Episodes

Thursday Aug 03, 2023
The Impact of the Defense Sector in the Electronic Industry Ecosystem
Thursday Aug 03, 2023
Thursday Aug 03, 2023
We have a very interesting topic today! The impact of the defense sector on the electronic industry.
Our guest Nathan Edwards, an Executive Director, U.S. Partnership for Assured Electronics (USPAE) will share with us what goes in a Defense Electronic Consortium (DEC) and how all of these impact the electronics eco-system. We will also touch a little about supply chain diversification and onshoring efforts here in the US.
Watch through the end, this is a very special episode you don’t want to miss.
We have a very interesting topic today! The impact of the defense sector on the electronic industry.
Show Highlights:
- Introduction to Nathan Edwards
- Nathan briefly share his background in the electronic industry in both government and commercial sector
- What is United States Partnership for Assured Electronics (USPAE) and what is its involvement in the Defense Electronic Consortium (DEC)?
- Nathan explains what goes on DEC
- Small and medium size electronic companies could benefit in participating in the government ecosystem
- A study shows that 86% of 649 manufacturing firms receive less than 10% of their revenue from defense
- Electronics in the banking industry, from the tamper-proof electronics, security, authenticity, and some reliability and recovery
- Is something similar to the US Defense Electronics Consortium exist in different countries?
- Nathan discusses about the recent policy chain in the Defense Production Act, Title II
- Electronic supply chain diversification and onshoring in the United States
- A policy that will go in to effect in 2027 under the National Defense Authorization Act states that semiconductors, printed circuit boards and interconnects cannot be produced by some of the companies in China
- Nathans thoughts regarding production of electronic components in Latin America, especially Mexico
- Nathan volunteers to mentor emerging talents at his school district’s high school and middle school and get them involved in electronics sector
- The electronics industry requires a full depth of STEM from chemist, manufacturers, mathematician, designers and more
- Career Technical Education (CTE) offers biomedical tech, STEM, IT, and it is sponsored under the State Department of Educations as well as the Federal Department of Education
- Two critical things to a successful onshoring are reliable, skilled workforce, and capital to invest in the state-of-the-practice equipment
Links and Resources:
- Reinventing the business of electronics. Nexar puts your business ahead of the curve, learn more here
- Watch related, previous episodes:
- Connect with Nathan Edwards via LinkedIn
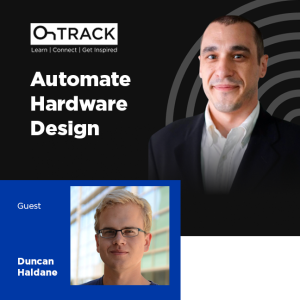
Wednesday Oct 26, 2022
JITX, a Way for Hardware Engineers to Write Codes
Wednesday Oct 26, 2022
Wednesday Oct 26, 2022
This is a very interesting episode, especially for hardware engineers. Duncan Haldane, the CEO, and co-founder of JITX joins us to share a very interesting approach to PCB design. JITX is a way for hardware engineers to write code to design circuit boards.
I know you are excited to hear more! Watch this episode or listen on the go. Be sure to check out the show notes and additional resources below.
Show Highlights:
- Duncan talks about the Series A funding from Sequoia Capital and the general availability of JITX as an actual product.
- Duncan's path to engineering started in robotics
- How can an electrical engineer benefit from JITX? Duncan explained in detail
- JITX is very well integrated with Altium, it works natively with the existing designs and libraries
- Hardware-generated code transforms the job of an engineer a little bit so that they don't have to manually look through all of the different specs for every component that they need
- JITX is a Nexar partner and uses Octoparts data, in addition, they built a different type of database that's meant for part optimization.
- Reusable expert hardware engineering knowledge is one of JITX’s ultimate goals
- They are building full automation for boards, new kinds of routing algorithms, new kinds of placement algorithms, and checks for physical geometry
- The future is optimization
- Zach and Duncan excitedly talked about AI, and how it can be used to drive some parameters to create new designs
- Electrical engineers’ job is secure, automation can help with the shortage, but will not replace electrical engineers’ jobs
- What the future looks like for JITX
Links and Resources:
Connect with Duncan Haldane on LinkedIn
Visit JITX website
Read JITX Launches General Availability And Announces $12M Series A From Sequoia Capital
Connect with Zach on LinkedIn
Visit Nexar website
Visit Octopart website
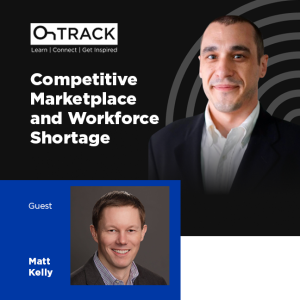
Tuesday Oct 04, 2022
Overcoming Technological Challenges in the PCB Industry
Tuesday Oct 04, 2022
Tuesday Oct 04, 2022
Matt Kelly is the Chief Technologist at IPC. In this episode we will discuss all about the technological challenges the industry is facing. Matt will help us understand the “ecosystem” involving the semiconductor industry, advanced packaging, and IC substrates.
Check the show notes and additional resources below.
Show Highlights:
- Matt Kelly’s role as the Chief Technologist at IPC
- The Moore's Law is continuing, but it is economically becoming difficult to maintain, this has become the driving force behind heterogeneous integration
- What does the CHIPS Act really mean for manufacturers?
- Production of semiconductors is an expensive business–one fabrication infrastructure can cost an average of 20 billion dollars
- Matt stresses the need in the industry to use, and understand the “ecosystem” involving the semiconductor industry, advanced packaging, and IC substrates
- The US has a 20-year market leader, knowhow gap, weak sub-tier supply, skilled workforce shortage, and lack of raw materials
- The industry needs to spend time looking at the big picture, take the bigger messages, and convert them into actual change
- A significant shift in the workforce–PCB designers are a scarce commodity. In the near future, printed circuit board designers may have to double as IC substrate designers
- The global supply chain is alive and well, a change to a regional and global mindset is necessary to overcome most of the industry challenges
- Matt shares the same scenario with produce shoppers in the summertime, you try to buy your fresh fruits and vegetables locally from your local farmers or whatever, but yet you still go to the grocery store
- IPC’s focus is on increasing workforce skills development in the areas of design and assembly
- IPC is sponsoring the Advanced Packaging Symposium, Building the Substrate and Packaging Assembly Ecosystem in Washington, DC, on October 11th and 12th
Links and Resources:
Follow Matt Kelly on LinkedIn
Learn more about the IPC’s Advanced Packaging Symposium, Building the Substrate and Packaging Assembly Ecosystem
Watch related podcast episode:
The Benefits of Diversifying PCB Industry Supply Chain
IPC CEO John Mitchell on the Supporting American Printed Circuit Boards Act
What is in the PCB Bill?
Connect with Zach on LinkedIn
Full OnTrack Podcast Library
Altium Website
Claim the special offer for Podcast listeners only

Wednesday May 18, 2022
Landing a Full-Time Engineering Career at NASA
Wednesday May 18, 2022
Wednesday May 18, 2022
This episode will learn how a childhood dream can turn into reality through hard work, determination, and networking. Andrew Hartnett dreamt of working with NASA at a very young age. He will share with us exactly how he landed his Computer Engineer position in this very sought-after agency.
Altium 365: Where the World Designs Electronics
Get Your First Month of Altium Designer® for FREE
Show Highlights:
- Andrew’s background, from his 3rd-grade drawing and high school robotics team to landing a co-op internship program at NASA’s Johnson Space Center (JSC)
- He joined The First Robotics Team in high school
- A lot of networking and determination is what helps him land the co-op internship program
- He started working full-time in January 2010
- Briefly discuss Upverter and the benefits of having high-school level educational programs for aspiring PCB designers
- What is NASA’s co-op internship program? Andrew describes the advantages of the co-op program over a typical internship
- Get exposure to things you don’t get at school
- Experience designing and actual assembly of PCB
- Andrew talks about electronic design standards at NASA and shares details about testing, reliability, and the challenges of sending electronic devices to the space
- Addressing devices’ heat, and vibration in space
- Andrew talks more about First Robotic Competition and stresses the importance of hands-on experience for high school kids or younger
Links and Resources:
Visit NASA’s JSC website
Learn more about JSC’s Internship Program
Making electronic design easy, visit Upverter's website
Register at Altium Education for Free
Altium Designer Free Student License
Connect with Zach on LinkedIn
Full OnTrack Podcast Library
Altium Website
Download your Altium Designer Free Trial
Learn More about Altium Nexus
Get Your First Month of Altium Designer® for FREE
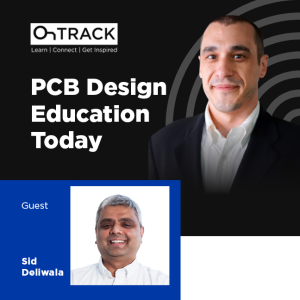
Wednesday May 04, 2022
Hands-on Learning for PCB Design Students
Wednesday May 04, 2022
Wednesday May 04, 2022
In this episode, we will talk about the importance of engaging and exposing the PCB Design students to today’s real-world industry demands. Our guest Sid Deliwala is the Director of Lab Programs in the Electrical and Systems Engineering Department at the University of Pennsylvania. Sid will share with us how he makes Electrical and Computer Engineering (ECE) fun and meaningful for our future innovators.
Altium 365: Where the World Designs Electronics
Download your Altium Designer Free Trial
Show Highlights:
- Sid talks about his background and his advocacy for hands-on training
- Tinker and play – learn the fundamentals, try new things and take risks
- Making the Electrical and Computer Engineering (ECE) major meaningful
- Everything in the circuit world, in the hardware world, is also very data-driven
- End to end experience for students, holistic understanding of Software, hardware, and PCB design
- Preparing students to work in a multidisciplinary engineering environment
- If the cloud, the analog world, and all the digital circuitry that's needed to make things work rolled into one, it'll certainly be a very, very exciting time for all the future innovations
- You don't have to be an expert on everything, but you should at least have been exposed to everything in engineering
- Sid talks about the Penn Electric Racing – every year they participate in FSAE annual competition
- The problem with offshore PCB manufacturing – students have to wait for at least 3-weeks to receive their PCB for their project
- Importance of DFM and the difference it will make for students if they get the chance to visit the manufacturing company
- The supply chain and semiconductors shortage is real, the students experience current industry problems first-hand
- Sid expresses his sentiments toward a completely optimized system, it has some disadvantages
Links and Resources:
Sid Deliwala’s Director Profile, University of Pennsylvania
Podcast with Eric Bogatin: Pathological Design Features
Read Altium’s Newsletter: Staying on Top of the Supply Chain with Altium
Full OnTrack Podcast Library
Altium Website
Download your Altium Designer Free Trial
Learn More about Altium Nexus
Altium 365: Where the World Designs Electronics

Tuesday Mar 22, 2022
3D Printing Circuit Boards for Fast Prototyping
Tuesday Mar 22, 2022
Tuesday Mar 22, 2022
Let’s talk about the future of printed circuit board prototyping. Sean Patterson, the President of Nano Dimension USA is here to introduce the technology behind DragonFly IV®, the multi-material 3D printer for electronics fabrication. He will walk us through its current capabilities, what it can do and what we may expect from it in the future.
Sit back, relax and enjoy this episode. Make sure to listen through the end and check the show notes with the additional resources below.
Altium 365: Where the World Designs Electronics
Show Highlights:
- Sean talks about the growing company.
- They have 39 members in the US, and 500 globally. There are still plenty of roles available, visit Nano Dimension’s website here
- Started as an additive manufacturing company, specifically for circuit boards to now multi-material, and multi-layer 3D printing option for electronics through
- Sean excitedly shares all the exciting things that the DragonFly IV can do.
- Faster electronic prototyping and proof of concept
- Environmental and sustainability advantages
- A manufacturing plant in the office
- An electromechanical structure that's functionally, mechanically, and electrically, to solve a problem
- The evolution of electronic manufacturing offers a solution that works–there are many better ways, weight reduction, and size reduction
- Nano Dimensions is helping the electronics industry ecosystems systems get prepped now, to support the adoption of this technology
- DragonFly IV uses FR4-like, and the conductive ink is a silver nanoparticle
- What’s the future look like for Nano Dimensions?
- What materials will be available in the future?
- What will be the ultimate capability of the DragonFly?
Links and Resources:
Connect with Sean Patterson on LinkedIn
Visit Nando Dimension’s website here
Full OnTrack Podcast Library
Altium Website
Download your Altium Designer Free Trial
Learn More about Altium Nexus
Altium 365: Where the World Designs Electronics

Monday Mar 14, 2022
Master the Basics of PCB Electronics Design and ECAD Software
Monday Mar 14, 2022
Monday Mar 14, 2022
Altium launches a new curriculum into the college in university space called Altium Education. In this episode, Rea Callender, Altium’s Vice President of Education tell us what is in the curriculum, who is it for, and how it will help PCB designers and aspiring designers advance into their career.
Altium 365: Where the World Designs Electronics
Watch the video, click here.
Show Highlights:
- Altium launches Altium Education, which aims to educate anyone who knows nothing about printed circuit board design, to learn the skills to create a printed circuit board, and send it off to manufacturing
- Students can still apply for Free Altium Designer® license
- Altium is taking the lead in PCB Design Education
- Teaching the process of circuit board design
- Modular approach with 16 units that college professors can use to supplement their course
- Student can take the curriculum for free and take it as a self-phase learning tool
- Altium Education have received positive feedback from college professors prior to its launch
College professor - excellent response
- There is currently no curriculum similar to Altium Education, it is a supplemental course, it's not meant to displace anything
- Pcdandf survey reports that in 15 years, approximately 78% of the workforce to retire which may lead to the talent shortage
- Altium Education will help attract talent to the field
- It will equip the students with proper skills in PCB design
- It is designed for High School students, College students, and Professional
Links and Resources:
Register to Altium Education for Free
Connect with Leah Callender on LinkedIn
Yoshi Fukawa Episode - Coming Soon
Connect with Zack on LinkedIn
Download your Altium Designer Free Trial
Learn More about Altium Nexar
Altium 365: Where the World Designs Electronics
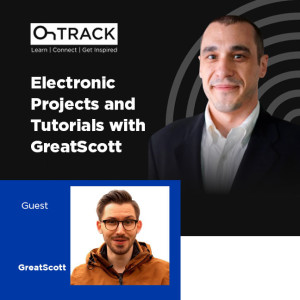
Friday Mar 11, 2022
Making Electronics Education Fun
Friday Mar 11, 2022
Friday Mar 11, 2022
It's a privilege to have another well-known YouTube Creator GreatScott. He is creating electronics projects, tutorials, and everything in between. He makes electronics education fun with his experience, skills, and practical approach. This is going to be an exciting discussion so make sure to watch through the end and check out the additional resources below.
Altium 365: Where the World Designs Electronics
Watch the video, click here.
Show Highlights:
- How GreatScott started in the electronics industry and his interest in creating fun videos
- He started in 2013, at the age of 18, and created his first circuit project the next year
- First job application and the task was in the field of electrical power engineering
- GreatScott’s practical approach with his projects as implemented on his recent vacuum project, Every Device should have this Upgrade! (Endless Battery Run Time)
- The trajectory of GreatScott's career path–what brought him up into power engineering
- Followed his mother's advice to go for renewable energies and took a renewable energy course at a University in Germany
- GreatScott recommends courses in Electronic Engineering and joining an internship program at the same time—duales studium or dual studies, for those looking for a career or interested in electronics
- GreatScott YouTube Channel showcases about 50 Electronic Basics Video Series
- Interesting and funny videos GreatScott recently created
- Testing circuits I found on the Internet: Inverter! It does work, BUT…
- DIY LiPo Supercharger! (Charge, Protect, 5V/12V Boost V2)
- Planning to do the 3rd on the series (free energy schematic circuit designs)
- ElectroBOOM YouTube Channel is also creating fun and engaging electronics videos
- What to expect on the DIY or Buy video series on the GreatScott channel
- Tear down doesn't fit for Scott - his goal for his videos is to create, unique and practical projects
- Engineers improve their skills through mistakes and criticisms
- GreatScott's plan in the future
- Continue making fun and educational videos
- Learn to weld
- Include a wider assortment of projects and topics
- Launch an upcoming video for his two circuit boards creation (aluminum printed circuit board)
Links and Resources:
Follow GreatScott on Instagram, Twitter and Facebook
GreatScott Altium Designer Affiliate Page
Connect with Zack on LinkedIn
Altium 365: Where the World Designs Electronics
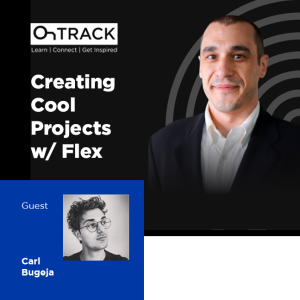
Tuesday Mar 01, 2022
PCB Motor Robots Creation with Carl Bugeja
Tuesday Mar 01, 2022
Tuesday Mar 01, 2022
In this episode, Carl Bugeja, an Electronics Engineer and a well-known Youtube Creator, talk about his experience designing electronics, how he started, and his fascination with inventing new things. He will also share some exciting robotics projects he is currently working on. Watch through the end, and make sure to check out the additional resources below.
Altium 365: Where the World Designs Electronics
Watch the video, click here.
Show Highlights:
- Carl's background in PCB and electronics design 02:02
- A startup with a friend, Carl designed cool stuff such as drones, bluetooth, and alarm techs
- He created and and documented his electronics projects which he started sharing on Youtube
- Carl first started using Altium Designer® when he was in his third year in the University, and love using it since then
- Carl shares his design process, and his approach to PCB design
- The first project that Carl shared on YouTube is a PCB Motor 04:28
- How PCB Motor project got started 06:39
- Soft robotics
- The benefits of using flexible PCBs 09:36
- There’s nothing you can’t do with a flexible PCB
- An opportunity to play around and create a new concept
- Trial and error is Carl’s way to learning and improving his skills with creating flex PCBs 10:41
- One of Carl’s most challenging project and most viewed video on Youtube is his Jumping PCB 13:12
- Check out Carl's recent projects 18:46
- Carl's firmware writing skills is acquired from his actual projects and work experience 17:00
- The importance of building a good relationship with your manufacturer 22:38
- Check out Carl Bugeja’s YouTube Channel here
Links and Resources:
- Watch Carl talks about why he love using Altium Designer®
- Connect with Carl Bugeja on LinkedIn
- Carl Bugeja’s YouTube Channel
- Carl Bugeja’s Hackaday Page
- Altium Designer Free Trial
Connect with Zack on LinkedIn
Full OnTrack Podcast Library
Altium Website
Download your Altium Designer Free Trial
Learn More about Altium Nexar
Altium 365: Where the World Designs Electronics
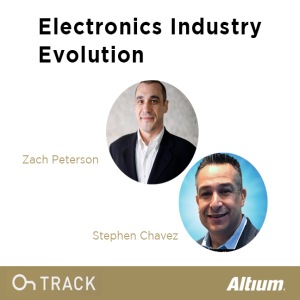
Wednesday Dec 15, 2021
Mastering Your PCB Design Tool as the Industry Evolves
Wednesday Dec 15, 2021
Wednesday Dec 15, 2021
“One of the fundamental things that I'm very passionate about is continuous development.” - Stephen Chavez
We are thrilled to have Stephen Chavez on the podcast again! He is one of the respected Electrical Engineers in the electronics industry. Stephen is the chairman of the Printed Circuit Engineering Association (PCEA) and oversees the design team of a renowned military aerospace company. In this episode, Stephen will generously share his work experience and how he sees the evolution of the electronics industry. This is a not-to-be-missed episode as it will give you enough courage and motivation to keep on learning to become a successful electronics and design engineer of today’s generation!
