed, to meet their tests.
On the component / part manufacturing side:
Converting lines from large components to smaller ones because not many people buying them.
Manufacturers shutting down entire lines so they can produce more popular sizes.
On the vendor side:
Vendors have moved towards part allocation - big companies get first in line for parts.
“You can only buy parts with if you have bought with us in the past year” - this is allocation.
Once a company is in allocation, they begin to stockpile components.
What kind of lead times are most common right now:
Short lead time - 16 weeks
Medium - 32 weeks
Long - 80 weeks
What makes this part shortage so different?
Mainly a market driven shortage, that cannot be pinpointed to a specific material shortage
It’s almost an ‘emotional shortage’ where people may be hoarding more than they need.
The extended duration of it is also unlike previous shortages.
It’s a scenario where the market compounded onto itself with its reaction to it.
HOT TIP: The next big thing is Broadband Satellite. SpaceX and low flying satellites to make everybody wireless. This is huge, it’s a lot of hardware.
Component Shortage Hacks to get through the Crisis:
- Overall, be as proactive as possible.
- Evaluate common design guidelines and step out of them. For example, can we change the norm values, parameters and tolerances? It doesn’t always require the most stringent guideline, there is room for adjustment, depending on the type of device and requirements.
- Be proactive, for example run your schematic through ActiveBOM and get flags on what components are not recommended. Don’t wait until layout, do it early on.
- You can also use Octopart, there are other free services.
- Leverage your procurement organization, give them the heads up with difficult components so they can be aware of the situation in advance.
- Create multiple footprints for designs.
- No single sourcing for components, don’t get tied into a single organization.
Where do you source parts or find out about availability during the shortage?
- Read the quarterly reports to get the latest, look at the numbers, watch the trend.
- Keep aware of the issues i.e. part availability reports
- Texas Instruments also has a lot of information.
PCB Component Shortages and using ActiveBom:
“ActiveBOM came out just in time. It has been the go to tool for us.”
Now we run legacy products through ActiveBOM.
Links and Resources:
John Watson Podcast on PLM and Library management
OnTrack article about Part Shortages
Watch John Watson clips on Youtube
Download the latest Altium Designer 19 today.
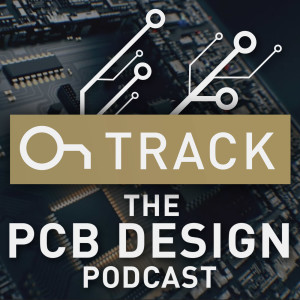
Wednesday Dec 05, 2018
Stephen Chavez Calls on PCB Designers to Get Involved
Wednesday Dec 05, 2018
Wednesday Dec 05, 2018
Stephen Chavez is a leader at a military aerospace company, former Marine, CID and CID+ instructor as well as an Executive board member of the IPC designers council. With 28 years in the industry and heavily involved with IPC, Stephen has a passion for PCB design and fabrication. If you want to keep learning or get involved in the industry, Stephen will encourage you to get connected, step out of your comfort zone and pay it forward. Listen in and get great tips about where to find training and how to push yourself to keep learning.
Listen to the Stephen Chavez Podcast or watch the video here.
Show Highlights:
The Best Professional Development:
- AltiumLive Munich - learn more or register today
- IPC APEX, San Diego - manufacturing perspective, fabricators, if you don’t have time to get into a board shop this is the place to be, machines are running live
- PCB West - pure design for PCB designers; content is second to none
- DesignCon
- Del Mar Electronics and Design Show
- PCB Carolinas (1,000 people/ 1 day conference)
- IPC Designers Council, etc.
- CID Training
- Reading--Trade magazines - UP Media (Printed Circuit Design & Fab and Circuit Assembly) and 007 iConnect - the articles and content in these magazines are the best.
Get Involved!
- Ask around (for resources, help, mentors)
- Take Risks and take initiative--spend money, assert yourself
- Serve/Volunteer
- Networking/Relationship building
Live part of everyday outside of your comfort zone
- Don’t be afraid to ask questions--others have the same questions and dont ask!
- Expand your network, meet people
- My network comes with me in every new relationship I build
- Add value to others
- Don’t sit on the sidelines
Links and Resources:
The Digital Route, November 2018 Column
Breaking the Design Data Bottleneck, interview in iConnect007
AltiumLive Munich - learn more or register today
Altium Designer 19 - learn more or call your account manager to learn more
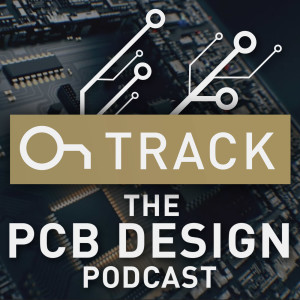
Tuesday Aug 14, 2018
Concurrent Engineering with Bill Brooks from Nordson Asymtek
Tuesday Aug 14, 2018
Tuesday Aug 14, 2018
Learn about what is involved in true concurrent engineering and get practical tips for including stakeholders early on in the design process with Bill Brooks from Nordson Asymtek. When project collaborators come together up front, then they move forward together. Hear how Bill spends the time up front to get everyone aligned during the PCB design process to ensure fabrication and assembly processes progress with minimal issues.
Show Highlights:
- Bill had an interesting childhood. His Dad was an inventor and worked on the Pioneer 10 spacecraft. He introduced Bill to the electronics industry.
- He also started a board shop in the garage and created his own hydro-squeegee, using peanut oil.
- Bill’s career started when he worked as an Electronics Technician for almost two years. When his employer started hiring designers to do PCB layout work, he grasped the opportunity.
- Back in the day, people used to sign their PCB artwork.
- There are a host of stakeholders involved, the designer is like the glue that holds everything together. Some of the stakeholders are: Fabrication, Assembly, Testing, Marketing, Managers and Engineers.
- When do you get the stakeholders involved in the PCB Design process? The IPC standard is to have a design review upfront, before design.
- The designer is the only one who can control moving the design through the process and make the board survive.
- We involve many stakeholders from the outset. Divisions like purchasing takes care of primary suppliers to ensure they can provide what’s required.
- We do system integration in-house. Partnering with other companies has become a big deal and it’s working very well.
- What does Concurrent Engineering mean? Considering all aspects, together, upfront, then moving forward together. Spend the time upfront to avoid wasted time and effort later in the process.
- Educate people who have control, they take care of everyone and everything goes smoothly, works correctly, and is right first time.
- Bill’s Dad used to say ‘the hurrier I go, the behinder I get.’ You need a disciplined management team to do the work upfront, be quick but don’t hurry.
- A ‘quick and dirty prototype’ is a myth.
- Use software to load projects into a common depository - keep it current and work in cohesion with regular refreshing.
- Bill and their team use Playbook, which enables managers to have a full overview of every division’s progress and enable proper scheduling.
- Designers after hours: in 2008 Bill was introduced to sculpting. Started attending classes, commencing a 6-year love affair with sculpting. He now teaches on Saturdays.
- Rick Hartley encouraged Bill to do mentoring. Bill is now part of the International IPC Executive Board and has received an award for his contributions.
Links and Resources:
AltiumLive 2018: Annual PCB Design Summit
Hey everyone this is Judy Warner with Altium's OnTrack Podcast. Thanks again for joining. Today we have another great guest - do you ever get tired of me saying that? Another great guest because we just have them every time, and we'll be talking with Bill Brooks today from Nordson ASYMTEK, and before we get started, I just wanted to remind you to please follow me on LinkedIn. On Twitter I'm @AltiumJudy and Altium is on LinkedIn, Facebook, and Twitter - and also if you'd rather watch this on video we also have this on Altium's YouTube channel under videos, and you'll see all of our podcasts recorded there as well.
So today we have Bill Brooks, has been a great contributor to the industry, as well as being a very talented designer in his own right. So I thought you would enjoy learning about his long history in the craft of PCB design, so Bill welcome; thank you so much for joining us here. Bill comes from just up the freeway here from our office in La Jolla, so it's handy to get him over. So Bill won't you talk about your professional history? I think you, like many printed circuit board designers; you were kind of set up to be in this industry, but you found your own path. So, tell us a little bit about that?
Yeah I guess when I was a kid I didn't know where I was gonna go...
Yeah me neither.
-my dad kind of introduced me to the electronics world, and right out of high school actually, I was still in high school - my dad was working in the aerospace industry and he decided to start his own printed circuit board shop. He looked around San Diego at the time, and there weren't a lot of shops to go get boards made and he said: well, I can do this. And so he looked up the information and we started making printed circuit boards in the garage.
Good times, that was a long time ago where you could set up a board shop in your garage.
Yeah it was - today it'd be completely illegal.
Yeah right.
[laughter]
I think the neighbors complained, he created his own hydro-squeegee and he was using a fusing oil, which was I guess peanut oil, and he bought this big 50 gallon drum of peanut oil and he used a check valve, and he put this - - he used air pressure to push it through a check valve and to spray it so he could put the boards down to get them hot after they had been coated with solder and then squeegee ''em out as he pushed on the pedal on the floor. And it would just make this nice beautiful-
It's a handheld hot air leveling machine!
-Yeah it was very dangerous, in fact, I think he got burned a couple times.
Oh I'm sure!
-but the neighbors just loved it because they’d look down at the corner of the cul-de-sac and they’d see this giant plume of black smoke coming out the back of the house, going: what's he doing over there? But dad was kind of an inventor and he liked to invent things. So he didn't go out and he was kind of a 'shade tree mechanic' - he'd figure out how to get something done on a dime and do it himself. And I guess that same ingenuity was something I picked up, I figure out how to get things done.
So how did you end up going down the design path, from building boards in the garage?
Hmmm it was kind of convoluted. I thought I wanted to be an Electronics Tech and eventually Electronics Engineer, and I started down that path. I got a job with a company that was making television headend equipment; the transmitter part of it, there was channel 52 UHF subscription television, Oak Systems and I started working as Electronics Tech for them and I did a lot of work for them for, oh at least two years as a Tech, and they were hiring in printed circuit board designers to do the layout work. And I had already learned how to do layout work with my dad's shop when I was younger and I looked at that, and I said: welI can do that. How much do you make? And I think I was making like seven bucks an hour at the time, and they were making like 10 or 11. And I said: I could do that, and I told my bosses I want to do that - I can do that! And they were: okay we'll get you in the other department and I started working in the drafting department. So I got a $3 an hour raise and I started doing layout work instead. And it kind of set me down that path. So that's how I got started anyway.
So Bill, a lot of people that have been around a while, both you and I have been around a while. There's no college to learn what you've learned. So how did you pick up, we were discussing this earlier; you've done so many aspects - RF, some electronics and mechanical, how did you pick up all those skill sets, sort of along the way?
Yeah that's kind of a long story really. My dad started me when he had his shop, and gave me a printed circuit board to do as a way to teach me how to do layout-
Okay.
-and we went to the TI Handbook and found a circuit for an audio amplifier - 10 watt audio amplifier and he said, why don't you try to build that? And so I made a schematic, I took the schematic from it, and I laid out the board and we manufactured the board and I bought the parts and I put them on the board, and I soldered them and turned it on and talked through a microphone - it worked and I went: yes that's hot!
It's so funny.
I remember in seventh or eighth grade, we had a science fair in junior high and everybody made their science project; we had a bunch of tables all set up and my dad said, well why don't you make something - - an electronic metronome? It has to do with music, and so I drew a schematic and I put the whole thing up there, and I built the metronome and I turned it on so it'd go 'tick-tock' 'tick-tock' you know, and I thought that was amazing. It was a really great and one of my friends said: Bill that was so cool, how you did that because I didn't have to do any of the work and I still got credit for it and I said well it was it was a challenge. So I took it on I put it up there but I didn't win a darn thing!
The guys who made the volcano that spews out all the stuff - they got that prize. So people didn't appreciate what I was doing. I felt a little bit geeky and kind of out of the norm as I was growing up. But I was fascinated with electronics. I was almost intimidated by it. My dad was a very good R&D guy, and he worked in the aerospace industry and he actually worked on the Pioneer 10 spacecraft, it traveled all the way past Jupiter and it's outside our solar system headed on for Aldebaran now I think.
That's crazy.
So that's kind of a neat thing and I think on one of his print circuit boards, if you find down in the little corner you'll find his initials there-
Out in the outer regions of space.
-yeah and I talked with Dr. Walker Fillius, he was the principal on the project at UCSD and after my dad passed away and he sent me back an email and he said: you know someday these little green men out there they're gonna find that and wonder: what does that mean? Why did they put that there? And a lot of people did that back in those days, you used to be so proud of your artwork you'd want to sign it and they did.
Right, that's funny.
Yeah.
So from I have to say, I think that was probably really invaluable experience for you, very young, to put together that design affected manufacturing, affected assembly, affected performance. Like at a very young age, you saw that whole overarching process - sort of on a small scale - but still; and not everybody gets that experience even today, few designers.
Few designers have ever been in a shop and actually made a print circuit board. A lot of them are dealing with the drafting side of it; they don't see the whole process.
Right and it makes such a difference to decisions you make as a designer.
Absolutely.
Right and so I can see how that sort of set you on a path to be a little bit more globally minded about the whole soup-to-nuts kind of - - from design to reliability or how something is actually functioning.
It has a lot to do with curiosity, it's funny; I've been listening to a book about Leonardo da Vinci and one thing that was amazing about him is, he had this insatiable curiosity, to almost distraction, I mean he would look at things and go: why does it work that way? And he'd start, he'd set himself a task to figure it out - and he didn't have a college or someplace to go learn those things - he had to do it himself. I've done a lot of the same kind of things in my life. I get fascinated with something and I go: well, I can figure that out, I'll go figure it out - all it takes is being brave enough to try and not being afraid to fail. Failure is just an opportunity to learn more.
So I think it was Edison once said , he did like hundreds of different ways to try to do a light bulb and he said, well now I know a hundred different ways not to make a light bulb, it's okay-
I still finally need way to know how to do it right?
-but those those skills and the curiosity drove me into expanding my knowledge base. Getting into printed circuit boards, I wanted to learn how to take the thing I knew how to make, and turn it into something that was a product. I wanted to find out how to make that product appealing to somebody so that it made them happy with the product and not unhappy with it. And that kind of dovetails with what we were talking about before.
We have, as designers we're kind of the glue to the whole design process. We may not come up with the initial idea that needs to be created, but we take that idea and we turn it into reality and we not only have to turn it into reality, so that it's electrically functional, but it can be manufactured in a reasonable way that's not super expensive, that's reliable, that survives harsh environments or abuse. It has to be testable so you can provide for test points and things of that nature. There are a whole bunch of stakeholders involved.
People who are - their job is keyed on being able to take what I create and turn it into a product that they can actually sell. The marketing people have to make sure that the product meets the customer’s needs. I have to be aware of that when I'm designing it so, I don't design in some function that makes it fail there. I have to be aware of those things. So the designer - they're kind of the key glue to the whole group.
But I find that very refreshing and I think most professional designers, from our early days of making a simple 2 layer board say, it's so much more complex now. So we tend to like head down, into our specialty right and I think, as you have said some engineers/designers have never been inside of a board shop.
Right it gives you myopia, you can only see just your part of the whole process.
And I can understand that because, I don't say that from a critical perspective, it's a very complex process. We're time constrained, resource-constrained, so it's hard to put your head up for a moment so-
You just named some of the stakeholders.
-I would say fabrication for sure, assembly, testing...
You mentioned a marketing department, probably managers too.
Managers all have cost and time constraints, they have time to market that they have to be worried about. The engineers of course, typically are going to be concerned about, can they get the parts or are the parts available; are they gonna be end of life parts?
Yeah that's a whole fun bag of fun there.
The hardest part for some designers is, they'll get the board 90% done and then the engineer comes back and goes: I can't get that part anymore, I need to put a different part in and that's bigger than the one I gave you before. And so you got to go back and fix the circuit, so you can fit that bigger part in there and make it work. And it gets quite challenging.
So when do you recommend to get those stakeholders on board and collaborating?
That's a great question and funny - if you go through the IPC; I think it's 2221-standard - it's like the very first - almost first paragraph and the thing it says: make sure you have a design review up front first, before the designing begins. Why do they say that? Those people all are going to bring their expertise, and their wants and desires, and their concerns to that meeting. Well they're gonna be a part of that and give that information to the designer who really is the only person who has control over what it ends up being. The creator - they are the creator; they take all the information and they create something that can be built, tested, cost-effective, survive, functional, not have EMI problems, EMC problems... it has to pass safety agency requirements like TV and UL you know?
Yeah.
Or stand somebody handling it and giving it an ESD shock - thousands of volts - how's it going to survive that? You know, we do Hipot testing, there's a lot of work that goes into making a board that just is not - just connect the dots.
So you're now working with Nordson ASYMTEK, which makes assembly equipment correct, or is there more than that?
Their key thing, the company I work for they're making robotic equipment. The equipment allows manufacturers to do high-speed manufacturing very reliably and typically they're dispensing fluids. They have a few divisions that do board inspection. They have one that does plasma cleaning-
Mm-hmm.
-it's very common, I think it's MARCH - - I think is the name of it, something like that, but primarily we focus on fluid dispensing; got lots of patents on fluid dynamics, how to dispense a dot of material that's the exact amount of the material, in the right viscosity, of the right mix of materials, and at the right place , at the right time.
Right.
Very, very challenging stuff - we've come up with some really high tech equipment that are making our customers real happy.
That's great, so when you do, on a practical, where the rubber meets the road stuff - when you embark on a new design - do you get the stakeholders together? I mean how do you do that?
We get a large number of them involved. We have a purchasing department that cares about who our primary suppliers are. They review them; we go qualify them, make sure that they're going to be able to supply what we want, when we want it, at the price we want it. We use third-party vendors to make the boards, assemble the boards, test them. We put everything together in-house. They call us a system integrator kind of thing - and I guess that's one way to refer it. So the final assembly stuff all happens in the factory; and then we ship overseas and here in the United States and Europe.
So you used a term which I've heard before and just tell me what it means to you, is the term 'concurrent engineering'?
I was introduced to that a while back, and to me it was confusing at first. Of course I've been in the industry a long time and there used to be a model where engineering would be a little black box and inside, all the engineers do all their stuff in there, and it was black magic, and they got it all done and then they went; pop - and they threw it over the fence and said: okay, you guys figure out how to make it. And that's as far as they went. Engineers were done; okay, I'm working on my next thing have fun. And the manufacturing engineers get it and go: oh my god, how are we gonna build this thing? And they almost had to re-engineer it to make it producible. So that model was going along for quite a long time here in the United States, before they started analyzing what the Japanese were doing and looking at their manufacturing process. It was very organized, and they introduced just-in-time, which has affected the whole supplier chain.
But partnering with other companies to be able to be successful has become a big deal and they can reduce the number of staff that they need to do what they need to do. They can have highly qualified people doing what they need to do - they don't need masses of people - and then they can subcontract things out get them delivered on time, put them together and get them out the door and they're very very good at it.
Concurrent engineering means thinking about everything up front. Not just your part of putting it in a black box and playing around with it until you're happy and then flipping it out and saying: you guys figure out how to build it. You want to bring the people that are stakeholders in up front. And then together, you move as a group. And the people involved in the engineering part of it have to understand those people's jobs, because they're their customers.
Right.
They're the ones - they're gonna use what they create. So we spend more time up front to make sure that they don't have to work harder, that they don't have to redo it, that we don't waste money and time out there with failures and have to come back and make changes and send it back out, saying: how about this one? No that's not good enough you've got to do it again. Oh how about that one? No that's not good either. So you educate the people that have control of it - they put the intelligence into it to take care of them and everything goes smoothly, and we make a lot more product, a lot less expensive, and that's right the first time.
You and I were swapping some little statements right? So one I remember you saying - - I don't remember who you cited: the hurrier I go...
That was my dad...
-that was your dad.
Yeah 'the hurrier I go, the behinder I get'.
[laughter]
Yeah and that's so true I mean it's funny if you have this: I'm the only important person in the world, and what I'm doing is the most important thing and I don't care what anybody else thinks or wants to do. You can create something, in fact, I've seen some amazing sculpture, of components that were soldered together and in the most amazing ways and it was an electrical circuit, it worked, functioned.
Yeah - but if you touched it, it would fail, if you moved it, it would fail. It wasn't built - it was just to see what would happen to the electrons when they get moved around that way. So people - and there's a desire - typically management, has traditionally figured, well - if you whip the horses harder and make them go faster you'll get there sooner.
I have seen that by the way being a board manufacturer and selling to and working with designers. The constraints are brutal sometimes...
They can be.
-and it's like, well if you want me to put out good work, you need to give me a little bit more margin right and so I think, to your point is, you had also said that it's really a myth, the idea of a quick and dirty prototype.
Yeah it really is
- it's kind of a myth - I've worked in environments where there was a philosophy that said: we can be faster if we just slap something together and we go build it and we bring it back and see what it does. I think the people that had that idea probably didn't have any simulation tools. They didn't have any way to predict how it was going to behave - so they would make one and go try it, and then they'd find out how it didn't work and make another adjustment. So I remember working on a board that had 17 or 18 different iterations of them trying different things...
That's so expensive and such a time suck!
-Very expensive and it takes a lot of patience - you just kind of have to work with them and keep going and keep going. But we win when you get a management group who - I happen to work for one - it's very, very smart people, they'd like to do it right the first time. So they spend the extra time upfront. They do the research, they analyze what's going on, and then they go build it. When they build it and bring it in we're like 98 percent there, most of the time. Very few times maybe we get one or two little blue wires and we're good to go and take a few changes boom - you're out the door. And that's a good thing and CAD tools help us do that too, by the way.
Yeah well, and that's a really insightful management team I think, to know that if you take the disciplined time to do it up front, it really saves you so much on the back end in regards to time, money, and resources. I always like John Wooden's quote; he used to say: be quick but don't hurry, it's the same thing - like be nimble and quick - we don't want you dragging your feet but don't be hasty.
I think part of it is just having a good work ethic, the self-discipline to say: you know what, I'm here, I'm gonna focus on this, I'm gonna get it done, and I'm not gonna let Joe come over and talk to me over a half hour about the thing he was doing up on the mountains last weekend, or stop and shoot with people at the water cooler or whatever. I'm gonna stay focused on it and when I'm not here then I'm doing other things, but when I'm here I'm focused. And I think that the managers; they should analyze the people and look and see what kind of people they have, and try to work with them to get them to have that work ethic. We've got lots of distractions in our world, plenty of them, things that can take us all over the place, so it's just a personal discipline I think.
So we talked about, in those cases - I'm thinking about the people that are designers that are listening to us that may not have such an insightful management team as the one you work with and I'm sure you've worked for other less insightful management teams. How do you recommend that you tactfully, and professionally, push back to say, I need five more minutes to get this right - how do you do that?
Well to frame it as pushback, is probably not politically nice but it's a communication. I think one of the things that you don't do, is you don't go off into a dark room somewhere and then pop out with a design later on and they're going: what's happening what's, happening, what's happening. So you have to have a lot of open lines of communication with your team.
We use SVN as a way to load our projects into a common repository and then the other engineers that are working, can download that and refresh it, make it current so the master is in the SVN file. So I'm working on basically a copy that I refresh every time I do some work. And I do that regularly, I don't wait very long and I'm refreshing it - I'd do it many times an hour sometimes. And sometimes maybe I go for a couple hours and then we'll refresh it, but it's mostly based on how much change I have made to it.
The idea is to keep it current and keep the lines of communication with the other people concurrent so that they're aware of what's going on if they're busy working on the schematic while I'm working on the board we can do that in parallel, and I can do my parts get them done and then they can say, oh I found out I have to change this part, or I need this other circuit in there and I've just uploaded it - you can pull it in and and make the changes. And we do that very often.
Which is really great and I know here at Altium, R&D is working very hard to make sure that people can work concurrently and building those subversion networks and, even going beyond that, as we delve into Nexus and other products is to enable that, so you guys are seeing each other work in real time.
Often times this is kind of a neat thing about that tool. We typically, the group I'm in is the new product development group, so we take the 'pie in the sky guys' stuff and we turn it into a product. Then we have Reliability Engineers who have to design a testbed to test the product. So oftentimes when the schematic gets to 90% they've got a copy of it and they're looking at it while we're designing it...
And there's the concurrent engineering isn't there!
-Exactly.
It really is a tool that enables that concurrent chain.
It enables it - so we're able to do that and then the guys in production want to know what's going on with it, so they can pull down a copy and look at it, and then the next time we have a review meeting they'll bring their thoughts to the meeting and they can say: we like what you did over here, but we'd like to change this because it helps us be more efficient, and we can run that back there because we need to do that; we listen to them...
Which is so great.
-having that dynamic - real-time communication - it's really huge in being successful the first time.
Yeah that's great, it's great to hear. So but...
tact is used to push back.
-tact yes.
I used to joke with my boss; did you ever see the movie The Money Pit?
Yes.
And the: we're gonna fix the house and the farmer shows up and says, how long is it gonna take? Two weeks, two weeks. We used to do that. Looks like, wow this will take two weeks. Most people can accept two weeks, but we've got a new tool now at work; Playbook - and it allows them to get all the stakeholders involved in helping us schedule the project. So people who say I'm gonna have my test part of it ready at this time, and I'm gonna have the board ready at this time, and I'm gonna have my schematic ready at this time.
The managers can see the whole thing without having a good run around and bug everybody - it's all right there.
If there's a problem with a schedule - update it so we know what's going on. Tell us, and they get it; they see the impacts, they see when things are going to happen and they can strategize and make plans on how they're gonna pull something in or adjust something to be successful.
That's great to create the level of transparency right?
Yeah so pushback is really more...
Well you know, that makes it sound like the manager's a bad guy. They've got a job to do and they've got to get a product to market in a timely way, at the right cost, so I'm just saying is sometimes to your earlier comment like the whips to the backs - at times it feels like that and sometimes you have to stop and go: okay...
How can I communicate better?
Yes, how can I communicate this in a way that makes me me your ally here?
Exactly.
I want to help you win, we're on the same team by the way, and me getting this done right the first time...
You can help me be successful in doing it the first time, and you, and you, because I want to get all the things that you need into the design. That way you're happy with it and you can make it and you're not gonna go; damn that Bill Brooks - why did he do this?
Oh gosh we love the finger pointing don't we?
Yeah I've lived through a lot of that.
Well Bill, this has been really good and really practical, I think where the rubber meets the road. And this part of the podcast, I sometimes like to call Designers After Hours. I want to particularly focus on what you do after hours because you are a very creative kind of - use both sides of your brain - but you have a very strong right brain. So can you tell us a little bit about what you do after hours when you're not designing boards?
Gosh - let's see; was it 2008? I went through a divorce and I was trying to find something to do with my spare time and I got introduced by another engineer at Datron World Communications where I used to work; and he was taking classes in sculpting and he showed me a picture of a sculpture that he was creating; this head of his wife, and I had met his wife - she was wheelchair bound and it was so neat to see the love, you know. He is caring for her and she needs him to push her around and whatever. But he was making a sculpture of her and I thought that was really cool and the likeness was amazing! I thought, you really did a good job, I was really impressed with it. How in the world did you learn how to do that? Because I'm taking classes in Carlsbad.
Bullshit - what? Nobody teaches that right, I don't see classes for sculpture anywhere. Where do you find that? And he says, no it's real, you should come check it out. So I made a point to go down and meet the teacher and the teacher introduced me to it and I thought, this looks like too much fun I’ve got try it. And that started about a six-year love affair with sculpting. And now I'm currently teaching it so - there's a place called The Green Art House in Fallbrook and every Saturday I've got a class there and I teach sculpting and it's fun.
And we will share this link by the way, because your mind will be blown. He doesn't just do a little hobby sculpting - these are amazing sculptures he makes! And oh my goodness, and then I start prodding him about painting... Oh yeah I would love to take a painting class. Bill says, oh yeah I do that too.
About two years ago - maybe almost three - I was at a gallery where I had my bronze sculptures that I had made from the sculpting studio and I was trying to see how they would be accepted in the public and so forth. So I had them in a gallery and I met a guy there, Richard Struggles who's a teacher, and he teaches how to paint and so I got brave one day and I thought: I could do this. So I went down to Michael's and I went through the paint department found the primary colors and some paintbrushes and a canvas and I said I could do this and I just bought it and took it home and I thought I'll find a picture I like and I'm gonna try it.
Well about three hours later I said, you know it's not bad - it doesn't look too bad, I bet if somebody taught me I could do better. So I asked him, I says I see you teaching people, can I come? He said sure come on down. So that started me learning how to paint and I've done about eight or nine paintings. One of them's a triptych; it's some cheetahs it's hanging in my mother's home, behind her couch and it's real pretty and a lot of horses.
I know I love horses I owned a horse and so I love your sculptures and your paintings of horses.
I used to have horses too - so I know that bond and the connection with the animal - it's amazing.
So anyways, just for giggles we will share Bill's amazing artwork there because he does have a good after-hours gift there. Will you please share with me any - I know you've shared with me some links and things we'll make sure we put those up for our listeners that could glean more information from Bill. Bill's also taught PCB at our local college here, and he has mentored many people as well as being mentored throughout his career.
I can blame that on Rick Hartley.
Rick Hartley who we just had on the podcast today.
Yes he was, in fact, he cornered me. We were doing an interview right after the Top Gun at PCB West, and he said: Bill, you've got a lot of experience. Have you ever thought of mentoring? And I said, no I never thought about it, to me making boards was just a way to get a paycheck. Get paid, go home, buy food take care of family do all that stuff. And that seed it planted, made me seek out the IPC Designers Council and I joined the local group in San Diego, eventually became part of the board, and then I joined the International Group and actually became part of the Executive Committee and also the Education Committee. And I think I've got an Emeritus Status now with them. I mean I've been with them a long time and I've contributed as much as I could. In fact they gave me an award once for contributing to the industry so it's good fun.
Yeah we'll provide all the links we can. We thank you again for joining us Bill.
Thanks for joining us today in office and again this has been Judy Warner with Altium's OnTrack Podcast and Bill Brooks with Nordson ASYMTEK. Thanks for listening, we'll see you next time. Until then, always stay on track.
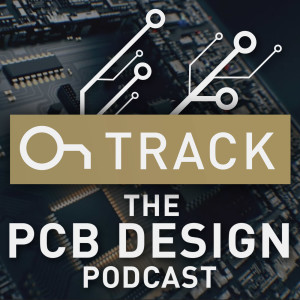
Tuesday Jul 31, 2018
Ted Pawela, Altium COO, Shares Vision for the Future
Tuesday Jul 31, 2018
Tuesday Jul 31, 2018
Ted Pawela, Altium COO, joins Judy Warner to discuss how Altium intends to fundamentally transform the electronics design industry, what Altium’s vision for the future looks like, and what to expect in Altium Designer 19. They also touch on Altium’s upcoming international design conference, AltiumLive: Annual PCB Design Summit, and why everyone in the community is encouraged to attend. Learn about Altium’s vision to bring PCB design and manufacturing closer together — a world where design turnbacks and respins can be avoided by bringing DFM constraints into the design tool itself. Listen to this special episode of the OnTrack podcast to learn more and remember to share your comments and ideas below.
Show Highlights:
- Ted started out in ocean engineering - multidisciplinary in nature, not just physics or mechanical.
- Altium’s commitment and advocacy of engineers/industry - Altium stands for the Engineer
- The Altium origin story - anyone who needs a tool should have it, so let’s give them tools no matter what age or budget i.e. free product including Octopart and Upverter
- Upverter is for the makers and inventors of tomorrow.
- It’s our mission to transform the electronics industry.
- The whole product realization process is discontinuous. We want to change that.
- AltiumLive announcement and AD19 announcement
- Goal is to deliver incremental pcb design capabilities that would take us to places we haven’t been before - like High Speed Design - it’s not something we can deliver in one release. AD18 was the foundation.
- Design and manufacturing worlds can come closer together.
- The power of CAD can be problematic - it can be overwhelming, needs to be feedback from the tool to help find problems.
- New company acquired - PCB:ng (NG=next generation) is board assembly manufacturing, low volume, high mix. Good for prototypes. Their mission is to create a manufacturing line where designers can know everything about it so design constraints can be removed from the start.
- Ciiva - another company trying to solve the same problem. They created a bill of material that allows you to know the lifecycle state of what you are selecting.
- We all want manufacturing insights at design time, Altium is bringing the pieces together to transform the industry.
- AltiumLive - Designers, manufacturers, fab, assembly, all came together to discuss industry problems. It’s about inspiring the community to think about current industry challenges and discuss possible solutions.
- How many Industry Conferences are out there? PCB West, DesignCon (chip and board level), PCB Carolinas, Electronica, Embedded World - but are there any that put the PCB designer front and center?
- Altium wants to provide this for the PCB designer; see AltiumLive 2017 Retrospective to see the presentations from last year. You don’t have to be an Altium Designer user to come to AltiumLive.
- Altiumlive 2018 this year will have one day, before AltiumLive officially begins, of extra learning sessions you can add on, the two options (which will run concurrently) include: University Day, focused on learning Altium Designer or High Speed Design with Lee Ritchey.
Links and Resources:
Hi everyone, this is Judy Warner with Altium's OnTrack Podcast, thanks for joining us again.
Today I have a rare treat for you, but before we get started I'd like to invite you to please subscribe to our podcast on your favorite podcast app or favorite us on an RSS feed, and remember we also record this on video simultaneously, so if you want to see our sunshiny faces you can go over to YouTube on Altium's channel and go under videos, and you'll see all the podcasts recorded in video.
I'd also like to invite you to connect with me on LinkedIn, I share lots of information to engineers and PCB designers and I'd love to connect with you there as well and on Twitter, I'm @AltiumJudy. So today, I have the rare treat of inviting in one of our esteemed executives; I esteem you Ted. So Ted Pawela is with us today, he is the COO here at Altium and we're going to talk a lot about the direction of Altium and really kind of get a peek behind the curtain. So I'm excited to share him with you, so Ted, welcome.
Thanks Judy, I appreciate you having me on here and I'm actually really excited about the the podcast series that you're doing, and see a lot of the feedback from people and it's a little bit humbling to be here given the actual magnitude of the guests that you've had here from industry and so forth, so I'm not sure I can live up to that but I'll do my very best.
Well, I think you rank but we're glad to have you. So before we get started, I thought it'd be fun for the audience to know a little bit about your engineering background. So you haven't always dwelled in the halls of the executive world; you kind of came up through engineering, so tell us a little bit about your background there?
