Episodes
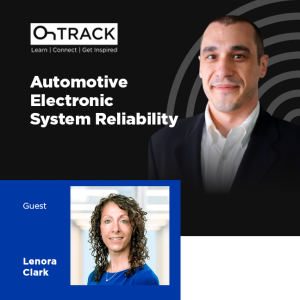
Wednesday Sep 14, 2022
Better Performance and Enhanced Reliability in the Automotive Electronics industry
Wednesday Sep 14, 2022
Wednesday Sep 14, 2022
Performance and reliability are big in the automotive industry, especially now that electronically powered and automated vehicles are starting to become more popular.
In this episode, we will learn so much about automotive electronics and the reliability of electronics systems that goes in the vehicle. Our guest Lenora Clark, the director of autonomous driving and safety technology at ESI automotive will share with us the importance of material choices for your PCB can affect the reliability and performance of your vehicle’s system design.
Show Highlights:
- Lenora is Chemist by education. She joined MacDermid, now MacDermid Alpha Electronic Solutions, as a bench top chemist, developing chemicals for PCB manufacturers
- Her focus was on surface finishing helping PCB fabricator improve their process from a chemical standpoint to enhance the performance and reliability of PCBs
- From working with surface finishing, she worked her way up and became the project manager, product line director for surface finishing, and later the Director of OEMs
- She is now a director at ESI automotive
- Chips don’t float, they are anchored to a PCB to work
- Lenora briefly described her role and emphasis on enhanced reliability to meet the end users' needs
- There is so much happening in the automotive space towards reinventing themselves and keeping up with the amount of innovation that's happening right now
- One of the challenges in the industry is extreme miniaturization
- Miniaturization is not just the board itself and the packaging but also feature density
- Other than the heat, electromagnetic shielding is also a concern with enclosure designs
- Lenora emphasizes that her current role is to make recommendations based on a material perspective, both for liability and for enhanced function
- ECUs (Electronic control unit) manages data transmission between different parts of the vehicle
- Lenora is Chemist by education. She joined MacDermid, now MacDermid Alpha Electronic Solutions, as a bench top chemist, developing chemicals for PCB manufacturers
- I think the future of the vehicle architecture is not completely defined yet. I do think it will be less complex than what we see today - Lenora Clark
- Collaborators like Mobileeye by Intel are working with makers to bring an entire system where there are different, sensors and a central computing unit to help make the decision – autonomous driving
Links and Resources:
Connect with Lenora Clark on LinkedIn
Visit ESI Auto website
Related Podcast Episode:
How to Select the Best Surface Finish for your PCB
Electronics Manufacturability and Reliability

Wednesday Sep 07, 2022
Electronics Manufacturability and Reliability with QA Guru Cheryl Tulkoff
Wednesday Sep 07, 2022
Wednesday Sep 07, 2022
Let’s talk about Electronics reliability with the QA guru Cheryl Tulkoff.
In this episode Cheryl and I will talk about risk assessment, planning for not only success but also a failure, and understanding the difference between quality and reliability. This discussion is going to be very informative for every PCB designer who wants to get ahead of their game. Watch through the end, and make sure to check the additional resources below.
Show Highlights:
- Cheryl shares her rewarding career experience in the electronics industry
- She worked at IBM where she was immersed in electronic manufacturing from beginning to end
- She also worked at DfR Solutions and National Instruments where she learned all the skills and knowledge in electronics manufacturability, quality & reliability consulting
- To produce a successful electronic product it is important to have the awareness to resolve every problem, from the chip level, board level, system level, and the environment level
- Cheryl explains why unique or non-aligned standards exist in the industry – no one size fits all
- A great piece of advice for all PCB designers is to know what you are designing and who you are designing it for, look at the risks, and then manage them appropriately
- Planning for success may also include celebrating failures. Budget for failure analysis is often disregarded due to the “success-driven roadmap” mentality
- Failure should be part of design management
- Cheryl and Zach talk about the “Startup Culture”
- Software reliability and hardware reliability go hand in hand
- What rate of failure is tolerable? Defining what is quality and reliability separately for the product you are designing
- Manufacturers can not ensure reliability for you
- Cheryl shares her experience being involved in litigation as an expert witness
- Redundancy practices in the industry, is it typical?
- What can designers do to mitigate failures?
- Understanding what you are designing and who you are designing it for
- Collect as much feedback as possible – from users, industry experts, and professional organizations
Links and Resources:
- Connect with Cheryl Tulkoff on LinkedIn
- Read Cheryl Tulkoff articles on Research Gate
- Checkout Cheryl Tulkoff book Design for Excellence in Electronics Manufacturing
- Connect with Zach on LinkedIn
- Full OnTrack Podcast Library
- Altium Website
Get Your First Month of Altium Designer® for FREE
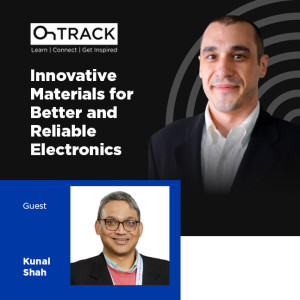
Wednesday Aug 31, 2022
How to Select the Best Surface Finish for Your PCB
Wednesday Aug 31, 2022
Wednesday Aug 31, 2022
You would not want to miss this informative, knowledge-packed conversation with Dr. Kunal Shah. Dr, Kunal generously gives us all a crash course on surface finishes and understanding different types of materials that could affect signal integrity, reliability and electronic shelf life. He will also tackle in detail the pros and cons of various types of nickel-free finishes.
Watch this podcast episode now or listen on the go. Make sure to check the notes and additional resources below.
Show Highlights:
- PCB Designers must be knowledgeable of various manufacturing processes and materials
- One of the things that makes liloTree unique is its innovation in materials development and ensuring better and robust reliability of the electronic assembly
- liloTree offers eco-friendly solutions (organic surface finishes) that enhance reliability and offer better performance in terms of signal integrity
- Dr. Kunal shares his background and how he founded liloTree
- Manufacturers are trying to find alternatives for ENIG (Electroless nickel immersion gold) due to nickel causing signal integrity loss in the high-frequency application
- There are several nickel-free surface finish, but designers must understand selection criteria – pros and cons of each types of materials
- immersion tin does have higher insertion loss
- OSP (organic solderability preservatives) is an organic-based surface finish. It provides good signal integrity, but has low shelf life issues
- Hard Gold has good signal integrity but very costly
- Electro-less palladium, immersion gold or autocatalytic gold it includes cumbersome process and need to babysit it
- A PCB must have both good signal integrity, great performance, and extended shelf life
- Designers must realize the impact of the supply chain issues on the PCB manufacturing life cycle
- Shelf life is critical. Boards are getting manufactured in one part of the world and it may take a few months before they get assembled in another side of the world
- LiloTree has developed the best nickel-free option, specifically designed from a signal integrity perspective, reliability perspective, and cost effectiveness perspective
- Another challenge of nickel based finishes is overplating and the skip plating in the PCB pads that could lead to micron scale level failures
- The liloTree nickel free solution includes a “barrier layer” which has multiple benefits including slower growth of intermetallics, delaying of natural embrittlement and eventually an extended shelf life
- How to overcome multiple reflow issues?
- Dr. Kunal explains the different ways they offer their solution to the market
- They offer their prototype lab where manufacturers and OEM can apply liloTree technology to evaluate and test it
- PCB manufacturer from OEM or assemblies feedback, the solution will be shipped directly to the manufacturer and set it up in their existing plating line
- Sending the boards to liloTree’s in-house plating line
Links and Resources:
Connect with Dr. Kunal Shah on LinkedIn
Visit liloTree website
Connect with Zach on LinkedIn
Full OnTrack Podcast Library
Altium Website
Get Your First Month of Altium Designer® for FREE
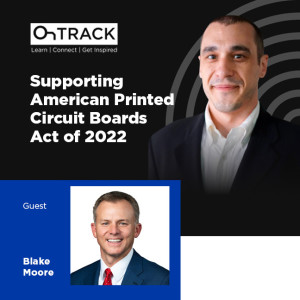
Wednesday Aug 24, 2022
What is in the PCB Bill?
Wednesday Aug 24, 2022
Wednesday Aug 24, 2022
In this episode, Representative Moore, one of the co-sponsors of H.R.7677, the Supporting American Printed Circuit Boards Act of 2022, will give us brief but insightful details about the bill.
Show Highlights:
- Representative Blake Moore explains the reasons behind the efforts to push the Supporting American Printed Circuit Boards Act of 2022
- Rep. Moore briefly touches on the topic of material sourcing and potential environmental challenges
- A potential roadblock concerning raw materials is overcoming challenges coming from the energy and commerce committee
- What is the ideal market share for the US in the PCB manufacturing industry?