Altium 365: Where the World Designs Electronics
Show Highlights:
- Stephen and Zach’s best advice on how to get on top of things as the electronics industry evolves
- Stephen’s career progress in the electronics industry and his affiliation with PCEA (Printed Circuit Engineering Association)
- The need for cross-collaboration as designing changes and gets complex
- Altium 365 offers seamless collaboration in the cloud
- Digital thread or model-based design
- How’s the process today?
- The evolution of toolsets
- The difference between the tools of today and the past
- Taking advantage of the tool you’re using versus the manual approach
- The importance of tool training
- PCEA’s mission for the next generation engineers
- Secrets of PCB Optimization with Rick Hartley
- What do you need to consider when designing circuit boards
- Designer’s triangle
- Layout solvability
- Performance
- Design for Manufacturing (DFM)
- Intricate details that go into designing a PCB
- What it takes to fabricate and assemble a printed circuit board especially for young engineers
- Mike Creeden on Empowering PCB Engineers through PCEA
- Manufacturing aspect - filtering your suppliers
- Mistakes engineers make when choosing the materials for design
- Balancing success in circuit design
- Engineering learning practices in the past vs today
- MCAD, CAD for tool collaboration
- Autorouting in RF designs
Links and Resources:
Previous Podcast Episodes with Stephen Chavez
- Stephen Chavez Calls on PCB Designers to Get Involved
- Is IPC-CID Certification Really Important to Your Career?
- Stephen Chavez on Staying out of Your Comfort Zone
- Judy Warner and Stephen Chavez on the Approachability of the Pros
Printed Circuit Engineering Association (PCEA)
AltiumLive 2022 Connect: Now open for registration
Connect with Stephen Chavez on LinkedIn
Connect with Zach Peterson on LinkedIn
Watch Zach’s latest Altium Academy courses on Youtube
Read Zach’s articles on Altium’s resource hub
Full OnTrack Podcast Library
Altium Website
Download your Altium Designer Free Trial
Learn More about Altium Nexus
Altium 365: Where the World Designs Electronics
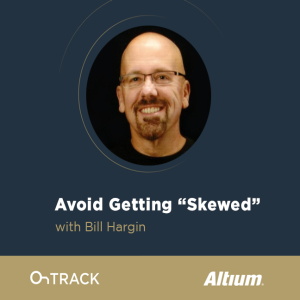
Tuesday Oct 19, 2021
Deterministic Solutions to Solve Skew Problems
Tuesday Oct 19, 2021
Tuesday Oct 19, 2021
Everything that goes to making a board works against signal integrity...physics screw things up.
-Bill Hargin
Avoid getting your design “skewed”! Today’s guest is Z-Zero’s Founder and CEO, Bill Hargin. Together we will dive into the cause of getting skews in your board. There are many details, and many questions answered, so make sure to watch through the end and check out the additional resources below.
Altium 365: Where the World Designs Electronics
Show Highlights:
- Introduction, a brief overview of Z-Zero and Bill’s background
- Hardware Manager at Boeing (Electronic cooling and CAD design)
- He became the Director of Sales and Marketing at Hyperlynx
- High-speed marketing and five years in laminate space
- Sharing his deep knowledge of signal integrity - travel around the world doing workshops
- 2018 - full time at Z-Zero, a software company he founded. Z-Zero is an EDA start-up that offers solutions for stackup design, field solver, automation, library
- Bill presents every year at the PCB West on topics of stackup design and material selection
- Bill offers more resources through webinars and blog articles on z-zero.com
- What are Skews, and why is it’s a problem?
- Comprehensive overview and solutions
- Deterministic solutions
- Stochastic Solutions
- Comprehensive overview and solutions
- What is a Glass-weave skew (GWS)?
- Prepreg glass types, what is spread glass?
- Bill’s deterministic solutions to avoid skew
- Angled routing
- Rotating artwork 10 degrees (waste about 15% of the material, higher cost)
Links and Resources:
Bill Hargin on LinkedIn
Z-Zero Website
Who Should Be Concerned about the Fiber-Weave Effect?
Read the blogs:
How to Avoid Getting Totally Skewed – Part 1
How to Avoid Getting Totally Skewed, Part 2
How to Avoid Getting Totally Skewed, Part 3
How to Avoid Getting Totally Skewed, Part 4
Watch the Webinars:
Glass-Weave Skew - Part 1 - Who Cares?
Glass-Weave Skew - Part 2 - Mitigation Methods
Altium 365: Where the World Designs Electronics

Wednesday Jul 29, 2020
Insertion Loss is a Complex Issue: John Coonrod is Here to Explain It
Wednesday Jul 29, 2020
Wednesday Jul 29, 2020
Altium 365 Podcast Listener Discount
The OnTrack Podcast welcomes John Coonrod back to the show. John is Technical Marketing Manager at Rogers Corporation and a senior engineering professional with a rich background in PCB design, fabrication, processing, and modeling. John also has extensive experience with circuit materials, making him the ideal candidate for the topic of today’s podcast: insertion loss.
Show Highlights
- 01:45—Clarifying terms: a quick overview of Microstrips vs Striplines
- 02:20—Exploring laminates, multilayered circuits, and plated through-holes
- 06:42—Applying electromagnetic fields: a prerequisite for understanding insertion loss
- 09:25—The four components of insertion loss
- 13:10—RO4350B™; a friend to all fabricators?
- 15:10—Pros and Cons of electroless nickel immersion gold (ENIG)
- 18:13—John’s advice to design engineers on modeling for ENIG’s performance range
- 21:33—Navigating the relationship between solder masks and insertion loss
- 24:20—A call to viewers and listeners: Got a copper-related topic you’d like to hear John and Judy discuss? Submit your requests!
Resources:
John Coonrod on Linkedin
Rogers Corporation Website (Advanced Connectivity Solutions)
(Includes Coonrod’s corner videos, data sheets, calculators and more)
Autonomous driving Resource Page (Guides, Videos and Material selection)
ROG Mobile App (Resources accessible from your smartphone or tablet)
White Paper High Performance PCBs: Judy Warner, Chris Savalia, Michael Ingham
Altium 365 Podcast Listener Discount

Tuesday Jul 07, 2020
Tuesday Jul 07, 2020
Istvan Novak, Principal Signal and Power Integrity Engineer for Samtec Inc. and winner of the DesignCon 2020 Engineer of the Year Award joins the OnTrack podcast to talk picosatellites, simulation tools, and the rising importance of power integrity.
Altium 365 Podcast Listener Discount
Show Highlights
- Introduction to Istvan Novak
- A brief look at Samtec Inc., the successful computer equipment manufacturing company headquartered in Indiana.
- Istvan’s path to becoming a Power Integrity expert
- CubeSats and the students who make them
- The challenges of dimensionality: has power integrity become more important than signal integrity?
- When Power Integrity is an afterthought
- The value of expert disagreement
- “Regardless of what we want to simulate, we can find good simulation tools to do it”: Good design and the challenges of modeling and simulation
- Closing thoughts; the first working Picosatellite; and the first electrosmog map of the globe
Resources:
- Istvan Novak on LinkedIn
- Samtec: gEEk spEEk SI Webinars.
- Samtec Silicon-to-Silcon Solutions Website
- The SI-List Archives
- Istvan Novak: DesignCon 2020 Engineer of the Year Award
- BUDAPEST UNIVERSITY OF TECHNOLOGY AND ECONOMICS Picosatellite
- Istvan Novak’s Electrical Integrity Website
- Picotest Website
- Signal Integrity Journal
- Design 007 Magazine, See pg. 38 Do You Really Need That Ferrite Bead in the PDN?
- First Electrosmog Map of the globe
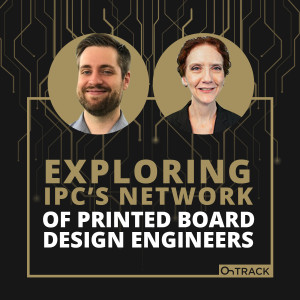
Wednesday Jun 03, 2020
Exploring IPC’s Network of Printed Board Design Engineers
Wednesday Jun 03, 2020
Wednesday Jun 03, 2020
The renowned global trade association known as IPC has put together a network of printed board design engineering affiliates under the name IPC Design. IPC Design’s affiliates are comprised of PCB design engineers across the globe who are working to advance the art and science of printed design engineering.
IPC Design’s Patrick Crawford and Teresa Rowe join the OnTrack Podcast
Work from Anywhere. Connect with Anyone.
Show Highlights
- What is IPC Design, and what is its primary mission?
- Increased global presence and participation: How IPC is molding its future.
- IPC Design’s worldwide buy-in, its fresh new participants, and how the quarantine has affected participation.
- Has productivity gone up since quarantine?
- Lessons in remote working and the importance of taking time for yourself.
- Between January 2020 and now.
- What’s in store for the future: IPC’s collaborative content model.
- America, Europe, and Asia: IPC’s leadership group and global design committee.
- IPC Design is looking to fill a leadership role in Asia.
- What’s in it for you, the designer? Teresa and Patrick count the ways designers will benefit from IPC Design.
- ”Let’s start up a chapter!”: How individuals, student groups, and companies can get affiliated with IPC Design.
- Translators of the world, connect! How IPC Design can serve and collaborate with STEM groups all over the globe.
Resources:
Teresa Rowe on LinkedIn
Patrick Crawford on LinkedIn
IPC Website
Link to IPC Design webpage
Link to IPC Design enrollment page
Patrick Crawford’s video presentation on IPC Design
Realtime with IPC
IPC CEO John Mitchell on the Impact of COVID-19 on the Electronics Supply Chain
Work from Anywhere. Connect with Anyone.
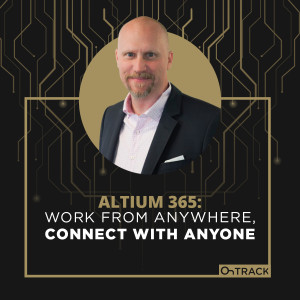
Tuesday May 05, 2020
Altium 365: Work from Anywhere, Connect with Anyone
Tuesday May 05, 2020
Tuesday May 05, 2020
Altium 365 has launched in the midst of a worldwide quarantine effort—a time when companies have drastically reduced the in-office workforce, and financial constraints and travel restrictions have never been tighter.
Altium’s VP of marketing, Lawrence Romine, joins the OnTrack Podcast to explain how Altium 365 removes the obstacles presented by the lockdown effort, why it’s the perfect tool for the post-coronavirus environment, and how the launch timing couldn’t be more serendipitous.
Work from Anywhere. Connect with Anyone.
Show Highlights:
- Altium 365 has launched on schedule; a brief look at why the timing couldn’t be more perfect.
- Working remotely. The Altium 365 cloud based platform which Altium Designer and Concord Pro run on.
- Seamless integration: the symbiotic relationship between Altium Designer and Altium 365.
- Arduino, SkyShips, and you: the various types of Altium 365 users, and how the addition of new features addresses their individual needs.
- Flattening the curve: Altium’s conscientious approach to the learning curve when adding new features.
- Design Reviews in a pandemic—a use case: How Altium 365 removes the obstacles presented by a remote work environment.
- Some users describe the experience of Altium 365’s cloud-based real-time collaboration as “similar to working in Google Docs”. Lawrence elaborates.
- It’s as easy as sending a link: How Altium 365 frees up budgets by eliminating excessive travel, phone calls, and emails.
- “Simplicity is the ultimate expression of sophistication”: Lawrence recalls an automotive experience from his life in praise of Altium 365’s design ethic.
- As simple as using a web browser: How sales personnel are utilizing Altium 365 as a demonstration tool for prospective clients.
- Lawrence’s predictions about the farside of the COVID-19 calamity.
Links and Resources:
Exclusive Sharable Listener Discount Link
Altium Designer-Altium 365
Altium 365 Customer Stories Videos: Skyship, Arduino, Project March
Altium 365 Webpage
AltiumLive: Altium 365
Altium 365 Security
Now you can get the ultimate PCB design productivity with the easiest platform for PCB design. Easily communicate design changes to your team with Altium 365.
Work from Anywhere. Connect with Anyone.
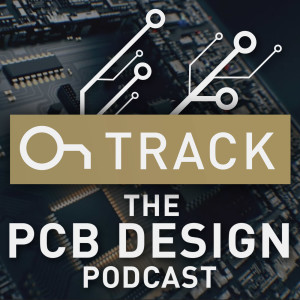
Tuesday Jul 17, 2018
Paste Interconnects and Paste Sintering with Chris Hunrath from Insulectro
Tuesday Jul 17, 2018
Tuesday Jul 17, 2018
Paste Don’t Plate! People are doing 90 layer multilayers with paste interconnects. Want to learn more? Find out about paste sintering from Chris Hunrath to learn more about its applications and benefits to PCB designers. What must designers consider and what are the advantages of Ormet’s products? Listen in for insights from the expert in this week’s episode.
Show Highlights:
- New material developments make paste interconnect technology more feasible
- Ormet’s paste sinters at one temperature forming a new alloy with higher melting point
- Paste interconnects allow for changing build sequence in which vias are formed i.e. drill, add paste, and then laminate - giving you interconnects inside a double-sided core with no visible vias
- Multilayer PCBs: Can split up a 32-layer board to two 16-layers (even as many as 4 x 18 layer multilayers - which is much easier to build
- Also reduces risk depending on design - electrically test each half and only use the good ones
- Ormet process/paste interconnect process eliminates traditional drawbacks i.e. excess copper on surface features
- Eliminate backdrilling with paste interconnect process without extra copper in the via
- Ormet paste eliminates electrolysis and plating process
- Signal integrity benefits
- Applications: RF, high-layer multi cap, avoid secondary remelt, downhole assembly etc
- Design considerations: Where to split up layers for best design benefit; Via at 1:1 or less aspect ratio - only in 1 B stage layer and correct size via for applying paste; Size of receptor pad for laser drill via must be correct to prevent paste from running - spread glass is good for B-stage; annular ring around the via to register laser drilling; with many paste interconnects - don't paste to the edge.
- Paste melts and forms alloy with inter layer copper creating a permanent metallurgical joint
- People are doing 90 layer multilayers with paste interconnects.
- HDPUG (HDP User Group) is creating HDI test vehicles with paste interconnects and HDPUG members will have access to reliability data for breaking up big PCBs
- Paste don’t plate!
- Future topics: Many ways to use conductive inks in electronics, copper foil, integrity issues and printed electronics. Material science behind electronics, new design tools, various versions of conductive inks
Links and Resources:
Chris Hunrath on Linkedin
Click to listen to Chris Hunrath’s other episodes about Spread Glass or Material Sets.
Hi everyone. This is Judy Warner with Altium's OnTrack Podcast. Welcome back, here we are again with your friend and mine, Chris Hunrath from Insulectro who's going to teach us about paste sintering today, which I don't know much about, but we're going to learn about it together. But before we get started, remember to hit all the typical Altium social media platforms Facebook, LinkedIn, and Twitter please follow me on LinkedIn and also remember we are recording on YouTube as well as Podbean and we can be found on all your favorite podcast apps.
Alright, so today we're going to talk about - I don't even know how to set this up entirely cause I'm just as much as a student. So Chris, welcome back! Thank you again, and I know this isn't a new technology - it's just not one that has crossed my path. So tell us about what paste sintering is and what the applications are, and benefits to our designers that are listening today?
Okay, interconnect technology, as you mentioned is not new, what's happened recently though is there's been some new material developments that make it more feasible for the circuit boards. Certainly in ceramic fire technology, metal - powdered metals have been used to make interconnects and traces and circuits on ceramic circuit boards, but those fire at 850-plus degrees Celsius, which would obviously destroy most PCB materials so there's some new technologies out now. There are different kinds of pastes that are used for interconnects. The one that we work with, and the one that we promote, is something from a company called Ormet, and their material is interesting because it sinters at one temperature and then it forms a new alloy with a higher melting point.
Okay I feel like we need to back up and explain what paste interconnect technology actually is. Like how it's performed and then we can go into the material science part just so I can keep up, Chris I want to be able to keep up.
So multi-layer PCBs - also not new - typically what you do is, you print and edge any number of layers, you drill and then you plate. Typically electroless copper, to make the non-conductive surfaces conductive, and then you build up the thickness with electrolytic copper.
Mmm-hm.
And some people call it a semi-edited process, because you are using the electroless first as a seed layer. There are some other technologies used to make that dielectric surface conductive, and then you build up with electrolytic copper and so that's how you link the layers of the z-axis.
So if you think of a classically - as a circuit board - as a web of foils printed and etched, all your XY connections, and then the drilled holes - whether they're laser drilled, blind vias, or drilled through holes, the plating links everything in the z-axis. Now one of the challenges when you do that, is you're consuming real estate at all the layers. So let's say you have a 12 layer multi-layer - relatively simple multi-layer by today's standards - but you need to connect layer 1 to layer 10 you've taken up the real estate in all the other layers - you can't route circuits in those places, because there's a via in the way, unless you wanted them to connect to that via and they're part of that net. So there's a term called any layer HDI - I don't know if you're familiar with that term? Basically it means you could put a via anywhere you want in any layer. Nowadays that's done typically by what we call build up technology. So you start with a core of some sort - again it could be double sided, it could be a multi-layer core, and then you sequentially build layers and you only go one layer deep with a laser drill sometimes two - depending on the design - but that's not true for any layer.
Anyway, you go one layer deep you plate, you print and etch, and you do it again and again and that allows you to put vias almost anywhere you want in any layer, the downside is, it's almost like building multiple circuit boards. So the cost really starts to increase. And of course you're putting the board through multiple lamination cycles and that has some undesirable material side effects depending on the material. Some materials can withstand three lamination cycles, some six, some ten, but it is hard on the materials to go through that lamination process, over and over again.
Right.
Especially electric phenolics, which are very common for lead-free assembly, because they're relatively economic and they're also - they also will survive lead pre-assembly, but they tend to get more brittle every time they see a thermal cycle though, so that causes some issues too. So what paste interconnects allow you to do, is change the sequence in which the vias are formed. So instead of laminating drilling and plating you can actually drill, add the paste, and then laminate, so it changes the build sequence and this is important both for the fabricator and the designer to understand what that means. So typically what you would do is, you would take a B stage layer of some sort; you can either drill it and paste, fill it with what we call a postage stamp process or you could pre-tack it, vacuum tack it at low temperature to a core of some sort, or substrate, laser drill through the B stage, apply the paste and then when you laminate the paste interconnects, the layers in the z-axis - you could literally take a piece of prepreg, laser drill it with a stencil or with a Mylar Stencil, I'll talk about how that works in a little bit - apply the paste, remove the Mylar laminate between two copper foils, and now you've got interconnects inside a double-sided cork.