That's true it's probably not a very prototypical upbringing into the industry and so forth, but I actually started my... I guess you could say my engineering career, back in the education space. My undergraduate degree was actually in Ocean Engineering, and the interesting thing, I think about Ocean Engineering and Altium, is that Ocean Engineering is one of those disciplines, or one of those engineering fields that is multidisciplinary in nature, so it doesn't focus only on mechanical or only on physics, or any given thing, but it's actually very multidisciplinary. In fact, like when I think back on it, I did a thesis project that was to create an underwater acoustic transponder system - which sounds pretty fancy, but it was basically a device where you could send acoustic signals underwater to tell this device to do something. In this case, it was to release a buoy from the bottom, that had a rope tied to it. It might be attached to an anchor or something else you might want to recover, and that system, we had to actually design the electronics as well as the mechanical system. It all had to work underwater so I think back on that a lot because, following that, I spent a lot of time more in kind of mechanical domains, and so this in some ways as a homecoming for me.
Right.
To come back to being at Altium and be involved in electronics, so that was kind of the beginning. I worked in the underwater defense industry for 10 or 11 years as a real engineer doing actual design work and at that time I wasn't really focused on electronics, but more in the worlds of underwater acoustics and mechanical systems and how those converged. So they're kind of different kinds of physics, different equations that you have to solve, and so I spent a lot of time trying to make those two things mathematically work together. And then from there I actually ended up, because I was working with software, and in this case it was Ansys software and, actually Abacus software at the time you know, that has now become Somalia over at TISOL, but I was working with those two softwares which are simulation softwares in the mechanical world and I was presenting at conferences and things like that. And I had the opportunity actually, to join Ansys and I did, and that kinda took me from that world of, real hardcore engineering into the software side of the business and and I loved that and I've now been at a number of software companies, all engineering software companies, and it's become something that I have a passion for, and that I really enjoy and love and feel really fortunate to have found my way to Altium.
Well we're glad to have you, you've definitely been a change agent here for good and what I really love about Altium and I think that you appreciate it like I do, is if you walk through these halls very long here at the La Jolla office there really are a lot of people that have kind of that cross-disciplinary feel or... but we really do advocate and care about the engineer and that sounds kind of corny.
Yeah...
But I think because there are lots of people, even like myself that were in fabrication or where I was selling and sort of in the weeds, It makes me feel excited to come to work in the morning and to be able to advocate and to help enable, sort of the next generation of technology, and be part of that so...
Yeah, I'm excited about that as well and I think, fundamentally it comes down to this sort of basic notion that's independent of any industry, is that if you do the right thing for your customers and you really think about them, that they do good things by you as well and so I think we get that here.
Yeah.
From the top of the organization through to, and across all places in the organization and definitely that is kind of a cultural element here that I both appreciate and I'm kind of committed to perpetuating and extending as much as we can.
Well a fun note here, is that Ted actually hired me into the organization.
That's true...
-and I actually reported direct to him when I first joined and I - I think we really resonated on that note, and that really, Ted's really been the empowering force behind everything that I do here personally at Altium. So I really appreciate this Podcast, the Newsletter, AltiumLive, so we've had a blast doing some of that stuff and doing things really with with the designer and engineer mind. So that's been fun - well to your point, I think that's a good jumping-off point what we wanted to talk about today is Altium's identity, you know.
What from your perspective, what is it that Altium stands for?
So, I think, you said it, maybe in different words at the beginning of this and I think Altium stands for the engineer, for the designer, for the people who actually have to do the work. And I think that it's one of the things that makes us different from other software companies so we're not really thinking about things like, typical things that I've seen in other companies, like how do we sell higher into organizations? How do we get executives to buy in so that we can do kind of top-down? How we can get top-down decisions to standardize on our software and things like that. The thing about - that I really noted about Altium - and the culture of doing business and working with people here, is that it's really focused on that. The guy who's got to do the work.
And and I think largely, I believe that's the thing that we, that we really stand for and you'll probably remember that... you know, I tell the story to a lot of people and pretty frequently, about when I came here you know, trying to uncover what I felt was, or what was the fundamental kind of characteristics of Altium's brand and it's identity and, and it kind of rooted in a discussion I had with one of our board members David Warren, who has since retired, but but David was one of the first couple of guys into the company and when they started the company it wasn't, it wasn't a company yet, it was actually a couple of guys who are trying to build electronics at the time, and this goes back 30 years or so.
You know CAD software, E-CAD software in particular, it existed but it was really expensive. It only ran on expensive high-end computers and I think, nobody in the room, yourself included may remember those days but I remember those days when we had to buy Apollo workstations and big expensive machines.
Yes.
You know that $50,000 in back - this was back in the 80s...
Yeah.
-that was your barrier to entry so it was a lot of money and a lot of people who were involved in design didn't have access to that, they didn't have those budgets.
Right.
And so, and these two guys were among those. And they actually set out to say, how could we - how could we have software like that for ourselves? Well they decided to create it, and they wanted to create it in a way that it would be accessible not just for themselves but for anybody who needed it so they built it to run on on PCs and that was the genesis of Altium.
Right
There were people out there who were doing and trying to do amazing things in the world of technology and engineering who didn't have access to all the tools and they wanted to provide that access for themselves, and for others, and you know for me, and for the company, I mean that's really a core part of what we stand for. Be for the engineer but make that technology accessible and make it accessible to people who need it, even when they don't have big budgets to work with, sometimes they don't have any budgets to work with. So that, to me, that's really what Altium stands for.
Yeah I think we have the best sort of origin story ever, especially because Dave Warren, at the time was - I believe he was teaching at University - he said to me once that there was all these young passionate people that have these great ideas and no access and so there was he was kind of incensed by that and that sort of, filtered and still sort of lives in this company, this feeling of anyone - anyone who needs a tool should have it. Because you can have a great idea at any age, at any phase so let's give them tools. And I really love that, that it's lasted long past the time that Dave Warren and these two guys sort of kicked this company off, it's really persisted and I really I really like that.
Yeah, I think it's not just persisted because it's in the spirit of the employees who work here and everything, but I can tell you that we make our decisions on that basis. I mean the basis of, kind of being true to what we represent, and so we think about that. We think about who are the underdogs, and how do we empower them? And not, kind of like leave them behind, in pursuit of purely making money in business - and we are a business - we're a commercial business, and of course we want to make money; our shareholders expect us to make money and, on the other hand we think that there's many ways to do that. And you know, everyone may know, we have multiple products and kind of like multiple price points - that's one way. But we also try to think out of the box a little bit and so as an example; we have, I guess one of our brands called Octopart, where people can go and search for parts and so forth, and you can do that as an engineer and you don't pay to use that - it's actually kind of a seller pays model right?
Right.
So when somebody buys parts after they've searched throughout the parts and we may get a small fraction of that revenue, or people advertise on that site and we get a little bit of revenue from that, but we don't have to charge it to the user and we think about - that's an example - but we are always thinking about how do we take a product like Upverter for example, that actually was, before we acquired it, they charged a subscription fee. We made it free, with the intent that we would find ways to kind of indirectly monetize that in a in a seller pays kind of model.
Right.
Because we want to make that technology accessible to the maker community, to the kind of inventors and creators of tomorrow who who don't have money today. So you know, it's like I said, it's a core part of the decision-making process here; is how do we stay true to that vision of making technology accessible to everyone?
Yeah, it's just so refreshing to hear from an executive a software company I think - you know - it's not something I think you hear a lot, like money does lead in many cases, but it's clear to me that there's a guiding principle behind that. That,of course you have to be disciplined and answer to stockholders and do all those things, but you can do that in fresh and new ways and...
That's the key, because I think again, we want it, we need to be a sustainable business or else the technology that we provide won't be here.
Right.
In ten years or something and of course we don't want that to happen…
Right but there are, interesting and different ways you can do it requires that you maybe, are willing to think outside of the conventional wisdom or the best practices and so forth and… that's one of the things that I like about Altium, is that we really do try to break those... mmm... norms and...
Yeah.
-and you know, think about how we can do it differently and just don't accept status quo. Don't accept best practice just because that's the way it's always been done.
Well to me, it's innovation and...
Yeah.
-and we try to build innovation into our software all the time, so we're building innovation into our model too which I really love. So what would you say, do we... would you say we have a defined mission? I mean, beyond what you kind of spelled out, so like an actual defined mission?
Oh absolutely, so I think everyone at Altium, we've refined this thinking in the way that we articulate it internally, but if you were to look at the things that we present externally, like when we do go to shareholder meetings, and in particular, we do a technology day to our Investor Community and we've done it the last several years in Australia. And that you can see the presentations on the web and so forth, but that's a real clue for anybody who really wants to know where Altium is going. If you'd look at those things directionally that gives you a lot of guidance and the thing that we say over and over and over again is that it's our mission to transform the electronics industry.
And specifically, what I mean by that, is that creating electronics is more than just about the design process and the design tools and and so there's what I would - kind of call it a value chain - that's involved right, you have people who think about the product and what's the intent of the product and that kind of breaks down into requirements for mechanical systems, for electronic systems, and all of that.
But even then, the job's not over, because there have to be components that are supplied to that or that are selected from that and then found and acquired. There has to be a board that gets manufactured; the bare board. There has to be the assembly and fabrication of the full, system level board and everything and sometimes it's multiple boards, and then it's all got to be put together and so the job’s not really done until everybody does that and the thing that is sort of striking about the electronics industry, is that that's a really discontinuous process, we kind of like, all think within our sort of domains with our blinders on and we believe that it's our... it's gonna sound a little silly - but it's our self-directed destiny to kind of change that. That's what we want to do, so the mission of the company is to really change, to transform the way that electronics are conceived, designed, manufactured and delivered to the world, and we think there's lots of opportunities to do that a lot better.
Well I know personally, a lot of people have asked me about, why are you buying these... you know, how does... why? I remember Happy Holden last year saying; Upverter? And so it's because they think of us primarily as just a CAD provider right?
Right.
And so I think not a lot of people understand that we have our sights set much higher than that - along those lines - I'd like to dig into that a little bit more. But before we do that, we are sort of - AltiumLive will be here in San Diego in October, and we will be, at least doing a marketing release then, of showing what will be in Altium Designer 19.
We will.
And you mentioned to me that I had kind of thought - even just working here - you're down the hall from me but my impression was that Altium Designer 19 was going to be sort of an iterative release and that Altium Designer 18 was massive. We changed the platform, we really revolutionized the tool in so many ways so I thought: well we're going to catch our breath, add a few little bells and whistles and be on our way down the road, but you're telling me no, it's going to be big. So, can you without giving away the secret sauce, tell us a little bit about sort of the intent?
Yeah well, so I mean there's things that are still forming, it's kind of like the cake is still in the oven baking right now, so not necessarily ready to share a lot of detail but here's what I will tell you about that.
First of all you're right, Altium Designer 19, it's not just another release, just like 18 wasn't just another release and, in fact, if I shorten it just for the sake of simplicity, AD, AD18, AD19 and, AD20 are really a set of releases that are linked together in a fundamental way, and so what we wanted to do with that series of releases was in part - it kind of gets to this thing that I was talking about, this idea of transforming the electronics industry and specifically what we wanted to do with AD18, 19 and 20 - was to deliver incremental PCB design capabilities that would take us to places we hadn't been before so, and specifically into high speed design. Historically... you know...
Yay! my favorite subject
I know you have lots of time invested into that segments of the industry and know lots of people there and and we think that's important that we can do better to support that and AD18, 19, and 20, that was one of the core kind of objectives there, was to help Altium to kind of grow up in terms of high speed design capabilities. But it wasn't something that... I mean it's kind of massive, and it's, in terms of being able to do it, so it wasn't something we were able to deliver in a single release...
Right.
-in fact when I think about high speed design, specifically AD18, was kind of like delivering foundational capabilities that are required to do the kind of complex and large designs that typically we see in high speed.
Right.
So you didn't see particular high speed capabilities there, not big ones yet, anyways in AD18, but what you did see was that we moved from our old 32-bit platform to 64-bit.
Right.
We went from single threaded activity to multi-threaded within the application, and things like that; that are kind of the plumbing...
Yeah, it's like the foundation...
That's right, they need to be there for us to be able to exercise those high-speed capabilities that we wanted to build in. With AD19 you'll start to see more of the capabilities now coming out. It won't be complete but there will certainly be designs in the realm of high speed that people will start to be able to do and it'll become visible that we're really going somewhere with that and then AD20, will be the one where we move a lot towards a more completed set of capabilities for high speed.
So that's one sort of key thing that I would say is that - certainly at AltiumLive, and as we come out with AD19 - you will see real capabilities that start to bring us into that world. The other thing though, is making real this idea of beginning to bring about industry transformation, and specifically, even at AltiumLive last year, one of the things we heard over and over again in the talks was people who were in board fabrication and assembly and manufacturing and who think about DFM and things like that, who were saying over and over and over again: you guys out there in the design community don't think about us. I know the manufacturing world, not nearly enough and often enough, and conversely we heard from people on the design side saying kind of similar things back to manufacturing so those two worlds have been historically siloed, as you said.
It comes up, I cannot tell you how often this comes up in this podcast series it's just a persistent problem, everybody knows it's there.
Yeah it is a huge problem and I think in one of the things that I'm really excited about with AD19 is that you're going to see some you're gonna see some things that are fairly dramatic in terms of helping to bring those two worlds together to where people who are doing design will be in contact with people who are involved in manufacturing while they're designing. And you know, the ultimate endgame for that, is that you would imagine a world where when you are doing design, you don't only have design constraints to think about but the manufacturing constraints are things that guide what you can and can't do and how you create that so that you avoid those kind of like downstream... not exactly mistakes,but those downstream things that you didn't think about that cause design turn backs and spends that are really not needed.
Right, they're not needed and cost so much money and time.
Yes so, AD19 is going to be, I think it's gonna be really impactful and kind of transformative in the way that design and designers, and people in the manufacturing side of the business will be able to work together. So I don't want to spill too much of that, but it's gonna be, I honestly think this is in many ways, a bigger, more transformative thing than AD18 was which was pretty huge, for us at least, in seeing our tool transform.
When you said that to me I'm like: wait what? I was shocked when you said that to me about a week ago I was like, wait I work here and I don't know, and I talked to developers regularly and I think because I get just little glimpses of pieces I'm not seeing the overarching where I think you, from where you sit, you're getting the overarching perspective.
Maybe so, but like I said, I think the key thing here is it will really be something that changes the way we think about CAD and what we should expect from our CAD tools.
Which is great; I've said for many years, that the power of CAD has actually been problematic, because, if you are not 30-40 years into this industry you can get so much power in that tool. It's like, I was saying to someone, I go: there needs to be a feedback from the tool that says, no stop dummy, you know. Like there is no place that says, no stop, this is a bad idea...
Right.
-those cores don't match. Those holes are too small those vias are... you know. There's, of course we can put in parameters and things that help them design well, but there's... so to hear that coming together would just be life-changing, so that's very exciting.
Yeah, and like I said, it's not something that I think we won't realize - that full vision of AD19.
Right.
It'll be that again, this combination of 18, 19, and 20 - you'll be able to see now with AD19, how those things kind of link together and we'll be telling people, we'll disclose our road map for AD20, so people can see how that whole thing plays out but there's gonna be a lot there and it will be enough to change the way that designers and manufacturers are working together. It will change more; well it'll be changing them in even more dramatic ways as we are able to deliver everything through those three releases.
Right.
But there's gonna be enough there that I think, it's really exciting to think about, and talk about and you know...I guess, the other thing for me, or maybe not the other thing - but on a related note - I remember last year at AltiumLive how all those conversations seemed to be centered around standards. And so, couldn't we come out with a single standard for how data is represented and so forth and...
(that's a hot topic)
Standardization, I just have to say, I mean standardization is such a hard thing to do to get everybody within an industry to do that and I think the reality is that standardization isn't the answer. The standardization is a solution that people kind of assume is the right way to solve the problem, so they... and so we tend to kind of like think about how. First you know, how could we solve this problem? If the problem is that people just don't work together and when I design I don't end up with something that's manufacturable until I go through many spins, as an example that's the problem right and then, the solution is just to make it work right. I mean as a designer, or as for somebody in manufacturing, do I really care about standardization? No, I don't, but what I wanted to have happen is that it just works.
Right.
-and I don't have to think about it, I don't have to do anything extra, nor does the person on the other side of the wall that we're throwing things back and forth over. We just want it to work.
Right.
-and that's the approach that we're taking and and again you'll see the it gets to what you were saying why do we acquire these companies for example?
Right.
So we did, just recently, a small acquisition of a company called PCB:NG; NG is for Next Generation and that's a company that does board assembly manufacturing and they do it on small scale, so it's the idea that they do low-volume, high-variety kind of, high-mix kind of designs. So when people want to build prototypes and so forth and their whole mission has been to really change, to be able to create a manufacturing line where the designers can know everything about it so they kind of design in those constraints from the start. Which is very aligned with the idea that I was talking about, and where Altium has been thinking, and now if you rewind back a couple of years ago we acquired a company called Ciiva and Ciiva was really focused on a couple of things. One was to have a Bill of Material that was smarter, and smarter in the sense that you understood straight away what was the life cycle state of the components that you select.
Right.
And the parts that you select - are those things even available anymore? So you don't select and design in things that you couldn't even buy if you wanted to.
Right.
And then there's the notion… that it happens frequently by the way - it does happen frequently.
And it's such a headache.
And in Ciiva you know, the other thing that they were really focused on was to understand those manufacturing constraints as well and so there's kind of this nice convergence of thinking where the Ciiva guys were trying to solve that problem, PCB:NG guys were trying to solve that problem, and Altium is trying to solve that problem, and so bringing them all together now gives us a way that we can say, how do we make it just work and so having that small manufacturing company gives us a way that we can prove this out. We can make it happen having sort of, like full access to everything in that facility and on their line and as well having the people on the side of thinking about the supply chain in the Bill of Material and the design side. We can do all of those things and so we don't intend to kind of like make PCB:NG into some big volume manufacturer. It's never gonna be Foxcon, what we want it to be but we want to make it just work and once we prove it there, then we can take it to all manufacturers.
Right.
And that's the idea and and so we'll again, start to give you a glimpse of that, and more than a glimpse, we'll give actual real capabilities in AD19 that will allow people to begin to solve that problem or, not even salvage, just make it work.
Right just make it work.
So AD19 in my mind is, is a huge step forward.
Well I'm very excited so I'm gonna put a pin in our conversation real quick and just let our listeners know that, all of... you know, sometimes people just think of us being the creators of Altium Designer and don't realise we sort of have been acquiring these companies so we will have an area at AltiumLive in San Diego and in Munich if you're able to join us, where all of those brands will be joining us. I'm hoping to put them in an area that I'm calling Altium Alley, so we'll have Upverter, Ciiva, the PCB:NG, and so, we can start to see how this all fits together.
Yeah.
So I'm excited about that. So let's talk a little bit about AltiumLive, since we are rolling out AD19 at that time, at least to give a sneak peak of it. You and I worked very closely together and sort of had a shared passion for the idea - it was AltiumLive, our first ever users' conference was really Ted's brainchild and then, I was brought on board and then we worked closely together and then it took a village - it took an Altium village - to put on that users conference so can we talk a little bit about why AltiumLive, why do we decide, as a company to begin doing a users' conference, and sort of what, is our intention behind that? Because we want to sell more software?
[Laughter]
Well of course we want we always want to sell more software.
Of course we do, there's no doubt about that... I'm obviously being very facetious.
-yeah but if I come back to the beginning of our conversation, you know I mentioned this notion that if you do the right thing for your customers that they support you and and good things happen as a result of that and and I think, AltiumLive is really built on that idea. So we wanted to create a forum in which our users, but more than that, people in the industry could come together to kind of talk about and collaborate on how do we solve the challenges that we face as an industry. So the fact that we had manufacturers there and manufacturer's reps and everything else as well as... you know, so these are people that don't know Altium Designer. If they saw it they wouldn't know whether it was Altium Designer or another tool per se...
Right.
-possibly but they're involved in the industry and they're relevant right, to the way that we do design and so forth. As well as all the design people. So we wanted a place where our users could come and they could learn and they could get better at their craft and they could connect with one another so - I think Judy you came up with the idea - that it was about, connect, learn and inspire...
Right.
-and that's really the idea right, I mean in terms of connect; it's always good to be able to meet your peers, to talk with your peers, who you face common challenges with, and talk about how do you overcome those, how do you approach them, how does your company support you in those things. Those are always really valuable conversations and so that's - I think - what the connect part is all about. Learning is pretty obvious, people always want to learn how do I get better and that's both in terms of using tools but more than that, it's about becoming better as an engineer. So a lot of the curriculum, if you will, that was associated with that, and in the sessions that we had they weren't about how do I use Altium Designer, they were how do I solve these challenges from an engineering perspective...
Right what are better routing practices...
-Right, speakers about specific tools, because it's like, how do I do these things? So the learning part of it was really important. And inspire, obviously if we're going to transform the industry, we want to bring together the people, the stakeholders in the industry, who are likewise, facing these bigger challenges, not just how do I design better, but how do I design in a way that I know it can be manufactured and that manufacturers don't have to go back and completely recast the Bill of Materials and force me to change the design. And how do I ensure that these parts are actually available and all of that - but it's really again about inspiring the community to think about how we solve these problems of the industry. The fact that it's sort of discontinuous in terms of that flow and so forth and we've got a lot of ideas at Altium about how we solve that, but we definitely don't have all the answers and and nor would we want to try to solve those in absence of all the thought leaders and practitioners in the industry right.
So I think that's the third part of it, is really to bring together those leading practitioners and thought leaders from the industry to say, how do we take this, how do we take our whole industry forward in a way that I... don't want this to sound a little too trivial but, we talk about IoT how do we deliver 50 billion devices by 2025 or whatever.
Right,
-whatever those numbers are, but I think that there's lots of places where electronics are important even in absence of IoT, but the smarter we make our world, the better that's going to be, the more ability we have to solve some of the big picture problems in the world using electronics and engineering and so forth and that's only going to happen when we all come together to figure out how do we do all this better and more effectively.
I loved the convergence at our event it was like magical to see - and such spirited conversations - between fabricators and even our keynotes right. I remember one of the keynotes in Munich saying something about fabrication and then our friend Julie Ellis is like, wait a minute, and then having this really honest challenging almost debate right, but it was so beneficial. I think everybody was really, I think empowered, by having really those frank conversations and really learning from each other. You know a thing that I really like Ted, is that if you look across North America at least, well I would even say Europe, how many events are there for designers? I mean for printed circuit board designers or engineers already, what events are out there? We have PCB West which has some good tracks, Design Con is chip and board level, PCB Carolinas I can think, Electronica, Embedded World... so there's just a handful, but is there any that just focuses and kind of exclusively puts the designer front and center?
No, they're kind of lost - they don't really have a place and what I love about AltiumLive, is that gets to be sort of the center of the conversation but shoulder to shoulder with all the other stakeholders right, so it's like they get their own party where they can just dig in and get such deep learning not only from really incredible thought leaders like our keynotes but also from each other.
Right, we saw that happening a lot right then, and now you can see it just if you go even on the website for AltiumLive and you look at last year's recorded sessions and so forth you see that pretty clearly. It was pretty striking, and my hope is that over time people will actually start to see this event as something that's not an Altium event it's their event.
Right.
And that's the spirit behind it frankly, is that the same as with products, and solving these problems that everything we can't there's no way that Altium can do it on its own or any one company could on its own. We have to do it as a community so I really see AltiumLive as a community and I hope it grows and I hope that the control of the agenda and the content and all of that kind of stuff stays with the users, the designers and the people in the industry who are actually doing the work. That's my vision for it, that it's not us and it's not about our software...
Right
-it's really just about us using the fact that we have lots of customers and users and so forth as a way of using our position to help bring them together.
Right, absolutely, and I've shared with people that you don't need to be an Altium user to come to this event.
No that's true...
-and it's like no one really believes that but it really is true. You could come using another mainstream tool and you would have to endure us rolling out the new release of Altium Designer for 45 minutes...
Right.
-other than that, you will just be getting good learning, meeting with other designers so...
Yeah if I go by memory right, we had something in the order of, I don't know, a dozen main stage presentations or so, and of those, two of them were by Altium people.
Right.
And the rest were not. We had probably, I think two dozen, actual learning sessions that were, kind of focused on training and developing skills and so forth and of those, I think maybe four or so were really focused on Altium Designer. And sure, we could show what we typically did was show, how after you spent the bulk of the time learning, how you attack a problem, you'd show how that could be done in Altium Designer, but it wasn't about solving it with Altium Designer, it was about solving it so, and I'm frankly, I'm kind of like proud of that and proud we didn't make it a place where you just come and hear about Altium and we market to you, and sell to you and so forth it's not about that.
Well you really are the champion of that and I am your proud sidekick in that regards because honestly I didn't know any company would let somebody like me, do this, but it's being driven from the top so I love that, that you're kind of holding on to that. This is about community...
Right.
-dang it - so for those of you who are listening, please know that you are welcome to join us at AltiumLive 2018 in San Diego, October 3rd through 5th, and the website is up, registration's open, and because the attendees asked us to last year, we've added a full university's day, where there's more tool training because people actually complained a little bit that we didn't train them enough on our tool. So kudos to us, but we again, didn't want to mingle that into our main program, so we set aside 100 - 160 spots on the front end where we will teach you in the tool, and keep the rest of it rather tool agnostic and then also in parallel our friendly Ritchie has agreed to teach a full day on high speed design which will be a real treat. And all of this, the price is silly-low, and it's in beautiful San Diego so there's just no downside to it as far as I can see so we're all looking forward to seeing you there.
Absolutely.
I wrote a note here Ted, and I'm just gonna ask you about it and we may have already covered it but you had mentioned something to me about AltiumX was that about the transformation part, our x-factor?
Well that's a little bit of a, little bit of an internal code name, right now for the the projects surrounding this connection between Altium Designer 19 and manufacturing...
Okay.
So we've kind of covered it and you won't see a product called AltiumX, but yeah, you know as often happens when products and projects kind of come to life, they don't have a brand associated with them and we look for clever little ways to talk about them internally before we know that people can kind of rally around and know what we're talking about and AltiumX was that, well for this project at least for a while. And we've talked about different ways to brand it and talk about it and so forth but it's really the key thing; is it's a part of Altium Designer, this isn't gonna be a separate product and actually I will say that that's one of the things that's interesting and and I think valuable about Altium Designer, is that it's always been this idea of that it's not kind of like module, by module, by module, but it's one thing that gives you the capabilities that you need and where there are exceptions, it's because we have partners involved and they need to know how much of their product is going on, and so forth but largely if it's Altium, if it's things that we develop internally, we make it a part of that product.
So it's really simple to know what it is you want, you want that one thing Altium Designer, it's really simple to buy it there's one price and it's hopefully really simple to to work with us, and do business with us and in that notion, we call it easy-to but that's when you get to the spirit of Altium, and and our identity and everything, I think that's another piece of it that I didn't talk about before, but it's another part of what we think is really important, is that we just make it easy for people to know what they're dealing with, who they're dealing with and how they work with us and so forth. Even how they use the product, try to work hard to make everything easy to do.
Right, and I think we're living up to that - we're not perfect, we've got lots of growing to do...
That's true.
Always but when I, because I have the privilege of sponsoring teams and different things as part of my job. Often people will come to me and go, oh my gosh! This was so easy to install it only took me... I was up and running in an hour instead of half a day or whatever, so I I sort of hear that feedback so it makes me proud to be part of this team.
So Ted, thanks so much, I know you're such a busy guy and you're spinning a few dozen plates at all times so, thanks for taking the time to sit down with us and share with the people who are listening to podcast.
Well, thanks for giving me the chance to do that and I hope that I was able to give enough insight and something interesting and exciting for people to think about. Love to have people come to AltiumLive and hear more about what we're doing and also hear from their peers in the community but, like I said we're really excited about kind of the journey that we're on. This whole transformation of electronics and we are now starting to feel like we can, we're starting to see light at the end of that tunnel and we've got a long ways to go but there's enough light there that I think with AD19 and AltiumLive that's gonna really start to be exposed in ways that will stop people in their tracks, and so I'm excited about that.
I'm so excited about that and I don’t even know about some of the stuff you guys do, so we'll all learn at AltiumLive so, I hope you will join us. Thank you so much for listening to our podcast. I do encourage you to register for AltiumLive, coming up in October in San Diego we should be in Munich, I believe the mid-January. We're just locking that down now, so bear with us while we get that locked down. And remember, whether you use our tools or not, you're more than welcome and we would love to have you just join us and rub shoulders and be part of the community. So thank you, again Ted, for joining us today. And thank you for listening, or watching, and we look forward to being with you next time, until then always stay on track.
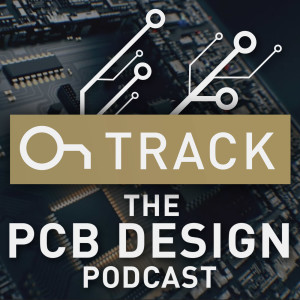
Tuesday Jul 24, 2018
PC Board Stack-up Best Practices with Rick Hartley
Tuesday Jul 24, 2018
Tuesday Jul 24, 2018
What do you do if you have an interference problem? Rick Hartley is an industry leader in the correct design of circuits and PC boards to prevent and solve noise, signal integrity and EMI problems. He consults and teaches internationally and he has taught seminars at numerous conferences, including the IEEE EMC Symposium, PCB West, IPC Apex/Expo and others. He is a past member of the Editorial Review Board of Printed Circuit Design Magazine and has written numerous technical papers and articles on methods to control noise, EMI and signal integrity.
Listen to this episode where Rick shares the worst ideas for a 4-layer and 6-layer stackups. He also offers a sneak peek of what to expect at his AltiumLive 2018 Keynote Presentation: The Extreme Importance of PC Board Stack-up.
Show Highlights:
- Contest - can you guess how many countries the OnTrack podcast has reached? You can win a Summit pass to be Judy’s personal guest at AltiumLive 2018! Just tag #OnTrackPodcast on Twitter with your best guess!
- Mid-80s - in digital domain things started to not work right and no one had answers. There was research to do (120 books later), learned what causes function vs. not function
- In the 90s, began to realize the problem wasn’t clock frequency, the problem is the frequency associated with the rising and falling edges of signals.
- Person who helped me the most - Ralph Morrison
- I didn’t learn what I needed in college, it had to come from experience.
- Energy and Fields and how they move - the energy is in the fields, not in the Voltage and current.
- Field dielectric / routing
- AltiumLive Keynote talk: The Extreme Importance of PC Board Stack-up
- If I’m contacted with an Interference problem, the question I ask is: “What is your printed circuit board stackup?”
- The most critical item is the board stackup, and it’s what people most often get wrong.
- Two or three voltage planes in a stackup with no grounds anywhere - a very serious problem e.g. high layer count board, 20 ground planes in board + signal routed on layer 1 and ground plane on layer 2 - return - 100% of signal on layer 1 would be in ground plane on layer 2. No current from that trace would be in any other ground layers, because energy is in the dielectric between layers 1 and 2
- With 2 or 3 signal layers, and then a plane - all signals try to reference one plane, all fields intermingling in the dielectric space, all coupling energy into one another and that’s one of the places where EMI comes from.
- It’s a matter of keeping fields isolated from one another for proper functioning.
- 4-Layer worst stack-up
- 6-Layer worst stack-up
- What to expect at AltiumLive (Early bird pricing - 10% off through end of July.)
- Setting the record straight: 15 years ago, Rick wrote a paper called ‘Board Stackup to Control EMI’ and “some ideas that I suggested in that paper, I have since learned are not good ideas.” Ignore this paper because the physics have changed. The speeds have become too fast.
Links and Resources:
High Speed PCB Designer’s Guide, Martyn Gaudion
You can also read more articles featuring Rick Hartley in the OnTrack Newsletter here and here.
Hey everyone this is Judy Warner with Altium's OnTrack podcast. Thank you again for joining. We want to thank you so much for continuing to listen and we wanted to share with you that from May to June the listenership has doubled and absolutely exploded because I have amazing guests like I have today. Which is Rick Hartley.
But before we get going with Rick, I wanted to give a few of you a shout out. I wanted to say thank you for the notes and ideas for the show that you sent: To Daud Zoss, I'm sorry if I'm killing your name; Dave Rehack, Spencer Kelly gave us some really good ideas for our future shows. Enoch Sotello and also a nice sharp shout out from a LinkedIn group, the Arkansas Signal Integrity community and I'm sure you guys will enjoy hearing from Rick today.
So I thought I'd throw a fun thing out there since AltiumLive is going to be hosted in San Diego, October 3rd, 4th, and 5th. I thought I'd give you a little trivia question today. So can you guess how many countries the OnTrack Podcast has reached? If you guess close to the number, then I you will be my personal guest at AltiumLive and I'll give you a free ticket there. So how about that? So you can tweet your answers using the hashtag #ontrackpodcast.
So whoever is closest, and we will announce the winner on our next podcast. Thanks again for listening. So today we are talking to, in fact, one of our keynote speakers for AltiumLive, a dear friend and longtime associate, Rick Hartley and I'm sure for many of you, he is no stranger and he is a celebrated speaker. He's been a leader in IPC for many years and a very gifted designer. So Rick, welcome thank you so much for joining me today, it's a joy to have you.
Thank you Judy, it's a pleasure to be here.
So what I thought we'd talk about today Rick, well first let's queue up and tell people who may not know you - the six people on the planet that may not know Rick Hartley - a little bit about your education and your background and sort of how you became a signal integrity guru?
Oh, you want me to tell this?
Yes I do.
I'll try to make it brief.
Okay.
I basically started life in 1965 as a technician with a two-year tech degree and working for a large company in the east, and I spent a couple of years there and decided that wearing one hat a day for six to eight months wasn't what I wanted to do at the age of 20. That I really wanted to be able to wear five hats a day. And so I moved to a small company in Columbus Ohio - I'm still in Columbus - and basically joined an R&D group where I got to do just that. I would be testing boards one day and troubleshooting the next, and so on. Within a couple of years I moved to field service, and from field service I learned a lot about troubleshooting problems and field service as you can well imagine. From field service I moved into the engineering department in that company where I became a designer and as a designer - the designers back then designed everything but the circuit - they designed the circuit boards, the cabinets, the chassis, the wiring harnesses, the interconnects, everything except the actual circuit schematic and I spent a fair amount of time doing that.
And then, over time, with school in the evening I earned a degree in engineering became an EE and worked several years as a circuit designer around 1976, seven-ish time frame, the company - I had moved companies by then. The company I was working for asked me to; they said you have some background with printed circuit design? I said yes, we would like for you to help out doing part-time circuit design, part-time board layout. I said, sure no problem. After six months of that, I decided board design was really the thing I liked most.
And so I moved full-time into circuit board design, away from full-time circuit design. For a long time I was doing basically RF design, RF layout, which is a little more challenging, especially back then. Digital layout then wasn't too challenging. Anyway moved into board layout, spent a number of years there and along the way somewhere, about the mid eighties, things started to not work right in the digital domain, and frankly, most people didn't know why this was happening. They - most of the engineers I worked with, - were scratching their heads; I was certainly scratching mine. And over time, by doing a lot of reading; I purchased over 120 books since then, between the mid 80s and now, and read them all. Some of them, three or four times, and basically learned what causes things to function versus not function, what causes interference and so on, and probably the person that helped me the most to get to the understanding I have today, is Ralph Morrison, and I'm going to talk a little bit about Ralph as I go through this.