- The CHIPS Act and defining industrial policy
- Initiatives in developing a qualified workforce that can fill the new manufacturing jobs and all of the other jobs that come along with it to support the industry
- Sign up for the Electronic Design to Delivery Index to help guide you through supply chain turmoil
Links and Resources:
Sign up for the Electronic Design to Delivery Index
Learn more about the Supporting American Printed Circuit Boards Act of 2022
Learn more about the CHIPS Act
Watch the related episodes:
Data Security, 5G and Onshore PCB Manufacturing with Dr. Rob Spalding
IPC CEO John Mitchell on the Supporting American Printed Circuit Boards Act
The Benefits of Diversifying PCB Industry Supply Chain
Full OnTrack Podcast Library
Altium Website
Get Your First Month of Altium Designer® for FREE
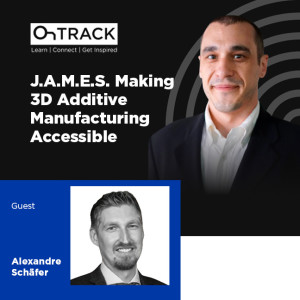
Wednesday Aug 17, 2022
The Promising and Challenging Future of 3D Printed Electronics
Wednesday Aug 17, 2022
Wednesday Aug 17, 2022
The business development manager of J.A.M.E.S., Alexandre Schafer talks about the organization’s vision to push the Additively Manufactured Electronic technology to become more accessible to the industry.
Show Highlights:
- What is J.A.M.E.S. and how did Alexandre become involved in the organization?
- J.A.M.E.S (Jetted Additively Manufactured Electronic Sources) is an online community of professionals, stake holder, manufacturers who share the same vision of accelerating the AME technology
- Alexadre’s AHA moment was seeing a drone’s PCB created through AME process
- The current technology readiness level is currently between experimental and demonstration pilot phase
- Introducing new technology to the industry has it’s challenges:
- Influencing engineers’ mindset
- Which design tool to use? In an ideal world a tool with both ECAD and MCAD design capabilities is necessary–a fully working 3D auto router will be amazing
- Design standards are inexistent at the moment
- On another note, the lack of design standards opens up to wider creative possibilities. Standardation is the enemy of freedom -Zach Peterson
- Moving forward to future plans: Scaling up, manufacturing of the equipments and creation of additive process design rules
- Availability of resources and current efforts to educate PCB designers through AME Academy
Links and Resources:
Follow J.A.M.E.S on LinkedIn
Connect with Alexandre Schafer on LinkedIn
Access Register to AME Academy
Visit J.A.M.E.S website
Full OnTrack Podcast Library
Altium Website
Get Your First Month of Altium Designer® for FREE

Tuesday Jun 28, 2022
IPC CEO John Mitchell on the Supporting American Printed Circuit Boards Act
Tuesday Jun 28, 2022
Tuesday Jun 28, 2022
Supply chain security and having access to trusted manufacturers in the US would be an ideal outcome of the Printed Circuit Board Act.
IPC President and CEO John Michell talk about how the organization helps shape the current bipartisan proposal to help bring back PCB manufacturing in the US and how this can contribute to a globally resilient supply chain.
Get Your First Month of Altium Designer® for FREE
Show Highlights:
- John Mitchell briefly talks about his background and dives right into the topic, the Supporting American Printed Circuit Boards Act
- John emphasizes the role of the IPC as the voice of the electronics industry
- Supply chain security and having more trusted PCB manufacturers in the US would be a great outcome of the Printed Circuit Board Act
- Adapting the existing legislation on manufacturing defense products to broader use, especially with electronics
- Raise awareness of the different aspects of the electronics supply chain shortages and other issues related to it
- Eradicate the notion that PCBs are just a piece of plastic, but an essential piece in every electronic
- The IPC's influence on shaping laws relating to the electronics
- John explains IPC's role and involvement, which includes solving industry problems related, but not limited to, the workforce, supply chain, and advanced packaging issues
- The IPC SEA Tools: Standards, Education, and Advocacy
- John stresses that having manufacturers in different regions is a key to a resilient supply chain
- Identify what electronic products to manufacture where
- The Printed Circuit Board is a 60 billion industry globally, and only 3-5% of volume comes from the US
- John explains the impact of the changing administrations in the US on the current progression of different bills and legislations relating to the electronic industry
Links and Resources:
Connect with John Mitchell on LinkedIn
Visit the IPC website here
Learn more about the Supporting American Printed Circuit Boards Act of 2022
Watch John Mitchell’s previous episodes:
- IPC CEO John Mitchell on the Impact of COVID-19 on the Electronics Supply Chain
- John Mitchell, CEO of IPC, Visits The White House to Participate in the Pledge to America’s Workers
Watch a recent related episode: The Benefits of Diversifying PCB Industry Supply Chain
Full OnTrack Podcast Library
Altium Website
Get Your First Month of Altium Designer® for FREE

Wednesday Jun 15, 2022
Occam Process: Assembly without Solder
Wednesday Jun 15, 2022
Wednesday Jun 15, 2022
Have you heard of assembly without solder? In this episode, Joseph (Joe) Fjelstad, founder and president of Verdant Electronics, talks about the Occam process.
Let’s hear about Joe’s 50 years of experience in the electronics industry and how he got started with solderless assembly for electronics.
Altium 365: Where the World Designs Electronics
Show Highlights:
- Joe talks about his background and previous roles in the industry, including his position as the educational director in the IPC and Kurchatov Institute of Atomic Research in the Soviet Union
- “Assembly without solder” Joe recollects how he arrived at the idea of a better way to build electronics – build a component board and put circuits on it.
- Joe shares how he came up with the Occam process and its benefits “It absolutely doesn't need to be for everything, but it can be for a lot of things, and it can make products that will be at once cheaper, better performing, lighter, more environmentally friendly.”
- Download Joe’s book for free: Solderless Assembly for Electronics: The SAFE Approach
- More about the Occam Process
- Did Joe coin “Design with Manufacturing”? He shares his efforts in promoting solid work relationships between PCB designers and manufacturer
- Occam Process vs. 3D printing, could 3D printing bypass solderless assembly? Read Joe’s article Putting 3D interconnection technologies into perspective from chip to system
- Joe commended the microvia technology, “they know how to build these things”
Links and Resources:
Connect with Joseph Fjelstad on LinkedIn
Visit Verdant Electronics website
Read Joe Fjelstad Interview: Breaks Down His Occam Process
Download Joe’s book for free: Solderless Assembly for Electronics: The SAFE Approach
Connect with Zach on LinkedIn
Full OnTrack Podcast Library
Altium Website
Download your Altium Designer Free Trial
Learn More about Altium Nexus
Altium 365: Where the World Designs Electronics
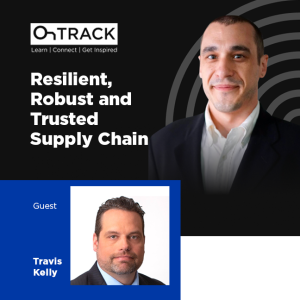
Wednesday Jun 08, 2022
The Benefits of Diversifying PCB Industry Supply Chain
Wednesday Jun 08, 2022
Wednesday Jun 08, 2022
To develop a resilient ecosystem, understanding the root cause of the PCB industry supply chain shortages is a must.
In this episode, Travis Kelly, president and CEO of Isola Group will help us understand what is going on with the current supply chain in the electronics industry. Travis will also give us his insight into the new legislation introduced in the US Congress: Bipartisan Bill to Bring Electronics Manufacturing to America and Strengthen Supply Chains.
Tune in, or listen on the go. Stay up to date with the latest discussion in the PCB Industry.
Altium 365: Where the World Designs Electronics
Watch the video, click here. t
Show Highlights:
- Travis's introduction and a brief overview of PCB manufacturing and fabrication in the United States
- About 20 years ago, the US produced roughly 26% of the world's PCBs; today, that number is down to 4%
- There used to be over 2000 fabricators in the late 1990s and early 2000 to less than 140 today
- What are the main drivers of the PCB industry supply chain shift?
- The industry recognizes the benefits of working in a global economy; Travis explained the need to diversify manufacturing capabilities in certain regions
- Identify what makes sense to have a robust supply chain domestically, e.g., 5G, 6G, medical, aerospace, obviously defense, banking infrastructures
- Travis stresses that there are ways to reduce the overall cost of PCB and electronics production and still manufacture domestically
- Looking at the entire ecosystem and pointing out vulnerabilities outside of just chips and advanced packaging, how to address each one?
- Focus on a balanced approach, not over-indexing; strategically, where does it make sense to build brick and mortar to have a resilient, robust, and trusted supply chain?
- What does it mean to bring manufacturing onshore?