That's cool.
So then if you print and etch that, now you've got a core with connections between the layers with no visible vias; they're all internal. Yeah there's some technology around the paste and again we can talk about that, in a little bit.
So how is it applied - is it squeegeed in?
Yeah.
Okay, just like with a silkscreen?
Well no screen - so what typically what you do is, you apply a 1 mm Mylar mask to the B stage and you tack it simultaneously. Then when you drill through the Mylar and the prepreg B stage to get down to your copper features, then you apply the paste, and the Mylar's your mask, and then you remove that just prior to lamination.
And that stays inside the hole? It doesn't just I don't know the consistency of it. My mind was - pictured it just wanting to drop out of that hole - but it must have some kind of stability?
Yeah it's a liquid and there is a tack right. There are a number of ways to do this, but the most common method is to laser drill, apply the paste, dry the paste... you would do it a second time to top it off and then when you remove the Mylar, the liquid paste stays on top of the paste that's already been applied. Then you dry it again, then you go to laminate.
Does it air dry or do you have to cure it what do you do?
You don't really cure it because it's metal powder - metal powder based - so there isn't really a polymer matrix. Unlike print electronic sinks - which is a again another story - you would just dry off any of the carrier solvent used for the application process. It is a liquid - well it's a paste, not a liquid - but but when you dry off the the solvent that's in it; which is less than 10 percent by weight, then it's just powdered metal and that's how it makes a connection. So think about this right, you've seen a lot of PCB designs - imagine a 32 layer board, which most shops can do, but it's not at the low end of technology. Imagine splitting it up to two 16 layer multi layers right?
A lot easier.
A lot easier to build and then you just paste them together at the end, and depending on the design, you can electrically test each half and only use the good ones. So your risk is light.
Oh, right.
There's a lot of advantages to this. Or what if you want to put together three 16 layer multi layers, or four, or 18 or four 18 layer multi layers - it's been done you know. Now a shop; instead of trying to build a 72 layer multilayer - if they're building 18 layer components - it's a lot more manageable.
Hmm, that totally makes sense. So you explained some of the benefits - it's a nightmare, and you've seen, we've all seen these cross-sections of these crazy stackups with all the sequential LAM and drilling cycles and all of that. And then - and also kind of an unintended consequence you can get, is you can - from a performance standpoint - if you do enough of that right can't you get excess copper on the surface features?
Yes - that's a very good point. So in other words, if you're going through many plating cycles depending on how you break that up and you're trying to meet a wrap requirement, that could definitely add up and make it - make fine line etching more difficult there's a lot of - there are some some drawbacks to traditional processing and then with with an Ormet style process, or a paste interconnect style process, you can eliminate some of those things even with an RF design.
Let's say you have very sensitive surface features and you don't want to play with that layer. You might want to put on the surface finish, the nickel gold, but you don't want to put any additional copper - you want just the original foil copper. You could do that with this paste because you could create that as, almost like a double sided board, and then bond it to the rest of the stack up at the very end, and you're done.
Interesting. So I think you mentioned too, there's some good signal integrity benefits, did we cover that I don't recall?
No, so one of the things that a lot of designs call for is something called back drill. So you're familiar with that, so you do the back drilling to get rid of the unwanted copper. So again, in my earlier example let's say you're connecting layer 1 and 10, and let's just say it's a 22 layer - 26 layer multi-layer. You're going to have a lot of extra copper metal in that via that you really don't need or want. So common technology is to back drill down to layer 10. Now of course drilling to that precise location or depth, to remove the copper up to layer 10, but not beyond. It can cause a reliability concern that's a bit of a challenge. So there's those issues.
What you can do with the paste technology is let's just separate that board at layer 10, and not put a via on that half that goes from layer 11 to whatever the other layer is and you're done. So you can eliminate back drilling and the parasitic effects of having that extra copper and the via so that's another application. So there's some signal integrity benefits, there are some RF applications, there are some high layer cap, multi-layer applications, but also many layer HDI applications; it really depends on how you design it and use the paste.
So if you're a designer what kind of design considerations do you need to make up front?
Okay, my recommendation would be is: think about the design, think where it would make sense to split up the layers and provide the most design benefit. Generally speaking, we like the via to have a one-to-one or less, aspect ratio. Now that might sound restrictive, but it's only in that one B stage layer.
So then that's an important consideration. So in other words, if I have 5 mm of B stage, I won't want my via to be 5 mm or larger where I'm going to apply the paste. It has to do more with the paste physics and how it fills the via and then of course the pad, the receptor pad that you're putting the laser drill via on, needs to be a sufficient size for where the paste doesn't have the opportunity to run on one side or the other of the pad.
So we do like an annular ring around the via, that's going to have a lot to do with how well you can register your laser drilling, usually that's pretty good. The other consideration is, the B stage you use, spread glasses - bringing up spread glass again. Spread glass is good, because it tends to keep the paste corralled, whereas if you have an open weave and that prepreg resin's melting and flowing and during the lamination cycle the paste could run to that area. So spread glass is better. Higher viscosity resins tend to be better. We like low flow prepregs. So those are some of the design considerations.
Another design consideration is - and I've seen this happen before - where if you have a ground area and you're making a lot of paste interconnects along a wide track. You don't want to put the paste interconnect to the edge of the track because what ends up happening is, during lamination, the resin wants to flow off the surface of the track down the sides to fill - hydraulic effect, and it's going to move the paste with it. I've seen vias actually move during lamination. So just some common-sense things. Keeping in mind that it's the B stage where your interconnect is. You want to make sure you put that in some good locations, and in that particular case all they had to do is, go back and shift the vias a little bit to one side and then everything was fine. So it's just those kinds of things. Certainly they could contact us, we can give them some design hints and I can give you some literature to go along with this video or podcast.
Yeah, yeah, very good. Ormet and the paste interconnect - paste sintering - has been around for a little while. What's been the sort of acceptance of it industry-wide? Is it being widely accepted, is it just on certain applications?
It's been around a long time. It was primarily used for quick-turn mic review work, and also large format boards where you're literally stitching very large boards together so you can - again the idea is you can make boards that are nearly finished and then electrically interconnect them. The nice thing about the Ormet paste is it doesn't melt at reflow assembly.
Hmm, so it changes chemically right, so once the sintering is done then it doesn't change, then it doesn't morph and heat?
What attracted us to this technology over some other paste interconnects - because there's other processes where you would apply a paste of some sort and then make a connection with pressure in the z-axis - but what interested us in the Ormet material is: the paste melts at one temperature and alloys - so the paste is basically copper particles with a tin alloy powder. When the tin alloy powder melts - and the melting starts at about 130° Celsius, it starts reacting with the copper and forms an alloy with the copper instead. What's interesting about the Ormet material is, it's alloying with the inner layer coppers as well, on the PCB layers. So we have a metallurgical joint, not just a pressure or contact connection.
So it's - and unlike, the tin lead or lead-free alloys and solder, the melt - the new melting point, when it forms an alloy with copper is one phase is 415°, the other is 630° Celsius. So it's not going to remelt that assembly. So it's a permanent connection, so really the paste applications from other technologies like flip chip and whatnot packages where you didn't want to have a secondary or - if you have a secondary reflow operation - you didn't want to have any more remelt. It has some applications there. Or a down hole assembly is another application where the board might be subjected to the temperatures near the solder melting point is another good application for this material.
So that's what interests us because you know when a board's in use, it heats up the z-axis expansion with other types of pastes interconnects, you have a resistance change every time the board is heated even from, let's say 40, 50, 60° Celsius in normal use, not even in any kind of environment - parts of the board would heat up from the components and you'd have a change in resistance, and that's what this is designed to circumvent because it forms that metallurgical bond with the copper inner layers.
Interesting.
So yeah it's a different technology than the paste you would use in printed electronics.
Okay well that's been fascinating. Again I feel like a newcomer to old technology but - and I've known about Ormet that I think got acquired by Merck now, but I've just never had someone sit down and explain it to me. So thank you for doing that.
90 layer multi layers people are getting - 90...
What!
Yes, 90 layer multi layers with paste interconnects yeah.
That's crazy, I didn't even know a 90 layer board existed I guess.
Yeah I've only really seen them into the 60s I guess personally, so.
Yeah you know, one common design was a 72 layer multi-layer, again made out of eighteen layer components, and one of the things with the chip tests the ATE companies, they built some high layer count multi layers and you need a lot of IOs, there's a trend to go to wafer level testing were you’re testing the entire wafer. You need lots of interconnects and that's one way to get there, is to use the Ormet paste to put in lots of layers. So we're seeing more interest in it lately, and I think that's one of the reasons why the technology hasn't taken off until now, is because there just wasn't the demand.
Right ahead of its time maybe a little bit...
Yeah.
Well, I know you've shared with me some cross-sections or I think you did, and so please be sure to share those with us and we'll put those up on our website and we can share your website and Ormet or Mark's website, so the designers can get more information. Is there any place else besides your two websites that you would recommend for more information?
You know I've mentioned HDPUG (High Density Packaging Users Group) in the past - they're actually contracting some PCB manufacturers to make some HDI test vehicles with paste interconnects. So there's going to be some data - anybody who's an HDPUG member will have some access to some really good reliability data and they're pretty complex boards so it'll really push the technology but for breaking up big thick and ugly PCBs, that's pretty well-established.
Yeah very cool. Okay well thank you. So tell us about that fish on the wall behind you?
[laughter]
So it was a gift from my sister, actually it's made from recycled materials so there's an old PCB cut up on there, and the old spark plug wire, and a few other odds and ends. Some artists put together actually I didn't buy it; my sister bought it on Catalina Island and somehow we went out there as a family trip and somehow she smuggled it off the island and gave it to me just before she headed back to Virginia. So it was kind of cool.
Oh that's fun a good throwback to your diver self.
Yeah so - just the last thing on Ormet, is 'paste don't plate'.
[laughter].
Is that their tagline or is that yours?
Actually that's their tagline. We were sharing it with the IPC shows, but another nice benefit to the Ormet - which I didn't mention earlier is - there's no electrolysis, no plating processes in these interconnect layers so it circumvents all that.
Which is like bizarre for me to think about but...
Yeah but if you're capacity constrained, no plating, that's another benefit.
Well thanks again this has been really good. If you have anything else juicy to share with the listeners just email it over before we get this one up.
Okay.
And thanks again for this one. Now I know we've talked about exploring down the road a little bit on copper foil, integrity issues, and also printed electronics. So I'm sure I'll hit you up again soon Chris.
Yeah definitely. I would like to talk about some of the material science behind printed electronics and I know you guys are working on some new design tools and print electronics; there are a lot of different ways to use that in electronics... I should back up, but there's a lot of different ways to use conductive inks in electronics there are so many different versions of the inks.
Which is another subject I know nothing about so it'll be good. I'll be a student with our listeners and, I know they're out there, I know what conductive inks are, but as far as all the applications, all the different materials available, that just seems like something that's in writing a lot, that people are really turning towards a solution.
Lots of new technologies are coming out in that space and it's going to be fun to watch it all.
Yeah yeah it will be.
Okay Chris, thanks for another good podcast and we'll see you soon.
Thanks for having me.
My pleasure. Again this has been Judy Warner with the OnTrack Podcast and Chris Hunrath from Insulectro, we'll see you next time - until then - always stay OnTrack.
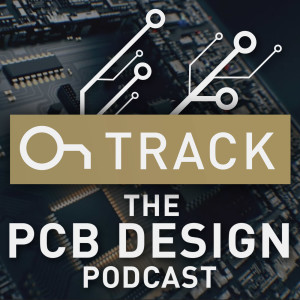
Tuesday Jun 12, 2018
Flex and Material Sets with Chris Hunrath
Tuesday Jun 12, 2018
Tuesday Jun 12, 2018
The rise in flex applications across all industries from medical to automotive, aerospace and military uses means more opportunity for material suppliers to innovate and meet demand. Here what industry expert Chris Hunrath has to share, from general guidelines for designing circuits unique for flex and materials that can be autoclaved over and over. Listen in to this week’s OnTrack expert to learn about flex and material sets.
Show Highlights:
- Medical applications (i.e. instruments for surgery), automotive, aerospace, military
- Foils - as you go thicker, its harder to make electrodeposited. More bend cycles out of rolled and yield
- General Guidelines for designing circuits unique for flex:
- In general, avoid circuits making turns or bends in bend/flex area - don’t make the circuits go in different directions there and also avoid plated holes in those areas.
- From a stackup standpoint, balance the construction. Thinner is usually better.
- Look for opportunities for cracking at the bend point.
- Cross hatch ground planes have multiple advantages.
- Pyralux HT, DuPont - new product with unbelievable thermal performance. A continuous operating temperature. Imagine a flex circuit that can be autoclaved over and over.
- We are a material sciences company. There are really unique ways to put these building blocks together.
Links and Resources:
See all the show notes
Hi everyone this is Judy Warner with the Altium OnTrack Podcast. Thanks again for joining us. Today we have another incredible subject matter expert that you'll be familiar with because we've had him here before, which is Chris Hunrath from Insulectro and we're going to talk about flex and material sets and all kinds of really great things. So hang tight for that. Before we get going please, I invite you to connect with me on LinkedIn, I share a lot of things there for designers and engineers and on Twitter I'm @AltiumJudy and Altium is on Facebook, Twitter and LinkedIn. Today Chris has some Show and Tell and so I encourage you if you - Chris will take time to describe what he's showing, but if you want to see it, feel free to go to our YouTube channel at Altium, click under videos and you'll see all our podcasts there. And you can click on this podcast and then you'll be able to visually see the materials and things that Chris is referring to today - and that's always available by the way - on YouTube so we record simultaneously in video and in audio so just know that's always an opportunity there for you.
So Chris, welcome back, thank you.
Thanks, Hi.
Thanks for joining again.
So at the end of last time's podcast, we were talking about the rise in flex applications and sort of the increasing amount of business actually Insulectro's doing around flex materials, new materials are going out so I really wanted to take this opportunity to learn about what is driving this uptick in flex, what applications are driving it , what the cost, performance implications of that is, and so let's just start with what is driving this uptick in flex?
So a lot of it's medical, you know, and the way electronics are finding their way into medical applications. Actually it's everything, it's automotive, it's aerospace military - military has always been a big user of flex, but of course you know, all the new inventions that are used in medical applications - certainly some devices are implantable and that's something that's not new, but then we're seeing a lot of applications where instruments are being created that are used, for surgeries and things and they use flex circuits and that's because you can make things very small which is always an advantage when it comes those applications and we're even seeing some applications where the products are reused. They're being sterilized, autoclaved, what have you and then they're being reused. But lots of new techniques, lots of new devices being developed using flex. Most people are familiar with traditional flex applications like your laptop screen, very often the interconnect between the main system and the screen is a flex circuit. You know the old flip phones all had flex circuits, your inkjet printers had a dynamic flex circuit between the printhead and the actual motherboard and the printer, and actually that's something I do want to point out is, you know we describe flex applications in two main buckets. One is dynamic flex and the other is the flex to install and it's just exactly what it sounds like is flex to install. Typically you're only bending the circuit once or twice to fit it in whatever it needs to go into and then that's it. Whereas dynamic flex, the part’s flexed in use many, many, many times.
I think that something that most people can relate to because you can see it, is the flex inside copy machines right, you can see that dynamic flex moving again and again and so are the materials - the entire circuitry is rated to have X amount of dynamic motions for the life of, it or how does that work?
Yeah actually that's a pretty good point and that can become very complex. A lot of it has to do with layer count, the base material. You know the most popular base material for flex circuits in reflow assembled PCB - a little different than printed electronics applications - where you're using conductive adhesive, but if you're doing reflow assembly, the most common material's polyimide film, and one of the most common materials is Kapton, but the thickness of the materials, the type of copper circuitry, the thickness of the copper foil - all those - play into a number of bend cycles even the type of copper, whether you use rolled annealed, which is very common in Flex, versus electron deposited-
Okay
-well that can get very complex. There are some good design guidelines out there by IPC and others you know. Again I always shout out to the board shops, some of them have good teams that help people choose the right construction, right stack up to get the most bend cycles out of the device.
Are those the two most common types of copper used in flex by the way Chris? Is a rolled anneal an electroless?
Oh it's electro- deposited.
I'm sorry electro-deposited okay.
Yeah - and yes but unless you're dealing with very thin foils rolled annealed is the most common. That's what we call 'RA foils' the most common. Actually I have a sample here. This is some Pyralux clad. You can't see the dielectric inside, but it's got rolled annealed copper on both sides and it can vary from - you used to be limited to half ounce or 18 micron and thicker so a little side note on foils: as you go thicker it's harder to make electro positive foils because it's more plating time on the drum. With rolled annealed it's the opposite, thinner foils are harder to manufacture because you need more rolling processes to make the foil thinner and thinner and thinner.
I see.
You used to be limited to 18 micron or half ounce, now we can get rolled annealed coppers thinner, down to 9 micron or quarter ounce. You can get a rolled annealed, but the structure is much better for flexing because the grain boundaries are in this direction platelet-type, overlapping grain boundaries which is better for bending. Any foil boundaries are like this and if you bend it you can cleave the grain boundaries in. You get more but it's not that easy - foil doesn't work and flex but you typically get more bend cycles out of rolled annealed.
Okay very good. That's something actually I didn't know and it's something I've talked to my friend Tara Dunn, who's in flex - and it's just something that's never come up so I think that's kind of an interesting point. So, you mentioned with military applications - because my background - military was always SWaP right, Size, Weight and Power - so are those the same type of things that drive the other applications - obviously in smaller spaces - we can fold things up on themselves and get them into smaller packaging. When you talk about the dynamic, what other kind of things sort of drive the desire and the fit for flex?
So something that's applicable to both military and medical, is you want to reduce the size, so I have here - this is a 50-ohm SMA coax right. It's basically one circuit, you've got the shield layer, the shielding around the center conductor - but this is one channel or one circuit and I have here flex, and you can see how many circuits you have on this piece. So, imagine if you had to have one of these - for each one of these-
For each channel right.
Now if you - depending on the design, whether it's strip line, micro strip, and whether or not you have in-plane shielding, it might be every other one's a signal. But still the weight and size is the difference between having cables right, which I'm holding up right now, versus having a flex circuit is huge right.
And in the case of medical, some of those traces can be as narrow as 20 micron. So you can fit a lot of circuitry into a very small space. And you know depending on the on the medical device. We see some of our customers will build circuits that are very, very long and very, very narrow, and you can imagine how they're used in surgery and other medical applications. And you might have twenty circuits on that part but it's in a very, very, very small space.
Oh that totally makes sense.