But anyway, by just getting my arms around why people have signal integrity problems, why there are interference issues, it's helped me over time to become I guess what people call a guru, I'm not sure I am, but you know whatever, whatever the title is.
A good guru will never say they're a guru Rick so it's okay, I'll call you a guru.
All right.
That's pretty much how I got there it was just a matter of, it was a matter of stumbling along frankly, for years and years - not fully knowing why, and little by little, gathering the knowledge, because sadly, I didn't learn in college, the stuff I really needed to know to take me to where I needed to be. I mean, it had to come through experience, it had to come through just hard-won, hands-on on the job experience. Because it didn't come from college, sadly. And that's kind of where, how I got to where I am today. And of course this all started in the mid-80s. By the mid-90s, I was really beginning to have a pretty good understanding of the issues and it's really all just built since then.
And I think, you and I had a talk and you were actually in our OnTrack newsletter a year or so ago, and I remember you saying around that time is, when you... didn't you talk about... oh I'm gonna forget the term now, because I'm not an engineer - rise times.
Yes oh absolutely.
Was that something, was it around that time that you started realizing that rise times were problematic?
That's exactly, it was actually in the 90s, when I started realizing that the problem wasn't clock frequency, the problem is the frequency associated with the rising and falling edges of signals. If you have a device on a circuit board, that is being clocked at a low frequency - two, three megahertz, but you have a rise time with two, three, four, five hundred picoseconds, you'll have energy in every transmission event that extends upwards to a gigahertz or beyond, even though you're only clocking at a low frequency. So it isn't the clock, the clock really sets the timing for the circuit. That's really why it's called a clock, it sets timing. The rise times are really the key element that drive signal integrity, and even worse; drive EMI issues and interference issues. It's really all about rise time, yes.
That's - I thought that was fascinating when you talked about that earlier. Now I've sat in a few of your classes and I've learned a couple, in my novice kind of way, a couple really key things that really impressed me when I sat in one of your classes at IPC, and in that room of say 50 people, you asked the people in that room: who in this room are EEs and also printed circuit board designers? And a handful of people raised their hand and you asked the question; which one's harder, the circuit design or the board design? And they all like guffawed at that and just said, duh, printed circuit board design.
To which someone like me went, wait - I thought the EE was the heavy lifter, the one that kind of got the creds for doing the hard work but you really taught me then, that - and I think this is a lot - because circuit boards have become so complex over time too but that probably wasn't always true - and I had just missed that, that it had become. So why is it that you asked that question, and what made you choose to go from EE to actual board design?
The, just frankly, the challenges. I found even in the late 70s, I found the challenges of board design to be more stimulating and more invigorating and it made me feel just more alive everyday to go to work than to be designing circuits and setting up test procedures and that sort of thing. And not that there's anything wrong with that, my god, I asked the question of those guys which is more challenging and most of them said board design. If you ask them which took them longer to learn, they would probably say circuit design took them longer, there's more to understand to become a good quality circuit designer, to really get what it takes to design circuits, to function properly. But once you have that knowledge, the actual effort and energy and time expended once you're there - once you're at that knowledge level - is actually greater to lay out a circuit board than it is to do a circuit design and that's why they all answered that way.
There is you're right.
There was a time when circuit board design was ridiculously easy. I have a circuit hanging on my wall, you can't see it from this camera but it's a two layer board that I designed in 1985. It has no planes and it's just routed power and ground and routed signals it's hideously complex because it's over 200 ICs, on a circuit board it's really packed, and that's why it's hanging there because it is such a complex, by the way hand taped, artwork. It's a very complex artwork and that makes people go 'oooh' when they walk in that's why it's there.
But the reality is, how that was laid out was immaterial, because its layout just almost didn't matter, you could do almost anything back then and the circuit would still work. I remember seeing a tape layout in the 1990s, of a guy from the aerospace world where I spent in the early 90s; a board this guy laid out in the 80s, that there was a corner powering ground pin IC for, like a 20 pin part, and there was a decoupling cap sitting above the IC, and he had a trace routed from the decoupling cap, all the way around the body of the IC and back up to the power pin of the device. It was probably an inch and a half long trace from it, and it was a skinny little, 10 mil trace, and the circuit worked. And it's because things were so slow back then compared to today. And it's about rise time not clock frequency. Rise times back then were measured in the tens, in some cases even hundreds, of nanoseconds.
Today they're measured in the hundreds of Picoseconds so they are at least a thousand times faster than then - a hundred to a thousand times faster than they were in the 80s and that's why, things today are harder to make work than they were in those days.
Well that just blows my mind to think of things - I mean, I know that it's happened it's just hard to get your head around those kind of numbers sometimes.The other thing you said, and then we're going to jump into what you're going to talk about at AltiumLive. The other thing I learned from you, which I've told you about this. A few times it just made my head explode was when you started talking about the energy in a circuit board is in the dielectric and it was like; wait what? No it's running like water through pipes on the traces, like that's how I pictured it and you explained it, and you showed a field you had and I all of a sudden, like well, I knew some energy moves through the dielectric, but not the way you explained and literally; it was like I felt embarrassed, and I remember walking up to you and going: okay don't tell anyone but I didn't know that. And you said...
People don't know that.
-then you said, it's okay judy EEs don't know that, and I'm like, okay all right I don't feel so bad. So why don't we know that Rick?
Because it's not talked about generally in college. Voltage and current are important parameters, they are - I just had a discussion very recently with Eric Bogatin on this exact subject. Voltage and current are extremely important parameters for identifying how transmission lines work, why signal integrity issues arise. These are all things that you need to know, but the reality is if - and if you're trying to track down signal integrity issues - probably best to talk about voltage and current more than the fields. But when you're trying to identify why an interference problem has occurred, why did energy move from circuit A to circuit B, how in the world did it get over to circuit B?
Where did that - because the voltage and current followed the traces that we routed in circuit A. So how did the energy...
The reason is that, as you just said, the energy is in the fields, not in the voltage and current and the fields travel through the dielectric space between the copper features. And that's the key element. When you route a trace you're routing half of a transmission line, the other half of the transmission line is the plane, usually in most boards today, a plane where the energy returns. So you have the forward current traveling down the trace that you've routed, and you have the return current traveling in the plane directly under the trace that's routing across the board. And that current is being established because there are fields with energy creating the voltage and current in the transmission line. And that's the key element to understand. If the energy weren't in the voltage IRAM, sorry, weren't in the fields; radio wouldn't work. Think about it, radio broadcasting of fields into free space, that get picked up by antenna that focused the energy into a radio. Anything that uses broadcast medium works in exactly that fashion. And the reason it works, is because the energy is in the fields. Now you can capture those fields with copper structures.
And when you do, then they will channel through the dielectric between the copper features; that's what an antenna does and an antenna focuses the fields into a center point, that focuses them to a transmission line, to the receiver and that's exactly what an antenna is. So bottom line, because the energy is in the fields, and the fields travel through the dielectric space, that's how things can sometimes spread. If we don't route traces properly, if we route, for example, two or three layers of traces above a plane; all of those trace layers are capable of coupling energy into one another, which causes the fields to then spread to places where they shouldn't be. Or, if you change layers improperly - that's something I'm going to talk about, at AltiumLive, is well - the main thing I want to talk about is board stackup.
Yeah so let's just jump in right there I think that's a good place to segue. So Rick is doing, han hour keynote at AltiumLive and the title of his talk is: 'The extreme importance of PC board stack up.' So let's just jump right off there. So you've already started to talk about energy and fields and how they move. Talk about that relative to stack up and why that can be problematic in not so obvious places?
Yeah I will, yes the main question that I ask people; if someone contacts me and says: Rick we've got an interference problem of some kind, be it EMI, be it interference between circuits, whatever. I've had, within the last year of it, people contact me to talk about op-amp circuits that were being interfered with by other things in a circuit board or inside a system. Why does this happen is the question that's often asked. The first question I ask them is, what is your printed circuit board stack up? Because the most critical item to get correct, to have correctly done, is the board stack up.
The most critical item is the board stack up and that's why I ask that question because what people often get wrong is the board stack. I will often see examples of people who have put two or three voltage planes next to each other in a board stack, with no grounds anywhere nearby. And that's one of the things I'm going to talk about at AltiumLive; why that's a problem. It's a very serious problem. For example, if you had a circuit board that was many layers thick, and you had, let's say twenty ground planes in the board. If you had a signal routed on layer 1, and there was a ground plane on layer 2, all 100% of the return current from that signal on layer 1 would be in the ground plane on layer 2, and there will be no current from that trace in any of the other ground layers because the energy is in the dielectric...
Yeah.
Between layers one and two, it establishes a forward current in the trace and a return current - a reverse current, in that. All the other planes, it's like they're not even there. They don't even get used because the energy focuses itself in that tight area, and as I said a minute ago, if you have two or three signal layers and then a plane, now all these signals are all trying to reference that one plane. So all of those fields are intermingling with one another, in that dielectric space and they're all coupling energy into one another, and that's where the interference factor comes from. That's where - it's one of the places where EMI comes from - there are many things that cause EMI, that's just one of the many problems. So it's a matter of keeping fields isolated from one another. That's what we have to do if we expect things to function properly.
Well I think, besides your prolific reading habits being an EE, I think, has obviously served you well and so, to understand how fields move and because, like I said, I have a very fundamental understanding of designs and certainly not of field theory and all of that, and how physics work but I think that's one reason why you've been such a popular speaker and consultant. You talked about - or you're going to talk about - and let's kind of tease it up a little bit; is the worst four layer stack up. What does that mean?
Well there are actually two four layer stack ups that I'm particularly not fond of. One of them is - and I see this a lot in the automotive and appliance industries - where they will put a single ground plane on, let's say layer three, and they'll put routing with routed power, on one, two, and four. And what we talked about a minute ago, having more than one routing layer referencing a single plane,in this case layers one and two; are both trying to reference the plane on layer three. And the result is the field, even if you route them in orthogonal directions, the traces, the fields will still inter-lead one another and we'll couple energy. And the energy that couples, won't be enough to cause a signal integrity problem if you do the stack - if you just do the routing correctly - but it will still be enough that it can cause EMI problems.
What a lot of people don't realize is that it takes as little as eight to ten microamps - microamps, millionths of an amp of common load current coupled into a balanced antenna to cause an FCC Class B, radiated admissions failure.
Wow.
So as it takes that little bit of current to cause an EMI problem, and it doesn't take much coupling of fields to create eight to ten, or even milliamps of noise current. So it's a problem that people need to pay attention to. So that's one of the four layers. The other four layer that's a problem, is the one everybody uses - and that's powering ground on two and three, and the reason that's a problem - if a circuit board is extremely thin - if a circuit board is say 10, 15, 20 mils thick; then those two power and ground planes on 2 & 3 are going to be very close together. And when you do that, when the power and ground planes are extremely tight - a few mils to maybe at most 10 mils away from one another, then you can get away with having power and ground on 2 & 3 or 4 layer. But if it's a 62 Milotic, a 1.6 millimeter thick board, and you have the planes on 2 & 3, they're going to be about a millimeter apart - and when planes are a millimeter apart, there's several things that go wrong.
One, we rely on the planes to help deliver power. The planes basically become the low impedance path for power delivery 2 and IC, if you asked a lot of people, a lot of Engineers, where does power come from in a circuit board? Their answer will be the power plane.
All right.
Of course we know that's not true. The energy comes from the dielectric space between the power plane and the ground plane.
See there it is again...
Exactly. If the dielectric space is tight, the capacitance will be fairly high but most of all the inductance of the planes will be very low, and when the inductance is low, now you have a low impedance delivery path for power. If the planes are far apart, as they are in a conventional 62 ml thick, four layer board, the impedance is so high it doesn't do a good job of delivering power, and you end up with large LD/IDT voltage drops across the power system that we can refer to as power bus switching noise, and that issue alone can cause signal integrity problems but mostly will cause EMI problems.
That's, again, it's like can't, my head's exploding again. Four layer board, 062 - standard thickness of your run-of-the-mill board, I mean this is not fancy, and you're saying this is a bad idea! And I'm like wait, what the earth does not flash? I mean it just that's what it sounds like to me like - it's crazy but it's fascinating and I can't wait to hear - I'm sure you'll dig into this more?
Well I'm gonna get into it more because there are routing implications with that four layer board as well.
Okay.
I mean it's worse than just - than just power delivery. If you have a trace routed on layer one referencing the power plane and you want to change layers to layer four, you're going to have to move the reference to the ground plane, which means the energy in the dielectric space between one and two has to somehow move through that board to the dielectric space between three and four. How is it going to get there? And there are people who will say, oh, it uses the decoupling capacitors. Well that's true, if the frequency is low enough. If rise times look low enough, then that's what will happen. That's why for years, we could get away with four layer boards with power and ground on two and three because rise times were so slow.
Gotcha.
But now all of a sudden, rise times are measured in the hundreds of Picoseconds and that four layer board just doesn't work well. But we're gonna get into that in more detail at AltiumLive.
Okay. You also talked about a six layer?
mm-hmm...
-please don't make my brain explode again Rick, but go ahead, tell me the six layer that's a bad idea?
The six layer board that everyone uses is signal, plane - like power ground, two signals, the other plane. If you put power into that, they'll put ground on five and then a signal and six. And this is a common six layer board that just about everybody on the planet uses and it's even worse than the four layer board with power and ground on two and three. And we're gonna get into intimate detail at AltiumLive about why. It's about, I mean, think about what we said about power delivery with the four layer board. If you have planes a millimeter apart and that's not good enough, what do you think putting them on two and five, of a six layer board where they're even further apart, is gonna do two power delivery?
And now, worse than that, you have the fields between two and five sharing the dielectric space with signals that are on three and four, and all of those fields are saying hello to each other; hey let's get together and party, and they do get together to party and they wreak havoc! And this is a bad board stack, and we're going to talk more about why it's a bad board stack, and then we're gonna get into exactly what to do to fix it. There is a solution. To be able to use that board stack and make it work, and we're gonna talk about how to do that.
Well I can't wait and I intentionally wanted to have you on today to tease that out because, for those of you that don't know already, Rick teaches all over North America, and sometimes out of the country as well. If you haven't seen it, we will share all these links in the show notes. But he's been teaching, he's been on, at least a North American tour, with a series put on by UP Media called 'PCB Today' and those are two days right, Rick?
It's a two day event, and then we go through everything we've discussed here and much, much, much, much more.
Right so two days; so I highly recommend UP Media's PCB2DAY with Rick Hartley. We will share that link for any of you that might want to get a full two days. At AltiumLive we're gonna have you drink from the fire hose and give you an hour of Rick Hartley talking as fast as he can. Rick also speaks at PCB West, which is in Santa Clara in September, I think it's September 12 this year, or that week of September.
It's September 11, 12, and 13 I believe -
It's a three-day event, again loaded with great content there's an exposition day but Rick teaches more than one class there and they're always packed, so.
I'm actually teaching six classes this year.
That's crazy and besides Rick, there's a lot of really other illustrious teachers. It's like good luck with that one; picking your courses because it's a really good show also put on by UP Media so...
I mean that show has Dan Beeker and Susy Webb, there's a host of people; Mike Creeden, I think is going to be there this year, there's just a boatload of people with talent talking about...
Such talent! And by the way, I want to boast just for five seconds, because I have the neatest friends in the whole wide world. And that is that Susy Webb will also be teaching at all AltiumLive, Mike Creeden will be there; I don't know if he's teaching yet, Eric Bogatin, who Rick mentioned, will also be a keynote speaker , and I think that conversation you were talking about having with Eric, was probably on an email feed that I was eavesdropping on.
It was actually just a direct email with Eric because yah, I think you were involved?
I got looped in there and, a significant portion went over my head, but it was just interesting to see you guys kind of bantering about your subject. So again, Eric will be one of the other keynote speakers so I'm very privileged to know some very bright, gifted people, and Altium is bringing all these wonderful folks together. So I hope you will join us and I hope this conversation has encouraged you to join us. And we do have early bird pricing, which is like ten percent off through the end of July. So please be my guest we will - - Rick has shared links with us to other resources. Oh! You wanted to mention something about a paper that's floating out there, that you no longer endorse. So why don't you mention something about that?
Yeah about 15 years ago, I wrote a paper called 'Board Stack Up to Control EMI,' and while the basic content of the paper is more or less correct, some of the board stacks that I I suggested in that paper; I have since learned were not good ideas, and in fact, the four layer and six layer that we just talked about, are two of them, that I recommended in that paper, because I believed at that time, that they were the right thing to do. I've since learned why they aren't, so if you happen to stumble across that paper again; it's called ' 'Board Stack Up to Control EMI,' ... or to help control EMI, something to that effect, and if you stumble across that, just ignore it.
Ignore it cause we're gonna get Rick Hartley 2.0 where things have gotten faster and he's, I don't know that you've gotten smarter; I think just the physics of the boards people are designing have changed.
The physics have changed and that's a key point. That's a very good point Judy, and that's partly why, I mean, it's possible that when I wrote that paper, that four and six layer boards were fine...
Yeah exactly but the speed...
-but they're not today.
And again that's why we always advocate here that you need to always be learning because technology does not stand still and what worked yesterday, is not going to work tomorrow. And so we we try our best to stay on top of it. Rick thank you so much for joining us. I also am going to put in a photo, hopefully it won't embarrass you Rick; of - -
You know, what I want to say about Rick Hartley and people like Susy Webb, Mike Creeden, Eric Bogatin; we are all - you all as designers and engineers are really standing on their shoulders and they used to do this stuff by hand. So I have the neatest photo ever of Rick Hartley with a big fat 70s tie I think, handling out the biggest board ever that I've seen - the biggest tape up I've ever seen.
That's actually the one hanging on my wall...
It is, that's the one? So I'm going to share that and the links too because you guys that just have snazzy racy tools and you started designing ten years ago won't believe the stuff these guys and gals did by hand. So, well Rick we totally and completely look forward to AltiumLive, thanks so much for agreeing to come and invest in the design community, and thanks again for doing this podcast you are a dear friend.
Judy, thank you so much for having me. Yeah and thank you so much for all that you do for the industry Rick, we really appreciate you.
It's a pleasure.
Again this has been Judy Warner with Altium's OnTrack Podcast and Rick Hartley of - how do you say that?
R Hartley Enterprises.
We look forward to seeing, or we look forward to you tuning in next time. Until then, remember to always stay on track.
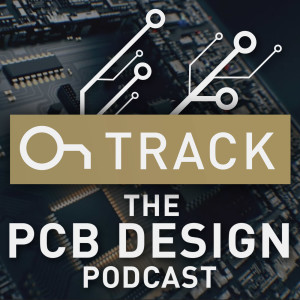
Tuesday Jul 10, 2018
Tuesday Jul 10, 2018
Learn about Embedded Passives Technology with Bruce Mahler from Ohmega Technologies. OhmegaPly® embedded resistor-conductor material is popular, but it’s not new. Ohmega has been making this product since 1972. So why is it getting so much attention lately? It’s reliable and has stood the test of time for five decades--but emerging technologies are making it more relevant than ever. Tune in to learn more about embedded passive and embedded components and find out if it may be the key to solving your current PCB Design challenges.
Show Highlights:
- OhmegaPly® is a true thin-film, Nickel-Phosphorous (NiP) alloy. In the manufacturing process, about 0.05 to 1.00 microns of the alloy is electro-deposited onto the rough, or “tooth side”, of electrodeposited copper foil.
- Embedded passive and embedded components: ER - Embedded resistors, EC - embedded capacitors
- People tend to think of this technology as something new. Ohmega has been making this product since 1972. It’s the oldest, new technology out there.
- Functionality - it can be used in so many different ways.
- Mica - old copper clad laminator, conceived the technology as a way to add functionality to a copper material. Developed in early 70s as a new product.
- First users of the technology - Cannon electronics in Japan saw the potential in the product for cameras.
- Other early user was - Control Data Corporation. From there alot of mainframes utilizing the technology.
- Ohmega ply - thin film resistive foil, plated process, nickel phosphorus, varied thickness and sheet resistivity, fractions of a micron-thick film. Very linear, as film deposit is thinner, resistivity goes up. Thin film technology.
- We make it in Culver City, CA for 40+ years.
- Work with Rogers/Arlon, Taconic, Isola, Nelco and other laminators
- If you use a tiny discreet resistive element, they can be hard to handle. Etching a 5 or 10 mil trace is no problem.
- Space restrictions, solution - print and etch a resistor
- Why would I want to use Ohmega ply? What are the cost, reliability, performance indicators? “There’s no other way I can design this unless I get rid of my resistors!”
- Most designers use Ohmega ply for densification. Helps when: hard time routing, too many passives, board is a little too thick
- Example: MEMs or Micro-Electro Mechanical System microphones for cell phones.
- Applications: military, space based applications - satellites,
- Uses include: Sensors, IOT, Wearables, Automotive, Memory, Heater, Biomedical
- Ohmega wants to talk technology with PCB designers. Leverage their expertise, they operate as a part of your design team and happy to be a resource for you. Technical people are available to help.
- Ohmega and Oak Mitsui - technology partners - Ohmega/FaradFlex is a combined resistor/capacitor core consisting of OhmegaPly RCM laminated to Oak-Mitsui’s FaradFlex capacitive laminate materials.
- Printed circuit board copper lead times are getting longer
- Self-reliant company
- Very close relationships with raw material suppliers
Links and Resources:
Ohmega Technical Library and Tools
Hey everybody it's Judy Warner again with Altium's OnTrack Podcast. Thanks for joining us again. We have yet another amazing guest on a fascinating topic that I hope you will enjoy and learn about today. But before we get started I wanted to invite you to please connect with me on LinkedIn. I like to share a lot of content relative to designers and engineers and I'd be happy to connect with you personally, and on Twitter I'm @AltiumJudy and Altium is on Facebook, Twitter and LinkedIn. We also record this podcast simultaneously on video, so on the Altium YouTube channel you can find us under videos, and then you will see the whole series of podcasts that we record. So that is all the housekeeping we have for the moment.
So let's jump right into our topic today which is, embedded passives and I have a wonderful expert for you today, and an old friend, Bruce Mahler of Ohmega Technologies. Bruce, welcome, thanks so much for joining us and giving us a lesson today on embedded technology.
Thank You Judy, it's great being on board here and I look forward to talking to you and the audience about embedded resistors in particular, as well as other embedded passives.
Okay, so before we get going I want to make sure that I'm calling this technology the right thing because I always think of them being embedded passives but I don't think I'm right. How would you characterize the technology exactly?
Well the OhmegaPly® product, our embedded resistive product, is ER embedded resistors, PCT planar component technologies it goes by many names: embedded resistors, embedded capacitors; I think the most common now is ER embedded resistors EC embedded capacitors in particular. When we're talking about passive elements - and those are the two main ones that are really driving the embedded passive world - and a better component world right now so yeah, OhmegaPly® is just fine with me.
Okay so let's jump in now, you told me something recently that I was kind of shocked to learn about and I'd like you to give us a brief history of Ohmega Technologies and sort of the evolution of this technology. What I was really shocked to learn is the age of the company. So can you tell us more about that?
Sure many people who are looking at using embedded passives, think of it as a new technology, something just on the market. It's been out a year or two - no new applications yet but people are looking at it. So when we're asked, this OhmegaPIy® product , how long have you been making it for? And I said oh since about 1972, and they said wait a second, 1972? I said yeah that's actually , we're going on 46 years now and it's amazing that it's probably the oldest new technology out there.
[laughter]
That's a good way to put it.
I think that has a lot to do with the functionality of the material, how it could be used in so many different ways. And so just briefly a history of the technology: originally the OhmegaPly® embedded resistive thin film material was developed, conceived, and developed by Mica Corporation. Many of your old listeners on board know Mica used to be a copper clad laminator, supplied epoxy glass laminates and polyamide glass, did a number of other things, and it was conceived in the early 70s as a way of adding functionality to a laminate material. So rather than just getting copper foil bonded to a dielectric it was a copper coil that had a functional purpose beyond copper traces bonded to a dielectric and so, after many years of development at Mica, a product OhmegaPly® was developed; the Mica laminate product was MicaPly that's how the name originally came about and it was originally developed in the early 70s as a new product.
Now with any new product, somebody had to be the first to go ahead and try it you know, who was going to be on the bleeding edge of any new technology, who was going to be the route maker? And the interesting thing is that back in the early seventies - about again, '72, '73 - the first users of the technology were two absolutely opposite companies in absolutely opposite areas of the electronic industry. One of those happened to be Canon electronics in Japan. Canon, making AE-1 SLR cameras at the time, looked at the technology as being a great way of making a step potentiometer who could eliminate the ceramic potentiometers circuits that they were currently using, at the time and it fit very neatly into their camera system. So they were very simple, these were surface resistors, put in FR4, make resistive elements in the potentiometers, and they started using it in their AE-1 camera. Very quickly Nikon and Pentax started doing the same thing. The other first user happened to be somebody completely opposite - now we're talking about the early 70s - and that user was Controlled Data Corporation; used to be in business a long time ago. CDC's aerospace group who had some very dense multi-layer boards of mixed dielectric layers of PTFE Teflon, layers of FR4, ECL ecologic, lots and lots of termination needs and absolutely no real estate on some of their high-speed digital boards for termination.
So the idea of being able to print and etch a resistive element, and embed it within a circuit layer, particularly underneath an IC package, speeded up board area for them, allowed them to terminate. They got some other benefits of better electricals. They started using us and then very quickly thereafter, other divisions of CDC started using us in things like their cyber mainframe computer systems, and it kind of dovetailed into people like Cray Research and their supercomputers, and we went from there to super mini computers , places like Digital Equipment and Prime and Wayne, and Data General and Harris. All the guys in the 80s who had ecologic termination needs. So it was the heyday back in the 80s, and a lot of mainframes, supercomputers, super mini computers, kind of like with those very, very powerful systems that people now carry in their cellular phones-
In their pocket right?
-at the time it was very, very powerful though. And so, although two different areas of growth we - in the 70s and 80s - found new applications and digital application, particularly termination, but we also started working very closely with the military aerospace industry where they saw the elimination of solder joints being a very positive thing. You know, high g-force doesn't affect it -vibration - there's no joint there in the resistor circuits. So we started working with a lot of them in the military aerospace, space-based applications, radars, antenna power dividers, high-speed digital systems - just a variety of different things. And it's evolved from there, it seems that every five years new technology comes on that says I need to use that. We can talk more about that - we'll get back to maybe the basics of what do we actually do, how do we make it.
Yeah so let's talk about OhmegaPly®, what is it? What is it like to process, and let's just go in and tell us the whole story.
Oh man, you want to go right back to the beginning again. Okay the OhmegaPly® technology is a thin film resistive foil. Now we became Ohmega Technologies - a spinoff of Mica - started as a separate independent company in 1983, and we basically took over that whole technology from Mica, and what that technology involves, is taking copper foil as a standard EDE electrodeposited copper foil that the printed circuit industry uses, and we threw in a reel-to-reel deposition process as a plated process. We plate a very thin coating of a nickel phosphorous NiP resistive alloy onto the mat or two side of that copper and by varying the thickness of that resistive coating we can vary the sheet resistivity. And so this product - a true thin film nickel phosphorus alloy - we're talking about fractions of a micron thick film, so it's truly thin film. So we have a variety of different sheet resistivities, a 10 ohm per square is about a 1 micron thick film, a 25 ohm per square's a 0.4 micron, 50 ohm is 0.2 micron. So it's very linear, as the film that we deposit gets thinner the sheet resistivity goes up. Now we start getting into the dangerous territory of talking about things like ohms per square and I don't want to start having your listener's eyes cross over some strange area, but suffice it to say, it follows thin film technology.
So what we do is, we make a resistive foil that's a copper foil resistive coating. Now what that foil does, that's what we make at our facilities, in our factory in Culver City California very close to LAX or a few miles away. We've been doing it now , for literally 40 years plus at that facility. That resistive foil then gets laminated or bonded to a variety of dielectrics. We work with people like Rogers Arlon, Taconic, we work with Isola we work with Noko, we do some work with DuPont we're working with others out there, but essentially the resistive foil can be bonded to almost any kind of dielectric just like any other copper foil. Standard pressing, heat pressure, it bonds to a variety of dielectrics. Now that laminate product - a copper clad laminate with the resistive film between the copper and the substrate - goes to the printed circuit board community, the PCB community, then prints and etch copper circuitry. They normally will do a print develop, extra process to create copper circuits.
Now they go through a separate (an additional) print develop bed strip so it's a two-print operation and the first print is defining where they have copper traces, then they etch away all excess copper and they etch away all excess resistive film underneath their copper. Now they have copper circuitry. Underneath all that copper circuitry is a resistive material, but electrically it's shorted out by the copper above it. Well you have a spot for tracers.
Makes sense.
That's a point think of it as a treatment of copper only like a zinc or a brass.
Okay.
Now the board shops come back and they apply more photoresist over that copper circuitry and they print a second piece of artwork and that artwork protects all the areas that they wish to keep as copper, and exposes for etching the copper that will be the resistive element. Now in almost all cases, the first etch will define the width of that copper that will be the width of that resistive element. So the second image artwork defines a length of copper that will be the length of the resistor. So it's a very simple piece of artwork to use; very easy to register, but after protecting the copper with photoresist, now they etch away the exposed copper using the 'aplan' based etchings, and they leave behind the resistive film that was underneath it, and they have a resistive element.
Interesting.
-stripping photoresist off the board; leaves them with copper circuitry with resistive elements that are integral to that copper plane. Those resistors can be tested for value, they can go through standard multi-layer processing, laid up with other cores, pressed and then forget you have the resistive elements embedded, if it goes through traditional drilling, print, develop, etch, strip process, or plate process I should say.
So you do a drilling and you desmear, you plate, you etch and your embedded resistor inside; and as a bare board now, prior to shipping for assembly, the board shop can do traditional testing, and they can measure resistor values to ensure they're within spec. They could also be used on the surface of a board, in which case you solder mask over the resistive elements along with your copper traces, and that protects them from abrasion and scratching. The key here is this though: if you use a discrete resistive element, an 0402, an O201. An O201 is a 10 mil by 20 mil resistor. They're pretty small;
Yeah.
-hard to handle, hard to assemble. So if I go to a board shop now and say: hey guys I want you to etch a copper trace that's 10 mil wide, they're gonna look and they'll laugh and say: come on you're insulting us!-
Yeah.
-we do 5 & 5, 4 & 4, 3 & 3, 2 & 2 technology. So etching a 10 mil trace isn't a big deal, five mil trace is not a biggo. When they etch that copper trace, they're essentially defining the width of the resistor, so it's like a controlled impedance trace. They're creating a resistive element of a certain width. Now you say: can you cover it with photoresist and have a little box window that's 20 ml long? Sure that's not a big deal if you etch the copper away. Now they've left themselves with a 10 mil by 20 mil resistive element, which does not push the art at all, it's already built in, no assembly, and all that. So if you say: hey can they do a 5 mil by 10 mil resistor? Sure, we have applications that are using 50 micron by 100 micron resistor. If a board shop connected that copper trace, that's the limit of the resistor width you can print. So you can get a significantly small, very, very, precise resistors that could be located right where you want them, under a package, and that's where we're doing a lot of newer applications like microfluidic heaters, you're talking about a couple mils, by four or five mils you can get very small heat rises in a very localized area, very low power, but I'm ahead of myself.
Okay yeah well so I'm thinking about our audience right now, who are EEs doing design, or just purist board designers for the most part. Why would I want to use OhmegaPly® over traditional? I mean you just mentioned one, if I had space restrictions and I didn't want to use these tiny, tiny parts that seems like a no-brainer but is it real estate, is it cost? Like what drives people - I think I'm opening a can of worms, sorry but what is the cost, performance, reliability implications? And if I was a designer, why would I want to use OhmegaPly®?
Okay, it's a good question and people use it for a variety of reasons. The best reason we like to hear is: I have a design and there's no other way I can design this thing unless I get rid of my resistor and so, kind of I get a tear, I well up a bit, I get very emotional-
[laughter]
-with those. Because then it's all driven by performance and densification.
Right.
But look at everybody - realistically - cost is a big driver, as is performance, and obviously densification all goes hand in hand with reliability. I would say most designers design with us for a number of reasons. The key reason that we focus on densification and that is this: if I have a certain number of resistors on a board and I said: I'm having a hard time routing. I have a lot of passes on my board, either I have to route in more layers, so I'm adding to a multi layer design for its traditional through hole, and I'm gonna have to go to HDI which adds a lot of cost to my board. Or my form factor, my X&Y; dimension is a little too big I need to shrink it down, or my board’s a little too thick, I'm gonna make it a little thinner. So here's a tool, a technology that allows you to do that.
So let's say I have one resistor in a unit area of a board, and somebody says, well gee I want to etch in a pretty natural resistor. Okay who’s cost’s it going to be? It's gonna cost whatever our materials, divided by one. There's gonna be one resistor. Now instead I have ten resistors - what's the cost? It's our unit cost divided by ten because it's the same material that goes through the same print and etch process. So the greater the number of the resistors lower the cost per unit resistor. One application that uses our technology - and this is where it reinvents itself. A number of years ago - five/six years ago - it started being used in MEMS microphone.
If any of your listeners out there, any of your designers have a cell phone, you very likely have us in your cell phone in the MEMS microphone that you're talking out of, or you're listening out of right now. Now why use us in a MEMS microphone? We're part of an RC filter network which improves the sound fidelity significantly. So it's been found to be a very significant offering by the MEMS microphone makers and their end customers who are the cell phone manufacturers - but in very massive, mass quantity production - for many, many years over in the Far East, particularly in China, where our product is used extensively. So in those applications it was a combination of densification, they can make these MEMS microphone boards. The PCB's thinner because they eliminate the chip resistor, you don't have to assemble it, they can make them a little bit smaller and because you're talking about such small little element - even a few resistors only a couple resistors - in that design, you're talking about a fraction of a cent to put these resistive elements in a board. Fraction of a cent, no assembly-
Yeah when they're in the millions that matters.
-all that's very important. There's another example. If I'm a designer and say: hey I have a high-density IO/IC. My fast rise times I have some termination issues but I'm on a 300 micron pad batch and there's no way I can put a discrete component on my surface. To go ahead and terminate, I have too far to go. I have too many of these line. So I have IO of hundreds of traces, maybe a thousand traces, and I do it but guess what? If you're able to take every trace, every logic trace coming off that that IO and I build a resistor as part of that trace - to have a trace it has just a little of the copper removed - leaving a resistive element behind.