- Building a strategic and competitive PCB industry ecosystem requires more than just automated facilities; it’s also essential to invest on:
- Workforce development – hiring and building up a talented workforce domestically
- Promote STEM in schools
- Create awareness of PCB industry design and manufacturing as part of the sought after career in tech
- Travis gives insight into the new legislation introduced in the US Congress: Bipartisan Bill to Bring Electronics Manufacturing to America and Strengthen Supply Chains
- He emphasizes the importance of understanding the root cost of the imbalanced supply chain vs. addressing just the symptoms
- Continue to educate the Whitehouse on understanding the issue extensively and not just focusing on the semiconductor shortages
- Considering the cost of the end products (for consumers) when navigating and drawing solutions
- The role of the Printed Circuit Board Association of America (PCBAA) in the industry: educate, advocate and legislate
Links and Resources:
Connect with Travis Kelly on LinkedIn
Follow PCBAA on LinkedIn
Visit Isola Group’s website
Eshoo & Moore Introduce Bipartisan Bill to Bring Electronics Manufacturing to America and Strengthen Supply Chains
Connect with Zach on LinkedIn
Full OnTrack Podcast Library
Altium Website
Download your Altium Designer Free Trial
Learn More about Altium Nexus
Altium 365: Where the World Designs Electronics
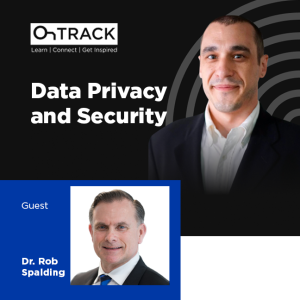
Wednesday Apr 27, 2022
Data Security, 5G and Onshore PCB Manufacturing with Dr. Rob Spalding
Wednesday Apr 27, 2022
Wednesday Apr 27, 2022
In this episode, we are very pleased to have Dr. Rob Spalding. He is a retired Brigade General at the US Air Force and now the CEO of SEMPRE (Secure EMP-Resistant Edge), a tech company based in Washinton DC that provides military-grade 5G and high-performance edge computing infrastructure for telecom operators, first responders, government and enterprise customers.
Today, Rob and I will talk about all things security! Rob will tackle the importance of being proactive when it comes to protecting your data, and his advocacy to bring a better understanding of technology and innovation in Washington, DC (White House).
Altium 365: Where the World Designs Electronics
Show Highlights:
- Rob’s background and career before he became the CEO of SEMPRE
- What is SEMPRE? What are the problems it solves and the solutions it offers?
- Rob clarifies what’s written in his 5G report, which was taken out of context in 2018
- He emphasizes building enough spectrum into the network to take full advantage of the 5G technology
- Rob’s take on PCB manufacturing, and semiconductor manufacturing onshore
- Onshore manufacturing has its advantage in controlling and protecting intellectual property
- Most corporations are making decisions on the basis of, what's my margin?
- TSMC has built itself up to be the best chip company in the world because they own the manufacturing line
- Hardware-level security in base stations
- Ability to zerorize crypto–shutting infrastructure down, and shut that thing down physically destroy certain things
- SEMPRE uses FPGAs as a security advantage
- It's data that really drive value in the economy
- If we can’t protect our data, then we can't protect the integrity of who we are as individuals and who we are as a nation
- Rob demonstrates how vulnerable is the public from being spied on
- A recent survey reveals that there will be a talent shortage in the PCB design and manufacturing industry in the next 15 years
- Rob suggests allocation of budget to sponsor American kids through four-year degree programs in STEM
- During the Cold War, the US had initiated education for national security–a lot of scientists and engineers in the space race were educated through this initiative
- The advantages of bringing the manufacturing back to the US
Links and Resources:
Connect with Dr. Rob Spalding on LinkedIn
Visit SEMPRE website
Read about the shortage of talents in the PCB industry in 15 years: In an Unpredictable World, PCB DESIGN ENGINEERING Stays Steady
US Government Calls for Revitalizing American PCB Manufacturing
Connect with Zack on LinkedIn
Full OnTrack Podcast Library
Altium Website
Download your Altium Designer Free Trial
Learn More about Altium Nexus
Altium 365: Where the World Designs Electronics
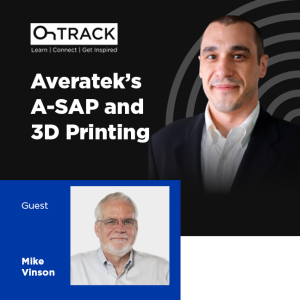
Tuesday Apr 05, 2022
The Many Benefits of Additive Process in PCB Manufacturing
Tuesday Apr 05, 2022
Tuesday Apr 05, 2022
In this episode, we will continue with the topic of Design WITH Manufacturing, and joining us is Mike Vinson, the Chief Operating Officer at Averatek. Mike will help us understand Averatek’s advanced PCB manufacturing processes, including the technology and chemistry behind A-SAP and 3D printing.
Altium 365: Where the World Designs Electronics
Show Highlights:
- Mike Vinson's background
- Mike explains what is an Additive Process
- A-SAP–a semi-additive process used to make very fine features for high definition, and high density interconnects on print circuit boards.
- The ability to add metalization other than copper, such as platinum, gold, palladium
- 3D printing–a fully-additive process where all of the material is just added on, and nothing is subtracted away
- Averatek’s business’s scope
- Licensing the technology and selling the chemistry
- The current clientele is North America
- Efficient and secure prototyping
- Is the 3D surface solderable?
- MIDs or molded interconnect devices, are cool, but are they affordable?
- Tara Dunn, Averatek’s VP in Marketing, is the primary point of contact for licensing
- Tara is also one of Altium’s Industry Expert contributor
- What’s in the Averatek’s IPC Paper
- What does the economy look like for A-SAP technology? Will it be accessible, and cost-effective?
- Mikes talks about the scalability of materials set in A-SAP technology
- How can PCB designers take advantage of the A-SAP capabilities so that they can create more compact, smaller features, more advanced products?
- How about a transparent substrate? Averatek has worked with transparent polyimides and has done some other transparent substrates
- What are the things to look forward to in additive processes and the additive manufacturing realm in general?
Links and Resources:
Connect with Mike Vinson on LinkedIn
Visit Averatek's website
Check out Tara Dunn’s Articles on Altium Resource Hub
Watch Previous Episode Mike Vinson:
Sub-25 Micron Traces with Averatek ASAP Technology
Semi-Additive Process Technology at Averatek
Connect with Zack on LinkedIn
Full OnTrack Podcast Library
Altium Website
Download your Altium Designer Free Trial
Learn More about Altium Nexus
Altium 365: Where the World Designs Electronics
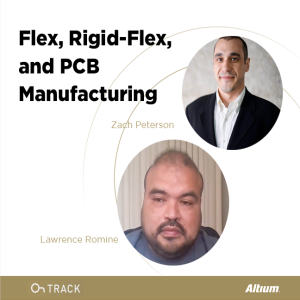
Tuesday Jan 04, 2022
High-Reliability PCB Design with Juan Frias
Tuesday Jan 04, 2022
Tuesday Jan 04, 2022
The aerospace industry has driven the high-reliability design in the center focus. Juan Frias, our guest for today, is a very experienced PCB designer who has designed for Aerospace, Military, Industrial, Semiconductor, Communications, Medical, and Automotive; he will be sharing the tips for a successful design for manufacturability. We will also tackle Flex and Rigid-Flex design. This conversation will be fun and insightful, so watch through the end and make sure to check the additional resources below.
Altium 365: Where the World Designs Electronics
Show Highlights:
- High-Reliability Design WITH Manufacturing, how did the Aerospace industry influence this focus?
- The advantages of working closely with the manufacturing team
- Focus on improving the design process and eliminating back and forth communication and miscommunications
- Understanding what will work BEST for your manufacturer
- Working with flex and rigid-flex designs
- Space savers
- Reliability and stability advantages
- Choosing between flex versus a rigid-flex board, what are the considerations?
- Can you use BGA on Flex?
- How does the manufacturer influence the material selection
- Board-spin on existing design–the systemized process of ordering materials that are running low
- The design preparation process for fabrication
- What do designers need to know about stiffener
- The importance of creating a prototype to save time and money
- PCB Validation, test and Inspections, who does what?
- Typically the customers are the only ones who can do a test with the product because they have the entire system on their end
- PCB designers perform the electrical tests and control impedance lines
- Identifying a good designer to do business with–-local vs. overseas
- See you at the AltiumLive 2022. Register here
Links and Resources:
AltiumLive 2022 Connect: Now open for registration
E-Book: Navigating PCB Manufacturing: Part 1
Three Common PCB Design Mistakes You Can Spot in Your Gerbers
How to Successfully Design a BGA
Connect with Zach Peterson on LinkedIn
Watch Zach’s latest Altium Academy courses on Youtube
Read Zach’s articles on Altium’s resource hub
Full OnTrack Podcast Library
Altium Website
Download your Altium Designer Free Trial
Learn More about Altium Nexus
Altium 365: Where the World Designs Electronics
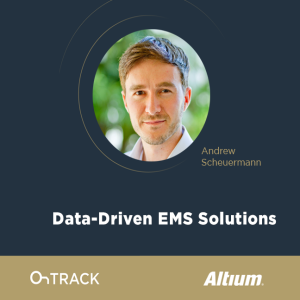
Tuesday Aug 17, 2021
Data-Driven Smart Manufacturing
Tuesday Aug 17, 2021
Tuesday Aug 17, 2021
A Silicon Valley rising star advocates higher efficiency in electronics manufacturing.
In this episode, Andrew Scheuermann, CEO, and Co-founder of Arch, shares his company’s mission to drive digitization and sustainable innovation in electronics manufacturing. He will discuss Surface Mount Technology machine optimization and how factories can benefit from advanced analytics.