Now - just to be clear 20 micron circuitry - it’s not easy to do, it's doable, not easy to do, but certainly 50 microns is, most board shops can do that these days and again you can fit a lot of circuits in a small space and of course they can flex, they can bend. But in the case of rigid flex where you have a rigid part and bridged with a flex part - and here's another example where you have this - is not necessarily rigid flex but you'd have components here and then a connector here. You're replacing all these cables right, of this section, so that's how it drives weight and space and even reliability. Fewer interconnections tend to be more reliable so that really helps. So flex has been growing quite a bit for us, for our business and so, a lot of its based on DuPont Kapton and DuPont Pyralux products and then they - there's a B-stage system for laminating the different layers and of course the core, or the clad material as the foil on both sides and then our customers will print and etch to whatever pattern they need and put those layers together as building blocks.
Right so let's talk a little bit about design for flex since most folks listening here will be engineers or layout folks. What are some things that people need to keep in mind about designing these kind of circuits that's sort of unique to flex?
So there's a couple of good - again some good guides out there - both by IPC, DuPont has flex manuals, for different types of categories. Whether it's multi-layer, single sided, double-sided flex, they have some good guidelines on that, but in general what you want to avoid is you don't want circuits to make turns or bends in the bend area. So, for example, I'm going to use this one is an example again.
Okay.
If this is the flex area in this middle section here, you wouldn't have the circuits go in different directions in that area, so you might want to keep them. You want to keep them basically parallel in that area and you also don't want plated through holes in those areas. Again these are just real general rule - basic guidelines. The other thing you want to avoid is what we call an I-beam effect, where you have circuits directly above each other with a dielectric in between. You want to stagger them. That helps, again - more important for dynamic flex than bended, to install, but it's important not to have the I-beam effect because that could lead to cracks...
That makes sense.
-concentrates on bending. And in general from a stack up standpoint, you want to try and balance the construction. Thinner is typically better. There's again - there's all kinds of iterations there's - if it's a multi-layer flex - there's loose leaf constructions where you wouldn't necessarily bond the different layers together in the flex or bend region. You'd have them not connected. A bookbinder system is another way to do it where depending on the direction of the bend, the layers that are on the outside of the bend are actually longer. The layers on the inside - and again the fabricators that are skilled in that know how to space that - and to change the length of the circuit. But you know from a simpler standpoint, or from a more general standpoint thinner is typically better balanced. Balanced constructions are typically better for flex.
Well balanced construction is always a good idea, I'm just saying but I could see that right. Because I think you - what you're saying if I'm hearing you right, is you have to look for those opportunities for cracking right, or stressing at the bend radius, because that makes sense right. Just from a physics standpoint it makes sense that things would want to give or pull right?
Right, when you bend a flex circuit the other side compresses against it right, and every circuit will fail at some point. It's a matter of how many cycles you get out of it before it fails.
Right how do you measure those cycles by the way?
Well there are some standardized tests and there's an MIT bend test - there's some other testing that's done to see how a particular material, or even a design or stack up performs where it's bent repeatedly until you get failure. And then you can - you can rate the stack up or the and/or the material.
Where can you get that data? You mentioned IPC as a source. Is there any other thing - resources you could share - that I could share with the listeners where they could maybe look at some of these readings?
Yeah actually so DuPont's website, the Pyralux website, has some data on that and certainly some of the folks there could put your listeners in touch with some of the design guidelines.
Okay alright I know some folks there if you and I can't find him through the website then Jonathan just came in to talk at IPC designers Council Orange County I'll reach out to him see if...
Oh Jonathan Weldon, yeah he's a great resource for that. So speaking of Jonathan Weldon, he's been working with HDPUG; they've been looking at shield layers or for reference planes and they've been looking at the difference in solid planes and cross hatch systems, and so this is just a simple - this is actually a simple test circuit microstrip construction where you have a reference plane on one side and your tracer on the other. Imagine if there were a strip line construction and you had copper on both sides with your transmission line in the middle, one of the challenges with all PCBs, and especially with flex, is absorption of moisture and then that moisture released during assembly causing delamination and one of the things that you can do to mitigate that is to bake the parts. Well if you have soft solid copper areas - baking does not work as well - because the moisture has got to go around the copper it can't go through it.
Right.
So cross hatch ground planes are great for two purposes. One is, it's a moisture egress for baking, the other advantage is it's actually better for flexibility it makes the part more flexible.
Hmm, that makes sense.
The downside is the high frequency applications - you can run into some issues.
Yeah.
So and one of the interesting things that Jonathan and company, they were looking at, was the difference between a round opening and a - what's typically used as it's..
Kind of a diamond shape?
Exactly, exactly and really it's more of a square turned on its side, but yeah the diamond shape versus the you know... It's funny how a circuit design is always in orthogonal patterns but that's not necessarily the best way to go and anyway the round shape was better for signal performance.
Oh, for the high speed applications?
Yeah it makes sense because if you took a circle that fit inside a square you actually have less open area so...
This is true okay, alright.
Yeah, so there's some interesting data on that but I would recommend to a customer, depending on their their frequency bandwidth bit rate, depending on what kind of design it is, that they would look at using an open plane. It works basically with a screen, for lack of better words, versus a solid plane because the reliability goes way up.
Okay now you just made me think of something. Last time we talked, we were talking about prepregs and glass, being reinforced right. When you're using adhesive systems for flex, I'm assuming they're non-reinforced?
Right.
It's a more stable material though so tell us a little bit about that, about the stability, the dimensional stability?
Yeah so - so really in flex circuits the Kapton film, a polyImide film, because it's a thermoset, it is acting like the fiberglass in your flex circuit.
Okay.
You don't have skew issues because there's no glass, so you don't have micro-DK effects. Now if you do have a crosshatch plane, you will have a different - you'll have a micro impedance effect if you would. But that usually doesn't change with differential pairs unless - again depending on where you put the traces - but you don't have the fiberglass micro-DK effect at all. Now, Kapton's interesting - it's very thermally stable but it's not as mechanically strong as glass reinforced laminate. So it tends to change more from mechanical distortion than it does for thermal. It's not shrinking like epoxies do when they cure. Certainly when you - when you remove all the copper (and I actually have a piece here) this is a piece of Pyralux AP, with all the copper etched off. This is 100 percent polyimide, used to have copper cladding on it and the copper's been mostly etched off. You can see a little bit of copper left from the tape I use to run this through an etcher, but the material is pretty strong but it can distort mechanically, more so than thermally. So again this is kind of like the fiberglass in a regular PCB, and then you'd have B-stages of some sort, to put all the layers together.
So the actual substrate is creating the stability in the case of flex? Okay that makes sense.
It's a polyimide film, in the case of Pyralux, which is a DuPont branded flex material it's based on Kapton film.
Okay so we talked about ground planes, we talked about where to not put - - is there any other sort of design for flex things that you'd want to mention that are just rather commonplace?
Yeah so there's a lot of things, for example, you could use a pad that's a little bit larger than you would normally use that would go underneath the cover. Now let me backup a little bit and talk about cover lay. So what cover lay is, it's basically Kapton adhesive laminate, that is the flexible equivalent of solder mask. Now unlike solder mask which is used in PCB, which is photoimageable, cover lay has to be mechanically formed and then laminated over the circuitry. So you have openings and this - again this is a another good example - you have openings in the cover lay I don't know if you can see that on this? But there's openings on the cover lay for each individual pad and then that's laminated over. One of the ways to get more reliability out of the pads is to make the pad a little bit bigger than the opening in the cover lay. So you have cover lay over the perimeter of the pad - it's kind of like what we call solder mask defined pad and rigid - except you're doing it in flex, and that's that's one way to get reliability. But there - again there are a lot of different things in flex that you should be aware of, and that's where some of these design guides and things...
Okay well we'll try to track some of those down and put those in the show notes because I think that would be really helpful to have something kind of, tangible. Something I remember learning from someone else, is also talking about tear dropping pads?
Yes. Is that something that you would recommend as well?
Yeah that's good for a couple of different reasons. One is that the more material that goes under the cover lay, again helps mechanically support the pad. It's also important - typically you don't put holes or pads into your bend area, but it could be an area where you could concentrate bending. So in other words, you go from a trace to a pad, that's going to become a concentration of - right at the edge of the pad - concentration of stress and so if you do the teardrop, that distributes that stress over a larger area and helps prevent circuit cracking. But again, you would try and avoid that in your design. We would make that a bend area. And actually, speaking of rigid flex, one of the things that you would typically do is the cover lay would go into the rigid portion only 50 mils.
Okay.
-Okay and then you would keep the cover lay and its adhesive out of the plate through hole areas in the rigid portion and rigid flex - and that's also a 'keep out' region for plated through hole so you wouldn't want plate through holes going through that region. So again a lot of this stuff is spelled out in some of the manuals that you get from DuPont and others.
Alright, I'll reach out to Jonathan and - and you and I can scrounge up some things and we'll make sure to include those here. Last thing I wanted to talk to you about - which I was just stunned by - is that you told me that DuPont has come out with a new material that has unbelievable thermal performance. Can you tell us a little bit about that?
Yeah so - classically in flex, you have your your B-stage, or adhesives that are part of the package, and then you have your core materials, which are your building blocks and you print and etch your core, just like rigid, and you would have - you would put them together with either your rigid or your flex adhesives to make a multi-layer system. What's different about this new product, it's called Pyralux HT, and in fact, I got my Pyralux HT mug here...
Nice, nice.
-but instead of using acrylic or epoxy adhesives to bond the Kapton layers together, you would use this thermoplastic polyimide layer. It's got a very high melting point and thermoplastic's already used in PCB, people familiar with EPI-P and LC, those systems. The only way thermoplastics work in PCB, or reflow assembled PCB, is to have a high melting point otherwise it would melt at assembly. So this is a piece of the thermoplastic polyimide that DuPont manufacturers. It's the HT bonding film. This could either be a cover lay or it could be an adhesive layer to put - to make a multi-layer PCB.
Okay.
-But the nice thing about this, is it has a - 225 Celsius operating temperature, which is very, very high.
What does that convert to in Fahrenheit?
Oh gosh - 225 C it's over 400 degrees Fahrenheit.
I see, 225 - - Fahrenheit okay I wasn't hearing you correctly, so it was Fahrenheit okay.
Oh no - hang on, 225 C, I should know all this without me - - 437 Fahrenheit.
Wow.
So you know, some applications...
-and that's an operating - continuous operating temperature? Which is crazy, cuz some materials can take that heat for a little while but not continuing operating temperature right?
Right, so most PCB materials that go through a reflow assembly, which is either done at 260 Celsius, depending on the type of solder work, or 288 C, they can withstand that for a short period of time most PCB materials survive that. It's the operating temperature most epoxy systems will come in around 130 to 150 C operating temperature - maximum operating temperature.
That's wild, so I'm guessing - so what are the applications where this will be exciting news?
So applications where you had, fiberglass, coax or some other applications like that where you had wired - high temperature wired connections - or cable connections, you could replace now with a printed circuit board. So engine compartments, aircraft engine compartments, aerospace, down hole, I mean there are a lot of different applications. Even from a medical standpoint. Imagine making a flex circuit that could be auto plated over and over and over again. You don't have to worry what's gonna...
I was gonna ask you about that earlier. I don't really know what temps they autoclave at but you mentioned that before that medical applications could - to cut autoclave to kill the bacteria, but like what's the normal temp of an autoclave, how many times can you do that?
So we have one customer that builds some parts that are autoclaved at 135 C but it's with steam, and it's hard on circuits, it's hard on electronics.
Yeah seems like that would be.
But for HT it wouldn't be any issue because you're nowhere near on the melting point. Now it will absorb some moisture, which could be removed from - could be removed with a bake but a lot of applications it won't matter if the assembly is already done. It doesn't really matter.
Okay.
You know there is some change in the transmission properties of the material when it absorbs some moisture. Again that could be removed with a bake but that is one of the challenges with reusable medical devices, is sterilization and how well the materials hold up, and an HT would be good for that. The downside of HT, is it does require a 600 degree lamination - Fahrenheit.
Okay well there you go, so how many board shops have lam presses that go up to that temp?
So we took a look at our customer base, and it's not a lot of them, or some of our customers had laminate, or have lamination presses that are capable, they're rated that high, but they haven't been turned up that high for a long, long time. So it's funny, some of our customers have started making some HT, all the weaker heaters, that the press might be 10 years old, they turn it up for the first time to a higher temperature; they start popping heaters and they have to go and replace them. But actually we're seeing a trend though. A lot of our customers are buying laminating equipment and right now that's a whole 'nother story because lean times are way out on equipment in general, but what we're seeing is people are making sure they have that high temperature capability and it's not just for something like HT, it's for LCP and FEP as well.
Okay.
They have some good properties, electrical and and signal properties.
They do.
That's a big deal these days.
Performance wise they're very good.
Right they're harder to fabricate but they do have some good properties you know. Even - we talked about last time - repeat glass-reinforced PTFE materials, some of them require high lamination temperatures.
Yeah they do.
Yeah all right. One more material I do want to mention - sorry - so this material actually is a Teflon Kapton laminate it's called...
-wait hold on - Teflon Kapton? Oh okay.
It's called 'TK' - it's a Pyralux product from DuPont and so it has a core of Kapton to act as the XY stabilizer, but then it has a Teflon material on both sides and again, this is a building block but it's very low loss, and very low DK. So a DK of about two and a half with a very, very low loss. But unlike glass reinforced Teflon systems, this has no fiberglass so, no skew and no detrimental effect from the fiberglass. It's using the Kapton instead, as the stabilizer, because if you had a piece of - I should have brought out a piece of Teflon - but PTFE films you can easily - it can be mechanically stretched.
Yeah, one time when I was in the RF and microwave board space, I had the board shop I was working for take all the materials like Rogers, Taconic, whatever and I had them strip all the copper off and I went like the 4000 series 6000 series 3000 series all the way up to 58, 80 and strip off the copper. Because when you see them clad, they don't look that different from each other. But I'm like here's Teflon - this is like a piece of rubber, and imagine heating that up, exposing that to aqueous hot processes and so I think that really helped people to understand how vastly different they are and I think it was a good visual actually to help people understand how radically different these are and when you start stripping off all the copper and you have fine lines and all that then it's - it's a whole different animal.
TK material is - the core material is nice because the Kapton layer does provide mechanical strength. Again though, the TK, instead of requiring 600 degree lamination, it requires 550. So it's still a high temperature product which requires the right press book, the right materials, and lamination, and it also requires a press being capable. And the other too is the board shop needs to get accustomed to the dimensional changes during the lamination process with these materials.
Right.
Again - a lot of it's mechanically driven, but you need to know how to work with it so that's something I think the boardshop needs to have experience with.
Well and I imagine that you're not going to see these materials outside of sort of high performance or high speed capable board shops?
That's true...
-I don't know if that's true I guess I'm looking to you for an answer in there but it's an assumption I would make.
Here's the interesting thing about AP, AP by itself, is actually pretty good electrically. It's the adhesive layers you use that incur a lot of the loss. So then if you get into the thermoplastic systems that have better electrical performance, now you're getting into the temperature range. So it's one of those give-and-take situations, but you can mix and match the materials to some degree. You could use, for instance HT bonding film with AP clads, your operating temperature would default to the AP operating temperature, which is still pretty high at 180 °C, but electrically it's pretty good. You get away from the acrylic and the epoxy adhesives, which aren't great electrically, in terms of loss, dielectric constant so yeah, I think as I think as board shops become better equipped with high temperature systems, you'll see a broader use of these materials.
Right, I mean the market is going to drive us there one way or the other right, if there's a demand then the board shops will do what they need to do. One thing - a comment I want to make about that is - I was in one board shop and I was stunned and then just felt like wow I could've had a V8 moment, is they were providing really high speed, high performance circuits to some high-end military stuff, and they had moved completely away from rigid high performance laminates and used multiple layers of flex materials and the performance - and I'm like - oh well that seems like an obvious, but I had no idea that was even happening. Is that something you have seen, where they just use...
Yeah, if you wanted to get rid of skew completely you could use a film based system.
Yeah it was crazy, I mean that makes sense and I'm sure there's some challenges there cuz I could tell they had to rigidize the bottom, or put some kind of carrier or something, because they didn't want it to flex quite that much but they just stacked these film systems on top of each other and I'm like huh, didn't know you could do that but they were clearly doing it on a routine basis so that was interesting.
Yeah I've seen some board designs where you might have 12 cores of Pyralux...
Yeah,right.
-and then use regular rigid prepreg as a bonding system so and the board's not - when it's all done, it's not flexible it's rigid.
It is rigid, but it's a weird - it's weird to see anyway...
I actually have a board here.
Ok let's see it.
Unfortunately it's single sided so it's kind of like a potato chip, but because there's only one layer of copper and one layer of prepreg, but this is actually DuPont's AP product with Isola's tachyon prepreg, and it's a spread glass prepreg. So you have the spread glass prepreg on one side and you've got the Pyralux AP in the other. So you minimize how much glass is in here, which really drops the amount of impact or micro DK effect which would lead to skew and other signal performance issues. So there are lots of different ways you could use the flex materials even in a rigid design.
Yeah I did see that and I was shocked and I - it's something I hadn't heard a lot about. Anyways well, we're about out of time today, again. But thank you so much, every time I talk to you, I feel like I learned so, so much and it's fascinating to me where the industry is going and what's happening with flex and it's exciting it's really an enabler right and these high, high temp products and that so it's a really exciting time to see. We always break through one way or another it's just interesting to see who gets it done. So it's very interesting to see what we're doing with flex.
Oh thank you Judy for giving us the opportunity to talk about some of the materials we supply but yeah it's - these are all building blocks and, I kind of view it as a material science company in tech...
You are yeah.
-we provide all these different building blocks to meet the need of what the customer needs.
And there is - and there's really unique ways to put those building blocks together so it's fascinating to learn about. Ok so something I didn't ask you last time, but I'm gonna ask you now. Are you a geek or a nerd? [Laughter]
So the best way I heard the two described is the difference between a geek and a nerd is - a geek is the one who gets things done.
Oh interesting okay.
So I would like to think I'm somebody who'd get stuff done, so that would put me in the geek camp but in any case.
Alright check geek, and the second question I have for you: on a scale from one to ten how weird are you?
[Laughter] Oh gosh, I would say - five.
I'm sorry but if we're in this industry we're at least 5 or above. I think we have to be a little wacky to do what we do - okay well thanks I appreciate it so much and again, we were talking on the phone yesterday we have more to cover, so I'm gonna for sure have you back again and talk about printed electronics which is on the rise and you know a lot about. And also I'm very excited to talk about - oh there it is!
Electronics, that's a whole other - whole other world of electronics and yeah.
Wait, wait, wait bring that back and tell our listeners what exactly that is.
So this was printed with a zebra label printer where the - and no changes to the machine by the way - but the special foil is put into the system where you normally put a roller with a pigment film, so instead of printing a black label you're printing metal foil so yeah, it's kind of interesting.
Yes what is that for?
Well this is something did for me at our booth this is just an antenna but you could really you could make electronic designs on the fly now...
Dude, you're still not answering my question here. What is that intended for?