So it's a resistor built-in trace which is one of our products: ORBIT Ohmega resistors built-in trace - you can terminate every one of those drivelines - they're underneath the IC package, so they take up no board area. They terminate off that driveline, you improve impedance now, naturally reduce line delay, you also save money because now you literally have hundreds of resistors in a square inch of area or a couple square inches of area, and it saves a lot of cost by not having to assemble and put those discretes on your board now. So cost is a big driver. I just mentioned a couple of them. Densification is as well, but our material also is essentially inductive free. So you know, it means that you have less inductive reactance with fast rise times. So what happens; you get less EMI coming off your board, it's a cleaner signal. Our materials, also because of that, used in certain applications for absorbers or, R cards where they used us, that resistive film, to suppress some of the EMI coming off for-
-interesting
-as a shielding agent. So there's another application. So we're used extensively, not just in power dividers and R cards and absorbers, but obviously as terminators, as in filters, pull-up/pulldown resistors and now we're seeing a lot of activity in heater elements. We're in the military aerospace uses a 'cell' so my active laser activation where they have tiny resistive elements on PCBs that can go ahead and activate a laser for laser guidance for smart munitia, missile systems, or heater elements that can go ahead and maintain heat on critical components in avionics or even in space based applications. Or our product is used in satellites and even in deep space probes. We were on the Mars Express Beagle 2 Lander, on the surface of Mars where we have an Ohmega heater, key critical components up to above minus 15° C. It would work great if the parachute did not land on top of the lander
[laughter]
and prevent the deployment of the solar array but hey it was a great application for our product.
Well it's again - I think just such a surprise - or at least it was to me, when I learned about one: how old the technology is and two: that it's really because of complexity and just all the different things that are going on in the industry right now that it's growing - it's growing at a quick pace.
Significantly so, we've had a wonderful record year; every year is a record year. But that's the nice thing, that the resistive film is like a blank slate. What you do with it is a new assignor and so yeah in the 80s it was all ecologic termination and then it goes into power dividers, and they're still doing all that stuff. But you know what's happening now is, we're saying, it’s utilized in so many different ways so we talked about the MEMS microphone. Well there's new sensor technology, there's accelerometers or other there's other MEMS-type sensors who use us. Now we see automotive sensor technology that says: hey, we could use this, not only is it obviously super-high reliability, been out for decades you know, can be done in high volumes, very cost-effective, density impact identification. But there's some critical components you could use in automotive, 5G technology-
What about IoT Bruce, it seems like ideal for IoT, provided the cost-
-in IoT you're saying?
Yes.
The Internet of Things well that's why I'm talking about sensor technologies. IoT is a combination of a lot of things.
Yes.
Technologies are getting into it, we see our stuff on flexible materials, and wearables.
Your wearables, yeah that was the other thing I was wondering about.
Wearable devices, we can get smaller home devices, home audio devices, and as things get thinner, smaller, everybody wants things densified. So getting rid of the passives especially, really allows you to do that. So yeah IoT is a big thing, automotive, even memory devices going to DDR4, going out to DDR5 , those fast data rates are causing needs for termination again, and 'Genic' has approved the embedded resistor within some of the DDR4 structures. So memory is another area. So between sensor technologies and automotive, and home devices in things like memory devices, and things like heater microfluidic heater bio biomedical type things you know. We have micro heaters on an embedded board, you can have fluid come in and have basically a breakdown to the protein to do analysis, they use us for things like that. It's pretty exciting - so yeah it's been around for 45 years but guess what, we think that the new technologies, the new applications, it's almost like just starting over again.
Yeah I can see that.
Especially, we have the reliability long-term use, high volume low volume, high density/low density, so many different ways of doing it so, that's nice to have that background, make people feel good about using the technology, but knowing that all these new things are developing. I mean I can't wait for the next 45 years.
That's fun.
Well a couple of things I wanted to ask you about what made me think of calling you and wanting to do this - sort of a side note - is, you hear about passives being on allocation and all of that and I'm like: I wonder if Bruce is seeing an uptick just because people are freaking out over automotive buying up whole lines - I don't know if you're seeing that, it was just a curiosity I had?
Well yeah I know what you're saying, we definitely see an uptick, and now part of that uptick within the context of the of the industry. First off, I do want to tell your audience, especially your designers, we've been doing this for 40 - 45 years plus, as I mentioned - 46 years. I'd like to say that I was only 2 years old when I first got introduced to technology-
-We're going with that; I was three, you were two - let's go with that!
But we also have designers at our company whose job it is to work with the design community, particularly a PCB designer who could help them optimize their design, who can develop real footprints of resistors. What we don't want your your listeners to do, is reinvent the wheel; we want you to use our knowledge, talk to our people - say: hey here's what I think I'd like to do, I have an application I want to use, does it make sense for your technology? If it doesn't, we don't want you wasting your time. So ultimately you're gonna say, we're not gonna use it anyway we want you to have an optimized design because we want you to be successful. So think of us as an extension of yourself, of your team.
We're part of your design team we're there to help and assist. If you go to our website ohmega.com, there's a lot of white papers, there's a lot of good information there that people could read and reference. But more importantly is the communication with our staff, technical people who can really help you. Now talking about in general, the industry, there is an uptick in that. We talked about passive, so I mentioned it; we're in filters and MEMS microphones, resistors and capacitors and in one case, one of the capacitive materials, the embedded capacitor material FaradFlex, which is a embedded capacitor material, it's produced by Oak Mitsui. So Ohmega Technologies, my company and Oak Mitsui, got together and combined the material and had our resistive material on their capacitor material so we'd have one layer resistive capacitor.
What? My head just exploded!
What we did was we found that it's pretty simple, from a technology standpoint, to stick two technologies, each separately have its own complexity but working together really worked very well. Importantly enough it had such synergistic effects in terms of improved power, lower RTC characteristics, or change of resistance to function the temperature down to almost nothing, the stability is astounding over a wide temperature range that we applied and we got a jointly held patent for the combined technology which we have in the US, and also all over the world now. So it's a joint technology pact between Ohmega Technologies and between Oak Mitsui and Mitsui Mine in Japan for this technology, and we see applications where if somebody wants to get a resistor and embed it, they also want to embed the capacitor. They get rid of capacitors that are passive. A lot of times they want to get rid of resistors too. So it goes hat in hand with a lot of those.
In general, there is a lot of movement in the industry to embed it, but it's a growing thing because of densification, growing needs for real estate, smaller, thinner, lighter. You touched upon something and that is material sources, right now the industry is going through some uptick. I think part of that's military aerospace that has increased the amount of funding and a lot of military programs, but also other areas. So we've seen that as well and our products are used in a lot of stuff. Radar systems F-35, F-22, a lot of missile systems, Eurofighter, just all over the place. A lot of satellites, a lot of SATCOM, a lot of other things like that.
A lot of radars on the ground as well, but we're seeing that uptick because the IoT, as you mentioned, in the Internet of Things, there's more and more sensitive technologies being demanded into a lot of different product. People are amazed at how many sensors go into so many things these days and the key with a lot of that, is densification, smaller, faster, cheaper - so that gets hand-in-hand with the 5G, the automotive, self-driving cars that are coming up; a lot of the sensors the Lidar, other sensor technologies are going to self-driving automobiles and what everybody says is: hey, this all sounds great, but you know what? If I have a printed circuit board not using a computer and I have a failure in that it's okay. So it's annoying my computer goes, I swap a board, I put up a board, but I cannot afford to have any failure. I cannot afford to have anything go wrong, if I'm in an automobile that's driving itself, do you have room for any kind of failure? And so it's taken very seriously in the industry and going to a lot of these conferences and hearing the talks, the people involved with testing a lot of these are very concerned. They have to have absolute... as tough as it was, they have to make it even tougher for testing. Nothing can fail, so a lot of that comes into what can we do to improve reliability? Hey let's get rid of solder joints.
We want a kind of thing doesn't cause something go 'ding' and fly off a board anymore - or you know X&Y; expansion or z-axis expansion, all those things. Get rid of those solder joints, mechanical joints, improve the reliability while you enhance, densify, improved electrical performance. So we're saying that that's going on right now. And the other thing is that companies are concerned about, the industry is facing some interesting things right now in the printed circuit industry copper lead times are really out.
Yeah, that's crazy too.
-yeah the industry is getting smaller and smaller, yet at the same time the end-users and designers have to rely more and more on fewer and fewer resources. So we've been around since like I said 1972, so for 46 years we've been supplying this technology and we have never ever not been able to supply this in those 46 years. It's important for us that, A) we manufacture everything ourselves we make that resistive film we test it, we have test facilities which make sure that the product is what it should be before it ships out the door. We have hands-on manufacturing that's critical we don't want to subcontract making our product because we feel it's too important to our customers. They're relying on us. If we subcontracted, what would happen if whoever we had make it, went out of business? Or they sold the business; I don't want to do it anymore, and then we can't get product, our customers can't. We don't want to rely on someone else; that's number one.
Number two, we have very good close working relationships with our raw material suppliers. Most of our raw materials are USA-based, we get them in from the US you know. We want to have a critical supply chain. When you're talking about scarce resources like copper and other things, it's important that we have that kind of relationship with our suppliers so that we always have product. We're always there to support our customer needs when they need it, how they need it, and that to me is very, very important because a lot of companies are coming to us saying: oh yeah we're giving two months lead time on getting product, and how are we supposed to deal with that? And say what about you guys? I said: you want some of our stuff we'll ship it tomorrow. To us that's very important. Customer; you've got to go ahead and satisfy customer needs and especially their concerns that's absolutely critical in the industry today.
Yeah and it's refreshing because we get in this weird cultural thing as a business and it's like: Oh faster, cheaper or we're gonna be the lean supply chain and buy out. We get into this whole frenetic thing, but we forget if we're not meeting any of the customers we'll be out of business. So I really love that philosophy. Now as far as our listeners go Bruce, we're gonna share all of this in the show notes right. Everything that's on your website I encourage it, so we're going to supply all those links and the website you guys, if you're interested you can call Ohmega Technologies directly, get the help that Bruce alluded to. But they have a really great website with some really neat things that will go into even more depth than Bruce has gone into so far.
So thank you so much. So Bruce, as we wrap up here. First of all, thank you Bruce is joining us from IMS in Philadelphia today even though he's - at Ohmega in Culver, so thank you for hopping out of the show for a few minutes to give our listeners a treat, so thank you for that. When I wrap up the podcast I always like to have a little feature in here called 'designers after hours' because most of us techie weirdos have a little bit of a right brain and have interesting hobbies I've found. Is there anything that you do after hours that is creative, compelling, interesting or otherwise, or do you have any after hours? do you just work all the time Bruce?
Do I have any after hours? That's a good question.
Yeah we encourage people to call us and that keeps me rather active and the staff at Ohmega and we welcome that; please, please, please call us, email us, we'd love to talk to you and listen to you. As to me yeah I enjoy travel, I enjoy writing you know, I always have . Now it's mostly technical things or papers that I publish. But you know, I love doing fiction as well, I do do that and I get very involved. Between that and having a lot of crazy grandchildren running underfoot, that keeps me going.
That fills up your plate. So also, would you say you are a geek or a nerd?
I'm sorry?
Would you say you are a geek or a nerd?
That's a good question, I'm probably more geek than nerd yeah they've cleaned me up over the years, so I think I'm more geeky.
Yeah I would say you're more geeky, but you are walking on the razor's edge my friend. You can you can dip into that nerd space pretty easily.
[laughter]
Oh man, and I've been so good I haven't cracked any jokes, you can be mad about.
[laughter]
Here I am, now you're telling me I'm close-
-no, no only in the best kind of way that you like go into this nerdy space of technology but that's really -
-you want to know something; it's been a long time, I've been doing this a long time and I'm so excited - it's like it's a renewal if people get that I'm excited about technology about where Ohmega fits into technology it's because I really AM. It's genuine, our president Allan Leve, over at Ohmega Technologies, here's a guy who's had the same kind of passion. So every time we see something, we're always sending articles: look at this it’s neat isn't it? So if you call that nerdy, you call that geeky, that's fine. You know what we call it being enthused with technology and how we fit into that technology.
Absolutely.
-because I've been called a nerd and a geek I'm gonna drown myself in a Phillies steak salad.
-extra cheese and onions.
[laughter]
No - when I say you teeter is only because I remember when I was working at Transline Technology, you came in and you were showing us how it's done, how it's processed as a board shop - and I remember listening to you going: this guy totally knows his stuff and it was so articulate and I'm like, boy when I grow up I want to be able to talk like this. Like Bruce Mahler does, man he's got it going on! So that's why I say-
-just wait until I grow up really.
-well it is an exciting time in technology there's no grass growing under our feet so I share your enthusiasm for everything that's in the market and you're seeing everything so that is really exciting. Well thank you again for -
-thank you I appreciate it Judy, the opportunity to spend time with you and spend time with your audience, and hi to everyone out there - look forward to talking with you, look forward to working with you and like I said; a lot of exciting things out there right now in our industry so we're working in the best industry out there.
We are, now we're gonna send poor Bruce back to booth duty where he can stand in a booth. Sorry to send you back to booth but thank you so much. Again this has been Judy Warner with Altium's OnTrack Podcast and Bruce Mahler of Ohmega Technologies. Thanks for tuning in again until we hear or talk to you next time always remember to stay on track.
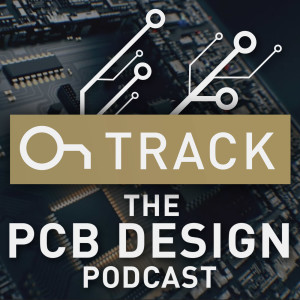
Tuesday Jul 03, 2018
Tuesday Jul 03, 2018
What finish should I use for my PCB Design? There’s no one single answer, it depends. Meet chemist and surface finish expert Mike Carano, the Vice President of Technology and Business Development at RBP Chemical, industry leaders in high performance chemical technology. Mike emphasizes a key question when it comes to surface finishes, “What are the reliability requirements of the environment?” Learn about the chemistry behind different finishes, fabrication and get tips for avoiding corrosion in unexpected environments in this episode of the OnTrack Podcast.
Show Highlights:
- Mike was Inducted into IPC hall of fame.
- RBP Chemical - veteran owned small business, based in Milwaukee, founded in 1954 as a supplier for the printing industry and over the years evolved into surface finishes and also carry product lines for Embedded Medical Devices and Semiconductor and Mining industries.
- On using solder mask over bare copper method - prior to going out to assembly the copper needs to be made pristine.
- What are the surface finishes and which to use when? 50% of industry using hot air solder leveling (HASL), a surface finish with a long successful history.
- Other surface finishes: Electroless nickel immersion gold (ENIG), Electroless Nickel Electroless Palladium Immersion Gold (ENEPIG) - which is common in IC substrate, packaging industry.
- Future of surface finishes: Tin-silver, Direct palladium copper
- What finish should I use? There’s no one answer, it depends.
- Are there common examples of things that can go wrong? ie. High frequency design applications - ENIG is a well known issue that most engineers learn about the hard way.
- Where is the final product going to be used? Is it a domestic product or for the military?
- Reliability first, cost last. Cost should not be driving force.
- The environment is what really matters i.e. Shock-drop or Brunel fracture - consider for mobile phones, ENIG - tin-nickel bond, not tin-copper, corrosion environments, temperature extremes
- What are the reliability requirements of the environment?
- The most high quality board fabricators have strong process control and automation in place to ensure chemical stability.
- Board designers are looking for electrical performance. Need to ask about the environment.
- I would put every designer in a circuit board fabricator for a week and let them build a board they design.
- To learn, you need to practice and get practical information on building the bareboards.
- Creep corrosions on the mill automation machines because the OEM is specifying the finish.
- Japanese techniques i.e. Shokuku chemical
- Most substrate work is done in Asia; IC substrate packaging at its best is in Japan.
- Advice for learning: IPC courses, CID and CID+ training is one way to learn more.
Links and Resources:
IPC Hall of Fame Interview Video
HDP Users Group (HDPUG)
Hey everyone it's Judy Warner with Altium’s OnTrack podcast. Welcome back we are glad to have you join us again today we have a very unique topic and speaker which was actually brought about by Mark Okumura who is the Senior Principal Hardware Engineer from ETS Lindgren who reached out to me and asked me about the topic of surface finishes and lucky for you I happen to know the guy who is a chemist and expert on surface finishes. A longtime friend Mike Carano from RBP Chemical. Before Mike and I get started, I wanted to please invite you to connect with me on LinkedIn or on Twitter, I'm @AltiumJudy. Altium is on LinkedIn, Twitter, and Facebook, and also please know that we're recording on YouTube in case you want to see our sunshiny faces. So Mike, welcome thanks so much we’re delighted to have you.
Thanks for inviting me.
It's good to know friends in high places right?
Well, I have friends in low places.
[Laughter]
I don't believe it, well maybe, so Mike, I’ve got a question. First of all let's talk about your background a little bit so as a way of introduction Mike Carano was inducted into the IPC Hall of Fame a few years ago and I had the privilege of doing the video interview that was highlighting his induction into the IPC Hall of Fame because he has served on so many committees and boards for IPC, but he really is the go-to guy on chemistry. So Mike, tell us a little bit about your background how you got into chemistry specifically related to the printed circuit board electronics industry?
Well sometimes Judy, things happen by accident really, chemistry and sciences were always a love of mine so I always liked to experiment - my parents got me the chemistry set, and everything from blowing up golf balls to me making things at home, everything from even experimenting with making wine that's chemistry - that seemed like a good thing to do right? I also realized that probably owning a vineyard would not be in the immediate future so onward and upward with chemistry, particularly the area of physical and advanced chemistry electrochemistry working on a Master's Degree, I happened to be walking up on campus one day back in 1980, 24 years old, and there's a gentleman standing outside this building and he noticed my chemistry books he says, hey come here I want to talk to you, and I thought, oh what's this about? And I noticed the sign on the door there, Youngstown Ohio City Electrochemicals, and he asked me if I wanted to interview for a position there. Well it was perfect because graduate school was more part-time. I was doing some teaching assistance and what do you know, I interviewed for this thing on surface finishing chemistry having no idea really what I was getting into, but I did. The idea was finishing my Master's degree, and go on and do something else - maybe do this for two years - well 39 years later here I am still in the industry. In some way, shape, or form, so that's how I got into this and as the company, Electrochemicals in those days, founded primarily on the metal finishing industry - you know, surface finishing for doorknobs and bumpers and decorative plating. Well the company was just then getting into printed circuit board chemistry and a lot of people didn't even know what that was in those days because it was a fledgling industry there was mostly - remember Judy way back then was the 80% of the industry was really run by the OEM...
Yeah
-So digital equipments the the Adelphi’s, the Delco’s the IBM's, but pretty soon there was that switch, and then I got involved in IPC and pretty soon was formulating chemistries and technical service, traveling globally around the world was fascinating for me, and here I am today, and still in the industry in some way, shape, or form. You know, you evolve, you continue to evolve matter of fact, just like surfaces they've evolved.
Yeah right.
Where we are today, I'm sure they'll continue to evolve in the very near future.
Yeah for sure, so can you give us a quick overview, I know you were Chief for many many years and now you're with RBP can you give us a quick thumb nutch of RBP?
Absolutely, great opportunity, company privately owned (veteran owned) small business, our company is based in Milwaukee Wisconsin and was founded in 1954 and has been privately held since. The current CEO and majority owner is Mr Mark Kannenberg, he's my immediate boss, Mark served in Vietnam, he's a West Point graduate and also a Harvard MBA, but he always wanted to kind of get in the business of owning his own company even though he had many, many opportunities. So he's now been running RBP for these last 30 years. Under his control the company has grown beautifully - initially, the company was founded as a supplier of materials and chemistries for the printing industry, newspapers, newsprint magazines, but over the years also evolved into surface finishing, surface treatment and printed circuit board chemistry, which is the company today, because as I said it continues to evolve. Today and we have four major product lines the printed circuit board and photochemical milling chemistries. We have a great product line in the area of embedded medical devices, and we also serve the semiconductor and the mining industries with some specialty additives. A lot of people don't understand the connection but there's a connection all the way through the platforms because the chemistries are basically adapted to work in all those industries which makes working with RBP fascinating for me - the diversification but yet the the continuity and the familiarity - so great opportunity and I've enjoyed it immensely.
Good, thank you for sharing that Mike, so let's jump right into surface finishes. I'm sure most of our listeners who are engineers and designers will be familiar with surface finishes but let's just go back to our ABCs for a second and just define surface finishes for us for PCBs.
Sure that is the part of the board that is really going to be used to prevent oxidation of the base metal, as you know, typically we have copper as the base metal if you're using the solder mask over bare copper method where you basically put solder mask down that nice green stuff and the copper is showing, you have to make that copper solderable, you have to preserve the solderability so typically, prior to that board going out to the assembly operation, the copper has to be basically made pristine with a finish that does not oxidize so that you can join the component leads, whatever they may be, whether they be surface mounts, through-hole, BGA, QFNS, QFPs, they have to be able to to wet that surface and form a reliable joint. So the surface finish is critical for that application and for that end product.
So tell us - give us just a rundown - of what the surface finishes are and then we're gonna jump in to which one to use when.
Sure well, here in North America and primarily for the military, we're still using - at least 50 or so percent of the industry - uses hot-air solder leveling. Basically you're taking that solder mask over bare copper board, flexing it, cleaning the copper and then dipping it into a molten solder pot to coat the surface. But over the years, due to a lot of other constraints, one of them was to get rid of lead. And even when we have lead-free, hot air leveling, the other surface finishes have evolved, as a matter of fact, have taken center stage primarily outside of North America. With these surface finishes are we hear the term ENIG, which is Electroless Nickel Immersion Gold we also hear about Electroless Nickel Electrons Palladium Immersion Gold also known as ENAPEG, and while that may be an expensive finish, you see that used quite a bit in the packaging industry, the semiconductor packaging IC substrate industry. Then there is OSP Organic Solderability Preservatives, which is actually the only one of these to be non-metal-containing and then we have immersion silver, and immersion in tin, and again we expect that there’ll be other additions of these finishes coming up in the near future. Potentially a tin silver or direct palladium over copper to get rid of the gold altogether. There's a lot of movement in this area to enhance the surface finish reliability at the same time managing costs because you see how precious metals like gold and palladium can contribute significantly to the cost of that board. Which then makes you wonder, okay what finish should I use and when should I use it? So that's a rundown of our finishes and each one of them - I can tell you this Judy - when people ask me, and I travel all over the world, what finish should I use...
Yeah
-no one finish fits all.
That's a loaded question isn't it Mike? It depends, that's the answer.
It depends right.
Well as I mentioned in the beginning, this gentleman Mark Okumura reached out to me and said, are you ever going to talk on your podcast, or do you have any information about surface finishes? Because in his particular case - and this is just one of many many high frequency application engineers and designers - have found out the hard way that if they use ENIG the Electroless Nickel Immersion Gold, that if it's high frequency then we have the skin effect and then the signal begins moving through the nickel and the nickel is lossy, and unfortunately that's a well-known issue it's been going on forever but it seems like people have learned that the hard way, unfortunately one at a time, that's just one example. So can we talk about when we talked a few weeks ago, about environment playing a huge role on how to make a selection on your surface finishes. So can you jump into that a little bit?
What I mean by environment is, where is that final product going to be used, and let me just preface it this way, if you're in this industry, whether you're in the printed circuit board industry directly or you're an assembler or you're an OEM. Choosing the final finish for that product may be the most important decision you make, because it is going to impact that long-term reliability of least of that solder joint now as I’m saying solder joint, I'm using it interchangeably with lead-free as well. And compounding that, is again, where are the boards going to be used? Is it to finish in harsh use environments such as automotive under the hood, military aerospace - and that's one application. But then, what about consumer items like mobile phones, smartphones, desktop computers, smart tablets, household devices. You don't need a product or a finish that adds $9 a surface square foot of the board if you're using it in a washing machine in your house, or in a microwave, or even a desktop or laptop computer. Now military aero things like class 3, or class 3A that have to work 24 hours a day, seven days a week and can't fail - you can't fail. You may look at that and you say, well do I need ENAPEG, do I need ENIG? Do I need to make the OSP also work? And some people really are surprised when they find out that OSP’s a very reliable finish. It's not wire bondable but in terms of reliability in forming the copper tin in a metallic, and having a reliable solder joint, it's fantastic.
So think about that, it also happens to be the lowest cost finish but I am of the opinion, and I asked somebody this, and I listed ten things I have cost of the finish at the bottom, because that should not be the driving force of what you put on the board. It's the environment where the board is used and then you ask yourself other questions. Is cosmetics important? Do I have to have a shiny silvery finish or don't I need one? I'm worried about shock drop, we know for example, if something I have in my hand drops a lot like a smartphone. you worry about brittle fracture of the components - actually fraction when that phone hits the ground - we've all dropped our phones and the mobile phone companies, the Apples of the world and the Samsung's, conduct shock drop tests all the time because that's important criteria. You don't want to spend money on a new phone, drop it and find out the components fell off. So that's why you don't see ENIG used a lot on the smartphone, you use things like something that makes it much stronger - copper tin and a metallic bond - whereas with ENIG, your tin is formed with the nickel so it's a tin-nickel bond not a tin copper one.
I see.
So, we all know, and there's been hundreds of papers published by many, many companies and fantastic researchers around the world, showing that the tin to copper in a metallic is much stronger than the tin to nickel in a metallic. So that's something to consider as well, not just the cost. But you might use ENIG in medical devices, we know the military is starting to look at ENIG as a final finish, but they also do some things to ensure the reliability of that component as it is attached to the surface. So there's a myriad of things to look at - oh and corrosion environment - in terms of creep corrosion, and that's an issue and silver tends to be somewhat prone to creep corrosion, but in an industrial environment kind of outside, or in a clay modeling studio or in a paper mill where sulphur is emitted.
Yeah that's interesting.
So, if you told me, well I'm making this part because I work for General Motors and I'm modeling, I'm gonna use clay to model my next car and I'm gonna have all these computers hooked up inside that studio, I think I'll use boards with silver on them. Well you probably don't want to, your work is gonna be lost, so that's one consideration. As I said shock drop is another, but again where are you using the final product? Industrial automation, using it outside, base stations, all of those things. Industrial controllers where we're subjected to not just environmental contaminants,but maybe significant vibration, temperature extremes etc. So always look at the environment where you're using it and what the reliability requirements are. Can you afford the warranty, what is the warranty when you take something back? If it's inexpensive, you can use an inexpensive finish but if the cost of failure is great, you should rethink that finish which you're going to use and how you're going to use it.
That totally makes sense to me. You had mentioned that a lot of people think that OSP is generally a sort of low-tech product, but you were pushing back against that when we discussed that, why is that?
Well 25 years ago OSP was what you would call the single attachment finish - one reflow, maybe one through-hole, and that was it. It lasted four to five months whereas the other finishes, like hot air leveling - one year, two year shelf life - that's changed. Companies have made significant improvements in the reliability. Also the the ability of the OSP to reduce oxygen penetration on the copper, and that again is what you're trying to do, you're trying to prevent the underlying copper from oxidizing so that when the solder melts and spreads on the surface, it spreads and encapsulates the leads on the side on the components and solidifies and it's a highly reliable. If the surface is oxidized even slightly and doesn't wet properly you've lost your reliability, but OSP has come on strong now and you see it in automotive under the hoods, major telecommunication companies using it for the reasons of getting away from brittle fracture, you see them in smartphones - a significant number of smartphones - and I have experience in those areas so, I'm talking from personal experience - the reliability is there with the right finish. Now the low-tech you find, if you buy a low-tech OSP from somebody you've never heard of, you’re taking a risk, but the companies out there - two or three that are making significant contributions to the performance of OSP - they've upped the game significantly. Many of them are fifth-generation molecules, these are synthesize organic azone molecules, that just do a fantastic job, and I would not hesitate to recommend it for numerous applications.
It's interesting how that's evolved over time, I wasn't aware of that until you mentioned it to me recently, and that's some of the magic of chemistry that just runs in the background of our industry until sometimes - it seems like - until there's a problem.
That's right.
We don't talk about it, so I'm glad to sort of have this discussion.
That’s a good point, to that point Judy, when Black Pad showed up what people will call brittle fracture...
Yeah.
-it set the industry back 15 years for ENIG because they didn't understand it, they wanted to blame the phosphorus content of the nickel deposit, but that turned out to be incorrect, it turned out that the cause of that was the galvanic effect. When you put immersion gold on top of nickel you're not electrolytically plating it, you're doing an immersion deposit, also known as galvanic cells, so to deposit on nickel, some nickel actually has to corrode and leave the surface, so that the gold can take its place. And that's the main difference of an immersion deposit. Well, what was happening because of the way things were being run, pH, nickel morphology, roughness, etc that galvanic effect was significantly large, causing this corrosion - significant corrosion - to take place on the nickel surface, and that would impact negatively the formation of the solder joint. And there you would get brittle fracture, you drop something, It breaks. So, things are better now, but I still would be very careful, if you told me, I'm gonna put ENIG on my board today, I would say do a first article, make sure that the board design you have, will not end up with this issue.
That's a good advice and, for people who are listening. Again - you're going to hear me say this over and over again - and I'm not going to apologize for it, is that you need to get into a board house, find the time because most really good, world-class board houses - you're going to go in and you're going to be surprised to see... and Mike can talk about this, the complexity of the labs they have in place to make sure that their chemicals are stable and doing what they're supposed to do. Mike, I imagine you've spent just more than a little bit of time inside of board houses discussing chemical balance and, if you would, jump in on what the choice of surface finish has on the fabricator and why the designer should know about that?
Right yeah, well first let's go back to your first question about these board fabricators the ones that are high-quality board fabricators and I'm looking at not just on the surface finishing side, but also other aspects of the circuit board fabrication including electroless copper, direct metallization, the amount of control that they have in place, process control automation, to keep plating and other the key ingredients within a very tight operating window. And that's not difficult if you invest the time, and you have the commitment to ensure that. I can’t tell you how many times Judy, have been in situations where I've had to troubleshoot a problem because someone said I've got this issue, I've got that issue, you go there and you find out that they were running the chemistry basically way outside the window. Well, why'd you do this? Well, we only check it once every two shifts. Well, you can't have a high volume operation like what you're doing and then check the chemistry once every two shifts and I'm telling you, 90% of these problems that I see related to process, are related to incorrect use of the chemistry and mishandling of the controls that are available to you.
Now does that mean that the fabricator needs to work much closer with the supplier, but if the supplier is already doing this for them, the fabricator needs to take some responsibility. But again, I've been with a number of companies who have complete failure analysis labs also in their facility. So, they take it to a very high level, they're basically their own qualification facility to ensure that they understand where the issues are. They categorize every defect and those are the kinds of ones you want to work with.
Absolutely, and I've worked for shops like that where they literally had PhDs in chemistry renting the lab. They were doing their own cross section and when suddenly, there's a spike in volume - if you're not on top of it and you don't have those people and all of a sudden - whoops production went up, but we're still checking our bass at the same rate we were before. And then like, oh what happened? Well there's all these things that need to be taken into consideration and adjust it accordingly. So, what other fabrication considerations are there that that maybe designers or engineers that are designing boards would want to consider as they decide what they're going to choose?
Well good that's a good point, and you and I know design is important, because there's this conundrum in our supply chain. The fabricator is looking for design for manufacturing and the designer is designing something to work in a certain fashion. Electrical performance, dielectric spacing, and and they don't take into consideration potentially what that does, how that impacts the bare board fabrication process. That's a very significant right? What - and I'm gonna go back to this - because I find this to be an issue as well on the assembly side boards come into the assembler, they come from somewhere, and they call me and say I have the the plating is lifting from the surface when we assemble, or the solder mask is lifting well I said do you did you specify the grade of solder mask, do you even know what solder mask is being put on the board that you're bringing in to assemble? Well no. Now I find out - it's very easy for me to find out - that they’re using, the fabricator... wherever, typically not here, are using a low $10 a kilo solder mask because no one specified it. And of course, that $10 a kilo or less solder mask is probably gonna work beautifully in a handheld child's toy, it's not going to work very well for your medical device. And you're gonna have all these other problems. So I think, I hope the designers would get more involved in understanding the difficulties in making a bare board and also understand: just don't specify ENAPEG because it sounds great, or sounds sexy. Because number one, you're probably not paying for it, somebody else has to pay for that ENAPEG and at $12 and $10 a square foot. Understand - and this is where the board designers are looking for the electrical performance - do they ask where the board is going to be used? Is it going to be in a harsh-use environment, is it going to be in a benign environment clay modeling studio? These are the key questions for them. Typically what I see designers do is, say this is how the board should be built, these are the layers, these are the holes, and you should use this material with this dielectric constant. That's all great, but it's not enough.
Right
And I've been teaching this advanced troubleshooting course with printed circuit board fabrication for years, and you'd be surprised at the number of designers that actually take that course, and they ask the craziest questions. Which tells me they haven't been outside of the board fabrication, outside of their design studio. Understand that you need to live with that a little bit I would put every designer at least in a circuit board fabricator for two weeks and have them build a board that they designed.
Yep I agree it's hard - we encouraged that here a lot - and almost every guest on here says the same thing. Because you and I've been around the block a little while, and understand that there's time constraints for them to get out. However the long-term cost of not getting out there and not onboarding. And this is another plug - you and I've been around IPC awhile - this is another plug for CID and CID+ training, as well because there you onboard some of these things that may be outside of the obvious things that are around manufacturing and assembly. So Kelly Dack wants to start field trips on every CID course. I'm like, yes let's do it!
You know, to me that would be fantastic, and to be honest with you and being heavily involved myself in an IPC, one of the things that I've suggested that when CIDs and the CID+ students earned their certifications, they should also have to get some understanding in coursework and practical on the bare board fabrication. You should make it like you did in college, the practicals, you just didn't do the book work, you had to go into the lab...
Exactly!
-apply what you just learned from the book, because if you couldn't resort to practice, at the end of the day you can't practice it. You've not learned.
And as we both know, the cost of ignorance in these areas is so high, like avoidable mistakes.
Costly... I've seen an entire clay modeling studio shut down, a paper mill shut down, because, again the paper mill folks were buying the controls from the OEM who was specifying the boards to be made but the finish... So the poor industrial automation company using these expensive controls were wondering why these inexpensive instruments are no longer doing what they're supposed to do. And they find out that there's creep corrosion in there because the OEM specified immersion silver or bought the board somewhere cheap where the individual companies decided to cut corners, like they do, to meet the cost. Like not putting enough gold on, not putting enough nickel on. You know, there are specs for a reason.
There is, absolutely.
And that's obviously a discussion for another time.
Yeah that's a whole other podcast, and then there's everything you're doing - HDPUG - which is another podcast I'd like to get you on for as well. I want to put a pin in our conversation right now because I realized, in the beginning I failed to mention to our listeners that you may hear some background noise here. There's some... well, what I was telling our producers is, we're building a better podcast but it’s noisy in here, but really what's happening is we have some construction and of course it's overhead in the green room here in our La Jolla office, so it's directly overhead, on this day of course, so please, please excuse any background noise.