Altium 365: Where the World Designs Electronics
Watch the video, click here. [link to website live page]
Show Highlights:
- Introduction to Andrew and the founding of Arch Systems
- Understanding the founders, Andrew Scheuermann and Tim Burke’s experimentalist and theoretical personas, respectively
- The key to finding their niche
- Starting Startx - top 5 startup in the world
- Platform mindset - software and hardware technology that could be deployed to any kind of machine
- Become a world expert in Surface Mount Technology (SMT) machines
- Industrial Automation, how does software makes the world go round?
- Opportunity identified for SMT industrial control automation and useable, meaningful data
- Data-driven, smart manufacturing
- In-depth analytics-getting data out of legacy machines
- Digital Proof of concept, why is this valuable?
- 20 - 40 or even 60 percent improvement in manufacturing efficiency
- Predicted quality, 99% OK what do you do with the 1%?
- How do you get data out of the machine and translate them into meaningful solutions?
- Universal translation, aggregation, data security
- Andrew explains ArchFX broker being deployed on-premise
- The benefits of advanced analytics - Improved Quality, reliability, speed, better-increased margins, Informed CapX spend
Arch Systems Website
Arch Systems Overview Video
The ArchFX Platform: The Proven Fast Track to Transformation
Full OnTrack Podcast Library
Altium Website
Download your Altium Designer Free Trial
Learn More about Altium Nexus
Altium 365: Where the World Designs Electronics
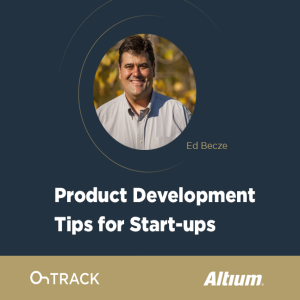
Tuesday Jul 27, 2021
Key Factors of Thoughtful Design
Tuesday Jul 27, 2021
Tuesday Jul 27, 2021
“Engage your suppliers early on the design process” - Ed Becze
Everyone wants a lower price, and often the “real cost” is not realized until it’s too late. In this episode, Ed Becze of Pegmatis, a highly experienced R&D company with end-to-end product development capabilities, joins us to help start-ups and design engineers like you avoid electronic product development failures.
Altium 365: Where the World Designs Electronics
Watch the video, click here.
Show Highlights:
- Introduction and the interesting origin of Pegmatis’s company name
- Ed explains the foundation of a good product development process
- A thoughtful development plan mitigates risk early on—engage vendors and suppliers early on the design process (understand parts, availability, vendor capabilities aligned with your product)
- Holistic understanding of electronic product development: strategy, cost, and your design team’s experience level
- Start-up challenges, how to prevent failures:
- Understanding the risk of “development by demo”
- Address the lack of system-level design experience (use external expertise if needed)
- Don’t trust the data sheets—only 5% of chipset providers give adequate design rules to follow. The rest, you are on your own.
- Manufacturing test is absolutely critical—test equipment and test development are often overlooked
- Engage early on the design process. Ed stresses the benefits of nurturing your relationships with your vendors and manufacturers.
- Successful product development relies exclusively on your network—find capable vendors
- Supply chain intelligence, plan ahead when coping with supply challenges
- Cost reduction—do it, but follow the process that is within the constraints of what you intended to create.
- What are the costs of NOT thoughtfully designing? It’s huge! Money and time. Delays inTime to market are extremely expensive.
Links and Resources:
Pegmatis Website
Ed Becze on LinkedIn
Full OnTrack Podcast Library
Altium Website
Download your Altium Designer Free Trial
Altium 365: Where the World Designs Electronics
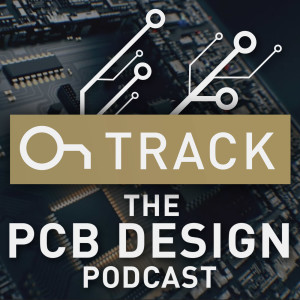
Tuesday Apr 02, 2019
Materials 101 with EIPC Chairman Alun Morgan
Tuesday Apr 02, 2019
Tuesday Apr 02, 2019
Meet Alun Morgan, Technology Ambassador for Ventec, a world leader in the production of high quality, high performance copper clad laminates and prepregs with a world-wide distribution network. Alun interacts with customers around the world promoting Ventec materials, and brings the latest market requirements to Ventec in order to develop new products.
Watch the Video here.
Show Highlights:
- Alun is a Material Scientist, with a B.Sc. Hons in Metallurgy from the University of Surrey. Once he became involved in PCB manufacturing he found it such a fascinating field that he has spent his entire career refining his knowledge.
- Everything Ventec does can also apply to smaller scale operations who are making PCBs.
- Alun was a Keynote Speaker at AltiumLive
- The FR-4 we use today has it roots around 60 years ago; there was an FR1, 2 and 3, as well as FR-5. According to the NEMA specification from the 1960s, FR is defined as Flame Retardant.
- FR-4 also means the fourth generation of materials in the NEMA classifications system. It defines the resin kind and the reinforcement type.
- FR-4 is an epoxy resin and the reinforcement is typically woven glass fibres for strength.
- The substrate itself is a composite of these two materials; the resin, the reinforcement and the conductor which is copper.
- Why the different composites? The main reason is its strength, it’s a very good insulator, and it’s available. It also bonds chemically to glass fibres very well.
- Lead-Free soldering created a major change about 20 years ago when lead was banned from electronic assemblies causing a range of performance issues.
- Higher temps expand materials dramatically, and because there is no reinforcement in the Z-axis, the expansion is considerable.
- When materials are heated beyond the TG, or Glass Transition temperature, thermal expansion is rapid and massive.
- The solution to this is adding inorganic fillers to modified, lead-free compatible materials to reduce the Z-axis expansion of which there are several types such as silica-based materials.
- Losses impact - some inorganic fillers have lower loss than the epoxy resin they’re replacing.
- How to choose materials? Talk to your manufacturers about the correct materials, ask which material they use the most and which of them work most successfully. Do beware of SI though, as this is a very fast-moving aspect currently.
- It is strongly advised to attend materials courses, and ask questions. Ventec is always ready to assist and answer questions. Go to a boardshop and see how these things are produced.
- Alun is also the EIPC Chairman and anyone involved with PCBs is welcome to attend their events. There are two conferences every year and the next will be in Austria, on June 14th and 15th. This will include a facility tour of ATNS, the biggest grossing PCB shop in Europe.
Links and Resources:
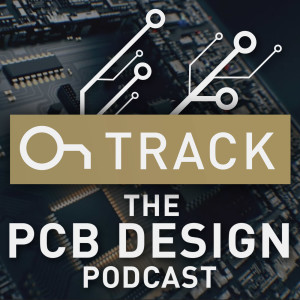
Tuesday Mar 19, 2019
Why Protect Vias and What is IPC 4761?
Tuesday Mar 19, 2019
Tuesday Mar 19, 2019
Why do we need to protect vias? Here to answer is Gerry Partida, Director of Engineering at Summit Interconnect Technologies. Summit is an advanced technology manufacturer creating custom printed circuit boards. Summit focuses on complex rigid and rigid-flex products and offers extensive expertise in RF/Microwave applications. In today’s episode, Gerry will help us untangle IPC 4761 and get actionable info that you can apply to your designs.
Watch the Video here.
Show Highlights:
- IPC 4761 comprises design guidelines on seven existing methods of via protection
- Combinations: Capping one side vs the other side, dry film soldermask with soldermask over, or via plugged with solder mask capped over with soldermask or not, plated shut via epoxy filled and plated over, or via and pad also known as Type 7 which is popular for HDI (High Density Interconnect)
- Why protect Vias? To prevent solder paste from running down an open via to the other side of the board, preventing solder balls on the secondary side, moisture protection, sealing to prevent chemistry entering and becoming trapped, to ease the subsequent processes, and finally assembly
- For via protection with a surface finish like ENIG or ENEPIG, both sides of the via need to be open during the ENIG or ENEPIG process.
- IPC 6012 Class 3 now prescribes the same thickness for copper wrap plating
- Why do people fill? Primary reason is to get the via at the pad connection in the component
- When you’re talking about High Speed Digital, you don’t want to go from trace to via
- Place via in land to avoid delay and reduced real estate for routing
- Slight reduction in reliability when via is plated, epoxy-filled and plated over versus a via only plated in the final
- Peel strength is much lower when you epoxy-fill is in the center and plated over
- You have to buy IPC standards
- Encroach soldermask clearances - encroaching soldermask on top of the LAN but not in the hole is an excellent solution.
Links and Resources:
Click here to view all Episodes
Or click here to access the Altium Designer Free Trial Today.