So I'm gonna use that for an antique stereo I have. I have an antique FM stereo the tube, old tube radio, I'm going to use that as an antenna.
I see - oh see definitely five-weird. I say I'm gonna make that matrix instead of the hot crazy matrix I'm gonna make like the geeky-weird matrix and so yeah - you're at least at a five -high and a geek.
But anyway printed electronics is pretty exciting, I mean and again, it's all material science based. As the materials get better you're gonna be able to do more things. Higher conductivity inks, higher temperature inks, I mean there's all kinds of things you can do in that area. Typically the substrates are different - they're typically lower cost, lower temperature capable substrates, but you could - you can make all kinds of things so we'll get it the next time.
Okay we'll definitely do that and the other thing I'm excited to talk to you about - because I know nothing about it - is paste interconnects and you shared a little bit, so anyways we have at least one or two more podcasts ahead of us, so for our listeners; stay tuned and we'll make sure and share everything Chris has talked about today and hook you up with resources through DuPont, HDPUG, IPC, wherever we can find and we'll make sure and share those resources that will help you lay out a better flex and onboard as much information as you can.
So Chris, thanks again, we'll see you next time and we'll tackle another hot topic. Again this has been Judy Warner with the OnTrack Podcast. Thanks for tuning in and thank you to Chris Hunrath from Insulectro, we will see you next time. Until then, always stay on track.
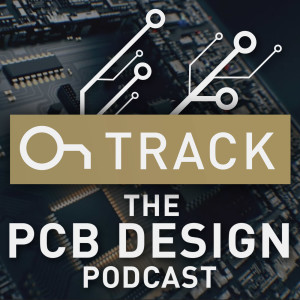
Wednesday May 30, 2018
DFA Tips from Duane Benson at Screaming Circuits
Wednesday May 30, 2018
Wednesday May 30, 2018
Duane Benson from Screaming Circuits shares DFA Tips and a piece of history as he shares the story behind the scenes in developing quick turn prototypes. Listen to learn how one entrepreneur brought fresh perspective to the business that led to great success. And see why Screaming Circuits is uniquely positioned to handle all the leading edge components that PCB designers have available.
Show Highlights:
- Screaming Circuits was founded on the premise to get prototypes built quickly. It was a struggle to get small volume prototypes built and a market need was discovered.
- For prototyping - going abroad invites its own set of risks.
- A traditionally 6-8 week process, Screaming Circuits does in hours.
- We don’t specialize in a vertical industry, so we see a lot of the leading edge components.
- Layout isn’t taught in schools or its self taught. The experts who knew how to make layouts work perfectly have retired.
- We built a business around stuff being wrong. Stuff isn’t going to be right when it arrives to us and we have to fix it.
- Why are we having a problem sourcing parts?
- Personal interests? Photography and decaying industrialism.
Links and Resources:
Downloadable Circuit Talk
Twitter: @pcbassembly, @duanebenson
Screaming Circuits on Youtube
Hey everyone this is Judy Warner with Altium’s OnTrack podcast. Welcome back to another podcast session with us. As always we have another incredible guest with us today but before we get started I wanted to invite you to please connect with me on LinkedIn. I'm very active there and share a lot of resources for engineers and PCB designers and also - I don't think I shared this in past podcasts - but we are also recording this on YouTube as well as just an audio. So you can always go to YouTube and go to the Altium channel, look under videos and you'll find these also in video format if you should prefer to listen to this and watch it in video format. And also with Altium, you can always follow us on Facebook LinkedIn or Twitter and we love engaging with you. We always love to hear from you about subject matter experts or subjects you'd like to hear or learn more about. So, without further ado, I'd like to welcome our guest today who is Duane Benson of Screaming Circuits, out of Canby, Oregon, correct Duane?
Canby that's correct.
So Duane welcome, we've crossed paths for several years now and it's a delight to have you and learn more about Screaming Circuits and EMS and how designers can do things to to be more effective in the design for assembly and just learn about Screaming Circuit’s model, which is a very unique model by the way, I'm eager to jump in.
Well thank you I'm really happy to be here thank you for asking me to participate in this.
My joy. So why don't you start out by telling our listeners a little bit about who and what Screaming Circuits is, because it really does have a highly unique model, and kind of the why behind you guys started the company and created this model?
Well it started back in 2003, actually that fifteen years ago now. Yikes..
Yeah, I know, how did that happen?
So about that time our parent company Milwaukee Electronics they had a number of customers that were struggling to get small volumes of prototypes put together back in the back in the olden days - if I can use that term. Prototypes quite often were sort of slotted in on an ‘as available’ basis. So say you might need five prototypes and the EMS company would say, well we’ve got a big run going on and I can put you u on the machine in two weeks so you can get your prototypes then. And two weeks come along and something else came up, so another week... Even going back before that, back in my day they didn't focus, for example, building a prototype.We'd have a big bag of parts and some blank circuit boards, and we'd hand them to this poor technician on a Friday afternoon and the engineers would go, could you have these built up by Monday?
So it was becoming a real struggle to to get prototypes, get small volumes of any sort built and a couple of our customers came and asked us and said, can you can you help us out with this? It's just not working and the Milwaukee Electronics’ management thought about it a little bit and thought, why can't we short-circuit the process?
No pun intended right?
Laughter.
So the management experimented a little bit and then decided, , there's an actual business here. So back about that time they brought Jared Store out here to start up what they called the Screaming Circuits division to focus specifically on getting prototypes done quickly.
Mm-hmm.
And , from that time the initial focus of the initial business was basically Jared with email and phone and one of our partners Sunstone Circuits, they built the blank circuit boards - the raw fabs. They'd give us a call and say, hey one of our customers needs some prototypes built, can you guys do it? And that's how the business started.
So you guys created the synergy. Now I've had the pleasure of meeting Jared once at least, through the phone and email and Jared was young right? He was the son of the owner so, I have to insert that. Because I kind of love that those of us who are kind of old dogs in the industry - I kind of love that he said, well why can't we do this? And he just kind of, like you said, a phone and a thing and just said why not. Because he wasn't constrained by the way things were done in the past which I kind of love that.
Exactly he was a young entrepreneur, in fact, I don't know if he'll want to admit this but this was his first job out of college this was kind of an experiment for him to get into a career, into business and he did a fantastic job. Basically by ignoring all of the old rules.
I know yeah.
Yeah and then in 2004 - well somewhere between late 2003 and early 2004 - we first went online with a very, very simple quote system. We boiled it down into six different factors and based on that, came up with a quote and it was all kitted at that point. So we'd say, hey it's going to cost you this much, send us your kit, send us your files, and we'll build them up for you.
Now since that time, when we were talking earlier, it seems like it's morphed into not just specifically prototypes but just quick-turn. It could be quick-turn pre-production quick-turn production even right?
Yeah
The world of manufacturing of electronics has really changed in the last decade and a half . There was a time when electronics were not going to be designed and built in this country. Back in the 90s, when I was working for InFocus again, everybody was outsourcing everything and then over the next decade after that, it was all going going away.
Yeah.
And there was going to be nothing but high volumes manufactured offshore. Well about the time we started doing this, coincidentally the open-source hardware movement came about with the Arduino and some of the other things that came with that. Kickstarter showed up and that really changed the hardware design dynamic. It lowered the barriers to entry to building a hardware company and over the last decade and a half the hardware startup has come back with a vengeance. The problem is, as manufacturing is really, really expensive - unless you're doing super high volumes - so these companies would run a Kickstarter, they'd sell a thousand of an electronic board and nobody would build it for them. So then, , they'd then run off into into Asia and they toured all these shops and these people would either say, no that's not enough or they’d change the design, steal the intellectual property and, you can't. There's little details like that so, getting a hundred or a thousand or five thousand is extraordinarily difficult. And yet there's an awful lot of companies that sell just that many of something.
Yeah, it's really interesting that it morphed into that niche right?
Yeah.
You had, it sounds like you had everything, in place to fill it right? You'd built it to do address prototype - traditional prototypes - and as the market changed you were kind of ideally positioned to address those kind of start-up Kickstarter things. So you and Sunstone have worked together in parallel, I take it throughout this process?
Yes they've been our partners since the beginning, and at this point they build the vast majority of our circuit boards and we do, if necessary, go elsewhere. Or if a customer sends us the boards or requests something else, but the vast majority of our boards are built by Sunstone. They're about ten miles away over in Mulino Oregon.
Another big city like Canby…
Laughter - well compared to Milano Canby is the big cities...
Yes well it's a beautiful area. So, tell us about what you would see in a given day and then I would like to ask you to jump into speaking to designers that may be listening, and go into kind of some DFM tips and tricks. But before we do that, tell us about what are you going to see in a day?
To get a picture of what happens there at Screaming Circuits there's two factors that are pretty important. One is a traditional EMS company. We we see about as many different jobs through here in a week as a traditional medium-sized EMS company we'll see in a year.
Wow!
And the other factor that's important to notice, is that in - using that term the olden days - getting a quote and an order for a project might be a three to four week process going back and forth with all the files, component availability, making sure the design works and then after you place the order, you've got the NPI process which is another three to four work weeks. So, you've got a six to eight week process that we do in six to eight hours.
How is that possible? I mean we may not have enough time here Duane, but I've been in the EMS industry and it’s an extremely complex process, just getting the components you need and making sure they're right and there's not obsolete parts, and that you've got a clean BOM, and it's so complex. How have you condensed it without giving away your secrets?
Well there's a lot of things that matter if you're building a hundred thousand of something or a million of something. At that point fractions of a penny count and you're going to spend a lot more time quoting. You're gonna have to worry about getting large quantities of components if you need 20 of a board you can go to Digi-Key and get the parts for a buck, that would cost you a quarter of a penny if you bought them at high volume, and that's still fine now, that's part of it and then you don't have to worry about some of the inefficiencies that would absolutely kill a high-volume manufacturing manufacturer. You don't have to worry about those because if you have to tweak things by hand, while that is more expensive per unit, if you're building 20 or a hundred or a thousand it doesn't matter quite so much. So really what we've done is, we've stepped back and we said, what is important and what is not. The objective is to get working boards into an engineer's hands as quickly as possible and you'll notice there aren't things like how do we make it the absolute least expensive, or things of that sort, it's about getting the working board's as quick as possible so you focus on just the things that matter for that.
Right, you mentioned when we talked a few weeks ago, about it becoming what you had called a transactional model, which is really a different industry and you can go online, place your order in a very transactional fashion, but it also speeds up your time to market, and gives you something highly valuable?
Yes it does, we don't we don't spend an awful lot of time on the financial component of it. For the most part you give us a credit card and we start building so we don't have to worry about the bank component of it. For larger companies we do, because some people, the government or whatever, they have to operate that way. But for the most part you just give us a credit card and that again cuts some time out of it. We also look at each order as an individual transaction, that's why we call it transactional manufacturing, or unforecastable. We don't have to worry about the fact that you're not gonna need exactly 500 every month for the next 24 months. In traditional EMS, you have to worry about that, you plan for that. We don't worry about that, we don't care.
Yeah it's interesting as well it's neat model and I see it as a real enabler. So, congratulations to you guys. All right, let's dig in and give our listeners that are designers and engineers some tips around DFA. The way that you and I originally came to know each other is, I had been blogging and writing and then I came across a little publication you put out called Circuit Talk in which you were doing what I was doing, which was giving designers some really immediate tips to apply to make their jobs hopefully a little bit easier and so, I think you've done a really nice job of that. So can you talk about why you started Circuit Talk and then go ahead and share some of those tips or tricks that are around design for assembly that's gonna make designers’ jobs easier and smooth the time to deliver a good product in time to market.
Well thank you. You know the volume of jobs that we get - it does lead to chaos of sorts - but it also is a huge advantage in that we get to see every single mistake that anybody's gonna make. We don't specialize in a vertical industry so we don't only see mistakes related to a certain type of component tree. Name a component that's leading-edge, we've undoubtedly seen it and, so we see these things - and it's not just beginners, it's not just experienced designers, it's not just big or small or university - everybody makes the same mistakes. It's so complex and there are so many variables, so many new types of components. Geometries are shrinking and in parallel to that people have less and less time to design these things. Quite often layout isn't taught at schools, or it's self-taught. The experts who knew exactly how to make a layout work perfectly have retired now, or they've been let go, or things have changed so fast they can't keep up.
Mm-hmm.
So we see these problems every day. Case in point, one that I write about quite often relates to the QFN Quad Flat-Pack No Lead, and then the DFM. The DFM leads along one side. They have this big metal heat slug in the middle, looks like a very simple component, it's cool, it's small, has great signal characteristics. But most of the CAD software, when you try and use a QFN, the footprint is wrong. It comes from the library with the solder paste layer, not designed specifically for the component, so you've got to imagine flipping a QFN upside down. You've got a little row of contacts around the outside - very small - and then a big giant heat slug in the middle that covers almost the entire component. So most of the library components we found have a full aperture opening, so the solder paste layer is completely open for that heat slug in the middle. And what happens is you end up with too much solder in the middle, so the part floats up and the connects on the side don't connect.
Oh boy.
Yeah and this is even more prevalent with some of the open-source CAD software, or some of them with a lot of user-generated content, nobody told those folks how to make the footprint properly.
I see.
Quite often the manufacturers, in their data sheets, even specify it that way. But what you need to do is, to modify the footprint so in that center pad, you get somewhere between 50 and 75 percent paste coverage. So, you take out the default paste layer for the center pad and you put in a little windowpane-looking thing - problem solved.
Interesting. Yeah it's a little scary, unless you have a partner that's on the ball to what you can accidentally pick up off a data sheet or how to interpret that data right? So okay well, that's a good one.
Another one we run across these tiny little micro BGA's 0.4 mm pitch, some of them even 0.3 mm. I've actually seen a 0.24 mm pitch BGA. Yeah, some of the rules change with the bigger BGA's. You want non-solder mask defined pads, so you want the solder mask opening to be slightly larger than the little pad where the BGA ball’s gonna sit down.
Yeah.
With some of the 0.4 mm pitch BGAs, you want solder mask pad or defined pads, otherwise you get bridging.
Oh yeah, that makes sense.
Yeah, it kind of depends on the geometry of the solder ball, but that's a pretty common error as well. So you see these things that component manufacturers haven't fully studied, haven't fully published and they are just setting people up for problems.
Yeah, and what I have found - and not just in relation to components - I have talked to people who manufacture either components, or they manufacture laminates, and what's not widely understood is that sometimes the studies they’re doing is us.
Yeah we’re their guinea pigs.
Yeah, and then we yell and scream and we give them back data and then they produce overtime accurate data sheets. I was stunned to hear that, but it's absolutely true. They need to get stuff to market because the market is demanding it, and the testing is so complex and so widespread, and the applications are so widespread, that they can only go so far. And then the rest of the data has to come from real world.
Yeah the the hardware industry really is paralleling what the software industry did. We had open source software then open source hardware. With software, we started calling it ‘beta test the world’ because you couldn't beta test anymore, it's too complex.
Right, it’s too complex, so we become the beta testers and I don't think that's often understood. When I first understood it my jaw about dropped because I'm from the old school, like you are and it's like; wait nothing would ever go out that was not fully vetted or understood and tested, and things have just gotten so complex. And so there's just a hard limitation there, it's not a bad business practice or whatever, but it's a reality that I think is wise for designers and engineers to keep in mind - another encouragement to work closely with people like you, that can say, we've seen this already a bunch of times, we know what's going to occur here.
Yeah we've built our whole business around everything being wrong basically, start to finish. It sounds kinda funny, but It's all about this stuff probably isn't going to be right coming into us, so we've got to figure out how to make it work.
I don't know, like what happened to the world Duane? This is not how we started but here we are. Another thing you talked to me a little bit about, you had mentioned one time in a conversation, about polarity markings.
Oh yeah. That's that's maybe third or fourth in terms of the issues that we see here with diodes especially. Capacitors somewhat, but diodes even more so. Any kind of ambiguity, when you're dealing with machines, it's a problem. If you've got a barrier diode for example, it's backwards from what you would consider a conventional diode. So if someone marks it with a plus and it's a barrier diode and they're expecting us to know whether the plus goes to the anode or the cathode, we're gonna put it in the conventional manner, not knowing it's a barrier diode it's gonna be backwards so you can't use a plus to mark a diode. You might think minus, Also, does that mean negative or is that the lion on the diode symbol you can't do that because it doesn't tell us anything you've got to say K for cathode not C - because then we might think it's a capacitor, or the full diode symbol the down - lot of people will put in silkscreen, the mark that's on the bottom of a surface mount diode...
Uh-hu.
-which at first glance seems like it makes a lot of sense - but only if you give us the exact diode that you got the marker off of. I've seen two diodes 0.603s in the exact same package from the exact same manufacturer just a couple characters off, in the part number, and literally, on one the mark is the anode mark on the other it's the cathode mark. I've got to I've got to do a datasheet and I have a clipping from that data sheet on the Screaming Circuits blog that shows that it's got this part anode mark, this part cathode mark. I made the same mistake myself. On one of my boards I put the little marker on there and I gave gave the company the orientation and the CAD files, and then I made a substitution because one part was no longer available and used the other one - same thing but it was backwards because I went from cathode mark to anode mark. So, remove ambiguity. A few years ago I would say, it's okay to mimic the silkscreen - just give us the exact part. But with supply chain availability being such an issue right now, I would not rely on the mark that's underneath the diode because they can reverse if we have to substitute something.
Okay I'm gonna put a pause there and talk about what the heck is going on with supply chain. Stuff about diodes like these, very basic building blocks to design, why are we having problems sourcing parts?
Well we've been told a couple of things from suppliers. One is, they're telling us that the automotive companies are buying up literally an entire line. They'll come to a component manufacturer and say this particular part: I need all of your production, all of it and so there it goes out of stock. Internet-of-Things companies - the super, hyper-mobile devices are also causing issues because they're increasing the demand in the super small components. Well then the companies that make the parts don't have fab capacity to also make the larger ones so, some of the component manufacturers are telling us that they're going to stop making some of the bigger form factors 1206s 0805s even 0603s may become even more and more scarce because if they can make 0402 or 0201 to cover all that range they'll do it and not make the other form factors.
Holy... I don't know what to say about that - if I was a design engineer I'd be freaking out - this puts people in a really tough spot!
It really does and it's gonna change the way some things are designed. We have always had a policy that we will not substitute anything without explicit approval. Even looking at a bypass capacitor - 0.1 microfarad 16 volt bypass capacitor - in some cases you need exact parameters. There’s parameters you need to be exactly the same so you can't substitute. But there are also plenty of cases where it's just sort of by guess and by golly: yeah it's a 0.1, it could be 16 volt, 10 volt, 25 volt, 50 volt, whatever. If that's the case, people are gonna have to start being really flexible in terms of what they will accept for a component and maybe at some point the industry will have a flag on a bill of material that says: this one's engineered so it has to be exact. This one, just make it close.