So Mike, you sit on boards for international companies as well as companies here and you are a respected and trusted advisor. You mentioned to me about things that the Japanese are doing that are very innovative and that is that they're mixing finishes and doing selective finishes can you tell us a little bit about that?
Yeah, and this is if you can see the IC substrate side in the Japanese, or the ones who really made miniaturization go. I mean they understood how to make things small, not just lawn mowers and engines like Toyota Camrys and things like in the Prius, but they figured out early on how to do it with circuit boards and and putting more functionality on the chip. Matter of fact, that's where OSP was actually invented was in Japan, in those days it was called pre-flux because it was in the rudimentary 1970s day, but they pioneered the OSP and matter of fact, today the leading OSP company in the world is Shikoku Chemicals out in Japan, they continue to evolve that chemistry and I trust them immensely.
So, going back to that question what you do is, in the IC substrate market, where you've got a complex chip that has to have gold leads or gold wire bonding, you have on one side of the substrate, nickel gold, and then you bond the chip with the wires to that feature. But then on the flip side, which is going to be a BGA feature, you have bare copper which is OSP. So they have the BGA balls on the bottom side and the IC substrate - the chip actually, the the die as they call it - on the top side. So you have ENIG - selectively on one side and bare copper meaning OSP - on the other and of course it's a flip chip. So with the IC substrate or the IC chip in there, you marry that BGA to the Barriss surface of the copper board meaning an OSP, and you've got this fantastic package, if you will, instead of doing it all in the nickel gold or all in ENIG and handle it selectively. And they've developed these processes, and they've also developed a selective imaging, if you will, to make that happen. but it's relatively easy to do, once you understand the ramifications and how to make it work, and make sure you don't get an OSP that doesn't say, ‘attack’ the exposed nickel gold. All these things, it's pretty pretty intricate, but it's been around for some time and with a lot of success so I've selected ENIG as they call it.
Interesting, so I was just gonna ask you, what does that do to cost and process ? You're saying it's not difficult, how about cost implications?
Well there is an additional cost of putting the second imaging step down to protect the board from plating where you don't want it to go, but instead of doing the entire IC substrate in nickel gold, you're doing just one portion of it where the wires from the chip are placed, from the die so, that does help you significantly in the long run. It also makes the BGA perform better because you're marrying basically tin to bare copper making another opportunity there.
Do you think that will find its way here into North America?
Well, the thing is there's only a few fabricators here who do work in the substrate industry, most of the substrate work is done in Asia for the Amcor’s and the Intel's and the Samsung’s so you see a lot of the supply chain there. Some big American owned companies in Asia are doing it in volume, but again, if you want to see IC substrate packaging at its best it's the Japanese.
Yeah that makes sense.
Yep they’re the leaders,and they've been doing that for 30 years, so they tend to be ahead of their time, but now the time has come.
Yeah well it's interesting to get your perspective on sort of a global scale, as well this has been great. Our time is coming to a close here, but will you please share with us links to any white papers or slide decks or anything you have? Because I think how I want to wrap up is Mike, if you are a designer what would you do with all this information? And we've kind of shared it sort of anecdotally and quickly here, but if you wanted to learn more about this where would you go, and what kind of things maybe can you share with our listeners that we can throw on the show notes so they can maybe get better at this.
Well very good. I would encourage you designers who haven't taken an IDC course outside of design - I encourage you to take them - you look on the IPC website. We just had Apex where, in addition to technical papers, there were workshops on a number of different subjects including my Advanced Troubleshooting course, but there were also courses on the Basics of Bare Board Fabrication, and some of the instructors do a great job of giving you the tour, if you will, of the very basics. So you can get a feel for how the board starts with bare laminate, actually starts from the design, and actually ends with the finished product, going out to assembly from a manufacturing standpoint, and you can follow that up by taking the Advanced Troubleshooting, so you can understand where some of the problems and technical issues come from when the board is fabricated, with the various chemical steps and the mechanical steps like drilling and plating and immersion gold and silver. Whatever you need to do, that would be something you should do, and also watch for IPC Tech Ed, where they're going to be putting more and more of these courses. Standalones in different parts of the company whether it be San Jose, San Diego. We just did a course in Boston back in April which was well attended, and we just had the High Reliability Conference in Baltimore a few weeks ago, which had a high military aero content to it. But there's a webcast as well. And also, I encourage you to look at the IPC website - http://ipc.org/. Go through the technical papers, look for the events that are going on there but obviously at every Apex there will be this myriad of courses to take, and I encourage you to go to your boss and say, look this is something I think will benefit me, and you're gonna send me there anyways for the other events, so why not get there on a Sunday and take this course?
Yeah good advice.
SMTA is another good place that has a lot of technical papers and seminars and webinars related to things like surface finishes and design for reliability etc. Matter of fact, IPC actually has a Design for Manufacturing workshop that is taught by some really highly-skilled people too, so that might be something that a designer would benefit from. Again, because the designer or an actual designer is actually teaching the course from experience because he lives it...
Yeah
-let me build bare boards... I'm talking like Gary Ferrari and Susie Webb and those folks, they've actually built boards but they also design. Happy Holden and he's built boards, he designs boards, he understands - they get it.
Right.
That would be an interesting perspective for all those out there.
Okay good, that's great stuff. Well we'll make sure to attach the links to IPC and I know they're doing a lot with education right now, and so I'll make sure - and if you have anything to share with me please do - and we'll make sure we also include links to RBP Chemical.
Yeah, https://www.rbpchemical.com/
And then we will share anything else that you want, and I'm hoping I might be able to twist Mike's arm to come teach a surface finish course at Altiumlive in October. But we'll see, he's so in demand, hie’s a popular guy - but if I had my wish, that's what we would do because I think it'd be a great place again hope to have about five six hundred designers there so I think they would benefit.
So Mike thank you again, you're a dear friend, and thank you so much for always freely sharing your information. Mike also writes a column for PCB007 Magazine, called Trouble in Your Tank, and that's where I learned a lot and actually how I became friends with Mike as I was asking him if I could please take some of his content and repurpose it for blogs I was writing. So we'll also include that link to his column. So Mikey, thank you again you're a dear contributor and friend to the industry and thanks so much for taking time out of your busy day to do this with us it's been fun.
Well, thank you Judy, thanks for inviting me. I appreciate it, you have a great day.
Thanks you too again. This has been Judy Warner with Altium’s OnTrack podcast and Mike Carano of RBP Chemical. please join us again next time - until then - always stay OnTrack.
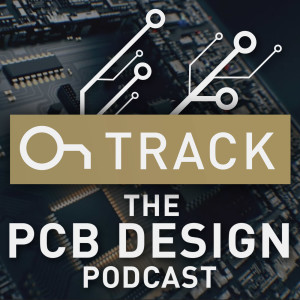
Wednesday May 30, 2018
DFA Tips from Duane Benson at Screaming Circuits
Wednesday May 30, 2018
Wednesday May 30, 2018
Duane Benson from Screaming Circuits shares DFA Tips and a piece of history as he shares the story behind the scenes in developing quick turn prototypes. Listen to learn how one entrepreneur brought fresh perspective to the business that led to great success. And see why Screaming Circuits is uniquely positioned to handle all the leading edge components that PCB designers have available.
Show Highlights:
- Screaming Circuits was founded on the premise to get prototypes built quickly. It was a struggle to get small volume prototypes built and a market need was discovered.
- For prototyping - going abroad invites its own set of risks.
- A traditionally 6-8 week process, Screaming Circuits does in hours.
- We don’t specialize in a vertical industry, so we see a lot of the leading edge components.
- Layout isn’t taught in schools or its self taught. The experts who knew how to make layouts work perfectly have retired.
- We built a business around stuff being wrong. Stuff isn’t going to be right when it arrives to us and we have to fix it.
- Why are we having a problem sourcing parts?
- Personal interests? Photography and decaying industrialism.
Links and Resources:
Downloadable Circuit Talk
Twitter: @pcbassembly, @duanebenson
Screaming Circuits on Youtube
Hey everyone this is Judy Warner with Altium’s OnTrack podcast. Welcome back to another podcast session with us. As always we have another incredible guest with us today but before we get started I wanted to invite you to please connect with me on LinkedIn. I'm very active there and share a lot of resources for engineers and PCB designers and also - I don't think I shared this in past podcasts - but we are also recording this on YouTube as well as just an audio. So you can always go to YouTube and go to the Altium channel, look under videos and you'll find these also in video format if you should prefer to listen to this and watch it in video format. And also with Altium, you can always follow us on Facebook LinkedIn or Twitter and we love engaging with you. We always love to hear from you about subject matter experts or subjects you'd like to hear or learn more about. So, without further ado, I'd like to welcome our guest today who is Duane Benson of Screaming Circuits, out of Canby, Oregon, correct Duane?
Canby that's correct.
So Duane welcome, we've crossed paths for several years now and it's a delight to have you and learn more about Screaming Circuits and EMS and how designers can do things to to be more effective in the design for assembly and just learn about Screaming Circuit’s model, which is a very unique model by the way, I'm eager to jump in.
Well thank you I'm really happy to be here thank you for asking me to participate in this.
My joy. So why don't you start out by telling our listeners a little bit about who and what Screaming Circuits is, because it really does have a highly unique model, and kind of the why behind you guys started the company and created this model?
Well it started back in 2003, actually that fifteen years ago now. Yikes..
Yeah, I know, how did that happen?
So about that time our parent company Milwaukee Electronics they had a number of customers that were struggling to get small volumes of prototypes put together back in the back in the olden days - if I can use that term. Prototypes quite often were sort of slotted in on an ‘as available’ basis. So say you might need five prototypes and the EMS company would say, well we’ve got a big run going on and I can put you u on the machine in two weeks so you can get your prototypes then. And two weeks come along and something else came up, so another week... Even going back before that, back in my day they didn't focus, for example, building a prototype.We'd have a big bag of parts and some blank circuit boards, and we'd hand them to this poor technician on a Friday afternoon and the engineers would go, could you have these built up by Monday?
So it was becoming a real struggle to to get prototypes, get small volumes of any sort built and a couple of our customers came and asked us and said, can you can you help us out with this? It's just not working and the Milwaukee Electronics’ management thought about it a little bit and thought, why can't we short-circuit the process?
No pun intended right?
Laughter.
So the management experimented a little bit and then decided, , there's an actual business here. So back about that time they brought Jared Store out here to start up what they called the Screaming Circuits division to focus specifically on getting prototypes done quickly.
Mm-hmm.
And , from that time the initial focus of the initial business was basically Jared with email and phone and one of our partners Sunstone Circuits, they built the blank circuit boards - the raw fabs. They'd give us a call and say, hey one of our customers needs some prototypes built, can you guys do it? And that's how the business started.
So you guys created the synergy. Now I've had the pleasure of meeting Jared once at least, through the phone and email and Jared was young right? He was the son of the owner so, I have to insert that. Because I kind of love that those of us who are kind of old dogs in the industry - I kind of love that he said, well why can't we do this? And he just kind of, like you said, a phone and a thing and just said why not. Because he wasn't constrained by the way things were done in the past which I kind of love that.
Exactly he was a young entrepreneur, in fact, I don't know if he'll want to admit this but this was his first job out of college this was kind of an experiment for him to get into a career, into business and he did a fantastic job. Basically by ignoring all of the old rules.
I know yeah.
Yeah and then in 2004 - well somewhere between late 2003 and early 2004 - we first went online with a very, very simple quote system. We boiled it down into six different factors and based on that, came up with a quote and it was all kitted at that point. So we'd say, hey it's going to cost you this much, send us your kit, send us your files, and we'll build them up for you.
Now since that time, when we were talking earlier, it seems like it's morphed into not just specifically prototypes but just quick-turn. It could be quick-turn pre-production quick-turn production even right?
Yeah
The world of manufacturing of electronics has really changed in the last decade and a half . There was a time when electronics were not going to be designed and built in this country. Back in the 90s, when I was working for InFocus again, everybody was outsourcing everything and then over the next decade after that, it was all going going away.
Yeah.
And there was going to be nothing but high volumes manufactured offshore. Well about the time we started doing this, coincidentally the open-source hardware movement came about with the Arduino and some of the other things that came with that. Kickstarter showed up and that really changed the hardware design dynamic. It lowered the barriers to entry to building a hardware company and over the last decade and a half the hardware startup has come back with a vengeance. The problem is, as manufacturing is really, really expensive - unless you're doing super high volumes - so these companies would run a Kickstarter, they'd sell a thousand of an electronic board and nobody would build it for them. So then, , they'd then run off into into Asia and they toured all these shops and these people would either say, no that's not enough or they’d change the design, steal the intellectual property and, you can't. There's little details like that so, getting a hundred or a thousand or five thousand is extraordinarily difficult. And yet there's an awful lot of companies that sell just that many of something.
Yeah, it's really interesting that it morphed into that niche right?
Yeah.
You had, it sounds like you had everything, in place to fill it right? You'd built it to do address prototype - traditional prototypes - and as the market changed you were kind of ideally positioned to address those kind of start-up Kickstarter things. So you and Sunstone have worked together in parallel, I take it throughout this process?
Yes they've been our partners since the beginning, and at this point they build the vast majority of our circuit boards and we do, if necessary, go elsewhere. Or if a customer sends us the boards or requests something else, but the vast majority of our boards are built by Sunstone. They're about ten miles away over in Mulino Oregon.
Another big city like Canby…
Laughter - well compared to Milano Canby is the big cities...
Yes well it's a beautiful area. So, tell us about what you would see in a given day and then I would like to ask you to jump into speaking to designers that may be listening, and go into kind of some DFM tips and tricks. But before we do that, tell us about what are you going to see in a day?
To get a picture of what happens there at Screaming Circuits there's two factors that are pretty important. One is a traditional EMS company. We we see about as many different jobs through here in a week as a traditional medium-sized EMS company we'll see in a year.
Wow!
And the other factor that's important to notice, is that in - using that term the olden days - getting a quote and an order for a project might be a three to four week process going back and forth with all the files, component availability, making sure the design works and then after you place the order, you've got the NPI process which is another three to four work weeks. So, you've got a six to eight week process that we do in six to eight hours.
How is that possible? I mean we may not have enough time here Duane, but I've been in the EMS industry and it’s an extremely complex process, just getting the components you need and making sure they're right and there's not obsolete parts, and that you've got a clean BOM, and it's so complex. How have you condensed it without giving away your secrets?
Well there's a lot of things that matter if you're building a hundred thousand of something or a million of something. At that point fractions of a penny count and you're going to spend a lot more time quoting. You're gonna have to worry about getting large quantities of components if you need 20 of a board you can go to Digi-Key and get the parts for a buck, that would cost you a quarter of a penny if you bought them at high volume, and that's still fine now, that's part of it and then you don't have to worry about some of the inefficiencies that would absolutely kill a high-volume manufacturing manufacturer. You don't have to worry about those because if you have to tweak things by hand, while that is more expensive per unit, if you're building 20 or a hundred or a thousand it doesn't matter quite so much. So really what we've done is, we've stepped back and we said, what is important and what is not. The objective is to get working boards into an engineer's hands as quickly as possible and you'll notice there aren't things like how do we make it the absolute least expensive, or things of that sort, it's about getting the working board's as quick as possible so you focus on just the things that matter for that.
Right, you mentioned when we talked a few weeks ago, about it becoming what you had called a transactional model, which is really a different industry and you can go online, place your order in a very transactional fashion, but it also speeds up your time to market, and gives you something highly valuable?
Yes it does, we don't we don't spend an awful lot of time on the financial component of it. For the most part you give us a credit card and we start building so we don't have to worry about the bank component of it. For larger companies we do, because some people, the government or whatever, they have to operate that way. But for the most part you just give us a credit card and that again cuts some time out of it. We also look at each order as an individual transaction, that's why we call it transactional manufacturing, or unforecastable. We don't have to worry about the fact that you're not gonna need exactly 500 every month for the next 24 months. In traditional EMS, you have to worry about that, you plan for that. We don't worry about that, we don't care.
Yeah it's interesting as well it's neat model and I see it as a real enabler. So, congratulations to you guys. All right, let's dig in and give our listeners that are designers and engineers some tips around DFA. The way that you and I originally came to know each other is, I had been blogging and writing and then I came across a little publication you put out called Circuit Talk in which you were doing what I was doing, which was giving designers some really immediate tips to apply to make their jobs hopefully a little bit easier and so, I think you've done a really nice job of that. So can you talk about why you started Circuit Talk and then go ahead and share some of those tips or tricks that are around design for assembly that's gonna make designers’ jobs easier and smooth the time to deliver a good product in time to market.
Well thank you. You know the volume of jobs that we get - it does lead to chaos of sorts - but it also is a huge advantage in that we get to see every single mistake that anybody's gonna make. We don't specialize in a vertical industry so we don't only see mistakes related to a certain type of component tree. Name a component that's leading-edge, we've undoubtedly seen it and, so we see these things - and it's not just beginners, it's not just experienced designers, it's not just big or small or university - everybody makes the same mistakes. It's so complex and there are so many variables, so many new types of components. Geometries are shrinking and in parallel to that people have less and less time to design these things. Quite often layout isn't taught at schools, or it's self-taught. The experts who knew exactly how to make a layout work perfectly have retired now, or they've been let go, or things have changed so fast they can't keep up.
Mm-hmm.
So we see these problems every day. Case in point, one that I write about quite often relates to the QFN Quad Flat-Pack No Lead, and then the DFM. The DFM leads along one side. They have this big metal heat slug in the middle, looks like a very simple component, it's cool, it's small, has great signal characteristics. But most of the CAD software, when you try and use a QFN, the footprint is wrong. It comes from the library with the solder paste layer, not designed specifically for the component, so you've got to imagine flipping a QFN upside down. You've got a little row of contacts around the outside - very small - and then a big giant heat slug in the middle that covers almost the entire component. So most of the library components we found have a full aperture opening, so the solder paste layer is completely open for that heat slug in the middle. And what happens is you end up with too much solder in the middle, so the part floats up and the connects on the side don't connect.
Oh boy.
Yeah and this is even more prevalent with some of the open-source CAD software, or some of them with a lot of user-generated content, nobody told those folks how to make the footprint properly.
I see.
Quite often the manufacturers, in their data sheets, even specify it that way. But what you need to do is, to modify the footprint so in that center pad, you get somewhere between 50 and 75 percent paste coverage. So, you take out the default paste layer for the center pad and you put in a little windowpane-looking thing - problem solved.
Interesting. Yeah it's a little scary, unless you have a partner that's on the ball to what you can accidentally pick up off a data sheet or how to interpret that data right? So okay well, that's a good one.
Another one we run across these tiny little micro BGA's 0.4 mm pitch, some of them even 0.3 mm. I've actually seen a 0.24 mm pitch BGA. Yeah, some of the rules change with the bigger BGA's. You want non-solder mask defined pads, so you want the solder mask opening to be slightly larger than the little pad where the BGA ball’s gonna sit down.
Yeah.
With some of the 0.4 mm pitch BGAs, you want solder mask pad or defined pads, otherwise you get bridging.
Oh yeah, that makes sense.
Yeah, it kind of depends on the geometry of the solder ball, but that's a pretty common error as well. So you see these things that component manufacturers haven't fully studied, haven't fully published and they are just setting people up for problems.
Yeah, and what I have found - and not just in relation to components - I have talked to people who manufacture either components, or they manufacture laminates, and what's not widely understood is that sometimes the studies they’re doing is us.
Yeah we’re their guinea pigs.
Yeah, and then we yell and scream and we give them back data and then they produce overtime accurate data sheets. I was stunned to hear that, but it's absolutely true. They need to get stuff to market because the market is demanding it, and the testing is so complex and so widespread, and the applications are so widespread, that they can only go so far. And then the rest of the data has to come from real world.
Yeah the the hardware industry really is paralleling what the software industry did. We had open source software then open source hardware. With software, we started calling it ‘beta test the world’ because you couldn't beta test anymore, it's too complex.
Right, it’s too complex, so we become the beta testers and I don't think that's often understood. When I first understood it my jaw about dropped because I'm from the old school, like you are and it's like; wait nothing would ever go out that was not fully vetted or understood and tested, and things have just gotten so complex. And so there's just a hard limitation there, it's not a bad business practice or whatever, but it's a reality that I think is wise for designers and engineers to keep in mind - another encouragement to work closely with people like you, that can say, we've seen this already a bunch of times, we know what's going to occur here.
Yeah we've built our whole business around everything being wrong basically, start to finish. It sounds kinda funny, but It's all about this stuff probably isn't going to be right coming into us, so we've got to figure out how to make it work.
I don't know, like what happened to the world Duane? This is not how we started but here we are. Another thing you talked to me a little bit about, you had mentioned one time in a conversation, about polarity markings.
Oh yeah. That's that's maybe third or fourth in terms of the issues that we see here with diodes especially. Capacitors somewhat, but diodes even more so. Any kind of ambiguity, when you're dealing with machines, it's a problem. If you've got a barrier diode for example, it's backwards from what you would consider a conventional diode. So if someone marks it with a plus and it's a barrier diode and they're expecting us to know whether the plus goes to the anode or the cathode, we're gonna put it in the conventional manner, not knowing it's a barrier diode it's gonna be backwards so you can't use a plus to mark a diode. You might think minus, Also, does that mean negative or is that the lion on the diode symbol you can't do that because it doesn't tell us anything you've got to say K for cathode not C - because then we might think it's a capacitor, or the full diode symbol the down - lot of people will put in silkscreen, the mark that's on the bottom of a surface mount diode...
Uh-hu.
-which at first glance seems like it makes a lot of sense - but only if you give us the exact diode that you got the marker off of. I've seen two diodes 0.603s in the exact same package from the exact same manufacturer just a couple characters off, in the part number, and literally, on one the mark is the anode mark on the other it's the cathode mark. I've got to I've got to do a datasheet and I have a clipping from that data sheet on the Screaming Circuits blog that shows that it's got this part anode mark, this part cathode mark. I made the same mistake myself. On one of my boards I put the little marker on there and I gave gave the company the orientation and the CAD files, and then I made a substitution because one part was no longer available and used the other one - same thing but it was backwards because I went from cathode mark to anode mark. So, remove ambiguity. A few years ago I would say, it's okay to mimic the silkscreen - just give us the exact part. But with supply chain availability being such an issue right now, I would not rely on the mark that's underneath the diode because they can reverse if we have to substitute something.
Okay I'm gonna put a pause there and talk about what the heck is going on with supply chain. Stuff about diodes like these, very basic building blocks to design, why are we having problems sourcing parts?
Well we've been told a couple of things from suppliers. One is, they're telling us that the automotive companies are buying up literally an entire line. They'll come to a component manufacturer and say this particular part: I need all of your production, all of it and so there it goes out of stock. Internet-of-Things companies - the super, hyper-mobile devices are also causing issues because they're increasing the demand in the super small components. Well then the companies that make the parts don't have fab capacity to also make the larger ones so, some of the component manufacturers are telling us that they're going to stop making some of the bigger form factors 1206s 0805s even 0603s may become even more and more scarce because if they can make 0402 or 0201 to cover all that range they'll do it and not make the other form factors.
Holy... I don't know what to say about that - if I was a design engineer I'd be freaking out - this puts people in a really tough spot!
It really does and it's gonna change the way some things are designed. We have always had a policy that we will not substitute anything without explicit approval. Even looking at a bypass capacitor - 0.1 microfarad 16 volt bypass capacitor - in some cases you need exact parameters. There’s parameters you need to be exactly the same so you can't substitute. But there are also plenty of cases where it's just sort of by guess and by golly: yeah it's a 0.1, it could be 16 volt, 10 volt, 25 volt, 50 volt, whatever. If that's the case, people are gonna have to start being really flexible in terms of what they will accept for a component and maybe at some point the industry will have a flag on a bill of material that says: this one's engineered so it has to be exact. This one, just make it close.
Another thing, our industry is changing so fast, it's just a big reason why Altium and I've decided this podcast would be a good idea. Same reason why your Circuit Talk publication is a good idea because it's like we can't get the education out fast enough or get the news out. Like holy cow, why can't I get this capacitor? It's not a unique form factor specialized BGA they're capacitors! This is like bread and butter, so it's been puzzling to learn about that and I'm just really interested to see how these component manufacturers are going to deal with this and and again how designers are going to be forced to think hard about these parts it's really strange. Anyway sorry for taking a little side trip there.
That's important, it's a significant issue. We're being told this could last until 2020 and when we get out of this allocation, the industry is going to be different and, as I said, a lot of the bigger form factors consider moving all to 402s. It's more difficult to deal with these smaller ones but those are the ones, when the component manufacturers catch up, it's going to be in the smaller form factors because they can sell them to people building small devices as well as big. So think about that, be very, very careful when you're picking the specific component and tell us, and other manufacturers like us, what parameters are important.
Goodness that’s a great tip. You know I hadn't thought about it until just this minute when you were talking; I'm wondering if this will drive an uptick in embedded?
Embedded like embedded passives?
Uh-hu better passives.
I don't know I've been waiting to see that. I joined this company in 2005 and embedded passives were in the news at that point, and I actually made a prediction on the Screaming Circuits blog, that in ten years - I think I said - 80% of the passives would be embedded passives. I don't know that we've ever seen one. I guess technically you wouldn't see it because it's inside it.
No but you would know it was there, because I know it from my board manufacturing past, you would know cuz you would have to process it differently. It's a different process but I don't know what the cost trade-offs are there, but I've met Bruce Mahler from Omega and I've met some of those folks, and I'm just wondering if this allocation will drive, but I don't know what the cost trade-offs are or performance comparative. That makes me think, I need to call Bruce Mahler and get him on the blog because it's an interesting thing to ponder in lieu of what's going on in the marketplace.
Yeah.
Anything else you would mention off the top of your head that's something you see repeatedly that's a design for assembly thing that you would recommend designers to take a look at closely?
Well the polarity, the QFNs, BGAs as I mentioned. Something that isn't necessarily quite so obvious is the data files that is an important part of design for assembly. Ambiguity on a board is bad, ambiguity in a data file is bad. Bills of Materials, if there are parts in there that don't match the board, that's probably 80% of the jobs that come through here, have some sort of a Bill of Materials issue. So, double-check that that's accurate and that it matches your CAD files. If you can give your manufacturer the intelligent CAD files like an ODB++ or IPC 2581, that significantly reduces the chance of error, but then there's a little irony in there too that a lot of board houses still prefer Gerber's so we have seen cases where someone saves and then; oh yeah, I can give you the ODB++, but they forget they made a slight change and so now we have Gerber's that don't match the ODP++ so, make sure all of your files are consistent. Make sure the Bill of Material is clear and finalized. All in all if you add up all of the files issues that we see, that's probably one of the most common problems. I mean, I run into those problems for myself. I designed some boards and run up to the factory here, and I know how to do this, in theory I know how to do this, but I regularly make mistakes that my co-workers chide me for.
Well I think again, that leads to the complexity of the data that's available. The data sheets; whether they're right. I mean it is such a complex thing and it amazes me that we can even manufacture circuit boards and then put components on it and come out workable sometimes. Because it is such a complex process, I'm really glad that - actually I appreciate it - I don't understand all those steps but having worked for for both a really high end EMS that sold to tier one’s, very complex boards, and also having worked for a variety of board shops. I really appreciate the complexity in both those disciplines, and I think sometimes because a board shows up as a line item on a BOM that complexity sometimes can get lost on you. But yeah we're building things, even here Altium, into our own tool that helps, like an active BOM, things like that, that hopefully help. I think design tool manufacturers like us, I think we're doing a better job helping in that regard.
Right yeah, definitely!
Well the last couple items I wanted to talk to you about... well thank you for all that by the way, and again, we will share in the show notes your website. The Circuit Talking, I would recommend to anyone who is listening or watching - that you subscribe to Duane's blog or just Circuit Talk or whatever and we'll put all the links in because again, he's got his feet in the fire and runs up against these things as he said. Because they're putting through such a width of product. Like I used to work for an EMS, and like you said, it was a vertical. So we worked with military Tier one, and so the type of bores we saw was a niche, but you're seeing everything.
Yeah, literally I mean we worked on a camera board, the electronics of it, for National Geographic - it's a plexiglass globe, they drop it to the bottom of the ocean, it's got a chain on it and when the chain rusts through the camera bobs to the top and they pick it up again. We've got stuff being built for the 2020 Mars Rover so, literally down in the ocean up into space and and anything in between, we've built Ardium base stuff, real simple things, through holes; we built a board with five thousand placements. It's just all over the place and it's just absolutely the most fascinating place I've ever worked certainly, because of that.
Yeah I can see that and again, kudos for you - it's easier to do a quick podcast or write a blog post or produce a Circuit Talk that can go out to thousands of people and get that information out in that kind of global sense and be helpful right.
Yeah rather than tell one person at a time.
Exactly it's kind of a scalability of getting that knowledge out, so I really appreciate what you've done over the years. One thing I wanted to ask you about which it was a fun thing is about; I don't know six to eight months ago, I had the privilege to go with the Altium team for the first time, to a Maker Faire because we have Circuit Maker and Circuit Studio - Circuit Maker is free and and now we've bought a company called Upverter, which is also free, and in the cloud, and we also have Circuit Studio. So, we went there with those products and because of my position here as Director of Community Engagement, I hadn't had any exposure really to the Maker community, other than seeing stuff online, and I went and it was like drinking from a firehose. It was so much fun… goofiest things... it was so much fun. So, I'm walking the aisles, kind of collecting things to write about, or learn about, and I come across Duane Benson, wearing what looks like rap swag around his neck - it was like a clock you were wearing right, or something - he looks like a rapper and I'm used to thinking of him as this Duane Benson from Screaming Circuits and here you are, like fully immersed in the Maker space, and you had designed this device and had LEDs on it and I'm like: what are you doing here?
So tell me about how you've come to serve Makers. It doesn't seem like, from a profitability or a business model, that it would be a market that a company like Screaming Circuits would address. So how'd you get there Duane?
Well you could say that I'm a bit of a method actor, I mean I love... I've been designing small circuit boards for a very long time and writing the software for them for a very long time and one way of looking at it, is I'm a Hacker and a Maker who happens to be lucky enough to have a manufacturing facility. But more specifically, those Hackers and those Makers they are starting businesses.
Yes they are.
Many of those businesses become our customers whether they be crowdfunding or bootstrapping or getting investments, they are the future. The Maker community has a lot of students in it. It has a lot of weekday engineer weekend Hackers, it has a lot of people who aspire to start a new business and just such a wealth of creativity. And part of our mission I always like to look at, I'm just one person, we're just one company but if we can make our tiny little corner of the planet just a little bit better then we've been successful and all of those people who want to design electronics...
M-Hmm..
-We know what they don't know. I mean, we know what kind of problems they’re going to run across before they do, and so if we know what they don't know why don't we pass that off? And some of those people will have boards built with our competitors. Some of them will build them themselves, some of them will have us build them. Whatever, we're helping them understand this industry better. And we are helping them build better boards. That's what we really want to do. That's why we're at the Maker Faires ultimately. It does always have to lead back to more business for us, and it does. People see Screaming Circuits, they get the Circuit Talk and they read it, and it's Circuit Talk a Screaming Circuits publication so all of that winds its way back eventually, to helping the business here, and that's how we can afford to do it. But if we can help the business build and grow the business and help these budding designers - everybody wins.
This is why I love you, and love you guys. I just I love that philosophy, I love that approach. I try to live by an old Zig Ziglar thing and this reminds me of you and Screaming Circuits’ model that you just explained. Zig Ziglar used to say, you really can't have everything you want in life. If you just help enough other people get what they want.
Right.
So it's kind of knowing unconsciously that if you put good things out in the world, and you do the right thing, and you're ethical, and you have integrity, and you serve people, that good will come back to you and and you'll do okay. And I think that's a big key to your success actually, by kind of leading with service and and not ignoring the bottom line. We are in business to make money, we have to do that, or we're not in business anymore. So, I really appreciate that.
Well we're wrapping up now and I think you've listened to a couple of these podcasts now and so two questions for you. One are you a nerd or a geek?
[Laughter] I’m a Gunerd…
That's the best answer I've ever gotten yes you're a Gunerd.
Yeah, there was a time when those were really pejorative terms but I think nerds and geeks have taken it back and said, you know what, no we're not going to be ashamed of liking technology and loving it,we're proud of it. I mean, yeah so I’m a Gunerd.
Oh my gosh, I'm totally gonna steal that and use it somehow Duane, that will come back to haunt you later I promise.
[Laughter]
And the other question is, but I think I know what the answer is, if you've listened to podcasts. I always ask designers and electronics professionals in the end - this is ‘designers after hours’ - so because there is so much creativity involved a lot of people, like you said are Makers or Hackers, or they play a musical instruments or they're sculptors or whatever. So, what is your kind of guilty pleasure that you like to do after hours?
It would have to be photography. I chase animals around and take pictures of them, animals, landscapes, and then I have sort of a weird passion for old, decaying industrial sites as well. But photography would probably have to be my passion when I'm not playing with electronics.
That's so cool. Do you have a website where you share any of that or is it just mostly personal stuff and you keep your photos and share them with friends and family and whatnot?
It's mostly a personal thing I have had them on websites before but it's just my thing.
And and what do you mean about industrial sites?
Well, old decaying, industrial and rusty factories. There's a place here just north of Canby Oregon City and we've got a waterfall on the Willamette River and most people think of waterfalls as pristine, and nature and that's all wonderful, I love that. But this one: back in the 1800's they started building paper mills and they built a set of locks. It's the oldest - well till they just recently closed down - it was the oldest continuously operated locks west of the Mississippi. And so now, you overlook the river from a nice restaurant and you see this shut down, decaying, industrial plant and - well no it's not the beauty of the river - but I see a sort of beauty in the symmetry and in the the way people constructed these things. It's almost like an architectural dig, you can see things from a hundred years ago, from eighty years ago, from sixty years ago, and you can see the evolution of that, as this thing built up and then as they abandoned it, and there's just for some reason... I really enjoy that that sort of a view as well as the natural views as well.
They do have a really unique aesthetic and things have changed. It is kind of like a little time capsule and the rest is actually beautiful and sometimes the design itself is beautiful.
Yeah well thank you again, this has been fabulous and I'm sure we can talk more and more, but thank you so much for giving me so much of your time and sharing DFA tips and the story of Screaming Circuits, and we wish you continued success and we'll certainly share the website and Circuit Talk. And if there's anything else you'd like to share with us, give me a holler and I'll make sure we include those in the show notes.
Thank you very much, it's been a privilege to be on the show here, thank you.
Again this has been Judy Warner with Altium’s OnTrack Podcast and Duane Benson from Screaming Circuits. we look forward to seeing you next time until then always stay OnTrack.