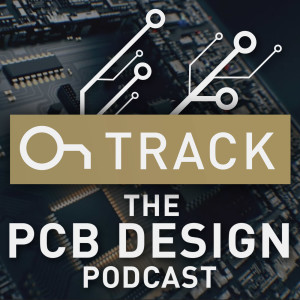
Tuesday Feb 26, 2019
Semi-Additive Process Technology at Averatek
Tuesday Feb 26, 2019
Tuesday Feb 26, 2019
In today’s OnTrack Podcast Judy talks to Mike Vinson, the COO of Averatek about their breakthrough innovation in which they use a semi-additive process incorporating a liquid metal ink as the catalyst seed layer. This special catalytic precursor “ink” can be imaged to create the patterns or areas where conducting metal is to be deposited. This ink controls the horizontal dimensions of line width and spacing and creates the ability to get down to 1 mm and sub-1 mm line and traces. Keep an eye on this technology! Welcome to the future.
Watch the VIDEO HERE.
Show Highlights:
- Mike’s background is in semiconductors primarily in the area of interconnects.
- At Averatek they create HDI solutions.
- What does Averatek’s technology enable engineers and product developers to realize? Lower layer count, Improve Yield, Cost reduction and High Value
- What is Semi-Additive Process Technology? Fundamentally the ink carries plating onto the surface of the substrate, depositing them in very thin layers.
- Also called atomic layer deposition - Averatek calls it lipid metal ink.
- Process allows for very precise and very small circuits.
- Learn the jargon: SAP (Semi-Additive Process).
- Copper can be left undisturbed by the etching process.
- Can be run in a traditional board shop - new technologies are emerging.
- Lithography capital equipment is indeed a worthwhile investment.
- Liquid Metal Ink where are you in getting this to market? Strategy is to license and sell liquid metal ink.
- What type of design considerations will EDA tools need to build-in to enable design with this technology? Smaller lands and increased density.
- Evolution: Lines & Spaces first then other areas.
- Thieving areas parameters will change.
- This tech will work for both flex, rigid-flex, and rigid circuits.
Links and Resources:
Email: mike@averatek.com
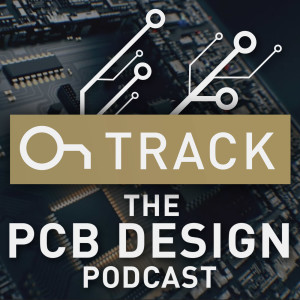
Tuesday Feb 05, 2019
Printed Electronics Applications and Innovations
Tuesday Feb 05, 2019
Tuesday Feb 05, 2019
The use of printed electronics is on the rise, and Chris Hunrath from Insulectro is here to talk about how to design for it. Learn about the different applications and design possibilities that are available to PCB designers. The proliferation of more advanced printed electronics materials from polyester film, polycarbonate, to transfer film for fabric and flexible circuitry have enabled interesting new applications for printed electronics. Listen in to learn the latest from Chris Hunrath, an expert in material supplies for circuit board design.
Watch the video, click here.
Show Highlights:
- Insulectro has seen a significant growth in sales of printed electronics products, this is an area of massive growth.
- Printed Electronics have traditionally been used in RFID along with metal f
- oils such as anti-theft devices and security access cards - items with conductive inks and membrane touch switches, for example: coffee makers, dishwashers, rear window defoggers, etc.
- Interesting new applications include: glucose test strips, wearables - sensors of all kinds, automotive, and self darkening windows.
- Self darkening windows are used in skyscrapers and aeroplanes, silver conductive ink, placing current on the window, giving the user control and saving energy.
- Printed Electronics is a high-growth area: business doubled every year in the past five years, doing very well in both substrates and inks.
- Predominant applications driving this uptick in usage: Capacitive Touch switching, in general it saves costs, lighter in weight and has no moving parts (i.e. car dashboards: a lot of work being done on it today) makes it more reliable.
- The molded structure: print the matte side and ink moves with plastic when molding, circuitry is totally encapsulated in the injection molding process.
- Ink technology: silver is used and is cheaper than gold and more conductive; silver flake or conductive particles make it possible to have the ink move with the plastic.
- Insulectro offers materials for Printed Electronics, some examples: polyester film - trade name Mylar and other brands, polycarbonate, transfer film for fabric and flexible circuitry in wearables.
- What’s the difference between conventional and printed electronics? Conductivity, and Resistance - know the sheet resistance and use a comparable copper thickness and width.
- Altium Designer 19 and Tactotek, who do in-mold structural electronics are working on relative design features in Altium.
- Printed Electronics whiteboard video
- There are inks that can sense chemistry and can be ion selective i.e. blood glucose, natural gas, carbon monoxide and so forth,
- Applications in wearables: Neural bypass, can pick up nerve impulses, movement sensors, chemistry sensors and more, and can withstand several washings.
- Higher silver loading inks can be used in many different applications.
- Chris shows an example of printed antenna that uses silver inks.
- Can be used in materials that you couldn’t use in a traditional PCB process.
- Conductive ink kits for children - you can draw conductive inks with a pen.
- Chris shows an example of substrate with high temperature ink, that has a 500-degree operating temperature.
- Events where you can see examples at the Insulectro booth: IPC Apex in San Diego, DesignCon in Santa Clara and Insulectro typically at IT TechEX.
- Conductive adhesive is more ideal for components, soldering to printed electronics is very delicate.
- Screen printing is the main way to print and is very scalable.
- Printed electronics is easier and cheaper to get started and environmentally more friendly.
- Stay posted for more developments in this exciting field!
Links and Resources:
Tactotek IMSE / Printed Electronics Podcast
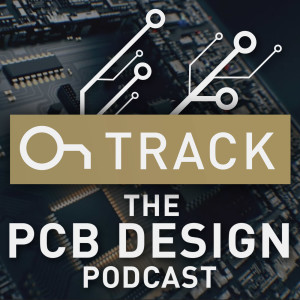
Tuesday Jan 29, 2019
Embedded Capacitance and Embedded Passives with John Andresakis
Tuesday Jan 29, 2019
Tuesday Jan 29, 2019
Listen in to Judy Warner and guest John Andresakis from DowDupont and learn about embedded resistance materials. There are several benefits that make this a beneficial technology. Did you know that you can take up to 90% of your decoupling caps off the surface of the board, while improving reliability and reducing inductance? Learn about several design considerations for using embedded capacitors and build on the knowledge of experts like Rick Hartley and Eric Bogatin who both addressed inductance in their AltiumLive San Diego keynotes.
Watch the video, click HERE.
Show Highlights:
- Senior Technical Marketing Leader - Interconnect Solutions at DowDupont; 30 years experience mostly on the materials side and now at DowDupont, soon to be the new Dupont.
- Embedded capacitance -cross connections with: Rick Hartley's keynote at Altiumlive (inductance) and Eric Bogatin's keynote as well
- This reduces inductance
- Film based materials now allow embedded capacitor layers to be 1 mil or below with excellent yields
- People were practicing some form of this 30+ years ago, but according to patents 25 years or so. There used to be material concerns, but with the advanced materials i.e. improvements in technology more is possible.
- What manufacturers are providing this service? Most of them!
- It's like a version of a rigid flex, without the flex part sticking out.
- This isn’t a very hard thing to implement, it wouldn’t be difficult for the manufacturer to get up to speed on this. The things involved are not difficult to learn.
- Learn more at IPC APEX - stop by DowDuPont and Insulectro - booth 624
Links and Resources:
IPC Standard: 2316 Design Guide for Embedded Passive Device Printed Boards
DuPont Interra HK04J Planar Capacitor Laminate
IPC Standard: 4821 for embedded passive devices
Rick Hartley on the Importance of PC Board Stack-up at AltiumLive
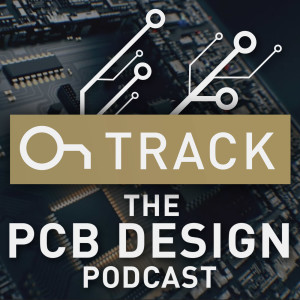
Tuesday Dec 18, 2018
Altium Designer 19: Highlights from the Latest Release with David Marrakchi
Tuesday Dec 18, 2018
Tuesday Dec 18, 2018
Altium Senior Technical Marketing Engineer, David Marrakchi is here on the show to talk about Altium Designer 19. This latest release is part two of three major releases Altium has planned to level up high-speed design capabilities. As an engineer who likes to wear multiple hats - and with experience in the field as an Electrical Engineer - David has done it all from developing requirements to schematic capture and PCB layout, across industries including home automation, military, and medical. Now he is bringing his rich skillset to the intersection of innovation and implementation by helping people understand Altium Designer and how to get the most out of the PCB design tools, easily and in the least amount of time. David is an inside expert on Altium Designer sharing his expertise on the overall processes of PCB design and product realization; playing a major role in creating product demonstrations, webinars, whiteboard videos, and interactive articles that illuminate the processes of printed circuit board manufacturing.
Watch the Podcast Video here and see more Altium Designer 19 videos.
Show Highlights:
Altium Designer 19 is released. David is hosting webinars to demonstrate new features. You can join live or on-demand--sign up for live webinars here: https://www.altium.com/webinars
What’s new in Altium Designer 19?
High Speed Design Features: What they are and how do they help designers?
- Advanced Layer Stack Management: Impedance solver, material library (vast array, pre-defined) and microvia support. Very important for tracks carrying high speed signals.
- Micro via (more info in the Interactive Routing webinar)
- Impedance modeling
- Material values - (there are always new materials coming out!)