Another thing, our industry is changing so fast, it's just a big reason why Altium and I've decided this podcast would be a good idea. Same reason why your Circuit Talk publication is a good idea because it's like we can't get the education out fast enough or get the news out. Like holy cow, why can't I get this capacitor? It's not a unique form factor specialized BGA they're capacitors! This is like bread and butter, so it's been puzzling to learn about that and I'm just really interested to see how these component manufacturers are going to deal with this and and again how designers are going to be forced to think hard about these parts it's really strange. Anyway sorry for taking a little side trip there.
That's important, it's a significant issue. We're being told this could last until 2020 and when we get out of this allocation, the industry is going to be different and, as I said, a lot of the bigger form factors consider moving all to 402s. It's more difficult to deal with these smaller ones but those are the ones, when the component manufacturers catch up, it's going to be in the smaller form factors because they can sell them to people building small devices as well as big. So think about that, be very, very careful when you're picking the specific component and tell us, and other manufacturers like us, what parameters are important.
Goodness that’s a great tip. You know I hadn't thought about it until just this minute when you were talking; I'm wondering if this will drive an uptick in embedded?
Embedded like embedded passives?
Uh-hu better passives.
I don't know I've been waiting to see that. I joined this company in 2005 and embedded passives were in the news at that point, and I actually made a prediction on the Screaming Circuits blog, that in ten years - I think I said - 80% of the passives would be embedded passives. I don't know that we've ever seen one. I guess technically you wouldn't see it because it's inside it.
No but you would know it was there, because I know it from my board manufacturing past, you would know cuz you would have to process it differently. It's a different process but I don't know what the cost trade-offs are there, but I've met Bruce Mahler from Omega and I've met some of those folks, and I'm just wondering if this allocation will drive, but I don't know what the cost trade-offs are or performance comparative. That makes me think, I need to call Bruce Mahler and get him on the blog because it's an interesting thing to ponder in lieu of what's going on in the marketplace.
Yeah.
Anything else you would mention off the top of your head that's something you see repeatedly that's a design for assembly thing that you would recommend designers to take a look at closely?
Well the polarity, the QFNs, BGAs as I mentioned. Something that isn't necessarily quite so obvious is the data files that is an important part of design for assembly. Ambiguity on a board is bad, ambiguity in a data file is bad. Bills of Materials, if there are parts in there that don't match the board, that's probably 80% of the jobs that come through here, have some sort of a Bill of Materials issue. So, double-check that that's accurate and that it matches your CAD files. If you can give your manufacturer the intelligent CAD files like an ODB++ or IPC 2581, that significantly reduces the chance of error, but then there's a little irony in there too that a lot of board houses still prefer Gerber's so we have seen cases where someone saves and then; oh yeah, I can give you the ODB++, but they forget they made a slight change and so now we have Gerber's that don't match the ODP++ so, make sure all of your files are consistent. Make sure the Bill of Material is clear and finalized. All in all if you add up all of the files issues that we see, that's probably one of the most common problems. I mean, I run into those problems for myself. I designed some boards and run up to the factory here, and I know how to do this, in theory I know how to do this, but I regularly make mistakes that my co-workers chide me for.
Well I think again, that leads to the complexity of the data that's available. The data sheets; whether they're right. I mean it is such a complex thing and it amazes me that we can even manufacture circuit boards and then put components on it and come out workable sometimes. Because it is such a complex process, I'm really glad that - actually I appreciate it - I don't understand all those steps but having worked for for both a really high end EMS that sold to tier one’s, very complex boards, and also having worked for a variety of board shops. I really appreciate the complexity in both those disciplines, and I think sometimes because a board shows up as a line item on a BOM that complexity sometimes can get lost on you. But yeah we're building things, even here Altium, into our own tool that helps, like an active BOM, things like that, that hopefully help. I think design tool manufacturers like us, I think we're doing a better job helping in that regard.
Right yeah, definitely!
Well the last couple items I wanted to talk to you about... well thank you for all that by the way, and again, we will share in the show notes your website. The Circuit Talking, I would recommend to anyone who is listening or watching - that you subscribe to Duane's blog or just Circuit Talk or whatever and we'll put all the links in because again, he's got his feet in the fire and runs up against these things as he said. Because they're putting through such a width of product. Like I used to work for an EMS, and like you said, it was a vertical. So we worked with military Tier one, and so the type of bores we saw was a niche, but you're seeing everything.
Yeah, literally I mean we worked on a camera board, the electronics of it, for National Geographic - it's a plexiglass globe, they drop it to the bottom of the ocean, it's got a chain on it and when the chain rusts through the camera bobs to the top and they pick it up again. We've got stuff being built for the 2020 Mars Rover so, literally down in the ocean up into space and and anything in between, we've built Ardium base stuff, real simple things, through holes; we built a board with five thousand placements. It's just all over the place and it's just absolutely the most fascinating place I've ever worked certainly, because of that.
Yeah I can see that and again, kudos for you - it's easier to do a quick podcast or write a blog post or produce a Circuit Talk that can go out to thousands of people and get that information out in that kind of global sense and be helpful right.
Yeah rather than tell one person at a time.
Exactly it's kind of a scalability of getting that knowledge out, so I really appreciate what you've done over the years. One thing I wanted to ask you about which it was a fun thing is about; I don't know six to eight months ago, I had the privilege to go with the Altium team for the first time, to a Maker Faire because we have Circuit Maker and Circuit Studio - Circuit Maker is free and and now we've bought a company called Upverter, which is also free, and in the cloud, and we also have Circuit Studio. So, we went there with those products and because of my position here as Director of Community Engagement, I hadn't had any exposure really to the Maker community, other than seeing stuff online, and I went and it was like drinking from a firehose. It was so much fun… goofiest things... it was so much fun. So, I'm walking the aisles, kind of collecting things to write about, or learn about, and I come across Duane Benson, wearing what looks like rap swag around his neck - it was like a clock you were wearing right, or something - he looks like a rapper and I'm used to thinking of him as this Duane Benson from Screaming Circuits and here you are, like fully immersed in the Maker space, and you had designed this device and had LEDs on it and I'm like: what are you doing here?
So tell me about how you've come to serve Makers. It doesn't seem like, from a profitability or a business model, that it would be a market that a company like Screaming Circuits would address. So how'd you get there Duane?
Well you could say that I'm a bit of a method actor, I mean I love... I've been designing small circuit boards for a very long time and writing the software for them for a very long time and one way of looking at it, is I'm a Hacker and a Maker who happens to be lucky enough to have a manufacturing facility. But more specifically, those Hackers and those Makers they are starting businesses.
Yes they are.
Many of those businesses become our customers whether they be crowdfunding or bootstrapping or getting investments, they are the future. The Maker community has a lot of students in it. It has a lot of weekday engineer weekend Hackers, it has a lot of people who aspire to start a new business and just such a wealth of creativity. And part of our mission I always like to look at, I'm just one person, we're just one company but if we can make our tiny little corner of the planet just a little bit better then we've been successful and all of those people who want to design electronics...
M-Hmm..
-We know what they don't know. I mean, we know what kind of problems they’re going to run across before they do, and so if we know what they don't know why don't we pass that off? And some of those people will have boards built with our competitors. Some of them will build them themselves, some of them will have us build them. Whatever, we're helping them understand this industry better. And we are helping them build better boards. That's what we really want to do. That's why we're at the Maker Faires ultimately. It does always have to lead back to more business for us, and it does. People see Screaming Circuits, they get the Circuit Talk and they read it, and it's Circuit Talk a Screaming Circuits publication so all of that winds its way back eventually, to helping the business here, and that's how we can afford to do it. But if we can help the business build and grow the business and help these budding designers - everybody wins.
This is why I love you, and love you guys. I just I love that philosophy, I love that approach. I try to live by an old Zig Ziglar thing and this reminds me of you and Screaming Circuits’ model that you just explained. Zig Ziglar used to say, you really can't have everything you want in life. If you just help enough other people get what they want.
Right.
So it's kind of knowing unconsciously that if you put good things out in the world, and you do the right thing, and you're ethical, and you have integrity, and you serve people, that good will come back to you and and you'll do okay. And I think that's a big key to your success actually, by kind of leading with service and and not ignoring the bottom line. We are in business to make money, we have to do that, or we're not in business anymore. So, I really appreciate that.
Well we're wrapping up now and I think you've listened to a couple of these podcasts now and so two questions for you. One are you a nerd or a geek?
[Laughter] I’m a Gunerd…
That's the best answer I've ever gotten yes you're a Gunerd.
Yeah, there was a time when those were really pejorative terms but I think nerds and geeks have taken it back and said, you know what, no we're not going to be ashamed of liking technology and loving it,we're proud of it. I mean, yeah so I’m a Gunerd.
Oh my gosh, I'm totally gonna steal that and use it somehow Duane, that will come back to haunt you later I promise.
[Laughter]
And the other question is, but I think I know what the answer is, if you've listened to podcasts. I always ask designers and electronics professionals in the end - this is ‘designers after hours’ - so because there is so much creativity involved a lot of people, like you said are Makers or Hackers, or they play a musical instruments or they're sculptors or whatever. So, what is your kind of guilty pleasure that you like to do after hours?
It would have to be photography. I chase animals around and take pictures of them, animals, landscapes, and then I have sort of a weird passion for old, decaying industrial sites as well. But photography would probably have to be my passion when I'm not playing with electronics.
That's so cool. Do you have a website where you share any of that or is it just mostly personal stuff and you keep your photos and share them with friends and family and whatnot?
It's mostly a personal thing I have had them on websites before but it's just my thing.
And and what do you mean about industrial sites?
Well, old decaying, industrial and rusty factories. There's a place here just north of Canby Oregon City and we've got a waterfall on the Willamette River and most people think of waterfalls as pristine, and nature and that's all wonderful, I love that. But this one: back in the 1800's they started building paper mills and they built a set of locks. It's the oldest - well till they just recently closed down - it was the oldest continuously operated locks west of the Mississippi. And so now, you overlook the river from a nice restaurant and you see this shut down, decaying, industrial plant and - well no it's not the beauty of the river - but I see a sort of beauty in the symmetry and in the the way people constructed these things. It's almost like an architectural dig, you can see things from a hundred years ago, from eighty years ago, from sixty years ago, and you can see the evolution of that, as this thing built up and then as they abandoned it, and there's just for some reason... I really enjoy that that sort of a view as well as the natural views as well.
They do have a really unique aesthetic and things have changed. It is kind of like a little time capsule and the rest is actually beautiful and sometimes the design itself is beautiful.
Yeah well thank you again, this has been fabulous and I'm sure we can talk more and more, but thank you so much for giving me so much of your time and sharing DFA tips and the story of Screaming Circuits, and we wish you continued success and we'll certainly share the website and Circuit Talk. And if there's anything else you'd like to share with us, give me a holler and I'll make sure we include those in the show notes.
Thank you very much, it's been a privilege to be on the show here, thank you.
Again this has been Judy Warner with Altium’s OnTrack Podcast and Duane Benson from Screaming Circuits. we look forward to seeing you next time until then always stay OnTrack.
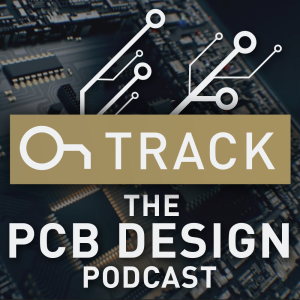
Tuesday May 08, 2018
David Carmody’s DFM Report Integrating Design and Assembly
Tuesday May 08, 2018
Tuesday May 08, 2018
Do you know your fabricator? Meet David Carmody, Division Manager and CID+ at San Diego PCB Design. As a service bureau, San Diego PCB works on a variety of PCB design projects. Learn why David says, “You gotta know who you’re fabbing with” and how he is using DFM Reports to help customers integrate design and assembly in this episode of The OnTrack Podcast.
Show Highlights:
- Memorable designs in telecom space and the development board for Dragon II, a SpaceX project, for the capsule they hope to take to Mars
- Package on packages, dropping the DDR - removing the burden on the designer
- Palomar advisory program - student programs for learning PCB design
- San Diego PCB acquired by Milwaukee Electronics, EMS and Engineering Services
- DFM report - a “stoplight report” for customers before starting build - customers love it and it fixes issues proactively especially with packaging
- A lot of engineers don’t know the manufacturing side and DFM reports can help with this
- “You gotta know who you’re fabbing with”
- Will additive manufacturing processes be the answer? The business model remains to be seen.
- 3D printing - you can’t print copper (yet)
- Altium User Groups - have Altium in the title but we don’t run them! We’d love to support.
- Altium User Group in San Diego is very active and supportive.
- Advice from a Pro: Always keep learning, it will keep you fresh and make work more fun.
- PCB design isn’t the only practice David has mastered - he’s a martial artist too
Links and Resources:
David Carmody on Linkedin
San Diego Altium Users Group Website
Tecate, NM Manufacturing Facility
Hi everyone this is Judy Warner with Altium’s OnTrack podcast - welcome back. Once again I have another incredible guest to speak with us today, but before we get started please follow me and connect with me on LinkedIn. I try to share a lot of things relative to engineering and PCB design and on Twitter I'm @AltiumJudy and Altium is on Facebook, Twitter, and LinkedIn, and if you'd please subscribe and give us some comments so we know what you'd like to hear more about that would be great.
So today again we have a great guest which is David Carmody of San Diego PCB David has a new title now: he is the division manager and he also has a CID. So David, welcome and thank you for joining me here at Altium today. So, we've known each other for a little while and I've had the benefit of being over at San Diego PCB and looking over your shoulder to some pretty wild complicated designs. So tell us a little bit about your day-to-day from the perspective of design bureaus and the kind of work that you see?
Okay, we do get a lot of different designs, a bunch of varied designs, so we see a lot of military application, we see a lot of new technology - wearable technologies and things like that as well; it is pretty much all over the map though. I mean we get a little bit of anything and everything just because of the the nature of the service entity. A lot of the more upscale - so to speak -designs are the real nanotechnology sort of stuff where we're cramming a ton of the little parts into a board that's less than a half square inch total in size, or we're packing everything into a big housing that has to get heat out somehow because, I mean, we're sending up high output micro processors into into space and there is no airflow so we need to get the heat out in other ways. So there's a lot of that sort of stuff that we do get to see and and play with and and learn from as well.
I think San Diego is kind of a neat place to work too because there is a lot of Defense here and there's also call comments and telecoms, and even in our local area, although I'm sure you see work from all over the country? We do we also have kind of some neat things right here in our own backyard.
Oh yeah.
So across that variety what would you say some of your more memorable designs would be?
I was gonna say we do have have some telecom stuff that's gone on and those are those are fun boards just because they've got big processors on them and lots of high-speed lines, things like that. Most memorable, for me personally, would probably be a SpaceX design. I was able to design the development board for the Dragon 2.
Oh my gosh!we’re not worthy! Do you mean the dragon heavy that they just launched - the second Falcon that ever went?
Yeah the the Dragon 2 which is the capsule that they hope to take to Mars one day.
Oh so that that one!
Yeah. I did the development board for that so it's just basically a big processor board with a lot of RF communications on it and things like that and they're breaking out all the other boards from that, and that was a fun project. I got to be a part of that was really cool.
Yes, I sold some R4s to them and got to go through that facility a few times so I'm like a weirdo SpaceX geek and then we also sponsor the hyperloop pod teams for universities. So Ben that's helping us here with recording this; he and I got to go up and hang out at SpaceX and see them do that.
I saw some of those pictures.
So sorry for being so weird but I’m a kinda SpaceX geek.
Yes, it’s been fun. We do have a couple of space contracts we've worked directly with NASA and MIT and also with Space Micro so, we've definitely learned our way around the Class 3A specifications and we know that inside and out.
Not easy, really dense stuff. So you talked a little bit about the nanotechnology, is that where you sort of see the bleeding edge going? What are the the most challenging designs?
I was gonna say the packaging is actually changing quite a bit, we're seeing some things that the packaging is doing that's well, quite frankly, I'm not terribly happy with because it takes away some of our place - but things like package-on packages is coming around. That's really cool technology, I mean, you put down the DSP or the PGA - whatever it happens to be - and then you can drop the DDR right on top of it. There's nothing for us to do; it's purely an assembly process, if that.
Wow.
So that stuff is definitely interesting and removing a burden, so to speak, on the designer but yeah, then the package size itself is just getting smaller and smaller. We're being pushed into HDI technology more and more often. 0.3 millimeter BGAs are pretty common, 0.4s are all over the place now. I mean even big ones. So the 0.3 three millimeter BGA's are getting common. I've been able to work on things as small as 0.15 millimeter though. So it was a flip chip sort of design where we're pushing the envelope on that thing so it was experimental, and things like that. I don't think they actually ever built it was costly, that whole get up then but that's that the trend we're seeing. Just everyone's pushing the package design more and more all the time.
Something I noticed I took a peek at, even though I've known you for a while - I took a peek at your LinkedIn profile. I don't know that I'd ever done that and I like to ask people a lot, how'd you get into this industry? Because most of us didn't start out this way, but we ended up here. So did you start out there? I notice you took courses at Palomar College which is local here, and I don't know if they still do, but they used to have PCB design courses?
That they do I'm actually on the Palomar Advisory Committee right now and we're helping to restructure some of that stuff and try to join up a little bit more, their student base through there. They've got a pretty good offering right now to make it better but yeah it's still active and it's it's one of the few places that you can really go for formal education. So it's good that they're there keeping it alive, and not just keeping it alive but updating it.
Right, and that's kind of where you started out was it not?
It was.
Or did you just join them recently as part of the Advisory Committee, or did you start learning design there?
I did technically start learning some design there but it was an accident really.
[Laughter] See, my point is, we didn't do this on purpose.
No absolutely not. Basically I had gone through their program and really gravitated - back then at least - 3d was just emerging. It was all in AutoCAD, there was no such thing as SolidWorks, it was just coming around. So I ended up jumping into AutoCAD 3d mechanical sort of stuff and and did my degree on that and then got on to nothing but waiting list after waiting list. So at that point I was talking to a guy that I was working with, he goes: call my brother in law, he does something in computers. And I talked to this guy, he was a PCB designer at Intel - I'm actually working with him now, we recently hired him, but yeah he's working out in our Arizona office but he gave me some excellent time; never actually met him face to face at the time but he gave me some phone time and told me what to look for, and what this industry had to offer and gave me a couple of places to go after. And I went after both - I ended up getting an offer from both of them, but I liked the smaller business so I took that side of things and spent 12 years back at an ‘unnamed company’ as the Design Manager.
Laughter, well not as awesome as Sandy Opie…
Well I don't know, it hasn't been a year yet, so San Diego PCB was acquired actually by Milwaukee Electronics right.
Yes it’s been about a year and four months now, time flies. So Milwaukee is a really capable EMS shop up in- remind me?
It's Milwaukee.
Oh is it Milwaukee!
Yes, their primary branch is in Milwaukee - okay this confuses everyone - because we have multiple brands out there now. So our Milwaukee electronics brand has most of our engineering services and the EMS as well there. Up in Canby, Portland Oregon, now that's where we have Screaming Circuits - that is our quick term prototype house and there is also EMS there as well. Most people don't know that but the factory shares the floor for that and then we also have - actually it's also called Milwaukee Electronics - despite that, it's in Tecate Mexico but they've got a huge building down there and they're there literally clawing the mountain out from being behind this building.