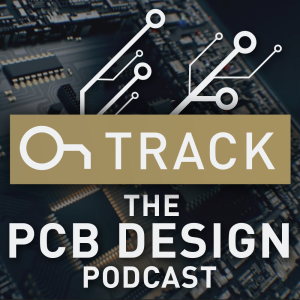
Tuesday May 22, 2018
Lee Ritchey and High Speed Digital Design
Tuesday May 22, 2018
Tuesday May 22, 2018
When Lee Ritchey “got through launching things to the moon” his career took off (in Silicon Valley...before it was Silicon Valley!) and he is now widely regarded as one of the premier authorities on high speed PCB and system design. He is the founder of Leading Edge and author of Right the First Time.
Show Highlights:
- Lee started as a microwave engineer who designed chips that went up on the Apollo
- ICs and “faking” logic
- High Speed design courses first offered at Berkeley.
- He wrote the books to make the students happy and provide the coursework that didn’t exist.
- High speed signal path losses - how do we control skew? Where does it come from?
- And what’s the answer? Spread glass.
Links and Resources:
Lee Ritchey on Linkedin
Lee Ritchey’s Presentation at AltiumLive 2017 in Munich
SI forum - an email forum that is a very good resource for SI questions.
- All one needs to do is send an email to: si-list-freelists.org
- Type subscribe in the subject line to become a member.
Disclaimer: We respect the unique perspectives of all of our OnTrack podcasts guests. Therefore, we choose to offer their uncensored opinions in favor of full transparency. However, all opinions expressed are exclusively those of our guests and do not reflect the views of Altium or our employees.
Hi everyone, this is Judy Warner. Welcome back to the OnTrack Podcast. If you would please subscribe, and let us know what you'd like to hear more about here on OnTrack.
Today, another amazing guest Lee Ritchey, who truly needs no introduction. But if you haven't met Lee before - Lee is considered to be one of the industry's premier authorities on high-speed PCB and system design. He's the founder and president of Speeding Edge - an engineering consulting and training company, some of you have read his book. He's author of 'Right the First Time' and he has a very illustrious, amazing background, and we also had the privilege of having Lee speak last year at AltiumLive in Munich, so I'm delighted to have this conversation with Lee. Not too long after Design Con, so I know he'll have some great wisdom to share.
So, before Lee and I get started, also please connect with me on LinkedIn or on Twitter @AltiumJudy and Altium is also on LinkedIn, Twitter, and Facebook. Lee I'm going to start with a very high-level question. First of all, welcome. It's good to see you again.
Thanks for the invite.
Always my pleasure.
So, you're known as the high speed authority in our industry, but how did you get there? How did you, out of all the paths you could have taken sort of in your technology field, how did you end up kind of going down this rabbit hole?
I started out as a microwave engineer on the Apollo program, which as you probably know, was a long, long time ago. And the company I went to work for was in Silicon Valley, when it was not yet Silicon Valley. Well, after we got through launching things to the moon, NASA decided, well we're done with that, and lots of us - like sixty thousand of us - had to go find something else to do.
Wow.
Well I was in Silicon Valley and integrated circuits were starting to be a big play and the big jobs were designing things with integrated circuits digitally. And so I interviewed for a job designing equipment for testing digital integrated circuits, and got the job. And said, oh now I’ve got to go learn something about logic. So I went to bookstores and got books and I faked it, and that's how I got got my start. And of course, since I was already in the microwave end of things, transmission lines were already part of that, and that was what you had to be good at if you wanted to use ECL, and the high speed computers back then were ECL.
That's how I switched from microwave to what everybody called digital, and for a long time digital was slow enough so you could pretend it was digital, but I never did and always designed on transmission lines and so, as the speed went up all around the industry, everybody needed to learn how to do something with this high speed stuff. And I had a design company from '82 to '92 where we designed pretty much all the early work for Sun, Silicon Graphics, Cray - people like that, and invariably I would get a new client and the engineers knew nothing about high-speed design. So I'd spend two days teaching them the basics so that we could design their board. Out of which grew the courses that I do now. Which I first began to offer at UC Berkeley, and the complaint after every course was: there's no book, there's no textbook, and that's where the books that you mentioned, came from as I had to write those to make the students happy at UC Berkeley. And in 1999, we decided that we didn't like working for companies so we started Speeding Edge.
Okay.
That's it, that's how I got here by - almost by accident.
Well I always say, most of us got here by accident. I mean some EEs take a nice, clean, straight path, but even they don't take that straight path., I know I didn't end up here on purpose either. But that's interesting, I didn't know that's how your book came to be. So the last time I saw you, you were actually speaking at DesignCon. And how often are you teaching these days actually ?
Most of my classes are private and I would guess about every two months or so.
Okay.
There are two-day, three, and day classes so, that's about as often as I want to do that. I don't know if you've lectured for 14 hours in a row, but it kind of wears out.
I don't think I know anything about anything enough to talk for 14 hours, maybe raising kids I don't know - like I don't think I know about anything to talk that long so now we - now we know for sure, you're way smarter than me.
Oh no, I just came from a different path that's all.
Well you and I were talking recently, preparing for this call and we sort of went down this path talking about PCI Express. So can you kind of talk a little bit about the evolution of speed and the extremely acute curve that we've taken in the last couple of years?
All right, well maybe let's start with PCI itself, which is the Bus architecture that is in - has been - in all the personal computers that you can buy, that's what PCI stands for: Personal Computer Interface, and it was a parallel Bus that you might have seven or eight plug-in cards, all on this Bus. That CPU could talk to any of those, any time, and then originally there was - it clocked at 33 megahertz, and it wasn't too long before the CPUs got faster than the Bus, and all of a sudden we were - what we call - IO-bound. We couldn't get any more performance out of a PC, because the Bus was too slow. So we upped the speed to 66 megahertz, and then a hundred, and for a lot of reasons they're too complicated for today, we couldn't go past 100 and that block limited how fast you could make a personal computer. And so we realized the architecture had to change. And the reason is that if the CPU can talk to any spot in the backplane at any time - to do that really fast, you have to have really, really short connections and that was not realistic. So we turned to an architecture that actually is old. The difference was signaling protocol, that is in PCI Express, has its origins way back with IBM. I was using it in '74, where we would connect two boxes to each other, where we couldn't do that with a parallel Bus, because the the noise in the background was too high. And so that's not a new technique adjust that early on, as you know, the guts of a computer is a parallel architecture meaning lots of bits switching in parallel, and the differential links that we're talking about here are serial.
So at each end, you had to go from a parallel Bus to a serial stream on the line, the other end - go back. And at that time, the serializers and deserializers were extremely complex and expensive. So the only reason you'd ever do that, is there were - if you were stuck, you couldn't do it any other way. Well as we'd gotten to where we have a billion transistors in an IC, these serializers and deserializers are what we call basically free. So all of a sudden it doesn't cost much to go from parallel to serial and back. And the advantage of that is, you can - you can drive... Well let me start from - in a parallel Bus were either series or parallel terminated - if you're lucky, you can drive that at 2 gigabits per second, that's very hard to do. With a serial Bus - we can drive them and we are right now driving them at 32 gigabits per second, which you could never do any other way, and this is how we're getting all the performance we need in the internet. Everyplace else is with these serial lengths and that's what PCI Express is. We switch from a parallel Bus to a serial Bus, to allow us to go faster.
Well, when you have serial links there, you can only have a driver and a CI receiver on the same net. So how is it the CPU's going to talk to six or seven devices like it was doing with the old parallel Bus? And the answer is, we have to have a switch chip somewhere so that we can switch between the CPU of whatever we want to talk to. Well early on, those were expensive chips, so we only use PCI Express in real high-end PCs like a gamer would buy. But we've now integrated those switch circuits right in the CPU so it's not an extra part to buy.
Oh okay.
So it's everywhere. So pretty much everywhere we've got PCI Express, well in itself it's not really all that big a deal because the early PCI Express was - well depends on your point of view - as fast as 500 megabits per second on the line and that's not special, to these terms. The rub is, we have started to go up the performance curve where we've got Gen 1, Gen 2, Gen 3, and so on. And Gen 3, which is it just about around the corner for everybody - it's 8 gigabit per second. That's not slow, and we start to see things that we could ignore at lower rates.
The one we're going to talk about today is not lost - it's the thing we called skew. Skew is the fact that the two sides of a differential pair don't arrive at the receiver at the same time - and some numbers on this, the most common until recently - most common data rate in switches and routers for the internet, was 10 gigabits per second. Where one bit is 100 picoseconds. And I did a test board in 2013 at DesignCon where we discovered 62 picoseconds of error in a path which is almost an entire data bit at 10 gigabits per second - which destroys the work. The link does not work and of course, we've got Gen 4 coming in at 16 gigabits and Gen 5 at 32 - where 32 of the bit period is only 30 picoseconds. So that error I just talked about, is two whole bits which means, nothing's gonna work right? So the question is, where does this skew come from?
So is that, Lee let me interrupt you for just a moment. Is that what you - the course a you taught this year at DesignCon, was that your focus?
Yes well the bootcamp, I call it 'Getting to 32 gigabits per second' which covers a number of things, skew being one of them.
Okay.
Of course the first worry almost everybody had, is loss. So we had this flurry of activity to make low loss materials and smooth Cochrane on and on like that. At the same time we were doing that, I see manufacturers figured out a way to improve their circuits so that loss is not a player anymore - not a big deal anymore. For example, the latest Vertex I guess their Vertex 8 or 9 from Xanax, at 28 gigabits per second, the Lincoln tolerates 38 GB of loss. Meaning that we start out with say a thousand millivolts and we wind up with four at the receiver, and it still works, so all the drive to have the world's best, lowest loss laminate is not a player anymore. Skew is, skew's killing everybody. All these laminates from people like Rogers and - you mentioned one earlier - I can't remember.
Taconic.
Taconic are simply not necessary - not necessary. At any rate, skew is just - and that was the theme of DesignCon this year. It is how do we control this bloody thing? So my impression - I guess that comes up next - is where's it come from?
Yeah, where does it come from Lee?
Well if the two sides were different to pair with different links, that would be, I think obviously, one way that can happen.
Right.
But pretty much everybody else had to design physical links to a few mills, so that tends not to be what the problem is. The problem is - and these are what we call micro defects or micro effects - the glass cloth in laminates you know, on average has a pitch between threads of about 16 mils - between 16 to 20 mils - Traces are 4 or 5 mils wide, so there's a huge difference between the width of a trace and the spacing of those glass fibers. Well, laminate is a mixture of glass and resin, and the dielectric constant of glass is on around 6 and the dielectric constant of resins is less than 3. That means that the lower the dielectric constant, the faster the signal is going to go.
That's right.
So if I had one side of a differential pair on the glass, and on the other one in between, there are two different speeds. That's where the problem comes from.
Now along those lines, I was just talking to Chris Hunrath from Insulectro, and he was talking about spread glass. What do you think?
That's what the answer is.
It is?
Okay cuz you know I've been here at Altium a little over a year and I guess I missed the spread glass thing, but I'm like, that actually sounds like it makes sense.
Well I and my colleagues have been the drivers of spread glass.
Really? Tell us about that.
Well so we found - I've got to confess - we found out by accident,
That's how all good inventions are found right?
Yes, and it had to do with - let me think about when that was - about 2005, we were trying to improve the uniform distribution of glass by using two plies of thin glass, hoping that they would sort of average out. And I had a fabricator in Oregon who says: you know, if you use a single ply of 33:13, you could save some money. So we built the test board and by chance that was really spread very nicely and so we had no skew problems. So all of a sudden, we thought we've solved all the world's problems by just using this glass. And then we built our test board from a different weaver.
So and this weaver spread the glass in one direction but not the other?
Yeah.
So, if you were to get that DesignCon paper you'd discover that we had really good skew one way.
One direction - - [laughter].
And so back to square one. Why aren't people spreading glass? So we got to digging around - and it was for laser drilling of blind vias.
Because, if you think about it, if you have like the classic 4 mil core was called 1080 glass. If you look at that, the glass bundles are round or not spread out, there are big voids between. Well so, if the guy drilling a laser drilled blind via wanted to get rid of the glass, he'd set the intensity to burn the glass and then go tear right through the backstop directly right, and so the laser drilling industry is the one responsible for spreading glass.
Like you said, complete accident.
It is, and they don't care about signal integrity, they care about laser drilling - so I and a guy named Scott 'Hindiga' of Cisco, started going to IPC's sessions on 'Standards for the Last Week' with the intention of getting some standards for how you spread the glass. Well it was got a whole lot like herding cats.
[laughter]
What an IPC committee being like herding cats? I don't know what you're talking about Lee [laughter]
Yeah, so around the table we had five or six weavers and they would not tell us how they wove their glass.
Because it was proprietary?
Yes, so he couldn't come up with the standard, and the only standard that the laser drilling people had was, you take the section of this cloth and they put it in the chamber and see how - put compressed air on one side and see how leaky it was. That's it - that's all there is today. If it was leaky, let's make it an X, and it was good. That would not be good enough for what we're doing here. So we are not done solving this problem, and there's about seven or eight different ways that people approach it. Now if you were at DesignCon this year, you'd discover two papers were presented by Cisco where, when they built the boards at five degrees to the weave, they got the best skew results. So that's how they're...
- Wow, yeah.
Can you imagine what that happens to you in a fab shop if you say pop this artwork on their at 5 degrees?
[Laughter]
-well I remember hearing about - from a colleague, he was an EE - they were actually at some point, because of the glass crossing and there being those bundles, they were actually starting to do it at - basically laying the prepreg at a diagonal. Do you follow what I'm saying?
Oh yes.
-do you remember that? That was kind of going on for a while to see if that would help, and I think it did help a little bit but again, the expense. There's so much loss of materials doing that, that it didn't make sense, or there was the trend of making that weave super, super tight so at least it was consistent, even if it was lossy. So, I feel like we've been going at this from a lot of angles - but hearing from Chris Hunrath, at Insulectro, it sounds like some people are really moving towards that spread glass and getting some good results.
Oh, that's my choice, but if you were to get the PCI Express Design Guide from Intel, they would tell you one of two things: you route all the signals at fifteen degrees through the X and Y-axis, or route them X and Y, and then you have the fabricator rotate the artwork 15 degrees on the panel.
Yeah.
That's in the standard for PCI Express.
I had no idea that was in the standard. I've heard about it, but that being - kind of anecdotally, but I didn't know it was actually written in the standard.
Yup it's in the standard from Intel, and you can - if you imagine a backplane where you have a regular array of pins for connectors and so forth - there is no way to route it at a 15 degree angle, because it's constrained by the pin array that's X and Y - so that's not a choice. So that leaves you with only the choice of popping the thing at an angle on the panel and then - you've been around enough to know the fab shop's gonna look at you like you have lost your mind.
Yeah.
Well we're not doing that, we're not doing that. We found some weaves that we know are well enough controlled that we're succeeding without that.
Okay good, that's good news. So this spread glass - so that's helping with the skew, you're saying, among other things?
It solves the problem.
It does?
Yeah.
That's amazing.
The rub is, you've got to be very careful who the weaver is.
Well can't you spec in a certain -
- What if I tell you that I had two weavers with the same stuff? That's the problem. When you say 33:13; there's no standard, that just means there's X in this direction Y in that direction, that's all that means.
Are there are prepreg providers that are - it sounds like there's prepreg providers that are doing it the way that you prefer. Or maybe other high speed...
There are, there are.
So do tell or can you tell?
Well the Doosan material I mentioned to you before we started this, is one of them.
Okay.
And a couple of Isola materials are okay but nothing else is.
That's a good hint, it's a good hint, look I mean I'm doing this podcast hoping to have a takeaway - so I don't just bring up all the problems and then say have a nice day thank you for sharing that. Right that's the goal like: yeah I found out what works, good luck! No.
So I have been seeing this word and this thing skews, so thanks for sharing that. One thing I could see as a potential problem - and tell me if I'm right or not - since that speed curve has risen so acutely, it seems like, the people who weren't previously doing high-speed design must be getting pulled into that space whether they want to go there or not right ? That - would that be a correct statement?
That's true yes.
When you and I were talking before this call about - let's talk about resources. About where these designers that are coming into this space I mean - speak just a moment about DesignCon, cuz I know you're pretty passionate about that show, and particularly giving out really good information?
DesignCon is the only conference I know where the level of information you need in this area exists. It's where everyone who has done research, or has studies and that sort of thing that are advancing the state of the art, that's where the papers get presented. It used to be - that was it. There were no tutorials, no education, that sort of thing. But over the last four or five years, we've added several things. This year we had three all-day boot camps on topics that matter to people who are trying to get on top of things. I did one title ‘Getting to 32 gigabits per second’ which dealt with all these topics. Intel did a three-hour on 'what is this PCI Express and what do you have to worry about' for people who have not seen it before and if it was five years ago, you might see there was nothing there for a board designer.
Now you would say it's the place you go for a board designer. There was a time when the PCB West was, but that has - I've been keeping track of that for a while - not offering the kinds of things you need for the these topics and I'm not sure why. I certainly have been talking to people who run it saying that you've got to offer tutorials, you used to do that. We used to offer stuff for engineers and they quit doing that because well, the guy who was running it was a board designer and he considered design an art, and their art dropped the stuff that appealed to engineering. Now, that stuff has to be learned by the designers.
It does, and as an old board designer person, I had to learn it from the board manufacturing side because I didn't realize - because I had left the industry for a while and come back, that things had sped up so much, that board designers all of a sudden weren't just dealing with: oh here's the specs, just adhere to the tolerances, do what the documentation says and have a nice day. There wasn't like now, high-speed board designers have to think about performance and all this wacky stuff. I mean the way we clean the board, the way we etch the board, the way we drill the board, everything can in a positive or negative way, affect the performance and it mortified me to think we got to a space where we could be completely IPC compliant and the board wouldn't perform as expected.
Yeah that's a good thing to observe and that is standards. By definition standards document the past by definition, and there are no standards group I can think of right now that has more behind the curve than IPC is, because they...
Why do you think that is? I have my suspicions, you're probably right actually, and you're more of an authority than me. But I'm just wondering why? What's caused that to happen?
Well who's driving it? Well, volunteers are driving it. Where do they come from? Well when IPC was at its prime, the standards committees were all staffed by engineers from aerospace companies.
Yeah true.
And the quality of the work was superb.
It's very true.
That's not true anymore - not true anymore, who goes to the IPC now? I don't, nothing there for me...
Why do you think the committee's aren't run by aerospace engineers anymore, or the Intels of the world, or Ciscos? Why why do you think it's not?
I wish I knew.
Yeah I really don't know either, I thought maybe you'd have some...
In the aerospace, that part of it, the aerospace contractors got out of the standards business and remember Jimmy Carter had a thing, The Commercial off-the-shelf Masters what... at any rate we're going.
Yeah - faster, cheaper...
Yes and the standards bodies that aerospace had, lost their money for example.
So they lost their funding to focus on that kind of thing.
I can see you probably heard of that. You know the last time it was updated? 1998.
[Laughter]
How outdated do you think that is?
And the update was to correct some spelling.
[laughter]
Oh my gosh, that's just plain sad, but they've come out with AS9100 and other things to replace it. I don't know the quality of those specs.
Well aerospace is on average about 15 years behind the industry now, it used to be the other way around.
Yeah, it's just really sad but I think that speaks to a lot of the way that politics have been run unfortunately, and the way things are getting funded.
Yes aerospace doesn't drive technology anymore.
Yeah, that's a crazy thing to think - to say out loud - I don't know, for you and I who have been around a little while. So, before we get too far off track, so DesignCon is definitely one place. Now because Design Con, if you pay to go to DesignCon, you can get all the proceedings. What can you do if you didn't go to DesignCon?
Well you can, for a hundred bucks, buy all the proceedings for a given year.
So someone could go on their website right now and for a hundred bucks buy...
All the papers that were presented this year correct.
That's amazing. Okay well that's a really good resource. Obviously your book which - because we were gonna talk - I went on your website and I noticed you're having some kind of fire sale on - I don't know if it's part one or something - but 'Right the First Time' - it looked like you were selling it and then it sounds like you now have a digital library of things you've published over the years?
That's true, and back on the topic of the books. We have two volumes and there was really gonna be one but - I don't know if you've written books or not - but you start out with great enthusiasm and this long list of topics. Then I had a deadline which was a Berkeley class, and I was only halfway through my list. And so I said: okay, this is volume one, next year we'll do volume two and what you probably don't know is, our books are printed in color. You have to have that in order to illustrate a lot of the things that matter. No technical publisher will publish in color, none of them.
Really, I didn't know about that I know it's expensive, but I didn't know that they wouldn't do it in color.
Yeah, so we were so focused, we formed our own publishing company and we went to a printer and said: we want to print this book. You see, there's a little secret about publishing.
Bonus material!
You have to give them a check for all the books before they turn the press on.
Oh boy that's expensive.
So for each of these two lines I wrote a check for $50,000.
Wow!
Crossed my fingers that someone would buy them, otherwise my garage would be full of books. Well, we sold out of volume 1 and volume 2 came along it sold faster than volume 1 did because it was a pull from volume 1. I am just debating, do I want to write another check for like $50,000 to get to print more volume one's, and the answer is no. So it became an eBook .
Oh ok.
So if you go on the website, when you buy you get them both, one's an e-book and the other is a hard copy.
Ok smart.
Then 200 books from now they'll both be eBook.
[laughter]
You got smarter.
My garage will be empty
[laughter].
I thought it essential that the books be in color.
That makes sense because some of those diagrams you can't distinguish between certain things without color being present.
No the color's for this industry. And so we are publishers and we sell our own books and people pay. I may be where I need to write volume through 3 and there needs to be a volume 3, to cover the things you and I just talked about. But I have told my friends - if I start talking about writing another book - their job is to slap me around until I get rid of the idea.
[laughter]
Well I'm not gonna slap you because this speed curve's going ahead now, we need to learn about skew and stuff. So - and who else Lee Ritchey, is gonna write that book?
I have actually written another book, working newsletters and articles that are on that - and someone should put them together but it's not me.
You know, we should get our friend Barry Matties to do that for you. Maybe he will.
You saw my distraction behind me which is the model railroad and that's more important.
Okay well I'm going to ask you about that, so I'm putting a hold on that subject, but let's cover a couple more quick things. One: you and I had an interesting conversation about circuit board manufacturers that are capable of doing good high-speed work and I made a comment and you corrected me right away because I said: well you know, board manufacturing hasn't changed that much in North America over ... blah, blah, blah. And you said, no that's not true. And I said except for places like TTM and you said which TTM?
Yes.
So tell me what you meant by that and fill our listeners in you know, of that conversation you and I had, cuz I thought it was very valuable actually.
Well when you say TTM, you're really talking about a dozen or so fab shops, which were acquired one by one. All have different capabilities for different markets, and if you're not careful and you get a bid from some - say TTM - they'll choose the fab shop that has the most capacity at the moment, which may not have the skills you need. And so I learned the hard way, you have to know what their capabilities are and when you give them the order, you say what plant is allowed to build the board.
And they'll accept that request and send it to the best location?
They won't get my business if they don't.
I am writing the check you will send it here.
Yes, yes and if you don't do that you won't get paid.
Yeah that totally makes sense. Well you and I talked about Stafford Springs which is a board shop, one of TTM's facilities I've always wanted to go through and it sounds like you've been through and that sounds like at least one of the locations that is capable of doing those high-speed designs?
That's right, and another one is in Hillsboro Oregon. It was originally called Merricks.
Oh yeah I remember Merricks.
Yeah and of course if I'm building small volumes it's my - my choice is a little place down in Orange called MEI.
It's not MEI anymore.
No it's got another name.
It's Summit Technologies which I agree they - I know Jerry Partita there - I hope to have him on this podcast actually because I think they've done a real good job there.
Yeah so you're sort of testing out something that we all say explicitly. If you're designing for this kind of space you need to be in direct conversation with the engineer at the fab shop, so that you don't make decisions that are not realistic. So I always have got that guy at the other end when I'm designing a new board.
I think that comes up again and again on this podcast by the way, people saying you have to talk to the key people at the board house which I totally agree with.
So let's talk about - I used to blog on Microwave Journal about what shops I thought - because I was working for Transline Technology, which is a really small board house in Orange County but they're quite good at RF and microwave. But I used to try, because I would see board houses say, sure yeah we do high-speed or the microwave because they've been built on say Rogers 4350 which processes much like FR4 -
- not really
- well not exactly but close. It's pretty stable but then they would take an order for something that was PTFE because they built some 4350, and then they'd fail and say, sorry we tried to build three times and we failed. And I kept seeing this happen over and over again. So I started writing about what I thought people should know, what they should look for in a good board manufacturer, i.e. what percentage of their work is high speed.
So let's stop for just a second and clarify what high speed means.
Okay.
Because RF & microwave is not high speed with respect to the digital world.
Yes that's true.
Actually RF and microwave were simple compared to digital boards. I consider them to be trivial.
Yeah but some of the stuff you do on those for microwave boards are funky and weird.
That's not because they need to be like that. That's because RF engineers say things that are goofy
[laughter]
It is true because again why I started blogging is because RF engineers were starting to lay out their own boards which was not a good model.
Yeah, remember I'm an RF Engineer, and so most of the stuff you see people asking for on those RF and microwave boards is goofy; it's not good engineering, pure and simple. At any rate, so when we're talking about high-speed I'm talking about, cuz this is far away the majority, of things that must be digital.
Yes high speed digital, yeah.
Yeah and the people who can do that are good at laminating high layer type boards, and very rare in our microwave or high layer board count - almost never.
- Yeah this is true.
It is two different animals.
So if a guy says I'm a high speed fabricator and I make RF microwave boards, that's a different capability than what I need.
Yes it's true. So let's just talk about high-speed digital so you're right, somebody who can do high layer counts what would you look for laundry-list wise?
Well at the top of the list, is boards like mine. If you're not making boards like mine, you're gonna lean on me, and I'm not ready for that.
Yeah good point.
Yeah it really is, that's my first thing, you're making boards with the same class that I want you to builm, if the answer is no I'm gonna go someplace else.
And I would say, and how much of their work is like your work because if it's a really small percentage that would make me nervous too.
Yeah but it's my experience that if somebody's making high count boards, that's about all they're making.
Yeah it's true, they kind of - they kind of aim at that. And they're good at it, they're busy.
Yeah and they're busy and that's what makes them profitable actually. So and that also you will see in the equipment set.
There you go, exactly - exactly.
You won't see archaic… you'll see the most modern tools that gives them the precision and...
Yeah exactly, a really good vacuum lamination guy can supply and will build a twenty four layer board with ten mill vias and 12:1 aspect ratios.
Yeah. And so you've gotta go find fabricators who are in your sweet spot.
Yeah I agree with that.
And so - and of course - if you're in it for a little while you figure out there's about six choices in the US.
Yeah there's - it's true - there's not a lot and as you're speaking those are coming to mind I won't sell for anybody today but they are relatively easy to find.
Now - and now just before we finish that - six years ago, there were none in Asia because they were busy making consumer electronics.
Yeah I'm interested in your perspective on that, because I don't really know what that is - if it wasn't kind of cookie cutter consumer. So what's the state of the ability in China these days?
We've got as good a capability in Korea and China as there is in the US.
I guess that's good news from a price point standpoint?
Yeah and it's bad news for the American laminators though.
I know I'm an American and I feel whatever but we gotta - - it is what it is.
Don't forget not so long ago we made TVs.
I know we made a lot of stuff.
It's the nature of the business that we go where the low-cost labor is.
Yes that's true.
Okay, now back to your trains. So always at the end of the podcast here, which we are beginning to wrap up here, and thank you so much for your time. I always learn a lot from you Lee. You are working on - this part of the podcast I call 'designers after hours' because my observation has been, a lot of people that I know that are pretty smart engineers and designers, have neat hobbies after hours. So tell us about your after-hours fun?
Well the one that you can see in the background - there's a lot of railroad.
Let's see it, can you flip your screen that way without disrupting us?
Oh there it is.
Can you see it?
Yip I sure can.
And the one you can't see is I repair vacuum tube radios.
You do what?
Old, radios vacuum tube radios.
No way.
Yeah.
Just for fun - who still uses vacuum tube radios?
Well we're starting to get Wi-Fi guys who think that vacuum tubes are the way to go. But I started out making my spending money as a kid, fixing the radios. I've always been in there you just may know...
I know.
-so I'm just back to fixing old radios.
That's kind of a fun hobby, but vacuum tubes - like that cracks me up.
Yeah you probably didn't know you can buy new vacuum tubes?
I didn't - I didn't but I was talking to someone recently and I - it cracked me up because I remember doing this as a kid so, is - remember going to like the drugstore - the hardware store and you could test the vacuum tubes?
Yeah, come on over I've got a tester.
No way - somebody mentioned that
- I was like whoa! Like my childhood came flooding back going with my dad to the store and sticking in the vacuum tube testers that's funny.
[laughter]
Yeah, good times - good times.
Well we're about out of time Lee, so thank you again for your time. And I know we could go further and further but I will share the link to your information about your books, and I will also share the link you shared with me for the design concept people that download white papers, and if you think of anything else just let me know and we'll put it on the show notes here. So we don't leave people feeling hopeless. We get them registered for DesignCon and get some papers in their hand, and get some books in their hands so they could do their job better.
One last thing we talked about I oughta mention, if you can - if you do those - what do you call the thing we did in Munich?
Oh AltiumLIve.
Oh yeah if you keep doing those I would argue you should start offering these training courses.
Okay, all right you heard it here from the mouth of Lee Ritchey.
I have to go show this to the CEO later - proof!
It's been my pleasure.
Thanks so much Lee. And we will talk to you soon again. This has been Judy Warner with the OnTrack podcast. Thank you for joining us and thank you Lee Ritchey, have a good day. Have a good day. Bye.
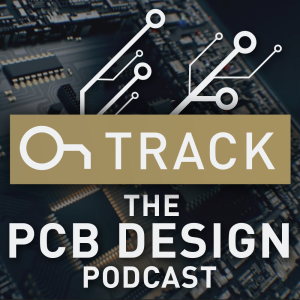
Tuesday May 15, 2018
Upverter and The Future of Browser-Based PCB Design
Tuesday May 15, 2018
Tuesday May 15, 2018
Making and checking parts is the most frustrating aspect of PCB design. Find out how Zak Homuth set out to change that and what is next for Upverter, EE Concierge and the future of PCB design in a browser-based setting.
Show Highlights:
- Why the Upverter parts library? Verified parts at scale, in a high-quality way.
- Verified parts - free to use for everybody coming soon!
- Verifying Datasheets, it’s a lot of work and at the heart of design frustrations.
- I wanted to take the magic of Github and Google Docs and create something for hardware designers.
- From concept to manufacturing in 20 hours.
- This is a conduit for bringing ideas to life.
Links and Resources:
Verified Parts on Upverter
A note about Verified Parts coming soon to Octopart
Indestructible pantyhose + Funny Video
Hey everybody, it's Judy Warner with Altium's OnTrack Podcast. Welcome back, we have
another amazing guest for you today but before we get started, please follow me on LinkedIn. I post a lot of things for engineers and PCB designers and I'd love to connect with you, and on Twitter I'm @AltiumJudy and Altium is also on Facebook, Twitter, and LinkedIn. So please
give us a follow.
Well today I have a really extra special treat for you.
Zak, I think I'm gonna destroy your last name so I can say Zak?
Yeah.
Your last name is?
Homuth.
Homuth - see I would have killed it. So, this is Zak Homuth, he is one of the - are you a co-founder of Upverter correct?
Yes.
So Altium acquired Upverter and EE Concierge in August of 2017. So a lot of people have asked me why Upverter, what was Altium's interest in Upverter, because it seems like sort
of out of our lane. So I thought I'd bring Zak in today and let you hear straight from the horse's mouth. So start out by - if you would Zak - just telling us about what is Upverter, and what is EE Concierge, and what you were trying to create when you launched that company?
Yeah sure, so Upverter is cloud-based, schematic capture and PCB layout. And what cloud-based means is, it runs in the web browser. You type Upverter.com into Google Chrome, it shows up and you can do your schematics, your layouts right there you know, order the
boards for manufacturing right from your web browser. You don't need to download anything, it's collaborative, which was kind of our big superpower for a really long time. Which is that a bunch of users can work on the same schematic, in the same layout, at the same time, in a very Google Docs kind of way. That's Upverter, and then EE Concierge came out of an experiment we ran back in 2015, trying to figure out what was the most frustrating part of doing a PCB design. And it turned out it was making and checking parts. And Upverter - until that point - had a shared global parts library and what that meant was every time I added a part, those parts were available for the community but without somebody checking those parts…
Yeah, that could be a nightmare.
-Yeah it was - it was really scary for people, they were spending a lot of time checking parts, they were spending a lot of time making their own copy of a part that was already in the library, a lot of that you know, wasted duplicates...
You can not have a messy library.
-Yeah and so EE Concierge grew out of that. It was our attempt to clean up and verify and guarantee the quality of the parts inside of Upverter, and so we built a small army of Electrical
Engineers all over the world. They work in an uber-like model where they can kind of log on, make a couple of parts, check a couple of parts, log off again. They can do it full-time, they can do it twenty hours a day, they can do it an hour a day you know, or an hour a week if that's what they want to do. And we built a machine intelligence to check all the work that they were doing to make sure that we had the best possible parts in the world inside the Upverter parts library and then, EE Concierge was born out of realizing that that's probably not specific to Upverter - probably every engineer has the problem.
Yeah there's that.
-so we built a plug-in for Altium Designer so that Altium users could leverage these verified parts which inevitably caught the eye of Altium and one thing led to another but - that you know that's EE Concierge. It was this idea of verified parts at scale, and then kind of outsourcing at scale, for electrical engineering. But in like a high quality way.
Right so, how many parts are in the library now?
Yeah so there's about a million-and-a-half parts...
Holy cow!
-in the Upverter library of those million and a half, about 275,000 are verified these days. And to
different levels of verified, some of them just have verified symbols, some have verified footprints. It depends on kind of what era of EE Concierge they were made in. But it but we've got about 25,000 like really, really rock-solid ones and they're the 25,000 that most people use.
That's awesome. So what's the plan kind of going forward, to get the rest of them? You said you have some kind of machine learning to help you verify that. Like what's the path going forward to get the rest or - you know million parts like you said - not everybody's using a million parts right? There's infrequent wonky ones in there?