New Part Search:
- Find a part that both meets requirements and that is also available!
- Search and filter with parametric information - global parametric supplier search. i.e. size, package, height, frequency, stock, model, and compare two parts.
Routing Improvement:
- New follow mode (allows for locking i.e. curves)
- HOTKEY / SHORTCUT: ctrl+f to lock to contour
Trace Glossing Improvements
Draftsman
Multiboard
Printed Electronics
Check out this Podcast with Tactotek to learn more.
Altium has a culture that embraces a mindset of continual “Relentless Innovation”
Some users say they’d rather us fix more bugs--why do we choose to continually innovate?
What value do you think this commitment to innovation provides to our users and the design community as a whole?
If you are an existing Altium Designer User you can download the latest version now at Altium.com.
If you are new to Altium Designer, we invite you to get behind the wheel and take it for a test drive and see why Altium has become the fastest growing PCB Design company in the world.
Links and Resources:
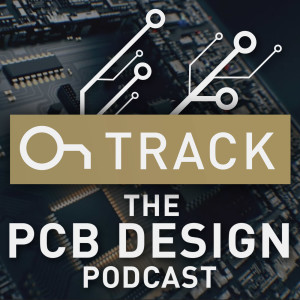
Tuesday Aug 14, 2018
Concurrent Engineering with Bill Brooks from Nordson Asymtek
Tuesday Aug 14, 2018
Tuesday Aug 14, 2018
Learn about what is involved in true concurrent engineering and get practical tips for including stakeholders early on in the design process with Bill Brooks from Nordson Asymtek. When project collaborators come together up front, then they move forward together. Hear how Bill spends the time up front to get everyone aligned during the PCB design process to ensure fabrication and assembly processes progress with minimal issues.
Show Highlights:
- Bill had an interesting childhood. His Dad was an inventor and worked on the Pioneer 10 spacecraft. He introduced Bill to the electronics industry.
- He also started a board shop in the garage and created his own hydro-squeegee, using peanut oil.
- Bill’s career started when he worked as an Electronics Technician for almost two years. When his employer started hiring designers to do PCB layout work, he grasped the opportunity.
- Back in the day, people used to sign their PCB artwork.
- There are a host of stakeholders involved, the designer is like the glue that holds everything together. Some of the stakeholders are: Fabrication, Assembly, Testing, Marketing, Managers and Engineers.
- When do you get the stakeholders involved in the PCB Design process? The IPC standard is to have a design review upfront, before design.
- The designer is the only one who can control moving the design through the process and make the board survive.
- We involve many stakeholders from the outset. Divisions like purchasing takes care of primary suppliers to ensure they can provide what’s required.
- We do system integration in-house. Partnering with other companies has become a big deal and it’s working very well.
- What does Concurrent Engineering mean? Considering all aspects, together, upfront, then moving forward together. Spend the time upfront to avoid wasted time and effort later in the process.
- Educate people who have control, they take care of everyone and everything goes smoothly, works correctly, and is right first time.
- Bill’s Dad used to say ‘the hurrier I go, the behinder I get.’ You need a disciplined management team to do the work upfront, be quick but don’t hurry.
- A ‘quick and dirty prototype’ is a myth.
- Use software to load projects into a common depository - keep it current and work in cohesion with regular refreshing.
- Bill and their team use Playbook, which enables managers to have a full overview of every division’s progress and enable proper scheduling.
- Designers after hours: in 2008 Bill was introduced to sculpting. Started attending classes, commencing a 6-year love affair with sculpting. He now teaches on Saturdays.
- Rick Hartley encouraged Bill to do mentoring. Bill is now part of the International IPC Executive Board and has received an award for his contributions.
Links and Resources:
AltiumLive 2018: Annual PCB Design Summit
Hey everyone this is Judy Warner with Altium's OnTrack Podcast. Thanks again for joining. Today we have another great guest - do you ever get tired of me saying that? Another great guest because we just have them every time, and we'll be talking with Bill Brooks today from Nordson ASYMTEK, and before we get started, I just wanted to remind you to please follow me on LinkedIn. On Twitter I'm @AltiumJudy and Altium is on LinkedIn, Facebook, and Twitter - and also if you'd rather watch this on video we also have this on Altium's YouTube channel under videos, and you'll see all of our podcasts recorded there as well.
So today we have Bill Brooks, has been a great contributor to the industry, as well as being a very talented designer in his own right. So I thought you would enjoy learning about his long history in the craft of PCB design, so Bill welcome; thank you so much for joining us here. Bill comes from just up the freeway here from our office in La Jolla, so it's handy to get him over. So Bill won't you talk about your professional history? I think you, like many printed circuit board designers; you were kind of set up to be in this industry, but you found your own path. So, tell us a little bit about that?
Yeah I guess when I was a kid I didn't know where I was gonna go...
Yeah me neither.
-my dad kind of introduced me to the electronics world, and right out of high school actually, I was still in high school - my dad was working in the aerospace industry and he decided to start his own printed circuit board shop. He looked around San Diego at the time, and there weren't a lot of shops to go get boards made and he said: well, I can do this. And so he looked up the information and we started making printed circuit boards in the garage.
Good times, that was a long time ago where you could set up a board shop in your garage.
Yeah it was - today it'd be completely illegal.
Yeah right.
[laughter]
I think the neighbors complained, he created his own hydro-squeegee and he was using a fusing oil, which was I guess peanut oil, and he bought this big 50 gallon drum of peanut oil and he used a check valve, and he put this - - he used air pressure to push it through a check valve and to spray it so he could put the boards down to get them hot after they had been coated with solder and then squeegee ''em out as he pushed on the pedal on the floor. And it would just make this nice beautiful-
It's a handheld hot air leveling machine!
-Yeah it was very dangerous, in fact, I think he got burned a couple times.
Oh I'm sure!
-but the neighbors just loved it because they’d look down at the corner of the cul-de-sac and they’d see this giant plume of black smoke coming out the back of the house, going: what's he doing over there? But dad was kind of an inventor and he liked to invent things. So he didn't go out and he was kind of a 'shade tree mechanic' - he'd figure out how to get something done on a dime and do it himself. And I guess that same ingenuity was something I picked up, I figure out how to get things done.
So how did you end up going down the design path, from building boards in the garage?
Hmmm it was kind of convoluted. I thought I wanted to be an Electronics Tech and eventually Electronics Engineer, and I started down that path. I got a job with a company that was making television headend equipment; the transmitter part of it, there was channel 52 UHF subscription television, Oak Systems and I started working as Electronics Tech for them and I did a lot of work for them for, oh at least two years as a Tech, and they were hiring in printed circuit board designers to do the layout work. And I had already learned how to do layout work with my dad's shop when I was younger and I looked at that, and I said: welI can do that. How much do you make? And I think I was making like seven bucks an hour at the time, and they were making like 10 or 11. And I said: I could do that, and I told my bosses I want to do that - I can do that! And they were: okay we'll get you in the other department and I started working in the drafting department. So I got a $3 an hour raise and I started doing layout work instead. And it kind of set me down that path. So that's how I got started anyway.
So Bill, a lot of people that have been around a while, both you and I have been around a while. There's no college to learn what you've learned. So how did you pick up, we were discussing this earlier; you've done so many aspects - RF, some electronics and mechanical, how did you pick up all those skill sets, sort of along the way?
Yeah that's kind of a long story really. My dad started me when he had his shop, and gave me a printed circuit board to do as a way to teach me how to do layout-
Okay.
-and we went to the TI Handbook and found a circuit for an audio amplifier - 10 watt audio amplifier and he said, why don't you try to build that? And so I made a schematic, I took the schematic from it, and I laid out the board and we manufactured the board and I bought the parts and I put them on the board, and I soldered them and turned it on and talked through a microphone - it worked and I went: yes that's hot!
It's so funny.
I remember in seventh or eighth grade, we had a science fair in junior high and everybody made their science project; we had a bunch of tables all set up and my dad said, well why don't you make something - - an electronic metronome? It has to do with music, and so I drew a schematic and I put the whole thing up there, and I built the metronome and I turned it on so it'd go 'tick-tock' 'tick-tock' you know, and I thought that was amazing. It was a really great and one of my friends said: Bill that was so cool, how you did that because I didn't have to do any of the work and I still got credit for it and I said well it was it was a challenge. So I took it on I put it up there but I didn't win a darn thing!
The guys who made the volcano that spews out all the stuff - they got that prize. So people didn't appreciate what I was doing. I felt a little bit geeky and kind of out of the norm as I was growing up. But I was fascinated with electronics. I was almost intimidated by it. My dad was a very good R&D guy, and he worked in the aerospace industry and he actually worked on the Pioneer 10 spacecraft, it traveled all the way past Jupiter and it's outside our solar system headed on for Aldebaran now I think.
That's crazy.
So that's kind of a neat thing and I think on one of his print circuit boards, if you find down in the little corner you'll find his initials there-
Out in the outer regions of space.