Right I've seen photos of it, it's really quite lovely, at least the photos are, it looks really modern.
It's a very impressive facility. I was able to visit there and I had seen pictures of it when the shop floor was was only 50% filled; that place is full and like I said they're calling out the mountain now behind them, so that they can add on and I think gain about 30% more square footage. Growing like crazy.
How has that been, that acquisition, for your customers and for you, there's obviously synergy there between the two firms so how has that been for you?
The two companies, the acquisition itself was great, Milwaukee Electronics is a fantastic company to work for. I really enjoy all the people that are there. The synergy has taken some time to get things rolling, but I'm starting to see a little bit of a snowball effect and so we're starting to pick up some momentum to where Screaming Circuits is sending us customers back and we're sending them customers in and we're starting to get a collaborative database of the customers going right now, so that we can take a more active role on that and and really sell to both sides. There's been a little bit of crossover, but like I said, it took probably six months before I saw even the first crossover and right then another one happened, and then another one, but now we're up to where we're getting about at least one customer a week or something like that, that's doing some sort of crossover. so it's definitely building up speed. But it's still going to take a little bit more time.
So since our listeners and watchers here will are mostly engineers and PCB designers, what do you think the benefit is to collaborating design to EMS - what are the benefits you think that occur there?
When you're collaborating, one of the biggest things that's coming out right now, is basically DFM report that we've been doing, it's something that I've been doing for years. Say a customer has their own design team, they want me to be a second set of eyes - something like that. I'll go through the design either on a cursory level if you just want me to look at DFM/DFA sort of issues. Do you want me to look at your circuits, do you want me to look at this whole thing - make sure that you placed it correctly? I coined that a ‘stoplight report’ a long time ago, and basically it's just - we give a nice little green note if it's informative only: this looks good it was done right, give a yellow note if, hey you might want to look into this, you might have some potential issues or, hey this part’s hanging off the board edge you're gonna knock it off, this needs a correction before it goes out - and those are obviously the red items - so customers seem to love that. I mean it's really easy, real clear-cut. They can kind of skim through it, hit the items that they want and that is really building up some speed right now with with a few customers because they've had an internal source for a long time. They've been using Screaming Circuits forever, but Screaming Circuits is going: okay you're going into bigger yields, you need to fix these sorts of items - let's fix them ahead of time and that's what we're being utilized to do.
That sounds absolutely incredible especially now, because in the marketplace so many engineers are laying out their own boards. They may or may not have time or access to spend a lot of time with their fabricators our assembler, so I think to have that sort of oversight would be very welcome. I don't know if that's what's driving it or just having a second set of eyes what do you think?
Probably a bit of both, I mean the engineers obviously get EMI and and EM theory, they do that really well, so they they always lay out the board well for that. But they aren't necessarily the best packagers, most PCB designers are puzzlers so, we do the packaging portion real well that's what we like to play with. But if you’re a good PCB designer you're going to know the EM side and you're also going to know the manufacturing side. A lot of the engineers don't know that, so they don't really look at that. I mean, I've been given boards that were completely routed and they said: rip out all the routing because this guy did it with 6mm vias with a 12mm pad on an 80mm thick board and so, it's just wrong all the way around. And placement wasn't bad on that…
But the aspect ratio is the killer.
-and he used decent trace widths, but I mean, the most problematic piece of the board, and he killed it.
And like it's a good thing that companies like Altium and other EDA companies make such powerful, great software - but there's no place in the software that says: no, stop dummy, you can run DRCs or whatever, but it won't necessarily flag it for for DFM if your aspect ratio is off or whatever, unless you've turned those settings on or off I can imagine right?
Yes but you can still improperly program DRCs too, you can say: hey I want 1mm holes on this board…
I've heard you and Mike Creeden say that a design tool is only as good as the designer.
-yeah you absolutely need that and I mean, someday in the future would it be great to see the tools incorporate that sort of stuff? Yes, but at the same time you’ve got to know how your fab works too…
And you don't want to limit yourself either because you could potentially create self-limiting things that are really irritating...
-oh yeah.
So I think we're gonna just keep giving you powerful tools and you guys have to work it out.
Yeah I mean, we can just zoom up and zoom up and, hey that via looks plenty big enough to me, I could put my fist through it, but not in reality. The packaging thing that I was referring to earlier that is just starting to drive this industry just because of big 0.4 millimeter pitch BGA. I'm working with a fabricator that can't quite do the the latest and greatest and all of a sudden that pattern starts to become a challenge that’s almost impossible to break out.
Right yeah I don't know where this train’s going…
Yup I don't know - it will stop somewhere at some point…
I know, I know, except it seems like we just keep creating some breakthrough so I'm keeping my eye on things like additive manufacturing, whatever we could do it 1mm, controlled trace and pull it off but there's no clear front-runner.
Yeah, the additive processes are very interesting, haven't seen anyone really start pulling off a business model out of it. The 3d printing technologies is also very interesting but you can't print copper unfortunately, so they can't - yet at least - so there's some major hurdles there too that they have to go through.
It'll be interesting. Well I wanted to shift gears a little bit because you, along with your colleague Randy Clemens here in San Diego, run a really solid Altium user group here and for those listeners that don't know this, Altium User Groups, they have our name in the title but we don't run them - they're completely run by the users, for the users they're very democratic and we just lend support and it's something that we've been talking a lot about here, is that we would like to grow the user community and help people launch groups. So can you give us a little bit of background and give us the do's and don'ts maybe, if people that are thinking about starting a local users group from what things have worked, when things maybe haven't worked, and how do we get more people to launch user groups?
Just sign up - just for a little background on that - there was a user group that was here for quite a while that was run by Bill Brooks and it had some traction, it was running for quite a while and then either the community or whatever, started to kind of drop off a little bit. Randy and I saw that as a bad thing basically, and we talked to Altium, talked to a few people here, and then put together a general terms for the the group. Randy has always done Google boards, the blog and stuff, so he's very good at that, he's got a pretty major Altium tutorial board actually that's out there. So he took some of that and ported it over and turned it into a San Diego Altium User Group Board, you can just google that: San Diego Altium User Group and you'll find his board. If you sign up you'll get meeting invites so it's really that easy. All of our IP, as it were, is all up there and and I mean fully freely distributable so anyone can go ahead and take that as a template and start porting it over. Randy would probably help if anyone asked to set up or clone a board but Altim is really great on this thing, they're really helping us out, they help promote it you guys are actually doing lunches for us and all of that, so we really, really appreciate all that support. Lunch is a good way to get people out - just feed them and they will come.
Exactly, you feed them and they show up. So we were restarting the group, it had a little bit of a slow start and it's kind of typical. I think we had all of three people show up once plus the the huge group of Altium group and San Diego PCB group because we host the location but no I mean our last last attendance was in the 30s somewhere, so it's it's doing real well now.
What do you think the benefits are to the users that participate regularly?
One of the big things is we always bring Chris Carlson out for new updates and stuff so we can see things as they're coming out. He gave us a wonderful tutorial on 18 not long ago, really to help us all dive into it as as the interphase changed.
I thought Randy was gonna eat us alive - he came out he's like yeah bring him - he had a slide deck going, and ‘what about this?’ God bless Chris Carlson, our senior FAE, he addressed most of those things and just said, no Randy we just moved it over here, it's just over there and we tackle most of it. But what I really appreciate is that Chris actually took four things back to our R&D team, and I think that kind of real-time feedback, it helps us make better tools right? And if we make better tools we sell more software, it's not rocket science right?
Right and we're happier designers…
Right your’e happier and you’re productive and so I think it's a win-win and I think Altium is doing a good job culturally. So say you were in... I don't know... New Hampshire okay, and you knew there was a pretty good-sized design community what would you say the first steps would be to get something going?
First of all, probably to clone that board that we've already got…
And we will share this, by the way, in the show notes and we'll share that if you want to go take a look at it, because Randy has done a good job of kind of making a charter, it would be a good model to share.
-so it's a fairly basic charter but yeah, clone that board, start marketing it against that, call Altium…
Me, call me I will help you.
-so get them to put it out in a newsletter and a blog or something along those lines so you can start that foot traffic and then invite your buddies, invite your friends and get them to do the same.
I interrupted you there, so you said that Chris came out and you got to see the latest and greatest, Chris did a good thing on showing you AD18 - what other kind of benefits do you think the users see over time?
I mean we've already kind of hit on the the dynamic feedback and that's obviously great information, but just the user-to-user help is always nice too. I mean I've had people come in with a laptop and and open it up and go, look I'm struggling over here, what the heck do I need to do? What rule do I need to write to make this thing work right? And we can just basically rub shoulders and get things moving and get a workaround if it needs it just to move it along.
Well I've been really impressed since I've been down here for about a year now and just seeing the group it's just very active and it seems like a really healthy thing and yeah all I get to do, is use my card and buy you guys lunch and if you want a speaker we’ll send one, if you don't want one we won't interfere so I think that user-to-user and that you guys really get to own it, is sort of a powerful model because it's not like we're going to come down and spring a free sales pitch...
Yeah well, Altium doesn't go in they're not salesy.
Yeah but we try actually, not to do it.
No, it's been fantastic for that.
Well I wanted to bring this up because you and Randy spoke at AltiumLive and Randy took a little part of his time speaking to talk about the Altium user groups and I was so surprised! I'm like, well you can spend your time talking about that if you want Randy, but I didn't think there would be that much interest - but I happened to pop in the back door just to see how it was going and people were really engaged and then people came and talked to me after. I think there's kind of a hunger to do it. I'm just wondering... I just wanted you to share with our listeners, if people did want to do it they would see, oh here's some steps to take because I don't know, though, that maybe we've done a really good job of advertising it because we do want to stay out of it, we want to contribute but not inserting ourselves into an organic user’s group. So, thanks for sharing that part.
Hm-mm yeah, for the AltiumLive, Lawrence Romine asked Randy to do a little bit of a spiel on that and yeah, there were a lot of people from LA that sounded like they were going to be starting their own, or a couple of them, depending on the demographics or Geographics up there and then there were quite a few out of state as well that that sounded like they wanted to start one.
I went to one in Utah, which I guess has been going on for a while. So, I got connected with someone actually at AltiumLive and we ended up connecting and there was like 80 people there to see Ben Jordan talk about AD18, I'm like okay, Wow! 80 - it was huge, but I think that group has been very active and been around for a long time so it wasn't like a new thing and they actually come from Salt Lake and south of there, so it was almost like two combined groups. So anyways, thank you for sharing about that. Any final thoughts?
Nothing that I can think of right off the top of my head.
Well thank you so much for coming in today…
-Thank you
You’re a good sport and we really appreciate you in San Diego PCB and thank you for sharing. Oh one thing I wanted to ask you was because the upper-end (age-wise) is starting to kind of age out in the industry and we're getting new ones coming in, what is one - since you're sort of a veteran designer - what is say, one or two pieces of advice that you would give to a young designer?
The number one thing I would say is, never stop learning. I mean I got into a rut at one point where I wasn't learning I couldn't stand up on the the current trends, things like that, and that job got to be a drag, it really did because it's - overall - we did the same thing over and over all the time. It's very repetitive, but if you're standing up on the latest trends you always have something else to reach at and something else to go after. Always have the latest way to solve something too, so it just makes the job overall a breeze; makes it a lot easier to do day-to-day and keeps it fun and interesting.
Very good. Okay, last question: I said that was the last one but I like my very last, last question - I call this part of the podcast designers after hours okay - so there's people like you and I know in common, like Bill Brooks who started the Alts Music Group. There's the sculptor, I just spoke to Chris Hunrath earlier today, who's a scuba diver. So what do you like to do after hours?
Honestly Mike my side is a little sore right now because I did some martial arts last night so that's one of my little best-kept secrets, so to speak, been doing that for a long time done Tan Sido, got a third-degree black belt there, and then migrated over to Kung Fu and have a black sash.
Well, remind me to never make you mad! You’re so soft spoken and could kick my butt.
[Laughter]
Pat's the one that always bounces that around the office but he's honestly the only one I’d ever damage too…
[Laughter]
That's cool. See, another interesting after hour designer. Well David, thanks again and I know we'll see you soon again.
This has been Judy Warner and David Carmody of San Diego PCB. Thank you for joining us today we'll make sure to share our links below and please visit us again next time.
Until then, remember to always stay on track.
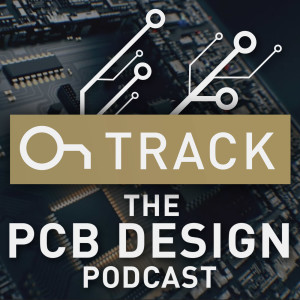
Monday Apr 30, 2018
Why is Spread Glass popular? Chris Hunrath from Insulectro
Monday Apr 30, 2018
Monday Apr 30, 2018
Why is spread glass popular? What can you use instead of FR4? Listen and learn from industry veteran Chris Hunrath, who joins us from the San Jose Insulectro facility for a deep dive into what material sets are used in printed circuit board assembly and manufacturing. Get expert insights and learn about new materials on the market to help with your PCB design before going to fabrication and assembly.
Show Highlights:
- What is Insulectro? Operating for over 50 years, Insulectro provides materials for electronics, everything from laminates, prepregs, flex materials, copper foils, conductive inks, substrates, process chemistries, imaging materials and lamination materials. With 11 stocking locations, the newest in Toronto and 9 branches, Insulectro is a leader in providing electronic materials to industry.
- Prepregs - 175 different types to cut from in San Jose facility alone!
- Spread glass is becoming more popular - electrical and fabrication benefits because it is more electrically uniform. No open areas, the filaments are spread across (aka fanned out or mechanically spread) and this has signal benefits especially for differential pairs. Better from a drilling standpoint too.
- New materials are gaining traction - with low loss that laminate at normal temperatures
- Insulectro distributes for both Isola and DuPont
- Isola’s line-up of high-speed, low-loss material sets - Isola has a suite of laminates that are low loss, some of them with DKs close to the teflon range and they laminate at the normal temperatures which makes a composite build much simpler.
- Low-loss, low-Dk materials that can help with their signal integrity requirements
- I-Speed® - Low loss system, not as cheap as FR4 but its close and could be a good next step for people looking to upgrade material
- Having the right material set for a design is critical
- Challenges are more often in the fabrication than the design
- Copper is a really good moisture barrier, you have to bake the parts prior to assembly.
- I’ve seen people underestimate the baking and end up with scrap. Moisture is avoidable.
- Bonus Material: In Designer's After Hours, Chris Hunrath shares what kind of electric creatures lurk in La Jolla!!
Links and Resources:
Chris Hunrath on Linkedin
HDPug Research on High Frequency Flex
Understanding Glass Fabric by Isola Group
Hi this is Judy Warner with the OnTrack podcast. Thanks again for joining us. Once again I have another amazing guest for us who is the go-to guy in PCB laminates.
I am with Chris Hunrath today but before Chris and I get started I would like to please invite you to subscribe, or to favorite us on your RSS feed, or you can connect with me personally on LinkedIn. I share lots of stuff relative to engineers and PCB designers and on Altium I'm at @AltiumJudy and Altium is on Facebook Twitter and LinkedIn.
So please give us a subscribe and a connection and we’d love to interact with you and hear more about what you'd like to hear on this podcast but I'm sure you're going to enjoy today's guest.
Chris is the VP of technology at Insulectro and I'm gonna let Chris go ahead and tell you a little bit about Insulectro for those three people on the planet who might not know who Insulectro is. So, welcome Chris and tell us about Insulectro.
Okay thanks.
So yeah Insulectro has been around over 50 years. We supply materials to the circuit board industry - actually multiple industries - but mostly we've been focusing on electronic materials. Everything from laminates, prepregs, flex materials. copper foils, conductive inks. Different kinds of plastic substrates used with conductive inks, process chemistries, imaging materials, drilling materials, lamination materials. Also we have 11 stocking locations. We just opened one up in Toronto and we have nine branches. So I'm based in the San Jose branch in the Silicon Valley area so that's a little bit about Insulectro.
Yeah nothing going on there in San Jose?
Lots yeah, so since the San Jose facility is one of the four branches where we do fabrication on master sheets and master roles of prepreg and laminate we do cutting, tooling, vacuum packing, and will also do that on the lamination materials, the release films, and the press pads and things like that. So we do that in four branches…
I'm going to ask you more about that later because you just told me about that yesterday and I had no idea you guys did that. Actually I saw you more as a distribution channel. But before I ask you about that, why don't you give us a little bit of background on your history in the industry and how you came to this? I always say no and no one does this on purpose, unless you're an EE right?
So yeah those printed circuit boards - those of us that got pulled into the industry ,, have been here a long time. So I started actually back in 1983, I was going to school for chemistry and one of the shops back east, actually in New Jersey, was looking for someone to work in plating on the night shift, and ,, the rest is history as they say. I got pulled into the business and the next thing I knew I was coming to California to to work with our sales team. So that's how I got started in this, and then I joined Insulectro in 2001 and it's been great being with this company. So many different materials we get to work with and so many different customers.
I think you're a familiar name and face - being the VP of Technology but you also do trade shows and stuff. You present a lot and are really articulate explaining the technology of laminates because it's gotten a lot more complicated than it used to be back in 1983. I started in ‘84 by the way, and it used to just be, we'll get some FR4 some, prepreg and you're off to the races.
Right yep, back then it was FR4 and polyimide. A little side note, actually the company I worked for made multi wire circuit boards so we also had an adhesive to embed the wires and that's a whole nother story for another time. Primarily it was FR4 and and polyimide and now there are so many different materials and then if you add the Flex materials on top. There's a lot to to work with, it's a lot of complexity but also a lot of opportunity. I mean electronics are going into everything and we're seeing that with our printed electronics products as well ,. A lot of interesting applications from wearables to medical to consumer electronics so that's been pretty cool to be a part of that as well.
Yeah so tell us about what you're seeing on the front lines of current technology and marketing trends that are having an impact on laminate suppliers - ultimately since our audience here is mostly engineers and PCB designers - how that's sort of flowing down and what the impact is?
Okay.
Yeah so big question sorry.
Yeah that's okay, that's all right. It's become a bigger opportunity - a big part of our business - but if you look at materials in general, everybody knows people are looking for higher speeds and high-speed digital and they're looking for lower loss in RF applications the Internet of Things also even data communications and those types of things; car electronics, radar, self-driving cars. All these things need low loss materials. One of our challenges - and again - it's an opportunity as a supplier to the industry; is having the right stuff available for customers and certainly the Bay Area. It's always been a quick turn market, but it's that the time window has shrunk and one of our challenges is supplying all these different materials to our customers, and of course with every laminate system, every resin system you have the different core thicknesses, the different copper weights and then you have the prepregs with different thicknesses, and resin contents. Add to that also spread glass. It’s becoming very popular I'm sure most of the people who watch this will be familiar with the spread glass systems. They have electrical and fabrication benefits but but again, it adds to the part numbers, the variety of materials we have to stock. So we we currently have here, just in San Jose, we have a hundred and seventy-five rolls of prepreg we cut from for customers. And ,, it always seems like our customers need something we don't have in stock.