Yeah there's kind of two answers to that. So how we make this maximally useful to the most engineers is similar to what Altium and Octopart did, after Octopart was acquired we worked really, really hard to make sure that Octopart was for everybody. It wasn't just you know
Octopart for Altium, it wasn't just parts for Altium, it was Octopart for everybody, or CAD, you know Mentor, everybody. So we're trying to do the same thing with the EE Concierge, we
want verified parts for everyone. So in the next couple weeks we're gonna launch verified parts on Octopart, so we're taking that 250,000 parts and we're putting them on Octopart free for everybody to use. And you can download them in EAGLE, Altium, Upverter. We're working on Mentor, I think we've got Cadence or CAD as part of that, so like in any format, free. Just find them, download them, use them. That's what we want so that's kind of one avenue for the EE Concierge. And then the other is - this is a little bit more kind of futurist and out there answer -
That's okay.
But if you were gonna build an AI that could read data sheets, first thing you would do is have a
huge number of people read data sheets and enter that information very reliably into a piece of software, so that you can check it all. And so the kind of like dot, dot, dot - is we think if we get good enough at doing EE Concierge, and we do it for long enough, potentially we can read data
sheets with a computer, kind of our self-driving car version of the Uber model.
Like and then part of me goes; and you're assuming the data sheets are correct?
Yes it's a real problem and so we had to do a lot of stuff at EE Concierge to catch like, if TI ships a datasheet, and the datasheet has a problem, they'll rev the datasheet and then they'll rev the datasheet, and then not only that, but they'll reuse packages and they'll reuse symbols and the reuse bits and pieces of that datasheet across other parts that they make. We had to build a ton of stuff to be able to catch when they made an update to one datasheet and apply those changes to all the other parts to use the same bits and pieces of the datasheet. It's an ongoing thing - it's a hard problem for us but yeah it's a real - it's a real issue.
Well it's like amazing to me that we're here like...
-at all [laughter]
I mean just from being in like - I started in the industry way back in the 80s - and like everything was done by hand and all that, so just that we could possibly even get to that point - it's just so sci-fi to me - but it's amazing, it's so great. So tell us a little bit about how did you get it, tell us about your personal history and how you went down the Upverter rabbit hole and popped up here.
Yeah sure yes, so I was kind of into software and computers before that was a cool thing I was on the internet pretty early, I was I think five or six when my dad brought home you know our first computer and you know I tore it apart and tried to figure all that kind of stuff out. I was building video games when I was seven, and...
-of course you were [laughter]
-all that but I studied Computer Engineering at the University of Waterloo in Canada and Computer Engineering is a little bit of Software Engineering, a little bit of Electrical Engineering, and then you know all the physics, and boring, normal engineering stuff that you have to do [laughter]
Waterloo is a co-op University and so every four months you'd go to school, and then every four months you'd go get a job, and so I got a bunch of these cool jobs, kind of all over the world, I used it as an excuse to travel. And so I worked in Canada's capital Ottawa, for the insurance company that insures the majority of Canadian doctors, and so they had some really interesting data. And I built a search engine and a database for them to to be able to search when wrong-side surgeries happen right, you know when they operate on the wrong lung or whatever. I built a search engine so that doctors could figure out the root cause of some of this error because that was important for the insurance company to try to prevent this from happening. So I did that, I worked in Germany for IBM, I worked in India for Infosys, and then I got a job in Waterloo working for a company called Sandvine and Sandvine build what are called deep packet inspection - telecommunications service. And so ISPs would install these in their network and it would sit between their subscribers - the people who use the Internet and the rest of the internet - and it would look at all the traffic that flowed through the box to try to figure out how much is Skype, and how much is YouTube, and how much is pornography and Facebook and everything else. Because if you think about it, ISPs are kind of like the water utility. They know that they sold so much water but they don't really know what the water was used for, how much is watering lawns right, and so we were giving ISPs that kind of intelligence. Anyways, I started off as a lab tech, I tore the boxes apart, tried to figure out why they weren't working, put them back together and made them work and I kind of worked my way up to actually designing the box. So I designed two of them for Sandvine before quitting, and I quit because I was really frustrated that on our side of the cubicle wall there were ten of us working on the hardware that was so essential for this company to exist - but on the other side of the wall there were 300 software guys who had Git, and they had version control, and they had collaborative tools, and they could test their code by pushing a button on their computer. I had to carry a 120 pound server around a building, and use screwdrivers and shit to like - and that's, that's part of hardware - I never wanted to take that away from hardware but it felt like it could be easier and you know. We were using Mentor Graphics’ tools and I was frustrated by the archaic kind of 80s feel of it all you know?
-yeah.
I used a Mac at home - I couldn't use the software on my own computer if I wanted to, and I was trying to build stuff at home and this was kind of before IoT was like a thing. This is right before Arduino, before all that stuff. But I wanted to do that stuff at home and it was just so hard to do any of that you know from my Mac, from home, without a huge budget - it's an endless amount of time and at the time we were seeing cloud tools like Gmail and Google Docs and Github, kind of emerging and so I left, because I was pretty frustrated that if this is like the state-of-the-art, if like one of the most complicated telecommunications servers that anybody had built today, was built by some punk kid in this office in Waterloo, working mostly alone, using tools that felt kind of clunky and out of date, like there has to be something better than there and and so we left to build it and it was really no more complicated than: can we take some of the magic of Github, and some of the magic of Google Docs, and build a tool like that for hardware engineers and maybe it takes forever to disrupt Mentor, or Cadence, or Altium, or any of the big guys that have been at this for decades. But we assumed there were enough people like us that just wanted to spend two hours on a Saturday afternoon designing a piece of hardware. There must be something we can build for them - a little bit like Google Docs right, it doesn't have all the features, you can't make fancy tables, you can't do it all, but it's slowly taking over the world and we wanted to do the same thing for hardware.
Well I think you point out something that I really noticed. It seems like there's a block of people that are like my age, the old 80s people and we've kinda just built upon old... and then there's the next generation that were five, okay I was 20 when I got my first computer, you guys kind of grew up with these things in your hands, and it I think it's kind of hardwired in your brain. So I think, there's more efficient, better ways to do things and we are building on old Legacy stuff, so sometimes we just can't see it. And so I think it's really very exciting because I think people are gonna be: oh thank god, somebody's built something modern you know, on the cloud that thinks, and operates you know, which I think was the big draw actually for Altium, which we can talk about that a little bit later so - so the Upverter I was going to ask you, but you've
answered it partially, is why Upverter? Out of the various other things you could do, why didn't you go into - I don't know - you have a very entrepreneurial spirit, so there's lots of things you could have done. Like why did you pick this one thing?
Yeah, so when we started Upverter, I quit my job before I knew what I was going to do. I knew I wanted to build something, I knew I wanted to start a company, I knew I was kind of done with working for the man, and I recruited two of my kind of college roommates. So these are guys that went to Waterloo with me. We lived in this terrible, decrepit, run-down house next to the campus, near the engineering buildings. You know we lived together, we worked together, we did our co-op jobs together we - you know we were thick as thieves. But I called them up and I said you know, how do you feel about quitting your job and like doing something new? And they both quit like the next day and so we got together in this old decrepit student townhouse and we wrote down hundred ideas of things that we were excited about, things that we were passionate about, things that we believed needed to be fixed. I was shouting loudly in the corner that we needed to build this - this hardware tool that was the Google Docs for hardware. That was my passion, that was what I was excited about. But Steve and Mike, they had some cool ideas of their own. There was a bunch of stuff that they wanted to build that a lot of it is actually been built, and a lot of it ended up being quite substantially large companies. So our second pick our kind of the front runners....
So what was on your cut list?
-Yeah so the second pick was, we wanted to build drones, and this was before drones were
cool. We wanted to build very large-scale drones that would be towed behind container ships and provide a bigger radar footprint than the ship can have itself because it's so close to the
water and you'd do this for a bunch of reasons. But the really burning reason at the time was Somalian pirates. If you could fly one of these drones above a container ship, you could get ten or a hundred times the radar footprints so you could really move the ship before anything bad happened. If you wanted to. Anyways, a company ended up doing this, and started right around the same time that we did and ended up being acquired for something on the order of two or three billion dollars and so we missed that one a little bit. But but we just - we just didn't even know where to start on it. But it was - it was the second pick.
That's crazy.
So we didn't really talk about this ahead of time, but you know I think I know around the time AltiumLive went down, there were people, kind of gurus in the industry, and they're like so -
ultimately it was in October, so and Altium acquired you guys in August and I remember some people, like it was like all the buzz, like what are you guys doing? Why that customer? And
so what I want to talk about is - who uses Upverter? I'm thinking makers, hackers, hobbyists and maybe EEs that want to be startups or do personal projects - like who do you think the Upverter audience is, and how's Upverter going to serve them, and how many people are on Upverter? Tell us about your ecosystem a little bit?
Yeah so it's the 'misfits' mostly, these are the guys...
The land of the misfit toys! I like these guys! It really is, these are the guys that are unserved by the eCad industry at large, they're using operating systems or tool sets, or computers that can't run traditional eCAD, they're in funny parts of the world, they're students, they don't have electrical engineering degrees. In lots of cases they're the weekend warriors that can't steal a copy of the eCad that they use at work and bring it home, they're makers and hobbyists and hackers yes, but they're also - you know we helped some Nigerian kids put their country's first satellite into orbit...
That's cool!
-and they couldn't have done it using traditional eCad tools.
That's cool I love that!
-Yeah we - some of the first augmented reality startups were built using Upverter. Like kind of odd stuff like that where you couldn't necessarily use a traditional eCAD tool, you couldn't necessarily iterate at the cycles that one of those tools would let you you iterate at. But also like children on the internet, and you know Mac users and all that kind of stuff where you just can't use a traditional eCAD tool.
Right.
But misfits mostly, we think of them as kind of an - not really the next generation of electrical engineers - but but very much a different breed, a different type of 'doer of electronics'. Well it is kind of grass roots though I think that we are gonna see more amazing things, like drones being dragged behind boats, that are gonna come up organically and kind of like you, I think you're the perfect sort of head of this brand, like 'yeah dropped out of school, this wasn't working, I don't like it whatever, so yeah I can see that happening over the next five, ten, twenty years. I think we're gonna see amazing stuff out of that space. So how many people, I don't know how you quantify that, have used Upverter, or use Upverter or actively log on a month?
Yeah-
So how do you do that?
At the time we were acquired by Altium, it was a little over 50,000 people used Upverter,
they use it in a very 'bursty' way, they'll show up - they'll work frantically for two days - ten days a month, and then they'll disappear and we won't see them for a long time ,and then they'll come back. And we correlate that with their kind of idea cycle right. They'll have an idea, looking very excited about the idea, they'll work on the idea, they'll do that thing, and then they'll go away you know, probably because they built the thing and they want to play with it. It could just be that their focus has moved and they're they're onto something new, and then we'll see them come back, six months a year you know, a couple of days later - depends on -how much time and energy they put into their ideas. But that's okay for us, like we we never aspired to be the daily tool like somebody like Altium is, like we aspired to be this conduit for people to bring their ideas to life and you can only be as useful as people have ideas right. So if you have an idea every day, we can be useful every day.
Most people don't - most people have inspiration quarterly, or a couple times a year and that's
that's what that looks like. We have many thousands of monthly active users so thousands and thousands of people log on every month, to work on their ideas, and their little projects. And the average project is worked on for quite a small amount of time, relative to you know, what you would expect from other eCAD tools. We'll see products going from conception to manufacturing in like 20 hours or less. And so that's pretty amazing, if you consider that's two or three days of work.
That's unbelievable, so if - you said something earlier that I wanted to ask you about and that was - you mentioned that people can go into manufacturing. Do you have sources like fabrication, assembly sources that are related to Upverter?
Yeah, and we've had this in a couple of different forms over the years. We've had, what we like to call the print button, kind of refactored a couple of times inside of Upverter. We're currently refactoring it again right now, and part of that is as a result of the acquisition. We have another
company we acquired, Siva, who does a lot of stuff in the manufacturing space, and we're refactoring our print button to use some of their technology and would be better linked up with Octopart, so it should be a better experience for our users as a result of doing it. But yeah,
over the years, we've had a button, you click it, you give us your credit card number, and a couple days later something shows up in the mail which, which is what you designed.
Awesome.
-And we'll do that again in the very near future.
And it - was that assembled also, or just the bare board?
-We used to just do bare boards, and then we experimented with assembly for a little while, the new - the newest, latest and greatest version - that we're working on right now will be fully assembled and it'll probably include whatever enclosure your device fits inside.
Oh my gosh, I mean I'm like ridiculously excited about this.
Yeah, it's gonna be pretty cool.
Okay so I always ask - I don't always ask this - but I wanna ask this now. Okay, are you a geek or a nerd?
I - - geek, but I don't know why. I don't know what the difference is really...
It's just your gut - open question.
Okay, geek.
-I think you're a geek cuz I don't think there's - I don't think - I think... whatever [laughter]
It's something we ponder here on the OnTrack Podcast. What is a nerd and what is a geek, we've...
-big questions [laughter]
We've decided what geeks are cooler; nerds seem more like, at least to me, physics - like...
-okay
-children 'Coopers'
-oh Science...
-yes more deep on the science side but this has not been proven, so if anyone wants to comment below and tell us what you think a geek and a nerd is, we're all ears. So but you were geeking out there, this is why I stopped you.
-Okay
-cuz I'm like, oh you are like totally geeking out and I'm tracking with you man, I'm like, oh this
is like - we're having a geeking out moment right now [laughter].
So I was talking to our Head of Operations the other day, and I was just saying that during that AltiumLive, people were asking why would Altium, a professional e-tool, pick up Upverter,
and basically I think Altium has a vision to kind of embrace every level of PCB designer and also embrace and serve those 'misfits', those marginalized, or that don't have access you know, those that can pay for Altium Designer and they do it professionally, well great...
-Yes
But that we want to serve the wider community. So I was asking Ted Pawela about it, and he was saying - and I just wanted to get you to chime in here - is that sort of what we were
talking about earlier - is that cloud - I mean a lot of software programs are going to cloud-based.
You know there used to be security issues, but they've tightened those up - so technology is
moving towards cloud based, and if we don't sort of pay attention and go that way too, I think will be sort of left behind and that, also the next generation, or the new, or the upcoming, or the
grassroots, organically-grown innovators, I think are gonna - like you - are going to be cloud natives right, and are going to be frustrated, like you were when you were at Waterloo. And to
also meet those people where they are, not expect them to cough up the money or fit into our model, but figure out where they're going, and what their model is, and what their needs are. And so that was - that's what I think Altium saw as very attractive - seeing Upverter as a huge enabler to serve that community. Would you agree with those?
Yeah - so when we were in the kind of acquisition process with Altium, I spent a lot of time on the phone with Arum, our CEO, talking about kind of his vision for the future of Altium, and his vision for the future of electronics, and one of the things we talked a lot about was making
Altium synonymous with PCB design. And part of that is, you can't just serve the tradespeople in the mainstream - there's a million people in their basements that have ideas, that want to invent stuff, and those things include electronics. You need to be there if you're gonna be synonymous with PCB design and so - so a big part of it was that. But then also a big part of it is like, the world's changing knowledge work's moving to the cloud, is becoming collaborative you know. The Windows operating system may or may not be the operating system of the future. You look
at mobile, you look at tablets, you look at what's happening with Apple, and you know all of that. They're you know, there's a version of the world where Altium is constrained to only serving a chunk of a market because of the way we built our technology, and so I don't know, Arum obviously hasn't said any of this, but there might be a little bit of this that it is an edge on
the future.
Well I can tell you that personally, it's a really exciting place to be, because I love that. I love
that you know, I interact a lot with University students and that. But we've also gone to you know, I went to the New York City Maker Faire and to see what people are developing is so
exciting. So to be able to serve that community, and see what they come up with, is just a blast. Like I love to see it, and especially like you had a start early with IoT like it's gonna explode what we can make. And like I said, they're gonna be making it in their garage, in their basement, or their shed...
-It has to - it has to explode. Like we're talking about you know billions of devices all over the world...
-billions like capital B.
-yeah like a hundred or two hundred thousand professional electrical engineers aren't gonna invent billions of devices; we need to include a bigger chunk of the world, in the design
of these things and you know, and then
- that's not to say the tradespeople won't have their place, like of course they will - but we need grassroots, we need people building stuff in their basement. And we need it at a scale that we've never needed it at, more than now.
I know, I'm really excited about what you're doing - I'm really excited what you guys developed, and I'm so excited that that you're part of our team. So sort of wrapping up here, I want to sort of segue into what I call 'designers after hours.'
Okay.
So, I don't think you have any after hours, you might get to have a beer after work once in a while. This guy's from Toronto and he's here an awful lot and I don't think you have any after hours right now, but if you did have after hours Zak, what would you do, or what do you like to do?
Yeah well my wife and I bought a house in the Canadian wilderness about 18 months ago, and so my after hours, for the last 18 months, has been turning this kind of run-down cabin into a home for my family and so I've been watching a lot of YouTube videos, and buying a lot of power tools, and trying to figure out how to do all that stuff. But when I'm - when I'm here in
San Diego, and when I'm stuck here for the weekend, [whispers] I buy a couple videogames [Judy laughs] that's - that's kind of my thing.
Okay, and here's another super fun thing about Zak. I want you to share about - his wife is also an entrepreneur. So tell us about your wife's business cuz that's really fun.
Yeah so my wife is a very successful entrepreneur, she started a company when she was quite young, that did eCommerce, and she sold that. And then she ran another company which was for angel investors, and she sold that. And then she did something with hair extensions, and
her new thing is called Sheerly Genius, and Sheerly Genius makes indestructible pantyhose.
And you can hang a human being from stuff with nothing more than a pair of pantyhose.
There is a video, we are going to share the link of Zak, hanging his wife... [Zak laughs]
from a second-floor balcony with pantyhose - it is a real thing.
It is a is real thing.
Okay, so what are the materials?
Yeah so it's heavy molecular weight polyethylene, which is what the fiber is made out of, and it's special in that it's incredibly strong, but also a low denier - or denir - I'm not sure how you're supposed to say that word - but so it's a 30 denier fiber which is what you can make hosiery products out of, but it's incredibly strong. It's like the the strongest dental floss you could
possibly imagine, and she found a way to weave this into pantyhose but also to like wrap lycra in it so that it's stretchy - but it's still sheer, but it's like incredibly and ridiculously strong, so it will never run.
-It's like 'superhero pantyhose' you guys really you're gonna have fun watching this video that we'll connect below, and we will also connect to Upverter, and EE Concierge and Zak's LinkedIn profile, if you'd like to connect with him, and any other things that we think that..
-Sounds good [laughter]
-you might want to connect to. So Zak, thanks again.
Thank you.
-I'm so looking forward to working with you and seeing what we kind of collaborate with and
sort of reach - reach to the grassroots-end of the design community.
-Me too .
I'm really excited about it so thank you so much for joining us.
Of course thanks for having me.
This has been Zak Homuth, is that close enough?
-Yeah.
Zak Homuth and Judy Warner with Upverter and Altium, and EE Concierge. And we will
look forward to seeing you next time.
Until then, always stay on track.
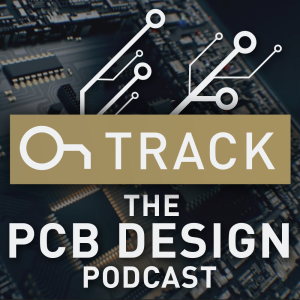
Tuesday May 08, 2018
David Carmody’s DFM Report Integrating Design and Assembly
Tuesday May 08, 2018
Tuesday May 08, 2018
Do you know your fabricator? Meet David Carmody, Division Manager and CID+ at San Diego PCB Design. As a service bureau, San Diego PCB works on a variety of PCB design projects. Learn why David says, “You gotta know who you’re fabbing with” and how he is using DFM Reports to help customers integrate design and assembly in this episode of The OnTrack Podcast.
Show Highlights:
- Memorable designs in telecom space and the development board for Dragon II, a SpaceX project, for the capsule they hope to take to Mars
- Package on packages, dropping the DDR - removing the burden on the designer
- Palomar advisory program - student programs for learning PCB design
- San Diego PCB acquired by Milwaukee Electronics, EMS and Engineering Services
- DFM report - a “stoplight report” for customers before starting build - customers love it and it fixes issues proactively especially with packaging
- A lot of engineers don’t know the manufacturing side and DFM reports can help with this
- “You gotta know who you’re fabbing with”
- Will additive manufacturing processes be the answer? The business model remains to be seen.
- 3D printing - you can’t print copper (yet)
- Altium User Groups - have Altium in the title but we don’t run them! We’d love to support.
- Altium User Group in San Diego is very active and supportive.
- Advice from a Pro: Always keep learning, it will keep you fresh and make work more fun.
- PCB design isn’t the only practice David has mastered - he’s a martial artist too
Links and Resources:
David Carmody on Linkedin
San Diego Altium Users Group Website
Tecate, NM Manufacturing Facility
Hi everyone this is Judy Warner with Altium’s OnTrack podcast - welcome back. Once again I have another incredible guest to speak with us today, but before we get started please follow me and connect with me on LinkedIn. I try to share a lot of things relative to engineering and PCB design and on Twitter I'm @AltiumJudy and Altium is on Facebook, Twitter, and LinkedIn, and if you'd please subscribe and give us some comments so we know what you'd like to hear more about that would be great.
So today again we have a great guest which is David Carmody of San Diego PCB David has a new title now: he is the division manager and he also has a CID. So David, welcome and thank you for joining me here at Altium today. So, we've known each other for a little while and I've had the benefit of being over at San Diego PCB and looking over your shoulder to some pretty wild complicated designs. So tell us a little bit about your day-to-day from the perspective of design bureaus and the kind of work that you see?
Okay, we do get a lot of different designs, a bunch of varied designs, so we see a lot of military application, we see a lot of new technology - wearable technologies and things like that as well; it is pretty much all over the map though. I mean we get a little bit of anything and everything just because of the the nature of the service entity. A lot of the more upscale - so to speak -designs are the real nanotechnology sort of stuff where we're cramming a ton of the little parts into a board that's less than a half square inch total in size, or we're packing everything into a big housing that has to get heat out somehow because, I mean, we're sending up high output micro processors into into space and there is no airflow so we need to get the heat out in other ways. So there's a lot of that sort of stuff that we do get to see and and play with and and learn from as well.
I think San Diego is kind of a neat place to work too because there is a lot of Defense here and there's also call comments and telecoms, and even in our local area, although I'm sure you see work from all over the country? We do we also have kind of some neat things right here in our own backyard.
Oh yeah.
So across that variety what would you say some of your more memorable designs would be?
I was gonna say we do have have some telecom stuff that's gone on and those are those are fun boards just because they've got big processors on them and lots of high-speed lines, things like that. Most memorable, for me personally, would probably be a SpaceX design. I was able to design the development board for the Dragon 2.
Oh my gosh!we’re not worthy! Do you mean the dragon heavy that they just launched - the second Falcon that ever went?
Yeah the the Dragon 2 which is the capsule that they hope to take to Mars one day.
Oh so that that one!
Yeah. I did the development board for that so it's just basically a big processor board with a lot of RF communications on it and things like that and they're breaking out all the other boards from that, and that was a fun project. I got to be a part of that was really cool.
Yes, I sold some R4s to them and got to go through that facility a few times so I'm like a weirdo SpaceX geek and then we also sponsor the hyperloop pod teams for universities. So Ben that's helping us here with recording this; he and I got to go up and hang out at SpaceX and see them do that.
I saw some of those pictures.
So sorry for being so weird but I’m a kinda SpaceX geek.
Yes, it’s been fun. We do have a couple of space contracts we've worked directly with NASA and MIT and also with Space Micro so, we've definitely learned our way around the Class 3A specifications and we know that inside and out.
Not easy, really dense stuff. So you talked a little bit about the nanotechnology, is that where you sort of see the bleeding edge going? What are the the most challenging designs?
I was gonna say the packaging is actually changing quite a bit, we're seeing some things that the packaging is doing that's well, quite frankly, I'm not terribly happy with because it takes away some of our place - but things like package-on packages is coming around. That's really cool technology, I mean, you put down the DSP or the PGA - whatever it happens to be - and then you can drop the DDR right on top of it. There's nothing for us to do; it's purely an assembly process, if that.
Wow.
So that stuff is definitely interesting and removing a burden, so to speak, on the designer but yeah, then the package size itself is just getting smaller and smaller. We're being pushed into HDI technology more and more often. 0.3 millimeter BGAs are pretty common, 0.4s are all over the place now. I mean even big ones. So the 0.3 three millimeter BGA's are getting common. I've been able to work on things as small as 0.15 millimeter though. So it was a flip chip sort of design where we're pushing the envelope on that thing so it was experimental, and things like that. I don't think they actually ever built it was costly, that whole get up then but that's that the trend we're seeing. Just everyone's pushing the package design more and more all the time.
Something I noticed I took a peek at, even though I've known you for a while - I took a peek at your LinkedIn profile. I don't know that I'd ever done that and I like to ask people a lot, how'd you get into this industry? Because most of us didn't start out this way, but we ended up here. So did you start out there? I notice you took courses at Palomar College which is local here, and I don't know if they still do, but they used to have PCB design courses?
That they do I'm actually on the Palomar Advisory Committee right now and we're helping to restructure some of that stuff and try to join up a little bit more, their student base through there. They've got a pretty good offering right now to make it better but yeah it's still active and it's it's one of the few places that you can really go for formal education. So it's good that they're there keeping it alive, and not just keeping it alive but updating it.
Right, and that's kind of where you started out was it not?
It was.
Or did you just join them recently as part of the Advisory Committee, or did you start learning design there?
I did technically start learning some design there but it was an accident really.
[Laughter] See, my point is, we didn't do this on purpose.
No absolutely not. Basically I had gone through their program and really gravitated - back then at least - 3d was just emerging. It was all in AutoCAD, there was no such thing as SolidWorks, it was just coming around. So I ended up jumping into AutoCAD 3d mechanical sort of stuff and and did my degree on that and then got on to nothing but waiting list after waiting list. So at that point I was talking to a guy that I was working with, he goes: call my brother in law, he does something in computers. And I talked to this guy, he was a PCB designer at Intel - I'm actually working with him now, we recently hired him, but yeah he's working out in our Arizona office but he gave me some excellent time; never actually met him face to face at the time but he gave me some phone time and told me what to look for, and what this industry had to offer and gave me a couple of places to go after. And I went after both - I ended up getting an offer from both of them, but I liked the smaller business so I took that side of things and spent 12 years back at an ‘unnamed company’ as the Design Manager.
Laughter, well not as awesome as Sandy Opie…
Well I don't know, it hasn't been a year yet, so San Diego PCB was acquired actually by Milwaukee Electronics right.
Yes it’s been about a year and four months now, time flies. So Milwaukee is a really capable EMS shop up in- remind me?
It's Milwaukee.
Oh is it Milwaukee!
Yes, their primary branch is in Milwaukee - okay this confuses everyone - because we have multiple brands out there now. So our Milwaukee electronics brand has most of our engineering services and the EMS as well there. Up in Canby, Portland Oregon, now that's where we have Screaming Circuits - that is our quick term prototype house and there is also EMS there as well. Most people don't know that but the factory shares the floor for that and then we also have - actually it's also called Milwaukee Electronics - despite that, it's in Tecate Mexico but they've got a huge building down there and they're there literally clawing the mountain out from being behind this building.
Right I've seen photos of it, it's really quite lovely, at least the photos are, it looks really modern.
It's a very impressive facility. I was able to visit there and I had seen pictures of it when the shop floor was was only 50% filled; that place is full and like I said they're calling out the mountain now behind them, so that they can add on and I think gain about 30% more square footage. Growing like crazy.
How has that been, that acquisition, for your customers and for you, there's obviously synergy there between the two firms so how has that been for you?
The two companies, the acquisition itself was great, Milwaukee Electronics is a fantastic company to work for. I really enjoy all the people that are there. The synergy has taken some time to get things rolling, but I'm starting to see a little bit of a snowball effect and so we're starting to pick up some momentum to where Screaming Circuits is sending us customers back and we're sending them customers in and we're starting to get a collaborative database of the customers going right now, so that we can take a more active role on that and and really sell to both sides. There's been a little bit of crossover, but like I said, it took probably six months before I saw even the first crossover and right then another one happened, and then another one, but now we're up to where we're getting about at least one customer a week or something like that, that's doing some sort of crossover. so it's definitely building up speed. But it's still going to take a little bit more time.
So since our listeners and watchers here will are mostly engineers and PCB designers, what do you think the benefit is to collaborating design to EMS - what are the benefits you think that occur there?
When you're collaborating, one of the biggest things that's coming out right now, is basically DFM report that we've been doing, it's something that I've been doing for years. Say a customer has their own design team, they want me to be a second set of eyes - something like that. I'll go through the design either on a cursory level if you just want me to look at DFM/DFA sort of issues. Do you want me to look at your circuits, do you want me to look at this whole thing - make sure that you placed it correctly? I coined that a ‘stoplight report’ a long time ago, and basically it's just - we give a nice little green note if it's informative only: this looks good it was done right, give a yellow note if, hey you might want to look into this, you might have some potential issues or, hey this part’s hanging off the board edge you're gonna knock it off, this needs a correction before it goes out - and those are obviously the red items - so customers seem to love that. I mean it's really easy, real clear-cut. They can kind of skim through it, hit the items that they want and that is really building up some speed right now with with a few customers because they've had an internal source for a long time. They've been using Screaming Circuits forever, but Screaming Circuits is going: okay you're going into bigger yields, you need to fix these sorts of items - let's fix them ahead of time and that's what we're being utilized to do.
That sounds absolutely incredible especially now, because in the marketplace so many engineers are laying out their own boards. They may or may not have time or access to spend a lot of time with their fabricators our assembler, so I think to have that sort of oversight would be very welcome. I don't know if that's what's driving it or just having a second set of eyes what do you think?
Probably a bit of both, I mean the engineers obviously get EMI and and EM theory, they do that really well, so they they always lay out the board well for that. But they aren't necessarily the best packagers, most PCB designers are puzzlers so, we do the packaging portion real well that's what we like to play with. But if you’re a good PCB designer you're going to know the EM side and you're also going to know the manufacturing side. A lot of the engineers don't know that, so they don't really look at that. I mean, I've been given boards that were completely routed and they said: rip out all the routing because this guy did it with 6mm vias with a 12mm pad on an 80mm thick board and so, it's just wrong all the way around. And placement wasn't bad on that…
But the aspect ratio is the killer.
-and he used decent trace widths, but I mean, the most problematic piece of the board, and he killed it.
And like it's a good thing that companies like Altium and other EDA companies make such powerful, great software - but there's no place in the software that says: no, stop dummy, you can run DRCs or whatever, but it won't necessarily flag it for for DFM if your aspect ratio is off or whatever, unless you've turned those settings on or off I can imagine right?
Yes but you can still improperly program DRCs too, you can say: hey I want 1mm holes on this board…
I've heard you and Mike Creeden say that a design tool is only as good as the designer.
-yeah you absolutely need that and I mean, someday in the future would it be great to see the tools incorporate that sort of stuff? Yes, but at the same time you’ve got to know how your fab works too…
And you don't want to limit yourself either because you could potentially create self-limiting things that are really irritating...
-oh yeah.
So I think we're gonna just keep giving you powerful tools and you guys have to work it out.
Yeah I mean, we can just zoom up and zoom up and, hey that via looks plenty big enough to me, I could put my fist through it, but not in reality. The packaging thing that I was referring to earlier that is just starting to drive this industry just because of big 0.4 millimeter pitch BGA. I'm working with a fabricator that can't quite do the the latest and greatest and all of a sudden that pattern starts to become a challenge that’s almost impossible to break out.
Right yeah I don't know where this train’s going…
Yup I don't know - it will stop somewhere at some point…
I know, I know, except it seems like we just keep creating some breakthrough so I'm keeping my eye on things like additive manufacturing, whatever we could do it 1mm, controlled trace and pull it off but there's no clear front-runner.
Yeah, the additive processes are very interesting, haven't seen anyone really start pulling off a business model out of it. The 3d printing technologies is also very interesting but you can't print copper unfortunately, so they can't - yet at least - so there's some major hurdles there too that they have to go through.
It'll be interesting. Well I wanted to shift gears a little bit because you, along with your colleague Randy Clemens here in San Diego, run a really solid Altium user group here and for those listeners that don't know this, Altium User Groups, they have our name in the title but we don't run them - they're completely run by the users, for the users they're very democratic and we just lend support and it's something that we've been talking a lot about here, is that we would like to grow the user community and help people launch groups. So can you give us a little bit of background and give us the do's and don'ts maybe, if people that are thinking about starting a local users group from what things have worked, when things maybe haven't worked, and how do we get more people to launch user groups?
Just sign up - just for a little background on that - there was a user group that was here for quite a while that was run by Bill Brooks and it had some traction, it was running for quite a while and then either the community or whatever, started to kind of drop off a little bit. Randy and I saw that as a bad thing basically, and we talked to Altium, talked to a few people here, and then put together a general terms for the the group. Randy has always done Google boards, the blog and stuff, so he's very good at that, he's got a pretty major Altium tutorial board actually that's out there. So he took some of that and ported it over and turned it into a San Diego Altium User Group Board, you can just google that: San Diego Altium User Group and you'll find his board. If you sign up you'll get meeting invites so it's really that easy. All of our IP, as it were, is all up there and and I mean fully freely distributable so anyone can go ahead and take that as a template and start porting it over. Randy would probably help if anyone asked to set up or clone a board but Altim is really great on this thing, they're really helping us out, they help promote it you guys are actually doing lunches for us and all of that, so we really, really appreciate all that support. Lunch is a good way to get people out - just feed them and they will come.
Exactly, you feed them and they show up. So we were restarting the group, it had a little bit of a slow start and it's kind of typical. I think we had all of three people show up once plus the the huge group of Altium group and San Diego PCB group because we host the location but no I mean our last last attendance was in the 30s somewhere, so it's it's doing real well now.
What do you think the benefits are to the users that participate regularly?
One of the big things is we always bring Chris Carlson out for new updates and stuff so we can see things as they're coming out. He gave us a wonderful tutorial on 18 not long ago, really to help us all dive into it as as the interphase changed.
I thought Randy was gonna eat us alive - he came out he's like yeah bring him - he had a slide deck going, and ‘what about this?’ God bless Chris Carlson, our senior FAE, he addressed most of those things and just said, no Randy we just moved it over here, it's just over there and we tackle most of it. But what I really appreciate is that Chris actually took four things back to our R&D team, and I think that kind of real-time feedback, it helps us make better tools right? And if we make better tools we sell more software, it's not rocket science right?
Right and we're happier designers…
Right your’e happier and you’re productive and so I think it's a win-win and I think Altium is doing a good job culturally. So say you were in... I don't know... New Hampshire okay, and you knew there was a pretty good-sized design community what would you say the first steps would be to get something going?
First of all, probably to clone that board that we've already got…
And we will share this, by the way, in the show notes and we'll share that if you want to go take a look at it, because Randy has done a good job of kind of making a charter, it would be a good model to share.