-yeah and I talked with Dr. Walker Fillius, he was the principal on the project at UCSD and after my dad passed away and he sent me back an email and he said: you know someday these little green men out there they're gonna find that and wonder: what does that mean? Why did they put that there? And a lot of people did that back in those days, you used to be so proud of your artwork you'd want to sign it and they did.
Right, that's funny.
Yeah.
So from I have to say, I think that was probably really invaluable experience for you, very young, to put together that design affected manufacturing, affected assembly, affected performance. Like at a very young age, you saw that whole overarching process - sort of on a small scale - but still; and not everybody gets that experience even today, few designers.
Few designers have ever been in a shop and actually made a print circuit board. A lot of them are dealing with the drafting side of it; they don't see the whole process.
Right and it makes such a difference to decisions you make as a designer.
Absolutely.
Right and so I can see how that sort of set you on a path to be a little bit more globally minded about the whole soup-to-nuts kind of - - from design to reliability or how something is actually functioning.
It has a lot to do with curiosity, it's funny; I've been listening to a book about Leonardo da Vinci and one thing that was amazing about him is, he had this insatiable curiosity, to almost distraction, I mean he would look at things and go: why does it work that way? And he'd start, he'd set himself a task to figure it out - and he didn't have a college or someplace to go learn those things - he had to do it himself. I've done a lot of the same kind of things in my life. I get fascinated with something and I go: well, I can figure that out, I'll go figure it out - all it takes is being brave enough to try and not being afraid to fail. Failure is just an opportunity to learn more.
So I think it was Edison once said , he did like hundreds of different ways to try to do a light bulb and he said, well now I know a hundred different ways not to make a light bulb, it's okay-
I still finally need way to know how to do it right?
-but those those skills and the curiosity drove me into expanding my knowledge base. Getting into printed circuit boards, I wanted to learn how to take the thing I knew how to make, and turn it into something that was a product. I wanted to find out how to make that product appealing to somebody so that it made them happy with the product and not unhappy with it. And that kind of dovetails with what we were talking about before.
We have, as designers we're kind of the glue to the whole design process. We may not come up with the initial idea that needs to be created, but we take that idea and we turn it into reality and we not only have to turn it into reality, so that it's electrically functional, but it can be manufactured in a reasonable way that's not super expensive, that's reliable, that survives harsh environments or abuse. It has to be testable so you can provide for test points and things of that nature. There are a whole bunch of stakeholders involved.
People who are - their job is keyed on being able to take what I create and turn it into a product that they can actually sell. The marketing people have to make sure that the product meets the customer’s needs. I have to be aware of that when I'm designing it so, I don't design in some function that makes it fail there. I have to be aware of those things. So the designer - they're kind of the key glue to the whole group.
But I find that very refreshing and I think most professional designers, from our early days of making a simple 2 layer board say, it's so much more complex now. So we tend to like head down, into our specialty right and I think, as you have said some engineers/designers have never been inside of a board shop.
Right it gives you myopia, you can only see just your part of the whole process.
And I can understand that because, I don't say that from a critical perspective, it's a very complex process. We're time constrained, resource-constrained, so it's hard to put your head up for a moment so-
You just named some of the stakeholders.
-I would say fabrication for sure, assembly, testing...
You mentioned a marketing department, probably managers too.
Managers all have cost and time constraints, they have time to market that they have to be worried about. The engineers of course, typically are going to be concerned about, can they get the parts or are the parts available; are they gonna be end of life parts?
Yeah that's a whole fun bag of fun there.
The hardest part for some designers is, they'll get the board 90% done and then the engineer comes back and goes: I can't get that part anymore, I need to put a different part in and that's bigger than the one I gave you before. And so you got to go back and fix the circuit, so you can fit that bigger part in there and make it work. And it gets quite challenging.
So when do you recommend to get those stakeholders on board and collaborating?
That's a great question and funny - if you go through the IPC; I think it's 2221-standard - it's like the very first - almost first paragraph and the thing it says: make sure you have a design review up front first, before the designing begins. Why do they say that? Those people all are going to bring their expertise, and their wants and desires, and their concerns to that meeting. Well they're gonna be a part of that and give that information to the designer who really is the only person who has control over what it ends up being. The creator - they are the creator; they take all the information and they create something that can be built, tested, cost-effective, survive, functional, not have EMI problems, EMC problems... it has to pass safety agency requirements like TV and UL you know?
Yeah.
Or stand somebody handling it and giving it an ESD shock - thousands of volts - how's it going to survive that? You know, we do Hipot testing, there's a lot of work that goes into making a board that just is not - just connect the dots.
So you're now working with Nordson ASYMTEK, which makes assembly equipment correct, or is there more than that?
Their key thing, the company I work for they're making robotic equipment. The equipment allows manufacturers to do high-speed manufacturing very reliably and typically they're dispensing fluids. They have a few divisions that do board inspection. They have one that does plasma cleaning-
Mm-hmm.
-it's very common, I think it's MARCH - - I think is the name of it, something like that, but primarily we focus on fluid dispensing; got lots of patents on fluid dynamics, how to dispense a dot of material that's the exact amount of the material, in the right viscosity, of the right mix of materials, and at the right place , at the right time.
Right.
Very, very challenging stuff - we've come up with some really high tech equipment that are making our customers real happy.
That's great, so when you do, on a practical, where the rubber meets the road stuff - when you embark on a new design - do you get the stakeholders together? I mean how do you do that?
We get a large number of them involved. We have a purchasing department that cares about who our primary suppliers are. They review them; we go qualify them, make sure that they're going to be able to supply what we want, when we want it, at the price we want it. We use third-party vendors to make the boards, assemble the boards, test them. We put everything together in-house. They call us a system integrator kind of thing - and I guess that's one way to refer it. So the final assembly stuff all happens in the factory; and then we ship overseas and here in the United States and Europe.
So you used a term which I've heard before and just tell me what it means to you, is the term 'concurrent engineering'?
I was introduced to that a while back, and to me it was confusing at first. Of course I've been in the industry a long time and there used to be a model where engineering would be a little black box and inside, all the engineers do all their stuff in there, and it was black magic, and they got it all done and then they went; pop - and they threw it over the fence and said: okay, you guys figure out how to make it. And that's as far as they went. Engineers were done; okay, I'm working on my next thing have fun. And the manufacturing engineers get it and go: oh my god, how are we gonna build this thing? And they almost had to re-engineer it to make it producible. So that model was going along for quite a long time here in the United States, before they started analyzing what the Japanese were doing and looking at their manufacturing process. It was very organized, and they introduced just-in-time, which has affected the whole supplier chain.
But partnering with other companies to be able to be successful has become a big deal and they can reduce the number of staff that they need to do what they need to do. They can have highly qualified people doing what they need to do - they don't need masses of people - and then they can subcontract things out get them delivered on time, put them together and get them out the door and they're very very good at it.
Concurrent engineering means thinking about everything up front. Not just your part of putting it in a black box and playing around with it until you're happy and then flipping it out and saying: you guys figure out how to build it. You want to bring the people that are stakeholders in up front. And then together, you move as a group. And the people involved in the engineering part of it have to understand those people's jobs, because they're their customers.
Right.
They're the ones - they're gonna use what they create. So we spend more time up front to make sure that they don't have to work harder, that they don't have to redo it, that we don't waste money and time out there with failures and have to come back and make changes and send it back out, saying: how about this one? No that's not good enough you've got to do it again. Oh how about that one? No that's not good either. So you educate the people that have control of it - they put the intelligence into it to take care of them and everything goes smoothly, and we make a lot more product, a lot less expensive, and that's right the first time.
You and I were swapping some little statements right? So one I remember you saying - - I don't remember who you cited: the hurrier I go...
That was my dad...
-that was your dad.
Yeah 'the hurrier I go, the behinder I get'.
[laughter]
Yeah and that's so true I mean it's funny if you have this: I'm the only important person in the world, and what I'm doing is the most important thing and I don't care what anybody else thinks or wants to do. You can create something, in fact, I've seen some amazing sculpture, of components that were soldered together and in the most amazing ways and it was an electrical circuit, it worked, functioned.
Yeah - but if you touched it, it would fail, if you moved it, it would fail. It wasn't built - it was just to see what would happen to the electrons when they get moved around that way. So people - and there's a desire - typically management, has traditionally figured, well - if you whip the horses harder and make them go faster you'll get there sooner.
I have seen that by the way being a board manufacturer and selling to and working with designers. The constraints are brutal sometimes...
They can be.
-and it's like, well if you want me to put out good work, you need to give me a little bit more margin right and so I think, to your point is, you had also said that it's really a myth, the idea of a quick and dirty prototype.
Yeah it really is
- it's kind of a myth - I've worked in environments where there was a philosophy that said: we can be faster if we just slap something together and we go build it and we bring it back and see what it does. I think the people that had that idea probably didn't have any simulation tools. They didn't have any way to predict how it was going to behave - so they would make one and go try it, and then they'd find out how it didn't work and make another adjustment. So I remember working on a board that had 17 or 18 different iterations of them trying different things...
That's so expensive and such a time suck!