Yeah.
It's the one thing they need for that application. But you know we try and up our game here and have the right things. And that comes from going to our customers and talking to the people in their design group, in their sales department and asking them; what do you see? You know, years ago we used to work on forecasts. Customers would have a very predictable usage on materials and they'd have forecasts out for some time. We would base our stock on that and we do forecasting today but it's not the same thing anymore. I mean customers may get an order and they have four days to turn it and they don't know what the build’s gonna be until the stackup’s done and and that creates those challenges. But you know, we try again, we try and improve what we stock and what we have here and get better and better at that. It's just never boring that's for sure.
Yeah right, you gotta have a big crystal ball…
Yeah just talk a little about spread glass.
Yeah spread glass now that kind of puzzles me in context of high speed so I'm curious. Teach us about spread glass?
So there's different kinds of glass, what they call standard E glass and then of course the low dielectric constant glass. I'll talk a little bit more about that in a few minutes. But the spread glass is basically that the the fibers, instead of having a crossover and a weave - like you would in a fabric for like clothing - the actual filaments and the weave are spread out, so you don't have open areas and crossover areas, or areas of higher density glass and that makes the system more electrically uniform. So when you have traces that go through the PCB they’re not either going through high resin content areas, or high glass content areas because they'll have different signal properties so you want to make it more uniform.
Are they more in glass spindles - are you saying it's not woven?
Well it is woven but instead of having a high concentration of glass with open areas of just pure resin, the filaments are spread across so you're filling in the open areas.
Okay so they're kind of fanned out you're saying?
Yes exactly there's different terminologies there’s mechanically spread, there's flat glass, but but basically what ends up happening is, the crossover areas where you would have what we call glass knuckles, they're thinner and of course, the open areas now have some glass. So again the system is more uniform it's a composite. So the composite’s more uniform and and like I said that has signal benefits, especially for differential pairs. If you had one trace and a diff pair running over mostly resin, and one running over mostly glass, they'll have different propagation velocities. So you'd have different electrical results, so the spring glass is better for that. It is better from a drilling standpoint, either laser or mechanical drilling. Because you're not going through high concentrations of glass where the crossovers are so there is a benefit there. There are some caveats though, to how it works with filling ground planes. Because the resin doesn't easily move through the glass fabric - you could have some problems filling, so we have to offer not just the spread version, we have to offer the standard versions as well because very often, designs - if they're strip line - you'll have a reference plane on either side of a signal and those reference planes could be heavy copper and they require a certain amount of fill. So you need the standard fabrics to use as well in a stack up. So you might have a mixture of those types of systems - so yeah it does add some complexity.
So now we're not only doing hybrid materials now we're doing hybrid prepreg you're saying?
Well there are different varieties I guess you have to do it that way anyways because if you're doing hybrid you're matching the materials to the bond ply that you're using anyways I suppose, but now you're adding in this kind of third layer almost.
Right.
And then we also have standard copper foil and then we have HVLP or VLP copper and low-profile coppers, so so yeah so it adds. And then of course, all the different copper weights - really everything from 5 micron through four or five/six ounces, so it's all over the place. But yeah actually going on the hybrid thing too we are seeing a lot of mixing the resin systems. In other words you would never mix B-stages in the same layer in other words you wouldn't have one kind of resin melt but you can mix cores so you could have one type of resin system as long as it's fully cured adjacent to another kind of resin system and we see that with RF, because very often what you do is, you have your low loss layer on the outside and then you would have your - whether it's high-speed digital or just DC - you would have that in the other layers and that system would be mixed and there are challenges there too even if you're not mixing the B-stages. Some materials require higher lamination temperatures and if you're not using a standard material that can withstand that, you would have issues or you would have to use a low loss material that has normal laminating temperatures. And typically when we say normal laminating temperatures, we're talking in the 375 degrees Fahrenheit range. Whereas some of the more exotic PCB materials - the filled PTFE systems LCP FEP - they require much higher laminating temperatures more like 550 to 600 Fahrenheit.
For a while I was at an RF - it really never took took flight - but I'm sure you remember not too many years ago, we got on the fusion bonding bandwagon. We thought that was going to solve all our problems but I remember being at a shop where I think we were running our lamp press at like 700 - 800 degrees Fahrenheit for 12 hours with some crazy profile. That's not very sustainable but it was homogenous DK and it had some great performance benefits but it really never took flight. So my gosh let's talk about hybrid a little bit more because I left the industry for a while to raise kids, and when I came back it was like Rumpelstiltskin waking up to all this high speed stuff and I was like wow! And what I did see was an awful lot of hybrids. So can you talk a little bit about what you think - certainly RF and microwave is an obvious one - but talk about what is driving the demand of high-speed digital RF and hybrid technology overall?
Well it's - in very broad terms - it's about electronics, doing all kinds of different things from a design standpoint though it's about mixing, mixing proper material properties in composites that's what you do. You choose one material over another because of its properties and you separate those layers out to get what you need out of a design. So it's driven by cost, some of its also driven by how you would fabricate. In other words, if you had a material that was hard to laminate you could use that as a double-sided low loss layer and then bond the other layers. Conventionally that would run the DC or other signals you would have in the design. We do have some new materials, so one thing I didn't mention earlier is that we distribute for both Isola and DuPont.
Okay.
Isola does have a suite of laminates that are low loss, some of them even with DKs close to the Teflon range, and they laminate at normal temperatures. So making a composite build is a lot simpler. You don't have to do two separate laminations, unless you had buried micro vias. But you wouldn't do it because of the materials. You would do it because it's for the design but you can do it in one lamination cycle so that's one thing we're trying to bring to market and that's something that's been a growth item for us. Some of these new materials like Tera MT40 for example, the Astra MT77. Astra has the lower dielectric constant - a dielectric constant of just under three - that's for certain, for RF designs, whereas the I-Tera is for the mid-DK, what we call the 3.4 - 3.5 DK range but they're both low loss and they’re both laminated. Again at normal temperatures, so that seems to be getting some good traction.
How do they stand up cost-wise against some of the traditional high speed laminate providers?
Well as a resin system PTFE is expensive and then if you're reinforcing it with ceramic or fiberglass, that adds cost as well, so we actually stack up - no pun intended - pretty well with the PTFE-based product. It's not as well-known, many of the designers are familiar with the PTFE based laminates for RF applications so, they go with what they know very often, until they have a need and then they start looking at alternatives. And there's so many different, projects coming on with our customers, we're quite busy trying to keep that education process going.
So I'm putting myself in a designer's shoes today and I was talking to Lee Ritchie yesterday and he was talking about how the speed curve has gone up near vertical in the last five years and I think you and I would both agree that we've seen that trend. I'm putting myself in a designer's shoes, so how do I get educated fast enough to keep up with all these moving pieces? Because like I said, when I left the industry and came back it was completely like a waterfall as far as onboarding all the different laminate manufacturers and then learning about matching bond, prepregs and bonding systems and cover weights. And then, let's just throw in, that we might have this on an aluminum carrier or whatever. How can we do a good job other than hosting a podcast so I get people educated?
I think the IPC design councils are helpful for that. Some of our folks have presented, I presented, our other people presented. Certainly, if you're an OEM or a designer and you get boards from a board shop, reach out to the board shop and say, what are my options? The board shops have to live and breathe this stuff and certainly, folks like myself and folks at DuPont and Isola will also support the board shop in that effort. In fact that's becoming a bigger part of what I do. I travel with my customer to their customers and talk about their options and the pros and cons because you would think, in theory you would want the highest performance at the lowest cost but, it's not just single performance. It could be mechanical performance, it could be thermal performance, there are a lot of different attributes that you would need in the design and you don't know unless you talk, unless the designers were talking to the folks that have the materials background. You can't put all that together and I've seen projects where people have used the same old stuff and then they get unexpected results and so that's what we're trying to do. It's better for everybody if we hit it right the first time. So, that's what we do, we go in and we say, these are the options, this is when you use fired glass, this is when you use standard, this is when you go for the lowest loss possible, this is where you go for a better economy. We have a material called high speed that's very economical and it's pretty low loss, it's a 006 loss tangent and it's compact. It's not as cheap as FR4, but it's close to a lot of the other materials out there. So it's a nice scale of economy. Now it's not for every design but those who have been using FR4 for a long time and want to upgrade to a total low loss system, it might be a good next step. And that product has actually doing pretty well for us. The 4UIS has been growing pretty well and then the high-end products are growing pretty well. The products in between not so much, but, I think it's just a matter of what people need and the design.
All right, that makes sense. Does Insulectro and/or DuPont and Isola put out resources online that designers can get a hold of?
Yeah both companies, obviously all three of us actually, have websites with links to connect slash sheets, tech data sheets, and other things but I don't know if a website will ever be a good substitute for actually having a conversation with someone who's knowledgeable. Certainly that's a good place to start. The other thing too is sometimes a design will have some IPC slash sheet numbers on them, the specification sheets for different materials, and sometimes you're locked into that. So we've seen that with our customers, sometimes they're locked into a particular material set and it may not be the best. And again that goes back to having a conversation with the people involved. And sometimes they’re willing to change and sometimes not. Sometimes they have no choice. Certainly all old legacy military designs are examples where people are really stuck on very old old systems. And there's definitely a better mousetrap in those cases. But like I said, there's no substitute for having the conversation.
So Insulectro for instance, we were just at IPC Apex and I'm sure Chris, you were doing presentations there. I assume that going to trade shows also, there would be opportunities to have face-to-face conversations?
Yeah certainly, seek out - if you're buying boards - seek out your PCB shop. The folks at those trade shows, or sit in on some of the technical sessions, and then certainly, if Insulectro, Solar DuPont are there, great place to go get some information on materials.
Great.
Well I know I sound like I repeat myself often about this, but I've often said, and I used to blog on Microwave Journal to tell people, please go talk to your workshop, please go to your workshop because I think it kind of all ends and starts there and and because, like you said they have to deal with so many laminate and resin systems and all these things every day. A lot of times they could be helpful, it's just sometimes I think designers are so strapped for time. Sometimes they're doing the jobs of two people and so I'm always trying to help the designer get resources as best they can.
Yeah and it's something we appreciate, and what we see happening too, is they'll pick up a data sheet and they look at differences there - sometimes there are very minor differences between resin contents and electrical performance. You don't know the dielectric constant of a loss and they'll pick the lowest on the datasheet, but that might not be the best for the fabrication and having the right material to make the board come out right, yield well, do well after assembly, do well in the field. You're not really giving up anything even if the loss is very minor, higher in loss, but yet the board performs well it's definitely a good trade. So that's part of the problem, sometimes some of the designers who are pressed for time will pick a particular material set. Yeah it might have the lowest numbers, but it may not be the best fabrication. If you can't build it, or if the board shop doesn't yield well, it doesn't do anybody any good.
So I was just talking also to Kelly Dack, Chris.
You would probably recognize his face. Anyways we were just talking about this and it's like what looks good on paper is... First thing, it isn’t always this linear process when it comes to design and fabricating. So, back to the hybrid designs. What would you say for someone that's designing hybrids, some of the the challenges are of those boards and some of the benefits? Obviously performance is one of the benefits.
Yes performance and cost, because very often the very low loss materials, come at a premium, because of the resin systems - the cost of the resin systems - and the cost to make the materials and so on and so forth. So that is another benefit - it can be a challenge for the board shop and it really depends on the materials. The challenges are more often in fabrication than they are in the actual design part of it. Yeah, like I said before, it just varies so much, I mean one of the requirements usually for an RF design is to have a certain level of precision when it comes to forming the circuitry. When we say forming, it could be a plating and etching, it could be just print and etch, depending on the the technology used. And then you would laminate that into a standard FR4 system, and sometimes those materials aren't really compatible. So yeah, that goes back to being able to have materials that have the right CT properties, the right adhesion the right lamination properties.
But you look at some of these high speed materials and sometimes they can be more fragile. I mean they might for instance - and correct me if I'm wrong here - this is second-hand knowledge here, but they might survive the fab process, and lamination cycles, or even multiple lamination cycles, because then you introduce buried and blind vias. And then there's multiple thermal excursions and then you take it to assembly and you've got through-hole and surface mount part and they have to go through another two thermal excursions. And so that it all adds up and it it's not obvious at the outset right?
Yeah those are all good points, all things that have to be considered in the fabrication and use of the part and there's a lot there too. One of the things I'm seeing, is copper is a really good moisture barrier. So one of the things that we try and preach to our customers and their customers or the assemblers if it's a CM, is you have to bake the parts prior to assembly and you can't underestimate that. There was a really good paper put out around 2011 - 2012 at IPC that showed just how long it takes for the moisture to get around because if you have a strip line construction, or if you have a reference plane and RF design, that moisture has got to go around that copper plane. It can't go through it and I've seen people underestimate the baking and end up with with scrap. It's kind of a shame because if moisture is the only reason why you're doing the laminating and assembly it really is avoidable yeah sometimes it's a pain did it bake a board for two, four, six, sometimes 24 hours but, that's what it takes to yield well but it's it's still worth it and that’s something that comes up a lot.
Well I know that I worked for a smaller art shop and we had the case where we were doing kind of pre-production quantities and the board was cooking along, no problem, and then one day it wasn't working. Guess what, it had rained for a week and we didn't have them in an airtight storage or whatever, so we had to completely look the way we were storing and make sure we were baking this, because in California, it doesn't rain that much and it wasn't first and foremost on our brains and when it came down to that, it was like what? Yeah didn't see that one coming at all.
I've seen that happen yeah, I've seen that it where customers or assemblers, they don't bake for years and think everything is great and they want to know what's changed and it's well material’s the same...
Had a heavy winter...
Yeah and it turns out it was something like that, it's always best practice to bake and it varies so much by design - ground planes are a problem. In fact there was a great study done recently with HD Paragon, I don't know if you if your listeners are familiar?
Maybe not, but we’ll put that link below in the show notes. Because they're an amazing asset to our industry.
So they did a great study on crosshatch ground planes on flex so there's some performance trade-offs to the crosshatch ground planes, but they do create a window. Moisture will get in more easily but it can get out more easily and when - as opposed to a solid plane - there is a frequency cut off where that is usable and one of the things the study looked at was diamond-shaped versus round openings in the ground plane. But I always like to put, or recommend putting, openings in the ground plane when you can afford it - just as a moisture egress.
Hmm, that’s new to me, so neat but it completely makes sense right? if you're locking in moisture inside of the laminate because you're capping it off, you're trapping it right?
Right, and a lot of the PCB processes are water based or aqueous based chemistries, even up to the surface finish. You know, Enog one of the most popular surface finishes, it sits in a hot bath for 30 minutes, actually two hot baths. The gold bath in the NIP and the nickel plating bath or high temperature what, 180 Fahrenheit - 190 Fahrenheit for 20 or 30 minutes in each bath. That's a big opportunity for the moisture uptake on the part, and if you can imagine, that's near when the part is finished. It usually gets routed and cleaned and electrical tests and a few other things. But then it goes out to the company that does the assembly some assemblers require the board shop to bake, which is okay if you put it in a moisture proof bag, but even that's not a guarantee because the workshop loses control over when it was opened and how long it stays in the atmosphere before it gets assembled and so on and so forth...
-or just before it gets bagged.
Yeah right.
And it may already be present and you're just vacuum sealing a moisture-laden board. It’s so many moving pieces, I always say, I wish my dear friends that were printed circuit board designers or engineers that are designing boards now understood the complexity of board manufacturing because you and I've been talking this whole time about just the laminates this is not drilling, laminating buried and blind vias, filling vias. There's so many moving pieces and I think sometimes copper bond treatments? Yeah all of that and I think in this day and age, a bare board is a line item on your bomb. It's not like pulling a component off the shelf and so I think the closer board fabricators and engineers can get together the better for both actually. Because sometimes I think the board fabricators also get exasperated with designers, but the technology is being driven in a certain way. And they're gonna be the first ones to see it and can actually help enable the board manufacturers in many cases so it kind of goes both ways
An experienced designer will know what the board shop needs and that's again - that comes from communication - things like minimum clearances, designed for manufacturability, those types of things, and in fact all the board fabricators I know are very good about working with their customers to try. And again it's in everyone's best interest to yield well and have a part that survives.
Absolutely, and back to Kelly Dack, we had a long conversation - actually two people here at Altium, all of our AEs and FEs here - are required to take the CID course and so two guys here recently took it and for the first time I got to look through the workbook. Holy cow this thing is like this thick and a huge percentage of that is the DFM things. It's understanding, so to hopefully save time and money and headache on the end of the designer.
Well Chris, I know we've only got started but we need to do this again clearly, because the other thing I want to talk with you about is flex, because flex is on the rise and I know you'll have a lot of insight there and I would love to ask you more about that. But before we go I always do this thing at the end of the podcast called ‘designers after hours’ because most people in our industry usually have some kind of interesting hobby. or a lot of us, even though we kind of act left brained, we have a pretty active right brain too actually, so sometimes we're creative or do something interesting. So do you have anything that you enjoy doing after hours, sort of unique?
Yeah so actually I've been I've been diving, gosh since the late 70s…
Diving? Oh scuba diving I thought you said dieting, okay!
Yeah so actually I started back east when I was living in New Jersey I actually did some shore diving and some wreck diving and that was a lot of fun. Now in California, when I was living in Southern California, it was Catalina Island and the Channel Islands and so on and so forth. But here in northern Cali the best place to go is Monterey. I've done some abalone diving up in Mendocino, but that's free diving that's not scuba. But, in fact, I've taken my sister my niece there. There's divers also and we've gone down to Monterey and I've done that so that's one of things I like to do. It's something I don't get to do as often as I like of course.
I know we're all so busy. Well speaking of free diving for abalone my mom and dad grew up here in San Diego - I grew up in in Orange County just about two hours north of here - but my mom, when she was a teenager used to free dive for abalone in La Jolla Cove. So about a year ago I moved down here and I'm itching to go get certified and do diving here because there's some really neat dive spots here. But we went to the area where my mom used to free dive and my daughter came up from snorkeling one day and pulled up two abalone shells, which is so rare.
Yeah
Well down here it's so picked over it's like there's divers out every weekend so it's really rare to find live abalone anymore. But anyway, she brought up a couple of shells.
Interesting fact about La Jolla, you can find electric rays down there so Rays are capable of delivering an electric shock.
Really?
Yeah well check it out they're pretty cool - but don't touch them - yeah, they're pretty cool.
Yes my interest in electronics and nature stops. Well thank you Chris, so much, this has been fascinating and I want to ask you 50 more questions but if you will say yes we'll do this again in a month or so and we'll talk about flex.
Sounds great.
Okay thanks so much Chris.
Again this has been Judy Warner and Chris Hunrath with the OnTrack podcast. Thanks for joining today, we look forward to you tuning in again and until then, remember to always stay OnTrack.