-so it's a fairly basic charter but yeah, clone that board, start marketing it against that, call Altium…
Me, call me I will help you.
-so get them to put it out in a newsletter and a blog or something along those lines so you can start that foot traffic and then invite your buddies, invite your friends and get them to do the same.
I interrupted you there, so you said that Chris came out and you got to see the latest and greatest, Chris did a good thing on showing you AD18 - what other kind of benefits do you think the users see over time?
I mean we've already kind of hit on the the dynamic feedback and that's obviously great information, but just the user-to-user help is always nice too. I mean I've had people come in with a laptop and and open it up and go, look I'm struggling over here, what the heck do I need to do? What rule do I need to write to make this thing work right? And we can just basically rub shoulders and get things moving and get a workaround if it needs it just to move it along.
Well I've been really impressed since I've been down here for about a year now and just seeing the group it's just very active and it seems like a really healthy thing and yeah all I get to do, is use my card and buy you guys lunch and if you want a speaker we’ll send one, if you don't want one we won't interfere so I think that user-to-user and that you guys really get to own it, is sort of a powerful model because it's not like we're going to come down and spring a free sales pitch...
Yeah well, Altium doesn't go in they're not salesy.
Yeah but we try actually, not to do it.
No, it's been fantastic for that.
Well I wanted to bring this up because you and Randy spoke at AltiumLive and Randy took a little part of his time speaking to talk about the Altium user groups and I was so surprised! I'm like, well you can spend your time talking about that if you want Randy, but I didn't think there would be that much interest - but I happened to pop in the back door just to see how it was going and people were really engaged and then people came and talked to me after. I think there's kind of a hunger to do it. I'm just wondering... I just wanted you to share with our listeners, if people did want to do it they would see, oh here's some steps to take because I don't know, though, that maybe we've done a really good job of advertising it because we do want to stay out of it, we want to contribute but not inserting ourselves into an organic user’s group. So, thanks for sharing that part.
Hm-mm yeah, for the AltiumLive, Lawrence Romine asked Randy to do a little bit of a spiel on that and yeah, there were a lot of people from LA that sounded like they were going to be starting their own, or a couple of them, depending on the demographics or Geographics up there and then there were quite a few out of state as well that that sounded like they wanted to start one.
I went to one in Utah, which I guess has been going on for a while. So, I got connected with someone actually at AltiumLive and we ended up connecting and there was like 80 people there to see Ben Jordan talk about AD18, I'm like okay, Wow! 80 - it was huge, but I think that group has been very active and been around for a long time so it wasn't like a new thing and they actually come from Salt Lake and south of there, so it was almost like two combined groups. So anyways, thank you for sharing about that. Any final thoughts?
Nothing that I can think of right off the top of my head.
Well thank you so much for coming in today…
-Thank you
You’re a good sport and we really appreciate you in San Diego PCB and thank you for sharing. Oh one thing I wanted to ask you was because the upper-end (age-wise) is starting to kind of age out in the industry and we're getting new ones coming in, what is one - since you're sort of a veteran designer - what is say, one or two pieces of advice that you would give to a young designer?
The number one thing I would say is, never stop learning. I mean I got into a rut at one point where I wasn't learning I couldn't stand up on the the current trends, things like that, and that job got to be a drag, it really did because it's - overall - we did the same thing over and over all the time. It's very repetitive, but if you're standing up on the latest trends you always have something else to reach at and something else to go after. Always have the latest way to solve something too, so it just makes the job overall a breeze; makes it a lot easier to do day-to-day and keeps it fun and interesting.
Very good. Okay, last question: I said that was the last one but I like my very last, last question - I call this part of the podcast designers after hours okay - so there's people like you and I know in common, like Bill Brooks who started the Alts Music Group. There's the sculptor, I just spoke to Chris Hunrath earlier today, who's a scuba diver. So what do you like to do after hours?
Honestly Mike my side is a little sore right now because I did some martial arts last night so that's one of my little best-kept secrets, so to speak, been doing that for a long time done Tan Sido, got a third-degree black belt there, and then migrated over to Kung Fu and have a black sash.
Well, remind me to never make you mad! You’re so soft spoken and could kick my butt.
[Laughter]
Pat's the one that always bounces that around the office but he's honestly the only one I’d ever damage too…
[Laughter]
That's cool. See, another interesting after hour designer. Well David, thanks again and I know we'll see you soon again.
This has been Judy Warner and David Carmody of San Diego PCB. Thank you for joining us today we'll make sure to share our links below and please visit us again next time.
Until then, remember to always stay on track.
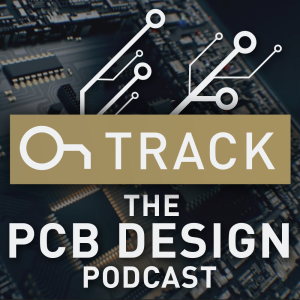
Tuesday Apr 17, 2018
SKA Africa Telescope and Multiboard PCB design
Tuesday Apr 17, 2018
Tuesday Apr 17, 2018
Omer Mahgoub, Electrical Engineer for the Square Kilometre Array (SKA) Africa talks about the project and shares how he got started in the field of PCB Design. Join Omer and Judy Warner for a conversation on Multi-board PCB design in the context of extremely sensitive devices.
Show Highlights:
- The goal of the Square Kilometre Array is to be the largest radio telescope in operation.
- Bigger and more sensitive
- Project scope - built in South Africa and Australia
- Meercat is 64 / 25% of project - Phase 1
- Next phase - Australia 158 low frequency range antennas
- Multitudes of BGA Fanouts, tight pitches, narrow tracks, etc.
- Extremely sensitive device, signal integrity is crucial
- One aspect of project is to develop local economy, so we are working with local manufacturers to improve manufacturing technology. There is a lot of giving back involved in this project.
Links and Resources:
Omer's comedic AltiumLive presentation recording
Omer’s AltiumLive presentation slides
Hi this is Judy Warner. I'm so excited to introduce you to another AltiumLive 17 Alumni speaker which is Omer Mahgoub from SKA in South Africa and he has been designing really complex boards for the SKA - which is the Square Kilometre Array - telescope and I'm gonna get out of the way and let Omer tell you a little bit about the SKA if it's something you don't know about.
So, Omer welcome and thank you so much for taking the time to tell us a little bit about your work.
Hi Judy thanks for having me, it's a pleasure to be here thank you to the SKA - which stands for the Square Kilometre Array. She SKA is a radio telescope project that's currently being built in South Africa and Australia and its goal is to be the world's largest radio telescope upon completion. I'm not sure if the listeners are familiar with what a radio telescope is but essentially, as opposed to an optical telescope, which is what most people are used to, and you look through to see the Stars and the planets. The sky a radio telescope receives radio signals. So in essence it's a large satellite receiving radio signals.
Okay. So tell us the purpose of the data you're collecting in those large receivers - what type of data they're receiving and what the purpose is?
Okay. So there are different purposes for radio telescopes. One of the main reasons is to observe the galaxy and to understand how the galaxy was formed and to understand how galaxies evolve today. Also, how they rotate and also their location, what has shaped them, and so on. Also to track new galaxies that are forming and to just map that journey. There are other purposes for example to study the earth’s magnetic fields that help guide birds and bees and compass needles and also to study interstellar gases. Another reason which most people might be interested in, is also to detect other types of life out there. Not necessarily aliens, but any any objects which might be occurring in distant planets.
Mm-hmm fascinating.
So, all the big questions of life.
That’s exactly it and which is why a lot of questions have not been answered so far by existing telescopes which is why we need to go bigger and more sensitive.
So tell us a little bit about the scope of this project. I know it's massive - and what parts of the SKA are up already and when is the due date that they feel this will be completed?
Okay so, initially when this project was started it was going to be a big process between different countries for the hosting of the telescope itself. Of the location of the telescope and so initially, the three countries that were supposed to get to be hosts were Argentina, South Africa, and Australia. South Africa and Australia, their bid went ahead and it was between the two of them and it was eventually decided that both South Africa and Australia would host this. So the actual location of the telescope will be in both South Africa and in Australia. There are a number of member countries involved in this project since it's an international consortium of countries such as Brazil, France, Japan, Malta, South Korea, Poland, Portugal, Russia, and Spain. African countries as well as Botswana, Ghana, Kenya, Madagascar, Mauritius Mozambique, Namibia and Zambia. So one source in South Africa who were bidding - they had to build, what they call pathfinders or cursor telescopes - to prove that they were capable of this. So the significant project at the time was called Meerkat which is what we are currently busy with here in South Africa and by March or April of this year that should consist of at least 64 receivers or telescopes. And then this will essentially be phase one of SKA.
Ok so Meerkat is those 64 telescopes?
Yes.
Okay with 64 telescopes making up phase 1, which towards the end should have at least 200 dishes.
So 64 is quite a quite a bit of the project really? I mean it's what - yes over 25 percent of the total project?
Yes.
Yes so, that’s for phase 1. Just to explain a bit further between the two phases. For phase 1 there will be the 200 issues including 64 Meerkat dishes but in Australia it will be 150 000 antennas for a low frequency range. So the frequency range for meerkat is between 350 to 14 gigahertz and then the low frequency antennas in Australia will be between 50 megahertz and 350 megahertz that's a lot of power.
I can imagine the boards that you make - right away my mind goes to the boards and is that just antennas? The antenna portions of the board I mean, this is kind of a novice question but how do you achieve that kind of power?
So just to explain a bit further on where I'm based with the team in South Africa. We work on what is called the digital back-end and what the back-end is responsible for is that it basically is to receive the incoming radio signals from the dish which are analog signals and essentially digitizes so you can imagine our boards are mostly to digitize these signals and just perform the processing in them.
Okay understood, very good. Going onto - so since you're doing it would it be fair to say that what you're doing there in South Africa and just sort of a little bit of the heavy lifting of this project then?
Yes you could say that.
Yeah, so tell us a little bit about specific challenges of designing these boards. I know before we got on the phone you were talking specifically about BGA fan outs. Can you talk about that and and what kind of size BGA's that you typically work with and then how you address the fan outs for those?
For those we deal with a lot of FPGA processing boards and a very high density board. Very high density BGA is starting from around 600 all the way to over thousand volts. Very, very narrow pitches of less than a millimeter point six, and six millimeters so it becomes very challenging to fan out and route all the signals in between which is why I was really glad to see all the advances on Altium 18 during the summit last year which would have made our work tremendously easier and thinner.
Yes.
But we will definitely be using those and so that's one of our biggest challenges - definitely to fan out signals and the multitudes of high-speed signals that we have running on these boards.
Have you have you had the opportunity yet to transition to Altium Designer 18?
Uhm, not yet because we're still creating our existing designs on the existing version of Altium but for which every new design that we’ll be moving onto we will definitely be on Altium 18.
Okay those are really tight pitches and I don't know how you guys do that honestly! It boggles my mind that's incredible! So talk a little bit more about the high-speed signalling and what kind of challenges that poses for you and and how you address them?
So some of the biggest challenges of this telescope is that it's an extremely sensitive device so signal integrity is crucial for our boards. And one of the main issues we have especially in South Africa, is manufacturing capability because the electronics industry is not very big here. So having to send out a board with such narrow tracks and with these kind of technicalities - a lot of our local manufacturers are unable to actually manufacture them - so it becomes really tricky because another aspect of the project is also to help develop the local economy. So we've been working very closely with some local manufacturers to help them get the equipment and expertise to be able to manufacture these kind of boards.
Yes, so tell me a little bit more about that. As one from the bare board industry and where I was focused on actually high-speed boards for a long time, that's really fascinating to me because these boards are not easily made and there's not that many in the whole wide world actually that can build consistently and reliably in that sort of phase you're talking about. So how do you go about and and where's the funding and how does that all work?
So, for example, some of our latest boards had buried vias buried and blind vias, and the manufacturers here do not have the equipment to be able to manufacture or to be able to make those. Some of them who can were able to get some government grants to buy some new equipment specifically for this project. So we were very happy to have that. Even the etching process for these narrow tracks is also quite complicated as opposed to your regular levels.
Mm-hmm.
Though as they are getting up to speed some of our initial board that we needed unfortunately had to be manufactured in China because we needed the quantities. But for the boards for which we were still prototyping we were able to successfully manufacture those here in South Africa and we were quite pleased with the results.
Oh that's wonderful! I love to hear that you're able to help through the SKA, help grow the economy and bring some technology there, that's very exciting.
Yes that that was one of the critical aspects of the SKA because the location of the SKA is also good, because you need a very radio quiet zone with no cell phone interference and that sort of thing. So it's actually based in the middle of the desert and that's also how the location has helped to uplift the community because now, you know, schools get to benefit from that a lot of extra jobs are created as well so there there is a lot of giving back involved with this project.
I love that, oh that's really great news - and you know, sometimes people say, well why go to space? Why build things like SKA?
Yes a lot of people always tell me, why is so much money being spent on this, when it can be spent on housing or help to fight poverty, without realizing that this does actually help people to uplift themselves.
I couldn't have said it better because what you realize is, when you do start doing some of these things, not only is the data that you will collect helpful and us really understanding the universe and probably have practical applications. It does really help fuel communities and put people to work and grow your seed community. So I think that's a really lovely backstory.
I think there's been thousands of scholarships already for people to get into science and engineering from this project.
Tell me a little bit more about that?
So a lot of times people, for example from the town, where the telescope is based, a lot of student’s studies are being paid for and all of them are being sponsored to attend University especially in the STEM fields. Because once this budget is complete we are going to need a lot of astronomers and engineers to work on this telescope because this is a very long-term project. I mean it's only expected to be completed around 2024 so, by that time we would need to develop the skills for people to use this and to maintain it.
That's incredible. So speaking of students how in the world does Omer Mahgoub from South Africa end up working on the SKA? You know, based in a remote area. Tell us a little bit about you and how you came to the field that you are?
All right so I studied electronic engineering, at the University of Pretoria which is about 1,500 kilometres from here, from Cape Town, and I was previously working in the electronic defense industry - about four or five years - and then I think at some point my CV was online and I wasn’t actively looking for a job, but my CV just happened to be online and I was contacted for this. And since this was in a different town, I wasn't really considering moving at the time, but I just decided to go for the interview anyway and once I got it, I started to seriously consider it and I saw what a great opportunity it would be, and I decided to accept. And it's been six years now.
That's a great story. So Omar do you remember being a kid and kind of naturally being drawn to how things worked and how did you know to choose that major?
So, I was always interested in gadgets and was something that I enjoyed. I enjoyed gadgets - but I feel like my parents actually fooled me into studying engineering because as a kid, I used to love the TV show MacGyver and I would always ask my parents, like you know, what do you see? What did he do? And they would tell me, no he's an engineer that's what his job is, and ever since then I had wanted to study engineering and it was only later on that I realized that they had actually lied to me.
God bless parents.
Yeah.
But I'm glad that they did.
Yeah well, you obviously wouldn't have lasted long if you didn't have sort of a propensity for it. So they must have heard something right? I knew a fellow, Omar, that told me once he was an electrical engineer and he was part of the early development of chips and that actually, just the 256 K chip, you know, way back in the olden days and he was from a small town in the Midwest and he saw some men climbing telephone poles and he asked his parents, what does that guy do? And they said he's an engineer so he's like, that's what I'm gonna do, I'll be an engineer. Because he wanted to climb telephone poles. Then he got to college and he's like, you people are never gonna let me climb my telephone pole are you? But then he ended up being quite a genius guy developing chips.
So hopefully he’ll get to climbing.
His son went to Princeton, I think there was some brains in that family by the way. So yeah, I don't know that he ever got to climb a telephone pole! So, well can you share some websites cause I'm sure there are some incredible photos. I know I've seen some let's share the websites where people can go both to your local website and to the the international website.
So our local website, SKA Africa is at www.SKA.co.za and the International site is https://www.skatelescope.org.
Very good. So I always ask people at the end of this podcast is that you're now shifting to what I call ‘designers after hours’ so I think there's a lot of artistry and creativity in designers like you. So what kind of interesting hobbies or things do you do in your spare time?
In my spare time I - well naturally I enjoy video games - I love playing video games and I'd like to consider myself to be a sporty person. I love playing tennis and soccer. I try to play at least three to four times a week. The thing is that I try to stay active you know, especially after sitting in an office all day, staring at your computer screen.
Yeah that totally makes sense. What would you say; would you say you were a geek or a nerd?
I would say neither, but perhaps more of a nerd.
Well you're more of a nerd, well probably with the stuff you're working on?
I'm not gonna argue with that one.
Well it's been a delight to speak with you Omer. Is there anything else you'd like to share that we haven't covered perhaps?
No not really, but I just want to say that I'm really excited about getting to use Altium 18. I'm so envious after having seen all the videos. I've actually installed it and played it on repeat but I'm looking forward to using it and seeing how easy it will make my future designs.
Well we're excited for you to use it also and we hope that you'll have the opportunity to come back to AltiumLive 18. We will make sure to post Omer’s presentation below where he spoke and had some incredible slides. And not only that, he was like a stand-up comedian and I stepped into his session and I was trying hard not to laugh really loud because they were filming. But he’s been the straight man during this call but he was really funny. Like tell the audience why the United States is not part of SKA?
That was not supposed to have been - I still don't know how I didn't remove that!
I love it, no tell us...
So the United States they're even they they're not part of the SKA is because they would have insisted that it be called the Point Three Eight Six Square Mile Ratio.
It's too wordy.
Yeah SKA, it's way easier.
Yeah well, we will definitely post your your presentation below, both the video and your slide deck because there are some beautiful photos in your slide deck that show some radio telescopes and some sites that are really inspiring. And the scope; it boggles the mind, so we will be sure to share that.
So Omer, thank you again so much for sharing your experience with us and we hope to talk to you soon. Especially after you've gotten onto Altium Designer 18 and give us some feedback so we can make it better.
Definitely will do, I'll try to find some bugs.
Okay it's on!
Thank you Judy.
Thank you so much, this has been Judy Warner with the OnTrack podcast. Thank you for joining us and we look forward to seeing you next time and until then always remember to stay OnTrack.
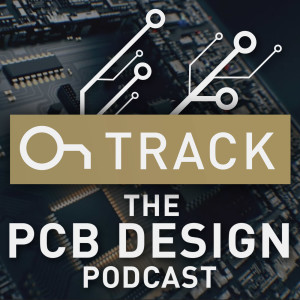
Tuesday Apr 03, 2018
Model Copper Roughness Properly, a Discussion with Bert Simonovich
Tuesday Apr 03, 2018
Tuesday Apr 03, 2018
Bert Simonovich is founder of Lamsim Enterprises and an expert in innovative signal integrity and backplane solutions. He holds two patents and author of several publications. Anyone involved with the design and fabrication of high-speed circuit cards and backplanes or people who needs to estimate PCB transmission lines losses will find value in the paper Bert shared at DesignCon 2018, “A Causal Conductor Roughness Model and Its Effect on Transmission Line Characteristics”.
Listen in to Join Judy Warner and Bert discuss copper roughness and the paper he presented at DesignCon 2018.
Copper roughness is located between the laminate and the copper
- From a manufacturing perspective, the rougher the copper the better
- But for high speed, the rougher the copper the higher the loss
- If you don’t model it correctly you cannot simulate it accurately
- The Huray model dilemma - where do you get the parameters to use for the model?
- Last year’s paper was about correcting the dielectric constant due to roughness
- New model is dubbed the Cannonball-Huray model
- The effort is collaborative, building on each others’ research i.e. Rogers, Polar
- As speed goes up, material properties are more important i.e. Fiber weave effect
- Accurate modeling is very important especially with new standards and tighter margins
Links and Resources:
Bert’s Articles on Signal Integrity Journal
Hi everyone this is Judy with the OnTrack podcast welcome back. If you are new to our podcast make sure to subscribe on your favorite RSS feed you can follow me on LinkedIn please.
Please. I love having friends on LinkedIn or at Twitter I'm @AltiumJudy and as far as Altium goes you can follow us on LinkedIn Twitter or Facebook.
So today I am at Design Con 2018 at the Santa Clara Convention Center and I'm delighted to have my dear friend Bert Simonovich who hails from Canada and so we're gonna chat with Bert today about the paper he submitted and all the things he's involved in. I also want to share with you about our fun history in Hobart and how we got to know each other. So Bert, welcome to our podcast and we only get to see each other maybe once or twice a year but I'm always so happy to see you.
Likewise, likewise Judy.
I'm glad you showed up this year and I'm glad I could get you. Last year I couldn't get you because you were so busy with your papers and everything; you were desperate, you were booked to the gunnels last year so I'm glad we got to run into each other.
So, to give you a little bit of background about Bert... well let me start from when Bert and I met. So what was it 2006 six or 2010?
Yeah 2010, something like that.
Yeah, so Bert was sort of in a transition period in his career and we met on LinkedIn and then we actually met at the show at Design Con and we connected through social media and we're old enough you know, and respectable enough in our careers that we didn't feel like that was creepy or anything. So we connected and we met upstairs; the top of the escalators here at Design Con, and we got acquainted and just networked and boy oh boy we didn't know the number of ways that our past would continue to cross over the years so, we hit it off immediately and Burt knew an awful lot about backplane and tell me again, you worked for a huge company up in Canada?
Okay so yeah we live in Ottawa area and I started my career at Bell Northern Research which was the research and development arm of Northern Telecom or eventually North Dell in Bell Canada.
There you go,
so it's essentially the same as like the AT&T; down here - researching, development and then that later got to fold it into the Nortel umbrella and I was there my entire career. It was 32 years until 2009 when they filed for bankruptcy and then my career ended…
Abruptly.
And that was kind of a shock. Then I was fortunate that I was able to you know - we weren't in bad shape financially - so it didn't hit us like it hit others. So I've considered myself fortunate, but what I missed was the day-to-day and and not knowing what the future was because at that time there was the downturn economy so it's hard for everybody and certainly harder for older ones and we were able to get out and fortunately got our pensions early and that kind of kept us going.
Yeah so that's right about the time I met you, not long after that right, and so you're like: mmm what am I gonna do now? I have all this knowledge and expertise how am I gonna apply it and so on your own dime you flew down here. We met and I was hoping that we were just networking to see how we could help one another professionally and whatnot, since that time - boy oh boy.
IMS came up from the UK to Montreal and we met again there.
That's right we met again there. We met at IMS so then, all of a sudden, our lives started weaving because I was in the RF and microwave space from the bare board side, and then I was doing the guest blogging for Microwave Journal and then you got to know all the folks - or you knew those folks in that space and then you got to know the Microwave Journal folks who have since launched the Signal Integrity Journal and now you're on that editorial review or review board for that magazine?
That's right.
And now, I think you just told me, this is your first year now that you're in the Technical Review Committee?
Technical Program Committee Yeah.
Right for Design Con so you actually reviewed the papers then that were being subpoenaed by some papers?
Yes.
Did they divvy them up?
Yes they basically divvy it up so there's quite a few reviewers for it to get the diversity and not just one person, several people review the same paper as well.
Right good. So, not only is he reviewing papers he's also submitting papers. So I want to say congratulations that you are a finalist for best paper.
Oh thanks Judy.
Well I don't know that’s third time in a row now?
Actually five.
Five! You've been nominated that many times or you've submitted, but you've been nominated that many times. I see, so you are like a rockstar! So, tell us about the paper that you submitted this year.
Okay. This paper is actually a follow-up from last year's paper that I presented and last year after I presented it, there was a great discussion afterwards. It was the end of the day and people - there were no more papers after - and people that were interested stayed and we had a good little wrap of things and were discussing some of my results. And although I was close there was some doubt as to actually what it was, why there was still differences and my co-author Vladimir he had an idea that it's possibly due to causality of the metal.
Okay.
And Vladimir works for a mentor and so he had this idea and I had data and my technique and we decided to collaborate and see how well it would work. So he incorporated his algorithms into the tool and we checked it out and that brought the data exactly right on.
Wow! So this paper is kind of a wrap or closing the loop at the end of last year's paper basically?
That's correct, it's kind of a follow-up in a way and it kind of answers the question that we were suspecting. - the people who were discussing as a group were suspecting - so that was very satisfying when I had that. So we said, well we've got to publish this now so we'll do that.
So it was a copper roughness issue?
Well it's part of modeling called copper roughness, to model copper roughness properly and get the right model afterwards so you can do the simulations.
Isn’t that hard? I mean it seems like copper roughness, which is the roughness - for anyone that's not clear on this of our listeners - copper roughness is between the laminate and the copper. Not on the topside of them it's on the bottom side where it's being bonded to the laminate but it's not always the same?
No the thing is with roughness from a PCB manufacturing perspective, the rougher the better.
Right because there's adhesion.
Right peel strength. Nowadays, for high speed past 10 gigabit, now everything starts to matter and now people are talking 25 gigabit - 56 gigabit all the stuff lost, now becomes a factor. So it turns out the rougher the copper the higher the loss, so how do you model that? If you don't model that correctly you can't simulate it in advance.
Exactly.
So the bottling techniques in accuracy - so there's been different models out there one that's been very popular is the Hury model that was presented back in 2010 because I remember going to that presentation. Basically it was dubbed the ‘snowball model’ because when you look at the roughness profile under an electron scanning microscope, it looks like a stack of snowballs type of thing.
Okay.
Uh-huh and that's where it got coined the snowball model but it's the Hury model and it's very accurately shown that you get very good results measured to simulation. The problem was where do you get the parameters to feed that model? Back then to get it, if you tuned the parameters you could get an excellent fit to the loss but that doesn't help for tools so how do I get that? Unless you're building a board or measuring the board to get the parameters so you can use those again if you're going to build that same geometry in a new design. So that's very time-consuming - pretty accurate - but not practical for smaller companies. If you need a good answer now, rather than a good answer later as Eric Bogatin always says, that never helps you. So, one of my early contract positions, because I started going in consultancy after Nortel. One of my clients they wanted to do some analysis on dielectrics but they also wanted to include their roughness and I knew nothing about roughness at that time. So I started to do my own research into this so that I could try and do the work, and found that it was all over the place in a way.
Anyway, I completed the analysis not even based on what I knew at the time and it was okay, but that seed sort of stuck. So I started in it and once you get an interest in something then try to go further and further. So it's been a pet project of mine so I decided to think about the Hury model and say: well, is there a way to get these parameters based on datasheet value only? If I know the roughness from a datasheet the, height of the roughness, can I get the radius though? So I thought about it and you know, I thought about: okay, this is the stack of spheres. If I stack them up can I determine the radius of the sphere from that stack? So you know it's basic geometry of things and eventually you can get that number if you know this height. So I thought - just out of curiosity - I'm gonna try it and when I did, I got reasonably good results, almost right off the bat. I'm not perfect, but I can tweak things a little bit more and I'm saying okay… That's how it kind of began so it's been over a few years, off and on. I did a paper earlier in 2015, when I first presented some of it, and that was quite successful and every year it's been kind of incremental and testing it against other data and then eventually other software came out like simBR and I started having success with the model there and that was great and so it kind of went. So lately, after that, then I started thinking about I never get the the actual delay property. So in order to model things, you need proper loss and then also the the delay property or the phase. So then I thought well, perhaps, how does the roughness come into it? Because I noticed the rough with the copper I get different phases for the same material. Anyway so I worked out some some things and that's what last year's paper was about, to correct the the dielectric constant due to roughness...
It was really last year's paper.
Uh-huh and so that that worked out very well and when I correct that, I get very good results with it so that's it in a nutshell how I got from there to here.
Wow. So I know you've worked also with Polar instruments. Tell us about how that came about?
Yes so last year Polar had introduced the Hurray model into their tool and I hadn't really met Martin but in his newsletters I always got it and he announced that they were going to come out with the remodel and a Polar tool so I emailed Martin and said; look let me check it out to see how well it works. So they gave me a trial thing just to check it out and I tested it out against my data and there was just a couple of hiccups, but we sorted them out and now the tool - it's a great tool - we can get the parameters now basically from data sheet to fill in. So we've dubbed the model really like a ‘cannonball’ Hury model because it's a combination of both.
Well Martin spoke, I think I shared this with you earlier that in October Martin Godean from Polar presented a talk at Altium Life in Munich and I was chairing the room he was in and he pulls up this stack of cannonballs - you and I hadn't talked about this - then he starts citing all this work by Bert Simonovich. I nearly fell out of chair, like my friend Bert? So I really love that Bert, you've like been such a collaborative force in this industry about these models and you know that you reached out to talk to Polar and really made it better. Not so much in a self-serving way but it's good for the industry really, it's good for designers right?
I think so.
And so I really appreciate that generosity of spirit that you have and it's what I liked about you when I first met you and here we are all these years later who knew.
That's right.
So, what's next Bert? Tell us first of all, where can our listeners find your papers because I'm sure they'll want to get their hands on those?
Yes so I published papers that I have on my website at my company is http://lamsimenterprises.com.
Okay.
Well I'm sensing we'll try to put that in text somewhere I relate to this podcast so folks can find that and then they can find your consulting services there as well but then find all your papers there. Did Design Con aggregate the papers that come out of the show?
Oh yeah they have the proceedings.
But only the attendees get their proceedings right? So they can come to your website is the bottom line, right?
Right, so anyways so for my papers, I have my papers that I published on my website and it's not just Design Con I’ve also done EDI Con papers and that's part of the signal integrity journal. There's an offshoot of that - is EDI Con - and I attended that the last two years, they were the first two. So there's Boston that was great time. Actually you went to the first one?
Yeah I went to the first one I can't believe how our lives have just crossed so many times. We just met each other here and went hi.
And you met and you met my wife.
Yeah I met your wife on that trip.
Bert and I got to go to Fenway Park and have a private party at night and overlooking the fields and they brought out... what are those? I'm such a sports nut.
The trophies from the World Series.
- thank you the World Series trophies. They brought those out so we could you know take photo ops with and we had great food and we got to take over Fenway for a few hours and I met Bert's wife who's just a doll and we had a great time. So who knew when we met how our paths would cross?
But I think Design Con in general is about is networking, meeting new people, learning new things spreading the seed of papers. Like I was mentioning even last year's paper - Rogers took that and then confirmed the data or the theory part of it and then they presented results this year.
It’s such a great collaborative effort and I don't know I find it very refreshing because you know, like well I have a secret and if you give me a lot of money it might tell it to you. This is much more open handed and collaborative. I liked what you said earlier today - which was somebody will present something and then an offshoot will take off and then it'll take off and then someone will build on that and bring it back as something else. It's really the industry together - collaborating.
That's also for mine like 2010 with the snowball model, who knew? That room was packed to the rafters and out - that presentation from Paul Hury and Eric Bogaton’s and he presented that year and I was just dumbfounded and I'm going, well I don't understand it but that's cool, and that who knew that that would be the seed for my work, my research work.
And and then went into Polar and Rogers and it's just like an idea that sprung legs.
And that's just my example. One example of many you just look around - like Eric likes to say - come drink from the fire hose, that's the Design Con there’s just so much stuff and it's there and it's just a great place for that kind of thing.
It is a great show. So, a couple closing items. Number one what would you say for circuit board designers, are some of the kind of greatest challenges they're facing today? Looking forward into emerging technology is there any specific - one or two things maybe - that are sort of plaguing them at this point? Or things maybe they need to onboard and that they are not taking right now?
Just in general as the speeds are going up the actual material properties are really becoming a factor. A big thing is fiber - we've talked a lot about that - fiber weave effect and the industry is looking how to mitigate that effect. A lot of nice papers over the last few years, talking about that and again there's a lot of things on the roughness, getting good modeling because it's important now. And now with everything like the new Pam-4 standards, 56 gigabit. The margins are tighter, so fabricating boards is more demanding.
Yeah it ain't what it used to be I can tell you. I started in the board fabrication industry in 1984. Oh my gosh that seems like such easy stuff compared to today. I was just speaking with John Belushi from ASC and I said it used to be you just got your board, your fab drawing you had your sort of mechanical, here's the size of the footprint, this is the size of the trace plus or minus this, and off to the races you go. Now it's like a board fabricator has to think about everything they're doing and how that is going to impact. You can go to a board shop, make a board and be well within IPC standards and its’ still not performing to the designers intent.
I think it's not just the board shop, I think sort of the industry as well, you have to specify what you want properly in your fabrication notes.
What fabrication notes. What I'm saying is documentation, I think is an issue.
Yes and and the thing I'm seeing is if you want consistent results you have to nail down your design. Basically nail it down and not let the fabricator substitute material for different weaves. For instance if you have a stack up that you first designed it's got to be included verbatim on the fabrication notes. So you must use this material, this weave.You can’t substitute, and you can't play around with all the line widths and space to do things different. By specifying things on the notes that restricts what they can do you should end up getting what you want otherwise you may not.
And you had told me earlier in your consultancy business that you will talk about modeling certainly, but then you also give them the added benefits of giving them some guidelines of how to spec in these.
Yeah so typically a lot of my business is design reviewing boards before fabrication. After they do the design like Altium Board Designer would lay it out, so now there's a design review at the end so some of the clients they'd like to get some review over that visual review and I do that sort of thing for them. But as part of that, I review the stack up even from the board shop because the stack up people are human and could make an error. Typo or a lot of times they're just templates and they don't cut and paste properly or something, and it may not be correct. I haven't found anything that wasn't correct but I do that anyways, just check it, double check that the impedance is correct in things. But on top of that I also say that I'm going to review their fabrication notes to ensure there's consistency there and usually I find that a lot of these are smaller companies or startups. They're not aware of what's needed or they have one set of fab notes and they have the same design all over. They just use it over and over but that could add confusion in the shop.
Yeah absolutely.
At the end of the day part of the design review it's also part of a bit of educating as well to some clients so they realize some of the importance and they appreciate that as well.
Yeah and it is so sorely needed and people don't, like you said especially smaller companies, they don't always have the resources to go out and spend endless hours in a board shop getting educated or whatever the issue is. Or educated about signal integrity or whatever it is, so I think what you're offering in your business and in that niche is really valuable so that's great.
Well my friend I'm gonna let you get back out on the show floor. I'm sure you have a lot to do today I'm sure you're a busy guy so yeah I so appreciate you spending a little time with me and I'm so glad we got to connect I know you're getting so busy - such a big shot these days - it's been a delight thank you.
Actually, the reason I knew you were here, I saw something on LinkedIn and saw you were responding to somebody and I go: wait a minute is Judy here? So then I LinkedIn messaged you last night and I said, are you here? and yeah so let’s connect today.
See there's a lesson to everybody, LinkedIn really is useful. Gosh you and I've met a lot of friends through LinkedIn. I'm so glad to see my friends. I don't get to see you enough so I'm glad to see you whenever I get to see you, I'm not gonna complain. So best to you, congratulations on your nomination again.
Thank you Judy and the same to you.
And have a great show and I look forward to catching up with you next time.
This has been Judy Warner with the OnTrack podcast please remember to subscribe on your favorite RSS feed and we look forward to talking with you next time and always remember to stay OnTrack.