-Very expensive and it takes a lot of patience - you just kind of have to work with them and keep going and keep going. But we win when you get a management group who - I happen to work for one - it's very, very smart people, they'd like to do it right the first time. So they spend the extra time upfront. They do the research, they analyze what's going on, and then they go build it. When they build it and bring it in we're like 98 percent there, most of the time. Very few times maybe we get one or two little blue wires and we're good to go and take a few changes boom - you're out the door. And that's a good thing and CAD tools help us do that too, by the way.
Yeah well, and that's a really insightful management team I think, to know that if you take the disciplined time to do it up front, it really saves you so much on the back end in regards to time, money, and resources. I always like John Wooden's quote; he used to say: be quick but don't hurry, it's the same thing - like be nimble and quick - we don't want you dragging your feet but don't be hasty.
I think part of it is just having a good work ethic, the self-discipline to say: you know what, I'm here, I'm gonna focus on this, I'm gonna get it done, and I'm not gonna let Joe come over and talk to me over a half hour about the thing he was doing up on the mountains last weekend, or stop and shoot with people at the water cooler or whatever. I'm gonna stay focused on it and when I'm not here then I'm doing other things, but when I'm here I'm focused. And I think that the managers; they should analyze the people and look and see what kind of people they have, and try to work with them to get them to have that work ethic. We've got lots of distractions in our world, plenty of them, things that can take us all over the place, so it's just a personal discipline I think.
So we talked about, in those cases - I'm thinking about the people that are designers that are listening to us that may not have such an insightful management team as the one you work with and I'm sure you've worked for other less insightful management teams. How do you recommend that you tactfully, and professionally, push back to say, I need five more minutes to get this right - how do you do that?
Well to frame it as pushback, is probably not politically nice but it's a communication. I think one of the things that you don't do, is you don't go off into a dark room somewhere and then pop out with a design later on and they're going: what's happening what's, happening, what's happening. So you have to have a lot of open lines of communication with your team.
We use SVN as a way to load our projects into a common repository and then the other engineers that are working, can download that and refresh it, make it current so the master is in the SVN file. So I'm working on basically a copy that I refresh every time I do some work. And I do that regularly, I don't wait very long and I'm refreshing it - I'd do it many times an hour sometimes. And sometimes maybe I go for a couple hours and then we'll refresh it, but it's mostly based on how much change I have made to it.
The idea is to keep it current and keep the lines of communication with the other people concurrent so that they're aware of what's going on if they're busy working on the schematic while I'm working on the board we can do that in parallel, and I can do my parts get them done and then they can say, oh I found out I have to change this part, or I need this other circuit in there and I've just uploaded it - you can pull it in and and make the changes. And we do that very often.
Which is really great and I know here at Altium, R&D is working very hard to make sure that people can work concurrently and building those subversion networks and, even going beyond that, as we delve into Nexus and other products is to enable that, so you guys are seeing each other work in real time.
Often times this is kind of a neat thing about that tool. We typically, the group I'm in is the new product development group, so we take the 'pie in the sky guys' stuff and we turn it into a product. Then we have Reliability Engineers who have to design a testbed to test the product. So oftentimes when the schematic gets to 90% they've got a copy of it and they're looking at it while we're designing it...
And there's the concurrent engineering isn't there!
-Exactly.
It really is a tool that enables that concurrent chain.
It enables it - so we're able to do that and then the guys in production want to know what's going on with it, so they can pull down a copy and look at it, and then the next time we have a review meeting they'll bring their thoughts to the meeting and they can say: we like what you did over here, but we'd like to change this because it helps us be more efficient, and we can run that back there because we need to do that; we listen to them...
Which is so great.
-having that dynamic - real-time communication - it's really huge in being successful the first time.
Yeah that's great, it's great to hear. So but...
tact is used to push back.
-tact yes.
I used to joke with my boss; did you ever see the movie The Money Pit?
Yes.
And the: we're gonna fix the house and the farmer shows up and says, how long is it gonna take? Two weeks, two weeks. We used to do that. Looks like, wow this will take two weeks. Most people can accept two weeks, but we've got a new tool now at work; Playbook - and it allows them to get all the stakeholders involved in helping us schedule the project. So people who say I'm gonna have my test part of it ready at this time, and I'm gonna have the board ready at this time, and I'm gonna have my schematic ready at this time.
The managers can see the whole thing without having a good run around and bug everybody - it's all right there.
If there's a problem with a schedule - update it so we know what's going on. Tell us, and they get it; they see the impacts, they see when things are going to happen and they can strategize and make plans on how they're gonna pull something in or adjust something to be successful.
That's great to create the level of transparency right?
Yeah so pushback is really more...
Well you know, that makes it sound like the manager's a bad guy. They've got a job to do and they've got to get a product to market in a timely way, at the right cost, so I'm just saying is sometimes to your earlier comment like the whips to the backs - at times it feels like that and sometimes you have to stop and go: okay...
How can I communicate better?
Yes, how can I communicate this in a way that makes me me your ally here?
Exactly.
I want to help you win, we're on the same team by the way, and me getting this done right the first time...
You can help me be successful in doing it the first time, and you, and you, because I want to get all the things that you need into the design. That way you're happy with it and you can make it and you're not gonna go; damn that Bill Brooks - why did he do this?
Oh gosh we love the finger pointing don't we?
Yeah I've lived through a lot of that.
Well Bill, this has been really good and really practical, I think where the rubber meets the road. And this part of the podcast, I sometimes like to call Designers After Hours. I want to particularly focus on what you do after hours because you are a very creative kind of - use both sides of your brain - but you have a very strong right brain. So can you tell us a little bit about what you do after hours when you're not designing boards?
Gosh - let's see; was it 2008? I went through a divorce and I was trying to find something to do with my spare time and I got introduced by another engineer at Datron World Communications where I used to work; and he was taking classes in sculpting and he showed me a picture of a sculpture that he was creating; this head of his wife, and I had met his wife - she was wheelchair bound and it was so neat to see the love, you know. He is caring for her and she needs him to push her around and whatever. But he was making a sculpture of her and I thought that was really cool and the likeness was amazing! I thought, you really did a good job, I was really impressed with it. How in the world did you learn how to do that? Because I'm taking classes in Carlsbad.
Bullshit - what? Nobody teaches that right, I don't see classes for sculpture anywhere. Where do you find that? And he says, no it's real, you should come check it out. So I made a point to go down and meet the teacher and the teacher introduced me to it and I thought, this looks like too much fun I’ve got try it. And that started about a six-year love affair with sculpting. And now I'm currently teaching it so - there's a place called The Green Art House in Fallbrook and every Saturday I've got a class there and I teach sculpting and it's fun.
And we will share this link by the way, because your mind will be blown. He doesn't just do a little hobby sculpting - these are amazing sculptures he makes! And oh my goodness, and then I start prodding him about painting... Oh yeah I would love to take a painting class. Bill says, oh yeah I do that too.
About two years ago - maybe almost three - I was at a gallery where I had my bronze sculptures that I had made from the sculpting studio and I was trying to see how they would be accepted in the public and so forth. So I had them in a gallery and I met a guy there, Richard Struggles who's a teacher, and he teaches how to paint and so I got brave one day and I thought: I could do this. So I went down to Michael's and I went through the paint department found the primary colors and some paintbrushes and a canvas and I said I could do this and I just bought it and took it home and I thought I'll find a picture I like and I'm gonna try it.
Well about three hours later I said, you know it's not bad - it doesn't look too bad, I bet if somebody taught me I could do better. So I asked him, I says I see you teaching people, can I come? He said sure come on down. So that started me learning how to paint and I've done about eight or nine paintings. One of them's a triptych; it's some cheetahs it's hanging in my mother's home, behind her couch and it's real pretty and a lot of horses.
I know I love horses I owned a horse and so I love your sculptures and your paintings of horses.
I used to have horses too - so I know that bond and the connection with the animal - it's amazing.
So anyways, just for giggles we will share Bill's amazing artwork there because he does have a good after-hours gift there. Will you please share with me any - I know you've shared with me some links and things we'll make sure we put those up for our listeners that could glean more information from Bill. Bill's also taught PCB at our local college here, and he has mentored many people as well as being mentored throughout his career.
I can blame that on Rick Hartley.
Rick Hartley who we just had on the podcast today.
Yes he was, in fact, he cornered me. We were doing an interview right after the Top Gun at PCB West, and he said: Bill, you've got a lot of experience. Have you ever thought of mentoring? And I said, no I never thought about it, to me making boards was just a way to get a paycheck. Get paid, go home, buy food take care of family do all that stuff. And that seed it planted, made me seek out the IPC Designers Council and I joined the local group in San Diego, eventually became part of the board, and then I joined the International Group and actually became part of the Executive Committee and also the Education Committee. And I think I've got an Emeritus Status now with them. I mean I've been with them a long time and I've contributed as much as I could. In fact they gave me an award once for contributing to the industry so it's good fun.
Yeah we'll provide all the links we can. We thank you again for joining us Bill.
Thanks for joining us today in office and again this has been Judy Warner with Altium's OnTrack Podcast and Bill Brooks with Nordson ASYMTEK. Thanks for listening, we'll see you next time. Until then, always stay on track.